汽车轮毂用高强韧铝合金的成型与控制
《7A04高强铝合金轮毂锻造成形工艺研究》
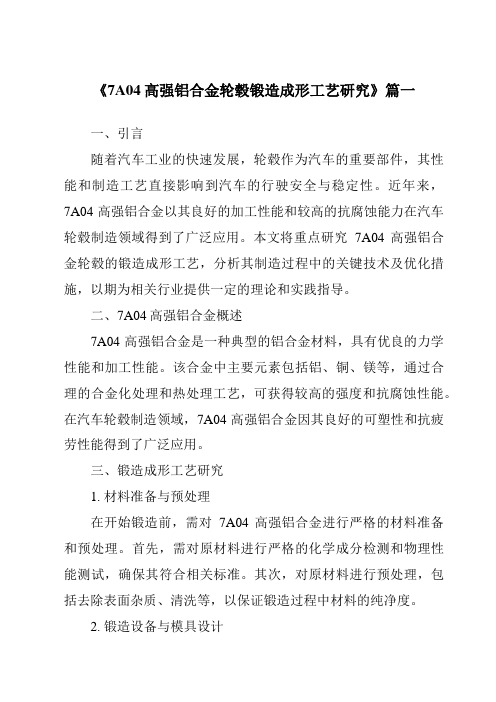
《7A04高强铝合金轮毂锻造成形工艺研究》篇一一、引言随着汽车工业的快速发展,轮毂作为汽车的重要部件,其性能和制造工艺直接影响到汽车的行驶安全与稳定性。
近年来,7A04高强铝合金以其良好的加工性能和较高的抗腐蚀能力在汽车轮毂制造领域得到了广泛应用。
本文将重点研究7A04高强铝合金轮毂的锻造成形工艺,分析其制造过程中的关键技术及优化措施,以期为相关行业提供一定的理论和实践指导。
二、7A04高强铝合金概述7A04高强铝合金是一种典型的铝合金材料,具有优良的力学性能和加工性能。
该合金中主要元素包括铝、铜、镁等,通过合理的合金化处理和热处理工艺,可获得较高的强度和抗腐蚀性能。
在汽车轮毂制造领域,7A04高强铝合金因其良好的可塑性和抗疲劳性能得到了广泛应用。
三、锻造成形工艺研究1. 材料准备与预处理在开始锻造前,需对7A04高强铝合金进行严格的材料准备和预处理。
首先,需对原材料进行严格的化学成分检测和物理性能测试,确保其符合相关标准。
其次,对原材料进行预处理,包括去除表面杂质、清洗等,以保证锻造过程中材料的纯净度。
2. 锻造设备与模具设计选择合适的锻造设备和模具是锻造成形工艺的关键。
根据轮毂的形状和尺寸要求,设计合理的模具结构,确保在锻造过程中能够获得理想的轮毂形状和尺寸精度。
同时,选择合适的锻造设备,如液压机、机械压力机等,以满足轮毂锻造过程中的压力和温度要求。
3. 锻造过程与控制在锻造过程中,需严格控制温度、压力和时间等参数。
首先,将预处理后的材料加热至适当的温度范围,以降低材料的塑性变形抗力。
其次,在设定的压力下进行锻造,通过多次锻打和整形,使材料逐渐成形为所需的轮毂形状。
最后,对锻造过程中的温度、压力和时间进行实时监控和调整,以确保轮毂的成形质量和性能。
四、关键技术及优化措施1. 合金成分优化通过对7A04高强铝合金的合金成分进行优化,可以进一步提高其力学性能和抗腐蚀性能。
通过调整合金中各元素的含量比例,以及采用先进的合金化处理技术,可以提高材料的强度、硬度、延展性和抗疲劳性能。
《汽车用高强韧类高真空压铸铝合金材料技术条件》-编制说明
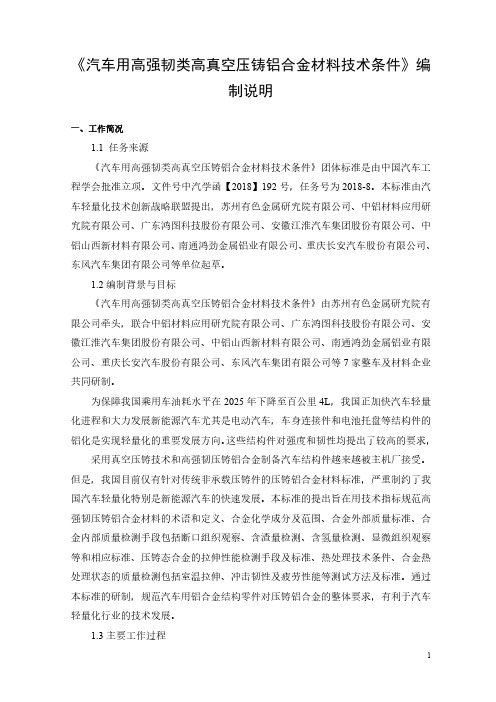
《汽车用高强韧类高真空压铸铝合金材料技术条件》编制说明一、工作简况1.1任务来源《汽车用高强韧类高真空压铸铝合金材料技术条件》团体标准是由中国汽车工程学会批准立项。
文件号中汽学函【2018】192号,任务号为2018-8。
本标准由汽车轻量化技术创新战略联盟提出,苏州有色金属研究院有限公司、中铝材料应用研究院有限公司、广东鸿图科技股份有限公司、安徽江淮汽车集团股份有限公司、中铝山西新材料有限公司、南通鸿劲金属铝业有限公司、重庆长安汽车股份有限公司、东风汽车集团有限公司等单位起草。
1.2编制背景与目标《汽车用高强韧类高真空压铸铝合金材料技术条件》由苏州有色金属研究院有限公司牵头,联合中铝材料应用研究院有限公司、广东鸿图科技股份有限公司、安徽江淮汽车集团股份有限公司、中铝山西新材料有限公司、南通鸿劲金属铝业有限公司、重庆长安汽车股份有限公司、东风汽车集团有限公司等7家整车及材料企业共同研制。
