一片晶圆到底可以切割出多少的晶片数目
晶圆切割[整理]
![晶圆切割[整理]](https://img.taocdn.com/s3/m/422743f9afaad1f34693daef5ef7ba0d4b736d5a.png)
芯圆切割(Wafer Dicing)本文介绍,IC封装(packaging)的后端工艺(back-end)之一:晶圆切片(wafer dicing)。
在过去三十年期间,切片(dicing)系统与刀片(blade)已经不断地改进以对付工艺的挑战和接纳不同类型基板的要求。
最新的、对生产率造成最大影响的设备进展包括:使两个切割(two cuts)同时进行的、将超程(overtravel)减到最小的双轴(dual-spindle)切片系统;自动心轴扭力监测和自动冷却剂流量调节能力。
重大的切片刀片进步包括一些刀片,它们用于很窄条和/或较高芯片尺寸的晶圆、以铜金属化的晶圆、非常薄的晶圆、和在切片之后要求表面抛光的元件用的晶圆。
许多今天要求高的应用都要求设备能力和刀片特性两方面都最优化的工艺,以尽可能最低的成本提供尽可能高的效率。
切片机制(The Dicing Mechanism)硅晶圆切片工艺是在“后端”装配工艺中的第一步。
该工艺将晶圆分成单个的芯片,用于随后的芯片接合(die bonding)、引线接合(wire bonding)和测试工序。
一个转动的研磨盘(刀片)完成切片(dicing)。
一根心轴以高速,30,000~60,000rpm (83~175m/sec的线性速度)转动刀片。
该刀片由嵌入电镀镍矩阵黏合剂中的研磨金刚石制成。
在芯片的分割期间,刀片碾碎基础材料(晶圆),同时去掉所产生的碎片。
材料的去掉沿着晶方(dice)的有源区域之间的专用切割线(迹道)发生的。
冷却剂(通常是去离子水)指到切割缝内,改善切割品质,和通过帮助去掉碎片而延长刀片寿命。
每条迹道(street)的宽度(切口)与刀片的厚度成比例。
关键工艺参数硅圆片切割应用的目的是将产量和合格率最大,同时资产拥有的成本最小。
可是,挑战是增加的产量经常减少合格率,反之亦然。
晶圆基板进给到切割刀片的速度决定产出。
随着进给速度增加,切割品质变得更加难以维持在可接受的工艺窗口内。
晶圆---简介

晶圆是制造IC的基本原料硅是由沙子所精练出来的,晶圆便是硅元素加以纯化(99.999%),接着是将这些纯硅制成长硅晶棒,成为制造积体电路的石英半导体的材料,经过照相制版,研磨,抛光,切片等程序,将多晶硅融解拉出单晶硅晶棒,然后切割成一片一片薄薄的晶圆。
我们会听到几寸的晶圆厂,如果硅晶圆的直径越大,代表著这座晶圆厂有较好的技术。
另外还有scaling技术可以将电晶体与导线的尺寸缩小,这两种方式都可以在一片晶圆上,制作出更多的硅晶粒,提高品质与降低成本。
所以这代表6寸、8寸、12寸晶圆当中,12寸晶圆有较高的产能。
当然,生产晶圆的过程当中,良品率是很重要的条件。
晶圆是指硅半导体积体电路制作所用的硅晶片,由于其形状为圆形,故称为晶圆;在硅晶片上可加工制作成各种电路元件结构,而成为有特定电性功能之IC产品。
晶圆的原始材料是硅,而地壳表面有用之不竭的二氧化硅。
二氧化硅矿石经由电弧炉提炼,盐酸氯化,并经蒸馏后,制成了高纯度的多晶硅,其纯度高达0.99999999999。
晶圆制造厂再将此多晶硅融解,再于融液内掺入一小粒的硅晶体晶种,然后将其慢慢拉出,以形成圆柱状的单晶硅晶棒,由于硅晶棒是由一颗小晶粒在熔融态的硅原料中逐渐生成,此过程称为“长晶”。
硅晶棒再经过研磨,抛光,切片后,即成为积体电路工厂的基本原料——硅晶圆片,这就是“晶圆”。
晶圆工艺晶圆的生产工艺流程从大的方面来讲,晶圆生产包括晶棒制造和晶片制造两大步骤,它又可细分为以下几道主要工序(其中晶棒制造只包括下面的第一道工序,其余的全部属晶片制造,所以有时又统称它们为晶柱切片后处理工序):晶棒成长-- 晶棒裁切与检测-- 外径研磨-- 切片-- 圆边-- 表层研磨-- 蚀刻-- 去疵-- 抛光-- 清洗-- 检验-- 包装1、晶棒成长工序:它又可细分为:1)、融化(Melt Down):将块状的高纯度复晶硅置于石英坩锅内,加热到其熔点1420°C以上,使其完全融化。
200毫米晶圆-概念解析以及定义

200毫米晶圆-概述说明以及解释1.引言1.1 概述200毫米晶圆是一种在半导体制造过程中广泛使用的基础材料。
晶圆是一种扁平而圆形的硅基片,通常用于制造集成电路和其他电子元件。
随着科技的不断进步,对晶圆的要求也越来越高。
200毫米晶圆因其尺寸较大,具有更高的集成度和更高的生产效率,逐渐成为半导体行业的主流选择。
相比之下,100毫米或150毫米晶圆的制造成本相对较高,而300毫米晶圆则受到供应链和工艺等因素的限制。
而200毫米晶圆则在成本和生产效率之间取得了良好的平衡。
200毫米晶圆的制造过程需要经历多道工序,包括切割、抛光、清洗等。
