电弧炉冶炼操作(铸钢王继朋)
电弧炉冶炼含硼合金钢的操作讲解

电弧炉冶炼含硼合金钢的操作讲解首先,电弧炉冶炼含硼合金钢的操作前需要准备若干原料和设备。
原料主要包括:钢水、高纯度硼铁、合金块等。
设备主要包括:电弧炉、电源、铜嘴、氧气和氮气气体供应系统等。
操作过程如下:1.启动电弧炉:检查电弧炉的设备和安全防护装置,确保操作的安全性。
然后,将电弧炉的电源连接,启动电炉,在规定的温度和时间条件下预热电弧炉。
2.加入原料:在预热完毕的电弧炉中,根据冶炼配方,依次加入预先准备好的钢水、高纯度硼铁和合金块。
同时,使用氧气和氮气气体供应系统,控制电弧炉中的气氛,使其保持在所需的合金化条件下。
3.搅拌和冶炼:启动电弧,开始冶炼过程。
在电弧炉内,电弧会提供炉内的高温,使原料熔化,并进行混合和合金化反应。
定期使用搅拌设备对炉内的钢水进行搅动,保证合金均匀分布,并促进反应进行。
4.控制温度和时间:根据冶炼配方和工艺要求,控制冶炼过程的温度和时间。
通过调节电弧炉的电源和搅拌设备的转速,控制炉内的温度和反应速率。
5.取样和分析:在冶炼过程中,定期从电弧炉中取样。
然后将取样的钢水送到实验室进行化学成分分析,以确定冶炼的合格性。
6.出钢和浇铸:冶炼完成后,根据工艺要求,将合金化的钢水通过铜嘴流出电弧炉,并进行浇铸。
在浇铸过程中,保持钢水的温度和流动性,确保铸造质量。
7.炉内操作结束:冶炼完成后,关闭电弧炉的电源。
清理电弧炉内的渣皮、渣坑等废渣物质。
通过以上步骤,可以实现电弧炉冶炼含硼合金钢的操作。
在操作过程中需要注意安全,控制好温度、时间和原料的加入量,同时根据取样和分析结果,对冶炼过程进行调整和优化,以得到所需的含硼合金钢产品。
电炉炼钢工艺流程
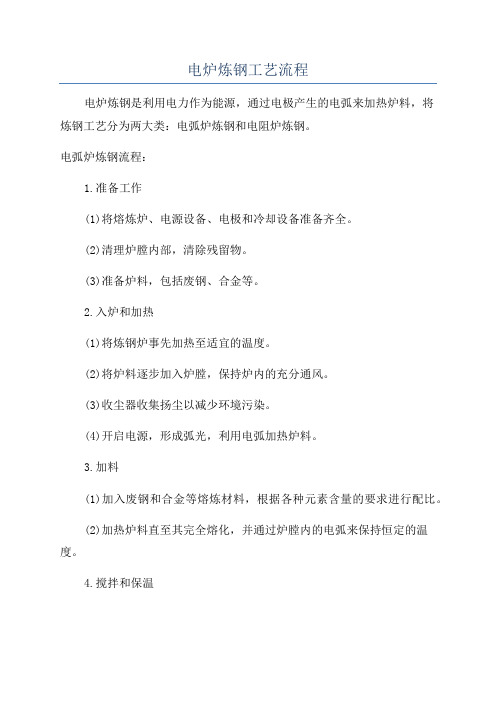
电炉炼钢工艺流程电炉炼钢是利用电力作为能源,通过电极产生的电弧来加热炉料,将炼钢工艺分为两大类:电弧炉炼钢和电阻炉炼钢。
电弧炉炼钢流程:1.准备工作(1)将熔炼炉、电源设备、电极和冷却设备准备齐全。
(2)清理炉膛内部,清除残留物。
(3)准备炉料,包括废钢、合金等。
2.入炉和加热(1)将炼钢炉事先加热至适宜的温度。
(2)将炉料逐步加入炉膛,保持炉内的充分通风。
(3)收尘器收集扬尘以减少环境污染。
(4)开启电源,形成弧光,利用电弧加热炉料。
3.加料(1)加入废钢和合金等熔炼材料,根据各种元素含量的要求进行配比。
(2)加热炉料直至其完全熔化,并通过炉膛内的电弧来保持恒定的温度。
4.搅拌和保温(1)通过搅拌装置(机械手、气枪等)对炉内炉料进行搅拌,以保证均匀加热。
(2)在最佳温度下保温,以提高合金和炉料的反应速度。
5.放钢和渣(1)根据钢种要求,加入脱氧剂和合金稀释剂。
(2)按照配方要求加入炉渣,帮助除去杂质和渣夹。
6.合金调整和测温(1)根据测温结果,调整冶炼条件,确保达到合适的温度。
(2)根据钢种需要,加入适量的合金元素,保证合金成分符合技术要求。
7.出钢(1)开启出钢口,将炼好的钢液顺利倾出。
(2)根据需要对炼钢炉进行钢包保温、修补等工作。
(3)将倾出的钢液进行调节和再加工,以满足用户要求。
(4)进行钢液的凝固和结晶,得到成品钢。
电阻炉炼钢流程:电阻炉是通过电流通过炉体自身的电阻产生热能,实现炉料加热熔化。
1.准备工作(1)检查电阻炉的各项设备和电源的正常运行。
(2)清理炉内和炉外的杂质和残留物。
(3)准备好炉料,包括废钢、矿石等。
