石英陶瓷
石英在陶瓷中的作用

石英在陶瓷中的作用
石英在陶瓷中起到了多种作用,具体作用如下:
1.加快干燥:在烧成前,石英作为瘠性原料,可降低泥料的可塑性,减少成型
水分,降低干燥收缩并加快干燥过程。
2.减小坯体变形:石英在高温时部分溶于液相,提高液相粘度。
石英晶型转变
的体积膨胀可以抵消坯体的部分收缩,从而减小坯体变形。
3.增加机械强度:残余石英可以与莫来石一起构成坯体骨架,增加机械强度。
同时,石英也能提高坯体的白度和透光度。
4.提高釉的耐磨与耐化学侵蚀性:在釉料中,SiO2是生成玻璃的主要组分。
增
加釉料中石英含量能提高釉的熔融温度和粘度,降低釉的热膨胀系数,提高釉的耐磨性、硬度和耐化学腐蚀性。
5.调节膨胀系数:石英的加入还可以调节陶瓷的膨胀系数。
1/ 1。
石英陶瓷的应用
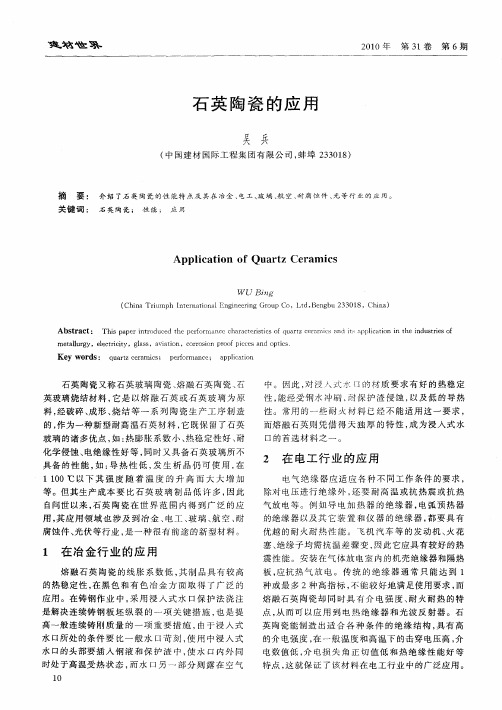
石英陶瓷 又称石英 玻璃 陶瓷 、 融 石英 陶瓷 、 熔 石
中 。因此 , 浸 式水 q 的材 质要 求 有好 的热稳 定 对 性 , 经受钢 水 冲刷 , 保 护渣 侵 蚀 , 能 耐 以及低 的导热
英玻璃 烧结材料 , 是 以熔 融 石 英 或石 英 玻 璃为 原 它
料, 经破碎 、 成形 、 结 等一 系 列 陶 瓷生 产 工序 制 造 烧 的, 作为 一种新 型耐高 温石英 材料 , 它既保 留了石英 玻璃 的诸 多优点 , : 如 热膨 胀 系数小 、 热稳定 性好 、 耐
11 0℃以下 其 强 度 随 着 温 度 的 升 高 而 大 大 增 加 0 等 。但 其生产 成本 要 比石 英 玻 璃 制 品低 许 多 , 因此
自问世 以 来 , 英 陶 瓷 在 世 界 范 围 内 得 到 广 泛 的 应 石
2 在 电工 行 业 的应 用
电气绝 缘 器应 适 应各 种 不 同工 作条件 的要 求 ,
点, 从而 可以应 用 到 电 热绝 缘 器 和光 波反 射器 。石 英 陶瓷能制 造 出适 合 各种 条 件 的绝 缘结 构 , 具有 高
应用 。在铸 钢作业 中 , 用 浸 人式 水 口保 护法 浇 注 采
是解决 连续铸 钢板 坯 纵裂 的一 项 关键 措 施 , 是提 也 高一般 连续铸 刚质 量 的一 项 重 要措 施 , 于浸 入式 由 水 口所 处的条件 要 比一 般 水 口苛 刻 , 用 中浸 入式 使 水 口的头部要插 入 钢 液 和保 护 渣 中 , 水 口内外 同 使
形 石 英 陶 瓷 坩 埚 是 太 阳 能 电 池 用 多 晶 硅 铸 锭 生 产 用
的主要 消耗 材 料 ,此种 坩埚 纯 度 高 、 内在 质量好 、 高
熔融石英陶瓷的配方

熔融石英陶瓷的配方
熔融石英陶瓷的配方通常包含以下材料:
1. 石英粉:石英是熔融石英陶瓷的主要成分,它具有高硬度、耐磨性和耐高温性能。
石英粉的粒径大小和分布对陶瓷的性能有一定影响。
2. 镁质材料:镁质材料可以提高熔融石英陶瓷的抗压强度和耐热性能。
常用的镁质材料包括镁粉、氧化镁等。
3. 磷酸盐:磷酸盐可以增加熔融石英陶瓷的塑性,提高成型性能。
常用的磷酸盐有磷酸三钠等。
4. 粘结剂:粘结剂可以增加熔融石英陶瓷的粘结力和保形性。
常用的粘结剂包括聚羧酸盐、硅酸盐等。
5. 其他添加剂:根据需求,还可以添加一些特殊的添加剂,如颜料、助燃剂等。
以上是一般常见的熔融石英陶瓷配方的主要成分,具体的配方比例和工艺条件可以根据具体的应用要求来确定。
石英陶瓷的研究及应用进展
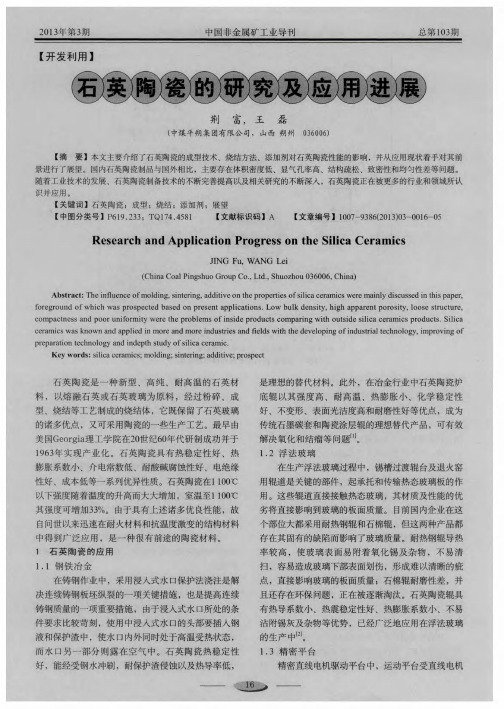
著提 高坯体密 度。振动压力 注浆成 型工艺在引入 振动
装置 的同时又引入压力 装置 ,以加快料 浆 中水分 的排
除 ,缩短 吸浆 时间 ,从而解 决了颗粒偏析 的问题 ,减 少 了坯 体内部存在 的缺陷 ,提 高了坯体 的密度和均匀 性 。振动压力注浆成型技术 的关键是要制备 出流动性
以上的高 温下连续工 作5 0 h 以上 ,使之熔 化 、长晶 ,
面 ,并通过液体介质 ,均等地作用在粉料 模件的各个
方向 ,使粉料 致密化 。这种 方法 ,可任 意改变塑性模 具的形状 和尺寸 ,工艺灵 活方便 ,适用性 强 ,坯 体在
然后 用来制造太 阳能 电池的多 晶硅硅锭 。 由于其使 用 条件 十分苛 刻 ,对坩埚的纯度 、强度 、外观及 内在 质 量 、高温性 能 、尺寸精度等都有十分严格 的要求 。石 英 陶瓷坩埚 是 目前不可替 代的材料 ,由于是一次性使 用 ,所 以需 求量巨大。近年来 ,随着经济 的发展 ,能
荆富等 :石英 陶瓷的研究及应用进展
初级部件 发热 影响最 大 ,所 以精密平 台应选择导热 系
