电泳的工艺流程铝合金电泳
[课程]电泳的工艺流程--铝合金电泳
![[课程]电泳的工艺流程--铝合金电泳](https://img.taocdn.com/s3/m/d0dd1e75ce2f0066f4332289.png)
[课程]电泳的工艺流程--铝合金电泳电泳的工艺流程--铝合金电泳电泳的工艺流程--铝合金电泳首先:电泳涂装(electro-coating)是利用外加电场使悬浮于电泳液中的颜料和树脂等微粒定向迁移并沉积于电极之一的基底表面的涂装方法。
电泳涂装的原理发明于是20世纪30年代末,但开发这一技术并获得工业应用是在1963年以后,电泳涂装是近30年来发展起来的一种特殊涂膜形成方法,是对水性涂料最具有实际意义的施工工艺。
具有水溶性、无毒、易于自动化控制等特点,迅速在汽车、建材、五金、家电等行业得到广泛的应用。
电泳涂装是把工件和对应的电极放入水溶性涂料中,接上电源后,依靠电场所产生的物理化学作用,使涂料中的树脂、颜填料在以被涂物为电极的表面上均匀析出沉积形成不溶于水的漆膜的一种涂装方法。
电泳涂装是一个极为复杂的电化学反应过程,其中至少包括电泳、电沉积、电渗、电解四个过程。
电泳涂装按沉积性能可分为阳极电泳(工件是阳极,涂料是阴离子型)和阴极电泳(工件是阴极,涂料是阳离子型);按电源可分为直流电泳和交流电泳;按工艺方法又有定电压和定电流法。
目前在工业上较为广泛采用的是直流电源定电压法的阳极电泳。
1-经表面处理后的工件;2-电源;3-工件;4-喷水冲洗;5-槽液过滤;6-沉积槽;7-循环泵电泳涂装与其他涂装方法相比较,具有下述特点:(1)采用水溶性涂料,以水为溶解介质,节省了大量有机溶剂,大大降低了大气污染和环境危害,安全卫生,同时避免了火灾的隐患;(2)涂装效率高,涂料损失小,涂料的利用率可达90%,95%;(3)涂膜厚度均匀,附着力强,涂装质量好,工件各个部位如内层、凹陷、焊缝等处都能获得均匀、平滑的漆膜,解决了其他涂装方法对复杂形状工件的涂装难题;(4)生产效率高,施工可实现自动化连续生产,大大提高劳动效率;(5)设备复杂,投资费用高,耗电量大,其烘干固化要求的温度较高,涂料、涂装的管理复杂,施工条件严格,并需进行废水处理;(6)只能采用水溶性涂料,在涂装过程中不能改变颜色,涂料贮存过久稳定性不易控制。
电泳处理工艺流程
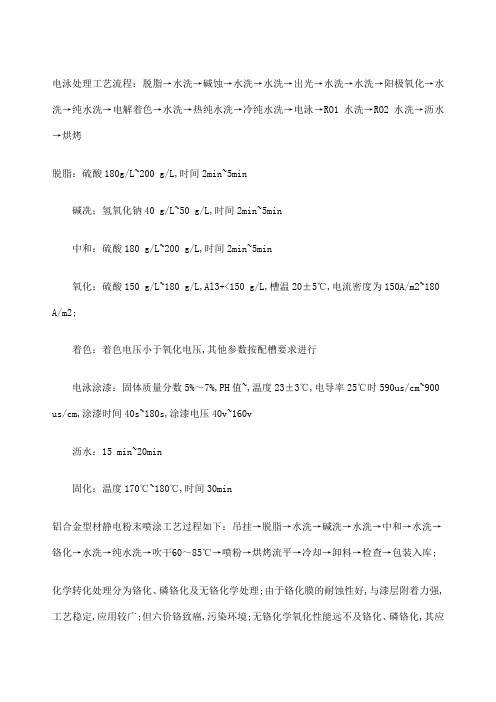
电泳处理工艺流程:脱脂→水洗→碱蚀→水洗→水洗→出光→水洗→水洗→阳极氧化→水洗→纯水洗→电解着色→水洗→热纯水洗→冷纯水洗→电泳→RO1水洗→RO2水洗→沥水→烘烤脱脂:硫酸180g/L~200 g/L,时间2min~5min碱冼;氢氧化钠40 g/L~50 g/L,时间2min~5min中和:硫酸180 g/L~200 g/L,时间2min~5min氧化:硫酸150 g/L~180 g/L,Al3+<150 g/L,槽温20±5℃,电流密度为150A/m2~180 A/m2;着色:着色电压小于氧化电压,其他参数按配槽要求进行电泳涂漆:固体质量分数5%~7%,PH值~,温度23±3℃,电导率25℃时590us/cm~900 us/cm,涂漆时间40s~180s,涂漆电压40v~160v沥水:15 min~20min固化:温度170℃~180℃,时间30min铝合金型材静电粉末喷涂工艺过程如下:吊挂→脱脂→水洗→碱洗→水洗→中和→水洗→铬化→水洗→纯水洗→吹干60~85℃→喷粉→烘烤流平→冷却→卸料→检查→包装入库;化学转化处理分为铬化、磷铬化及无铬化学处理;由于铬化膜的耐蚀性好,与漆层附着力强,工艺稳定,应用较广;但六价铬致癌,污染环境;无铬化学氧化性能远不及铬化、磷铬化,其应用受到一定限制;发展趋势目前,铝型材表面处理工艺相对成熟,其产品也丰富多彩;与发达国家相比,我国铝型材表面处理仍有较大差距,主要表现生产装备落后,环境污染严重,能耗高;因此,未来一定时期,铝型材表面处理的发展趋势是开发并推广清洁环保、高效节能技术,其具体表现为:1喷涂前处理的无铬化学氧化工艺;当前的无铬氧化槽液稳定性和膜层性能仍很难满足要求,需要进一步提高和完善;2环保型电解抛光技术;开发以有机醇为主要成分的电解抛光工艺不但有利环保,而且抛光效果比“传统三酸”更好,发展前途被广为看好;3高速高效阳极氧化技术20;通过改变电流波形、槽液成份等,使成膜速度提高至1μm/min,其生产效率可提高约3倍;4电解着色向多色彩化方向发展;为了生产更多颜色的阳极氧化型材,欧洲开始采用多色化电解着色技术21,即在同一电解着色槽中可以得到红、黄、蓝、灰等多种颜色;该技术已有应用,但大批量生产主要为蓝色、灰色铝型材,其应用仍需进一步研究;5槽液闭路循环回收技术和装备22;阳极氧化生产各工序采用闭路循环回收,不但可以实现低排放或零排放,还可提高槽液稳定性,降低化学品消耗;主要包括氧化槽液除铝回收硫酸;碱蚀槽分离AlOH3回收碱,镍盐电解着色回收镍并除去杂质,常温封闭除沉淀和金属杂质等;6坚固耐划、超强耐候性的电泳涂料;目前电泳漆存在容易出现划痕的缺点,在丰富电泳涂层外观的同时,应开发坚固耐划、耐候性更强的阳极电泳涂料;。
