电弧炉冶炼技术操作规程
电弧炉炼钢工安全操作规程范文
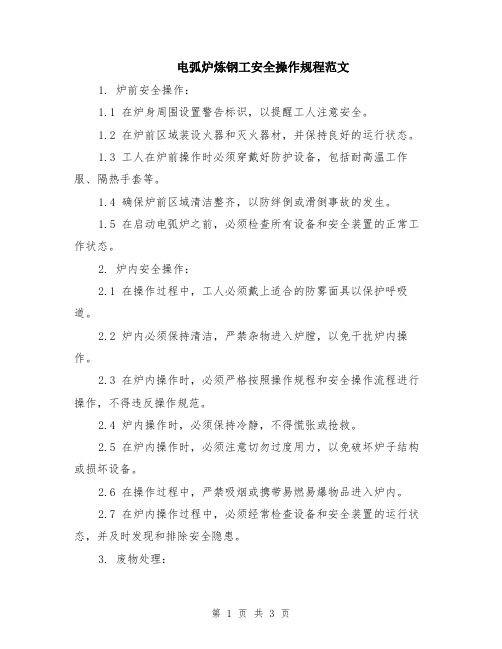
电弧炉炼钢工安全操作规程范文1. 炉前安全操作:1.1 在炉身周围设置警告标识,以提醒工人注意安全。
1.2 在炉前区域装设火器和灭火器材,并保持良好的运行状态。
1.3 工人在炉前操作时必须穿戴好防护设备,包括耐高温工作服、隔热手套等。
1.4 确保炉前区域清洁整齐,以防绊倒或滑倒事故的发生。
1.5 在启动电弧炉之前,必须检查所有设备和安全装置的正常工作状态。
2. 炉内安全操作:2.1 在操作过程中,工人必须戴上适合的防雾面具以保护呼吸道。
2.2 炉内必须保持清洁,严禁杂物进入炉膛,以免干扰炉内操作。
2.3 在炉内操作时,必须严格按照操作规程和安全操作流程进行操作,不得违反操作规范。
2.4 炉内操作时,必须保持冷静,不得慌张或抢救。
2.5 在炉内操作时,必须注意切勿过度用力,以免破坏炉子结构或损坏设备。
2.6 在操作过程中,严禁吸烟或携带易燃易爆物品进入炉内。
2.7 在炉内操作过程中,必须经常检查设备和安全装置的运行状态,并及时发现和排除安全隐患。
3. 废物处理:3.1 废物必须按照规定分类处理,严禁将废物随意丢弃或混入其他垃圾中。
3.2 废物处理区域必须设置警示标志,以提醒工人注意废物处理的安全。
3.3 废物处理过程中必须采取必要的个人防护设备,包括防护眼镜、手套等。
3.4 废物处理过程中禁止触摸腐蚀性物质,以免对身体造成伤害。
3.5 废物处理过程中应注意防止废物溅出,以免造成工人受伤。
4. 紧急情况处置:4.1 工人应熟悉紧急情况处置流程,并接受相关应急训练。
4.2 在紧急情况下,工人必须保持冷静,并立即采取必要的安全措施。
4.3 在紧急情况发生时,应立即通知相关人员,并采取必要的救援措施。
4.4 在紧急情况下,必须按照应急预案进行疏散,并确保所有人员安全撤离。
4.5 在紧急情况下,工人不得擅自返回现场,必须等待相关人员的指示。
5. 安全检查:5.1 定期对电弧炉和周边设备进行安全检查,并做好检查记录。
电弧炉冶炼操作规程
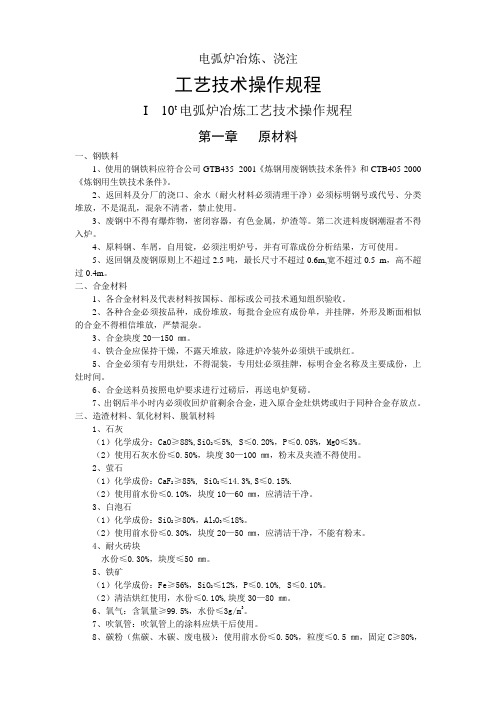
电弧炉冶炼、浇注工艺技术操作规程I 10t电弧炉冶炼工艺技术操作规程第一章原材料一、钢铁料1、使用的钢铁料应符合公司GTB435 -2001《炼钢用废钢铁技术条件》和CTB405-2000《炼钢用生铁技术条件》。
2、返回料及分厂的浇口、余水(耐火材料必须清理干净)必须标明钢号或代号、分类堆放,不是混乱,混杂不清者,禁止使用。
3、废钢中不得有爆炸物,密闭容器,有色金属,炉渣等。
第二次进料废钢潮湿者不得入炉。
4、原料钢、车屑,自用锭,必须注明炉号,并有可靠成份分析结果,方可使用。
5、返回钢及废钢原则上不超过2.5吨,最长尺寸不超过0.6m,宽不超过0.5 m,高不超过0.4m。
二、合金材料1、各合金材料及代表材料按国标、部标或公司技术通知组织验收。
2、各种合金必须按品种,成份堆放,每批合金应有成份单,并挂牌,外形及断面相似的合金不得相信堆放,严禁混杂。
3、合金块度20—150 ㎜。
4、铁合金应保持干燥,不露天堆放,除进炉冷装外必须烘干或烘红。
5、合金必须有专用烘灶,不得混装,专用灶必须挂牌,标明合金名称及主要成份,上灶时间。
6、合金送料员按照电炉要求进行过磅后,再送电炉复磅。
7、出钢后半小时内必须收回炉前剩余合金,进入原合金灶烘烤或归于同种合金存放点。
三、造渣材料、氧化材料、脱氧材料1、石灰(1)化学成分:CaO≥88%,SiO2≤5%, S≤0.20%,P≤0.05%,MgO≤3%。
(2)使用石灰水份≤0.50%,块度30—100 ㎜,粉末及夹渣不得使用。
2、萤石(1)化学成份:CaF2≥85%, SiO2≤14.3%,S≤0.15%.(2)使用前水份≤0.10%,块度10—60 ㎜,应清洁干净。
3、白泡石(1)化学成份:SiO2≥80%,Al2O3≤18%。
(2)使用前水份≤0.30%,块度20—50 ㎜,应清洁干净,不能有粉末。
4、耐火砖块水份≤0.30%,块度≤50 ㎜。
5、铁矿(1)化学成份:Fe≥56%,SiO2≤12%,P≤0.10%, S≤0.10%。
电弧炉炼钢工安全操作规程(三篇)

电弧炉炼钢工安全操作规程第一章总则第一条为了保障电弧炉炼钢过程中工人的生命安全和身体健康,规范操作流程,防止事故的发生,制定本安全操作规程。
第二条本规程适用于电弧炉炼钢工的操作人员。
第三条电弧炉炼钢工应具备熟悉电弧炉炼钢工艺和操作流程,并且具备相关的安全知识和操作技能。
第四条电弧炉炼钢工应遵守国家相关法律法规和企业制度,遵循安全原则,严格执行本规程。
第五条电弧炉炼钢工作人员应定期接受安全培训和考核,提高自身的安全意识和技能水平。
第二章作业准备第六条所有的电弧炉炼钢作业前,需要经过作业前的准备工作。
第七条电弧炉炼钢作业前,作业人员应检查炉膛是否清洁,各项设备是否正常运行。
第八条作业人员应戴上防护用具,如防护眼镜、耳塞、防护手套等。
第九条作业人员应检查电弧炉门是否密封,电缆是否完好,并确保安全。
第十条作业人员应熟悉电弧炉的熔炼过程和操作流程,了解各个设备的工作原理和操作方法。
第三章作业操作第十一条作业人员应按照规定的操作流程进行作业,不得擅自改变操作方式和参数。
第十二条作业时应保持机器设备的良好状态,如发现设备有异常情况,应及时报告,并在专业人员的指导下进行处理。
第十三条作业人员应仔细观察电弧炉的工作状态,发现异常情况应及时处理,确保安全。
第十四条作业人员应注意炉内的温度和气体情况,避免炉内温度过高或者产生有害气体。
第十五条作业人员应关注周围环境的安全状况,防止火灾和爆炸事故的发生。
第十六条作业期间,不得使用手机等与工作无关的设备,以免分神造成事故。
第四章事故应急处理第十七条电弧炉炼钢工作中如发生事故,应立即停止作业,保护好自己和他人的安全。
第十八条在事故发生后,应及时向上级报告,寻求专业的帮助和指导。
第十九条在事故处理过程中,应按照安全流程,采取安全措施,不能擅自行动。
第二十条在事故处理过程中,应优先保护好被困人员的生命安全,然后进行其他救援措施。
第二十一条在事故发生后,应及时进行事故原因的调查,找出事故的根本原因,做好事故的记载并加以总结。
电弧炉炼钢工安全操作规程
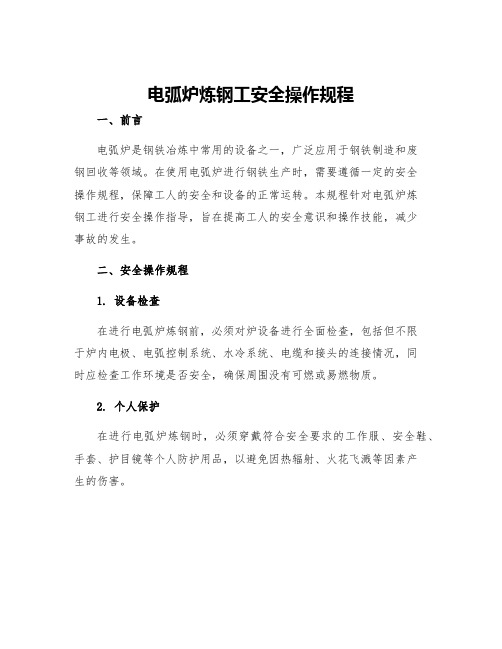
电弧炉炼钢工安全操作规程一、前言电弧炉是钢铁冶炼中常用的设备之一,广泛应用于钢铁制造和废钢回收等领域。
