浮头式换热器(过程设备设计课程设计说明书)参考word
浮头式换热器设计说明书

浮头式换热器设计说明书设计者:徐凯指导教师:张玲张亚男秦敏系别:机械工程系专业:热能与动力工程日期:2009.11宁夏理工学院前言换热器是非常重要的换热设备。
在国民生产的各个领域得到了广泛的应用。
本设计说明书主要介绍浮头式换热器的原理和设计思路及整个设计过程。
在浮头式换热器中,浮头式换热器的两端的管板,一端不与壳体相连,该端亦称浮头。
管子受热时,管束连同浮头可以沿轴向自由伸缩,完全消除了温差应力。
浮头式换热器主要有如下特点:浮头式换热器的一端管板固定在壳体与管箱之间,另一端管板可以在壳体内自由移动,这个特点在现场就能清楚地看出来。
这种换热器的壳体和管束的热膨胀是自由的,管束可以抽出,便于清洗管间和管内。
其缺点是结构复杂造价高,一般比固定管板高20%左右,在运行中浮头处发生泄漏不易检查处理。
浮头式换热器适应于壳体和管束温差较大或壳程介质易结垢的工作条件下。
本书内容系统、完整,理论与实际并重。
书中对浮头式换热器设计中所需的各学科知识均有简要的介绍和解释。
同时该书对换热器在编写时注重介绍的方法简明扼要,条理清楚,深入浅出,紧密结合工程实际。
期间得秦敏、张春兰、张亚男、张玲等老师的悉心指导。
在此表示真挚的感谢!由于编者水平有限,其中难免不妥之处,恳请各位读者批评指正。
编者:徐凯2009-11-26目录第一章绪论第二章设计任务和设计条件 (1)第三章确定设计方案 (3)3.1 换热器类型的确定 (3)3.2 管程及壳程的流体安排 (3)第四章确定物性数据 (4)4.1定性温度的确定 (4)4.2列表 (6)第五章传热面积的估算 (7)第六章工艺结构尺寸的确定 (9)6.1 管径和管内流速的确定 (9)6.2 管程数和传热管数的确定 (9)6.3 平均传热温差的校正 (10)6.4 传热管排列和分程方法确定 (10)6.5 壳体内径的确定 (11)6.6 折流板的确定 (11)6.7 其它附件的确定 (12)第七章所设计换热器的校核算 (13)7.1 传热热流量的核算 (13)7.2 壁温的校核计算 (15)7.3 换热器内流体的流动阻力的核算 (17)参考文献 (19)换热器原理课程设计心得体会 (21)第一章绪论1.1换热器课程设计的目的和要求课程设计是《换热器原理》课程的一个总结性教学环节,是培养学生综合运用本门课程及有关课程的基本知识去解决某一设计任务的一次训练。
浮头式换热器(过程设备设计课程设计说明书)
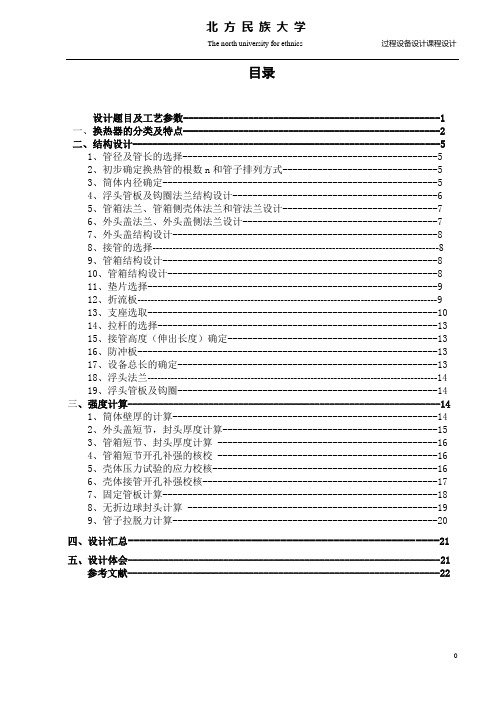
目录设计题目及工艺参数---------------------------------------------------1一、换热器的分类及特点---------------------------------------------------2二、结构设计-------------------------------------------------------------51、管径及管长的选择---------------------------------------------------52、初步确定换热管的根数n和管子排列方式-------------------------------53、筒体内径确定-------------------------------------------------------54、浮头管板及钩圈法兰结构设计-----------------------------------------65、管箱法兰、管箱侧壳体法兰和管法兰设计-------------------------------76、外头盖法兰、外头盖侧法兰设计---------------------------------------77、外头盖结构设计-----------------------------------------------------88、接管的选择--------------------------------------------------------------------------------------89、管箱结构设计-------------------------------------------------------810、管箱结构设计------------------------------------------------------811、垫片选择----------------------------------------------------------912、折流板------------------------------------------------------------------------------------------913、支座选取----------------------------------------------------------1014、拉杆的选择--------------------------------------------------------1315、接管高度(伸出长度)确定------------------------------------------1316、防冲板------------------------------------------------------------1317、设备总长的确定----------------------------------------------------1318、浮头法兰---------------------------------------------------------------------------------------1419、浮头管板及钩圈----------------------------------------------------14三、强度计算--------------------------------------------------------------141、筒体壁厚的计算-----------------------------------------------------142、外头盖短节,封头厚度计算-------------------------------------------153、管箱短节、封头厚度计算 --------------------------------------------164、管箱短节开孔补强的核校 --------------------------------------------165、壳体压力试验的应力校核---------------------------------------------166、壳体接管开孔补强校核-----------------------------------------------177、固定管板计算-------------------------------------------------------188、无折边球封头计算 --------------------------------------------------199、管子拉脱力计算-----------------------------------------------------20四、设计汇总-----------------------------------------------------21五、设计体会--------------------------------------------------------------21参考文献--------------------------------------------------------------22设计题目:浮头式换热器工艺参数:管口表:符号公称直径(mm)管口名称a 130 变换气进口b 130 软水出口c 130 变换气出口d 130 软水进口e 50 排尽口设备选择原理及原因:浮头式换热器的结构较复杂,金属材料耗量较大,浮头端出现内泄露不易检查出来,由于管束与壳体间隙较大,影响传热效果。
浮头换热器的课程设计说明书

化工原理课程设计设计题目:浮头式换热器的设计指导教师李毅学生姓名凌风2010 年 10 月 20 日浮头式换热器设计任务书一、设计题目:浮头式换热器的设计二、设计原始数据操作条件:①大豆油:入口温度133℃,出口温度40℃②冷却介质:循环水,入口温度30℃,出口温度40℃③大豆油处理量:5000kg/h④允许压降:不大于1×105Pa⑤大豆油定性温度下的物性数据:根据液体相对密度共线图查得86.5℃下大豆油的密度为: =925 kg/m3根据液体粘度共线图得86.5℃下大豆油的粘度为:μ=0.000850 Pa/s根据液体比热容共线图得86.5℃下大豆油的定压比热容为:2.052 kJ/(kg·℃)CP0 =查表得86.5℃下大豆油的导热系数为λ=0.1559 W/(m·℃)⑥循环冷却水在定性温度下的物性数据如下:ρ=994 kg/m3密度:i=4.08 kJ/(kg·℃)定压比热容:CPiλ=0.626 W/(m·℃)导热系数:iμ=0.000725 Pa/s粘度:i⑦每年按330天计算,每天24小时连续运行。