然后,在晶圆上可以进行光刻、薄膜沉积、离子注入和扩散等步骤,最终制造出集成电路的各个组件。
除了制造集成电路,200毫米晶圆在其他领域也有着广泛的应用。
例如,它可以用于制造太阳能电池板、LED芯片和传感器等。
因此,随着人们对电子产品和新能源需求的不断增长,200毫米晶圆的市场需求也在逐渐扩大。
总之,200毫米晶圆在半导体制造业中具有重要的地位。
它的尺寸恰到好处,使得制造成本和生产效率得到平衡。
随着技术的不断发展,我们可以期待200毫米晶圆在未来的应用领域中发挥更重要的作用。
1.2 文章结构文章结构部分的内容如下:在本文中,将按照以下结构进行阐述:引言部分将提供关于200毫米晶圆的背景信息和概述;正文部分将依次介绍三个要点,包括第一个要点、第二个要点和第三个要点;结论部分将对本文的主要内容进行总结,并对结果进行分析,并展望200毫米晶圆的未来发展方向。
通过这样的结构安排,旨在全面介绍和探讨200毫米晶圆的相关问题,并对其应用前景进行展望。
1.3 目的本文的目的是探讨200毫米晶圆在半导体制造领域的应用,并对其优势和挑战进行分析。
首先,我们将介绍晶圆的基本概念和制造工艺,然后重点关注200毫米晶圆在集成电路生产中的应用情况。
通过比较不同尺寸的晶圆,我们将评估200毫米晶圆的优势和劣势,并分析其在提高集成电路生产能力和降低制造成本方面的潜力。
晶圆 芯片数量 换算

晶圆(Wafer)是半导体制造中的基本材料,它通常是圆形的硅片,用于制造各种集成电路(IC)芯片。
晶圆上的芯片数量取决于多个因素,包括晶圆的直径、芯片的设计和制造技术、以及晶圆上的布局密度等。
以下是一些基本的换算关系和概念:1. 晶圆直径与芯片数量的关系:晶圆的直径通常以英寸(")为单位,常见的有200mm(8英寸)、300mm(12英寸)、450mm(18英寸)等。
随着技术的发展,晶圆的直径越来越大,芯片的数量也随之增加。
2. 晶圆上的芯片布局:晶圆上的芯片通常是按照一定的矩阵排列的,每个芯片之间有一定的间隙。
例如,一个典型的300mm晶圆可能在直径方向上有多个芯片轨道,每个轨道上可以排列多个芯片。
3. 芯片产率:晶圆经过切割后,实际上可以得到的芯片数量会少于理论上的最大数量,这是因为切割过程中可能会损坏一些芯片,以及边缘的部分可能不适合切割芯片。
因此,实际的芯片产率通常会低于100%。
具体的换算公式如下:设晶圆直径为D英寸,晶圆上的芯片直径为d英寸,晶圆上的芯片数量为N,则有以下关系:N = (π *(D/2)²) / (π * (d/2)²)这个公式是一个简化的模型,它假设芯片在晶圆上均匀分布。
实际上,由于芯片之间的间隙和切割损失,实际的芯片数量会少于这个理论值。
例如,如果一个300mm(12英寸)的晶圆上每个芯片直径为100mm(4英寸),则理论上的芯片数量为:N = (π * (12/2)²) / (π * (4/2)²) = (π * 36) / (π * 4) = 9这意味着一个12英寸的晶圆上理论上可以有9个4英寸的芯片。
然而,实际上的芯片数量会少于这个理论值。
请注意,这些计算是基于理想情况的简化模型,实际的芯片数量会受到多种因素的影响。
晶圆切割晶圆切割和微加工新技术
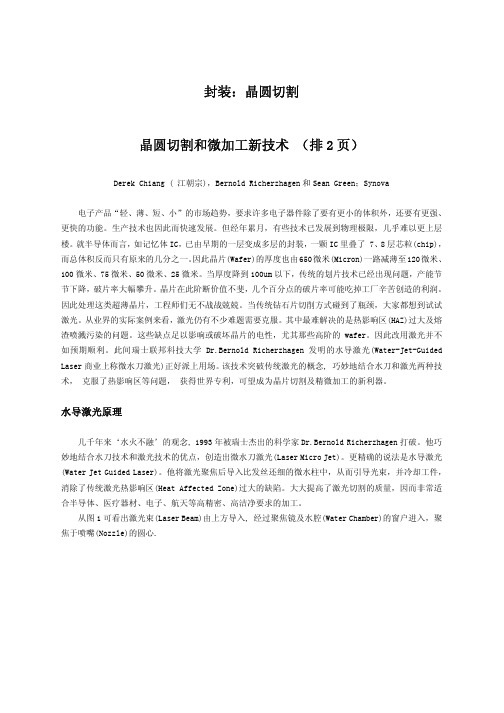
封装:晶圆切割晶圆切割和微加工新技术 (排2页)Derek Chiang ( 江朝宗),Bernold Richerzhagen和Sean Green;Synova电子产品“轻、薄、短、小”的市场趋势,要求许多电子器件除了要有更小的体积外,还要有更强、更快的功能。
生产技术也因此而快速发展。
但经年累月,有些技术已发展到物理极限,几乎难以更上层楼。
就半导体而言,如记忆体IC,已由早期的一层变成多层的封裝,一颗IC里叠了 7、8层芯粒(chip),而总体积反而只有原来的几分之一。
因此晶片(Wafer)的厚度也由650微米(Micron)一路减薄至120微米、100微米、75微米、50微米、25微米。
当厚度降到100um以下,传统的划片技术已经出现问题,产能节节下降,破片率大幅攀升。
晶片在此阶断价值不斐,几个百分点的破片率可能吃掉工厂辛苦创造的利润。
因此处理这类超薄晶片,工程师们无不战战兢兢。
当传统钻石片切削方式碰到了瓶颈,大家都想到试试激光。
从业界的实际案例来看,激光仍有不少难题需要克服。
其中最难解决的是热影响区(HAZ)过大及熔渣喷溅污染的问题。
这些缺点足以影响或破坏晶片的电性,尤其那些高阶的wafer。
因此改用激光并不如预期顺利。
此间瑞士联邦科技大学Dr.Bernold Richerzhagen发明的水导激光(Water-Jet-Guided Laser商业上称微水刀激光)正好派上用场。
该技术突破传统激光的概念, 巧妙地结合水刀和激光两种技术, 克服了热影响区等问题, 获得世界专利,可望成为晶片切割及精微加工的新利器。
