弹簧线设计与生产工艺
弹簧制造工艺

第五讲:弹簧结构分析与制造工艺(第四章:弹簧制造工艺)2014-8-3,上海讲座用第一节:概述一:弹簧在电器产品中的应用电器中常用的弹簧有:※:螺旋弹簧:(1:压缩弹簧;2:垃伸弹簧;3:扭转弹簧;4:片黄)1:压缩弹簧:在交流直动式接触器中常常采用压缩弹簧-主要是触头压缩弹簧和铁心反力弹簧。
如下特性。
电器的负载特性(机械特性)是电器的重要特性之一。
作用在衔铁上的机械力和衔铁行程关系特性P或F=称为机械特性,也称反力特性。
弹性元件(螺旋弹簧和簧片)构成。
弹簧构成电磁电器机械特性(反力特性)如图所示此特性是由作用于衔铁的机械力和作用于触头的压力组合而成的特性.在断路器上,触头也是采用压缩弹簧,如下所示:2:垃伸弹簧在断路器四连杆机构多数采用,拉伸弹簧:在直流接触器中的衔铁反力弹簧是拉伸弹簧。
3:扭转弹簧: 脱扣器上采用的扭簧。
4:片黄:在继电器中广泛采用。
从上述情况看,弹簧成为我们电器中一个十分重要的零件。
它的质量直接影响我们各种电器的性能。
二:弹簧的基本性能弹簧的基本性能是在载荷作用下产生形变,卸载时释放能量恢复原形;加载变形过程遵循一定的规律。
1:弹簧的特性线:其特性就是:载荷P(M)与变形F (ϕ)之间的关系曲线成为弹簧的特性线,如图4-1所示。
弹簧的特性线大致有三种类型:①直线型;②渐增型;③渐减型。
有些弹簧的特性线是上述两种或三种的组合(图4-2),称为组合型特性线。
度后,变为渐增型;蝶形弹簧的特性线(图4-2b)开始为渐减型,后为渐增型,整个特性线呈S 形;图4-2d 是两个不同高度压缩弹簧组合的特性线,加载开始只有一个弹簧承受载荷,当加载到一定程度时,第二个弹簧也开始承受载荷,特性线成为两个弹簧的特性线,因而其斜率发生了改变.拉伸弹簧的特性线基本上是一条直线,由于其线性好,故广泛用于电器元件和计量器具中.图2 组合型特性a)压缩弹簧特性曲线,b)碟形弹簧特性c)圆锥弹簧特性d)两个压缩弹簧组合特性曲线 2.弹簧刚度(有两种表述方法)弹簧所受载荷P 与变形量F 之比,即产生单位变形量所需荷载称为弹簧刚度.对于压缩和拉伸弹簧的刚度为f P P=' (4-1a) 式中'P ── 压缩和拉伸弹簧刚度(mm N /); P ── 弹簧所受负荷力(N);f ── 弹簧的变形量(mm).对于扭转弹簧的刚度为ϕM M=' (4-2a) 式中'M ── 扭转弹簧的刚度(cm N /);M ── 扭转弹簧的扭矩(cm N ⋅);ϕ── 扭转弹簧的扭转角.特性线为渐增型弹簧,其刚度随着载荷的增加而增大;渐减型弹簧,其刚度随着载荷的增加而减小.而对于直线型弹簧,其刚度不随载荷变化而变化,即常数==FP P '或: 3'8ncGd y P F P P === 38Pcy Gd n ⋅= (4-1b) 常数==ϕMM ' (4-2b) 因此,对于具有直线型特性线的弹簧,其刚度也称为弹簧常数. 弹簧的特性线对于设计和选用弹簧的类型起着重要的指导作用.设计弹簧时可用分析计算及实验的方法找出它的特性线.但即使是最精确得计算,其结果和实际的数值也总会有一定的差异.这是由于弹簧在制造过程中不可避免的存在工艺差异,所用材料组织也并非绝对均匀之故.因此,在设计弹簧时必须经过反复试验,修改尺寸和参数,使之达到理想的结果.三:弹簧的分类 弹簧的类型很多,分类方法不一,按其形状和结构可分为以下几种类型。
弹簧工艺介绍
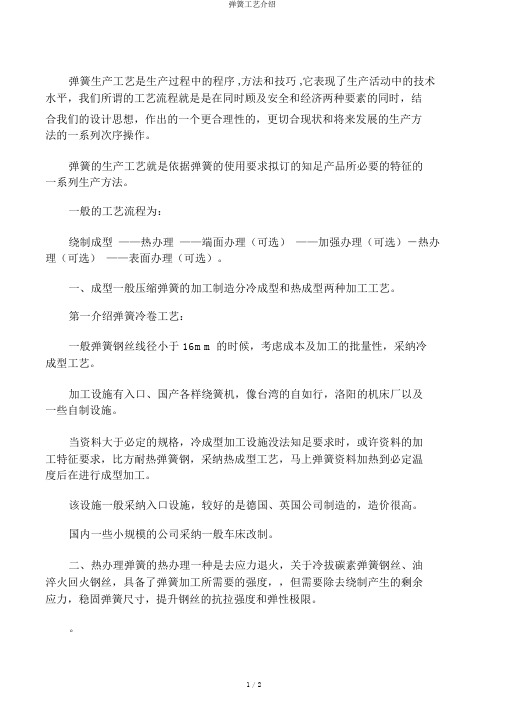
弹簧生产工艺是生产过程中的程序 ,方法和技巧 ,它表现了生产活动中的技术水平,我们所谓的工艺流程就是是在同时顾及安全和经济两种要素的同时,结合我们的设计思想,作出的一个更合理性的,更切合现状和将来发展的生产方法的一系列次序操作。
弹簧的生产工艺就是依据弹簧的使用要求拟订的知足产品所必要的特征的一系列生产方法。
一般的工艺流程为:绕制成型——热办理——端面办理(可选)——加强办理(可选)-热办理(可选)——表面办理(可选)。
一、成型一般压缩弹簧的加工制造分冷成型和热成型两种加工工艺。
第一介绍弹簧冷卷工艺:一般弹簧钢丝线径小于 16mm 的时候,考虑成本及加工的批量性,采纳冷成型工艺。
加工设施有入口、国产各样绕簧机,像台湾的自如行,洛阳的机床厂以及一些自制设施。
当资料大于必定的规格,冷成型加工设施没法知足要求时,或许资料的加工特征要求,比方耐热弹簧钢,采纳热成型工艺,马上弹簧资料加热到必定温度后在进行成型加工。
该设施一般采纳入口设施,较好的是德国、英国公司制造的,造价很高。
国内一些小规模的公司采纳一般车床改制。
二、热办理弹簧的热办理一种是去应力退火,关于冷拔碳素弹簧钢丝、油淬火回火钢丝,具备了弹簧加工所需要的强度,,但需要除去绕制产生的剩余应力,稳固弹簧尺寸,提升钢丝的抗拉强度和弹性极限。
还有一种钢丝强度很低,需要对绕制的弹簧进行淬火、回火办理。
三、端面办理为了保证压缩弹簧的垂直度,使两支承圈的端面与其余部件保持接触,减少挠度,保障主机特征,一般压缩弹簧的两头面均要进行磨削加工。
一般均采纳自动磨削办理。
四、加强办理为了使弹簧表层产生与工作应力相反的剩余应力,提升弹簧的承载能力、使用寿命,在加工制造过程中采纳的一些加强举措,比方强压、立定办理、喷丸办理五、表面办理:电泳漆、喷塑、电镀等为了提升弹簧的耐腐化能力,或许雅观性,对加工后的弹簧表面进行办理。
常用的表面办理有电泳漆、喷塑、电镀等。
钢板弹簧生产工艺

钢板弹簧生产工艺钢板弹簧是一种弹性元件,广泛应用于工业制造和机械设备中。
其主要特点是可以储存和释放能量,具有较高的弹性和耐久性。
下面介绍钢板弹簧的生产工艺。
第一步:原材料准备钢板弹簧的原材料主要是优质碳素钢板。
在生产过程中,需要根据弹簧的用途和要求选择适合的钢板。
