提高滚动轴承套圈滚道和滚子精度有序超精法
用“正交试验法”优化精超滚锥轴承滚道的工艺参数

L efn I Yu e g
( e at n f c aia E g er gT c nlg , a a oaia C l g ,D l n Lann 0 7 D pr met h ncl n i ei eh o y D l n V cncl ol e a a ioig1 6 3 , o Me n n o i e i 1
排 见 表 5所 示 。
1 2 试 验 方 案 设 计 .
1 3 试 验 结 果 及 分 析 .
() 1 制定 因 素水平 表 : 响精 超 加工 质 量 的 因 素 影 较 多 , 过分 析筛 选 , 定 考 察超 精 时 间 、 件 转 速 、 经 确 工 油石 硬度 、 精 头压 力 、 精 头 振 频 、 超 超 超精 头 振 幅 、 超 精头 往复 速度 七 个 因 素 。这 七个 因素 均 可 以 取各 种 水平 , 形成 无 数种 组合 , 虑工 件 的超精 时 间对精 超 考
1 优化 精超滚 锥轴 承套 圈滚 道工 艺参数 的试验
1 1 试 验 条 件 .
() 1 试验 设 备 :S 3 0滚 子轴 承滚 道 超 精 机 , JF0 主
要 性 能参数 见表 1 示 。 所
表 1 超 精 机 主 要 参 数
设 备 型 号 主 轴 转速
/ r・ mi 。 n 。
验 , 过 试 验 的 方 法 确 定 其 工 艺 参 数 。 为 了 通 过 通
最 少 的试 验 , 得 最 佳 的 效 果 , 定 用 “ 交 试 验 获 确 正
法’ ’ 。
高精度轴承关键部件精密超精密加工技术

精密·制造
三、高精度轴承的精密超精密加工技术
1 磨削加工技术
加工工艺:
磨削是指用磨料,磨具切除工件上多余材料 的加工方法。磨削加工是应用较为广泛的切削加 工方法之一。
根据工艺目的和要求不同,磨削加工工艺方法有多种形式,为了适应发展需要, 磨削技术朝着精密,低粗糙度,高效,高速和自动磨削方向发展。磨削加工方法的形
2 3 6
深沟球轴承
5
圆锥滚子轴承
推力球轴承
精密·制造
二、高精度轴承各部件加工工序概述
2 轴承的结构(深沟球轴承)
精密·制造
二、高精度轴承各部件加工工序概述
3 轴承加工工艺流程
洛阳汇普轴承加工流程图
精密·制造
二、高精度轴承各部件加工工序概述
保持架
体用 并以 将隔 其离 保滚 持动 在体 轴︐ 承通 内常 ︒还 引 导 滚 动 原材料——剪料——裁环——光整——成形——整形——冲铆钉孔
实际切削路程比普通磨削路程要长;
实际的切削宽度增加,增大金属去除率,提高生产效率; 单颗磨粒的运动轨迹为正弦曲线,一个砂轮上拥有多颗磨粒,相邻的磨粒运动 轨迹便会重叠,使被加工工件表面成网状结构,有利于提高工件的表面质量。
磨削力比普通磨削要小,这样便可以提高加工的稳定性,减小磨削热的产生,
精密·制造
三、高精度轴承的精密超精密加工技术
4 油石超精研加工技术
目前轴承超精密加工中广泛采用的是油石超精研 加工,简称超精加工,一般是指用低压弹性地将细粒 度磨料的油石压在工件加工表面上,工件做旋转运动, 油石在垂直于工件旋转方向上按一定规律做快速往复 摆动,并提供良好的润滑与冷却条件,降低加工表面 粗糙度,提高几何精度。
可实现超精密性能的轴承解决方案

可实现超精密性能的轴承解决方案致力于追求精密及性能,助您步向成功在机床行业取得成功要靠顶尖性能。
扩展速度能力、维持高旋转精度、高系统刚性、生热低、噪音低、振动级低,只是众多要求中的一部分而已。
SKF 新一代超精密轴承足以满足精密应用中对性能不断提高的要求。
除了具有高度创新的方案之外,我们的专家还持续提供销售和应用工程支持。
我们对于追求超精密性能巨细靡遗。
定制解决方案定制能力是我们的关键优势之一。
我们可以根据要求,提供特定的内外径公差,不同接触角的配组轴承,特别预负荷,特殊轴向游隙,个别装填等级,特殊油脂,具体包装要求,检测报告,以及其他方案。
改进性能机床设计正变得越来越复杂。
为了满足对主要部件的特殊要求,我们进一步开发出超精密轴承,以提高性能、机器运行时间、速度和精度。
