塑料件应力开裂原因分析及检测方法简述
塑料件产生应力的原因__概述及解释说明

塑料件产生应力的原因概述及解释说明1. 引言1.1 概述本文旨在深入探讨塑料件产生应力的原因及其影响,并提供解决方法和控制措施。
塑料件作为一种重要的工程材料,在各个领域得到广泛应用,但由于其特殊的物理性质,常常会受到应力的影响。
因此,了解和掌握塑料件产生应力的原因对于提高产品质量、延长使用寿命具有重要意义。
1.2 文章结构本文分为五个部分进行论述。
首先,在概述部分将简要介绍整篇文章内容以及目的。
接下来,在“塑料件产生应力的原因”部分将详细阐述塑料材料性能特点、加工过程中应力的产生机制以及外界环境因素对塑料件应力的影响。
然后,在“应力对塑料件的影响和问题”部分将探讨塑料件在受到应力作用时可能出现的变形和破裂现象,以及对产品质量和寿命所带来的影响。
接着,在“实例分析和案例研究”部分将通过具体案例描述、背景介绍以及应力分析方法和结果的讨论,说明应力问题的实际存在和解决方案的实施效果。
最后,在“结论与展望”部分将对研究结果进行总结归纳,并提出未来研究方向的建议和展望。
1.3 目的本文的目标是通过对塑料件产生应力原因的深入剖析,揭示塑料件在不同环境下受到应力影响的机制,并探讨这些应力对产品性能和寿命所带来的相关问题。
同时,本文旨在提供解决方法和控制措施,帮助读者更好地理解和应对塑料件应力问题。
通过阅读本文,读者将了解到如何通过科学合理地设计材料、优化加工过程以及改善环境条件来避免或减轻塑料件产生应力带来的负面影响,从而提高产品质量和使用寿命。
2. 塑料件产生应力的原因:2.1 塑料材料性能特点:塑料作为一种常见的工程材料,具有许多独特的性能特点,如轻质、耐腐蚀、绝缘性等。
然而,塑料也存在着一些局限性,其中之一就是容易受到应力的影响。
首先,塑料具有较高的流动性。
在加工过程中,由于温度和压力的变化,塑料会发生熔化和流动,并且在冷却过程中形成所需形状。
这个过程中,由于内部分子链间摩擦、碰撞与拉伸等相互作用影响,在形成过程中产生应力。
塑料应力开裂机理
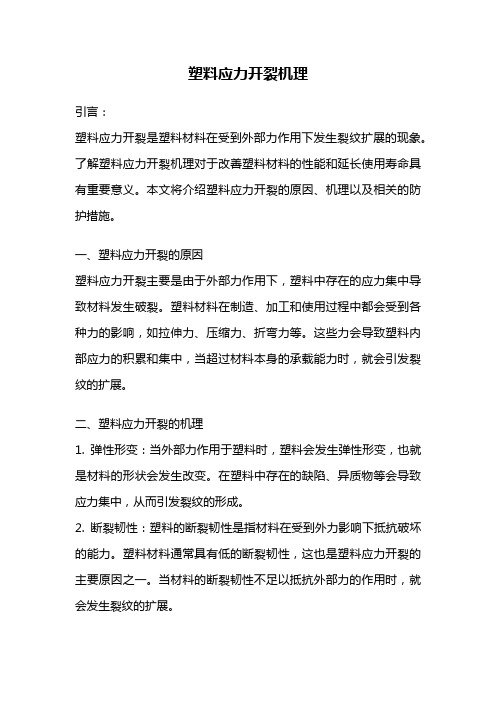
塑料应力开裂机理引言:塑料应力开裂是塑料材料在受到外部力作用下发生裂纹扩展的现象。
了解塑料应力开裂机理对于改善塑料材料的性能和延长使用寿命具有重要意义。
本文将介绍塑料应力开裂的原因、机理以及相关的防护措施。
一、塑料应力开裂的原因塑料应力开裂主要是由于外部力作用下,塑料中存在的应力集中导致材料发生破裂。
塑料材料在制造、加工和使用过程中都会受到各种力的影响,如拉伸力、压缩力、折弯力等。
这些力会导致塑料内部应力的积累和集中,当超过材料本身的承载能力时,就会引发裂纹的扩展。
二、塑料应力开裂的机理1. 弹性形变:当外部力作用于塑料时,塑料会发生弹性形变,也就是材料的形状会发生改变。
在塑料中存在的缺陷、异质物等会导致应力集中,从而引发裂纹的形成。
2. 断裂韧性:塑料的断裂韧性是指材料在受到外力影响下抵抗破坏的能力。
塑料材料通常具有低的断裂韧性,这也是塑料应力开裂的主要原因之一。
当材料的断裂韧性不足以抵抗外部力的作用时,就会发生裂纹的扩展。
3. 热应力:塑料材料在制造和使用过程中受到温度的影响,温度变化会引起材料的热胀冷缩,从而产生热应力。
热应力会使塑料材料发生变形和应力集中,增加裂纹的形成和扩展的可能性。
三、塑料应力开裂的防护措施1. 选择合适的材料:不同的塑料材料具有不同的性能和应用范围,在选择材料时应根据具体的使用条件和外部力的作用选择合适的材料,以提高塑料的抗裂性能。
2. 控制加工条件:在塑料制品的生产过程中,控制加工条件对于减少塑料应力开裂具有重要意义。
合理控制加工温度、速度和压力,避免过大的应力集中,减少材料的应力开裂风险。
3. 增加塑料的韧性:通过添加改性剂、增强剂等,可以有效提高塑料材料的韧性,增加其抗裂性能。
同时,适当调整材料的配方和加工工艺,以提高材料的韧性和耐热性。
4. 设计合理的结构:在塑料制品的设计过程中,合理的结构设计可以减少应力集中,避免裂纹的形成和扩展。
通过改变结构的形状和尺寸,减少应力集中点,提高塑料制品的抗裂性能。
【解决】pc塑胶原料龟裂解决方案

【关键字】解决pc塑胶原料龟裂解决方案篇一:常见塑料制品开裂的原因浅析及检测方法简述常见塑料制品开裂的原因浅析及检测方法简述引言工程塑料因为其优异的特性——高强度、耐热、耐冲击、抗老化等而被广泛应用于工业零件及各种外壳制造上。
但在制造或使用过程中,塑料制品很有可能被钉螺丝或涂胶水,这样的处理常常会诱发塑料制品的应力开裂,致使次品率很高。
而开裂是塑料制品经常出现的致命缺陷,包括制作表面丝状裂纹、微裂、顶白、开裂及因制件粘模、流道粘模而造成的创伤。
引起开裂的原因涉及模具、成型工艺、塑料材料、环境应力等方面。
开裂原因浅析及改进建议不同的开裂原因会导致不同的开裂类型,如果按照开裂的时间分类,塑料制品开裂现象通常有两种情况:(一)脱模开裂,塑料制品从模具脱出或在机器加工过程中出现开裂,这种开裂原因和后果比较容易预估;(二)应用开裂,塑料制品在放置一段时间后或使用过程中出现开裂,这种开裂往往难以预测,且产生的后果可能是毁灭性的。
以下主要从塑料材料的选择和环境应力的角度出发,结合以上两种开裂类型简单阐述开裂原因及改进建议。
1. 材料类型所致开裂的原因分析及改进建议下面通过两个案例,从选材背景及加工后出现的问题来分析材料选择对产品开裂可能造成的影响。
圆孔性连接器(代表成型中空制品)一直以来,客户在生产成型小型圆孔时,选择的都是聚苯硫醚PPS GF30/GF40这种材料,器件没有出现任何开裂现象。
在开发大圆孔径系列连接器时,客户再次选用全球多家知名厂家的PPS GF30/GF40材料。
加工的结果是制品开裂非常严重,有些属于脱模开裂,有些属于应用开裂,而且不同厂家同类型含量的PPS均存在制品开裂问题。
客户和材料厂商起初怀疑是塑料冲击强度不够,但同时发现冲击强度比PPS GF30/GF40低的PA6和PC材料却反而不开裂。
在选用一些知名厂家提供的高抗冲击性PPS GF40材料后,开裂问题依然存在(图1)。
