韶钢气烧石灰竖窑工艺技术优化实践
韶钢气烧石灰竖窑工艺技术优化实践
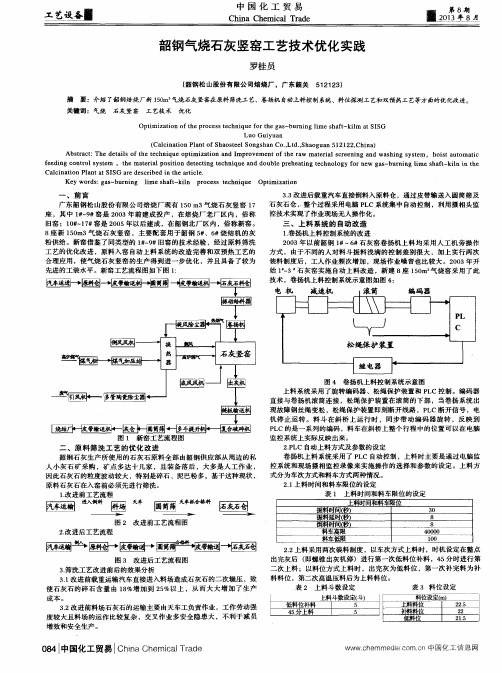
( Ca l c i n a t i o n P l a n t o f S h a o s t e e l S o n g s h a n Co . , L t d . , S h a o g u a n 5 1 2 1 2 2 , Ch i n a )
一
、
3 . 3 改进 后载重 汽车直接倒料 入原料 仓 ,通过皮 带输送 入圆 筒筛及 石灰 石仓 , 整个 过程采 用 电脑 P L C系 统集 中 自动控 制 ,利用摄相 头监 控技 术实现 了作业现 场无人操 作化 。
三、上料 系统的 自动改造
1 . 卷扬机 上料控 制系统 的改进 2 0 0 3 年 以前 韶钢 1 # ~ 6 群石灰窑卷 扬机 上料 均 采用 人工 机旁 操作 方 式 ,由于不 同的人对 料 斗振料 浅满 的控制 差别 很大 ,加 上实行 两 次 装料制度 后 ,工人 作业频 次增加 ,现场作 业噪 音也 比较 大 。2 0 0 3 年 开 始1 ~ 3 石灰窑 实施 自动 上料改 造 ,新 建 8座 1 5 0 ma 气烧 窑采 用了 此 技术 ,卷扬 机上料 控制系统 示意图如 图 4 :
石灰 竖 窑 工 艺技 术 优 化
关 键 词 : 气烧
Op t i mi z a t i o n o f t he p r oc e s s t e c h ni qu e f or t h e ga s -b ur n i n g l i me s ha f t -ki l m a t S I S G
Abs t r a c t :The de t a i l s o f t he t e c h ni qu e o pt i mi z a t i o n a n d I mp r ov e me nt of t he r a w ma t e r i a l s c r e e n i n g a n d wa s h i n g s y s t e m , ho i s t a u t o ma t i c
气烧麦尔兹石灰竖窑的生产操作优化

整合 后 数 据 实 现 了实 时 共 享 ,各 环节 运 行 规 范 顺 畅 ,已基 本 达 到 预 期 目标 。现在 从 顾 客 的需
()排产计划 编制和传输 :排产计划 由业 1
务公司合 同员录入 ,计划信息科计划员进 行汇
总 和 编制 排 产 计 划 ;热 轧 系 统 定 时访 问经 销 系
窑是从瑞士引进 的大型先 进石灰竖窑 ,以转炉 煤气为燃料 ,设计年产优 质冶金石灰 3 万 吨 , 6 分别于 20 — 6 0 80 投产 。投产后 由于煤 0 80 、20 — 7
制度 ,很好地解决 了煤气 热值波动对产品质量
的影响和窑炉安全运行的威胁 。
24 煤气供 应量 偏低 时 的应对 措施 .
()窑前仓 保持高料 位加料 ,减少 二次碎 1
石量 。
( 2 )适 当延长停窑后喷枪冷却时间,改变停 窑即停喷枪冷却风机的做法 。
此 ,我们结合产 品的实物质量要求确定 了一个 最佳 的助燃风过剩 系数 。同时 ,在产量 较低时 适 当降低助燃 风过剩 系数 ,在产量较高时适当 增加助燃风过剩系数。
需在 8 h内将通道温度 、废气温度缓慢恢复正常 后 ,保温 6 8 , ~ h 然后改回原设置产量。
26 其 它优化 措施 .
人 窑 煤 气 量 恒定 的条 件下 :增 加 助燃 风过
剩系数 ,通道温度会降低 ;降低助燃 风过剩 系
数 ,通道温度会升高 。但是过多 的助燃 空气会
产生过多的废气量 ,窑 的工作压力和热损失会 增加 ,制约窑产量 的提高和增加燃料消耗。因
( 3 )备用煤 气风机 和空气 风机每月定时轮
气烧矩形石灰竖窑大修优化设计
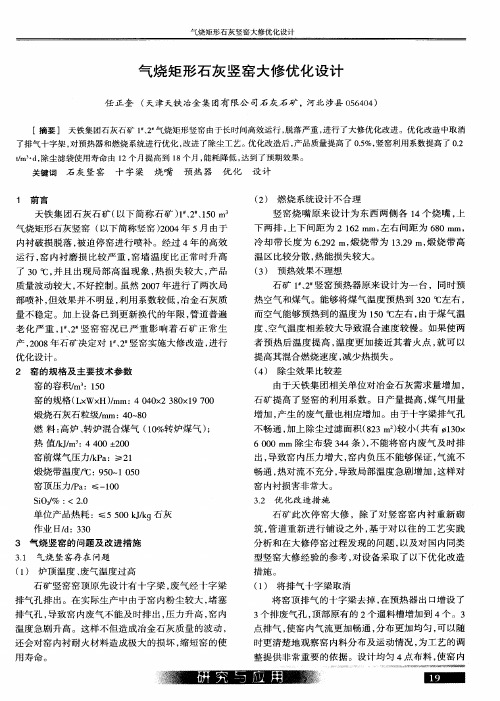
而空 气能够预热到 的温度 为 10℃左右 , 5 由于煤气 温 度、 空气 温度相差较 大导致 混合速度较慢 。如果使 两 者 预热后 温度提 高 , 温度 更加接 近其着 火点 , 就可 以
提高其混合燃烧速 度 , 减少 热损失 。
( ) 除 尘 效 果 比较 差 4
t 3d 除 尘 滤 袋 使 用 寿 命 由 1 月 提 高 到 1 个 月 , 耗 降 低 , 到 了预 期 效 果 。 / ・, m 2个 8 能 达
关键词 石 灰 竖窑 十 字梁
1 前 言
烧嘴
预热 器
优化
设 计
( ) 燃烧 系统设计不合理 2 竖窑烧 嘴原来 设计 为东西 两侧 各 1 4个烧 嘴 , 上
2 1 年第6 00 期
天舜 分 幺
( ) 除 尘 工 艺 的 改进 4
原料高度 比较 接近 , 粒度 分布更加均 匀合理 , 减少 了
粒度不均带来生烧 过烧 的问题 。
对除尘器进行了改造 , 由原先 的 4 除尘箱体增 个 加到 6 , 个 除尘总过滤面积 由 83m 增加到 1 3 z 2 2 6I 2 n ( 10 600 m  ̄ 3 x 0 m除尘布袋 34条 )除尘效果明显增 4 ,
不 畅 通 , 上 除 尘 过 滤 面 积 (2 2 小 ( 有  ̄ 3 x 加 83m ) 较 共 10
60 0m 0 m除尘布 袋 3 4条 )不能将 窑 内废气 及时排 4 ,
出, 导致窑 内压力增大 , 内负压不 能够保证 , 窑 气流不 畅通 , 热对 流不充分 , 导致局部温度 急剧增加 , 这样对
窑 内衬 损 害 非 常 大 。
32 优 化 改 造 措 施 .
