锌合金压铸产生缩孔的原因
压铸内部缩孔原因

压铸内部缩孔原因
压铸是一种常见的金属加工方法,它通过将熔融金属注入到模具中,然后冷却凝固,最终得到所需的零件或产品。
然而,在压铸过程中,有时会出现内部缩孔的问题。
那么,为什么会出现压铸内部缩孔呢?压铸内部缩孔的原因之一是熔融金属的气体含量过高。
在金属熔化的过程中,如果没有采取适当的措施去除气体,那么在注入模具时,气体就会被封闭在金属内部。
当金属冷却凝固时,气体会被困在缩孔中,形成内部缩孔。
金属液体的流动性也会影响内部缩孔的形成。
如果金属液体的流动性不好,那么在注入模具时,金属液体会在一定地方停滞不前,无法填充整个模具空腔。
这样,就会在停滞的地方形成内部缩孔。
模具的设计和制造也会对内部缩孔产生影响。
如果模具的冷却系统设计不合理,导致金属在注入模具之前过早冷却,那么金属液体就会凝固不完全,形成内部缩孔。
另外,如果模具的排气系统不畅通,气体无法及时排出模具,也会造成内部缩孔的形成。
金属的成分和温度也会对内部缩孔产生影响。
在压铸过程中,如果金属的成分不均匀或掺杂有其他杂质,就会导致凝固不均匀,形成内部缩孔。
而金属温度过高或过低,也会影响金属的凝固过程,从而导致内部缩孔的形成。
总结起来,压铸内部缩孔的原因主要包括熔融金属的气体含量过高、
金属液体的流动性不好、模具设计和制造问题以及金属的成分和温度等因素。
为了避免内部缩孔的产生,需要在压铸过程中注意控制气体含量、优化金属流动性、合理设计和制造模具,并对金属的成分和温度进行合理控制。
只有在各个方面都做好了工作,才能有效地避免压铸内部缩孔的问题的发生,从而提高产品质量和生产效率。
铸件缩孔缩松产生的原因

铸件缩孔缩松产生的原因
一、金属铸件缩孔缩松的原因
1、模具质量不合格:模具的表面没有经过预处理,工作表面毛糙度不够,加工精度不高,导致熔模渗入的位置不正确,从而影响铸件缩孔的精度。
2、砂芯质量不合格没有经过预处理或抛光处理,表面毛糙度不均,加工精度低,砂芯内部出现裂纹,导致不同部位的造型不稳定,从而影响铸件缩孔的精度。
3、工艺条件不合理:模具配套不当,熔模温度过高或过低,模具保温不足,充型压力不足,熔模渗入缓慢,从而影响铸件缩孔的精度。
4、冷却不当:铸件出模后,冷却时间过长或过短,容易出现开裂现象,从而影响铸件缩孔的精度。
二、金属铸件缩孔缩松的改善措施
1、严格模具质量:采用高强度的整体钢,并且经过精密加工,表面经过研磨抛光,以保证熔模渗入的位置准确,从而提高铸件缩孔的精度。
2、严格砂芯质量:采用高质量的砂芯,经过彻底的预处理,能够保证砂芯表面毛糙度均匀,加工精度高,避免出现裂纹,从而确保缩孔的精度。
3、调整熔模温度:严格控制熔模的温度,熔模温度过高可以导致金属分子值过大,熔态液体容易流失。
压铸件的缩孔缩松问题解决方案
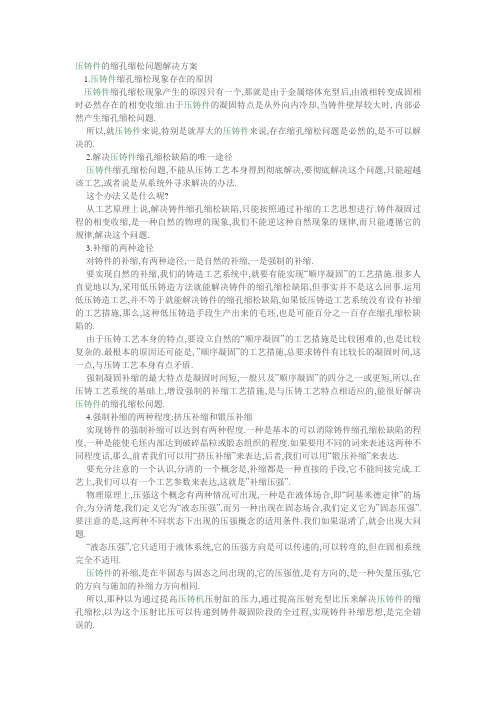
压铸件的缩孔缩松问题解决方案1.压铸件缩孔缩松现象存在的原因压铸件缩孔缩松现象产生的原因只有一个,那就是由于金属熔体充型后,由液相转变成固相时必然存在的相变收缩.由于压铸件的凝固特点是从外向内冷却,当铸件壁厚较大时, 内部必然产生缩孔缩松问题.所以,就压铸件来说,特别是就厚大的压铸件来说,存在缩孔缩松问题是必然的,是不可以解决的.2.解决压铸件缩孔缩松缺陷的唯一途径压铸件缩孔缩松问题,不能从压铸工艺本身得到彻底解决,要彻底解决这个问题,只能超越该工艺,或者说是从系统外寻求解决的办法.这个办法又是什么呢?从工艺原理上说,解决铸件缩孔缩松缺陷,只能按照通过补缩的工艺思想进行.铸件凝固过程的相变收缩,是一种自然的物理的现象,我们不能逆这种自然现象的规律,而只能遵循它的规律,解决这个问题.3.补缩的两种途径对铸件的补缩,有两种途径,一是自然的补缩,一是强制的补缩.要实现自然的补缩,我们的铸造工艺系统中,就要有能实现“顺序凝固”的工艺措施.很多人直觉地以为,采用低压铸造方法就能解决铸件的缩孔缩松缺陷,但事实并不是这么回事.运用低压铸造工艺,并不等于就能解决铸件的缩孔缩松缺陷,如果低压铸造工艺系统没有设有补缩的工艺措施,那么,这种低压铸造手段生产出来的毛坯,也是可能百分之一百存在缩孔缩松缺陷的.由于压铸工艺本身的特点,要设立自然的“顺序凝固”的工艺措施是比较困难的,也是比较复杂的.最根本的原因还可能是, ”顺序凝固”的工艺措施,总要求铸件有比较长的凝固时间,这一点,与压铸工艺本身有点矛盾.强制凝固补缩的最大特点是凝固时间短,一般只及”顺序凝固”的四分之一或更短,所以,在压铸工艺系统的基础上,增设强制的补缩工艺措施,是与压铸工艺特点相适应的,能很好解决压铸件的缩孔缩松问题.4.