新型车身涂装输送设备
汽车涂装线用摆杆输送机
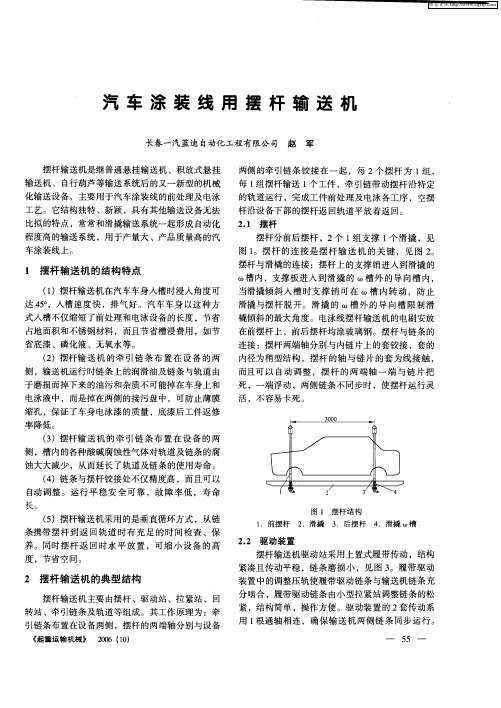
省底漆 、磷化液、无氧水等。 ()摆杆输 送机 的牵引链 条布置在 设备 的两 2 侧 ,输送机运行时链条上的润滑油及链条与轨道 由 于磨损而掉下来的油污和杂质不可能掉在车身上和 电泳液中 ,而是掉在两侧的接污盘中,可防止薄膜 缩孔 , 保证了车身 电泳漆的质量 , 底漆后工件返修
率 降低 。
维普资讯
汽 车 涂 装 线 用 摆 杆 输 送 机
长春一汽蓝迪 自 动化工程有限公 司 赵
摆杆输送机是继普通悬挂输送机、条铰接在一起 ,每 2 个摆杆 为 1 , 组 每1 组摆杆输送 1 个工件 ,牵引链带动摆杆沿特定
()摆杆输 送 机在 汽 车车身 人槽 时浸 人 角度 可 1 达 4。 5,人槽 速 度 快 ,排 气 好 。 汽 车车 身 以这 种 方
槽 内 ,支撑板 进人 到滑 撬 的 叫槽 外 的 导 向槽 内 ,
当滑撬倾 斜人槽 时支撑销 可在 叫槽 内转动 ,防止
滑撬与 摆 杆 脱 开 。 滑 撬 的 叫槽 外 的 导 向槽 限 制 滑
的轨 道运 行 ,完 成 工件 前处 理及 电泳各 工序 ,空摆
输送机 、自行葫芦等输送系统后的又一新型的机械 化输送设备 ,主要用于汽车涂装线 的前处理及电泳
工艺。它结构独特 、 新颖 ,具有其他输送设备无法 比拟的特点,常常和滑撬输送系统一起形成 自 动化
程 度高 的输 送 系统 ,用于 产量 大 、产 品质量 高 的汽 车涂装 线 上 。
养 。同时 摆 杆 返 回 时水 平 放 置 ,可 缩 小 设 备 的 高
度 ,节 省空 间 。
图 1 摆 杆 结 构
1 .前摆杆
2 .滑撬
3 .后摆 杆
4 .滑撬 槽
电泳涂装线的悬挂式输送机

32 I汽车工艺与材料ATSd、^ 万方数据
2008年第3期
辅髓柏工
件.要求更高层次的维护保养。 (3)运行程序复杂导致启动时
间较长;每个系统的设计都针对特 定的产品和应用。
(4)源于多角度的全盘考虑 和控制的复杂性导致工程系统较复 杂.有的场合还需要对系统进行模 拟。
(5)与普通悬链不同.组件不 能互换。
推杆悬链具有多项功能,对于 这样一个功能全面.具有高度柔性 的系统,如果保养恰当.它能提供 高达98%的利用率。但推杆悬链系 统在使用中仍存在一定弊病。
(1)由于需要较多的驱动和 拉紧装置.停止器.开关和双倍的 链条,还需要额外的轨道来存储工 件,因此推杆悬链的造价要比普通 悬链输送系统高得多。
(2)推杆悬链有较多的运动部
采用普通悬链输送工件要求环 形链条有固定的运行轨迹.固定的 吊具要求安装在环形链条的中心线 上.这就导致在连续输送工件通过 涂装线的各工序时,不能拥有多种 速度以适应不同处理工艺的要求; 不能手动或自动地在两条输送链间 实现工件的转挂;工件只能在全线 停止运行的情况下停止运行:工件 在处理槽的进.出口必须有垂直弯 段,占用了很多场地面积。因此. 虽然普通悬链是一种较为经济的输 送结构,但目前已很少用于汽车车 身的输送,多用于汽车零部件的涂 装生产线。
工字钢型普通悬链是锻造的, 链条被设计成非铆接结构,在人工 安装时不需要专用工具。链节的尺 寸为3英寸(1英寸=25.4 mm).、4 英寸和6英寸。这种系统比轻型悬链 有更大的负载能力.但是结构要复
01-地面输送系统设备基础知识-202009
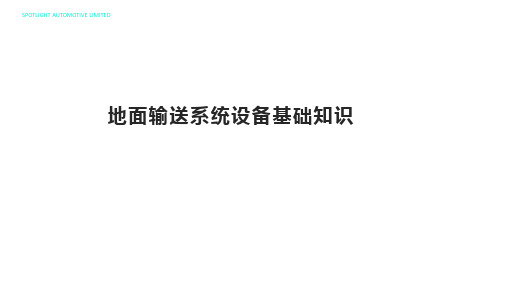
举车身作用; • 4.护罩:钢网折弯而成,保护滚子链和传动链轮; • 5.导向轮:导向作用,出口设置一对
二、常见设备的结构及用途
8、输送设备-移载机
移载机: 主要用来配合侧顶机横向转移车身的输送设备,一
般用于滑橇转换处和车间交接处. 主要结构: • 1.伸缩叉:一般采用进口MIAS品牌,端头带有定位
②工作原理:磁场对电流的受力作用,使电动机转动,把电能转换成机械能。
2、电机的铭牌
要想正确使用电机,除了了解电机结构,还要看动电机的铭牌,熟悉其相关参数,才能更好、更安全、 更有效的使用
以Y132M-4型电机为例,介绍相关参数 具体含义。
电机铭牌
型号说明
3、电机的正反转原理及编程控制
3.1 电机正反转原理及控制电路图
系统停止过程:按下停止按钮SB1,接触器KM1线圈断电,与 SB2并联的KM1的辅助触点断开,以保证KM1线圈持续失电,串联在 电机回路中的KM1的主触点持续断开,切断电动机定子电源,电动机 停转。
对于这种控制线路,当药改变电动机的转向时,就必须先按停止按 钮SB1,再按下反转按钮SB3,才能使电机反转。如果不先按下SB1, 而直接按下SB3,电动机是不会反转运行。
SPOTLIGHT AUTOMOTIVE LIMITED
地面输送系统设备基础知识
输送系统培训
学习要求
按时 积极讨论、分享
震动或静音 举手
目录
➢ 一、输送系统设备概述 ➢ 二、常见设备结构及用途 ➢ 三、输送电机结构原理与编程控制 ➢ 四、输送常见故障处置及维护保养
一、输送系统设备概述
1、输送辊床的简述
电机的正反控制过程,采用两个接触器( (触点)KM1、KM2)、三 个开关(SB1、SB2、SB3)、保护元件断路器(FU)和热敏电阻(FR)等连接 组成控制电路。主电路采用两个接触器(KM1、KM2) 、断路器(FU) 、 热敏电阻(FR)和三相电机(3M)组成,三相电源U-V-W供电,具体过程 如下:
汽车涂装车间前处理电泳线输送设备的介绍

