油气管道无损检测方法选择_雷晓青
石油管道无损检测技术的发展研究
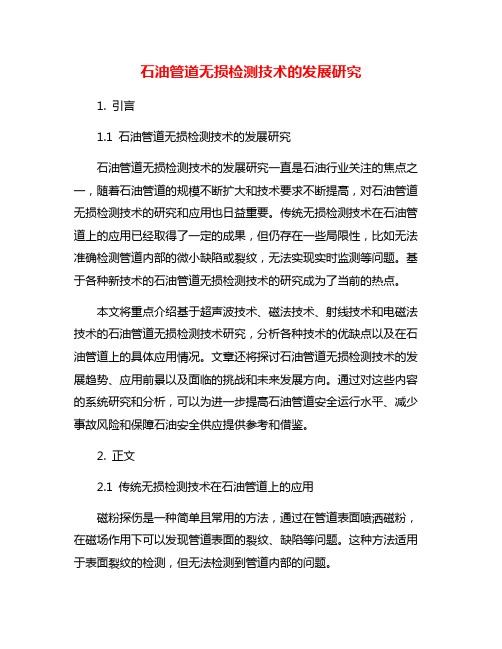
石油管道无损检测技术的发展研究1. 引言1.1 石油管道无损检测技术的发展研究石油管道无损检测技术的发展研究一直是石油行业关注的焦点之一,随着石油管道的规模不断扩大和技术要求不断提高,对石油管道无损检测技术的研究和应用也日益重要。
传统无损检测技术在石油管道上的应用已经取得了一定的成果,但仍存在一些局限性,比如无法准确检测管道内部的微小缺陷或裂纹,无法实现实时监测等问题。
基于各种新技术的石油管道无损检测技术的研究成为了当前的热点。
本文将重点介绍基于超声波技术、磁法技术、射线技术和电磁法技术的石油管道无损检测技术研究,分析各种技术的优缺点以及在石油管道上的具体应用情况。
文章还将探讨石油管道无损检测技术的发展趋势、应用前景以及面临的挑战和未来发展方向。
通过对这些内容的系统研究和分析,可以为进一步提高石油管道安全运行水平、减少事故风险和保障石油安全供应提供参考和借鉴。
2. 正文2.1 传统无损检测技术在石油管道上的应用磁粉探伤是一种简单且常用的方法,通过在管道表面喷洒磁粉,在磁场作用下可以发现管道表面的裂纹、缺陷等问题。
这种方法适用于表面裂纹的检测,但无法检测到管道内部的问题。
超声波探伤是一种非破坏性检测方法,通过将超声波引入管道内部,利用超声波在不同介质中的传播速度和反射情况来识别管道内部的缺陷、腐蚀等问题。
这种方法具有高精度、高灵敏度的优点,可以检测到管道内部的各种问题。
传统无损检测技术在石油管道上的应用具有各自的优缺点,可以根据具体情况选择合适的方法进行应用。
2.2 基于超声波技术的石油管道无损检测技术研究超声波技术是目前广泛应用于石油管道无损检测领域的一种有效方法。
通过发送高频的超声波信号,可以对管道内部的缺陷、腐蚀等问题进行有效检测。
这种技术具有非侵入性、高灵敏度、高分辨率等优点,在石油管道安全监测中发挥着重要作用。
目前,基于超声波技术的石油管道无损检测技术研究趋向于改进检测精度和提高检测效率。
油气管道变形检测的技术方法有哪些

油气管道变形检测的技术方法有哪些油气管道的变形检测是为了保障管道的安全运营,预防泄漏和爆炸等事故的发生。
目前主要的油气管道变形检测技术方法包括:1.无损检测技术:无损检测技术是一种通过对管道表面进行检测,不需要对管道进行破坏或取样的方法。
主要包括超声波检测、磁粉检测、涡流检测和射线检测等。
这些技术能够检测到管道内部或外部的腐蚀、裂纹、疲劳等问题,从而确定管道的变形情况。
2.激光检测技术:激光检测技术通过激光束的测量,计算出管道的形状和尺寸,从而确定管道的变形情况。
激光检测技术具有高度精确度和快速性的特点,能够对管道的变形进行在线实时监测。
3.声波检测技术:声波检测技术通过对管道内部发送声波信号,并通过接收信号的回波进行分析,确定管道的变形情况。
该技术非常适用于检测管道内部的缺陷或损伤,如裂纹、腐蚀等。
4.振动检测技术:振动检测技术通过对管道应力状态下的振动信号进行检测和分析,确定管道的变形情况。
该技术可以根据振动信号的变化识别管道的变形或异常情况。
5.计算机视觉技术:计算机视觉技术通过对管道的照片或视频图像进行分析,提取出有关管道变形的特征信息,从而确定管道的变形情况。
该技术具有非接触、高效率和自动化的特点。
6.应力分析技术:应力分析技术通过对管道的应力状态进行数值分析,确定管道的变形情况。
该技术可以基于管道的物理性质和外部载荷,计算出管道的应力分布和变形情况。
7.光纤传感技术:光纤传感技术通过将光纤安装在管道表面或内部,利用光纤光学特性的变化来监测管道的变形情况。
该技术具有高度灵敏度和实时监测的特点。
以上是目前常用的油气管道变形检测技术方法,各种方法都有其适用的场景和特点。
在实际应用中,通常需要结合多种技术来进行综合检测,以提高检测的准确性和可靠性。
油气管道无损检测方法选择

利 用射 线 ( x射线 、 射 线 、 中子射 线 等 ) 穿 过 材
料 或工件 时 的强度 衰减 ,检测其 内部 结构 不连续 性 的检测 技术【 ” 。
体 积型 缺 陷检 出率 高 .而面积 型缺 陷的检 出率 受 多种 因素 影 响 :适宜 检验厚 度较 薄 的工 件而不 适
超 声波 在被检 测材料 中传播 时 ,材料 的声学特 性和 内部组织 的变 化对超 声波 的传播 产生一 定 的影
响, 通 过对超 声波 受影 响的程度 和状 况 , 探测 了解材
质、 焊接 方法 以及可 能产 生 的缺 陷等 。 选 择几 种无 损
检测 方 法 。 相 互补充 和验 证 。 因为任何 一种无 损检 测 方 法都 不是万 能 的 ,每种 无损 检测方 法都有 自身 的 优 点 与不足 ,不 同的检测 部位 需要选 择不 同 的无 损 检 测方 法 。综 合利 用各 种无损 检测方 法才 能够保 证
缺陷。
料表 面开 口缺 陷处 。再 通过 显象剂 将渗人 的渗透 液
吸 出到表 面 , 显示 缺 陷的影像 的无损 检测方 法 。 磁粉 检测 和渗透 检测统 称为表 面检测 。
1 无损检测概述
所 谓无 损检测 . 是 在不损 坏试 件 的条 件下 。 以物
理或 化学方 法为 手段 , 借助先 进 的技术 和器材 。 对试 件 的内部及 表 面的结构 、性 质状 态进行 检测 和测试 的方 法 。 油 气管 道常用 的无损 检测 方法有 射线 检测 、
法。
关 键 词 射 线 检 测 超 声 波检 测 磁粉 检 测 渗 透检 测 油气 管道
Ab s t r a c t nl e f e a t u r e s o f t h e c o mmo n l y u s e d NDT me t h o d s f o r o i 1 / g a s - p i p e l i n e t e s t i n g a r e a n a l y z e d . C o mb i n e d w i t h w o r k i n g e x p e i— f e n c e o v e r t h e y e a r s , h o w t o s e l e c t t h e ND T me t h o d or f o i / l g a s - p i p e l i n e a r e i n t r o d u c e d . T h e NDT me t h o d s h a l l b e s e l e c t e d i n a c c o r — d a n c e w i t h t h e c o n s t r u c t i o n a c c e p t a n c e c r i t e r i a a n d s p e c i f i c a t i o n ,t h e a p p l i c a b l e s c o p e o f NDT s t a n d a r d ,t h e t o - b e - t e s t e d we l d i n g s e a m t y p e a n d t e s t i n g a r e a , a n d t h e p o s s i b l e d e f e c t t y p e s e t c . . Ke y wo r d s r a d i o g r a p h i n s p e c t i o n ;u l t r a s o n i c i n s p e c t i o n ;ma g n e t i c p a r t i c l e i n s p e c t i o n ;f l u o r e s c e n t p e n e t r a n t i n s p e c t i o n ;o i / l g a s