钢板会经过切割、裁剪和修整等工艺,确保其大小和形状符合要求。
第二步:弯曲加工接下来,钢板将会经过弯曲加工。
弯曲加工是钢板弹簧生产中最重要的一步,它决定了弹簧的形状和性能。
弯曲加工可以通过机械加工方法或者热加工方法进行。
机械加工方法包括弯折、滚轧和冷弯等,而热加工方法主要是指热处理。
在弯曲加工过程中,需要根据设计要求将钢板进行弯曲、压缩和拉伸等操作,以形成所需形状和弹性。
第三步:热处理完成弯曲加工后,弹簧会经过热处理,以提高其强度和弹性。
热处理是通过加热和冷却来改变钢板的组织和性能的方法。
具体来说,弹簧会先被加热到一定温度,然后进行保温,最后快速冷却。
这样可以使钢板获得更均匀的组织结构和更好的弹性性能。
第四步:表面处理表面处理是为了提高弹簧的耐蚀性和表面光洁度。
常见的表面处理方法包括镀锌、镀镍、喷涂等。
这些方法可以有效地增加弹簧的寿命和耐候性,提高其在不同环境下的使用性能。
第五步:组装和检测最后,弹簧会经过组装和检测。
组装包括将弹簧和其他零部件进行装配,确保其稳定性和可靠性。
检测是为了确保弹簧达到设计要求和产品质量标准。
常见的检测方法包括外观检查、尺寸测量和性能测试等。
综上所述,钢板弹簧的生产工艺包括原材料准备、弯曲加工、热处理、表面处理、组装和检测等环节。
每个环节都非常重要,直接影响到弹簧的性能和质量。
只有在严格遵循工艺流程的情况下,才能生产出高质量的钢板弹簧。
弹簧加工工艺
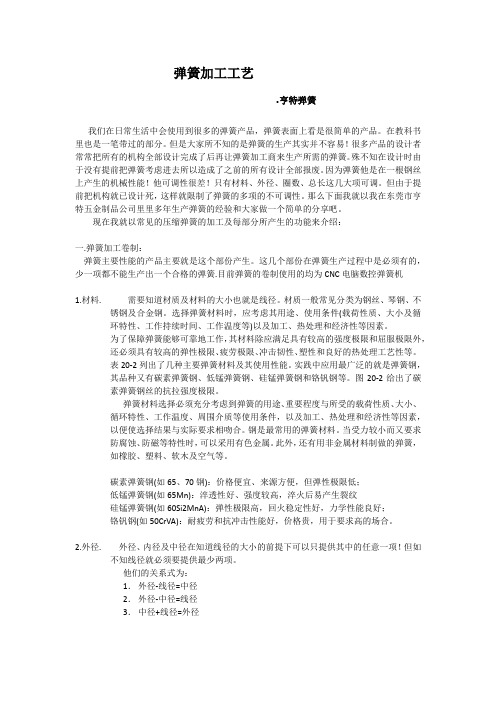
弹簧加工工艺.亨特弹簧我们在日常生活中会使用到很多的弹簧产品,弹簧表面上看是很简单的产品。
在教科书里也是一笔带过的部分。
但是大家所不知的是弹簧的生产其实并不容易!很多产品的设计者常常把所有的机构全部设计完成了后再让弹簧加工商来生产所需的弹簧。
殊不知在设计时由于没有提前把弹簧考虑进去所以造成了之前的所有设计全部报废。
因为弹簧他是在一根钢丝上产生的机械性能!他可调性很差!只有材料、外径、圈数、总长这几大项可调。
但由于提前把机构就已设计死,这样就限制了弹簧的多项的不可调性。
那么下面我就以我在东莞市亨特五金制品公司里里多年生产弹簧的经验和大家做一个简单的分享吧。
现在我就以常见的压缩弹簧的加工及每部分所产生的功能来介绍:一.弹簧加工卷制:弹簧主要性能的产品主要就是这个部份产生。
这几个部份在弹簧生产过程中是必须有的,少一项都不能生产出一个合格的弹簧.目前弹簧的卷制使用的均为CNC电脑数控弹簧机1.材料. 需要知道材质及材料的大小也就是线径。
材质一般常见分类为钢丝、琴钢、不锈钢及合金钢。
选择弹簧材料时,应考虑其用途、使用条件(载荷性质、大小及循环特性、工作持续时间、工作温度等)以及加工、热处理和经济性等因素。
为了保障弹簧能够可靠地工作,其材料除应满足具有较高的强度极限和屈服极限外,还必须具有较高的弹性极限、疲劳极限、冲击韧性、塑性和良好的热处理工艺性等。
表20-2列出了几种主要弹簧材料及其使用性能。
实践中应用最广泛的就是弹簧钢,其品种又有碳素弹簧钢、低锰弹簧钢、硅锰弹簧钢和铬钒钢等。
图20-2给出了碳素弹簧钢丝的抗拉强度极限。
弹簧材料选择必须充分考虑到弹簧的用途、重要程度与所受的载荷性质、大小、循环特性、工作温度、周围介质等使用条件,以及加工、热处理和经济性等因素,以便使选择结果与实际要求相吻合。
钢是最常用的弹簧材料。
当受力较小而又要求防腐蚀、防磁等特性时,可以采用有色金属。
此外,还有用非金属材料制做的弹簧,如橡胶、塑料、软木及空气等。
弹簧的设计和选择
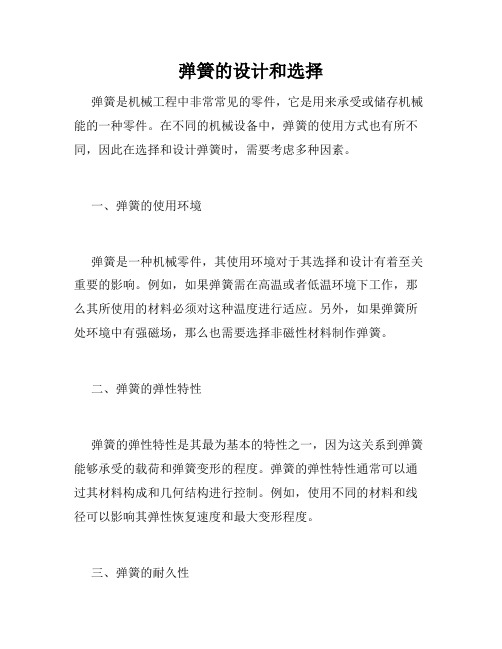
弹簧的设计和选择弹簧是机械工程中非常常见的零件,它是用来承受或储存机械能的一种零件。
在不同的机械设备中,弹簧的使用方式也有所不同,因此在选择和设计弹簧时,需要考虑多种因素。
一、弹簧的使用环境弹簧是一种机械零件,其使用环境对于其选择和设计有着至关重要的影响。
例如,如果弹簧需在高温或者低温环境下工作,那么其所使用的材料必须对这种温度进行适应。
另外,如果弹簧所处环境中有强磁场,那么也需要选择非磁性材料制作弹簧。
二、弹簧的弹性特性弹簧的弹性特性是其最为基本的特性之一,因为这关系到弹簧能够承受的载荷和弹簧变形的程度。
弹簧的弹性特性通常可以通过其材料构成和几何结构进行控制。
例如,使用不同的材料和线径可以影响其弹性恢复速度和最大变形程度。
三、弹簧的耐久性弹簧的耐久性对于机械设备的寿命和效率有着非常重要的影响,因为弹簧一旦失效,很可能会导致机械设备失效。
为了保证弹簧的耐久性,应该采用优质的材料和制造工艺。
此外,定期检查或更换弹簧,也是确保机械设备正常运行的一个重要环节。
四、弹簧的设计弹簧的设计是一个非常重要的环节,因为它直接关系到弹簧的弹性和承载能力。
在进行弹簧的设计时,首先需要确认弹簧的用途和工作条件。
然后,根据工作条件和弹簧的形状、尺寸等因素,进行合理的构造设计。
在实际制作过程中,还需要考虑到弹簧的制造工艺和加工精度等问题。
五、弹簧的选择选择适合的弹簧不仅直接关系到机械设备的性能和寿命,还牵涉到成本和可维护性等因素。
在选择弹簧时,需要首先确认机械设备的工作条件和要求,并根据这些因素选择合适的弹簧类型和材料。
有些情况下,甚至需要进行弹簧的定制设计和制造。
从选择和设计弹簧的角度来看,弹簧是一种非常重要的机械零件。
无论是在工业生产中还是日常生活中,都可以看到它的身影。
因此,对于我们来说,学习弹簧的选择和设计,不仅可以帮助我们更好地理解机械设备的工作原理,还能够提高我们的机械制造能力和水平。
弹簧钢丝生产工艺技术

弹簧钢丝生产工艺技术quotquotquotquot第十三篇弹簧钢丝生产工艺技术第一章国内外重要用途弹簧钢丝发展状况弹簧是一种常用的弹性工作元件,也是各种机械设备和仪器仪表上的基础零件。