为保障我国乘用车油耗水平在2025年下降至百公里4L,我国正加快汽车轻量化进程和大力发展新能源汽车尤其是电动汽车,车身连接件和电池托盘等结构件的铝化是实现轻量化的重要发展方向。
这些结构件对强度和韧性均提出了较高的要求,采用真空压铸技术和高强韧压铸铝合金制备汽车结构件越来越被主机厂接受。
但是,我国目前仅有针对传统非承载压铸件的压铸铝合金材料标准,严重制约了我国汽车轻量化特别是新能源汽车的快速发展。
本标准的提出旨在用技术指标规范高强韧压铸铝合金材料的术语和定义、合金化学成分及范围、合金外部质量标准、合金内部质量检测手段包括断口组织观察、含渣量检测、含氢量检测、显微组织观察等和相应标准、压铸态合金的拉伸性能检测手段及标准、热处理技术条件、合金热处理状态的质量检测包括室温拉伸、冲击韧性及疲劳性能等测试方法及标准。
通过本标准的研制,规范汽车用铝合金结构零件对压铸铝合金的整体要求,有利于汽车轻量化行业的技术发展。
1.3主要工作过程本标准于2017年3月开始标准学习;2017年4月到2018年4月份进行了标准相关的试验和数据收集工作;2018年5月15日,苏州有色金属研究院有限公司对本标准的任务来源、技术内容、编制说明等进行了简要介绍,并宣布成立标准起草组。
汽车轮毂用高强韧A356铝合金的成型与控制
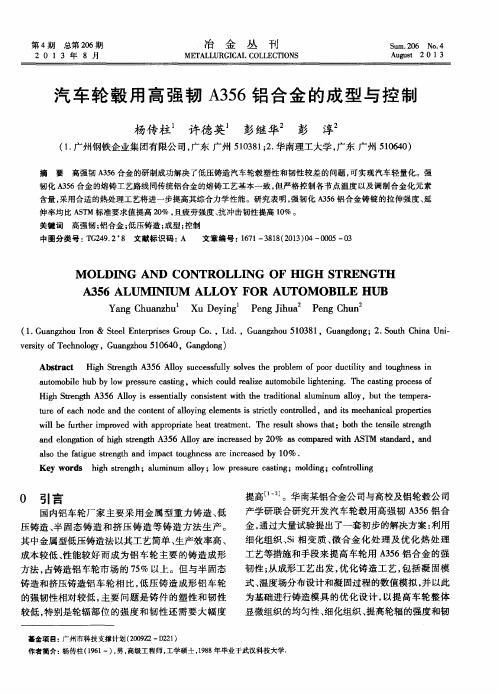
韧化 A 3 5 6合 金的熔铸工艺路线 同传统 铝合 金的熔铸工艺基本 一致 , 但严格控 制各节 点温度 以及调制 合金化 元素 含量, 采用合适 的热处 理工艺将进一 步提高其综合力学性 能。研究 表明 , 强韧化 A 3 5 6铝 合金铸 锭 的拉 伸强度 、 延 伸率均 比 A S T M 标准要求值提高 2 0 %, 且疲劳强度 、 抗 冲击韧性提高 1 0 %。 关键词 高强韧 ; 铝合金 ; 低 压铸 造 ; 成型; 控制 文章编号 :1 6 7 1 —3 8 1 8 ( 2 0 1 3 ) 0 4— 0 o 0 5—0 3 中图分类号 : T G 2 4 9 . 2 8 文献标 识码 :A
随这些元 素 的氧化 程度增 加 。理想 的投入 和溶 解温 度应 控制 在 7 3 0~ 7 5 0℃ 之 间 , 并 用钟 罩将 中 间合金
压人熔体 中搅拌。
1 . 3 精 炼温 度
处理成型的工艺与控制过程 , 分析实验结果 。
采用惰性气体和精炼除杂剂。在除气和除杂过 程中 , 高温有利于降低熔体粘度 , 降低气 、 杂上浮阻 力; 但高温同时促进熔体吸气和高活性合金元素的
素反应。理想的精炼温度控制在 7 0 0~ 7 3 0℃之问。
I 塑 堡 竺 I
烹
1 . 4 浇铸温 度
表面撒上 覆盖剂
同传统 A l — s i 合金一样 , 浇铸温度控制为7 2 0~
7 5 0 o C。
加入S i 、Mg 等主要合金元素
加入中间合金, 调制 熔体中 合金元素含量
控制在 7 0 0 — 7 2 0℃ , 待硅料熔化并搅拌均匀后 , 降
低熔 体 温度 至 6 8 0— 7 0 0℃, 投入纯镁料 , 表 面覆 盖 防止 Mg 元 素氧化 的覆 盖溶 剂 。
汽车轮毂用A356铝合金合金化的研究进展
