EC系列板材成形试验平台技术资料
板材三维曲面多点成形技术
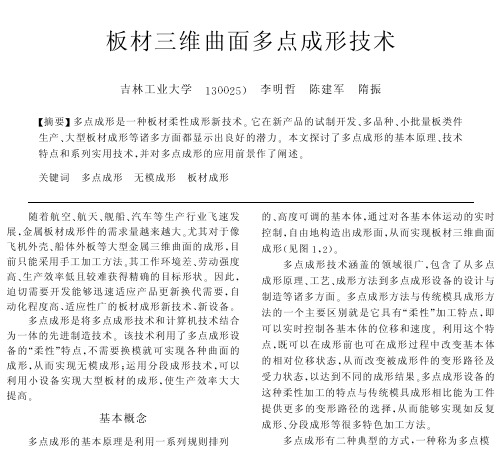
板材三维曲面多点成形技术吉林工业大学!"##$%&李明哲陈建军隋振’摘要(多点成形是一种板材柔性成形新技术)它在新产品的试制开发*多品种*小批量板类件生产*大型板材成形等诸多方面都显示出良好的潜力)本文探讨了多点成形的基本原理*技术特点和系列实用技术+并对多点成形的应用前景作了阐述)关键词多点成形无模成形板材成形随着航空*航天*舰船*汽车等生产行业飞速发展+金属板材成形件的需求量越来越大)尤其对于像飞机外壳*船体外板等大型金属三维曲面的成形+目前只能采用手工加工方法)其工作环境差*劳动强度高*生产效率低且较难获得精确的目标形状)因此+迫切需要开发能够迅速适应产品更新换代需要+自动化程度高*适应性广的板材成形新技术*新设备)多点成形是将多点成形技术和计算机技术结合为一体的先进制造技术)该技术利用了多点成形设备的,柔性-特点+不需要换模就可实现各种曲面的成形+从而实现无模成形.运用分段成形技术+可以利用小设备实现大型板材的成形+使生产效率大大提高)基本概念多点成形的基本原理是利用一系列规则排列的*高度可调的基本体+通过对各基本体运动的实时控制+自由地构造出成形面+从而实现板材三维曲面成形/见图!+$&)多点成形技术涵盖的领域很广+包含了从多点成形原理*工艺*成形方法到多点成形设备的设计与制造等诸多方面)多点成形方法与传统模具成形方法的一个主要区别就是它具有,柔性-加工特点+即可以实时控制各基本体的位移和速度)利用这个特点+既可以在成形前也可在成形过程中改变基本体的相对位移状态+从而改变被成形件的变形路径及受力状态+以达到不同的成形结果)多点成形设备的这种柔性加工的特点与传统模具成形相比能为工件提供更多的变形路径的选择+从而能够实现如反复成形*分段成形等很多特色加工方法)多点成形有二种典型的方式+一种称为多点模具成形!其特点是在板材成形前就调整好各基本体的位置!而在成形过程中基本体间没有相对运动"其实质与模具成形基本相同!只是把模具分成离散点"另一种称为多点压机成形!其特点是在成形前不对基本体进行调整!而在成形过程中调整基本体位置!此时的每对基本体都相当于一台小型压机!故称为多点压机成形法"多点压机成形更能体现多点成形的优点"图#调整后的马鞍形成形面图$多点成形样件多点成形设备则是以计算机辅助设计%辅助制造%辅助测试&’()*’(+*’(,-技术为主要手段的板材柔性加工新装备!它以可控的基本体群为核心!板类件的设计%规划%成形%测试都由计算机辅助完成!从而可以快速经济地实现三维曲面自动成形"技术特点与传统的模具成形相比!多点成形具有其自身的特点.#/实现无模成形通过对各基本体运动的控制来构造出各种不同的成形曲面!可以取代传统的整体模具!节省模具设计%制造%调试和保存等所需的人力%物力和财力!显著地缩短产品生产周期!降低生产成本!提高产品的竞争力"与模具成形法相比!不但节省加工制造模具的费用!而且节省大量的修模与调模时间"与手工成形方法相比!成形的产品精度高%质量好!并且显著了提高生产效率"$/优化变形路径通过基本体调整!实时控制变形曲面!随意改变板材的变形路径和受力状态!提高材料成形极限!实现难加工材料的塑性变形!扩大加工范围"0/实现无回弹成形可采用反复成形新技术!消除材料内部的残余应力!并实现少无回弹成形!保证工件的成形精度"1/小设备成形大型件采用分段成形新技术!可以连续%逐次成形超过设备工作台尺寸数倍的大型工件"2/易于实现自动化曲面造型%工艺计算%压力机控制%工件测试等整个过程全部采用计算机辅助!实现’()*’(+*’(,一体化生产!工作效率高!劳动强度小!极大地改善了劳动者作业环境"实用技术适应不同的需求!多点成形已经形成了系列化的实用技术.#/无回弹反复成形技术反复成形法就是利用多点成形柔性化的特点!在多点成形中成形件围绕着目标形状连续不间断地反复成形!逐渐靠近目标形状!减小工件的回弹及材料内部的残余应力!实现板材小回弹或无回弹成形"如图0所示!反复成形时!首先使材料变形到比目标形状加上应有的回弹值还大一点的程度"在此状态下!再使材料往回变形"如果此时的变形量等于回弹值!就相当于卸载过程!继续加载使材料沿其回弹方向继续变形到超过目标形状"这样!以目标形状图0反复成形过程为中心!重复上述成形过程!使板料逐渐地靠近到目标形状!最后在目标处结束成形"在多次反复成形过程中!34$35新技术新工艺6$777年第#7期万方数据可使残余应力的峰值逐渐变小!最终可实现无回弹"无残余应力的变形#$%分段成形技术多点分段成形充分利用了多点成形设备的柔性特点!把工件在不分离的情况下分成若干个成形区域分别成形!从而能够实现利用小设备对大型板材的成形&见图’(#图’分段成形技术这种成形方法可以减小设备尺寸!实现以往只能利用手工完成的大型板材的压制!从而大大降低产品的成本#同时!多点分段成形方法也可以提高板材的成形极限!但由于分段成形时!板材在每次成形时!都要受到未成形区及已成形区的影响!成形区的受力及变形情况比整体成形时要复杂得多!控制较难#应用该技术目前已成形出超过设备工作台面积)倍的样件!扭曲面总扭曲角超过’**+&见图,(#图,分段成形样件-%多道成形技术对于变形量很大的制品!选取最佳路径多道成形!使成形过程中板材各部分变形尽量均匀!以消除起皱等成形缺陷!提高板材的成形能力#’%闭环成形技术即将自动控制技术与./0!./1结合起来!对成形后的工件进行三维测量!将测量的数据反馈到./1系统!经过控制算法运算后!计算出基本体群形状的修正量!传递给控制系统再次成形!这样反复几次!可以达到精确的目标形状#结语多点成形技术可以实现无模成形!节省模具制造费用与时间2可以改善被成形件的变形条件!实现无回弹成形!并实现在小设备上成形大型件#多点成形技术特别适合于三维曲面板制品的多品种小批量生产及新产品的试制!所加工的零件尺寸越大!其优越性越突出#多点成形技术在飞机和航天器的蒙皮!轮船和舰艇的外板!车辆!大型容器和城市雕塑等三维曲面板制品加工中!有着广阔的应用前景!并将产生应有的经济效益和社会效益#参考文献3%李明哲!中村敬一%基本的4成形原理5检讨&板材多点成形法5研究第3报(%平成’年度塑性加工春季讲演会论文集!366$7,368,$$$%9:;<=>?@:!A B >C ;<@:B ?D E %!9B F D :G H C :;DI C J K :;<7L I F ?M :N F ?K L ;B I L E D B J :;<K ?D >C OI C J L -G OP B J I L E ?P >??D !Q C B J G ;L F C I 9L D ?J :L F P R J C E ?P P :;<0?E >;C F C <S !3666!T )7$))8$T *-%李明哲!