PCB制程管控及审核重点
PCB制程管控及审核重点
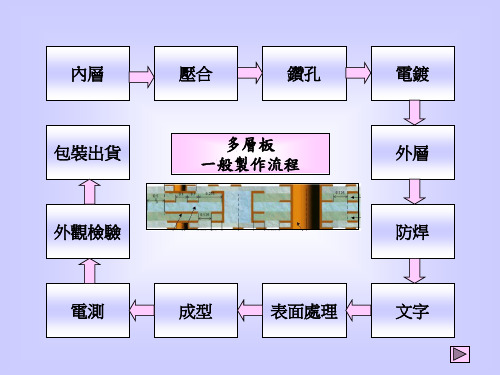
除膠渣 去除孔內膠渣
化學銅 以化學置換方式於孔 內壁形成銅導體
制程管控
A.水破試驗 B.刷痕測試
稽核重點 參數於管制範圍
A.藥液配槽校驗
重修流程
B.背光級數/孔壁粗糙度 切片檢查記錄
銅箔 膠片 基板 膠片 銅箔
電鍍
去毛頭
除膠渣
化學銅
電鍍銅
流 程 作用
電鍍銅
以電鍍方式於孔內壁 形成銅導體,達到客戶 指定面/孔銅厚度
前處理
防焊
塞孔
塗佈 後烘烤
底片
綠漆 銅箔 膠片 基板 膠片 銅箔 綠漆
底片
預烤
曝光
清洗
顯影
流程 顯影
作用 防焊區域形成
清 洗 去除板面殘餘藥液
後烘烤 增加防焊綠漆之硬度
制程管控 顯影不潔,曝偏
A.烤箱參數設定 B.依賴度測試 *硬度 *剝離力
稽核重點 重修管控
參數是否在管制範圍
重修管控 人員檢測動作
A.升溫速率 B.升壓速率 C.板厚,凹陷,皺折,板翹
製作半撈,鉆孔用之 A.層間對準度
工具孔
B.尺寸漲縮
稽核重點 是否有壓合防呆設計
人員認證
棕化
壓合
預疊
壓合
銅箔 膠片 基板 膠片 銅箔
鉆靶 清洗
半撈 去毛邊
流程 半撈 去毛邊 清洗
作用 去除不規則之板邊 去除板邊銳利錂角 清除殘屑
制程管控 銑刀規格 參數設定
乾膜 基板 乾膜
裁切
前處理
覆膜
曝光
顯影
內層
AOI
清洗
去膜
蝕刻
流程 蝕刻
作用
內層線路 形成
制程管控
PCB供应商制程审核要点

PCB供应商制程审核要点内层1、针对预清洁线是否有建立预先点检表单?是否已经执行(已经填写)?2、刷磨/预清洁化学药水是否有证据证明其有按照理化室文件规定的频率进行分析?3、是否有证据证明预清洗倾槽与更槽计划有符合文件要求?4、是否有证据证明所有的化学品与文件上管控的物质有监督并管控?5、槽液测试是否每班测试一次以确保预清洁品质良好?6、无尘室的预清洁线入口到无尘室是否有良好的压力?7、无尘室的温度,湿度与尘埃粒子是否按照10K(万级)最高要求管控,并且有管控实效通知系统?8、无尘室的压膜与曝光区是否用的是黄灯并且所有的外部窗户使用的是UV膜?9、是否有证据可以证明干膜或是湿膜储存在温度与湿度管控的环境内?并且,到期管控有先进先出目录?10、在压膜前是否有粘尘滚轮清洁机器?11、针对干膜压膜,是否检查了压膜滚轮的温度并使用红外线表进行确认?12、是否有文件规定的干膜检验标准指导书以判定接受或判退?13、所有的制程工具与材料是否有相应的定义并管控在制定区域?包括老化敏感材料有效期过期?14、是否有文件规定干膜剥膜/重工程序有定义最大的重工次数?15、对干膜压膜,是否有对压膜滚轮温度进行检验并对红外线表进行确认?16、是否对工作菲林的最新版本进行管控?17、是否有证据表明管控了曝光的最大次数并对工作菲林曝光次数进行监控?18、在确定曝光次数后,是否使用粘尘滚轮对底片进行清洁?审核粘尘滚轮的状况?19、在底片设计阶段,是否确认了前后对准度的工具/制程最大公差?是否被定义为关键SPC参数?20、在这些制程是否对上下对准度进行确认?21、可允许的最大曝光次数是否有文件规定并有相应的系统对其跟踪?22、是否能证明菲林的曝光次数有进行监控并且底片没有超出文件规定的使用期限?23、曝光和显影之间是否按文件规定最大的静置时间并有按照此要求执行?24、DES 线是否有预启动点检表?是否已经进行(有完整地填写)?25、是否能证明所有的化学品有进行监控并有管控清单?26、DES线是否有文件规定不良品与返工计划,并且有客观证据说明有按照其要求执行?27、在批量蚀刻前是否先进行首件确认,以保证蚀刻机设备与线径?28、是否至少定期稽核一次蚀刻站并有相应的维护记录作为品质文件?29、蚀刻机运作速度是否有规定并且有文件规定铜重量/厚度?30、过滤系统是否完善?清洁频率与更换频率是多少?31、是否有文件规定最大水洗污染水准,水洗流动率与对传导性进行确认?32、是否有专门的对DES线清洁,烘干与无沾污进行检验?33、剥膜机是否有过滤系统以去除干膜膜屑?34、是否有作业员单独操作每个重要项目(控制,电源,地面)以防止刮伤?35、是否规定作业员的清洁计划?36、现场是否有系统规定主要测试哪条线径?37、是否有文件规定线径测试的频率?外层AOI1、所有层数是否100%进行AOI检测?2、所有的工具是否有相应的规定并放置在指定的区域?3、是否对电源/接地层进行检验并按照抽样计划定期统计?4、是否根据客户资料制定AOI程序,并且由工程建立所需的AOI关键参数设备与程序?5、AOI程序是否有相应的参数,其涉及到最小线径,最小间距,等?6、是否有不良标准板用于确认每台AOI机是否能够在开始每批测试前测出所有的不良?7、现场是否系统要求干膜首件发现重复不良时作出相应的通知?8、若一批内出现了各种不良,此信息是否立即反馈给DES作业员并审核其作业动作?