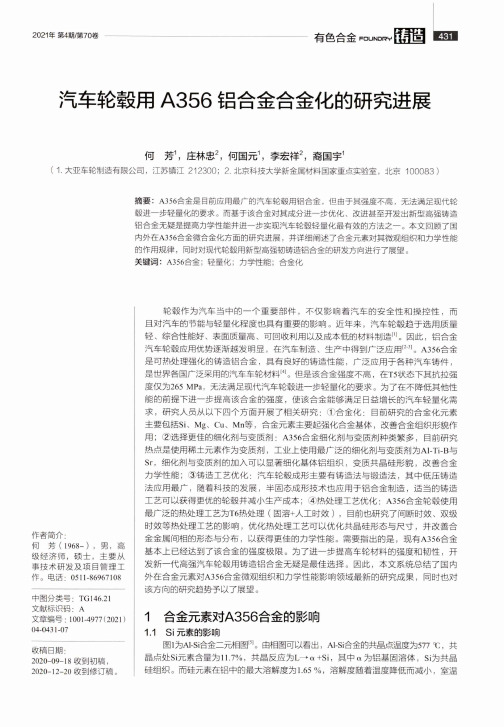
2021年第4期/第70卷有色合金im431汽车轮毂用A356铝合金合金化的研究进展何芳1,庄林忠2,何国元1,李宏祥2,裔国宇1(1.大亚车轮制造有限公司,江苏镇江212300; 2.北京科技大学新金属材料国家重点实验室,北京100083)摘要:A356合金是目前应用最广的汽车轮毂用铝合金,但由于其强度不高,无法满足现代轮毂进一步轻量化的要求。
而基于该合金对其成分进一步优化、改进甚至开发出新型高强铸造铝合金无疑是提高力学性能并进一步实现汽车轮毂轻量化最有效的方法之一。
本文回顾了国内外在A356合金微合金化方面的研究进展,并详细阐述了合金元素对其微观组织和力学性能的作用规律,同时对现代轮毂用新型高强韧铸造铝合金的研发方向进行了展望。
关键词:A356合金;轻量化;力学性能;合金化作者简介:何芳(1968-),男,高 级经济师,硕士,主要从 事技术研发及项目管理工 作。
电话:*************中图分类号:TG146.21文献标识码: A文章编号:1001*4977(2021)轮毂作为汽车当中的一个重要部件,不仅影响着汽车的安全性和操控性,而 且对汽车的节能与轻量化程度也具有重要的影响。
近年来,汽车轮毂趋于选用质量 轻、综合性能好、表面质量高、可回收利用以及成本低的材料制造[1]。
因此,铝合金 汽车轮毂应用优势逐渐越发明显,在汽车制造、生产中得到广泛应用[M]。
A356合金 是可热处理强化的铸造铝合金,具有良好的铸造性能,广泛应用于各种汽车铸件,是世界各国广泛采用的汽车车轮材料[〜。
但是该合金强度不高,在T5状态下其抗拉强 度仅为265 MPa,无法满足现代汽车轮毂进一步轻量化的要求。
为了在不降低其他性 能的前提下进一步提高该合金的强度,使该合金能够满足日益增长的汽车轻量化需 求,研究人员从以下四个方面开展了相关研究:①合金化:目前研究的合金化元素 主要包括Si、Mg、Cu、Mn等,合金元素主要起强化合金基体,改善合金组织形貌作 用;②选择更佳的细化剂与变质剂:A356合金细化剂与变质剂种类繁多,目前研究 热点是使用稀土元素作为变质剂,工业上使用最广泛的细化剂与变质剂为Al-Ti-B与 Sr,细化剂与变质剂的加入可以显著细化基体铝组织,变质共晶硅形貌,改善合金 力学性能;③铸造工艺优化:汽车轮毂成形主要有铸造法与锻造法,其中低压铸造 法应用最广,随着科技的发展,半固态成形技术也应用于铝合金制造,适当的铸造 工艺可以获得更优的轮毂并减小生产成本;④热处理工艺优化:A356合金轮毂使用 最广泛的热处理工艺为T6热处理(固溶+人工时效),目前也研究了间断时效、双级 时效等热处理工艺的影响,优化热处理工艺可以优化共晶硅形态与尺寸,并改善合 金金属间相的形态与分布,以获得更佳的力学性能。
《7A04高强铝合金轮毂锻造成形工艺研究》

《7A04高强铝合金轮毂锻造成形工艺研究》篇一一、引言随着汽车工业的快速发展,轮毂作为汽车的重要部件,其性能和制造工艺日益受到关注。
7A04高强铝合金因其优良的机械性能和抗腐蚀性能,在轮毂制造中得到了广泛应用。
本文旨在研究7A04高强铝合金轮毂的锻造成形工艺,探讨其工艺流程、参数优化及性能分析,以期为轮毂制造提供理论支持和工艺指导。
