刀具的切削三要素与加工效率
切削用量三要素计算公式

切削用量三要素计算公式切削用量三要素计算公式是指在切削过程中,根据切削速度、进给速度和切削深度来计算切削用量的公式。
切削用量是切削过程中切除材料或切削液的量,是衡量切削过程中切削效果的一个重要指标。
在切削加工过程中,切削用量的合理控制对于提高切削效果、延长刀具寿命和提高加工效率都起到至关重要的作用。
切削用量三要素包括切削速度、进给速度和切削深度。
切削速度是指刀具与工件相对运动的速度,单位通常是m/min。
进给速度是指切削刃每转一周,工件上移动的距离,单位通常是mm/rev。
切削深度是指刀具切削刃在一个工件上的进入深度,单位通常是mm。
切削用量的计算公式为:切削用量=切削速度×进给速度×切削深度切削用量的计算公式可以根据不同的切削形式和加工要求进行调整。
下面将分别介绍一些常用的切削用量计算公式。
1.对于铣削加工:切削用量=切削宽度×进给速度×加工长度其中,切削宽度是指铣刀径向切削刀具之间的距离,通常是成刀具直径的倍数。
2.对于车削加工:切削用量=切削深度×进给速度×加工长度其中,切削深度是指刀具在工件中切削的最大深度。
3.对于钻削加工:切削用量=钻孔直径×进给速度×加工长度其中,钻孔直径是指钻头直径,进给速度是指每转一周,工件上移动的距离。
4.对于镗削加工:切削用量=镗孔直径×进给速度×加工长度其中,镗孔直径是指镗刀直径。
需要注意的是,切削用量的计算公式只是一个理论值,实际加工时往往需要根据具体材料性质、刀具情况、工件形状和加工要求等因素进行适当调整。
切削用量的合理选取对于加工质量的影响非常大。
合理的切削用量可以确保工件表面质量良好,避免切削过程中产生过大的切削力和切削热量,减少工件表面的热影响区,避免刀具磨损过快和强制振动的产生,提高切削效率和工件精度。
因此,在选择切削用量时应充分考虑刀具材料、刀具形状、刀具刃数、切削方式、切削速度和切削深度等因素,并根据实际情况进行调整。
切削用量三要素

切削用量三要素在机械加工过程中,切削用量是影响切削加工质量和生产效率的重要因素之一。
正确的切削用量选择可以提高切削工具的寿命,减少切屑生成,确保加工质量和提高生产效率。
切削用量的选择与切削速度、进给速度和切削深度等因素密切相关,这三个要素可以被认为是切削用量的决定因素。
一、切削速度切削速度是切削用量中最直接影响切削加工的因素之一。
切削速度的选择应考虑切削材料的硬度、切削工具的材料和形状、切削液的冷却效果等因素。
通常情况下,切削速度过高会导致切削工具的快速磨损,增加切削工具的更换次数和维护成本;而切削速度过低则会降低生产效率。
因此,在实际加工过程中,需要合理选择切削速度,以确保切削加工的效果和经济性。
二、进给速度进给速度是指切削工具在单位时间内切削工件的移动速度。
进给速度的选择应综合考虑切削材料的硬度、切削工具的材料和形状、工件表面质量要求等因素。
进给速度过高会导致切削工具与工件之间的磨擦增加,容易引起工件表面质量的损坏;而进给速度过低则会降低生产效率。
因此,在实际加工过程中,需要根据具体情况选择合适的进给速度,以确保加工质量和生产效率。
三、切削深度切削深度是指切削工具切削工件的深度。
切削深度的选择应综合考虑切削工具的结构和刚度、切削材料的硬度、工件的形状和材料等因素。
切削深度过大会导致切削力和切削温度的增加,容易引起切削工具的磨损和断刀现象;而切削深度过小则会降低生产效率。
因此,在实际加工过程中,需要根据具体情况选择合适的切削深度,以确保切削加工的质量和经济性。
综上所述,切削用量的选择应综合考虑切削速度、进给速度和切削深度等三个要素。
合理选择这三个要素可以提高切削工具的寿命,减少切屑的生成,确保加工质量和提高生产效率。
在实际加工过程中,需要根据具体情况进行调整和优化,以达到最佳的切削效果。
切削用量三要素的定义及公式

切削用量三要素的定义及公式好的,以下是为您生成的关于“切削用量三要素的定义及公式”的文章:在咱们日常的机械加工领域中,切削用量三要素那可是相当重要的角色。
这就好比是烹饪中的盐、糖和酱油,用量合适,才能做出美味的菜肴;在机械加工里,切削用量三要素调配恰当,才能加工出合格又精致的零件。