强制补缩的两种程度:挤压补缩和锻压补缩实现铸件的强制补缩可以达到有两种程度.一种是基本的可以消除铸件缩孔缩松缺陷的程度,一种是能使毛坯内部达到破碎晶粒或锻态组织的程度.如果要用不同的词来表述这两种不同程度话,那么,前者我们可以用“挤压补缩”来表达,后者,我们可以用“锻压补缩”来表达.要充分注意的一个认识,分清的一个概念是,补缩都是一种直接的手段,它不能间接完成.工艺上,我们可以有一个工艺参数来表达,这就是”补缩压强”.物理原理上,压强这个概念有两种情况可出现,一种是在液体场合,即“阿基米德定律”的场合,为分清楚,我们定义它为“液态压强”,而另一种出现在固态场合,我们定义它为”固态压强”.要注意的是,这两种不同状态下出现的压强概念的适用条件.我们如果混淆了,就会出现大问题.“液态压强”,它只适用于液体系统,它的压强方向是可以传递的,可以转弯的,但在固相系统完全不适用.压铸件的补缩,是在半固态与固态之间出现的,它的压强值,是有方向的,是一种矢量压强,它的方向与施加的补缩力方向相同.所以,那种以为通过提高压铸机压射缸的压力,通过提高压射充型比压来解决压铸件的缩孔缩松,以为这个压射比压可以传递到铸件凝固阶段的全过程,实现铸件补缩思想,是完全错误的.5.采用“先压铸充型,后模锻补缩”的工艺,是解决铸件缩孔缩松缺陷的有效途径,也是一种终极手段.“先压铸充型,后模锻补缩”的工艺,我们可简称为“压铸模锻”工艺.它的本质,是一种连铸连锻工艺,就是将压铸工艺与液态模锻工艺相结合,将这两种设备的最有效功能组合在一起,完成整个工艺过程.这种连铸连锻的“压铸模锻”设备,外型与普通立式或卧式的压铸机很相似,其实就是在压铸机上,增加了液压的锻压头.可以加上的最大锻压补缩力,能等于压铸机的最大锁模力.要注意的是,这种压铸模锻机最重要的公称参数,并不是锁模力,而是模锻补缩力,相当于四柱油压机的锻压力意义,这是我们在设备选择时必须充分留意的.不然,买了一台锁模力很大,但模锻补缩力很小的压铸模锻设备,其使用价值就大打折扣了.运用这种压铸模锻机生产的毛坯,尺寸精度很高,表面光洁度也极高,可以相当于6级以上机加工手段所能达到的精度与表面粗糙度水平.它已能归属于“极限成形”----的工艺手段,比“无切削少余量成形”工艺更进了一步研究对既定条件下压铸模具的压铸工艺参数进行快速择定。
分析铸造缩松缺陷形成原因及对策

分析铸造缩松缺陷形成原因及对策铸造缩孔缺陷是在铸造过程中常见的一种问题,它会给制造业带来很多麻烦和损失。
本文将分析铸造缩孔缺陷的形成原因,并提出相应的对策,以期为相关行业提供帮助和指导。
一、铸造缩孔缺陷的形成原因分析1.1 完全凝固不均匀在铸造过程中,铸件凝固是逐渐进行的,如果凝固速度不均匀,就会导致缩孔缺陷的形成。
常见的原因包括铸件的凝固时间过短、冷却速度不均匀、局部温度过高等。
1.2 金属液收缩过大铸造过程中,金属液在凝固过程中会收缩,如果收缩过大,就容易形成缩孔。
这主要是由于铸件材料的物理性质不合理,或者是铸型的设计不合理所导致的。
1.3 铸造材料含有气体铸造材料中含有气体会在凝固过程中释放出来,如果释放过快,就会形成孔洞。
常见的原因是铸造材料中含有气体的含量过高,或者是在铸造过程中没有采取有效的排气措施。
1.4 基材与液态金属的相容性差如果铸件的基材与液态金属的相容性差,就容易在凝固过程中产生裂纹和缩孔。
一般来说,基材与液态金属的相容性差会导致界面张力增大,从而影响凝固过程。
二、对策提出2.1 优化铸造工艺参数通过优化铸造工艺参数,可以降低缩孔缺陷的发生概率。
具体来说,可以调整金属液的浇注温度和速度,控制铸件的凝固时间,改进冷却系统等措施。
2.2 优化铸造材料选择合适的铸造材料也是减少缩孔缺陷的关键。
应选择具有较低的收缩率和较好的流动性的材料,以确保凝固过程中的收缩程度可控。
2.3 采取有效的排气措施在铸造过程中,采取有效的排气措施可以减少气体对铸件凝固过程的干扰,从而降低缩孔缺陷的风险。
排气措施可以包括加入剂、提高浇注温度、采取适当的连续浇注等。
2.4 提高基材与液态金属的相容性为了减少缩孔缺陷的形成,可以通过提高基材与液态金属的相容性来增加界面的稳定性。
可以通过改变基材化学成分、调整金属液的配方等方式来实现。
三、结语以上是对铸造缩孔缺陷形成原因及对策的分析。
通过优化铸造工艺、材料选择、排气措施以及提高基材与液态金属的相容性等方法,可以有效降低缩孔缺陷的发生概率,提高铸件的质量和产能。
铸件缩孔、缩松产生的原因