这些改进包括:•提供更多尺寸和系列的密封轴承,在轴承内预存润滑脂并将污物排除在外,而不影响速度性能•提供更多预负荷等级,在速度和刚性方面支持几乎所有可能的需求•优化内外圈倒角,以改进安装精度•优化轴承保持架和外圈之间的引导间隙,以提高在高速时的表现•附加特点,如在开式轴承外圈具有两个润滑孔,以便直接进行油润滑,达到更高速度的同时降低运行温度•优化轴承内部配置,并为N10系列圆柱滚子轴承重新设计一个 PEEK保持架,以使其在脂润滑时能将速度提高达30%•优化的BTW系列设计(双向角接触推力球轴承)以提高速度性能,减少摩擦、噪音和振动等级,减少重量,方便操作,更精确的预负荷控制和改进系统刚性体验SKF新一代超精密轴承的积极成效提供更多价值的应用合作伙伴专门的应用知识深入了解主轴轴承如何应对不同的操作条件,对于开发可靠的解决方案十分重要。
我们在SKF的生产过程均采用高精密机床。
我们所有的客户都能分享到我们的产品和服务中所体现出的经验和专门技能。
全球性主轴服务中心我们的技术中心拥有轴承、润滑、密封件、状态监测和其他各方面的专家团队,为世界各地的机床行业提供服务。
增加超精研工序提高钢球精度,降低球轴承异音
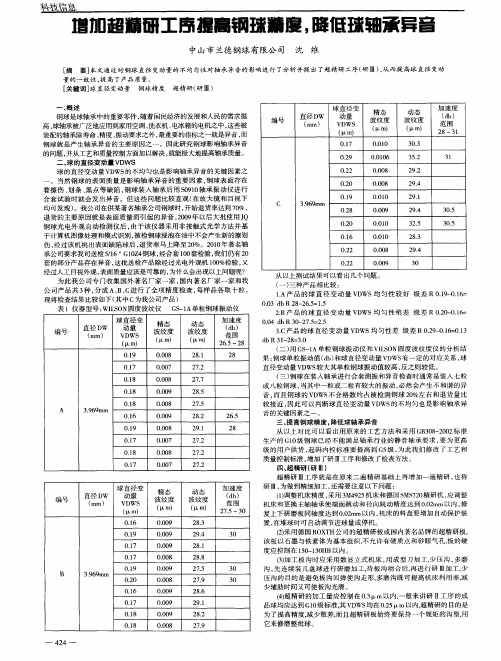
[ 关键词 ] 球直径 变动量 钢球精度 超精研( Ⅲ) 研
一
、
概 述
钢球是球轴承 中的重要零件, 随着 国民经济的发展和人 民的需求提 高, 球轴承被广泛地应用到家用空调 、 洗衣机 、 电冰箱的电机之 中, 这些被
编号
球 直径 变 精 态 直径 D W 动量 波纹度 ( mm) VD WS
( m)
O1 .7 O2 .9 O-2 2 02 .O O 1 .9
动 态 波纹度
( m】
3 . 03 3 . 52 2 2 9. 2 4 9. 2 1 9. 2 . 94 3 . 25 2 _ 83 2 . 94 3 0
( m)
00 0 .1
一
。
C
3.6 mm 99
O.8 2 0-0 2 O.6 1 0. 22 0. 22 3 . 05 3 . 05
从 以上测试结果可 以看 出几个问题 。 ( ) 一 三种 产 品相 比较 : 1 . 品 的球 直径 变 动量 V WS均 匀性 较好 级 差 R 01— . - A产 D . 0 6 9 1-
2 4 9. 2. 81
2 . 88 2 . 75
3 0
( ) G 一 A 粒钢球振动仪和 V L O 二 用 S 1单 IS N圆度波纹度仪 的分析结 果: 钢球单粒振动值 (b 和球 直径变动量 V WS d) D 有一定的对应关 系, 球 直径变动量 V WS 大其单 粒钢球振 动值较 高 , D 较 反之则 较低 。 ( ) 三 钢球在装入轴承进行合套 测振 和异音检查时通常是装入七 粒 或八粒钢球 , 当其 中一粒 或二粒 有较 大的振动 , 必然会产生不 和谐 的异 音, 而且钢球 的 V WS D 不合格数 约 占被检 测钢球 2 %左 右和退货量 比 0 较接 近 , 因此可 以判断球直 径变动量 VD WS的不均匀也 是影响轴承 异 音 的关键 因素之一 。 三、 提高钢球精度 。 降低球轴承异音 从 以上对 比可以看 出用原 来 的工 艺方法 和采 用 G 3 8 2 0 标 准 B 0—02 生产的 G1 级 钢球 已经不 能满足轴 承行业 的静 音轴承要求 , 为更 高 0 要 级 的用户供货 , 起码 内控标 准要提 高到 G 级 , 5 为此我们 修改 了工艺 和 质量控制标准 , 增加 了研 Ⅲ工序 和修改 了检查方法 。 四、 精研 ( Ⅲ) 超 研 超精研 Ⅲ工序 就是在原来 二遍精研 基础上再增 加一遍精研 , 也称 研 Ⅲ, 为做 到精 细加工 , 还需要 注意以下 问题 : () 1 调整机床精度 , 采用 3 9 5 M4 2 机床 和德国 S 7 0 MS 2 精研机 , 应调整 机床和更换主轴轴 承使端 面跳动和径 向跳动精度达 到 O 2 m以内, .m 0 修 复上下研磨板 同轴度 达到0 2 m以内, 床的料盘要增加 自动保护装 .r 0a 机 置, 在堆球时可 自动调节进球量或停机。 f1 2采用德 国 R X H公司 的超精研 板或 国内著名 品牌的超精研板, OT 该板 以石墨与铁素 体为基本组织 , 不允许有 硬质点和砂 眼气孔, 的硬 板
滚动轴承滚道磁力研磨超精加工的实验研究

滚动轴承滚道磁力研磨超精加工的实验研究湛江海洋大学工程学院 张世亮 何 真 摘要 介绍了用磁力研磨装置对滚动轴承滚道进行超精加工的方法,阐述了该磁力研磨装置的设计与计算,给出了实验初步结果。
该加工方法为滚动轴承滚道的超精加工提供了一种新的途径。
关键词 轴承滚道 磁力研磨 超精加工1 概述 滚动轴承是仪器设备中广泛使用的支承件。
在许多精密仪器设备中,滚动轴承的工作精度对仪器设备的使用性能有着很大的影响。
滚动轴承内外圈滚道和滚动体的超精研磨加工,是滚动轴承制造中一项非常重要的加工内容,是确保滚动轴承制造精度、使用寿命的重要环节。