汽车涂装车间前处理电泳线输送设备的介绍发布时间:2022-08-17T08:58:56.207Z 来源:《福光技术》2022年17期作者:闫水恒[导读] 介绍了积放式输送链(C型勾)?摆杆链输送机?全浸入翻转输送系统(Ro-DipM和Ro-DipE)及E-Shuttle多功能穿梭式输送机这几种汽车涂装车间前处理电泳线输送设备的结构?特点和应用情况中汽昌兴(洛阳)机电设备工程有限公司河南省洛阳市 471003摘要:介绍了积放式输送链(C型勾)?摆杆链输送机?全浸入翻转输送系统(Ro-DipM和Ro-DipE)及E-Shuttle多功能穿梭式输送机这几种汽车涂装车间前处理电泳线输送设备的结构?特点和应用情况?关键词:汽车;涂装;前处理;输送设备在现代汽车涂装行业,设备开发的第一目标就是在满足不断严格的环保要求这一前提下尽量保持原有的质量水准?特别是在智能化的涂装车间内,机械化输送设备是生产的命脉,是最重要的关键设备,贯穿于涂装生产的全过程?其中前处理电泳输送设备是整个涂装车间输送系统的核心,对车身电泳表面质量起决定性作用,它的选用还直接影响到工厂车间面积?空间利用率和整个项目的投资?本文对目前汽车涂装车间常用的前处理电泳输送设备进行了介绍和对比?1常见的前处理电泳输送设备1.1积放式悬挂输送链(C型勾)积放式悬挂输送链是悬挂输送机的一种变形,是20世纪80年代中期快速发展起来的机械化运输设备,可实现工件装卸的自动化,以及快速运输?积放存储等?它既能按照工艺节拍程序来运行,也可以改变节距来运输?它属于单链式空中输送系统,通常设置于前处理电泳室体中心线的上方,由上下2层轨道组成:牵引轨道在上,作为主要的牵引动力来源;承载轨在下,由2根槽钢焊接而成?通过牵引链条上的推杆推动小车沿承载轨道运行?载荷小车可在主线和辅线之间自由转送,从而实现积放功能?积放式悬挂输送链需要设置专用的轨道来控制工件的停止或运行?链条及轨道设置于槽体中心的正上方,链条轨道下设置有接油盘?工件通过转换站转载到“C”型吊具上并固定,运行过程中,工件在槽体出入口的上下坡角度为30°?可通过多条链的组合来实现不同的速率及节距;通过道岔来实现工件在不同线体间的分合及存储?1.2摆杆链输送系统摆杆链输送系统适用于大批量生产的前处理电泳线,通常与滑橇输送系统配合使用?滑橇装载于U形摆杆的支撑杆上,前后摆杆成对使用,电泳电流通过固定在电泳前摆杆上的导电铜刷导入,然后通过摆杆上的支撑件传导给车身?摆杆中间安装有一个导向轮,空的摆杆返回时需要该导向轮作为导向和支撑?摆杆输送机主要由摆杆链组件?驱动单元?张紧单元?入口塔?出口塔架?轨道系统等组成?两条链条分别布置在槽体的左右侧,摆杆上端的轴通过连接板与链条铰接在一起,前后两个摆杆为一组,每一组摆杆上固定一个滑橇和工件?工件在入口塔架处由入口滚床转接到摆杆上,入口滚床设置推车机构及阻挡器,保证工件转接平稳,并设置两组对射开关来检测滑橇是否成功转接?牵引链条带动摆杆沿特定的轨道运行,使工件完成前处理及电泳的各个工序?工件在出口塔架处由摆杆转接到出口滚床,出口滚床两侧设置导向轮对滑橇进行导向,出口滚床入口端设置弹簧支腿和接近开关,用于检测滑橇是否成功脱离摆杆?空摆杆沿槽体下部的摆杆返回轨道平躺着返回?摆杆输送机在前处理及电泳的关键工位(如脱脂?磷化?电泳)设计有驼峰,以利于排出工件内的空气,从而保证工件的电泳质量?摆杆系统的轨道布置在槽体的两侧,室体的顶部根据槽体的位置设置上下坡段,一般为45°?轨道底部设置有不锈钢接油盘,连接处需要满焊,安装前进行漏液测试,防止焊接处漏油而导致槽液的污染?运行过程中摆杆始终保持竖直向下的状态,通过前后摆杆的高度差来实现工件倾斜一定的角度?在轨道的返回段,摆杆则处于水平状态,以节约设备空间?摆杆输送机在工件入槽时浸入角度可达45°,不仅缩短了前处理和电泳设备的长度,比空中悬挂输送系统更节省厂房占地空间,而且降低了槽体容积,减少了能源及药剂消耗?摆杆输送机的牵引链条布置在槽体的两侧,输送机运行时链条上的润滑油?链条与轨道因磨损而掉下来的油污和杂质不会掉到车身上及槽液中,可有效减少油污导致的车身缩孔,保证车身电泳漆的品质,降低底漆后工件返修率?另外,槽内的各种酸碱腐蚀性气体对轨道及牵引链条的腐蚀也大大减少,从而延长了轨道及牵引链条的使用寿命?链条与摆杆采有铰接形式,摆杆一端固定,另一端可以自由上下移动,使摆杆运行平稳,可靠安全,故障率较低,使用寿命长?摆杆链输送系统一般为垂直自动循环,摆杆返回时呈水平状态放置,便于维修保养及检查,同时降低了整体设备的高度,节省厂房的空间?1.3Ro-Dip翻转输送系统1996年第三代Ro-Dip开始推广运用,能实现工件360°旋转?目前全球应用最多的就是第三代(简称Ro-DipM),运行模式是连续的,是车身连续翻转的机械式解决方案?而现在的第四代Ro-DipE则更加智能化?柔性化。
摆杆输送系统在涂装生产线上的设计应用

摆杆输送系统在涂装生产线上的设计应用发表时间:2019-12-04T14:48:53.780Z 来源:《防护工程》2019年15期作者:徐登坡张戎[导读] 汽车涂装生产线的前处理及电泳工序通常采用的输送设备有自行葫芦、普通悬挂输送机、积放式悬挂输送机。
中汽昌兴(洛阳)机电设备工程有限公司河南省洛阳市 471003摘要:为解决车身涂装前处理电泳线输送设备高效率与低故障的矛盾,设计采用了摆杆输送系统,用于车身涂装线输送。
该输送形式具有承载能力强、运行平稳、节能降噪、节约空间、生产效率高、维修方便等优点。
关键词:涂装生产线;摆杆链;电泳滑橇;节拍汽车涂装生产线的前处理及电泳工序通常采用的输送设备有自行葫芦、普通悬挂输送机、积放式悬挂输送机。
摆杆输送系统作为一种新型、实用的输送设备,它结构独特、新颖,具有其他输送设备无法比拟的特点,常常和滑橇输送系统一起形成自动化程度高的输送系统,用于高节拍、高质量的汽车涂装生产线上。
1摆杆输送系统在涂装线上的应用背景1.1推杆链的使用情况一般涂装的前处理、电泳输送系统采用推杆积放链输送系统,主要存在以下问题。
①入槽角度小,排气效果差。