二、材料与设备本研究所用材料为7A04高强铝合金,主要设备包括锻压机、加热炉、模具等。
在锻造过程中,需对材料进行预热和热处理,以保证其可锻性和成形质量。
三、锻造成形工艺1. 工艺流程7A04高强铝合金轮毂的锻造成形工艺流程主要包括材料准备、加热、预处理、锻造、热处理和检验等步骤。
首先,将原材料进行预处理,包括清洗、除锈等;然后进行加热,使材料达到适当的锻造温度;接着进行预处理,如镦粗、挤压等,以改善材料的可锻性;随后进行锻造,通过模具将材料锻造成轮毂形状;最后进行热处理和检验,以提高轮毂的性能和质量。
2. 参数优化在锻造过程中,需要优化多个工艺参数,包括加热温度、锻造速度、模具温度等。
加热温度过高或过低都会影响材料的可锻性和成形质量,因此需严格控制加热温度。
此外,合理的锻造速度和模具温度也是保证轮毂成形质量和性能的关键因素。
在优化参数的过程中,需进行多次试验,以确定最佳工艺参数组合。
四、性能分析通过对7A04高强铝合金轮毂的锻造成形工艺进行研究,我们发现优化后的工艺参数组合可以显著提高轮毂的性能。
具体表现在以下几个方面:1. 机械性能:优化后的轮毂具有较高的抗拉强度和屈服强度,能够满足汽车行驶过程中的各种工况需求。
2. 抗腐蚀性能:7A04高强铝合金具有良好的抗腐蚀性能,经过优化后的轮毂能够更好地抵抗环境腐蚀,延长使用寿命。
3. 尺寸精度:通过精确控制锻造工艺参数,可以保证轮毂的尺寸精度和形状精度,满足装配要求。
五、结论本研究通过对7A04高强铝合金轮毂的锻造成形工艺进行研究,得出以下结论:1. 优化后的7A04高强铝合金轮毂锻造成形工艺可以提高轮毂的机械性能、抗腐蚀性能和尺寸精度,满足汽车行驶过程中的各种需求。
铝合金车轮的制造工艺

铝合金车轮的制造工艺1. 引言铝合金车轮是现代汽车中常见的一种重要零部件,具有重量轻、强度高、耐腐蚀等优点。
本文将介绍铝合金车轮的制造工艺,包括原材料选择、铸造、加工和表面处理等方面。
2. 原材料选择在铝合金车轮的制造过程中,原材料的选择对提高车轮性能至关重要。
常用的铝合金材料包括A356、A357和A356.2三种。
这些材料具有良好的机械性能、气密性和耐腐蚀性,能够满足车轮在使用中的要求。
3. 铸造过程铝合金车轮的铸造过程主要包括模具制作、熔炼铝合金、浇注和冷却等步骤。
3.1 模具制作模具是铝合金车轮的铸造过程中的重要工具。
模具的制作需要根据车轮的设计要求进行。
常用的模具材料有砂型、金属型和永久型等。
3.2 熔炼铝合金选定合适的铝合金材料后,需将其熔炼成液态铝合金。
熔炼可以采用电炉或气炉等方式进行,确保铝合金达到熔点后,进行下一步的浇注。
3.3 浇注和冷却将熔融的铝合金倒入模具中,使其充满整个模腔。
然后,通过冷却过程将铝合金逐渐凝固,形成车轮的基本形状。
冷却的时间和方式需要根据车轮的结构和尺寸来确定。
4. 加工过程在铝合金车轮的制造过程中,通常还需要进行一些加工工序,以达到车轮的精度和平衡性要求。
4.1 车轮机械加工车轮的外观和尺寸要求通常需要进行车削、铣削、钻孔等机械加工工序。
这些加工工序旨在调整车轮的形状和尺寸,使其满足设计要求。
4.2 热处理为提高车轮的力学性能和微观结构,通常需要进行热处理工艺,如时效处理和淬火等。
