制动系统设计DOC
(完整word版)制动系统设计
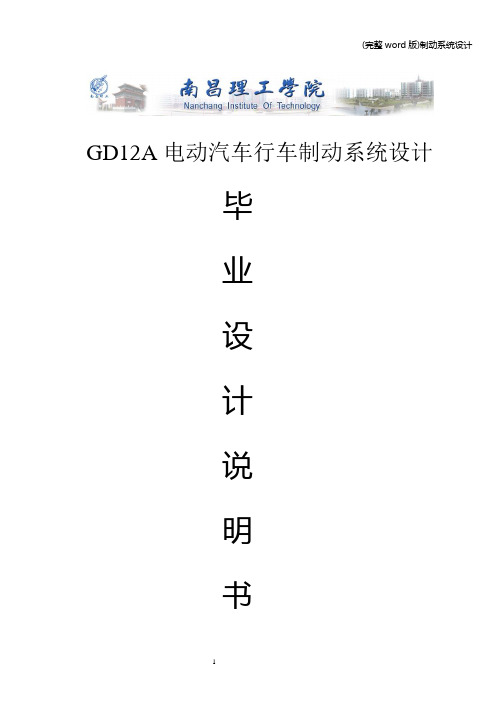
GD12A电动汽车行车制动系统设计毕业设计说明书姓名:俞翼鸿专业:汽车维修与检测班级:(2)指导老师: 邹章鸣南昌理工学院机械工程系1.。
目录摘要Troduction前言第一章绪论 (6)1。
1 制动系统设计的意义 (6)1。
2 制动系统研究现状 (6)1.3 本次制动系统应达到的目标 (6)1.4 本次制动系统设计要求 (6)第二章制动系统方案论证分析与选择 (7)2.1 制动器形式方案分析 (7)2。
1.1 鼓式制动器 (7)2。
1。
2 盘式制动器 (9)2。
2 制动驱动机构的结构形式选择 (10)2.2.1 简单制动系 (10)2。
2。
2 动力制动系 (10)2。
2。
3 伺服制动系 (11)2。
3 液压分路系统的形式的选择 (11)2.3.1 II型回路 (11)2.3.2 X型回/路 (12)2。
3。
3 其他类型回路 (12)2。
4 液压制动主缸的设计方案 (12)第三章制动系统设计计算 (15)3.1 制动系统主要参数数值 (15)3.1.1 相关主要技术参数 (15)3.1.2 同步附着系数的分析 (15)3.2 制动器有关计算 (16)3.2。
1 确定前后轴制动力矩分配系数β (16)3。
2。
2制动器制动力矩的确定 (16)3.2。
3 后轮制动器的结构参数与摩擦系数的选取 (17)3.2.4 前轮盘式制动器主要参数确定 (18)3。
3 制动器制动因数计算 (19)3.3.1 前轮盘式制动效能因数 (19)3.3。
2 后轮鼓式制动器效能因数 (19)3。
4 制动器主要零部件的结构设计 (20)第四章液压制动驱动机构的设计计算 (22)4。
1 后轮制动轮缸直径与工作容积的设计计算 (22)4.2 前轮盘式制动器液压驱动机构计算 (23)4.3 制动主缸与工作容积设计计算 (24)4.4 制动踏板力与踏板行程 (24)4.4。
1 制动踏板力 (24)4.4.2 制动踏板工作行程 (25)第五章制动性能分析 (26)5.1 制动性能评价指标 (26)5.2 制动距离S (26)5。
汽车制动系统 教学设计

汽车制动系统教学设计教学目标:1. 了解汽车制动系统的作用和原理;2. 掌握汽车制动系统的组成部分及其功能;3. 能够分析汽车制动系统的故障并进行相关的维修与调整。
教学内容:1. 汽车制动系统的作用和原理a. 介绍制动系统的作用,即使汽车减速和停车。
b. 解释制动系统的工作原理,包括制动力的产生和传递。
2. 汽车制动系统的组成部分及其功能a. 主缸:介绍主缸的结构和功能,即把踏板力转化为制动液的压力。
b. 制动盘/制动鼓:介绍制动盘和制动鼓的结构和作用,即接受制动液传递的压力并将其转化为摩擦制动力。
c. 制动片/刹车鞋:介绍制动片和刹车鞋的结构和作用,即与制动盘或制动鼓产生摩擦力,以实现制动效果。
d. 制动液:介绍制动液的种类和性能要求,以及其在制动系统中的作用。
e. 刹车助力器:介绍刹车助力器的结构和作用,即在减小驾驶员施加的力的情况下增加制动力。
3. 汽车制动系统的故障分析及维修与调整a. 讲解常见的制动系统故障,并分析可能的原因。
b. 介绍如何判断故障所在的部位,以及可能的维修和调整方法。
c. 强调维修和调整时的安全注意事项,如正确使用安全防护设备和保持工作区域的清洁等。
教学方法:1. 讲解法:通过课堂讲解,向学生介绍制动系统的作用、原理和组成部分,并解答学生的问题。
2. 示范法:老师可带领学生实际操作汽车制动系统,展示其组成部分和工作原理。
3. 实践操作:学生在指导下进行相关维修和调整实践操作,并记录操作过程和结果。
教学评估:1. 口头回答问题:提问学生有关制动系统的基本概念、作用、原理和组成部分的问题,评估学生掌握情况。
2. 操作实践评估:对学生进行实际的维修和调整操作,评估其操作技能和安全意识。
3. 书面作业评估:布置相关练习题或实践报告,评估学生对制动系统故障分析和维修的理解和应用能力。
教学资源:1. 汽车制动系统的教学PPT和讲义;2. 功能正常的汽车制动系统的实物或模型;3. 汽车制动系统相关的工具和设备。
制动系统设计手册(NEW)

总体上写得不错,需要进一步改进的建议如下:
1.主要零部件的典型结构图。
2.分泵、总泵、吊挂助力器和阀等试验验证与试制验证的方法与标准(结合参考上次L项目验证计划)细化与补充。
3.分泵、总泵、吊挂助力器和阀的DFMEA分析的主要内容。
3.做到图文并茂,无经验的年轻的设计人员(《设计手册》主要读者)一看就明白。
3.3.6制动管路的布置:
首先以不与其它零部件干涉为前提,应尽量理顺;其次各管路的结构应合理,尤其是管路两端在整车行驶过程中有相对运动的件应考虑吸震方案,必要时采用软管连接;另外,在进行管路布置时应考虑管子的卡固,在空间允许的前提下管卡子的间隔以500~600mm为佳,当然在局部障碍部位可能要密一些。
