挤压铸造工艺原理特点分类
压力铸造分类

压力铸造分类压力铸造是一种常见的铸造工艺,根据不同的压力源,可以将其分为普通压铸和低压铸造。
下面将对两种压力铸造进行详细介绍。
普通压铸是一种铸造工艺,它利用高压将熔化的金属通过模具中的喷口注入模腔中,然后在模具中冷却凝固。
这种工艺适用于生产中小型铸件,如汽车发动机罩、传动箱等。
普通压铸的优点是生产效率高,能够快速生产大量的铸件,且铸件质量高,表面光滑,尺寸精度高,线条流畅,不易变形。
缺点是模具成本高,需要定期维护和更换。
低压铸造是一种新兴的铸造工艺,它的原理是将金属熔化后注入模具中,在注入金属的同时,通过低压将金属推入模腔中,然后在模具中冷却凝固。
这种工艺适用于生产大型铸件,如风电叶片、船舶舵轮等。
低压铸造的优点是可生产大型铸件,且铸件质量高,表面光滑,尺寸精度高,线条流畅,不易变形。
缺点是生产效率较低,成本较高。
除了普通压铸和低压铸造外,还有其他的压力铸造工艺,如高压铸造和挤压铸造。
高压铸造是一种利用高压将金属熔化后注入模具中的铸造工艺。
它适用于生产高强度、高精度的铸件,如航空发动机叶轮、火箭发动机涡轮等。
高压铸造的优点是能够生产高强度、高精度的铸件,缺点是成本高、生产效率低。
挤压铸造是一种利用挤压力将金属压入模腔中的铸造工艺,它适用于生产大尺寸、复杂形状的铸件。
挤压铸造的优点是能够生产大尺寸、复杂形状的铸件,缺点是模具成本高。
总的来说,压力铸造是一种高效、高质量的铸造工艺,适用于生产各种尺寸、形状的金属铸件。
不同的压力源对应不同的压力铸造工艺,每种工艺都有其适用范围和优缺点。
在选择铸造工艺时,需要根据铸件的尺寸、形状和材料等因素综合考虑,选择最适合的铸造工艺。
各种典型铸造技术的原理和方法
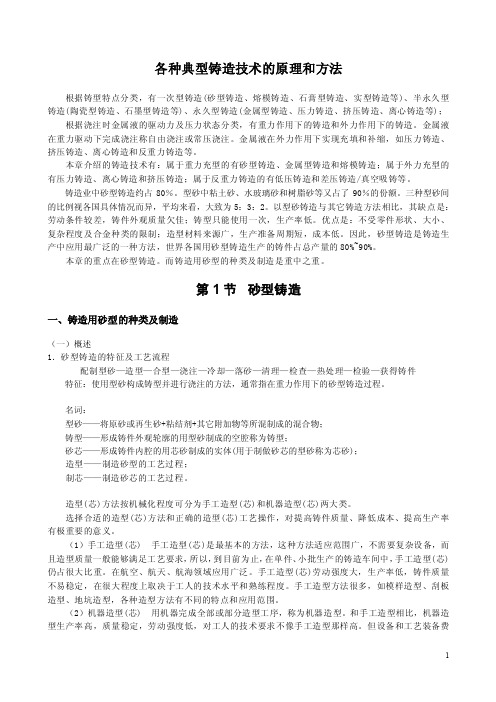
各种典型铸造技术的原理和方法根据铸型特点分类,有一次型铸造(砂型铸造、熔模铸造、石膏型铸造、实型铸造等)、半永久型铸造(陶瓷型铸造、石墨型铸造等)、永久型铸造(金属型铸造、压力铸造、挤压铸造、离心铸造等);根据浇注时金属液的驱动力及压力状态分类,有重力作用下的铸造和外力作用下的铸造。
金属液在重力驱动下完成浇注称自由浇注或常压浇注。
金属液在外力作用下实现充填和补缩,如压力铸造、挤压铸造、离心铸造和反重力铸造等。
本章介绍的铸造技术有:属于重力充型的有砂型铸造、金属型铸造和熔模铸造;属于外力充型的有压力铸造、离心铸造和挤压铸造;属于反重力铸造的有低压铸造和差压铸造/真空吸铸等。
铸造业中砂型铸造约占80%。
型砂中粘土砂、水玻璃砂和树脂砂等又占了90%的份额。
三种型砂间的比例视各国具体情况而异,平均来看,大致为5:3:2。
以型砂铸造与其它铸造方法相比,其缺点是:劳动条件较差,铸件外观质量欠佳;铸型只能使用一次,生产率低。
优点是:不受零件形状、大小、复杂程度及合金种类的限制;造型材料来源广,生产准备周期短,成本低。
因此,砂型铸造是铸造生产中应用最广泛的一种方法,世界各国用砂型铸造生产的铸件占总产量的80%~90%。
本章的重点在砂型铸造。
而铸造用砂型的种类及制造是重中之重。
第1节砂型铸造一、铸造用砂型的种类及制造(一)概述1.砂型铸造的特征及工艺流程配制型砂—造型—合型—浇注—冷却—落砂—清理—检查—热处理—检验—获得铸件特征:使用型砂构成铸型并进行浇注的方法,通常指在重力作用下的砂型铸造过程。
名词:型砂——将原砂或再生砂+粘结剂+其它附加物等所混制成的混合物;铸型——形成铸件外观轮廓的用型砂制成的空腔称为铸型;砂芯——形成铸件内腔的用芯砂制成的实体(用于制做砂芯的型砂称为芯砂);造型——制造砂型的工艺过程;制芯——制造砂芯的工艺过程。
造型(芯)方法按机械化程度可分为手工造型(芯)和机器造型(芯)两大类。
选择合适的造型(芯)方法和正确的造型(芯)工艺操作,对提高铸件质量、降低成本、提高生产率有极重要的意义。
挤压铸造工艺优势与应用简介
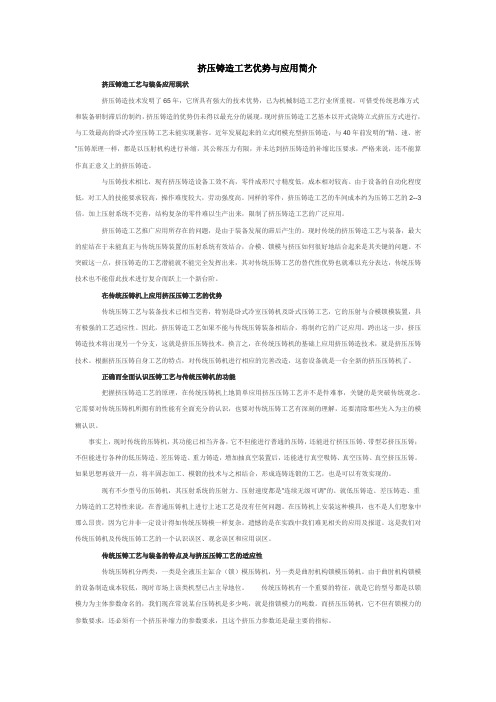
挤压铸造工艺优势与应用简介挤压铸造工艺与装备应用现状挤压铸造技术发明了65年,它所具有强大的技术优势,已为机械制造工艺行业所重视。
可惜受传统思维方式和装备研制滞后的制约,挤压铸造的优势仍未得以最充分的展现。
现时挤压铸造工艺基本以开式浇铸立式挤压方式进行,与工效最高的卧式冷室压铸工艺未能实现兼容。