热处理可以改善车轮的硬度、强度和耐磨性等性能。
4.3 动平衡车轮在运行过程中需要保持良好的平衡性能,以提高行驶稳定性和舒适性。
通过动平衡机检测和调整车轮的平衡性,确保车轮在高速旋转时不会产生震动和噪音。
5. 表面处理铝合金车轮经过铸造和加工后,还需要进行表面处理,以提高车轮的耐腐蚀性和外观质量。
5.1 喷砂除氧化皮车轮表面经过一定时间的氧化,会形成氧化皮。
喷砂工艺可以将氧化皮除去,恢复铝合金表面原有的光亮度。
超高强含铝中锰钢的强韧化机制及组织调控
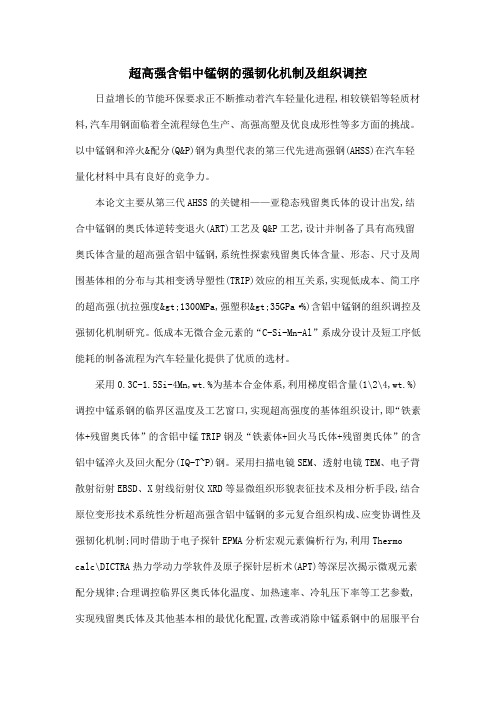
超高强含铝中锰钢的强韧化机制及组织调控日益增长的节能环保要求正不断推动着汽车轻量化进程,相较镁铝等轻质材料,汽车用钢面临着全流程绿色生产、高强高塑及优良成形性等多方面的挑战。
以中锰钢和淬火&配分(Q&P)钢为典型代表的第三代先进高强钢(AHSS)在汽车轻量化材料中具有良好的竞争力。
本论文主要从第三代AHSS的关键相——亚稳态残留奥氏体的设计出发,结合中锰钢的奥氏体逆转变退火(ART)工艺及Q&P工艺,设计并制备了具有高残留奥氏体含量的超高强含铝中锰钢,系统性探索残留奥氏体含量、形态、尺寸及周围基体相的分布与其相变诱导塑性(TRIP)效应的相互关系,实现低成本、简工序的超高强(抗拉强度>1300MPa,强塑积>35GPa·%)含铝中锰钢的组织调控及强韧化机制研究。
低成本无微合金元素的“C-Si-Mn-Al”系成分设计及短工序低能耗的制备流程为汽车轻量化提供了优质的选材。
采用0.3C-1.5Si-4Mn,wt.%为基本合金体系,利用梯度铝含量(1\2\4,wt.%)调控中锰系钢的临界区温度及工艺窗口,实现超高强度的基体组织设计,即“铁素体+残留奥氏体”的含铝中锰TRIP钢及“铁素体+回火马氏体+残留奥氏体”的含铝中锰淬火及回火配分(IQ-T~P)钢。
采用扫描电镜SEM、透射电镜TEM、电子背散射衍射EBSD、X射线衍射仪XRD等显微组织形貌表征技术及相分析手段,结合原位变形技术系统性分析超高强含铝中锰钢的多元复合组织构成、应变协调性及强韧化机制;同时借助于电子探针EPMA分析宏观元素偏析行为,利用Thermo calc\DICTRA热力学动力学软件及原子探针层析术(APT)等深层次揭示微观元素配分规律;合理调控临界区奥氏体化温度、加热速率、冷轧压下率等工艺参数,实现残留奥氏体及其他基本相的最优化配置,改善或消除中锰系钢中的屈服平台及PLC塑性失稳现象。
汽车轮毂用高强韧A356铝合金的成型与控制
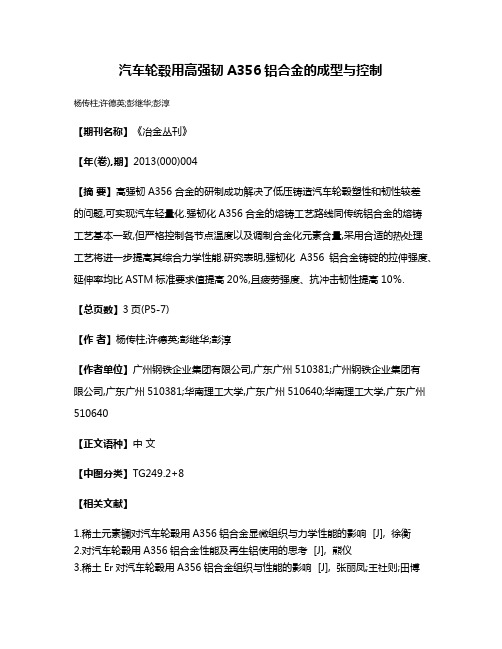
汽车轮毂用高强韧A356铝合金的成型与控制
杨传柱;许德英;彭继华;彭淳
【期刊名称】《冶金丛刊》
【年(卷),期】2013(000)004
【摘要】高强韧A356合金的研制成功解决了低压铸造汽车轮毂塑性和韧性较差
的问题,可实现汽车轻量化.强韧化A356合金的熔铸工艺路线同传统铝合金的熔铸
工艺基本一致,但严格控制各节点温度以及调制合金化元素含量,采用合适的热处理
工艺将进一步提高其综合力学性能.研究表明,强韧化A356铝合金铸锭的拉伸强度、延伸率均比ASTM标准要求值提高20%,且疲劳强度、抗冲击韧性提高10%.