2.入炉和加热(1)将炼钢炉预先加热至适宜的温度。
(2)逐步加入炉料,保持通风和顺畅的炉内气流。
(3)开启电源,使电流通过炉体,产生热能。
3.加料和熔化(1)加入炉料,实现其完全熔化。
(2)通过控制电流和炉内温度,保持炉料的恒定熔化状态。
4.炉内观察和保温(1)观察炉内炉料的状况,保持熔化状态的均匀性。
电炉炼钢工艺技术操作规程
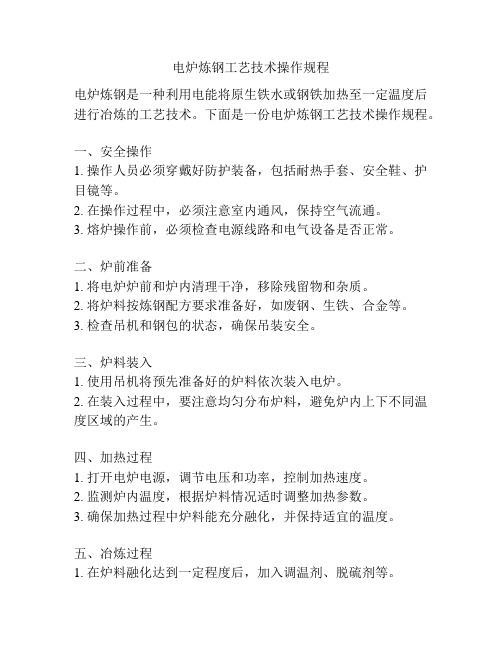
电炉炼钢工艺技术操作规程电炉炼钢是一种利用电能将原生铁水或钢铁加热至一定温度后进行冶炼的工艺技术。
下面是一份电炉炼钢工艺技术操作规程。
一、安全操作1. 操作人员必须穿戴好防护装备,包括耐热手套、安全鞋、护目镜等。
2. 在操作过程中,必须注意室内通风,保持空气流通。
3. 熔炉操作前,必须检查电源线路和电气设备是否正常。
二、炉前准备1. 将电炉炉前和炉内清理干净,移除残留物和杂质。
2. 将炉料按炼钢配方要求准备好,如废钢、生铁、合金等。
3. 检查吊机和钢包的状态,确保吊装安全。
三、炉料装入1. 使用吊机将预先准备好的炉料依次装入电炉。
2. 在装入过程中,要注意均匀分布炉料,避免炉内上下不同温度区域的产生。
四、加热过程1. 打开电炉电源,调节电压和功率,控制加热速度。
2. 监测炉内温度,根据炉料情况适时调整加热参数。
3. 确保加热过程中炉料能充分融化,并保持适宜的温度。
五、冶炼过程1. 在炉料融化达到一定程度后,加入调温剂、脱硫剂等。
2. 控制加热和冷却速率,使炉料冶炼达到理想状态。
3. 根据需要,进行合金调整,如加入锰、铬、钒等元素。
六、出钢操作1. 钢料冶炼完毕后,停止加热,关闭电源,将电炉内压力降至常压。
2. 采用吊机将电炉钢水倒入钢包中,注意均匀倒入,防止喷溅。
3. 保持钢包温度,进行后续加工和浇铸操作。
七、炉后清理1. 关闭电炉主电源,断开电源线路。
2. 清理炉前、炉后区域,移除炉渣和废物,保持工作环境整洁。
3. 检查电炉设备和配件的状态,进行维修和保养。
以上是一份电炉炼钢工艺技术操作规程,对于电炉炼钢操作过程中需要注意安全、控制加热参数和冶炼过程中加入合适的冶炼剂等方面都进行了详细说明。
在实际操作中,操作人员还需要根据具体生产情况和炼钢配方要求进行调整,以确保炼钢工艺技术的顺利进行。
铸钢冶炼工艺流程
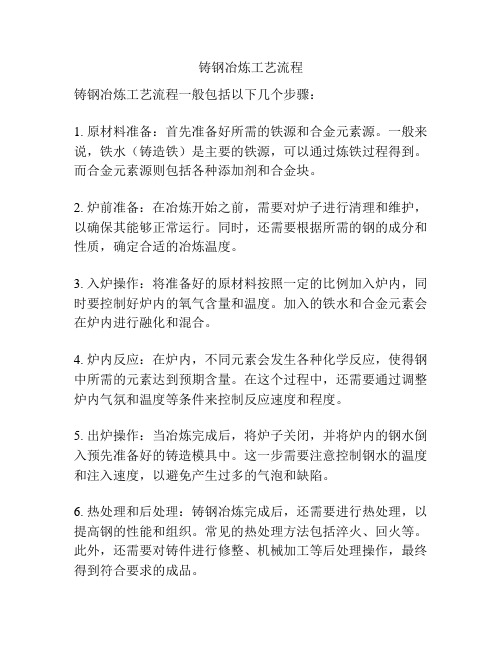
铸钢冶炼工艺流程
铸钢冶炼工艺流程一般包括以下几个步骤:
1. 原材料准备:首先准备好所需的铁源和合金元素源。
一般来说,铁水(铸造铁)是主要的铁源,可以通过炼铁过程得到。
而合金元素源则包括各种添加剂和合金块。
2. 炉前准备:在冶炼开始之前,需要对炉子进行清理和维护,以确保其能够正常运行。
同时,还需要根据所需的钢的成分和性质,确定合适的冶炼温度。
3. 入炉操作:将准备好的原材料按照一定的比例加入炉内,同时要控制好炉内的氧气含量和温度。
加入的铁水和合金元素会在炉内进行融化和混合。
4. 炉内反应:在炉内,不同元素会发生各种化学反应,使得钢中所需的元素达到预期含量。
在这个过程中,还需要通过调整炉内气氛和温度等条件来控制反应速度和程度。
5. 出炉操作:当冶炼完成后,将炉子关闭,并将炉内的钢水倒入预先准备好的铸造模具中。
这一步需要注意控制钢水的温度和注入速度,以避免产生过多的气泡和缺陷。
6. 热处理和后处理:铸钢冶炼完成后,还需要进行热处理,以提高钢的性能和组织。