咱先来说说切削速度,这可是三要素中的“速度担当”。
切削速度就是刀具切削刃上选定点相对于工件的主运动的瞬时速度。
想象一下,你拿着一把锋利的刀,快速地在一块木头上划过,这个划过的速度就是切削速度。
公式是 v = πdn/1000 ,这里的 v 表示切削速度,d 是工件待加工表面或刀具的最大直径,n 是主运动的转速。
给您举个小例子吧,我之前在工厂实习的时候,有一次师傅让我加工一个圆柱形的零件。
我一开始没太注意切削速度,就按照自己的想法随便调了机器的转速。
结果呢,加工出来的零件表面那叫一个粗糙,简直没法看。
师傅过来一看,就指出是切削速度不对。
后来在师傅的指导下,我重新计算并调整了切削速度,加工出来的零件那表面光滑得跟镜子似的,我当时心里那个美啊!接下来聊聊进给量,它就像是你一步一步往前走的步伐大小。
进给量是刀具在进给运动方向上相对工件的位移量。
用 f 来表示,单位通常是 mm/r 或者 mm/行程。
比如说车床上车削螺纹,每转一圈刀具沿着轴向移动的距离就是进给量。
有一回,我们车间接到一个紧急订单,要加工一批细小的轴类零件。
我负责其中一部分,为了赶进度,我把进给量调得过大。
结果零件的尺寸偏差超出了允许范围,差点就造成了损失。
这让我深刻认识到,进给量可不能随意乱调,得根据具体的加工要求来。
最后说说背吃刀量,这是刀具切入工件的深度。
就好比你切西瓜,切下去的厚度就是背吃刀量。
用 ap 表示,单位是 mm 。
记得有一次,我在加工一个比较厚的金属板,一开始背吃刀量设置得太小,加工效率特别低,半天也没弄出个样子来。
后来我大胆地增加了背吃刀量,效率一下子就提上去了,但同时也要注意刀具的承受能力,不能一味地加大,不然刀具可能会受损。
车工切削三要素

(2)试车后背吃刀量ap=(dw - dm)/2 =(28.4 -24) /2 =2.2mm
手柄应转的格数为:2.2/0.05=44格
(2).进给量f
工件每转一转时,车刀在进给运动方向上移动的距离 叫进给量,用(f)表示,单位是mm/r(也叫每转进给量) 。
二、如果加工直径为20mm,长度40mm的台阶轴是选 择进给量为0.2mm/r。 问主轴需要旋转多少格完成加工?
三、直径为31mm,长度为100mm的半精加工零件,现 在需要加工成直径为30mm,长度为100mm的轴。 问:1、背吃刀量是多少?中滑板手柄转动一格,刀架 前进0.02mm,需要多少格? 2、选择进给量为0.15mm/r,主轴需要旋转多少转完成? 3、如果使用转速为800r/min,切削速度是多少?
二:车削运功和切削用量
1. 切削运动
刀具与工件间的相对运动称为切削运动, 切削运动可分为主运动和进给运动。
(1)主运动 车削时形成切削速度的运动叫主运动。工件的旋
转运动就是主运动。
(2)进给运动 使工件多余材料不断被车去的运动叫进给运动。车外圆
是纵向进给运动,车端面、切断、车槽是横向进给运动。
2、车削时工件上形成的表面
纵向进给量 进给量
横向进给量
沿床身导轨方向
与车身导轨方 向垂直
3、切削速度V
主运动的线速度叫切削速度,单位为m/min。 车削外圆时的切削速度计算公式为:
V=πdwn/1000
其中: dw—工件待加工表面的直径,(mm);
n—工件的转速,(r/min); V —切削速度,( m/min)。
例3:车削直径为300mm的铸铁带轮外圆, 若切削速度为60m/ min,试求车床主轴转速。
车工切削三要素

主运动 进给运动
3. 切削用量
切削用量(又叫切削三要素)是衡量车削运动大小的参数。 它包括背吃刀量、进给量、切削速度。
(1) 背吃刀量ap
对于外圆车削,背吃刀量为工件上已加工表面 和待加工表面间的垂直距离,单位为mm。即: ap=(dw-dm)/2 其中: dw—工件待加工表面的直径,(mm);
解:根据公式V=πdn/1000 得:n=1000V/ πd
=1000 ×60/3.14 ×300 =63.69r/min
注意:在实际生产中,理论上计算出的主轴转 数应从车床转速表中最接近的一档选取。
作业:
一、现有直径为45mm的棒料,要求加工成直径为 40mm的光轴。 问:如果一次完成外圆加工,则背吃刀量的大小 是多少?