推杆积放链采用30°入槽,入槽角度小,不但使槽体长度加长,而且车身内腔气体不易排出,导致槽液难以完全进入内腔,使得电泳漆膜较薄,很多位置膜厚在5μm以下,防腐性能差。
②沥水效果差。
由于沥水角度小,导致车身内部的液体难以排出,在烘干过程中增加了烘房的能耗,局部区域电泳漆膜难以烘干。
③输送链易被腐蚀,且对槽污染大。
推杆积放链在槽体上方,常年受槽液的酸碱气体腐蚀,目前已出现严重的锈蚀现象;同时链条上的油脂和杂物容易掉进下方的槽液和车身上,导致车身电泳漆膜出现缩孔、颗粒等问题。
1.2摆杆链与传统输送方式的对比①前处理、电泳工艺过程的产品质量得到很大的提高:电泳漆膜均匀度、光洁度等性能参数明显高于自行葫芦、普通悬链、积放式悬挂输送机。
②提高了车身在前处理、电泳工艺段运行的稳定性、可靠性;③延长输送机在前处理、电泳工艺段特殊工况条件下的使用寿命;④摆杆链能实现车身45b入槽,减少浸槽的体积,缩短前处理、电泳线的设备长度,大大减少了工程建设的投入成本和生产过程的运行费用,工艺设备可节省大约10%的投资成本,运行成本可节省20%的费用;⑤轨道和牵引链布置在槽体两侧,杜绝输送机对车身的污染,提高生产率。
空中车体输送线设备描述
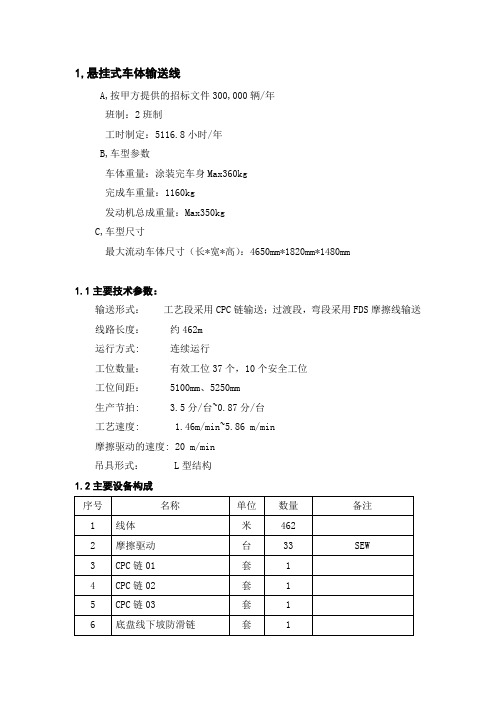
1,悬挂式车体输送线A,按甲方提供的招标文件300,000辆/年班制:2班制工时制定:5116.8小时/年B,车型参数车体重量:涂装完车身Max360kg完成车重量:1160kg发动机总成重量:Max350kgC,车型尺寸最大流动车体尺寸(长*宽*高):4650mm*1820mm*1480mm1.1主要技术参数:输送形式:工艺段采用CPC链输送;过渡段,弯段采用FDS摩擦线输送线路长度:约462m运行方式: 连续运行工位数量:有效工位37个,10个安全工位工位间距: 5100mm、5250mm生产节拍: 3.5分/台~0.87分/台工艺速度: 1.46m/min~5.86 m/min摩擦驱动的速度: 20 m/min吊具形式: L型结构1.2主要设备构成1.3设备描述内饰转底盘过渡区及底盘转终端一线过渡区采用空中CPC链与FDS摩擦输送完成车身底盘装配作业,同时实现后桥、发动机、油箱等车身底盘件与车体的合装工作。
其设备结构如下:1、轨道:输送段轨道采用16#槽钢及角钢8*75*75焊接组合,通过可调吊座与辅梁相连;工艺段轨道为组合结构,在主轨两侧设有并行两条平衡轨,保证装配作业时吊具平稳。
轨道安装后,表面光滑,所有接头打磨平整,安装精度达到轨道纵向直线度误差每米小于1.5mm,全长不超过5mm;轨道端面对轨道纵向中心线的垂直度误差小于1.5mm;水平轨道的水平度允差不应大于1/1000,全长不应大于5mm;轨道接头对接平齐,小车运行时无卡阻和明显振动。
2、车组吊具:用来支撑车体完成底盘输送线,终端一线输送线及空抱具返回输送线的传输。
车组吊具由摩擦车组、吊具框架、可调支撑臂、吊具本体、连系杆组成。
摩擦车组由前小车、两个承载中车、后小车、连接挂钩及摩擦梁组成,车组采用精铸件,车组走轮为聚氨酯轮,摩擦梁由矩形管焊接制成;吊具框架由型材焊接制成;吊具为L型型可张开结构,由方管焊接制成。
车体支撑,采用前部为销定位+支撑块,后部为支撑板构造,确保车体在输送过程中不发生滑移及脱出。
涂装车间如何选择输送方式

如何选择合适的输送形式标签:输送2011-12-05 16:52 星期一在规划中对输送形式进行选择时,要充分考虑不同的车送形式对车身涂层质量的影响,以及所需投资(包括工艺设备和土建公用)的高低,所能达到的净产能的大小,设备运行、维修、维护成本等因素。
悬挂输送形式:1)自行葫芦输送机(EMS):EMS因只适用于间歇式的前处理、电泳线、产能较低,且由于对涂层质量影响较大和设备的维修频率较高等因素,在大型涂装线中基本不采用EMS。
但是,由于EMS所需投资低,因而在车身涂层质量要求不高时仍被采用。
为提高产能,改进后的EMS在脱脂、磷化和电泳3个工序均采用双工位,在设备利用率为8.5﹪时,净产能可提高到18辆/h。
2)推杆式悬链输送机(OHC):OHC能满足大型涂装的产能需求,但缺点是:输送机上的润滑油和冷凝水会下掉,污染车身和槽液;通常,其上下坡角度最大只能达到300,一方面因车顶所泡和滴水性较差,因而会对车身电泳涂层质量产生不利影响;另一方面,槽体较大,将造成投槽费用的增加和降低厂房利用率。
因此,在高档汽车涂装线,一般不采用该种输送形式,但由于其造价不高,因而在日本和中日合资企业仍被广泛采用。
3)摆杆输送机:目前,摆杆输送机有两种,两者的区别主工是空摆杆返回的路线和形式不一样。
在中高级轿车涂装线中,摆杆输送机获得了广泛应用,其主要优点是:(1)消除了输送设备对车身的污染;(2)入、出槽角度可达到450,节约了工艺槽的长度,同时对消除车顶气泡和出槽倒水较有利。
垂直地链输送机:垂直地链输送机是一种运送成件物品的运输机械,广泛地应用在流水生产的各种行业中,尤其是涂装车间的生产线。
设备特点:可根据工艺流程的要求组成平面封闭线路,在输送过程中能完成诸如底涂、烘干、喷漆等工艺过程;能输送各种形状、尺寸、质量的物品;运行速度范围较大,5-18m/min;;;该输送机安装在地面的坑道里,可提高车间面积的利用率。
垂直地链输送机主要由下列部件组成:传动装置、头轮装置、张紧装置、牵引链条、机身及过渡轨道、小车承载轨和载工件用的小车地面输送形式:1)地面推杆式输送机的主要优点是造价低,但由于其不利于立体布置,厂房利用率低,设备安装、维护、使用不方便等,使其现在只是与摩擦式输送机相配合,一般应用在喷漆室、烘干室等工位。
汽车涂装线滑橇式自动输送系统
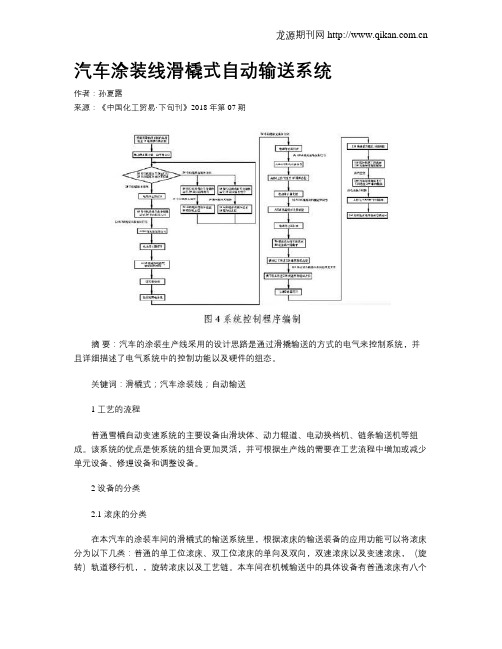
