注塑成型工艺条件调试规定
注塑成型工艺调整方法

注塑成型工艺调整方法注射保压时间、冷却时间注射时间、保压时间和冷却时间须根据产品厚度、模具温度、材料性能等进行设定。
注射时间设定一般以略大於螺杆完成注射行程移动的时间即可,过长的注射时间不但会产生机械磨损、能耗增加等负面影响,同时也会延长成型周期。
保压时间设定根据产品厚度来设定,薄壁产品在成型时可不用保压时间;在设定保压时间时,只要产品表面无明显凹陷即可,也可用称重法来确定,逐步延长保压时间直至产品质量不再变化的时间即可定为最佳保压时间。
冷却时间同样需根据产品厚度、模具温度、材料性能来确定,一般无定型聚合物所需冷却时间要比结晶型聚合物时间长。
注射压力、速度注射压力设定要遵循宜低不宜高的原则,只要能提供足够动力达到所要求的注射速度、使熔体能够顺利充满型腔即可,过高的压力容易使制品内产生内应力;但在成型尺寸精度较高的制品时,为防止产品收缩过度,可以采用高压力注射以减少制品脱模後的收缩。
注射速度会影响产品的外观质量,其设定应根据模具的几何结构、排气状况等进行设定,一般在保证良好的外观前提下,尽量提高注射速度,以减少充填时间。
在注射成型中,熔体在模具内流动时,模壁会形成固化层,因而降低了可流动通道的厚度,一般根据模具结构和注射速度不同,模壁会有0.2mm左右的固化层。
因此成型中通常采用较快的注射速度。
注射行程、多级注射参数在成型中,首先须确定注射行程,理论上,注射行程可按下式计算?s S1=4(CVp+Va)/ρDs2式中?sS1??注射行程 Vp?产品体积ρ?树脂密度 C?型腔数目Va?浇口体积 Ds?螺杆直径在实际生产中,若已知“产品+浇口”的总重量,则可用下式来计算注射行程?sS1=(M/Mmax)?Smax+(5~10)mm式中?s S1---注射行程,mmM?“产品+浇口”总重量,gMmax?注塑机最大注射量,gSmax?注塑机最大注射行程,mm由於浇道系统及模具各部位几何形状不同,为满足产品质量要求,在不同部位对充模熔体的流动状态(主要指流动时压力、速度)有不同要求。
注塑工艺各项参数调整
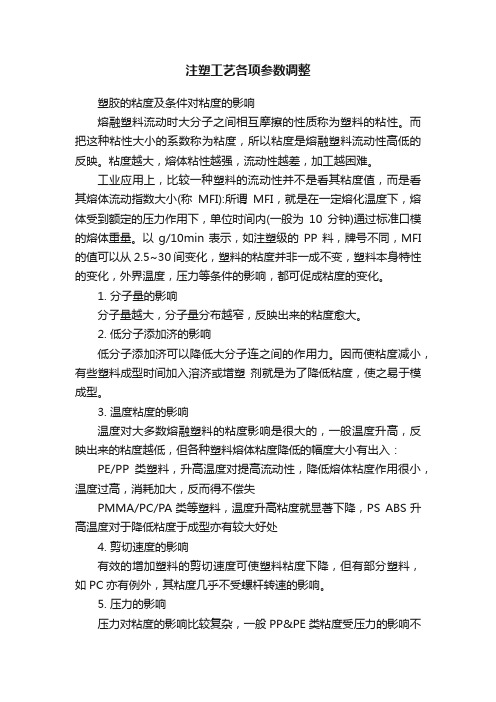
注塑工艺各项参数调整塑胶的粘度及条件对粘度的影响熔融塑料流动时大分子之间相互摩擦的性质称为塑料的粘性。
而把这种粘性大小的系数称为粘度,所以粘度是熔融塑料流动性高低的反映。
粘度越大,熔体粘性越强,流动性越差,加工越困难。
工业应用上,比较一种塑料的流动性并不是看其粘度值,而是看其熔体流动指数大小(称MFI):所谓MFI,就是在一定熔化温度下,熔体受到额定的压力作用下,单位时间内(一般为10分钟)通过标准口模的熔体重量。
以g/10min表示,如注塑级的PP料,牌号不同,MFI 的值可以从2.5~30间变化,塑料的粘度并非一成不变,塑料本身特性的变化,外界温度,压力等条件的影响,都可促成粘度的变化。
1. 分子量的影响分子量越大,分子量分布越窄,反映出来的粘度愈大。
2. 低分子添加济的影响低分子添加济可以降低大分子连之间的作用力。
因而使粘度减小,有些塑料成型时间加入溶济或增塑剂就是为了降低粘度,使之易于模成型。