在使用电弧炉进行钢铁生产时,需要遵循一定的安全操作规程,保障工人的安全和设备的正常运转。
本规程针对电弧炉炼钢工进行安全操作指导,旨在提高工人的安全意识和操作技能,减少事故的发生。
二、安全操作规程1. 设备检查在进行电弧炉炼钢前,必须对炉设备进行全面检查,包括但不限于炉内电极、电弧控制系统、水冷系统、电缆和接头的连接情况,同时应检查工作环境是否安全,确保周围没有可燃或易燃物质。
2. 个人保护在进行电弧炉炼钢时,必须穿戴符合安全要求的工作服、安全鞋、手套、护目镜等个人防护用品,以避免因热辐射、火花飞溅等因素产生的伤害。
3. 开始工作在炉内装料前,应停掉电弧,然后将熔渣清除干净。
装料时应注意将铁水均匀倒入炉内,并且稳定掌握电弧电流和电压,以保证高效炼钢的同时减少电弧对设备的损伤。
4. 维护设备在炼钢过程中,应根据需要随时检查设备的运行情况,并维护设备的正常运行。
如发现异常情况,必须立即停机检查和处理,不能擅自改变设备的参数,更不能强行维护或修理设备。
5. 废品处理废弃物料中可能含有有毒或有害物质,必须妥善控制并做好处理。
操作人员必须结合工艺流程安排好废弃物料的暂存和运输处理计划,确保处理过程符合环保要求。
三、操作细节1. 电极的调整电极调整是决定炉内电弧质量的重要环节。
在开始操作前,应确保电极位置准确和稳定,特别是对于高炉等大型炉体,需要多人协同操作,确保电极的精细调整。
2. 熔渣处理在炉内产生的大量熔渣需要进行处理。
在操作中,要尽量减少熔渣与炉体的直接接触,以避免熔渣和炉体之间的电弧损伤。
同时,也要及时排除炉内污浊的杂物,保持炉内环境的清洁。
3. 电弧控制在炼钢过程中,工作人员必须掌握电弧控制的技能,熟练调节电弧强度和电流。
同时,在操作中还需留意电极电弧的稳定性、燃烧情况、冲击和避免来电现象。
四、紧急处理1. 电弧炉漏水如果发现电弧炉水冷系统出现漏水,应立即停机处理。
ZG230-450
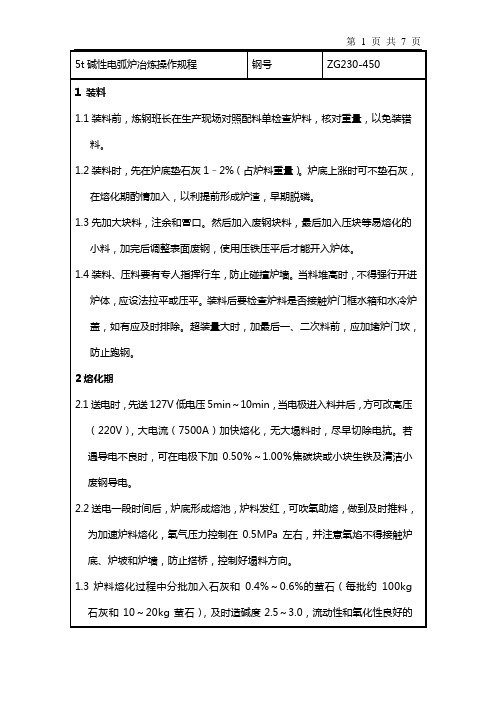
1 装料1.1装料前,炼钢班长在生产现场对照配料单检查炉料,核对重量,以免装错料。
1.2装料时,先在炉底垫石灰1–2%(占炉料重量)。
炉底上涨时可不垫石灰,在熔化期酌情加入,以利提前形成炉渣,早期脱磷。
1.3先加大块料,注余和冒口。
然后加入废钢块料,最后加入压块等易熔化的小料,加完后调整表面废钢,使用压铁压平后才能开入炉体。
1.4装料、压料要有专人指挥行车,防止碰撞炉墙。
当料堆高时,不得强行开进炉体,应设法拉平或压平。
装料后要检查炉料是否接触炉门框水箱和水冷炉盖,如有应及时排除。
超装量大时,加最后一、二次料前,应加堵炉门坎,防止跑钢。
2熔化期2.1送电时,先送127V低电压5min~10min,当电极进入料井后,方可改高压(220V),大电流(7500A)加快熔化,无大塌料时,尽早切除电抗。
若遇导电不良时,可在电极下加0.50%~1.00%焦碳块或小块生铁及清洁小废钢导电。
2.2送电一段时间后,炉底形成熔池,炉料发红,可吹氧助熔,做到及时推料,为加速炉料熔化,氧气压力控制在0.5MPa左右,并注意氧焰不得接触炉底、炉坡和炉墙,防止搭桥,控制好塌料方向。
1.3炉料熔化过程中分批加入石灰和0.4%~0.6%的萤石(每批约100kg石灰和10~20kg萤石),及时造碱度2.5~3.0,流动性和氧化性良好的熔化渣,保持渣量为料重的2%~4%。
1.4当炉料熔清(钢液表面看不到废钢,用铁耙搅拌钢液能够顺畅)后,经充分搅拌后看火花判断含碳量,要求C大于0.45%,然后取1#样分析C、P,若碳含量不够时必须用炼钢生铁或碳粉增碳,用生铁增碳时按20kg增C0.01%计算,可不再取样,用其他增碳剂时必须重新取样,必要时可插电极增碳。
取样位置在靠近炉门电极和2#电极间熔池深1/3处(各期取样位置相同),样瓢表面需覆盖一层薄渣。
脱碳量以此样为准。
1.5熔化末期,根据配碳量和含磷量高低,如含磷较高。
可分批加入不超过料重的1.5%的碎矿石或氧化铁皮放初期渣(每批约30kg矿石),并补充适量的石灰、萤石,造好流动性良好的熔化渣,以利脱磷。
铸造工(电弧炉冶炼)安全操作规程
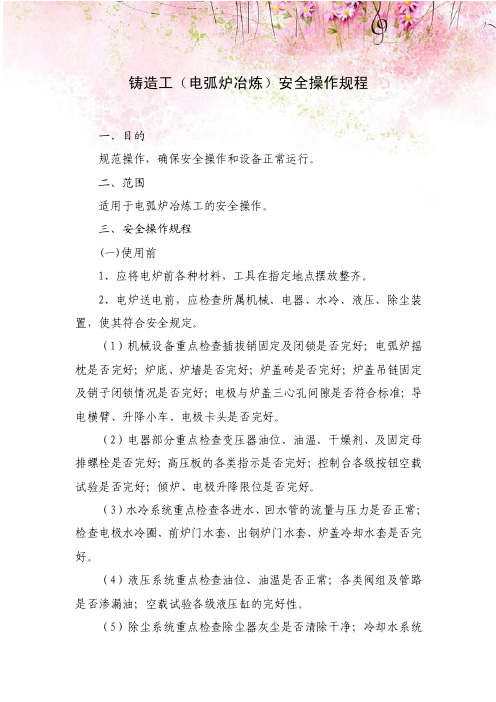
铸造工(电弧炉冶炼)安全操作规程一、目的规范操作,确保安全操作和设备正常运行。
二、范围适用于电弧炉冶炼工的安全操作。
三、安全操作规程(一)使用前1、应将电炉前各种材料,工具在指定地点摆放整齐。
2、电炉送电前,应检查所属机械、电器、水冷、液压、除尘装置,使其符合安全规定。
(1)机械设备重点检查插拔销固定及闭锁是否完好;电弧炉摇枕是否完好;炉底、炉墙是否完好;炉盖砖是否完好;炉盖吊链固定及销子闭锁情况是否完好;电极与炉盖三心孔间隙是否符合标准;导电横臂、升降小车、电极卡头是否完好。
(2)电器部分重点检查变压器油位、油温、干燥剂、及固定母排螺栓是否完好;高压板的各类指示是否完好;控制台各级按钮空载试验是否完好;倾炉、电极升降限位是否完好。
(3)水冷系统重点检查各进水、回水管的流量与压力是否正常;检查电极水冷圈、前炉门水套、出钢炉门水套、炉盖冷却水套是否完好。
(4)液压系统重点检查油位、油温是否正常;各类阀组及管路是否渗漏油;空载试验各级液压缸的完好性。
(5)除尘系统重点检查除尘器灰尘是否清除干净;冷却水系统是否完好;除尘罩轨道是否有障碍物等。
3、当出钢坑和炉前出渣坑中有水,炉底过深,炉壁损坏超过规定时,不得送电炼钢。
4、炉料要有专人负责检查。
严禁将易爆物,密封容器及水、雪块或带水的炉料入炉,以防爆炸。
5、每次开炉前,操作工要将导电横臂、电极卡头、炉盖上的灰尘、脏杂物清理干净。
6、当停炉超过24小时,应检查炉膛情况。
发现炉内潮湿或者有水,应设法进行烘烤,干燥后方可装料熔炼。
(二)操作时1、待检查确认正常后方可送电。
2、需要二次装料时,在装料前必须把炉门坎垫高,垫牢,以防钢水跑出。
炉料高出炉壳需要吊车压料时,要有专人指挥,并遵守挂钩工安全操作规程。
3、应检查好阀门,压力表,氧气管,卡头要把好,卡紧。
4、吹氧时要有专人看管阀门和仪表,并互相配合好,操作时严禁将手放在卡子上,以防回火伤人,氧气压力应保持0.6~0.8MPa,吹氧熔化合金时,也不要超过1.2MPa。
三相电弧炉炼钢操作规程
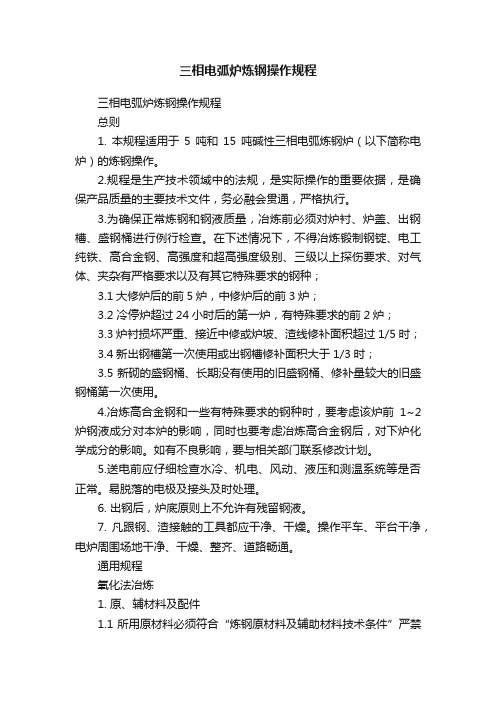
三相电弧炉炼钢操作规程三相电弧炉炼钢操作规程总则1. 本规程适用于5吨和15吨碱性三相电弧炼钢炉(以下简称电炉)的炼钢操作。
2.规程是生产技术领域中的法规,是实际操作的重要依据,是确保产品质量的主要技术文件,务必融会贯通,严格执行。