三、设备型式浮头式换热器四、设计任务1.编写课程设计说明书2.设计计算列管式换热器的管径尺寸、管内流速、热负荷、传热面积、管程数、管数、壳程数和接管尺寸等3.工艺流程图及换热器工艺条件图4.设计评述目录一、设计方案 (3)1.1选择换热器的类型 (3)1.2流动空间及流速的确定 (3)二、物性数据 (4)三、计算总传热系数 (4)3.1热流量 (4)3.2平均传热温差(逆流) (4)3.3冷却水用量 (4)3.4总传热系数K (4)四、计算传热面积 (5)五、工艺结构尺寸 (5)5.1管径和管内流速 (5)5.2管程数和传热管数 (5)5.3平均传热温差校正系数 (6)5.4传热管排列和分程方法 (6)5.5壳体内径 (6)5.6折流板 (6)5.7接管 (7)六、换热器核算 (7)6.1热量核算 (7)6.2换热器内流体的流动阻力 (9)6.3换热器主要结构尺寸和计算结果 (10)七、主体设备图 (11)八、参考文献 (11)九、主要符号说明 (11)十、总结 (12)一、设计方案1.1选择换热器的类型两流体温度变化情况:入口温度133℃,出口温度40℃循环水,入口温度30℃,出口温度40℃本设计任务为煤油冷却器的设计,两流体在传热过程中无相的变化,该换热器用循环冷却水冷却,冬季操作时进口温度会降低,考虑到这一因素,估计该换热器的管壁温和壳体壁温之差较大,因此初步确定选用带膨胀节的固定管板式换热器;固定管板式换热器结构比较简单,制造简单,制造成本低,管程可用多种结构,规格范围广,在生产中广泛应用。
浮头式换热器课程设计

目录一 设计任务书某生产过程中,需将6000kg/h 的原油从175℃冷却至130℃,压力为0.4MPa ;冷却介质采用循环水,循环冷却水的压力为0.3MPa ,循环水进口温度25℃,出口温度为55℃。
试设计一台列管式换热器,完成该生产任务。
二 设计计算2.1确定设计方案2.11 选择换热器类型 两流体的温度变化情况:原油进口温度175℃,出口温度130℃; 循环冷却水进口温度25℃,出口温度55℃。
考虑到换热器的管壁温度和壳体温度之差较大,因此初步确定选用浮头式换热器。
2.12 管程安排由于循环冷却水较易结垢,若其流速太低,将会加速污垢增长速度,使换热器的热流量下降,故总体考虑,应使循环冷却水走管程,原油走壳程。
2.2 确定物性数据定性温度:对于一般气体和水等低黏度流体,其定性温度可取流体进出口温度的平均值。
故 壳程原油的定性温度为:5.1522)130175(=+=T ℃ 管程循环冷却水的定性温度为:402)5525(=+=t ℃ 已知原油在定性温度下的有关物性数据如下: 密度 0ρ=820kg/m 3 导热系数 0λ=0.128W/m ℃ 定压比热容 0p C =2.20kJ/kg ℃ 粘度 0μ=0.665mPa ﹒s 循环冷却水在40℃下的物性数据如下:密度 i ρ=992.2kg/m 3 导热系数 0λ=0.634W/m ℃ 定压比热容 0p C =4.1744KJ/kg ℃ 粘度 0μ=0.656mPa ﹒s2.3 估计传热面积2.31 热流量 (忽略热损失)h kj t C m Q p /452.260000000⨯⨯==2.32 冷却水的用量h kg t C Q m p i /2.4773301744.459400000=⨯==2.33 平均传热温差 先按照纯逆流计算得:36.112105120ln )105120('=-=mt ℃ 2.34 初算传热面积由总传热系数的选择表可得:K 的取值范围为290 ~698)/(02C m W ,在K 的取值范围内,取K=320)/(02C m W 。
浮头式换热器课程设计说明书

浮头式换热器课程设计说明书(共25页)--本页仅作为文档封面,使用时请直接删除即可----内页可以根据需求调整合适字体及大小--1.方案确定选择换热器的类型浮头式换热器:主要特点是可以从壳体中抽出便于清洗管间和管内。
管束可以在管内自由伸缩不会产生热应力。
换热面积的确定根据《化工设备设计手册》选择传热面积为 400m 2换热管数N 的确定我国管壳式换热器常用碳素钢、低合金钢钢管,其规格为φ19× 2、φ25× 、φ32× 3、φ38 × 3、φ57 × 等,不锈钢钢管规格为φ19 × 2、φ25 × 2、φ32 × 2、φ38 × 、φ57 × 。
换热管长度规格为、、、、、、、、等。
换热器换热管长度与公称直径之比,一般在 4~25 之间,常用的为 6~10。
管子的材料选择应根 据介质的压力、温度及腐蚀性来确定。
选用32×3mm 的无缝钢管,材质为 0Cr18Ni9,管长为 6000mmn=A/πd 0L 3-5式 3-5:n —换热管数 A —换热面积m 2 d0—换热管外径mm L —换热管长度mm故 -3-3400n==6133.1432600010⨯⨯10⨯⨯根表拉杆直径 /mm表拉杆数量换热器公称直径DN/mm400<d400≤d<700700≤d<900900≤d<2600 44810拉杆需 10根。
换热管的排布与连接方式的确定换热管排列形式如图所示。
换热管在管板上的排列形式主要有正三角形、正方形和转正三角形、转三角形。
正三角形排列形式可以在同样的管板面积上排列最多的管数,故用的最为广泛,但管外不易清洗。
为便于管外便于清洗可以采用正方形或转正方形的管束。
换热管中心距要保证管子与管板连接时,管桥有足够的强度和宽度。
管间需要清洗时还要留有进行清洗的通道。
换热管中心距宜不小于倍的换热管的外径。
浮头式换热器设计说明书

1 绪论1.1 换热设备在工业中的应用在炼油、化工生产中,绝大多数的工艺过程都有加热、冷却和冷凝的过程,这些过程总称为换热过程。
传热过程的进行需要一定的设备来完成,这些使传热过程得以实现的设备就称之为换热设备。
据统计,在炼油厂中换热设备的投资占全部工艺设备总投资的35%~40%,因为绝大部分的化学反应或传质传热过程都与热量的变化密切相关,如反应过程中:有的要放热、有的要吸热、要维持反应的连续进行,就必须排除多余的热量或补充所需的热量。
工艺过程中某些废热或余热也需要加以回收利用,以降低成本。
综上所述,换热设备是炼油、化工生产中不可缺少的重要设备。
换热设备在动力、原子能、冶金及食品等其他工业部门也有着广泛的应用。
1.2 换热设备的分类1.2.1按作用原理或传热方式可分为:直接接触式、蓄热式、间壁式。
1.2.1.1直接接触式换热器,如下图所示热流体图1.1其传热的效果好,但不能用于发生反应或有影响的流体之间。
蓄热式换热器,如下图所示图1.2其适用于温度较高的场合,但有交叉污染,温度被动大。
1.2.1.3 间壁式换热器,又称表面式换热器利用间壁进行热交换。
冷热两种流体隔开,互不接触,热量由热流体通过间壁传递给冷流体。
1.2.2 按其工艺用途可分为:冷却器(cooler)、冷凝器(condenser)、加热器(一般不发生相变)(heater)、蒸发器(发生相变)(evaporator)、再沸器(reboiler)、废热锅炉(waste heat boiler)。
1.2.3 按材料分类:分为金属材料和非金属材料换热器。
1.3 国内外的研究现状上个世纪70年代初发生世界性能源危机,有力地促进了传热强化技术的发展。
为了节能降耗,提高工业生产的经济效益,要求开发适用不同工业过程要求的高效能换热设备。
因此,几十年来,高效换热器的开发与研究始终是人们关注的课题,国内外先后推出了一系列新型高效换热器。
近年来,国内已经进行了大量的强化传热技术的研究,但在新型高效换热器的开发方面与国外差距仍然较大,并且新型高效换热器的实际推广和应用仍非常有限。
浮头式换热器设计说明书

1 绪论1.1 换热设备在工业中的应用在炼油、化工生产中,绝大多数的工艺过程都有加热、冷却和冷凝的过程,这些过程总称为换热过程。
传热过程的进行需要一定的设备来完成,这些使传热过程得以实现的设备就称之为换热设备。
据统计,在炼油厂中换热设备的投资占全部工艺设备总投资的35%~40%,因为绝大部分的化学反应或传质传热过程都与热量的变化密切相关,如反应过程中:有的要放热、有的要吸热、要维持反应的连续进行,就必须排除多余的热量或补充所需的热量。
工艺过程中某些废热或余热也需要加以回收利用,以降低成本。
综上所述,换热设备是炼油、化工生产中不可缺少的重要设备。
换热设备在动力、原子能、冶金及食品等其他工业部门也有着广泛的应用。
1.2 换热设备的分类1.2.1按作用原理或传热方式可分为:直接接触式、蓄热式、间壁式。
1.2.1.1直接接触式换热器,如下图所示热流体图1.1其传热的效果好,但不能用于发生反应或有影响的流体之间。
蓄热式换热器,如下图所示图1.2其适用于温度较高的场合,但有交叉污染,温度被动大。