3. 温度粘度的影响温度对大多数熔融塑料的粘度影响是很大的,一般温度升高,反映出来的粘度越低,但各种塑料熔体粘度降低的幅度大小有出入:PE/PP类塑料,升高温度对提高流动性,降低熔体粘度作用很小,温度过高,消耗加大,反而得不偿失PMMA/PC/PA类等塑料,温度升高粘度就显著下降,PS ABS升高温度对于降低粘度于成型亦有较大好处4. 剪切速度的影响有效的增加塑料的剪切速度可使塑料粘度下降,但有部分塑料,如PC亦有例外,其粘度几乎不受螺杆转速的影响。
5. 压力的影响压力对粘度的影响比较复杂,一般PP&PE类粘度受压力的影响不是很大,但对PS的影响却相当显著,实际生产中,在设备较完善的机器上,应注意发挥高速注射,即高剪切速度的作用,而不应盲目地将压力提高。
注射温度的控制对成型加工的影响所谓炮筒温度的控制是指塑料在料筒内如何从原料颗料一直均匀地被加热为塑性的粘流体,也就是料筒烤温如何配置的问题。
注塑成型工艺调整的操作规范

注塑工艺调整的操作规范1.目的为规范注塑工艺调整,确保模具安全,稳定产品品质和提高生产效率,特制定本规范。
2.范围:适用于各注塑部件成型工艺调整及设定。
3.职责:技术员,组长,工艺工程师对注塑工艺进行设定及调整,其他人员禁止调整成型工艺。
4.成型工艺设定方法4.1调机前准备工作。
4.1.1 依调度单通知加料工将原料加入烘箱并按要求进行烘干,并将螺杆清洗干净。
4.1.2 依照生产使用原料设定料管组温度并进行加热。
4.2 成型工艺设定方法及调整须知。
4.2.1 依据速度慢快慢的原则调整开合模,顶出压力及速度,保证开合模动作顺畅。
锁模压力以锁紧模具为原则,不影响产品品质,以最小为佳。
合理设置低压压力及低压保护时间.4.2.2 模具生产时按标准成型条件表设定相关工艺参数。
若模具首次生产,应参考模具中心提供之成型条件设定成型参数,并认真查看模具结构,根据流道及产品结构适当调整注射压力及速度,以避免产品粘模无法取出。
4.2.3 确认原料烘干到位及料管温度达设定温度,模具动作及结构无异常后,适当调整注射压力及速度,用半自动成型第1模产品,确认产品无重大结构及外观缺失后,继续调整至正常参数,产品初件送检合格后方可开机生产。
4.2.4 待成型条件稳定后,记录成型条件,连续生产1天以上,将最终成型条件提交,申请标准成型条件。
4.2.5 当机器或环境变异时,原来的标准成型条件不能满足生产要求时,改变标准成型条件,并将新的成型条件记录,稳定后升级为标准成型条件,与原条件一并保存。
4.2.6 正常生产时,注塑成型条件表或标准成型条件表必须挂在机台上的指定位置,订单完成换模时,班组长必须及时将成型条件放回文件夹内分类保管。
4.2.7 注塑机正常生产中,允许生产工艺参数与标准成型条件表上的参数有一定偏差:模温+/- 5℃料管温度+/-10 ℃时间+/- 0.5压力+/-10bar、速度+/-10%、位置+/-10 。
4.3调整须知:工艺调整超出标准成型条件允许范围时,需经主管批准,验证中成型条件及标准成型条件属于受控文件,检验人员对制程进行监控,禁止随意更改。
第43:注塑成型条件设定方法

