汽车硬点设计
汽车转向系硬点布置

好 混凝 土的坍落度 ,保证其符合客观需要 。而在灌注过程 中 ,如 措 施 一 吊扣 搭 共 体 的 设 计 与 施 工 【『1.公 路 交 通 技 术 ,2003(5).
果 出现 了堵塞的问题的话 ,此 时需要用备用 的关注 口,有效保障 79-82
(上 接 第 175页 ) 万 向节夹角调整方法为 :逆时针旋转齿轮位置 ,缩 短管柱长
栓 的施工工作 。
六 、结语
为 了提升工作效率 ,降低拱肋 自重 给塔架带来 的危 害 ,各段
中承式钢管混凝 土拱桥施工对于提升桥梁质量有很好 的帮
拱肋间待端 口标高调整完成后 ,可以快速进行焊接处理 。当此环 助 ,但是在施工过程中要很好的把控每一个环 节 ,不但要对施工
节完成后 ,然后放松扣索 。当完成 了全部的钢管拱肋 吊装工作 材料进行管控 ,也要对每一步施工工艺进行 监管 。只有这样 ,才
格 后 ,保证 吊装 就 位 。
便进行 。不仅如此 ,还要具体结合施工现场的具体情况 ,然后 以
在安装过程 中,保证 两岸和上下游位 置的对称一致 ,在此基 此为基础来对 吊杆进行 张拉 ,直到将全桥 的吊杆索力调整 到与
础上进行 吊装 ,同时要做好拱肋风缆绳及拱肋联结的外法兰螺 客观实际需要相 一致 的范围内。
科技风 2016年 4月下
应 用 技 术
现 了超过 了试 吊的位移值 时 ,此时应该严格处理 ,立 即停止 吊装 灌 注工作 的开展 。
行 为 ,然后通过应用 张拉缆风来让塔架 的位移 回到一个 正确的
(二 )纵 、横 梁 及桥 面施 工
范 围 内 。
对于纵 、横梁及桥 面的施工来说 ,要 有效保证 横梁和纵梁的
基于知识的轿车车身硬点布置参数化设计

了符合要求的车身总体造型。
[ 关键词 ] 车车身布置 ; 轿 参数化设计 ; 车身硬 点 ; 知识驱动
[ 中图分类号 ]U 6 .2 43 8 [ 文献标志码 ] B [ 文章编号 ]1 7 — 122 1)3 0 3 — 6 3 34 ( 20 — 0 9 0 0 4
L mm / 0 83 7
知识工程顾问模块实现了简单的基于知识的参数
化设 计 .它能 将 隐含 的设 计实 践嵌 入 整个设 计 过
轴距
2 3 5l
程, 并转化为明确的知识 。 设计人员可以把在产品
设计 中涉及 的行业 设计 标 准 、尺 寸关 联 、尺 寸约
后悬 发动机罩C 点X 位置