油气管道缺陷无损检测与在线检测诊断技术的探析

油气管道缺陷无损检测与在线检测诊断技术的探析油气管道是石油、天然气等能源资源的重要输送通道,对于国家能源安全和经济发展具有重要意义。
油气管道在长期使用过程中难免会出现各种缺陷,这些缺陷可能会导致管道泄漏、爆炸等严重事故,给人民生命财产安全带来巨大风险。
油气管道的无损检测与在线检测诊断技术显得尤为重要。
本文将从油气管道的缺陷特点、无损检测技术及在线检测诊断技术等方面对该问题进行探讨。
一、油气管道缺陷特点油气管道缺陷主要包括内外腐蚀、焊接缺陷、应力腐蚀开裂、管道内结垢等。
这些缺陷在管道长期运行中会逐渐加剧,导致管道壁厚度减薄、管道内部压力承载能力下降,甚至引发管道泄露或爆炸事故。
内外腐蚀是油气管道常见的缺陷,其特点是发展速度缓慢但难以察觉,一旦蔓延到一定程度就会对管道的安全性造成严重影响。
焊接缺陷主要由于焊接时的操作不当、焊缝质量不良等原因导致,这种缺陷在管道使用过程中易发生破裂。
应力腐蚀开裂是由于管道受到应力和介质腐蚀的共同作用引起的,这种缺陷常常发生在管道接头和焊缝处。
管道内结垢会导致介质流通不畅,增加管道的阻力,加剧腐蚀速度,最终导致管道破裂。
由于油气管道运行环境的特殊性,其缺陷检测难度较大,因此需要借助先进的无损检测技术和在线检测诊断技术来保障管道的安全运行。
二、无损检测技术无损检测技术是指在不破坏被测体的情况下对被测体进行检测和评价的技术手段。
在油气管道的无损检测中,常用的技术包括超声波检测、磁粉探伤、液态渗透检测、射线检测等。
超声波检测是常用的一种无损检测技术,其原理是利用超声波在材料中传播的特性来检测材料内部的缺陷。
超声波可以穿透材料并在缺陷处发生反射或衍射,通过接收回波信号来判断缺陷的位置、大小和形状。
磁粉探伤是利用磁粉检测剂在磁场作用下检测材料表面和亚表面的缺陷,其原理是磁粉在磁场下会聚集在缺陷处形成磁粉斑。
液态渗透检测是利用液态渗透剂的渗透性来检测材料表面裂纹、开裂等表面缺陷。
射线检测是利用射线照射被测体,通过检测射线透过被测体后的衰减情况来判断材料的内部缺陷。
无损检测工作常见质量问题与监管方法

一
无损检 测 工作 作为检 查 与 评定 焊接 接 头质 量 的 项 有效 手段 ,在 油气 田产 能 建设 地面 安装 工 程 的
1 无损检测工作的一般流程
要准确 、及时制订 出检 测工作监管措施 ,不 断完
善监管 方法 ,准确查 找检 测工作中存在 的不 足 ,首先 要对无损检测 工作流 程进 行分析 ,从中发现 并了解检
d o i : 1 0 , 3 9 6 9 / j . i s s n , 1 0 0 1 — 2 2 0 6 , 2 0 1 7 S 0 3 6
摘
要 :为提高对无损检 测工作的问题发现 能力及监管工作效率 ,结 合多年ຫໍສະໝຸດ 事专业检测 及监 督工作经验 ,提
出一些便于操 作 、针对 性强的监 管措施 。在简 要介绍无损 检测 工作一 般流程 的基础上 ,论述 了检测标 准用错 、
1 . Ch a n g q i n g Qu a l i t y Su p e r v i s i o n S t a t i o n o f P e t r o l eu m & Na t u r a l Ga s E n g i n e er i n g, Xi a n 7 1 0 01 8, Ch i n a 2. T e c h n o l o g y Mo n i t o r i n g Ce n t e r o f P e t r o Ch i n a Ch a n g q i n g Oi l f i e l d Co mp a n y,Xi a n 71 0 0 1 8, Ch i n a Ab s t r a c t :I n o r d er t o e n h a n c e t h e a b i l i t y o f f i n d i n g q u a l i t y p r o b l e ms i n n o n d e s t r u c t i v e t e s t i n g a n d t h e s u p e r v i s i o n e f f i c i e n c y, s o me o p e r a t i o n a l a n d r el i a b l e s u p e r v i s i on me a s u r e s a r e b r o u gh t f o r wa r d b a s e d o n t h e ma n y y e a r s’ e x p e r i e n c e i n i n s p e c t i o n a n d s u p er v i s i o n . Th i s p a p e r d i s c u s s e s c o mmo n p r o b l e ms i n n on d e s t r u c t i v e t e s t i n g, s u c h a s mi s u s i n g t e s t i n g s t a n d a r d, u n f a mi r wi t h a p p l i c a t i v e s c o p e o f t e s t i n g s t a n d a r d, i n c o mp l e t e t e s t i n g i n f o r ma t i o n, p a r t i a l l y mi s s i n g t e s t i n g, f a l s e t e s t — i n g r e s u l t a n d l o w t es t e d r a t e o f d e f e c t s .