随着科学 技术的发展 ,石 英陶瓷的新成 型工艺 不
断涌现并得到广泛应用 。 目前 ,应用较为成熟 的新成
数和热膨胀系数小 ,对 温度变化不敏感 的材料 。由于
石英 陶瓷具有导 热系数 低 ,使得热量不易传递 ,升温 减 缓 ;又 由于较 小 的热膨 胀 系数使 得 平 台热变 形较
的高 温粘度 ,因此 损坏速 度总 计只有0 . 0 2 5 mm/ s 。 在原子 能工业 中 ,作为在核 燃料 的基 质( S i 02 -UO体 系) 和辐射屏 蔽材料 使用 ,石英 陶瓷 的某些性 能还被 用作射 电望远镜的光学反射器使用 ,也 是红外线高 质
石英在陶瓷釉料中的作用的研究进展
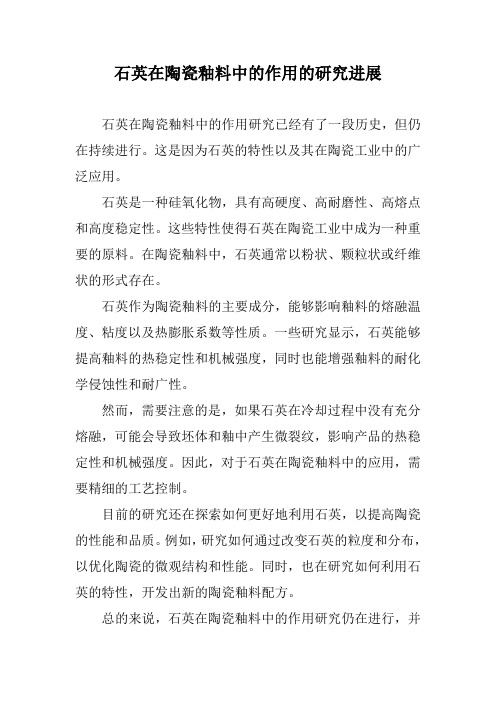
石英在陶瓷釉料中的作用的研究进展
石英在陶瓷釉料中的作用研究已经有了一段历史,但仍在持续进行。
这是因为石英的特性以及其在陶瓷工业中的广泛应用。
石英是一种硅氧化物,具有高硬度、高耐磨性、高熔点和高度稳定性。
这些特性使得石英在陶瓷工业中成为一种重要的原料。
在陶瓷釉料中,石英通常以粉状、颗粒状或纤维状的形式存在。
石英作为陶瓷釉料的主要成分,能够影响釉料的熔融温度、粘度以及热膨胀系数等性质。
一些研究显示,石英能够提高釉料的热稳定性和机械强度,同时也能增强釉料的耐化学侵蚀性和耐广性。
然而,需要注意的是,如果石英在冷却过程中没有充分熔融,可能会导致坯体和釉中产生微裂纹,影响产品的热稳定性和机械强度。
因此,对于石英在陶瓷釉料中的应用,需要精细的工艺控制。
目前的研究还在探索如何更好地利用石英,以提高陶瓷的性能和品质。
例如,研究如何通过改变石英的粒度和分布,以优化陶瓷的微观结构和性能。
同时,也在研究如何利用石英的特性,开发出新的陶瓷釉料配方。
总的来说,石英在陶瓷釉料中的作用研究仍在进行,并
有望在未来持续取得新的突破。
熔融石英坩埚的介绍

坩埚的介绍
④石英陶瓷的导热率很低,在1100℃以下几乎不变。
⑤石英陶瓷的抗弯强度随温度的升高而增加,这一点与其他陶 瓷不同,主要是由于石英陶瓷随着温度的升高其塑性增加脆性 减小的缘故。从室温到600℃。抗弯强度随温度的升高而增加 几乎呈线性。从室温到1100℃,刚玉陶瓷的抗弯强度降低67%, 而石英陶瓷反而增加33%I 21。 ⑥石英陶瓷坯体在干燥及烧成时收缩很小,一般小于5%,因 此,石英陶瓷易于制作大件制品。
双面注浆成型工艺介绍 石英砂 熔融 煅烧 水碎(煅烧后)
烧结
烘干
浇注成型
混合
烘干
成型
包装
技术研发部
石英坩埚的生产工艺及其特点
技术研发部
坩埚的检验
双面注浆成型的检测方法:
坩埚的检验要求
材料品质稳定,内部无缺陷 尺寸稳定 热力学与化学上的可靠性 可预见的晶型转变与铸锭工艺相符合 材料可以经历一个热循环过程 可预见的热传导性
石英坩埚的现状和趋势
技术研发部
石英坩埚的现状和趋势
坩埚的尺寸变化
• 从G4,G5,一直到G6,坩埚壁厚保持不变 • 坩埚体积增大,容纳的硅锭体积增大,少 子寿命<2微秒的红色区域基本不变,从而 硅锭有效利用率增加,而单位公斤的硅锭 能耗显著降低
技术研发部
石英坩埚的现状和趋势
坩埚的尺寸变化
250Kg 65%利用率 160Kg
铸锭工艺
讲解人: 讲解人:李刚 日期: 日期:2011.9.7
坩埚的介绍
石英陶瓷又称熔融石 英陶瓷 、石英玻璃陶 瓷 、石英玻璃烧结制 品 、熔融石英烧结制 品(
fused silica
或fused
silica ceramic) ,是采用
石英陶瓷制品裂纹产生的原因分析及控制方法

要 因素 。
石英料浆 具有触变性较 大 , 悬 浮性差 、 易沉淀等 特
点, 采用泥浆浇注成型方法生 产的石英 陶瓷制 品 , 容易
产生颗粒分布的不均匀 、 壁厚方向分层等缺陷; 又因其 含水量 高 , 干燥 过程 中容易使 制 品产 生微裂 纹 、 隐裂 、
上 海 建 树
石英陶瓷制品裂纹产生的 原 因分析及 控制 方法
上海玻璃钢研究院有 限公 司 胡 伟
石英 陶瓷制 品是 以石英玻璃为原料 ,采用 泥浆浇 注法成型 , 经过干燥 、 烧结等工序制作而成… 。石英陶瓷 制 品保持 了石英玻璃 的耐 高温热冲击 和低 的热膨 胀系 数、 低的热导率等优 良特性 , 而且还具有石英玻璃所 没
质量 , 提高制 品成 品率的重要 因素 。
陶瓷材料在受力和环境因素( 或二者联合 ) 作用下 会产生微观裂纹 , 随着作用力的变化 , 微裂纹不断扩展 , 最终导致制品开裂1 6 1 。 裂纹按照其形成的原因可分为以
下几种类型 : 加载 时形成 的裂 纹 ; 交变载荷下 的疲劳裂 纹; 应力和温度联合作用 下的蠕变裂纹 ; 应力 和化学介 质联合作用下 的应力腐 蚀裂纹 ;化学成份不 均匀产生