水导激光原理几千年来‘水火不融’的观念, 1993年被瑞士杰出的科学家Dr.Bernold Richerzhagen打破。
他巧妙地结合水刀技术和激光技术的优点,创造出微水刀激光(Laser Micro Jet)。
更精确的说法是水导激光(Water Jet Guided Laser)。
晶圆切割die数dpw计算公式

晶圆切割Die数DPW计算公式引言概述:在半导体制造中,晶圆是半导体芯片的基础,而晶圆上的小块区域被称为Die。
DPW(Dies Per Wafer)是一个关键的性能指标,它表示在一个晶圆上能切割出的Die的数量。
本文将详细介绍晶圆切割Die数DPW的计算公式,以及与该公式相关的重要参数。
正文:1. 晶圆切割Die数DPW的计算公式1.1 晶圆面积与Die数关系:晶圆直径与面积计算:解释晶圆直径与面积的关系,介绍常用的晶圆面积计算公式。
Die的尺寸与面积关系:阐述Die的尺寸如何影响Die的面积计算,说明在制造中常见的Die尺寸标准。
1.2 有效利用晶圆面积:排列方式的选择:探讨晶圆上Die的排列方式,以及不同排列方式对DPW的影响。
晶圆边缘效应:解释晶圆边缘部分的效应,以及在计算DPW时如何考虑晶圆边缘的影响。
1.3 其他因素的考虑:切割误差的补偿:介绍在实际切割过程中可能出现的误差,以及如何在计算DPW时进行补偿。
晶圆上的保留区域:讨论晶圆上可能需要保留的区域,以及这些区域如何影响DPW的计算。
2. 与DPW计算公式相关的重要参数2.1 晶圆直径(Diameter):直径的测量与影响:介绍晶圆直径的测量方法,以及晶圆直径对DPW的影响。
常见晶圆直径尺寸:提供常见的晶圆直径尺寸,说明它们在不同制造环境中的应用。
2.2 Die的尺寸(Die Size):Die尺寸的标准:解释Die尺寸的标准化,以及标准尺寸对DPW 的计算的重要性。
尺寸的测量与控制:介绍如何测量Die的尺寸,并控制制造过程中的尺寸变化。
2.3 晶圆的形状(Wafer Shape):不同形状的晶圆:探讨不同形状晶圆的特点,以及这些形状对DPW计算的影响。
形状的变化与制程:说明晶圆形状可能因制程变化而引起的影响。
3. DPW计算的应用与优化策略3.1 制造成本的考虑:DPW与成本关系:分析DPW与制造成本的关系,讨论如何在提高DPW的同时降低制造成本。
晶圆切割工艺
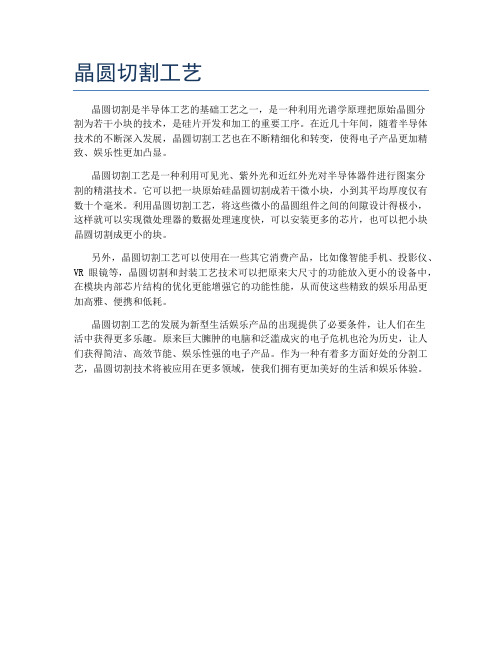
晶圆切割工艺
晶圆切割是半导体工艺的基础工艺之一,是一种利用光谱学原理把原始晶圆分
割为若干小块的技术,是硅片开发和加工的重要工序。
在近几十年间,随着半导体技术的不断深入发展,晶圆切割工艺也在不断精细化和转变,使得电子产品更加精致、娱乐性更加凸显。
晶圆切割工艺是一种利用可见光、紫外光和近红外光对半导体器件进行图案分
割的精湛技术。
它可以把一块原始硅晶圆切割成若干微小块,小到其平均厚度仅有数十个毫米。
利用晶圆切割工艺,将这些微小的晶圆组件之间的间隙设计得极小,这样就可以实现微处理器的数据处理速度快,可以安装更多的芯片,也可以把小块晶圆切割成更小的块。
另外,晶圆切割工艺可以使用在一些其它消费产品,比如像智能手机、投影仪、VR眼镜等,晶圆切割和封装工艺技术可以把原来大尺寸的功能放入更小的设备中,在模块内部芯片结构的优化更能增强它的功能性能,从而使这些精致的娱乐用品更加高雅、便携和低耗。
晶圆切割工艺的发展为新型生活娱乐产品的出现提供了必要条件,让人们在生
活中获得更多乐趣。
原来巨大臃肿的电脑和泛滥成灾的电子危机也沦为历史,让人们获得简洁、高效节能、娱乐性强的电子产品。
作为一种有着多方面好处的分割工艺,晶圆切割技术将被应用在更多领域,使我们拥有更加美好的生活和娱乐体验。
半导体产量单位
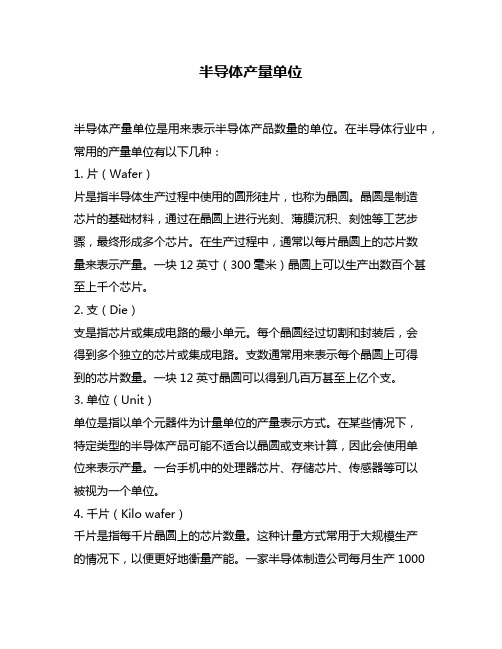
半导体产量单位半导体产量单位是用来表示半导体产品数量的单位。
在半导体行业中,常用的产量单位有以下几种:1. 片(Wafer)片是指半导体生产过程中使用的圆形硅片,也称为晶圆。
晶圆是制造芯片的基础材料,通过在晶圆上进行光刻、薄膜沉积、刻蚀等工艺步骤,最终形成多个芯片。
在生产过程中,通常以每片晶圆上的芯片数量来表示产量。
一块12英寸(300毫米)晶圆上可以生产出数百个甚至上千个芯片。
2. 支(Die)支是指芯片或集成电路的最小单元。
每个晶圆经过切割和封装后,会得到多个独立的芯片或集成电路。
支数通常用来表示每个晶圆上可得到的芯片数量。
一块12英寸晶圆可以得到几百万甚至上亿个支。
3. 单位(Unit)单位是指以单个元器件为计量单位的产量表示方式。
在某些情况下,特定类型的半导体产品可能不适合以晶圆或支来计算,因此会使用单位来表示产量。
一台手机中的处理器芯片、存储芯片、传感器等可以被视为一个单位。
4. 千片(Kilo wafer)千片是指每千片晶圆上的芯片数量。
这种计量方式常用于大规模生产的情况下,以便更好地衡量产能。