油气管道无损检测技术

油气管道无损检测技术管道作为大量输送石油、气体等能源的安全经济的运输手段,在世界各地得到了广泛应用,为了保障油气管道安全运行,延长使用寿命,应对其定期进行检测,以便发现问题,采取措施。
一、管道元件的无损检测(一)管道用钢管的检测埋地管道用管材包括无缝钢管和焊接钢管。
对于无缝钢管采用液浸法或接触法超声波检测主要来发现纵向缺陷。
液浸法使用线聚焦或点聚焦探头,接触法使用与钢管表面吻合良好的斜探头或聚焦斜探头。
所有类型的金属管材都可采用涡流方法来检测它们的表面和近表面缺陷。
对于焊接钢管,焊缝采用射线抽查或100 %检测,对于100 %检测,通常采用X射线实时成像检测技术。
(二)管道用螺栓件对于直径>50 mm的钢螺栓件需采用超声来检测螺栓杆内存在的冶金缺陷。
超声检测采用单晶直探头或双晶直探头的纵波检测方法。
二、管道施工过程中的无损检测(一)各种无损检测方法在焊管生产中的配置国外在生产中常规的主要无损检测配置如下图一中的A、B、C、E、F、G、H工序。
我国目前生产中的检测配置主要岗位如下图中的A、C、D、E、F、G、H工序。
图一大口径埋弧焊街钢管生产无损检测岗位配置(二)超声检测全自动超声检测技术目前在国外已被大量应用于长输管线的环焊缝检测,与传统手动超声检测和射线检测相比,其在检测速度、缺陷定量准确性、减少环境污染和降低作业强度等方面有着明显的优越性。
全自动相控阵超声检测系统采用区域划分方法,将焊缝分成垂直方向上的若干个区,再由电子系统控制相控阵探头对其进行分区扫查,检测结果以双门带状图的形式显示,再辅以TOFD (衍射时差法)和B扫描功能,对焊缝内部存在的缺陷进行分析和判断。
全自动超声波现场检测时情况复杂,尤其是轨道位置安放的精确度、试块的校准效果、现场扫查温度等因素会对检测结果产生强烈的影响,因此对检测结果的评判需要对多方面情况进行综合考虑,收集各种信息,才能减少失误。
(三)射线检测射线检测一般使用X射线周向曝光机或Y射线源,用管道内爬行器将射线源送入管道内部环焊缝的位置,从外部采用胶片一次曝光,但胶片处理和评价需要较长的时间,往往影响管道施工的进度,因此,近年来国内外均开发出专门用于管道环焊缝检测的X射线实时成像检测设备。
油气管道巡线无损检测技术研究

油气管道巡线无损检测技术研究引言:随着石油和天然气行业的发展,油气管道的建设和运营变得越来越重要。
然而,油气管道的安全隐患也日益凸显,一旦发生泄露、爆炸等事故将会造成巨大的经济损失和人员伤亡。
因此,油气管道的巡线无损检测技术的研究十分重要。
本文将介绍目前主流的油气管道巡线无损检测技术,并探讨其优缺点和应用前景。
一、磁流体无损检测技术磁流体无损检测技术是一种基于磁力线漏磁信号的检测方法。
这种方法可以通过测量油气管道壁上的漏磁信号来判断管道壁的缺陷情况。
磁流体无损检测技术具有灵敏度高、检测速度快、操作简便等优点,可以对管道内部的缺陷进行有效检测。
然而,这种方法对管道表面的杂散磁场有一定的影响,仅适用于管道外表面的检测,对于管道内表面的缺陷检测效果不理想。
二、超声波无损检测技术超声波无损检测技术是一种基于声波的检测方法。
这种方法利用超声波在材料中传播时的声速和声频变化来判断材料的缺陷情况。
超声波无损检测技术具有精度高、探测范围广等优点,可以对管道内外表面的缺陷进行有效检测。
然而,这种方法需要人工操作,无法实现全自动化监测,且在一些高温高压环境中应用受到限制。
三、红外热像无损检测技术红外热像无损检测技术是一种基于红外热传导原理的检测方法。
这种方法利用红外相机拍摄管道表面的热图,通过分析热图中的温度变化来判断管道表面的缺陷情况。
红外热像无损检测技术具有高效、非接触等优点,可以对管道表面的热损伤、腐蚀等缺陷进行有效检测。
然而,这种方法对环境温度的影响较大,灵敏度较低,对一些微小缺陷的检测效果不理想。
四、电磁涡流无损检测技术电磁涡流无损检测技术是一种基于涡流感应原理的检测方法。
这种方法通过测量油气管道表面感应涡流的强度和分布情况来判断管道表面的缺陷情况。
电磁涡流无损检测技术具有高灵敏度、高分辨率等优点,可以对管道表面的微小缺陷进行有效检测。
然而,这种方法对管道材料的电导率较为敏感,无法适用于非导电材料的检测。
浅析石油天然气钢质管道的无损检测
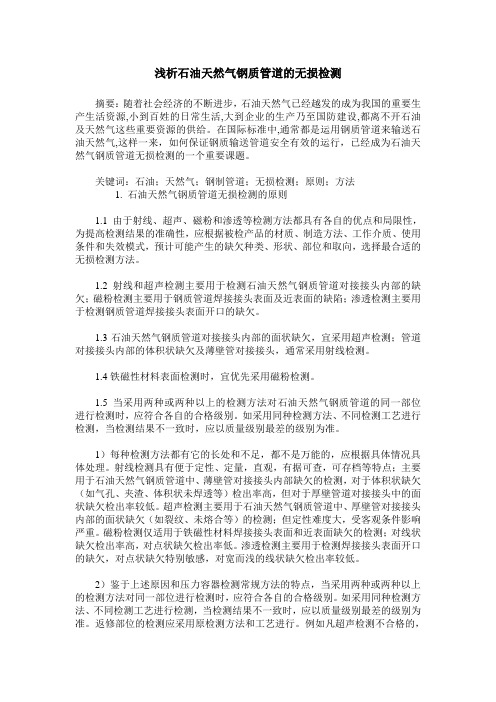
浅析石油天然气钢质管道的无损检测摘要:随着社会经济的不断进步,石油天然气已经越发的成为我国的重要生产生活资源,小到百姓的日常生活,大到企业的生产乃至国防建设,都离不开石油及天然气这些重要资源的供给。
在国际标准中,通常都是运用钢质管道来输送石油天然气,这样一来,如何保证钢质输送管道安全有效的运行,已经成为石油天然气钢质管道无损检测的一个重要课题。
关键词:石油;天然气;钢制管道;无损检测;原则;方法1. 石油天然气钢质管道无损检测的原则1.1 由于射线、超声、磁粉和渗透等检测方法都具有各自的优点和局限性,为提高检测结果的准确性,应根据被检产品的材质、制造方法、工作介质、使用条件和失效模式,预计可能产生的缺欠种类、形状、部位和取向,选择最合适的无损检测方法。
1.2射线和超声检测主要用于检测石油天然气钢质管道对接接头内部的缺欠;磁粉检测主要用于钢质管道焊接接头表面及近表面的缺陷;渗透检测主要用于检测钢质管道焊接接头表面开口的缺欠。
1.3石油天然气钢质管道对接接头内部的面状缺欠,宜采用超声检测;管道对接接头内部的体积状缺欠及薄壁管对接接头,通常采用射线检测。
1.4铁磁性材料表面检测时,宜优先采用磁粉检测。
1.5 当采用两种或两种以上的检测方法对石油天然气钢质管道的同一部位进行检测时,应符合各自的合格级别。
如采用同种检测方法、不同检测工艺进行检测,当检测结果不一致时,应以质量级别最差的级别为准。
1)每种检测方法都有它的长处和不足,都不是万能的,应根据具体情况具体处理。
射线检测具有便于定性、定量,直观,有据可查,可存档等特点;主要用于石油天然气钢质管道中、薄壁管对接接头内部缺欠的检测,对于体积状缺欠(如气孔、夹渣、体积状未焊透等)检出率高,但对于厚壁管道对接接头中的面状缺欠检出率较低。