例如:残铜,线路缺口,短路,断路?9、AOI不良确认是否有独立的确认站并且有收集不良资料并进行有意义的报告?10、修补后的板子是否有重新过AOI确认找出的不良已经全部修补OK?11、AOI站的产率是否每日进行跟踪并及时反馈给I/L制程建立相应的改善小组?是否对直通率与最终生产率目标进行定义?12、若产量低于目标,是否采取相应的改善措施?13、是否针对最高不良项目有要求使用柏拉图进行分析?是否采取持续有效的改善方法以减少最高不良?"14、返工指导书是否符合IPC规范?15、是否有明确的说明若返工时超过3条线路断路,则报废?16、是否针对已经焊接的线路进行胶带测试,以确保修补板的可靠性?棕化1、是否能证明棕化药水供应商在3个月前有对棕化线进行稽核?若没有这样做,是否采取了相应的措施?2、是否有进行DOE确保最好的棕化厚度以保证在热压测试制程发生分层?3、是否对微蚀率进行监控?其是否有SPC图管控并有正在进行的措施?4、氧化粘合强度测试是否针对所有材料类型的每条线每周进行一次测试?5、棕化药水是否有定量给料系统?6、是否使用DI水进行水洗?7、机器是否干燥并无污染?8、是否能证明黑化厚度有很好的管控?9、氧化板是否颜色统一,外表无刮伤/或操作导致损坏?10、离子污染测试是否按照要求每次换班执行一次?11、氧化线是否返工?若有返工,是否有文件规定最大返工次数?压合1、叠合线无尘室是否有相应的温度与湿度管控?2、是否规定氧化线-叠合作业的静置时间?3、现场是否有文件以确保每对预叠有按照凡谷承认的要求执行?4、是否定期检查以确保实际降温率不超过5度/分?温度升温与降温速率是多少?5、每批钢板是否定期清洁并打磨?钢板的厚度是否定期检查其厚度?6、是否能证明压合平台是否平整/平行并至少1-6个月检查一次?7、压合后的板厚是否进行抽樣检验, 对每PNL至少检验的5个点?8、X-RAY冲床是否管控对准度的设计补偿精确度?9、是否有品质检验程序文件对压合板数脂沾污进行定义?10、所有用于凡谷型号的板材,是否每周对压合产品检测一次TG与△TG?11、是否有文件规定X-RAY钻孔对准度的接受/判退标准?12、是否有文件定义对X-RAY钻孔系统进行尺寸测量确认?钻孔1、钻孔机是否有破损钻咀与不良钻咀尺寸鉴定能力?2、钻孔机是否能够清楚地定义钻孔参数,包括堆叠厚度?3、是否在开始生产前,对钻孔程序进行检验?4、是否能证明钻轴偏移管控良好?5、堆叠高度,每钻咀的最大钻次,进刀速度是否对板材类型,板厚,曾数,与孔尺寸进行管控?6、是否通过切片或X-RAY对钻咀对准度进行检验?频率是多少?7、是否对钻咀破损有调查改善计划并减少了不良次数?是否有客观证据证明已经有管控此项?8、是否有文件规定钻孔重工/修补程序并有相关品质点检表?9、所有PCB漏钻孔位于钻孔机台面上已经钻过的位置?10、再次研磨的钻咀是否在使用前进行检验与确认?11、是否有文件规定并对最大研磨次数进行管控?12、在使用之前是否对铝板进行检验,以确保无凹陷与刮伤?13、每轴底部的板子是否检验其孔尺寸,孔位,孔对准度与孔数量等?14、对钻孔精确度,孔径,孔数量,孔位与铜箔表面确认,是否有相应的检验程序?15、钻孔机孔位对准度能力数据是否对每台机器/每轴进行跟踪?16、钻孔机偏移度是否追踪到每台机器/每轴?17、在钻孔后是否通过良品测试机器或X-RAY检验其对准度?18、钻孔制程是否使用SPC?19、所有的PASS/REJECT板是否贴有相应的标签以避免混料或遗失?20、是否有SPC管控并有最近更新关键参数管控?21、所有超出管控的项目是否有相应的改善对策?化学沉铜1、去毛刺线是否有启动前点检表?是否已经运行(完整填写)?2、去毛刺机器是否有风刀,流动性&超声波?3、在去冲孔孔内毛刺后,是否检验孔?若有,是否有持续改善的资料?4、去毛刺后,板面与孔是否完全干燥?5、去毛刺线是否有开机点检表?目前是否运行?6、生产线上的温度,抽水机,槽液条件等是否管控在制程规范内?7、是否能证明化学药水分析有定期完成?8、化学沉铜线是否有开机点检表?目前是否运行(完整填写)?9、是否检查化学沉铜的孔两面的背光?10、化学沉铜在开始生产前是否有进行是试镀?11、化学沉铜线生产是否有规定的品质确认程序的判定接受/判退标准。
论述PCB板制作及品质控制

论述PCB板制作及品质控制
PCB(Printed Circuit Board,印刷电路板)制作是电子产品制造过程中至关重要的一环。
以下是PCB板制作及品质控制的基本步骤和要点:
1. 设计:根据电路设计需求,使用电路设计软件进行PCB设计,并生成相应的Gerber文件。
2. 材料准备:选择符合要求的基板材料和焊接材料。
基板材料通常是经过玻璃纤维增强的环氧树脂材料,焊接材料一般是金属合金。
3. 单面或双面铜箔覆盖:基板通过化学或机械镀铜的方式,在表面覆盖一层铜箔,形成铜层,以实现电路导电功能。
4. 光刻:将Gerber文件中的电路线路图案,通过光刻技术转移到覆铜层上。
在曝光、显影和蚀刻等步骤后,形成所需的电路图案。
5. 孔钻及金属化孔:根据Gerber文件的要求,使用机械钻床钻孔,并通过化学方法在孔内镀上金属,以获得连接层。