与车身导轨方 向垂直
3、切削速度V
主运动的线速度叫切削速度,单位为m/min。 车削外圆时的切削速度计算公式为:
V=πdwn/1000
其中: dw—工件待加工表面的直径,(mm);
n—工件的转速,(r/min); V —切削速度,( m/带轮外圆, 若切削速度为60m/ min,试求车床主轴转速。
(2)试车后背吃刀量ap=(dw - dm)/2 =(28.4 -24) /2 =2.2mm
手柄应转的格数为:2.2/0.05=44格
(2).进给量f
工件每转一转时,车刀在进给运动方向上移动的距离 叫进给量,用(f)表示,单位是mm/r(也叫每转进给量) 。
纵向进给量 进给量
横向进给量
沿床身导轨方向
车工切削三要素
(2)进给运动 使工件多余材料不断被车去的运动叫进给运动。车外圆
是纵向进给运动,车端面、切断、车槽是横向进给运动。
2、车削时工件上形成的表面
简要说明切削用量的含义及其三要素

简要说明切削用量的含义及其三要素切削用量,这个词听起来挺专业的,其实说白了就是在加工材料的时候,我们所用到的各种量度。
想象一下吧,就像我们在厨房做饭时,切菜的厚度、火候的掌控、调料的用量,都是影响成品的重要因素。
切削用量也是一样,里面有几个关键的要素,分别是切削深度、进给量和切削速度。
来,咱们一个个聊聊。
切削深度。
这个就像你在切西瓜时,一刀下去切多深,直接影响到你能不能一口吃到心仪的果肉。
深了,西瓜汁四溅;浅了,吃得心里总觉得没满足感。
在加工中,切削深度指的是刀具进入工件的深度。
深度适中,能让材料有效去除,效率提升;要是太深,刀具就容易磨损,甚至崩裂,哎呀,那就得不偿失了。
想象一下,一个厨师在切牛排时,刀子如果扎得太深,那牛排就容易变成碎片,简直是悲剧。
然后是进给量。
这玩意儿可有意思了,想象一下你吃面条,吃得快了,肚子饱了,吃得慢了,可能会觉得不够。
进给量就是在单位时间内,刀具移动的距离。
说白了就是切削的速度。
快了,效率高,但可能会导致切削不够干净;慢了呢,又浪费时间。
就像你跑步,如果一步迈得太大,容易摔跤;如果一步迈得太小,没法跑起来。
找到一个合适的进给量,才能达到最佳的加工效果。
咱们得说说切削速度。
这就像你开车一样,速度快了,路上风景飞速而过,慢了呢,感觉都快睡着了。
在切削过程中,切削速度就是刀具相对于工件的移动速度。
这个速度过高,刀具容易发热,磨损加快;过低呢,又影响加工效率。
就像你看一场电影,节奏快了,情节就紧凑;节奏慢了,可能会让人昏昏欲睡。
合适的切削速度,才能让加工过程流畅。
为什么切削用量这么重要呢?因为这直接关系到加工质量、效率和刀具寿命。
要是切削用量设定得当,那简直是如鱼得水,事半功倍。
可要是搞错了,哎呀,刀具磨损得飞快,甚至整个加工流程都得停下来重新调整,浪费了时间和成本,真是“得不偿失”。
实际上,掌握好这三要素,就像是掌握了一门绝活。
想象一下,那个老厨师在厨房里,一边切菜一边聊家常,动作流畅,切出来的每片菜都是完美的厚度,火候恰到好处,那画面多美。
切削三要素
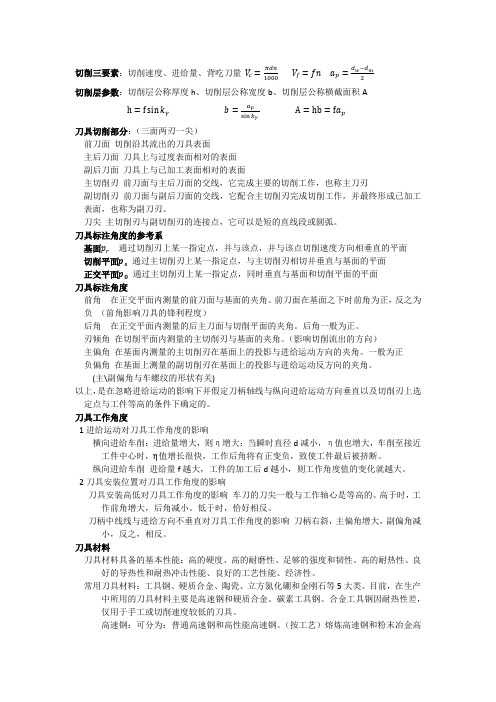
切削三要素:切削速度、进给量、背吃刀量 V c=πdn1000 V f=fn a p=d w−d m2切削层参数:切削层公称厚度h、切削层公称宽度b、切削层公称横截面积Ah=f sin kγ b=a psin kγA=hb=fa p刀具切削部分:(三面两刃一尖)前刀面切削沿其流出的刀具表面主后刀面刀具上与过度表面相对的表面副后刀面刀具上与已加工表面相对的表面主切削刃前刀面与主后刀面的交线,它完成主要的切削工作,也称主刀刃副切削刃前刀面与副后刀面的交线,它配合主切削刃完成切削工作,并最终形成已加工表面,也称为副刀刃。
刀尖主切削刃与副切削刃的连接点,它可以是短的直线段或圆弧。