真空助力器的直接作用在于降低制动踏板力,当制动踏板力太大时,仅依靠人的输入力(按照标准要求人的最大输入力不得大于700N)可能不足以使整车完全制动,而利用真空对助力器内橡胶膜片及反馈盘的作用可以成数倍(取决于真空助力器的助力比)地放大制动踏板的输入力,即增大制动总泵活塞的输入力,从而增大制动管路的压力。当然真空助力器助力比的选取应合适,助力比太大易使驾驶员失去踏板感,而太小又使人在制动过程中感到吃力,且对于一定规格的助力器来说,助力器的助力比越大,其最大输出拐点越低,这就容易造成整个制动过程在初期省力,但在后期特废力,严重时也会刹不住车,故真空助力器助力比的选取以使制动踏板力调整适当为宜。另当某一规格的助力器对整车制动踏板力的调整不能满足要求且适当调整助力比仍不能达到要求时应更换助力器的规格。
3.3制动系统各总成零部件在设计和布置过程中的注意事项:
3.3.1制动器总成:
优先采用社会成熟资源,但在与整车实际应用时应考察制动器的效能、制动底板、制动蹄铁、制动鼓的刚性与整车的符合性。
盘式制动器制动系统设计

XXX大学本科生毕业设计(论文)HX7200制动系设计学生姓名:______________学号:______________班级: ______________专业:______________指导教师:______________4月目录目录 ............................................................................................................................ 错误!未定义书签。
摘要 .......................................................................................................................... 错误!未定义书签。
Abstract ......................................................................................................................... 错误!未定义书签。
第1章绪论......................................................................................................... 错误!未定义书签。
1.1本课题研究背景............................................................................................. 错误!未定义书签。
1.2制动系统旳研究现实状况............................................................................. 错误!未定义书签。
制动系统设计计算报告
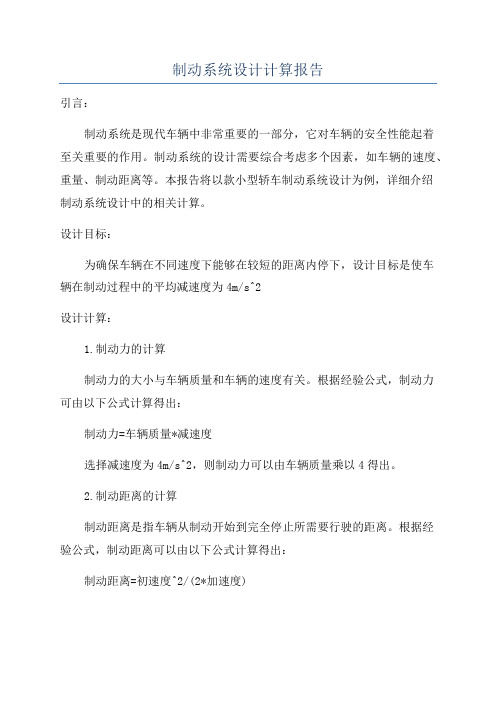
制动系统设计计算报告引言:制动系统是现代车辆中非常重要的一部分,它对车辆的安全性能起着至关重要的作用。
制动系统的设计需要综合考虑多个因素,如车辆的速度、重量、制动距离等。
本报告将以款小型轿车制动系统设计为例,详细介绍制动系统设计中的相关计算。
设计目标:为确保车辆在不同速度下能够在较短的距离内停下,设计目标是使车辆在制动过程中的平均减速度为4m/s^2设计计算:1.制动力的计算制动力的大小与车辆质量和车辆的速度有关。
根据经验公式,制动力可由以下公式计算得出:制动力=车辆质量*减速度选择减速度为4m/s^2,则制动力可以由车辆质量乘以4得出。
2.制动距离的计算制动距离是指车辆从制动开始到完全停止所需要行驶的距离。
根据经验公式,制动距离可以由以下公式计算得出:制动距离=初速度^2/(2*加速度)在制动过程中,加速度是负值(减速),所以加速度取为-4m/s^2、根据具体车辆的初始速度,可以计算出相应的制动距离。
3.制动盘和制动钳的尺寸计算制动盘和制动钳的尺寸需要考虑车辆的速度和质量。
根据经验公式,制动盘的直径与车速和减速度有关,可以通过以下公式计算得出:制动盘直径=停车速度*车辆质量*系数/制动力在本设计中,选择停车速度为60 km/h,车辆质量为1000 kg,系数为0.7、根据以上参数,可以计算出制动盘的直径。
根据制动盘的直径,可以确定制动钳的尺寸。
制动盘和制动钳的尺寸需要满足制动力的需求,并能够有效散热,以免在制动过程中过热导致制动力减弱。
4.制动液系统的计算制动液的压力和制动钳的工作效果有关。