它在周期性弯曲、扭转交变应力下工作,能产生较大的弹性变形,因而能把机械能或动能转变成变形能,或把变形能转变为动能、机械能。
它适用于缓冲或减震、机械的储能以及控制运动方向(如气门、离合器、制动器、调节器)。
弹簧在各种工业领域及人们日常生活中具有无法取代的作用。
各种机械、电器、仪器、仪表离不开弹簧,一辆轿车上弹簧的种类就有上百种。
家庭中的弹簧更是不计其数,只要用电池就要用弹簧。
从尺寸和重量上看,小弹簧只有米粒大小,而大弹簧的重量有几十公斤;价值上,别针只值几分钱,而航天飞行器上的专用弹簧价值几万元。
制造弹簧的主要原料是弹簧钢丝。
在线材制品生产中,弹簧钢丝无论在产品数量上还是品种上都占有很重要的地位。
数量上占优质钢丝产量的一半以上,品种上按不同的生产工艺、化学成分和用途可分为quot余种。
按生产工艺可分为冷拉、退火、油回火;按化学成分可分为碳素、合金、不锈钢;按用途可分为非机械弹簧、机械弹簧、气门弹簧。
既能制造普通弹簧,也能制造高级重要弹簧。
在使用上能适应低温、中温和高温工作环境,还能用于静载荷或动载荷。
其产量之高、品种之多、用途之广,是其他钢丝品种无可比拟的。
使用中对弹簧的要求是尺寸精度高,抗松弛性能好,疲劳强度高,能够在应力负荷下不产生松弛,并且在规定的疲劳周期内不会出现早期失效。
这就对弹簧钢丝的力学性能,主要是弹性和韧性,提出了相应的要求。
??quot??第一章国内外重要用途弹簧钢丝发展状况第一节弹簧钢丝的力学性能弹簧钢丝的力学性能本质上是由加工工艺决定的,其次是由材料中的碳和锰含量以及材料规格决定的。
弹簧钢丝的应用多半需要卷成螺旋弹簧,延展性是至关重要的。
抗拉强度本身并不重要,但它是弹性极限的可靠度量,是弹簧应用中的一个控制因素。
弹簧线生产工艺

弹簧线生产工艺
弹簧线是用来制作弹簧的材料。
弹簧线的生产工艺包括原材料准备、热处理、拉丝、表面处理等步骤。
首先,原材料准备是弹簧线生产的第一步。
通常情况下,弹簧线采用高品质的碳钢或合金钢制成。
在生产之前,原材料需要经过筛选和预处理,以确保其质量符合要求。
接下来,原材料需要经过热处理过程。
这一步骤是为了提高材料的强度和硬度,以适应不同类型的弹簧的使用需求。
热处理过程一般包括两个步骤:淬火和回火。
淬火是通过快速加热和快速冷却来提高材料的硬度。
回火则是通过加热和缓慢冷却来减轻材料的硬度,增加其韧性。
拉丝是弹簧线生产的关键步骤之一。
通常情况下,原材料会经过多道次的拉丝过程,以逐步降低其直径。
拉丝的目的是为了提高弹簧线的强度和韧性,并且使其表面光滑并且具有一致的直径尺寸。
最后,弹簧线需要进行表面处理以提高其耐腐蚀性和外观质量。
常见的表面处理方法包括镀锌、搪塑和镀铬等。
其中,镀锌是最常用的表面处理方法,通过在弹簧线表面镀一层锌来提高其耐腐蚀性能。
总之,弹簧线的生产工艺经过原材料准备、热处理、拉丝和表面处理等多个步骤。
每一步骤都十分关键,对最终产品的质量和性能有着重大的影响。
因此,在生产过程中需要严格遵守相
关的工艺要求和质量检验标准,以确保生产出符合要求的高品质弹簧线。
弹簧生产工艺流程

弹簧生产工艺流程弹簧是一种机械零件,常用于各种机械设备中,具有很广泛的应用。
下面是一篇关于弹簧生产工艺流程的文章,大致介绍了弹簧的生产过程。
弹簧生产工艺流程弹簧的生产工艺流程是指在制作弹簧的整个过程中所需经过的步骤和工艺,下面就为大家详细介绍一下弹簧生产的工艺流程。
1. 材料准备: 弹簧的原材料一般为钢线或不锈钢线,生产之前需要对材料进行检验、筛选和准备工作。
首先要检查原材料的质量,确保其符合生产要求,并采取相应的处理措施,如抛光、退火等,使原材料变得更加适合制作弹簧。
2. 弹簧设计: 根据客户需求和应用要求,设计合适的弹簧结构和尺寸。
弹簧的设计包括确定弹簧的形状、直径、线径、圈数、材料等参数,并根据弹力需求计算和确定弹簧的初压和工作压缩量。
3. 弹簧成型: 弹簧成型是指将材料按照设计要求进行形状变换的过程。
一般情况下,弹簧生产使用机械设备完成成型,根据弹簧的形状和尺寸,选择合适的机械设备,并调整设备参数,使得成型的弹簧符合设计要求。
4. 热处理: 热处理是使钢材经过适当的加热和冷却过程,改变结构和性能的方法。
对于某些弹簧而言,热处理是必不可少的,如退火、淬火等。
热处理可以提高弹簧的强度、耐磨性和耐腐蚀性能。
5. 表面处理: 表面处理是为了提高弹簧的外观和性能。
根据需要,可以进行抛光、喷砂、电镀等工艺,以增加弹簧的光泽度和外观质量,并提高其耐腐蚀性。
6. 弹簧检测: 弹簧生产完成后,需要进行严格的质量检测。
常规的检测手段包括外观检查、尺寸测量、力学性能测试等。
检测可以确保弹簧的质量符合设计要求,并对检测不合格的弹簧进行处理。
7. 包装运输: 检测合格的弹簧进行包装,并妥善保护防止损坏。
根据弹簧的尺寸和重量,选择合适的包装方式和运输工具,以确保产品安全运输到客户手中。
综上所述,弹簧的生产工艺流程包括材料准备、弹簧设计、弹簧成型、热处理、表面处理、弹簧检测和包装运输等环节。
每个环节都需要严格控制和操作,以确保产品质量和制造效率。
奥氏体不锈钢弹簧钢丝生产工艺流程

奥氏体不锈钢弹簧钢丝生产工艺流程:1)流程图:盘条表面处理入库包装检验2)简述:盘条:从上海宝钢等钢厂采购回原料后(Φ5.5—11mm)需进厂检验,包括表面(是否存在结疤、裂纹、折叠、耳子等缺陷)和尺寸检验,还包括力学性能检验,不同炉号原料进行化学元素分析抽检。
表面处理:盘条或经过固溶处理的钢丝沾皮膜剂后烘干,皮膜剂的作用是在钢丝表面形成一层粗糙、多孔、能吸附和携带拉丝粉的载体,拉丝时借助这层润滑载体将拉丝粉带入模具中。
皮膜剂使用为外购指定厂家。
拉丝:依靠冷加工强化达到标准规定或客户要求的强度。