刀具标注角度的参考系基面p r通过切削刃上某一指定点,并与该点,并与该点切削速度方向相垂直的平面切削平面p s通过主切削刃上某一指定点,与主切削刃相切并垂直与基面的平面正交平面p0通过主切削刃上某一指定点,同时垂直与基面和切削平面的平面刀具标注角度前角在正交平面内测量的前刀面与基面的夹角。
前刀面在基面之下时前角为正,反之为负(前角影响刀具的锋利程度)后角在正交平面内测量的后主刀面与切削平面的夹角。
后角一般为正。
刃倾角在切削平面内测量的主切削刃与基面的夹角。
(影响切削流出的方向)主偏角在基面内测量的主切削刃在基面上的投影与进给运动方向的夹角。
一般为正负偏角在基面上测量的副切削刃在基面上的投影与进给运动反方向的夹角。
(主\副偏角与车螺纹的形状有关)以上,是在忽略进给运动的影响下并假定刀柄轴线与纵向进给运动方向垂直以及切削刃上选定点与工件等高的条件下确定的。
刀具工作角度1进给运动对刀具工作角度的影响横向进给车削:进给量增大,则η增大;当瞬时直径d减小,η值也增大,车削至接近工件中心时,η值增长很快,工作后角将有正变负,致使工件最后被挤断。
纵向进给车削进给量f越大,工件的加工后d越小,则工作角度值的变化就越大。
2刀具安装位置对刀具工作角度的影响刀具安装高低对刀具工作角度的影响车刀的刀尖一般与工作轴心是等高的。
切削用量的含义及其三要素
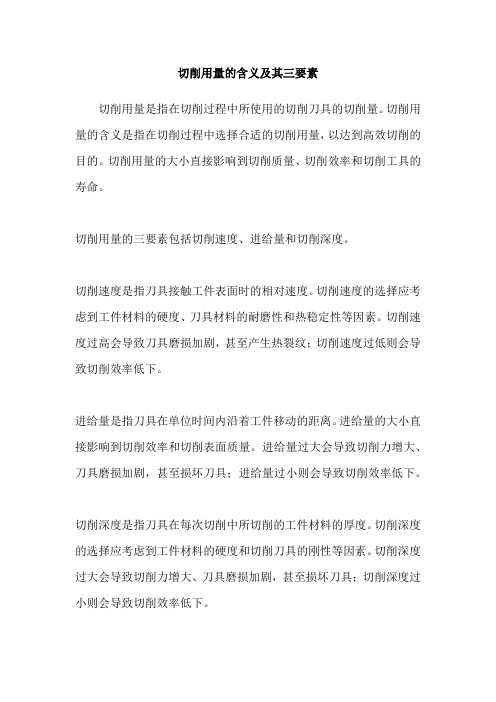
切削用量的含义及其三要素
切削用量是指在切削过程中所使用的切削刀具的切削量。
切削用量的含义是指在切削过程中选择合适的切削用量,以达到高效切削的目的。
切削用量的大小直接影响到切削质量、切削效率和切削工具的寿命。
切削用量的三要素包括切削速度、进给量和切削深度。
切削速度是指刀具接触工件表面时的相对速度。
切削速度的选择应考虑到工件材料的硬度、刀具材料的耐磨性和热稳定性等因素。
切削速度过高会导致刀具磨损加剧,甚至产生热裂纹;切削速度过低则会导致切削效率低下。
进给量是指刀具在单位时间内沿着工件移动的距离。
进给量的大小直接影响到切削效率和切削表面质量。
进给量过大会导致切削力增大、刀具磨损加剧,甚至损坏刀具;进给量过小则会导致切削效率低下。
切削深度是指刀具在每次切削中所切削的工件材料的厚度。
切削深度的选择应考虑到工件材料的硬度和切削刀具的刚性等因素。
切削深度过大会导致切削力增大、刀具磨损加剧,甚至损坏刀具;切削深度过小则会导致切削效率低下。
在实际应用中,切削用量的选择需要综合考虑以上三要素,并根据具体情况进行合理调整。
切削用量的过程是一个不断试验、调整和优化的过程,需要根据实际情况进行实验和经验总结,以达到最佳的切削效果。
同时,随着数控技术的发展,切削用量的选择也越来越多地依赖于数控系统的自动计算和优化。
切削三要素计算公式【终于全了】

金属切削技能在机械加工中是一个基本的技能,也是很多机械加工人常常挂在嘴边的一个词,虽然金属切削技能很基本,但是深入了解金属切削后你会发现里面的学问还真的很多,不少数控车床的操作者,对车床的切削原理知道得很少,常常不知道如何正确选择主轴转速S、进刀量F,以及进刀的深度,即切削三要素的计算公式,希望这篇文章能对他们有所帮助。
众说周知,提高加工效率时,提高切削三要素(切削线速度,吃刀深度,进给量)是最简单、最直接的方法。
但刀具切削三要素的提高,一般会受到现有机床设别条件的限制。
在切削三要素的确定法则:依次确定吃刀深度,进给量以及切削线速度。
吃刀深度一般根据加工余量确定,粗加工进给量根据机床功率确定,精加工进给量根据表面粗糙度确定;切削线速度根据刀具材质和机床主轴转速确定。
主轴转速S、进刀量F,进刀的深度,在切削原理课程中称为切削加工三要素,如何正确选择这三个要素是金属切削原理课程的一个主要内容,我这里想尽可能简单地介绍一下选择这三个要素的基本原则:(一) 切削速度(线速度、园周速度)V(米/分)要选择主轴每分钟转数,必须首先知道切削线速度V应该取多少。