6. 电镀:将整个PCB板放入电镀槽中,通过电化学方法,使得电镀铜附着在导线和连接孔上,形成导电层。
7. 裁剪:将大板裁剪成所需的小板大小。
8. 防焊涂覆:在需要防止焊接的区域覆盖防焊涂覆层,以防止焊接过程中铜箔短路。
9. 防腐涂覆:对整个PCB板表面涂覆防腐层,以提高PCB板的抗腐蚀和耐用性。
十. 品质控制:在制作过程中,需要进行严格的品质控制,包括PCB板的尺寸精度、线路连接的可靠性、焊盘质量等方面的检验。
常见的品质控制方法包括目视检查、X射线检测、电气测试、仿真测试等。
在PCB板制作过程中,品质控制的好坏将直接影响到最终产品的性能和可靠性。
因此,确保制作过程的准确性和良好的品质控制对于电子产品的稳定运行至关重要。
印制电路板的质量控制与检验
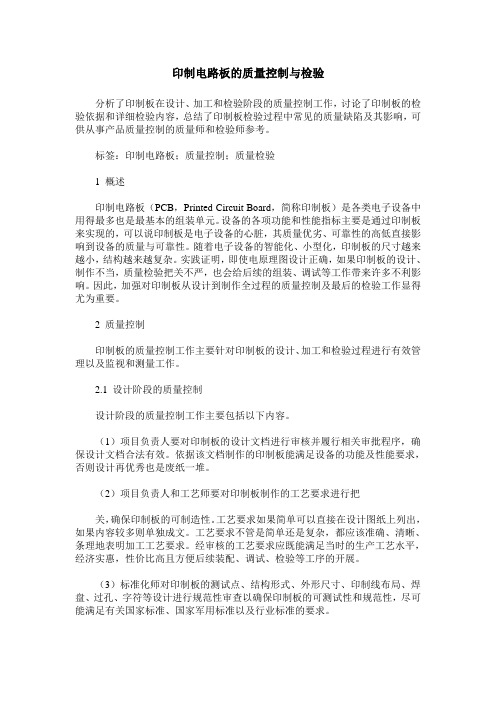
印制电路板的质量控制与检验分析了印制板在设计、加工和检验阶段的质量控制工作,讨论了印制板的检验依据和详细检验内容,总结了印制板检验过程中常见的质量缺陷及其影响,可供从事产品质量控制的质量师和检验师参考。
标签:印制电路板;质量控制;质量检验1 概述印制电路板(PCB,Printed Circuit Board,简称印制板)是各类电子设备中用得最多也是最基本的组装单元。
设备的各项功能和性能指标主要是通过印制板来实现的,可以说印制板是电子设备的心脏,其质量优劣、可靠性的高低直接影响到设备的质量与可靠性。
随着电子设备的智能化、小型化,印制板的尺寸越来越小,结构越来越复杂。
实践证明,即使电原理图设计正确,如果印制板的设计、制作不当,质量检验把关不严,也会给后续的组装、调试等工作带来许多不利影响。
因此,加强对印制板从设计到制作全过程的质量控制及最后的检验工作显得尤为重要。
2 质量控制印制板的质量控制工作主要针对印制板的设计、加工和检验过程进行有效管理以及监视和测量工作。
2.1 设计阶段的质量控制设计阶段的质量控制工作主要包括以下内容。
(1)项目负责人要对印制板的设计文档进行审核并履行相关审批程序,确保设计文档合法有效。
依据该文档制作的印制板能满足设备的功能及性能要求,否则设计再优秀也是废纸一堆。
(2)项目负责人和工艺师要对印制板制作的工艺要求进行把关,确保印制板的可制造性。
工艺要求如果简单可以直接在设计图纸上列出,如果内容较多则单独成文。
工艺要求不管是简单还是复杂,都应该准确、清晰、条理地表明加工工艺要求。
经审核的工艺要求应既能满足当时的生产工艺水平,经济实惠,性价比高且方便后续装配、调试、检验等工序的开展。
(3)标准化师对印制板的测试点、结构形式、外形尺寸、印制线布局、焊盘、过孔、字符等设计进行规范性审查以确保印制板的可测试性和规范性,尽可能满足有关国家标准、国家军用标准以及行业标准的要求。
2.2 加工阶段的质量控制加工阶段的质量控制工作主要包括以下内容。
PCB制程管控及审核重点

加强制造过程的监控,确保工艺参 数正确;采用高可靠性的材料和工 艺;定期检查PCB线路,发现断路 及时修复。
常见问题三:阻抗不匹配
总结词
阻抗不匹配是指PCB上的线路阻抗与预期值不符,导致信号传输质 量下降的现象。
详细描述
阻抗不匹配可能由线路宽度、长度、介质常数等参数变化引起。阻 抗不匹配可能导致信号反射、失真或延迟。
流程监控
对制程中的关键环节进行 实时监控,确保流程的稳 定性和一致性。
管控工具与技术
工具选择
根据制程需求,选择合适 的生产设备和检测工具。
技术更新
关注行业新技术发展,及 时引进和应用先进的制程 技术。
工具维护
定期对生产设备和检测工 具进行维护和保养,确保 其正常运行和准确性。
管控标准与规范
标准制定
PCB制程管控及审核重点
目 录
• PCB制程概述 • PCB制程管控要点 • PCB制程审核重点 • PCB制程常见问题及解决方案 • PCB制程发展趋势与展望
01 PCB制程概述
PCB制程简介
PCB制程是将电子零件与电路以导电铜箔印刷的方式,安装在基板(PCB)上,以 实现电子电路的连接与组装的一种工艺。
THANKS FOR WATCHING
感谢您的观看
柔性PCB技术
总结词
柔性PCB技术具有柔性和可弯曲的特性,适用于各种不规则表面和空间受限的应 用场景。
详细描述
柔性PCB技术利用柔性基材和特殊的加工工艺,实现了PCB的可弯曲和可折叠特 性。这种技术广泛应用于穿戴设备、折叠屏手机等领域,为现代电子产品带来了 更灵活的设计和更轻薄的外观。
绿色环保PCB技术
02
良好的PCB制程可以简化生产流程,提高生产效率,降低生产
PCB各工艺质量控制重点
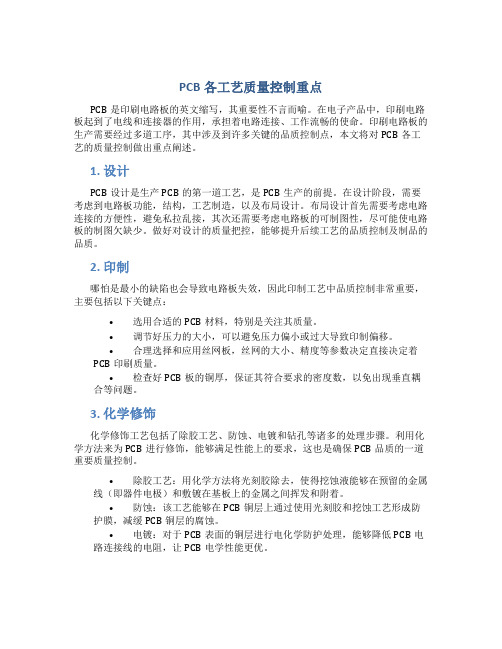
PCB各工艺质量控制重点PCB是印刷电路板的英文缩写,其重要性不言而喻。
在电子产品中,印刷电路板起到了电线和连接器的作用,承担着电路连接、工作流畅的使命。
印刷电路板的生产需要经过多道工序,其中涉及到许多关键的品质控制点,本文将对PCB各工艺的质量控制做出重点阐述。