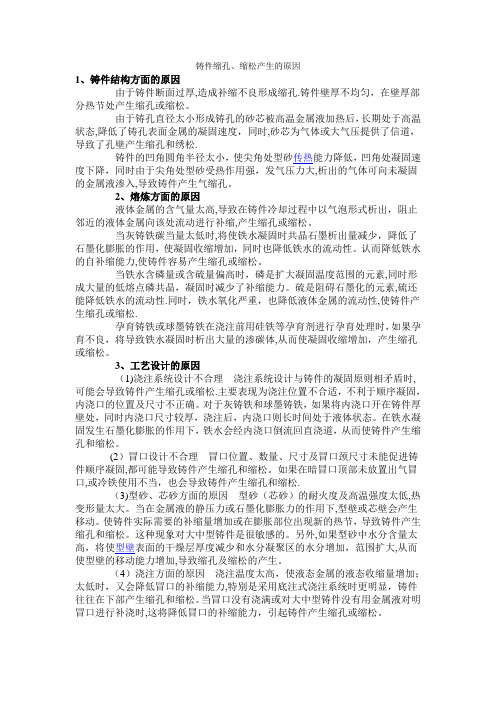
铸件缩孔、缩松产生的原因1、铸件结构方面的原因由于铸件断面过厚,造成补缩不良形成缩孔.铸件壁厚不均匀,在壁厚部分热节处产生缩孔或缩松。
由于铸孔直径太小形成铸孔的砂芯被高温金属液加热后,长期处于高温状态,降低了铸孔表面金属的凝固速度,同时,砂芯为气体或大气压提供了信道,导致了孔壁产生缩孔和绣松.铸件的凹角圆角半径太小,使尖角处型砂传热能力降低,凹角处凝固速度下降,同时由于尖角处型砂受热作用强,发气压力大,析出的气体可向未凝固的金属液渗入,导致铸件产生气缩孔。
2、熔炼方面的原因液体金属的含气量太高,导致在铸件冷却过程中以气泡形式析出,阻止邻近的液体金属向该处流动进行补缩,产生缩孔或缩松。
当灰铸铁碳当量太低时,将使铁水凝固时共晶石墨析出量减少,降低了石墨化膨胀的作用,使凝固收缩增加,同时也降低铁水的流动性。
认而降低铁水的自补缩能力,使铸件容易产生缩孔或缩松。
当铁水含磷量或含硫量偏高时,磷是扩大凝固温度范围的元素,同时形成大量的低熔点磷共晶,凝固时减少了补缩能力。
硫是阻碍石墨化的元素,硫还能降低铁水的流动性.同时,铁水氧化严重,也降低液体金属的流动性,使铸件产生缩孔或缩松.孕育铸铁或球墨铸铁在浇注前用硅铁等孕育剂进行孕育处理时,如果孕育不良,将导致铁水凝固时析出大量的渗碳体,从而使凝固收缩增加,产生缩孔或缩松。
3、工艺设计的原因(1)浇注系统设计不合理浇注系统设计与铸件的凝固原则相矛盾时,可能会导致铸件产生缩孔或缩松.主要表现为浇注位置不合适,不利于顺序凝固,内浇口的位置及尺寸不正确。
对于灰铸铁和球墨铸铁,如果将内浇口开在铸件厚壁处,同时内浇口尺寸较厚,浇注后,内浇口则长时间处于液体状态。
在铁水凝固发生石墨化膨胀的作用下,铁水会经内浇口倒流回直浇道,从而使铸件产生缩孔和缩松。
(2)冒口设计不合理冒口位置、数量、尺寸及冒口颈尺寸未能促进铸件顺序凝固,都可能导致铸件产生缩孔和缩松。
如果在暗冒口顶部未放置出气冒口,或冷铁使用不当,也会导致铸件产生缩孔和缩松.(3)型砂、芯砂方面的原因型砂(芯砂)的耐火度及高温强度太低,热变形量太大。
压铸件缩孔产生的原因

压铸件缩孔产生的原因
压铸件缩孔产生的原因如下:
1、材料问题。
压铸件内部缩孔与材料的含气量有关。
如果铸件所用材料中含气过多,就容易导致压铸件内部产生缩孔。
2、制造工艺问题。
制造工艺也是产生压铸件内部缩孔的一个重要原因。
压铸件的制造过程中,须保证熔金温度、铸造压力的稳定性,如果这些参数设定不当,就会导致材料内部出现过多气泡而产生缩孔。
3、设计问题。
良好的设计可以减少压铸件内部产生缩孔的可能性。
如果冷却功能失效,压铸件一直处于膨胀状态,内部气孔膨胀过多,从而导致压铸表面出现明显的缩孔。
此外,型芯本身也有关系,如果型芯料太硬或太薄,也会出现缩孔现象。
4、冷却不足。
如果冷却功能失效,压铸件一直处于膨胀状态,内部气孔膨胀过多,从而导致压铸表面出现明显的缩孔。
此外,型芯本身也有关系,如果型芯料太硬或太薄,也会出现缩孔现象。
锌合金压铸件缺陷及原因
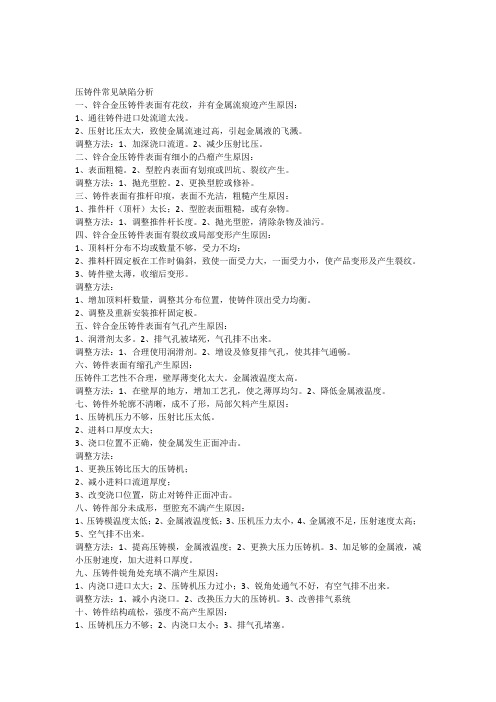
压铸件常见缺陷分析一、锌合金压铸件表面有花纹,并有金属流痕迹产生原因:1、通往铸件进口处流道太浅。
2、压射比压太大,致使金属流速过高,引起金属液的飞溅。
调整方法:1、加深浇口流道。
2、减少压射比压。
二、锌合金压铸件表面有细小的凸瘤产生原因:1、表面粗糙。
2、型腔内表面有划痕或凹坑、裂纹产生。
调整方法:1、抛光型腔。
2、更换型腔或修补。
三、铸件表面有推杆印痕,表面不光洁,粗糙产生原因:1、推件杆(顶杆)太长;2、型腔表面粗糙,或有杂物。
调整方法:1、调整推件杆长度。
2、抛光型腔,清除杂物及油污。
四、锌合金压铸件表面有裂纹或局部变形产生原因:1、顶料杆分布不均或数量不够,受力不均:2、推料杆固定板在工作时偏斜,致使一面受力大,一面受力小,使产品变形及产生裂纹。
3、铸件壁太薄,收缩后变形。
调整方法:1、增加顶料杆数量,调整其分布位置,使铸件顶出受力均衡。
2、调整及重新安装推杆固定板。
五、锌合金压铸件表面有气孔产生原因:1、润滑剂太多。
2、排气孔被堵死,气孔排不出来。
调整方法:1、合理使用润滑剂。
2、增设及修复排气孔,使其排气通畅。
六、铸件表面有缩孔产生原因:压铸件工艺性不合理,壁厚薄变化太大。
金属液温度太高。
调整方法:1、在壁厚的地方,增加工艺孔,使之薄厚均匀。
2、降低金属液温度。