近年发展起来的立式闭模充型挤压铸造,与40年前发明的"精、速、密"压铸原理一样,都是以压射机构进行补缩,其公称压力有限,并未达到挤压铸造的补缩比压要求,严格来说,还不能算作真正意义上的挤压铸造。
与压铸技术相比,现有挤压铸造设备工效不高,零件成形尺寸精度低,成本相对较高。
由于设备的自动化程度低,对工人的技能要求较高,操作难度较大,劳动强度高。
同样的零件,挤压铸造工艺的车间成本约为压铸工艺的2--3倍。
加上压射系统不完善,结构复杂的零件难以生产出来,限制了挤压铸造工艺的广泛应用。
挤压铸造工艺推广应用所存在的问题,是由于装备发展的滞后产生的。
现时传统的挤压铸造工艺与装备,最大的症结在于未能真正与传统压铸装置的压射系统有效结合,合模、锁模与挤压如何很好地结合起来是其关键的问题。
不突破这一点,挤压铸造的工艺潜能就不能完全发挥出来,其对传统压铸工艺的替代性优势也就难以充分表达,传统压铸技术也不能借此技术进行复合而跃上一个新台阶。
在传统压铸机上应用挤压压铸工艺的优势传统压铸工艺与装备技术已相当完善,特别是卧式冷室压铸机及卧式压铸工艺,它的压射与合模锁模装置,具有极强的工艺适应性。
因此,挤压铸造工艺如果不能与传统压铸装备相结合,将制约它的广泛应用。
跨出这一步,挤压铸造技术将出现另一个分支,这就是挤压压铸技术。
换言之,在传统压铸机的基础上应用挤压铸造技术,就是挤压压铸技术。
根据挤压压铸自身工艺的特点,对传统压铸机进行相应的完善改造,这套设备就是一台全新的挤压压铸机了。
正确而全面认识压铸工艺与传统压铸机的功能把握挤压铸造工艺的原理,在传统压铸机上地简单应用挤压压铸工艺并不是件难事,关键的是突破传统观念。
挤压铸造工艺原理、特点、分类
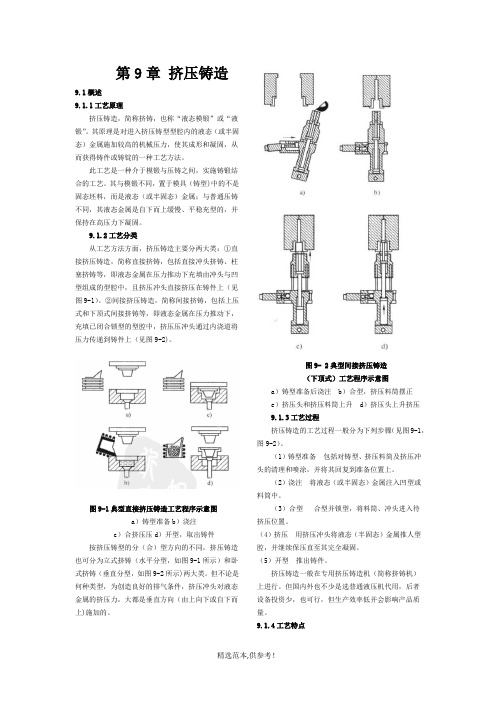
第9章挤压铸造9.1概述9.1.1工艺原理挤压铸造,简称挤铸,也称“液态模锻”或“液锻”。
其原理是对进入挤压铸型型腔内的液态(或半固态)金属施加较高的机械压力,使其成形和凝固,从而获得铸件或铸锭的一种工艺方法。
此工艺是一种介于模锻与压铸之间,实施铸锻结合的工艺。
其与模锻不同,置于模具(铸型)中的不是固态坯料,而是液态(或半固态)金属;与普通压铸不同,其液态金属是自下而上缓慢、平稳充型的,并保持在高压力下凝固。
9.1.2工艺分类从工艺方法方面,挤压铸造主要分两大类:①直接挤压铸造,简称直接挤铸,包括直接冲头挤铸、柱塞挤铸等,即液态金属在压力推动下充填由冲头与凹型组成的型腔中,且挤压冲头直接挤压在铸件上(见图9-1)。
②间接挤压铸造,简称间接挤铸,包括上压式和下顶式间接挤铸等,即液态金属在压力推动下,充填已闭合锁型的型腔中,挤压压冲头通过内浇道将压力传递到铸件上(见图9-2)。
图9-1典型直接挤压铸造工艺程序示意图a)铸型准备b)浇注c)合挤压压d)开型,取出铸件按挤压铸型的分(合)型方向的不同,挤压铸造也可分为立式挤铸(水平分型,如图9-1所示)和卧式挤铸(垂直分型,如图9-2所示)两大类。
但不论是何种类型,为创造良好的排气条件,挤压冲头对液态金属的挤压力,大都是垂直方向(由上向下或自下而上)施加的。
图9- 2典型间接挤压铸造(下顶式)工艺程序示意图a)铸型准备后浇注 b)合型,挤压料筒摆正e)挤压头和挤压料筒上升 d)挤压头上升挤压9.1.3工艺过程挤压铸造的工艺过程一般分为下列步骤(见图9-1,图9-2)。
(1)铸型准备包括对铸型、挤压料简及挤压冲头的清理和喷涂,并将其回复到准备位置上。
(2)浇注将液态(或半固态)金属注入凹型或料筒中。
(3)合型合型并锁型,将料筒、冲头进入待挤压位置。
(4)挤压用挤压冲头将液态(半固态)金属推人型腔,并继续保压直至其完全凝固。
(5)开型推出铸件。
挤压铸造一般在专用挤压铸造机(简称挤铸机)上进行。
挤压铸造文档
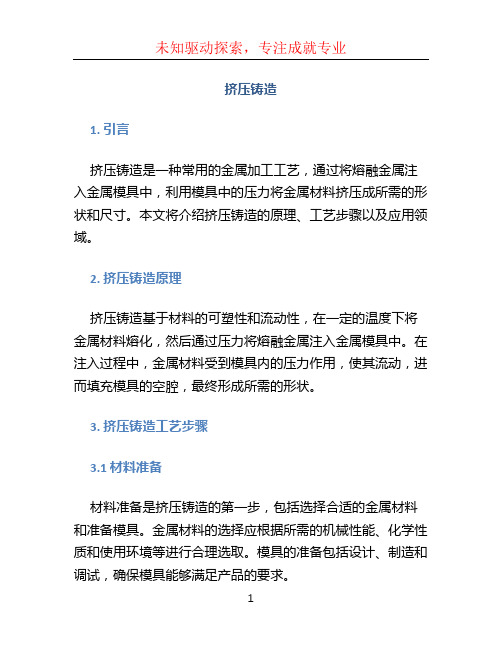
挤压铸造1. 引言挤压铸造是一种常用的金属加工工艺,通过将熔融金属注入金属模具中,利用模具中的压力将金属材料挤压成所需的形状和尺寸。
本文将介绍挤压铸造的原理、工艺步骤以及应用领域。
2. 挤压铸造原理挤压铸造基于材料的可塑性和流动性,在一定的温度下将金属材料熔化,然后通过压力将熔融金属注入金属模具中。
在注入过程中,金属材料受到模具内的压力作用,使其流动,进而填充模具的空腔,最终形成所需的形状。
3. 挤压铸造工艺步骤3.1 材料准备材料准备是挤压铸造的第一步,包括选择合适的金属材料和准备模具。