V的选择:取决于刀具材料、工件材料、加工条件等。
刀具材料:硬质合金,V可以取得较高,一般可取100米/分以上,一般购置刀片时都提供了技术参数:加工什么材料时可选择多少大的线速度。
高速钢:V只能取得较低,一般不超过70米/分,多数情况下取20~30米/分以下。
工件材料:硬度高,V取低;铸铁,V取低,刀具材料为硬质合金时可取70~80米/分;低碳钢,V可取100米/分以上,有色金属,V可取更高些(100~200米/分).淬火钢、不锈钢,V 应取低一些。
加工条件:粗加工,V取低一些;精加工,V取高些。
机床、工件、刀具的刚性系统差,V取低。
如果数控程序使用的S是每分钟主轴转数,那么应根据工件直径,及切削线速度V计算出S:S(主轴每分钟转数)=V(切削线速度)*1000/(3.1416*工件直径)如果数控程序使用了恒线速,那么S可直接使用切削线速度V(米/分)(二)进刀量(走刀量)F主要取决于工件加工表面粗糙度要求。
桥式镗刀切削三要素

桥式镗刀切削三要素提高加工效率时,提高切削三要素(切削速度,吃刀深度,进给量)是最简单、最直接的方法。
但刀具切削三要素的提高,一般会受到现有机床设别条件的限制。
所以最廉价的办法就是选好刀具材质。
在切削三要素的确定法则:依次确定吃刀深度,进给量以及切削线速度。
吃刀深度一般根据加工余量确定,粗加工进给量根据机床功率确定,精加工进给量根据表面粗糙度确定;切削线速度根据刀具材质和机床主轴转速确定。
从提高加工效率的角度来考虑,增加切深恐怕是非常值得考虑的一个方法。
其重要原因之一,是实验表明,切削深度一旦等于进给的10倍,再增加切深对刀具耐用度的影响将极小。
而如果是提高切削速度,改变切削速度会使刀具耐用度以近两倍的速度变化;如果改变进给,也可使刀具耐用度有大致相等的改变。
因此,在我们大批量生产模式的毛坯还不能实现所谓“净尺寸化”的时候,提高切深是既能实现高效率的生产节拍,又不致使刀具费用大幅度上升的一个两全其美的选择。
硬质合金刀具是目前刀具市场的主流刀具,大家对此刀具都很熟悉,可以根据实际加工现场情况调整硬质合金刀具的切削三要素,从而最大化的保证刀具寿命和加工效率,但立方氮化硼刀具发展时间不长,很多人没接触过此类刀具,但随着硬材料和难加工材料的出现,立方氮化硼刀具也逐渐出现在大家的视野。
但很多人经常认为立方氮化硼刀具只局限于高速切削,和精加工工序。
其实不然,随着超硬材料刀具行业的不断研发和创新,目前立方氮化硼刀具已广泛应用于粗加工工序和断续切削工况中。
立方氮化硼刀具的选型和硬质合金刀具是一样的,根据不同工件材质,选择不同刀具牌号及刀具结构形式。
用于精加工工序的一般是复合焊接式立方氮化硼刀片,它只有刃口部位是立方氮化硼材料,基体还是硬质合金基体,吃刀深度控制在0.5mm以内,所以只能用于精加工工序,而对于余量较大,表面不规整的则选择整体式立方氮化硼刀片,通体都是立方氮化硼材质,吃刀深度在1-10mm之前,刀具寿命一般在3小时/刃口。
数控车切削三要素
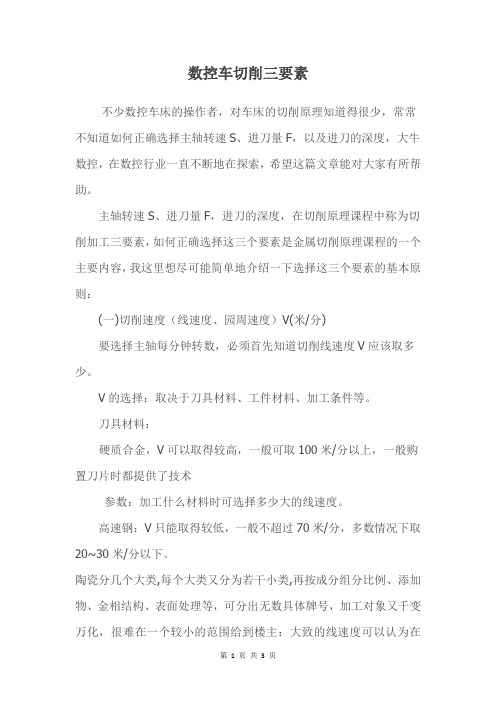
数控车切削三要素不少数控车床的操作者,对车床的切削原理知道得很少,常常不知道如何正确选择主轴转速S、进刀量F,以及进刀的深度,大牛数控,在数控行业一直不断地在探索,希望这篇文章能对大家有所帮助。
主轴转速S、进刀量F,进刀的深度,在切削原理课程中称为切削加工三要素,如何正确选择这三个要素是金属切削原理课程的一个主要内容,我这里想尽可能简单地介绍一下选择这三个要素的基本原则:(一)切削速度(线速度、园周速度)V(米/分)要选择主轴每分钟转数,必须首先知道切削线速度V应该取多少。
V的选择:取决于刀具材料、工件材料、加工条件等。