第43问注塑成型条件设定方法一、开合模参数的设定方向:连续生产中,必须考虑工艺在今后生产中的稳定性,所以,开关模的参数设定必须保证开合模动作平稳设备不晃荡。
在产品取出方便的条件下,开关模位置越短越好。
低压保护设定,保证产品在模腔里合模起不到高压而报警,确保模具不会被压坏;高压锁模力最好设定低些,保证PL面不出披锋为止;设定太高,相反会有一定的坏处。
锁模力太高,易损坏模具;PL面排气不良,产品易困气烧焦;产品内应力大,出模后才可弃放;影响产品尺寸等。
具体的设定技巧:1.合模参数设定:以高压、慢速起步,短行程;中压、快速运行,导柱惯性到导套前;低压、匀速靠近腔面前;微压、低速惯性接触母模;高压、中速起高压合模。
有行位的模具,开模速度不可太快;2.开模参数设定:以高压、慢速离开母模;中压、快速运行惯性至终点前;高压、低速到开模终点。
3.低压保护位置与低压压力值的设定:接触模具的低压、低速设定必须能推动模具(特别是有弹簧或有行位的模具),但力量不能大于压坏产品的力(产品厚度被压至到原来的4/5所需要的力量);低压保护要调好,因为新模成品的形状与脱模情况不太了解;有抽蕊以及绞芽的模具,要先行手动试验,功能正常后方可用自动;4.高压锁模位置与高压锁模力的设定:高压位置设定方法。
(先不设定高压锁模力值,用前面设定的所有参数合模,模具会停在一个位置上,显示位置值将是实际的高压位置,在这位置上加上0.5㎜~1㎜就行)。
确认合模力是否充足:合模力(g)≥成形面投影面积(cm²)×模具内的平均压力(通常为400kg/cm²)。
合模力的大小计算可按《合模力设定方法》进行。
直压式机台需注意锁模力是否足够,肘节式机台注意十字头是否伸直,以防射出时模具后退,而出现大毛边涨坏模具;锁模力设定依据:最小锁模力=最高射出压力×(产品的投影面积+流道的投影面积);实际锁模力=最小锁模力×(1+5%~20%),再慢慢加到不出现毛边为止,闭模到30~50mm时,速度要转为慢速。
注塑工艺管理规定

注塑工艺管理规定引言概述:注塑工艺是一种通用的塑料加工方法,广泛应用于制造各种塑料产品。
为了确保注塑工艺的高效、稳定和可靠,注塑工艺管理规定起到了关键的作用。
本文将详细介绍注塑工艺管理规定的内容和要点。
正文内容:一、注塑工艺参数设置1.熔融温度控制:- 确定合适的熔融温度,以保证塑料材料完全熔化,并避免过热引起材料变质。
- 根据不同的塑料材料,设置相应的熔融温度范围。
- 定期检查和校准熔融温度控制装置,确保其准确性和稳定性。
2.注射速度控制:- 注射速度的控制对产品的质量和尺寸稳定性有着重要影响。
- 根据产品的形状和尺寸,选择合适的注射速度。
- 注意控制注射速度的变化范围,避免突变引起的质量问题。
3.注射压力控制:- 根据模具结构和塑料材料的特性,设置适当的注射压力。
- 注意控制注射压力的稳定性,以保证产品不会因为注射压力过高而产生翘曲或变形等问题。
4.冷却时间控制:- 合理的冷却时间是保证产品尺寸和性能稳定的关键。
- 根据产品的材料和形状,确定适当的冷却时间。
- 在生产过程中,及时调整冷却时间以适应环境温度和产品质量需求的变化。
5.模具温度控制:- 模具温度的控制对注塑工艺的稳定性和产品质量有重要影响。