蔡中义等%板材多点反复成形的残余应力分析%机械工程学报U $***!-V &3(7,*8,’’%李明哲!赵晓江等%多点分段成形中的几种成形方法%中国机械工程!366)!T &3(7T )86*W 国家T V -X .Y 9Z 主题资助项目及教育部垮世纪优秀人才基金资助项目责任编辑吕德隆9B F D :G H C :;D [C J K :;<I C J -OZ >??D 9?D L F R L J D PQ :F :;\;:]?J P :D SC I 0?E >;C F C <S @:9:;<=>?.>?;Q :L ;^B ;Z B :_>?;‘a b c d e f c 9BF D :G R C :;D [C J K :;<&9R [(:P L ;?g I F ?M :N F ?O ?I C J K :;<D ?E >;C F C <SI C J P >??D K ?D L FH L J D P %Y D >L P P >C g ;<C C OH C D ?;D :L F :;K L ;SL P H ?E D P P B E >L P O ?]?F C H K ?;D CI ;?g HJ C O B E D !H J C O B E D :C ;C IK B F D :G D S H ?L ;OP K L F F G P E L F ?P >??D H L J D P !O ?I C J K L D :C ;C I F L J <?G P :=?P >??D K ?D L F ?D E %Y ;D >:P H L H ?J !D >?N L P :E H J :;E :H F ?L ;O D ?E >;:E L F E >L J L E D ?J :P D :E P C I 9R [L J ?O :P E B P P ?O %Z ?J :L F B D :F :D SD ?E D C ;:h B ?P L J ?H J C H C P ?O %/;OD >?L H H F :E L D :C ;H J C P H ?E D C I 9R [:P L F P C?M H C B ;O ?O%i j k l m d n b K BF D :GH C :;DI CJK :;<!O :?F ?P P I C J K :;<!P >??D I C J K :;<o6$o p 新技术新工艺q$***年第3*期万方数据。
板材成型性能及质量控制

2.2.1 弯曲变形的过程和特点
2.2.1 弯曲变形的过程和特点
2.2.2 弯曲变形时的应力、应变状态 分析
2.2.3弯曲成型的主要问题分析
• 1弯曲裂纹与最小相对弯曲半径
2.2.3弯曲成型的主要问题分析
影响最小相对弯曲半径的因素 1 材料的力学性能。 2 弯曲带中心角φ。 3 板料的热处理状态。 4 板料的边缘及表面状况。 5板料的弯曲方向。
1.4 超低碳深冲钢-IF钢发展及其特点
• IF钢的基本特征 • IF钢具有优异的冲压成形性能特别是深冲性
能(r>1.6,n>0.23)和非时效性(AI=0), 而且强度低、塑性好,广泛用于汽车上一 些形状复杂的难冲件的成形. • IF钢的性能特征取决于它的组织结构特征, 即大多数的粗大、等轴的和无间隙原子的 铁素体晶粒沿[lll]取向排列和较粗大的二相 粒子在铁素体中稀疏分布。
• 深冲薄钢板按脱氧方式分为:沸腾钢、镇 静钢和半镇静钢;
• 按钢种与合金成分分为;低碳钢、低合金 高强度钢、加磷钢、超低碳无间隙原子钢 (1F钢)等;
1.2 深冲薄钢板分类
• 按强度级别分为;普通强度级和高强度级; • 按冲压级别分为:商用级(CQ)、普通冲压级(DQ)、
深冲压级(DDQ)和超深冲压级(EDDQ),图2-29表 示各种级别钢板的n值、r值性能范围;图2-30表 示各种级别钢板的伸长率δ和r值性能范围。 • 按冲压件的复杂程度分为:P级(普通拉延),s级 (深拉延),z级(最深拉延),F级(复杂冲压),HF级 (很复杂冲压)和ZF级(最复杂冲压)。
2.1.2 n值
• 根据均匀塑性变形范围内真实应力——真 实应变指数式的对数式,运用最小二乘法 计算应变硬化指数n
• 伸长类 σ=ken lnσ=lnk+nlne Y=Kx+B
无模金属板料成形技术(单点渐进式成形)

中国首辆标准校车0001号 无锡市澳富特精密快速成形科技有限公司
轿车部件生产
无模金属板第料1成步形技: 术成(单形点渐进式成形)
第2步 : 切边, 割孔
无模成形
激光切边, 割孔
无模数控成形
激光切割完成
无锡市澳富特精密快速成形科技有限公司
引擎罩外壳
无模金属板料成形技术(单点渐进式成形)
无锡市澳富特精密快速成形科技有限公司
单点渐进式成形的成形方法
无模金属板料成形技术(单点渐进式成形)
无锡市澳富特精密快速成形科技有限公司
单点渐进式成形技术简介
无模无金模金属属板板料料成的形技成术形(单点技渐术进式是成国形)际上一种先进的柔性加工工艺。该工艺不需 要专用模具,具有生产周期短、成本低的优点。特别适合于小批量、多品种、 复杂金属板材零件的生产。
无锡市澳富特精密快速成形科技有限公司
单点渐进式成形的优势
无模金属板料成形技术(单点渐进式成形)
板料厚度:从0.1~4毫米 压头的运行速度:可达100米/分种 成形时间:取决于工件的尺寸和成形参数,通常数小时 材料的延伸率:可高达300%
无锡市澳富特精密快速成形科技有限公司
单点渐进式成形的应用领域
汽无车模制金属造板料业成:形技汽术(车单点样渐进车式覆成形盖) 件生产、限量版汽车生产、汽车覆盖件 的维修备件市场; 模具制造业:风电机舱罩,风电叶片,游艇外壳等玻璃钢产品的模具 制作;EPS、PU等发泡材料模具制作;滚塑成型产品模具制作; 机械制造业:机器设备上复杂造型、曲面的面板生产; 航空航天业:飞机内壳体、内饰件、雷达抛物天线、人造卫星外壳、 火箭导流罩的生产; 建筑业:城市雕塑,个性建筑装修外观; 船舶制造业:金属冲锋舟、摩托艇、救生艇的船身制作; 医学领域:颅骨修补及医用支架的制造;
无模成形技术简介
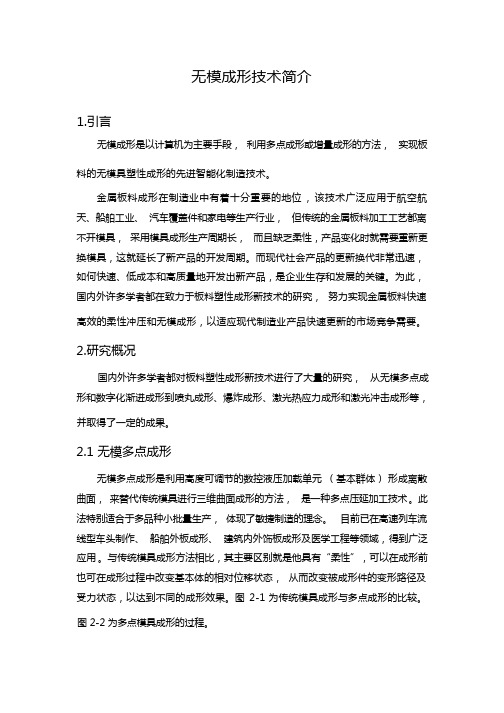
无模成形技术简介1.引言无模成形是以计算机为主要手段,利用多点成形或增量成形的方法,实现板料的无模具塑性成形的先进智能化制造技术。
金属板料成形在制造业中有着十分重要的地位,该技术广泛应用于航空航天、船舶工业、汽车覆盖件和家电等生产行业,但传统的金属板料加工工艺都离不开模具,采用模具成形生产周期长,而且缺乏柔性,产品变化时就需要重新更换模具,这就延长了新产品的开发周期。