竖窑产能提升的技术改造

采用不一次上到位,根据顶温分段上料。出料采用延长每一次
的出料时间,在原来的基础上每次增加2分钟的出料时间,以
此来保证产量的提高,同时窑内“三带”得到稳定;窑顶压力
采用废气除尘排烟机调控式“微负压”控制,由180~270Pa
改为-80~0Pa;煅烧区温度控制在1000~1100℃。实施后,
窑内物料循环由原来24h缩短到18h。
整理课件
谢 谢!
整理课件
整理课件
项目实施效益
效益计算:单窑平均每天增产30.73吨,3 窑每天共增产92.19吨,每吨石灰销售价 370元,每吨石灰成本324.72元,每吨石 灰利润45.28元。
92.19t/天×30天/月×12个月/年= 33188.4t/年。
3318.4t/年×33.28元/t=1502770.7元/ 年。
项目实施效果
从上表的统计对比可以看出,通过提高助燃风的入 窑风量,改善窑内的煅烧状况,加快窑内物料的煅 烧分解速度和冷却速度。1#120m3石灰竖窑日生 产量已由未改造前的平均102.17吨/日上升到改造 后的平均132.9吨/日;改造前石灰质量平均活性 度218.13ml,平均CaO含量88.53%,改造后石 灰质量平均活性度225.87ml,平均CaO含量 89.80%。保证了质量,提高了产量,极大地提高 了3×120m3石灰竖窑的有效利用系数,取得了良 好的效果和经济效益。
4.2.2、在鼓风机的出口管道上增设流量孔板和差压变送器,对入窑风量、 风压进行检测。
整理课件
改造后的风机效果图
整理课件
工艺改进
快烧快冷煅烧工艺的应用
我车间传统石灰生产工艺采用“七进七出”进出料制度和废气 直排式“正压”控制,窑内物料循环慢,窑内透气性差,造成
浅谈石灰窑煅烧工艺的改进杨亮山

浅谈石灰窑煅烧工艺的改进杨亮山发布时间:2023-07-14T08:02:33.739Z 来源:《工程建设标准化》2023年9期作者:杨亮山[导读] 冶金石灰是炼钢中的重要原料,它的用量很大,它的质量直接关系到炼钢的生产效率、能耗、钢材的消耗、钢材的质量以及经济效益。
90年代末,麦尔兹窑、套筒窑、日本的焦炭竖窑技术等都取得了一些成效,但是由于资金问题,一直没有得到广泛的应用。
目前,在石灰工业中,垂直烧成的固体燃料石灰占了很大比重。
如何对这类竖窑进行改造,在原有的基础上,大大提高产品的品质,降低生产成本,是目前我国的一个重大课题。
新疆圣雄电石有限公司新疆维吾尔自治区吐鲁番市 838100摘要:冶金石灰是炼钢中的重要原料,它的用量很大,它的质量直接关系到炼钢的生产效率、能耗、钢材的消耗、钢材的质量以及经济效益。
90年代末,麦尔兹窑、套筒窑、日本的焦炭竖窑技术等都取得了一些成效,但是由于资金问题,一直没有得到广泛的应用。
目前,在石灰工业中,垂直烧成的固体燃料石灰占了很大比重。
如何对这类竖窑进行改造,在原有的基础上,大大提高产品的品质,降低生产成本,是目前我国的一个重大课题。
关键词:石灰窑;煅烧;改进一、石灰窑主要设备及配套设施(一)石灰窑的基本结构和设备石灰窑由窑体、送料装置、布料装置、燃烧装置等构成。
不同类型的石灰窑,其结构、锻烧方式各有差异,生产工艺大致相同,但其生产设备的价值却相差甚远,其应用效果也必然存在差异。
(二)主要设备石灰窑的主要辅助设备有送料装置、布料机、送风装置、燃烧装置、排灰装置等,相对来说,混合烧制石灰窑布料是最重要的,因为当燃料与石灰石一起进入窑内时,需要用布使炉料在窑内得到合理的分配,从而消除炉壁的影响,平衡炉内的阻力,使整个炉段“上火”均匀。
布袋的形状和使用效果直接关系到烧结机的生产效率。
目前生产的布料器种类繁多,如旋转布料器、海螺布料器、固定布料器等,技术中心开发的三段式布料器,充分发挥了“漏斗喉效应”、“倒置 W型收料角”等作用,并与可调式挡料板组合在一起,具有结构简单、易于实现原料均匀搅拌、尺寸合理分配等问题的优点[1]。
韶钢气烧竖窑生产轻烧白云石的工艺技术
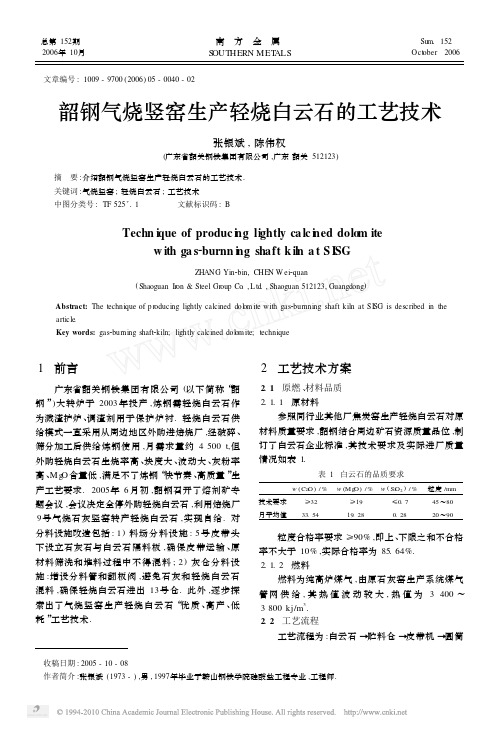
总第152期2006年10月 南 方 金 属S OUT HERN MET ALS Su m.152Oct ober 2006 收稿日期:2005-10-08 作者简介:张银斌(1973-),男,1997年毕业于鞍山钢铁学院硅酸盐工程专业,工程师. 文章编号:1009-9700(2006)05-0040-02韶钢气烧竖窑生产轻烧白云石的工艺技术张银斌,陈伟权(广东省韶关钢铁集团有限公司,广东韶关512123)摘 要:介绍韶钢气烧竖窑生产轻烧白云石的工艺技术.关键词:气烧竖窑;轻烧白云石;工艺技术中图分类号:TF 525+.1 文献标识码:BTechn i que of produc i n g li ghtly ca lc i n ed dolo m itew ith ga s 2burnn i n g shaft k il n a t S I SGZHANG Yin 2bin,CHE N W ei 2quan(Shaoguan Ir on &Steel Gr oup Co .,L td .,Shaoguan 512123,Guangdong )Abstract:The technique of p r oducing lightly calcined dol om ite with gas 2burnning shaft kiln at SI SG is described in the article .Key words:gas 2burning shaft 2kiln;lightly calcined dol om ite;technique1 前言广东省韶关钢铁集团有限公司(以下简称“韶钢”)大转炉于2003年投产,炼钢需轻烧白云石作为溅渣护炉、调渣剂用于保护炉衬.轻烧白云石供给模式一直采用从周边地区外购进焙烧厂,经破碎、筛分加工后供给炼钢使用,月需求量约4500t,但外购轻烧白云石生烧率高、块度大、波动大、灰粉率高、Mg O 含量低,满足不了炼钢“快节奏、高质量”生产工艺要求.2005年6月初,韶钢召开了熔剂矿专题会议,会议决定全停外购轻烧白云石,利用焙烧厂9号气烧石灰竖窑转产轻烧白云石,实现自给.