汽车涂装线滑橇式自动输送系统作者:孙夏露来源:《中国化工贸易·下旬刊》2018年第07期摘要:汽车的涂装生产线采用的设计思路是通过滑撬输送的方式的电气来控制系统,并且详细描述了电气系统中的控制功能以及硬件的组态。
关键词:滑橇式;汽车涂装线;自动输送1 工艺的流程普通雪橇自动变速系统的主要设备由滑块体、动力辊道、电动换档机、链条输送机等组成。
该系统的优点是使系统的组合更加灵活,并可根据生产线的需要在工艺流程中增加或减少单元设备、修理设备和调整设备。
2 设备的分类2.1 滚床的分类在本汽车的涂装车间的滑橇式的输送系统里,根据滚床的输送装备的应用功能可以将滚床分为以下几类:普通的单工位滚床、双工位滚床的单向及双向,双速滚床以及变速滚床,(旋转)轨道移行机,,旋转滚床以及工艺链。
本车间在机械输送中的具体设备有普通滚床有八个单工位的为单向的,八个单工位的为双向的,十一个双工位的为双向的,旋转滚床有七个,轨道移行机共十六个,其中旋转的轨道移行机有八个,十个变速滚床,还有四个工艺链条。
各种滚床根据分类的不同分别有以下定义:①普通滚床:这个滚床输送的速度是一定的,是不可调整的;②变速滚床:这个滚床可以控制运行的方向,可以控制速度,是可以调整的,有双向的功能;③旋转滚床:这个滚床的电气控制可以按照圆周旋转来更换方向定位;④轨道移行机:它是一种可以平行移动的装备,一般是有两部分组成的:输送电机、移动电机。
2.2 滚床的功能本车间的工艺流程在生产工艺上主要包括以下功能:电泳车身之后的中涂打磨、喷涂、擦净、面漆的流平、烘干、冷却、检查以及喷蜡等等。
3 控制系统的配置、架构和选择3.1 电气系统中硬件的配置本涂装车间的动力区可分为四个,每个动力区都有一套PLC来对它进行控制,另外,控制柜的组成部分是数目不相同的继电器还有PLC控制柜。
根据控制系统的要求,电气控制系统可分为管理控制级和控制级和设备级。
工业局域网由上位机和PLC连接在通信单元中,即控制系统和控制层,控制系统中的设备层由通信网络构成。
2024年涂料输送机操作规程
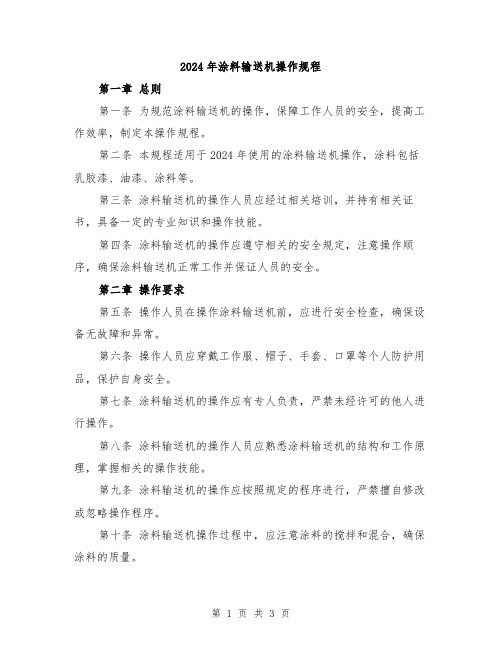
2024年涂料输送机操作规程第一章总则第一条为规范涂料输送机的操作,保障工作人员的安全,提高工作效率,制定本操作规程。
第二条本规程适用于2024年使用的涂料输送机操作,涂料包括乳胶漆、油漆、涂料等。
第三条涂料输送机的操作人员应经过相关培训,并持有相关证书,具备一定的专业知识和操作技能。
第四条涂料输送机的操作应遵守相关的安全规定,注意操作顺序,确保涂料输送机正常工作并保证人员的安全。
第二章操作要求第五条操作人员在操作涂料输送机前,应进行安全检查,确保设备无故障和异常。
第六条操作人员应穿戴工作服、帽子、手套、口罩等个人防护用品,保护自身安全。
第七条涂料输送机的操作应有专人负责,严禁未经许可的他人进行操作。
第八条涂料输送机的操作人员应熟悉涂料输送机的结构和工作原理,掌握相关的操作技能。
第九条涂料输送机的操作应按照规定的程序进行,严禁擅自修改或忽略操作程序。
第十条涂料输送机操作过程中,应注意涂料的搅拌和混合,确保涂料的质量。
第十一条操作人员应按照涂料输送机的容量和速度要求,控制涂料的输出量和运输速度。
第三章安全措施第十二条操作人员在操作涂料输送机时,应保持机器周围的整洁,防止杂物堆积和涂料泼溅。
第十三条涂料输送机的操作前,应确保机器周围没有人员,防止发生人身伤害。
第十四条涂料输送机操作人员应注意机器的运行情况,如发现异常情况应立即停机检修。
第十五条涂料输送机操作时,应远离机器转动部件,以免发生意外伤害。
第十六条涂料输送机在运行中,应严禁私自调整机器的参数和操作控制。
第四章故障处理第十七条涂料输送机发生故障时,操作人员应立即停机,并尽快报告维修人员进行修复。
第十八条在等待维修期间,操作人员应确保机器周围的安全,防止发生意外。
第十九条涂料输送机的维修应由专业的维修人员进行,严禁非专业人员乱修或随意拆卸机器。
第二十条涂料输送机维修完成后,操作人员应进行测试和试运行,确保机器正常工作。
第五章管理责任第二十一条使用涂料输送机的单位应建立相关的管理制度,明确各个岗位的职责和义务。
浅谈涂装车间常见的几种前处理电泳输送设备
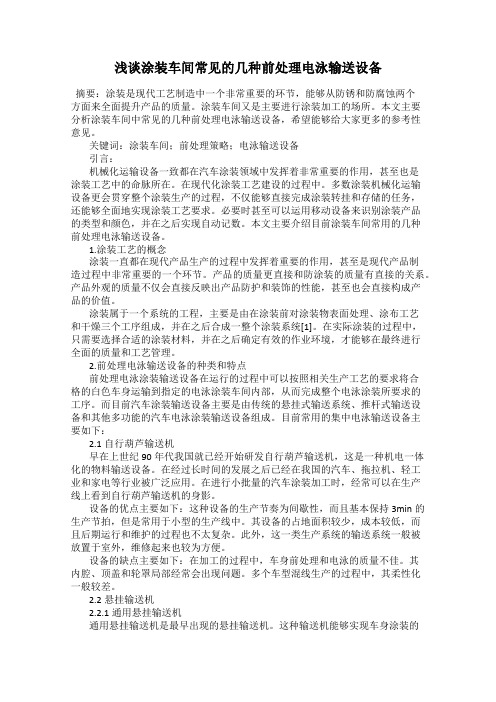
浅谈涂装车间常见的几种前处理电泳输送设备摘要:涂装是现代工艺制造中一个非常重要的环节,能够从防锈和防腐蚀两个方面来全面提升产品的质量。
涂装车间又是主要进行涂装加工的场所。
本文主要分析涂装车间中常见的几种前处理电泳输送设备,希望能够给大家更多的参考性意见。
关键词:涂装车间;前处理策略;电泳输送设备引言:机械化运输设备一致都在汽车涂装领域中发挥着非常重要的作用,甚至也是涂装工艺中的命脉所在。
在现代化涂装工艺建设的过程中。
多数涂装机械化运输设备更会贯穿整个涂装生产的过程,不仅能够直接完成涂装转挂和存储的任务,还能够全面地实现涂装工艺要求。
必要时甚至可以运用移动设备来识别涂装产品的类型和颜色,并在之后实现自动记数。
本文主要介绍目前涂装车间常用的几种前处理电泳输送设备。
1.涂装工艺的概念涂装一直都在现代产品生产的过程中发挥着重要的作用,甚至是现代产品制造过程中非常重要的一个环节。
产品的质量更直接和防涂装的质量有直接的关系。
产品外观的质量不仅会直接反映出产品防护和装饰的性能,甚至也会直接构成产品的价值。
涂装属于一个系统的工程,主要是由在涂装前对涂装物表面处理、涂布工艺和干燥三个工序组成,并在之后合成一整个涂装系统[1]。
在实际涂装的过程中,只需要选择合适的涂装材料,并在之后确定有效的作业环境,才能够在最终进行全面的质量和工艺管理。
2.前处理电泳输送设备的种类和特点前处理电泳涂装输送设备在运行的过程中可以按照相关生产工艺的要求将合格的白色车身运输到指定的电泳涂装车间内部,从而完成整个电泳涂装所要求的工序。