1. 设计PCB设计是生产PCB的第一道工艺,是PCB生产的前提。
在设计阶段,需要考虑到电路板功能,结构,工艺制造,以及布局设计。
布局设计首先需要考虑电路连接的方便性,避免私拉乱接,其次还需要考虑电路板的可制图性,尽可能使电路板的制图欠缺少。
做好对设计的质量把控,能够提升后续工艺的品质控制及制品的品质。
2. 印制哪怕是最小的缺陷也会导致电路板失效,因此印制工艺中品质控制非常重要,主要包括以下关键点:•选用合适的PCB材料,特别是关注其质量。
•调节好压力的大小,可以避免压力偏小或过大导致印制偏移。
•合理选择和应用丝网板,丝网的大小、精度等参数决定直接决定着PCB印刷质量。
•检查好PCB板的铜厚,保证其符合要求的密度数,以免出现垂直耦合等问题。
3. 化学修饰化学修饰工艺包括了除胶工艺、防蚀、电镀和钻孔等诸多的处理步骤。
利用化学方法来为PCB进行修饰,能够满足性能上的要求,这也是确保PCB品质的一道重要质量控制。
•除胶工艺:用化学方法将光刻胶除去,使得挖蚀液能够在预留的金属线(即器件电极)和敷镀在基板上的金属之间挥发和附着。
•防蚀:该工艺能够在PCB铜层上通过使用光刻胶和挖蚀工艺形成防护膜,减缓PCB铜层的腐蚀。
•电镀:对于PCB表面的铜层进行电化学防护处理,能够降低PCB电路连接线的电阻,让PCB电学性能更优。
•钻孔:为了确保PCB板的通电性,钻孔的直径和深度需要合适,而且将钻孔拱口防护也是很关键的,若拱口防护不完善,则会导致铜连接不上或者没有电性能。
4. 组装在PCB生产的最后工阶段组装,同时也是PCB最为关键的一道工艺。
正确的组装工艺流程,是确保PCB电路运行正常的关键。
品保课制程管控及教育训练内容及PCB检验标准
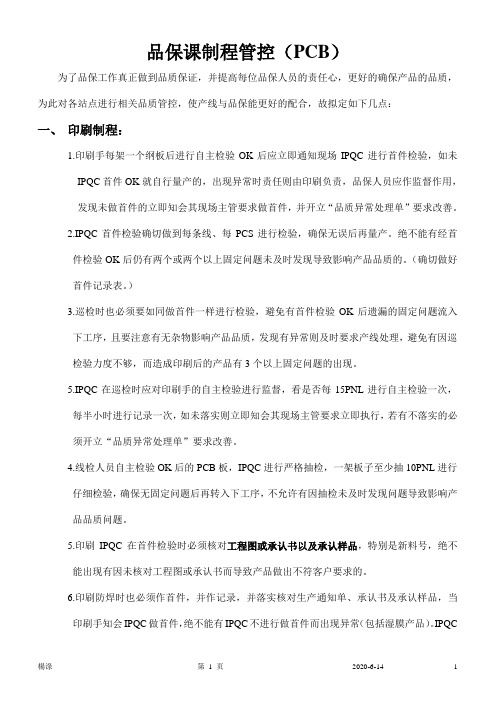
品保课制程管控(PCB)为了品保工作真正做到品质保证,并提高每位品保人员的责任心,更好的确保产品的品质,为此对各站点进行相关品质管控,使产线与品保能更好的配合,故拟定如下几点:一、印刷制程:1.印刷手每架一个纲板后进行自主检验OK后应立即通知现场IPQC进行首件检验,如未IPQC首件OK就自行量产的,出现异常时责任则由印刷负责,品保人员应作监督作用,发现未做首件的立即知会其现场主管要求做首件,并开立“品质异常处理单”要求改善。
2.IPQC首件检验确切做到每条线、每PCS进行检验,确保无误后再量产。
绝不能有经首件检验OK后仍有两个或两个以上固定问题未及时发现导致影响产品品质的。
(确切做好首件记录表。
)3.巡检时也必须要如同做首件一样进行检验,避免有首件检验OK后遗漏的固定问题流入下工序,且要注意有无杂物影响产品品质,发现有异常则及时要求产线处理,避免有因巡检验力度不够,而造成印刷后的产品有3个以上固定问题的出现。
5.IPQC在巡检时应对印刷手的自主检验进行监督,看是否每15PNL进行自主检验一次,每半小时进行记录一次,如未落实则立即知会其现场主管要求立即执行,若有不落实的必须开立“品质异常处理单”要求改善。
4.线检人员自主检验OK后的PCB板,IPQC进行严格抽检,一架板子至少抽10PNL进行仔细检验,确保无固定问题后再转入下工序,不允许有因抽检未及时发现问题导致影响产品品质问题。
5.印刷IPQC在首件检验时必须核对工程图或承认书以及承认样品,特别是新料号,绝不能出现有因未核对工程图或承认书而导致产品做出不符客户要求的。
6.印刷防焊时也必须作首件,并作记录,并落实核对生产通知单、承认书及承认样品,当印刷手知会IPQC做首件,绝不能有IPQC不进行做首件而出现异常(包括湿膜产品)。
IPQC应对未做首件机种加大抽检力度。
NG的及时知会产线停产处理。
直至处理OK后再量产。
二、电镀制程:1.IPQC对电镀制程做到每小时巡检一次,针对一铜、二铜、镀镍、镀金、蚀刻等站点进行巡检,并做好相关记录,杜绝因巡检不及时与未及时发现异常而导致产品报废率增加。
PCBA制程介绍及管制重点
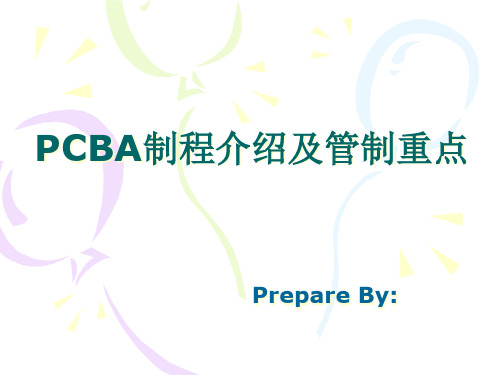
6 制程参数设定
SIC
7 不良品作业方式 SIC
8 产品良率监控
SPC
Remarks
型号,品牌,产地,有效期等
如水洗,标签/印章位置 如区分,修补等 如在线调整,停线trol Item
File
1 ESD 2 程式正确 3 产品制程要求 4 人员作业 5 不良品作业方式 6 产品良率监控
如静电袋,外箱等 如操作方式等
总结
IPQC的职责就是通过定时和不定时的巡回检 查,及时发现制程问题点,反馈和追踪相关人员 解决,有效的减少和预防不良问题发生,使制程 处于稳定的,有效的管制中,达成公司和客户的 需求.
结束语
我们还在路上,余晖消失之前都不算终点。
Thank you for coming, send this sentence to you, we are still on the road, before the afterglow disappears are not the end.