铝合金电泳工艺流程

铝合金电泳工艺流程
铝合金电泳工艺流程是一种将铝合金制品进行表面处理的方法,通过电泳工艺,可以使铝合金制品具有更好的耐腐蚀性和美观度。
下面将介绍一下铝合金电泳工艺流程。
首先,在进行电泳工艺之前,需要对铝合金制品进行预处理。
预处理步骤包括清洗、除油和除氧化等。
清洗的目的是去除铝合金表面的污垢和杂质,保证电泳涂层的附着力。
除油是将表面的油脂和污染物去除,以便涂层的充分附着。
除氧化是消除铝合金表面的氧化膜,获得较好的涂层表面。
接下来是电泳涂装。
首先,将经过预处理的铝合金制品浸入含有活性阴极复合物的电泳漆槽中,形成电泳液。
电泳液中的活性阴极复合物可以为铝合金表面提供触媒,使得附着在铝合金上的电泳漆能够充分固化。
然后,施加电流,使涂有电泳漆的铝合金制品成为阴极,在电泳液中的活性阳离子聚集到铝合金表面。
电泳液中活性阳离子的聚集过程是一个吸附、碳酸化、成膜的过程,形成均匀而致密的电泳涂层。
最后,经过一定时间的电泳,将电泳涂层固化和干燥。
在电泳固化和干燥之后,还需要进行后处理。
后处理包括上光、检查和包装等。
上光是为了提高电泳涂层的光亮度和光洁度,使之更具美观度。
检查是为了确保电泳涂层质量符合要求,没有瑕疵和缺陷。
包装是为了保护电泳涂层,防止在运输和使用过程中受到损坏。
总结起来,铝合金电泳工艺流程包括预处理、电泳涂装和后处
理。
通过这一流程,可以得到具有较好耐腐蚀性和美观度的铝合金制品。
铝合金电泳工艺在建筑、汽车等行业得到广泛应用,成为一种理想的表面处理方法。
铝合金消光电泳涂漆工艺原理

1.铝合金消光电泳涂漆工艺原理铝合金的消光电泳涂漆是在阳极氧化膜的表面进行的。
与光亮电泳类似,其生产工艺流程如下:除油→水洗→碱蚀→水洗→水洗→中和→水洗→阳极氧化→水洗→纯水洗→电解着色→纯水洗→热纯水洗→纯水洗→电泳→RO1水洗→R O2水洗→滴干→预干→固化。
消光电泳与透明电泳基本一致,均是以铝型材作为阳极,在直流电的作用下,发生电化学反应,带电荷的涂料粒子受电场的作用,向被涂物移动,使电泳涂料析出沉积在型材表面,形成一层漆膜,整个反应包括电泳、电解、电沉积和电渗四个同时进行的过程。
不同之处主要包括电泳漆原料和生产工艺参数,消光电泳漆较光亮性电泳漆其分子量要大得多,一般在70000—80000g/mol之间;另外,在工艺控制上,其电泳电压、槽液温度及电泳时间皆有区别,通常情况下,对于同一色号料来说,消光电泳电压、时间及温度都要高于透明电泳,此外,与光亮电泳相比多了一道预干工序,减少阴冷潮湿天气滴干时产生的水迹状物,这与电泳漆特性有密切关系。
2.立式氧化消光电泳涂漆质量影响因素与控制方法普通电泳涂漆并不能掩盖型材的表面缺陷,而消光电泳也只能掩盖小部分基材表面缺陷,且因氧化生产流程较长且流水作业连贯性强,尤其是采用氧化立吊式自动化生产,往往是同一类缺陷在一个时间段所生产的产品中存在较多,每一个工艺阶段产生的缺陷到固化处理后会基本暴露,这也导致电泳型材的成品率比普通氧化型材要低,而消光电泳属于高端产品,其表面处理后的细微缺陷则更易显现出来。
生产中常见缺陷的原因及对策如下:(1)水痕对此类缺陷比较一致的说法是进入电泳槽前型材表面水膜不均匀造成的。
特别是冷天出现概率较大,我们采取减少热纯水洗,延长滴干时间,或是避开阴冷潮湿天气集中生产,对于热天生产出现的少量水痕,一是将型材热水洗后充分冷却,再进人电泳前的纯水槽;再是及时更换一定量的纯水,保证纯水槽温与室温一致;三是将型材快速从纯水槽转移至电泳槽,操作人员动作协调是可以避免这类缺陷出现的。
铝合金电泳工艺

3.电泳工序是电泳涂装工艺过程的核心,是 决定涂装质量的关键工序。需要控制的参数 主要有槽液固体分、PH值、电导率、温度、 电泳电压、电泳时间等。
RO循环水洗是指利用RO(反渗透)回收系 统,把电泳槽液中的部分水分离出来作为经 过电泳后的工件表面的清洗用水,并通过液 位差使水洗水重新溢流回电泳槽以达到电泳 漆回收之目的和保证电泳后水洗水的有关参 数符合工艺要求。RO循环水洗槽控制参数主 要有固体分、 PH值和电导率。