对分料设施改造包括:1)料场分料设施:5号皮带头下设立石灰石与白云石隔料板,确保皮带运输、原材料筛洗和堆料过程中不得混料;2)灰仓分料设施:增设分料管和翻板阀,避免石灰和轻烧白云石混料,确保轻烧白云石进出13号仓.此外,逐步探索出了气烧竖窑生产轻烧白云石“优质、高产、低耗”工艺技术.2 工艺技术方案2.1 原燃、材料品质2.1.1 原材料参照同行业其他厂焦炭窑生产轻烧白云石对原材料质量要求,韶钢结合周边矿石资源质量品位,制订了白云石企业标准,其技术要求及实际进厂质量情况如表1.表1 白云石的品质要求w (Ca O )/%w (Mg O )/%w (Si O 2)/%粒度/mm技术要求≥32≥19≤0.745~80月平均值33.5419.280.2820~90 粒度合格率要求≥90%,即上、下限之和不合格率不大于10%,实际合格率为85.64%.2.1.2 燃料燃料为纯高炉煤气,由原石灰窑生产系统煤气管网供给,其热值波动较大,热值为3400~3800kj/m 3.2.2 工艺流程工艺流程为:白云石→贮料仓→皮带机→圆筒筛→皮带机→天车抓料→过渡料仓→容积斗→9号窑→螺锥机星型出灰机→链板机→多斗提升机→圆筒筛→皮带机→13号仓.2.3 工艺控制措施白云石中CaCO3在900℃左右开始分解,其最佳煅烧温度在1000~1100℃.而白云石中MgCO3在730℃左右开始分解,因此,生产轻烧白云石时应以MgCO3的分解为基础,但由于白云石为CaCO3与MgCO3以1∶1关系存在的复合物,因此单烧白云石对其温度控制不很敏感,只要适当减小物料在煅烧带的停留时间即可.2.3.1 工艺参数控制煤气压力19.5~21kPa;煤气流量8000~9000m3/h;侧风流量6000~6500m3/h;底风流量4500~5500m3/h;上料量10~12斗/批.2.3.2 工艺操作1)上料在轻烧白云石生产过程中,吸取气烧竖窑生产石灰的先进操作,采取了“分批装料,高温压料”操作:出完灰后,加料5~6斗,等到下一次出灰前约15m in,即窑顶烟气温度达到450℃左右时再压料5~6斗.从而降低窑顶烟气温度,控制在250~450℃,减少了热损失,同时也稳定了利用热烟气作热源的煤气和空气预热温度.2)出灰由于7号、8号、9号窑出灰后共用2号链板机输送,而轻烧白云石和石灰是两种成品,所以只能分开出灰.实际操作是:正点时先出7号和8号窑的石灰,待石灰出完全部进仓后,再出9号窑的轻烧白云石,通过打翻板分料,分仓指定进入13号仓.3 存在问题及改进措施1)轻烧白云石易粉化特性及全灰进仓,导致成品中灰粉率高,粉率约有15%~20%.焙烧厂已计划对轻烧白云石筛分、分料工艺进行改进,筛下的粉料进中间仓,实施处排处理,提高块灰的成品质量.2)烟气外排粉尘量大.一是调整优化工艺参数,降低煅烧粉化率,适当减低烟气总量;二是对旋风除尘器、换热器及多管陶瓷除法器集灰斗的卸灰机进行检修或更换,加强密封性,改善烟气除尘效果.3)出灰过程中时有塌料现象,不利于窑况稳定、顺行.一是加强白云石原材料进厂质量把关,减少杂质量,改善白云石的筛洗质量;二是改进出灰制度,由每小时出一次灰改为每半小时出一次灰,增加窑炉松料频次,减少棚料、挂炉现象.4 结语1)随着炼钢溅渣护炉工艺的广泛推广,以燃烧低热值高炉煤气的竖窑生产轻烧白云石工艺技术是可行的.2)韶钢气烧竖窑在生产石灰的经验基础上,通过优化调整工艺参数,利用现有设备,成功探索出生产“优质、高产、低耗”轻烧白云石,为同行业气烧竖窑转产轻烧白云石或焦炭窑改气烧生产轻烧白云石提供了宝贵技术经验.3)轻烧白云石生产中灰粉率高,必须通过生产操作、工艺改进或设备整改,进一步降低成品灰粉率,实现优质保供.参考文献[1] 李寿庭,王诚训,任方卓.转炉用耐火材料生产工艺[M]北京:冶金工业出版社,1992.标 题 新 闻宝钢名列2006年度世界500强第296位.14总第152期张银斌等:韶钢气烧竖窑生产轻烧白云石的工艺技术。
气烧石灰竖窑工艺事故原因和处理

c o mb us t i o n v e r t i c a l l i me k i l n
Wa n g Gu o q i a n g B i n Ho n g we i L i a n g F e n l a n ( S o n g s h a n Co . , L t d . , o f S h a o s t e e l ,S h a o g u a n 5 1 2 1 2 2,C h i n a )
中图分类 号 :T Q 1 7 5 . 6 5 4
文 献标 识码 :A
文章 编号 :1 6 7 3 — 7 7 9 2( 2 0 1 4 )0 3 — 0 0 1 6 — 0 3
Ca u s e a n d h a nd l i ng o f a c c i de n t s i n pr o c e s 将 明显 地 影 响气
体 流动过 程 的阻 力 损 失 。在 靠 近 窑 壁处 , 物 料堆 积 与 窑壁之 间 的孔 隙率 与物料 之 间堆积 的孑 L 隙率 相 比
较大, 加 之物 料高 温 收缩造 成环 形缝 隙 , 使得气 流 易 于从 周边 通 过 , 即在 窑的 同一 断面上 , 周边 空气 和煤 气 的分 配较 中心处 为 多 , 由于空 气 、 煤 气分 配 的不均 匀, 致使 在 同一断 面 温 度 不 均匀 , 煅烧 不 均 匀 , 这一 现 象就 是窑 壁效应 。 1 . 2 石 灰 石的 化学 成分 因素 石灰 石 的 化 学 成 分 主要 是 C a C O ,还 含 有
韶钢气烧石灰竖窑工艺技术优化实践

韶钢气烧石灰竖窑工艺技术优化实践摘要:介绍了韶钢焙烧厂新150m3气烧石灰竖窑在原料筛洗工艺、卷扬机自动上料控制系统、料位探测工艺和双预热工艺等方面的优化改进。
关键词:气烧石灰竖窑工艺技术优化一、前言广东韶钢松山股份有限公司焙烧厂现有150 m3气烧石灰竖窑17座,其中1#~9#窑是2003年前建成投产,在焙烧厂老厂区内,俗称旧窑;10#~17#窑是2005年以后建成,在韶钢北厂区内,俗称新窑。