因此 , 控 制烧结 制度 , 既满 足性能 的要求 , 又 保证制 品 不 产生大量的 d一 方 石英 ,是提高石 英 陶瓷制 品成品 率 的关键 。石英 陶瓷制 品在 1 0 5 0 o C 时, p一方石英 会
温差 引起 的热应力将是永 久应力 ,制品在冷却过 程中 或后续工序 中会 因无法承受外力作用而开裂。
起裂纹 的原 因, 旨在有效抑制 裂纹的形核诱导 因素 , 消 除裂纹 的扩展条件 , 控制制 品的质量 , 提高产 品的成 品 率, 拓宽石英 陶瓷材料 的工程化应用领域 , 是 很有现实
陶瓷主要成分

陶瓷主要成分陶瓷是一种非金属材料,广泛应用于建筑、医学、电子等领域。
它具有耐高温、耐腐蚀、绝缘性能等优点,因此备受关注。
陶瓷的主要成分包括粘土、瓷土、石英、长石等。
本文将详细介绍陶瓷的主要成分及其特性。
1. 粘土:粘土是陶瓷制作中最常见的成分之一。
它主要由含有大量黏土矿物质的沉积岩变质而成。
粘土含有高比例的硅酸盐矿物质,例如膨润土、伊利石等。
这些矿物质使粘土具有塑性和可塑性,从而使其易于塑造成各种形状。
2. 瓷土:瓷土是陶瓷中的一种特殊粘土。
与普通粘土相比,瓷土中几乎不含有机质和杂质。
它主要由高岭石和石英砂组成。
瓷土的主要特点是具有较高的温度稳定性和耐腐蚀性。
因此,它在制作高温陶瓷时得到广泛应用。
3. 石英:石英是一种硅酸盐矿物质,也是陶瓷的主要成分之一。
它具有良好的热稳定性和化学稳定性。
石英能在高温下保持稳定的结构,不易熔化。
因此,石英在陶瓷中被广泛用作增强剂和填料。
4. 长石:长石是一种具有钠、钾和铝等元素的矿物质。
它在陶瓷中常被用作助熔剂,可以降低陶瓷的烧结温度。
长石还具有增加陶瓷强度和改善表面光洁度的作用。
除了以上几种主要成分外,陶瓷中还含有少量的辅助成分,如石膏、硼砂等。
这些辅助成分能够改善陶瓷的加工性能和性能特性。
陶瓷的主要成分在陶瓷制作过程中起着重要的作用。
首先,粘土的塑性使得陶瓷易于成型。
粘土的可塑性使得陶瓷制作过程中可以通过挤压、拉伸等方式塑造成各种形状。
其次,瓷土的高温稳定性使得陶瓷在高温下不易形变。
瓷土的耐腐蚀性能使得陶瓷具有很好的抗化学腐蚀性能。
石英的存在可以提高陶瓷的热稳定性和化学稳定性。
长石的加入可以降低陶瓷的烧结温度,提高陶瓷的强度和光洁度。
除了这些主要成分外,陶瓷的制作还需要考虑成分的配比、烧结温度和时间等因素。
成分配比的合理性直接影响到陶瓷制品的性能和质量。
正确的烧结温度和时间可以确保陶瓷具有良好的致密性和强度。
综上所述,陶瓷的主要成分包括粘土、瓷土、石英和长石等。
石英陶瓷基复合材料的特点

石英陶瓷基复合材料的特点
石英陶瓷基复合材料的特点包括以下几个方面:
1. 抗腐蚀性:石英陶瓷基复合材料具有极强的抗腐蚀性能,这是由于石英的高硬度和优良的抗化学腐蚀能力。
2. 抗高温性:石英陶瓷基复合材料可以承受极高的温度,这是因为石英和陶瓷都具有很好的高温性能。
这种材料可以在高温高压下稳定工作,而不会发生变形或损坏。
3. 抗疲劳性:石英陶瓷基复合材料的抗疲劳性和耐久性都很强,这得益于石英和陶瓷的结合。
这种材料的使用寿命较长,可以在长时间的使用过程中保持性能的稳定。
4. 绝缘性能优良:石英陶瓷基复合材料具有优良的绝缘性能,可以作为绝缘材料使用。
5. 加工性能好:石英陶瓷基复合材料的硬度较高,但加工性能良好。
这种材料可以进行研磨、打磨、切割等加工,方便了其在各种领域中的应用。
6. 应用范围广:由于石英陶瓷基复合材料具有上述优良特性,使其在航空航天、电子、化工、能源等领域中得到了广泛应用。
例如,它可以作为航空发动机部件的隔热材料、高温燃烧室的防护材料、电子器件的基板等。
此外,石英陶瓷基复合材料还可以用作建筑材料、环境材料等。
总的来说,石英陶瓷基复合材料是一种具有优异性能的新型材料,具有广泛的应用前景。
熔融石英陶瓷的制备技术综述
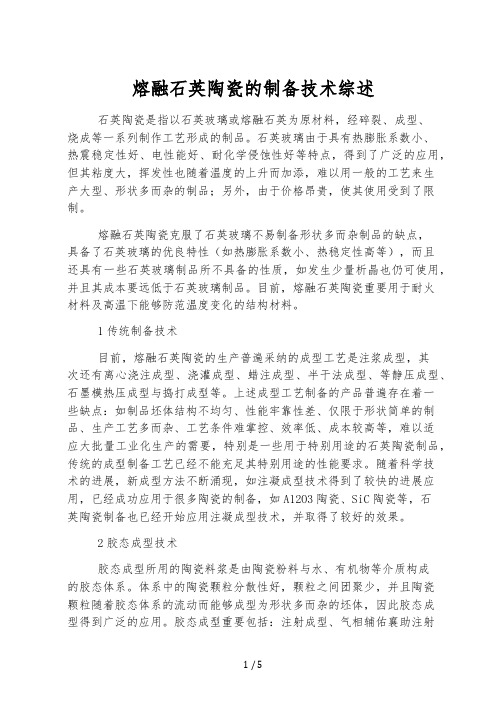
熔融石英陶瓷的制备技术综述石英陶瓷是指以石英玻璃或熔融石英为原材料,经碎裂、成型、烧成等一系列制作工艺形成的制品。
石英玻璃由于具有热膨胀系数小、热震稳定性好、电性能好、耐化学侵蚀性好等特点,得到了广泛的应用,但其粘度大,挥发性也随着温度的上升而加添,难以用一般的工艺来生产大型、形状多而杂的制品;另外,由于价格昂贵,使其使用受到了限制。
熔融石英陶瓷克服了石英玻璃不易制备形状多而杂制品的缺点,具备了石英玻璃的优良特性(如热膨胀系数小、热稳定性高等),而且还具有一些石英玻璃制品所不具备的性质,如发生少量析晶也仍可使用,并且其成本要远低于石英玻璃制品。