常见的热处理方法包括淬火、回火等。
此外,还需要对铸件进行修整、机械加工等后处理操作,最终得到符合要求的成品。
需要注意的是,具体的铸钢冶炼工艺流程会因钢的种类、规格和用途的不同而有所差异,上述流程只是一个常见的概述。
实际操作中,还需要根据具体情况进行工艺参数的优化和调整。
铸钢电炉的炉前操作步骤BD-10页
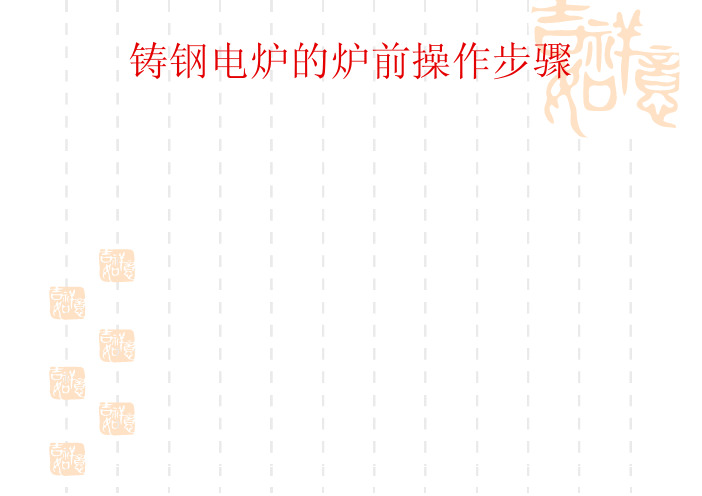
铸钢电炉的炉前操作步骤
1.通电熔化:开始先通电4~8min供给中频 电炉60%左右的功率,待电流冲击停止 后,逐渐将功率增至最大植。
2.捣料助熔:随着埚下部炉料熔化,随时注 意捣料,防止“搭桥”,并继续添加炉料。
3.造渣:大部分炉料熔化后,加入造渣材料 (质量比为:石灰粉:氟石粉=2:1)造渣 覆盖钢液,造渣材料加入量为钢液重量的 1%~1.5%。
4.取样扒渣:大约95%的炉料熔毕时,取钢 样分析,并将其余5%的炉料加入炉内。
全 部炉料溶毕后,降低功率至40%~60%,倾 炉扒渣,并另造新渣。
5.脱氧:渣料溶毕后,往炉渣面上加脱氧剂 (质量比为:石灰粉:铝粉=2:1)进行扩 散脱氧。
脱氧过程中可用石灰粉和氟石粉 调整炉渣的粘度,使炉渣具有良好的流动 性。
6.调整成分:根据化学分析结果,调整钢液 化学成分,其中含硅量应在出钢前10min以 内进行调整。
7.测温,做圆杯试样:测量钢液温度,并作 圆杯试样,检查钢液脱氧情况。
8.加补充铁合金:钢液温度达到 1630~1650°C,圆杯试样收缩良好时,扒 除一半炉渣后,加入补充铁合金,并将补 充铁合金压入钢液内。
9.终脱氧出钢:补充铁合金溶毕后,每吨钢 液插铝0.15-0.25%终脱氧,插铝后2~3min 以内停电倾炉出钢。
。
电炉炼钢工艺技术操作规程

电炉炼钢工艺技术操作规程《电炉炼钢工艺技术操作规程》一、工艺流程1. 原料确认:a. 确认炼钢原料的种类和数量,保证原料质量符合要求。
b. 对原料进行挑选、称重和布料,根据工艺要求进行合理的配比。
2. 炉前准备:a. 确保电炉设备正常运转,检查电缆线路的接头、绝缘情况。
b. 检查电炉炉体和电极的状况,保证设备完好。
3. 加料操作:a. 先加入底料,再依次加入合金和其他辅助材料,保证加料的顺序和速度符合工艺要求。
b. 加料时注意保护炉体和电极,防止发生结焦或损坏。
4. 炉补煅炼:a. 启动电炉加热,控制温度升至煅炼温度,进行煅炼反应,保证炉内氧化物还原,达到炼钢目的。
b. 在煅炼过程中,及时调整电极的位置和电流,保持炉料的均匀加热。
5. 吹氧气喷吹:a. 在炉料煅炼后,进行吹氧气喷吹,促进碳和其他杂质的氧化。
b. 控制氧气流量和喷吹时间,避免过量的氧气造成炉料的过度氧化。
6. 保温保热:a. 关掉氧气,进行保温保热,使溶钢的温度保持稳定,有利于渣的分离清洁。
7. 出钢操作:a. 在保温保热后,根据工艺要求进行出钢操作,确保出钢顺利、迅速,并严格按照规程进行预处理。
8. 残渣槽处理:a. 将残渣槽内的残渣清理干净,防止残渣对下一炼钢过程产生影响。
9. 炉体清理:a. 关掉电炉,进行炉体的清理、检修、保养。
确保设备的长期稳定运行。
二、安全注意事项1. 操作人员必须穿戴好防护用品,遵守安全操作规程,严禁违章操作。
2. 加料、炉补煅炼和吹氧气喷吹过程中,必须确保炉内氧气充足,避免产生有毒气体。
3. 控制好电炉的加热温度和电流大小,避免设备过热和火灾事故的发生。
4. 规范操作程序,避免喷溅炉料、炮炸和其他意外情况的发生。