七、铸件外轮廓不清晰,成不了形,局部欠料产生原因:1、压铸机压力不够,压射比压太低。
2、进料口厚度太大;3、浇口位置不正确,使金属发生正面冲击。
调整方法:1、更换压铸比压大的压铸机;2、减小进料口流道厚度;3、改变浇口位置,防止对铸件正面冲击。
八、铸件部分未成形,型腔充不满产生原因:1、压铸模温度太低;2、金属液温度低;3、压机压力太小,4、金属液不足,压射速度太高;5、空气排不出来。
调整方法:1、提高压铸模,金属液温度;2、更换大压力压铸机。
3、加足够的金属液,减小压射速度,加大进料口厚度。
九、压铸件锐角处充填不满产生原因:1、内浇口进口太大;2、压铸机压力过小;3、锐角处通气不好,有空气排不出来。
铸件产生缩孔和缩松产生的原因及防止措施(音频讲解,实用方便)

铸件产⽣缩孔和缩松产⽣的原因及防⽌措施(⾳频讲解,实⽤⽅便)铸件缩松、缩孔问题防治⽅案来⾃制造⼯业联盟 00:00 10:29
缩孔是集中在铸件上部或最后凝固部位容积较⼤的孔洞
合⾦的液态收缩和凝固收缩愈⼤、浇注温度愈⾼、铸件愈厚,缩孔的容积愈⼤. 缩松是分
散在铸件某区域内的细⼩缩孔
形成原因:铸件最后凝固区域的收缩未能得到补⾜,或因为合⾦呈糊状凝固,被树枝状晶体
分隔开的⼩液体区难以得到补缩所⾄
逐层凝固合⾦,缩松倾向⼩。
糊状凝固合⾦缩松倾向⼤,缩孔倾向⼩。
防⽌缩孔和缩松的措施 1)选择合适的合⾦成分选⽤近共晶成分或结晶温度范围较
窄的合⾦ 2)⼯艺措施顺序凝固原则,获得没有缩孔的致密铸件。
定向凝固就是在铸
件上可能出现缩孔的厚⼤部位通过安放冒⼝等⼯艺措施,使铸件远离冒⼝的部位先凝固,然后
靠近冒⼝部位凝固,最后冒⼝本⾝凝固。
⽬的是铸件各个部位的收缩都能得到补充,⽽将缩孔转移到冒⼝中,最后予以清除措施
1、安放冒⼝
2、在⼯件厚⼤部位增设冷铁。
压铸件气缩孔产生的机理

压铸件气缩孔产生的机理
压铸件气缩孔产生的机理主要有以下几点:
1. 液态金属内的气体:在压铸过程中,金属液体与温度较高的模具表面接触,其中含有的气体容易被压入金属液中。
当液态金属冷却凝固时,气体会被包裹在金属内部形成气缩孔。
2. 流道和浇口中的气体:在压铸过程中,液态金属通过流道和浇口进入模腔,其中可能存在气体,如空气和水蒸气。
当金属液体充满整个模腔时,气体被包裹在金属内部,当金属冷却凝固时,气体形成气缩孔。
3. 金属液体中的氢气:在压铸过程中,金属液体与水或潮湿空气接触时,水分中的氢气会溶解到金属液体中。
当金属冷却凝固时,溶解的氢气析出并形成气缩孔。
以上是压铸件气缩孔产生的一些常见机理,实际情况可能还会受到其他因素的影响,如金属合金成分、铸造工艺参数等。
为了减少气缩孔的产生,可以采取一些改进措施,如增加充型压力、优化浇注系统设计、改善金属液的纯净度等。
压铸不良原因与措施

压铸不良原因与措施压铸是一种常见的金属加工方法,用于制造各种各样的金属零件。
然而,在压铸过程中常常会出现一些不良情况,导致产品质量下降或无法使用。
以下是一些常见的压铸不良原因及相应的措施。
1.缩孔(针眼)原因:高温熔融金属凝固时,金属液缩小所形成的孔洞。
措施:-控制材料的熔点和凝固温度,避免温度过高。
-提高注入压力和速度,确保金属充实完全。
-控制铸造工艺参数,如浇注温度、压力和速度,减少气体夹杂物。
2.气孔原因:熔融金属中混入空气或水分,冷凝成孔洞。
措施:-净化材料,确保金属液没有杂质。
-增加浇注温度,减少金属和气体冷凝。
-提高注入速度,使气体远离金属液。
3.热裂纹原因:金属在凝固过程中,由于残余应力、金属浓缩和组织缺陷等原因引起的开裂。
措施:-优化铸造工艺,减少或消除金属残余应力。
-控制金属的凝固速度,避免快速凝固造成应力集中。
-添加合适的合金元素,改善金属组织结构。
4.狭长缺陷原因:熔融金属填充模腔的过程中,金属液流动不均匀,形成局部过渡缩小的缺陷。
措施:-设计合理的铸造模具,确保金属液能够均匀填充模腔。
-调整铸造工艺参数,如入口和出口位置、浇注温度和速度,改善金属液流动状态。
-使用合适的流道和浇口设计,使金属流动更加均匀。
5.长气孔原因:金属液注入模腔的过程中,气体无法顺利排出,形成长而突出的孔。
措施:-增大出口尺寸,提高气体排出的通道。
-调整浇注顺序,避免气泡在金属液中积聚。
-使用适当的排气装置,确保顺畅排出气体。
6.表面不良原因:压铸件表面出现裂纹、气孔、疤痕等缺陷。
措施:-增加模具的冷却系统,提高金属液凝固速度。
-优化模具表面处理,减少摩擦和热传导。
-控制铸造工艺参数,如浇注温度和速度,减少金属液与模具的接触时间。