目前,熔融石英陶瓷重要用于耐火材料及高温下能够防范温度变化的结构材料。
1传统制备技术目前,熔融石英陶瓷的生产普遍采纳的成型工艺是注浆成型,其次还有离心浇注成型、浇灌成型、蜡注成型、半干法成型、等静压成型、石墨模热压成型与捣打成型等。
上述成型工艺制备的产品普遍存在着一些缺点:如制品坯体结构不均匀、性能牢靠性差、仅限于形状简单的制品、生产工艺多而杂、工艺条件难掌控、效率低、成本较高等,难以适应大批量工业化生产的需要,特别是一些用于特别用途的石英陶瓷制品,传统的成型制备工艺已经不能充足其特别用途的性能要求。
随着科学技术的进展,新成型方法不断涌现,如注凝成型技术得到了较快的进展应用,已经成功应用于很多陶瓷的制备,如A12O3陶瓷、SiC陶瓷等,石英陶瓷制备也已经开始应用注凝成型技术,并取得了较好的效果。
2胶态成型技术胶态成型所用的陶瓷料浆是由陶瓷粉料与水、有机物等介质构成的胶态体系。
体系中的陶瓷颗粒分散性好,颗粒之间团聚少,并且陶瓷颗粒随着胶态体系的流动而能够成型为形状多而杂的坯体,因此胶态成型得到广泛的应用。
胶态成型重要包括:注射成型、气相辅佑襄助注射成型、直接凝固注模成型、温度诱导成型、电泳沉积成型、注凝成型、压滤成型和离心注浆成型等。
2.1注射成型技术注射成型是借助高分子聚合物高温熔融、低温凝固的特性使坯体成型后,再把有机物脱除。
石英陶瓷本构-概述说明以及解释

石英陶瓷本构-概述说明以及解释1.引言1.1 概述石英陶瓷是一种非常重要的工程材料,具有优异的物理和化学性能,在多个领域得到广泛应用。
它主要由石英颗粒和陶瓷基质组成,具有高温稳定性、低热膨胀系数、优异的绝缘性能等特点。
石英陶瓷的制备过程包括原材料选择、预处理、成型、烧结等多个步骤。
其中,石英颗粒的选择对最终产品的性能有着重要的影响。
合适的颗粒尺寸和分布可以提高材料的致密性和强度。
陶瓷基质则起到增强材料力学性能的作用,同时也可以调节材料的热膨胀性能和导热性能。
由于石英陶瓷的复杂结构和特殊性质,对其本构关系的研究也显得尤为重要。
本构关系描述了材料在外部力作用下的变形和应力响应规律,是工程设计和模拟的基础。
石英陶瓷的本构关系可以通过实验和理论方法得到。
实验方法通常包括压缩试验、拉伸试验和扭剪试验等,通过测量应力-应变曲线可以获得材料的本构特性。
而理论方法则基于固体力学和微观结构特征,以数学模型描述材料的本构关系。
石英陶瓷的本构特性包括弹性模量、屈服强度、延展性等指标。
了解材料本构特性可以帮助我们更好地理解和预测材料在使用过程中的行为。
此外,对本构关系的深入研究也有助于优化石英陶瓷的制备工艺和改善其性能。
综上所述,石英陶瓷是一种具有广泛应用价值的工程材料。
了解其概述和本构关系对于进一步开发和利用该材料具有重要意义。
本文将深入探讨石英陶瓷的本构特性及其对实际工程应用的影响,以期为相关领域的研究和应用提供一定的理论指导。
1.2 文章结构本文共分为三个部分:引言、正文和结论。
在引言部分,我们会对石英陶瓷的概念进行概述,介绍其在工程领域中的重要性,并对文章的结构进行简要概括。
正文是本文的主要部分,将详细探讨石英陶瓷的本构。
我们将从石英陶瓷的基本特性入手,进一步深入研究其力学行为和变形特性。
首先,我们将介绍石英陶瓷的基本组成和物理性质,包括晶体结构、化学成分以及热物性等方面。
然后,我们将重点讨论石英陶瓷的力学行为,包括弹性和塑性变形、破裂行为以及疲劳寿命等方面。
石英陶瓷环对ph
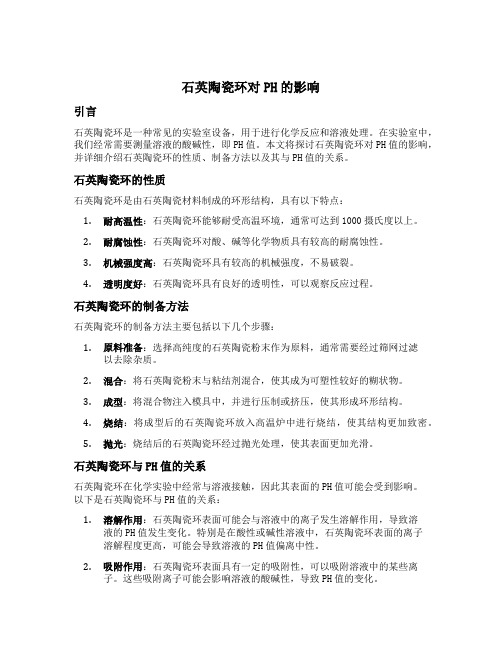
石英陶瓷环对PH的影响引言石英陶瓷环是一种常见的实验室设备,用于进行化学反应和溶液处理。
在实验室中,我们经常需要测量溶液的酸碱性,即PH值。
本文将探讨石英陶瓷环对PH值的影响,并详细介绍石英陶瓷环的性质、制备方法以及其与PH值的关系。
石英陶瓷环的性质石英陶瓷环是由石英陶瓷材料制成的环形结构,具有以下特点:1.耐高温性:石英陶瓷环能够耐受高温环境,通常可达到1000摄氏度以上。
2.耐腐蚀性:石英陶瓷环对酸、碱等化学物质具有较高的耐腐蚀性。
3.机械强度高:石英陶瓷环具有较高的机械强度,不易破裂。
4.透明度好:石英陶瓷环具有良好的透明性,可以观察反应过程。
石英陶瓷环的制备方法石英陶瓷环的制备方法主要包括以下几个步骤:1.原料准备:选择高纯度的石英陶瓷粉末作为原料,通常需要经过筛网过滤以去除杂质。
2.混合:将石英陶瓷粉末与粘结剂混合,使其成为可塑性较好的糊状物。
3.成型:将混合物注入模具中,并进行压制或挤压,使其形成环形结构。
4.烧结:将成型后的石英陶瓷环放入高温炉中进行烧结,使其结构更加致密。