根据客户提供的信息,我们分析,很可能是由于成型塑料圆孔的模具型芯采用的是硬质合金材料。
塑料件应力开裂原因分析及检测方法简述
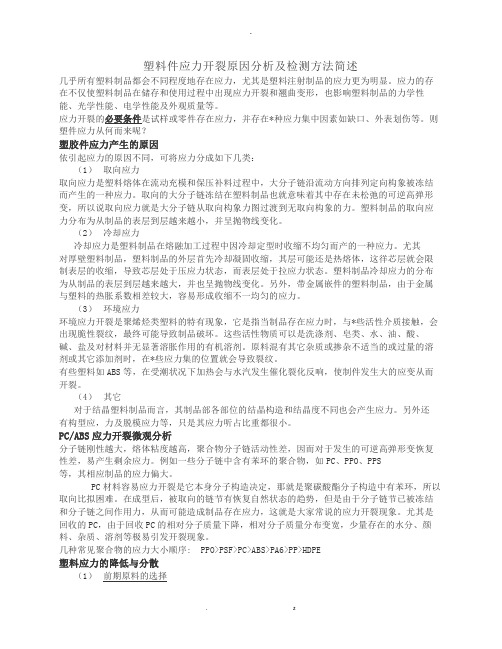
塑料件应力开裂原因分析及检测方法简述几乎所有塑料制品都会不同程度地存在应力,尤其是塑料注射制品的应力更为明显。
应力的存在不仅使塑料制品在储存和使用过程中出现应力开裂和翘曲变形,也影响塑料制品的力学性能、光学性能、电学性能及外观质量等。
应力开裂的必要条件是试样或零件存在应力,并存在*种应力集中因素如缺口、外表划伤等。
则塑件应力从何而来呢?塑胶件应力产生的原因依引起应力的原因不同,可将应力分成如下几类:(1)取向应力取向应力是塑料熔体在流动充模和保压补料过程中,大分子链沿流动方向排列定向构象被冻结而产生的一种应力。
取向的大分子链冻结在塑料制品也就意味着其中存在未松弛的可逆高弹形变,所以说取向应力就是大分子链从取向构象力图过渡到无取向构象的力。
塑料制品的取向应力分布为从制品的表层到层越来越小,并呈抛物线变化。
(2)冷却应力冷却应力是塑料制品在熔融加工过程中因冷却定型时收缩不均匀而产的一种应力。
尤其对厚壁塑料制品,塑料制品的外层首先冷却凝固收缩,其层可能还是热熔体,这徉芯层就会限制表层的收缩,导致芯层处于压应力状态,而表层处于拉应力状态。
塑料制品冷却应力的分布为从制品的表层到层越来越大,并也呈抛物线变化。
另外,带金属嵌件的塑料制品,由于金属与塑料的热胀系数相差较大,容易形成收缩不一均匀的应力。
(3)环境应力环境应力开裂是聚烯烃类塑料的特有现象,它是指当制品存在应力时,与*些活性介质接触,会出现脆性裂纹,最终可能导致制品破坏。
这些活性物质可以是洗涤剂、皂类、水、油、酸、碱、盐及对材料并无显著溶胀作用的有机溶剂。
原料混有其它杂质或掺杂不适当的或过量的溶剂或其它添加剂时,在*些应力集的位置就会导致裂纹。
有些塑料如ABS等,在受潮状况下加热会与水汽发生催化裂化反响,使制件发生大的应变从而开裂。
(4)其它对于结晶塑料制品而言,其制品部各部位的结晶构造和结晶度不同也会产生应力。
另外还有构型应,力及脱模应力等,只是其应力听占比重都很小。
常见塑料制品开裂的原因浅析及检测方法简述

常见塑料制品开裂的原因浅析及检测方法简述引言工程塑料因为其优异的特性——高强度、耐热、耐冲击、抗老化等而被广泛应用于工业零件及各种外壳制造上。
但在制造或使用过程中,塑料制品很有可能被钉螺丝或涂胶水,这样的处理常常会诱发塑料制品的应力开裂,致使次品率很高。
而开裂是塑料制品经常出现的致命缺陷,包括制作表面丝状裂纹、微裂、顶白、开裂及因制件粘模、流道粘模而造成的创伤。
引起开裂的原因涉及模具、成型工艺、塑料材料、环境应力等方面.开裂原因浅析及改进建议不同的开裂原因会导致不同的开裂类型,如果按照开裂的时间分类,塑料制品开裂现象通常有两种情况:(一)脱模开裂,塑料制品从模具脱出或在机器加工过程中出现开裂,这种开裂原因和后果比较容易预估;(二)应用开裂,塑料制品在放置一段时间后或使用过程中出现开裂,这种开裂往往难以预测,且产生的后果可能是毁灭性的。
以下主要从塑料材料的选择和环境应力的角度出发,结合以上两种开裂类型简单阐述开裂原因及改进建议。
1。
材料类型所致开裂的原因分析及改进建议下面通过两个案例,从选材背景及加工后出现的问题来分析材料选择对产品开裂可能造成的影响。
1。
1圆孔性连接器(代表成型中空制品)一直以来,客户在生产成型小型圆孔时,选择的都是聚苯硫醚PPS GF30/GF40这种材料,器件没有出现任何开裂现象.在开发大圆孔径系列连接器时,客户再次选用全球多家知名厂家的PPS GF30/GF40材料。
加工的结果是制品开裂非常严重,有些属于脱模开裂,有些属于应用开裂,而且不同厂家同类型含量的PPS均存在制品开裂问题。
客户和材料厂商起初怀疑是塑料冲击强度不够,但同时发现冲击强度比PPS GF30/GF40低的PA6和PC材料却反而不开裂。
在选用一些知名厂家提供的高抗冲击性PPS GF40材料后,开裂问题依然存在(图1)。
根据客户提供的信息,我们分析,很可能是由于成型塑料圆孔的模具型芯采用的是硬质合金材料。
金属材料导热和散热能力较强,而一般塑料材料散热能力较弱,金属材料和塑料挤出时不可避免会产生收缩相差较大的情况,塑料产品不同部位温度也有较大差别,对于延展性不好(断裂伸长率偏小)的塑料,无疑会发生断裂的现象。
塑料件应力开裂原因分析及检测方法简述

塑料件应力开裂原因分析及检测方法简述1.材料本身的问题:塑料材料选择不当、材料质量不过关或添加剂使用不当等都可能导致塑料件的应力开裂。
例如,在高温环境下,一些塑料材料会发生老化或失去强度,容易出现应力开裂。
2.设计不合理:塑料件的设计不合理也是应力开裂的常见原因之一、例如,墙厚过薄、变截面和过小的毛胚等都可能导致塑料件的应力集中,进而导致开裂。
3.加工工艺问题:塑料件在加工过程中如果没有采取适当的工艺措施,例如注塑温度过高、注塑压力过大、注塑速度过快等都可能导致应力集中和应力开裂。
1.观察外观:通过目测可以检测到塑料件的开裂情况。
开裂通常是由于应力集中导致的,因此在塑料件表面或边缘会出现明显的裂纹。
2.断面观察:将塑料件进行切割,观察其断面的结构和裂纹情况。
这种方法可以更直观地了解塑料件的应力分布情况,从而确定是否存在应力开裂。
3.拉伸试验:通过进行拉伸试验,可以测试塑料件的断裂强度和断裂伸长率。
如果塑料件的强度较低或伸长率较小,说明存在应力开裂的风险。
4.光散射检测:利用光散射原理,通过照射塑料件表面,观察光的散射情况来判断塑料件的应力状态。
应力集中的区域通常会散射更多的光。
5.应力测量:通过应力分析仪等设备对塑料件进行应力测试。
可以直接测量塑料件内部的应力分布,从而判断是否存在应力开裂的潜在风险。
总之,塑料件应力开裂的原因和检测方法多种多样,需要综合考虑材料、设计、加工和使用等方面的因素。
合理选择材料、优化设计、控制加工工艺以及进行适当的检测,可以降低应力开裂的风险,提高塑料件的使用寿命和可靠性。
常见塑料制品开裂的原因浅析及检测方法简述
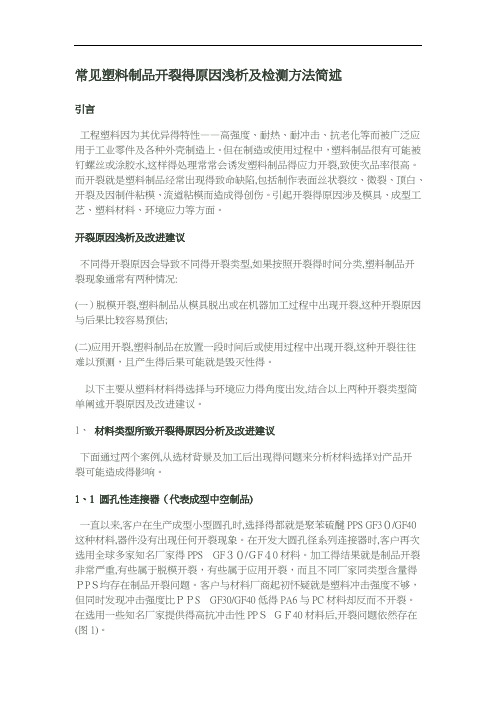