4、电导率 电泳液初始电导率取决于电泳液的固体分、PH值、温度、 纯水的纯净度及杂质离子等因素,控制这些因素即可使 电泳液的初始电导率在正常范围。随着电泳生产过程的 延续,槽液本身产生NH4+及NH3将会使槽液的电导率增大, 同时从前道工序带来的杂质离子也会增加并在电泳槽中 积聚,致使槽液电导率增大,引起电泳液的劣化、电压 下降、泳透力降低,进而引起涂层表面粗糙、针孔等缺 陷增多,严重时造成电泳液的报废。 5、电泳电压 电泳电压是由电泳树脂本身的分子量和结构特性决定的, 一般有适用的电压范围,在此范围内,涂层厚度随电压 的升高而增加。
6、电泳时间 从电泳涂层的厚度增长来看,通电初期 膜厚度增长速率较快,然后增长速率减 缓,一般在2-3min后厚度趋于饱和,故 电泳时间通常为2-3min,电泳时间过长, 会使涂膜有变粗糙的倾向。另外,在电 泳结束后,要尽量缩短工件出槽时间, 以免使涂层再溶解而影响涂层质量。
第五节、电泳涂装主要设备
RCOO-+H+-----RCOOH↓
四、电渗
分散介质向着电泳粒子泳动相反方向运动的现象称
为电渗。在电泳涂装过程中的电渗作用是由于吸附于 阳极上涂层中的水化正离子,在阳极电场的作用下, 产生向负极运动的内渗力,而使其穿透沉积的涂层, 使沉积涂层中的含水量显著减少,所得到的膜水份含 量低至2~5%,而槽中含量90%,非常之大,故未烘 干的涂膜是可冲洗,可直接进行烘烤而得到结构致密、 平整光滑的涂层。
电泳工艺参数
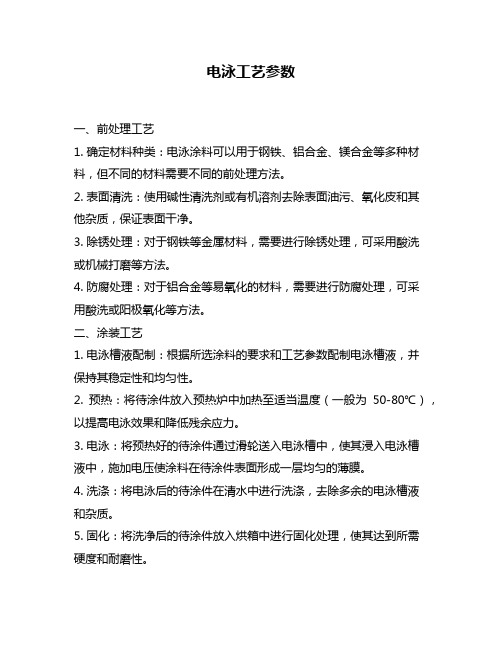
电泳工艺参数一、前处理工艺1. 确定材料种类:电泳涂料可以用于钢铁、铝合金、镁合金等多种材料,但不同的材料需要不同的前处理方法。
2. 表面清洗:使用碱性清洗剂或有机溶剂去除表面油污、氧化皮和其他杂质,保证表面干净。
3. 除锈处理:对于钢铁等金属材料,需要进行除锈处理,可采用酸洗或机械打磨等方法。
4. 防腐处理:对于铝合金等易氧化的材料,需要进行防腐处理,可采用酸洗或阳极氧化等方法。
二、涂装工艺1. 电泳槽液配制:根据所选涂料的要求和工艺参数配制电泳槽液,并保持其稳定性和均匀性。
2. 预热:将待涂件放入预热炉中加热至适当温度(一般为50-80℃),以提高电泳效果和降低残余应力。
3. 电泳:将预热好的待涂件通过滑轮送入电泳槽中,使其浸入电泳槽液中,施加电压使涂料在待涂件表面形成一层均匀的薄膜。
4. 洗涤:将电泳后的待涂件在清水中进行洗涤,去除多余的电泳槽液和杂质。
5. 固化:将洗净后的待涂件放入烘箱中进行固化处理,使其达到所需硬度和耐磨性。
三、工艺参数1. 电泳时间:根据待涂件的大小、形状和材料种类等因素确定电泳时间,一般为1-5分钟。
2. 电压:根据所选涂料的要求和工艺参数确定施加的电压大小,一般为100-400伏。
3. 槽温:根据所选涂料的要求和工艺参数确定电泳槽内的温度,一般为25-35℃。
4. 液位:保持槽内液位稳定,并确保待涂件完全浸入槽内。
5. 搅拌速度:根据所选涂料的要求和工艺参数确定搅拌速度大小,以保证槽内液体均匀混合。
四、质量控制1. 涂层厚度:通过测量涂层厚度来检查电泳效果,一般要求涂层厚度为10-25微米。
2. 色泽和光泽:观察涂层的色泽和光泽,确保其符合要求。
3. 耐腐蚀性:通过盐雾试验等方法检测涂层的耐腐蚀性能,确保其符合要求。
4. 粘附力:通过拉伸测试等方法检测涂层的粘附力,确保其符合要求。
五、安全防护1. 电泳槽液具有刺激性和腐蚀性,操作时需佩戴防护手套、眼镜等防护用品。
铝及铝合金阳极氧化与电泳涂装工艺

2. 碱蚀(碱洗)
槽号: 槽号:
配置及工艺参数: 配置及工艺参数:
NaOH:30-60g/l : 水质: 水质:生水 温度:40-60 ℃ 温度: 时间: 时间:1-25min
槽液维护与控制: 槽液维护与控制: 液位化验: 次 班 液位化验:1次/班 槽液控制: 槽液控制:35-45g/l Al3+ : ≤ 80g/l
6#/8#
槽体参数 45000L×2
安全操作要点
1.碱洗出槽应先把料挂倾斜,并迅速转到清洗槽清洗,清洗及空留时间不应过长。 碱洗出槽应先把料挂倾斜,并迅速转到清洗槽清洗,清洗及空留时间不应过长。 碱洗出槽应先把料挂倾斜 2.加碱时,要戴面罩和橡胶手套。万一被碱灼伤,应迅速用水冲洗,然后就医。 加碱时,要戴面罩和橡胶手套。万一被碱灼伤,应迅速用水冲洗,然后就医 加碱时 3.两个碱槽槽边都安装有抽碱雾罩,每15天必须做一次清理工作。 两个碱槽槽边都安装有抽碱雾罩, 天必须做一次清理工作 两个碱槽槽边都安装有抽碱雾罩 天必须做一次清理工作。