在拉丝前根据其冷加工强化系数,计算总减面率,确定成前尺寸。
成品需经过多道次拉拔,使用6/600、8/450直进式拉丝机。
拉丝模的使用:一般成品线径≥2.0mm以上采用硬质合金模,线径<2.0mm时采用钻石模;拉丝粉的使用:一般粗拔时前2或3道模使用钙皂拉丝粉,其余道次使用钠皂。
固溶处理:采用管式炉将钢丝加热到1000—1100℃左右,保温一段时间后快速淬水冷却,以消除加工硬化,钢丝固溶为连续处理。
检验:主要包括钢丝表面质量、尺寸公差、弹高弹宽及力学性能等项目,分操作工自检及质检员专检两部分,最终由质检员对产品质量进行判定。
包装:包装工根据质检员判定结果,将合格、不合格产品分开。
包装前,清点产品的数量、核对钢号、炉号、规格等,并写好标牌,再使用打包机器,根据产品的不同包装要求进行包装,保证产品在运输过程中不松散。
入库:包装完毕的产品要及时入库,入库要准确过磅,由库管员核对实物的相关信息。
生产全过程贯彻实施GB/T19001-2008《质量管理体系要求》,操作工及质检员按照质量体系文件《作业指导书》内容要求执行。
弹簧加工工艺流程

弹簧加工工艺流程1.弹簧设计:首先需要对弹簧的设计进行规划,包括确定弹簧的形状、尺寸、材料选择等。
设计师通常会使用计算机辅助设计软件来完成这个过程。
设计的目标是确保弹簧能够满足所需的弹性性能和力学特性。
2.原材料准备:弹簧加工的原材料通常是弹簧钢丝。
在加工过程中,原材料的质量和尺寸精度对最终产品的性能有很大影响。
因此,需要对原材料进行检查和筛选,确保其符合设计要求。
一般来说,原材料应该是均匀、无缺陷和无应力的。
3.弹性冷加工:弹簧钢丝通常需要进行弹性冷加工,以使其具有所需的形状和弹性性能。
这个过程通常包括拉拔、旋压和卷制等操作。
在拉拔过程中,将钢丝通过模具逐渐拉伸,使其截面积减小,长度增加,以获得所需的直径和硬度。
旋压是通过将钢丝在模具上旋转来增加其强度和弹性。
卷制是将钢丝从线材形成为弹簧的过程,通过自动或半自动卷弹簧机来完成。
4.热处理:为了提高弹簧的强度和耐磨性,通常需要进行热处理。
热处理一般包括两个步骤:回火和淬火。
回火是将已经制成的弹簧加热到适当温度,然后冷却,以减轻内部应力和提高韧性。
淬火是将回火后的弹簧加热到较高温度然后迅速冷却,以提高强度和硬度。
热处理过程需要严格控制温度和时间,以确保产品质量。
5.表面处理:弹簧通常需要进行表面处理,以提高其耐腐蚀性和装饰性。
常用的表面处理方法包括镀锌、镀镍、喷涂等。
镀锌是将弹簧浸入含有锌的溶液中,通过化学反应在表面形成一层保护膜,以防止腐蚀。
镀镍是将弹簧浸入含有镍的溶液中,以增加其硬度和耐磨性。
喷涂是将特殊涂料喷洒在弹簧表面,以改善其外观和保护性能。
6.检验和质量控制:在弹簧加工过程的各个阶段,都需要进行检验和质量控制,以确保产品符合设计要求和客户需求。
常用的检验方法包括外观检查、尺寸测量、硬度测试等。
质量控制包括对每个加工步骤的参数监控和记录,以及对最终产品的全面检查。
总之,弹簧加工工艺流程是一个复杂的过程,需要严格的控制和监控。
具备强大的技术实力和质量管理能力的企业可以通过流程的优化和创新,提高生产效率和产品质量,从而为客户提供更好的产品和服务。
弹簧加工制作工艺知识学习

弹簧的材料
常用金属弹簧材料有: (1)钢线 (2)琴钢丝 (3)高碳素弹簧钢丝 (4)不锈钢丝 (5)可焊不锈钢丝 (6)镀镍线 (7)镀锌线 (8)磷铜线
弹簧回火的目的
(1)消除弹簧淬火后的内应力 (2)稳定弹簧的组织和几何参数尺寸 (3)获得所需要的机械性能
弹簧清洗的目的
主要是用于不锈钢弹簧钢丝 (1)脱脂 (2)除油污 (3)增强质感和美观
它们的形状不同,而且就它们各自就有很 多种不同形状,因材料性能—硬度、人性 等的不同而不同。切断用的刀,刀刃上往 往设有凹口,这样切出来的端面毛刺少。
回火处理会使料件收缩,即角度缩小,节 距变小。所以,弹簧制作师傅编制制作程 序时,会把角度参数和节距参数适当地设 计小一些。
弹簧断面需要磨平,形成一个平面与弹簧 轴垂直。这一步是靠“端面磨簧机”来完 成的。机器的大概原理是这样的:主要由 中间一放置盘,上下分别两砂轮盘组成
弹簧加工制作工艺学习
弹 簧的定义
弹簧:是利用材料的弹性形变进行缓冲、 复位、储能的机械零件。
弹簧的作用
(1)储能和作为动力 (2)避振和缓冲 (3)载荷 (4)测力 (5)加固
弹 簧的 种类
弹簧的种类很多,一般按结构或形状分, 有螺旋弹簧、板弹簧、碟形弹簧、扭杆弹 簧、涡卷弹簧、片状弹簧、环形弹簧、平 卷弹簧、恒力弹簧。按变形状况分有压缩 弹簧、拉伸弹簧、扭转弹簧、按材料分有 金属弹簧和非金属弹簧 。
机加 定 磨头
工成 型 型
手工
成 包品顾 装出客
货
以上工艺中每个流程都需要检验合
格后才能进入下一个流程
调试好的刀具
为了能更好的理解弹簧加工过程,现场截取了一些图片:
图一:调试好的机器在生产加工弹簧半成品
碟形弹簧的计算设计及制造
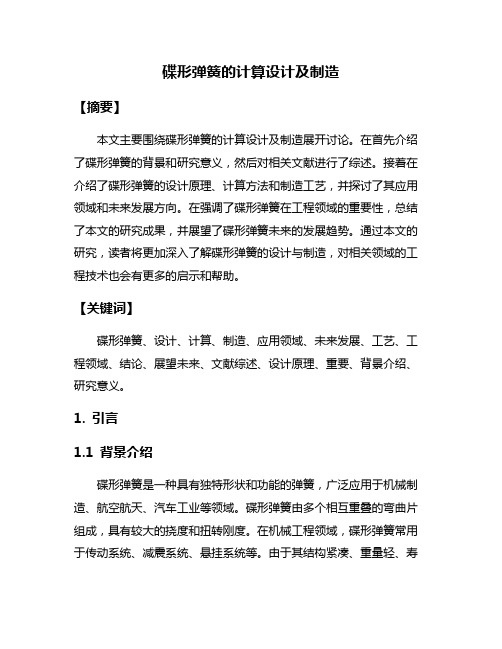
碟形弹簧的计算设计及制造【摘要】本文主要围绕碟形弹簧的计算设计及制造展开讨论。
在首先介绍了碟形弹簧的背景和研究意义,然后对相关文献进行了综述。
接着在介绍了碟形弹簧的设计原理、计算方法和制造工艺,并探讨了其应用领域和未来发展方向。
在强调了碟形弹簧在工程领域的重要性,总结了本文的研究成果,并展望了碟形弹簧未来的发展趋势。
通过本文的研究,读者将更加深入了解碟形弹簧的设计与制造,对相关领域的工程技术也会有更多的启示和帮助。
【关键词】碟形弹簧、设计、计算、制造、应用领域、未来发展、工艺、工程领域、结论、展望未来、文献综述、设计原理、重要、背景介绍、研究意义。