根据经验公式,制动液的压力可以由以下公式计算得出:制动液压力=制动力/制动钳有效面积制动液压力需要根据制动钳的效率和制动力来选择合适的值。
根据经验,选择制动液压力为5MPa。
结论:根据以上计算结果,制动系统的设计可以满足要求。
制动力、制动距离、制动盘和制动钳的尺寸以及制动液压力的计算都能够保证车辆在制动过程中的安全性。
制动系设计

第二节 制动器的结构方案分析
4. 盘式制动器
与鼓式制动器相比盘式制动器具有: ① 热稳定性好 ② 水稳定性好 ③ 制动力矩与汽车运动方向无关 ④ 易于构成双回路制动系 ⑤ 尺寸小、质量小、散热良好 ⑥ 衬块磨损均匀 ⑦ 更换衬块容易;缩短了制动协调时间
⑧ 易于实现间隙自动调整。
第二节 制动器的结构方案分析
第一节 概述
6. 制动系设计应满足的要求
① 具有足够的制动效能(行车制动以制动减速度和制动距离为 评价指标;驻车制动以可靠停使的最大坡度为评价指标)
② 工作可靠 ③ 制动时不应当丧失操纵性和方向稳定性 ④ 防止水和污泥进入制动器工作表面 ⑤ 热稳定性良好 ⑥ 操纵轻便,并具有良好的随动性
第二节 制动器的结构方案分析
作业
如右图所示,车辆的质量为m,制动减速度为a, 地面附着系数为φ,其余参数如图所示,试求车
辆在制动时,前后桥制动器的最大制动力。
本章主要内容
第一节 概述 第二节 制动器的结构方案分析 第三节 制动器的设计 第四节 制动驱动系统
第一节 概述
1. 制动系的功能
① 能够以控制和重复的形式降低车速,在需要时可将车停下来 ② 能够在下坡时保证车辆以稳定车速行驶 ③ 使汽可靠地停在原地或坡道上
第一节 概述
2. ABS防抱死刹车系统
第三节 制动器设计
1. 行车制动
第三节 制动器设计
2. 制动力分配曲线
第三节 制动器设计
3. 驻车制动
第三节 制动器设计
4. 弹簧式盘式制动器
第三节 制动器设计
5. 多片湿式制动器设计
第四节 制动驱动系统
1. 驱动形式
① 机械制动 ② 气压制动 ③ 液压制动
制动系统设计规范精选全文完整版

可编辑修改精选全文完整版一、国标要求1、GB 12676-1999《汽车制动系统结构、性能和试验方法》2、GB 13594-2003《机动车和挂车防抱制动性能和试验方法》3、GB 7258-1997《机动车运行安全技术条件》二、整车基本参数及样车制动系统主要参数整车基本参数样车制动系统主要参数三、计算1. 前、后制动器制动力分配1.1 地面对前、后车轮的法向反作用力 公式:gz h dt du mGb L F +=1 ………………………………(1) gz h dt du mGa L F -=2 (2)参数:1z F ——地面对前轮的法向反作用力,N ;2z F ——地面对后轮的法向反作用力,N ;G ——汽车重力,N ;b ——汽车质心至后轴中心线的水平距离,m ;a ——汽车质心至前轴中心线的距离,m 。
m ——汽车质量,kg ;gh ——汽车质心高度,m ;L ——轴距,m ;dt du——汽车减速度,m/s 2四、制动器的结构方案分析制动器有摩擦式、液力式和电磁式等几种。
电磁式制动器虽有作用滞后小、易于连接且接头可靠等优点,但因成本高而只在一部分重型汽车上用来做车轮制动器或缓速器。
液力式制动器只用作缓速器。
目前广泛使用的仍为摩擦式制动器。
摩擦式制动器按摩擦副结构形式不同,分为鼓式、盘式和带式三种。
带式只用作中央制动器。
一、鼓式制动器鼓式制动器分为领从蹄式、双领蹄式、双向双领蹄式、双从蹄式、单向增力式、双向增力式等几种,见图la ~f 。
不同形式鼓式制动器的主要区别有:①蹄片固定支点的数量和位置不同。
②张开装置的形式与数量不同。
③制动时两块蹄片之间有无相互作用。
因蹄片的固定支点和张开力位置不同,使不同形式鼓式制动器的领、从蹄数量有差别,并使制动效能不同。
制动器在单位输入压力或力的作用下所输出的力或力矩,称为制动器效能。
在评比不同形式制动器的效能时,常用一种称为制动器效能因数的无因次指标。
制动器效能因数的定义为,在制动鼓或制动盘的作用半径R 上所得到的摩擦力(RM μ)与输入力0F 之比,即RF M K 0μ=式中,K 为制动器效能因数;μM 为制动器输出的制动力矩。
汽车制动器设计毕业设计(论文)word格式
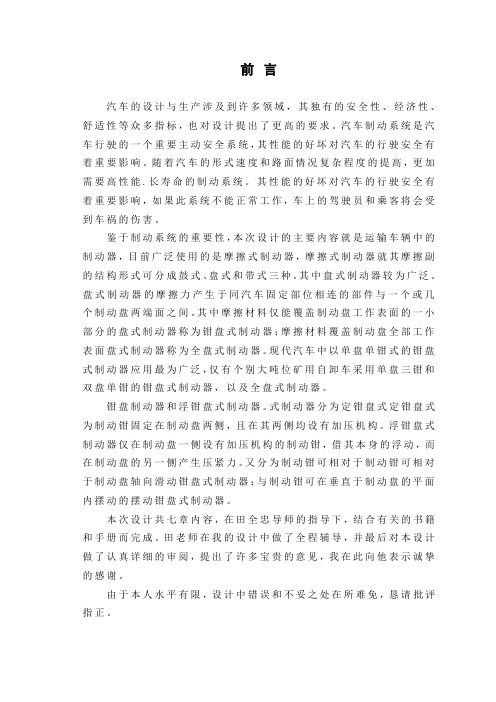
前言汽车的设计与生产涉及到许多领域,其独有的安全性、经济性、舒适性等众多指标,也对设计提出了更高的要求。
汽车制动系统是汽车行驶的一个重要主动安全系统,其性能的好坏对汽车的行驶安全有着重要影响。
随着汽车的形式速度和路面情况复杂程度的提高,更加需要高性能.长寿命的制动系统。
其性能的好坏对汽车的行驶安全有着重要影响,如果此系统不能正常工作,车上的驾驶员和乘客将会受到车祸的伤害。