3.为确保正常炼钢和钢液质量,冶炼前必须对炉衬、炉盖、出钢槽、盛钢桶进行例行检查。
在下述情况下,不得冶炼锻制钢锭、电工纯铁、高合金钢、高强度和超高强度级别、三级以上探伤要求、对气体、夹杂有严格要求以及有其它特殊要求的钢种;3.1大修炉后的前5炉,中修炉后的前3炉;3.2 冷停炉超过24小时后的第一炉,有特殊要求的前2炉;3.3炉衬损坏严重、接近中修或炉坡、渣线修补面积超过1/5时;3.4新出钢槽第一次使用或出钢槽修补面积大于1/3时;3.5 新砌的盛钢桶、长期没有使用的旧盛钢桶、修补量较大的旧盛钢桶第一次使用。
4.冶炼高合金钢和一些有特殊要求的钢种时,要考虑该炉前1~2炉钢液成分对本炉的影响,同时也要考虑冶炼高合金钢后,对下炉化学成分的影响。
如有不良影响,要与相关部门联系修改计划。
5.送电前应仔细检查水冷、机电、风动、液压和测温系统等是否正常。
易脱落的电极及接头及时处理。
6. 出钢后,炉底原则上不允许有残留钢液。
7. 凡跟钢、渣接触的工具都应干净、干燥。
操作平车、平台干净,电炉周围场地干净、干燥、整齐、道路畅通。
通用规程氧化法冶炼1. 原、辅材料及配件1.1 所用原材料必须符合“炼钢原材料及辅助材料技术条件”严禁有毒、有害、易燃、易爆物以及对钢液质量有害的金属和非金属进入炉内。
1.2应根据所炼钢种冶炼方法、原材料成份、前炉钢对本炉钢的影响、冷停炉时间长短的影响、吹氧助熔的需要、计划钢产量等进行仔细计算,拟制配料单,配碳量应保证全熔化后氧化沸腾脱碳的需要,生铁配入量不得超过炉料重的15%,不足之碳量可配入电极块或冶金焦碳补足。
1.3所配炉料大小块度应合适,配比为:大块料20~40%,中块料30~40%,小块料(包括钢屑)30~50%。
电弧炉熔炼工安全操作规程
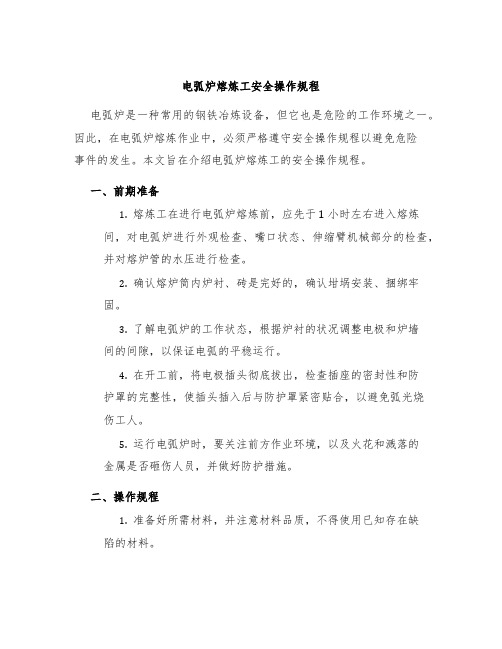
电弧炉熔炼工安全操作规程电弧炉是一种常用的钢铁冶炼设备,但它也是危险的工作环境之一。
因此,在电弧炉熔炼作业中,必须严格遵守安全操作规程以避免危险事件的发生。
本文旨在介绍电弧炉熔炼工的安全操作规程。
一、前期准备1.熔炼工在进行电弧炉熔炼前,应先于 1 小时左右进入熔炼间,对电弧炉进行外观检查、嘴口状态、伸缩臂机械部分的检查,并对熔炉管的水压进行检查。
2.确认熔炉筒内炉衬、砖是完好的,确认坩埚安装、捆绑牢固。
3.了解电弧炉的工作状态,根据炉衬的状况调整电极和炉墙间的间隙,以保证电弧的平稳运行。
4.在开工前,将电极插头彻底拔出,检查插座的密封性和防护罩的完整性,使插头插入后与防护罩紧密贴合,以避免弧光烧伤工人。
5.运行电弧炉时,要关注前方作业环境,以及火花和溅落的金属是否砸伤人员,并做好防护措施。
二、操作规程1.准备好所需材料,并注意材料品质,不得使用已知存在缺陷的材料。
2.操作过程中,熔炼工人必须穿戴适宜的劳动防护用品,包括头盔、手套、防护服、安全带等。
3.在熔化钢水时,要掌握钢液温度、化学成分和炼钢工艺的参数等,以确保钢水质量。
4.在进行操作时,要严格按照规定操作,禁止违章操作和操作失误。
如需更改操作方法,必须报经班组长同意后方可进行。
5.在电弧炉熔炼操作过程中,要及时调整炉衬和电极之间的间隙,保持电弧熔化钢水的稳定,避免冷却堵塞和产生爆炸。
6.熔炼工在操作过程中不得在电弧炉周围晃动,以免引燃周围易燃物,保证周围环境的安全。
7.如果发现电弧炉有异常情况,如出现炉内压力异常增大、有异味或声响,需要立即向负责人报告,停止操作,迅速撤离现场并进行必要的警示措施。
三、结束操作1.在电弧炉关闭前,熔炼工应检查操作是否符合规程,关闭所有管道和开关。
2.关闭电源之前,熔炼工人应对电弧炉进行全面的检查,并清除炉内残留物、护套等余渣。
3.拆卸电极时,工作人员必须停止电弧熔炼过程,并保持熔炼间内散热,以避免烧伤和出现其他危险情况。
2023年电弧炉炼钢工安全操作规程

2023年电弧炉炼钢工安全操作规程____年电弧炉炼钢工安全操作规程第一章总则第一条为了保障电弧炉炼钢工作的安全性和高效性,制定本规程。
本规程适用于所有从事电弧炉炼钢工作的人员。
第二条电弧炉炼钢工作包括电弧炉操作、钢水处理和设备检修等工作。
第三条电弧炉炼钢工作应严格按照国家有关炼钢工作的法律法规和标准要求进行。
第四条电弧炉炼钢工作需要特别注意安全防护,确保操作人员的人身安全和设备的安全运行。
第二章电弧炉操作安全规程第一条操作人员必须经过专业培训并持有相应的资格证书方可上岗。
第二条操作人员必须熟悉电弧炉的结构、工作原理和操作流程,并具备相应的操作技能。
第三条操作人员在操作电弧炉时,必须佩戴符合要求的个人防护装备,包括防护服、防护手套、防护眼镜和安全帽等。
第四条操作人员在操作电弧炉时,必须保持清醒状态,不得饮酒、吸烟或使用药物。
第五条操作人员在操作电弧炉前,必须检查电弧炉设备的各项安全装置和工作状态,确保设备完好并符合操作要求。
第六条操作人员在操作电弧炉时,必须严格按照操作规程要求进行操作,不得擅自停止或改变操作过程。
第七条操作人员在操作电弧炉时,必须保持操作台面整洁,不得堆放杂物或其他危险物品。
第八条操作人员在操作电弧炉时,必须保持良好的工作状态,不得分心或疏忽,以免造成事故。
第九条操作人员在操作电弧炉时,必须定期进行安全检查和维护,及时消除设备故障和隐患。
第十条操作人员在操作电弧炉时,必须严格遵守电弧炉操作的安全流程,确保操作的顺利进行。
第三章钢水处理安全规程第一条钢水处理工作必须由经过专业培训并持有相应的资格证书的人员进行。
第二条钢水处理工作必须在符合安全要求的环境下进行,防止发生火灾和爆炸等事故。
第三条钢水处理工作必须严格按照操作规程进行,不得擅自停止或改变处理过程。
第四条钢水处理工作必须使用符合要求的设备和器具,确保设备的安全性和操作的有效性。
第五条钢水处理工作必须佩戴符合要求的个人防护装备,包括防护服、防护手套和防护眼镜等。
电弧炉熔炼工安全操作规程
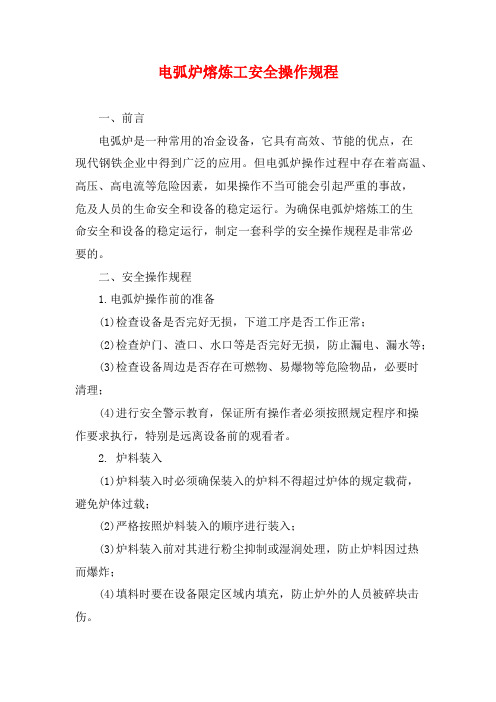
电弧炉熔炼工安全操作规程一、前言电弧炉是一种常用的冶金设备,它具有高效、节能的优点,在现代钢铁企业中得到广泛的应用。
但电弧炉操作过程中存在着高温、高压、高电流等危险因素,如果操作不当可能会引起严重的事故,危及人员的生命安全和设备的稳定运行。
为确保电弧炉熔炼工的生命安全和设备的稳定运行,制定一套科学的安全操作规程是非常必要的。
二、安全操作规程1.电弧炉操作前的准备(1)检查设备是否完好无损,下道工序是否工作正常;(2)检查炉门、渣口、水口等是否完好无损,防止漏电、漏水等;(3)检查设备周边是否存在可燃物、易爆物等危险物品,必要时清理;(4)进行安全警示教育,保证所有操作者必须按照规定程序和操作要求执行,特别是远离设备前的观看者。