PCBA制程介绍及管制重点
Prepare By:
一.基本术语
EMS (Electronics Manufacturing Serving): 电子制造服务
SMT (Surface Mount Technology) 表面贴装技术
Solder Paste :锡膏 Stencil:钢网 Printing:印刷 Placement:贴片 Placement Equipment:贴片机 Nozzle:吸嘴
Pad
After solder paste printing印上锡膏
Solder paste on the pad
Pick /Place SMD & Reflow 上零件並热熔
pcb管理制度及流程
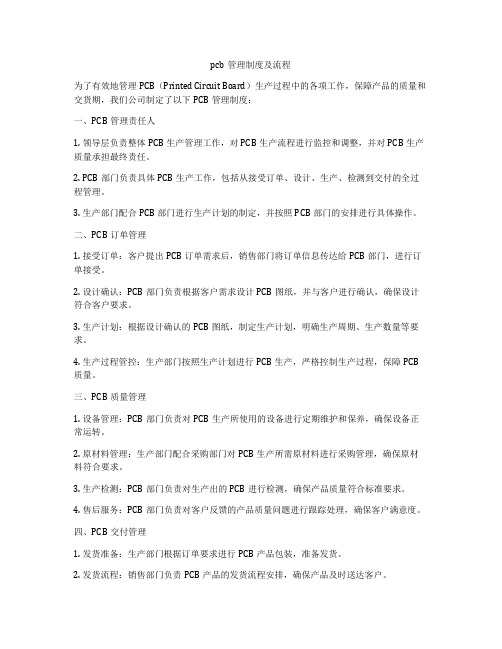
pcb管理制度及流程为了有效地管理PCB(Printed Circuit Board)生产过程中的各项工作,保障产品的质量和交货期,我们公司制定了以下PCB管理制度:一、PCB管理责任人1. 领导层负责整体PCB生产管理工作,对PCB生产流程进行监控和调整,并对PCB生产质量承担最终责任。
2. PCB部门负责具体PCB生产工作,包括从接受订单、设计、生产、检测到交付的全过程管理。
3. 生产部门配合PCB部门进行生产计划的制定,并按照PCB部门的安排进行具体操作。
二、PCB订单管理1. 接受订单:客户提出PCB订单需求后,销售部门将订单信息传达给PCB部门,进行订单接受。
2. 设计确认:PCB部门负责根据客户需求设计PCB图纸,并与客户进行确认,确保设计符合客户要求。
3. 生产计划:根据设计确认的PCB图纸,制定生产计划,明确生产周期、生产数量等要求。
4. 生产过程管控:生产部门按照生产计划进行PCB生产,严格控制生产过程,保障PCB 质量。
三、PCB质量管理1. 设备管理:PCB部门负责对PCB生产所使用的设备进行定期维护和保养,确保设备正常运转。
2. 原材料管理:生产部门配合采购部门对PCB生产所需原材料进行采购管理,确保原材料符合要求。
3. 生产检测:PCB部门负责对生产出的PCB进行检测,确保产品质量符合标准要求。
4. 售后服务:PCB部门负责对客户反馈的产品质量问题进行跟踪处理,确保客户满意度。
四、PCB交付管理1. 发货准备:生产部门根据订单要求进行PCB产品包装,准备发货。
2. 发货流程:销售部门负责PCB产品的发货流程安排,确保产品及时送达客户。
3. 交付验收:客户接收到PCB产品后进行验收,确认无误后签收。
4. 售后服务:PCB部门负责做好产品售后服务跟踪,解决客户在使用过程中遇到的问题。
五、PCB应急管理1. 突发事件处理:PCB部门负责应对突发事件,保障生产流程的正常进行。
2. 应急预案:PCB部门制定应急预案,配合其他部门进行突发事件的应对工作。
PCB电路板制造中的质量管理

PCB电路板制造中的质量管理
作为电子产品中不可或缺的一个组成部分,PCB电路板的制造质量对整个电子产品的质量和性能有着至关重要的影响。
因此,在PCB电路板制造过程中,对于质量管理的重视程度也显得尤为重要。
1.制造前的质量控制
首先,PCB电路板的制造过程的质量控制应该从制造前先开始。
即在PCB电路板的设计和布局时,应该仔细论证和评估各种不同方案的性能和质量等级。
在与客户充分沟通的基础上,充分考虑PCB电路板的板厚、贴膜厚度、线路宽度和间距等关键参数,以确保产品的性能和质量稳定可靠。
2.制造中的质量管控
其次,在PCB电路板的制造过程中,应采取一系列的质量管控措施,以确保产品质量。
例如,严格的原器材选型、颜色管理标准和严格的工艺控制等。
有一个好的制造流程体系和标准化流程能够保证生产工艺的紧密结合和协同工作,从而使得产品的质量得以管理和控制。
同时,生产线的自动化程度和自动化设备也是非常重要的。
3.制造后的质量保障
除了在PCB电路板制造过程中对质量的管控外,还应该对制造的PCB电路板进行质量检验和质量保障。
例如,使用测试设备进行电学和质量测量,以确保产品的质量达到预设标准。
此外,通过一定方式的追溯和质检管理,更能保证产品质量的稳定可靠。
在PCB电路板制造管理中,无论是前期的规划、中间的制造工序、还是后期的产品检验,都需经过专业严谨的流程,以实现全面的品质保障。
只有这样,才能保证PCB电路板的品质稳定,达到高标准的生产效率和质量要求。
因此,综上所
述,在PCB电路板制造管理过程中,严格的质量控制和管理是至关重要的,只有这样,才能够打造出更优良的产品。
PCB绘制规范及审核要点

PCB绘制规范及审核要点PCB设计规范及审核要点前言为了提高工作效率,为了减少不同的人犯同样的错的几率,统一部门内的设计原理器件与PCB 封装图库,由专人负责库更新及管理,凡设计中遇到新的器件,则应由使用人画好器件原理图与PCB 封装图,交由负责人更新规定库。
为确保硬件设计的成功率及生产的便利,硬件设计时,应从设计库中提调规定库,若工程师的库与管理员处的库存在出入,则将认定工程师处的库为非法库,无论在何种情况下,都应认定管理员处的库为最新库,当有需要变更时,应优先变更管理员库,并注明变更时间及原因,再由管理员统一发布更新(亦注明更新内容及时间)为尽量降低采购成本及库房管理成本,设计过程中,凡使用器件,均应优先从库中进行搜索,确认型号及封装一、PCB设计规范1、单板尺寸及定位、螺丝位尺寸a、一般情况下,PCB板的厚度默认为1.6mm,也可特殊说明采用1.2mm或其他b、在画板之前,确认单板尺寸,并在keepout层勾勒单板外形尺寸,以及定位孔、螺丝孔位置,与结构工程师确认尺寸!c、关于单板尺寸、定位孔及螺丝孔径,应以结构工程师为主导d、单板上,若存在割槽等需要挖空时,应注意开槽宽度至少要大于0.8mm,开槽距离板边缘至少要大于2mm,避免因留边过细而断开,除非有特殊要求e、单板上,若存在开槽用于插入其他PCB时,应注意槽宽度,至少要大于实际插入PCB板厚度,但不宜过宽,以0.2mm为宜2、布局基本原则a、确认单板上的可布局区域,调入网络器件b、一般情况下,以制作双面板为主,提倡将贴片器件统一放置一层,插件器件放置另一层c、PCB板的方向规定,以正式产品正视图为参考,凡人眼直视面,均应定义为顶层d、PCB板上下方向应与正式产品摆放方向一致e、布局时,应参考硬件模块示意图,原则上,应将主芯片放置中央位置,其他外设部分按照不同功能模块分区排列f、一般情况下,时钟产生器尽量靠近到用该时钟的器件。