鉴于制动系统的重要性,本次设计的主要内容就是运输车辆中的制动器,目前广泛使用的是摩擦式制动器,摩擦式制动器就其摩擦副的结构形式可分成鼓式、盘式和带式三种。
其中盘式制动器较为广泛。
盘式制动器的摩擦力产生于同汽车固定部位相连的部件与一个或几个制动盘两端面之间。
其中摩擦材料仅能覆盖制动盘工作表面的一小部分的盘式制动器称为钳盘式制动器;摩擦材料覆盖制动盘全部工作表面盘式制动器称为全盘式制动器。
现代汽车中以单盘单钳式的钳盘式制动器应用最为广泛,仅有个别大吨位矿用自卸车采用单盘三钳和双盘单钳的钳盘式制动器,以及全盘式制动器。
钳盘制动器和浮钳盘式制动器。
式制动器分为定钳盘式定钳盘式为制动钳固定在制动盘两侧,且在其两侧均设有加压机构。
浮钳盘式制动器仅在制动盘一侧设有加压机构的制动钳,借其本身的浮动,而在制动盘的另一侧产生压紧力。
又分为制动钳可相对于制动钳可相对于制动盘轴向滑动钳盘式制动器;与制动钳可在垂直于制动盘的平面内摆动的摆动钳盘式制动器。
本次设计共七章内容,在田全忠导师的指导下,结合有关的书籍和手册而完成。
田老师在我的设计中做了全程辅导,并最后对本设计做了认真详细的审阅,提出了许多宝贵的意见,我在此向他表示诚挚的感谢。
由于本人水平有限,设计中错误和不妥之处在所难免,恳请批评指正。
第一章盘式制动器概述§1.1盘式制动器原理及特点图.1-1增力式盘式制动器零件图1、2—压盘3、7—摩擦盘4—半轴壳5—半轴6—回位弹簧8—中间壳体9—调整螺栓 10—斜拉杆11—调节叉 12—拉杆13—压盘凸肩14—壳体肩台上图是运输车辆增力式盘式制动器零件图。
车辆制动系统方案毕业设计

车辆制动系统方案毕业设计一、引言随着汽车行业的发展,车辆安全问题越来越受到人们的关注。
而车辆制动系统作为车辆最重要的安全保障之一,其性能的稳定和可靠直接影响车辆行驶的安全。
因此,本文将研究一种车辆制动系统方案,对其进行系统设计,并在实际驾驶过程中进行测试验证,以达到优化车辆制动系统性能的目的。
二、方案设计本方案设计的车辆制动系统分为三个部分:制动控制部分、制动执行部分以及传感反馈部分。
1. 制动控制部分制动控制部分采用可编程控制器(PLC)作为控制核心,通过传感器采集车速、制动踏板行程等参数,来实时控制制动器的工作,进而控制车辆的制动。
2. 制动执行部分制动执行部分采用气动式制动器,将制动控制部分发送的控制信号转换为气源控制信号,通过阀门的控制实现制动器的工作,进而实现车辆的制动。
3. 传感反馈部分传感反馈部分主要由传感器组成,包括制动踏板行程传感器、制动器传感器等,通过采集数据并传输给制动控制部分进行处理,从而实现对制动系统的实时监测和反馈。
三、实验结果分析1. 实验方法在本次实验中,我们通过实验台模拟车辆行驶状态,对所设计的车辆制动系统进行测试。
在测试过程中,我们对比了原有制动系统和新设计的制动系统的刹车距离、制动灵敏度等指标差异,并通过数据对比来对所设计的方案进行分析。
2. 实验结果在测试中,我们发现采用所设计的车辆制动系统后,车辆的刹车距离、制动灵敏度等指标得到了显著的提升。
在同样的行驶路线下,新设计的制动系统刹车距离相比原有制动系统减少了近30%,同时制动灵敏度得到了明显的提高。
四、结论本文根据车辆制动系统的需求,设计了一种新的车辆制动系统方案,并在实验中对其进行了有效性验证。
通过测试数据分析,我们发现所设计的车辆制动系统在刹车距离、制动灵敏度等指标上得到了显著的提升,同时也保证了车辆的安全性和可靠性,可为未来的车辆制动系统的研究和应用提供一定的参考价值。
制动系统设计与计算

从上述计 算和图表 中可以看 到,该车 的制动器 附着系数 利用曲线 负荷ECE 标准。
空载
附着系数利用法规线 GB21670
GB21670 -2008中要求:在车辆所有载荷状态下,当制动强度z处于0.15~0.80之间时,后轴附着系数利用 于前轴上方;当附着系数ψ在0.2~0.8之间时,制动强度z≥0.1+0.7(ψ-0.2)。
G* (b+z*hg )/L 10457.36 N
φ*Fz1
8124.393 N 2372.323 N.m G*(az*hg)/L 7079.145 φ*Fz2 5499.833 N 1605.951 N.m
空载
G*
汽车前轮最大法向反作用力Fz1‘
(b+z*hg )/L
8768.286 N
汽车前轮空载最大地面附着力Fxb1' φ*Fz1
7077.212377 3255.907623
0.9
2.46178968
8266.739706 3358.020294
1
2.807471264
9524.017208 3392.382792
β曲线(与制动系统的参数有关,制动系统参数定义完成后,β曲线就定义完成)
前制动器所能提供的最大制动力
后制动器所能提供的最大制动力
制动强度 前轴的利用附着系数 0
后轴的利用附着系数
0.1
0.2
0.3
0.4
0.5
0.6
同上
0.7
0.8
0.9
同上 空载
1
1.1