多年以来,国内的各轴承制造企业都是采用以油石研磨为工作原理的各种轴承超精研磨机来对轴承内外圈滚道进行超精加工的。
尽管此加工方法具有加工效率高,能满足加工精度要求的优点,但也存在着机床结构复杂,污染环境,机床的调整操作费事,操作工人工作环境恶劣且劳动强度大,以及对前道工序的形位精度有一定影响等缺点。
2 工作原理及研磨装置 磁力研磨是一种较新的超精加工方法。
它能实现对金属材料或非金属材料的内外圆柱表面、球面、平面及各种异型曲面的研磨、抛光、去毛刺等加工[1、2]。
这种加工方法的最大特点就在于其磨具为柔性磨具(由磨料形成的磁刷),磨料(具)对工件表面的形状能很好地适应,它在对工件表面进行研磨的同时能较好地保持工件表面原有的形位精度。
磨料(磁刷)刚度的大小由磁场励磁电流的强弱来决定,通过调节磨具刚度的大小,就能调节磨具对工件表面研磨力的大小。
磁力研磨使用的磨料为磁性磨料(具有导磁性能的铁粉材料和具有研磨性能的氧化铝、氧化钛等金属陶瓷微粉材料。
将这两种材料按照4∶1的比例混合后烧结,然后粉碎成平均直径为50L m左右的微粉磨料)。
处在磁场和磨料中的工件,在旋转的同时再叠加一个微小的轴向振动,利用磁刷与工件之间的相对运动,使磁刷逐渐削去工件表面的微小凸起,以达到对工件研磨的目的。
根据上述原理,笔者在C6132A普通车床上研制出了一套滚动轴承外圈滚道磁力研磨实验装置,其结构原理如图1所示。
我国轴承套圈超精研技术的改进要点

我国轴承套圈超精研技术的改进要点我曾经在《怎么样提高高精度轴承的超精质量?》一文中写到:“超精加工主要要提高和改善被加工工件表面的微观质量,这些微观质量包括粗糙度、沟形、圆度和金属条纹的走向。
”轴承套圈沟道超精研工序主要是为了降低被加工沟道的粗糙度,这是最基本的要求,无论是最原始的棍棒超精机还是采用无心支撑结构的自动化超精机,原理大同小异,都是如此。
高水平的和低档的轴承套圈超精研设备的主要区别是轴承套圈沟道形状精度的改善程度和被加工工件表面应力状态的差异。
轴承套圈沟道形状精度的改善主要取决于三个方面:首先,要约束超精前的轴承沟道磨加工形状的基础精度,轴承沟道的基准精度和位置精度在磨削工序也要精确地控制,因为这些需要约束的被加工工件的磨削工序的精度及其对超精加工的结果的影响是不容忽视的;其次,超精研设备的制造精度也会对被超精工件沟道表面形状的变化起到很大的影响,品质较差的超精机非但不能够改善磨削工序形成的形状精度,反而会破坏磨削工序形成的形状精度;第三,超精余量的大小不仅与超精加工的节拍有关,而且也与轴承沟道超精后的表面质量有关系。
假如我们的轴承产品没有对轴承的噪音和轴承的寿命提出特殊的要求,假如我们的轴承产品仅仅满足于参与国内外市场的低价格竞争,假如我们的轴承产品不想走出国门或者不想替代进口产品,那么,使用低价位的超精研设备是可以的。
因为,在中低档产品的轴承市场上,中国的轴承企业打了很多顽强的战役,在空调类家电市场和电机市场,我们的微型和小型轴承取得了不俗的销售业绩,这些成绩的取得也部分得益于我国轴承加工设备的发展和进步。
而在我国高精尖产品领域,大量的高附加值高利润轴承还是依靠进口。
我国生产的最好的轴承设备,即使出口到国外,也只是应用在普通轴承生产线上;部分大陆境内的外资和合资的轴承加工企业采购国内的轴承设备,也主要用在中低档轴承的生产线上。
迄今为止,我国高水平的进口轴承设备所占的比率很小,部分原因是由于高水平的进口轴承设备的价格普遍高于国产的轴承设备,其主要原因还是国内大部分企业生产的轴承精度和效率要求偏低,在引进更好水平的进口轴承设备方面的要求还不是特别强烈。
提高汽车滚动轴承质量的方法

提高汽车滚动轴承质量的方法
1. 采用高品质材料。
选用高强度、高耐磨、高温抗性等特殊材料,能够提高滚动轴承的质量。
2. 提高制造精度。
通过提高制造精度、加工精度和检验精度等手段,能够有效改善滚动轴承的加工精度和规格精度。
3. 加强润滑和封闭。
通过合理的润滑和封闭方式,能够有效降低滚动轴承的磨损和使用寿命。
4. 增加附加装置。
通过增加附加装置,如封盖、挡圈等,能够有效减少外力对滚动轴承的影响,提高其使用寿命。
5. 优化结构设计。
通过优化结构设计,如优化滚子数量、倾角、尺寸等,能够显著提高滚动轴承的耐磨性和使用寿命。
6. 加强质量管理。
通过质量管理手段,如全面质量管理、应力分析等,能够有效降低滚动轴承的失效率,提高其质量和使用寿命。
高精度轴承的装配与调整
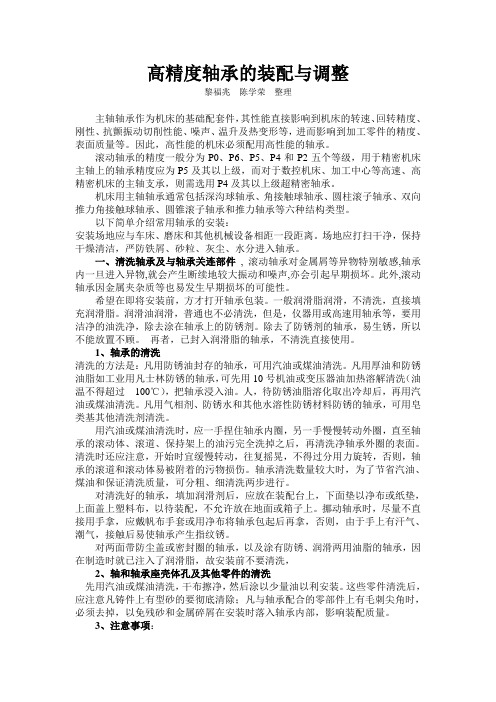