一家半导体制造公司每月生产1000万个芯片,可以表示为1000K片。
5. 百万支(Million die)百万支是指每百万个芯片或集成电路的数量。
这种计量方式常用于大规模集成电路生产中,特别是在存储器和微处理器领域。
一家公司每年生产10亿个存储器芯片,则可以表示为1000M支。
6. 亿支(Billion die)亿支是指每十亿个芯片或集成电路的数量。
这种计量方式通常用于大规模集成电路生产中,特别是在微处理器领域。
一家公司每年生产1000亿个微处理器,则可以表示为100G支。
总结:半导体产量单位包括:片(Wafer)、支(Die)、单位(Unit)、千片(Kilo wafer)、百万支(Million die)和亿支(Billion die)。
不同单位适用于不同的场景和需求,可以根据具体情况选择合适的单位来表示半导体产品的产量。
切单(Singulation),一个晶圆被分割成多个半导体芯片的工艺SKhynixNewsroom

切单(Singulation),一个晶圆被分割成多个半导体芯片的工艺SKhynixNewsroom一个晶圆要经历三次的变化过程,才能成为一个真正的半导体芯片:首先,是将块儿状的铸锭切成晶圆;在第二道工序中,通过前道工序要在晶圆的正面雕刻晶体管;最后,再进行封装,即通过切割过程,使晶圆成为一个完整的半导体芯片。
可见,封装工序属于后道工序,在这道工序中,会把晶圆切割成若干六面体形状的单个芯片,这种得到独立芯片的过程被称作做“切单(Singulaton)”,而把晶圆板锯切成独立长方体的过程则叫做“晶片切割(Die Sawing)”。
近来,随着半导体集成度的提高,晶圆厚度变得越来越薄,这当然给“切单”工艺也带来了不少难度。
一、晶圆切割(Wafer Dicing)的发展历程图1. 晶圆切割方法的发展历程(切单)下载图片前道和后道工序通过各种不同方式的互动而进一步发展:后道工序的进化可以决定晶圆上die单独分离出的六面体小芯片)的结构和位置,以及晶片上焊盘(电连接路径)的结构和位置;与之相反,前端工艺的进化则改变了后端工艺中的晶圆背面减薄和“晶片切割(Die Sawing)”晶圆的流程和方法。
因此,封装的外观日益变得精巧,会对后端工艺带来很大的影响。
而且,根据包装外观的变化,切割次数、程序和类型也会发生相应的变化。
▶请参见“轻、薄、短、小”,半导体封装的演变(“Light, Thin, Short and Small”, The Development of Semiconductor Packages)。
那么,现在就让我们一起通过芯片“切单”的演化过程,来看看五种切割方法吧。
二、划片切割(Scribe Dicing)图2. 早期的划片切割法:划片后进行物理上的分割(Breaking)@直径为6英寸以下的的晶圆下载图片早期,通过施加外力切割的“掰开(Breaking)”是唯一可以把晶圆分割成六面形的Die的切割法。
不同尺寸芯片在同一片晶圆的切割方法
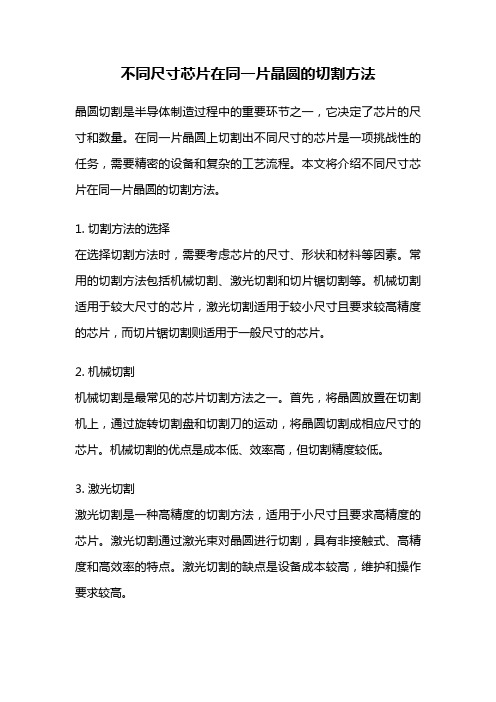
不同尺寸芯片在同一片晶圆的切割方法晶圆切割是半导体制造过程中的重要环节之一,它决定了芯片的尺寸和数量。
在同一片晶圆上切割出不同尺寸的芯片是一项挑战性的任务,需要精密的设备和复杂的工艺流程。
本文将介绍不同尺寸芯片在同一片晶圆的切割方法。
1. 切割方法的选择在选择切割方法时,需要考虑芯片的尺寸、形状和材料等因素。
常用的切割方法包括机械切割、激光切割和切片锯切割等。
机械切割适用于较大尺寸的芯片,激光切割适用于较小尺寸且要求较高精度的芯片,而切片锯切割则适用于一般尺寸的芯片。
2. 机械切割机械切割是最常见的芯片切割方法之一。
首先,将晶圆放置在切割机上,通过旋转切割盘和切割刀的运动,将晶圆切割成相应尺寸的芯片。
机械切割的优点是成本低、效率高,但切割精度较低。
3. 激光切割激光切割是一种高精度的切割方法,适用于小尺寸且要求高精度的芯片。
激光切割通过激光束对晶圆进行切割,具有非接触式、高精度和高效率的特点。
激光切割的缺点是设备成本较高,维护和操作要求较高。
4. 切片锯切割切片锯切割是一种常用的切割方法,适用于一般尺寸的芯片。
切片锯切割通过旋转切割盘和带有切割锯片的切割机,对晶圆进行切割。
切片锯切割的优点是成本适中、效率高,但切割精度相对较低。
5. 切割工艺流程不同尺寸芯片的切割工艺流程相似,但具体参数和设备设置会有所不同。
一般而言,切割工艺流程包括以下几个步骤:(1) 切割前的准备:对晶圆进行清洗和检查,确保表面平整和无瑕疵。
(2) 切割参数设置:根据芯片尺寸和要求,设置切割机的参数,如切割速度、刀具压力等。
(3) 切割过程:将晶圆放置在切割机上,启动切割机并调整参数,开始切割过程。
(4) 切割后处理:将切割好的芯片进行清洗和检查,确保质量合格。
(5) 包装和封装:对切割好的芯片进行包装和封装,以保护芯片不受损坏。
6. 工艺优化和改进为了提高切割效率和精度,工艺优化和改进是必不可少的。