【总页数】3页(P5-7)
【作者】杨传柱;许德英;彭继华;彭淳
【作者单位】广州钢铁企业集团有限公司,广东广州510381;广州钢铁企业集团有
限公司,广东广州510381;华南理工大学,广东广州510640;华南理工大学,广东广州510640
【正文语种】中文
【中图分类】TG249.2+8
【相关文献】
1.稀土元素镧对汽车轮毂用A356铝合金显微组织与力学性能的影响 [J], 徐衡
2.对汽车轮毂用A356铝合金性能及再生铝使用的思考 [J], 熊仪
3.稀土Er对汽车轮毂用A356铝合金组织与性能的影响 [J], 张丽凤;王社则;田博
彤
4.汽车轮毂用A356铝合金合金化的研究进展 [J], 何芳;庄林忠;何国元;李宏祥;裔国宇
5.汽车轮毂用A356铝合金特点 [J], 毛协民
因版权原因,仅展示原文概要,查看原文内容请购买。
《7A04高强铝合金轮毂锻造成形工艺研究》范文

《7A04高强铝合金轮毂锻造成形工艺研究》篇一一、引言随着汽车工业的快速发展,轮毂作为汽车的重要部件,其性能和制造工艺日益受到关注。
7A04高强铝合金因其优良的机械性能和抗腐蚀性能,被广泛应用于汽车轮毂的制造。
本文旨在研究7A04高强铝合金轮毂的锻造成形工艺,以提高轮毂的制造质量和生产效率。
二、7A04高强铝合金概述7A04高强铝合金是一种铝-锌-镁系合金,具有较高的强度、良好的塑性和抗腐蚀性能。
其优良的机械性能使其成为制造汽车轮毂的理想材料。
然而,7A04高强铝合金的加工难度较大,需要采用合适的锻造成形工艺。
三、锻造成形工艺研究1. 材料准备首先,选择合适的7A04高强铝合金原材料,并进行严格的质检,确保原材料的质量符合要求。
然后,对原材料进行预处理,包括除锈、清洗和预热等步骤,以提高材料的可锻性。
2. 锻造设备与工艺参数选择合适的锻造设备,如液压锻造机或机械锻造机,并根据材料特性和产品要求设置合适的工艺参数,如锻造温度、锻造速度和锻造压力等。
这些参数将直接影响轮毂的成形质量和生产效率。
3. 锻造过程在锻造过程中,首先将7A04高强铝合金加热至预定温度,然后进行预锻造,以消除材料的内部应力。
接着进行主锻造,通过多次锻打和整形,使材料达到所需的形状和尺寸。
最后进行终锻造,完成轮毂的最终成形。
4. 后处理工艺锻造完成后,对轮毂进行后处理工艺,包括淬火、回火和表面处理等步骤。
这些后处理工艺可以提高轮毂的机械性能和抗腐蚀性能,同时改善其表面质量。
四、研究结果与分析通过研究7A04高强铝合金轮毂的锻造成形工艺,我们得到了以下结果:1. 合适的锻造温度和速度可以提高材料的可锻性,降低锻造过程中的能量消耗。
2. 通过合理的预锻造、主锻造和终锻造过程,可以得到形状和尺寸符合要求的轮毂。
3. 后处理工艺可以显著提高轮毂的机械性能和抗腐蚀性能,同时改善其表面质量。
五、结论本文研究了7A04高强铝合金轮毂的锻造成形工艺,通过合适的材料准备、锻造设备和工艺参数以及后处理工艺,可以得到符合要求的轮毂。
超高强铝合金铸造技术及装备控制系统的发展
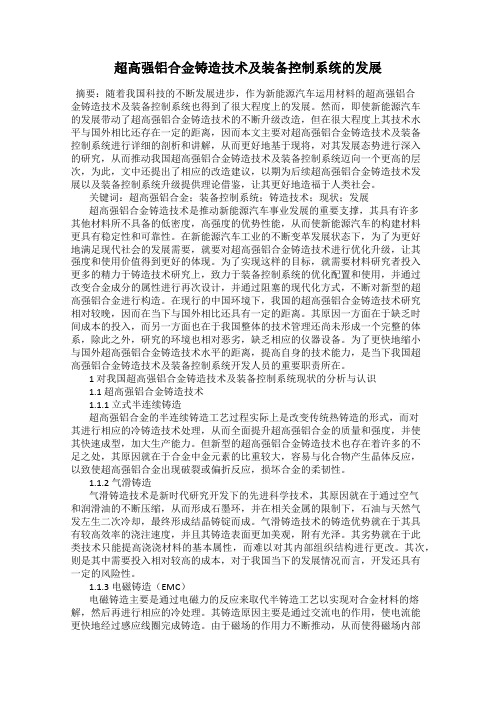
超高强铝合金铸造技术及装备控制系统的发展摘要:随着我国科技的不断发展进步,作为新能源汽车运用材料的超高强铝合金铸造技术及装备控制系统也得到了很大程度上的发展。
然而,即使新能源汽车的发展带动了超高强铝合金铸造技术的不断升级改造,但在很大程度上其技术水平与国外相比还存在一定的距离,因而本文主要对超高强铝合金铸造技术及装备控制系统进行详细的剖析和讲解,从而更好地基于现将,对其发展态势进行深入的研究,从而推动我国超高强铝合金铸造技术及装备控制系统迈向一个更高的层次,为此,文中还提出了相应的改造建议,以期为后续超高强铝合金铸造技术发展以及装备控制系统升级提供理论借鉴,让其更好地造福于人类社会。
关键词:超高强铝合金;装备控制系统;铸造技术;现状;发展超高强铝合金铸造技术是推动新能源汽车事业发展的重要支撑,其具有许多其他材料所不具备的低密度,高强度的优势性能,从而使新能源汽车的构建材料更具有稳定性和可靠性。
在新能源汽车工业的不断变革发展状态下,为了为更好地满足现代社会的发展需要,就要对超高强铝合金铸造技术进行优化升级,让其强度和使用价值得到更好的体现。
为了实现这样的目标,就需要材料研究者投入更多的精力于铸造技术研究上,致力于装备控制系统的优化配置和使用,并通过改变合金成分的属性进行再次设计,并通过阻塞的现代化方式,不断对新型的超高强铝合金进行构造。
在现行的中国环境下,我国的超高强铝合金铸造技术研究相对较晚,因而在当下与国外相比还具有一定的距离。
其原因一方面在于缺乏时间成本的投入,而另一方面也在于我国整体的技术管理还尚未形成一个完整的体系,除此之外,研究的环境也相对恶劣,缺乏相应的仪器设备。
为了更快地缩小与国外超高强铝合金铸造技术水平的距离,提高自身的技术能力,是当下我国超高强铝合金铸造技术及装备控制系统开发人员的重要职责所在。
1 对我国超高强铝合金铸造技术及装备控制系统现状的分析与认识1.1 超高强铝合金铸造技术1.1.1 立式半连续铸造超高强铝合金的半连续铸造工艺过程实际上是改变传统热铸造的形式,而对其进行相应的冷铸造技术处理,从而全面提升超高强铝合金的质量和强度,并使其快速成型,加大生产能力。
- 1、下载文档前请自行甄别文档内容的完整性,平台不提供额外的编辑、内容补充、找答案等附加服务。
- 2、"仅部分预览"的文档,不可在线预览部分如存在完整性等问题,可反馈申请退款(可完整预览的文档不适用该条件!)。
- 3、如文档侵犯您的权益,请联系客服反馈,我们会尽快为您处理(人工客服工作时间:9:00-18:30)。
参考文献
[1] 张正智,越人.国内外铝合金车轮制造业的现状与发展趋势[J].汽车工程学报,2004(12).