8座新150m3气烧石灰竖窑,主要配套用于韶钢5#、6#烧结机的灰粉供给。
新窑借鉴了同类型的1#~9#旧窑的技术经验,经过原料筛洗工艺的优化改进,原料入窑自动上料系统的改造完善和双预热工艺的合理应用,使气烧石灰竖窑的生产得到进一步优化,并且具备了较为先进的工装水平。
新窑工艺流程图如下图1:二、原料筛洗工艺的优化改进韶钢石灰生产所使用的石灰石原料全部由韶钢供应部从周边的私人小灰石矿采购,矿点多达十几家,且装备落后,大多是人工作业,因此石灰石的粒度波动较大,特别是碎石、泥巴粉多。
基于这种现状,原料石灰石在入窑前必须先进行筛洗。
1.改进前工艺流程2.改进后工艺流程3.筛洗工艺改进前后的效果分析3.1改进前载重运输汽车直接进入料场造成石灰石的二次辗压,致使石灰石的碎石含量由18%增加到25%以上,从而大大增加了生产成本。
3.2改进前料场石灰石的运输主要由天车工负责作业,工作劳动强度较大且料场的运作比较复杂,交叉作业多安全隐患大,不利于减员增效和安全生产。
3.3改进后载重汽车直接倒料入原料仓,通过皮带输送入圆筒筛及石灰石仓,整个过程采用电脑PLC系统集中自动控制,利用摄相头监控技术实现了作业现场无人操作化。
三、上料系统的自动改造1.卷扬机上料控制系统的改进2003年以前韶钢1#~6#石灰窑卷扬机上料均采用人工机旁操作方式,由于不同的人对料斗振料浅满的控制差别很大,加上实行两次装料制度后,工人作业频次增加,现场作业噪音也比较大。
石灰竖炉(石灰立窑)工艺流程

【河南中材水泥设备制造网】石灰竖炉(又名石灰立窑、石灰回转窑),主要包括炉壁和设在炉壁上的烧嘴,在竖炉的中央植入一个柱状炉芯,炉芯和炉壁之间有环形间隙。
【关键词】石灰竖炉,石灰立窑,石灰回转窑,工艺流程一、石灰竖炉工艺概述装载机将合格的原燃料分别装入石灰石仓和煤炭仓,然后通过输送皮带运至混配料仓。
原燃料按设定值用电子秤准确称量,通过振动绘料机均匀给料后进行混匀,然后由提升料车把混合料运至炉顶受料斗,通过炉顶蜗壳式布料器完成炉内布料。
炉料靠自重缓慢向下运动,相继通过予热带、锻烧带、冷却带。
炉料在下降过程中,与炽热的上升煤气流进行着复杂的热交换,并伴随着石灰石的分解和生石灰的晶粒的发育成长过程。
当全过程完成时,也被助燃空气冷却降温至4 0 -- 6 0℃,然后由卸料机在不漏气的情况下卸至炉外成品皮带上。
由多斗提升机将石灰运至成品料仓。
如果需要筛分,先进行筛分后装入块灰仓和粉灰仓。
2..工艺特点(1) 自动称量、均匀配料对入炉石灰石和煤炭准确称量和合理配比是石灰竖炉优质锻烧和节能降耗的关键环节之一。
(2)均匀给料、旋转布料炉顶加料系统由受料斗、传动和旋转布料器组成。
由料车向旋转布料器均匀而定量给料,促使物料在入炉前进一步混合。
旋转布料器是圆周式定点布料,可自动也可手动定点布料,炉内断面上石灰石和煤炭呈"点、网"状分布,料面呈"M"形状,从而使炉内气流分布均匀,对锻烧带稳定起到了关键性的作用。
(3)合理供风、密封出灰该部分由离心风机、风帽、卸灰机组成。
风机按要求定量供风。
风帽则是我们自行设计,风帽保证炉内供风均匀,有效地抑制了竖炉的偏烧和过烧现象。
卸灰机可使园周各处排料均匀,保证料柱均匀平稳下降和料柱异常时的及时排除,既保证了炉内气流稳定和防止炉气外泄,又提高了现场环境。
(4)自动控制,安全可靠该石灰炉系统采用了自动控制技术。
在布料、混配、供风和卸灰等关键设备上使用了以确保各个关键设备的安全运行。
气烧石灰竖窑的窑壁效应产生原因、预防与处理方法
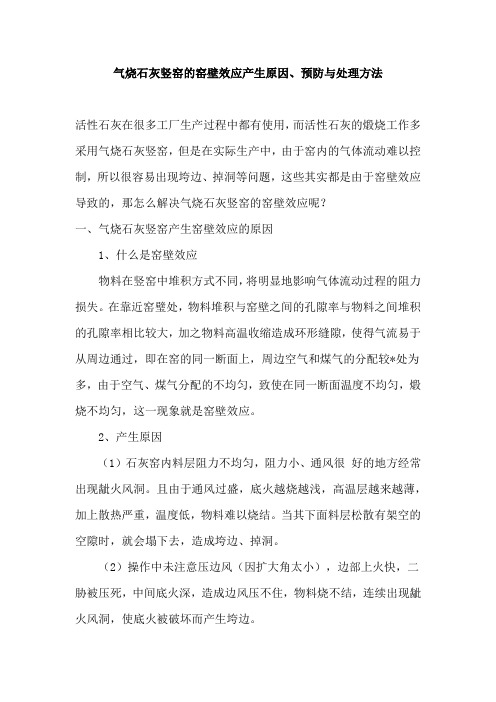
气烧石灰竖窑的窑壁效应产生原因、预防与处理方法活性石灰在很多工厂生产过程中都有使用,而活性石灰的煅烧工作多采用气烧石灰竖窑,但是在实际生产中,由于窑内的气体流动难以控制,所以很容易出现垮边、掉洞等问题,这些其实都是由于窑壁效应导致的,那怎么解决气烧石灰竖窑的窑壁效应呢?一、气烧石灰竖窑产生窑壁效应的原因1、什么是窑壁效应物料在竖窑中堆积方式不同,将明显地影响气体流动过程的阻力损失。
在靠近窑璧处,物料堆积与窑壁之间的孔隙率与物料之间堆积的孔隙率相比较大,加之物料高温收缩造成环形缝隙,使得气流易于从周边通过,即在窑的同一断面上,周边空气和煤气的分配较*处为多,由于空气、煤气分配的不均匀,致使在同一断面温度不均匀,煅烧不均匀,这一现象就是窑壁效应。
2、产生原因(1)石灰窑内料层阻力不均匀,阻力小、通风很好的地方经常出现龇火风洞。
且由于通风过盛,底火越烧越浅,高温层越来越薄,加上散热严重,温度低,物料难以烧结。
当其下面料层松散有架空的空隙时,就会塌下去,造成垮边、掉洞。
(2)操作中未注意压边风(因扩大角太小),边部上火快,二胁被压死,中间底火深,造成边风压不住,物料烧不结,连续出现龇火风洞,使底火被破坏而产生垮边。
(3)石料或燃料粉料比例过高,石料中二氧化硅含量高、熔剂或配煤量不够、煤料混合不匀,造成物料不易烧结。
二、解决气烧石灰竖窑窑壁效应的方法1、预防方法石灰石的分解速度与煅烧温度的关系取决于窑内高温空气的分布与走向,而高温空气的分布与走向主要取决于窑内石料粒度的分布,即石料与石料之间的空隙大小才是决定空气的流量和走向的关键,也是热能分配均衡的重要路径。
其关键点就在于如何把不同粒径的石料进行布置在不同区域内来达到,通过对小粒度石料之间因空隙小“风阻大”原理达到热风流速慢、热量少而缩短煅烧时间,同时增加大粒度石料区域的高温空气流量和流速加快煅烧时间,使窑内煅烧带热量均衡、阻力均衡,达到整个窑面“上火”均匀一致。
气烧活性石灰竖窑的技术改造研究
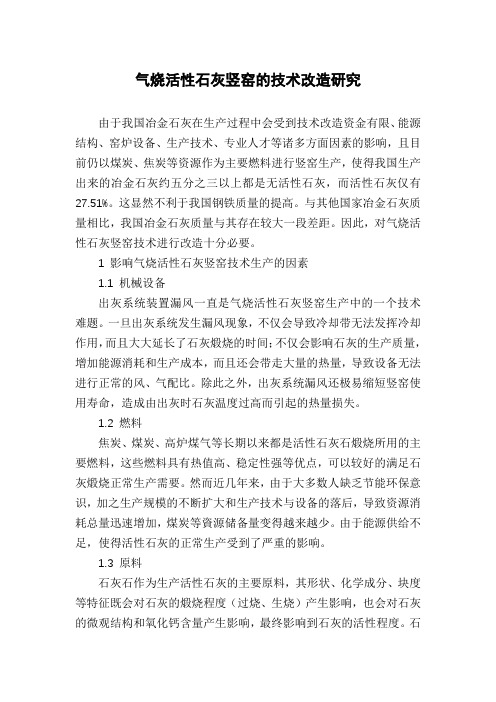
气烧活性石灰竖窑的技术改造研究由于我国冶金石灰在生产过程中会受到技术改造资金有限、能源结构、窑炉设备、生产技术、专业人才等诸多方面因素的影响,且目前仍以煤炭、焦炭等资源作为主要燃料进行竖窑生产,使得我国生产出来的冶金石灰约五分之三以上都是无活性石灰,而活性石灰仅有27.51%。
这显然不利于我国钢铁质量的提高。
与其他国家冶金石灰质量相比,我国冶金石灰质量与其存在较大一段差距。
因此,对气烧活性石灰竖窑技术进行改造十分必要。