金属材料的选择应根据所需的机械性能、化学性质和使用环境等进行合理选取。
模具的准备包括设计、制造和调试,确保模具能够满足产品的要求。
3.2 加热与熔化将金属材料放入熔炉中进行加热,直到达到熔点,使其变为熔融状态。
在加热过程中,需要注意控制加热温度和时间,避免金属材料的过热或烧损。
3.3 挤压铸造将熔融金属通过挤压机的压力注入预热好的金属模具中。
在注入的过程中,可以通过控制挤压机的压力和速度来控制金属材料的流动性和填充性能。
在注入后,保持一定时间以保证金属材料充分冷却和凝固。
3.4 冷却与脱模经过一定时间的冷却后,金属材料逐渐凝固,然后可以进行脱模。
脱模可以通过拆卸模具或者采用其他合适的方法进行。
3.5 后处理在脱模后,需要对挤压铸造件进行后处理,包括切割、修整、清洁和检测等步骤。
通过后处理可以使挤压铸造件达到所需的尺寸、表面光洁度和质量要求。
4. 挤压铸造的应用领域挤压铸造广泛应用于各个行业,特别是在汽车、航空航天、电子和家电等领域。
以下是挤压铸造的一些常见应用: - 汽车行业:引擎零部件、车身结构件、车轮等。
- 航空航天行业:飞机结构件、发动机零部件等。
- 电子行业:散热器、电子外壳等。
- 家电行业:厨具、灯具等。
5. 结论挤压铸造是一种重要的金属加工工艺,具有高效、精密、经济的特点。
通过合理的工艺控制和材料选择,可以获得高质量的挤压铸造件。
挤压铸造
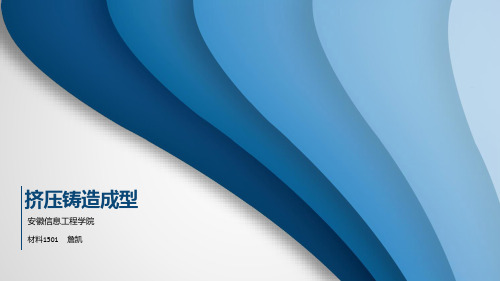
挤压铸造成型
3.在挤压铸造工艺中应用人工神经网络 挤压铸造工艺参数的确定主要靠经验,而且这些参数很难确定,人 工神经网络是一个比较新的学科,在非线性系统、错误诊断、预测、 自适应控制等方面已取得了很大成功。但我国才刚刚起步,应加强 对人工神经网络预测挤压铸造工艺参数的研究。
挤压铸造成型
应用实例:
挤压铸造成型
7.铸型涂料 为了防止铸件黏焊铸型,使铸件能顺利地从型腔中取出,以降低铸件表
面粗糙度,提高铸型的寿命,减缓金属液在加压前的结壳速度,以利于金 属液在压力下充型,在挤压铸型的表面一般都必须喷涂涂料。在挤压铸造 中不能采用涂料层来控制铸件的凝固,因为施加在金属液上的高压将使涂 料层剥落,引起铸件产生夹杂缺陷,为此,采用50μm左右的薄层涂料。。
挤压铸造成型
适用范围:
1、在材料种类方面适用性较广,可用于生产各种类型的合金,如铝合 金、锌合金、铜合金、灰铸铁、球墨铸铁、碳钢、不锈钢等。
2、对于一些复杂且性能上有一定要求的零件,采用挤压铸造合适。 因为挤压铸造既能容易成形,又能保证产品性能的要求。
3、在工件壁厚方面,一般来讲不能太薄,否则将给成形带来困难。
挤压铸造成型
1.工艺原理及特点 (1)工艺原理 将一定量的液体金属(或半固态金属)浇入金属
型腔内,通过冲头以高压(50〜100MPa)作用于液体金属上, 使之充型、成形和结晶凝固,并产生一定塑性形变,从而获得优 质铸件。
(a)熔化
(b)充型
(c)挤压
(d)顶出铸件
挤压铸造成型
(2)工艺特点 适用的材料范围较宽,不仅是普通铸造合金,也适用于高性能的变形合金,
挤压铸造成型
安徽信息工程学院 材料1501 詹凯
目录
挤压铸造工艺简介
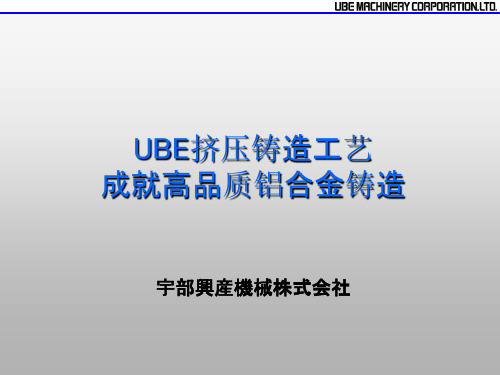
应力 [MPa]
200
180
160
σu=143MPa
140
120
100
80
σu=67MPa
60
普通压铸
40
挤压铸造
20
0
104
105
106
107
108
重复次数(Cycle) [次]
3.挤压铸造工艺的应用实例
3.挤压铸造工艺的应用实例
ABS valve body
压射单元的
YY
小型化
・压射行程
350T
800T
・油缸直径
X 3,250mm 4,100mm
XX
・熔杯直径
Y 2,600mm 3,400mm
・熔杯回倾角度
Z 2,000mm 3,700mm
1.挤压铸造工艺的概要
UBE压铸机的开发历史
昭和 35年
1960年
45年 1970年
55年 1980年
平成 2年 1990年
650
AC4CH挤压铸造 AZ91挤压铸造 600
AZ91普通铸造 550
AC4CH普通铸造
AC4CH熔点: 615℃ AZ91熔点: 595℃
热电偶
0
10
20
30
40
注汤后的时间经过 (sec)
熔杯内温 度测定
2.挤压铸造件的特征