石英晶体振荡器外壳要接地。
PCB板程序管控细则

PCB板程序管控细则PCB板程序管控细则是指针对PCB板设计与制造过程中的各个环节,制定详细的规定和控制措施,确保PCB板质量和生产效率的一套指导性文件。
以下是关于PCB板程序管控细则的一些建议,包括设计、制造、检测等方面的控制要点。
1.设计阶段:-PCB设计师应熟悉并遵守相关的PCB设计规范和标准,确保设计的可制造性和可维修性。
-PCB设计前,需要进行严格的电子元器件选型和文档库管理,确保元器件的质量和供应链的稳定性。
-对于高速信号线的设计,需要进行严格的信号完整性分析和仿真,确保信号传输的可靠性。
2.制造阶段:-PCB制造厂家需要有严格的质量管理体系,并进行质量控制,包括检验原材料、控制生产过程、进行成品检验等。
-PCB板的制造工艺需要符合相关的制造要求,包括焊接工艺、阻抗控制、盲穿孔等。
-PCB制造过程中需要进行严格的工艺文件控制,确保制造过程的数据和参数的准确性和一致性。
3.检测阶段:-在PCB板制造完成后,需要进行严格的检测,包括外观检查、尺寸检测、焊接质量检测、电性能测试等。
-对于高层板、复杂板、高速板等特殊类型的PCB板,需要进行更加严格的检测和验证,确保其性能和可靠性。
4.文档控制:-对PCB板的设计、制造、检测等环节需要建立相关的文档控制程序,确保各个环节的数据和文件的准确性和一致性。
-设备参数、制造过程和工艺、检测数据等需要进行详细记录和管理,以便追溯和后续改进。
5.过程改进:-在PCB板的设计、制造和检测过程中,需要及时发现和纠正问题,建立相关的纠正预防措施,以提高PCB板的质量和生产效率。
-同时,需要进行过程的持续改进,通过统计数据和分析,找到问题的根本原因,并进行相应的优化和改进。
以上是关于PCB板程序管控细则的一些建议和控制要点。
在实际操作中,可以根据具体的情况进行细化和完善,以确保PCB板制造过程的各个环节都能够得到有效的管控和控制。
只有通过严格的管控,才能够提高PCB板的质量和生产效率,满足客户的需求和要求。
PCBA 制程工艺控制要点
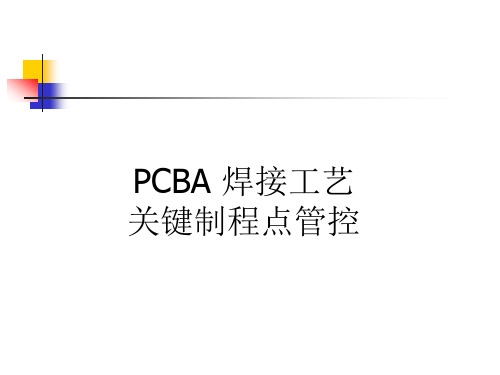
三、钢网管控
d. 钢网开口比例:在通常情况下,如没有特殊要求,钢网开口 比例选用1:1,如有特殊要求或在实际生产中有较多不良 ,开口比例可选用1:0.9到1:1.2之间(焊盘开口:钢网开 口)。 e. 钢网清洗:钢网在反复印刷的过程中很容易脏污,故必须对 钢网做定时清洗。一般情况下,机器每印刷3 – 5 片板时都 应该进行一次自动擦拭,累计印刷15片板时应进行一次人 工手工擦拭。
二、锡波参数管控
b. 锡液温度:温度对焊接的影响是至关重要的,无论回流焊还 是波峰焊工艺,温度参数始终是最关键的参数之一。波峰焊锡 液温度的设定值范围在260 - 270℃,对于某些非常简单的板, 也可以设定到255℃,但不能再低,否则会产生焊接不良。一 般来讲,温度高,焊接品质会好;但因为焊接是一个在高温下 完成的过程,在焊接过程中所有参与焊接的元器件及板材都会 经受热冲击,在其内部产生热应力,如控制不好,热应力就会 导致相关材料损毁,最终结果可能是虽然焊接质量好,但板子 在后端测试不良。所以锡液温度调整必须保持一个原则:就低 不就高。如果经试验验证,在温度低的情况下也能取得好的焊 接品质,则必须将低的温度值作为标准参数,不得再继续使用 高的温度设定值。
二、 锡膏管控
锡膏是SMT表面贴装制程最重要的材料。由于锡膏特殊的化学 特性,它必须在特定的环境条件下保存和使用才能发挥其作用, 否则会严重影响焊接的品质。锡膏的主要管控要点有: a. 锡膏的保存:锡膏要密封保存在2-10℃的环境中。建议冰箱的温 度保持在5℃左右为最好。因锡膏有有效期限制,所以必须遵循 “先进先出”的原则。 b. 锡膏的解冻和搅拌:锡膏在使用前必须要进行解冻,即所谓的回 温。回温时间在4小时左右。在锡膏从冰箱取出时,必须马上记 录起始时间和标明回温结束时间。回温时间到之后,才能对此罐 锡膏进行使用。锡膏在使用前还必须要搅拌,搅拌时间在3-5分 钟。 c. 锡膏在钢网上的使用时间:在钢网上停留的锡膏,如果停留时间 会超过2小时,则必须先将锡膏回收到锡膏罐中,并拧紧盖子保 存;如锡膏在钢网上持续印刷时间超过8小时,则剩余的锡膏必 须作报废处理。
PCB制程管控及审核重点

PCB制程管控及审核重点PCB(Printed Circuit Board,印制电路板)作为电子设备的核心组件之一,其质量和性能直接影响着整个电子系统的稳定性和可靠性。
在 PCB 的生产过程中,制程管控和审核是确保产品质量的关键环节。
本文将详细探讨 PCB 制程管控及审核的重点,以帮助相关从业者更好地理解和把握这一重要领域。
一、PCB 制程管控的重要性PCB 制程管控旨在确保每个生产步骤都按照预定的规范和标准进行,从而生产出符合设计要求和质量标准的 PCB 产品。
有效的制程管控可以:1、提高产品质量:通过对各个制程环节的严格监控和控制,减少缺陷和误差的产生,提高 PCB 的成品率和可靠性。
2、降低生产成本:减少废品和返工,优化生产流程,提高生产效率,从而降低生产成本。
3、满足客户需求:确保 PCB 产品能够满足客户对性能、规格和交货期等方面的要求,提高客户满意度。
4、增强企业竞争力:优质的 PCB 产品有助于企业在市场竞争中脱颖而出,赢得更多的订单和市场份额。
二、PCB 制程管控的主要环节1、原材料管控覆铜板选择:根据 PCB 的性能要求和使用环境,选择合适的覆铜板类型(如 FR-4、铝基板等)、厚度和材质。
阻焊剂和油墨:确保阻焊剂和油墨的质量、颜色和耐腐蚀性符合要求。