1 影响气烧活性石灰竖窑技术生产的因素1.1 机械设备出灰系统装置漏风一直是气烧活性石灰竖窑生产中的一个技术难题。
一旦出灰系统发生漏风现象,不仅会导致冷却带无法发挥冷却作用,而且大大延长了石灰煅烧的时间;不仅会影响石灰的生产质量,增加能源消耗和生产成本,而且还会带走大量的热量,导致设备无法进行正常的风、气配比。
除此之外,出灰系统漏风还极易缩短竖窑使用寿命,造成由出灰时石灰温度过高而引起的热量损失。
1.2 燃料焦炭、煤炭、高炉煤气等长期以来都是活性石灰石煅烧所用的主要燃料,这些燃料具有热值高、稳定性强等优点,可以较好的满足石灰煅烧正常生产需要。
然而近几年来,由于大多数人缺乏节能环保意识,加之生产规模的不断扩大和生产技术与设备的落后,导致资源消耗总量迅速增加,煤炭等資源储备量变得越来越少。
由于能源供给不足,使得活性石灰的正常生产受到了严重的影响。
1.3 原料石灰石作为生产活性石灰的主要原料,其形状、化学成分、块度等特征既会对石灰的煅烧程度(过烧、生烧)产生影响,也会对石灰的微观结构和氧化钙含量产生影响,最终影响到石灰的活性程度。
石灰石的化学成分与形状等特征与其所在地理位置和当地气候条件等有着直接的关系。
有些石灰石矿山地质结构复杂,岩石种类多样,导致石灰石原料成分波动性大,不利于煅烧;有些石灰石质地坚硬、结构致密,不易分解,在煅烧过程中往往需要花费较长时间。
2 气烧活性石灰竖窑技术对工艺的要求2.1 对透气性要求十分严格与回转窑不同,气烧竖窑对透气性具有较高的要求。
论竖窑煅烧冶金石灰工艺

论竖窑煅烧冶金石灰工艺
是的,竖窑煅烧冶金石灰工艺是一种非常古老和有效率的是非技术。
泥坯用竖窑煅烧,可以快速地获得高品质的冶金石灰。
这种技术
通常被称为“砖窑烧”,像砖一样从挤压机挤出,然后烧制在窑炉内,形成冶金石灰。
砖窑烧的主要优点是可以一次完成一系列运行步骤,
从而减少原材料的损失,该技术也使用较少的能量和生产工艺,因此
能够实现较高的产量和质量。
此外,该技术还可以在更短的时间内完
成煅烧,因此减少了使用石灰的浪费。
竖窑石灰窑工艺流程
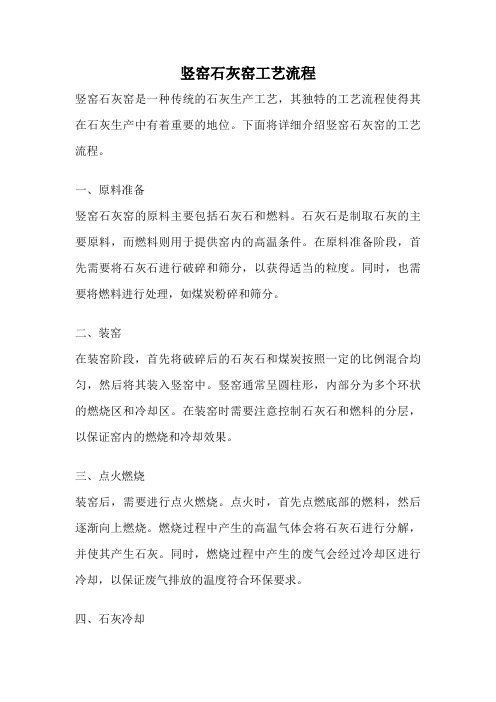
竖窑石灰窑工艺流程竖窑石灰窑是一种传统的石灰生产工艺,其独特的工艺流程使得其在石灰生产中有着重要的地位。
下面将详细介绍竖窑石灰窑的工艺流程。
一、原料准备竖窑石灰窑的原料主要包括石灰石和燃料。
石灰石是制取石灰的主要原料,而燃料则用于提供窑内的高温条件。
在原料准备阶段,首先需要将石灰石进行破碎和筛分,以获得适当的粒度。
同时,也需要将燃料进行处理,如煤炭粉碎和筛分。
二、装窑在装窑阶段,首先将破碎后的石灰石和煤炭按照一定的比例混合均匀,然后将其装入竖窑中。
竖窑通常呈圆柱形,内部分为多个环状的燃烧区和冷却区。
在装窑时需要注意控制石灰石和燃料的分层,以保证窑内的燃烧和冷却效果。
三、点火燃烧装窑后,需要进行点火燃烧。
点火时,首先点燃底部的燃料,然后逐渐向上燃烧。
燃烧过程中产生的高温气体会将石灰石进行分解,并使其产生石灰。
同时,燃烧过程中产生的废气会经过冷却区进行冷却,以保证废气排放的温度符合环保要求。
四、石灰冷却燃烧过程持续一段时间后,需要对石灰进行冷却。
冷却可以采用自然冷却或水冷却的方式。
在冷却过程中,石灰会逐渐固化,形成坚硬的石灰块。
冷却后的石灰块可以用于建筑材料、炼钢、环保等领域。
五、石灰取出冷却后的石灰块可以通过人工或机械的方式取出。
在取出过程中需要注意保护石灰块的完整性,避免石灰块破碎或损坏。
竖窑石灰窑工艺流程简单明了,但在实际生产中需要严格控制各个环节的参数,以确保石灰的质量和生产效率。
同时,竖窑石灰窑工艺也存在一定的能耗和环境污染问题,因此在使用过程中需要结合科学技术和环保要求,进行优化和改进。
石灰窑煅烧过程的能耗分析与优化策略研究

石灰窑煅烧过程的能耗分析与优化策略研究摘要:本文通过对石灰窑煅烧过程的能耗分析,提出了一些优化策略,以降低其能耗。
通过实验数据分析,发现降低石灰石粒度和提高煤种质量是降低能耗的有效方法。
此外,采用预热技术和优化燃烧方式也能够有效减少能耗,从而提高石灰窑的能源利用效率。
关键词:石灰窑、能耗分析、优化策略、预热技术、能源利用效率引言:石灰窑煅烧是生产石灰的重要工艺环节,但其能耗问题一直困扰着相关产业。
为了解决这一问题,本文对石灰窑煅烧过程进行了能耗分析,并提出了一些优化策略。
通过实验数据分析,我们发现降低石灰石粒度和提高煤种质量是降低能耗的有效方法。
此外,采用预热技术和优化燃烧方式也能够有效减少能耗,从而提高石灰窑的能源利用效率。
本文的研究结果对石灰窑煅烧的工业生产具有重要意义,并为节能减排提供了有益的参考。
一.石灰窑煅烧能耗分析石灰窑煅烧是生产石灰的重要工艺环节,其能耗问题一直是制约其产业发展的关键问题。
因此,对石灰窑煅烧过程进行能耗分析,对于找出能耗的主要来源,制定合理的优化策略,提高能源利用效率具有重要意义。
在石灰窑煅烧过程中,能源消耗主要集中在两个方面,即石灰石的煅烧和煤的燃烧。
其中,石灰石的煅烧是能源消耗的主要来源,其能耗占到煅烧过程总能耗的70%以上。
在煅烧过程中,石灰石的煅烧温度需要达到1000℃以上,燃烧所需的能量非常大。
此外,煤的燃烧也是能耗的一个重要来源。
针对以上问题,本文提出了一些优化策略。
1.降低石灰石粒度是降低能耗的有效方法之一。
石灰石的粉碎度越高,表面积就越大,煅烧过程中与空气接触的面积就越大,能耗就越低。
2.提高煤种质量也能够有效减少能耗。
优质煤的燃烧效率高,煅烧过程中能够释放更多的热量,能够满足煅烧过程中的能源需求。
3.采用预热技术和优化燃烧方式也能够有效减少能耗。
预热技术能够充分利用余热,减少能源浪费。
优化燃烧方式能够使煤的燃烧更加充分,达到更高的燃烧效率。
通过实验数据分析,本文证明了以上优化策略的有效性。
浅析韶钢烧结工艺的节能环保措施

浅析韶钢烧结工艺的节能环保措施陈永春 张铁梁(广东韶钢松山股份有限公司,广东 韶关 512123)摘要:随着科学技术的发展,我国钢铁生产技术水平显著提高,并在多个钢铁厂得到了广泛应用。