1.2.1.3 间壁式换热器,又称表面式换热器利用间壁进行热交换。
冷热两种流体隔开,互不接触,热量由热流体通过间壁传递给冷流体。
1.2.2 按其工艺用途可分为:冷却器(cooler)、冷凝器(condenser)、加热器(一般不发生相变)(heater)、蒸发器(发生相变)(evaporator)、再沸器(reboiler)、废热锅炉(waste heat boiler)。
1.2.3 按材料分类:分为金属材料和非金属材料换热器。
1.3 国内外的研究现状上个世纪70年代初发生世界性能源危机,有力地促进了传热强化技术的发展。
为了节能降耗,提高工业生产的经济效益,要求开发适用不同工业过程要求的高效能换热设备。
因此,几十年来,高效换热器的开发与研究始终是人们关注的课题,国内外先后推出了一系列新型高效换热器。
近年来,国内已经进行了大量的强化传热技术的研究,但在新型高效换热器的开发方面与国外差距仍然较大,并且新型高效换热器的实际推广和应用仍非常有限。
浮头式换热器设计说明书
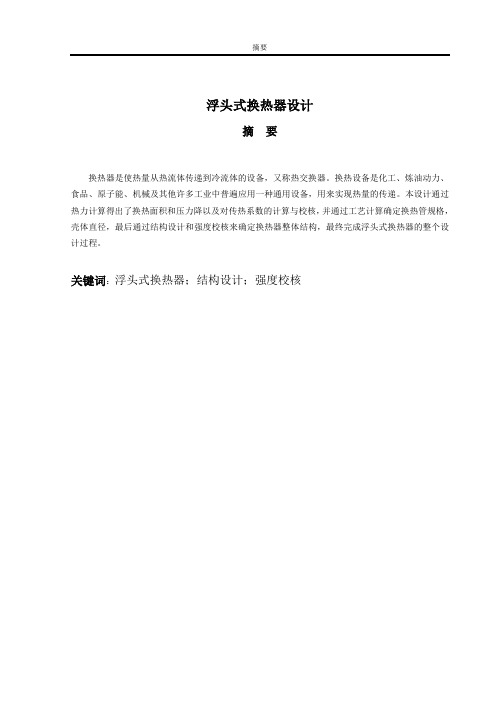
这类换热器是在芯筒与外筒之间的空间内将传热管按螺旋线形状交替缠绕而成,相邻两层螺旋状传热管的方向相反,并采用一定形状的定距件使之保持一定的间距。它适用于同时处理多种介质、在小温差下需要传递较大量且管内介质操作压力较高的场合。
1.
在换热器向高参数、大型化发展的今天,管壳式换热器仍占主导地位。它的基本结构是在壳体内放置了许多管子组成的管束,管子的两端(或一端)固定在管板上,管子的轴线与壳体的轴线平行。为了增加流体在管外空间的流速并支撑管子,改善传热性能,在筒体内间隔安装多块折流板,用拉杆和定距管将其与管子组装在一起。换热器的壳体上和两册的端盖上装有流体的进出口。
(1)实现所规定的工艺条件
(2)强度足够及结构可靠
(3)便于制造、操作与维修
(4)经济上合理
1.3
在进行换热器设计时,对换热器各种零,部件的材料,应根据设备操作压力,操作温度,流体的腐蚀性能以及对材料的制造工艺性能等的要求来选取。当然,最后还要考虑材料的经济合理性。一般为了满足设备操作压力和操作温度,即从设备的强度和刚度的角度来考虑,是比较容易达到的,但对于材料的耐腐蚀性能,有时往往成为一个复杂的问题。如在这方面考虑不周,选材不妥,不仅会影响换热器的使用寿命,而且也大大提高设备的成本。至于材料的制造工艺性能,是与换热器的具体结构有着密切关系。
管壳式换热器虽然在换热效率,设备结构的紧凑性和单位面积的金属消耗量等方面都不如其它新型换热器,但它具有结构坚固、可靠性高、适应性广、易于制造、处理能力大、生产成本低、选用的材料范围广、换热表面的清洗比较方便、能承受较高的操作压力和温度。在高温、高压和大型换热器中,管壳式换热器仍占绝对优势,是目前使用最广泛的一类换热器。根据热补偿方法的不同,管壳式换热器有下面几种形式
浮头式换热器设计说明书

浮头式换热器设计说明书摘要本设计说明书是关于浮头式换热器的设计,主要是进行了换热器的工艺计算、换热器的结构和强度设计。
设计的前半部分是工艺计算部分,主要是根据给定的设计条件估算换热面积,从而进行换热器的选型,校核传热系数,计算出实际的换热面积,最后进行压力降和壁温的计算。
设计的后半部分则是关于结构和强度的设计,主要是根据已经选定的换热器型式进行设备内各零部件(如接管、折流板、定距管、钩圈、管箱等)的设计,包括:材料的选择、具体尺寸确定、确定具体位置、管板厚度的计算、浮头盖和浮头法兰厚度的计算、开孔补强计算等。
关于浮头式换热器设计的各个环节,设计说明书中都有详细的说明。
浮头式换热器:其结构如图2所示。
管子一端固定在一块固定管板上,管板夹持在壳体法兰与管箱法兰之间,用螺栓连接;管子另一端固定在浮头管板上,浮头管板夹持在用螺柱连接的浮头盖与钩圈之间,形成可在壳体内自由移动的浮头,故当管束与壳体受热伸长时,两者互不牵制,因而不会产生温差应力。
浮头部分是由浮头管板,钩圈与浮头端盖组成的可拆联接,因此可以容易抽出管束,故管内管外都能进行清洗,也便于检修。
由上述特点可知,浮头式换热器多用于温度波动和温差大的场合,尽管与固定管板式换热器相比其结构更复杂、造价更高。
1.1设计任务根据给定的工艺设计条件,此设计为无相变热、冷流体间换热的浮头式换热器设计任务。
1.2总体设计①确定结构形式。
由于介质换热温差较大,因此选用浮头式换热器。
②合理安排流程。
安排冷的污水走壳程,处理过的热清水走管程。
1.3热工计算①原始数据○2定性温度与物性参数○3物料与热量恒算○4有效平均温差○5初算传热面积○6换热器结构设计○7管程传热与压降○8壳程传热与压降结构设计与强度设计1)换热流程设计:采用壳程为单程、管程为单程的结构型式.2)换热管及其排列方式:采用的无缝钢管,材料为2520钢,热管排列方式为三角形排列,如图所示,共101根。
另外6根拉杆,共排列107根。
浮头式换热器计算说明书

设备设计说明书
目 录
AES 浮头式换热器的设计............................................................................................................................ 1 第 1 章 概述................................................................................................................................................. 1 第 1·1 节 设备的简介................................................................................................................................1 第 1·2 节 设备的基本结构......................................................................................................................3 第 2 章 结构设计......................................................................................................................................... 4 第 2·1 节 材料的选择................................................................................................................................4 第 2·2 节 主要结构设计............................................................................................................................7 第 3 章 设计计算......................................................................................................................................... 8 第 3·1 节 筒体及封头壁厚计算................................................................................................................8 第 3·2 节 管板计算..................................................................................................................................13 第 3·3 节 浮头法兰计算..........................................................................................................................19 第 3·4 节 钩圈计算..................................................................................................................................22 第 3·5 节 球冠形封头计算......................................................................................................................22 第 3·6 节 开孔补强计算..........................................................................................................................22 第 3·7 节 鞍座支反力计算..................................................................................... 