满载 制动强度 前轴的利用附着系数
0 0.1
0.2
0.3
0.4
课程设计制动系设计

课程设计制动系设计一、教学目标本课程旨在通过制动系设计的学习,让学生掌握制动系统的组成、工作原理及其设计方法。
具体目标如下:1.了解制动系统的功能和重要性;2.掌握制动系统的组成部件及其作用;3.理解制动系统的工作原理;4.学习制动系统的设计方法和流程。
5.能够分析制动系统的性能指标;6.能够运用制动系统设计方法进行初步设计;7.能够评估制动系统的安全性和可靠性。
情感态度价值观目标:1.培养学生对汽车工程领域的兴趣和热情;2.培养学生具备安全意识和责任感,注重行车安全;3.培养学生具备创新精神和团队合作意识。
二、教学内容本课程的教学内容主要包括以下几个部分:1.制动系统的功能和重要性;2.制动系统的组成部件及其作用,如制动盘、制动鼓、制动片、制动鞋、制动油管、制动泵等;3.制动系统的工作原理,如液压制动系统、气压制动系统、电子制动系统等;4.制动系统的设计方法,包括制动盘、制动鼓、制动片等的设计计算和选型;5.制动系统的性能评价,如制动效能、制动距离、制动稳定性等;6.制动系统的维修保养和故障诊断。
三、教学方法为了提高教学效果,本课程将采用多种教学方法相结合的方式进行教学:1.讲授法:通过教师的讲解,使学生掌握制动系统的基本概念、原理和设计方法;2.讨论法:学生进行小组讨论,分享学习心得和经验,提高学生的思考和分析能力;3.案例分析法:分析实际案例,使学生更好地理解制动系统的工作原理和设计方法;4.实验法:安排实验室实践环节,让学生亲自动手进行制动系统的拆装和检测,提高学生的动手能力。
四、教学资源为了支持本课程的教学,我们将准备以下教学资源:1.教材:选用权威、实用的制动系统设计教材,为学生提供系统的学习资料;2.参考书:提供相关领域的参考书籍,丰富学生的知识体系;3.多媒体资料:制作课件、视频等多媒体资料,提高学生的学习兴趣和效果;4.实验设备:准备制动系统的实验设备,为学生提供实践操作的机会。
制动系统设计范文
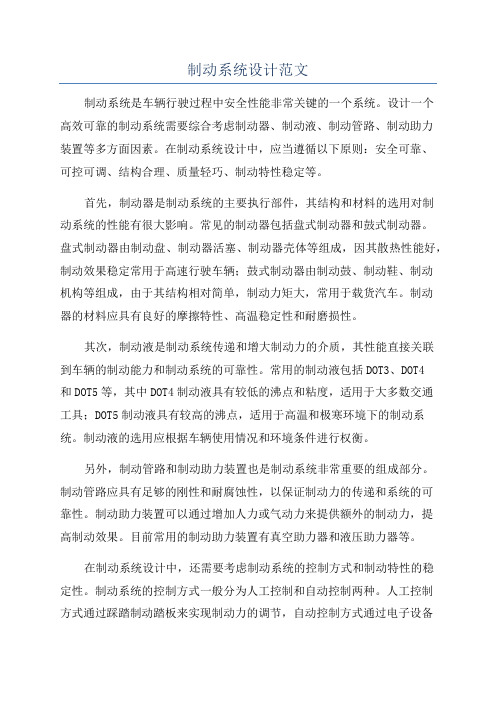
制动系统设计范文制动系统是车辆行驶过程中安全性能非常关键的一个系统。
设计一个高效可靠的制动系统需要综合考虑制动器、制动液、制动管路、制动助力装置等多方面因素。
在制动系统设计中,应当遵循以下原则:安全可靠、可控可调、结构合理、质量轻巧、制动特性稳定等。
首先,制动器是制动系统的主要执行部件,其结构和材料的选用对制动系统的性能有很大影响。
常见的制动器包括盘式制动器和鼓式制动器。
盘式制动器由制动盘、制动器活塞、制动器壳体等组成,因其散热性能好,制动效果稳定常用于高速行驶车辆;鼓式制动器由制动鼓、制动鞋、制动机构等组成,由于其结构相对简单,制动力矩大,常用于载货汽车。
制动器的材料应具有良好的摩擦特性、高温稳定性和耐磨损性。
其次,制动液是制动系统传递和增大制动力的介质,其性能直接关联到车辆的制动能力和制动系统的可靠性。
常用的制动液包括DOT3、DOT4和DOT5等,其中DOT4制动液具有较低的沸点和粘度,适用于大多数交通工具;DOT5制动液具有较高的沸点,适用于高温和极寒环境下的制动系统。
制动液的选用应根据车辆使用情况和环境条件进行权衡。
另外,制动管路和制动助力装置也是制动系统非常重要的组成部分。
制动管路应具有足够的刚性和耐腐蚀性,以保证制动力的传递和系统的可靠性。
制动助力装置可以通过增加人力或气动力来提供额外的制动力,提高制动效果。
目前常用的制动助力装置有真空助力器和液压助力器等。
在制动系统设计中,还需要考虑制动系统的控制方式和制动特性的稳定性。
制动系统的控制方式一般分为人工控制和自动控制两种。
人工控制方式通过踩踏制动踏板来实现制动力的调节,自动控制方式通过电子设备来控制制动力的大小。
制动特性的稳定性是指制动效果在不同工况下的一致性,要求制动负荷、制动力矩等参数能够在不同速度和路况下保持稳定。
在汽车行驶过程中,制动系统发挥着至关重要的作用,其设计要基于安全性能的考量,并需要考虑各个部件之间的协调配合,以确保整个系统运行稳定可靠。
制动系统设计计算书

制动系 统设计 计算书
(Φ 式制动 器,前:后= :)
mm
轴距L= 1765
空载
满载
811.700565 827.34375
785
843.3
885
960
478
510
0.54
0.53
后轴负 荷G2 (kg) 后轴质 量分配 % 3.汽车动 轴荷分配 计算: 3.1 动轴 荷计算: 当汽 车以减速 度jt制动 时,由于 减速度而 产生的惯 性力,使 轴荷分配 相应改 变:
=
Lb - b hg
=
4.4 满载 时前后轴 附着力 矩:(道 路附着系 数Φ =0.65时 的附着力 矩) 前轴附着 力矩:
j0
=
Lb - b hg
=
Mj前 = Pt1' ? Rk1 =
#VALUE!
#VALUE! #VALUE!