2. 炉料装入(1)炉料装入时必须确保装入的炉料不得超过炉体的规定载荷,避免炉体过载;(2)严格按照炉料装入的顺序进行装入;(3)炉料装入前对其进行粉尘抑制或湿润处理,防止炉料因过热而爆炸;(4)填料时要在设备限定区域内填充,防止炉外的人员被碎块击伤。
3. 电弧炉启动(1)启动设备前,应检查外部场地和操作区域是否摆放整齐,安全可靠保持正常状态,同时通风设备应该运转;(2)按照标准操作程序启动电弧炉,严格按照操作要求进行操作,启动同时保持注意力集中;(3)电弧炉启动前应确保大、小炉缸内均无积水。
如果发现积水,必须及时排水。
4. 熔炼操作(1)在熔炼过程中,操作者必须始终关注炉体的温度、压力、速度等指标,及时采取措施,保证炉料的熔化和成分的正确性;(2)操作者必须手持防爆电吹风、钢棒、钳子等,从炉口为起始点,带有保护工具向两侧清理炉口周围的灰渣;(3)在操作过程中,注意及时把有用的炉渣倒出,避免对炉体的溶解造成影响。
5. 炉后操作(1)操作者必须确保电弧炉已彻底停止工作,温度下降至安全值之后才能走出炉房;(2)在清理炉渣时,必须穿好防护服,戴护目镜、耳罩、手套等防护用品;(3)在炉后操作时,一定要注意安全,特别是接触高温设备时必须使用防护设备,并确保设备处于安全状态。
电弧炉炼钢工安全技术操作规程
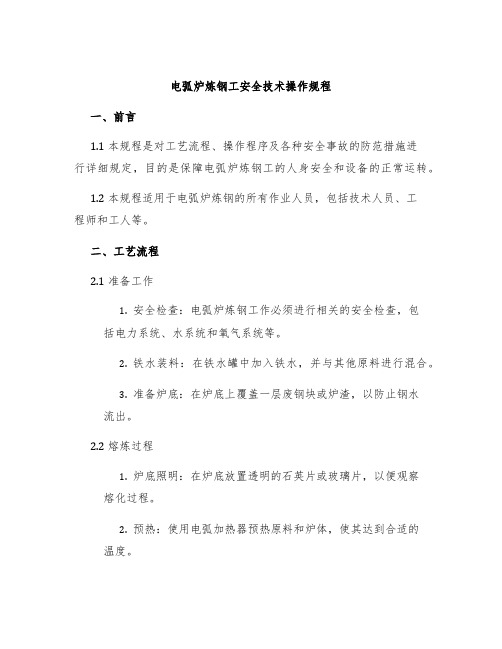
电弧炉炼钢工安全技术操作规程一、前言1.1 本规程是对工艺流程、操作程序及各种安全事故的防范措施进行详细规定,目的是保障电弧炉炼钢工的人身安全和设备的正常运转。
1.2 本规程适用于电弧炉炼钢的所有作业人员,包括技术人员、工程师和工人等。
二、工艺流程2.1 准备工作1.安全检查:电弧炉炼钢工作必须进行相关的安全检查,包括电力系统、水系统和氧气系统等。
2.铁水装料:在铁水罐中加入铁水,并与其他原料进行混合。
3.准备炉底:在炉底上覆盖一层废钢块或炉渣,以防止钢水流出。
2.2 熔炼过程1.炉底照明:在炉底放置透明的石英片或玻璃片,以便观察熔化过程。
2.预热:使用电弧加热器预热原料和炉体,使其达到合适的温度。
3.技术操作:根据需要控制电弧炉的工作电流和炉膛电极的位置,以控制炉内的能量和熔化程度。
4.向炉中加入其他物料:在必要时向炉中添加石灰、硅钙、铝土等物料,以保证生产合格产品。
2.3 出钢1.排钢:当钢熔液温度达到要求时,打开冷却水阀门,使钢熔液流入钢包中。
2.切割:被装满的钢包用切割机进行一定的切割,以便于钢水的装卸。
三、安全操作规程3.1 安全设施1.炉体必须保证完整并没有损坏,未经允许的个人不得进行任何的维修。
2.操作区域必须清洁、宽敞、灭火器必须放置在显眼的位置,以便进行随时使用。
3.电弧炉操作人员必须穿着防护服、防火鞋,电焊面具和手套等必要的保护用品。
3.2 用电安全1.操作人员必须熟悉电弧炉的电力系统的工作原理,并有能力进行必要的维修和检修。
2.电线必须采用绝缘材料,并安装在合适的位置,以防止热炉熔化。
3.外来人员不得触碰电力系统的任何部分,不得进行电弧炉的维修和检修工作。
3.3 防火安全1.在操作过程中,熔化的物料和熔化的炉渣时常会纷飞四溅,所以操作人员必须戴上头盔和防火眼镜,以保护眼睛、面部皮肤和头部。
2.贮放的油、液化气、乙炔等易燃物品必须远离炉子,以免发生火灾。
3.操作人员必须及时消除炉子周围和炉底附近的积水,以免接触到电力系统和导致火灾或爆炸。
电弧炉设备操作规程(2024)
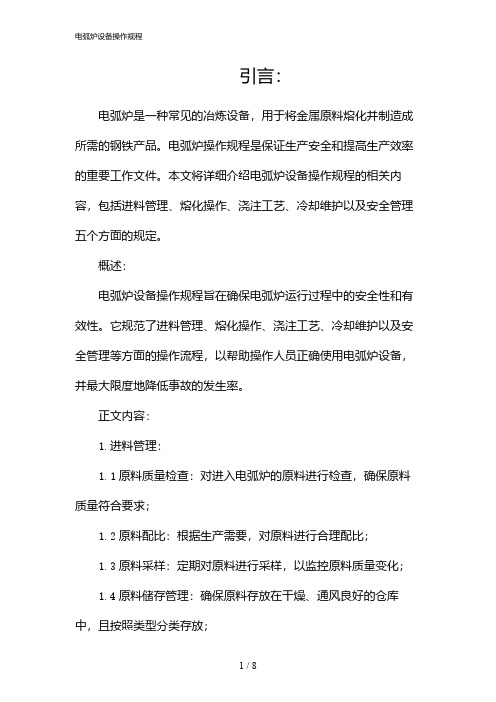
引言:电弧炉是一种常见的冶炼设备,用于将金属原料熔化并制造成所需的钢铁产品。
电弧炉操作规程是保证生产安全和提高生产效率的重要工作文件。
本文将详细介绍电弧炉设备操作规程的相关内容,包括进料管理、熔化操作、浇注工艺、冷却维护以及安全管理五个方面的规定。
概述:电弧炉设备操作规程旨在确保电弧炉运行过程中的安全性和有效性。
它规范了进料管理、熔化操作、浇注工艺、冷却维护以及安全管理等方面的操作流程,以帮助操作人员正确使用电弧炉设备,并最大限度地降低事故的发生率。
正文内容:1.进料管理:1.1原料质量检查:对进入电弧炉的原料进行检查,确保原料质量符合要求;1.2原料配比:根据生产需要,对原料进行合理配比;1.3原料采样:定期对原料进行采样,以监控原料质量变化;1.4原料储存管理:确保原料存放在干燥、通风良好的仓库中,且按照类型分类存放;1.5原料运输:运输原料时,应遵守相应的安全操作规程,防止原料的损坏或泄漏。
2.熔化操作:2.1电弧炉预热:根据炉型和工艺要求,对电弧炉进行预热;2.2炉底清理:在每次操作前,清理炉底残渣,确保下次操作的顺利进行;2.3电弧点火:使用专用设备进行电弧点火,确保电弧炉快速点火;2.4炉内搅拌:根据需要进行炉内搅拌,以促进熔料的均匀熔化;2.5熔炼温度控制:根据工艺要求,严格控制熔炼温度,并对温度进行监控。
3.浇注工艺:3.1炉渣处理:定期清理炉渣,并对炉渣进行分析,确保其质量符合要求;3.2出钢方式:根据产品要求,选择合适的出钢方式,确保钢水质量;3.3浇注温度控制:控制浇注温度,确保产品质量和成型效果;3.4浇注速度控制:根据产品要求,控制浇注速度,防止钢液溅出;3.5浇注过程监控:对浇注过程进行实时监控,及时处理异常情况。
4.冷却维护:4.1冷却水质量管理:定期对冷却水进行检测,确保水质符合要求;4.2冷却设备维护:定期对冷却设备进行检查和维护,确保其正常运行;4.3冷却管清洗:定期清洗冷却管道,防止堵塞和水垢结垢;4.4冷却速度控制:根据产品要求,控制冷却速度,避免产生内应力;4.5冷却过程监控:对冷却过程进行监控,及时处理异常情况。
电炉冶炼安全技术操作规程范本
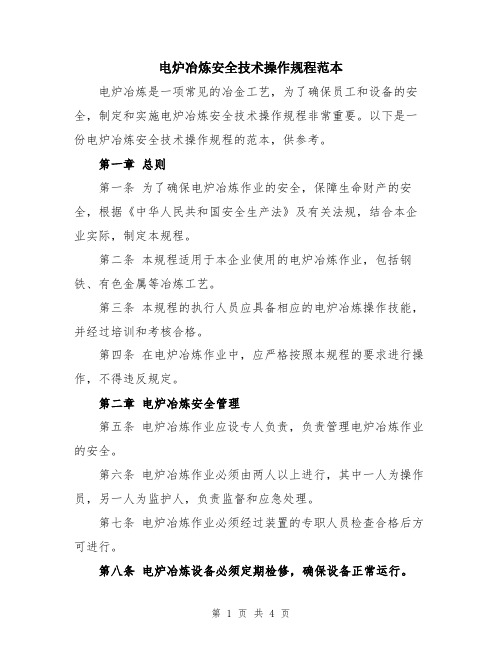
电炉冶炼安全技术操作规程范本电炉冶炼是一项常见的冶金工艺,为了确保员工和设备的安全,制定和实施电炉冶炼安全技术操作规程非常重要。
以下是一份电炉冶炼安全技术操作规程的范本,供参考。
第一章总则第一条为了确保电炉冶炼作业的安全,保障生命财产的安全,根据《中华人民共和国安全生产法》及有关法规,结合本企业实际,制定本规程。
第二条本规程适用于本企业使用的电炉冶炼作业,包括钢铁、有色金属等冶炼工艺。
第三条本规程的执行人员应具备相应的电炉冶炼操作技能,并经过培训和考核合格。
第四条在电炉冶炼作业中,应严格按照本规程的要求进行操作,不得违反规定。