35#、36# 、 槽体参数
槽液维护与控制:
PH: 大于4 大于 导电率: 导电率 ≤100 µs /cm 温度: 温度: 60 ± 5℃ ℃
温度: 温度: 60 ± 10℃ ℃ 时间: 时间:3-5 min
35000L×2
操作要点
1.水质应控制在 在5-7最佳,导电率小于 水质应控制在PH在 最佳 导电率小于80µs /cm。 最佳, 水质应控制在 。 2.汤洗时间必须保障在 分钟以上,不能超过 分钟。 汤洗时间必须保障在3分钟以上 不能超过10分钟 分钟。 汤洗时间必须保障在 分钟以上, 3.35#与36#循环更替使用。 与 循环更替使用 循环更替使用。
铝件电泳前处理工艺

铝件电泳前处理工艺铝件电泳前处理工艺是指在进行铝件电泳涂装之前,对铝件进行一系列的表面处理工艺,以确保铝件表面的质量和涂装效果。
铝件电泳前处理工艺主要包括清洗、酸洗、除氧化膜和预处理等步骤。
清洗是铝件电泳前处理的第一步,其主要目的是去除铝件表面的油污、灰尘和杂质等。
常用的清洗方法有机械清洗、化学清洗和超声波清洗等。
机械清洗是通过物理力量将铝件表面的污垢清除,化学清洗是利用化学药剂溶解和分解污垢,超声波清洗则是利用超声波的振动力将污垢从铝件表面剥离。
清洗后的铝件表面应干净无污染,并且无油污残留。
酸洗是为了去除铝件表面的氧化层和铝合金表面的氧化物,并恢复铝件表面的金属光泽。
常用的酸洗方法有浸酸洗和刷酸洗两种。
浸酸洗是将铝件浸入酸液中进行反应,刷酸洗则是利用刷子将酸液刷在铝件表面。
酸洗后的铝件表面应平整光滑,并且无氧化层和氧化物残留。
除氧化膜是为了去除铝件表面的氧化膜,并避免在电泳过程中氧化膜的再生。
常用的除氧化膜方法有酸洗除氧和电解除氧两种。
酸洗除氧是将铝件浸入去氧化酸液中进行反应,电解除氧则是通过电解的方式将氧化膜从铝件表面溶解。
除氧化膜后的铝件表面应洁净无氧化膜,并且无残留的酸液。
预处理是为了增加铝件表面的粗糙度,提高铝件与涂料的附着力。
常用的预处理方法有机械预处理和化学预处理两种。
机械预处理是通过打磨、抛光等方式增加铝件表面的粗糙度,化学预处理则是利用化学药剂在铝件表面形成一层微细的转化膜。
预处理后的铝件表面应均匀粗糙,并且无残留的预处理剂。
铝件电泳前处理工艺是确保铝件表面质量和涂装效果的重要环节。
通过清洗、酸洗、除氧化膜和预处理等步骤,可以去除铝件表面的污垢和氧化物,增加铝件表面的粗糙度,从而确保铝件电泳涂装的质量和附着力。
铝件电泳前处理工艺的合理应用,可以提高铝件的质量和使用寿命,广泛应用于汽车、建筑、电子等领域。
【铝合金工艺】电泳
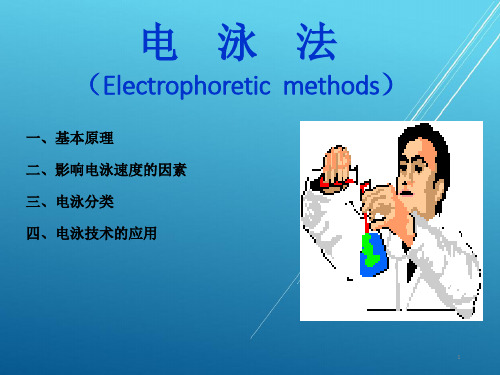
影响电泳速度的因素
3.溶液的pH值:决定了带电粒子解离的程度,也决 定粒子 所带净电荷的多少,pH值离等电点越远,则料子所带 净电荷就越多,则电泳速度越快 常用电泳缓冲液pH 范围在4.5-9.0。正极pH 负极 4.溶液的离子强度:所有离子产生的静电力,取决于 离子电荷的总数。 在保持足够缓冲能力前提下,离子强度要求最小。
③在一定浓度范围聚丙烯酰胺对热稳定。凝胶无色透明,易观察, 可用检测仪直接测定
④丙烯酰胺是比较纯的化合物,可以精制,减少污染
29
垂 直 电 泳 槽
30
垂
测
直
序
电
用
泳
槽
31
丙烯酰胺凝胶电泳
垂 直 电 泳 槽
32
丙 烯 酰 胺 凝 胶 电 泳
33
载体两性电解质PH梯度等电聚焦
等电点聚焦就是在电泳槽中放入载体两性电解质,当通以 直流电时,两性电解质即形成一个由阳极到阴极逐步增加的pH 梯度,当蛋白质放进此体系时,不同的蛋白质即移动到或聚焦 于与其等电点相当的pH位置上
4。可直接测出蛋白质的等电点,其精确度可达0.01pH单位
35
等 电 聚 焦 电 泳 槽
36
四、电泳技术的应用
1.分离:如氨基酸、蛋 白质、核酸 2.分析:物质的纯度及 分子量大小
37
2
Tiselius的移动界面电泳仪
移动界面电泳方法是用一 个U形玻璃管,在U形管的下现 部分放胶体溶液,如蛋白溶液 。U形管的管臂连接到电极上, 则缓冲系统中的蛋白质界面移 动就能被观察到。将血清分离 成白蛋白与三种球蛋白,为此 于1948年荣获诺贝尔奖
3
电泳概述
电泳:在电场中,