以上就是《电炉炼钢工艺技术操作规程》,希望在实际操作中严格按照规程要求进行,确保生产安全、质量和效率。
三相电弧炉炼钢操作规程
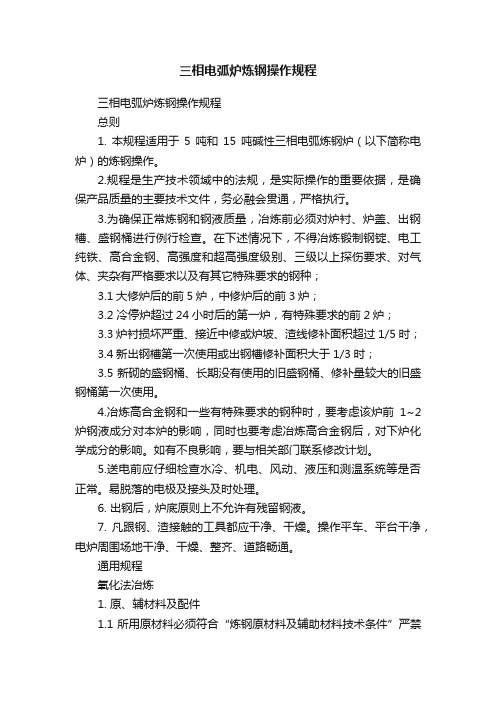
三相电弧炉炼钢操作规程三相电弧炉炼钢操作规程总则1. 本规程适用于5吨和15吨碱性三相电弧炼钢炉(以下简称电炉)的炼钢操作。
2.规程是生产技术领域中的法规,是实际操作的重要依据,是确保产品质量的主要技术文件,务必融会贯通,严格执行。
3.为确保正常炼钢和钢液质量,冶炼前必须对炉衬、炉盖、出钢槽、盛钢桶进行例行检查。
在下述情况下,不得冶炼锻制钢锭、电工纯铁、高合金钢、高强度和超高强度级别、三级以上探伤要求、对气体、夹杂有严格要求以及有其它特殊要求的钢种;3.1大修炉后的前5炉,中修炉后的前3炉;3.2 冷停炉超过24小时后的第一炉,有特殊要求的前2炉;3.3炉衬损坏严重、接近中修或炉坡、渣线修补面积超过1/5时;3.4新出钢槽第一次使用或出钢槽修补面积大于1/3时;3.5 新砌的盛钢桶、长期没有使用的旧盛钢桶、修补量较大的旧盛钢桶第一次使用。
4.冶炼高合金钢和一些有特殊要求的钢种时,要考虑该炉前1~2炉钢液成分对本炉的影响,同时也要考虑冶炼高合金钢后,对下炉化学成分的影响。
如有不良影响,要与相关部门联系修改计划。
5.送电前应仔细检查水冷、机电、风动、液压和测温系统等是否正常。
易脱落的电极及接头及时处理。
6. 出钢后,炉底原则上不允许有残留钢液。
7. 凡跟钢、渣接触的工具都应干净、干燥。
操作平车、平台干净,电炉周围场地干净、干燥、整齐、道路畅通。
通用规程氧化法冶炼1. 原、辅材料及配件1.1 所用原材料必须符合“炼钢原材料及辅助材料技术条件”严禁有毒、有害、易燃、易爆物以及对钢液质量有害的金属和非金属进入炉内。
1.2应根据所炼钢种冶炼方法、原材料成份、前炉钢对本炉钢的影响、冷停炉时间长短的影响、吹氧助熔的需要、计划钢产量等进行仔细计算,拟制配料单,配碳量应保证全熔化后氧化沸腾脱碳的需要,生铁配入量不得超过炉料重的15%,不足之碳量可配入电极块或冶金焦碳补足。
1.3所配炉料大小块度应合适,配比为:大块料20~40%,中块料30~40%,小块料(包括钢屑)30~50%。
电弧炉炼钢操作方法

电弧炉炼钢操作方法电弧炉是一种通过电能产生高温进行熔炼的设备,广泛应用于钢铁冶炼行业。
电弧炉炼钢的操作方法通常包括炉前准备、炉内熔炼和炉后处理等阶段。
首先,进行炉前准备工作。
在操作电弧炉炼钢之前,需要对设备进行全面的检查和维护,确保设备处于良好的工作状态。
对电弧炉的电极、炉壁、炉底等部件进行检查,确保其完好无损。
同时,检查冷却水、压力传感器等附件设备,确保其能够正常工作。
此外,还需要进行炉料的配比和装料工作,根据炉料的种类和质量要求进行配比,然后将炉料装入电弧炉。
其次,进行炉内熔炼工作。
在炉内熔炼的过程中,首先要进行点火。
点火时,首先打开电弧炉的冷却水,然后打开电源,使电极接触炉料,产生电弧,开始加热炉料。
在加热的过程中,需要根据炉内温度的变化来控制电弧的强度和炉料的加料速度,以保证炉料能够均匀加热到熔化温度。
在炉料熔化后,需要通过氧气吹砂等方式对炉料进行搅拌,以确保炉料充分混合,熔化均匀。
在炉料熔化和搅拌完成后,可以进行温度测量和成分分析等工作,以确保熔炼的质量能够达到要求。
最后,进行炉后处理工作。
在炉后处理中,首先需要对炉内渣进行清理。