刀具材料:硬质合金,V可以取得较高,一般可取100米/分以上,一般购置刀片时都提供了技术参数:加工什么材料时可选择多少大的线速度。
高速钢:V只能取得较低,一般不超过70米/分,多数情况下取20~30米/分以下。
陶瓷分几个大类,每个大类又分为若干小类,再按成分组分比例、添加物、金相结构、表面处理等,可分出无数具体牌号,加工对象又千变万化,很难在一个较小的范围给到楼主:大致的线速度可以认为在200~1200m/min的范围之内。
工件材料:硬度高,V取低;铸铁,V取低,刀具材料为硬质合金时可取70~80米/分;低碳钢,V可取100米/分以上,有色金属,V可取更高些(100~200米/分).淬火钢、不锈钢,V应取低一些。
加工条件:粗加工,V取低一些;精加工,V取高些。
机床、工件、刀具的刚性系统差,V取低。
如果数控程序使用的S是每分钟主轴转数,那么应根据工件直径,及切削线速度V计算出S:S(主轴每分钟转数)=V(切削线速度)*1000/(3.1416*工件直径)如果数控程序使用了恒线速,那么S可直接使用切削线速度V(米/分)(二)进刀量(走刀量)F主要取决于工件加工表面粗糙度要求。
精加工时,表面要求高,走刀量取小:0.06~0.12mm/主轴每转。
粗加工时,可取大一些。
主要决定于刀具强度,一般可取0.3以上,刀具主后角较大时刀具强度差,进刀量不能太大。
切削三要素及选择原则

切削三要素及选择原则1.切削速度:切削速度是指工件或刀具在切削过程中的相对运动速度。
切削速度的选择直接关系到切削加工的效率和刀具寿命。
一般来说,切削速度越高,切削效率越高,但也会对刀具造成磨损和损坏的风险。
因此,在选择切削速度时需要综合考虑刀具材料、工件材料、刀具结构和切削液等因素,以保证切削过程的稳定性和刀具的寿命。
2.切削深度:切削深度是指切削刀具进入工件的距离。
切削深度的选择会影响到加工后的工件表面质量和加工效率。
一般来说,切削深度越大,加工效率越高,但也会对刀具产生较大的负荷和热量,对刀具寿命造成影响。
因此,在选择切削深度时需要根据刀具的刚度和强度,合理确定切削深度,以保证切削过程的稳定性和刀具的寿命。
3.进给量:进给量是指切削过程中刀具在单位时间内沿工件表面的移动量。
进给量的选择会影响到加工后工件表面的光洁度和形状精度。
一般来说,进给量越大,加工速度越快,但也会增加切削过程中的振动和噪声,并可能导致工件表面质量下降。
因此,在选择进给量时需要考虑工件材料和形状、刀具尺寸和结构等因素,以保证加工后的工件表面质量和形状精度。
1.刀具供给条件:切削三要素的选择首先要满足刀具的供给条件。
根据刀具的特性和材料,确定切削速度、切削深度和进给量的范围,以保证切削过程的稳定性和刀具的寿命。
2.工件要求:根据工件的材料和加工要求,选择适当的切削速度、切削深度和进给量。
不同的工件材料和加工要求对切削三要素的选择有不同的要求,需要根据具体情况进行综合考虑。
3.加工效率:切削三要素的选择还要考虑加工效率。
在满足刀具供给条件和工件要求的前提下,选择合适的切削速度、切削深度和进给量,以提高加工效率,降低生产成本。
4.刀具寿命:切削三要素的选择还要考虑刀具寿命。
合理选择切削速度、切削深度和进给量,避免过高或过低,以延长刀具的使用寿命,并降低更换刀具的频率和成本。
5.加工稳定性:切削三要素的选择还要保证加工过程的稳定性。
车工切削三要素

(2).进给量f
工件每转一转时,车刀在进给运动方向上移动的距离 叫进给量,用(f)表示,单位是mm/r(也叫每转进给量) 。
进给量
纵向进给量 横向进给量
沿床身导轨方向 与车身导轨方 向垂直
3、切削速度V
主运动的线速度叫切削速度,单位为m/min。 车削外圆时的切削速度计算公式为:
V=πdwn/1000
注意:切断、车槽时的背吃刀量为车刀主切削刃的宽度 图