第二章电炉冶炼安全管理第五条电炉冶炼作业应设专人负责,负责管理电炉冶炼作业的安全。
第六条电炉冶炼作业必须由两人以上进行,其中一人为操作员,另一人为监护人,负责监督和应急处理。
第七条电炉冶炼作业必须经过装置的专职人员检查合格后方可进行。
第八条电炉冶炼设备必须定期检修,确保设备正常运行。
第九条电炉冶炼作业必须按照作业指导书进行,明确工艺参数和操作流程。
第十条电炉冶炼作业过程中发生事故或异常情况,应立即停止作业,并报告上级主管人员。
第三章电炉冶炼安全措施第十一条电炉冶炼作业必须穿戴符合国家安全标准的防护用品,包括防火服、防护手套、防护眼镜等。
第十二条在电炉冶炼作业现场必须设置明显的安全警示标志,提醒人员注意安全。
第十三条在电炉冶炼作业现场应设置灭火器材和应急疏散通道,并确保通道畅通。
第十四条电炉冶炼作业现场不得堆放易燃、易爆物品,保持场地整洁。
第十五条电炉冶炼作业时,应严禁携带易燃、易爆物品,禁止吸烟。
第十六条电炉冶炼作业现场必须保持通风良好,防止有害气体积聚。
第十七条电炉冶炼作业现场必须配备专用消防设备,如水源、灭火器材等,并定期检查。
第十八条电炉冶炼作业时应注意电炉周围的高温和电磁辐射,确保人员的安全。
第四章电炉冶炼操作步骤第十九条电炉冶炼作业前,必须进行安全检查,并确认电炉设备工作正常。
电炉冶炼安全技术操作规程范文(二篇)

电炉冶炼安全技术操作规程范文一、操作准备1. 执行安全作业分工,明确操作人员的职责和相应的安全防护措施。
2. 检查电炉设备的运行状态,确保设备正常工作并无任何隐患。
3. 检查冶炼材料的质量和储存情况,对不合格或损坏的材料进行分类处理。
4. 检查炉渣的清理情况,确保炉体内部无阻碍物。
5. 检查冷却水系统的运行状态,确保冷却系统正常工作并且水质符合要求。
二、操作步骤1. 开始操作前,操作人员应戴上防护眼镜、防护手套、耐高温服装等个人防护装备。
2. 打开电源,启动电炉设备,调整炉温至所需的冶炼温度。
3. 将冶炼材料平均均匀地放入电炉中,严禁将湿润的或有湿度的材料放入炉内。
4. 关闭电炉的充电门,打开电炉的废气排放口,确保炉内通风畅通。
5. 根据冶炼材料的性质和要求,适时加入辅助材料,如石灰石、熔剂等,并根据需要进行搅拌。
6. 根据冶炼过程中的炉温变化,及时调整电炉的加热量,保持合适的冶炼温度。
7. 定期检查冶炼过程中的冷却系统水流情况,确保冷却系统正常工作。
8. 当冶炼完毕或达到所需冶炼效果后,关闭电炉设备。
9. 打开电炉的排渣口,将炉渣倒出,并注意观察和记录炉渣的性质和质量。
10. 清理冶炼过程中产生的废弃物和杂物,确保工作环境整洁。
三、操作注意事项1. 操作人员应严格按照规程操作,不得擅自更改操作步骤或增减操作工序。
2. 在操作过程中发现设备异常或存在安全隐患时,应立即停止操作,并及时报告有关部门。
3. 不得将冶炼材料和辅助材料随意堆放,应按照规定的区域和方法储存。
4. 操作人员应定期接受安全教育和培训,提升安全意识和技能水平。
5. 在操作中严禁将手伸入电炉内部或触摸电炉设备的高温部分,以免发生烫伤或电击的危险。
6. 清理炉渣时,应穿戴好防护手套和护目镜,并小心翼翼地倒出炉渣,以免造成溅出伤害。
7. 操作人员应时刻关注电炉的温度和热辐射情况,保持安全的工作距离。
8. 在冶炼过程中,严禁私自操作或调整电炉设备,必须由指定的负责人进行操作和调整。
100吨直流电弧炉冶炼技术操作规程

100吨直流电弧炉冶炼技术操作规程第三章 100吨直流电弧炉冶炼技术操作规程第⼀节留钢留渣操作⼯艺⼀、废钢配(装)料1、配料原则保证冶炼过程的顺利进⾏,达到预期的钢种质量要求。
合理⽤料,经济配料,既满⾜品种质量要求,⼜降低成本。
2、配料⽅案●需通电(1)⽆铁⽔供应时:每炉配料可根据废钢状况合理配料,配料次数为2—4料篮,⽣铁配⼊量20—40t,分批装在第⼀料篮和第⼆料篮的中下部位,⽣铁不得配在第三和第四篮料内。
(2)有铁⽔供应时:根据废钢状况,每炉配料应装2—3料篮,尽量减少加料次数,具体每篮料的装⼊量按照技术中⼼配料通知单执⾏,料型合理搭配,防⽌电炉压料。
●不通电电炉炉长根据铁⽔(重量、温度、铁⽔Si含量等)情况,参照以下配料⽅案进⾏配料:好⼀个15~20吨左右废钢料篮。
开新炉在上表基础上减少废钢5吨、增加铁⽔15吨。
换炉停炉前最后⼀炉在上表基础上减少10吨废钢、5吨铁⽔。
当铁⽔量不⾜或波动⼤时,及时调整以确保电炉出钢温度满⾜⼯艺卡要求,3、炼钢使⽤的原材料应符合第⼆章“炼钢原材料技术标准和要求”中的规定。
使⽤铁合⾦应详细了解成份并符合技术条件,按顺序加⼊前需称量。
4、所配钢铁料需准确计算,收得率按90%计算。
5、料篮装料要严格按配料单进⾏,并由作业长签字确认。
料篮装料的次序:料篮底部铺⼀层轻碎废钢,然后平稳地装⼊重型废钢;中间装⼊中型废钢;上部为⼩型废钢和轻型废钢填空。
不易导电的炉料,不允许装在料篮中央,即电极下部。
每料篮靠炉门⼝侧的废钢应装轻薄料,⼤块料应配在第⼀篮中下部,底部配⼊3~5t轻薄料。
6、料篮装料⾼度不得⾼出料篮上限线,不能装⼊超过标准的⼤块板状废钢。
若发现有爆炸物品、密封容器、有⾊⾦属等,必须拣除。
7、每次料篮装完后,应⽰明炉号以及进料的次数和次序。
8、为保证⽣产节奏,每炉装料时间不得超过规定时间,若有设备、仪器出现故障,必须及时与有关检修部门联系,并⽴即修复好。
⼆、炉体和底电极的维护及进料前的准备。
电弧炉炼钢工安全操作规程

电弧炉炼钢工安全操作规程电弧炉炼钢是一种常见的钢铁生产方法,但由于涉及高温、高压以及有毒气体等危险因素,操作人员必须严格遵守安全规程,以确保工作人员的安全。
下面是一份电弧炉炼钢工安全操作规程,总计2000字。
一、一般安全操作规程1. 操作人员必须经过专业培训并取得相应的合格证书,方可进行电弧炉炼钢操作。
2. 在操作电弧炉炼钢前,必须详细检查设备的安全状态,确保各种安全装置的正常运行。
3. 在操作过程中,严禁穿戴松散的衣物,腰带等物品。
操作人员必须穿戴防火防热的工装,且应戴上防护手套、安全帽、护目镜、耳塞等个人防护装备。
4. 未经许可,严禁在设备上进行任何形式的维修作业。
5. 操作人员必须了解各种应急救援措施,熟悉应急通道和各种安全设施的使用方法。
二、电弧炉操作安全规程1. 在操作电弧炉前,必须确认电源已经切断,设备停电。
并且切断炉顶供气和水源,确保操作区域安全。
2. 操作人员必须通过无损检测等手段确保电弧炉炉体没有任何缺陷或损伤。
3. 在操作过程中,必须随时注意电弧炉内部的温度和压力变化。
若发现温度异常升高或压力异常增大,应及时报警,切断电源。
4. 操作人员必须根据操作指南和工艺要求准确控制电弧炉的电压、电流、时间等参数,以确保炼钢过程的安全和有效。