5.抛光:烧结后的石英陶瓷环经过抛光处理,使其表面更加光滑。
石英陶瓷环与PH值的关系石英陶瓷环在化学实验中经常与溶液接触,因此其表面的PH值可能会受到影响。
以下是石英陶瓷环与PH值的关系:1.溶解作用:石英陶瓷环表面可能会与溶液中的离子发生溶解作用,导致溶液的PH值发生变化。
特别是在酸性或碱性溶液中,石英陶瓷环表面的离子溶解程度更高,可能会导致溶液的PH值偏离中性。
2.吸附作用:石英陶瓷环表面具有一定的吸附性,可以吸附溶液中的某些离子。
这些吸附离子可能会影响溶液的酸碱性,导致PH值的变化。
3.表面电荷:石英陶瓷环表面可能带有电荷,这些电荷会影响溶液中的离子分布和酸碱平衡,从而影响溶液的PH值。
如何减小石英陶瓷环对PH值的影响为了减小石英陶瓷环对溶液PH值的影响,可以采取以下措施:1.预处理:在使用石英陶瓷环之前,可以对其进行预处理,如用酸或碱溶液浸泡,以去除表面的杂质和离子。
石英在陶瓷生产中的作用
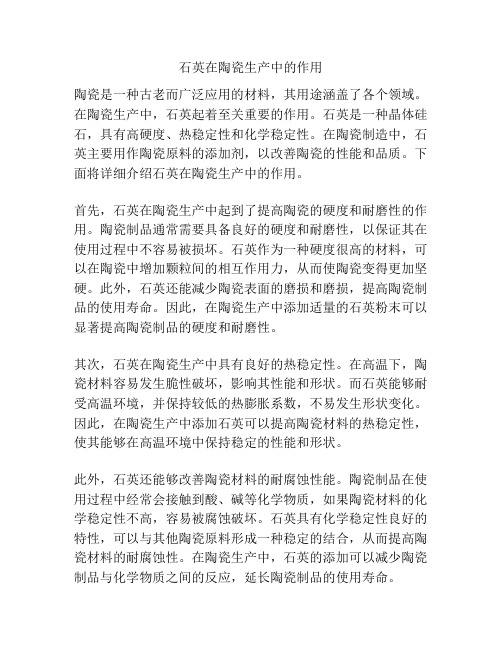
石英在陶瓷生产中的作用陶瓷是一种古老而广泛应用的材料,其用途涵盖了各个领域。
在陶瓷生产中,石英起着至关重要的作用。
石英是一种晶体硅石,具有高硬度、热稳定性和化学稳定性。
在陶瓷制造中,石英主要用作陶瓷原料的添加剂,以改善陶瓷的性能和品质。
下面将详细介绍石英在陶瓷生产中的作用。
首先,石英在陶瓷生产中起到了提高陶瓷的硬度和耐磨性的作用。
陶瓷制品通常需要具备良好的硬度和耐磨性,以保证其在使用过程中不容易被损坏。
石英作为一种硬度很高的材料,可以在陶瓷中增加颗粒间的相互作用力,从而使陶瓷变得更加坚硬。
此外,石英还能减少陶瓷表面的磨损和磨损,提高陶瓷制品的使用寿命。
因此,在陶瓷生产中添加适量的石英粉末可以显著提高陶瓷制品的硬度和耐磨性。
其次,石英在陶瓷生产中具有良好的热稳定性。
在高温下,陶瓷材料容易发生脆性破坏,影响其性能和形状。
而石英能够耐受高温环境,并保持较低的热膨胀系数,不易发生形状变化。
因此,在陶瓷生产中添加石英可以提高陶瓷材料的热稳定性,使其能够在高温环境中保持稳定的性能和形状。
此外,石英还能够改善陶瓷材料的耐腐蚀性能。
陶瓷制品在使用过程中经常会接触到酸、碱等化学物质,如果陶瓷材料的化学稳定性不高,容易被腐蚀破坏。
石英具有化学稳定性良好的特性,可以与其他陶瓷原料形成一种稳定的结合,从而提高陶瓷材料的耐腐蚀性。
在陶瓷生产中,石英的添加可以减少陶瓷制品与化学物质之间的反应,延长陶瓷制品的使用寿命。
另外,石英还能够改善陶瓷的透明性。
在某些特定的陶瓷制品中,例如瓷砖、瓷器等,透明度是一个重要的性能指标。
石英具有良好的光透过性,使得陶瓷制品在烧制的过程中能够具备较高的透明度。
因此,在陶瓷生产中适当添加石英可以提高陶瓷制品的透明性,增加其美观度和装饰性。
最后,石英还可以在陶瓷生产中起到助熔剂的作用。
石英的熔点较高,但其使用的含量较高时,可以与其他陶瓷原料相互作用,降低合成陶瓷材料的烧结温度,提高烧结速度,从而降低生产成本。
石英玻璃陶瓷生产工艺
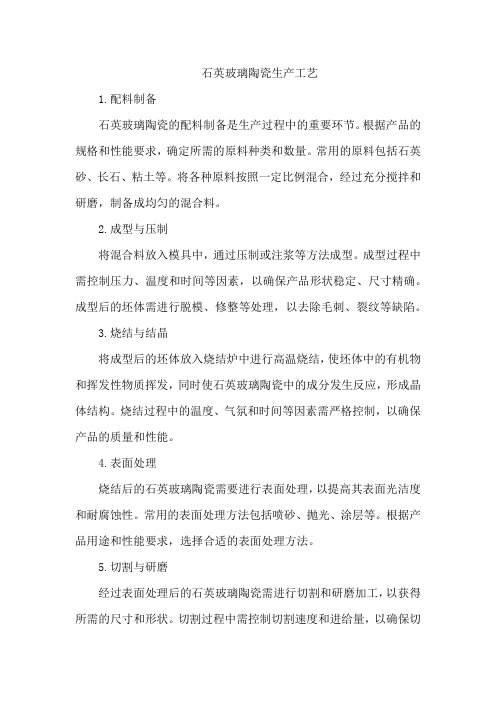
石英玻璃陶瓷生产工艺1.配料制备石英玻璃陶瓷的配料制备是生产过程中的重要环节。
根据产品的规格和性能要求,确定所需的原料种类和数量。
常用的原料包括石英砂、长石、粘土等。
将各种原料按照一定比例混合,经过充分搅拌和研磨,制备成均匀的混合料。
2.成型与压制将混合料放入模具中,通过压制或注浆等方法成型。
成型过程中需控制压力、温度和时间等因素,以确保产品形状稳定、尺寸精确。
成型后的坯体需进行脱模、修整等处理,以去除毛刺、裂纹等缺陷。
3.烧结与结晶将成型后的坯体放入烧结炉中进行高温烧结,使坯体中的有机物和挥发性物质挥发,同时使石英玻璃陶瓷中的成分发生反应,形成晶体结构。
烧结过程中的温度、气氛和时间等因素需严格控制,以确保产品的质量和性能。
4.表面处理烧结后的石英玻璃陶瓷需要进行表面处理,以提高其表面光洁度和耐腐蚀性。
常用的表面处理方法包括喷砂、抛光、涂层等。
根据产品用途和性能要求,选择合适的表面处理方法。
5.切割与研磨经过表面处理后的石英玻璃陶瓷需进行切割和研磨加工,以获得所需的尺寸和形状。
切割过程中需控制切割速度和进给量,以确保切割面平整、无毛刺。
研磨过程中需选用合适的研磨材料和研磨机,以保证研磨后的表面光洁度和精度。
6.质量检测对生产过程中的各个环节进行严格的质量检测,确保产品质量符合相关标准和客户要求。
常用的质量检测方法包括外观检查、尺寸测量、物理性能测试等。
对于不合格的产品需进行返工或报废处理。
7.包装与运输最后,将成品进行包装和运输。
包装需选用防震、防潮、防尘的材料,以确保产品在运输过程中不受损坏。