超声检测主要用于石油天然气钢质管道中、厚壁管对接接头内部的面状缺欠(如裂纹、未熔合等)的检测;但定性难度大,受客观条件影响严重。
油气管道缺陷无损检测与在线检测诊断技术的探析

油气管道缺陷无损检测与在线检测诊断技术的探析油气管道是石油和天然气运输的重要通道,对于石油和天然气的安全和可靠运输起着至关重要的作用。
由于油气管道长期运行和外部环境的影响,管道内部可能会出现各种缺陷,例如腐蚀、裂纹、变形等问题,这些缺陷可能会导致管道泄漏、爆炸等严重事故。
对油气管道进行无损检测和在线检测诊断是保障管道安全的重要手段。
本文将对油气管道缺陷无损检测与在线检测诊断技术进行探讨,以期能够更好地了解和保护油气管道安全。
一、油气管道缺陷无损检测技术1. 超声波检测技术超声波检测技术是通过超声波穿透管道材料,对管道内部的缺陷进行检测的一种技术。
超声波可以用来检测管道壁的厚度、裂纹、腐蚀等缺陷,是目前最常用的无损检测技术之一。
该技术具有检测精度高、操作便捷等优点,但是在对复杂形状的管道进行检测时,存在一定的局限性。
2. 磁粉探伤技术磁粉探伤技术是利用磁铁或电磁铁在管道表面产生磁场,将铁磁性粉末撒在磁场下,当管道表面出现缺陷时,粉末会在缺陷处聚集,形成磁粉堆积,从而可以通过观察磁粉的分布来判断管道的缺陷情况。
该技术对于检测管道表面的缺陷效果较好,但不能用于对管道内部缺陷的检测。
射线检测技术是利用X射线或γ射线穿透管道材料,对管道内部的缺陷进行检测的一种技术。
该技术对于检测管道内部各种缺陷具有较好的效果,但是对工作环境和操作人员的辐射防护要求较高,且成本较高。
1. 金属磁记忆技术2. 声发射技术声发射技术是通过监测管道内部产生的声波信号,来判断管道是否存在缺陷的一种技术。
当管道发生变形、裂纹等缺陷时,会产生压力波或弹性波的传播,通过对这些信号进行监测和分析,可以实现对管道缺陷的在线诊断。
3. 智能传感器技术智能传感器技术是利用传感器对管道进行实时监测和数据采集,通过对采集到的数据进行分析和处理,可以实现对管道的在线检测和诊断。
该技术具有实时性强、对管道形状和缺陷类型的适应性较好等优点。
三、技术的发展趋势随着科技的不断进步,油气管道缺陷无损检测与在线检测诊断技术也在不断地得到完善和创新。
油气管道无损检测技术

油气管道无损检测技术管道作为大量输送石油、气体等能源的安全经济的运输手段,在世界各地得到了广泛应用,为了保障油气管道安全运行,延长使用寿命,应对其定期进行检测,以便发现问题,采取措施。
一、管道元件的无损检测(一)管道用钢管的检测埋地管道用管材包括无缝钢管和焊接钢管。
对于无缝钢管采用液浸法或接触法超声波检测主要来发现纵向缺陷。
液浸法使用线聚焦或点聚焦探头,接触法使用与钢管表面吻合良好的斜探头或聚焦斜探头。
所有类型的金属管材都可采用涡流方法来检测它们的表面和近表面缺陷。
对于焊接钢管,焊缝采用射线抽查或100 %检测,对于100 %检测,通常采用X射线实时成像检测技术。
(二)管道用螺栓件对于直径> 50 mm 的钢螺栓件需采用超声来检测螺栓杆内存在的冶金缺陷。
超声检测采用单晶直探头或双晶直探头的纵波检测方法。
二、管道施工过程中的无损检测(一)各种无损检测方法在焊管生产中的配置国外在生产中常规的主要无损检测配置如下图一中的A、B、C、E、F、G、H工序。
我国目前生产中的检测配置主要岗位如下图中的A、C、D、E、F、G、H工序。
图一大口径埋弧焊街钢管生产无损检测岗位配置(二)超声检测全自动超声检测技术目前在国外已被大量应用于长输管线的环焊缝检测,与传统手动超声检测和射线检测相比,其在检测速度、缺陷定量准确性、减少环境污染和降低作业强度等方面有着明显的优越性。
全自动相控阵超声检测系统采用区域划分方法,将焊缝分成垂直方向上的若干个区,再由电子系统控制相控阵探头对其进行分区扫查,检测结果以双门带状图的形式显示,再辅以TOFD (衍射时差法)和B扫描功能,对焊缝内部存在的缺陷进行分析和判断。
全自动超声波现场检测时情况复杂,尤其是轨道位置安放的精确度、试块的校准效果、现场扫查温度等因素会对检测结果产生强烈的影响,因此对检测结果的评判需要对多方面情况进行综合考虑,收集各种信息,才能减少失误。
(三)射线检测射线检测一般使用X 射线周向曝光机或γ射线源,用管道内爬行器将射线源送入管道内部环焊缝的位置,从外部采用胶片一次曝光,但胶片处理和评价需要较长的时间,往往影响管道施工的进度,因此,近年来国内外均开发出专门用于管道环焊缝检测的X 射线实时成像检测设备。
石油天然气钢质管道无损检测 (2)

石油天然气钢质管道无损检测1. 引言石油和天然气是现代社会不可或缺的能源资源,其在工业和民用领域具有广泛的应用。
而钢质管道作为石油和天然气输送的主要通道,其安全可靠性至关重要。
为确保钢质管道运行安全,无损检测技术被广泛应用于管道的质量控制和缺陷检测。
本文将重点介绍石油天然气钢质管道无损检测技术的原理、方法和应用。
2. 无损检测原理无损检测是一种基于物理、化学和工程学原理,通过检测材料的表面或内部缺陷,不破坏被检测物体的技术。
常用的无损检测原理包括超声波检测、磁粉检测、涡流检测和X射线检测等。
2.1 超声波检测超声波检测是利用超声波在材料内部传播时的反射、透射、折射等特性来检测材料内部缺陷的一种方法。
通过发射超声波信号,接收返回的信号并分析,可以确定管道的腐蚀、裂纹、气泡等缺陷情况。
2.2 磁粉检测磁粉检测是通过涂布或撒布磁粉在被检材料上,利用磁粉在材料表面产生的磁场留下的磁粉图案来检测材料表面或近表面的缺陷的一种方法。
当材料表面存在缺陷时,磁粉会在缺陷处聚集形成磁粉图案,通过观察和记录这些磁粉图案可以判断缺陷的位置和性质。
2.3 涡流检测涡流检测是利用电磁诱导原理检测材料中导电性缺陷的一种方法。
通过将交变电源接入线圈产生交变磁场,当磁场感应到管道中的导电性缺陷时,会在缺陷处产生涡流,通过测量涡流的变化来识别和定位缺陷。