p i t fa t o y l y u a e n C t 5 i c mp e e t r t Ba e n t e p rmerc d sg ,Viu lB s c i u e o ma e on u o b d a o tb s d o a i v s o lt d a s. s d o h a a t e i o a i f i n s a a i s s d t k
基于 知识 的轿车车身硬 点布置参数化设计
罗诚 , 李旭 , 马春辉 , 张红 , 郑泽亮 ( 山东理工大学交通与车辆工程学 院 , 山东 淄博 2 54 ) 5 0 9
【 摘要】 参数化的设计方法在车 身设计 中 到 了大量的应用 。利用 Ct 进行 了某轿车车身总布置参数化设 得 aa 5 iv 计。 在其基础上使 用 VsaB s 进行二 次开发 , 建 了知识驱动 的车身硬 点布置参数化设计 系统 , 根据 i l ac u i 构 然后
汽车车身结构设计技术与方法
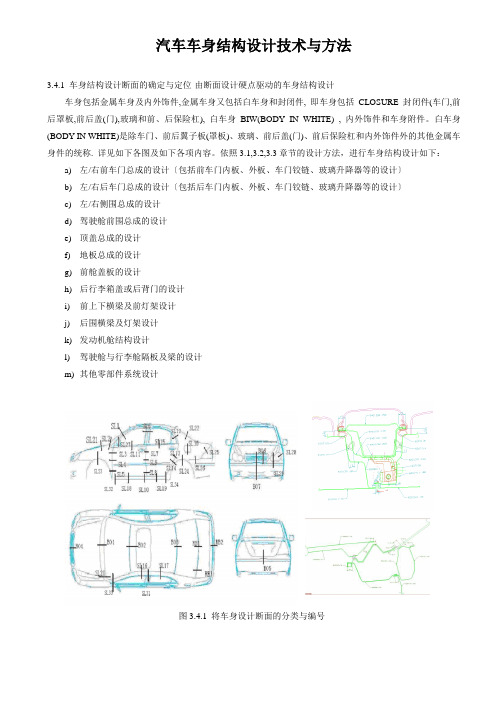
汽车车身结构设计技术与方法3.4.1 车身结构设计断面的确定与定位-由断面设计硬点驱动的车身结构设计车身包括金属车身及内外饰件,金属车身又包括白车身和封闭件, 即车身包括CLOSURE封闭件(车门,前后罩板,前后盖(门),玻璃和前、后保险杠), 白车身BIW(BODY IN WHITE) , 内外饰件和车身附件。
白车身(BODY IN WHITE)是除车门、前后翼子板(罩板)、玻璃、前后盖(门)、前后保险杠和内外饰件外的其他金属车身件的统称. 详见如下各图及如下各项内容。
依照3.1,3.2,3.3章节的设计方法,进行车身结构设计如下:a)左/右前车门总成的设计〔包括前车门内板、外板、车门铰链、玻璃升降器等的设计〕b)左/右后车门总成的设计〔包括后车门内板、外板、车门铰链、玻璃升降器等的设计〕c)左/右侧围总成的设计d)驾驶舱前围总成的设计e)顶盖总成的设计f)地板总成的设计g)前舱盖板的设计h)后行李箱盖或后背门的设计i)前上下横梁及前灯架设计j)后围横梁及灯架设计k)发动机舱结构设计l)驾驶舱与行李舱隔板及梁的设计m)其他零部件系统设计图3.4.1 将车身设计断面的分类与编号图3.4.2 基于参考车型的BENCHMARK断面的断面设计图3.4.3 选定车身密封断面的设计方案车身结构设计的步骤与过程如下所述:图3.4.5 建立benchmark车型白车身数字化原型车设计建模造型面硬点3.4.2 开闭件设计开闭件(CLOSURE)一样包括4门2盖或5门1盖(两厢有后尾门汽车)。