总之,压铸不良的原因和措施是多种多样的,需要根据不同情况采取相应的措施。
通过优化材料、设计模具、调整工艺参数等方法,可以有效地减少压铸不良,提高产品质量。
压铸内部缩孔原因

压铸内部缩孔原因压铸是一种常用的金属成型工艺,广泛应用于汽车、航空航天、军工等领域。
然而,在压铸过程中,会出现一些内部缩孔的问题,严重影响产品质量和性能。
本文将从压铸内部缩孔的原因进行分析,以期提供一些解决方案。
一、热胀冷缩引起的内部缩孔在高温状态下,金属材料会因热胀而膨胀,而在冷却过程中会因冷缩而收缩。
这种热胀冷缩的过程容易导致内部缩孔的形成。
一方面,当金属液体进入模具中,由于模具温度较低,金属液体在冷却过程中会迅速凝固,形成固态金属。
另一方面,由于金属材料的热胀冷缩特性,凝固的固态金属会产生收缩,导致内部形成缩孔。
这种内部缩孔的形成主要与金属材料的热胀冷缩系数有关,热胀冷缩系数越大,缩孔越容易形成。
二、金属液体内部气泡引起的内部缩孔在金属液体中,常常存在一些气体,如氧气、氢气等。
当金属液体进入模具中凝固时,这些气体会被困在金属内部形成气泡。
这些气泡会导致金属内部形成空洞,从而形成内部缩孔。
气泡的形成主要与金属液体的凝固过程有关,凝固过程越快,气泡越容易形成。
三、金属液体中夹杂物引起的内部缩孔金属液体中常常存在一些夹杂物,如氧化物、硫化物等。
这些夹杂物会导致金属内部形成缩孔。
夹杂物的形成主要与金属液体的纯净度有关,纯净度越低,夹杂物越容易形成。
四、模具设计不合理引起的内部缩孔模具设计不合理也会导致内部缩孔的形成。
例如,模具中存在过多的冷却水道,冷却速度过快,金属凝固过程中收缩过大,容易形成缩孔。
另外,模具中存在过多的死角或过于复杂的结构,容易造成金属液体在流动过程中停滞或聚集,也会导致内部缩孔的形成。
为了解决压铸内部缩孔的问题,可以采取以下措施:一、优化金属液体成分,提高金属液体的纯净度,减少夹杂物的形成。
二、合理控制金属液体的温度,避免热胀冷缩过大,减少内部缩孔的形成。
三、优化模具设计,减少冷却水道的数量,控制冷却速度,防止金属凝固过快。
四、合理优化模具结构,避免过多的死角或复杂结构,确保金属液体在流动过程中的均匀性。
如何解决压铸件的缩孔缩松问题

如何解决压铸件的缩孔缩松问题压铸件存在缩孔缩松问题是一个普遍的现象,有没有彻底解决这个问题的方法?答案应该是有的,但它会是什么呢?1、压铸件缩孔缩松现象存在的原因:压铸件缩孔缩松现象产生的原因只有一个,那就是由于金属熔体充型后,由液相转变成固相时必然存在的相变收缩。
由于压铸件的凝固特点是从外向内冷却,当铸件壁厚较大时,内部必然产生缩孔缩松问题。
所以,就压铸件来说,特别是就厚大的压铸件来说,存在缩孔缩松问题是必然的,是不可以解决的。
2、解决压铸件缩孔缩松缺陷的唯一途径:压铸件缩孔缩松问题,不能从压铸工艺本身得到彻底解决,要彻底解决这个问题,只能超越该工艺,或者说是从系统外寻求解决的办法。
这个办法又是什么呢?从工艺原理上说,解决铸件缩孔缩松缺陷,只能按照通过补缩的工艺思想进行。
铸件凝固过程的相变收缩,是一种自然的物理的现象,我们不能逆这种自然现象的规律,而只能遵循它的规律,解决这个问题。
3、补缩的两种途径:对铸件的补缩,有两种途径,一是自然的补缩,一是强制的补缩。
要实现自然的补缩,我们的铸造工艺系统中,就要有能实现“顺序凝固”的工艺措施。
很多人以为,采用低压铸造方法就能解决铸件的缩孔缩松缺陷,但事实并不是这么回事.运用低压铸造工艺,并不等于就能解决铸件的缩孔缩松缺陷,如果低压铸造工艺系统没有设有补缩的工艺措施,那么,这种低压铸造手段生产出来的毛坯,也是可能百分之一百存在缩孔缩松缺陷的。
由于压铸工艺本身的特点,要设立自然的“顺序凝固”的工艺措施是比较困难的,也是比较复杂的.最根本的原因还可能是,“顺序凝固”的工艺措施,总要求铸件有比较长的凝固时间,这一点,与压铸工艺本身有点矛盾。
强制凝固补缩的最大特点是凝固时间短,一般只及“顺序凝固”的四分之一或更短,所以,在压铸工艺系统的基础上,增设强制的补缩工艺措施,是与压铸工艺特点相适应的,能很好解决压铸件的缩孔缩松问题。
4、强制补缩的两种程度:挤压补缩和锻压补缩。
浅谈铸件缩孔缩松产生的原因

浅谈铸件缩孔缩松产生的原因铸件缩孔和缩松是出现在铸件制造过程中的常见缺陷,对铸件的质量和性能产生重要影响。
缩孔和缩松的产生主要有以下几个原因:1.缩孔:缩孔是指铸件中出现内部凹陷或空洞的缺陷。
其主要原因如下:-铸型设计不合理:铸型的收缩系统设计不合理、浇注系统设计不合理、毛坯料和铸型之间的空隙设计不合理等,都会导致金属液在凝固过程中无法顺利填充,从而形成缩孔。