高精度轴承的装配与调整黎福兆陈学荣整理主轴轴承作为机床的基础配套件,其性能直接影响到机床的转速、回转精度、刚性、抗颤振动切削性能、噪声、温升及热变形等,进而影响到加工零件的精度、表面质量等。
因此,高性能的机床必须配用高性能的轴承。
滚动轴承的精度一般分为P0、P6、P5、P4和P2五个等级,用于精密机床主轴上的轴承精度应为P5及其以上级,而对于数控机床、加工中心等高速、高精密机床的主轴支承,则需选用P4及其以上级超精密轴承。
机床用主轴轴承通常包括深沟球轴承、角接触球轴承、圆柱滚子轴承、双向推力角接触球轴承、圆锥滚子轴承和推力轴承等六种结构类型。
以下简单介绍常用轴承的安装:安装场地应与车床、磨床和其他机械设备相距一段距离。
场地应打扫干净,保持干燥清洁,严防铁屑、砂粒、灰尘、水分进入轴承。
一、清洗轴承及与轴承关连部件, 滚动轴承对金属屑等异物特别敏感,轴承内一旦进入异物,就会产生断续地较大振动和噪声,亦会引起早期损坏。
此外,滚动轴承因金属夹杂质等也易发生早期损坏的可能性。
希望在即将安装前,方才打开轴承包装。
一般润滑脂润滑,不清洗,直接填充润滑脂。
润滑油润滑,普通也不必清洗,但是,仪器用或高速用轴承等,要用洁净的油洗净,除去涂在轴承上的防锈剂。
除去了防锈剂的轴承,易生锈,所以不能放置不顾。
再者,已封入润滑脂的轴承,不清洗直接使用。
1、轴承的清洗清洗的方法是:凡用防锈油封存的轴承,可用汽油或煤油清洗。
凡用厚油和防锈油脂如工业用凡士林防锈的轴承,可先用10号机油或变压器油加热溶解清洗(油温不得超过100℃),把轴承浸入油。
人,待防锈油脂溶化取出冷却后,再用汽油或煤油清洗。
凡用气相剂、防锈水和其他水溶性防锈材料防锈的轴承,可用皂类基其他清洗剂清洗。
用汽油或煤油清洗时,应一手捏住轴承内圈,另一手慢慢转动外圈,直至轴承的滚动体、滚道、保持架上的油污完全洗掉之后,再清洗净轴承外圈的表面。
清洗时还应注意,开始时宜缓慢转动,往复摇晃,不得过分用力旋转,否则,轴承的滚道和滚动体易被附着的污物损伤。
滚子轴承套圈滚道凸度超精加工方法介绍
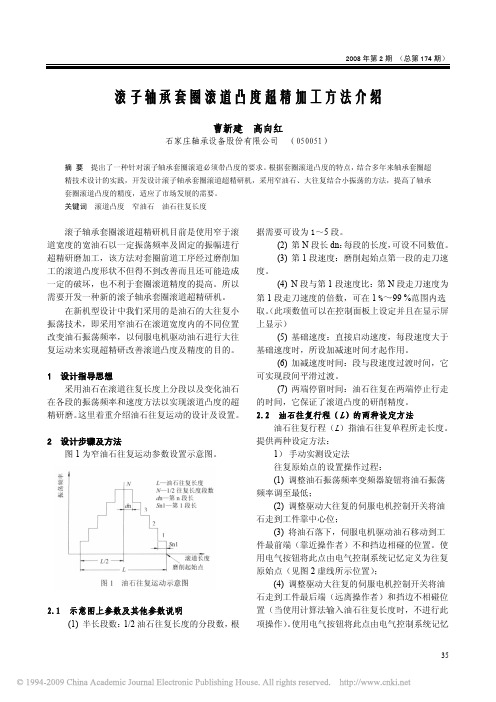
滚子轴承套圈滚道凸度超精加工方法介绍曹新建 高向红石家庄轴承设备股份有限公司 (050051)摘 要 提出了一种针对滚子轴承套圈滚道必须带凸度的要求。
根据套圈滚道凸度的特点,结合多年来轴承套圈超精技术设计的实践,开发设计滚子轴承套圈滚道超精研机,采用窄油石、大往复结合小振荡的方法,提高了轴承套圈滚道凸度的精度,适应了市场发展的需要。
关键词 滚道凸度 窄油石 油石往复长度滚子轴承套圈滚道超精研机目前是使用窄于滚道宽度的宽油石以一定振荡频率及固定的振幅进行超精研磨加工,该方法对套圈前道工序经过磨削加工的滚道凸度形状不但得不到改善而且还可能造成一定的破坏,也不利于套圈滚道精度的提高。
所以需要开发一种新的滚子轴承套圈滚道超精研机。
在新机型设计中我们采用的是油石的大往复小振荡技术,即采用窄油石在滚道宽度内的不同位置改变油石振荡频率,以伺服电机驱动油石进行大往复运动来实现超精研改善滚道凸度及精度的目的。
1 设计指导思想采用油石在滚道往复长度上分段以及变化油石在各段的振荡频率和速度方法以实现滚道凸度的超精研磨。
这里着重介绍油石往复运动的设计及设置。
2 设计步骤及方法图1为窄油石往复运动参数设置示意图。
图1 油石往复运动示意图2.1 示意图上参数及其他参数说明(1) 半长段数:1/2油石往复长度的分段数,根据需要可设为1~5段。
(2) 第段长dn :每段的长度,可设不同数值。
(3)N 第1段速度:磨削起始点第一段的走刀速度。
段与第1段速度比:第N 段走刀速度为第1速度:直接启动速度,每段速度大于基础,它可实平石往复在两端停止行走的时保长度。
提供法程:钮将油石振荡频率大往复的伺服电机控制开关将油石走服电机驱动油石移动到工件最控制开关将油石走(4) N 段走刀度的倍数,可在1 %~99 %范围内选取。
(此项数值可以在控制面板上设定并且在显示屏上显示)(5) 基础速速度时所设加减速时间才起作用。
(6) 加减速度时间:段与段速度过渡时间,现段间滑过渡。
轴承套圈滚道自动超精研机的电气设计

将加工完的工件通过下料槽送到下一工序 , 接料
架又从上料槽取套圈开始下一个加工循环。
件 电动机) 采用 15 W 、2 l 5 rn的电磁 . k 15一 0 / i 2 ra 3 1 电气设 计要求 . 调速异步电动机。 为方便机床调试 和零件加工 , 床需设计 有 机 油石振荡采用大 往复、 小振荡的方式。大往
4 3 半 自动操 作 .