[2]宋鸿武,李昌海,常海平,等.高强韧铝合金轮毂的轻量化铸旋新工艺[J].稀有金属,2012,36(4):631. [3]彭继华,唐小龙。何建亭,等.热处理对A356铝合金组织机构和力学性能影响[J].中国有色金属学报(英文版),2011,21(9):1950—
2.2人工时效
言,时效峰值的温度仅仅需要较小程度的提高,达到 时效峰值的时间将大大缩短。国外研究报道,A356 合金在150℃时达到时效峰值的时间为12~14 h,但
在170℃时仅需要2-4 h。时效温度超过190℃,时
效强度将大幅度降低。因此从时效效果和时效时间 两方面综合考虑,确定时效温度为170℃。
较低,特别是轮辐部位的强度和韧性还需要大幅度
基金项目:广州市科技支撑计划(200922一D221)
作者简介:杨传柱(1961一),男,高级工程师,工学硕士,1988年毕业于武汉科技大学.
万方数据
冶金丛刊
总第206期
性;结合有限元结构分析开展新型车轮的结构设计, 减小车轮厚度达到汽车轻量化的目的。本文基于汽 车铝合金车轮强韧化与轻量化的关键性技术项目开 发[3】。主要研究A356铝合金强韧化试制的熔铸、热 处理成型的工艺与控制过程,分析实验结果。
%
4
结语
在使用新型高效、长效细化变质复合剂和优化
合金的生产及汽车轮毂轻量化制造。实验表明,强 韧化A356铝合金铸锭的拉伸强度、延伸率均比 ASTM标准要求值提高20%,且疲劳强度、抗冲击韧
性提高10%。
化学成分的基础上,研究A356铝合金强韧化的熔 铸、热处理工艺及控制,可实现高强韧性能A356铝
引言
国内铝车轮厂家主要采用金属型重力铸造、低
提高¨‘2 J。华南某铝合金公司与高校及铝轮毂公司 产学研联合研究开发汽车轮毂用高强韧A356铝合 金,通过大量试验提出了一套初步的解决方案:利用 细化组织、Si相变质、微合金化处理及优化热处理 工艺等措施和手段来提高车轮用A356铝合金的强 韧性;从成形工艺出发,优化铸造工艺,包括凝固模 式、温度场分布设计和凝固过程的数值模拟,并以此 为基础进行铸造模具的优化设计,以提高车轮整体
1956.
万方数据
摘要高强韧A356合金的研制成功解决了低压铸造汽车轮毂塑性和韧性较差的问题,可实现汽车轻量化。强 韧化A356合金的熔铸工艺路线同传统铝合金的熔铸工艺基本一致,但严格控制各节点温度以及调制合金化元素 含量,采用合适的热处理工艺将进一步提高其综合力学性能。研究表明,强韧化A356铝合金铸锭的拉伸强度、延 伸率均比ASTM标准要求值提高20%,且疲劳强度、抗冲击韧性提高10%。 关键词高强韧;铝合金;低压铸造;成型;控制 中图分类号:TG249.2+8文献标识码:A 文章编号:1671—3818(2013)04—0005—03
1.1
峰值时效的强化效果。影响A17SiMg合金热处理的 因素不仅包括处理温度与时间,还受热处理前的微
观组织、合金化成分等的影响。 汽车轮毂用A356铝合金的热处理工艺流程 为:铸态毛坯入炉并升温一固溶温度下保温叶出炉
Si、Mg元素投入顺序和温度 si和Mg两种元素均容易氧化损失,因此投料
温度要尽可能低。采用速熔硅,投料时熔体温度应 控制在700—720℃,待硅料熔化并搅拌均匀后,降 低熔体温度至680—700 oC,投入纯镁料,表面覆盖
MOLDING
A356
AND CONTRoLLING
oFⅢGH
STRENGTH
ALUM叩姗)M
Yang Chuanzhul
ALLOY FOR
Xu Deyin91
AUTOMOBⅡ。E HUB
Peng Chun2
Peng Jihua2
(1.Guangzhou
Iron&Steel Enterprises Group Co.,Ltd.,Guangzhou 510381,Guangdong;2.South China Uni—
will be further improved with appropriate heat treatment.The result shows that:both the tensile strength and elongation of
hi曲strength
A356 Alloy
ItYe
increased by 20%as compared with ASTM standard,and
防止Mg元素氧化的覆盖溶剂。 1.2中间合金投入温度 中间合金中含有碱土、稀土元素,自由的碱土、
_÷水淬处理_÷入炉升温_时效温度下保温叶出炉后 空气介质中冷却。其特征在于:固溶处理时间短,固
溶处理温度为550 oC,处理保温时间为60~
120
min;人工时效处理时间短,时效温度为165—
min。