错误!未定义书签。 第 4 章 制造、安装与检验.....................................................................................................................28 第 5 章 经济性分析................................................................................................................................. 33 结论............................................................................................................................................................. 34 参考文献..................................................................................................................................................... 35 符号说明..................................................................................................................................................... 36 致谢............................................................................................................................................................. 38
浮头式换热器设计说明书
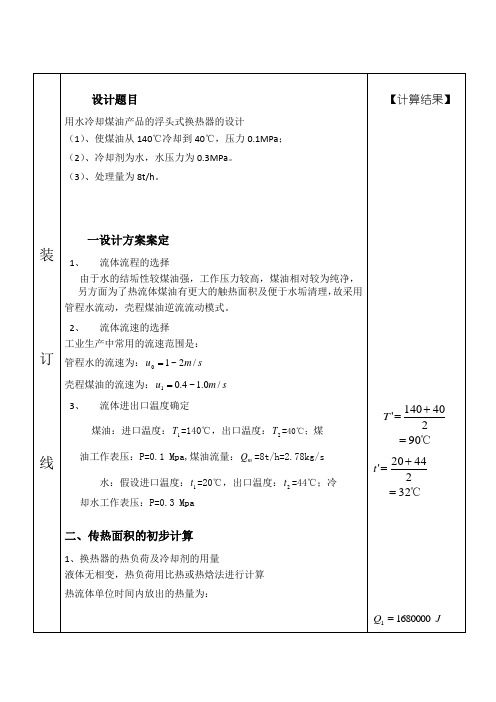
4746/168400 T JB MnR EHA -⨯装订线4. 管板与换热管的连接:管板与换热管采用胀接的形式,胀接长度mml37=,对于规格为5.225⨯φ换热管,由于管板壁厚2540>,为5.0322==+Kmml,,连接方式如下:5. 换热管中心距:由换热管外径mmd25=外,中心距mmt32=,根据GB151-1999标准,可查得分隔板槽两侧相邻管中心距mmSn44=6. 布管限定圆:根据GB151-1999标准,对于浮头式换热器,其布管限定圆直径为:)21(2bbbDDnL++-=b1=3b2=4b=11.52575.0min⋅≥δmm75.18=21075.18++≥δmm75.30=取标准设计值:mm40=δ装订线7. 管板管孔:根据GB151-1999标准,Ⅰ级管束(碳素钢管),当换热器mmd25=外时,其管孔直径mmd25.25=孔,允许偏差为:0~15.0+8. 管板连接:根据GB151-1999标准,管板与壳程圆筒、管板与法兰之间选择a型连接方式a型连接方式为:管板通过垫片于壳体法兰何管箱法兰连接管板与管箱用螺柱、垫片平面密封连接9. 壳体接管:由前已知壳体接管mmd1001=,管箱接管mmd802=,363=LD装订线16球冠形封头钩圈式浮头换热器外头盖推荐使用球冠形封头,根据《JB04746T.02钢制压力容器用封头》标准,取封头为DN500⨯8的PSH球冠形封头,总深度H=65mm,内表面积22033.0mA=,容积30063.0mV=,封头质量kgM9739.12=R=50017. 容器法兰1:根据JB-T4701-2000标准选取长颈对焊法兰,形式为突面密封面类型,则取MPaPN0.1=,mmDN400=,规格为:4559550054031====DHDD 23344524===dD δ,配合螺柱为:20M20个结构如图所示:mmA1383≤即可装订线2:根据JB-T4701-2000标准选取长颈对焊法兰,形式为凹凸面密封面类型,则取MPaPN0.1=,mmDN500=,规格为:55510060064031====DHDD 23385524===dD δ,配合螺柱为:20M20个结构如图所示:3:根据JB-T4721-92外头盖侧法兰,形式为凸面密封面类型,则取MPaPN0.1=,mmDN400=,规格为:5559060064031====DHDD 23325524===dD δ,配合螺柱为:20M20个结构如图所示:4钩圈式浮头法兰480800=+=i f D D372)104(2400)1(2=+-=++=bn b D D i fi426186290=+=b D3946400=-=c Dmm D G 384)53200(2=--=18钩圈 选择A 型钩圈t t ][σ=113直径比K=1.29查GB150-1998第九章,得Y=7.77120)](5.0[5.0=+-=fi c b D D D La厚度δ=42mm19管板计算:对延长部分兼做法兰的固定管板根据GB151-1999,初始数据:垫片压紧力作用中心圆直径384mm管子: 管子外径:mm d 25=外 管子壁厚:mm5.2=δ管子根数:mm n68=浙江工业大学课题:浮头式换热器设计班级:过控0601学号:200602060120设计者:徐庆清。
浮头式换热器(过程设备设计课程设计说明书)参考word

目录设计题目及工艺参数---------------------------------------------------1一、换热器的分类及特点---------------------------------------------------2二、结构设计-------------------------------------------------------------51、管径及管长的选择---------------------------------------------------52、初步确定换热管的根数n和管子排列方式-------------------------------53、筒体内径确定-------------------------------------------------------54、浮头管板及钩圈法兰结构设计-----------------------------------------65、管箱法兰、管箱侧壳体法兰和管法兰设计-------------------------------76、外头盖法兰、外头盖侧法兰设计---------------------------------------77、外头盖结构设计-----------------------------------------------------88、接管的选择--------------------------------------------------------------------------------------89、管箱结构设计-------------------------------------------------------810、管箱结构设计------------------------------------------------------811、垫片选择----------------------------------------------------------912、折流板------------------------------------------------------------------------------------------913、支座选取----------------------------------------------------------1014、拉杆的选择--------------------------------------------------------1315、接管高度(伸出长度)确定------------------------------------------1316、防冲板------------------------------------------------------------1317、设备总长的确定----------------------------------------------------1318、浮头法兰---------------------------------------------------------------------------------------1419、浮头管板及钩圈----------------------------------------------------14三、强度计算--------------------------------------------------------------141、筒体壁厚的计算-----------------------------------------------------142、外头盖短节,封头厚度计算-------------------------------------------153、管箱短节、封头厚度计算 --------------------------------------------164、管箱短节开孔补强的核校 --------------------------------------------165、壳体压力试验的应力校核---------------------------------------------166、壳体接管开孔补强校核-----------------------------------------------177、固定管板计算-------------------------------------------------------188、无折边球封头计算 --------------------------------------------------199、管子拉脱力计算-----------------------------------------------------20四、设计汇总-----------------------------------------------------21五、设计体会--------------------------------------------------------------21参考文献--------------------------------------------------------------22设计题目:浮头式换热器工艺参数:管口表:符号公称直径(mm)管口名称a 130 变换气进口b 130 软水出口c 130 变换气出口d 130 软水进口e 50 排尽口设备选择原理及原因:浮头式换热器的结构较复杂,金属材料耗量较大,浮头端出现内泄露不易检查出来,由于管束与壳体间隙较大,影响传热效果。
浮头式换热器说明书

第一章绪论1.1 换热器技术概况近年来,由于新科学技术和节约能源的发展,对被广泛应用的换热器,提高换热器的传热性能和开发新的节能型换热器,已成为换热器设计、制造方面的重要课题,我国石化行业的换热设备以管壳式换热器为主,而且传统弓形折流板换热器占到总量的70%~80%。
弓形折流板换热器固然有其优点,并在产业节能方面做出了巨大贡献,但在新的节能减排形势下,其缺点(压降大、存在大量流动死区、振动大、传热效率低等)严重限制了自身的生存和发展空间,同时也推进了强化传热理论和换热器的发展。
强化传热理论的工程应用根据强化传热理论…,在管的两侧范围内,需要增大传热系数较小的一侧才能有效改进总传热系数。
由于无法确定所有工况下,需要增大管内或管外的传热系数以得到最高的总传热系数,因此,强化传热理论在工程中的应用不是单一的模式,而是呈现出 3种趋势,即对管内、管外、管束整体的强化传热。
无论是那种类型的强化传热结构,都已经细化出许多更新类型,且其适用的工作环境和强化效果各异。
因此,几十年来,换热器的开发与研究始终是人们关注的课题,国内外先后推出了一系列新型高效换热器。
比如:气动喷涂翅片管换热器,焊接式板式换热器,螺旋折流板换热器,新型麻花管换热器和Titan绕丝花环换热器等。
而管壳式换热器由于应用广泛,发展也较迅速。
管壳式换热器又称列管式换热器,是以封闭在壳体中管束的壁面作为传热面的间壁式换热器。
虽然它在换热效率、结构紧凑性和金属材料消耗等方面,不如其它新型换热设备,但它具有结构坚固、操作弹性大、适应性强、可靠程度高、选材范围广、处理能力大、能承受高温和高压等特点,在换热设备中始终占有约70%的主导地位。
管壳式换热器是当前应用最广、理论研究和设计技术完善,运用可靠性良好的一类换热器,目前各国为改善该换热器的性能对其强化传热技术开展了大量的研究。
111管壳式换热器的研究和发展主要表现在两方面:一是新型高效传热管(如螺纹管、横纹管、波纹螺旋管、缩放管、绕丝花环管、异形翅片管)等的开发和应用,以强化管程传热。
浮头式换热器计算说明书
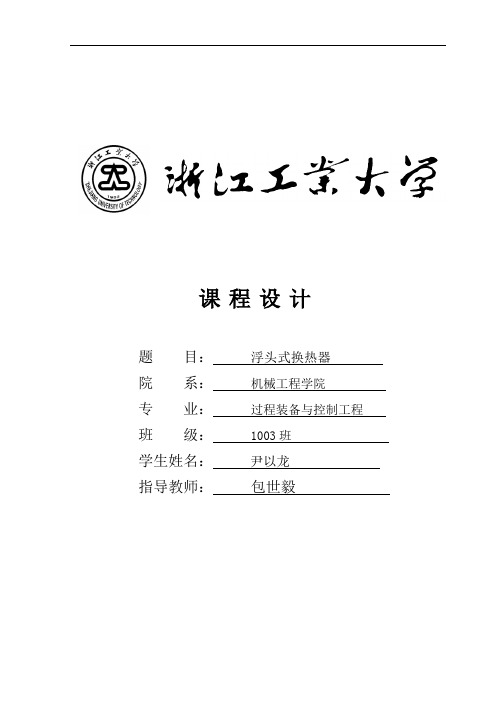
课程设计题目:浮头式换热器院系:机械工程学院专业:过程装备与控制工程班级:1003班学生姓名:尹以龙指导教师:***目录第一部分任务书 (1)第二部分计算说明书 (2)1.传热工艺计算 (2)1.1.原始数据 (2)1.2.定性温度及物性参数 (3)1.3.传热量和冷水流量 (3)1.4.有效平均温度 (3)1.5.管程传热面积计算 (4)1.6.结构初步设计 (4)1.7.壳程换热系数计算 (5)1.8.总传热系数计算 (6)1.9.结构初步设计 (7)1.10.壳程换热系数计算 (7)1.11.总传热系数计算 (8)1.12.核算管程压强降 (8)1.13.核算壳程压强降 (9)2.强度计算 (11)2.1.换热管材料及规格的选择和根数的确定 (11)2.2.确定筒体内径 (11)2.3.确定筒体壁厚 (12)2.3.1.筒体液压试验 (13)2.4.管箱封头厚度计算 (13)2.5.浮头侧封头厚度计算 (14)2.6.设备法兰的选择 (15)2.6.1.管箱侧法兰的选择 (15)2.6.2.浮头侧法兰的选择 (16)2.6.3.壳体上与浮头侧连接的法兰 (17)2.6.4.接管法兰的选择 (17)2.7.管板的设计 (18)2.8.钩圈式浮头 (22)2.8.1浮头法兰的计算 (24)2.8.2管程压力作用下浮头盖的设计 (28)2.9.浮动管板 (29)2.10.钩圈的选择 (30)2.11.折流板的选择 (31)2.12.拉杆和定距管的确定 (32)2.13.防冲板 (32)2.14.管箱短节壁厚的计算 (32)2.15.筒体、管箱的耐压试验的校核计算 (33)2.16.接管及开孔补强 (33)2.16.1 a,b孔的补强 (33)2.16.2 d,h孔的补强 (35)2.17. 支座择及应力校核 (37)2.17.1 支座的选择 (37)2.17.2 支座的应力校核 (38)2.18. 整体尺寸布局 (40)第一部分任务书一、设计题目设计题目:用水冷却煤油产品的浮头式换热器的设计二、设计条件(1)使煤油从180℃冷却到40℃,压力1.0MPa;(2)冷却剂为水,水压力为0.5MPa。
浮头式换热器设计说明书
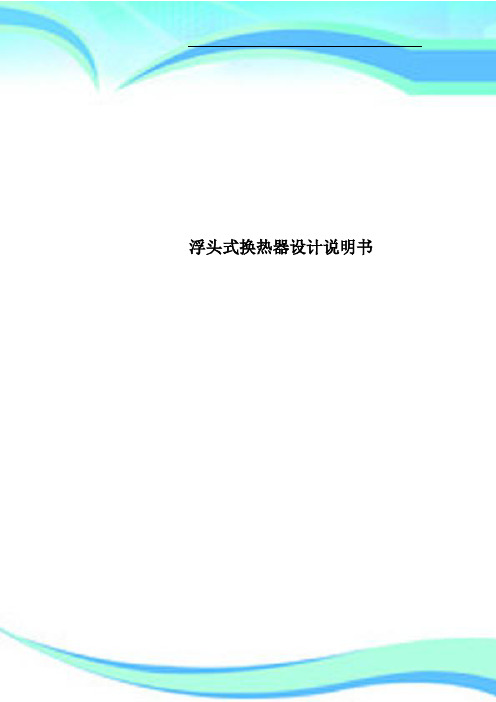
浮头式换热器设计说明书————————————————————————————————作者:————————————————————————————————日期:武汉工程大学邮电与信息工程学院毕业设计(论文)说明书论文题目 BES-900-1.0-165-4.5/25-2Ⅱ浮头式换热器设计学号 1002050314 学生姓名刘成专业班级 10过程装备与控制工程03班指导教师刘丽芳总评成绩2014年 6 月 1 日摘要 (2)Abstract (3)绪论 (4)一换热器的简单介绍 (4)二换热器的应用 (4)三管壳式换热器的分类及其特点 (4)四换热器在化学工业中的应用 (5)五换热器的选型 (7)第一章结构及强度计算 (8)1.1筒体的计算 (8)1.2管箱的结构设计 (9)1.3 浮头盖的设计 (14)1.4管板的计算 (27)1.5外头盖的计算 (32)1.6开孔补强计算 (33)1.7其他零部件设计 (36)第二章浮头式换热器的制造工艺 (41)2.1 总体制造工艺 (41)2.2 管箱、壳体、头盖的制造工艺 (41)2.3 换热管的制造工艺 (41)2.4 管板与折流板的制造工艺 (41)第三章浮头式换热器的检验、安装、使用和维修 (43)3.1换热管的水压试验 (43)3.2安装 (43)3.3使用 (44)3.4维护 (44)设计总结 (45)致谢 (46)参考文献 (47)附录 (48)换热器是将热流体的部分热量传递给冷流体的设备,又称热交换器。
换热器的应用广泛,它的主要功能是保证工艺过程对介质所要求的特定温度,同时也是提高能源利用率的主要设备之一。