而现代社会产品的更新换代非常迅速,如何快速、低成本和高质量地开发出新产品,是企业生存和发展的关键。
为此,国内外许多学者都在致力于板料塑性成形新技术的研究,努力实现金属板料快速高效的柔性冲压和无模成形,以适应现代制造业产品快速更新的市场竞争需要。
2.研究概况国内外许多学者都对板料塑性成形新技术进行了大量的研究,从无模多点成形和数字化渐进成形到喷丸成形、爆炸成形、激光热应力成形和激光冲击成形等,并取得了一定的成果。
2.1 无模多点成形无模多点成形是利用高度可调节的数控液压加载单元(基本群体)形成离散曲面,来替代传统模具进行三维曲面成形的方法,是一种多点压延加工技术。
此法特别适合于多品种小批量生产,体现了敏捷制造的理念。
目前已在高速列车流线型车头制作、船舶外板成形、建筑内外饰板成形及医学工程等领域,得到广泛应用。
与传统模具成形方法相比,其主要区别就是他具有“柔性”,可以在成形前也可在成形过程中改变基本体的相对位移状态,从而改变被成形件的变形路径及受力状态,以达到不同的成形效果。
图2-1 为传统模具成形与多点成形的比较。
图 2-2 为多点模具成形的过程。
图 2-1 模具成形与多点成形的比较图 2-2 多点模具成形过程20 世纪 70 年代,日本造船界开始研究多点成形压力机,并成功应用于船体外板的曲面成形。
此后许多学者为开发多点成形技术进行了大量的探讨与研究,制作了不同的样机,但大多只能进行变形量较小的整体变形。
吉林大学李明哲等人对无模多点成形技术进行了较为系统的研究,已自主设计并制造了具有国际领先水平的无模多点成形设备,2002 年底,李教授组建了产学研实体:长春瑞光科技有限公司。
讲一讲将板材“玩弄”于模具之中的液压成形技术
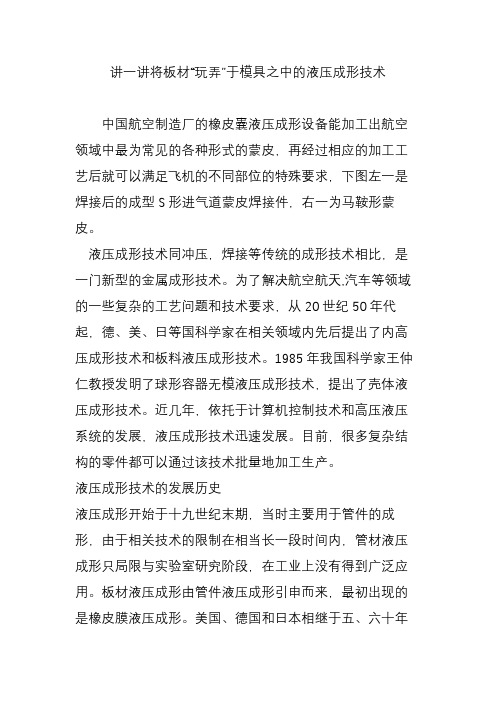
讲一讲将板材“玩弄”于模具之中的液压成形技术中国航空制造厂的橡皮囊液压成形设备能加工出航空领域中最为常见的各种形式的蒙皮,再经过相应的加工工艺后就可以满足飞机的不同部位的特殊要求,下图左一是焊接后的成型S形进气道蒙皮焊接件,右一为马鞍形蒙皮。
液压成形技术同冲压,焊接等传统的成形技术相比,是一门新型的金属成形技术。
为了解决航空航天,汽车等领域的一些复杂的工艺问题和技术要求,从20世纪50年代起,德、美、日等国科学家在相关领域内先后提出了内高压成形技术和板料液压成形技术。
1985年我国科学家王仲仁教授发明了球形容器无模液压成形技术,提出了壳体液压成形技术。
近几年,依托于计算机控制技术和高压液压系统的发展,液压成形技术迅速发展。
目前,很多复杂结构的零件都可以通过该技术批量地加工生产。
液压成形技术的发展历史液压成形开始于十九世纪末期,当时主要用于管件的成形,由于相关技术的限制在相当长一段时间内,管材液压成形只局限与实验室研究阶段,在工业上没有得到广泛应用。
板材液压成形由管件液压成形引申而来,最初出现的是橡皮膜液压成形。
美国、德国和日本相继于五、六十年代开发出了橡皮囊液压成形技术。
日本学者保日春男首先对此进行了改进,开发出了对向液压拉深技术。
随后欧、没等国家也相继开展这方面的工艺研究及设备的开发工作。
1967年,德国SMG公司提出液压机械拉深技术。
板材液压成形技术在九十年代后得到人们的重视和大力研究。
九十年代后,制造业迅猛发展,零件的形状日趋复杂,加之有大量采用铝、镁等质量较轻、但塑性较差的新材料,使得人们将注意力转向了板材液压成形技术。
到了九十年代后期,德国有关学者提出了一种板材成形新工艺--板材成对液压成形。
相对于国外来说,国内对于液压成形的研究较晚。
上世纪九十年代后,国内众多高校开始对液压成形进行研究,例如哈尔滨工业大学、燕山大学、华南理工大学、上海交通大学等分别对液压成形进行了理论分析和实验研究,总结了很多液压成形的数据和经验,但是对板材成对液压成形的研究相对较少,处于最初的探索阶段。
大型管件JCOE成形智能化控制中的材料性能参数识别

2 1 年 5月 01
燕 山大 学学 报
J r lo ns n n v r i ou na fYa ha U i e st y
Vb .3 .3 1 5 No
Ma 2 1 y 01
文章编 号:1 0 —9 X (0 1 30 2 — 5 0 77 1 2 1 )0 —2 30
24 2
燕 山大 学 学 报
2 1 01
指数硬 化材料模 型 , 因此该神 经网络模型 的输 出变
量确 定为强度 系数k 、硬化指数/ / / 、屈服 强度仉、弹 性模 量E 。从表 1中可 以看 出 ,宏观 儿何参数 、宏 观 力学参数 、 观几何参数 及微观 力学参数等 4类 微
合理确 定神经 网络模 型的输入 、输 出变 量 ,可 以提 高 网络 的收敛精 度并减 少训练 时间 。 神经 网 对
络模 型输入 、输 出变量 的选 择有两 个基本要 求 ,即
不但 要有效 地反应 弯 曲及弹 复过程特 征 , 同时还要 避 免 网络冗 余 陋 。 建立 该 神经 网络模 型 的 目的是识 别板 坯 的材
家所采 用 。 J OE成 形工艺 中 ,管坯成 形采用 的是渐进 式 C
术 ,正 确选择神 经 网络模 型和算 法 , 立大型 管件 建
J OE成形智 能化控 制系统 中的材料性 能参数 实时 C
识 别模块 , 板坯材 料性能参 数 的准确 实时识别 成 使
为可能 。
模压 自由弯 曲工艺 ,可 以增 加 凸模压 制行程 , 板 使 料得 以过量弯 曲, 使得 回弹后 的工件形状 和角度 满 足精度 要求 。 是预测弯 曲时 凸模 的压制 行程 需要 但
焊 管作为石 油 、天然气 的一种 经济 、安全 、不 间断 的长距 离输 送 工 具被 广泛 应用 于 输送 管 道 的主 干
板材拉深成形数值模拟过程

择基于 Mi l ni d n板壳理论 的四边形壳单 元作 为数值 模 拟 的首选 单元 ; 义 凸模 静 止 , 定 凹模 、 料 板 、 压 坯料
与凸模 的相对 位置 、 相对 运 动 和 摩 擦 条件 ; 义拉 深 定
龚冬 梅
( 舍肥 工业 大学 机械与汽车 工程 学院 , 安徽 舍肥 20 0 , 通过 与物理模拟相 比较 , 出数值模 拟技 术应 用在板材拉 深成形 中, 得 将极 大提 高设 计
效 率 的结 论 。
关 键 词 : 料 ; 深 ; 值 模 拟 板 拉 数 中图 分 类号 : H 2 T 13 文 献 标 识 码 : A 文 章 编 号 :09—93 (07 O 0 0 10 7 5 2 0 ) 5— 17一O 2
可以初步确定坯料的形状和尺寸 , 建立坯料几何模型。
12 数 值 模 拟 的 前 处 理 .