5. 在操作过程中,严禁进行恶意破坏或损坏电弧炉的设备和设施。
三、炼钢过程安全规程1. 在装料过程中,操作人员应保持适当的距离,防止热料溅出造成烫伤。
2. 在加料过程中,操作人员必须佩戴钢盔和防护面镜,以防止破碎物、溅落物飞溅伤人。
3. 在炉体冷却期间,禁止进行任何形式的接近或触摸。
等待炉体完全冷却后再进行操作。
4. 在冶炼过程中,严禁穿戴金属制品,以防止因金属接触而发生电击事故。
5. 在炉体维护和清洁时,必须先切断电源,确保设备停电,防止触电事故的发生。
四、有毒气体防护规程1. 在操作电弧炉炼钢过程中,产生大量的有毒烟尘和气体。
操作人员必须佩戴适当的防护口罩,以防止吸入有毒气体。
电弧炉熔炼工安全操作规程(3篇)
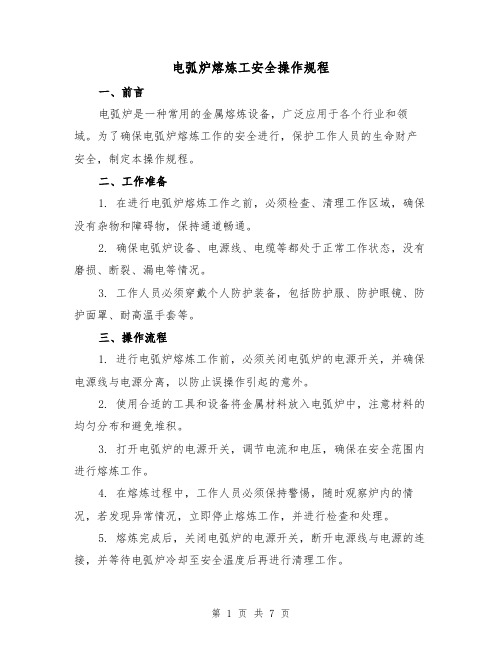
电弧炉熔炼工安全操作规程一、前言电弧炉是一种常用的金属熔炼设备,广泛应用于各个行业和领域。
为了确保电弧炉熔炼工作的安全进行,保护工作人员的生命财产安全,制定本操作规程。
二、工作准备1. 在进行电弧炉熔炼工作之前,必须检查、清理工作区域,确保没有杂物和障碍物,保持通道畅通。
2. 确保电弧炉设备、电源线、电缆等都处于正常工作状态,没有磨损、断裂、漏电等情况。
3. 工作人员必须穿戴个人防护装备,包括防护服、防护眼镜、防护面罩、耐高温手套等。
三、操作流程1. 进行电弧炉熔炼工作前,必须关闭电弧炉的电源开关,并确保电源线与电源分离,以防止误操作引起的意外。
2. 使用合适的工具和设备将金属材料放入电弧炉中,注意材料的均匀分布和避免堆积。
3. 打开电弧炉的电源开关,调节电流和电压,确保在安全范围内进行熔炼工作。
4. 在熔炼过程中,工作人员必须保持警惕,随时观察炉内的情况,若发现异常情况,立即停止熔炼工作,并进行检查和处理。
5. 熔炼完成后,关闭电弧炉的电源开关,断开电源线与电源的连接,并等待电弧炉冷却至安全温度后再进行清理工作。
四、安全注意事项1. 电弧炉熔炼工作时,工作人员必须集中注意力,不得分心进行其他活动,以防止发生意外事故。
2. 在熔炼金属时,应保持熔池的液面稳定,避免熔池溅出造成烧伤事故。
3. 在熔炼过程中,严禁使用湿手或带有金属饰品等导电物品,以免触电伤人。
4. 熔炼金属时,应注意防火安全,禁止在熔炼区域周围放置易燃物品,以免引发火灾。
5. 在进行电弧炉熔炼工作时,应定期对设备进行检查和维护,确保设备的正常运行和安全性能。
五、紧急情况处理1. 如遇到火灾,应立即拉响火警报警器,同时向工作区域内的所有人员发出紧急撤离指令,并使用灭火器进行初期扑灭。
2. 如遇到人员受伤事故,应立即停止工作,进行紧急救治,并报告相关部门进行处理。
3. 如遇到设备故障或漏电等电气事故,应立即切断电源,确保人员的安全,然后报告相关部门进行处理。
电弧炉冶炼技术操作规程

1.筑炉操作规程1.1大修工艺1.1.1绝热层。
砌筑时先在炉底紧贴炉壳底部铺一层10-15mm厚的石棉板,石棉板上铺一层硅藻土(厚度小于20mm),其上砌一层轻质粘土砖或粘土砖,其总厚度约80mm 左右。
1.1.2砌砖层1)平铺一层65mm左右的保温砖,砌砖需要加工好,砌至砖坡“八”字处时常出现三角缝隙,要最大限度的缩小砖缝,砌缝应≤1.5mm,砌好后需用粒度≤0.5mm的镁砂粉添缝,然后用木锤敲打使镁粉很好的渗入砖缝,最后扫去剩余镁粉。
2)砌好保温砖后,再砌一层65mm左右的镁砖,砖缝要求同上。
3)侧砌一层约115mm左右的镁砖,缝隙要求同上。
4)砌砖层相邻两层的砖缝应成45o或60o,以免砖缝重合,砌砖层必须干砌。
5)炉底砌完后,紧挨炉壳粘一层10mm左右的石棉板,再薄砌一层65mm的标准粘土砖,构成隔热层,可以湿砌。
1.1.3打结层。
1)镁砂颗粒配比为3~8mm者60%,小于或等于0.5mm者40%,打结采用平头风锤。
2)采用卤水粘结剂,卤水比重应达到1.3~1.4,使用温度为20~40o C,用量8~10%。
3)打结时压缩空气压力应大于6个大气压。
4)打结总厚度300mm左右,分层打结,第一层一般打结不大于80mm,以后各层不宜大于50mm。
5)新炉底打结前应将砖面预热到200o C左右。
6)炉底炉坡打结完后,最上层尽量平整一些,以便放平、放稳模胎,并用大小砖配合堵紧炉门,用平头风锤按每层50mm厚打结,同时衡量高度,以便于合计其后砌砖层厚度。
7)在打结炉壁的过程中,要注意出钢槽的位置,多用木质材料堵塞,以便在烤炉过程中燃烧干净而使出钢口畅通。
8)取下模胎,在打结壁上用D-4、D-6砖干砌上半炉壁,缝隙要求尽量小,砌完一层使用镁粉填充缝隙后再砌下层,相邻两层砖缝错开,共砌四层。
1.2中修工艺1.2.1炉壁厚度普遍小于100mm,局部严重损坏面积较大或炉底太薄(小于100mm)时需要中修。
电弧炉熔炼工安全操作规程范本

电弧炉熔炼工安全操作规程范本一、工作前的准备1、操作人员必须熟悉电弧炉熔炼工作流程和设备操作规范,接受相关的安全培训。
2、在进行熔炼工作之前,操作人员必须穿戴好防护服、防护眼镜、耳塞、耐高温手套和安全鞋等个人防护装备。
3、确认熔炼区域周围没有可燃物品和易燃材料,并保持通风良好。
4、对电弧炉设备进行检查,确保设备正常运行,并检查电源和控制系统是否正常。
5、检查冷却系统,确保水管路畅通,水压稳定。
二、熔炼工作操作规程1、将需要熔炼的金属或合金材料放置在电弧炉的炉座内,并确保材料与炉底接触良好。
2、戴上防护眼镜,通过控制系统启动电弧炉,调节合适的炉温,并注意观察炉温变化。
3、使用合适的工具将加热后的金属材料倾倒到需要的模具或铸造设备中,注意操作时避免烫伤和切割伤。
4、熔炼过程中,操作人员要注意炉温和冷却水温的稳定,如发现异常情况,应及时停止操作并报告上级。
5、禁止在熔炼区域吸烟、使用明火和进行其他危险操作,保持工作区域的整洁和安全。
6、熔炼结束后,关闭电弧炉主电源,等待炉温降至安全温度后方可进行下一步操作。
三、事故应急处理1、发生火灾时,操作人员应立即拉响报警器,并组织人员进行灭火。
在无法控制的情况下,应立即撤离现场,并向消防部门报警。
2、发生人员意外伤害事故时,立即停止工作,拨打急救电话,并进行必要的急救措施,同时通知上级和相关人员。
3、如发现设备故障或异常情况,应立即停止操作,排除故障后方可继续工作。
四、设备维护和安全管理1、定期对电弧炉设备进行维护和检查,保证设备运行稳定和安全。
2、定期检查冷却水系统,保证冷却系统畅通和水压正常。
3、严禁未经许可私自拆卸、更改或修理电弧炉设备。