清理炉渣需要先停止电弧加热,然后打开底部的渣门,让炉渣流出。
清理后,需要对熔炼的钢水进行抽样分析和温度控制,确保钢水的成分和温度符合要求。
同时,需要对熔炼得到的钢水进行连续测温,以确保温度变化在可控范围内。
最后,将熔炼得到的钢水倒出到浇铸设备中,进行铸造成型。
电弧炉炼钢的操作方法需要经过专业的培训和实践经验的积累才能熟练掌握。
操作人员需要了解设备的结构原理和工作原理,掌握炉料的配比和熔化规律,熟悉温度和成分分析的方法,掌握设备操作和维护的技巧。
同时,由于电弧炉炼钢涉及高温、高压等危险因素,操作人员需要时刻关注安全规定,正确使用个人防护装备,严格按照操作规程进行操作,以确保生产安全。
总之,电弧炉炼钢是一项复杂的工艺过程,需要经过专业的培训和实践经验的积累方能熟练掌握。
电炉炼钢操作方法及冶炼工艺73页PPT
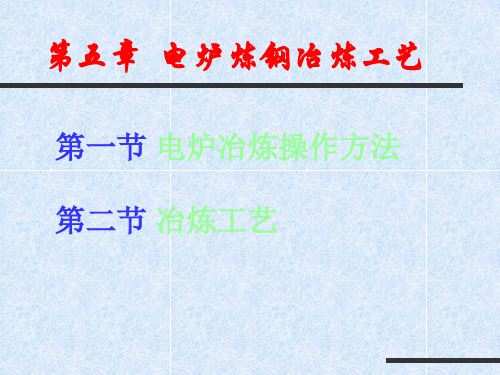
第一节 电炉冶炼操作方法 第二节 冶炼工艺
ቤተ መጻሕፍቲ ባይዱ
第一节 电炉冶炼操作方法
操作方法一般是按造渣工艺特点来划分的,有单渣 氧化法、单渣还原法、双渣还原法与双渣氧化法,目前普 遍采用后两种。
1)双渣还原法 又称返回吹氧法,其特点是冶炼过程中有较短的 氧化期(≤10min),造氧化渣,又造还原渣,能吹氧脱 碳,去气、夹杂。但由于该种方法脱磷较难,故要求炉料 应由含低磷的返回废钢组成。 由于它采取了小脱碳量、短氧化期,不但能去除 有害元素,还可以回收返回废钢中大量的合金元素。因此, 此法适合冶炼不锈钢、高速钢等含Cr、W高的钢种。
电炉装料情况
三、熔化期
传统冶炼工艺的熔化期占整个冶炼时间的 50%~70%,电耗占70%~80%。因此熔化期的长短影 响生产率和电耗,熔化期的操作影响氧化期、还原 期的顺利与否。
(1)熔化期的主要任务 将块状的固体炉料快速熔化,并加热到氧化温度; 提前造渣,早期去磷,减少钢液吸气与挥发。
(2)熔化期的操作 合理供电,及时吹氧,提前造渣。
为什么?脱磷反应与脱磷条件:
脱磷反应与脱磷条件:
脱磷反应:
2[P]+5(FeO)+4(CaO)=(4CaO·P2O5)+5 [Fe], △H<0
分析:反应是在渣-钢界面上进行,是放热反 应。
脱磷反应的条件:
高碱度,造高碱度渣,增加渣中氧化钙; 高氧化性,造高氧化性渣,增加渣中氧化铁;
二、装料
目前,广泛采用炉顶料罐(或叫料篮、料 筐)装料,每炉钢的炉料分1~3次加入。装料的 好坏影响炉衬寿命、冶炼时间、电耗、电极消耗 以及合金元素的烧损等。因此,要求合理装料, 这主要取决于炉料在料罐中的布料合理与否。
- 1、下载文档前请自行甄别文档内容的完整性,平台不提供额外的编辑、内容补充、找答案等附加服务。
- 2、"仅部分预览"的文档,不可在线预览部分如存在完整性等问题,可反馈申请退款(可完整预览的文档不适用该条件!)。
- 3、如文档侵犯您的权益,请联系客服反馈,我们会尽快为您处理(人工客服工作时间:9:00-18:30)。
电弧炉冶炼操作冶炼前的准备工作原材料的准备1. 废钢的要求1)废钢根据化学成分不同分类堆放(主要是高合金钢与普通碳素钢、高合金钢与不同种类的高合金钢)。
1)废钢应清洁,少锈,少油污及无泥砂,有色金属及爆炸物禁止入炉。
废钢尺寸应适合与装料,就我车间实际操作。
细长料长度应不大于1.2mm块状炉料边长不大于800mm重型废钢单重不大于3吨为宜,过大的炉料应先切割后入炉。