后轴附着 力矩:
4.5 最大 管路压力 :
产生 最大管路 压力矩时 (Φ =0.65)的 管路压力 为最大管 路压力, 故当Φ =0.65时,
表二
为汽车制 动时前后 在不同减 速度jt/g 值时动轴 荷分配 比:
表二 (见下 页):
jt/g=φ
G1' 空载 满载
G2' 空载 满载
4.汽车制 动力的计 算: 4.1.汽车 制动时所 需的制动 力Pτ(轴 制动力) 当汽车 以减速度 jt/g制动 时,前后 各自所需 的制动力 为: 前轴: Pτ1=G1 '×jt/g× 9.8 (N) 后轴: Pτ2=G2 '×jt/g× 9.8 (N)
0.1 58.5 57.9 41.5 42.1
0.2 62.2 61.9 37.8 38.1
制动系设计毕业设计
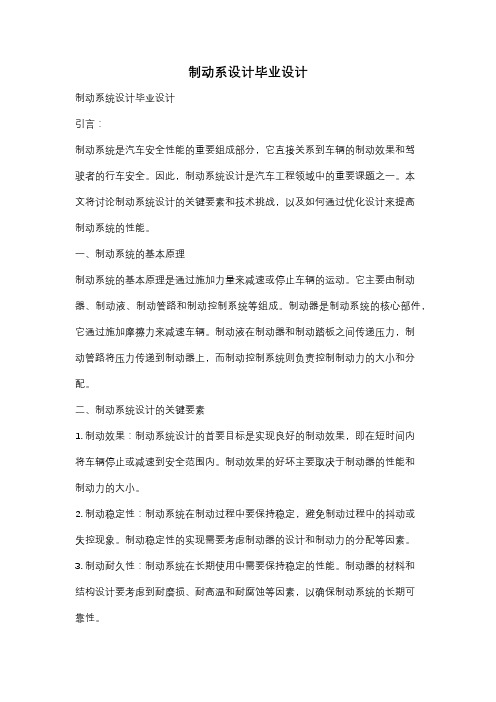
制动系设计毕业设计制动系统设计毕业设计引言:制动系统是汽车安全性能的重要组成部分,它直接关系到车辆的制动效果和驾驶者的行车安全。
因此,制动系统设计是汽车工程领域中的重要课题之一。
本文将讨论制动系统设计的关键要素和技术挑战,以及如何通过优化设计来提高制动系统的性能。
一、制动系统的基本原理制动系统的基本原理是通过施加力量来减速或停止车辆的运动。
它主要由制动器、制动液、制动管路和制动控制系统等组成。
制动器是制动系统的核心部件,它通过施加摩擦力来减速车辆。
制动液在制动器和制动踏板之间传递压力,制动管路将压力传递到制动器上,而制动控制系统则负责控制制动力的大小和分配。
二、制动系统设计的关键要素1. 制动效果:制动系统设计的首要目标是实现良好的制动效果,即在短时间内将车辆停止或减速到安全范围内。
制动效果的好坏主要取决于制动器的性能和制动力的大小。
2. 制动稳定性:制动系统在制动过程中要保持稳定,避免制动过程中的抖动或失控现象。
制动稳定性的实现需要考虑制动器的设计和制动力的分配等因素。
3. 制动耐久性:制动系统在长期使用中需要保持稳定的性能。
制动器的材料和结构设计要考虑到耐磨损、耐高温和耐腐蚀等因素,以确保制动系统的长期可靠性。
4. 制动舒适性:制动过程中产生的噪音、震动和刹车跳动等问题会影响驾驶者的舒适性。
制动系统设计需要考虑减少这些不良影响,提供平稳、静音的制动体验。
三、制动系统设计的技术挑战1. 制动力的分配:在制动系统设计中,如何合理分配制动力是一个关键问题。
前轮制动力过大会导致车辆打滑,后轮制动力过大则会导致车辆失控。
因此,制动系统设计师需要根据车辆的动力学特性和重心位置等因素来优化制动力的分配。
2. 制动器的材料选择:制动器的摩擦材料对制动效果和制动稳定性起着重要作用。
目前常用的制动器材料有有机材料、金属材料和陶瓷材料等。
设计师需要根据车辆的使用条件和性能要求来选择合适的制动器材料。
3. 制动系统的热管理:制动过程中会产生大量的热量,如果不能及时散热,会导致制动器的性能下降甚至失效。
(完整word版)三相异步电动机能耗制动系统设计

课程设计说明书作者:hh学号:jj学院:kk专业:pp题目:三相异步电动机能耗制动系统设计指导者:hh hh1、引言 (1)1.1课程研究背景 (1)1.2课程研究的价值 (1)1.3课程设计的任务 (1)2、三项异步电动机的基本结构和工作原理 (2)2.1三项异步电动机的基本结构 (2)2.1.1定子 (2)2.1.2转子 (3)2.2三项异步电动机的工作原理 (3)3、三相异步电动机的能耗制动 (4)3.1能耗制动的原理 (4)3.2能耗制动的设计 (5)3.2.1电器元件的选择 (5)3.2.2计算与校验 (6)3.2.3能耗制动原理图 (6)3.3能耗制动的分析 (7)3.3.1能耗制动特点[9] (7)3.3.2能耗制动控制线路 (7)结论 (7)参考文献: (8)1、引言1.1课程研究背景三相异步电动机又称三项感应电动机,它的应用非常广泛,几乎涵盖了农业生产和人类生活的各个领域。
随着电气化、自动化技术的发展,三项异步电动机得到了越来越好的控制。
而电气化控制相较其他控制方法而言,更简洁便于操作,所以应用比较广泛。
本课题的控制是采用PLC的梯形图编程语言来实现的。
梯形图语言是在可编程控制器中的应用最广的语言,因为它在继电器的基础上加进了许多功能、使用灵活的指令,使逻辑关系清晰直观,编程容易,可读性强,所实现的功能也大大超过传统的继电器控制电路。
三相异步电动机切断电源后,由于惯性作用,转子需要经过一定时间才能停止旋转,这往往不能满足有些机械设备的工艺要求,造成运动部件的停机位置不准确,同时也影响生产效率的提高,因此必须对电动机采取有效的制动措施。
停机制动方法有两大类,即机械制动和电气制动。
机械制动是采用机械制动装置来强迫电机迅速停止,常用的有电磁抱闸制动和电磁离合器制动等。
电气制动是使电动机产生一个与原来转子转动方向相反的制动转矩而使其迅速停止常用的有反接制动能、耗制动等[2]。
长期以来,能耗制动始终处于工业自动化控制领域的主战场,为各种各样的自动化控制设备提供了非常可靠的控制应用。
制动系统毕业设计.