-浇注工艺参数不合理:包括浇注温度过低、浇注速度过快、浇注压力不足等。
这些因素都会影响金属液的流动性和凝固过程,从而产生缩孔。
-快速凝固导致温度梯度大:金属液凝固过程中温度梯度大,会加快金属的凝固速度,导致空洞无法充分填充,形成缩孔。
-毛坯料中夹杂物:毛坯料中的夹杂物如气孔、沙眼等也会导致铸件内部形成缩孔。
2.缩松:缩松是指铸件内部存在小裂纹或局部结构不致密的缺陷。
其主要原因如下:-热应力引起的冷裂纹:在铸造过程中,由于金属液凝固和收缩产生热应力,当应力超过金属的强度时,就会发生冷裂纹,形成缩松。
-毛坯中的气体和夹杂物:毛坯中存在气孔、气泡等夹杂物,会导致铸件内部产生局部脱实和裂纹,形成缩松。
-铸造温度过低:铸造温度过低会导致金属液在凝固过程中形成局部冷凝物,使得金属液无法顺利填充,产生缩松。
-浇注系统设计不合理:浇注系统设计不合理会导致金属液流动不畅,使得铸件内部无法顺利充实,形成缩松。
为防止铸造缺陷的产生,可以采取以下措施:-合理设计铸型:铸型的收缩系统设计要合理,保证金属液顺利充实,并通过改变浇注位置、浇注顺序等因素来减小缩松和缩孔的产生。
-优化浇注工艺参数:要根据具体的铸造材料和结构特点,合理控制浇注温度、浇注速度和浇注压力等参数,以减少缩松和缩孔的产生。
-毛坯清洁处理:在铸造前要对毛坯进行彻底清洁,以排除夹杂物和气泡等缺陷,减少铸件内部缺陷的产生。
-采用适当的热处理工艺:通过热处理来改善铸件内部组织结构,减少缩松和缩孔的产生,提高铸件的力学性能和耐热性能。
锌合金模具收缩率

锌合金模具收缩率
锌合金模具的收缩率是一个复杂的问题,它受到多种因素的影响,包括合金成分、模具设计、制造工艺、冷却速度等等。
一般来说,锌合金模具的收缩率主要在浇注和冷却阶段产生。
在浇注阶段,由于锌合金液体的流动和填充,模具腔体被填满后,液体会在模具内冷却并凝固,导致体积收缩。
在冷却阶段,锌合金从液体冷却到固体,其内部结构发生变化,也会产生收缩。
另外,模具的设计和制造工艺也会对收缩率产生影响。
模具设计时应该考虑到浇注系统和冷却系统的合理布局,以减小收缩率对模具精度的影响。
制造工艺也会影响收缩率,例如铸造温度、模具温度、浇注速度等都会影响最终的收缩量。
锌合金模具的收缩率一般在0.3%~1.5%之间,具体数值取决于上述因素的综合影响。
为了减小收缩率对模具精度的影响,通常需要进行试模和修模,调整模具参数和工艺参数,以达到满意的精度要求。
总之,锌合金模具的收缩率是一个复杂的问题,需要考虑多种因素的综合影响。
为了获得高精度的模具,需要进行充分的试模和修模工作,调整相关参数,以确保模具的稳定性和精度。
同时,在生产过程中也需要对模具进行维护和保养,定期检查和修正模具精度,以保证生产的稳定性和产品质量。
铸件出现缩孔的原因

铸件出现缩孔的原因1. 你知道吗,铸件出现缩孔的一个原因可能是浇注温度不合理呀!就好比煮汤,温度太高或太低都会影响口感,浇注温度不合适,那铸件能好吗?比如浇注温度过高,液态金属收缩大,就容易产生缩孔啦!2. 哎呀,模具设计不合理也会导致缩孔哦!这就像给人做衣服,尺寸不合适怎么能合身呢?如果模具的型腔形状或尺寸不对,金属液的流动和凝固就会受影响,缩孔不就来了嘛,像那种型腔狭窄的地方就很容易出现缩孔呀!3. 喂喂喂,浇注速度也很关键呀!你想想,跑步太快或太慢都可能摔倒吧,浇注速度太快或太慢,铸件也会出问题呀!浇注速度过快,型腔里的气体来不及排出,缩孔就可能出现了,这多糟糕呀!4. 嘿,金属液的化学成分不对也不行呀!这就跟做菜调料放错了一样,味道能好吗?如果金属液中某些成分比例不合适,它的凝固特性改变,缩孔就可能冒出来了,可别小瞧这个呀!5. 哇塞,冷却条件不好也会让铸件出现缩孔呢!好比人在不合适的环境里会不舒服,铸件也是呀!冷却不均匀或者太快太慢,都会引发缩孔问题呢,这可不能马虎!6. 你们知道吗,熔炼工艺不当也是个原因呢!这就像酿酒,工艺不对酒就不香,熔炼工艺不好,铸件就容易有缩孔呀!比如熔炼时间过长或温度过高,都会有影响哦!7. 哎呀呀,铸件的结构设计也得注意呀!如果设计得太复杂或者有不合理的地方,那不就像走迷宫容易迷路一样嘛,缩孔就容易在这些地方出现啦!8. 说真的,浇注系统设计不合理也会惹麻烦呀!这就像交通规划不好会堵车一样,浇注系统设计不好,金属液的流动就不畅,缩孔就可能来啦,可不能随便设计呀!9. 大家想想,冒口设置不合理是不是也会导致缩孔呢?冒口就像是给铸件的一个保障,设置不对,缩孔就容易出现啦,就像没了可靠的后盾一样!10. 最后呀,操作工人的技术水平也很重要呢!就像司机开车技术好坏有很大影响一样,操作不当,铸件出现缩孔的可能性就大啦!我的观点结论就是:铸件出现缩孔的原因有很多,每一个环节都得认真对待,从设计到操作,都不能马虎呀!。