而目前汽车涂装输送设备主要是由传统的悬挂式输送系统、推杆式输送设备和其他多功能的汽车电泳涂装输送设备组成。
目前常用的集中电泳输送设备主要如下:2.1自行葫芦输送机早在上世纪90年代我国就已经开始研发自行葫芦输送机,这是一种机电一体化的物料输送设备。
在经过长时间的发展之后已经在我国的汽车、拖拉机、轻工业和家电等行业被广泛应用。
汽车涂装车间输送系统橇体检测及调整方法

汽车涂装车间输送系统橇体检测及调整方法发布时间:2022-09-28T07:52:43.258Z 来源:《福光技术》2022年20期作者:黄旭尘王高峰[导读] 涂装车间输送设备是汽车生产线四大车间中最为复杂的设备,橇体是涂装车间生产线最常见的输送设备单元,它作为白车身的直接载体,广泛应用于前处理、电泳、涂胶、喷漆和烘干等工位,且橇体数量巨大,净产能60JPH的涂装生产线橇体使用量达到600套左右。
中汽昌兴(洛阳)机电设备工程有限公司河南省洛阳市 471003摘要:随着汽车行业的发展,目前汽车涂装车间基本都采用滑橇输送系统作为车间的基本输送形式,具有布置灵活、功能多样和高自动化等特点,而橇体是将各种输送设备串联起来的关键一环,是车身在各生产工艺及车间间流转的重要载体。
随着人们对车身质量的要求越来越高,车身的加工精度也随之提高,多种加工工艺段(涂胶工位、喷漆工位、注蜡工位等)采用了机器人作业,这就对车身的定位精度有了更高的要求。
橇体承载着白车身穿梭于各种工位之间,橇体支撑的精度直接决定了车身的定位和加工精度。
关键词:涂装;橇体输送系统;支点;定位引言涂装车间输送设备是汽车生产线四大车间中最为复杂的设备,橇体是涂装车间生产线最常见的输送设备单元,它作为白车身的直接载体,广泛应用于前处理、电泳、涂胶、喷漆和烘干等工位,且橇体数量巨大,净产能60JPH的涂装生产线橇体使用量达到600套左右。
由于对汽车的质量和制造精度的要求不断提高,汽车的各种加工过程(如:涂胶、喷漆、打蜡等)都是由机械手完成,这就需要更高的车体定位精度。
雪橇载着白色的车体在不同的工位间穿梭,其支承的精确性直接影响到车辆的定位与加工。
涂装车间通常使用2种形式的橇体:电泳橇体和喷漆橇体,2种橇体结构类似,一般由焊接式骨架和支撑组成,采用装配式结构,多组支撑通过螺栓连接到橇体骨架,方便支撑的安装调整,同时提高了橇体支撑的互换性。
生产线所用橇体数量庞大,橇体装配后上线时须对所有橇体进行统一标准的尺寸测量,保证橇体支撑的安装精度在±1mm范围。
滑橇输送系统在汽车涂装中的应用

滑橇输送系统在汽车涂装中的应用发布时间:2022-08-24T01:38:26.776Z 来源:《新型城镇化》2022年17期作者:卢志业白绍华[导读] 我国汽车制造业在经历了整车进口、先进技术及汽车主要零部件的引进到国产汽车品牌的发展过程中,对汽车行业的输送设备及自动控制系统提出了越来越高的要求。
中汽昌兴(洛阳)机电设备工程有限公司河南省洛阳市 471003摘要:把PLC控制技术?工业局域网及现场总线应用于汽车生产工艺及车身输送的循环过程?滑橇式输送机完成焊后白车身的转接?转挂及自动存储?实现白车身的前处理电泳及钣金修理—涂胶—喷胶—烘胶—打磨—面漆等工艺过程?关键词:滑橇式输送机;PLC;DH+网络;设备网我国汽车制造业在经历了整车进口、先进技术及汽车主要零部件的引进到国产汽车品牌的发展过程中,对汽车行业的输送设备及自动控制系统提出了越来越高的要求。
滑橇式输送机以其噪音小、运行可靠的特点,已经愈来愈多的被汽车制造企业广泛引用,本文以东风公司车身涂装生产线为例,对滑橇式输送系统的自动控制进行了研究与设计。
1滑橇式自动输送系统的组成滑橇式输送系统主要由动力辊床、辊床升降机、动力旋转辊床、电动移行机、举升传递辊床、链式移行机、橇体等单元设备组成,其优点是系统组合灵活机动,可根据生产线工艺流程的需要随意增/减单元设备,便于安装调试、检修和设备调整。
1.1输送系统的工艺流程东风公司车身厂涂装车间的输送系统采用地面滑橇式输送机,用于转接焊装车间下线白车身(由焊装下线升降机转挂至涂装车间滑橇),并将其转挂至前处理电泳输送线。
在白车身完成前处理及电泳工艺后,重新转接回地面滑橇,完成白车身的钣金修理-涂胶-喷胶-烘胶-打磨-面漆等工艺过程,具体工艺流程如图1所示。
在完成以上工艺流程中输送系统同时实现车身的自动储运。
工艺流程图如图1所示。
图1 工艺流程图1.2电气控制系统的硬件配置涂装车间分为4个动力区,每一动力区由一套PLC进行控制,控制柜由PLC控制柜及数目不等的继电器柜组成。
汽车涂装输送系统总体设计

汽车涂装输送系统总体设计发布时间:2022-10-18T08:14:50.551Z 来源:《福光技术》2022年21期作者:郭冰涛张青春[导读] 汽车涂装生产线新技术、新工艺的应用及发展,不仅提高了汽车涂装车间的生产效率,增加了汽车企业的经济效益,并能够进一步满足人们对汽车的多样化需求,进而提高人们的生活品质。
随着科技的进步,汽车涂装生产线新技术、新工艺也在不断的发展;目前涂装车间机运系统主要分为摆杆输送系统和地面滑橇输送系统;本文主要就涂装工艺以及汽车涂装生产线新技术的应用及发展,汽车涂装材料进行分析研究。
郭冰涛张青春中汽昌兴(洛阳)机电设备工程有限公司河南省洛阳市 471003摘要:汽车涂装生产线新技术、新工艺的应用及发展,不仅提高了汽车涂装车间的生产效率,增加了汽车企业的经济效益,并能够进一步满足人们对汽车的多样化需求,进而提高人们的生活品质。
随着科技的进步,汽车涂装生产线新技术、新工艺也在不断的发展;目前涂装车间机运系统主要分为摆杆输送系统和地面滑橇输送系统;本文主要就涂装工艺以及汽车涂装生产线新技术的应用及发展,汽车涂装材料进行分析研究。
关键词:汽车涂装;生产线新技术、新工艺;发展涂装是机械产品生产加工中的一个过程,目的是为了防止机械产品外层表面的生锈或腐蚀,通过涂装来切断空气,达到防锈和防腐的目的,有利于提高产品质量。