带电颗粒向阴极或 阳极迁移,迁移的 方向取决于它们所 带电荷的种类,这 种迁移现象即谓电 泳
铝合金阳极氧化及电泳工艺介绍

铝合金阳极氧化及电泳工艺介绍1、上料工:上料之前先将导电杆弯沟处,导电梁与导电杆接触面用砂皮砂干净,注意导电杆与导电梁配合要紧密,确保充分良好的导电性,2、上料时注意工件与工件之间的间距,一般色料间距等于工件的水平宽度,间距过小,在阳极氧化和着色过程中会产生屏蔽,导致膜厚不均和颜色不一致。
3、上料时注意工件的倾斜度,不准水平上料,一般主杆比副杆要高10——15cm,第一支工件要低于液面2——3cm。
4、除油(又称脱脂):是将前到工序生产时留下的油污及灰尘去除,一般我们都采用硫酸。
也有采用脱脂剂,碱性的。
一般浓度控制在150——160g/L.常温控制。
5、除油后经过两道水洗,工艺要求;pH大于4,水溢流,常温控制。
6、碱洗:碱腐蚀在建筑用铝板和铝型材的阳极氧化中,碱腐蚀是最基本和最重要的预处理手段。
碱腐蚀得到无光缎面的细致腐蚀表面,这是高比例漫反射的结果。
铝合金中金属间化合物颗粒在碱腐蚀时的电化学特性。
不同的金属间化合物,甚至粒度不同的同一化合物也会有完全不同的电化学特性。
铝合金中由于金属间化合物第二相的存在形成表面腐蚀坑的机理有两种:第二相作为阴极(如Al3Fe)使得颗粒周围的铝基体优先溶解;第二相金属间化合物颗粒相对于铝基体是阳极(如Mg2Si)而优先溶解。
铝合金中第二相金属间化合物的存在,不论其相对于铝基体是阴极还是阳极,在碱腐蚀时表面都会形成腐蚀坑,从而产生无光的漫散射表面。
前者由于第二相周围的铝的局部溶解形成腐蚀坑;后者由于中间化合物的直接溶解而形成腐蚀坑。
目的;除去工件表面自然氧化膜,修整工件上轻微的划,碰伤及挤压痕,使工件表面平整光滑,工艺要求;温度50——60摄氏度,时间;色料,1——3分钟,白料3——5分钟,腐蚀砂面,10——15分钟(根据砂面大小来定)。
槽液浓度,根据铝离子浓度调整游离碱浓度。
工件出碱洗槽必须在一分钟内完成。
如转移时间过长会造成工件表面起挂痕。
7、碱洗后经过两次水洗,工艺要求,水溢流,常温控制,第一水洗槽最好温度控制在30摄氏度,8、中和槽:又称(出光槽),目的;去除碱蚀后留在工件表面的黑灰,因为合金含有铁,铜等元数,碱蚀后就会产生黑灰。
铝型材氧化、电泳生产工艺操作
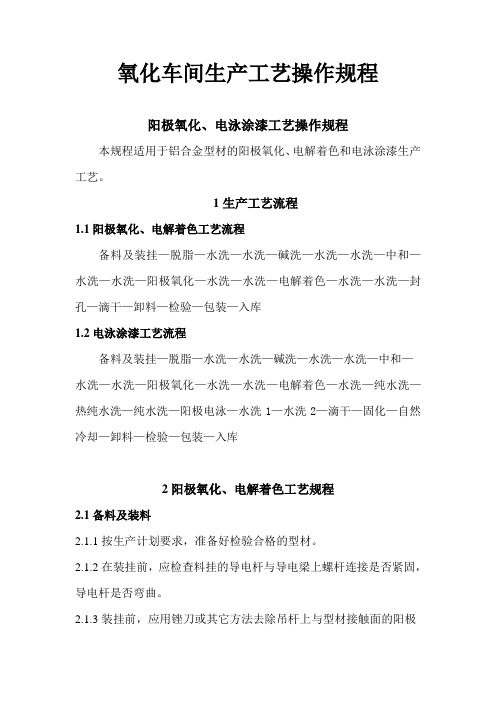
氧化车间生产工艺操作规程阳极氧化、电泳涂漆工艺操作规程本规程适用于铝合金型材的阳极氧化、电解着色和电泳涂漆生产工艺。
1生产工艺流程1.1阳极氧化、电解着色工艺流程备料及装挂—脱脂—水洗—水洗—碱洗—水洗—水洗—中和—水洗—水洗—阳极氧化—水洗—水洗—电解着色—水洗—水洗—封孔—滴干—卸料—检验—包装—入库1.2电泳涂漆工艺流程备料及装挂—脱脂—水洗—水洗—碱洗—水洗—水洗—中和—水洗—水洗—阳极氧化—水洗—水洗—电解着色—水洗—纯水洗—热纯水洗—纯水洗—阳极电泳—水洗1—水洗2—滴干—固化—自然冷却—卸料—检验—包装—入库2阳极氧化、电解着色工艺规程2.1备料及装料2.1.1按生产计划要求,准备好检验合格的型材。
2.1.2在装挂前,应检查料挂的导电杆与导电梁上螺杆连接是否紧固,导电杆是否弯曲。
2.1.3装挂前,应用锉刀或其它方法去除吊杆上与型材接触面的阳极氧化膜以及漆膜,确保良好的导电性。
2.1.4装挂时,应按照工艺卡片规定的支数挂料。
2.1.5装挂时,应尽量把相同断面或相近形状尺寸的型材装在同一挂上,型材与型材之间应保持均匀的间距(着色型材一般为30~35mm,非着色型材为20~25mm)和合适的倾角(>5℃),型材绑线位置距端头应<50mm。
2.1.6装挂时,型材重要的装饰面应朝向邻近阴极。
2.1.7型材装挂必须牢固,不得窜动。
2.1.8装挂时,应轻拿轻放,防止型材磕碰伤。
2.1.9装挂完毕后应仔细检查,型材之间不应相互接触,挂在吊杆最上面的型材在处理时不能露出液面。
2.2脱脂在酸液中使铝型材表面的油污和天然氧化膜等脏物与铝基体的结合力松弛,且趋于一致,便于碱洗时去除速度均一。
脱脂采用硫酸(工业纯H2SO4,GB/T534)溶液。
为降低成本,可以使用氧化槽排放的硫酸。
槽液成分及工艺制度如下:硫酸:150~180g/L温度:室温时间:1~3min生产合金元素含量较高的6061合金型材,或在使用废料较多的情况下,为防止铝材出现黑斑,可在硫酸中加入10~20g/L硝酸。
铝型材氧化、电泳生产车间工艺操作规程[1]