压铸件的缩孔缩松问题解决方案12页word文档
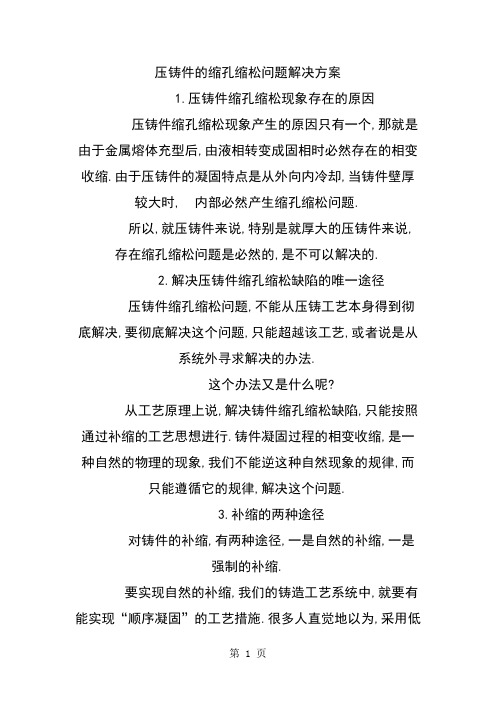
压铸件的缩孔缩松问题解决方案1.压铸件缩孔缩松现象存在的原因压铸件缩孔缩松现象产生的原因只有一个,那就是由于金属熔体充型后,由液相转变成固相时必然存在的相变收缩.由于压铸件的凝固特点是从外向内冷却,当铸件壁厚较大时, 内部必然产生缩孔缩松问题.所以,就压铸件来说,特别是就厚大的压铸件来说,存在缩孔缩松问题是必然的,是不可以解决的.2.解决压铸件缩孔缩松缺陷的唯一途径压铸件缩孔缩松问题,不能从压铸工艺本身得到彻底解决,要彻底解决这个问题,只能超越该工艺,或者说是从系统外寻求解决的办法.这个办法又是什么呢?从工艺原理上说,解决铸件缩孔缩松缺陷,只能按照通过补缩的工艺思想进行.铸件凝固过程的相变收缩,是一种自然的物理的现象,我们不能逆这种自然现象的规律,而只能遵循它的规律,解决这个问题.3.补缩的两种途径对铸件的补缩,有两种途径,一是自然的补缩,一是强制的补缩.要实现自然的补缩,我们的铸造工艺系统中,就要有能实现“顺序凝固”的工艺措施.很多人直觉地以为,采用低压铸造方法就能解决铸件的缩孔缩松缺陷,但事实并不是这么回事.运用低压铸造工艺,并不等于就能解决铸件的缩孔缩松缺陷,如果低压铸造工艺系统没有设有补缩的工艺措施,那么,这种低压铸造手段生产出来的毛坯,也是可能百分之一百存在缩孔缩松缺陷的.由于压铸工艺本身的特点,要设立自然的“顺序凝固”的工艺措施是比较困难的,也是比较复杂的.最根本的原因还可能是, ”顺序凝固”的工艺措施,总要求铸件有比较长的凝固时间,这一点,与压铸工艺本身有点矛盾.强制凝固补缩的最大特点是凝固时间短,一般只及”顺序凝固”的四分之一或更短,所以,在压铸工艺系统的基础上,增设强制的补缩工艺措施,是与压铸工艺特点相适应的,能很好解决压铸件的缩孔缩松问题.4.强制补缩的两种程度:挤压补缩和锻压补缩实现铸件的强制补缩可以达到有两种程度.一种是基本的可以消除铸件缩孔缩松缺陷的程度,一种是能使毛坯内部达到破碎晶粒或锻态组织的程度.如果要用不同的词来表述这两种不同程度话,那么,前者我们可以用“挤压补缩”来表达,后者,我们可以用“锻压补缩”来表达.要充分注意的一个认识,分清的一个概念是,补缩都是一种直接的手段,它不能间接完成.工艺上,我们可以有一个工艺参数来表达,这就是”补缩压强”.物理原理上,压强这个概念有两种情况可出现,一种是在液体场合,即“阿基米德定律”的场合,为分清楚,我们定义它为“液态压强”,而另一种出现在固态场合,我们定义它为”固态压强”.要注意的是,这两种不同状态下出现的压强概念的适用条件.我们如果混淆了,就会出现大问题.“液态压强”,它只适用于液体系统,它的压强方向是可以传递的,可以转弯的,但在固相系统完全不适用.压铸件的补缩,是在半固态与固态之间出现的,它的压强值,是有方向的,是一种矢量压强,它的方向与施加的补缩力方向相同.所以,那种以为通过提高压铸机压射缸的压力,通过提高压射充型比压来解决压铸件的缩孔缩松,以为这个压射比压可以传递到铸件凝固阶段的全过程,实现铸件补缩思想,是完全错误的.5.采用“先压铸充型,后模锻补缩”的工艺,是解决铸件缩孔缩松缺陷的有效途径,也是一种终极手段. “先压铸充型,后模锻补缩”的工艺,我们可简称为“压铸模锻”工艺.它的本质,是一种连铸连锻工艺,就是将压铸工艺与液态模锻工艺相结合,将这两种设备的最有效功能组合在一起,完成整个工艺过程.这种连铸连锻的“压铸模锻”设备,外型与普通立式或卧式的压铸机很相似,其实就是在压铸机上,增加了液压的锻压头.可以加上的最大锻压补缩力,能等于压铸机的最大锁模力.要注意的是,这种压铸模锻机最重要的公称参数,并不是锁模力,而是模锻补缩力,相当于四柱油压机的锻压力意义,这是我们在设备选择时必须充分留意的.不然,买了一台锁模力很大,但模锻补缩力很小的压铸模锻设备,其使用价值就大打折扣了.运用这种压铸模锻机生产的毛坯,尺寸精度很高,表面光洁度也极高,可以相当于6级以上机加工手段所能达到的精度与表面粗糙度水平.它已能归属于“极限成形”----的工艺手段,比“无切削少余量成形”工艺更进了一步研究对既定条件下压铸模具的压铸工艺参数进行快速择定。
锌合金压铸产品缩水的原因及处理方法
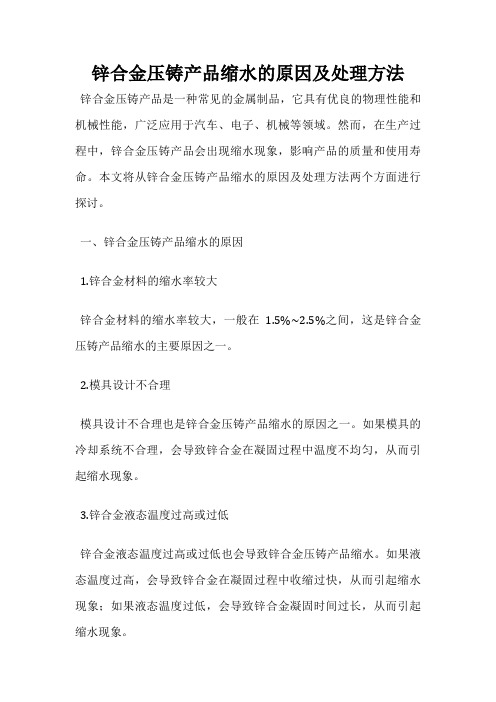