1. 引言1.1 背景介绍碟形弹簧是一种具有独特形状和功能的弹簧,广泛应用于机械制造、航空航天、汽车工业等领域。
碟形弹簧由多个相互重叠的弯曲片组成,具有较大的挠度和扭转刚度。
在机械工程领域,碟形弹簧常用于传动系统、减震系统、悬挂系统等。
由于其结构紧凑、重量轻、寿命长等优点,碟形弹簧逐渐成为各类机械设备中不可或缺的部件之一。
随着科技的进步和工业的发展,碟形弹簧的设计与制造也日益受到重视。
有效地设计和制造碟形弹簧,不仅可以提高机械设备的性能和可靠性,还可以节约成本和减少资源浪费。
深入研究碟形弹簧的计算设计及制造工艺,对于推动工程领域的发展具有重要意义。
本文旨在系统总结碟形弹簧的设计原理、计算方法、制造工艺、应用领域及未来发展方向,旨在为相关研究提供参考,促进碟形弹簧技术的进步和应用。
1.2 研究意义碟形弹簧在机械传动系统中起着重要作用,其设计合理与否直接影响到传动系统的稳定性和性能。
通过研究碟形弹簧的设计原理和计算方法,可以帮助工程师更加准确地选择合适的参数,提高传动系统的可靠性和传动效率。
碟形弹簧在航空航天、汽车制造、船舶制造等领域也有着重要的应用。
通过研究碟形弹簧的制造工艺,可以提高生产效率,降低生产成本,推动相关行业的发展。
1.3 文献综述在早期的研究中,碟形弹簧的设计和制造一直是一个备受关注的领域。
弹簧钢丝生产工艺

弹簧钢丝生产工艺
弹簧钢丝是一种用于制作弹簧的铁合金材料,其具有高弹性和高抗拉强度的特点,广泛应用于各种工业领域。
弹簧钢丝的生产工艺主要包括原材料选取、熔炼、连铸、轧制、拉拔、退火和表面处理等环节。
首先,原材料选取是弹簧钢丝生产的第一步。
常用的原材料是钢铁和其他合金元素。
钢铁通常选择具有高纯度和低含杂质的废钢进行回炉,以提高弹簧钢丝的质量。
第二步是熔炼阶段,将废钢和其他合金元素放入高炉中进行熔炼,同时加入适量的碳素、钴等合金元素。
经过高温熔化后,生成的钢液将被装入连铸机。
接下来是连铸过程,将熔化的钢水通过连铸机喷入水冷却的喷头中,形成连续的弧形结晶轮廓。
这样可以得到一种连续铸坯,利用这种连续铸坯进行下一步的轧制工艺。
然后是轧制阶段,将连铸机所得的连续铸坯放入轧机中进行轧制。
轧制过程中,轧辊将连续铸坯不断地压扁和拉长,使其逐渐变成所需的弹簧钢丝的形状和尺寸。
紧接着是拉拔阶段,将轧制好的钢丝放入拉拔机中进行拉拔。
拉拔是将钢丝放入逐渐缩小的模具中,通过不断的拉拔使其尺寸和直径变小,并提高其机械性能。
然后是退火工艺,将拉拔好的钢丝放入退火炉中进行退火处理。
退火是通过加热和冷却使钢丝结构发生改变,消除应力和缺陷,提高材料的塑性和韧性。
最后是表面处理,将退火后的弹簧钢丝进行喷洗、酸洗、磷化等处理,以去除表面氧化物和杂质,提高其耐腐蚀性和外观质量。
以上就是弹簧钢丝的生产工艺,通过这一系列的工艺环节,可以获得高质量、高性能的弹簧钢丝,以满足各种工业应用的需求。
弹簧的生产工艺
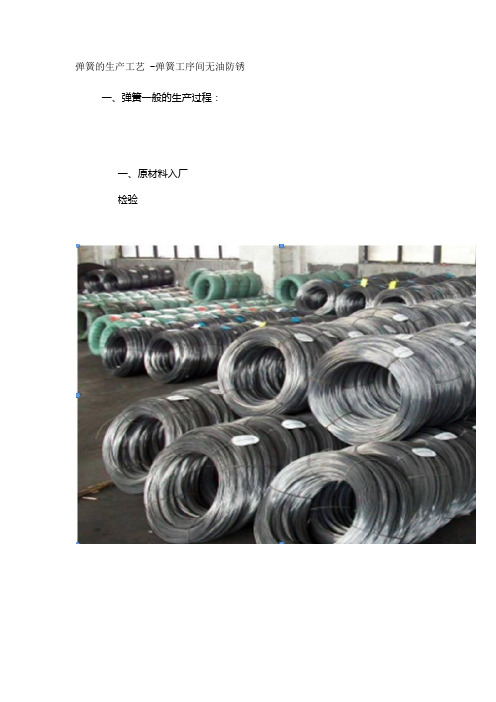
弹簧的生产工艺 -弹簧工序间无油防锈一、弹簧一般的生产过程:一、原材料入厂检验二、成型:冷成型/热成型以卷簧绕制为例三、热处理弹簧钢经过热处理得到回火屈式体组织,该组织是弹性极限最高的,也是弹簧工作状态所必需的。
四、立定、抛丸立定处理是弹簧的预变形处理,目的是增强弹簧的抗衰减性能,抛丸处理是增强表面硬度和提高疲劳寿命。
五、清洗、防护弹簧的清洗:弹簧加工过程中产生的油污,灰尘需要清洗干净弹簧的防护:常用的防护有镀锌,电泳,喷塑,发黑,防锈油。
二、无油防锈技术在弹簧行业的应用:随着国家环保产业的发展以及减少工序,节约成本,很多主机厂开始要求供应商的产品不上防锈油。
不上油,又要求防锈。
这就催生了无油防锈技术的发展,最早的无油防锈技术是气相防锈包装,产品清洗之后进行气相防锈包装,从而达到最终的防锈目的,气相防锈包装的防锈时间一般只能坚持1个月。
而不同的客户对库存的控制能力也不同,所以单纯的气相防锈袋无法满足国内大多数客户对于防锈的要求。
顺应市场。
维赛防锈依托于Chemtool和美国阿莫防锈50多年的气相防锈技术积累,研发了一系列的无油防锈产品。
下面着重介绍以下两款产品:一.水基清洗防锈剂RK-201L1.经济性:超低的添加比例,可以节约一定的成本2.设备适应性:适用于超声波设备,高压喷淋设备,或各种类型的简易设备可以是单槽机:清洗防锈二合一,单槽即可解决两个问题也可以是多槽机:清洗防锈二合一,可以解决清洗剂和防锈剂串液导致的不兼容问题3.清洗性:清洗后的产品洁净无白斑,满足清洁度要求4.防锈性:普通包装可达3-6个月以上的防锈周期,配合防锈包装可达6-12个月的防锈周期5.无油性:水性产品,经过烘干或者晾干,水分蒸发表面无残留二.碳氢清洗防锈剂RK-101K1.经济性:超长的使用寿命,可以节约一定的成本2.设备适应性:没有设备要求,客户只需要准备2-3个槽子,产品加工之后只需要浸泡3遍RK-305防锈剂,无需烘干、加热、超声波、喷淋等要求。
卷制弹簧销生产工艺