2.挤压铸造品德特征
换挡片内部品质比较/A390合金(ADC14相当)
・射出速度:max. 10 m/s
1.挤压铸造工艺的概要
UBE挤压铸造机的出厂数量
Europe: 38 sets
挤压铸造原理及缺陷分析

挤压铸造原理及缺陷分析挤压铸造是一种将熔融金属挤压入模具中制造零件的方法。
其原理是通过一个称为挤压器的设备,在高温下应用高压将熔融金属挤压入永久性金属模具中,形成所需形状的零件。
这种工艺是高效率、高精度和高可靠性的制造方法之一。
挤压铸造的过程是将熔化的金属通过压力挤压入设计好的金属模具中。
在挤压过程中,金属将受到高度的压缩力,以使其具有所需的形状和结构。
这种挤压过程需要高度的技巧和专业知识,以确保零件的质量可靠。
挤压铸造的优点包括高精度、高品质、高效率、低成本、短周期、较少的加工量和高重复性。
另外,挤压铸造可用于制造一些常规铸造方法无法制造的零件。
挤压铸造过程中存在的缺陷包括:1. 内部气孔:在挤压过程中,熔化的金属流动性良好,但可能会导致在制造过程中产生气泡。
这些气泡会影响零件的质量和强度,甚至可能导致零件崩溃。
2. 金属受力不均:在挤压过程中,金属受到的压力和力量可能不均匀分布,这可能导致零件的某些区域强度低下。
3. 熔化的金属会受到冷却:在挤压过程中,金属会受到自然冷却。
这可能会降低材料的可加工性,并影响零件的准确度和质量。
4. 模具磨损:在整个挤压过程中,模具接触熔化的金属多次,并经受高压挤压力作用。
这可能导致模具表面磨损、裂纹或其它缺陷,进而影响零件质量。
5. 长时间的实验和制造周期:挤压铸造通常需要花费较长的时间来制造。
这可能导致生产周期较长,并且对公司的成本和效率产生不利影响。
总之,虽然挤压铸造具有创新性、可靠性和高效性等优点,但同时也存在一些缺陷,需要在制造过程中得到控制和解决。
挤压铸造原理及缺陷分析

挤压铸造原理及缺陷分析挤压铸造技术与传统金属型重力铸造相比区别较大,对于某些铸件的生产有独特优势,然而实际生产中出现的一些铸造缺陷,成因也不同于传统铸造,本文试图从原理和生产实际出发,分析挤压铸造的原理和流程参数,及其铸造常见缺陷,利用技术上的经验和实践提出改进方法,已达到推进该项铸造技术的推广,减少损失。
挤压铸造原理及特点1.1.基本原理挤压铸造又可称为液态模锻,是将金属或合金升温至熔融态,不加处理注入到敞口模具中,立即闭合模具,让液态金属充分流动以充填模具,初步到达制件外部形状,随后施以高压,使温度下降已凝固的外部金属产生塑性变形,而内部的未凝固金属承受等静压,同步发生高压凝固,最后获得制件或毛坯的方法。
由于高压凝固和塑性变形同时存在,制件无缩孔、缩松等缺陷,组织细密,力学性能高于铸造方法,接近或相当锻造方法;无需冒口补缩和最后清理,因而液态金属或合金利用率高,工序简化,为一具有潜在应用前景的新型金属加工工艺。
1.2.挤压铸造的特点挤压铸造的工艺对铸造设备有特殊的要求,并且目前只对部分铸件有较好的效果。
首先,挤压铸造设备,需要提供低速但流量较大的液态金属填充能力,速度约为0.5~3m/s,流量可达1~5kg/s,这样熔融态金属才能平稳地将铸型内气体排出,并填充铸型,随后铸型填满的瞬间(50ms~150ms),应能将铸型内铸造比压提升到60~100MPa,这样合金便能在高压下凝固成型。
由于前述的低速大流量,且挤压铸造内浇道有冒口补缩的作用,内浇道口径较大,且位于铸件最肥厚的部位。
由于上述特点,挤压铸造适合厚壁铸件(10~50mm),但铸件尺寸不宜太大(小于200mm)。
与压铸相同,挤压铸造只可使用脱模剂,不适用保温涂料,故而金属凝固速度极快,达到300~400摄氏度/s,与金属型重力铸造冷却速度相比,达到了其3~5倍,伸长率高于其他铸造方法约2~3倍。
挤压铸造的生产工艺流程以直径190系列的铝活塞为例,介绍挤压铸造的工艺流程,挤压铸造借鉴于压力铸造和模锻工艺,其大体工艺流程为把液态金属直接浇入金属模内。
特种铸造之挤压铸造

1.凹型的结构(耐热模具钢) 整体凹型 垂直分型凹型 水平分型凹型 复合分型凹型 带芯棒凹型
S4-1 铸型垂直合型挤压铸造
2.冲头加压的工艺参数
1)压力 铸件壁厚越薄,施加压力需越大。 铸钢件压力大于有色金属件。 半固态时压力应大于液态合金。 2)浇筑后开始加压的时间:不超过15s 3)冲头的下压速度(金属液流速<0.8m/s) 过快:金属液产生涡流,卷气。 过慢:金属液过早凝固,挤压不能继续进行,不能成形。 4)保压时间 持续到铸件完全凝固时为止。 壁厚越厚,时间越长