- 根据塑料材料的熔融温度和产品要求,设置合适的模具温度。
- 定期检查和校准模具温度控制装置,确保其稳定性和准确性。
二、工艺优化与改进1.工艺优化:- 对于现有的注塑工艺,通过分析生产数据和实际情况,发现并解决工艺中存在的问题,以提高产品质量和生产效率。
- 运用工艺改进的方法,包括设计实验、模拟仿真和实际生产验证,逐步优化工艺参数。
2.材料优化:- 选择合适的塑料材料,根据产品要求进行材料的筛选和测试。
- 与材料供应商合作,了解不同塑料材料的性能特点和应用范围,选择最适合的材料。
3.模具优化:- 对于模具结构和设计存在的问题,进行优化和改进,以提高产品的尺寸稳定性和生产效率。
- 使用先进的模具制造技术,提高模具的加工精度和耐磨性。
注塑成型管理规范

注塑成型管理规范一、引言注塑成型是一种常见的塑料加工技术,广泛应用于各个行业。
为了确保注塑成型过程的质量和效率,制定一套科学的管理规范是非常重要的。
本文旨在提供一套注塑成型管理规范,以指导企业进行注塑成型工艺的优化和管理。
二、注塑成型工艺参数的设定1. 温度控制- 熔融温度:根据塑料材料的熔融指标和产品要求,确定合适的熔融温度范围。
- 注射温度:根据塑料材料的注射指标和产品要求,确定合适的注射温度范围。
- 模具温度:根据产品要求,确定合适的模具温度范围,以保证产品的质量和表面光洁度。
2. 压力控制- 注射压力:根据产品的尺寸、结构和塑料材料的流动性,确定合适的注射压力范围。
- 保压压力:根据产品的尺寸、结构和塑料材料的收缩性,确定合适的保压压力范围,以保证产品的尺寸稳定性和密度。
3. 注塑速度控制- 注射速度:根据产品的尺寸、结构和塑料材料的流动性,确定合适的注射速度范围。
- 保压速度:根据产品的尺寸、结构和塑料材料的收缩性,确定合适的保压速度范围,以保证产品的尺寸稳定性和密度。
4. 冷却时间控制- 模具冷却时间:根据产品的尺寸、结构和塑料材料的收缩性,确定合适的模具冷却时间,以保证产品的尺寸稳定性和表面质量。
三、注塑成型设备的维护与保养1. 注塑机的维护与保养- 定期检查注塑机的润滑系统,确保润滑油的充足和质量。
- 定期清洁注塑机的进料口、喷嘴和模具,防止杂质进入注塑机。
- 定期检查注塑机的电气系统,确保电源稳定和线路连接良好。
2. 模具的维护与保养- 定期清洗模具的表面,防止残留物影响产品的表面质量。
- 定期检查模具的冷却系统,确保冷却水的流通畅通。
- 定期检查模具的开合机构和导向系统,确保正常运行和定位准确。
3. 辅助设备的维护与保养- 定期清洗和更换冷却塔的冷却水,确保冷却效果良好。
- 定期检查和清洁热流道系统,确保热流道的流通畅通。
四、注塑成型品质控制1. 原材料控制- 严格选择符合产品要求的塑料原料,并建立供应商管理体系,确保原材料的质量稳定性。
注塑成型调校指引
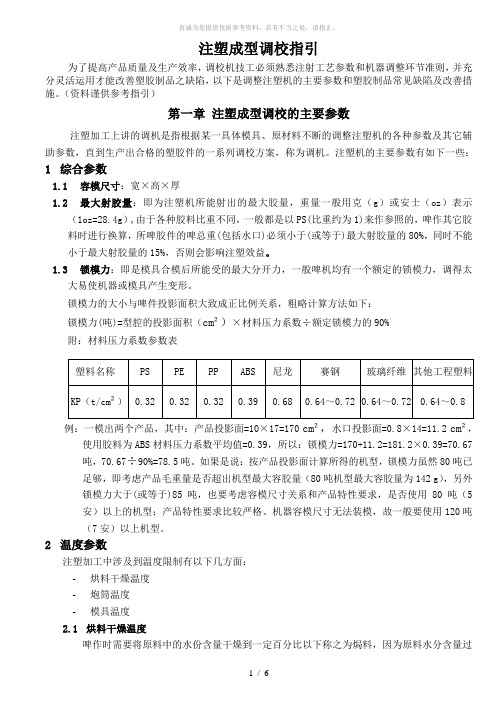
注塑成型调校指引为了提高产品质量及生产效率,调校机技工必须熟悉注射工艺参数和机器调整环节准则,并充分灵活运用才能改善塑胶制品之缺陷,以下是调整注塑机的主要参数和塑胶制品常见缺陷及改善措施。