常见塑料制品开裂得原因浅析及检测方法简述引言工程塑料因为其优异得特性——高强度、耐热、耐冲击、抗老化等而被广泛应用于工业零件及各种外壳制造上。
但在制造或使用过程中,塑料制品很有可能被钉螺丝或涂胶水,这样得处理常常会诱发塑料制品得应力开裂,致使次品率很高。
而开裂就是塑料制品经常出现得致命缺陷,包括制作表面丝状裂纹、微裂、顶白、开裂及因制件粘模、流道粘模而造成得创伤。
引起开裂得原因涉及模具、成型工艺、塑料材料、环境应力等方面。
开裂原因浅析及改进建议不同得开裂原因会导致不同得开裂类型,如果按照开裂得时间分类,塑料制品开裂现象通常有两种情况:(一)脱模开裂,塑料制品从模具脱出或在机器加工过程中出现开裂,这种开裂原因与后果比较容易预估;(二)应用开裂,塑料制品在放置一段时间后或使用过程中出现开裂,这种开裂往往难以预测,且产生得后果可能就是毁灭性得。
以下主要从塑料材料得选择与环境应力得角度出发,结合以上两种开裂类型简单阐述开裂原因及改进建议。
1、材料类型所致开裂得原因分析及改进建议下面通过两个案例,从选材背景及加工后出现得问题来分析材料选择对产品开裂可能造成得影响。
1、1圆孔性连接器(代表成型中空制品)一直以来,客户在生产成型小型圆孔时,选择得都就是聚苯硫醚PPS GF30/GF40这种材料,器件没有出现任何开裂现象。
在开发大圆孔径系列连接器时,客户再次选用全球多家知名厂家得PPS GF30/GF40材料。
加工得结果就是制品开裂非常严重,有些属于脱模开裂,有些属于应用开裂,而且不同厂家同类型含量得PPS均存在制品开裂问题。
客户与材料厂商起初怀疑就是塑料冲击强度不够,但同时发现冲击强度比PPS GF30/GF40低得PA6与PC材料却反而不开裂。
在选用一些知名厂家提供得高抗冲击性PPSGF40材料后,开裂问题依然存在(图1)。
根据客户提供得信息,我们分析,很可能就是由于成型塑料圆孔得模具型芯采用得就是硬质合金材料。
塑料件应力开裂原因分析及检测方法简述

塑料件应力开裂原因分析及检测方法简述几乎所有塑料制品都会不同程度地存在内应力,尤其就是塑料注射制品得内应力更为明显。
内应力得存在不仅使塑料制品在储存与使用过程中出现应力开裂与翘曲变形,也影响塑料制品得力学性能、光学性能、电学性能及外观质量等。
应力开裂得必要条件就是试样或零件内存在应力,并存在某种应力集中因素如缺口、表面划伤等。
那么塑件应力从何而来呢?塑胶件内应力产生得原因依引起内应力得原因不同,可将内应力分成如下几类:(1)取向内应力取向内应力就是塑料熔体在流动充模与保压补料过程中,大分子链沿流动方向排列定向构象被冻结而产生得一种内应力.取向得大分子链冻结在塑料制品内也就意味着其中存在未松弛得可逆高弹形变,所以说取向应力就就是大分子链从取向构象力图过渡到无取向构象得内力.塑料制品得取向内应力分布为从制品得表层到内层越来越小,并呈抛物线变化.(2)冷却内应力冷却内应力就是塑料制品在熔融加工过程中因冷却定型时收缩不均匀而产得一种内应力。
尤其对厚壁塑料制品,塑料制品得外层首先冷却凝固收缩,其内层可能还就是热熔体,这徉芯层就会限制表层得收缩,导致芯层处于压应力状态,而表层处于拉应力状态。
塑料制品冷却内应力得分布为从制品得表层到内层越来越大,并也呈抛物线变化.另外,带金属嵌件得塑料制品,由于金属与塑料得热胀系数相差较大,容易形成收缩不一均匀得内应力。
(3)环境应力环境应力开裂就是聚烯烃类塑料得特有现象,它就是指当制品存在应力时,与某些活性介质接触,会出现脆性裂纹,最终可能导致制品破坏.这些活性物质可以就是洗涤剂、皂类、水、油、酸、碱、盐及对材料并无显著溶胀作用得有机溶剂。
原料混有其它杂质或掺杂不适当得或过量得溶剂或其它添加剂时,在某些应力集得位置就会导致裂纹。
有些塑料如ABS等,在受潮状况下加热会与水汽发生催化裂化反应,使制件发生大得应变从而开裂。
(4)其它对于结晶塑料制品而言,其制品部各部位得结晶结构与结晶度不同也会产生内应力。
塑料件应力开裂原因分析及检测方法简述

塑料件应力开裂原因分析及检测方法简述文稿归稿存档编号:[KKUY-KKIO69-OTM243-OLUI129-G00I-FDQS58-塑料件应力开裂原因分析及检测方法简述几乎所有塑料制品都会不同程度地存在内应力,尤其是塑料注射制品的内应力更为明显。
内应力的存在不仅使塑料制品在储存和使用过程中出现应力开裂和翘曲变形,也影响塑料制品的力学性能、光学性能、电学性能及外观质量等。
应力开裂的必要条件是试样或零件内存在应力,并存在某种应力集中因素如缺口、表面划伤等。
那么塑件应力从何而来呢?塑胶件内应力产生的原因依引起内应力的原因不同,可将内应力分成如下几类:(1)取向内应力取向内应力是塑料熔体在流动充模和保压补料过程中,大分子链沿流动方向排列定向构象被冻结而产生的一种内应力。
取向的大分子链冻结在塑料制品内也就意味着其中存在未松弛的可逆高弹形变,所以说取向应力就是大分子链从取向构象力图过渡到无取向构象的内力。
塑料制品的取向内应力分布为从制品的表层到内层越来越小,并呈抛物线变化。
(2)冷却内应力冷却内应力是塑料制品在熔融加工过程中因冷却定型时收缩不均匀而产的一种内应力。
尤其对厚壁塑料制品,塑料制品的外层首先冷却凝固收缩,其内层可能还是热熔体,这徉芯层就会限制表层的收缩,导致芯层处于压应力状态,而表层处于拉应力状态。
塑料制品冷却内应力的分布为从制品的表层到内层越来越大,并也呈抛物线变化。
另外,带金属嵌件的塑料制品,由于金属与塑料的热胀系数相差较大,容易形成收缩不一均匀的内应力。
(3)环境应力环境应力开裂是聚烯烃类塑料的特有现象,它是指当制品存在应力时,与某些活性介质接触,会出现脆性裂纹,最终可能导致制品破坏。
这些活性物质可以是洗涤剂、皂类、水、油、酸、碱、盐及对材料并无显着溶胀作用的有机溶剂。
原料混有其它杂质或掺杂不适当的或过量的溶剂或其它添加剂时,在某些应力集的位置就会导致裂纹。
有些塑料如ABS等,在受潮状况下加热会与水汽发生催化裂化反应,使制件发生大的应变从而开裂。
塑料件应力开裂原因分析及检测方法简述

塑料件应力开裂原因分析及检测方法简述几乎所有塑料制品都会不同程度地存在内应力,尤其就是塑料注射制品的内应力更为明显。