可以通过优化切割参数、改进切割设备和提高工艺控制等方式来实现。
晶圆划片原理
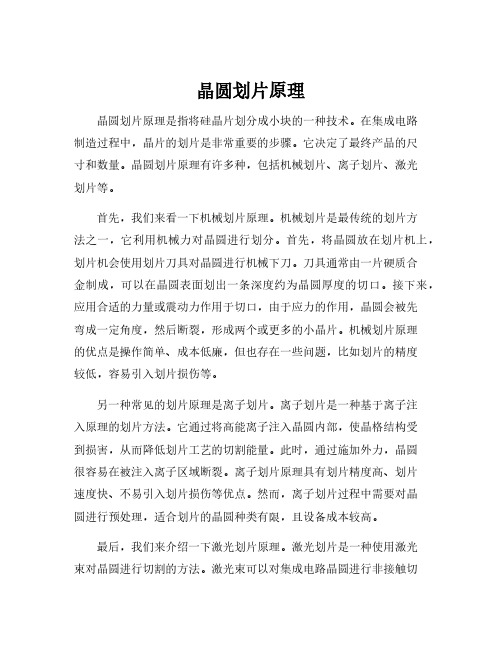
晶圆划片原理晶圆划片原理是指将硅晶片划分成小块的一种技术。
在集成电路制造过程中,晶片的划片是非常重要的步骤。
它决定了最终产品的尺寸和数量。
晶圆划片原理有许多种,包括机械划片、离子划片、激光划片等。
首先,我们来看一下机械划片原理。
机械划片是最传统的划片方法之一,它利用机械力对晶圆进行划分。
首先,将晶圆放在划片机上,划片机会使用划片刀具对晶圆进行机械下刀。
刀具通常由一片硬质合金制成,可以在晶圆表面划出一条深度约为晶圆厚度的切口。
接下来,应用合适的力量或震动力作用于切口,由于应力的作用,晶圆会被先弯成一定角度,然后断裂,形成两个或更多的小晶片。
机械划片原理的优点是操作简单、成本低廉,但也存在一些问题,比如划片的精度较低,容易引入划片损伤等。
另一种常见的划片原理是离子划片。
离子划片是一种基于离子注入原理的划片方法。
它通过将高能离子注入晶圆内部,使晶格结构受到损害,从而降低划片工艺的切割能量。
此时,通过施加外力,晶圆很容易在被注入离子区域断裂。
离子划片原理具有划片精度高、划片速度快、不易引入划片损伤等优点。
然而,离子划片过程中需要对晶圆进行预处理,适合划片的晶圆种类有限,且设备成本较高。
最后,我们来介绍一下激光划片原理。
激光划片是一种使用激光束对晶圆进行切割的方法。
激光束可以对集成电路晶圆进行非接触切割,其原理是通过激光束的热效应,在晶圆上产生局部加热,使局部区域温度升高,从而破坏材料的晶格结构。
接下来,通过外力,晶圆将在切割位置断裂。
激光划片原理具有划片精度高、划片速度快、不易引入划片损伤等优点。
然而,激光划片设备成本较高,使用过程中需要精确控制激光功率和位置,以避免损坏晶圆。
总的来说,晶圆划片原理有多种方法可供选择,每种方法都有其特点和适用范围。
在选择合适的划片方法时,需要综合考虑划片精度、划片速度、成本等因素。
随着集成电路制造工艺的不断进步,晶圆划片技术也在不断发展和创新,为集成电路制造提供了更多选择和可能性。
8寸晶圆
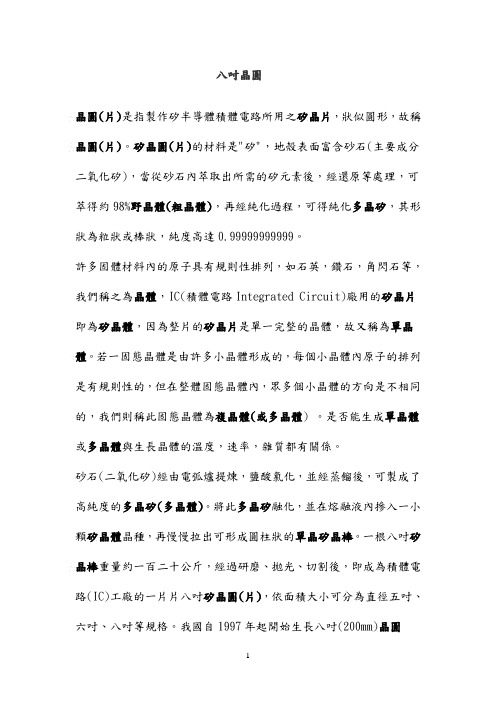
八吋晶圓晶圓(片)是指製作矽半導體積體電路所用之矽晶片,狀似圓形,故稱晶圓(片)。
矽晶圓(片)的材料是"矽",地殼表面富含砂石(主要成分二氧化矽),當從砂石內萃取出所需的矽元素後,經還原等處理,可萃得約98%野晶體(粗晶體),再經純化過程,可得純化多晶矽,其形狀為粒狀或棒狀,純度高達0.99999999999。
許多固體材料內的原子具有規則性排列,如石英,鑽石,角閃石等,我們稱之為晶體,IC(積體電路Integrated Circuit)廠用的矽晶片即為矽晶體,因為整片的矽晶片是單一完整的晶體,故又稱為單晶體。
若一固態晶體是由許多小晶體形成的,每個小晶體內原子的排列是有規則性的,但在整體固態晶體內,眾多個小晶體的方向是不相同的,我們則稱此固態晶體為複晶體(或多晶體) 。
是否能生成單晶體或多晶體與生長晶體的溫度,速率,雜質都有關係。
砂石(二氧化矽)經由電弧爐提煉,鹽酸氯化,並經蒸餾後,可製成了高純度的多晶矽(多晶體)。
將此多晶矽融化,並在熔融液內摻入一小顆矽晶體晶種,再慢慢拉出可形成圓柱狀的單晶矽晶棒。
一根八吋矽晶棒重量約一百二十公斤,經過研磨、拋光、切割後,即成為積體電路(IC)工廠的一片片八吋矽晶圓(片),依面積大小可分為直徑五吋、六吋、八吋等規格。
我國自1997年起開始生長八吋(200mm)晶圓(片),現已投入生長十二吋晶圓(片)。
最後矽晶圓(片)送至八吋晶圓廠內製造晶片電路,每塊矽晶圓(片)上可翻製出數以百計的相同矽晶片。
這些晶片電路再經封裝測試等程序,經過複雜的化學和電子過程處理(製程)後,其上佈滿著多層精細的電子線路,便成為市面上一顆顆的IC(積體電路Integrated Circuit)。
積體電路(IC,Integrated Circuit)主要用於電腦及相關產業。
是把數以千計萬計的電子元件如電阻、電容等設計均收縮在一片不到指甲大小的矽晶片上,如此傳統電子迴路的體積均予於小型化,例如桌上型電腦縮小成筆記電腦。
芯片的切割技术

芯片的切割技术
2020年3月
目录/Contents
01
芯片切割的概念
02
芯片切割的方式
03
激光切割技术
01 芯片切割的概念
芯片切割的概念
晶圆切割(Die saw),有时也叫“划 片”(Dicing)。一个晶圆上做出来的独立的 IC有几百个到几千个甚至上万个,切割的目 的是将整个晶圆上每一个独立的IC通过高速 旋转的金刚石刀片切割开来,为后面的工序 做准备。芯片的切割是指将晶圆上的多个芯 片分离开来,以便在后续的封装中对单个芯 片进行粘贴,键合等操作。
较小 极小 基本无厚度要求 可适应不同类型晶圆片 损耗很小
感谢聆听!