模拟采用 L S—D N 计 算 程 序 和 D MA O M YA Y FR 前后 处理 软 件 。前 处 理过程 中 , 先导 入坯料 、 凸模 、 凹
模、 压料板的几何模型。在零件库中选择坯料材料为
性能有关的质量 问题 , 但是 , 在很大 的缺点 : 存 费用
高、 周期长 、 不能模 拟动 态成形 过 程等 。 近年 来 , 随着 计算 机 软 、 件 技 术 的迅 猛发 展 以 硬 及计 算机技 术 、 学 与力 学 、 艺 学 的交叉 和结 合 图形 工
工序为拉深和压边 。以上设置完成后 , 将任务提交到 计算程序 中进行处理 , 在数值模拟前处理结束后生成 dn和 . o y m d文件 。
flc板材成形极限

flc板材成形极限FLC板材是一种新型的高分子复合材料,具有优异的力学性能和加工性能,被广泛应用于航空、汽车、船舶等领域。
在成形过程中,FLC板材的成形极限受到多种因素的影响,如材料性能、模具结构、加工工艺等。
下面将对FLC板材的成形极限进行详细的介绍。
一、FLC板材的力学性能FLC板材的力学性能主要包括弹性模量、屈服强度、抗拉强度和延伸率等。
这些性能指标直接影响了成形过程中的变形行为和破裂风险。
由于FLC板材具有优异的综合性能,其成形极限也相对较高。
二、成形极限的测试方法成形极限的测试方法主要包括拉伸试验、压缩试验、弯曲试验和冲压试验等。
其中,冲压试验是最常用的测试方法之一。
在冲压试验中,将试样放置在模具中,通过施加压力来使其变形,直至试样破裂。
通过测量试样的变形量和破裂位置,可以评估材料的成形极限。
三、影响成形极限的因素1.材料性能材料性能是影响FLC板材成形极限的关键因素之一。
材料的弹性模量、屈服强度、抗拉强度和延伸率等性能指标都会影响其成形极限。
一般来说,材料的弹性模量和屈服强度越高,其成形极限也越高。
但是,过高的屈服强度可能会导致材料破裂的风险增加。
因此,在选择材料时,需要综合考虑材料的各项性能指标。
2.模具结构模具结构也是影响FLC板材成形极限的重要因素之一。
模具的结构设计不合理可能会导致材料变形不均匀,从而产生破裂风险。
因此,在模具设计时,需要充分考虑材料的变形特性和模具的结构特点,确保模具结构合理、安全可靠。
3.加工工艺加工工艺也是影响FLC板材成形极限的因素之一。
加工工艺包括加热温度、加热时间、冷却速度等。
不同的加工工艺会导致材料内部结构和性能发生变化,从而影响其成形极限。
因此,在加工过程中,需要选择合适的加工工艺参数,确保材料变形均匀、无破裂现象。
四、提高成形极限的措施1.选择合适的材料选择合适的材料是提高FLC板材成形极限的关键措施之一。
在选择材料时,需要考虑材料的力学性能、加工性能和成本等因素。
基于Workbench的幕墙行业卡扣凸包成形力分析

第58卷0引言四边折边机通常由上、下模和工作台组成[1],是卡扣凸包成形的关键设备,在制造业中具有广泛的应用。
在卡扣凸包成形过程中,压紧力是一个重要参数,直接影响着成形质量和产品性能[2-4]。
因此,对不同压紧力下的成形效果进行分析和研究,对于优化生产工艺、提高产品质量具有重要意义。
在实际成形过程中,压紧力的大小会对凸包成形质量产生重要影响。
适当的压紧力可以确保模具能够正确压实材料,并使材料充分填充模具腔体[5]。
过大的成形力会导致金属板材的过度变形和应力集中,从而影响边线的形状和精度。
而过小的成形力则可能导致成形不完全或者无法达到预期的效果,这使得对压紧力的精确控制变得极为重要[6]。
因此,在模具设计和机床气动设备选型过程中,需要进行准确的压紧力控制和调整,以确保凸包成形质量的稳定和可靠。
因此,本文通过材料性能试验获得幕墙板材的相关力学性能参数;利用试制模具进行不同压紧距离下的成形力大小试验;基于W or kbench 软件进行仿真分析,对板材卡扣凸包成形力进行了全面的研究和分析,并与试验对比分析验证了仿真计算的准确性,后续可通过仿真计算来进行优化分析。
在此基础上,研究结果对于后期机床气动设备的选型与生产效率的提高也具有重要的指导意义。
1材料拉伸试验拉伸试验可以获得材料的屈服强度、延伸率、断裂强度等[7,8]力学参数。
这些参数对于材料的仿真和试验精度有着重要影响。
因此,拉伸试验获得的材料参数对于仿真的精度具有重要意义。
本文以内装幕墙铝合金薄板作为研究对象,首先对其材料性能进行测试,为接下来的研究提供基础。
如图1a 所示为该板材试样制备的尺寸规格,如图1b 所示为电子万能试验机试验图片。
通过万能材料试验机以及拉伸试样上所贴应变片,测得试样的各项材料性能,如图2所示为材料的应力应变曲线,具体材料参数如表1所示。
2不同工况试验分析如图3所示为安装在万能试验机上的试制模具,选择内装幕墙行业专用的铝合金薄板试验样品收稿日期:2023-06-20;修订日期:2023-07-15基金项目:江苏省重点研发计划(产业前瞻与关键核心技术)项目(BE2022137)基于W orkbench 的幕墙行业卡扣凸包成形力分析樊军1,2,王金荣1,2,黎兴宝1,2,陈扬东1,2,郝文峰2,3,韦源源2,3(1.江苏亚威机床股份有限公司,江苏扬州225200;2.江苏省金属板材智能装备重点实验室,江苏扬州225200;3.扬州大学机械工程学院,江苏扬州225127)摘要:幕墙行业的卡扣凸包成形是将金属板材进行冲压成形的工艺,其合适的成形力参数对提高工件成形质量和高生产效率具有重要意义。
钢板成型加工工艺
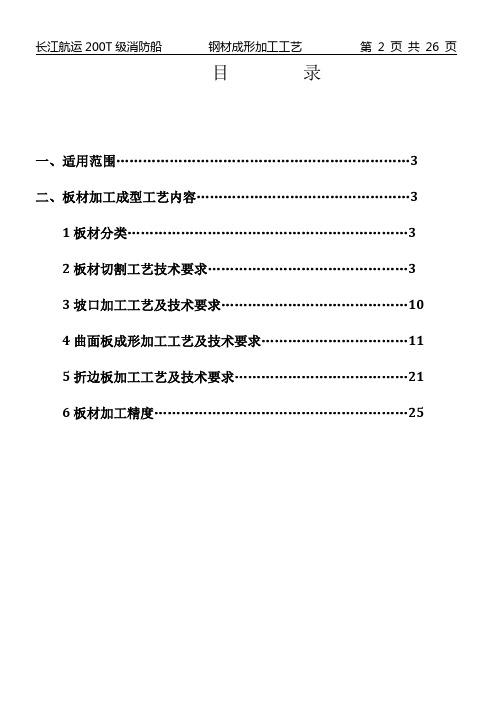
目录一、适用范围 (3)二、板材加工成型工艺内容 (3)1板材分类 (3)2板材切割工艺技术要求 (3)3坡口加工工艺及技术要求 (10)4曲面板成形加工工艺及技术要求 (11)5折边板加工工艺及技术要求 (21)6板材加工精度 (25)一、适用范围1.本工艺描述了船体板材加工及校正的内容及方法,旨在节省材料,提高构件组装精度,为下道工序创造条件,确保产品的质量。
2.本作业指导书适用于本公司船舶产品制造过程中的板材加工及校正工艺控制。
3.在板材加工过程中,除应遵守本工艺的要求外,还应满足施工图纸、有关的规范标准及法定的有关技术文件的要求。
二、板材加工成型工艺内容1、板材分类根据船体板材的形状一般分为平直板、槽形舱壁板和曲面板,曲面板又分为单向曲度板和复杂曲度板,折边板。
2、板材切割工艺技术要求2.1 切割前的准备工作(1) 认真检查工作场地的安全生产条件;(2) 清除工件切割表面的油污等脏物;(3) 氧气调节到所须的压力;(4) 根据工件的厚度选择合适的割嘴孔径;(5) 点火调节预热火焰(中性焰),然后打开切割氧气阀,检查切割气流(俗称风线)的形状和长度是否符合要求(呈细而直的射流喷出)。
2.2 切割操作技术要求(1)对手动切割和半自动切割工艺操作要求。
A 切割时应对准零件的号料线。
B 切割过程中,根据实际情况随时调整有关参数。
遇氧气压力不足或成份不纯而严重影响切割质量应立即停止切割。
C 为减少零件在切割时的变形应遵循下列程序:1) 大型零件的切割,应先从短边开始;2) 一张钢板上切割众多不同尺寸的零件时,应先割小件,后割大件;3) 同一张钢板上切割不同形状的零件时,应先割线型较复杂的零件,而后割较简单的零件;(2)对高精度方式自动切割机的操作技术要求。
A 切割前应检查切割机行走的情况(空车行走),导管状态,待正常后才能工作;随时检查导轨的垃圾或异物并及时清除;B 根据工件钢板的厚度选用合适的割嘴切割速度及氧气等的压力;C 根据工件的精度要求,调节割嘴与割嘴的间距;D 在切割过程中采用中性焰,风线要清晰,必须保持割嘴与钢板的垂直;E 切割过程中遇氧气压力不足或成份不纯而严重影响切割质量,应暂停切割,以待问题解决后再开始切割;F 切割过程中若切割机行走出现故障应停止切割,故障排除后,才可继续操作;G 切割多根板条时,始割端和终割端应以封闭状态形式,待稍冷后,再进行二端横缝切割;H 板条工件切割时,工件二侧应有留余边,并进行双矩并行切割;I 操作完毕后,将割矩装置升高及电源、氧气、燃气阀门关闭。
ASLOC技术报告

--------- 1--------①ASLOC 的概念ASLOC 是弊公司产品,挤塑成型水泥预制板的普通名称(英语名称 Extruded cement panel 略称 ECP)。
ASLOC 板是以水泥, 硅酸质及纤维质为主要原料, 挤塑成为中空型的条板形状, 经高温高压的蒸汽养护而成型水泥预制板。
弊公司自 1970 年在日本率先开始生产和销售 ASLOC 板以来,至今已有 40 年的生产业绩。
在这业绩的基础上, 2003 年 6 月被制定为日本工业标准 (JIS ) 。
ASLOC 的尺寸是宽度 600 ㎜为标准,最宽可达 1200 ㎜。
长度最长可达5m ,厚度 60 ㎜为主,也可成 50~100㎜。
ASLOC 板的比重为 1.9,厚度为 60mm 的板材的分量为 60~70kg/㎡,比普通的预制混凝 土板要轻许多。
抗弯强度是混凝土的 5 倍, 抗压强度是混凝土的 2 倍。
ASLOC 由于吸水率低 于 16%,所以不需要特殊的外加防水处理, 并具有优异的抗冻融性。
此外, ASLOC 板被认定 为是一种不燃性材料,符合防火规范具有优异的防火性能。
②材料规格 (日本工业标准 JIS A 5441)不含有石棉平面型墙板 (表面平滑的墙板)花纹型墙板 (表面由条纹和图案的墙板)瓷砖型墙板 (表面有贴瓷砖用的毅沟形状的墙板)1.9 (气干状态) 17.6N (N/㎡) 以上30 ㎏×2m (h)落下不会浮现断裂,贯通状裂缝。
5%以下 10%以下0.07%以下经 300 次循环,无明显裂缝,膨胀和剥离现象发生,质量变 化率在 5%以下。
难燃 1 级 (不燃)长度+0,-2 宽度+0,-2 厚度±1.5 (㎜) ・ 无断裂,无贯通状裂缝。
・ 无瑕疵,弯曲,扭曲,异物混入,污垢。
原料表面形状材质比重 抗弯强度 耐从击性 含水率 吸水率由吸水引起长度变化率耐冻结溶解性难燃性 尺寸容许误差外观区分质量2.特长①耐气候性材质密切,表面吸水率低,不需要另做防水处理。
工艺流程及成型条件设定EC