内应力的存在不仅使塑料制品在储存与使用过程中出现应力开裂与翘曲变形,也影响塑料制品的力学性能、光学性能、电学性能及外观质量等。
应力开裂的必要条件就是试样或零件内存在应力,并存在某种应力集中因素如缺口、表面划伤等。
那么塑件应力从何而来呢?塑胶件内应力产生的原因依引起内应力的原因不同,可将内应力分成如下几类:(1)取向内应力取向内应力就是塑料熔体在流动充模与保压补料过程中,大分子链沿流动方向排列定向构象被冻结而产生的一种内应力。
取向的大分子链冻结在塑料制品内也就意味着其中存在未松弛的可逆高弹形变,所以说取向应力就就是大分子链从取向构象力图过渡到无取向构象的内力。
塑料制品的取向内应力分布为从制品的表层到内层越来越小,并呈抛物线变化。
(2)冷却内应力冷却内应力就是塑料制品在熔融加工过程中因冷却定型时收缩不均匀而产的一种内应力。
尤其对厚壁塑料制品,塑料制品的外层首先冷却凝固收缩,其内层可能还就是热熔体,这徉芯层就会限制表层的收缩,导致芯层处于压应力状态,而表层处于拉应力状态。
塑料制品冷却内应力的分布为从制品的表层到内层越来越大,并也呈抛物线变化。
另外,带金属嵌件的塑料制品,由于金属与塑料的热胀系数相差较大,容易形成收缩不一均匀的内应力。
(3)环境应力环境应力开裂就是聚烯烃类塑料的特有现象,它就是指当制品存在应力时,与某些活性介质接触,会出现脆性裂纹,最终可能导致制品破坏。
这些活性物质可以就是洗涤剂、皂类、水、油、酸、碱、盐及对材料并无显著溶胀作用的有机溶剂。
原料混有其它杂质或掺杂不适当的或过量的溶剂或其它添加剂时,在某些应力集的位置就会导致裂纹。
有些塑料如ABS等,在受潮状况下加热会与水汽发生催化裂化反应,使制件发生大的应变从而开裂。
(4)其它对于结晶塑料制品而言,其制品部各部位的结晶结构与结晶度不同也会产生内应力。
塑件开裂原因及内应力分析

塑件开裂原因分析1引言开裂,包括制件表面丝状裂纹、微裂、顶白、开裂及因制件粘模、流道粘模而造成或创伤危机,按开裂时间分脱模开裂和应用开裂。
注塑制品一个普遍存在的缺点是有内应力,内应力的存在不仅是制件在储存和使用中出现翘曲变形和开裂的重要原因。
主要有以下几个方面的原因造成:1.加工方面:(1)加工压力过大、速度过快、充料愈多、注射、保压时间过长,都会造成内应力过大而开裂。
大力神云石胶(2)调节开模速度与压力防止快速强拉制件造成脱模开裂。
(3)适当调高模具温度,使制件易于脱模,适当调低料温防止分解。
(4)预防由于熔接痕,塑料降解造成机械强度变低而出现开裂。
(5)适当使用脱模剂,注意经常消除模面附着的气雾等物质。
(6)制件残余应力,可通过在成型后立即进行退火热处理来消除内应力而减少裂纹的生成。
2.模具方面:(1)顶出要平衡,如顶杆数量、截面积要足够,脱模斜度要足够,型腔面要有足够光滑,这样才防止由于外力导致顶出残余应力集中而开裂。
(2)制件结构不能太薄,过渡部份应尽量采用圆弧过渡,避免尖角、倒角造成应力集中。
(3)尽量少用金属嵌件,以防止嵌件与制件收缩率不同造成内应力加大。
(4)对深底制件应设置适当的脱模进气孔道,防止形成真空负压。
(5)主流道足够大使浇口料未来得及固化时脱模,这样易于脱模。
(6)主流道衬套与喷嘴接合应当防止冷硬料的拖拉而使制件粘在定模上。
3.材料方面:(1)再生料含量太高,造成制件强度过低。
(2)湿度过大,造成一些塑料与水汽发生化学反应,降低强度而出现顶出开裂。
(3)材料本身不适宜正在加工的环境或质量欠佳,受到污染都会造成开裂。
4.机台方面:注塑机塑化容量要适当,过小塑化不充分未能完全混合而变脆,过大时会降解。
塑件内应力分析2内应力的种类高分子材料在成型过程中形成的不平衡构象,在成型之后不能立即恢复到与环境条件相适应的平衡构象,是注塑制品存在内应力的主要原因。
另外,外力使制件产生强迫高弹形变也会在其中形成内应力。
塑料件应力开裂原因分析及检测方法简述
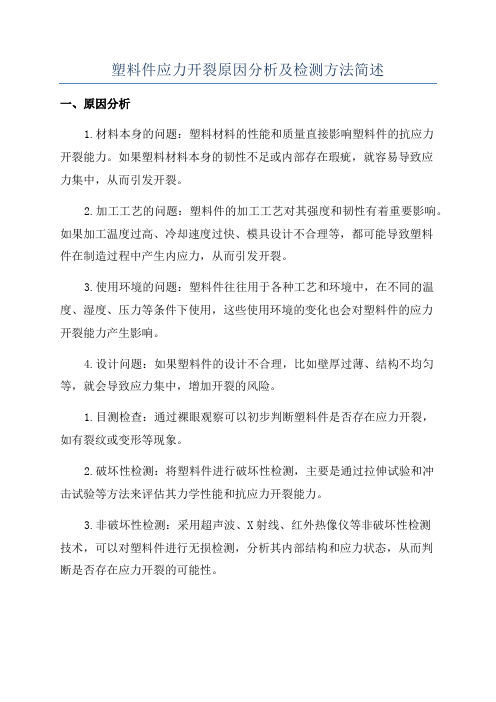
塑料件应力开裂原因分析及检测方法简述一、原因分析1.材料本身的问题:塑料材料的性能和质量直接影响塑料件的抗应力开裂能力。
如果塑料材料本身的韧性不足或内部存在瑕疵,就容易导致应力集中,从而引发开裂。
2.加工工艺的问题:塑料件的加工工艺对其强度和韧性有着重要影响。
如果加工温度过高、冷却速度过快、模具设计不合理等,都可能导致塑料件在制造过程中产生内应力,从而引发开裂。
3.使用环境的问题:塑料件往往用于各种工艺和环境中,在不同的温度、湿度、压力等条件下使用,这些使用环境的变化也会对塑料件的应力开裂能力产生影响。
4.设计问题:如果塑料件的设计不合理,比如壁厚过薄、结构不均匀等,就会导致应力集中,增加开裂的风险。
1.目测检查:通过裸眼观察可以初步判断塑料件是否存在应力开裂,如有裂纹或变形等现象。
2.破坏性检测:将塑料件进行破坏性检测,主要是通过拉伸试验和冲击试验等方法来评估其力学性能和抗应力开裂能力。
3.非破坏性检测:采用超声波、X射线、红外热像仪等非破坏性检测技术,可以对塑料件进行无损检测,分析其内部结构和应力状态,从而判断是否存在应力开裂的可能性。
4.应力测试:利用应力测试仪器对塑料件进行应力测试,可以定量分析其应力分布情况,判断是否存在应力集中现象,进而评估其抗应力开裂能力。
总之,塑料件应力开裂是一个复杂的问题,其原因可能涉及多个方面。
为了解决这个问题,需要从材料、加工工艺、使用环境以及设计等方面进行综合考虑。
同时,采用合适的检测方法对塑料件进行检测,可以帮助我们及时发现和解决应力开裂问题,提高塑料件的使用寿命和安全性。
实用文库汇编之塑料件应力开裂原因分析及检测方法简述

*作者:座殿角*作品编号48877446331144215458创作日期:2020年12月20日实用文库汇编之塑料件应力开裂原因分析及检测方法简述几乎所有塑料制品都会不同程度地存在内应力,尤其是塑料注射制品的内应力更为明显。
内应力的存在不仅使塑料制品在储存和使用过程中出现应力开裂和翘曲变形,也影响塑料制品的力学性能、光学性能、电学性能及外观质量等。
应力开裂的必要条件是试样或零件内存在应力,并存在某种应力集中因素如缺口、表面划伤等。