1、车门设计车门外板设计是依照光顺好的整体造型面和车门轮廓线的切割面片基础上加上周边翻边和门锁等特点后的车身零件. 分缝线通过两种方法获得(a)一样先将汽车内外外观面整体造型面光顺到A级曲面(CLASS A), 同时将造型边界线投影到XZ铅垂平面后光顺到A级曲线, 然后采纳该投影的边界线投影到光顺好的A级大造型面上与造型面相交获得的边界线,该交线理论上确信也是A级曲面。
汽车内饰设计多实例解析要点
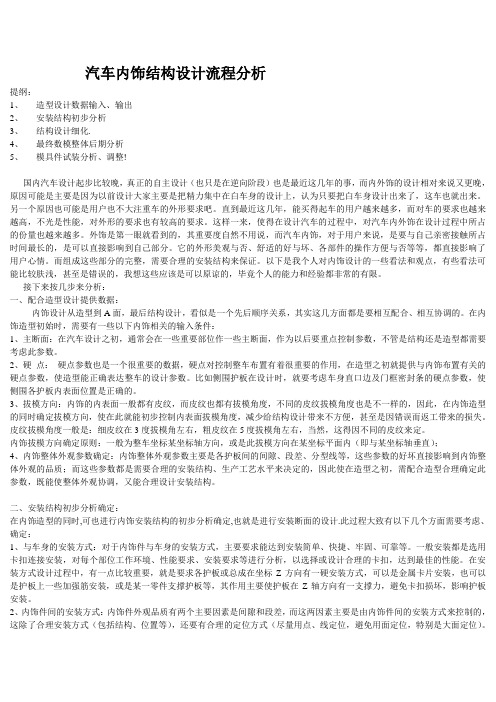
汽车内饰结构设计流程分析提纲:1、造型设计数据输入、输出2、安装结构初步分析3、结构设计细化.4、最终数模整体后期分析5、模具件试装分析、调整!国内汽车设计起步比较晚,真正的自主设计(也只是在逆向阶段)也是最近这几年的事,而内外饰的设计相对来说又更晚,原因可能是主要是因为以前设计大家主要是把精力集中在白车身的设计上,认为只要把白车身设计出来了,这车也就出来。
另一个原因也可能是用户也不大注重车的外形要求吧。
直到最近这几年,能买得起车的用户越来越多,而对车的要求也越来越高,不光是性能,对外形的要求也有较高的要求。
这样一来,使得在设计汽车的过程中,对汽车内外饰在设计过程中所占的份量也越来越多。
外饰是第一眼就看到的,其重要度自然不用说,而汽车内饰,对于用户来说,是要与自己亲密接触所占时间最长的,是可以直接影响到自己部分。
它的外形美观与否、舒适的好与坏、各部件的操作方便与否等等,都直接影响了用户心情。
而组成这些部分的完整,需要合理的安装结构来保证。
以下是我个人对内饰设计的一些看法和观点,有些看法可能比较肤浅,甚至是错误的,我想这些应该是可以原谅的,毕竟个人的能力和经验都非常的有限。
接下来按几步来分析:一、配合造型设计提供数据:内饰设计从造型到A面,最后结构设计,看似是一个先后顺序关系,其实这几方面都是要相互配合、相互协调的。
在内饰造型初始时,需要有一些以下内饰相关的输入条件:1、主断面:在汽车设计之初,通常会在一些重要部位作一些主断面,作为以后要重点控制参数,不管是结构还是造型都需要考虑此参数。
2、硬点:硬点参数也是一个很重要的数据,硬点对控制整车布置有着很重要的作用,在造型之初就提供与内饰布置有关的硬点参数,使造型能正确表达整车的设计参数。
比如侧围护板在设计时,就要考虑车身直口边及门框密封条的硬点参数,使侧围各护板内表面位置是正确的。
3、拔模方向:内饰的内表面一般都有皮纹,而皮纹也都有拔模角度,不同的皮纹拔模角度也是不一样的,因此,在内饰造型的同时确定拔模方向,使在此就能初步控制内表面拔模角度,减少给结构设计带来不方便,甚至是因错误而返工带来的损失。
整车总布置硬点设计规范
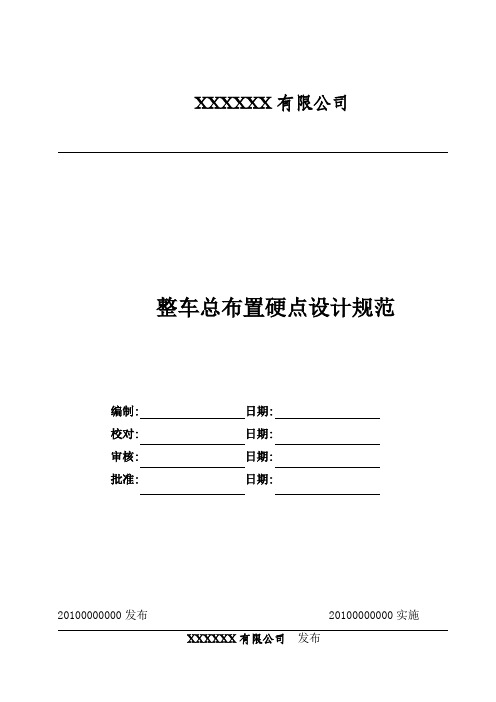
