2013干气制氢课件
制氢技术讲课

用中变气/原料气换热器代替原料加热炉,另设开工炉,正 常操作时用中变气预热原料,开工炉仅在开工时预硫化催化 剂和在线更换脱硫剂时用,这样做不仅降低了炉子规模,合 理利用中变气余热,减少用于加热原料的全部燃料气用量, 并减少了全装置的副产蒸汽量,同时由于由开工炉,脱硫催 化剂可以在线更换,从而缩小脱硫反应器的尺寸和脱硫剂的 用量。
C+O2→CO2 多数的煤与水发生反应,生成CO和H2(水煤气):
C+H2O→CO+H2 再通过变换反应将生成的CO更多转换成氢气:
CO+H2O→CO2+H2 上述变换气经过提纯即可得到较纯净的氢气。 这种工艺路线的原料价格比较便宜,但是工艺流程复杂, 生产条件苛刻,产氢率低,投资大,危险程度高,能耗高, 因而在制氢生产中很少采用,但在将来石油资源枯竭的时 候,它可以作为一种炼厂气制氢的替代方案使用。
制氢装置工艺流程简述
本装置是120万吨/年加氢裂化装置的配套装 置,由中石化北京设计院设计。装置以加氢干 气、加氢低分气和油田气为主要原料,采用烃 类水蒸气转化法造气,PSA法净化提纯的工艺 路 线 制 取 氢 气 , 设 计 产 氢 规 模 为 年 产 99.9% (V)的工业氢气2.9万吨,年开工8000小时, 相当于每小时产纯氢40000标准立方米。同时 本装置还担负着20000标准立方米的重整氢与 加氢低分气的提浓任务,所产的氢气中,每年 有28708吨供120万吨加氢裂化装置使用,其 余部分送入炼油厂氢气管网。
对本装置而言,有两种脱硫的流程:
溶剂脱硫部分所用的脱硫物质为甲基二乙醇胺(MDEA浓度25% wt)溶液,反应式如下:
OCH2CH2N(CH3)CH2CH2OH+H2S←→[HOCH2CH2NH+(CH3)CH2CH2OH]HS-
《化石燃料制氢》PPT课件

2)煤气化技术产H2。 煤气化产气组份:
H2 34.4% CO 45.3%
CO2 15.8% CH4 1.9% 气化炉
温度:1371°C
压力:27.6bar
煤制氢技术及努力方向
• 当前技术采用煤的部分氧化、气化技术; • 混合煤、氧、水蒸气产生混合气,用成熟的水煤气转化反应器
产生更多的H2, 同时把CO转化为CO2;用PSA技术分离H2。
2.1.2 天然气部分氧化重整制氢
• 变强吸热为温和放热,因而具有 能耗低的显著特点,且空速高, 设备小,投资低。
• 由于甲烷部分氧化反应可实现自 然反应,不需要外界提供额外热 量,因此设备简化,投资成本低。
• 但对于运行要求高,需大量纯氧。
• 当氧含量10~12%,5~30MPa下主 要生成甲醇、甲醛和甲酸;
• 我国生成的H2有80%以上用于合成氨 工业,而合成氨以煤为主,无烟煤、 焦炭占62~65%,轻油和重油占12~ 16%,天然气占18~23%。
• 虽然制氢消耗有限的化石燃料储量, 但在先进、成熟的制氢方法出现之前, 在未来几十年仍然扮演重要角色。
合成气制氢装置介绍 ppt课件

组分
H2
N2
AR
H2O
CO+CO2
温度
压力
组成,mol%
99.9
0.052
0.035
<50ppm
≤20ppm
40℃
1.75Mpa
2)、操作弹性
40~105%。
3)、年操作时数