那么塑件应力从何而来呢?塑胶件内应力产生的原因依引起内应力的原因不同,可将内应力分成如下几类:(1)取向内应力取向内应力是塑料熔体在流动充模和保压补料过程中,大分子链沿流动方向排列定向构象被冻结而产生的一种内应力。
取向的大分子链冻结在塑料制品内也就意味着其中存在未松弛的可逆高弹形变,所以说取向应力就是大分子链从取向构象力图过渡到无取向构象的内力。
塑料制品的取向内应力分布为从制品的表层到内层越来越小,并呈抛物线变化。
(2)冷却内应力冷却内应力是塑料制品在熔融加工过程中因冷却定型时收缩不均匀而产的一种内应力。
尤其对厚壁塑料制品,塑料制品的外层首先冷却凝固收缩,其内层可能还是热熔体,这徉芯层就会限制表层的收缩,导致芯层处于压应力状态,而表层处于拉应力状态。
塑料制品冷却内应力的分布为从制品的表层到内层越来越大,并也呈抛物线变化。
另外,带金属嵌件的塑料制品,由于金属与塑料的热胀系数相差较大,容易形成收缩不一均匀的内应力。
(3)环境应力环境应力开裂是聚烯烃类塑料的特有现象,它是指当制品存在应力时,与某些活性介质接触,会出现脆性裂纹,最终可能导致制品破坏。
这些活性物质可以是洗涤剂、皂类、水、油、酸、碱、盐及对材料并无显著溶胀作用的有机溶剂。
原料混有其它杂质或掺杂不适当的或过量的溶剂或其它添加剂时,在某些应力集的位置就会导致裂纹。
有些塑料如ABS等,在受潮状况下加热会与水汽发生催化裂化反应,使制件发生大的应变从而开裂。
常见塑料制品开裂的原因浅析及检测方法简述

罕见塑料制品开裂的原因浅析及检测方法简述之蔡仲巾千创作引言工程塑料因为其优异的特性——高强度、耐热、耐冲击、抗老化等而被广泛应用于工业零件及各种外壳制造上.但在制造或使用过程中, 塑料制品很有可能被钉螺丝或涂胶水, 这样的处置经常会诱发塑料制品的应力开裂, 致使次品率很高.而开裂是塑料制品经常呈现的致命缺陷, 包括制作概况丝状裂纹、微裂、顶白、开裂及因制件粘模、流道粘模而造成的创伤.引起开裂的原因涉及模具、成型工艺、塑料资料、环境应力等方面.开裂原因浅析及改进建议分歧的开裂原因会招致分歧的开裂类型, 如果依照开裂的时间分类, 塑料制品开裂现象通常有两种情况:(一)脱模开裂, 塑料制品从模具脱出或在机器加工过程中呈现开裂, 这种开裂原因和后果比力容易预估;(二)应用开裂, 塑料制品在放置一段时间后或使用过程中呈现开裂, 这种开裂往往难以预测, 且发生的后果可能是毁灭性的.以下主要从塑料资料的选择和环境应力的角度动身, 结合以上两种开裂类型简单论述开裂原因及改进建议.1. 资料类型所致开裂的原因分析及改进建议下面通过两个案例, 从选材布景及加工后呈现的问题来分析资料选择对产物开裂可能造成的影响.1.1圆孔性连接器(代表成型中空制品)一直以来, 客户在生产成型小型圆孔时, 选择的都是聚苯硫醚PPS GF30/GF40这种资料, 器件没有呈现任何开裂现象.在开发年夜圆孔径系列连接器时, 客户再次选用全球多家知名厂家的PPS GF30/GF40资料.加工的结果是制品开裂非常严重, 有些属于脱模开裂, 有些属于应用开裂, 而且分歧厂家同类型含量的PPS 均存在制品开裂问题.客户和资料厂商起初怀疑是塑料冲击强度不够, 但同时发现冲击强度比PPS GF30/GF40低的PA6和PC资料却反而不开裂.在选用一些知名厂家提供的高抗冲击性PPS GF40资料后, 开裂问题依然存在(图1).根据客户提供的信息, 我们分析, 很可能是由于成型塑料圆孔的模具型芯采纳的是硬质合金资料.金属资料导热和散热能力较强, 而一般塑料资料散热能力较弱, 金属资料和塑料挤出时不成防止会发生收缩相差较年夜的情况, 塑料产物分歧部位温度也有较年夜分歧, 对延展性欠好(断裂伸长率偏小)的塑料, 无疑会发生断裂的现象.图11.2中空管材制品(代表塑料型材机加工)某客户考虑到要提高产物强度, 将此前使用的PEEK的资料改为PEEK GF30和PPS GF40, 由于产物呈中空长管状(壁厚5mm),于是使用PEEK GF30和PPS GF40棒材(Φ95)进行机加工.加工的结果是制品有个别开裂现象, 基本属于应用开裂.呈现断裂处是壁厚到壁薄的过渡处.但选用纯的PEEK 、PP、 PC 、PEI等棒材加工则没有呈现开裂.(图2)根据以上信息, 我们初步推测塑料切屑处易局部升温(塑料传热慢), 从而招致更多残余应力;同时产物管径较年夜, 塑料具有后收缩不均衡的特点.图2综合以上两个案例可以看出, 在产物选材方面, 应该充沛考虑塑料资料的成型方式、部件结构、传热方式等实际工艺把持问题;对一些中空结构, 应该充沛考虑壁厚、中空尺寸太小等, 如壁薄、空芯年夜的部件应该尽量选用延展性好(断裂伸长率年夜)、传热性好的塑料, 而选用塑料棒材加工成管材时则要充沛考虑塑料热平衡问题, 尽可能选择延展性好的塑料棒材, 对一些延展性欠好的塑料管材, 尽可能防止选用棒材加工成管材(一般出厂管材已进行残余应力热处置).对一些延展性欠好的塑料, 采纳塑料管材和塑料棒材的效果是纷歧样的.2.环境应力所致开裂的原因分析及改进建议原料为GP-22型ABS+高浓度黑色母粒的塑料件从模具中拿出时完好无缺, 空气中放置2到3天后, 部份零件中铜嵌件周围呈现垂直裂纹, 有的甚至已完全裂开.因为塑料件在成型过程中未呈现任何问题, 说明问题不在于成型设备及工艺, 经初步分析确认, 问题主要由环境应力开裂引起, 引起环境应力开裂的原因可能有以下几个方面.(1)原料混有其它杂质或搀杂不适当的或过量的溶剂或其它添加剂.环境应力开裂是聚烯烃类塑料的特有现象, 它是指当制品存在应力时, 与某些活性介质接触, 会呈现脆性裂纹, 最终可能招致制品破坏.这些活性物质可以是洗涤剂、皂类、水、油、酸、碱、盐及对资料并没有显著溶胀作用的有机溶剂.环境应力开裂的需要条件是试样或零件内存在应力, 并存在某种应力集中因素如缺口、概况划伤等.而ABS里含有聚烯烃成份, 且原料里含的杂质或溶剂间接提供了这些活性物质, 当ABS塑料件在贮存的过程中由于种种偶然因素致概况呈现缺口或划伤时, 就会招致裂纹.(2)有些塑料如ABS等, 在受潮状况下加热会与水汽发生催化裂化反应, 使制件发生年夜的应变从而开裂.(3)塑料在机筒内加热时间太长, 也会促使制件脆裂.像聚苯乙烯及含有此成份的塑料应尽量少用金属嵌件, 因为这些塑料脆性的冷热比容年夜.