(资料谨供参考指引)第一章注塑成型调校的主要参数注塑加工上讲的调机是指根据某一具体模具、原材料不断的调整注塑机的各种参数及其它辅助参数,直到生产出合格的塑胶件的一系列调校方案,称为调机。
注塑机的主要参数有如下一些:1综合参数1.1容模尺寸:宽×高×厚1.2最大射胶量:即为注塑机所能射出的最大胶量,重量一般用克(g)或安士(oz)表示(1oz=28.4g),由于各种胶料比重不同,一般都是以PS(比重约为1)来作参照的,啤作其它胶料时进行换算,所啤胶件的啤总重(包括水口)必须小于(或等于)最大射胶量的80%,同时不能小于最大射胶量的15%,否则会影响注塑效益。
1.3锁模力:即是模具合模后所能受的最大分开力,一般啤机均有一个额定的锁模力,调得太大易使机器或模具产生变形。
锁模力的大小与啤件投影面积大致成正比例关系,粗略计算方法如下:锁模力(吨)=型腔的投影面积(cm²)×材料压力系数÷额定锁模力的90%附:材料压力系数参数表例:一模出两个产品,其中:产品投影面=10×17=170cm²,水口投影面=0.8×14=11.2cm²,使用胶料为ABS材料压力系数平均值=0.39,所以:锁模力=170+11.2=181.2×0.39=70.67吨,70.67÷90%=78.5吨。
如果是说:按产品投影面计算所得的机型,锁模力虽然80吨已足够,即考虑产品毛重量是否超出机型最大容胶量(80吨机型最大容胶量为142 g),另外锁模力大于(或等于)85吨,也要考虑容模尺寸关系和产品特性要求,是否使用80吨(5安)以上的机型;产品特性要求比较严格、机器容模尺寸无法装模,故一般要使用120吨(7安)以上机型。
注塑成型工艺条件调试规定
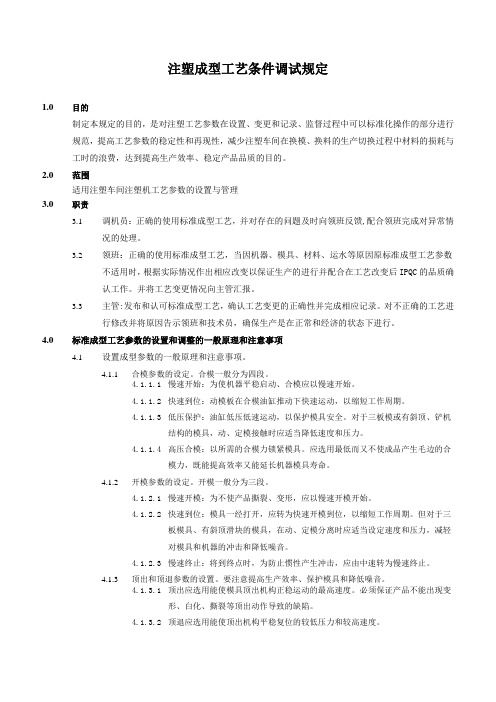
注塑成型工艺条件调试规定1.0目的制定本规定的目的,是对注塑工艺参数在设置、变更和记录、监督过程中可以标准化操作的部分进行规范,提高工艺参数的稳定性和再现性,减少注塑车间在换模、换料的生产切换过程中材料的损耗与工时的浪费,达到提高生产效率、稳定产品品质的目的。
2.0范围适用注塑车间注塑机工艺参数的设置与管理3.0职责3.1调机员:正确的使用标准成型工艺,并对存在的问题及时向领班反馈,配合领班完成对异常情况的处理。
3.2领班:正确的使用标准成型工艺,当因机器、模具、材料、运水等原因原标准成型工艺参数不适用时,根据实际情况作出相应改变以保证生产的进行并配合在工艺改变后IPQC的品质确认工作。
并将工艺变更情况向主管汇报。
3.3主管:发布和认可标准成型工艺,确认工艺变更的正确性并完成相应记录。
对不正确的工艺进行修改并将原因告示领班和技术员,确保生产是在正常和经济的状态下进行。
4.0标准成型工艺参数的设置和调整的一般原理和注意事项4.1设置成型参数的一般原理和注意事项。
4.1.1合模参数的设定。
合模一般分为四段。
4.1.1.1慢速开始:为使机器平稳启动、合模应以慢速开始。
4.1.1.2快速到位:动模板在合模油缸推动下快速运动,以缩短工作周期。
4.1.1.3低压保护:油缸低压低速运动,以保护模具安全。
对于三板模或有斜顶、铲机结构的模具,动、定模接触时应适当降低速度和压力。