XXXXXX有限公司整车总布置硬点设计规范编制:日期:校对:日期:审核:日期:批准:日期:20100000000发布 20100000000实施XXXXXX有限公司发布目录一概述 (2)二整车设计基准 (2)1.1 整车坐标系 (2)1.2 整车设计状态 (2)三整车总体设计硬点 (3)3.1整车外部尺寸参数控制硬点 (3)3.2底盘系统布置主要控制硬点 (5)3.3人机工程布置设计硬点 (8)四结束语 (9)一概述整车的总布置设计过程是设计硬点(Hard Point)和设计控制规则逐步明确、不断确定的过程。
设计硬点是确定车身、底盘与零部件相互关系的基准点、线、面及控制结构的统称,主要分为安装装配硬点(简称ASH,包括尺寸与型式硬点)、运动硬点(简称MTH)、轮廓硬点及性能硬点等四类。
设计硬点的确定过程就是总布置设计逐步深化的过程,后续的设计工作必须以确定的设计硬点为基础展开。
但随着设计的深入和方案的修改完善,部分设计硬点还有进一步调整的可能。
所有硬点值都是在整车坐标系下的坐标值,长度值表示到小数点后一位,十分位为估计值(四舍五入)。
角度值表示到小数点后一位,十分位为估计值(四舍五入),用度分秒表示时书写到分。
长度单位未注明均为mm,角度单位未注明均为°。
所有未注明的安装硬点均指与车身配合面上车身孔的几何中心点的坐标,例如:配合圆孔的坐标指配合面车身圆孔圆心坐标,椭圆孔或长圆孔的坐标指配合面椭圆孔或长圆孔的几何中心点的坐标,方形孔的坐标指配合面对角线交点的坐标。
二整车设计基准1.1 整车坐标系电动乘用车设计过程中,整车总布置在设计软件三维环境下进行。
整车坐标系采用右手坐标系,它是总布置设计和详细设计中的基准线。
整车坐标系与设计软件中整车文件的绝对坐标系重合。
整车坐标系的定义如下:高度方向,取汽车车架中间平直段的上平面为Z轴零线,上正下负;宽度方向,取汽车的纵向对称中心线为Y轴零线,以汽车前进方向左负右正;长度方向,取通过设计载荷时汽车前轮中心的垂线为X轴零线,前负后正;整车坐标系原点即为三个坐标轴的交点。
整车总布置设计硬点校核
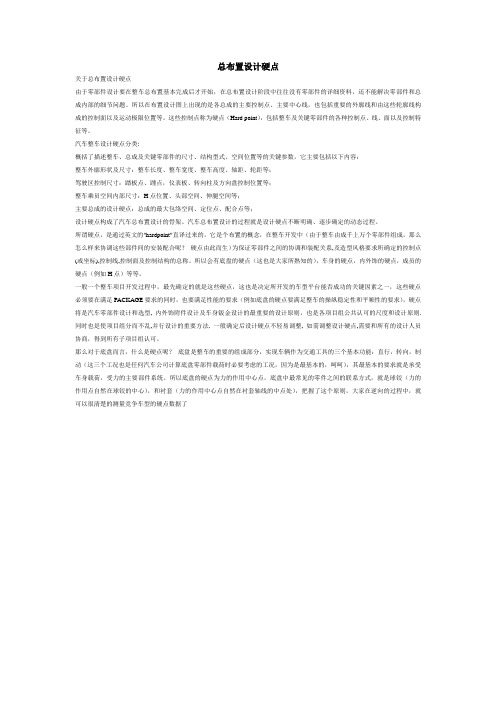
总布置设计硬点关于总布置设计硬点由于零部件设计要在整车总布置基本完成后才开始,在总布置设计阶段中往往没有零部件的详细资料,还不能解决零部件和总成内部的细节问题。
所以在布置设计图上出现的是各总成的主要控制点、主要中心线,也包括重要的外廓线和由这些轮廓线构成的控制面以及运动极限位置等。
这些控制点称为硬点(Hard point),包括整车及关键零部件的各种控制点、线、面以及控制特征等。