华东交通大学专科生毕业设计(论文)年级: 2014季春专业:铁道机车车辆层次:高起专姓名: XXXX201X年 X月 X日目录摘要 (2)关键词 (2)第1章制动系统 (2)第2章制动机的发展史 (3)第3章 CCBⅡ制动机 (4)3.1 CCBⅡ电空制动机概述 (4)3.2 CCBⅡ电空制动机构造及作用 (6)3.3 CCBⅡ电空制动机的控制关系 (26)总结 (42)致谢 (42)参考文献 (43)【摘要】CCBII制动机是新一代微机控制制动机,广泛应用在中国铁路重载货运运输中,确保制动机系统正常工作对机车安全运行意义重大。
制动机复杂的结构使对自身的故障诊断存在一定困难,需要开发CCBII制动机故障诊断系统。
本文首先对制动机结构和功能进行介绍,对制动机存在的故障特点进行分析,针对每类故障提出了相应的诊断策略,构建了制动机故障诊断整体方案。
针对制动机气动模块故障诊断的难题,本文提出了基于模型的故障诊断策略。
【关键词】电力机车;均衡风缸不减压;制动位;电空阀;压力开关1绪论有效的制动装置,又称制动系统(简称制动机),是铁道机车车辆的重要组成部分。
本章简单介绍制动的基本概念,对于制动系统的组成和作用,机车制动机的发展史也做了简单的讲述。
一、制动系统所谓制动,是指能够人为地产生列车减速力并控制这个力的大小,从而控制列车减速或阻止它加速运行的过程。
制动过程必须具备两个基本条件:实现能量转换;控制能量转换。
制动力是指制动过程中所形成的可以人为控制的列车减速力。
制动系统是指能够可控制的列车减速力,以实现和控制能量转换的装置或系统。
制动系统由制动机、手制动机和基础制动装置三大部分组成。
其控制关系(即工作流程)如下:图1-1 制动系统控制关系图无论是机车,还是车辆,都具有各自的制动系统,个各自的制动机、手制动机和基础制动装置。
当机车、车辆组成列车后,其各自的制动系统相互联系而构成一个统一的制动系统——列车制动系统。
- 1、下载文档前请自行甄别文档内容的完整性,平台不提供额外的编辑、内容补充、找答案等附加服务。
- 2、"仅部分预览"的文档,不可在线预览部分如存在完整性等问题,可反馈申请退款(可完整预览的文档不适用该条件!)。
- 3、如文档侵犯您的权益,请联系客服反馈,我们会尽快为您处理(人工客服工作时间:9:00-18:30)。
制动系统设计第七章制动系是汽车的一个重要的组成部分。
它直接影响汽车的行驶安全性。
为了保证汽车有良好的制动效能,应该合理地确定汽车的制动性能及制动系结构。
制动动力学7.1稳定状态下的加速和制动7.1.1加速力和制动力通过轮胎和地表的接触面从车辆传送到路面。
惯性力作用于车辆的重心,引起一阵颠簸。
在这个过程中当刹车时,前后轮的负载各自增加或减少;而当加速时,情况正好相反。
制动和加速加以区分。
下面,a的过程只能通过纵向的加速度x我们先来分析一辆双轴汽车的制动过程。
,在制动过最终产生结果的前后轮负载和??FF ZhZV随着静止平衡和制动减速的条件而变程中,图7.1 为:(7.1a)???Flhl??mgma?ll ZVVx(7.1b)?Flhl?mgl?ma ZhxV设作用于前后轴的摩擦系数分别为f和f,那么制hV动力为:??FFf ZVVXV.(7.2a)??Ff?F XhZhh(7.2b)图7.1双轴汽车的刹车过程它们的总和便是作用于车辆上的减速力。
(7.3)maF?F?xXVXh对于制动过程,f和f是负的。
如果要求两轴上hV的抓力相等,这种相等使 f=f=a/g,理想的制动xVh力分配是:)glh]/(alg?Fma[(l?)?xvXVx 7.4())gl/(?gl[?Fmaa]h xvxXh 7.5()的参数表现。
在)和参数(FF这是一个抛物线a xxvxh的右半部分,显示了一辆普通载人汽车的理想7.1图制动力分配。
实践中,向两边分配制动力通常被选用来防止过早的过度制动,或是由刹车片摩擦偏差而引起的后轮所死,因为后轮锁死后将几乎无法抓地,车辆将会失去控制。
然而防抱死刹车系统将会减轻这个问题。
当然,每一个负载状态都有它各自的理想制动力分配。
如果所有负载状态都必须由一个固定的分配去应对,那么最重要的条件往往就是空车载司机的情况。
虽然,固定的分配在更多负载时无法实现最优化的制动力分配,b线显示了当后轴的制动力未超过理想值直到最大减速度为0.8g时的制动力分配情况。
弯曲的分配曲线可通过如下方法应用。
图 7.2 半挂车的刹车过程情况(c)使用一个后轴限压阀,情况(d)使用减压阀。
那些负载变化巨大的车辆,比如说卡车,或火车站货车及很多前轮驱动车,都有减压阀,并且带.有一个可变的突变点,具体要看静止时的轴上负载(所谓的“制动力调节器”)。
在一辆双轴车上,轮子在制动中的负载只取决于减速度,而不取决于设定的制动力分配。
但这对于有三个或以上轴的车辆来说并不适用。
例如拖车,图7.2,高度协调了拖车接点的hk,h1和h2,拖拉机和拖车的重心,设定的制动力分配决定了连接力Fxk 和F2k,从而决定了各轴上力的分布。
这里建立的制定过程等式仍然有效,对于加速,加速度为正值。
7.2、制动系统设计与匹配的总布置设计硬点或输入参数新车型总体设计时能够基本估算如下基本设计参数, 这些参数作为制动系统的匹配和优化设计的输入参数.7.3、理想的前、后制动器制动力分配曲线7.3.1 基本理论(1) 地面对前、后车轮的法向反作用力在分析前、后轮制动器制动力分配比例以前,首先了解地面作用于前、后车轮的法向反作用力。
图7.3.1g h Fz1Fz2由图7.3.1,对后轮接地点取力矩得du h?mFL?Gb gz1dt式中:——地面对前轮的法向反作用力;——汽车重力;——汽车质心至后轴中心线的距离;——汽车质量;——汽车质心高度;du——汽车减速度。
dt对前轮接地点取力矩,得du h??GamFL g2z dt式中——地面对后轮的法向反作用力;F2z——汽车质心至前轴中心线的距离。
则可求得地面法向反作用力为h??Gdu g???Fb???1z Lgdt??h??Gdu(7.3.1)g???a?F??2z dtLg??(2) 前、后制动器制动力分配曲线在任何附着系数的路面上,前、后车轮同时抱死的条件是:前、后轮制动器制动力之和等于附着力;并且前、后轮制动器制动力分别等于各自的附着力,即:?G?F?F??21?FF??11z?FF??22z?消去变量,得1G4hgLGb(7.3.2))](?2F?b?F[?F???112h2hG gg7.3.2 计算算例与计算结果由上述结果可以分别得出车型A和车型B的前、后车轮同时抱死时前、后制动器制动力的关系曲线——理想的前、后轮制动器制动力分配曲线,简称I曲线。