\
鹎岛墩 油石 抬起 大往复停
l
.
/
l Y
拖板退 回 , 闭 关 主轴和振荡
将S A置于“ 周期” 按 S 2 挡, B 启动油
泵 , S3 按 B 启动 自动循环, 机床按 自动程
( 轴伸 出 ) 芯 压轮压 接料架返回
l Y
换成精超油石
( 洛阳大学 电信学院, 河南 洛 阳 4 12 ) 7 03
摘 要: 采用 P C控制机床的顺序动作 , L 实现了加工的 自动化 , 通过控制主轴转速和油石振荡速度 , 可满足各种滚
道 超精 的技术指标要求 。
关键词 : 滚动轴承 ; 滚道 ; 超精加工机 ; L PC 中图分类号 :H 3 .3" 8 .3 4 T 1 33 ; ̄5 0 2 ’ I 文献标志码 : B 文章编号 :00—36 ( 07 1 —02 O 10 7 2 2 0 ) 1 05一 3
损至需更换 时自动停机并使机床退至加工 的初始 状态 ,双油石工作 ) ( 油石转换 、 油石抬起 、 大往 复 进退、 粗超和精超的时间可根据工件情 况调整控
制。
单步时 , 自动加工 流程每启动一次走 一个 按 工步。
周期时, 启动后按 自动加工流程走 完一个循
环 即停 。
超精工艺

轴承套圈的超精加工技术简介一、概述轴承套圈经过下料、初期热处理、车削加工、中期热处理、磨削加工以后。
经过一系列严格检验后,就进入了超精加工工序。
轴承套圈超精加工主要是为了降低轴承套圈沟道或滚道的表面粗糙度,改善轴承套圈沟道或滚道的表面的应力状态。
除非上道工序对应的沟道或滚道磨削后的表面形状精度较低,轴承套圈超精加工一般不会改变加工面的形状精度和位置精度。
轴承套圈超精加工“是一种用细粒度的磨具对工件施加很小的压力,并作往复振动和慢速纵向进给运动,以实现微量磨削的一种加工方法”。
超精加工一种说法是由美国哥赖斯拉公司的维拉斯发明的,当时由于汽车车轮的滚子轴承经常产生异常的振动和噪声,问题出于轴承滚子在轴承套圈表面形成压痕所致。
经过采用软材料研磨轴承滚道表面之后,不但可以避免使轴承套圈工作表面产生压痕,而且还使得振动和噪声显著降低了。
维拉斯把这一加工方法实现了机械化,这就是最早的轴承套圈超精机。
轴承超精加工虽然发明在美国,但是现在在欧洲和日本得到进一步发展。
尤其是德国Thielenhaus公司,在轴承超精加工领域的研发技术居世界领先水平。
二、超精研加工工艺参数的选择超精研的工件旋转速度、施加于油石上的单位面积的压力、油石的振荡频率和振幅是超精研加工的主要工艺参数,这些参数的选择直接影响超精机加工工件的加工表面质量。
就加工方式来讲,一般分为采用一种油石和采用多种油石两种。
前者是采用一块油石把工作条件分为两段,称为一序两段法。
初超时,选择大的切削角,加大油石压力,就会使磨粒大量的破碎和脱落,尽可能地把前道工序的加工痕迹去掉。
前道工序的痕迹去掉后,加工表面呈梨皮形状,就得到人们称之为的超精加工的磨纹,这时就把切削角减小,降低油石压力,于是磨粒的切削作用也就降低,继续加工是把粗超时的痕迹除掉,逐渐得到平滑的加工表面,这时磨粒与加工表面的接触面积增加,进一步增加接触面积,油石就会气孔堵塞,最后致使切削完全停止,只作光超。
提高轴承紧固件生产效率的方法和工艺改进措施

提高轴承紧固件生产效率的方法和工艺改进措施提高轴承紧固件生产效率的方法和工艺改进措施随着工业化的发展和现代化制造业的需求不断增长,轴承紧固件的生产效率成为了生产制造企业关注的重点。
轴承紧固件在机械设备中起到连接和支撑的作用,其质量和性能直接关系到整个设备的正常运行和使用寿命。
提高轴承紧固件的生产效率既能增加企业的经济效益,也能提高产品质量,满足市场需求。
本文将从材料选择、工艺改进和设备优化等多个方面探讨提高轴承紧固件生产效率的方法和措施。
一、材料选择1.选择优质材料:轴承紧固件的材料要求具有一定的强度和硬度,能够耐受大扭矩和高温等复杂工况。
因此,在材料选择上应优先考虑高强度合金钢等优质材料,以提高轴承紧固件的使用寿命和可靠性。
2.材料优化:通过优化材料的化学成分和热处理工艺,可以提高轴承紧固件的硬度和强度,减少变形和断裂的可能性,同时提高生产效率。
二、工艺改进1.自动化生产:采用自动化生产线或机器人生产线,可以提高轴承紧固件的生产效率。
自动化生产能够实现从材料进料、加工、检测到包装的全过程自动化控制,减少人工操作,提高生产效率和产品一致性。
2.工艺优化:通过优化生产工艺,减少生产过程中的浪费和不良品的产生,从而提高产出率和利用率。
工艺优化可以包括工艺流程的优化、工艺参数的优化和设备配置的优化等方面。
3.工艺流程的简化:通过简化工艺流程,减少环节和操作,缩短生产周期,提高生产效率。
应重点关注生产过程中的瓶颈环节和低效环节,进行改进和优化。
4.装配工艺改进:在轴承紧固件的装配过程中,采用快速装配工艺和夹具,减少装配时间和人工操作,提高装配精度和效率。