汽车整车设计硬点分类:概括了描述整车、总成及关键零部件的尺寸、结构型式、空间位置等的关键参数,它主要包括以下内容:整车外廓形状及尺寸:整车长度、整车宽度、整车高度、轴距、轮距等;驾驶区控制尺寸:踏板点、踵点,仪表板、转向柱及方向盘控制位置等;整车乘员空间内部尺寸:H点位置、头部空间、伸腿空间等;主要总成的设计硬点:总成的最大包络空间、定位点、配合点等;设计硬点构成了汽车总布置设计的骨架。
汽车总布置设计的过程就是设计硬点不断明确、逐步确定的动态过程。
所谓硬点,是通过英文的"hardpoint"直译过来的,它是个布置的概念,在整车开发中(由于整车由成千上万个零部件组成,那么怎么样来协调这些部件间的安装配合呢?硬点由此而生)为保证零部件之间的协调和装配关系,及造型风格要求所确定的控制点(或坐标),控制线,控制面及控制结构的总称。
所以会有底盘的硬点(这也是大家所熟知的),车身的硬点,内外饰的硬点,成员的硬点(例如H点)等等。
一般一个整车项目开发过程中,最先确定的就是这些硬点,这也是决定所开发的车型平台能否成功的关键因素之一,这些硬点必须要在满足PACKAGE要求的同时,也要满足性能的要求(例如底盘的硬点要满足整车的操纵稳定性和平顺性的要求),硬点将是汽车零部件设计和选型, 内外饰附件设计及车身钣金设计的最重要的设计原则,也是各项目组公共认可的尺度和设计原则.同时也是使项目组分而不乱,并行设计的重要方法. 一般确定后设计硬点不轻易调整, 如需调整设计硬点,需要和所有的设计人员协商,得到所有子项目组认可。
汽车设计过程中的硬点研究与控制
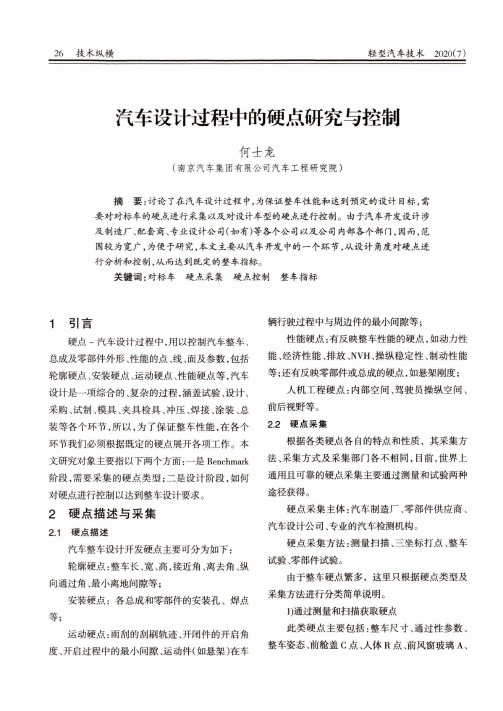
26 技术纵横轻型汽车技术2020(7)汽车设计过程中的硬点研究与控制何士龙(南京汽车集团有限公司汽车工程研究院)摘要:讨论了在汽车设计过程中,为保证整车性能和达到预定的设计目标,需要对对标车的硬点进行采集以及对设计车型的硬点进行控制。
由于汽车开发设计涉及制造厂、配套商、专业设计公司(如有)等各个公司以及公司内部各个部门,因而,范围较为宽广,为便于研究,本文主要从汽车开发中的一个环节,从设计角度对硬点进行分析和控制,从而达到既定的整车指标。
关键词:对标车硬点采集硬点控制整车指标1引言硬点-汽车设计过程中,用以控制汽车整车、总成及零部件外形、性能的点、线、面及参数,包括 轮廓硬点、安装硬点、运动硬点、性能硬点等,汽车 设计是一项综合的、复杂的过程,涵盖试验、设计、采购、试制、模具、夹具检具、冲压、焊接、涂装、总 装等各个环节,所以,为了保证整车性能,在各个 环节我们必须根据既定的硬点展开各项工作。