运输过程中需注意安全事项,避免碰撞和震动。
注凝石英陶瓷材料生产过程中碱土金属引起的析晶问题分析
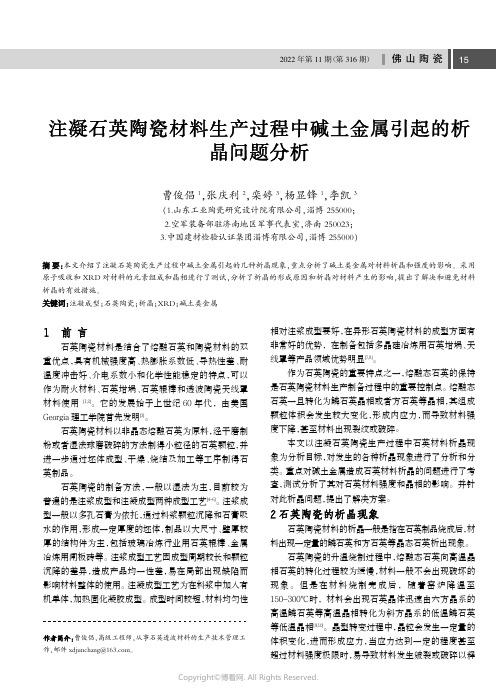
石英陶瓷材料是结合了熔融石英和陶瓷材料的双重优点,具有机械强度高、热膨胀系数低、导热性差、耐温度冲击好、介电系数小和化学性能稳定的特点,可以作为耐火材料、石英坩埚、石英辊棒和透波陶瓷天线罩材料使用[1,2]。
它的发展始于上世纪60年代,由美国Georgia理工学院首先发明[3]。
石英陶瓷材料以非晶态熔融石英为原料,经干磨制粉或者湿法球磨破碎的方法制得小粒径的石英颗粒,并进一步通过坯体成型、干燥、烧结及加工等工序制得石英制品。
石英陶瓷的制备方法,一般以湿法为主,目前较为普遍的是注浆成型和注凝成型两种成型工艺[4-6]。
注浆成型一般以多孔石膏为依托,通过料浆颗粒沉降和石膏吸水的作用,形成一定厚度的坯体,制品以大尺寸、壁厚较厚的结构件为主,包括玻璃冶炼行业用石英辊棒、金属冶炼用闸板砖等。
注浆成型工艺因成型周期较长和颗粒沉降的差异,造成产品均一性差,易在局部出现缺陷而影响材料整体的使用。
注凝成型工艺为在料浆中加入有机单体,加热固化凝胶成型。
成型时间较短,材料均匀性相对注浆成型要好,在异形石英陶瓷材料的成型方面有非常好的优势,在制备包括多晶硅冶炼用石英坩埚、天线罩等产品领域优势明显[7,8]。
作为石英陶瓷的重要特点之一,熔融态石英的保持是石英陶瓷材料生产制备过程中的重要控制点。
熔融态石英一旦转化为鳞石英晶相或者方石英等晶相,其组成颗粒体积会发生较大变化,形成内应力,而导致材料强度下降,甚至材料出现裂纹或破碎。
本文以注凝石英陶瓷生产过程中石英材料析晶现象为分析目标,对发生的各种析晶现象进行了分析和分类。
重点对碱土金属造成石英材料析晶的问题进行了考查,测试分析了其对石英材料强度和晶相的影响。
并针对此析晶问题,提出了解决方案。
石英陶瓷材料的析晶一般是指在石英制品烧成后,材料出现一定量的鳞石英和方石英等晶态石英析出现象。
石英陶瓷的升温烧制过程中,熔融态石英向高温晶相石英的转化过程较为缓慢,材料一般不会出现破坏的现象。
石英粉在陶瓷中的作用
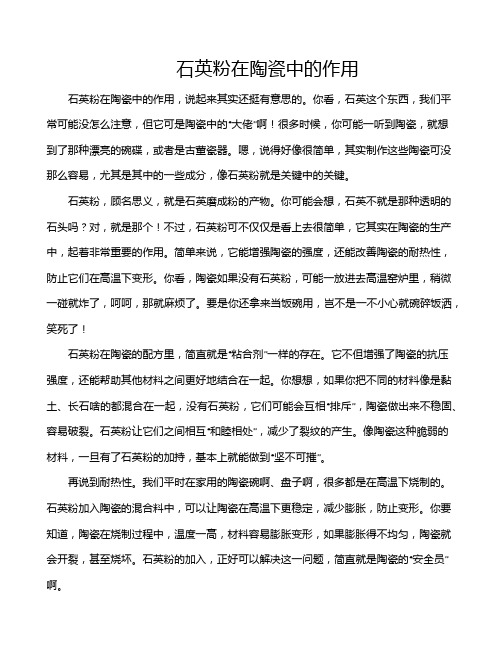
石英粉在陶瓷中的作用石英粉在陶瓷中的作用,说起来其实还挺有意思的。
你看,石英这个东西,我们平常可能没怎么注意,但它可是陶瓷中的“大佬”啊!很多时候,你可能一听到陶瓷,就想到了那种漂亮的碗碟,或者是古董瓷器。
嗯,说得好像很简单,其实制作这些陶瓷可没那么容易,尤其是其中的一些成分,像石英粉就是关键中的关键。
石英粉,顾名思义,就是石英磨成粉的产物。
你可能会想,石英不就是那种透明的石头吗?对,就是那个!不过,石英粉可不仅仅是看上去很简单,它其实在陶瓷的生产中,起着非常重要的作用。
简单来说,它能增强陶瓷的强度,还能改善陶瓷的耐热性,防止它们在高温下变形。
你看,陶瓷如果没有石英粉,可能一放进去高温窑炉里,稍微一碰就炸了,呵呵,那就麻烦了。
要是你还拿来当饭碗用,岂不是一不小心就碗碎饭洒,笑死了!石英粉在陶瓷的配方里,简直就是“粘合剂”一样的存在。
它不但增强了陶瓷的抗压强度,还能帮助其他材料之间更好地结合在一起。
你想想,如果你把不同的材料像是黏土、长石啥的都混合在一起,没有石英粉,它们可能会互相“排斥”,陶瓷做出来不稳固、容易破裂。
石英粉让它们之间相互“和睦相处”,减少了裂纹的产生。
像陶瓷这种脆弱的材料,一旦有了石英粉的加持,基本上就能做到“坚不可摧”。
再说到耐热性。
我们平时在家用的陶瓷碗啊、盘子啊,很多都是在高温下烧制的。
石英粉加入陶瓷的混合料中,可以让陶瓷在高温下更稳定,减少膨胀,防止变形。
你要知道,陶瓷在烧制过程中,温度一高,材料容易膨胀变形,如果膨胀得不均匀,陶瓷就会开裂,甚至烧坏。
石英粉的加入,正好可以解决这一问题,简直就是陶瓷的“安全员”啊。
不仅如此,石英粉还能够调节陶瓷的透明度。
你看那些高档的瓷器,表面光滑得像镜子一样,透亮透亮的。
这个效果,也是石英粉在起作用。
它能让陶瓷釉料变得更加均匀,增加光泽度,使得成品更加美观。
用石英粉做的瓷器,光是看一眼就能让人感受到那种精致感,真的是美不胜收。
说实话,要是没有石英粉的加持,陶瓷看起来就不那么高档了,可能就像是普通的陶土一样,质感大打折扣。
石英陶瓷砖的理化指标

石英陶瓷砖的理化指标
石英陶瓷砖是一种新型的建筑装饰材料,具有一系列理化指标。
首先,我们来看一下石英陶瓷砖的物理指标。
石英陶瓷砖的物理指
标包括密度、吸水率、抗折强度、耐磨性等。
石英陶瓷砖的密度通
常在 2.3-2.5g/cm³之间,密度的大小直接关系到砖的质地和硬度。