换热器既可是一种单独的设备,如加热器、冷却器和凝汽器等;也可是某一工艺设备的组成部分,如氨合成塔内的热交换器。
本设计说明书是关于浮头式换热器的设计,主要是进行了换热器的结构和强度设计。
这部分主要是根据设计课题和课题给定条件进行设备内各零部件(如管箱、浮头钩圈、管板、接管、折流板、隔板、定距管等)的设计,包括:材料的选择、具体尺寸确定、确定具体位置、管板厚度的计算、浮头盖和浮头法兰厚度的计算、开孔补强计算等。
浮头式换热器设计说明书
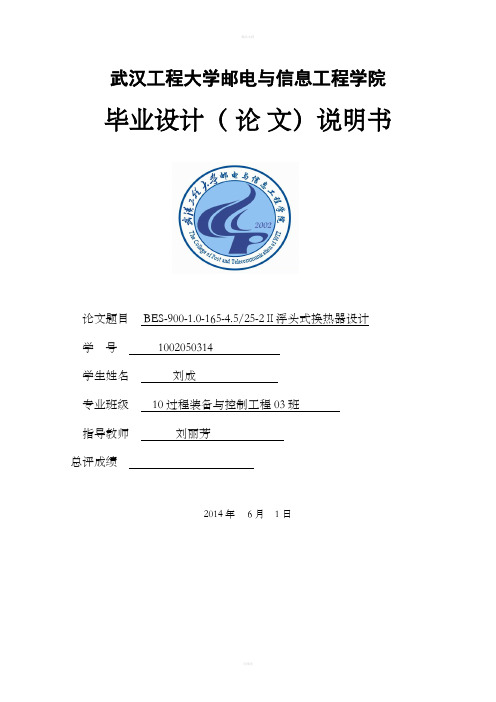
武汉工程大学邮电与信息工程学院毕业设计(论文)说明书论文题目 BES-900-1.0-165-4.5/25-2Ⅱ浮头式换热器设计学号 1002050314学生姓名刘成专业班级 10过程装备与控制工程03班指导教师刘丽芳总评成绩2014年 6 月 1 日摘要 (2)Abstract (3)绪论 (4)一换热器的简单介绍 (4)二换热器的应用 (4)三管壳式换热器的分类及其特点 (4)四换热器在化学工业中的应用 (5)五换热器的选型 (7)第一章结构及强度计算 (8)1.1筒体的计算 (8)1.2管箱的结构设计 (9)1.3 浮头盖的设计 (14)1.4管板的计算 (27)1.5外头盖的计算 (32)1.6开孔补强计算 (33)1.7其他零部件设计 (36)第二章浮头式换热器的制造工艺 (41)2.1 总体制造工艺 (41)2.2 管箱、壳体、头盖的制造工艺 (41)2.3 换热管的制造工艺 (41)2.4 管板与折流板的制造工艺 (41)第三章浮头式换热器的检验、安装、使用和维修 (43)3.1换热管的水压试验 (43)3.2安装 (43)3.3使用 (44)3.4维护 (44)设计总结 (45)致谢 (46)参考文献 (47)附录 (48)换热器是将热流体的部分热量传递给冷流体的设备,又称热交换器。
换热器的应用广泛,它的主要功能是保证工艺过程对介质所要求的特定温度,同时也是提高能源利用率的主要设备之一。
换热器既可是一种单独的设备,如加热器、冷却器和凝汽器等;也可是某一工艺设备的组成部分,如氨合成塔内的热交换器。
本设计说明书是关于浮头式换热器的设计,主要是进行了换热器的结构和强度设计。
这部分主要是根据设计课题和课题给定条件进行设备内各零部件(如管箱、浮头钩圈、管板、接管、折流板、隔板、定距管等)的设计,包括:材料的选择、具体尺寸确定、确定具体位置、管板厚度的计算、浮头盖和浮头法兰厚度的计算、开孔补强计算等。
浮头式换热器设计说明书

浮头式换热器设计说明书2021级工程实验班-设备设计说明书反应产物冷却器的设计姓名:XXX 班级:XXXX 学号:XXXXXXXXXXX摘要:本设备设计是根据AES浮头式换热器设计条件图(一)而设计的。
设备为浮头式换热器,其类型为:AES;换热器的管程介质为循环水,操作压力为:0.65MPa,操作温度(入口/出口)为:40/50℃;换热器的壳程介质为反应产物,操作压力为:0.1MPa,操作温度为(入口/出口):110/90℃;设计主要依据标准和法规为:TSG R0004-2021《固定式压力容器安全技术监察规程》、GB150.1~4-2021《压力容器》、GB151-1999《管壳式换热器》等。
对浮头式换热器进行了材料选择、结构设计和强度计算。
浮头换热器结构复杂,金属消耗大,成本较高;但是它的管束可以抽出,管、壳程方便清洗;介质间温差不受限制;可在高温、高压下工作;可用于结垢比较严重的场合;可用于管程易腐蚀场合。
易满足设计条件和经济性的要求。
关键词:换热器,强度计算,结构设计12021级工程实验班-设备设计说明书目录反应产物冷却器的设计 ------------------------------------------------------------------------------------------------- 1 目录 ----------------------------------------------------------------------------------------------------------------------- 2 第1章概述 ---------------------------------------------------------------------------------------------------------------- 4第1.1节设备的简介 --------------------------------------------------------------------------------------------- 4 第2章结构设计 --------------------------------------------------------------------------------------------------------- 6第2.1节材料的选择 --------------------------------------------------------------------------------------------- 62.1.1 壳程材料的选择 --------------------------------------------------------------------------------------- 6 2.1.2 管程材料的选择 --------------------------------------------------------------------------------------- 7 第2.2节主要结构设计 ------------------------------------------------------------------------------------------ 72.2.1 管程结构 ------------------------------------------------------------------------------------------------ 7 2.2.2 壳程结构 ----------------------------------------------------------------------------------------------- 10 2.2.3 外头盖端结构 ----------------------------------------------------------------------------------------- 13 2.2.4 容器法兰和管法兰 ---------------------------------------------------------------------------------- 14 2.2.5 支座 ----------------------------------------------------------------------------------------------------- 16第3章设计计算 -------------------------------------------------------------------------------------------------------- 17第3.1节管箱结构设计计算 ---------------------------------------------------------------------------------- 173.1.1管箱筒体 ------------------------------------------------------------------------------------------------ 17 3.1.2管箱法兰 ---------------------------------------------------------------------------------------------- 18 第3.2节平盖的结构设计计算 ------------------------------------------------------------------------------- 19 第3.3节管板的设计计算 -------------------------------------------------------------------------------------- 21 第3.4节壳程筒体结构设计计算 ---------------------------------------------------------------------------- 263.4.1 筒体设计计算 --------------------------------------------------------------------------------------- 26 3.4.2壳体法兰设计 ---------------------------------------------------------------------------------------- 26 第3.5节外头盖结构设计计算 ------------------------------------------------------------------------------- 313.5.1 外头盖筒体 ------------------------------------------------------------------------------------------ 31 3.5.2 凸型封头 --------------------------------------------------------------------------------------------- 32 3.5.3---------------------- 33 3.5.4外头盖法兰 ------------------------------------------------------------------------------------------- 38 3.5.5 浮头法兰的设计计算 ------------------------------------------------------------------------------ 42 3.5.6钩圈的设计计算 ------------------------------------------------------------------------------------- 49 3.5.7球冠形封头计算 ------------------------------------------------------------------------------------- 49 第3・6节开孔补强计算 -------------------------------------------------------------------------------------- 503.6.1管程开孔补强 ---------------------------------------------------------------------------------------- 50 3.6.2壳程开孔补强 ---------------------------------------------------------------------------------------- 51 3.6.3外头盖开孔补强 ------------------------------------------------------------------------------------- 54 第3・7节鞍座支反力计算 ---------------------------------------------------------------------------------- 54 第4章制造、安装与检验 -------------------------------------------------------------------------------------------- 55第4.1节液压试验 ----------------------------------------------------------------------------------------------- 56 第4.2节管程水压试验 ----------------------------------------------------------------------------------------- 56 第4.3节零部件的制造工艺及要求 ------------------------------------------------------------------------- 5722021级工程实验班-设备设计说明书4.3.1圆筒 ---------------------------------------------------------------------------------------------------- 57 4.3.2管箱 ---------------------------------------------------------------------------------------------------- 57 4.3.3换热管 ------------------------------------------------------------------------------------------------- 57 4.3.4管板 ---------------------------------------------------------------------------------------------------- 57 4.3.5折流板、支持板 ------------------------------------------------------------------------------------- 58 4.3.6管束的组装 ------------------------------------------------------------------------------------------- 58 第4.4节检验和验收 -------------------------------------------------------------------------------------------- 58 第5章经济性分析 ---------------------------------------------------------------------------------------------------- 59 参考文献 ------------------------------------- 60 符号说明 ------------------------------------------------------------------------------------------------------------------- 61 致谢 ------------------------------------------------------------------------------------------------------------------------- 6332021级工程实验班-设备设计说明书第1章概述第1.1节设备的简介本设备是一台单壳程四管程的AES浮头式冷却器。
- 1、下载文档前请自行甄别文档内容的完整性,平台不提供额外的编辑、内容补充、找答案等附加服务。
- 2、"仅部分预览"的文档,不可在线预览部分如存在完整性等问题,可反馈申请退款(可完整预览的文档不适用该条件!)。
- 3、如文档侵犯您的权益,请联系客服反馈,我们会尽快为您处理(人工客服工作时间:9:00-18:30)。
目录设计题目及工艺参数---------------------------------------------------1一、换热器的分类及特点---------------------------------------------------2二、结构设计-------------------------------------------------------------51、管径及管长的选择---------------------------------------------------52、初步确定换热管的根数n和管子排列方式-------------------------------53、筒体内径确定-------------------------------------------------------54、浮头管板及钩圈法兰结构设计-----------------------------------------65、管箱法兰、管箱侧壳体法兰和管法兰设计-------------------------------76、外头盖法兰、外头盖侧法兰设计---------------------------------------77、外头盖结构设计-----------------------------------------------------88、接