![铝型材氧化、电泳生产车间工艺操作规程[1]](https://img.taocdn.com/s3/m/cd774adad05abe23482fb4daa58da0116c171fa8.png)
氧化车间生产工艺操作规程阳极氧化、电泳涂漆工艺操作规程本规程适用于铝合金型材的阳极氧化、电解着色和电泳涂漆生产工艺。
1生产工艺流程1。
1阳极氧化、电解着色工艺流程备料及装挂—脱脂—水洗-水洗—碱洗—水洗—水洗—中和-水洗—水洗—阳极氧化-水洗—水洗—电解着色-水洗-水洗—封孔—滴干—卸料—检验—包装—入库1.2电泳涂漆工艺流程备料及装挂—脱脂—水洗—水洗—碱洗-水洗-水洗—中和—水洗—水洗—阳极氧化-水洗-水洗-电解着色-水洗-纯水洗—热纯水洗—纯水洗—阳极电泳—水洗1—水洗2-滴干—固化—自然冷却—卸料—检验-包装—入库2阳极氧化、电解着色工艺规程2.1备料及装料2.1.1按生产计划要求,准备好检验合格的型材。
2。
1。
2在装挂前,应检查料挂的导电杆与导电梁上螺杆连接是否紧固,导电杆是否弯曲.2.1.3装挂前,应用锉刀或其它方法去除吊杆上与型材接触面的阳极氧化膜以及漆膜,确保良好的导电性。
2.1。
4装挂时,应按照工艺卡片规定的支数挂料。
2。
1.5装挂时,应尽量把相同断面或相近形状尺寸的型材装在同一挂上,型材与型材之间应保持均匀的间距(着色型材一般为30~35mm,非着色型材为20~25mm)和合适的倾角(>5℃),型材绑线位置距端头应<50mm。
2.1.6装挂时,型材重要的装饰面应朝向邻近阴极。
2.1。
7型材装挂必须牢固,不得窜动。
2。
1。
8装挂时,应轻拿轻放,防止型材磕碰伤。
2.1.9装挂完毕后应仔细检查,型材之间不应相互接触,挂在吊杆最上面的型材在处理时不能露出液面。
2。
2脱脂在酸液中使铝型材表面的油污和天然氧化膜等脏物与铝基体的结合力松弛,且趋于一致,便于碱洗时去除速度均一.脱脂采用硫酸(工业纯H2SO4,GB/T534)溶液。
为降低成本,可以使用氧化槽排放的硫酸.槽液成分及工艺制度如下:硫酸:150~180g/L温度:室温时间:1~3min生产合金元素含量较高的6061合金型材,或在使用废料较多的情况下,为防止铝材出现黑斑,可在硫酸中加入10~20g/L硝酸.操作时,将型材从装料台吊起放置到脱脂槽内,处理时间到后, 将其吊出滴干,然后放入水洗槽中进行两次水洗.对于砂面型材,水洗后进入酸蚀槽进行磨砂处理.非砂面型材直接进入碱洗槽。
铝型材氧化、电泳生产车间工艺操作规程[1]
![铝型材氧化、电泳生产车间工艺操作规程[1]](https://img.taocdn.com/s3/m/4ae85f170975f46526d3e17c.png)
氧化车间生产工艺操作规程阳极氧化、电泳涂漆工艺操作规程本规程适用于铝合金型材的阳极氧化、电解着色和电泳涂漆生产工艺。
1生产工艺流程1。
1阳极氧化、电解着色工艺流程备料及装挂—脱脂-水洗—水洗—碱洗—水洗—水洗—中和—水洗—水洗-阳极氧化-水洗—水洗—电解着色—水洗—水洗—封孔—滴干—卸料—检验—包装—入库1。
2电泳涂漆工艺流程备料及装挂—脱脂—水洗—水洗—碱洗—水洗—水洗—中和—水洗—水洗—阳极氧化-水洗-水洗-电解着色—水洗—纯水洗—热纯水洗-纯水洗-阳极电泳—水洗1—水洗2-滴干-固化—自然冷却—卸料—检验—包装—入库2阳极氧化、电解着色工艺规程2。
1备料及装料2。
1。
1按生产计划要求,准备好检验合格的型材.2.1。
2在装挂前,应检查料挂的导电杆与导电梁上螺杆连接是否紧固,导电杆是否弯曲。
2.1.3装挂前,应用锉刀或其它方法去除吊杆上与型材接触面的阳极氧化膜以及漆膜,确保良好的导电性.2。
1.4装挂时,应按照工艺卡片规定的支数挂料。
2.1.5装挂时,应尽量把相同断面或相近形状尺寸的型材装在同一挂上,型材与型材之间应保持均匀的间距(着色型材一般为30~35mm,非着色型材为20~25mm)和合适的倾角(>5℃),型材绑线位置距端头应<50mm。
2.1。
6装挂时,型材重要的装饰面应朝向邻近阴极。
2.1。
7型材装挂必须牢固,不得窜动.2。
1.8装挂时,应轻拿轻放,防止型材磕碰伤。
2.1。
9装挂完毕后应仔细检查,型材之间不应相互接触,挂在吊杆最上面的型材在处理时不能露出液面.2。
2脱脂在酸液中使铝型材表面的油污和天然氧化膜等脏物与铝基体的结合力松弛,且趋于一致,便于碱洗时去除速度均一.脱脂采用硫酸(工业纯H2SO4,GB/T534)溶液。
为降低成本,可以使用氧化槽排放的硫酸。