其中,烧结工艺是钢铁生产过程中的重要环节,很大程度上影响铁水产质量,从而制约企业市场竞争力。
同时,烧结工艺资源浪费较严重,烟气严重污染环境,与可持续发展理念不符。
对此,本文结合行业技术发展对韶钢烧结工艺近年的节能环保措施进行了分析,以供相关学者参考。
关键词:韶钢;烧结工艺;节能环保0 引言钢铁厂是我国主要的耗能大户和污染物排放大户,造成了严重的社会影响,不利于国民经济的可持续发展。
尤其是自党的十八大以来,我国先后推出了建设资源节约型社会理念和征收环境保护税的策略,促使钢铁厂优化生产结构,改善烧结工艺,以实现企业的经济效益和生态效益。
1 浅析钢铁厂烧结工艺烧结工艺是韶钢生产过程的重要环节,对产品的质量与产量有重要的影响,烧结工序能耗约占整个流程能耗的10%。
烧结即将各种原材料按一定比例混合后点火燃烧,使基本成分达到熔点生成液相,再采用鼓风冷却技术处理后整粒。
通过烧结工艺,能有效提高烧结体的强度,达到“高炉”精料要求,从而生产出高质量铁水以满足炼钢需求。
创新烧结工艺,优化生产流程,以控制生产成本,提高产品质量,实现企业的经济效益和社会效益非常有必要[1]。
2 探究烧结工艺的节能环保措施2.1 节能降耗2.1.1 优化烧结设备在烧结工艺中需要应用很多的设备组合,其功能、性能对资源能耗、生产成本等会造成很大的影响。
我国很多钢铁厂为了控制生产投资成本,常常使用中型或小型、性能低的设备。
在这种情况下,会加大资源浪费量、增加生产成本,反而不利于企业的发展。
对此,需要根据自身发展实际进行分析,尽可能购置大型、性能优良的烧结设备,如:韶钢烧结使用的微波水分仪。
能充分发挥设备的功能与性能,提升生产过程控制精度,提高生产效率,减少资源浪费等,以达到节能降耗的目的,提高企业的经济效益。
提高气烧石灰窑产品活性度的设备改进
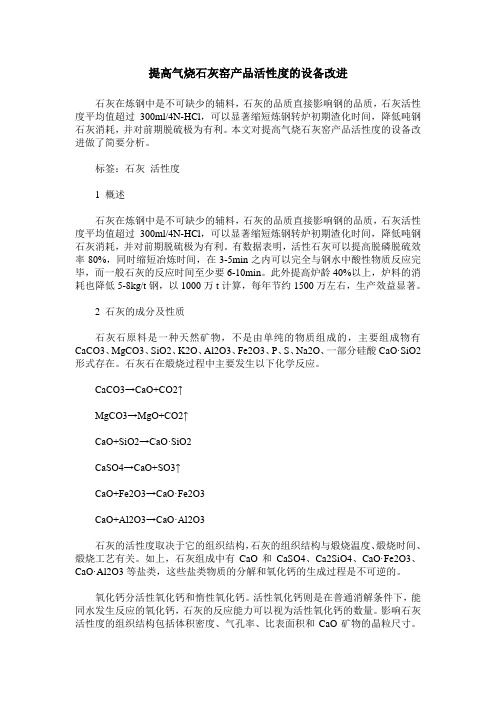
提高气烧石灰窑产品活性度的设备改进石灰在炼钢中是不可缺少的辅料,石灰的品质直接影响钢的品质,石灰活性度平均值超过300ml/4N-HCl,可以显著缩短炼钢转炉初期渣化时间,降低吨钢石灰消耗,并对前期脱硫极为有利。
本文对提高气烧石灰窑产品活性度的设备改进做了简要分析。
标签:石灰活性度1 概述石灰在炼钢中是不可缺少的辅料,石灰的品质直接影响钢的品质,石灰活性度平均值超过300ml/4N-HCl,可以显著缩短炼钢转炉初期渣化时间,降低吨钢石灰消耗,并对前期脱硫极为有利。
有数据表明,活性石灰可以提高脱磷脱硫效率80%,同时缩短冶炼时间,在3-5min之内可以完全与钢水中酸性物质反应完毕,而一般石灰的反应时间至少要6-10min。
此外提高炉龄40%以上,炉料的消耗也降低5-8kg/t钢,以1000万t计算,每年节约1500万左右,生产效益显著。
2 石灰的成分及性质石灰石原料是一种天然矿物,不是由单纯的物质组成的,主要组成物有CaCO3、MgCO3、SiO2、K2O、Al2O3、Fe2O3、P、S、Na2O、一部分硅酸CaO·SiO2形式存在。
石灰石在煅烧过程中主要发生以下化学反应。
CaCO3→CaO+CO2↑MgCO3→MgO+CO2↑CaO+SiO2→CaO·SiO2CaSO4→CaO+SO3↑CaO+Fe2O3→CaO·Fe2O3CaO+Al2O3→CaO·Al2O3石灰的活性度取决于它的组织结构,石灰的组织结构与煅烧温度、煅烧时间、煅烧工艺有关。
如上,石灰组成中有CaO和CaSO4、Ca2SiO4、CaO·Fe2O3、CaO·Al2O3等盐类,这些盐类物质的分解和氧化钙的生成过程是不可逆的。
氧化钙分活性氧化钙和惰性氧化钙。
活性氧化钙则是在普通消解条件下,能同水发生反应的氧化钙,石灰的反应能力可以视为活性氧化钙的数量。
影响石灰活性度的组织结构包括体积密度、气孔率、比表面积和CaO矿物的晶粒尺寸。
改进石灰竖窑煅烧工艺提高石灰质量

改进石灰竖窑煅烧工艺提高石灰质量
廉玉芝
【期刊名称】《水泥.石灰》
【年(卷),期】1993(000)001
【总页数】4页(P42-45)
【作者】廉玉芝
【作者单位】无
【正文语种】中文
【中图分类】TQ177.26
【相关文献】
1.影响安钢石灰竖窑产品质量的原因及改进措施 [J], 莫振涛
2.就持续改进韶钢气烧石灰竖窑技术之我见 [J], 何福礼
3.韶钢气烧石灰竖窑原料筛洗工艺技术的优化改进 [J], 罗桂员;王皓颖
4.麦尔兹气烧石灰竖窑的工艺改进 [J], 黄青;莫春;
5.石灰竖窑采用PC程控提高产品质量 [J], 廉玉芝
因版权原因,仅展示原文概要,查看原文内容请购买。
石灰石在竖式石灰窑内的煅烧工艺(精选5篇)

石灰石在竖式石灰窑内的煅烧工艺(精选5篇)第一篇:石灰石在竖式石灰窑内的煅烧工艺石灰石在竖式石灰窑内的煅烧工艺灰钙粉吧张志强关键词:石灰窑;氧化钙;灰钙粉;氢氧化钙1 竖式石灰窑结构简介竖式石灰窑内部分为3个区域,即预热区、煅烧区、冷却区预热区在窑的上部,其作用是使由煅烧区升上来的废气与新投入的石灰石和炭材相遇,进行热交换,对将进入煅烧区的石灰石和炭材进行预热,因为石灰石的分解温度为812℃,所以大家把预热区与煅烧区的温度分界点定为850℃。
煅烧区是在窑的中部,是窑内进行化学反应的主要区域,也是全窑温度集中的地方,中心温度可达1200℃,边缘区域的最低温度为815℃,由冷却区升上来的空气在此处起助燃作用。
煅烧区的温度和位置,决定于物料下降速度、混合料的粒度、风量大小、风压高低、窑料配比等因素。
煅烧区主要反应有:(a)燃料燃烧C + O2 = CO2+33 777 KJ/kg炭 C + O2 =CO+10216.5KJ/kg 炭(b)石灰石CaCO3分解CaCO3 =Ca0 + CO2-1788.9kJ/kg 冷却区是在窑下部,当煅烧好的生石灰下降到这个区域时,与鼓风机送入的冷空气相遇产生热交换,生石灰被冷空气冷却到1OO℃以下自窑下卸出。
进人窑内的空气则被生石灰预加热后,上升到煅烧区,参加燃烧反应。
2 影响石灰石煅烧的主要因素影响石灰石煅烧因素主要有煅烧温度、石灰粒度、石灰石与燃料(焦炭)的混合均匀程度。
2.1 温度对石灰石煅烧的影响石灰石煅烧速度与温度有极大关系。