2.4 X射线检测X射线检测是利用X射线对材料进行透射、散射或吸收的特性来检测材料内部缺陷的一种方法。
通过发射X射线束,通过检测X射线的强度和能量变化,可以确定材料内部的缺陷情况,如裂纹、焊接缺陷等。
3. 无损检测方法根据石油天然气钢质管道的特点和需求,常用的无损检测方法包括超声波法、磁粉法、涡流法和X射线法。
3.1 超声波法超声波法是一种广泛应用于钢质管道无损检测的方法。
通过使用超声波传感器对管道进行扫描,可以检测到管道内部的腐蚀、裂纹等缺陷。
超声波法具有非接触、高灵敏度、高准确性等特点,适用于管道的各个部位。
石油管无损检测技术探讨

石油管无损检测技术探讨近年来,石油管道的检测技术越来越多,无损检测新技术是一种较为先进的检查技术,在检测的过程中,可以更好地进行分析和判断,检查发现石油管道内部存在的问题,进而为我们的管理人员提供技术方面的参考。
本文主要探讨了所有管道的无损检测技术,研究了技术了具体的使用方法以及原理,提出了相关的建议,供参考和借鉴。
标签:石油管道;无损检测在石油管道的无损检测过程中,检查人员首先要明确检测的具体方法,开展检查工作所要遵守的原则和流程,在检测的过程中,把握好每一个要素,才能够真正提高石油管道无损检测技术的水平。
1、石油管无损检测技术油管属于一种井下通道的钢柱管,在石油开采过程注水、筑起等环节中应用,其能够重复使用,并能够被下入和起出。
在采用过程中,油管会因为各种原因导致弯曲,如抽油管受拉伸、酸化、压裂、高温等外部环境影响,活塞效应、螺旋效应、膨胀效应等作用。
无损检测技术即为不损伤材料和成品的检测,该项技术的检测原理为材料的内部结构对光、热、点的反应,通过反应情况即可判断材料内部是否异常。
应用无损检测技术检测油管的强度,确定其是否存在缺陷,对构建所能允许的负荷和使用寿命进行评价,根据检测结构对油管进行修理。
1.1石油管缺陷检测系统的信号采集及处理方法石油管检测系统的主要组成部分为传感器、数字信号处理设备以及相对应的支撑性装置。
在石油管的实际无损检测技术应用中,在石油管中进行探测传感器的运行,从而对石油管工作中存在的缺陷信息进行有效探析。
信号处理装置主要是将在探测传感器中所检测到的相应信息进行一个放大处理,在处理操作后将其相应的信息传输到转换仪器中,并做出相关的科学处理最终在计算机内进行缺陷的分析处理。
在石油管的无损检测过程中,在石油管及相应传感器的运动过程中,均应保证石油管的整体表面状态能够被扫描头扫描到,如出现未完整扫描的情况,那么则易出现漏检状况。
因此,在对石油管进行无损检测工作时,其主要的依靠力量为扫描头的全面旋转,而扫描范围应在石油管上方呈现一种螺旋线的轨迹方向,关于探测仪器的所处位置以及相应的速度均应进行科学准确的控制。
油气管道缺陷无损检测与在线检测诊断技术的探析
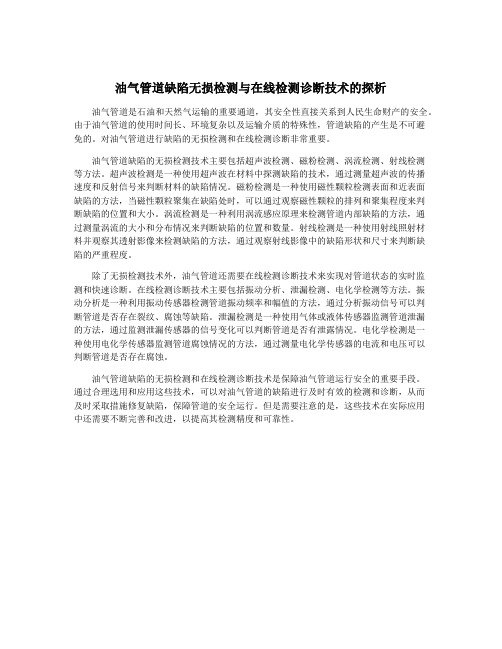
油气管道缺陷无损检测与在线检测诊断技术的探析油气管道是石油和天然气运输的重要通道,其安全性直接关系到人民生命财产的安全。
由于油气管道的使用时间长、环境复杂以及运输介质的特殊性,管道缺陷的产生是不可避免的。
对油气管道进行缺陷的无损检测和在线检测诊断非常重要。
油气管道缺陷的无损检测技术主要包括超声波检测、磁粉检测、涡流检测、射线检测等方法。
超声波检测是一种使用超声波在材料中探测缺陷的技术,通过测量超声波的传播速度和反射信号来判断材料的缺陷情况。
磁粉检测是一种使用磁性颗粒检测表面和近表面缺陷的方法,当磁性颗粒聚集在缺陷处时,可以通过观察磁性颗粒的排列和聚集程度来判断缺陷的位置和大小。
涡流检测是一种利用涡流感应原理来检测管道内部缺陷的方法,通过测量涡流的大小和分布情况来判断缺陷的位置和数量。
射线检测是一种使用射线照射材料并观察其透射影像来检测缺陷的方法,通过观察射线影像中的缺陷形状和尺寸来判断缺陷的严重程度。
除了无损检测技术外,油气管道还需要在线检测诊断技术来实现对管道状态的实时监测和快速诊断。
在线检测诊断技术主要包括振动分析、泄漏检测、电化学检测等方法。
振动分析是一种利用振动传感器检测管道振动频率和幅值的方法,通过分析振动信号可以判断管道是否存在裂纹、腐蚀等缺陷。
泄漏检测是一种使用气体或液体传感器监测管道泄漏的方法,通过监测泄漏传感器的信号变化可以判断管道是否有泄露情况。
电化学检测是一种使用电化学传感器监测管道腐蚀情况的方法,通过测量电化学传感器的电流和电压可以判断管道是否存在腐蚀。
油气管道缺陷的无损检测和在线检测诊断技术是保障油气管道运行安全的重要手段。
通过合理选用和应用这些技术,可以对油气管道的缺陷进行及时有效的检测和诊断,从而及时采取措施修复缺陷,保障管道的安全运行。
但是需要注意的是,这些技术在实际应用中还需要不断完善和改进,以提高其检测精度和可靠性。
石油行业中的无损检测技术应用方法
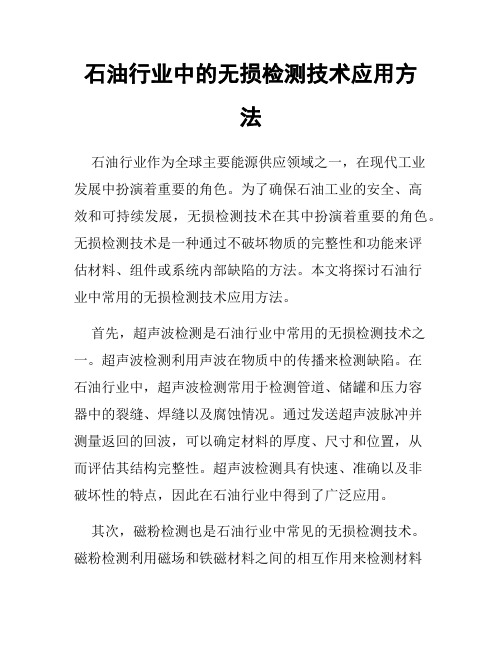
石油行业中的无损检测技术应用方法石油行业作为全球主要能源供应领域之一,在现代工业发展中扮演着重要的角色。
为了确保石油工业的安全、高效和可持续发展,无损检测技术在其中扮演着重要的角色。
无损检测技术是一种通过不破坏物质的完整性和功能来评估材料、组件或系统内部缺陷的方法。
本文将探讨石油行业中常用的无损检测技术应用方法。
首先,超声波检测是石油行业中常用的无损检测技术之一。
超声波检测利用声波在物质中的传播来检测缺陷。
在石油行业中,超声波检测常用于检测管道、储罐和压力容器中的裂缝、焊缝以及腐蚀情况。
通过发送超声波脉冲并测量返回的回波,可以确定材料的厚度、尺寸和位置,从而评估其结构完整性。
超声波检测具有快速、准确以及非破坏性的特点,因此在石油行业中得到了广泛应用。
其次,磁粉检测也是石油行业中常见的无损检测技术。
磁粉检测利用磁场和铁磁材料之间的相互作用来检测材料表面和近表面的缺陷。
在石油行业中,磁粉检测常用于检测钻井管和油井管道中的裂缝、疲劳性断裂以及电弧烧蚀。
该技术通过在被检测物体表面涂覆磁粉,并在施加磁场后观察粉末上产生的磁性漏磁场来定位缺陷。