垂直分型
水平分型
S4-2 旋转合型挤压铸造
用于生产大型薄壁件:机翼
S4-2 旋转合型挤压铸造
一 旋转合型挤压铸造的成形特点
1.充型过程平稳,不易卷气。 2.适用于生产大型薄壁件。 断面由大变小—阻力较小;散热慢
3.利于排气,排渣,避免夹渣、 气孔的缺陷。 4.利于补缩,获得致密铸件。
S4-2 旋转合型挤压铸造
第四章 挤 压 铸 造
定义:是指在两个半型分开的情况下,浇注金属液而后两个半型 合拢,将金属液挤压充填整个型腔,使之凝固成形的铸造方法, 又称液态金属冲压。(区别于压力铸造) 工艺流程是:喷涂料、浇合金、合模、加压、保压、泄压,分模、 毛坯脱模、复位。
与压力铸造的区别:施压部位同时作为型腔。
S4-1 铸型垂直合型挤压铸造
合型后不封闭的优缺点: 优点:
1)铸件内部气孔、缩松等缺陷少,组织致密,晶粒细小。 2)铸件尺寸精度高。
3)出现裂纹的倾向小。
4)应用合金种类范围广。 5)无浇冒口系统,金属液损失少,出品率高。
6)生产率高,易实现机械化。
缺点:
液压机成本高,不宜铸造复杂件
《挤压铸造制备铜-铝双金属构件关键技术及组织性能研究》范文

《挤压铸造制备铜-铝双金属构件关键技术及组织性能研究》篇一挤压铸造制备铜-铝双金属构件关键技术及组织性能研究一、引言随着现代工业的快速发展,对具有优良性能和特定结构的多金属复合材料的需求日益增长。
铜/铝双金属构件作为一种典型的复合材料,因其兼具铜的高导电性和铝的低密度、高导热性等优点,在电子、汽车、航空航天等领域具有广泛的应用前景。
挤压铸造作为一种重要的制备工艺,能够有效地将不同金属结合在一起,成为制备铜/铝双金属构件的主要方法之一。
本文将针对挤压铸造制备铜/铝双金属构件的关键技术进行深入的研究,并对其组织性能进行探讨。
二、挤压铸造制备铜/铝双金属构件关键技术(一)工艺原理挤压铸造是一种通过模具对金属液施加压力,使其在高压下填充并固化成型的工艺。
在制备铜/铝双金属构件时,通过将熔融的铜和铝液分别填充到模具中,再通过施加压力使两种金属紧密结合。
(二)关键技术点1. 合金设计:根据实际需求,设计合理的合金成分比例,以获得最佳的物理性能和机械性能。
2. 模具设计:模具的设计对于产品的成型和质量具有决定性影响。
需要考虑到金属的流动性、热传导性以及冷却速度等因素。
3. 工艺参数:包括温度、压力、时间等参数的合理设置,对于保证产品的质量至关重要。
(三)技术实现在实际操作中,需要严格控制合金的熔炼过程,确保熔融金属的纯净度和温度;同时,模具的预热和填充速度也需要精确控制,以保证金属液的填充质量和成型效果。
此外,还需要对产品进行后处理,如热处理、表面处理等,以提高产品的性能和稳定性。
三、组织性能研究(一)组织结构铜/铝双金属构件的组织结构对其性能具有重要影响。
通过合理的合金设计和工艺参数设置,可以获得均匀、致密的微观组织结构。
在铜和铝的界面处,通过合理的工艺控制,可以实现良好的冶金结合,提高产品的力学性能和耐腐蚀性。
(二)性能分析1. 力学性能:通过对产品的硬度、抗拉强度、延伸率等力学性能进行测试和分析,评估产品的性能表现。
挤压铸造工艺原理、特点、分类

第9章挤压铸造概述挤压铸造,简称挤铸,也称“液态模锻”或“液锻”。
其原理是对进入挤压铸型型腔内的液态(或半固态)金属施加较高的机械压力,使其成形和凝固,从而获得铸件或铸锭的一种工艺方法。
此工艺是一种介于模锻与压铸之间,实施铸锻结合的工艺。
其与模锻不同,置于模具(铸型)中的不是固态坯料,而是液态(或半固态)金属;与普通压铸不同,其液态金属是自下而上缓慢、平稳充型的,并保持在高压力下凝固。
从工艺方法方面,挤压铸造主要分两大类:①直接挤压铸造,简称直接挤铸,包括直接冲头挤铸、柱塞挤铸等,即液态金属在压力推动下充填由冲头与凹型组成的型腔中,且挤压冲头直接挤压在铸件上(见图9-1)。
②间接挤压铸造,简称间接挤铸,包括上压式和下顶式间接挤铸等,即液态金属在压力推动下,充填已闭合锁型的型腔中,挤压压冲头通过内浇道将压力传递到铸件上(见图9-2)。
图9-1典型直接挤压铸造工艺程序示意图a)铸型准备b)浇注c)合挤压压d)开型,取出铸件按挤压铸型的分(合)型方向的不同,挤压铸造也可分为立式挤铸(水平分型,如图9-1所示)和卧式挤铸(垂直分型,如图9-2所示)两大类。