1)浇冒口及废铸件上的粘砂及浇汤道需清理砂子及砖块后入炉,以免不导电而致石墨电极折断及炉衬的侵蚀。
1)增碳(炼钢)生铁必须有详细化学成分,以便还原期增碳使用。
2. 对合金的要求1)熟知各种合金的化学成分及含量,加入方法和加入时间。
注:常用合金材料性能及加入。
硅铁:主要用于脱碳剂及合金化。
硅铁中的杂质为P, Al等。
力叭时间一般为还原期稀薄渣形成后加入,含量一般75%,回收率95%左右。
锰铁:主要钢液的脱氧及合金化。
锰铁中含P量比较高(炼氧化法Mn 13寸往往P过高即此原因)。
力叭时间扒渣后随同造渣材料一起加入炉内。
含量70-78%回收率98%右。
铬铁:合金化,可分为高碳铬铁,中碳铬铁,低碳铬铁及微碳铬铁。
含量55^65%)回收率98%右。
P、S含量不高。
钼铁:合金化,钼铁属难熔合金,力叭时间在装料时同炉料一起装入或在熔化期及氧化前期力叭。
为节约用量,一般在熔毕样分析成分结果出来后按计算加入,并及时吹氧,使其完全熔化。
钼铁加入时会产生沸腾现象(称为钼沸腾)。
力口料时应将炉体向后摇起,加料人员站在路门侧面。
含量50-58%回收率98%上(按100% 计算)。
镍:还原期(后期)力叭,含量99%以上,回收率100%2)铁合金加入炉中以前需要烘烤(以除去水分及部分合金所含氢较高),块度适中。
3、造渣材料1)石灰(见表)块度要求20-80m。
粉末原则上不超过5%(S<0.15%2)萤石。
是由萤石矿直接开采而得。
改善炉渣流动性而不降低碱度,可增强渣钢面反应能力,对脱去钢液中的PS有利。
要求CaF含量越高越好,而SiO含量要低。
CaF>85% SiQ<4%块度2(—50mm入炉前干燥。
补炉及装料送电1、补炉1)补炉采用热补方式。
车间补炉是采取铁锹投补方法。
操作要点:对准炉衬冲蚀严重的地方快速、准确、薄补的原则。
补炉人员站在镁砂盘上时必须系好安全带,地面要有人监护。
凉补炉时注意将补过的地方补炉料踩实,大补炉后最好用薄铁皮覆盖后在装料。
2)出钢槽修补用补炉料,保证平整。
烘烤干燥。
确保在出钢过程中不散流,不翻浪。
(目的:减少在出钢过程中钢液吸气)2、装料1)对配好的炉料检查核对。
并考虑上一炉所冶炼的钢种对本炉钢的化学成分影响情况。
(如上一炉为Mn1)注: 我车间现料源熔清后几乎无碳(无配碳生铁)。
因此在装料前必须进行废电极块或蓝碳未配碳,配碳量根据所冶炼钢种高0.10〜0.30%己入。
2)装料前根据炉况力叭适量石灰,力叭量为炉料总量的1〜2%(目的:护炉、提前造渣)。
3)装料原则,上松疏,下致密,中间高,四周低。
炉门口处无大料。
大块重料装炉底,上面轻薄小料。
3、送电1 )送电前再一次检查炉内料状况,电极下方是否有不导电材料(炉料上有大面积砂子,砖块、石棉等)。
如有时必须处理或将炉壳稍错开,保证电极导电。
2)检查电器及机械设备正常,水冷系统,电极长度等。
电极短需要早期接换,接电极操作时必须炉顶2人操作,使用电极扳手时2人配合好,用力一致,动作协调,就绪后炉长指挥送电,无关人员远离炉体。
冶炼及操作一、熔化期:(任务:炉料快速熔化为均匀液体,早期脱磷,去除钢液中部分气体及杂质)1)传统熔化期约占冶炼时间一半。
这期间电能消耗占总电耗的50%以上。
因此,快速化料是缩短冶炼周期的基本条牛。
2)熔化期系用最大电流给电(变压器允许情况下)步骤:(以我车间实际情况)。
起弧阶段,电流应小一点4000Ar6000A之间。
穿井阶段及电极回升阶段,电流控制9000* 11000A之间。
低温区炉料熔化阶段电流控制应为最大。