磁粉检测具有灵敏度高、操作简便、成本低廉等特点,因此在石油行业维护和检修工作中得到了广泛应用。
除此之外,涡流检测也是石油行业中常用的无损检测技术之一。
涡流检测利用电磁感应原理来检测导电材料中的缺陷。
在石油行业中,涡流检测常用于检测管道和油井设备中的裂缝、焊缝以及腐蚀情况。
该技术通过在被检测物体表面施加交变电流,并观察由电流引起的涡流感应电压来检测缺陷。
涡流检测具有高灵敏度、高分辨率以及能够检测不同深度的缺陷等优点,在石油行业中发挥着重要作用。
再者,X射线检测是石油行业中应用广泛的无损检测技术。
X射线检测利用X射线通过物质时的吸收和散射来检测材料内部的缺陷。
在石油行业中,X射线检测常用于检测焊接部位、管道以及储罐等设备的裂缝、腐蚀以及金属杂质。
该技术通过产生和发射X射线,并采集经过被检测物体后残留的X射线来获取图像。
无损检测技术在石油管道安全管理中的应用
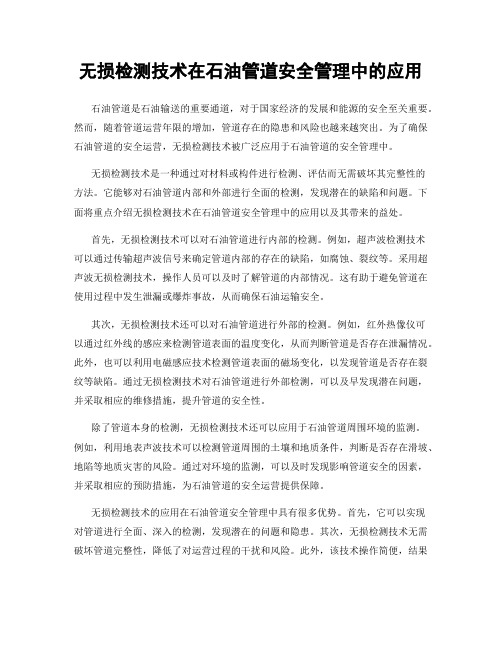
无损检测技术在石油管道安全管理中的应用石油管道是石油输送的重要通道,对于国家经济的发展和能源的安全至关重要。
然而,随着管道运营年限的增加,管道存在的隐患和风险也越来越突出。
为了确保石油管道的安全运营,无损检测技术被广泛应用于石油管道的安全管理中。
无损检测技术是一种通过对材料或构件进行检测、评估而无需破坏其完整性的方法。
它能够对石油管道内部和外部进行全面的检测,发现潜在的缺陷和问题。
下面将重点介绍无损检测技术在石油管道安全管理中的应用以及其带来的益处。
首先,无损检测技术可以对石油管道进行内部的检测。
例如,超声波检测技术可以通过传输超声波信号来确定管道内部的存在的缺陷,如腐蚀、裂纹等。
采用超声波无损检测技术,操作人员可以及时了解管道的内部情况。
这有助于避免管道在使用过程中发生泄漏或爆炸事故,从而确保石油运输安全。
其次,无损检测技术还可以对石油管道进行外部的检测。
例如,红外热像仪可以通过红外线的感应来检测管道表面的温度变化,从而判断管道是否存在泄漏情况。
此外,也可以利用电磁感应技术检测管道表面的磁场变化,以发现管道是否存在裂纹等缺陷。
通过无损检测技术对石油管道进行外部检测,可以及早发现潜在问题,并采取相应的维修措施,提升管道的安全性。
除了管道本身的检测,无损检测技术还可以应用于石油管道周围环境的监测。
例如,利用地表声波技术可以检测管道周围的土壤和地质条件,判断是否存在滑坡、地陷等地质灾害的风险。
通过对环境的监测,可以及时发现影响管道安全的因素,并采取相应的预防措施,为石油管道的安全运营提供保障。
无损检测技术的应用在石油管道安全管理中具有很多优势。
首先,它可以实现对管道进行全面、深入的检测,发现潜在的问题和隐患。
其次,无损检测技术无需破坏管道完整性,降低了对运营过程的干扰和风险。
此外,该技术操作简便,结果准确可靠。
最重要的是,通过无损检测技术发现的问题可以及时处理,避免事故的发生,提升石油管道的整体安全水平。
油气管道缺陷无损检测与在线检测诊断技术的探析

油气管道缺陷无损检测与在线检测诊断技术的探析油气管道是现代工业生产不可或缺的重要设施,但长期运行和环境条件使得管道容易出现各种缺陷。
由于管道缺陷可能导致泄漏、事故等严重后果,因此对油气管道进行缺陷无损检测和在线检测诊断技术的研究与应用具有重要意义。
油气管道缺陷无损检测技术是指通过对管道进行非破坏性检测,实现对管道缺陷的快速、准确判断的技术方法。
目前常用的无损检测方法包括超声波检测、磁粉检测、涡流检测等。
超声波检测方法通过对管道内部进行超声波的发射和接收,通过对超声波的传播和反射信号进行分析,可以判断管道是否存在缺陷。
磁粉检测方法是利用铁磁材料的磁化特性,通过施加磁场和涂覆磁粉,观察磁粉在管道表面是否产生磁粉线,从而判断管道是否存在表面缺陷。
涡流检测方法是利用感应电流原理,通过传感器对管道表面感应出的涡流信号进行分析,以判断管道是否存在缺陷。
在线检测诊断技术是指对油气管道进行实时监测和诊断,通过对管道运行状态的监控和数据分析,实现对管道缺陷和故障的及时发现和判断的技术方法。
目前常用的在线检测诊断技术包括振动监测、温度监测、压力监测等。
振动监测技术通过对管道振动信号的采集和分析,可以判断管道是否存在异常振动情况,从而判断管道的运行状态和缺陷情况。
温度监测技术是通过在管道上安装温度传感器或红外测温设备,实时监测管道的温度变化,从而判断管道是否存在过热或过冷等问题。
压力监测技术是通过安装压力传感器或压力表,实时监测管道内部的压力变化,从而判断管道是否存在泄漏或爆炸等风险。
油气管道缺陷无损检测与在线检测诊断技术的探析中,无损检测技术用于对管道进行快速、准确的缺陷判读,可以发现管道的内部和表面缺陷;在线检测诊断技术用于对管道进行实时监测和分析,可以发现管道的运行状态和异常情况。
这些技术的应用可以有效提高油气管道的安全性和可靠性,减少事故发生的风险,具有重要的应用价值。
但同时也需要注意技术的应用和操作规范,避免人为失误和技术误判,确保检测结果的正确性和可靠性。
油气管道无损检测方法的选择

油气管道无损检测方法的选择摘要:本文首先介绍了目前无损检测的应用背景与研究意义,在此基础上,介绍了目前我国应用在油气管道缺陷检测当中的无损检测技术,并分析了各自的优缺点。
通过以不同种典型案例下油气管道缺陷为例,介绍了针对不同工况下无损检测技术的选择方法,为实际的工程应用提供理论指导。
1.前言:随着石油化工产业的逐渐发展,油气管道的建设项目日益增多,石油天然气管道的铺设也与日俱增,但是诸多外界环境因素导致油气管道出现安全事故,逐渐引起人们的重视。
能够在事故发生之前,提前发现检测出安全隐患,可以有效的避免事故的发生。
随着科学技术的发展,无损检测技术得到了快速的发展,在石油天然气管道安全隐患检测中得到了有效的应用。
无损检测技术具有诸多优点,例如不具破坏性、检测较为全面、有助于提高油气管道运行的安全性。
随着无损检测技术在石油天然气管道领域的广泛应用,其检测的可靠与否直接影响到油气管道的安全运行。