但不论是何种类型,为创造良好的排气条件,挤压冲头对液态金属的挤压力,大都是垂直方向(由上向下或自下而上)施加的。
图9- 2典型间接挤压铸造(下顶式)工艺程序示意图a)铸型准备后浇注 b)合型,挤压料筒摆正e)挤压头和挤压料筒上升 d)挤压头上升挤压挤压铸造的工艺过程一般分为下列步骤(见图9-1,图9-2)。
(1)铸型准备包括对铸型、挤压料简及挤压冲头的清理和喷涂,并将其回复到准备位置上。
(2)浇注将液态(或半固态)金属注入凹型或料筒中。
(3)合型合型并锁型,将料筒、冲头进入待挤压位置。
(4)挤压用挤压冲头将液态(半固态)金属推人型腔,并继续保压直至其完全凝固。
(5)开型推出铸件。
挤压铸造一般在专用挤压铸造机(简称挤铸机)上进行。
但国内外也不少是选普通液压机代用,后者设备投资少,也可行,但生产效率低并会影响产品质量。
挤压铸造特点及应用

挤压铸造特点及应用挤压铸造是一种能够将金属材料通过压力挤压成型的铸造工艺。
相比于传统的铸造工艺,挤压铸造具有以下特点。
首先,挤压铸造具有高效性能。
挤压铸造的工艺能够在短时间内将金属材料形成所需的结构和形状,生产效率高,并且具有高度的一致性和重复性。
其次,挤压铸造的产品具有优良的机械性能。
挤压过程中,金属材料通过挤压力产生的高压力和高温度,能够使金属内部的结晶粒细化,并且使得材料中的夹杂物和气孔等缺陷得到排除,从而提高了产品的强度、硬度和韧性等机械性能。
再次,挤压铸造可以生产大尺寸和复杂结构的产品。
挤压铸造工艺能够按照模具的形状要求将金属材料挤压成形,因此可以生产出形状复杂、壁厚薄的产品,包括管道、棒材、异型材等。
同时,挤压铸造还具有较高的尺寸精度和表面质量,能够满足高要求的工程需求。
最后,挤压铸造还具有节约能源和环保的优点。
挤压铸造过程中,在减少熔化能耗的同时,还能够最大限度地减少材料的损耗和废弃物的产生,从而降低了资源的浪费和对环境的污染。
挤压铸造在工业生产中有着广泛的应用。
首先,在汽车工业中,挤压铸造被应用于生产汽车零部件,如车身结构件、发动机零部件、悬挂系统等。
挤压铸造能够生产出质量优良、精度高的零部件,提高汽车整体性能。
其次,在航空航天工业中,挤压铸造被广泛应用于生产航空发动机叶片、飞机结构件等关键零部件。
挤压铸造能够保证零部件的高强度和高温性能,提高航空器的安全性和可靠性。
此外,挤压铸造还被应用于制造机械设备的零部件和工具。
比如挤压铸造能够生产出高强度、耐磨损的传动轴、齿轮、螺纹和各种模具等工具件,提高机械设备的使用寿命和性能。
另外,挤压铸造还被广泛应用于建筑、电子、电力等领域。
比如在建筑领域,挤压铸造可以生产出抗震、防火性能优良的铝合金门窗、墙板等建筑材料。
在电子领域,挤压铸造可以生产出散热性能好的铝合金外壳、散热片等电子器件。
在电力领域,挤压铸造可以生产出高导热、高强度的铜导线、铝合金散热器等电力设备。
简述挤压铸造的原理及应用
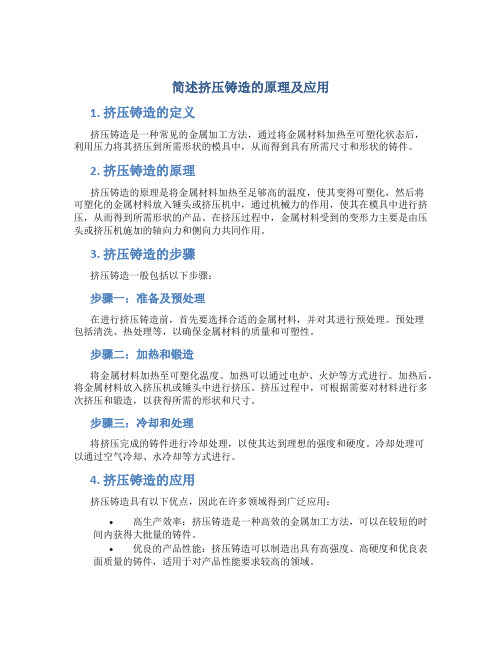
简述挤压铸造的原理及应用1. 挤压铸造的定义挤压铸造是一种常见的金属加工方法,通过将金属材料加热至可塑化状态后,利用压力将其挤压到所需形状的模具中,从而得到具有所需尺寸和形状的铸件。
2. 挤压铸造的原理挤压铸造的原理是将金属材料加热至足够高的温度,使其变得可塑化,然后将可塑化的金属材料放入锤头或挤压机中,通过机械力的作用,使其在模具中进行挤压,从而得到所需形状的产品。
在挤压过程中,金属材料受到的变形力主要是由压头或挤压机施加的轴向力和侧向力共同作用。
3. 挤压铸造的步骤挤压铸造一般包括以下步骤:步骤一:准备及预处理在进行挤压铸造前,首先要选择合适的金属材料,并对其进行预处理。
预处理包括清洗、热处理等,以确保金属材料的质量和可塑性。
步骤二:加热和锻造将金属材料加热至可塑化温度。
加热可以通过电炉、火炉等方式进行。
加热后,将金属材料放入挤压机或锤头中进行挤压。
挤压过程中,可根据需要对材料进行多次挤压和锻造,以获得所需的形状和尺寸。
步骤三:冷却和处理将挤压完成的铸件进行冷却处理,以使其达到理想的强度和硬度。
冷却处理可以通过空气冷却、水冷却等方式进行。
4. 挤压铸造的应用挤压铸造具有以下优点,因此在许多领域得到广泛应用:•高生产效率:挤压铸造是一种高效的金属加工方法,可以在较短的时间内获得大批量的铸件。
•优良的产品性能:挤压铸造可以制造出具有高强度、高硬度和优良表面质量的铸件,适用于对产品性能要求较高的领域。