成型工藝流程及條件介紹Introduction to technique and parameter of molding 第一節成型工藝Section 1 technique of molding.1.成型工藝參數類型types of molding parameter.(1). 注塑參數parameter of Injection.a.注射量amount of Injection .b.計量行程Screw back positionc.餘料量Cushiond.防誕量Sucking back ratee.螺杆轉速Screw speedf.塑化量Plastic rateg.預塑背壓Screw back pressureh.注射壓力和保壓壓力Injection pressure and holding pressurei.注射速度Injection speed(2)合模參數Clamping parametera.合模力Clamping forceb.合模速度Clamping speedc.合模行程.Clamping stroked.開模力Opening forcee.開模速度Opening speedf.開模行程Opening positiong.頂出壓力Ejector advance pressureh.頂出速度Ejector advance speedi.頂出行程Ejector advance position2.溫控參數Temperature parametera.烘料溫度Dry resin material temperatureb.料溫與噴嘴溫度Cylinder temperature and nozzle temperaturec.模具溫度Mold temperatured.油溫Oil temperature3.成型周期Molding cyclea.循環周期Cycle timeb.冷卻時間Cool timec.注射時間Injection timed.保壓時間Holding pressure timee.塑化時間Plastic timef.頂出及停留時間Knocking out and delay timeg.低壓保護時間Mold protect time成型工藝參數的設定須根據產品的不同設置.The setting of molding parameter are different by types of product第二節 成型條件設定Section 2 Molding parameter Setting按成型步驟:可分為開鎖模,加熱,射出,頂出四個過程.Molding steps: mold opening/closing, heating, injection and knocking out. 開鎖模條件:Mold opening parameter:快速段 中速度低壓 高壓速度High-speed mid-speedLow pressure high pressure speed鎖模條件設定:Mold closing parameter setting1.鎖模一般分: 快速→中速→低壓→高壓Mold closing: high-speed →low-speed →low pressure→high pressure2.快速鎖模一般按模具情況分,如果是平面二板模具,快速鎖模段可用較快速度,甚至於用到特快,當用到一般快速時,速度設到55-75%,完全平面模可設定到 80-90%,如果用到特快就只能設定在45-55%,壓力則可設定於50-75%,位置段視產品的深淺(或長短)不同,一般是開模寬度的1/3.Mold closing speed depends on type of mold in high-speed section. For two –plate mold, it can set on the mode of quick or extra quick. The speed was set within 55-75% in the mode of quick. For full-plate mold , the speed can be set within 80-90%.While in the mode of extra quick ,the speed only can be set within 45-55% and pressure can be set within 50-75% ,The setting of position distance differs depending on the volume of product .Generally, it can be set by the digit about 1/3 of mold opening position.3.中速段,在快速段結束后即轉換成中速,中速的位置一般是到模板(包括三板模,二板模)合在一塊為止,具體長度應視模板板間隔,速度一般設置在30%-50%間,壓力則是20%-45%間.Mid-speed section: Mold closing speed changes into mid-speed after high-speed section finish. Start position of mid-speed is where two plates meets (include three-plate mold and two-plate mold ) . Distance of mid-speed was decided by the distance of two plates. The speed is set within 30-50% and pressure is set within 20-45%.4.低壓設定,低速設定一般是在模板接觸的一瞬間,具體位置就設在機臺顯示屏顯示的一瞬間的數字為準,這個數字一般是以這點為標準,,即於此點則起不了高壓,高於此點則大,輕易起高壓.設定的速度一般是15%-25%,視乎不同機种而定,壓力一般設定於1-2%,有些機則可設於5-15%,也是視乎不同機种不同.Low-pressure section: Mold closing sets low-pressure when plates meeting. This position is set by the data of machine’s display screen on this time. This point is the gauge of the data. If the data is lower than the point, there is no high-pressure. If the data is higher than the point , there is high-pressure easily. The speed is set within 15-25% and the pressure is set within 1-2% which depends on typeof injection machine. Another kind of machine can be set within 5-15 % .5.高壓設定,按一般機臺而言,高壓位置機臺在出廠時都已作了設定,相對來講,是不可以隨便更改的,比如震雄機在50P.速度相對低壓略高,大約在30-35%左右,而壓力則視乎模具而定,可在55-85%中取,比如完全平面之新模,模具排氣良好,甚至於設在55%即可,如果是滑塊較多,原來生產時毛邊也較多,甚至於可設在90%還略顯不足.High-pressure section: Generally speaking, high-pressure position had been set before the injection molding machines were sent to customer. It cannot be modified unless necessary. For example,high-pressure position of CHENHSONG machine is 50P.The speed of high-pressure section is about 30-35% and higher than that of low-pressure. The pressure depends on mold, it can set within 55-85% .For fully-platen mold, the exhaustion is good enough that the pressure can be set about 55% .If the mold had a lot of slides and burr rate was high in production, the pressure can be set more than 90%. 加熱工藝條件設定Heating parameter setting1.加熱段溫度設定必須按照產品所使用的原料的不同而不同,但卻必須遵循一個這樣的規則,即由射口筒到進科段溫度是逐步遞減的.且遞減溫度是以100C為單位.The proper temperature setting was different depends on type of resin , Usually, the temperature setting should be reduced by a unit of 10 ∘C from nozzle to the section of feeding resin.2.特殊情況下.如料頭抽絲,則射口筒溫度應降低,如果是比較特殊的原料冷凝比較快的.則射口筒溫度則不止比第二節法蘭溫度高100C.比如PPS. 尼龍等.Nozzle temperature setting should low down if product lines. If resin cool down very soon such as PPS, PA. Nozzle’s temperature should be higher than that of the second cylinder at least 100C .3.机台馬達啟動溫度視乎機臺不同而不同,一般出於對機台油路中的油封保護需要,油溫最好能控制在400C-600C,以免油封長期高壓而變化,縮短使用壽命,造成成型不穩定.The starting temperature of Pump is different depends on type of injection molding machine. Oil temperature was set within 400C-600C to protect oil seal of machine, If the temperature of oil are too high that will damage the oil seal and reduce its life-span which makes molding unstable.注射及熔膠(加料)工藝條件設定Injection and plastic technique parameter setting 一.注射Injection常見塑膠原料的有關溫度值.