煅烧温度在900℃时,每小时只能煅烧0.33 cm;若在1000℃时,则每小时可烧透石灰0.66 cm,加快1倍;若在1 1O0℃,则每小时烧透1.4 cm,加快了3倍。
通常实际生产中石灰窑的煅烧温度应控制在1050℃左右,故要求窑内温度稳定且均匀分布,要求三个区域的位置适宜,同一截面的温度最好一致,这样石灰石分解就得到保证。
如果煅烧区下移,将使生成的石灰得不到充分冷却,空气得不到充分预热,冷却区缩短;如果煅烧区上移,石灰石预热不好(预热区缩短),热气得不到冷却,窑气带出热量增加。
气烧石灰竖窑工艺事故及处理
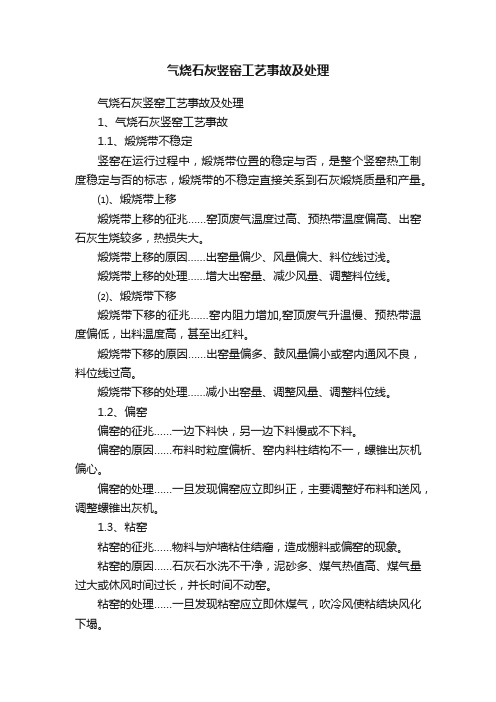
气烧石灰竖窑工艺事故及处理气烧石灰竖窑工艺事故及处理1、气烧石灰竖窑工艺事故1.1、煅烧带不稳定竖窑在运行过程中,煅烧带位置的稳定与否,是整个竖窑热工制度稳定与否的标志,煅烧带的不稳定直接关系到石灰煅烧质量和产量。
⑴、煅烧带上移煅烧带上移的征兆……窑顶废气温度过高、预热带温度偏高、出窑石灰生烧较多,热损失大。
煅烧带上移的原因……出窑量偏少、风量偏大、料位线过浅。
煅烧带上移的处理……增大出窑量、减少风量、调整料位线。
⑵、煅烧带下移煅烧带下移的征兆……窑内阻力增加,窑顶废气升温慢、预热带温度偏低,出料温度高,甚至出红料。
煅烧带下移的原因……出窑量偏多、鼓风量偏小或窑内通风不良,料位线过高。
煅烧带下移的处理……减小出窑量、调整风量、调整料位线。
1.2、偏窑偏窑的征兆……一边下料快,另一边下料慢或不下料。
偏窑的原因……布料时粒度偏析、窑内料柱结构不一,螺锥出灰机偏心。
偏窑的处理……一旦发现偏窑应立即纠正,主要调整好布料和送风,调整螺锥出灰机。
1.3、粘窑粘窑的征兆……物料与炉墙粘住结瘤,造成棚料或偏窑的现象。
粘窑的原因……石灰石水洗不干净,泥砂多、煤气热值高、煤气量过大或休风时间过长,并长时间不动窑。
粘窑的处理……一旦发现粘窑应立即休煤气,吹冷风使粘结块风化下塌。
1.4、塌窑塌窑的征兆……料柱下沉不顺行而产生局部或单边塌陷(窑边或窑中有漏洞),使生料下漏。
塌窑的原因……一般是由偏窑,严重粘窑或结坨较多而引起。
塌窑的处理……塌窑后要及时补料,减少风量,延长煅烧时间,使塌窑处阻力增加,逐步平衡窑内阻力。
1.5、悬窑悬窑的征兆……上部料结成料柱不下沉,而窑的下部仍能出料。
悬窑的原因……原料中杂质含量局部增多,入窑煤气偏流使局部燃气量过多,局部温度过高,且物料在高温处停留时间过长所致。
悬窑的处理……一旦发现粘窑应立即休煤气,吹冷风使粘结块风化下塌。
2、竖窑内气体的运动研究竖窑内气体运动,对于保证烧成带燃料燃烧所需要空气量的供应,气流在窑断面上的合理分布,以及降低气体流动过程阻力损失,保证竖窑产量、质量等方面都是有意义的。
- 1、下载文档前请自行甄别文档内容的完整性,平台不提供额外的编辑、内容补充、找答案等附加服务。
- 2、"仅部分预览"的文档,不可在线预览部分如存在完整性等问题,可反馈申请退款(可完整预览的文档不适用该条件!)。
- 3、如文档侵犯您的权益,请联系客服反馈,我们会尽快为您处理(人工客服工作时间:9:00-18:30)。
韶钢气烧石灰竖窑工艺技术优化实践
摘要:介绍了韶钢焙烧厂新150m3气烧石灰竖窑在原料筛洗工艺、卷扬机自动上料控制系统、料位探测工艺和双预热工艺等方面的优化改进。
关键词:气烧石灰竖窑工艺技术优化
一、前言
广东韶钢松山股份有限公司焙烧厂现有150 m3气烧石灰竖窑17座,其中1#~9#窑是2003年前建成投产,在焙烧厂老厂区内,俗称旧窑;10#~17#窑是2005年以后建成,在韶钢北厂区内,俗称新窑。
8座新150m3气烧石灰竖窑,主要配套用于韶钢5#、6#烧结机的灰粉供给。
新窑借鉴了同类型的1#~9#旧窑的技术经验,经过原料筛洗工艺的优化改进,原料入窑自动上料系统的改造完善和双预热工艺的合理应用,使气烧石灰竖窑的生产得到进一步优化,并且具备了较为先进的工装水平。
新窑工艺流程图如下图1:
二、原料筛洗工艺的优化改进
韶钢石灰生产所使用的石灰石原料全部由韶钢供应部从周边的私人小灰石矿采购,矿点多达十几家,且装备落后,大多是人工作业,因此石灰石的粒度波动较大,特别是碎石、泥巴粉多。
基于这种现状,原料石灰石在入窑前必须先进行筛洗。
1.改进前工艺流程
2.改进后工艺流程
3.筛洗工艺改进前后的效果分析
3.1改进前载重运输汽车直接进入料场造成石灰石的二次辗压,致使石灰石的碎石含量由18%增加到25%以上,从而大大增加了生产成本。
3.2改进前料场石灰石的运输主要由天车工负责作业,工作劳动强度较大且料场的运作比较复杂,交叉作业多安全隐患大,不利于减员增效和安全生产。
3.3改进后载重汽车直接倒料入原料仓,通过皮带输送入圆筒筛及石灰石仓,整个过程采用电脑plc系统集中自动控制,利用摄相头监控技术实现了作业现场无人操作化。
三、上料系统的自动改造
1.卷扬机上料控制系统的改进
2003年以前韶钢1#~6#石灰窑卷扬机上料均采用人工机旁操作方式,由于不同的人对料斗振料浅满的控制差别很大,加上实行两次装料制度后,工人作业频次增加,现场作业噪音也比较大。
2003年开始1#~3 # 石灰窑实施自动上料改造,新建8座150m3 气烧窑采用了此技术,卷扬机上料控制系统示意图如图4:
上料系统采用了旋转编码器、松绳保护装置和plc控制。
编码器直接与卷扬机滚筒连接,松绳保护装置在滚筒的下部,当卷扬系统出现故障钢丝绳变松,松绳保护装置即刻断开线路,plc断开信号,电机停止运转。
料斗在斜桥上运行时,同步带动编码器旋转,反映到plc的是一系列的编码,料车在斜桥上整个行程中的位置可以在电脑监控系统上实际反映出来。
2.plc自动上料方式及参数的设定
卷扬机上料系统采用了plc自动控制,上料时主要是通过电脑监控系统和现场摄相监控录像来实施操作的选择和参数的设定。
上料方式分为车次方式和料车方式两种情况。
2.1上料时间和料车限位的设定
2.2上料采用两次装料制度,以车次方式上料时,时机设定在整点出完灰后(即螺锥出灰机停)进行第一次低料位补料,45分时进行第二次上料;以料位方式上料时,出完灰为低料位,第一次补完料为补料料位,第二次高温压料后为上料料位。