一般在检测过程中,检测单位会根据被检测的油气管道的材质、焊接方式以及可能产生的缺陷问题进行评估,选择多种无损检测的方法,相互补充和验证。
为了提高检测结果的准确性,要提前了解被检测物的工况,以及每种无损检测方法的优点与不足,不同的检测部位需要根据自身的特点选择合适的无损检测方法,没有一种无损检测方法是万能的。
在充分考虑不同无损检测方法的优缺点,才能够保证不同的检测方法相互取长补短,更准确的检测出安全隐患[1]。
2.无损检测技术无损检测是指在不损害或不影响被检测对象使用性能、内部组织的前提下,以物理或化学方法为手段,借助现代化的技术和设备器材,对试件内部及表面的结构、性质、状态和缺陷的类型、性质、数量、形状、位置、尺寸、分布及其变化进行检查和测试的方法。
无损检测技术具有两方面的特点,首先是不具有破坏性,在检测过程中对被检测的对象不会造成任何伤害,这也是无损检测方法能够被广泛应用的主要原因;其次,无损检测的检测范围是全面性的,能够对被检测物的内部及表面的结构、性质、状态和缺陷等等特征进行全面的检测[2]。
- 1、下载文档前请自行甄别文档内容的完整性,平台不提供额外的编辑、内容补充、找答案等附加服务。
- 2、"仅部分预览"的文档,不可在线预览部分如存在完整性等问题,可反馈申请退款(可完整预览的文档不适用该条件!)。
- 3、如文档侵犯您的权益,请联系客服反馈,我们会尽快为您处理(人工客服工作时间:9:00-18:30)。
石油工业技术监督·2013年7月无损检测工作的可靠与否直接关系到管道的安全运行。
现行施工及验收规范对无损检测方法的选择有相应的规定,但有些规定比较笼统。
为了提高焊接缺陷的检出率,检测单位应当根据被检管道的材质、焊接方法以及可能产生的缺陷等,选择几种无损检测方法,相互补充和验证。
因为任何一种无损检测方法都不是万能的,每种无损检测方法都有自身的优点与不足,不同的检测部位需要选择不同的无损检测方法。
综合利用各种无损检测方法才能够保证不同的检测方法相互取长补短,更准确的反映焊接缺陷。
1无损检测概述所谓无损检测,是在不损坏试件的条件下,以物理或化学方法为手段,借助先进的技术和器材,对试件的内部及表面的结构、性质状态进行检测和测试的方法。
油气管道常用的无损检测方法有射线检测、超声波检测、磁粉检测和渗透检测。
1.1射线检测利用射线(X射线、γ射线、中子射线等)穿过材料或工件时的强度衰减,检测其内部结构不连续性的检测技术[1]。
1.2超声检测超声波在被检测材料中传播时,材料的声学特性和内部组织的变化对超声波的传播产生一定的影响,通过对超声波受影响的程度和状况,探测了解材料性能和结构变化的检测技术[2]。
1.3磁粉检测利用漏磁(场)和合适的检验介质发现试件表面和近表面的不连续性特征的无损检测方法。
1.4渗透检测利用液体的毛细管作用,将渗透液渗入固体材料表面开口缺陷处。
再通过显象剂将渗入的渗透液吸出到表面,显示缺陷的影像的无损检测方法。
磁粉检测和渗透检测统称为表面检测。
2油气管道常用无损检测方法的特点2.1射线检测2.1.1优点检测结果可用底片直接记录;可以获得缺陷的投影图像,缺陷定性定量准确。
2.1.2局限性体积型缺陷检出率高,而面积型缺陷的检出率受多种因素影响;适宜检验厚度较薄的工件而不适油气管道无损检测方法选择雷晓青中国石油长庆油田分公司技术监测中心(陕西西安710018)摘要分析了油气管道常用无损检测方法的特点,结合多年以来工作经验,提出了油气管道无损检测的选择方法。
指出,应根据施工及质量验收及规范、无损检测标准适用范围、被检焊缝型式和检测部位、可能产生的缺陷种类等方面,选择无损检测方法。
关键词射线检测超声波检测磁粉检测渗透检测油气管道Abstract The features of the commonly used NDT methods for oil/gas-pipeline testing are analyzed,Combined with working experi-ence over the years,how to select the NDT method for oil/gas-pipeline are introduced.The NDT method shall be selected in accor-dance with the construction acceptance criteria and specification,the applicable scope of NDT standard,the to-be-tested welding seam type and testing area,and the possible defect types etc..Key words radiograph inspection;ultrasonic inspection;magnetic particle inspection;fluorescent penetrant inspection;oil/gas pipeline工程质量监督28TECHNOLOGY SUPERVISION IN PETROLEUM INDUSTRY石油工业技术监督·2013年7月宜较厚的工件;适宜检测对接焊缝,检测角焊缝效果较差,不适宜检测板材、棒材、锻件;有些试件结构和现场条件不适合射线照相;对缺陷在工件中厚度方向的位置、尺寸(高度)的定量比较困难;检测成本高,检测速度慢;射线对人体有伤害。
2.2超声检测2.2.1优点面积型缺陷的检出率较高,而体积型缺陷的检出率较低;适宜检验厚度较大的工件,不适宜检验较薄的工件;检测成本低、速度快,仪器体积小、重量轻,现场使用较方便;对缺陷在工件厚度方向上的定位比较准确。
2.2.2局限性无法得到缺陷直观图像,定性困难,定量精度不高;检测结果无直接见证记录;材质、晶粒度对检测有影响;工件不规则的外形和一些结构会不适于超声检测;探头扫查面的平整度和粗糙度对超声检测有一定影响。