飞片是非常危险的,第一是会造成成品率的下降,第二是飞出来的硅片可能 会造成临近硅片的物理损伤。这就是为什么刀片需要这么高的转速的一个原因。
切割损伤02 芯片切割的方式来自芯片切割的方式8
刀片切割
用机械的方式对晶圆进行切割,通过空气静压主轴带动金刚石砂轮 划切刀具高速旋转,将晶圆或器件沿切割道方向进行切割或开槽。
方式
激光切割
激光划片是指把高峰值功率的激光束聚焦在硅片(或陶瓷基片、金 刚石薄膜等)表面,使硅材料表面产生高温汽化,从而打出连续的 盲孔,形成沟槽。 一般采用峰值功率高、模式好的1064nm或532nm波长激光光源。
刀片切割
9
刀片切割
刀片切割原理—撞击 当工作物是属于硬、脆的材质,钻石颗粒会以撞击(Fracturing)的方式,
切割示意图
激光切割机
技术比对
传统划片方式(砂轮)
切割速度
5-8mm/s
切割线宽 切割效果 热影响区 残留应力 对晶圆厚度要求 适应性 有无损耗
芯片的切割技术

芯片的切割技术:芯片切割的概念,芯片切割的方式,激光切割芯片切割的概念:晶圆切割(Die saw),有时也叫“划片”(Dicing)。
一个晶圆上做出来的独立的IC有几百个到几千个甚至上万个,切割的目的是将整个晶圆上每一个独立的IC通过高速旋转的金刚石刀片切割开来,为后面的工序做准备。
芯片的切割是指将晶圆上的多个芯片分离开来,以便在后续的封装中对单个芯片进行粘贴,键合等操作。
左图为芯片切割前,有图为芯片切割后另一个重要的概念,绷片:绷片(Wafer Mounter)——是一道辅助工序,主要是给晶圆的背面贴上一层有弹性和一定粘性的蓝膜,并固定在一个直径稍大的金属框架上,以利于后面的加工。
为了避免粘贴不牢靠而造成切割过程中的飞片问题,在绷膜的过程中要加60~80度的温度。
这是绷片的示意图飞片:在切割的过程中,刀片的转速往往达到几万转/分钟,而切割道的宽度往往只有几十到一百微米,所以对于设备的要求也是很高的。
如果前面绷膜的时候晶圆粘贴不牢靠或者有气泡存在,切割开来的硅片(Die)就会从蓝膜上飞出来,称作飞片。
飞片是非常危险的,第一是会造成成品率的下降,第二是飞出来的硅片可能会造成临近硅片的物理损伤。
这就是为什么刀片需要这么高的转速的一个原因。
这是切割过程钟可能存在的切割损伤芯片的切割方式:一般分为两种:刀片切割/激光切割刀片切割:用机械的方式对晶圆进行切割,通过空气静压主轴带动金刚石砂轮划切刀具高速旋转,将晶圆或器件沿切割道方向进行切割或开槽。
激光切割:激光划片是指把高峰值功率的激光束聚焦在硅片(或陶瓷基片、金刚石薄膜等)表面,使硅材料表面产生高温汽化,从而打出连续的盲孔,形成沟槽。
一般采用峰值功率高、模式好的1064nm或532nm波长激光光源刀片切割:刀片切割原理是撞击当工作物是属于硬、脆的材质,钻石颗粒会以撞击(Fracturing)的方式,将工作物敲碎,再利用刀口将粉末移除。
(容易产生绷碎:chipping)左边是切割时钻石颗粒的撞击示意图,这是刀片切割的仿真示意。
芯片制造之揭秘晶圆制造详解

芯片是当代最伟大的发明之一。
如果没有芯片的出现,很难想象当前的电子时代会是什么样子。
正是因为芯片的发明,所有的功能才得以浓缩在一个小小的芯片中。
芯片是集成电路的载体,它从晶圆上切割而来,通常是计算机或其他电子设备的重要组成部分。
以晶圆为基础,通过层层叠加,就可以完成想要的形状(即各种类型的芯片),而作为半导体产业的基础,晶圆是集成电路的基础载体,因此晶圆的重要性不言而喻。
本文着重讲解晶圆的生产以及发展现状。
1、什么是晶圆在现代技术的领域中,半导体晶圆作为集成电路和电子设备的基础构建模块,已经彻底改变了我们的生活。
晶圆是由纯硅(Si)制成的。
它通常分为6英寸、8英寸和12英寸等不同规格。
芯片厂购买晶圆,用来制造NAND 闪存和DRAM晶圆。
由于每家公司使用的纳米技术不同,生产的NAND闪存芯片在性能、成本等方面存在差异。
制造成为NAND闪存晶圆后,晶圆会被切割成一个个独立的晶片,专业术语称为Die(裸晶)。
这些微小的、平坦的硅片承载着令人瞩目的历史,其历史可以追溯到20世纪中期。
1.1、早期岁月:半导体晶圆的诞生半导体晶圆的历史始于20世纪60年代初,但其起源可以追溯到几十年前。
半导体的基础工作在20世纪30年代和40年代奠定,当时像朱利叶斯·利利内夫尔德、约翰·巴丁和沃尔特·布拉坦等研究人员开发了场效应晶体管(FET)和点接触晶体管,这标志着固体电子学的第一步。
直到20世纪60年代初,半导体晶圆的概念才真正成型。
像德州仪器、英特尔这样的公司对晶圆作为制造集成电路(ICs)的理想衬底的发展和商业化起到了关键作用。
硅,这种在沙子中发现的丰富元素,由于其半导体性质,被证明是半导体晶圆的理想材料。
最早的晶圆相对较小,直径大约为1英寸(2.54厘米)。