涂装是一项系统工程,包括很多程序和工序,涂装的表面处理、涂装、干燥、涂装要求也非常高,应根据涂装对象的材料和性质选择涂料,选用稳定性强、质量好的涂料。
涂刷工艺的应用,能起到保护、装饰等功能,能防止机械设备表面被腐蚀、破坏,同时选用色彩艳丽的涂料也能起到美化和装饰性效果。
涂装技术是汽车生产制造的重要环节。
随着汽车制造水平的不断提高,涂装技术也在不断优化和创新,工艺越来越熟练,涂装质量也越来越高。
目前,在汽车制造行业的生产加工中,实施大批量生产模式,对涂装要求更高,能否达到自动涂装的要求,是决定涂装质量的关键因素。
汽车涂装技术 任务九 转运机械化涂装设备
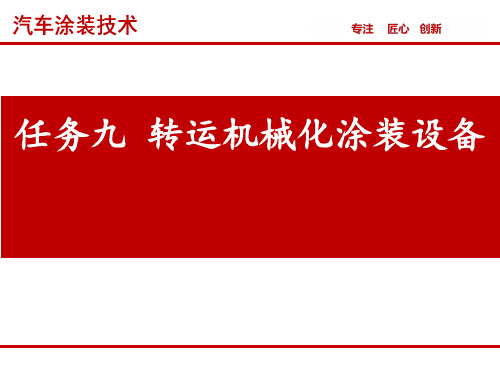
图14 CHAC中上涂搬送线
常用机械化涂装设备 9)NISSAN 摩擦驱动输送线 如图15所示,可根据需求灵活控制车身的输送速度,节能环保、容易维
护、便于保养。
图15 NISSAN 摩擦驱动输送线图
常用机械化涂装设备 10)前处理等待入口
如图16所示,使用吊具运转白车身从焊 装车间进入涂装车间,在进入预清理班组前 等待。
常用机械化涂装设备 首先进行漆膜补涂,其次使用红外线烤灯烘烤修补部分,使
修补后的漆膜固化,车身的修补区域经过红外线烤灯烘烤后,需 要对修补区域进行打磨处理,
红外线烤灯
常用机械化涂装设备 目的是:①去除修补区表面的颗粒物、毛刺、油污、灰尘。
常用机械化涂装设备
小结:
1.涂装生产线分类。 2.各种涂装输送设备的功能。
?思考:
☆ 1.任务导入的问题。 ☆ 2.使用什么涂装输送设备,可以将白车身从焊接车间运载至涂装车 间? ☆ 3.密封胶输送线的功能是?
凡是自强不息者,最终都会成功。——歌德 希望同学们在求学的路上,坚持不懈,自强不息
常用机械化涂装设备 11)升降机
如图17所示,用来举升和下降白车身。
图17 升降机
常用机械化涂装设备
12)180°转台 如图18所示,可180°旋转进行喷涂作业。
图18 180°转台
常用机械化涂装设备
13)电动移行机,如图19所示,由电动机提供动力, 运载车身。
图19 电动移行机
任务九 转运机械化涂装设备
任务九 转运机械化涂装设备
任务: 常用机械化涂装设备 ☆ 一、熟悉汽车涂装生产线。(了解) ☆ 二、明确各种涂装输送设备的功能。(重点)
常用机械化涂装设备 任务导入
IMC输送机的应用及运行控制特点分析
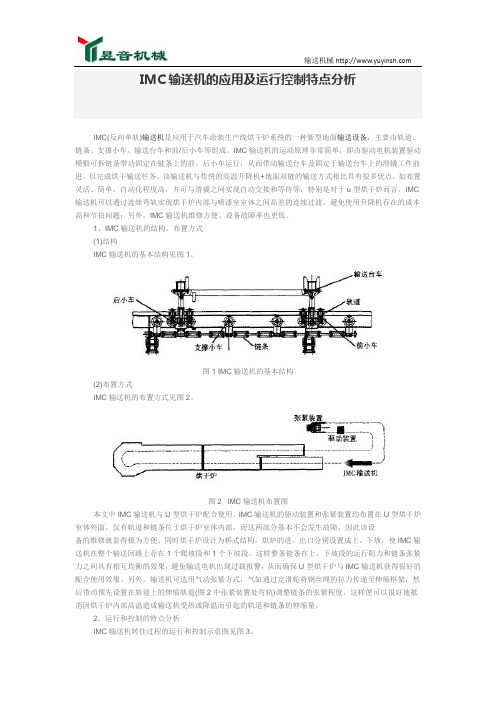
IMC输送机的应用及运行控制特点分析IMC(反向单轨)输送机是应用于汽车涂装生产线烘干炉系统的一种新型地面输送设备,主要由轨道、链条、支撑小车、输送台车和前/后小车等组成。
IMC输送机的运动原理非常简单,即由驱动电机装置驱动模锻可拆链条带动固定在链条上的前、后小车运行,从而带动输送台车及固定于输送台车上的滑撬工件前进,以完成烘干输送任务。
该输送机与传统的高温升降机+地面双链的输送方式相比具有很多优点,如布置灵活、简单,自动化程度高,并可与滑撬之间实现自动交接和等待等;特别是对于u型烘干炉而言,IMC 输送机可以通过连续弯轨实现烘干炉内部与喷漆室室体之间高差的连续过渡,避免使用升降机存在的成本高和节拍问题;另外,IMC输送机维修方便、设备故障率也更低。
1、IMC输送机的结构、布置方式(1)结构IMC输送机的基本结构见图1。
图1 IMC输送机的基本结构(2)布置方式IMC输送机的布置方式见图2。
图2 IMC输送机布置图本文中IMC输送机与U型烘干炉配合使用。
IMC输送机的驱动装置和张紧装置均布置在U型烘干炉室体外面,仅有轨道和链条位于烘干炉室体内部,而这两部分基本不会发生故障,因此该设备的维修就显得极为方便。
同时烘干炉设计为桥式结构,烘炉的进、出口分别设置成上、下坡,使IMC输送机在整个输送回路上存在1个爬坡段和1个下坡段,这样整条链条在上、下坡段的运行阻力和链条张紧力之间具有相互均衡的效果,避免输送电机出现过载报警,从而确保U型烘干炉与IMC输送机获得很好的配合使用效果。
另外,输送机可选用气动张紧方式,气缸通过定滑轮将钢丝绳的拉力传递至伸缩框架,然后带动预先设置在轨道上的伸缩轨道(图2中张紧装置处弯轨)调整链条的张紧程度,这样便可以很好地抵消因烘干炉内部高温造成输送机受热或降温而引起的轨道和链条的伸缩量。
2、运行和控制的特点分析IMC输送机转挂过程的运行和控制示意图见图3。
A-反占位检测开关;B-转挂成功检测开关;C-减速开关;D-占位开关;E-光电检测开关1-转挂区域检测开关1;2-转挂区域检测开关2图3 IMC输送机转挂过程运行控制示意图IMC输送机在正常生产情况下转挂过程的运行和控制步骤简述如下。
涂装设备培训教程(三)

一、垂直地链输送机1.基本介绍垂直地链输送机是一种运送成件物品的运输机械,广泛地应用在流水生产的各种行业中,尤其是涂装车间的生产线。
2.设备特点2.1.它可根据工艺流程的要求组成平面封闭线路,在输送过程中能完成诸如底涂、烘干、喷漆等工艺过程。
2.2.能输送各种形状、尺寸(长度可达数米)及质量(从小于1kg至2t)的物品。
2.3.运行速度范围较大,一般为0.5~18m/min,可调速。
2.4.该输送机是安装在地面的坑道里,可提高车间面积的利用率。
2.5.适应的工作环境温度范围较宽,为-20~45℃,牵引链及轨道允许的工作环境温度为-20~200℃。
温度超过200℃时,还可采用特殊润滑脂来满足工艺要求。
3.6.过渡轨道:用于连接头轮装置与机身和机身与张紧装置。
3.7.小车承载轨:用于支撑和导向小车,使牵引链条免受垂直荷载。
采用预埋槽钢作为轨道。
3.8.载工件用的小车:用于支撑工件,完成各种工艺操作。