化学药水:对蚀刻液、电镀液等化学药水进行定期检测和分析,保证其浓度和成分稳定。
2、内层制作图形转移:采用光刻或激光直接成像等技术,确保内层线路图形的精度和准确性。
蚀刻:控制蚀刻速度和蚀刻因子,避免过蚀或欠蚀,保证线路的线宽和间距符合设计要求。
内层检验:对内层线路进行自动光学检测(AOI)和人工目检,及时发现和修复缺陷。
3、压合层压参数:控制层压温度、压力和时间等参数,确保各层之间的结合力和平整度。
半固化片:选择合适的半固化片类型和厚度,保证 PCB 的厚度和介电性能。
压合后检验:检查压合后的 PCB 是否存在分层、气泡等缺陷。
4、钻孔钻孔参数:根据 PCB 的板厚、孔径和孔数等因素,设置合适的钻孔速度、转速和进刀量。
pcba制程介绍及管制重点

PCBA制程介绍及管制重点一、P C B A概述P C BA(P ri nt ed Ci rc u it Bo ar dA ss em bly)也称为电路板组装,是指将已经制造好的P CB(P ri nt ed Ci rc ui tB o ar d)上的元器件进行焊接和组装的过程。
PC BA广泛应用于电子设备领域,如手机、电脑、家用电器等。
本文将介绍P CBA的制程流程及管制重点。
二、P C B A制程流程2.1元器件采购和入库元器件采购是PC BA制程的第一步,这是保证后续制程成功的关键环节。
在采购前,需要根据产品的需求清单编制元器件采购清单,并选择合适的供应商。
采购回来的元器件需要进行入库,要确保元器件的品质和数量符合要求,并进行合理的存储和标识。
2.2S M T贴片S M T(Su rf ac eM ou nt T ec hn ol og y)是目前主流的表面贴装技术。
S MT 贴片是将超过80%的元器件表面贴装到PC B上,取代了传统手工焊接的方式。
S MT贴片具有高效、高质、高密度的特点,对于PC BA的制造起到了重要作用。
2.3D I P插件D I P(D u al in-l in eP a ck ag e)插件是通过插法将元器件插入P CB孔内,然后通过焊接固定的制程。
D IP插件适用于结构较大、功耗较高的元器件,如电解电容、电阻等。
DI P的插装工艺需要精确的位置和方向,操作人员需要专业技术和严格的操作流程。
2.4A O I(A u t o m ate d O p t i c a l I n sp ec t i o n)检测A O I检测是借助光学原理检测制程过程中的缺陷和错误,旨在提高制程质量和效率。
A OI检测可以检测焊盘上的缺失、偏差、短路、错位等问题,提前找到并解决潜在的制程缺陷。
2.5组装和组焊组装是将已经贴片或插件的P CB与外壳、连接线等组件进行组合的过程。
组焊则是将组装完成的P CB A与外部设备焊接连接,确保电路板与设备之间的电气连接良好。
PCB印制线路板流程及品质管理分析

PCB印制线路板流程及品质管理分析印制线路板(Printed Circuit Board,PCB)是一种用于支撑和连接电子元件的板状载体。
在现代电子产品中,PCB已成为不可或缺的基础组件。
PCB的制造过程涉及多个环节,包括设计、生产、质量检测等。
本文将对PCB印制线路板的制造流程及品质管理进行详细分析。
一、PCB印制线路板的制造流程:1.设计阶段:PCB的设计是整个制造过程的第一步。
设计师根据产品需求和电路要求制作PCB的布局图和线路图,确定板层、材料、大小等参数。
2.制板阶段:制板是将设计好的CAD图转化为实际PCB的过程。
制板主要包括以下几个步骤:选料、切割、厚化、打铜、光绘、蚀刻等。
在这一阶段,需要严格控制每个步骤的参数,确保PCB的质量。
3.成品检测:制造完成后,需要对成品进行检测。
主要包括外观检测、线路连通性测试、电性能测量等。
通过检测可以验证PCB的质量和可靠性。
4.表面处理:PCB的表面处理是为了增强其导电性和耐腐蚀性。
常见的表面处理方式有喷锡、化学沉铜、镍金等。
5.成品包装:最后一步是将成品包装好,以便运输和使用。
包装要求防潮、防静电等,确保成品不受外界环境影响。
二、PCB印制线路板的品质管理:1.设计质量管理:设计阶段的合理性和准确性对PCB的品质至关重要。
设计人员应根据产品需求和技术规范进行设计,确保布局合理、线路通畅,避免设计缺陷。
2.制造质量管理:在制造过程中,需要对每个环节进行严格控制,确保各项参数符合要求。
生产现场要实施流程控制、质量管理体系等措施,提高生产效率和品质稳定性。
3.检测质量管理:成品检测是PCB品质管理的最后一道关口。
提前制定检测方案和标准,建立稳定可靠的测试设备和方法,确保检测结果的准确性和可靠性。
4.表面处理质量管理:表面处理是PCB使用寿命和可靠性的重要保障。
要选择合适的材料和工艺,严格控制处理参数,避免出现处理不良或变质现象。
5.包装质量管理:成品包装对PCB的保护和运输起着重要作用。
pcb 厂内制程审核计划

pcb 厂内制程审核计划
审核目标是啥?
咱们要看看PCB制造过程是不是都按照标准和质量要求来的,
能不能提高生产效率,减少不良品,还有优化成本控制。
要审核哪些地方?
审核的范围嘛,就是整个PCB生产的流程,包括买原材料、生
产线上的操作、品质检测,还有仓储管理这些。
重点看啥?
重点要看几个方面,首先,原材料得没问题,不能有过期或者
损坏的;其次,生产线操作得规范,设备得正常运行,工艺参数也
得准确;还有,品质检测得靠谱,不良品得及时发现和处理;最后,还得看看生产环境是否整洁,安全措施是不是做到位了,员工操作
是否规范。
怎么审核呢?
现场看看、文件审查、跟员工聊聊,这些都得用上,才能全面了解制程管理的真实情况。
多久审核一次?
每个季度都得全面审核一次,这样才能保证制程管理持续优化和改进。
谁来审核?
审核团队得由品质管理、生产技术、仓储管理这些部门的人组成,这样才能保证审核的专业性和权威性。
审核完怎么办?
审核结束后,得赶紧整理审核报告,把审核过程和发现的问题都记录下来,还得提出改进措施和建议。
后续跟踪怎么做?