例1:要将直径为30mm的轴一刀车至24mm,试问 切削深度是多少?若试车时测得直径为28.4mm, 这时中拖板(每格为0.05mm)手柄应转多少格? 解:(1)背吃刀量ap=(dw - dm)/2 =(30-24)/2
=3mm
(2)试车后背吃刀量ap=(dw - dm)/2 =(28.4 -24) /2 =2.2mm 手柄应转的格数为:2.2/0.05=44格
二:车削运功和切削用量
1. 切削运动
刀具与工件间的相对运动称为切削运动,
切削运动可分为主运动和进给运动。
(1)主运动
车削时形成切削速度的运动叫主运动。工件的旋
转运动就是主运动。
(2)进给运动 使工件多余材料不断被车去的运动叫进给运动。车外圆
是纵向进给运动,车端面、切断、车槽是横向论上计算出的主轴转 数应从车床转速表中最接近的一档选取。
作业:
一、现有直径为45mm的棒料,要求加工成直径为 40mm的光轴。 问:如果一次完成外圆加工,那么背吃刀量的大 小是多少?
二、如果加工直径为20mm,长度40mm的台阶轴是选 择进给量为0.2mm/r。
问主轴需要旋转多少格完成加工?
其中: dw—工件待加工表面的直径,(mm);
n—工件的转速,(r/min); V —切削速度,( m/min)。
车削用量的三要素是什么

车削用量的三要素是什么
切削用量
定义:是指切削速度、进给量和切削深度三者的总称,这三者又称切削用量三要素。
切削速度v:在切削加工中,刀刃上选定点相对于工件的主运动速度。
v = πdn / 1000 ( m / min )
式中d --- 完成主运动的刀具或工件的最大直径(mm)
n --- 主运动的转速(r / min)
进给量f:工件或刀具的主运动每转或每双行程时,工件和刀具在进给运动中的相对位移量。
vf = n * f (mm / min)
切削深度ap:等于工件已加工表面与待加工表面间的垂直距。
对于外圆车削
ap = (dw - dm) / 2 (mm)
对于钻孔
ap = dm / 2 (mm)
式中dw --- 工件加工前直径(mm);dm --- 工件加工后直径(mm)。
简述切削三要素

简述切削三要素1. 嘿,机械小伙伴们!今天咱们来聊一个特别有意思的话题——切削三要素!说起这个,那可是加工界的"铁三角",就像是厨师炒菜的火候、调料和刀工一样重要!2. 切削速度就像是"快刀侠"的绝技!它说的就是刀具和工件打照面时的速度。
你想啊,速度太慢,加工效率低,跟蜗牛似的;速度太快,刀具容易发烫变钝,这可都不是咱们想要的!3. 我给大家打个比方,切削速度就像是骑自行车,太慢了累死人不说,还容易摔倒;太快了又容易翻车。
所以啊,得掌握好这个度,这样工件才能加工得又快又好!4. 进给量可是个有意思的东西!它就像是切菜时刀的进给深度。
你看那些大厨切菜,每一刀进给量都拿捏得死死的,切出来的菜才能整整齐齐。
咱们的刀具也是这个道理,进给量把握好了,加工出来的工件表面才会光滑得跟镜子似的!5. 要是进给量太大,那工件表面就跟波浪似的,凹凸不平;太小呢,效率又上不去,这可真是让人犯愁。
所以啊,这个进给量就得像大厨切菜一样,讲究个"恰到好处"!6. 切削深度简直就是"深度控"!它决定着每次切削能吃进去多少料。
这个深度要是控制得好,工件加工起来就特别带劲;控制不好,不是把刀具崩了,就是把工件毁了。
7. 我觉得切削深度就像是吃饭,一口吃太多容易噎着,吃太少又填不饱肚子。
所以这个深度啊,得根据工件材料、刀具强度来定,这样才能又高效又安全!8. 这三个要素之间的关系可有意思了!它们就像是"三个臭皮匠",谁也离不开谁。
速度要是快了,进给量和切削深度就得适当降低;要是想加大切削深度,速度和进给量可能就得放慢点。
9. 你看啊,这三要素配合起来,简直就像是在跳华尔兹,得配合得天衣无缝才行。
要是哪个节奏不对,那加工质量立马就露馅了!10. 在实际操作中,这三要素就像是"调味三件套"。