•节约材料:挤压铸造可以实现材料的节约,因为挤压过程中材料的利用率较高,可以有效减少材料浪费。
•可复杂加工:挤压铸造可以制造出复杂形状的产品,适用于一些形状特殊、难以通过其他加工方式获得的产品。
挤压铸造在许多领域都有广泛的应用,包括汽车工业、航空航天工业、机械制造业等。
例如,在汽车工业中,挤压铸造可以用于制造车身结构件、发动机零部件等。
在航空航天工业中,挤压铸造可以用于制造飞机零部件、导弹零部件等。
5. 总结挤压铸造是一种常见的金属加工方法,通过将金属材料加热、挤压和锻造,可以获得具有所需形状和尺寸的铸件。
挤压铸造原理及缺陷分析

挤压铸造原理及缺陷分析集团企业公司编码:(LL3698-KKI1269-TM2483-LUI12689-ITT289-挤压铸造原理及缺陷分析挤压铸造技术与传统金属型重力铸造相比区别较大,对于某些铸件的生产有独特优势,然而实际生产中出现的一些铸造缺陷,成因也不同于传统铸造,本文试图从原理和生产实际出发,分析挤压铸造的原理和流程参数,及其铸造常见缺陷,利用技术上的经验和实践提出改进方法,已达到推进该项铸造技术的推广,减少损失。
挤压铸造原理及特点1.1.基本原理挤压铸造又可称为液态模锻,是将金属或合金升温至熔融态,不加处理注入到敞口模具中,立即闭合模具,让液态金属充分流动以充填模具,初步到达制件外部形状,随后施以高压,使温度下降已凝固的外部金属产生塑性变形,而内部的未凝固金属承受等静压,同步发生高压凝固,最后获得制件或毛坯的方法。
由于高压凝固和塑性变形同时存在,制件无缩孔、缩松等缺陷,组织细密,力学性能高于铸造方法,接近或相当锻造方法;无需冒口补缩和最后清理,因而液态金属或合金利用率高,工序简化,为一具有潜在应用前景的新型金属加工工艺。
1.2.挤压铸造的特点挤压铸造的工艺对铸造设备有特殊的要求,并且目前只对部分铸件有较好的效果。
首先,挤压铸造设备,需要提供低速但流量较大的液态金属填充能力,速度约为0.5~3m/s,流量可达1~5kg/s,这样熔融态金属才能平稳地将铸型内气体排出,并填充铸型,随后铸型填满的瞬间(50ms~150ms),应能将铸型内铸造比压提升到60~100MPa,这样合金便能在高压下凝固成型。
由于前述的低速大流量,且挤压铸造内浇道有冒口补缩的作用,内浇道口径较大,且位于铸件最肥厚的部位。
由于上述特点,挤压铸造适合厚壁铸件(10~50mm),但铸件尺寸不宜太大(小于200mm)。
与压铸相同,挤压铸造只可使用脱模剂,不适用保温涂料,故而金属凝固速度极快,达到300~400摄氏度/s,与金属型重力铸造冷却速度相比,达到了其3~5倍,伸长率高于其他铸造方法约2~3倍。
一种汽车悬置支架挤压铸造工艺技术

一种汽车悬置支架挤压铸造工艺技术汽车悬置支架挤压铸造工艺技术是一种常见于汽车制造业的生产工艺,它通过将熔化的金属材料注入模具中,然后施加压力使其充分填充模具腔体,最终得到所需形状的零件。
本文将详细介绍汽车悬置支架挤压铸造工艺技术的原理、过程和优势。
一、工艺原理汽车悬置支架挤压铸造工艺技术是一种将熔化的金属材料通过机械力作用,使其在模具腔体中充分填充并形成所需形状的工艺。
其主要原理是利用压力将金属材料推动至模具腔体内,同时通过模具的几何形状使金属材料在充填过程中发生塑性变形,最终形成所需的汽车悬置支架。
二、工艺过程汽车悬置支架挤压铸造工艺技术的过程主要可以分为以下几个步骤:1. 材料准备:选择适合的金属材料,并按照一定的比例将其熔化。
通常使用的金属材料有铝合金、镁合金等。
2. 模具设计与制造:根据悬置支架的设计要求,设计合适的模具,并制造出模具。
3. 模具预热:将制造好的模具进行预热处理,以保证在注入熔化金属材料时能够保持合适的温度,避免出现冷热断裂等问题。
4. 注入金属材料:将熔化的金属材料注入至预热好的模具中,并施加一定的压力,使其充分填充模具腔体。
5. 冷却与固化:待金属材料充填完成后,模具中的金属材料开始冷却,并逐渐固化成为所需的形状。
6. 反压与脱模:在金属材料冷却固化之后,通过一定的反压作用,将悬置支架从模具中取出。
7. 修整与加工:取出的悬置支架经过修整与加工,去除多余的材料,并进行必要的加工处理,以达到最终的要求。
三、工艺优势汽车悬置支架挤压铸造工艺技术相比于其他传统的铸造工艺具有以下优势:1. 成型精度高:挤压铸造工艺能够通过模具的设计与加工,实现对悬置支架的高精度成型,保证其尺寸和形状的准确性。