本 文研究对象主要指以下两个方面:一是Benchmark 阶段,需要采集的硬点类型;二是设计阶段,如何 对硬点进行控制以达到整车设计要求。
2硬点描述与采集2.1硬点描述汽车整车设计开发硬点主要可分为如下:轮廓硬点:整车长、宽、高,接近角、离去角、纵 向通过角、最小离地间隙等;安装硬点:各总成和零部件的安装孔、焊点 等;运动硬点:雨刮的刮刷轨迹、开闭件的开启角 度、开启过程中的最小间隙、运动件(如悬架)在车辆行驶过程中与周边件的最小间隙等;性能硬点:有反映整车性能的硬点,如动力性 能、经济性能、排放、NVH、操纵稳定性、制动性能 等;还有反映零部件或总成的硬点,如悬架刚度;人机工程硬点:内部空间、驾驶员操纵空间、前后视野等。
2.2硬点采集根据各类硬点各自的特点和性质,其采集方 法、采集方式及采集部门各不相同,目前,世界上 通用且可靠的硬点采集主要通过测量和试验两种 途径获得。
硬点采集主体:汽车制造厂、零部件供应商、汽车设计公司、专业的汽车检测机构。
整车总布置硬点分析

-427.5 427.5
45.4 45.4
855
总布置:
1
前减震器总成 (2905-100)
1
5
2
2
4
3
6
3
5
6
4
序号
1 2 3 4 5 6
硬点名称
左前减振器安装孔中心(翻边、上表面)前 右前减振器安装孔中心(翻边、上表面)前 左前减振器安装孔中心(翻边、上表面)后左 右前减振器安装孔中心(翻边、上表面)后右 左前减振器安装孔中心(翻边、上表面)后右 右前减振器安装孔中心(翻边、上表面)后左
-17.7
前悬架上支点 X:15.8;Y:±555.5;Z:596.4
后副车架前安装点 X:2553.3;Y:±469.9;Z:
142.8
后悬架后衬套中心点 X:2718.3;Y:±621.4;
Z:-28.3
后悬架上支点 X:2629.7;Y:±566;Z:
622.4
安装硬点
1
底盘部件,如悬架,副车架与车身的定位面,安 装螺丝孔等是车身设计的基准和控制点。
重要底盘部件之间安装控制点,如转向器输 入端,转向拉杆与转向节安装点
门锁,玻璃升降器等内饰件,车身附件与车身安 装的点线面,是车身设计的基准和控制点。
空调和电器部件与车身安装的点线面
序 号
设计硬点
发动机曲轴中心线
整车总布置硬点分析
1.汽车硬点定义
总布置设计过程中,为保证零部件之间的协调 和装配关系,及造型风格要求所确定的控制点 (或坐标)、控制线、控制面及控制结构的总称, 俗称设计硬点,英美称为HARDPOINT。 这是 汽车零部件设计和选型,附件设计及车身设 计的最重要的各项目组公共认可的尺度和设 计原则。