4、在每次工作结束后,及时清理和整理工作区域,保持设备和周围环境的清洁和安全。
5、不得将危险废料随意丢弃,应按照相关规定进行分类和处理。
养成良好的安全习惯,遵守本规程,确保电弧炉熔炼工作的安全和稳定运行。
电弧炉操作规程(一)2024
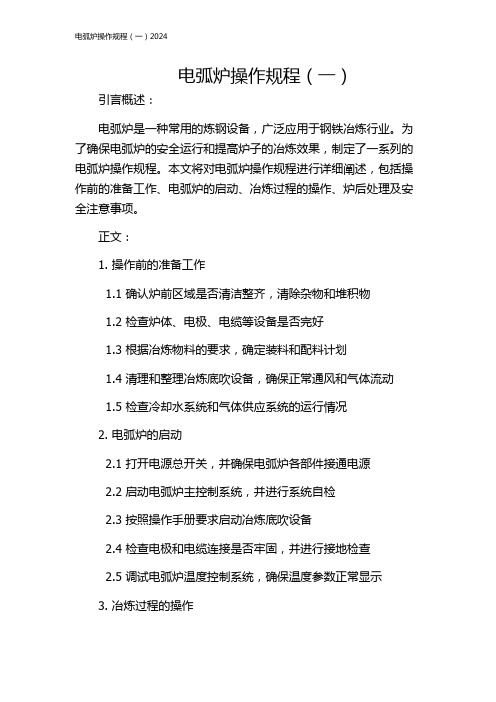
电弧炉操作规程(一)引言概述:电弧炉是一种常用的炼钢设备,广泛应用于钢铁冶炼行业。
为了确保电弧炉的安全运行和提高炉子的冶炼效果,制定了一系列的电弧炉操作规程。
本文将对电弧炉操作规程进行详细阐述,包括操作前的准备工作、电弧炉的启动、冶炼过程的操作、炉后处理及安全注意事项。
正文:1. 操作前的准备工作1.1 确认炉前区域是否清洁整齐,清除杂物和堆积物1.2 检查炉体、电极、电缆等设备是否完好1.3 根据冶炼物料的要求,确定装料和配料计划1.4 清理和整理冶炼底吹设备,确保正常通风和气体流动1.5 检查冷却水系统和气体供应系统的运行情况2. 电弧炉的启动2.1 打开电源总开关,并确保电弧炉各部件接通电源2.2 启动电弧炉主控制系统,并进行系统自检2.3 按照操作手册要求启动冶炼底吹设备2.4 检查电极和电缆连接是否牢固,并进行接地检查2.5 调试电弧炉温度控制系统,确保温度参数正常显示3. 冶炼过程的操作3.1 按照配料计划将冶炼物料装入炉内,并按要求进行分层3.2 启动电弧,调整电弧长度和位置,使其与炉料充分接触3.3 控制冶炼底吹设备的气流和氧气进料量,保持合适的氧化还原环境3.4 定期取样,进行化验分析,根据结果调整冶炼参数3.5 监控炉内温度、电流、电压等参数,及时发现异常情况并采取措施4. 炉后处理4.1 冶炼结束后,关闭电弧和冶炼底吹设备4.2 卸料前,进行残余渣的清理和处理4.3 将炉料倾倒到预定区域,并进行冷却处理4.4 按照规定对冶炼底吹设备进行清理和保养4.5 检查电极和电缆的磨损情况,及时更换损坏部件5. 安全注意事项5.1 熟悉电弧炉设备的操作和安全规程5.2 掌握紧急停机和事故处理程序,并进行相关训练5.3 注意人身安全,佩戴防护装备,避免操作错误造成伤害5.4 遵守炉体维护和保养规范,定期检查设备运行情况5.5 发现设备异常或风险情况,及时向领导报告并采取应急措施总结:电弧炉操作规程是确保电弧炉安全运行和冶炼效果的重要保障。
- 1、下载文档前请自行甄别文档内容的完整性,平台不提供额外的编辑、内容补充、找答案等附加服务。
- 2、"仅部分预览"的文档,不可在线预览部分如存在完整性等问题,可反馈申请退款(可完整预览的文档不适用该条件!)。
- 3、如文档侵犯您的权益,请联系客服反馈,我们会尽快为您处理(人工客服工作时间:9:00-18:30)。
1.筑炉操作规程1.1大修工艺1.1.1绝热层。
砌筑时先在炉底紧贴炉壳底部铺一层10-15mm厚的石棉板,石棉板上铺一层硅藻土(厚度小于20mm),其上砌一层轻质粘土砖或粘土砖,其总厚度约80mm 左右。
1.1.2砌砖层1)平铺一层65mm左右的保温砖,砌砖需要加工好,砌至砖坡“八”字处时常出现三角缝隙,要最大限度的缩小砖缝,砌缝应≤1.5mm,砌好后需用粒度≤0.5mm的镁砂粉添缝,然后用木锤敲打使镁粉很好的渗入砖缝,最后扫去剩余镁粉。
2)砌好保温砖后,再砌一层65mm左右的镁砖,砖缝要求同上。
3)侧砌一层约115mm左右的镁砖,缝隙要求同上。
4)砌砖层相邻两层的砖缝应成45o或60o,以免砖缝重合,砌砖层必须干砌。
5)炉底砌完后,紧挨炉壳粘一层10mm左右的石棉板,再薄砌一层65mm的标准粘土砖,构成隔热层,可以湿砌。
1.1.3打结层。
1)镁砂颗粒配比为3~8mm者60%,小于或等于0.5mm者40%,打结采用平头风锤。
2)采用卤水粘结剂,卤水比重应达到1.3~1.4,使用温度为20~40o C,用量8~10%。
3)打结时压缩空气压力应大于6个大气压。
4)打结总厚度300mm左右,分层打结,第一层一般打结不大于80mm,以后各层不宜大于50mm。
5)新炉底打结前应将砖面预热到200o C左右。
6)炉底炉坡打结完后,最上层尽量平整一些,以便放平、放稳模胎,并用大小砖配合堵紧炉门,用平头风锤按每层50mm厚打结,同时衡量高度,以便于合计其后砌砖层厚度。
7)在打结炉壁的过程中,要注意出钢槽的位置,多用木质材料堵塞,以便在烤炉过程中燃烧干净而使出钢口畅通。
8)取下模胎,在打结壁上用D-4、D-6砖干砌上半炉壁,缝隙要求尽量小,砌完一层使用镁粉填充缝隙后再砌下层,相邻两层砖缝错开,共砌四层。
1.2中修工艺1.2.1炉壁厚度普遍小于100mm,局部严重损坏面积较大或炉底太薄(小于100mm)时需要中修。
1.2.2清除炉底残渣、残钢和破坏严重的砖层,温度也以保持200o C为宜,其工艺同大修打结工艺。
2.烤炉制度参考以下烘烤表格2.1清扫干净炉底,其上先铺一层焦炭碎块,然后铺上碎电极块,要求导电良好。
3.炉盖大修3.1采用水冷炉盖使用寿命长,节约了大量炉盖砖。
3.2炉盖损坏需要大修时,应先把炉盖上的镁砂及其残钢残渣剔除干净。
3.3对金属损坏部分进行焊补。
3.4焊补后的炉盖要试压,试压压力为8~10kg/cm2,确保不漏水。
3.5在炉盖下面打结一层镁砂,以减少热损失,并用楔形耐火砖砌筑好电极孔。
4.钢包技术操作规程。
4.1钢包砌筑。
4.1.1砌筑前检查钢包机械部分是否好用,正常时方能砌筑,采用粘土弧形包砖和耐火砖及耐火泥,用卤水调和湿砌。
4.1.2新砌钢包在包底铺一层8~10mm厚的石棉板,砖块要求完好无损,砖缝≤2mm 并交错砌筑,包壳和砌砖之间缝隙用耐火砖面或镁砂填充结实,座砖与包底平面接触踏实且保持一致。
4.1.3砌好的新包烘烤烤≥4小时方能使用。
4.1.4经常检查钢包使用厚度,侵蚀超过4/5时不能使用。
如有个别砖破损或侵蚀严重,可以拆除补砌。
打结钢包如有局部侵蚀严重,可以进行一次性修补,要保证钢包质量和钢包形状。
4.1.5使用时,清理干净包内和座砖残物,将调好的耐火泥抹于水口四周(耐火泥内不许有砂粒和块状物)由上向下挤压,最终上端与包底平面持平。
4.2耐火砖钢包砌筑4.2.1先打结包底,厚度与座砖持平,耐火砖粒用水玻璃混碾合适,打结风压≥5kg/cm2。
4.2.2打完包底后放正模胎并固定牢实,进行包壁打结,打结层厚度30-40mm,打结程度要求紧实不允许稀松。
4.2.3经轻微烘烤后取出模胎,大火烘烤6小时以上方可使用。
4.3钢包准备4.3.1清理钢包内外及包底的残钢和残渣。
4.3.2将包底损坏的部位用调好的耐火砖粉面打结结实。
4.3.3把准备好的塞杆上的塞头对准水口,调整执行机构,确定接触良好时开始固定。