女口下图;起弧阶段穿井阶段电极回升阶段低温区炉料熔化阶段3)吹氧祝熔应在电极穿井完成后,炉内可见有熔池形成后进行(送电后约20分钟以后))专人吹氧,分人配合(一人开关氧气,一人摇炉,一人加料渣),开关氧气人员根据吹氧人习惯开氧气大小。
开关氧气时速度要慢。
4)熔化末期采用自动流渣操作。
(炉体前摇自炉门内自动向外流渣)。
目的:提前去除钢液中的部分磷。
及时补加新渣料,保证渣液流动性良好。
如炉渣过于粘稠用萤石加以稀释。
5)炉料全熔化,搅拌取样进行全分析(具体操作,将搅拌耙杆在炉门口烘干后进入炉内渣面上蘸好渣,防止在搅拌过程中将搅扌半耙熔化掉,顺时间方向推渣数下,在逆时针方向进入钢液中搅拌,然后用样勺同样蘸好渣后取样。
取样方位应基本在熔池正中央)。
全熔后的碳含量应高于所冶炼钢种的含碳量下限要求。
二、氧化期:任务(1、继续并最终完成钢液脱磷任务,使钢液中的磷降到规格范围内;2、去除钢液中的气体及非金属夹杂物;3、力n热并均匀钢液温度,一殳高于出钢温度20C以上)我车间现采取烬氧结合法,所以氧化期不明显。
氧化期的具体操作:1、确保渣量,渣量为炉料的2〜3%碱度R=2.0-3.5。
保持良好的流动性,且氧化铁含量要高。
脱磷的基本条件:“三高一低”(温度相对要低152〜1550C,高碱度,高氧化铁含量,大渣量且流动性好)。
2、氧化期最理想采用矿石-氧气综合法氧化,矿石要分批加入,控制好氧化速度。
(仅脱碳时温度应控制相对高点>155CC)防止大沸腾。
氧气压力不得大于8个大气压。
3、氧化顺序上先磷后碳,温度控制上先慢后快;造渣上先大渣量去磷,后薄渣脱碳。
(去磷时采取自动化渣操作,并及时补加石灰、萤石、氧化铁等;最后脱碳以吹氧为主)4、良好氧化渣应是泡沫渣,可包住弧光,有利于钢液升温和保护炉衬。
冷却后表面呈油黑色,断头致密而松脆。
这表明氧化渣FeO含量高,碱度合适。
女口氧化渣表面呈黑色炉内渣显得很薄,像水面一样,电弧声刺耳。
表明FeO含量高,碱度底,这时应补加石灰(我车间此种情况最常见)。
5、氧化期几种常见典型操作:1)碳高磷高,应在氧化初期,利用熔池湿度偏低时集中脱磷,并在脱磷的过程中逐渐升温,为后期脱碳创造条件。
2)碳高磷低,温度适当控制高一点,集中吹氧降碳,及时流渣并补充渣料。
3)碳低磷高,温度控制偏低一点,采用大渣量吹氧,加矿(氧化铁皮),自动流渣及时补充渣料,必要时扒渣重造新渣。
磷达要求范围后采取增碳操作。
4)碳低磷低(略)。
6、氧化末期搅拌取样进行全分析(操作同熔化期),使熔池进入净沸腾(也称清洁沸腾。
具体操作,按吨钢1〜2Kg加入锰铁,保持熔池平静)。
并调整难熔不氧化合金元素成分至下限(比如M0。
具备扒渣条件时即可进行扒渣(操作要点:迅速,平稳,彻底。
当扒渣到后期渣量少而稀薄的情况下,可视情况短时间下插2#3#电极浅入钢液,使渣液很快集中于炉门口附近,迅速扒除)。
7、增碳多是脱碳量不足或终脱碳过低所致,它是一种不正常操作。
因为增碳易使钢液中气体和夹杂物增加,既浪费原材料,又延长冶炼时间,所以尽量避免。
常见增碳方法有:1)补加生铁增碳。
2)停电插电极增碳。
但插电极增碳消耗电极量大,一般不提倡。
3)扒渣增碳,最常用增碳方法。
操作:必须将熔渣扒干净,增碳剂(焦粉;蓝碳末)加入后要用耙子在液面上进行充分推擀,促使钢液对碳的吸收。
三、还原期及出钢:还原期的基本任务:1)脱除钢液中的氧。
2)脱除钢液中的硫3)调整化学成分,使其满足规格要求。