5.质量控制和检测:建立完善的质量控制体系,加强对轴承紧固件的质量检测和监控,及时纠正生产中的问题和不良品,提高产品质量和出厂合格率。
三、设备优化1.设备更新和升级:及时更新和升级生产设备,采用先进的生产技术和设备,提高设备的自动化程度和生产效率。
特别是在高速、高精度和大批量生产中,应选择适应性强、稳定可靠的设备。
提高滚动轴承套圈滚道和滚子精度的有序超精法

讨 和经验 ,分析 选择一种 科学获取 超精参 数的方 法—— 有序超精法进行超精加工 ,以改善超精后 的 轴承套圈滚道 ,特别是大型轴承套圈滚道 、滚子精 度 ,从而满足高精度轴承的精度和低噪声要求。
这 里 所 说 的 轴 承 套 圈 滚道 是 广 义 的 ,而 滚 子 则
圈在装配后的回转精度就不高 ,且在 高速运转时会
套 圈
有 较 大 噪 声 。而 形 成 轴承 的滚 道 、滚 子 沿 轴 线剖 面
内轮廓度在 不同圆周角度上不一致 ,以及滚道、滚
子 的 圆度值 在 轴 向各 不 同 圆截 面 上不 一 致 且形 状 不 同的 原 因 ,就 是 传 统 的 习惯 性 对轴 承 套 圈滚 道 、滚
明工 件 主轴 的 调 速范 围 、油石 振 荡 架 的往 复 频 率 范
套圈的超精转速就越小 ,越容易超坏滚道轮 廓度 。 那么 ,传统的超精方法问题 出在哪里呢?
假 如 油 石 架 的往 复 频 率 等于 工件 转 速 ,比 如 工
围和往复幅度范围 ,有的超精机是将往复和振荡分 开控制的 ,结构较复杂 ,即往 复是大幅度小频次机
生 。 因为超 精 的 线速 度相 对 是要 恒 定 在 一个 合 适 范
围内,线速度太慢会影响表面粗糙度和效率 ,但太 快又会出现表面烧伤或粘铁 ,因此 ,线速度过慢和
过 快 都 影 响超 精 质 量 。而 且 ,所超 套 圈直 径越 大 ,
超精机极其罕见。即使是数控控制 ,一般会针对振 荡头的往复运动速度和幅度进行控制 ,但超精机 的 工件主轴转速通常被认为没必要进行数控控制。国 产超精机的使用说 明书 中通常都会在规格参数栏标
目前 ,国内外生产的超精机的主轴转动通常是 采用直流或交流变频调速的 ,振 荡架的振 荡频率也
超精油石对轴承套圈的加工技术

超精油⽯对轴承套圈的加⼯技术轴承套圈磨超加⼯新技术及其国内外发展状况-->1.前⾔作为整个⼯业基础的机械制造业,正在朝着⾼精度、⾼效率、智能化和柔性化的⽅向发展。
磨削、超精研加⼯(简称“磨超加⼯”)往往是机械产品的终极加⼯环节,其机械加⼯的好坏直接影响到产品的质量和性能。
作为机械⼯业基础件之⼀轴承的⽣产中,套圈的磨超加⼯是决定套圈零件乃⾄整个轴承精度的主要环节,其中滚动表⾯的磨超加⼯,则⼜是影响轴承寿命以及轴承减振降噪的主要环节。
因此,历来磨超加⼯都是轴承制造技术领域的关键技术和核⼼技术。
国外轴承⼯业,60年代已形成⼀个稳定的套圈磨超加⼯⼯艺流程及基本⽅法,即:双端⾯磨削——⽆⼼外圆磨削——滚道切⼊⽆⼼磨削——滚道超精研加⼯。
除了结构特殊的轴承,需要附加若⼲⼯序外,⼤量⽣产的套圈均是按这⼀流程加⼯的。
⼏⼗年来,⼯艺流程未出现根本性的变化,但是这并不意味着轴承制造技术没有发展。
简要地说,60年代只是建⽴和发展“双端⾯——⽆⼼外圆——切⼊磨——超精研”这⼀⼯艺流程,并相应诞⽣了成系列的切⼊⽆⼼磨床和超精研机床,零件加⼯精度达到3~5um,单件加⼯时间13~18s(中⼩型尺⼨)。
70年代则主要是以应⽤60m/s⾼速磨削、控制⼒磨削技术及控制⼒磨床⼤量采⽤,以集成电路为特征的电⼦控制技术的数字控制技术被⼤量采⽤,从⽽提⾼了磨床及⼯艺的稳定性,零件加⼯精度达到1~3um,零件加⼯时间10~12s。
80年代以来,⼯艺及设备的加⼯精度已不是问题,主要发展⽅向是在稳定质量的前提下,追求更⾼的效率,调整更⽅便以及制造系统的数控化和⾃动化。
2.轴承套圈的磨削加⼯在轴承⽣产中,磨削加⼯劳动量约占总劳动量的60%,所⽤磨床数量也占全部⾦属切削机床的60%左右,磨削加⼯的成本占整个轴承成本的15%以上。
对于⾼精度轴承,磨削加⼯的这些⽐例更⼤。
另外,磨削加⼯⼜是整个加⼯过程中最复杂,对其了解⾄今仍是最不充分的⼀个环节。
- 1、下载文档前请自行甄别文档内容的完整性,平台不提供额外的编辑、内容补充、找答案等附加服务。
- 2、"仅部分预览"的文档,不可在线预览部分如存在完整性等问题,可反馈申请退款(可完整预览的文档不适用该条件!)。
- 3、如文档侵犯您的权益,请联系客服反馈,我们会尽快为您处理(人工客服工作时间:9:00-18:30)。
35提高滚动轴承套圈滚道和滚子精度的有序超精法无锡机床股份有限公司 (江苏 214061) 胡建清本文分析滚动轴承套圈、特别是大、中型轴承套圈或滚子超精加工后,轴承成品在使用中无法达到较高精度要求、回转精度不高,且可能在高速运转时产生较大噪声的原因,结合笔者长期以来的探讨和经验,分析选择一种科学获取超精参数的方法——有序超精法进行超精加工,以改善超精后的轴承套圈滚道,特别是大型轴承套圈滚道、滚子精度,从而满足高精度轴承的精度和低噪声要求。