4.3.4重复检查塞头与水口砖及执行机构是否协调一致且接触良好。
4.3.5出钢前半小时烤包,待内壁通红方可盛钢使用。
5.碱性电弧炉氧化法冶炼工艺5.1配料注:炉料按大、中、小料搭配,一般大料40%,中料45%,小料15%5.1.2配碳:炉料的平均含碳量要满足氧化期中脱碳的基本要求(平均脱碳量≥0.30%),并且脱碳速度要达到0.01%/min以上,但不能大于0.05%/min,以便于钢水中气体和夹杂物的排出。
注:新修的炉衬易使钢水吸收气体,因此氧化脱碳量应适当增加。
5.1.4补炉材料:镁砂粒度:0.3~0.8mm;镁砂粉:20/40目;卤水比重:1.3~1.4。
5.1.5铁合金(参考合金块度和烘烤温度见表4)5.1.6渣料(相关标准见表5)表5合金块度和烘烤温度表45.2补炉和装料5.2.1要加强炉体维护,出钢前准备好扒补炉工具和补炉用的材料,出钢后立即撬掉炉门坎,迅速扒除炉底、炉坡的残钢残渣。
5.2.2扒完渣后,检查炉子情况,高温下迅速补好炉门两侧,出钢口及渣线,要保证出钢口坡度和熔池形状。
补炉原则:高温、快速、薄补。
5.2.3炉壁损坏严重时,可用镁砂、镁粉、卤水混合成团状补之。
5.2.4炉底太浅(上涨)则应在装料前加入小块矿石和萤石侵蚀炉底。
5.2.5装料前应先检查炉体、炉盖、冷却系统、电器设备和机械装置是否正常。
如有故障应先排出后再装料。
5.2.6为保护炉底及早造渣,装料前应在炉底铺约料重2%左右的石灰。
5.2.7装料要合理分布,确保密实不搭桥,小料装下层,以便尽早形成熔池,大料及难熔料装在电弧高温区,最上层和四周装剩余小料。
5.3熔化期5.3.1 按照合理的供电制度使用大功率熔化,缩短熔炼时间,通电后,紧闭炉门,清理出钢槽,严堵出钢口。
时刻注意穿井、塌料等现象。
5.3.2熔池形成以后,分批加入石灰、萤石,造流动性良好的熔渣,以利于早期去磷、稳定电弧、保护钢液、加强传热,渣量为装料量的2~3%。
5.3.3炉料在熔化过程中,一般以炉门口炉料发红而炉内形成熔池开吹为宜,氧压控制在10kg/cm2左右,配合作业,必要时用铁耙将粘在炉坡上的炉料及时推入熔池。
5.3.4为了早期去磷,在熔化末期加入小批矿石,其总量根据含磷情况为装料量的1~2%。
5.3.5炉料熔化90%以上取样做初步参考分析,取样时不能在吹氧管及电极底下舀取钢水。
5.3.6根据参考样Ⅰ,如果C%不能满足要求时,必须先进行增碳,增碳多用电极碎块,电极粉及炼钢生铁。
5.4氧化期:氧化期任务是:去磷、脱碳、除气和夹杂物及升温。
5.4.1脱磷的有利条件是高碱度氧化性强和流动性良好的炉渣,较大的渣量和较低的合适温度,可部分或全部扒除熔化渣,并补造相应的新渣。
5.4.2新渣形成,脱磷量合格,温度大于1560o C(热电偶)方可进行脱碳操作,吹氧管与水平线成30o角,插入熔池深度50~150mm,吹氧压力一般为5~10 kg/cm2,可随炉中钢水沸腾强弱,火焰大小来调节氧压。
吹氧时要移动吹氧管,以利于整个熔池沸腾和脱碳去气的均匀性。
5.4.3矿石脱碳。
加矿石分批进行,加矿石速度要保证激烈沸腾不跑钢,其间如果渣子太稀立刻加石灰,最终使炉渣成泡沫状自动流出,矿石用量应根据氧化脱碳量确定,为了使每吨钢水脱碳0.01%,需要加入矿石1~1.5kg,一般速度为0.01C/min。
5.4.4氧化过程如出现镁砂渣,破坏了钢渣的流动性而不利于钢水净化应及时换渣。
5.4.5根据磨碳花,观察火焰及钢水泛花来判断终点碳,脱碳基本到达终点,沸腾减弱时,停气放渣,取样分析,静沸腾5~8分钟,加一批锰铁,将炉中锰含量调至0.2%以上,降低钢水部分氧化性,增大输入功率扒渣开始进入还原。
5.4.6扒渣应具备下列条件:a. P≤0.015%。
b. C≤规格下限0.02~0.01%。
c.温度高出出钢温度30~40 o C(热电偶)d.渣面平静,满足静沸腾要求。
5.4.7试样Ⅱ结果汇报后,迅速扒渣,扒渣要较为彻底(根据钢种需要)5.5还原期。
还原期任务:脱氧、脱硫、调整钢液成分和温度。
5.5.1扒除氧化渣后,迅速按元素规格含量加合金;加入锰铁、硅铁和稀薄渣料(渣料配比:石灰:萤石:火砖=4:1.5:0.2);其用量为钢液重量的2.0~3.0%,稀薄渣料的作用是防止钢液吸气和降温,预防钢液过分增碳或增硅。
5.5.2加大输入功率化渣5~10分钟,薄渣形成后加入第二批石灰量(约为钢液总重的4~6%)和Fe—C粉,为了经济,一般碳粉量加大(经验数值,碳粉:硅铁粉=5:2,批量<料重的0.5%),脱氧剂分批加入(硫含量偏高时,可适当加量),加入后紧闭炉门,大功率化渣强制还原。
5.5.3经10~15分钟焖烧,待渣子变白后,搅拌并酌情追加石灰量并撒粉状脱氧剂,反复操作待渣子充分变白后,搅拌取样做全分析。
5.5.4白渣下还原应保持20分钟左右,一般能使钢液增碳0.02~0.05%(合金带入的碳除外),增硅0.08~0.15%,因此需预防成分出格。
5.5.5还原期成分不足时,可以用电极粉或无锈低硫、磷生铁增碳,增碳量应尽量控制不大于0.10%,对于高碳钢,则不允许大于0.15%。
5.5.6取试样Ⅲ时,渣子流动性要良好,并先要强力充分搅拌以保证试样的参考准确性,同时要注意着手温度的调整以保证合适的出钢温度。
5.5.7调整化学成分,硅调整应在流动性良好的白渣下进行,并且要保证熔化时间。
5.5.8终脱氧。
当钢水经过充分的脱氧,为了保证钢中氧能降低到0.002~0.003%,必须进行终脱氧,常用脱氧剂主要是铝。
用铝量根据钢种不同而有所不同,(如低碳钢用铝量为0.8~1.0kg/t,高碳钢用铝量为0.4~0.6kg/t)。
5.5.9出钢。
钢水的成分、温度和熔渣的流动性必须同时满足时方可出钢,出钢一般遵循钢渣混合、大流量混出原则。
出钢要配合作业,随时调整钢包高低、左右位置,使钢水对准钢包中心,避免冲刷包壁和塞杆。
5.6浇注5.6.1浇注时钢包的注口要正对铸型的浇口杯。
5.6.2 浇注开始时钢水流量要小一些,而后逐渐增大(钢水流量视铸件大小而定),钢水上升到冒口位置时要缓流,然后继续浇到冒口需要的高度,浇注过程不允许断流。
5.6.3如发生跑火现象时,一方面采取措施,一方面细流慢注。
5.6.4遇到钢水温度较高时,可少停一会,(时间不能过长否则容易造成塞头粘连难以打开现象)或采取细流慢注。
5.6.5浇注时如发生关不严注口的现象时,钢水会不断滴漏。
滴漏的处理方法:如果轻微滴漏,可用大勺接住钢水并挪动钢包。
如果严重滴漏时,应在铸型以外缓流。
5.6.6浇注时应立即在冒口上加覆盖剂,取下浇口杯(但冒口高于浇口杯时不能立即取下浇口杯,待冷却一段时间后再取)撬掉粘在砂箱溢出冒口的钢水。