2.3磁粉检测2.3.1优点适宜铁磁材料检测,不能用于非铁磁材料检验;可以检出表面和近表面缺陷,不能用于检查内部缺陷;检测灵敏度很高,可以发现极细小的裂纹以及其他缺陷;检测成本低,速度快。
2.3.2局限性工件的形状和尺寸有时对检测有影响,因其难以磁化而无法检测。
2.4渗透检测2.4.1优点渗透检测可以用于除了疏松多孔性材料外任何种类的材料;形状复杂的部件也可用渗透检测,并一次操作就可大致做到全面检测;同时存在几个方面的缺陷,用一次检测操作就可完成检测;不需要大型的设备,可不用水、电。
2.4.2局限性试件表面光洁度影响大,检测结果往往受操作人员水平的影响;可以检出表面开口缺陷,但对埋藏缺陷或闭合型表面缺陷无法检出;检测工序多,速度慢;检测灵敏度比磁粉检测低。
3油气管道无损检测方法的选择根据多年的工作经验,结合相关施工质量验收规范及无损检测标准,无损检测方法的选择,应从以下几方面考虑。
3.1根据施工及质量验收规范选择检测方法施工及质量验收规范已经明确无损检测方法的,必须依据相应的规范执行。
如《石油天然气站内工艺管道工程施工验收规范》(GB50540-2009)第7.4.4条规定:“管道焊缝应进行100%无损检测,检测方法优先选用射线检测或超声波检测,管道最终的连头口、穿越段的对接焊缝应进行100%射线检测加100%超声波检测”。
按照该规范理解,站场内的所有焊口均应进行无损检测,能实施射线或超声波检测的优先选择射线或超声波检测,这两种方法都不能实施时,才允许选择表面检测[3]。
3.2根据无损检测标准适用范围选择检测方法根据无损检测标准的适用范围,结合被检管道的材质、规格,选择合适的无损检测方法,超出无损检测标准范围获得的检测结果是不准确的。
以《石油天然气钢制管道无损检测》(SY/T4109 -2005)为例:射线检测适用于壁厚为2~50mm,材质为低碳钢、低合金钢等金属材料的石油天然气长输、集输及其站场管道环向对接接头的x射线、r射线检测与质量分级。
对于制管焊缝、承插角焊缝等就不能采用本标准实施射线检测。
超声波检测适用于壁厚为5~50mm,材质为低碳钢、低合金钢等金属材料的石油天然气长输、集输及其站场管道环向对接接头的超声波检测与质量分级。
对于弯头与直管、带颈法兰与直管、管径小于57mm、壁厚小于5mm的管对接接头均不能采用该标准进行超声波检测。
3.3根据被检焊缝型式、检测部位选择检测方法不同的焊缝型式、不同的检测部位需要采用不同的无损检测方法。
对接焊缝应优先选择射线或磁粉检测;T型焊接接头、角焊缝应优先选择磁粉或渗透检测;坡口、清根及工卡具焊疤部位应优先选择磁粉或渗透检测。
3.4根据可能产生的缺陷种类选择检测方法了解材料和焊缝中可能产生的缺陷种类,有助于正确选择无损检测方法,制定合理的检测方案。
对于焊缝内部气孔、夹渣、未焊透等体积型缺陷,适宜选择射线检测;对于焊缝内部裂纹、未熔合等面积型缺陷,应选择超声检测,并附加射线检测;对于铁磁性材料钢管及焊缝表面、近表面部位的裂纹、未熔合等缺陷,应选择磁粉检测;对于金属或非工程质量监督29TECHNOLOGY SUPERVISION IN PETROLEUM INDUSTRY石油工业技术监督·2013年7月金属材料管道及焊缝表面裂纹、未熔合等开口型缺陷应选择渗透检测。
4油气管道无损检测方法的选择常存在的误区4.1经无损检测合格的焊口,就能保证焊接质量焊缝的检测方法有外观检测、无损检测、力学性能试验和金相组织检验,只有经过了以上各项检验,才能判定焊缝各项指标合格。
无损检测只能检查焊缝表面或内部组织的致密性,因此,不能仅靠无损检测的结果就判定焊缝是否完全合格。
在实际运用中,由于力学性能、金相检验属于破坏性试验,管道焊缝只能进行外观检测、无损检测和水压试验。
4.2焊接完成即实施无损检测一些具有延迟裂纹的钢材,焊接后短时间不会产生裂纹,而在数小时或者数天后才会出现。
这种钢材必须要考虑无损检测的检验时机,一般安排在焊接完成24h后进行。
4.3不管采取哪种检测方法,都能完全发现焊接缺陷超声波检测对裂纹缺陷探测灵敏度较高,但定性不准,而射线检测对缺陷定性比较准确。
两者配合使用,就能保证检测结果既可靠又准确。
检测人员在检测过程中,对于那些不容易定性的缺陷,必须要借助其它检测方法进行补充检查或验证复查。
4.4射线检测比超声波检测灵敏度高实际应用时,经常存在重射线检测轻超声波检测的现象,具体表现在:(1)由于超声波检测只有检测报告,而没有直观的缺陷图像记录资料,超声检测人员就敷衍了事,不重视、缺乏责任心,有些检测人员甚至不检测就出具虚假检测报告。
(2)超声波检测要求操作人员具有较高的技术水平,要求检测人员熟练掌握理论知识并灵活运用,会调试仪器设备、探头性能等参数,会计算波形所处位置,及时判断是缺陷波还是几何反射波。
若检测人员不能达到上述要求就盲目检测,是很难正确检测出焊缝缺陷的。
(3)超声波检测对检测面的光洁度、焊缝表面缺陷(咬边等)处理要求较高,检测单位缺少相应的表面处理设备及人员,施工、监理单位对管道焊口表面处理质量把关不严格,致使超声波检测结果的可靠性得不到保障。
由于以上因素,人们形成了一种错误的观点,认为超声波检测灵敏度不如射线检测灵敏度高。
从各种检测统计资料来看,就缺陷的检出率,射线检测最高,超声波检测次之,表面检测最低。
所以选用超声波检测方法代替射线检测时,作为建设、监理、检测等单位一定要慎重。
4.5错误理解施工验收规范关于检测方法的规定有些施工及验收规范的制定,没有考虑到检测标准的覆盖范围,超出检测标准范围的焊口,没有明确规定应采取的检测方法。
这样一来,建设单位图省钱,检测单位图省事,对于不能进行超声检测的焊口,就不做任何检测或用表面检测来代替超声检测。
例如《石油天然气站内工艺管道工程施工及验收规范》(SY0402-2000)规定:若管道工作压力为6.4MPa,则超声波检测比例100%,射线抽查比例10%。
实际上直管与弯头、直管与带颈法兰、角焊缝均不能按照SY/T4109-2005实施超声检测,有些单位对这些焊口只进行表面检测或者干脆就不检测了,造成了这些焊口的漏检。