如果为了装配和强度的要求必需加入嵌件, 比如嵌件由金属铜制成, 而金属铜嵌件冷却时尺寸变动与塑料ABS的热收缩值相差很年夜, 致使嵌件周围发生较年夜的内应力, 于是造成了制品的开裂.具体改进办法如下:(1)更换嵌件所用资料, 使嵌件与ABS制品线膨胀系数应尽可能接近;(2)加年夜嵌件各尖角部位的圆角, 圆角太小可能引起产物应力集中, 招致产物开裂;(3)加年夜嵌件周围塑料层的厚度.在带有嵌件的塑料制品中, 嵌件的周围易呈现裂纹或招致制品强度下降, 这是由金属嵌件与塑料的热性能和收缩率分歧较年夜引起.因此, 在设计制件时, 应加年夜嵌件周围的壁厚, 借以克服这种困难, 成型前对金属嵌件进行预热也是一项有效办法.因为预热后可减少熔料与嵌件的温度差, 在成型中可以使嵌件周围的熔料冷却较慢, 收缩比力均匀, 发生一定的热料补缩作用, 可防止嵌件周围发生过年夜的内应力.由于塑料在料筒内塑化不均匀或在模腔内冷却速度分歧, 因此常会发生不均的结晶、定向和收缩, 致使制品存有内应力, 这在生产厚壁或带金属嵌件的制品时更为突出.存有内应力的制件在贮存和使用中常会呈现力学性能下降, 光学性能变坏, 概况有银纹, 甚至变形开裂.生产中解决这些问题的法子是对制件进行退火处置.高分子资料测试在衡量塑料等高分子资料的性能方面, 通常进行的测试项目有:。
塑件开裂原因及内应力分析

塑件开裂原因及内应⼒分析塑件开裂原因分析1引⾔开裂,包括制件表⾯丝状裂纹、微裂、顶⽩、开裂及因制件粘模、流道粘模⽽造成或创伤危机,按开裂时间分脱模开裂和应⽤开裂。
注塑制品⼀个普遍存在的缺点是有内应⼒,内应⼒的存在不仅是制件在储存和使⽤中出现翘曲变形和开裂的重要原因。
主要有以下⼏个⽅⾯的原因造成:1.加⼯⽅⾯:(1)加⼯压⼒过⼤、速度过快、充料愈多、注射、保压时间过长,都会造成内应⼒过⼤⽽开裂。
⼤⼒神云⽯胶(2)调节开模速度与压⼒防⽌快速强拉制件造成脱模开裂。
(3)适当调⾼模具温度,使制件易于脱模,适当调低料温防⽌分解。
(4)预防由于熔接痕,塑料降解造成机械强度变低⽽出现开裂。
(5)适当使⽤脱模剂,注意经常消除模⾯附着的⽓雾等物质。
(6)制件残余应⼒,可通过在成型后⽴即进⾏退⽕热处理来消除内应⼒⽽减少裂纹的⽣成。
2.模具⽅⾯:(1)顶出要平衡,如顶杆数量、截⾯积要⾜够,脱模斜度要⾜够,型腔⾯要有⾜够光滑,这样才防⽌由于外⼒导致顶出残余应⼒集中⽽开裂。
(2)制件结构不能太薄,过渡部份应尽量采⽤圆弧过渡,避免尖⾓、倒⾓造成应⼒集中。
(3)尽量少⽤⾦属嵌件,以防⽌嵌件与制件收缩率不同造成内应⼒加⼤。
(4)对深底制件应设置适当的脱模进⽓孔道,防⽌形成真空负压。
(5)主流道⾜够⼤使浇⼝料未来得及固化时脱模,这样易于脱模。
(6)主流道衬套与喷嘴接合应当防⽌冷硬料的拖拉⽽使制件粘在定模上。
3.材料⽅⾯:(1)再⽣料含量太⾼,造成制件强度过低。
(2)湿度过⼤,造成⼀些塑料与⽔汽发⽣化学反应,降低强度⽽出现顶出开裂。
(3)材料本⾝不适宜正在加⼯的环境或质量⽋佳,受到污染都会造成开裂。
4.机台⽅⾯:注塑机塑化容量要适当,过⼩塑化不充分未能完全混合⽽变脆,过⼤时会降解。
塑件内应⼒分析2内应⼒的种类⾼分⼦材料在成型过程中形成的不平衡构象,在成型之后不能⽴即恢复到与环境条件相适应的平衡构象,是注塑制品存在内应⼒的主要原因。
常见塑料制品开裂的原因浅析及检测方法简述

常见塑料制品开裂的原因浅析及检测方法简述引言工程塑料因为其优异的特性——高强度、耐热、耐冲击、抗老化等而被广泛应用于工业零件及各种外壳制造上。
但在制造或使用过程中,塑料制品很有可能被钉螺丝或涂胶水,这样的处理常常会诱发塑料制品的应力开裂,致使次品率很高。
而开裂是塑料制品经常出现的致命缺陷,包括制作表面丝状裂纹、微裂、顶白、开裂及因制件粘模、流道粘模而造成的创伤。
引起开裂的原因涉及模具、成型工艺、塑料材料、环境应力等方面。
开裂原因浅析及改进建议不同的开裂原因会导致不同的开裂类型,如果按照开裂的时间分类,塑料制品开裂现象通常有两种情况:(一)脱模开裂,塑料制品从模具脱出或在机器加工过程中出现开裂,这种开裂原因和后果比较容易预估;(二)应用开裂,塑料制品在放置一段时间后或使用过程中出现开裂,这种开裂往往难以预测,且产生的后果可能是毁灭性的。
以下主要从塑料材料的选择和环境应力的角度出发,结合以上两种开裂类型简单阐述开裂原因及改进建议。
1. 材料类型所致开裂的原因分析及改进建议下面通过两个案例,从选材背景及加工后出现的问题来分析材料选择对产品开裂可能造成的影响。
1.1圆孔性连接器(代表成型中空制品)一直以来,客户在生产成型小型圆孔时,选择的都是聚苯硫醚PPS GF30/GF40这种材料,器件没有出现任何开裂现象。
在开发大圆孔径系列连接器时,客户再次选用全球多家知名厂家的PPS GF30/GF40材料。
加工的结果是制品开裂非常严重,有些属于脱模开裂,有些属于应用开裂,而且不同厂家同类型含量的PPS均存在制品开裂问题。
客户和材料厂商起初怀疑是塑料冲击强度不够,但同时发现冲击强度比PPS GF30/GF40低的PA6和PC材料却反而不开裂。
在选用一些知名厂家提供的高抗冲击性PPS GF40材料后,开裂问题依然存在(图1)。
根据客户提供的信息,我们分析,很可能是由于成型塑料圆孔的模具型芯采用的是硬质合金材料。
金属材料导热和散热能力较强,而一般塑料材料散热能力较弱,金属材料和塑料挤出时不可避免会产生收缩相差较大的情况,塑料产品不同部位温度也有较大差别,对于延展性不好(断裂伸长率偏小)的塑料,无疑会发生断裂的现象。
注塑产品开裂或易断裂原因及解决办法
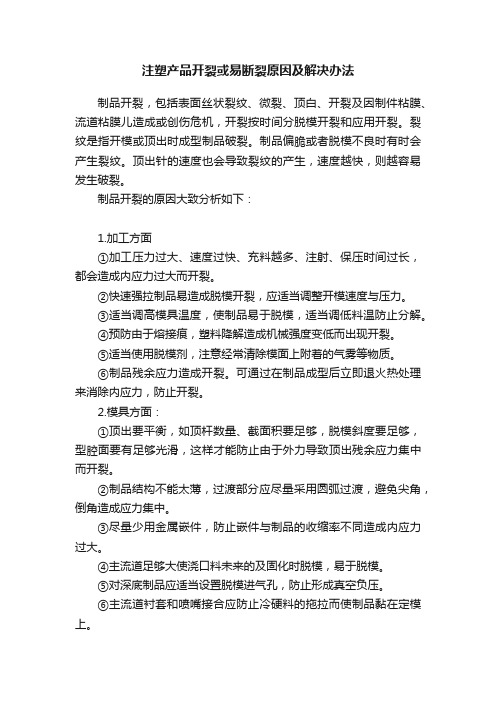
注塑产品开裂或易断裂原因及解决办法制品开裂,包括表面丝状裂纹、微裂、顶白、开裂及因制件粘膜、流道粘膜儿造成或创伤危机,开裂按时间分脱模开裂和应用开裂。
裂纹是指开模或顶出时成型制品破裂。
制品偏脆或者脱模不良时有时会产生裂纹。
顶出针的速度也会导致裂纹的产生,速度越快,则越容易发生破裂。
制品开裂的原因大致分析如下:1.加工方面①加工压力过大、速度过快、充料越多、注射、保压时间过长,都会造成内应力过大而开裂。