卷制弹簧销生产工艺英文回答:Step 1: Raw Material Selection.The type of steel used for spring pins depends on the desired characteristics of the pin, such as strength, corrosion resistance, and heat resistance. Common materials include spring steel (e.g., SAE 1070) and stainless steel (e.g., 302, 316).Step 2: Wire Drawing.The steel wire is drawn through a series of dies to reduce its diameter and increase its strength. This process can be repeated multiple times to achieve the desired diameter and mechanical properties.Step 3: Coiling.The wire is coiled into a spiral shape using a coiling machine. The pitch and diameter of the coils can be adjusted based on the specifications of the spring pin.Step 4: Forming.The coiled wire is formed into the desired shape using a press or other forming equipment. This step involves creating the head, body, and tail of the spring pin.Step 5: Heat Treatment.The formed spring pins undergo heat treatment to improve their strength and hardness. This process typically involves heating the pins to a specific temperature and then quenching them in oil or water.Step 6: Grinding.The ends of the spring pins are ground to remove burrs and ensure a smooth surface. This step is important to prevent wear and tear during installation and usage.Step 7: Inspection and Testing.The spring pins are inspected and tested to verifytheir dimensions, mechanical properties, and surface finish. This ensures that they meet the specified requirements and quality standards.中文回答:卷制弹簧销生产工艺。
压缩弹簧生产工艺流程

压缩弹簧生产工艺流程下载温馨提示:该文档是我店铺精心编制而成,希望大家下载以后,能够帮助大家解决实际的问题。
文档下载后可定制随意修改,请根据实际需要进行相应的调整和使用,谢谢!并且,本店铺为大家提供各种各样类型的实用资料,如教育随笔、日记赏析、句子摘抄、古诗大全、经典美文、话题作文、工作总结、词语解析、文案摘录、其他资料等等,如想了解不同资料格式和写法,敬请关注!Download tips: This document is carefully compiled by theeditor. I hope that after you download them,they can help yousolve practical problems. The document can be customized andmodified after downloading,please adjust and use it according toactual needs, thank you!In addition, our shop provides you with various types ofpractical materials,such as educational essays, diaryappreciation,sentence excerpts,ancient poems,classic articles,topic composition,work summary,word parsing,copy excerpts,other materials and so on,want to know different data formats andwriting methods,please pay attention!压缩弹簧生产工艺流程一、准备工作阶段。
在开始压缩弹簧的生产之前,有许多准备工作需要完成。
汽车弹簧的生产工艺流程

汽车弹簧的生产工艺流程英文回答:The production process of car springs involves several steps to ensure the quality and functionality of the springs. Here is a brief overview of the process:1. Material selection: The first step in the production process is selecting the appropriate materials for the car springs. Most commonly used materials for car springsinclude high-carbon steel and alloy steel. The selection of materials depends on the specific requirements