管的选择--------------------------------------------------------------------------------------89、管箱结构设计-------------------------------------------------------810、管箱结构设计------------------------------------------------------811、垫片选择----------------------------------------------------------912、折流板------------------------------------------------------------------------------------------913、支座选取----------------------------------------------------------1014、拉杆的选择--------------------------------------------------------1315、接管高度(伸出长度)确定------------------------------------------1316、防冲板------------------------------------------------------------1317、设备总长的确定----------------------------------------------------1318、浮头法兰---------------------------------------------------------------------------------------1419、浮头管板及钩圈----------------------------------------------------14三、强度计算--------------------------------------------------------------141、筒体壁厚的计算-----------------------------------------------------142、外头盖短节,封头厚度计算-------------------------------------------153、管箱短节、封头厚度计算 --------------------------------------------164、管箱短节开孔补强的核校 --------------------------------------------165、壳体压力试验的应力校核---------------------------------------------166、壳体接管开孔补强校核-----------------------------------------------177、固定管板计算-------------------------------------------------------188、无折边球封头计算 --------------------------------------------------199、管子拉脱力计算-----------------------------------------------------20四、设计汇总-----------------------------------------------------21五、设计体会--------------------------------------------------------------21参考文献--------------------------------------------------------------22设计题目:浮头式换热器工艺参数:管口表:符号公称直径(mm)管口名称a 130 变换气进口b 130 软水出口c 130 变换气出口d 130 软水进口e 50 排尽口设备选择原理及原因:浮头式换热器的结构较复杂,金属材料耗量较大,浮头端出现内泄露不易检查出来,由于管束与壳体间隙较大,影响传热效果。
该换热器的管束可以从壳体中抽出,便于清洗管间和管内,管束可以在壳体内自由伸缩,不会产生热应力。
浮头式换热器适用于较高的压力下工作,适用于壳体壁温于管壁温差较大或壳程流体易结垢的场合。
本设计的管程壁温和壳程壁温温差较大,工作压力属于中上,且管程内物料为重油,壳程内为轻汽油。
故本设计选择浮头式换热器。
一、换热器的分类及其特点换热器是一种实现物料之间热量传递的节能设备,是各种工业部门最常见的通用热工设备,广泛应用于化工、能源、机械、交通、制冷、空调及航空航天等各个领域。
换热器不仅是保证某些工艺流程和条件而广泛使用的设备,也是开发利用工业二次能源,实现余热回收和节能的主要设备。
工业生产中使用的换热器型式很多,而且仍在不断发展。
按使用目的不同,换热器可分为加热器、冷凝器、蒸发器和再沸器等。
由于使用的条件和工作的环境不同,换热器又有各种各样的型式和结构。
按传热原理和实现热交换的方法,换热器可分为间壁式、混合式和蓄热式3类,其中以间壁式换热器应用最为普遍。
间壁式换热器种类很多,如夹套式换热器、套管式换热器、蛇管式换热器、板式换热器、板翅式换热器和列管式换热器,列管式换热器又叫做管壳式换热器,是目前应用最广泛的一种换热器。
管壳式换热器的应用已有十分悠久的历史。
管壳式换热器是一种传统的标准换热设备,广泛应用于化工、石油、制冷、核能和动力等工业。
由于世界性的能源危机,工业生产中对换热器的需求量越来越多,对换热器的质量要求也越来越高。
在近代的许多化工过程中,如裂解、合成和聚合等,大都要求在高温高压下进行,有的压力高达250 MPa,温度则高达750℃,又腐蚀的情况下,实现换热更困难。
而管壳式结构具有选材范围广、换热表面清洗方便、适应性强、处理能力大、能承受高温和高压等特点。
一方面,伴随着现代化工厂生产规模的日益增大,换热设备也相应地向大型化方向发展,以降低动力消耗和余属消耗;另一方面,随着精细化工的迅速崛起,换热设备也有向小而精方向发展的趋势。
管壳式结构的换热器能满足这样的要求。
近几十年来,随着紧凑式换热器(板式、板翅式等)、热管式换热器和直接接触式换热器等的发展,管壳式换热器面临着挑战,在某些场合,管壳式换热器已被一些新型换热器所取代,但由于管壳式换热器具有高度的可靠性和广泛的适应性,它的产量至今仍占统治地位。
目前工业装置中管壳式换热器的用量占全部用量的70%。
管壳式换热器结构也有较大的改进和发展,从原来传统的弓形隔板加光滑管的结构,发展为其它类型的管间支撑物加强化管的结构,由于这些结构上的改进,使得管壳式换热器的传热与流体阻力性能有了明显的改善,加上本身固有的优点,如耐高温、耐高压、结构简单和清洗方便等,使得管壳式换热器在激烈的换热器竞争中得以生存和发展。
管壳式换热器主要包括固定管板式、浮头式、U形管式、填料函式等结构。
根据介质的种类、压力、温度、污垢,以及管板与壳体的连接方式、换热管的形式与传热条件、造价和维修检查情况等,结合各种结构形式的特点选择、设计和制造各种管壳式换热器。
图1.1固定管板式换热器的典型结构(1) 固定管板式换热器固定管板式换热器两端管板,采用焊接方式与壳体连接固定。
固定管板式换热器由管箱、壳体、管板和管子等零部件组成,如图1.1所示。
其结构简单紧凑,排管比较多,在相同换热器公称直径的情况下面积比较大,制造简单,但在最后一道壳体与管板的焊缝无法进行无损检测。
其优点是:①相同公称直径下,传热面积比浮头式换热器大20%~30%;②旁路泄露比较小;③锻件使用比较少;④没有内部泄露的存在。
缺点是:①壳体和管子壁温差一般小于等于50℃,大于50℃时应在壳体上设置膨胀节;②管板与管头之间容易产生温差应力而损坏;③壳程无法进行机械清洗;④管子腐蚀后造成连同壳体也报废,壳体部件寿命取决于管子寿命,因此设备寿命相对比较低;⑤不适用于壳程容易结垢的场合。
(2) 浮头式换热器浮头式换热器的一端管板与壳体固定,一端的管板可在壳体内自由浮动,壳体和管板对热膨胀是自由的,因此当两种介质温差较大时,管束与壳体之间不产生温差应力。
浮头端设计成可拆结构,使管束能容易地插入或抽出壳体,这样方便清洗和检修。
由于该换热器结构复杂,而且浮动端小盖在操作时无法得知其泄露情况,所以在安装时应特别注意其密封,如图1.2所示。
图1.2浮头式换热器(3) U形管式换热器该换热管两端是固定在同一块管板上的,结构简单,造价低。
管束可抽出,外壁便于清洗,但换热管清洗困难,所以介质必须是清洁且不结污垢的物料。
由于结构不紧凑的原因,影响传热效率,换热也不均匀。
一般用于高温高压的场合,壳程内一般按工艺要求设置折流板和纵向隔板,如图1.3所示。
图1.3 U形管式换热器的典型结构(4) 填料函式换热器填料函式换热器适用于壳程压力不高、较严重腐蚀的介质、温差较大且经常要更换管束的冷却器。