这里所说的轴承套圈滚道是广义的,而滚子则主要是指调心轴承用的滚子(直径较大的腰鼓形柱体)。
1. 产生超精参数选择不当原因仅以圆柱滚子轴承的外圈进行滚道超精为例,结合轴承外圈滚道超精示意图(见图1),分析重要原因之一:模糊超精导致超精参数选择不当。
圈旋转一个角度后检测沿轴线与另一个直径组成的剖面内滚道的直线度则变为0.002mm ;并且轮廓形状也不同,前者可能为中凸偏左如图2a 所示,最高点在距基准端面为a 的位置,但后者可能变为中凸偏右如图2b 所示,最高点在距基准端面为b 的位置。
以及滚道、滚子的圆度值在轴向各不同圆截面上不一致。
例如在距滚道基准面轴向距离为a 处测得的圆度为0.001 5mm ,但在距滚道基准面轴向距离为b 处的圆度可能就为0.002 5 mm 了,并且圆度的形状也可能存在差异,从而该轴承圈在装配后的回转精度就不高,且在高速运转时会有较大噪声。
而形成轴承的滚道、滚子沿轴线剖面内轮廓度在不同圆周角度上不一致,以及滚道、滚子的圆度值在轴向各不同圆截面上不一致且形状不同的原因,就是传统的习惯性对轴承套圈滚道、滚子的模糊超精形成的。
我们假设滚子磨削加工精度和轴承套圈终磨削加工精度都是理想的,以便于集中讨论轴承套圈终磨削后的超精过程;另外,可以从本文下面所叙述的有序超精原理,自然延伸和理解滚子的超精过程及其他种类套圈的超精过程,用相同的方法来解决所有类似的问题。
轴承业人士知道,在对如图1的轴承滚道进行超精时是由如下动作实现的:超精机工件主轴带动轴承套圈作旋转运动;油石通过气动或液动的压力将端头压在轴承套圈被超精的滚道面上,并在超精图1 轴承外圈滚道超精示意图1中,A 为轴承外圈滚道宽度,C 为轴承外圈宽度,D 为轴承外圈外径,d 为轴承滚道内径,B 为油石的宽度,W 为油石的厚度(指油石与滚道超精面中点的切线方向上)。
模糊超精的实际超精参数极有可能因不当,从而导致轴承的滚道、滚子沿轴线剖面内的轮廓度在各圆周角度上不一致。
例如在沿轴线与一个直径组成的剖面内滚道的直线度为0.003mm ,但将轴承套图 2(注:为清晰表述,图中画出轮廓有夸张)(b )(a )机的油石振荡架带动下,沿轴承套圈宽度方向作往复运动来达到对轴承套圈滚道表面进行超精加工的目的。
目前,国内外生产的超精机的主轴转动通常是采用直流或交流变频调速的,振荡架的振荡频率也是通过直流电动机或交流变频调速的,采用数控系统进行伺服控制工件主轴转速和振荡架往复运动的超精机极其罕见。
即使是数控控制,一般会针对振荡头的往复运动速度和幅度进行控制,但超精机的工件主轴转速通常被认为没必要进行数控控制。
国产超精机的使用说明书中通常都会在规格参数栏标明工件主轴的调速范围、油石振荡架的往复频率范围和往复幅度范围,有的超精机是将往复和振荡分开控制的,结构较复杂,即往复是大幅度小频次机构实现的,其移动幅度接近于滚道轴向全长;振荡是小幅度、高频次机构实现的,其移动幅度只有零点几或几毫米。
但更多的超精机形式是:振荡动作就是往复动作,往复和振荡是同一个动作,本文为了能简要说明问题,以便于对有序超精的理解,就以振荡和往复是同一个动作作为研究对象。
当然,所叙述的原理对于同时具有分开控制油石往复运动和振荡的超精机也是同样适用的。
所以,本文以针对移动幅度接近于滚道轴向全长的往复加以叙述为主,简要附带分析移动幅度很小的高频振荡。
在轴承生产厂家的操作工对轴承套圈进行超精加工时,会将工件转速和油石振荡往复频率和幅度调到一个认为合适的区间,然后对被超精的轴承套圈进行超精加工,以规格大小不同来控制超精时间的长短。
一般规格越大,所需超精的时间就越长,比如从几秒到几百秒不等。
操作工对超精中转速、往复频率、时间这三个参数控制并不是精确的,实际是相当模糊的,通常依靠操作工的经验。
在超精后用轮廓度仪检测,以检测结果进行参数调整,但这种调整又是模糊的,有时甚至调整后轮廓度变坏,比如有的操作工为了提高超精精度,便延长超精时间,结果却发现,延长超精时间所超出的轴承套圈的轮廓度反而比超精时间短的更差了。
操作工就是在不断进行模糊调整并找到一个经检测,让自已感觉满意的参数后便固定下来,但在检测时,一般还不一定会进行同一零件的多个角度检测,所以导致误判的可能性很大。
操作工超精轴承套圈中对径向剖面轮廓度在不同的圆周方向的状态模糊认识很常见,造成超精的滚道面不同圆周方向与基准端面(超精时轴承套圈与工件主轴接触的定位面)不对称、倾斜等,这种情况对中大型轴承套圈较易发生。
因为超精的线速度相对是要恒定在一个合适范围内,线速度太慢会影响表面粗糙度和效率,但太快又会出现表面烧伤或粘铁,因此,线速度过慢和过快都影响超精质量。
而且,所超套圈直径越大,套圈的超精转速就越小,越容易超坏滚道轮廓度。