of the car and the desired performance characteristics of the springs.2. Wire forming: Once the materials are selected, the wire forming process begins. This involves shaping the selected wire into the desired shape and size of the spring. The wire is usually fed into a machine that cuts and shapes it into the required form. The machine can be programmed to produce different types of springs, such as compressionsprings, extension springs, or torsion springs.3. Heat treatment: After the wire forming process, the springs undergo heat treatment to improve their strength and durability. Heat treatment involves subjecting the springs to high temperatures and then cooling them rapidly to achieve the desired properties. This process helps to remove any internal stresses and increase the spring's ability to withstand heavy loads.4. Shot peening: Shot peening is a process used to increase the fatigue life of the springs. It involves bombarding the surface of the springs with small metal particles, called shots, at high velocities. This process helps to create compressive stresses on the surface of the springs, which improves their resistance to fatigue and stress corrosion.5. Coiling and grinding: Once the heat treatment and shot peening processes are complete, the springs are coiled into their final shape. This involves winding the wire around a mandrel or a cylindrical object to create thedesired shape. After coiling, the springs undergo grinding to remove any excess material and achieve the required dimensions and surface finish.6. Surface coating: In some cases, car springs may undergo surface coating to protect them from corrosion and improve their appearance. This can involve processes such as electroplating, powder coating, or painting. The choice of coating method depends on the specific requirements of the car and the desired aesthetic finish.7. Quality control: Throughout the production process, quality control measures are implemented to ensure that the car springs meet the required specifications. This can involve dimensional checks, load testing, fatigue testing, and visual inspections. Any springs that do not meet the specified standards are rejected or reworked to meet the requirements.中文回答:汽车弹簧的生产工艺流程包括多个步骤,以确保弹簧的质量和功能。
- 1、下载文档前请自行甄别文档内容的完整性,平台不提供额外的编辑、内容补充、找答案等附加服务。
- 2、"仅部分预览"的文档,不可在线预览部分如存在完整性等问题,可反馈申请退款(可完整预览的文档不适用该条件!)。
- 3、如文档侵犯您的权益,请联系客服反馈,我们会尽快为您处理(人工客服工作时间:9:00-18:30)。
弹簧线设计与生产工艺
Z 向) S 向)
2.1.