4.1.1.4高压合模:以所需的合模力锁紧模具。
应选用最低而又不使成品产生毛边的合模力,既能提高效率又能延长机器模具寿命。
4.1.2开模参数的设定。
开模一般分为三段。
4.1.2.1慢速开模:为不使产品撕裂、变形,应以慢速开模开始。
4.1.2.2快速到位:模具一经打开,应转为快速开模到位,以缩短工作周期。
但对于三板模具、有斜顶滑块的模具,在动、定模分离时应适当设定速度和压力,减轻对模具和机器的冲击和降低噪音。
4.1.2.3慢速终止:将到终点时,为防止惯性产生冲击,应由中速转为慢速终止。
- 1、下载文档前请自行甄别文档内容的完整性,平台不提供额外的编辑、内容补充、找答案等附加服务。
- 2、"仅部分预览"的文档,不可在线预览部分如存在完整性等问题,可反馈申请退款(可完整预览的文档不适用该条件!)。
- 3、如文档侵犯您的权益,请联系客服反馈,我们会尽快为您处理(人工客服工作时间:9:00-18:30)。
注塑成型工艺条件调试规定
1.0目的
制定本规定的目的,是对注塑工艺参数在设置、变更和记录、监督过程中可以标准化操作的部分进行规范,提高工艺参数的稳定性和再现性,减少注塑车间在换模、换料的生产切换过程中材料的损耗与工时的浪费,达到提高生产效率、稳定产品品质的目的。
2.0范围
适用注塑车间注塑机工艺参数的设置与管理
3.0职责
3.1调机员:正确的使用标准成型工艺,并对存在的问题及时向领班反馈,配合领班完成对异常情
况的处理。
3.2领班:正确的使用标准成型工艺,当因机器、模具、材料、运水等原因原标准成型工艺参数
不适用时,根据实际情况作出相应改变以保证生产的进行并配合在工艺改变后IPQC的品质确
认工作。
并将工艺变更情况向主管汇报。
3.3主管:发布和认可标准成型工艺,确认工艺变更的正确性并完成相应记录。
对不正确的工艺进
行修改并将原因告示领班和技术员,确保生产是在正常和经济的状态下进行。
4.0标准成型工艺参数的设置和调整的一般原理和注意事项
4.1设置成型参数的一般原理和注意事项。
4.1.1合模参数的设定。
合模一般分为四段。
4.1.1.1慢速开始:为使机器平稳启动、合模应以慢速开始。
4.1.1.2快速到位:动模板在合模油缸推动下快速运动,以缩短工作周期。
4.1.1.3低压保护:油缸低压低速运动,以保护模具安全。
对于三板模或有斜顶、铲机
结构的模具,动、定模接触时应适当降低速度和压力。
4.1.1.4高压合模:以所需的合模力锁紧模具。
应选用最低而又不使成品产生毛边的合
模力,既能提高效率又能延长机器模具寿命。
4.1.2开模参数的设定。
开模一般分为三段。
4.1.2.1慢速开模:为不使产品撕裂、变形,应以慢速开模开始。
4.1.2.2快速到位:模具一经打开,应转为快速开模到位,以缩短工作周期。
但对于三
板模具、有斜顶滑块的模具,在动、定模分离时应适当设定速度和压力,减轻
对模具和机器的冲击和降低噪音。
4.1.2.3慢速终止:将到终点时,为防止惯性产生冲击,应由中速转为慢速终止。
4.1.3顶出和顶退参数的设置。
要注意提高生产效率、保护模具和降低噪音。
4.1.3.1顶出应选用能使模具顶出机构正稳运动的最高速度。
必须保证产品不能出现变