而吸水率是衡量砖材吸水性能的重要指标,石英陶瓷砖的吸水率一
般在0.1%以下,这表明了石英陶瓷砖的抗渗透性和耐腐蚀性能较好。
抗折强度是评价砖材抗压能力的指标,石英陶瓷砖的抗折强度较高,一般在50MPa以上,这表明了石英陶瓷砖具有较好的抗压性能。
耐
磨性是指砖材在使用过程中抵抗磨损的能力,石英陶瓷砖的耐磨性
较好,能够满足长期使用的要求。
其次,我们来看一下石英陶瓷砖的化学指标。
化学指标包括成分、放射性等。
石英陶瓷砖的成分主要是石英砂、粘土和其他辅料,其中石英砂含量较高,能够保证砖材的硬度和耐磨性。
此外,石英
陶瓷砖还需要符合国家相关的放射性标准,确保使用安全。
除了物理化学指标,石英陶瓷砖还需要符合一些其他的指标,
比如尺寸稳定性、平整度、色差等。
尺寸稳定性和平整度是保证砖
面铺贴效果的关键指标,而色差则直接关系到砖面的美观效果。
总的来说,石英陶瓷砖的理化指标涵盖了物理性能、化学成分以及其他相关指标,这些指标直接关系到石英陶瓷砖的使用性能和品质。
在选择和使用石英陶瓷砖时,需要根据这些指标进行综合评估,以确保砖材的质量和适用性。
石英陶瓷辊烧成温度
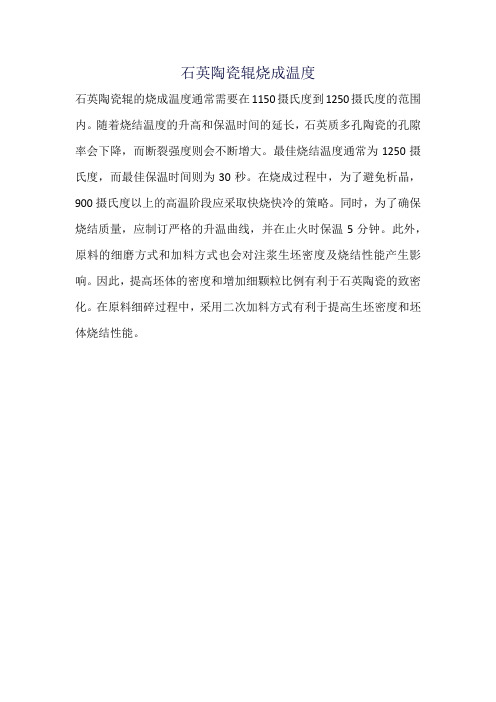
石英陶瓷辊烧成温度
石英陶瓷辊的烧成温度通常需要在1150摄氏度到1250摄氏度的范围内。
随着烧结温度的升高和保温时间的延长,石英质多孔陶瓷的孔隙率会下降,而断裂强度则会不断增大。
最佳烧结温度通常为1250摄氏度,而最佳保温时间则为30秒。
在烧成过程中,为了避免析晶,900摄氏度以上的高温阶段应采取快烧快冷的策略。
同时,为了确保烧结质量,应制订严格的升温曲线,并在止火时保温5分钟。
此外,原料的细磨方式和加料方式也会对注浆生坯密度及烧结性能产生影响。
因此,提高坯体的密度和增加细颗粒比例有利于石英陶瓷的致密化。
在原料细碎过程中,采用二次加料方式有利于提高生坯密度和坯体烧结性能。
- 1、下载文档前请自行甄别文档内容的完整性,平台不提供额外的编辑、内容补充、找答案等附加服务。
- 2、"仅部分预览"的文档,不可在线预览部分如存在完整性等问题,可反馈申请退款(可完整预览的文档不适用该条件!)。
- 3、如文档侵犯您的权益,请联系客服反馈,我们会尽快为您处理(人工客服工作时间:9:00-18:30)。
工艺学实践
石英陶瓷
学院:化学化工学院
专业班级:无机非金属材料工程111班
课程:无机非金属材料工艺学
指导老师:胡永刚老师
学号:***********
******
2013年11月13日
2.2.1国外发展现状
目前,美国、法国、德国、日本等国家具有较高的研制开发水平,石英陶瓷也得到了广泛应用。
主要用途是作为耐火材料及中等温度下的能抗拒温度剧变的结构材料。
根据使用条件的不同,研制开发的石英陶瓷制品具有不同的性能特点,既有高致密度、高强度的系列制品,也有低密度、高气孔的隔热保温制品和泡沫石英制品。
如美国的Ceradyne公司生产的熔融石英陶瓷导弹天线罩,法国的Vesuvius公司生产的玻璃水平钢化炉和金属带材热处理用棍棒等均代表了目前国际上熔融石英陶瓷研制生产的先进水平。
2.2.2国内发展现状
我国熔融石英陶瓷的生产基本是以钢铁冶炼用熔融石英水口以及玻璃窑炉用熔融石英耐火材料为主,多属中低档石英陶瓷制品。
20世纪90年代我国加强了熔融石英陶瓷的研制开发,目前我国的高档熔融石英陶瓷的研制也已达到了国际先进水平,山东中材高新材料股份公司研制开发的玻璃水平钢化炉用石英陶瓷辊、金属带材热处理炉用石英陶瓷空心辊,玻璃浮法窑用耐火材料等多种产品的质量在国内处于领先地位,得到了用户的认可,产品质量达到了国外同类产品的先进水平。
国内外石英陶瓷材料性能比较
2.3石英陶瓷的结构与性能
从液态转变成固态。
在浓悬浮体从液态转变成固态的过程中,体积没有收缩,介质没有量的变化。
注凝成型技术首次使用较低含量的有机物使陶瓷料浆原位固化,大大提高了陶瓷部件显微结构的均匀性,增加了陶瓷材料的可靠性。
由于该工艺与其它传统的成型工艺相比具有许多优越的特点,引起陶瓷界内专家的普遍关注,使得该技术得到了很块的发展,并己经在实际中获得了推广应用。
注凝成型工艺流程
料浆加入引发剂混合均匀后,经真空除气后,注入模具内,浇注过程中,对注凝成型料浆或成型模具或者是两者一前一后并有重叠的施以物理场如机械振动、超声波振动等的作用,从而实现注凝成型过程的动态化。
在40-80℃温度下固化,固化时间因制品尺寸形状不同而不同,一般在20min以上,坯体固化后进行脱模干燥烧成。
2.6石英陶瓷制备中的影响因素
2.6.1动态作用对注凝成型的影响