它是由车体、4个轮子和高强度的升缩轴构成。
4.设备的安装与调试4.1.小车行走轨道(予埋钢板)应保证在全长范围内高差不大于10mm;在接缝处高差不大于2mm。
4.2.输送机机身在安装时应保证链条行走轨道在全长范围内高差不大于5mm,在接缝处不大于2mm。
4.3.牵引链条运行应平稳,不得有卡阻现象,推爪到位应准确,重复误差不大于5mm。
4.4.小车行走轮设导向轨,设备内双侧导向,设备外单侧导向,转弯段导向外侧走轮.5.垂直地链输送机的维护和保养5.1.传动装置须定期加注和更换润滑油(润滑油可采用齿轮油。
)5.2.头轮装置;张紧装置的轴承部位须定期加注润滑脂。
5.3.链轮部位须定期涂润滑脂脂。
5.4.应定期清理轨道,防止杂物吊入轨道,影响输送机正常运行。
二、摆杆链输送机1.基本介绍摆杆输送机是最近十几年发展起来的新型输送设备,主要用于大规模生产的汽车涂装生产线。
如上海大众B5涂装线、上海通用汽车公司涂装线、金杯汽车厂轿车涂装线、烟台车身有限公司涂装线的前处理和电泳段都采用了摆杆链输送系统。
汽车电泳涂装输送设备

汽车电泳涂装输送设备摘要:简要介绍了汽车车身电泳涂装输送设备自行葫芦输送机、摆杆式输送机;详细介绍了目前在汽车车身前处理线上广泛应用的RoDip3系统;并对国外最新型的多功能穿梭机进行了探究。
关键词:电泳涂装输送设备;RoDip3;多功能穿梭机Abstract:Electrophoresis painting transport equipment s such as self-propelled hoist conveyor and swing rod conveyor are briefly introduced.RoDip3 system widely used in car body pretreatment lines now is introduced in detail. And the latest foreign vario shuttle is also studied.Key words:electrophoresis painting transport equipment; Rodip3;vario shuttle0前言改革开放和加入WTO以来,中国经济快速增长,更是一跃成为汽车生产制造全球第一大国。
在汽车生产制造的环节中,汽车车身的前处理,包括电泳和静电喷涂,都消耗了大量的资源。
所以,先进的汽车电泳涂装输送设备的出现不仅能帮助汽车企业提高竞争力,更有利于节能减排,也是新形势下建设美丽中国的必然要求。
在现代化的汽车车身前处理生产线上,机械化自动化的输送设备是电泳涂装的核心。
它能使得汽车车身的电泳效果更好,提高汽车车身的防腐蚀能力,并能够使下一步工序喷漆的顺利进行,其自身的工作效率也要高,并能长时间无故障连续运行。
下面本文将对一些汽车车身电泳涂装输送设备进行介绍和探讨。
1自行葫芦输送机我国于二十世纪九十年代初开始在工件的前处理、电泳线上使用自行葫芦输送机,是经过十几年的发展,已广泛应用于汽车、家用电器、农机、轻工等行业中。
- 1、下载文档前请自行甄别文档内容的完整性,平台不提供额外的编辑、内容补充、找答案等附加服务。
- 2、"仅部分预览"的文档,不可在线预览部分如存在完整性等问题,可反馈申请退款(可完整预览的文档不适用该条件!)。
- 3、如文档侵犯您的权益,请联系客服反馈,我们会尽快为您处理(人工客服工作时间:9:00-18:30)。
新型车身涂装输送设备
1 前言
在汽车车身的涂装过程中,车身的机械化输送系统是涂装生产线的大动脉,它贯穿于涂装生产线的全过程。
一个年产15万辆车身的涂装车间,其车身输送线的总长度在6500m左右。
车身的预处理和电泳是全自动进行的。
它要求输送系统运行连续平稳,车身的入槽角度大,出槽后的滴水时间短,同时希望投资少,运行费用低涂装质量好。
预处理需经过脱脂、表调、磷化、钝化加上各级水洗等共12个步骤。
阴极电泳也有7道工序。
车身输送的方式和输送链的结构,对产品质量有明显的影响。
尤其是预处理和电泳的输送设备的工作环境特别差,它要经受酸、碱、有机溶剂的不断侵蚀,要在高温、高湿的环境下长时间连续运行,如果因故障停止运行10min,会造成8辆车身因锈蚀而报废。
因此预处理、电泳的车身输送设备的设计是比较困难的,而输送系统对槽液和车身的污染,车顶内气泡的清除等更是一个令人头痛,而又难以克服的问题。
采用电动自行葫芦,龙门式自行行车,悬挂链+吊架,双摆链+滑橇等方法都无法从根本上解决问题。
世界上最新开发成功的全旋反向浸渍输送技术,即Ro Dip-Technology,从全新的理念上彻底解决了预处理、电泳车身输送过程中存在的问题。
RoDip从设备投资,运行费用,产品质量和维修保养等各个方面都明显优于目前在世界各地运行的车身输送系统。
在新建的大型车身涂装线上正在得到迅速推广和应用,目前在全世界已有11条生产线在运行中。
上海大众汽车公司的PoLo 生产线就采用了RoDip技术,2002年底该线将投入运行。
2 车身输送方式的发展
小批量生产时,在预处理和电泳过程中,大多采用电动自行葫芦+吊架的方式对车身进行脱脂、磷化和电泳处理。
大批量连续生产时采用的是普通悬挂链+吊架组成的系统。
该系统车身固定在吊架上,在悬链上吊架的间距是固定的,不能自动转挂、积放和垂直升降,其应用受到一定的限制。
目前大多数的涂装线都采用经过改进的积放式悬挂链,它由牵引轨道和承载轨道组合而成,有效地克服了普通悬挂链存在的问题。
悬挂输送系统的输送链在槽子中心的正上方,输送链必须加润滑油,容易造成槽液的污染,尤其是电泳漆,滴入一点点油,就会造成大量的缩孔。
槽子上方的链条和挡油板等还会有冷凝水滴到车身和槽子中造成污染。
车身固定在房式的吊架上,车身上方有吊架的横梁,其滴水也会滴到车身上造成污染,改成C型吊架后,可以部分减少滴水,但不能完全消除。