然而,随着对更复杂、更强大的电子设备的需求增长,晶圆的尺寸也必须随之增长。
在20世纪60年代末和70年代初,行业从1英寸晶圆过渡到更大的尺寸,如2英寸(5.08厘米)和3英寸(7.62厘米)。
晶圆数量计算公式

晶圆数量计算公式
晶圆数量=(晶圆直径^2*π)/(晶圆片尺寸^2)
其中,晶圆直径是指晶圆的直径(单位通常为毫米或英寸),晶圆片尺寸是指每个晶圆片的尺寸(通常为毫米)。
这个公式的含义是将晶圆划分为晶圆片,然后计算晶圆片数量。
晶圆的面积是由其直径的平方乘以π得到的,而每个晶圆
片的面积是由其尺寸的平方得到的。
通过将晶圆的面积除以每
个晶圆片的面积,就可以得到晶圆片的数量。
举一个例子来说明,假设有一个直径为300毫米的晶圆,而每个晶圆片的尺寸为5毫米。
那么根据上述公式计算,晶圆数
量为:
晶圆数量=(300^2*π)/(5^2)≈1130.97
所以,在这种情况下,晶圆的数量约为1131个。
需要注意
的是,这个公式是一个理论计算公式,在实际应用中可能存在
一些误差,因为还要考虑到边缘效应、晶圆不规则形状等因素。
因此,在实际应用中,还需要根据具体情况进行相应的修正和
调整。
晶圆出芯片计算方式
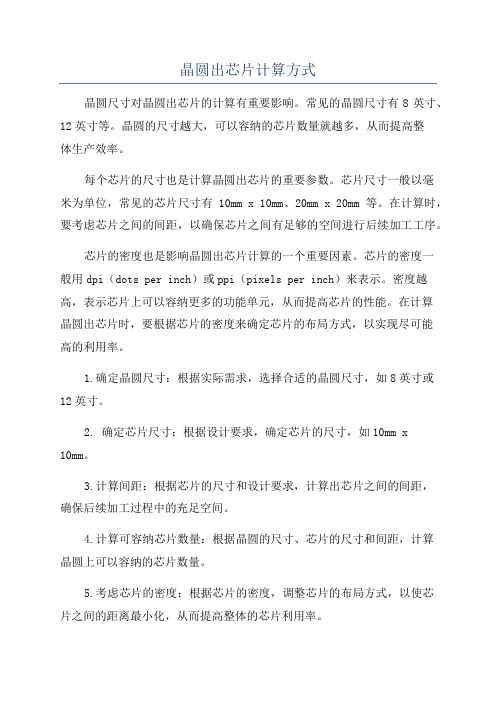
晶圆出芯片计算方式晶圆尺寸对晶圆出芯片的计算有重要影响。
常见的晶圆尺寸有8英寸、12英寸等。
晶圆的尺寸越大,可以容纳的芯片数量就越多,从而提高整体生产效率。
每个芯片的尺寸也是计算晶圆出芯片的重要参数。
芯片尺寸一般以毫米为单位,常见的芯片尺寸有10mm x 10mm、20mm x 20mm等。
在计算时,要考虑芯片之间的间距,以确保芯片之间有足够的空间进行后续加工工序。
芯片的密度也是影响晶圆出芯片计算的一个重要因素。
芯片的密度一般用dpi(dots per inch)或ppi(pixels per inch)来表示。
密度越高,表示芯片上可以容纳更多的功能单元,从而提高芯片的性能。
在计算晶圆出芯片时,要根据芯片的密度来确定芯片的布局方式,以实现尽可能高的利用率。
1.确定晶圆尺寸:根据实际需求,选择合适的晶圆尺寸,如8英寸或12英寸。
2. 确定芯片尺寸:根据设计要求,确定芯片的尺寸,如10mm x10mm。
3.计算间距:根据芯片的尺寸和设计要求,计算出芯片之间的间距,确保后续加工过程中的充足空间。
4.计算可容纳芯片数量:根据晶圆的尺寸、芯片的尺寸和间距,计算晶圆上可以容纳的芯片数量。
5.考虑芯片的密度:根据芯片的密度,调整芯片的布局方式,以使芯片之间的距离最小化,从而提高整体的芯片利用率。
6.改进设计:根据计算结果,可以对芯片的设计进行调整,以提高利用率和性能。
例如,可以优化芯片的布局方式,增加芯片的功能单元等。
在实际计算中,还需要考虑到晶圆制造的工艺因素,如切割线宽、切割原则等,以确保计算结果的准确性。
总之,晶圆出芯片的计算是一个复杂的过程,需要考虑到晶圆尺寸、芯片尺寸、密度等多个因素,并结合实际需求和工艺要求进行综合考虑,以达到最佳的效果。
通过合理的计算,可以提高晶圆的利用率,降低生产成本,提高半导体芯片的整体性能。
晶圆出芯片计算方式
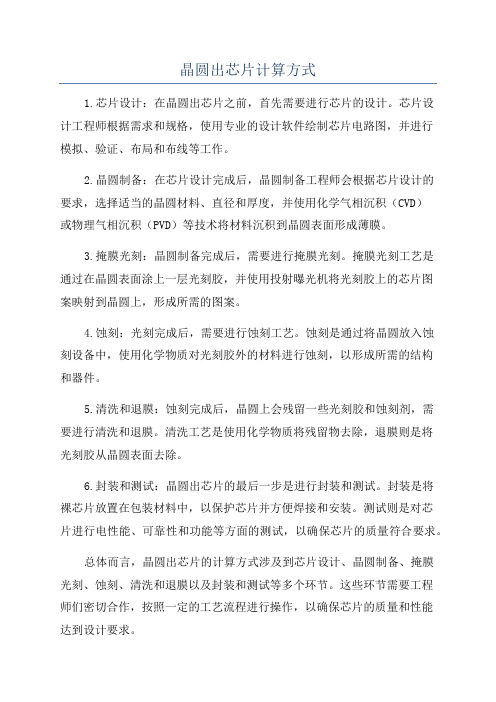
晶圆出芯片计算方式
1.芯片设计:在晶圆出芯片之前,首先需要进行芯片的设计。
芯片设
计工程师根据需求和规格,使用专业的设计软件绘制芯片电路图,并进行
模拟、验证、布局和布线等工作。
2.晶圆制备:在芯片设计完成后,晶圆制备工程师会根据芯片设计的
要求,选择适当的晶圆材料、直径和厚度,并使用化学气相沉积(CVD)
或物理气相沉积(PVD)等技术将材料沉积到晶圆表面形成薄膜。
3.掩膜光刻:晶圆制备完成后,需要进行掩膜光刻。
掩膜光刻工艺是
通过在晶圆表面涂上一层光刻胶,并使用投射曝光机将光刻胶上的芯片图
案映射到晶圆上,形成所需的图案。
4.蚀刻:光刻完成后,需要进行蚀刻工艺。
蚀刻是通过将晶圆放入蚀
刻设备中,使用化学物质对光刻胶外的材料进行蚀刻,以形成所需的结构
和器件。
5.清洗和退膜:蚀刻完成后,晶圆上会残留一些光刻胶和蚀刻剂,需
要进行清洗和退膜。
清洗工艺是使用化学物质将残留物去除,退膜则是将
光刻胶从晶圆表面去除。
6.封装和测试:晶圆出芯片的最后一步是进行封装和测试。
封装是将
裸芯片放置在包装材料中,以保护芯片并方便焊接和安装。
测试则是对芯
片进行电性能、可靠性和功能等方面的测试,以确保芯片的质量符合要求。
总体而言,晶圆出芯片的计算方式涉及到芯片设计、晶圆制备、掩膜
光刻、蚀刻、清洗和退膜以及封装和测试等多个环节。
这些环节需要工程
师们密切合作,按照一定的工艺流程进行操作,以确保芯片的质量和性能
达到设计要求。