浇注过程中对料浆和模具施加的动态作用,可使料浆中的陶瓷颗粒在机械波或其它物理场的作用下重新位移重排,形成均匀致密的显微结构,减少或消除由于气
泡和搭桥等现象所导致的非均匀结构。
尤其是在料浆往模型中注人的过程中或注人后,对模型和料浆施以物理场。
并且在注凝料浆开始胶凝固化前适当时间停止这种物理场作用,可使料浆中的颗粒得以均匀地排列,形成均匀的显微结构,图a 显示出采用振动波辅助注凝成型工艺中颗粒在振动波作用下通过位移消除搭桥现象,形成较紧密堆积的原理,因此可以有效地形成一个结构均匀、致密度高的陶瓷坯体,由这种坯体烧结的制品强度等性能明显改善,可靠性显著提高。
通过20-30min的机械振动可使生坯密度提高0.03-0.05g/cm3。
由图b的扫描电镜照片可以看出机械振动可使熔融石英陶瓷材料的显微结构更加均匀致密。
图a
图b
2.6.2固化温度对注凝成型的影响
在聚合过程中引发剂分解属于吸热反应,温度的提高有助于促进初级自由基的形成,提高引发效率而单体的聚合反应是放热反应,在反应引发之后,聚合过程中如果温度过高,聚合反应过程中会放出气体,聚合的速度非常快,气体来不及排除,被包裹在坯体中,形成气孔。
另外也会导致料浆中水分的汽化,在坯体中产生气孔。
为了提高坯体固化速度,成型可适当提高温度至50-80℃之间进行,温度低时固化时间长,温度高时固化时间短。
2.6.3有机单体、引发剂引入对注凝成型的影响
单体引人量与固化时间的关系见图c,由图可见有机单体的引人量越多,聚合速度越快,当料浆中有机单体的浓度大于某一范围后,加人引发剂后在极短的时间内发生聚合反应,料浆来不及浇注。
反之,有机单体的引人量越少,聚合速度越慢,固化时间越长,坯体强度也随之降低。
对于熔融石英料浆而言,适宜的有机单体引人量范围为0.5%-2.0%。
引发剂的作用是形成初级自由基,促进单体分子形成单体自由基,引发聚合反应。
随着引发剂加人量的增大,料浆中初级自由基浓度增大,引发速率增大,聚合反应速度加快。
引发剂用量较小时,聚合反应进行的缓慢,甚至不能进行反应,降低成型效率。
引发剂用量过大时,聚合反应剧烈,可能导致料浆不能完成浇注即凝固。
熔融石英陶瓷的注凝成型,引发剂用量与坯体固,由图d可见引发剂用量控制在每千克料浆的0.5-2.0ml范围内,聚合反应速度较为适宜。
c单体引入量与固化时间关系d引发剂用量与固化时间的关系
2.6.4石英陶瓷的相组成的变化与热稳定性
石英陶住相组成和热定性与烧结温度的关系
1000℃之前,坯体中主要发生了球磨时形成的硅溶胶的脱水与分解过程,分解的产物是无定形的二氧化硅。
由于原料中碱金属和碱土金属的氧化物、氧化铁等熔剂氧化物的含量极少,不可能形成足以影响坯体烧结的低共熔点的液相,这时
二氧化硅相变关系图
2.7石英陶瓷制备中可能出现的问题以及应对方法
2.7.1色斑
1)色斑产生的原因
色斑一般是内表面受到外来物质的污染而不是陶瓷本身的缺陷形成的。
石英陶瓷生产过程中要求内装硅胶干燥剂,是生产过程中石英陶瓷内表面唯一能接触到的物质。
接触变色硅胶水溶液的陶瓷,干燥后表面呈淡蓝色;接触无色硅胶水溶液的陶瓷,干燥后表面没有颜色变化。
石英陶瓷生产周期长,使用的变色干燥剂容易粉化,周转过程中由于变色硅胶干燥剂的摩擦、碰撞,容易产生粉末或小颗粒并透过纱布包装落到石英陶瓷内表面,在潮湿环境中吸收水分,使变色硅胶干燥剂中含有的氧化亚钴溶解到水分中,渗透污染到陶瓷内部。
同时陶瓷材料吸附力较强,使氧化亚钴能稳定地存在于陶瓷材料中,并随着环境温度的变化使石英陶瓷表现到蓝色的色斑变化。
2)色斑解决办法
a、硅胶干燥剂改为无色硅胶干燥剂(带致密且透气的无纺布包装);
b、硅胶干燥剂应在60-70 ºC,30min条件下烘干后使用,最多烘干2次;
c、使用包装袋包装石英陶瓷时必须使用绳子扎紧,不允许开口存放;
d、在石英陶瓷生产过程定点烘干、更换干燥。
2.7.2裂纹和蚀坑
1)裂纹和蚀坑产生的原因
物相分析包括价态分析、结晶基本成分分析和晶体结构分析。
本文采用X射线衍射方法来进行结晶基本成分分析。
X射线衍射是利用X射线的波长较小,
穿透样品时在晶格之间产生衍射,再利用劳埃方程和布拉格定律以及衍射花纹,来计算晶体的晶格常数,推断结晶相的成分。
实际分析中常用X衍射图谱与已知的PDF卡片对照的简易方法来判断样品中的结晶相成分。
2.8.3微观形貌测试
本设计的微观形貌的测试是利用扫描电子显微镜(SEM)完成的。
扫描电镜通过用二次电子和背散射电子信号成像,研究样品表面的显微结构和断面形貌特征。
其优点是景深大,放大倍数大,图像分辨率高,不破坏样品。
2.8.4其它性能测定
对所制成的石英陶瓷制分别品进行抗压、抗折强度,PH值、密度的测定,并讨论所制作的石英制品是否符合课程设计的要求。