180℃,处理保温时间为120~240
2.1固溶处理
稀土元素非常容易氧化。这两种合金化元素的加入
量微少,需要采取适当保护措施避免其严重烧损。
热处理固溶温度需要综合考虑以下因素:
(1)合金的熔点。
在中间合金中这些元素主要以较高熔点的金属间化 合物相存在,保证这些高熔点相的充分溶解和元素 在熔体中的充分扩散,希望熔体温度高,但同时将伴
(2)晶粒在固溶过程中的长大。 (3)合金元素的扩散能力或达到均匀饱和固溶
体的速度。
万方数据
第4期
杨传柱等:汽车轮毂用高强韧A356铝合金的成型与控制
・7・
后者受到合金元素扩散距离的影响。A356合 金中的扩散距离决定于初始枝晶胞的尺寸。固溶过 程中共晶硅的球化过程(球化所需时间)由诸多因 素控制,主要有:铸态组织中纤维状共晶硅的半径、 固溶温度、硅在铝中的互扩散系数、Al—si的界面能 等。铸态组织中共晶硅相越细小、固溶温度越高,则 达到硅相球化的时间越短。
Higll
Strength A356 Ahoy is essentially consistent with the traditional aluminum alloy,but the tempera-
ture of each node
and the
content
of alloying elements is strictly controlled,and its mechanical properties
第4期总第206期 2 0 1 3年8月
冶金丛刊
METALLURGICAL COLLECTIONS
Sum.206 August
No.4 20 1 3
汽车轮毂用高强韧A356铝合金的成型与控制
杨传柱1 许德英1 彭继华2 彭 淳2
(1.广州钢铁企业集团有限公司,广东广州510381;2.华南理工大学,广东广州510640)
also the fatigue strength and impact toughness are increased by 10%. Key words high strength;aluminum alloy;low pressure casting;molding;cofntrolling
O
的收得率达到80%左右,配置中间合金的投料时需
要考虑该收得率。
N:十精炼除杂
2热处理工艺
成分合格I
气体含量合格 熔体成分检测 熔体气体含量检测
为了提高可热处理Al—Si系合金的综合力学 性能,需要采用合适的热处理工艺旧J。国内外相关 AI-7Si—Mg的热处理标准工序目前均接近20小 时。处理时间长不仅限制了生产效率,而且耗能巨
3合金性能
铸态A356合金的化学成分及性能见表1和 表2。由表1和表2可见新产品的拉伸强度、伸长 率均高于ASTM标准中A356.2性能要求的20%。
A356合金的时效强化主要来源于M92Si析出。 基于硅原子的扩散模型,达到时效峰值的时间与时效
温度、扩散激活能和扩散系数相关。就A356合金而
表1铸锭的化学成分
l
随这些元素的氧化程度增加。理想的投入和溶解温 度应控制在730—750 cC之间,并用钟罩将中间合金 压入熔体中搅拌。 1.3精炼温度 采用惰性气体和精炼除杂剂。在除气和除杂过 程中,高温有利于降低熔体粘度,降低气、杂上浮阻 力;但高温同时促进熔体吸气和高活性合金元素的 烧损和氧化。选用六氯乙烷含量较少的精炼除杂 剂,避免分解产生的大量氯气与铝及微量合金化元 素反应。理想的精炼温度控制在700~730 oC之间。
静置30分钟 铸锭试样 性能检测
浇注Байду номын сангаас属型
大。固溶处理的目的是获得镁、硅均匀分布的过饱
图1
A356铝合金熔铸工艺路线
和铝晶胞,同时实现共晶硅相的完全球化;时效过程
析出big:Si及Si相,理想的时效时间应当控制达到
铝合金熔铸过程各节点的温度控制需要综合考 虑,元素的烧损、熔体粘度、合金元素是否充分和均 匀地扩散、熔体吸气等因素。
显微组织的均匀性、细化组织、提高轮辐的强度和韧
压铸造、半固态铸造和挤压铸造等铸造方法生产。 其中金属型低压铸造法以其工艺简单、生产效率高、 成本较低、性能较好而成为铝车轮主要的铸造成形 方法,占铸造铝车轮市场的75%以上。但与半固态
铸造和挤压铸造铝车轮相比,低压铸造成形铝车轮
的强韧性相对较低,主要问题是铸件的塑性和韧性
1.4浇铸温度
熔铸工艺
强韧化A356合金的熔铸工艺路线见图1,同传
统铝合金的熔铸工艺一致,除各节点严格控制温度 外。合金化元素含量的调制是重要环节。
型
’
表面撤上覆盖剂 加入si、Mg等主要合金元素 加入中间合金,调帝J熔体中 合金元素含量
同传统m—si合金一样,浇铸温度控制为720—