不同尺寸芯片在同一片晶圆的切割方法
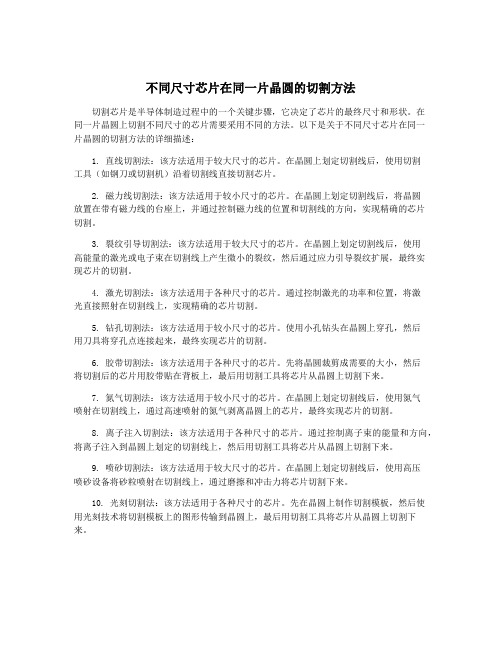
不同尺寸芯片在同一片晶圆的切割方法切割芯片是半导体制造过程中的一个关键步骤,它决定了芯片的最终尺寸和形状。
在同一片晶圆上切割不同尺寸的芯片需要采用不同的方法。
以下是关于不同尺寸芯片在同一片晶圆的切割方法的详细描述:1. 直线切割法:该方法适用于较大尺寸的芯片。
在晶圆上划定切割线后,使用切割工具(如钢刀或切割机)沿着切割线直接切割芯片。
2. 磁力线切割法:该方法适用于较小尺寸的芯片。
在晶圆上划定切割线后,将晶圆放置在带有磁力线的台座上,并通过控制磁力线的位置和切割线的方向,实现精确的芯片切割。
3. 裂纹引导切割法:该方法适用于较大尺寸的芯片。
在晶圆上划定切割线后,使用高能量的激光或电子束在切割线上产生微小的裂纹,然后通过应力引导裂纹扩展,最终实现芯片的切割。
4. 激光切割法:该方法适用于各种尺寸的芯片。
通过控制激光的功率和位置,将激光直接照射在切割线上,实现精确的芯片切割。
5. 钻孔切割法:该方法适用于较小尺寸的芯片。
使用小孔钻头在晶圆上穿孔,然后用刀具将穿孔点连接起来,最终实现芯片的切割。
6. 胶带切割法:该方法适用于各种尺寸的芯片。
先将晶圆裁剪成需要的大小,然后将切割后的芯片用胶带贴在背板上,最后用切割工具将芯片从晶圆上切割下来。
7. 氮气切割法:该方法适用于较小尺寸的芯片。
在晶圆上划定切割线后,使用氮气喷射在切割线上,通过高速喷射的氮气剥离晶圆上的芯片,最终实现芯片的切割。
8. 离子注入切割法:该方法适用于各种尺寸的芯片。
通过控制离子束的能量和方向,将离子注入到晶圆上划定的切割线上,然后用切割工具将芯片从晶圆上切割下来。
9. 喷砂切割法:该方法适用于较大尺寸的芯片。
在晶圆上划定切割线后,使用高压喷砂设备将砂粒喷射在切割线上,通过磨擦和冲击力将芯片切割下来。
10. 光刻切割法:该方法适用于各种尺寸的芯片。
先在晶圆上制作切割模板,然后使用光刻技术将切割模板上的图形传输到晶圆上,最后用切割工具将芯片从晶圆上切割下来。
- 1、下载文档前请自行甄别文档内容的完整性,平台不提供额外的编辑、内容补充、找答案等附加服务。
- 2、"仅部分预览"的文档,不可在线预览部分如存在完整性等问题,可反馈申请退款(可完整预览的文档不适用该条件!)。
- 3、如文档侵犯您的权益,请联系客服反馈,我们会尽快为您处理(人工客服工作时间:9:00-18:30)。
一片晶圆到底可以切割出多少的晶片数目
一片晶圆到底可以切割出多少的晶片数目?这个要根据你的die的大小和w 科普:wafer die chip的区别我们先从一片完整的晶圆(Wafer)说起:一块完整的wafer 名词解释:wafer 即为图片所示的晶圆,由纯硅(Si)构成。
一般分为6英寸、8英寸、12英寸规格不等,晶片就是基于这个wafer上生产出来的。
Wafer上的一个小块,就是一个晶片晶圆体,学名die,封装后就成为一个颗粒。
一片载有Nand Flash晶圆的wafer,wafer首先经过切割,然后die和wafer的关系品质合格的die切割下去后,原来的晶圆就成了下图的样子,就是挑剩下的Downgrade Flash Wafer。
筛选后的wafer这些残余的die,其实是品质不合格的晶圆。
被抠走的部分,也就是黑色的部分,是合格的die,会被原厂封装制作为成品NAND颗粒,而不合格的部分,也就是图中留下的部分则当做废品处理掉。
晶圆尺寸发展历史晶圆制造的流程一颗集成芯片供应商一般分为两大类:一类叫IDM,通俗理解就是集芯片设计、另一类叫Fabless,就是没有芯片加工厂的芯片供应商,Fabless 自己设计开发和推广销售芯片,与生产相关的业务外包给专业生产制造厂商,如与Fabless 相对应的是Foundry(晶圆代工厂)和封测厂,主要承接Fabless的生产和封装测试任务,典型的Foundry(晶圆代工厂)如台积电、格罗方德、中芯国际、台联电等,封测厂有日月光,江苏长电等。
一片晶圆到底可以切割出多少的晶片数目?目前业界所谓的6寸,12寸还是18寸晶圆其实就是晶圆直径的简称,只不过这个吋是估算值。
实际上的晶圆直径是分为150mm,300mm以及450mm这三种,而12吋约等于305mm,为了称呼方便所以称之为12吋晶圆。
国际上Fab厂通用的计算公式:聪明的读者们一定有发现公式中π*(晶圆直径/2)的平方不就是圆面积的式子吗?再将公式化简的话就会变成:X就是所谓的晶圆可切割晶片数(dpw die per wafer)。
那麽要来考考各位的计算能力了育!假设12吋晶圆每片造价5000美金,那麽NVIDIA最新力作GT200的晶片大小为576平方公厘,在良率50%的情况下,平均每颗成本是多少美金?。