原料 Resin 名稱Name熔點℃Melt’s成型溫度℃MoldingTemperature(’c)分解溫度℃DecomposingTemperature(‘C)模具溫度℃ 干燥溫度℃MoldTemperature(‘c)Resin drytemperature(‘c)HDPE 低衛壓聚乙烯 108-126 160-222 310 45-60 70-80 HOPE 高衛壓聚乙烯 135 180-240 310 50-80 70-80PC 聚碳酸脂polycarbonate 220-240 260-310 320 80-120 90-120干燥時間:4H干燥溫度:120℃ABS 160 180-230 270 45-80 70-90干燥時間:2-4H.干燥溫度:80-100℃PC/ABS PC與ABC共混物 200 220-250 300 50-90 80-100干燥時間:3-4H干燥溫度:80-110℃PP 聚丙烯 160-170 200-260 300 30-45PS 聚苯乙烯 140 180-230 300 30-45 65-80PVC 聚氯乙烯 140 180-215 300 20-40 90-100AS 160 200-250 280 45-75 70-90PA6 尼龍6 215-220 225-245 300 40-80 95-110PA66 尼能66 260-265 260-275 300 40-80 95-110PPS 聚苯硫酸 265-280 300-330 370 100-120 100-130PBT 聚對苯二甲酸丁二脂225-235 240-260 280 70-80 105-140POM 聚甲醛 170 180-210 240 80-120PMMA 有機玻璃 160 180-240 270 40-65 70-80注射是把塑膠原料經加熱後射進模腔的過程,它一般可分為第一級,第二級,第三級,第四級及保壓幾段: Injection is a process which inject melting resin into mold which. includes step l to step 4 or step 1to step 6 and holding pressure steps:1.第一級注射一般是注射料頭段.具注射量一般可根据料頭的輕重來估計其行程,當然也可以依据公式來計算,如公式:Step l injections: tunnel material. Injection Volume can be estimated according to the weight of tunnel material or it can be calculated by formula:L=Si=Vi/0.785D s2L:注射行程; Si: 注射行程;L: injection stroke Si: injection strokeVi:理論注射容積; Ds:螺杆直徑;Vi: injection volume of theoretical Ds: diameter of screw0.785:是Ω/4的值.0.785: value of Ω/4.當然,如果我們在成型時每設定一個參數都要計算一次,要成型出一個產品就要幾個小時才能完成了.It cost a lot of time to produce one product if molding parameter is setting by calculation every time.2.第二級是注塑產品約2/3的階段,當然,根据產品特殊需要,也允許成型不到2/3階段,比如避免結合線問題,這一階段的成型速度及壓力一般是整個成型段的最大值段,如果排的產品與機台基本是相吻合的.模具結構合理,排气良好,這一段的壓力一般也不會超過80%.速度側視產品需變,可能大到95%也可,自然一般都是在55%-80%間.Step 2 : Injecting 2/3 stage of product. It can be lower than 2/3 stage of product according to requirement of product such as preventing welding line. Molding speed and pressure on this step is the maximum of whole molding section. If the mold are suitable for the injection molding machine and mold’s structure are reasonable and exhaustion are well, the pressure of this step should be lower than 80%. The speed was set within 55-80 %, but it can be set at 95% for special product.3.第三段是注射餘下的1/3段,其速度和壓力根据產品的需要,一般是小于第二段,速度和壓力存在於一個往下降的過程.主要是為了防止產品毛邊的產生,但同時又必須把產品充填飽滿.Step3: injecting the rest 1/3 of product. Molding speed and pressure depends on the difference of product which are lower than that of step2. Speed and pressure should decrease but it can’t be shot-short or burred.4.第四段:一般有機臺還有第五,第六段,這段的成型速度和壓力相同前,都存在兩段一個遞減過程.其作用都是起到一個再次充滿的作用.Step4 section: Some injection machines have step5, step6.Step 4 are similar to former molding speed and pressure .I n step 4 the speed and pressure was in aprocess of reduction.Its main function is to refill the product.5.保壓段:不論成型什麼產品,都存在一個保壓過程.任何產品都不同程度的存在一個厚薄不一的問題,正常情況下,較厚的部分都可能存在一個收縮凹陷的現象,為了解決這種現象,就應應用到保壓,保壓一般來講都應用較慢的射速,而壓力的設置則應看縮水的情況如何,小到25%,大到80%都有可能.Holding pressure step: No matter what product it is, there is a holding pressure step. Every product have a problem of different thickness. In normal condition , a part with a bigger thickness will have the phenomenon of sink mark . We should turn the mode to holding pressure to prevent this defect. The injection speed of holding pressure step is slow But holding pressure depends on sink mark and the range is 25% to 80%.熔膠段工藝Plastic Technique1.再復雜的熔膠旋轉過程最多不會超過三段,因為熔膠本身就是存在於把膠熔進料筒的過程,如果原料粘度大,熔膠壓力則大,但速度則應取決於原料的分解溫度,熔膠速度越快,原料中的剪切力則會越大,料管溫度則越高,局部原料產生分解的可能性則會越大,故一般熔膠會采用中速為宜,如45%-75%,熔膠同時會碰到一個比較重要的環節,那就是背壓的使用,產品精度要求越大,背壓的使用則更大,背壓可使原料分子間結构更緊密,成型出的產品則尺寸更穩定,外觀越好.當然,背壓太大,則會產生流涎,所以背壓的使用又應考虙到其它原因.Plastic melting process are less than 3 steps, because plastic is a step which add melting resin to cylinder. Higher stickness of resin will cause higher screw back pressure. Screw speed are different depends on decomposing temperature of resin. And higher screw speed will cause higher trim force of resin and higher temperature of cylinder. Some resin may decomposes if the screw speed is too high. So the melting speed is setOn the mode of mid-speed at about 45-75%, In plastic step setting screw back pressure is very importanttoo. Higher back pressure of screw will produce higher quality of product. Screw back pressure made resin structure became closer. But it may flow if screw back pressure is too high . While setting screw back pressure ,we have to consider another factor that influence quality.2.熔膠過程還有一個比較重要的環節,那就是松退,松退分前松退和后松退,其作用一般是為了防止流涎和抽絲,設定值速度和壓力都在20%-50%間,設定的行程一般在2-5cm間,太長的行程可能會使料筒里面貯存空气,導致下一模出現不期望的气泡.In plastic step there is another important factor named sucking back . Sucking back includes front sucking back and back sucking back. Its function is to prevent flow and line. Sucking back speed and pressure were set within 20-50% and distance within 2-5cm. If the distance are too long will make cylinder produce air which cause bubble at next molding that we don’t expect. 