形、白化、撕裂等顶出动作导致的缺陷。
4.1.3.2顶退应选用能使顶出机构平稳复位的较低压力和较高速度。
4.1.4熔胶温度的设置。
熔胶温度通常包括料筒温度和热流道温度两部分。
4.1.4.1熔胶温度设定的范围,应当高于塑料的熔点或软化温度,低于塑料的分解温度。
4.1.4.2需注意设定温度与实际温度之间的差异。
必要时可通过目视检查塑料的熔融状
态或热电偶温度计检查。
4.1.5计量、背压和熔胶速度。
在塑料熔融、塑化过程中,熔料不断移向料筒前端(计量室内),
且越来越多,逐渐形成一个压力,推动螺杆向后退。
为了阻止螺杆后退过快,确保熔料均匀压实,需要给螺杆提供一个反方向的压力,这个反方向阻止螺杆后退的压力称背压。
螺杆的转速即为熔胶速度。
螺杆后移的距离即为计量。
4.1.
5.1注塑机不用于加工小于其注塑容量10%或大于其注塑容量70%的产品;
4.1.
5.2熔胶压力和熔胶速度要设置恰当,计量时间(熔胶时间)不大于最短冷却周期。
4.1.6填充参数的设置。
在高压合模完成后开始,注射油缸推动螺杆前进,把螺杆前熔融的塑料
注入模腔。
在保证成品没有气痕、烧焦等缺陷的前提下,应尽可能提高填充速度。
4.1.6.1必须采用多级注射工艺。
操作上以三级注塑工艺设置为基础,需要时设置为四
级、五级或更多级别的填充工艺。
4.1.6.2三级填充的设置要领为:第一级低速通过浇口,消除膨大效应和熔体破裂导致
的缺陷,第二级快速,提高生产效率;第三级低速,避免因模具排气不良导致
的缺陷。
操作中需根据实际情况灵活调整。
4.1.7保压参数的设置。
模腔填充完毕,熔体停止高速流动遇冷收缩定型。
保压的作用是保持一
定的压力将熔体经过尚未凝固的浇口不断填充冷却定型时材料体积收缩形成的凹陷或空
洞,使成品脱模时饱满。
4.1.7.1保压亦可分为多级设置不同级别的保压压力和保压时间。
通过目视检查或尺寸
测量成品来衡量保压设置是否合适。
4.1.7.2使用高分度电子秤称量成品重量。
在保压压力一定按1或0.5秒间隔递增设置
保压时间,或保压时间一定按10%或5%间隔递增设置保压压力。
通过测量每个
参数的成品平均重量,可评估最佳保压压力和保压时间的设置值。
该方法也可
用于评估保压速度的设置。
4.1.7.3薄壁产品填充完毕即已凝固,可不用保压。
4.1.8填充/保压切换模式。
熔体填充模腔完毕停止快速流动即进入收缩定型阶段。
注塑机注射
系统由填充却换为保压的模式通常有四种:位置/时间切换模式、时间切换模式、压力切
换模式、位置切换模式。
4.1.8.1必须优先使用“位置/时间”切换模式。
4.1.8.2“位置/时间”切换模式下,最佳位置参数的设置要领是:寻找产品投影面填充
完成99%~100%,产品重量填充到95%~99%的位置点,在该位置连续成型3~5模
产品,如果成型出来的产品重量稳定,该位置就是最佳切换位置。
4.1.9冷却时间:指模腔内成品冷却定型所需要的时间,从保压结束开始计算到模具开模为止结
束。
在满足以下两点要求时应设置最短冷却时间以提高生产效率:
4.1.9.1必须需保证产品脱模、取出顺利,没有白化、顶高、变形,产品能满足测量、试
装需求。