那么,传统的超精方法问题出在哪里呢?假如油石架的往复频率等于工件转速,比如工件主轴转速n=200r/min,油石架的往复频率f=200次/min,我们可以看到,当油石从轴承套圈的左侧移动到右侧,轴承套圈正好转了半转,而轴承套圈接下来的下一个半转结束,油石又正好从右移动到左侧;接下来轴承套圈再转一转时,油石又重复原来的轨迹超精了一个往复回到起点;当轴承套圈转了200转,油石沿原来的轨迹重复超精了200次,而轨迹外的轴承套圈表面就根本未被超精到,此时轴承套圈或超精的时间越长,滚道轴向轮廓度被破坏得越严重。
这样的超精不但不能起到提高精度的作用,反而将原来终磨削时良好的精度给破坏了,装配后降低轴承旋转精度、增加噪声。
那么,如果把工件主轴转速n改为400r/min,油石架的往复频率f 还是200次/min不变,显然,当工件每2转油石便振荡一个往复,工件下一个2转,油石就重复原来的轨迹进行下一个往复。
以此类推,我们可以发现,当工件转速等于油石振荡往复频率的倍数关系时,被超精的轴承套圈滚道的轮廓度会越超精越糟。
但是,是否工件转速除以油石往复频率只要不是倍数关系就可以超精好呢?分析发现并非如此,比如虽然未除尽,但余数很小,接近倍数关系导致油石的超精中心轨迹在下一个往复时与上一往复的轨迹偏离很小,接近重合,在有限的超精时间内超出的结果接近倍数关系的结果,同样不理想。
一般工件转速除以油石往复频率越易除尽,油石沿原轨迹超精的可能性越大,超精效果越糟。
那么,是否越不易除尽就越好呢?分析发现也非绝对如此,因为在有限的超精时间内,还是存在某些滚道表面未冷加工3637被超精到的可能性,而这种可能性,操作者又难以正确判断。
因此,超精参数控制不当,实际是以往由于不知道如何控制转速与往复运动频率、或难以达到对参数的精确控制,才导致滚动轴承套圈超精加工后、在装配使用中无法达到高精度要求、且可能在高速运转时产生较大噪声的原因。
而用以往的超精机是难以避开工件转速和油石往复频率的倍比情形、或近倍比情形的,在近倍比情形下操作者又不知道多长时间才能均匀完全超精。
2. 寻求最佳超精参数超精完成后,要正好使超精滚道表面能在每一沿轴线截面是均匀的,也就是在每一沿轴线截面的超精量在圆周各个角度是近乎相同的,避免在同一超精轨迹上重复超精,导致滚道另一些表面超精不到的情形发生,从而确保在各圆周角沿轴线截面的轮廓度是几乎相同的。
如图1所示,设轴承套圈在超精时的转速为n ,也就是超精机的工件主轴转速;油石架的振荡往复频率为f ,单件超精时间为t ,通过几何与运动关系,计算各有序超精的参数。
(1)首先计算油石厚度W 占用轴承套圈面的几何角α为α=2arcsin (W /d )(2)α占轴承套圈一周的比为[ 2arcsin (W /d )]/360°=[arcsin (W /d )]/180(3)如果油石一个振荡往复,而轴承套圈转动一转或若干转(m 转)左右后(这里的m ≥0,为方便计算,我们可以选1的扩大整数倍或缩小整数倍的值),油石刚刚不会与圆周起点与原超精轨迹完全重合,那么,轴承套圈的转数必须至少满足以下两点中的一点:油石运动一个往复,轴承套圈的转数是m +[arcsin (W /d )]/180°表示转了m 转后,正好多转过一个油石接触滚道的弧长角度的转数。
或者油石运动一个往复,轴承套圈的转数是m -[arcsin (W /d )]/180°表示转了m 转后,正好少转过一个油石接触滚道的弧长角度的转数。
因此油石一个往复,轴承套圈的转数应当是m ±[arcsin (W /d )]/180°两者可选其一。
(4)当在轴承套圈表面完整进行均匀超精,至少需要对油石进行多少个往复呢?分析得出至少需要往复次数为360°/2arcsin (W /d )=180°/arcsin (W /d )(5)完成超精一个轴承套圈,工件主轴至少需要转动多少转,转数为{m ±[arcsin (W /d )]/180°}×180°/arcsin (W /d ) =180°m /arcsin (W /d )±1我们发现:理论上要完成一个均匀超精过程,如果不去考虑超精光整要求的话,最少工件要转±1转即一整周,+表示正转;-表示反转。
当然,在实际使用中只需用正转即可,为超精出光整的工件,m 也极少会取0,因为如果工件真的只转1转,虽然能均匀超精整个轴承套圈,但很显然是远远无法达到光整要求的,因此,m 会取远大于1的数。
完成一个轴承套圈的均匀超精过程,工件主轴转数至少应当满足:180°m /a r c s i n (W /d )±1的整数Z (这个整数用字母Z 表示,是完成一个均匀超精的周期,当Z =1时,仅仅对超精面均匀超精了一个周期,还远远不能完全达到表面光整要求的作用)倍,显然,油石架往复次数必须是180°m /arcsin (W /d )的相同整数Z 倍。
当Z 等于1时是正好能超精完整一个周期,也是均匀超精至少要的周期;当Z 等于2时,就超精了两个周期;当Z 选择几就是超精几个周期;如果要超精得彻底些,就将Z 选大些,但效率会降低,反之效率就高些,这就要在实际超精实践中,按不同大小规格的零件进行适当选择,兼顾考虑。