②快速强拉制品易造成脱模开裂,应适当调整开模速度与压力。
③适当调高模具温度,使制品易于脱模,适当调低料温防止分解。
④预防由于熔接痕,塑料降解造成机械强度变低而出现开裂。
⑤适当使用脱模剂,注意经常清除模面上附着的气雾等物质。
⑥制品残余应力造成开裂。
可通过在制品成型后立即退火热处理来消除内应力,防止开裂。
2.模具方面:①顶出要平衡,如顶杆数量、截面积要足够,脱模斜度要足够,型腔面要有足够光滑,这样才能防止由于外力导致顶出残余应力集中而开裂。
②制品结构不能太薄,过渡部分应尽量采用圆弧过渡,避免尖角,倒角造成应力集中。
③尽量少用金属嵌件,防止嵌件与制品的收缩率不同造成内应力过大。
④主流道足够大使浇口料未来的及固化时脱模,易于脱模。
⑤对深底制品应适当设置脱模进气孔,防止形成真空负压。
⑥主流道衬套和喷嘴接合应防止冷硬料的拖拉而使制品黏在定模上。
3.材料方面①再生料含量太高,制品强度过低,易造成开裂。
②湿度过大,造成塑料与水汽发生化学反应,降低强度儿造成顶出开裂。
应遵守各材料的成型温度,缩短停留时间以减少树脂分解老化,强化干燥条件抑制加水分解。
还可以通过提高模具温度和延长冷却时间来提高制品的结晶化程度。
③材料本身不适宜加工环境或质量不佳,受到污染都会造成开裂。
4.机台方面:注塑机塑化容量要适当,过小塑化不充分未能完全混合而变脆,过大时会分解。
采用以下方法也有效果:减慢开模速度和顶出速度以减轻成型品所承受的负荷以减少裂痕。
- 1、下载文档前请自行甄别文档内容的完整性,平台不提供额外的编辑、内容补充、找答案等附加服务。
- 2、"仅部分预览"的文档,不可在线预览部分如存在完整性等问题,可反馈申请退款(可完整预览的文档不适用该条件!)。
- 3、如文档侵犯您的权益,请联系客服反馈,我们会尽快为您处理(人工客服工作时间:9:00-18:30)。
塑料件应力开裂原因分析及检测方法简述几乎所有塑料制品都会不同程度地存在内应力,尤其是塑料注射制品的内应力更为明显。
内应力的存在不仅使塑料制品在储存和使用过程中出现应力开裂和翘曲变形,也影响塑料制品的力学性能、光学性能、电学性能及外观质量等。
应力开裂的必要条件是试样或零件内存在应力,并存在某种应力集中因素如缺口、表面划伤等。
那么塑件应力从何而来呢?塑胶件内应力产生的原因依引起内应力的原因不同,可将内应力分成如下几类:(1)取向内应力取向内应力是塑料熔体在流动充模和保压补料过程中,大分子链沿流动方向排列定向构象被冻结而产生的一种内应力。
取向的大分子链冻结在塑料制品内也就意味着其中存在未松弛的可逆高弹形变,所以说取向应力就是大分子链从取向构象力图过渡到无取向构象的内力。
塑料制品的取向内应力分布为从制品的表层到内层越来越小,并呈抛物线变化。
(2)冷却内应力冷却内应力是塑料制品在熔融加工过程中因冷却定型时收缩不均匀而产的一种内应力。
尤其对厚壁塑料制品,塑料制品的外层首先冷却凝固收缩,其内层可能还是热熔体,这徉芯层就会限制表层的收缩,导致芯层处于压应力状态,而表层处于拉应力状态。
塑料制品冷却内应力的分布为从制品的表层到内层越来越大,并也呈抛物线变化。
另外,带金属嵌件的塑料制品,由于金属与塑料的热胀系数相差较大,容易形成收缩不一均匀的内应力。
(3)环境应力环境应力开裂是聚烯烃类塑料的特有现象,它是指当制品存在应力时,与某些活性介质接触,会出现脆性裂纹,最终可能导致制品破坏。
这些活性物质可以是洗涤剂、皂类、水、油、酸、碱、盐及对材料并无显着溶胀作用的有机溶剂。
原料混有其它杂质或掺杂不适当的或过量的溶剂或其它添加剂时,在某些应力集的位置就会导致裂纹。
有些塑料如ABS等,在受潮状况下加热会与水汽发生催化裂化反应,使制件发生大的应变从而开裂。
(4)其它对于结晶塑料制品而言,其制品部各部位的结晶结构和结晶度不同也会产生内应力。
另外还有构型内应,力及脱模内应力等,只是其内应力听占比重都很小。
PC/ABS内应力开裂微观分析分子链刚性越大,熔体粘度越高,聚合物分子链活动性差,因而对于发生的可逆高弹形变恢复性差,易产生残余内应力。
例如一些分子链中含有苯环的聚合物,如PC、PPO、PPS等,其相应制品的内应力偏大。
PC材料容易内应力开裂是它本身分子结构决定,那就是聚碳酸酯分子结构中有苯环,所以取向比较困难。
在成型后,被取向的链节有恢复自然状态的趋势,但是由于分子链节已被冻结和分子链之间作用力,从而可能造成制品存在应力,这就是大家常说的应力开裂现象。
尤其是回收的PC,由于回收PC的相对分子质量下降,相对分子质量分布变宽,少量存在的水分、颜料、杂质、溶剂等极易引发开裂现象。
几种常见聚合物的内应力大小顺序: PPO>PSF>PC>ABS>PA6>PP>HDPE塑料内应力的降低与分散(1)前期原料的选择a)选取分子量大、分子量分布窄的树脂聚合物分子量越大,大分子链间作用力和缠结程度增加,其制品抗应力开裂能力较强;聚合物分子量分布越宽,其中低分子量成分越大,容易首先形成微观撕裂,造成应力集中,便制品开裂。
b)选取杂质含量低的树脂聚合物内的杂质即是应力的集中体,又会降低塑料的原有强度,应将杂质含量减少到最低程度。
c)共混改性易出现应力开裂的树脂与适宜的其它树脂共混,可降低内应力的存在程度。
例如,在PC 中混入适量PS,PS呈近似珠粒状分散于PC连续相中,可使内应力沿球面分散缓解并阻止裂纹扩展,从而达到降低内应力的目的。
再如,在PC中混入适量PE , PE球粒外沿可形成封闭的空化区,也可适当降低内应力。
d)增强改性用增强纤维进行增强改性,可以降低制品的内应力,这是因为纤维缠结了很多大分子链,从而提高应力开裂能力。
例如,30%GFPC的耐应力开裂能力比纯PC提高6倍之多。
e)成核改性在结晶性塑料中加入适宜的成核剂,可以在其制品中形成许多小的球晶,使内应力降低并得到分散。
(2)成型加工条件的控制在塑料制品的成型过程中,凡是能减小制品中聚合物分子取向的成型因素都能够降低取向应力;凡是能使制品中聚合物均匀冷却的工艺条件都能降低冷却内应力;凡有助于塑料制品脱模的加工方法都有利于降低脱模内应力。
对内应力影响较大的加工条件主要有如下几种:①料筒温度较高的料筒温度有利于取向应力的降低,这是因为在较高的料筒温度,熔体塑化均匀,粘度下降,流动性增加,在熔体充满型腔过程中,分子取向作用小,因而取向应力较小。