2. 生产效率高:挤压铸造工艺具有高度自动化和连续化的特点,能够实现大规模生产,并且生产效率高,有利于降低制造成本。
3. 材料利用率高:挤压铸造工艺可以有效控制金属材料的用量,并且通过模具的设计,减少废料的产生,提高材料利用率。
对挤压加工的认识
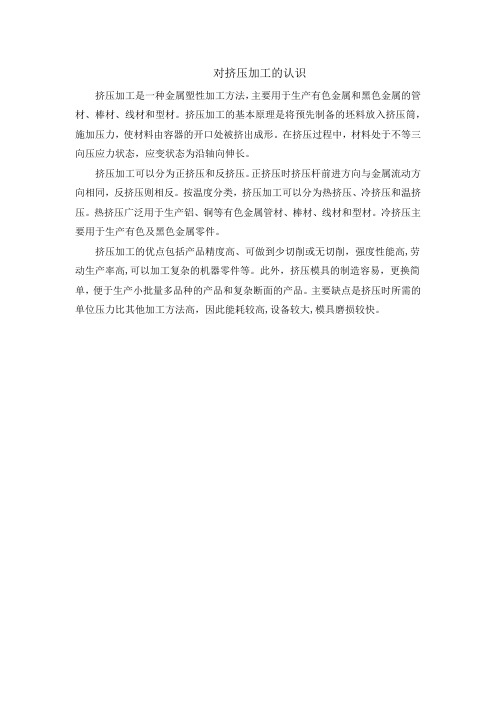
对挤压加工的认识
挤压加工是一种金属塑性加工方法,主要用于生产有色金属和黑色金属的管材、棒材、线材和型材。
挤压加工的基本原理是将预先制备的坯料放入挤压筒,施加压力,使材料由容器的开口处被挤出成形。
在挤压过程中,材料处于不等三向压应力状态,应变状态为沿轴向伸长。
挤压加工可以分为正挤压和反挤压。
正挤压时挤压杆前进方向与金属流动方向相同,反挤压则相反。
按温度分类,挤压加工可以分为热挤压、冷挤压和温挤压。
热挤压广泛用于生产铝、铜等有色金属管材、棒材、线材和型材。
冷挤压主要用于生产有色及黑色金属零件。
挤压加工的优点包括产品精度高、可做到少切削或无切削,强度性能高,劳动生产率高,可以加工复杂的机器零件等。
此外,挤压模具的制造容易,更换简单,便于生产小批量多品种的产品和复杂断面的产品。
主要缺点是挤压时所需的单位压力比其他加工方法高,因此能耗较高,设备较大,模具磨损较快。
- 1、下载文档前请自行甄别文档内容的完整性,平台不提供额外的编辑、内容补充、找答案等附加服务。
- 2、"仅部分预览"的文档,不可在线预览部分如存在完整性等问题,可反馈申请退款(可完整预览的文档不适用该条件!)。
- 3、如文档侵犯您的权益,请联系客服反馈,我们会尽快为您处理(人工客服工作时间:9:00-18:30)。
第9章挤压铸造概述
工艺原理
挤压铸造,简称挤铸,也称“液态模锻”或“液锻”。
其原理是对进入挤压铸型型腔内的液态(或半固态)金属施加较高的机械压力,使其成形和凝固,从而获得铸件或铸锭的一种工艺方法。
此工艺是一种介于模锻与压铸之间,实施铸锻结合的工艺。
其与模锻不同,置于模具(铸型)中的不是固态坯料,而是液态(或半固态)金属;与普通压铸不同,其液态金属是自下而上缓慢、平稳充型的,并保持在高压力下凝固。
工艺分类
从工艺方法方面,挤压铸造主要分两大类:①直接挤压铸造,简称直接挤铸,包括直接冲头挤铸、柱塞挤铸等,即液态金属在压力推动下充填由冲头与凹型组成的型腔中,且挤压冲头直接挤压在铸件上(见图9-1)。
②间接挤压铸造,简称间接挤铸,包括上压式和下顶式间接挤铸等,即液态金属在压力推动下,充填已闭合锁型的型腔中,挤压压冲头通过内浇道将压力传递到铸件上(见图9-2)。
图9-1典型直接挤压铸造工艺程序示意图
a)铸型准备b)浇注
c)合挤压压d)开型,取出铸件按挤压铸型的分(合)型方向的不同,挤压铸造也可分为立式挤铸(水平分型,如图9-1所示)和卧式挤铸(垂直分型,如图9-2所示)两大类。
但不论是何种类型,为创造良好的排气条件,挤压冲头对液态金属的挤压力,大都是垂直方向(由上向下或自下而上)施加的。
图9- 2典型间接挤压铸造
(下顶式)工艺程序示意图
a)铸型准备后浇注 b)合型,挤压料筒摆正
e)挤压头和挤压料筒上升 d)挤压头上升挤压
工艺过程
挤压铸造的工艺过程一般分为下列步骤(见图9-1,图9-2)。
(1)铸型准备包括对铸型、挤压料简及挤压冲头的清理和喷涂,并将其回复到准备位置上。
(2)浇注将液态(或半固态)金属注入凹型或料筒中。
(3)合型合型并锁型,将料筒、冲头进入待
挤压位置。
(4)挤压用挤压冲头将液态(半固态)金属推人型腔,并继续保压直至其完全凝固。
(5)开型推出铸件。
挤压铸造一般在专用挤压铸造机(简称挤铸机)
上进行。
但国内外也不少是选普通液压机代用,后者
设备投资少,也可行,但生产效率低并会影响产品质量。
工艺特点
产生;显微组织可细化;可进行固溶热处理;力学性
能高于其他普通铸件,对直接挤压铸造件(简称直接
挤铸件),可接近同种合金锻件水平。
2)铸件有较高的尺寸精度(铝合金和镁合金铸件
可达GBT 6414-1999的CT5),较低的表面粗糙度值(铝
铸件可达Ra=)。
3)工艺适应性较强,适用于生产多种铸造合金和
部分变形合金件。
4)工艺出品率高。
5)便于实现机械化、自动化生产。
6)此工艺一般适合生产形状不很复杂的厚壁铸件。
应用范围
本工艺已广泛用于生产各种铝合金,镁合金,锌
合金,铜合金,及其金属基复合材料的挤铸件。
国内
外应用情况见表9-1。