悬挂链的最大入槽角度为30°,对消除车顶内气泡和出槽时的倒水都十分不利。
20世纪80年代初在欧洲开始流行一种摆杆式输送链,它由2根同步的链条和“U”型摆杆组成。
车身被锁紧在滑橇上,滑橇分别锁在2根U型摆杆上。
双摆链在槽子的正上方没有输送机构,出入槽的角度可达45°,对消除车顶气泡和出槽倒水比较有利,解决了吊架和输送链滴水污染车身的问题。
但其输送轨道仍在槽子两侧的上方,车两侧有四根摆杆、在经过喷淋区时,会引起槽液飞溅,车身内腔的水不易倒干净。
车顶内的气泡也不能彻底清除。
而且摆杆或吊架总是随车身反反复复地出入槽液,会造成一定的污染。
1992年人们开始进行将车身入槽增角度增大到180°的试验。
到1994年进一步增大到210°,即Ro Dip-2,1995年在美国VOLVO工厂建成了第一条生产线并投入使用,世界上先后共建成5条Ro Dip-2生产线。
1996年人们成功地研究出Ro Dip-3技术。
在第三代Ro Dip中,车身在槽中可以360°自由旋转,并且是反向浸渍的,这就给预处理和电泳车身输送和工艺处理带来了巨大的变化。
其特殊的结构和突出的优点在生产过程中得到了充分的体现。
3 RO Dip的结构和特点
Ro Dip-Technology中文可译成全旋反向浸渍输送技术。
全旋是指车身可以360°自由旋转,反向浸渍是指车身入槽时旋转180°后底部向上,尾部向前反向前进。
Ro Dip输送系统是先将车身锁紧在滑橇上,再将滑撬锁紧在一根可以360°旋转的轴上。
这根轴的一边有一连续杠杆导辊
系统,其导向轮所处的位置决定了车身旋转的角度。
当车身移动到浸槽口时,导向轮让轴旋转90°,车身头部迅速垂直向下,当主轴再向前移动,车身再逐步旋转90°变成底向上,尾向前反向继续前进,在达到工艺要求的时间后,开始出槽,这时车身在杠杆导辊系统的作用下连续旋转180°变为正常方向前进,
Ro Dip的特殊结构形成了其显明的特点:
(1)车身可以在浸槽中360°任意旋转是Ro Dip最大的特点。
车身可根据工艺要求,任何时候处于任何角度,车身可以在浸槽中不停地摆动,使空腔内的槽液得到充分的流动,从而提高内腔的涂装质量。
(2)槽上方无任何输送设备,输送链和导向设备位于槽子外面两侧附近,不会因输送系统加油润滑等原因造成对槽液和车身的污染。
输送系统受酸雾、水蒸气的侵蚀也较少。
(3)车身的顶部和侧面均无输送设备,这样吊架滴水的问题可以彻底克服。
(4)由于无吊架或摆杆的干扰,在电泳槽中阳极管的排布可以更加自由合理。
底部阳极管也更好布置。
因为车顶直接对着阳极管,中间没有滑橇相隔。
(5)输送链完全平直,不随车身的位置在通道内上下起伏。
以60辆/h的预处理电泳线为例。
其输送链可以比双摆链缩短188 m,厂房的面积也可以相应缩小。
节点可以少78%。
返回链可以安排在槽体的下方,也可以放在上方。
(6)Ro Dip生产线的槽子是长方体的,与45°入槽相比每个浸槽的长度可以缩短6m,见图3-8-2。
水洗槽的长度只要一个车身长度+0.6m就行了。
通常摆杆到车身的距离为0.4m,RO Dip因无摆杆,槽子可以窄0.8m。
车身反向后只有车身和滑橇在槽液中,所以槽子的深度也可以略小一些。
槽子的总体积可以缩小19%~33%左右。
3.8.4 Ro Dip的优点
Ro Dip的特殊结构,带来了一系列明显的优点。
主要的有以下几个方面:节省投资:与采用双摆链的预处理电泳线相比,采用Ro Dip技术总投资大约可以节省15%左右。
这是由于槽体积缩小,循环泵数量减少,生产线和输送链缩短等原因造成的。
节能、节电:采用Ro Dip技术可以节省7%的电能,对一条大型生产线而言,其加热量可以从3 825 KW降到2935 KW,节省890KW,致冷量可以节省63 KW。
预处理的循环泵功率可以由925 KW降到662 KW,节省263 KW。
节省化学品:初次投槽时预处理材料可以节省19%,电泳漆可以节省33%。
一般大型电泳槽的体积在300m3以上,初次投槽可以少投100多吨槽液,价值120万元以上。
槽液的更新周期可以缩短三分之一,这对槽液参数的稳定及产品质量的提高均十分有利。
由于车身槽液夹带量非常少,可以节省化学品的消耗,在德国一条大型电泳线上,一年可因此节省的电泳漆,价值75万马克。
节水:由于车身是180°旋转出槽的,空腔内的槽液可以流得比较干净,槽液夹带量少,冲洗水量可以减少25%,废水的处理量也可以减少25%。
节省三废处理费用,有利于环境保护。
槽液污染少:除了没有输送链滴油,吊架滴水等对槽液的污染外,由于没有吊架或摆杆反复进出,这方面的污染也可以完全消除,因为大量的吊架或摆件反复出入各个不同的化学品处理区或暴露于空气中,必然会给槽液带来一定的污染。
节省维修费:由于输送链平直,节点少,所以设备运行平稳,可靠性高,寿命长。
由于输送链位于槽外侧的走道边。
所以维修十分方便。
维修保养工作量低,费用自然也降低。
工艺选择性强:在同一区域,可以进行浸渍处理,也可以让车身在槽上面行走,进行喷淋处理,这对于铝含量高的车身的磷化处理十分有利。
也可以让车身在该区域空跑,不作处理,根据工艺的不同要求可灵活选择处理方式。
这样更改工艺就简单多了。
适合柔性生产,在同一条线上可以适合多种车型的不同工艺要求。
产品质量显著提高:彻底根除了输送系统滴水、滴油、滴液对车身和槽液的污染;彻底消灭
了车身前后盖,车顶内和轮圈内的气泡;电泳漆膜均匀,普通电泳膜厚的波动在4μm左右,Ro Dip 系统涂装后的膜厚波动只有1.3μm。
平面和垂直的膜厚差距在1~2μm之间,流挂滴液减少,三平面的电泳漆沉淀减少,流平性好,漆膜光滑细致,打磨工作量少,节省打磨材料;车身内腔的电泳质量提高,其泳透率远高于其他输送系统。
可以提高车身的防腐蚀能力。