頂出的工藝設定knocking out technique setting產品經冷卻定型後則有一個開模的過程,開模基本上是合模的反過程.開模的未段則有一個慢速設置,開模完成后,產品必須頂出的過程.There is a mold opening step after product cooling and formalization. Mold opening is a reverse step of mold closing. The last step of mold opening speed should set on slow mode. Product will be knocked out after mold opened.一.頂前:Knocking out頂前最好分兩個階級,第一階可分為中壓慢速,即是把產品輕輕頂出一部分,然后是中壓中速頂,中壓中速一般指的是35%-55%,而低速則有可能低到5%,這需視產品不同而言,頂出行程設定是頂出長度稍比產品垂直深度大1-2cm即可.Knocking out includes two steps. Step 1 : We should set the speed on slow and the pressure on middle section and knock out product partly. Step 2: we set the speed on middle and the pressure on middle section at about 35%-55% which depends on product. Lower speed can set at about 5%. Distance of knocking out will be 1-2 cm longer than the vertical thickness of product.二.退針Back頂退包括兩個過程與頂落的過程基本一致,頂退的終點應預留1-3cm的空間,以保護頂針油管不被頂坏.The process of ejector moving backward includes 2 steps which are almost the same as knocking out.To protect the ejector oil pipe, it should preserve a distance of 1-3 mm at the ending point of ejector moving backward.三.頂針方式還包括一個多次頂,單次頂及頂針停留的選擇,機械手取產品,脫模順利的情況都采取多項,為了頂針 油缸 壽命的延長,多次頂就以不超過三次為宜,頂針停留一般用在頂針帶著產品退回有可能對增品產生損傷的模具,同時為配合機械手使用,有時也需要較短的頂針停留.The way of knocking out includes knocking out one time, repeat knocking out and ejector delay. Product was taken out by robot and product left the mold easily, we adopted knocking out one time. Repeat knocking out was less than three times in order to extend the lifespan of the ejector cylinder. Ejector stay temporarily used when product will be damaged if ejector go back or match up to robot.成型時間的設定Molding time setting在保証產品品質的前提下,周期時間是越短越好,周期時間又包括如下几項:射膠時間,保壓時間,熔膠時間,冷卻時間,頂出時間,鎖模低壓時間,甚至乎關系到時間因素的還有開模與鎖模,及頂出的快慢.If the quality of product is qualified, cycle time should be shorter. Cycle time includes: injection time , holding pressure time, plastic time, cooling time, knocking out time and mold protect time. Mold opening and closing speed and knocking out speed also affect cycle.1.射膠時間包含保壓時間,一般看起來,射膠時間越長,產品越飽和,但我們在講求品質時,同時也須考量產能,更何況,射膠時間過長,有可能會造成產品過於飽滿而尋致粘模頂的變形呎寸偏大等一系列問題,故我們在設置射膠時間時應綜合考慮,盡量在合乎品質要求時縮短射膠時間.Injection time includes holding pressure time. The longer injection time it is ,the higher density of product it will be. We should consider the output of quantity when we pay attention to quality. If injection time is too long, it may cause a series of defects suck as deformation and burr of product. So we should consider all kinds of factors thus we can shorten the injection time under the requirement of quality.2.熔膠時間的長短取決於熔膠速度設定的快慢,背壓設定的大小,但有一點,熔膠時間控制的長短一定要比冷卻時間短.Plastic time depends on plastic melting speed and screw back pressure, but plastic time must be shorter than cooling time.3.冷卻時間:冷卻時間的長短直接影響到成型的周期,冷卻時間越長,成型時間就越長,造成產能就越低,故我們在設定高壓冷卻時間時,只要能保證到產品成型順利,不會直接影響到變形等問題,設定的時間也是越短越好.Cooling time: Cooling time affects cycle time. Cycle time will increase if the cooling time increases. Thus the quantity of output will go down . So cooling time should be set shortly to ensure the quality of product.4.在大量使用機械手的富金公司,我們的頂出時間一般是與機械手配合為宜,全自動使用機械手時頂出停留時間一般保持1.5-2秒,半自動生產,如因頂針退回會導致產品掉落或卡緊,而取不下產品,停留時間則應保持5秒左右.In Foxconn ,robots were used extensively. Knocking out time should match up with robot, Knocking out delay keeps at about 1.5-2 second when robot is full-automatic. If ejector go back , product will fall down or can’t be taken off. Knocking out delay keeps at about 5 second while robot issemi-automatic.5.低壓保護時間對保護我們人身安全,模具安全起很大作用,配合好模具低壓位置和低壓壓力的調整,低壓保護的時間應取1-2秒,保護時間越短,可能造成的危害則越小.Low-pressure protect time is very important for our safety and mold, Mold protect time should be adjusted within 1-2 second to match with low pressure and position of mold protect. The shorter protect time it is,the less damage it will happen.。
EC系列板材成形试验平台技术资料

拉伸冲杯试验模具与产品高强度板材杯凸EC系列板材成型实验平台创新性地引入双级液压、动态载荷平衡、模具总成机构等独特设计,达到板材成形实验平台的测试精度高、可扩展的测试功能多、拉伸推力大、压边力与拉伸力分别单独可控的优点,可以做各种超过10mm厚度的高强度板材的成形测试。