槽液成分及工艺制度如下:硫酸:150~180g/L温度:室温时间:1~3min生产合金元素含量较高的6061合金型材,或在使用废料较多的情况下,为防止铝材出现黑斑,可在硫酸中加入10~20g/L硝酸。
- 1、下载文档前请自行甄别文档内容的完整性,平台不提供额外的编辑、内容补充、找答案等附加服务。
- 2、"仅部分预览"的文档,不可在线预览部分如存在完整性等问题,可反馈申请退款(可完整预览的文档不适用该条件!)。
- 3、如文档侵犯您的权益,请联系客服反馈,我们会尽快为您处理(人工客服工作时间:9:00-18:30)。
电泳的工艺流程铝合金电泳
电泳的工艺流程铝合金电泳
首先:电泳涂装(electro-coating)是利用外加电场使悬浮于电泳液中的颜料和树脂等微粒定向迁移并沉积于电极之一的基底表面的涂装方法。
电泳涂装的原理发明于是20世纪30年代末,但开发这一技术并获得工业应用是在1963年以后,电泳涂装是近30年来发展起来的一种特殊涂膜形成方法,是对水性涂料最具有实际意义的施工工艺。
具有水溶性、无毒、易于自动化控制等特点,迅速在汽车、建材、五金、家电等行业得到广泛的应用。
电泳涂装是把工件和对应的电极放入水溶性涂料中,接上电源后,依靠电场所产生的物理化学作用,使涂料中的树脂、颜填料在以被涂物为电极的表面上均匀析出沉积形成不溶于水的漆膜的一种涂装方法。
电泳涂装是一个极为复杂的电化学反应过程,其中至少包括电泳、电沉积、电渗、电解四个过程。
电泳涂装按沉积性能可分为阳极电泳(工件是阳极,涂料是阴离子型)和阴极电泳(工件是阴极,涂料是阳离子型);按电源可分为直流电泳和交流电泳;按工艺方法又有定电压和定电流法。
目前在工业上较为广泛采用的是直流电源定电压法的阳极电泳。
1-经表面处理后的工件;2-电源;3-工件;4-喷水冲洗;5-槽液过滤;6-沉积槽;7-循环泵
电泳涂装与其他涂装方法相比较,具有下述特点:
(1)采用水溶性涂料,以水为溶解介质,节省了大量有机溶剂,大大降低了大气污染和环境危害,安全卫生,同时避免了火灾的隐患;
(2)涂装效率高,涂料损失小,涂料的利用率可达90%,95%;
(3)涂膜厚度均匀,附着力强,涂装质量好,工件各个部位如内层、凹陷、焊缝等处都能获得均匀、平滑的漆膜,解决了其他涂装方法对复杂形状工件的涂装难题;
(4)生产效率高,施工可实现自动化连续生产,大大提高劳动效率;
(5)设备复杂,投资费用高,耗电量大,其烘干固化要求的温度较高,涂料、涂装的管理复杂,施工条件严格,并需进行废水处理;
(6)只能采用水溶性涂料,在涂装过程中不能改变颜色,涂料贮存过久稳定性不易控制。
一、电泳涂装的设备
电泳涂装的设备是由电泳槽、搅拌装置、涂料过滤装置、温度调节装置、涂料管理装置、直流电源装置、电泳涂装后的水洗装置、超滤装置、烘烤装置、备用罐等组成。
电泳槽槽体的大小及形状需根据工件大小、形状和施工工艺确定。
在保证一定的极间距离条件下,应尽可能设计小些。
槽内装有过滤装置及温度调节装置,以保证漆液一定的温度和除去循环漆液中的杂质和气泡。
搅拌装置可使工作漆液保持均匀一致,多采用循环泵,漆液的循环一般每小时4,6次,当循环泵开动时,槽内漆液液面应均匀翻动。
涂料管理装置的作用在于补充调整涂料成分,控制槽液的PH 值,用隔膜电极除去中和剂和用超滤装置排除低分子量成分等。
电泳电源的选择,一般采用直流电源。
整流设备可采用硅整流器或可控硅。
电流的大小与涂料的性质、温度、工作面积、通电方式等有关,一般为30,50A/m2。
水洗装置用于电泳涂装前后工件的冲洗,一般用去离子水,但需加压设备,常用的是一种带螺旋体的淋洗喷嘴。
烘烤装置用来促进电泳涂料的干燥成膜,可采用电阻炉、感应电热炉和红外线烘烤设备。
烘房设计要有预热、加热和后热三段,应根据涂料的品种和工件的情况制订。
二、影响电泳涂装的主要工艺参数
1、电压
电泳涂装采用的是定电压法,设备相对简单,易于控制。
电压对漆膜的影响很大;电压越高,电泳漆膜越厚,对于难以涂装的部位可相应提高涂装能力,缩短施工时间。
但电压过高,会引起漆膜表面粗糙,烘干后易产生“橘皮”现象。
电压过低,电解反应慢,漆膜薄而均匀,泳透力差。
电压的选择由涂料种类和施工要求等确定。
一般情况下,电压与涂料的固体分及漆温成反比,与两极间距成正比。
钢铁表面为40,70V,铝和铝合金表面可采用60,100V,镀锌件采用70,85V。
、电泳时间
漆膜厚度随着电泳时间的延长而增加,但当漆膜达到一定厚度时,继续延长时间,也不能增加厚度,反而会加剧副反应;反之,电泳时间过短,涂层过薄。