8400小时,连续运行时间为3年。
PPT课件
6
一、合成气制氢项目概述 2、制氢装置的规模、组成
PPT课件
7
一、合成气制氢项目概述 2、制氢装置的规模、组成
从化学原理来说,UCARSOLTM HS配方溶剂是基于叔胺和抑制剂的胺液。因此,基于UCARSOLTM HS溶剂的选择性脱硫系统,CO2的共吸收只能通过CO2水解形成碳酸氢根的形式被吸收。这样 UCARSOLTM HS溶剂再生时能耗相对较低。相反,基于普通胺液(MEA, DEA, DIPA,活化MDEA)的脱硫脱 碳工艺,溶剂可直接与CO2反应,形成稳定的碳酸盐,导致再生能耗较高。
PPT课件
23
二、生产原理、工艺流程、控制指标
2、脱硫单元
MDEA脱硫流程简述 MDEA脱硫有合成气脱硫和H2S富集两部分组成,流程描述如下: H2S富集部分 来自合成气脱硫部分的酸性气浓度为了满足下游装置的接收要求,需要进一步的富集。其先进 入H2S富集塔的底部,在此,其与贫液进行逆流传质, H2S基本被脱除,H2S富集塔顶部的CO2尾气 经气液分离后送往生物法尾气脱硫单元进一步脱除尾气中的H2S,经脱硫后的尾气满足环保要求后 送往锅炉烟囱放空。H2S在H2S富集塔底部进一步富集,随富液带出,经贫富液换热器后,被预热升 温,送至再生塔塔顶,再生塔底部设置有再沸器,为再生过程提供热源。再生塔塔釜再生的贫液送 至贫富液换热器后,用贫液泵加压后,至空冷器和水冷器换热冷却后,去H2S富集塔顶部作为吸收 液使用。H2S富集塔顶部产生的H2S浓度满足要求的酸性气送往界外硫回收装置。
制氢操作培训课件
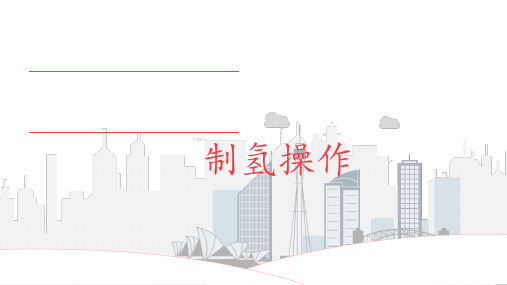
脱硫单元
• 系统循环量的控制 • 出系统粗氢气产品质量的控制 • 系统腐蚀的控制 • 胺液的降解 • 消泡剂的添加 • 气化脱硫与MDEA脱硫对比
脱硫单元
• (1)系统循环量的控制
•
富液循环量要<543m3/h,流速过快容易导致腐蚀
•
变换装置出口至T4201该段管线伴热不用投用
尽可能低,减少饱和水夹带以及灰尘夹带。(带水意味着带灰)
待蒸汽超过临界值后随着系统温度的升高压力会逐渐稳定。
• (2)进料温度控制
•
主要从系统物料平衡考虑
• (3)出料温度的监控
•
T4103出口温度
磷酸盐加药装置操作
• 低于30cm配置药剂,最终加水量控制在100cm。 • 搅拌器待药剂完全溶解后停运。 • 加药量根据系统补水负荷、排污量、磷酸根含量、PH及时调整。
引申:
系统压力的控制
1、系统气量 2、变换反应的好坏 3、脱硫循环量、溶剂温度的控 制、再生效果的好坏。 4、VPSA/PSA的有效吸附。 5、压缩机的运行情况。
变换催化剂的维护
• 4催化剂毒物
•
砷含量(煤中含有砷元素)
•
砷的主要来源为原料煤,气化装置使用的烟煤中砷的含量一般为
0.75~176ppm。工艺气中的砷含量为煤中所含砷的14%~22%,其余存在于粗渣
合物发生了分子链的无规则断裂、侧基和低分子的消除反应,致使聚合度
和相对分子质量下降。
•
①温度高降解
•
128℃,设计采用150℃ 蒸汽,待压缩单元正常运行后采用的是200℃
蒸汽。温度的控制要严格执行工艺指标。
•