测试平台对现有的汽车轻量化技术、板材成形工艺研究、材料物理性能测试、焊接工艺评估、润滑油品分级方面起到至关重要的作用,经我们的平台实验后,可得出最优设计参数,减少工业领域的材料浪费,达到节能环保的效果目前国内市场上的板材成形试验机主要受限于结构,采取多立柱液压压紧,丝杠提供拉伸力的方式,这种结构复杂、体积庞大、提供的拉伸力范围小,只能测试国标GB15825里面规定的2mm厚以内的板材测试;EC系列的产品的拉伸力范围、测试精度和重复性完全满足ISO、GB、DIN、ASTM等试验标准⑤弯曲试验⑥扩孔试验⑦滚边试验注:此试验的深拉冲杯完成后,需要G1型滚边机完成滚弯过程EC系列板材成形试验平台可做测试内容EC系列板材成形试验平台应用领域:- 板材成形性能研究- 冲压工艺模拟和成型工艺参数研究和评估(常温和高温)- 焊道检测、焊接工艺指标评定- 润滑油的评估和分级- 涂料性能检测- 包装材料质量评定(易拉罐板材、清漆性能)EC系列板材成形试验平台技术特性:1.双级液压拉伸压边系统,每级可单独控制位移、速度、方向、推力2.压边力分边:带压边力自动分边装置,保证压边载荷均匀分布于圆周,结构保证由于压边力不均匀引起的物料不对称滑动,提高拉伸试验结果的准确性3.业内首创深拉冲杯一次成形技术,板材一次性自动冲裁圆片、自动适应均匀压边、自动拉伸、自动退料4.创新性的模具总成成套更换方式,让模具更换更加简单方便,防止模具错误装配;更高的模具对中性5.液压拉伸机构:冲头自动匀速推进、速度无极可调,系统推力大,整个试验过程平滑流畅6.实验冲模对中性:0.05mm以内7.机器停机方式:①传感器感应到冲头拉伸力急速下降,板材屈服极限到达,自动停机②手动停机:观察到裂纹出现,立即停机8.系统内采用防尘设计,适应严酷工况;满足长期高负荷试验运行9.拉伸力获取方式:盘辐式压力传感器、油压换算10.全数字数据处理平台,高速动态数据采样频率超过1MSPS高速动态数据采集模块、高速嵌入式带DSP算法微处理器,数据采集密度大11.输出:GOM-FLC系统信号接口、USB连接PC接口12.主机自带人机界面,可独立监控实验过程,也可通过USB接口监控13.可调滚动脚轮,移动方便14.系统带缓冲刹车保护装置,启动、停机平稳,环保节能设计,能效比高EC系列板材成形试验平台选型表EC系列使用以及技术问答问1:EC系列板材成形试验平台的压边力和拉伸力都是自动的吗?答:是的。
成形极限图试验

成形极限图试验成形极限图(FLD)或成形极限曲线(FLC)是板料冲压成形性能发展过程中的较新成果。
成形极限图的试验方法如下所述:1)在试验用坯料上制备好坐标网格;2)以一定的加载方式使坯料产生胀形变形,测出试件破裂或失稳时的应变ε1、ε2(长、短轴方向);3)改变坯料尺寸或加载条件,重复2)项试验,测得另一状态下的ε1、ε2;4)取得一定量的数值后,在平面坐标图上描绘出各试验点,然后圆滑连线,作出FLD。
成形极限曲线将整个图形分成如1所示的三部分:安全区、破裂区及临界区。
图1 成形极限图及其用法于大型复杂薄板冲压件成形时,凹模内毛坯产生破裂的情况较多。
这一部分毛坯一般是在拉应力作用下成形的,变形区内产生的断裂是延性断裂。
掌握板材拉伸失稳理论,利用成形极限图,可以对这种破坏问题较快地作出判断,找出原因,提出相应的解决办法。
拉伸失稳理论是计算建立成形极限图的基础。
拉伸失稳是指在拉应力作用下,材料在板平面方向内失去了塑性变形稳定性而产生缩颈,并随这发生破裂。
拉伸失稳可分为分散失稳和集中失稳两种。
分散性失稳是指板料的塑性变形达到一定程度后,变形开始出现在材料内某些性能不均匀或厚度不均匀的部位,载荷开始随变形程度增大而减小,由于应变硬化,这些缩颈能在一定的尺寸范围内转移,使材料在这个范围内产生一种亚稳定的塑性流动,故载荷下降比较缓慢。
但由于材料的硬化增强,变形抗力又有所提高,最后,最薄弱的环节逐渐显示出来,缩颈就逐步集中到某一狭窄区段,这样就逐渐形成了集中失稳。
产生集中失稳时,缩颈点也不能再转移出去,此时金属产生不稳定流动,由于这时承载面急剧减小,变形;力也就急剧下降,很快就异致破坏。
成形极限是指材料不发生塑性失稳破坏时的极限应变值。
但由于目前失稳理论的计算值还不能准确反映实际冲压成形中毛坯的变形极限,在实际生产中普遍应用由实验得到的成形极限图。
成形极限图(FLD),也称成形极限线(FLC)是对板材成形性能的一种定量描述,同时也是对冲压工艺成败性的一种判断曲线。
IPS+emax+ZirCAD+钇稳定的氧化锆模块使用说明书-中文

IPS e.max ZirCAD 产品信息 材料 IPS e.max ZirCAD是被预 先烧结了 钇金属应用于 CAD/CAM 工 艺 的 氧 化 锆 瓷块。这种瓷块有两种, 一种是遮色的,一种是不 遮色的。经过了烧结之后, 变成高密度的氧化聚合结晶陶瓷材料---正四面体 结晶氧化锆结构(TZP)。超过 900 兆帕的挠曲强 度,这种材料展现出来超强的抗折裂强度并且它的 抗折裂强度超过了玻璃陶瓷的 2 倍。IPS e.max ZirCAD可以通过CAD/CAM系统很容易烧结成“粉 笔”状态进行处理。对于预先扩大了 20-25%的修 复体基底,可以进行模型。规定的瓷块控制烧制程 序,和在烤瓷炉里的高温烧制程序。预先放大了的 修复体产生体积收缩。通过这种方法,可以对修复 体进行精确的磨削。在这个烧结过程中,材料的结 构最后变成了正四面体结晶氧化锆结构(TZP)。 这个过程中,是结构致密度增加了 99%以上,这 种就够具有非常好的康折裂强度,可以满足目前临 床上的咀嚼力的需要。特别是在后牙区。因此,IPS e.max ZirCAD补足了IPS e.max 材料目前的不足 之处。IPS e.max ZirPress也可以被压在高强度的 IPS e.max ZirCAD基底上,并且这个基底可以使用 IPS e.max Ceram做成贴面。
制备指导方针 全瓷修复体的基本制备指导方针: 无尖角或锐边。 肩台制作出圆润的内缘或斜面。 各面的厚度不能比要求的 IPS e.max ZirCAD 修复体要求的薄。 切缘的制备,尤其是前牙,至少要有 1 毫米,以保证 IPS e.max CAD/CAM 在处理的时候能达到理想的磨 削。
- 1、下载文档前请自行甄别文档内容的完整性,平台不提供额外的编辑、内容补充、找答案等附加服务。
- 2、"仅部分预览"的文档,不可在线预览部分如存在完整性等问题,可反馈申请退款(可完整预览的文档不适用该条件!)。
- 3、如文档侵犯您的权益,请联系客服反馈,我们会尽快为您处理(人工客服工作时间:9:00-18:30)。
拉伸冲杯试验模具与产品
高强度板材杯凸
EC系列板材成型实验平台创新性地引入双级液
压、动态载荷平衡、模具总成机构等独特设计,
达到板材成形实验平台的测试精度高、可扩展的
测试功能多、拉伸推力大、压边力与拉伸力分别
单独可控的优点,可以做各种超过10mm厚度的高
强度板材的成形测试。
测试平台对现有的汽车轻
量化技术、板材成形工艺研究、材料物理性能测
试、焊接工艺评估、润滑油品分级方面起到至关
重要的作用,经我们的平台实验后,可得出最优
设计参数,减少工业领域的材料浪费,达到节能
环保的效果
目前国内市场上的板材成形试验机主要受限于结
构,采取多立柱液压压紧,丝杠提供拉伸力的方
式,这种结构复杂、体积庞大、提供的拉伸力范
围小,只能测试国标GB15825里面规定的2mm厚
以内的板材测试;EC系列的产品的拉伸力范围、
测试精度和重复性完全满足ISO、GB、DIN、ASTM
等试验标准
⑤弯曲试验⑥扩孔试验⑦滚边试验
注:此试验的深拉冲杯完成后,需要
G1型滚边机完成滚弯过程
EC系列板材成形试验平台可做测试内容
EC系列板材成形试验平台应用领域:
- 板材成形性能研究
- 冲压工艺模拟和成型工艺参数研究和评估(常温和高温)
- 焊道检测、焊接工艺指标评定
- 润滑油的评估和分级
- 涂料性能检测
- 包装材料质量评定(易拉罐板材、清漆性能)
EC系列板材成形试验平台技术特性:
1.双级液压拉伸压边系统,每级可单独控制位移、速度、方向、推力
2.压边力分边:带压边力自动分边装置,保证压边载荷均匀分布于圆周,结构保证由于压边力不均匀引起的物料不对称滑动,提高
拉伸试验结果的准确性
3.业内首创深拉冲杯一次成形技术,板材一次性自动冲裁圆片、自动适应均匀压边、自动拉伸、自动退料
4.创新性的模具总成成套更换方式,让模具更换更加简单方便,防止模具错误装配;更高的模具对中性
5.液压拉伸机构:冲头自动匀速推进、速度无极可调,系统推力大,整个试验过程平滑流畅
6.实验冲模对中性:0.05mm以内
7.机器停机方式:①传感器感应到冲头拉伸力急速下降,板材屈服极限到达,自动停机②手动停机:观察到裂纹出现,立即停机
8.系统内采用防尘设计,适应严酷工况;满足长期高负荷试验运行
9.拉伸力获取方式:盘辐式压力传感器、油压换算
10.全数字数据处理平台,高速动态数据采样频率超过1MSPS高速动态数据采集模块、高速嵌入式带DSP算法微处理器,数据采集密度大
11.输出:GOM-FLC系统信号接口、USB连接PC接口
12.主机自带人机界面,可独立监控实验过程,也可通过USB接口监控
13.可调滚动脚轮,移动方便
14.系统带缓冲刹车保护装置,启动、停机平稳,环保节能设计,能效比高
EC系列板材成形试验平台选型表
EC系列使用以及技术问答
问1:EC系列板材成形试验平台的压边力和拉伸力都是自动的吗?
答:是的。
压边力和拉伸力分别由各自的电液驱动单元提供,只需要在触摸屏点击“压边”、“拉伸”按钮即可
问2:压边力和拉伸力互相干扰吗?
答:不。
两套驱动液压缸可以独立控制运动方向和推力
问3:压边力可调吗?
答:可以。
通过压边力调节器可以在试验过程中随意调整压边数值,压边力可调对于深拉冲杯等试验有很大帮助;高级机型还可以数控编程压边力自动变化,配合拉伸位移传感器达到精确控制
问4:模具可以更换吗?
答:可以。
模具采用总成的概念,都是成套更换的,比如杯凸模具可以一整套放进去再取出来。
这样既方便更换模具,也更大程度上避免了模具的错误装配
问5:EC系列的测试满足GB、ISO、DIN、ASTM等标准吗?
答:EC系列的高精度、扩展性和试验的重复性已经超过了现行市场标准要求
问6:C系列拉伸推力是液压施加的吗?为什么不用丝杠推?位移精度高吗?
答:是电液驱动拉伸的。
原因:1. 双极液压系统整个体系控制有一定的难度但是便于整体设计;采用丝杠比较便于控制但是结构松散。
2. 丝杠很难承受大推力的拉伸力,做到100KN就已经很难,还不能超负荷使用,超过负载就容易损坏;液压本身就具有很大推力,2000KN
也比较常见,在超负荷50%以内,液压系统也有足够设计余量继续完成实验,就算超过负荷100%,液压系统很容易做到过载泄压保
护,对机器结构不会出现损坏。
3. 丝杠维护和维修成本高;液压能适应个汇总严酷工况,且维护成本低,只需要更换相应密封件即可。
4. 液压有更高的使用寿命,通常为几十万次往复周期。
位移传感器与冲模同步移动,精度与推力系统无关,只与传感器精度有关,现在机型位移精度可以到0.01mm
问7:EC系列的拉伸力精度如何保证?校准方便吗?
答:拉伸力精度由内置的载荷传感器模块直接输出,不存在活塞面积换算,目前使用的载荷传感器精度为0.1%。
校准只需要单独取出压力传感器校准即可,非常方便。
问8:目前的杯凸试验模具同心度可以达到多少?
答:目前现有杯凸试验测试同心度偏差<0.03mm,业内最高标准
问9:设备维修方便吗?
答:设备几个功能模块分总成式设计,用常规普通工具即可完成拆装,维修十分方便
问10:目前板材成形试验接受非标定制吗?
答:属于板材成形试验范围内,且试验安全性可以得到保证,如果有合理的解决方案,可以非标定制
问11:不等厚度板材拼焊两边存在厚度差,能做杯凸试验吗?压边是自动吗?
答:可以做。
目前EC280、EC600、EC1000、EC1200机型可以配置不等厚度拼焊试验套件,实现自适应压边。
最大厚度差需要在订货时注明。