(1) 车型B的I曲线下图为车型B空载和满载时候的I曲线)N(?2F.?1F(2) 车型A的I曲线下图分别为车型A空载、满载的I曲线)N(?2F.1F7.4、前、后轮制动器制动力矩的确定7.4.1车型B制动器的制动力矩计算车型B所采用的为:前面为盘式制动器,后面为鼓式制动器。
下面就两种制动器分别进行制动力矩的计算。
已知制动总泵的参数如下:(1) 盘式制动器的制动力矩计算(a) 基本参数(b) 计算依据假定衬块的摩擦表面全部与制动盘接触,且各处单位压力分布均匀,则制动器的制动力矩为:R?M2fF?0式中——摩擦系数;f——单侧制动块对制动盘的压紧力;F0——作用半径计算结果(c)下面为盘式制动器的制动力矩与摩擦系数之间的关系曲线。
(Nm)?Mf由上图可以看出,当摩擦系数在0.35~0.42之间时,盘式制动器所能提供的摩擦力矩在1205Nm~1447Nm之间。
当f=0.38时,鼓式制动器提供的摩擦力矩为1309Nm。
(2) 鼓式制动器的制动力矩计算(a) 基本参数(b) 计算依据在摩擦衬片表面取一横向微元面积,由鼓作用在微元面积上的法向力为:对于紧蹄:2??dsin??dF1dF1fRpbfR max对于松蹄:其中(c) 计算结果下图为鼓式制动器所能提供的制动力矩——摩擦.系数曲线。
(Nm)?Mf由上图可以看出,摩擦系数在0.35~0.42之间时,制动力矩在524Nm~706.53Nm之间。
当f=0.38时,鼓式制动器提供的摩擦力矩为598.316Nm。
(3) 确定同步附着系数通过上述关于制动器的制动力矩的计算,可以得.到前、后制动器之间的制动力分配的比例:?M?1??MM???21通过这个曲线与I曲线的交点处的附着系数为同步附着系数。
7.4.2确定车型A的制动器制动力矩(1) 基本原理选定同步附着系数φ,确定为0.7。
0并用下列计算前、后轮制动力矩的比值。
Mb?h1?g0?M ha?2?g0然后,根据汽车满载在柏油、混凝土路面上紧急制动到前轮抱死,计算出前轮制动器的最大制动力矩M;在根据前、后轮制动力矩的比值计算出后轮1max μ制动器的最大制动力矩M。
2maxμ(2) 基本参数计算结果(3)7.4.3 车型A的制动器改进结果前桥制动力矩为2323 Nm,后桥制动力矩1430Nm。
即所采用的盘式制动器制动力矩为2323/2=1161.5Nm,鼓式制动器为1430/2=715Nm。
通过确定前、后轮制动器的最大制动力矩,可以用7.3中提及的公式,用改变制动分泵的直径来改变原来制动器的制动力矩。
可以得出制动分泵改变情况如下:上,前桥采用盘式制动器,后桥采用鼓式制A在车型,鼓式制动器的缸动器。
盘式制动器的缸径为48mm 。
21mm径为7.5、比例阀的设计由于,对于具有固定比值的前、后制动器制动力的制动系特性,其实际制动力分配曲线与理想的制动力分配曲线相差很大,附着效率低。
因此,现代汽车均装有制动力调节装置,可根据制动强度,载荷等因素来改变前、后制动器制动力的比值,使之接近于理想制动力分配曲线,满足制动法规的要求。
7.5.1 基本参数由上述参数,用前面讨论过的盘式、鼓式制动器的计算方法,可以得出以下结果:的校核7.5.2 GMZ1GZM1调节后,汽车在空、满载时的状态如下:经如下图:那么可以得出,空载的时候,经比例阀调节后,后面的制动器提供的制动力是小于当时情况下的地面所能提供的制动力的;满载的时候,经比例阀调节后,后面的制动器提供的制动力是大于当时情况下的地面所能提供的制动力的。
.7.5.3 GZM2的校核经GZM2调节后,结果如下:同样,空载的时候,经比例阀调节后,后面的制动器提供的制动力是小于当时情况下的地面所能提供的制动力的;满载的时候,经比例阀调节后,后面的制动器提供的制动力是大于当时情况下的地面所能提供的制动力的。
7.5.4新曲线通过上面的计算可以看出,GZM1和GZM2可以满足0.7g时空载时的要求,但是不满足在满载时候的要求。
那么,理想的调节曲线如下:可以得出实际的新曲线,如下:上图中,1、4为GZM2曲线,2、3为新曲线。
比较上述图表,我们可以得出以下结论;如下表对照可得:空载状态满载状态新曲线更贴近理想的调节状态,也更能充分的利用地面附着系数。
7.6、总泵的校核由于相对与原车,前、后制动器轮缸直径发生了变化,因此需要校核原车总泵的容积是否满足改动后的容积要求。
7.6.1基本参数改动前,盘式制动器轮缸缸径,容积;''1v1D鼓式制动器轮缸缸径,容积;''2v2D总泵的缸径为,前腔容积,后腔容积''f_v D;'bv_改动后,盘式制动器轮缸缸径,容积;1D1v鼓式制动器轮缸缸径,容积;1D2v 总泵的缸径为;前腔容积,后腔容积;D bvv_f_7.6.2基本理论如果原总泵的前、后腔容量满足制动器的需要,那么就认为原总泵是满足要求的,反之,就认为是不满足。
7.6.3校核结果参数结果1.08个盘式制动器所需制动2 )液(mL5.542 2个鼓式制动器所需制动)液(mL6.398 mL总泵前腔容积()4.653 mL总泵后腔容积()由上可以得出,前、后腔的容积是满足前、后制动器的需要的。
7.7法规要求7.7.1 GB12676-1999法规要求由于GB12676-1999制动法规要求0 发动机脱开的型试验性能要求。
)规定6.6.2.2a)和空、满载试验车辆分别按6.6.2.1a 的试验方法进行,在规定的车速下,各类车辆试验结果必须达到下表规定的最低性能要求。
50080M1 5.8。
那么其规定的制动距离为:50.667m下面为车型A在GB12676-1999法规要求下,其制动距离和充分发出的平均减速度。
GB12676-1999由上可以得出,是符合法规要求的。
7.8 GB 7258-1997法规要求法规要求:汽车、无轨电车和四轮农7258-1997GB用运输车的行车制动,必须采用双管路或多管路,当部分管路失效时,剩余制动效能仍能保持原规定值的30%以上。
前失效和后失效的情况下,剩余制动效A下面为车型能占原规定值的比值。
法规要求的。
GB 7258-1997可以看出,是符合、结论7.9通过上面的分析可以得到:7.9.1 理论曲线下面为前、后制动器匹配后,整车的理想I曲线和 曲线。