而在较低料筒温度下,熔体粘度较高,充模过程中分子取向较多,冷却定型后残余内应力则较大。
但是,料筒温度太高也不好,太高容易造成冷却不充分,脱模时易造成变形,虽然取向应力减小,但冷却应力和脱模应力反而增大。
②模具温度模具温度的高低对取向内应力和冷却内应力的影响都很大。
一方面,模具温度过低,会造成冷却加快,易使冷却不均匀而引起收缩上的较大差异,从而增大冷却内应力;另一方面,模具温度过低,熔体进入模其后,温度下降加快,熔体粘度增加迅速,造成在高粘度下充模,形成取向应力的程度明显加大。
③注射压力注射压力高,熔体充模过程中所受剪切作用力大,产生取向应力的机会也较大。
因此,为了降低取向应力和消除脱模应力,应适当降低注射压力。
④保压压力保压压力对塑料制品内应力的影响大于注射压力的影响。
在保压阶段,随着熔体温度的降低,熔体粘度迅速增加,此时若施以高压,必然导致分子链的强迫取向,从而形成更大的取向应力。
⑤注射速度注射速度越快,越容易造成分子链的取向程度增加,从而引起更大的取向应力。
但注射速度过低,塑料熔体进入模腔后,可能先后分层而形成熔化痕,产生应力集中线,易产生应力开裂。
所以注射速度以适中为宜。
最好采用变速注射,在速度逐渐减小下结束充模。
⑥保压时间保压时间越长,会增大塑料熔体的剪切作用,从而产生更大的弹性形变,冻结更多的取向应力。
所以,取向应力随保压时间延长和补料量增加而显着增大。
⑦开模残余压力应适当调整注射压力和保压时间,使开模时模内的残余压力接近于大气压力,从而避免产生更大的脱模内应力。
(3)塑料制品的热处理塑料制品的热处理是指将成型制品在一定温度下停留一段时间而消除内应力的方法。
热处理是消除塑料制品内取向应力的最好方法。
对于高聚物分子链的刚性较大、玻璃化温度较高的注塑件;对壁厚较大和带金属嵌件的制件;对使用温度范围较宽和尺寸精度要求较高的制件;时内应力较大而又不易自消的制件以及经过机械加工的制件都必须进行热处理。
常采用的热处理温度高于制件使用温度10~20℃或低于热变形温度 5~10℃。
一般厚度的制件,热处理1~2小时即可。
提高热处理温度和延长热处理时间具有相似的效果,但温度的效果更明显些。
热处理方法是将制件放入水、甘油、矿物油、乙二醇和液体石蜡等液体介质中,或放入空气循环烘箱中加热到指定温度,并在该温度下停留一定时间,然后缓慢冷却到室温。
实验表明,脱模后的制件立即进行热处理,对降低内应力、改善制件性能的效果更明显。
此外,提高模具温度,延长制件在模内冷却时间,脱模后进行保温处理都有类似热处理的作用。
尽管热处理是降低制件内应力的有效办法之一,但热处理通常只能将内应力降低到制件使用条件允许的范围,很难完全消除内应力。
(4)塑料制品的设计①塑料制品的形状和尺寸为了有效地分散内应力,应遵循这样的原则:制品外形应尽可能保持连续性,避免锐角、直角、缺口及突然扩大或缩小。
对于塑料制品的边缘处应设计成圆角,其中内圆角半径应大于相邻两壁中薄者厚度的70%以上;外圆角半径则根据制品形状而确定。
对于壁厚相差较大的部位,因冷却速度不同,易产生冷却内应力及取向内应力。
因此,应设计成壁厚尽可能均匀的制件,如必须壁厚不均匀,则要进行壁厚差异的渐变过渡。
②合理设计金属嵌件塑料与金属的热膨胀系数相差5~10倍,因而带金属嵌件的塑料制品在冷却时,两者形成的收缩程度不同,因塑料的收缩比较大而紧紧抱住金属嵌件,在嵌件周围的塑料内层受压应力,而外层受拉应力作用,产生应力集中现象。
在具体设汁嵌件时,应注意如下几点,以帮助减小或消除内应力。
a.尽可能选择塑料件作为嵌件。
b.尽可能选择与塑料热膨胀系数相差小的金属材料做嵌件材料,如铝、铝合金及铜等。
c.在金属嵌件上涂覆一层橡胶或聚氨酯弹性缓冲层,并保证成型时涂覆层不熔化,可降低两者收缩差。
d.对金属嵌件进行表面脱脂化处理,可以防止油脂加速制品的应力开裂。
e.金属嵌件进行适当的预热处理。
f.金属嵌件周围塑料的厚度要充足。
例如,嵌件外径为D,嵌件周围塑料厚度为h,则对铝嵌件塑料厚度h≥;对于铜嵌件,塑料厚度h≥ D。
g.金属嵌件应设计成圆滑形状,最好带精致的滚花纹。
③塑料制品上孔的设计塑料制品上孔的形状、孔数及孔的位置都会对内应力集中程度产生很大的影响。
为避免应力开裂,切忌在塑料制品上开设棱形、矩形、方形或多边形孔。
应尽可能开设圆形孔,其中椭圆形孔的效果最好,并应使椭圆形孔的长轴平行于外力作用方向。
如开设圆孔,可增开等直径的工艺圆孔,并使相邻两圆孔的中心连接线平行于外力作用方向,这样可以取得与椭圆孔相似的效果;还有一种方法,即在圆孔周围开设对称的槽孔,以分散内应力。
(5)塑料模具的设计在设计塑料模具时,浇注系统和冷却系统对塑料制品的内应力影响较大,在具体设计时应注意如下几点。
①浇口尺寸过大的浇口将需要较长的保压补料时间,在降温过程中的补料流动必定会冻结更多的取向应力,尤其是在补填冷料时,将给浇口附近造成很大的内应力。
适当缩小浇口尺寸,可缩短保压补料时间,降低浇口凝封时模内压力,从而降低取向应力。
但过小的浇口将导致充模时间延长,造成制品缺料。
④浇口的位置浇口的位置决定厂塑料熔体在模腔内的流动情况、流动距离和流动方向。
当浇口设在制品壁厚最大部位时,可适当降低注射压力、保压压力及保压时间,有利于降低取向应力。
当浇口设在薄壁部位时,宜适当增加浇口处的壁厚,以降低浇口附近的取向应力。
熔体在模腔内流动距离越长,产生取向应力的几率越大。
为此,对于壁厚、长流程且面积较大的塑料件,应适当分布多个浇口,能有效地降低取向应力,防止翘曲变形。
另外,由于浇口附近为内应力多发地带,可在浇口附近设汁成护耳式浇日,使内应力产生在护耳中,脱模后切除内应力较大的护耳,可降低塑料制品内的内应力。
⑤流道的设计设计短而粗的流道,可减小熔体的压力损失和温度降,相应降低注射压力和冷却速度,从而降低取向应力和冷却压力。
⑥冷却系统的设计冷却水道的分布要合理,使浇口附近、远离浇口区、壁厚处、壁薄处都得到均匀且缓慢的冷却,从而降低内应力,⑦顶出系统的设计要设计适当的脱模锥度,较高的型芯光洁度和较大面积的顶出部位,以防止强行脱模产生脱模应力。