有时候要突出效率,那就得加快速度;有时候要求表面质量好,那就得控制进给;有时候要求加工余量大,那就得加大深度。
加工元件的三要素

加工元件的三要素
加工元件的三要素是切削速度、进给量和切削深度,它们在加工过程中起着至关重要的作用。
首先,切削速度是指刀具切削刃上选定点相对于工件待加工表面在主运动方向上的瞬时速度,是决定加工效率的重要因素。
切削速度的提高,可以缩短切削时间,提高加工效率,但同时也对刀具的磨损和加工质量产生影响。
因此,需要根据实际情况选择合适的切削速度,以平衡加工效率和加工质量的关系。
其次,进给量是指刀具在进给运动方向上相对于工件的位移量。
进给量的大小直接影响切削厚度和切削面积,进而影响切削力和切削热。
较小的进给量可以使切削更为轻快,减少刀具磨损,提高加工精度;较大的进给量则可以缩短切削时间,提高加工效率。
因此,需要根据工件材料、刀具材料和加工要求选择合适的进给量。
最后,切削深度是指切削层在基面上的尺寸,即工件上待加工表面的上一层在垂直于主轴轴线方向的相对位移。
切削深度的大小直接影响切削力和切削热,进而影响刀具的寿命和加工质量。
较小的切削深度可以使切削更为轻快,减少刀具磨损;较大的切削深度则可以提高加工效率。
因此,需要根据工件材料、刀具材料和加工要求选择合适的切削深度。
综上所述,加工元件的三要素是相互影响、相互制约的。
在实际加工过程中,需要根据具体情况综合考虑三要素的影响,选择合适的参数组合,以达到最佳的加工效果。
- 1、下载文档前请自行甄别文档内容的完整性,平台不提供额外的编辑、内容补充、找答案等附加服务。
- 2、"仅部分预览"的文档,不可在线预览部分如存在完整性等问题,可反馈申请退款(可完整预览的文档不适用该条件!)。
- 3、如文档侵犯您的权益,请联系客服反馈,我们会尽快为您处理(人工客服工作时间:9:00-18:30)。
刀具的切削三要素与加工效率
众说周知,提高加工效率时,提高切削三要素(切削线速度,吃刀深度,进给量)是最简单、最直接的方法。
但刀具切削三要素的提高,一般会受到现有机床设别条件的限制。
所以最廉价的办法就是选好刀具材质。
在切削三要素的确定法则:依次确定吃刀深度,进给量以及切削线速度。
吃刀深度一般根据加工余量确定,粗加工进给量根据机床功率确定,精加工进给量根据表面粗糙度确定;切削线速度根据刀具材质和机床主轴转速确定。
从提高加工效率的角度来考虑,增加切深恐怕是非常值得考虑的一个方法。
其重要原因之一,是实验表明,切削深度一旦等于进给的10倍,再增加切深对刀具耐用度的影响将极小。
而如果是提高切削速度,改变切削速度会使刀具耐用度以近两倍的速度变化;如果改变进给,也可使刀具耐用度有大致相等的改变。
因此,在我们大批量生产模式的毛坯还不能实现所谓“净尺寸化”的时候,提高切深是既能实现高效率的生产节拍,又不致使刀具费用大幅度上升的一个两全其美的选择。
立方氮化硼刀具的切削参数误区,大家一致认为立方氮化硼刀具只局限于高速切削,只能精加工。
立方氮化硼刀具应用于粗加工领域的案例如下:
1,加工灰铸铁
BN-S20牌号立方氮化硼刀具在粗加工灰铸铁时遇到夹砂,白口不崩刃!吃刀深度为2-3.5mm(根据实际加工余量),寿命是日本某品牌硬质合金刀具的15倍,效率提高1倍!
3,高锰钢,高铬铸铁,冷硬铸铁等难加工铸件。
铸件表面夹砂、气孔较多,原来
用硬质合金刀具加工,容易崩刃造成
刀具损耗严重加工成本高且效率低
下。
用BN-S20牌号整体式CBN刀具
加工,参数如下:
吃到深ap=2-3.5mm;走刀量
Fr=0.25mm/r;线速度v=85m/min 。
刀具耐用度:3小时/刃口。
随着立方氮化硼刀具方面的研究进展和加工中的实际需要,从原来的高速精加工,发展到可断续,可粗加工半精加工,亦可在普通机床中应用;使用成本也更经济实惠。