电泳时间应根据所用的电压,在保证涂层质量的条件下,越短越好。
一般工件电泳时间为1至3分钟,大型工件为3至4分钟。
如果被涂物件表面几何形状复杂,可适当提高电压和延长时间。
3、涂料温度
涂料温度高,成膜速率快,但漆膜外观粗糙,还会引起涂料变质;温度低,电沉积量少,成膜慢,涂膜薄而致密。
施工过程中,由于电沉积时部分电能转化成热能,循环系统内机械摩擦产生热量,将导致涂料温度上升。
一般漆液温度控制在某些方面15,30?。
4、涂料的固体分和颜基比
市售的电泳涂料的固体分一般为50%左右,施工时,需用蒸馏水将涂料固体分控制在10%,15%。
固体含量太低,漆膜的遮盖力不好,颜料易沉淀,涂料的稳定性差。
固体分过高,粘度提高,会造成漆膜粗糙疏松,附着力差。
一般颜基比为1比
2左右,高光泽电泳涂料的颜基比可控制在1比4。
由于实际操作中,涂料的颜料量会逐渐下降,必须随时添加颜料分高的涂料来调节。
5、涂料的PH值
电泳涂料的PH值直接影响槽液的稳定性。
PH值过高,新沉积的涂膜会再溶解,漆膜变薄,电泳后冲洗会脱膜。
PH值过低,工件表面光泽不一致,漆液的稳定性不好,已溶解的树脂会析出,漆膜表面粗糙,附着力降低。
一般要求施工过程中,PH值控制在7.5,8.5之间。
在施工工程中,由于连续进行电泳,阳离子的铵化合物在涂料中积蓄,导致PH值的上升。
可采用补加低PH值的原液,更换阴极罩蒸馏水,用离子交换树脂除去铵离子,采用阳极罩等方法降低PH值。
若PH值过低时,可加入乙醇铵来调节。
6、涂料电阻
被涂物件从前一道工序带入电泳槽的杂质离子等引起涂料电阻值的下降,从而导致漆膜出现粗糙不均和针孔等弊病。
在涂装施工中,需对涂料进行净化处理。
为了得到高质量涂膜,可采用阴极罩设备,以除去铵及钙、镁等杂质正离子。
7、工件与阴极间距离
距离近,沉积效率高。
但距离过近,会使漆膜太厚而产生流挂、橘皮等弊病。
一般距离不低于20cm。
对大型而形状复杂的工件,当出现外部已沉积很厚涂膜,而内部涂膜仍较薄时,应在距离阴极较远的部位,增加辅助阴极。
三、电泳涂装的方法及技巧
(1)一般金属表面的电泳涂装,其工艺流程为:
预清理?上线?除油?水洗?除锈?水洗?中和?水洗?磷化?水洗?钝化?电泳涂装?槽上清洗?超滤水洗?烘干?下线。
(2)被涂物的底材及前处理对电泳涂膜有极大影响。
铸件一般采用喷砂或喷丸进行除锈,用棉纱清除工件表面的浮尘,用80#,120#砂纸清除表面残留的钢丸等
杂物。
钢铁表面采用除油和除锈处理,对表面要求过高时,进行磷化和钝化表面处理。
黑色金属工件在阳极电泳前必须进行磷化处理,否则漆膜的耐腐蚀性能较差。
磷化处理时,一般选用锌盐磷化膜,厚度约1,2μm,要求磷化膜结晶细而均匀。
(3)在过滤系统中,一般采用一级过滤,过滤器为网袋式结构,孔径为
25,75μm。
电泳涂料通过立式泵输送到过滤器进行过滤。
从综合更换周期和漆膜质量等因素考虑,孔径50μm的过滤袋最佳,它不但能满足漆膜的质量要求,而且解决了过滤袋的堵塞问题。
(4)电泳涂装的循环系统循环量的大小,直接影响着槽液的稳定性和漆膜的质量。
加大循环量,槽液的沉淀和气泡减少;但槽液老化加快,能源消耗增加,槽液的稳定性变差。
将槽液的循环次数控制6,8次/h较为理想,不但保证漆膜质量,而且确保槽液的稳定运行
(5)随着生产时间的延长,阳极隔膜的阻抗会增加,有效的工作电压下降。
因此,生产中应根据电压的损失情况,逐步调高电源的工作电压,以补偿阳极隔膜的电压降。
(6)超滤系统控制工件带入的杂质离子的浓度,保证涂装质量。
在此系统的运行中应注意,系统一经运行后应连续运行,严禁间断运行,以防超滤膜干枯。
干枯后的树脂和颜料附着在超滤膜上,无法彻底清洗,将严重影响超滤膜的透水率和使用寿命。
超滤膜的出水率随运行时间而呈下降趋势,连续工作30,40天应清洗一次,以保证超滤浸洗和冲洗所需的超滤水。
(7)电泳涂装法适用于大量流水线的生产工艺。
电泳槽液的更新周期应在3个月以内。
以一个年产30万份钢圈的电泳生产线为例,对槽液的科学管理极为重要,对槽液的各种参数定期进行检测,并根据检测结果对槽液进行调整和更换。
一般按如下频率测量槽液的参数:
电泳液、超滤液及超滤清洗液、阴(阳)极液、循环洗液、去离子清洗液的PH 值、固体含量和电导率每天一次;颜基比、有机溶剂含量、试验室小槽试验每周2次。
(8)对漆膜质量的管理,应经常检查涂膜的均一性和膜厚,外观不应有针孔、流挂、橘皮、皱纹等现象,定期检查涂膜的附着力、耐腐蚀性能等物理化学指标。
检验周期按生产厂家的检验标准,一般每个批次都需检测。