4.1.9.2必须保证模具温度稳定,能连续生产。
4.1.10模具冷却系统的温度控制。
熔融态的塑料被高压注入模腔,在模腔内释放热量冷却到热变
形温度以下固化成型。
该过程是由熔料和模具的温差实现的。
由于不同的成型材料要求不
同的模具温度(模具温度应低于塑件热变形温度),若模腔表面温度异常,都会影响塑件
的变形、尺寸精度、力学性能和外观等质量指标,以及影响生产效率。
模具的常用冷却介
质是水和油,介质流动的通道通常叫“水道”、“水路”、“运水”。
常用制冷设备是水
塔和恒温机(加热或制冷)
4.1.10.1在串联或并联模具水路和制冷设备时,要注意均匀有效。
均匀是进出水管的方
向和位置要搭配恰当使模具能均匀散热;有效是指尽少串联水路,尽量避免因
一点受阻影响整组串联水路。
下图示意了3路运水的不同联接方式,其右边优
于左边,下边的优于上边。
(水路连接示意图)
4.1.10.2对于特殊产品或特殊模具,可通过局部制冷或局部加温实现生产目的。
4.2注塑成型工艺参数的管理流程。
4.2.1试产工艺参数的设置与标准化。
4.2.1.1试产时,调机员、领班需根据材料、模具、产品、机器的特点,设置相应的工
艺参数。
参数内容需符合“使用多级注射工艺”和“优先选用位置/时间切换模
式”两项原则。
所成型的产品满足品质要求,且维持较低的工艺不良率。
4.2.1.2试产结束时,调机员、领班填写《注塑成型工艺参数表》,并附上完整的走胶
板、完整的成型样板(含水口),一并交主管审核。
审核后发行的参数即为“S”
版参数,供后续试产或量产参考。
4.2.2量产工艺参数的设置。
4.2.2.1在开机前,技术员、领班按照工艺参表数据输入参数,并确认模具水路连接是
否正确,阀门是否打开。
4.2.2.2将保压时间设置为“0”,开机成型3~5模产品,检查保压切换位置是否偏移。
若出现偏移,微调直至找准切换点,然后输入参数表记录的保压时间。
4.2.2.3产品经自检合格,在成型5模产品后,取1模产品送IPQC做首件检查。
根据IPQC
反馈对参数微调,直到首件检查合格方可开机生产。
4.2.3标准成型参数的微调原则。
《注塑成型工艺参数表》记录的数据大体分为两部分内容。
一部分是与模具开合、顶针进退等辅助动作有关的,主要影响生产效率;第二部分是与温度、射出、保压有关的参数,与产品品质密切相关。
4.2.3.1对第一部分主要影响生产效率的参数,在调整上以符合一般操作要求和不影响
生产效率为准绳。
4.2.3.2第二部分参数的调整要求参照下面表格。
对于已经通过首件检验的产品,工艺
参数即使在表格允许范围内调整,也必须通知IPQC。
4.2.4临时成型工艺参数的设置。
由于机器、模具、材料、辅助设备故障、设计变更等原因,导致按标准工艺参数生产的产品无法满足品质要求,或制程中产品出现超过5%的工艺不良,技术员、领班有义务设置
临时成型工艺参数对成型工艺进行改进,确保生产顺利进行。
4.2.4.1在只能使用临时工艺参数生产产品时需将情况告知主管。
主管需主持调查变异
的原因并提出纠正预防措施。
4.2.4.2临时工艺参数若属于对原有工艺的改进与补充,参照本节第一条试产参数管理,
发行新的标准工艺参数。