4)调整钢液温度,为正常浇注创造条件。
脱氧操作:1、沉淀脱氧(直接脱氧)。
扒除氧化渣后,迅速将块状脱氧剂,如硅铁,锰铁和铝饼等脱氧剂直接投入(插入)钢液中,然后造还原稀薄渣,此法速度较快,可缩短还原时间,但脱氧产物易形成钢中夹杂。
2、扩散脱氧(间接脱氧)。
还原稀薄渣形成后,将脱氧剂(一般以粉状脱氧剂为主),加在渣表面上,通过降低渣中的氧含量来达到钢液的脱氧,扩散脱氧的产物不沾污钢液,但时间长,对降低电耗和炉衬使用提高不利。
3、综合脱氧。
即是将上述二种脱氧方法的综合运用,克服了各自得缺点,集中优点来完成钢液的脱氧任务。
我们车间全采用综合脱氧方法。
4、白渣脱氧。
操作:扒除氧化渣后,迅速加入稀薄渣料,尽量减少钢液吸气与降温,渣料比例石灰:萤石二齐4:1,渣量为炉料的2.5〜3%渣料加入前加入块状脱氧剂预脱氧,薄渣形成后调入各种合金,然后分批加入扩散脱氧剂;第一批应多一些,其他各批根据炉内状况加入,每批加入前,应对渣进行推渣搅拌,适时补加石灰,保持炉渣一定的碱度,总渣量控制为炉料的48左右扩散脱氧剂一般指焦炭粉,硅铁粉,硅钙粉等。
我们现用的合成精炼剂。
碱度=碱性氧化物:酸性氧化物。
即:R= CaO/S2OS原期碱度应保持在2.5〜3。
5、脱氧效果检验。
多采用经验判断法,脱氧杯观察法和化学分析法。
经验判断法根据炉渣的颜色判断脱氧好坏。
女口果渣白且保持时间长而稳定,表明渣中(FeO含量低,这时可判断为钢液脱氧良好。
脱氧杯观察法(常用),将钢液轻轻注入清洁、干燥、圆形的高筒杯中,凝固后表面平静或有不同程度的收缩,说明脱氧良好;如凝固过程中冒出一束束火花或凝固后不但不收缩,反而上涨,突起现象,这既脱氧不好。
见图;(化学分析法取渣样化验炉渣中的FeO含量)脱氧良好脱氧不良6、终脱氧多采用铝在出钢前2〜3min根据冶炼钢种的不同按纯钢0.7〜1Kg 插入钢液中,多采用出钢过程中抛投到钢包内。
低碳钢取上限,高碳及低合金废钢取下限。
钢液脱硫。
掌握好以下四方面: 1)高温,脱硫反应属吸热反应,高温有利于进行。
2)炉渣碱度要高,不小于2.5即>2.5O3)渣量要大且流动性要好。
4)炉渣中FeO含量要低。
钢液成分的调整常见单一元素在钢中的作用。
碳能影响规定钢的各种物化性能及力学性能。
如强度,塑性及焊接性能,对钢的淬火,退火等热处理有直接影响。
硅常用作还原剂和脱氧剂,存在于钢中提高固溶体强度,提高钢的抗腐蚀性,屈服极限。
锰能消除和减弱钢因硫引起的热脆性,增加钢的淬透性。
还原期合金补加公式:补加量钢水量(规格控制-化验分析)%/ (合金含量%<回收率%)例:冶炼50Mn已知装料15t,炉料综合收得率为90%还原分析锰含量为0.38%现控制为0.75%,用含量72%锰铁,收得率95%,求锰铁补加量?解:锰铁补加量=1500(0 90%<(0.75-0.38)%/(72% 95% =73K(为操作方便,一般合金加入取整数)高合金钢合金用量对元素控制成分的影响合金补加(减法本身)例:冶炼Mn13已知装料(氧化法)12t,炉料综合收得率为90%取样分析Mn含量为0.50%控制Mn含量为11.6%用含锰72%铁,收得率为95%求锰铁补加量?解:锰铁补加量=1200(0 90%(11.6-0.50)%/(72%95%-11.6)=2110K/实际加入中应考虑到元素的氧化及烧损量)钢液重量的校验(在冶炼过程中往往出现炉料重量不准情况,或炉料杂质多,钢液量波动较大,可惜调镍调钼元素的办法校验钢液重量)因镍、钼基本不氧化。