四、石灰窑料位探测工艺技术的优化改进
2001年以前,焙烧厂1#、2#、3#气烧石灰竖窑料位探测基本上采用人工手拉探尺进行探料,后来7#~13#气烧石灰竖窑也仍然沿用此方式。
2006年以后实现了全部淘汰。
2000年,焙烧厂在4#、5#、6#气烧石灰竖窑上首次使用了激光料位计,2004年又在1#、2#、3#气烧石灰竖窑上进行了推广应用,由于成本原因2008年以后基本上全部淘汰。
2006年,焙烧厂开始进行机械探尺的研究,先是在10#~13#气烧石灰竖窑上实现了探尺的机械化运行,取代了劳动强度较大的人工拉探尺操作。
2007年将机械探尺信号接入plc控制,从而实现了与卷扬机上料系统的全自动化操作,成功研制出机械式自动探尺。
机械式自动探尺主要由电液推杆、变径滚筒、编码器、探料尺、plc 上料系统等组成。
1.机械自动探尺工作原理
机械探尺在硬件方面就是比手拉探尺增加了一个传动比为1:2
的变径滚筒、电液推杆和编码器。
机械探尺的动力部件为电液推杆,当需要探料时,电液推杆伸出,探尺从顶端下降,当探尺探测到料位后,停止运动,电液推杆继续伸出,到达最大量程后开始收回,带动探尺回到顶端,此为一个周期。
电液推杆行程为60cm,因为变径滚筒的传动比为1:2,因此探尺的行程为120cm。
因为气烧石灰竖窑每批料的料位变动大概100cm,因此量程足够。
机械探尺探料全过程由plc自动控制。
当气烧石灰竖窑出灰时,电液推杆开始动作,反复伸缩,每次时间间隔3秒,由plc设定,进行料位探测。
而探尺所移动的量程经过编码器将数据传递给plc,经过运算后在电脑上以曲线图的形式显示出来。
机械探尺原理如图5。
因为编码器是精确仪器,因此为了防止在探料时钢丝绳滑动造成的误差,在滚筒上方安装一个制动机构,使每次电液推杆伸出探料时,探尺到达料位顶端时钢丝绳停止滑动,将准确的数据传送给plc。
而电液推杆每次探料完毕自动收回,将探尺提到顶端,防止探尺被石灰石埋住。
机械探尺除了自动探料之外,还可以在电脑操作系统中设定出灰线的数据,在气烧石灰竖窑出灰时,料位达到了所设定的出灰线位置时,系统自动停止出灰。
机械探尺在卷扬机上料过程中也在动作。
卷扬机每上一斗料,倒料完毕,单斗开始下降后,机械探尺就开始动作,每次动作一个周期,然后自动停止,等待下一斗料倒料完毕再动作。
每次探尺探料
的数据由编码器记录。
编码器将数据传送到plc,经过运算后将数据以曲线图形形式在电脑上显示出来。
料位趋势图如图6。
2.机械式自动探尺应用后的效果分析
2.1产品质量明显提高
由于机械探尺能够准确、真实的传送气烧石灰竖窑内料位的变化情况,因此对气烧石灰竖窑产品冶金石灰的质量提高起到了重要作用。
石灰产品的质量和气烧石灰竖窑的利用系数明显得到了提高。
2.2消除人为因素,大大降低劳动强度
由于机械探尺增加了编码器,实现了plc控制,因此能够实现实时数据传送,并形象直观的在电脑上显示出来。
使操作工能及时的发现窑况问题,并及时处理。
相比手拉探尺,机械探尺通过自动控制,消除了人为因素,大大降低了工人的劳动强度,操作工由一人负责一座窑改为无人操作,使每批料都真正实现了数据的客观性、真实性,并且做到了数据图形的统一性。
从而达到了气烧石灰竖窑窑况的稳定、顺行,石灰产品质量的稳定提高。
2.3降本增效,大大提升气烧石灰竖窑自动化程度
机械式自动化探尺替代激光料位计大大降低了氮气消耗量,是气烧石灰竖窑生产降本增效的有效措施。
采用电液推杆为探尺驱动装置,推杆行程大小可反映探尺在窑内的升降高度,利用编码器将行程量转化为数字信号输入plc控制系统,从而实现气烧石灰竖窑料位的自动探测。
五、双预热工艺技术的应用
近年来,随着炼铁工艺技术的不断进步,高炉煤气热值不断降低(约为750×4.18kj/m3),成为石灰窑优质高产的制约因素。
韶钢焙烧厂在国内同类型气烧竖窑上首次设计采用了金属管式换热器,于2000年12月在4#~6#气烧石灰竖窑上研究应用了双预热工艺技术,并分别于2002年底在1#~3#旧石灰窑系统进行了应用性的技术改造,新建8座气烧石灰窑也继续采用了这种工艺比较成熟且较为先进的技术。
从投入使用到现在各窑热交换系统运行稳定,实现了无故障运行,效果良好。
1.双预热工艺技术
1.1管式换热器设计和原理。
空、煤气换热器为带“麻花插件”的金属管式换热器,采取串联整体安装,顺排逆流设计。
温度较高的石灰窑烟气经窑顶烟囱连接管引至旋风除尘后,进入换热器,与引进的冷煤气、冷空气进行热交换,热交换后的烟气则通过多管陶瓷除尘器除尘后,经引风机达标排放;热交换后的热空气和热煤气通过管道、烧嘴进入石灰窑进行混合、燃烧。
增设管式换热器,大大提高了煤气燃烧温度(石灰窑煅烧温度由950℃~1080℃提高到1000℃~1200℃),进而提高活性石灰质量与产量。
1.2 配置声波吹扫器。
用氮气作介质,实行定时、定量吹扫,及时清除粘附在金属管壁上的粉尘,确保换热器保持良好的导热系数,换热效果好。
2.双预热工艺技术的应用效果
2.1双预热工艺系统运行技术参数如下表4所示:
2.2应用双预热工艺前(旧1#~3#石灰窑)后的技术经济指标比较如下表5所示:
六、结束语
新建8座气烧石灰竖窑采用了焙烧厂1#~9#窑中较为先进的技术,各系统的工艺得到了大大优化,特别是筛洗工艺的优化,自动上料和双预热工艺的应用为气烧石灰窑的提质增产创造了有利的
条件。
料位探尺是气烧石灰竖窑装出料控制的重要工具,对气烧石灰竖窑的窑况和正常生产起着至关重要的作用,从而直接影响石灰的产品质量和产量。
采用手拉探尺,人为操作误差大,工人劳动强度也大,用工人数也多,非常不合理;采用激光料位计;一次投资成本高,运行费用也比较大;而采用机械式自动探尺,料位的准确性与灵敏度略低于激光料位计,但完全能够满足气烧窑对料位的探测和控制,不仅一次性投资小,且运行费用极低,机械探尺的故障也比较少,具有很好的实用价值,值得推广应用。
通过工艺技术优化,石灰窑可以实现从原料筛洗到上料、出灰、出库的全自动控制。
作者简介:罗桂员,男,1973.06.10,工程师。
现就职于广东省韶关市韶钢集团松山股份有限公司焙烧厂。