3.定位长度:依据弹簧线比剪尺寸中的最短尺寸且需满足其最终比剪尺寸而定.
一般对于120(含)mm 以下者,定位长度取150mm;对于120mm 以上者,定位长度取”最短 比剪尺寸+30mm ”;定位长度公差均设计为±25mm.
2.1.4.绕弹簧长度及公差:依据最终弹簧长度规格及线材外被料材质而定.
2.1.4.1.一般设计原则:
弹簧长度:外被料高弹PVC 及TPE (导体裸铜)设定长度=弹簧长度规格x1.15+10mm; 外被料PU 及TPE (导体锡铜)设定长度=弹簧长度规格x1.1+10mm. 公差:设定为±10mm.
2.1.4.2.对于成品尺寸要求苛刻(如公差小,弹体长,OD 大者),或线材结构特殊者(如OD 大, 芯线材质PVC,有铜箔丝/尼龙绳等结构)须依实际状况作相应调整.
2.2.烤线:烤箱温度,保温时间及冷却方式设定依据线材外被料材质而定.
2.2.1.一般设计原则:
铁棒直径 铁棒长度 最大绕线长度 820mm 710mm φ6.0mm 1410mm 1300mm 820mm 710mm φ8.0mm 1360mm 1250mm 其它 820mm 710mm 外被料材质 烤箱温度设定 保温时间设定 冷却方式 PVC 130±10℃ 20±5分钟 风冷 PU 140±10℃ 25±5分钟 水冷 TPE 150±10℃ 40±5分钟 风冷或水冷
2.2.2.对于客户要求弹性严苛,考虑弹簧OD,弹体长度,及线材结构或本身线材结构状况 (如:芯线及外被料各自老化条件或材质,裸铜高温被氧化,铜箔丝/尼龙丝/尼龙绳受热 收缩,绝缘/外被厚度等等)依据一般原则需做相应参数调整(如调低/高烤温,加长保温 时间,变通冷却方式等).
2.3.二次绕线:
2.3.1.承接一次绕线改用反方向进行二次绕线.铁棒选用依据一次绕线时之,遇有特殊状况 可选用稍小/大的铁棒绕线.
2.3.2.保证弹簧长度及弹簧外径:为防止弹簧线在成品装配制程因受牵扯导致尺寸超规格, 故线缆绕线部份保证尺寸应比成品图规格公差少15%,且依此原则订立弹簧线零件 图公差(即客户提供的规格,有时客户提供的不一定对,工程人员应与客户沟通)。
2.3.3.弹簧长度公差订定:为合理订出弹簧公差,合乎制程能力,在不违反客户规格及2.3.2原 则时按以下原则订定,此亦适合弹簧长度公差之制程能力参考.
2.4.烤直角:遇成品图要求弹簧两端需烤成90℃直角时.线缆部烤直角机最高温度为600华氏度 (即315℃).设计原则以保证直角有好的定型度为准.一般温度设计为450~500华氏 度或550~600华氏度,转速12±2分钟/转.对于结构特殊者(如线径偏小/偏大,外被厚 度达1.2mm 以上等等),其转速要适当放慢.
2.5.两端比剪:比剪尺寸由客户给出并签确.注意对于非烤直角之弹簧线两端比剪,绕线工程规格
书应给出包含弹簧外径之尺寸(以便于线缆部作业,不至疏忽造成比剪错误);烤直角者则给
出两端直线部份尺寸即可.
2.6.半成品质检:a.外观:不得有破裂,变形,喇叭口等外观不良.
b.头,尾部比剪尺寸及弹簧部分尺寸须符合要求.
c.外被白色或浅灰色要增加擦线工序.要保持线材外被不被脏污,需保持干净.
2.7.包装方式:设计原则除满足成品图要求外,以保护弹簧线为主要目的.
无要求时包装方式设计为:外被材质PVC 之弹簧,每6PCS 一扎,用PVC 膜包扎.
外被材质PU,TPE 之弹簧,每10PCS 一扎,用PVC 膜包扎.
注:弹簧线总长度=A 端比剪尺寸+B 端比剪尺寸+π(弹簧体OD-线材OD )弹簧体长度/线材OD+50mm.
外被材质 弹簧长度 公差 150mm(含)以下 ±10mm PVC,PU,TPE 150~500mm(含) ±25mm 500~700mm(含) ±38mm PU,TPE 700mm 以上 ±50mm 500~700mm(含) ±50mm PVC 700mm 以上 ±80mm。