锌合金压铸产品缩水的原因及处理方法锌合金压铸产品是一种常见的金属制品,它具有优良的物理性能和机械性能,广泛应用于汽车、电子、机械等领域。
然而,在生产过程中,锌合金压铸产品会出现缩水现象,影响产品的质量和使用寿命。
本文将从锌合金压铸产品缩水的原因及处理方法两个方面进行探讨。
一、锌合金压铸产品缩水的原因1.锌合金材料的缩水率较大锌合金材料的缩水率较大,一般在1.5%~2.5%之间,这是锌合金压铸产品缩水的主要原因之一。
2.模具设计不合理模具设计不合理也是锌合金压铸产品缩水的原因之一。
如果模具的冷却系统不合理,会导致锌合金在凝固过程中温度不均匀,从而引起缩水现象。
3.锌合金液态温度过高或过低锌合金液态温度过高或过低也会导致锌合金压铸产品缩水。
如果液态温度过高,会导致锌合金在凝固过程中收缩过快,从而引起缩水现象;如果液态温度过低,会导致锌合金凝固时间过长,从而引起缩水现象。
二、锌合金压铸产品缩水的处理方法1.优化模具设计优化模具设计是解决锌合金压铸产品缩水问题的关键。
可以通过改善模具的冷却系统,使锌合金在凝固过程中温度均匀,从而减少缩水现象的发生。
2.控制液态温度控制液态温度也是解决锌合金压铸产品缩水问题的重要措施。
可以通过调整锌合金的液态温度,使其在凝固过程中收缩均匀,从而减少缩水现象的发生。
3.增加锌合金的成分增加锌合金的成分也可以减少锌合金压铸产品的缩水现象。
可以在锌合金中添加一些合适的元素,如铜、铝等,以增加锌合金的流动性和凝固性,从而减少缩水现象的发生。
锌合金压铸产品缩水是一个常见的问题,但是通过优化模具设计、控制液态温度和增加锌合金的成分等措施,可以有效地减少缩水现象的发生,提高锌合金压铸产品的质量和使用寿命。
压铸件螺纹孔处缩孔产生的原因

压铸件螺纹孔处缩孔产生的原因
压铸件螺纹孔处缩孔的产生原因可能有以下几种:
1. 模具设计不合理:模具中螺纹孔的设计、尺寸和形状不合理,导致压力分布不均匀,容易造成局部缩孔。
2. 材料问题:压铸件材料中存在各种夹杂物、气孔等缺陷,当受到压力时,这些缺陷会产生局部应力集中,导致局部缩孔。
3. 压力不均匀:在压力注入过程中,如果压力不稳定或者注入速度不均匀,容易造成螺纹孔处局部缩孔。
4. 组织变化:压铸过程中,材料会受到高温和高压的作用,导致其组织发生变化,如果压力不均匀或者温度不合适,容易产生局部缩孔。
5. 冷却问题:压铸过程中材料的冷却速度也会影响缩孔问题,如果冷却速度过快或者不均匀,容易产生局部缩孔。
综上所述,压铸件螺纹孔处缩孔产生的原因主要与模具设计、材料质量、压力、温度、冷却等因素有关。
- 1、下载文档前请自行甄别文档内容的完整性,平台不提供额外的编辑、内容补充、找答案等附加服务。
- 2、"仅部分预览"的文档,不可在线预览部分如存在完整性等问题,可反馈申请退款(可完整预览的文档不适用该条件!)。
- 3、如文档侵犯您的权益,请联系客服反馈,我们会尽快为您处理(人工客服工作时间:9:00-18:30)。
锌合金压铸产生缩孔的原因
作者:锌合金压铸来源:/
锌合金压铸件表面在以下情况下有鼓起的包称之为起泡,是铸件内缺陷的外部表现。
(1)压铸出来就发现。
(2)抛光或加工后显露出来。
(3)喷漆或电镀后出现。
(4)放置一段时间后发现。
缩孔产生原因:
a、金属液凝固过程中,由于体积缩小或最后凝固部位得不到金属液补缩,而产生缩孔。
b、厚薄不均的铸件或铸件局部过热,造成某一部位凝固慢,体积收缩时表面形成凹位。
由于气孔和缩孔的存在,使压铸件在进行表面处理时,孔洞可能会进入水,当喷漆和电镀后进行烘烤时,孔洞内气体受热膨胀;或孔洞内水会变蒸气,体积膨胀,因而导致铸件表面起泡。
2.晶间腐蚀引起:锌合金成分中有害杂质:铅、镉、锡会聚集在晶粒交界处导致晶间腐蚀,金属基体因晶间腐蚀而破碎,而电镀加速了这一祸害,受晶间腐蚀的部位会膨胀而将镀层顶起,造成铸件表面起泡。
特别是在潮湿环境下晶间腐蚀会使铸件变形、开裂、甚至破碎。
3.裂纹引起:水纹、冷隔纹、热裂纹。
水纹、冷隔纹:金属液在充型过程中,先进入的金属液接触型壁过早凝固,后进入金属液不能和已凝固金属层熔合为一体,在铸件表面对接处形成叠纹,出现条状缺陷,见图2。
水纹一般是在铸件表面浅层;而冷隔纹有可能渗入到铸件内部。
热裂纹:
a、当铸件厚薄不均,凝固过程产生应力;
b、过早顶出,金属强度不够;
c、顶出时受力不均;
d、过高的模温使晶粒粗大;
e、有害杂质存在。
当锌合金压铸件存在水纹、冷隔纹、热裂纹,电镀时溶液会渗入到裂纹中,在烘烤时化为蒸气,气压顶起电镀层形成起泡。