对于审核中发现的问题,得进行跟踪,确保改进措施得到有效执行,这样制程管理水平才能持续优化。
- 1、下载文档前请自行甄别文档内容的完整性,平台不提供额外的编辑、内容补充、找答案等附加服务。
- 2、"仅部分预览"的文档,不可在线预览部分如存在完整性等问题,可反馈申请退款(可完整预览的文档不适用该条件!)。
- 3、如文档侵犯您的权益,请联系客服反馈,我们会尽快为您处理(人工客服工作时间:9:00-18:30)。
乾膜 基板 乾膜
裁切
前處理
覆膜
曝光
顯影
內層
AOI
清洗
去膜
蝕刻
流程 蝕刻
作用
內層線路 形成
制程管控
A.蝕刻液酸度及比重 B.價銅含量 C.蝕刻/水洗噴淋壓力 D.蝕刻溫度及輸送速度 E.殘銅
稽核重點
酸性/鹼性/危險品管控 藥水配槽或自動添加校驗記錄 參數是否在管制範圍
乾膜 基板 乾膜
裁切
前處理
覆膜
曝光
缺口,刮傷,凹陷等
人員認證/首件記錄 良板/不良板區分
基板
裁切
前處理
覆膜
曝光
顯影
內層
AOI
清洗
去膜
蝕刻
流程 棕化
作用
在銅面形成氧化層, 便於內層板與膠片 間之結合
制程管控
A.槽液分析 B.信賴性測試
*剝離力 *熱應力 *銅箔失重 C.刮傷,氧化,露銅
稽核重點
參數是否在管制範圍 測試記錄
基板
棕化
預疊
顯影
內層
AOI
清洗
去膜
蝕刻
流程 作用
去 膜 去除剩餘的乾膜 清 洗 去除板面殘餘藥液
制程管控
A.去膜液濃度/溫度及輸送速度 B.噴灑及水洗壓力 C.冷風車頻率及烘乾溫度 D.添加頻率及添加量 E.斷/短路,刮傷
稽核重點
藥水配槽記錄 參數是否在管制範圍
自動添加校驗記錄 重修管控
A O I 內層線路檢查
除膠渣 去除孔內膠渣
化學銅 以化學置換方式於孔 內壁形成銅導體
制程管控
A.水破試驗 B.刷痕測試
稽核重點 參數於管制範圍
A.藥液配槽校驗
重修流程
B.背光級數/孔壁粗糙度 切片檢查記錄
銅箔 膠片 基板 膠片 銅箔
電鍍
去毛頭
除膠渣
化學銅
電鍍銅
流 程 作用
電鍍銅
以電鍍方式於孔內壁 形成銅導體,達到客戶 指定面/孔銅厚度
前處理
覆膜
外層
曝光 AOI
底片
乾膜 銅箔 膠片 基板 膠片 銅箔 乾膜 底片
顯影
蝕刻
清洗
去膜
流程 作用
顯 影 去除未被曝光 之乾膜
制程管控
A.顯影液濃度及溫度 B.顯影/水洗噴淋壓力 C.顯影點及輸送速度 D.添加量及添加頻率 E.顯影不潔,曝偏
稽核重點
酸性/鹼性/危險品管控 參數是否在管制範圍 置放時間是否管制
稽核重點 測試記錄
管控方式 重修管控
前處理
覆膜
外層
曝光 AOI
乾膜
銅箔 膠片 基板 膠片 銅箔 乾膜
顯影
蝕刻
清洗
去膜
流程 作用
制程管控
稽核重點
曝 光 外層線路 影像轉移
A.無塵室管理 B.曝光能量及真空度 C.底片進出及報廢管制 D.底片版序及曝光次數管控
溫濕度,落塵量,傳遞門,人員著裝 管制記錄,重工管制 管控方式,報廢記錄 管控方式,監控記錄
A.升溫速率 B.升壓速率 C.板厚,凹陷,皺折,板翹
製作半撈,鉆孔用之 A.層間對準度
工具孔
B.尺寸漲縮
稽核重點 是否有壓合防呆設計
人員認證
棕化
壓合
預疊
壓合
銅箔 膠片 基板 膠片 銅箔
鉆靶 清洗
半撈 去毛邊
流程 半撈 去毛邊 清洗
作用 去除不規則之板邊 去除板邊銳利錂角 清除殘屑
制程管控 銑刀規格 參數設定
PCB 制程管控及稽核重點
04/12
內層
壓合
鑽孔
包裝出貨
多層板 一般製作流程
外觀檢驗
電鍍 外層 防焊
電測
成型
表面處理
文字
流程 裁切
作用
將基板裁切至 適當工作尺寸
前處理 清潔並粗糙銅箔表面, 增強油墨與之附著力
制程管控
A.調刀距離 B.磨邊及圓角清潔 C.經緯向一致 D.下製程前烘烤
A.水破試驗 B.刷痕測試
稽核重點 刀具保養及更換記錄 首件記錄/清潔記錄
測試方式/記錄
基板
裁切
前處理
覆膜
曝光
顯影
內層
AOI
清洗
去膜
蝕刻
流程 覆膜
作用 將光阻劑(乾膜) 加諸於基板表面
補充: 濕膜
制程管控
A.儲存條件,FIFO及保存期限 B.氣泡,皺折,髒點
A.儲存條件,FIFO及保存期限 B.油墨粘度及膜厚 C.塗佈轉速及IR溫度 D.油墨刮傷露銅
稽核重點
棕化
壓合
預疊
壓合
銅箔 膠片 基板 膠片 銅箔
鉆靶 清洗
半撈 去毛邊
流程 鑽孔
作用 通孔製作
制程管控
A.鑽針管控 B.機臺參數設定 C.孔數,孔偏,孔壁粗糙
稽核重點
報廢管制及研磨記錄 斷針檢查及處理程序 首件檢查記錄
銅箔 膠片 基板 膠片 銅箔
鑽孔
鑽孔
流程 去毛頭
作用
去除鉆孔於板面產生 之多餘殘屑
前處理
覆膜
外層
曝光 AOI
乾膜 銅箔 膠片 基板 膠片 銅箔 乾膜
顯影
蝕刻
清洗
去膜
流程 蝕刻
作用
外層線路 形成
制程管控
A.蝕刻液酸度及比重 B.價銅含量 C.蝕刻/水洗噴淋壓力 D.蝕刻溫度及輸送速度 E.殘銅
稽核重點
酸性/鹼性/危險品管控 藥水配槽或自動添加校驗記錄 參數是否在管制範圍
前處理
覆膜
稽核重點 管控方式 重修管控
管控方式 測試記錄
重修管控
乾膜 基板 乾膜
裁切Hale Waihona Puke 前處理覆膜曝光
顯影
內層
AOI
清洗
去膜
蝕刻
流程 作用
制程管控
稽核重點
曝 光 內層線路 影像轉移
A.無塵室管理 B.曝光能量及真空度 C.底片進出及報廢管制 D.底片版序及曝光次數管控
溫濕度,落塵量,傳遞門,人員著裝 管制記錄,重工管制 管控方式,報廢記錄 管控方式,監控記錄
制程管控
稽核重點
A.面/孔銅厚度 B.手紋,刮傷,銅瘤 C.哈氏槽分析
重修流程 測試記錄
銅箔 膠片 基板 膠片 銅箔
電鍍
去毛頭
除膠渣
化學銅
電鍍銅
流程 作用
制程管控
前處理 清除表面異物
A.水破試驗 B.刷痕測試
覆 膜 將光阻劑(乾膜) A.儲存條件,FIFO及保存期限 加諸於基板表面 B.氣泡,皺折,髒點
外層
曝光 AOI
乾膜 銅箔 膠片 基板 膠片 銅箔 乾膜
顯影
蝕刻
清洗
去膜
流程 作用
制程管控
去 膜 去除剩餘的乾膜 清 洗 去除板面殘餘藥液
補充: 負片流程 黑孔 A O I 外層線路檢查
A.去膜液濃度/溫度及輸送速度 B.噴灑及水洗壓力 C.冷風車頻率及烘乾溫度 D. 添加頻率及添加量 E.斷/短路,刮傷
壓合
鉆靶
半撈
壓合
清洗
去毛邊
流程 預疊
作用
依設計將內層板 與膠片堆疊
制程管控
稽核重點
A.堆疊次序 B.膠片數量 C.裁切刀距調整 D.貼膠/鉚合作業
PP儲存條件,FIFO及保存期限 首件檢查記錄
膠片 基板 膠片
棕化
預疊
壓合
鉆靶
半撈
壓合
清洗
去毛邊
流程 壓合
銑靶
作用
制程管控
將預疊好之內層板, 膠片與銅箔壓合
裁切
前處理
覆膜
內層
AOI
清洗
底片 乾膜 基板 乾膜 底片
曝光 去膜
顯影 蝕刻
流程 作用
制程管控
顯 影 去除未被曝光 之乾膜
A.顯影液濃度及溫度 B.顯影/水洗噴淋壓力 C.顯影點及輸送速度 D.添加量及添加頻率 E.顯影不潔,曝偏
稽核重點
酸性/鹼性/危險品管控 參數是否在管制範圍 置放時間是否管制