②与氧气接触降解
脱硫单元
• (5) 消泡剂的添加 • 在胺液运行过程中加入消泡剂应慎重考虑。必须在确认溶剂已经发泡后
干气制氢

干气制氢1.工艺原理以催化干气为原料(轻石脑油为临时备用原料),采用加氢技术将原料中的烯烃饱和为烷烃,并将有机硫、有机氯等杂质转化为无机硫、无机氯,再通过脱氯、脱硫反应器脱除HCl和H2S,使精制后的气体硫含量小于0.5ppm,氯含量小于1ppm,烯烃含量小于0.1%(v)。
精制后的原料采用水蒸汽转化工艺将烃类转化为H2、CO、CO2,转化气中的CO采用中温变换,使其反应生成H2和CO2,变换气中的残余CO、CO2和CH4等杂质,采用变压吸附(PSA)的净化技术进行清除,从而得到纯度为99.9%(v)、CO+CO2<20ppm的产品氢气1.1干气(轻烃)蒸汽转化法制氢过程分为原料的净化,烃蒸汽转化,CO中温变换等工艺。
1.1.1原料净化时原料气在一定的温度、氢气压力和空速条件下,借助加氢催化剂作用,把原料气中硫化物、氯化物脱出,使原料气含硫流量降至0.2ppm,含氯量降直1ppm,以保护好后续催化剂的正常运行。
1.1.2当烃类蒸汽转化的精制原料气在一定压力、温度、空速、水碳比和催化剂作用下,烃和蒸汽进行反应,转化成气体氢和一氧化碳,同时伴生CO2和少量的残余CH4。
1.1.3转化气进行中温变换在一定的温、压力、空速、水气比和催化剂作用下,将CO与水反应生成氢气和CO2。
2.制氢的化学反应机理2.1原料烃中的硫化物以多种形态存在,一般分为无机硫化物和有机硫化物,有机硫化物不能在氧化锌脱硫剂上直接反应被脱除,必须经加氢生成无机硫化物方可被氧化锌脱硫及吸附脱除,有机硫化物在原料中一般由硫醇、硫醚、二硫化物和环状硫化物等,原料气中的硫化物绝大部分是有机硫化物。
加氢过程同样是有机氯转变为无机氯,采用高活性的金属氧化物为活性组分,脱氯剂与氯化氢反应,被固定载体上,达到脱出氯化物目的。
硫醇加氢:R-SH+H2=RH+H2S硫醚加氢:R-S-R’+H2=RH+R’H+H2S噻吩加氢:C4H4S+4H4=C4H10+H2S二硫化碳加氢:CS2+H2=CH4+H2S氧化锌脱硫:H2S+ZnS+H2O2.2烃类的蒸汽转化是将烃类与蒸汽转化为H2和CO少量残余CH4CH4+H2O=CO+H2CO+H2O=CO2+H22.3 CO中温变换是将转化气中的CO与水蒸气继续反应生成CO2和氢气。
制氢车间HAZOP培训课件
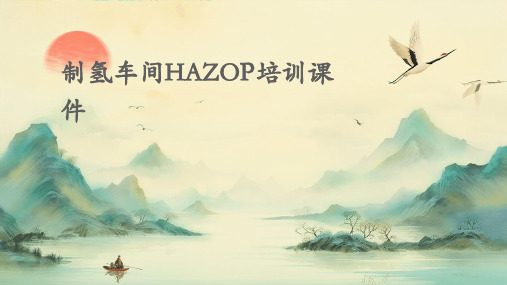
执行分析
按照分析计划,对制氢车间的工 艺流程进行逐一分析,使用引导 词系统对每个节点进行偏差识别 和风险评估。
风险矩阵与安全措施评估
根据分析结果,制定风险矩阵, 对每个风险进行等级划分,评估 现有安全措施的有效性,并提出 相应的改进建议。
引导词系统与使用
定义引导词 根据制氢车间的工艺特点和操作 条件,选择合适的引导词,如流 量、压力、温度、液位等,用于 描述工艺参数的偏差。
培训安排
为期一周的集中培训,每天6小时,共 计30小时。培训对象为制氢车间的操 作员、工艺工程师和技术人员。
培训效果评估与改进
评估方式
通过理论考试、小组讨论和个人报告等形式对培训效果进行评估。
改进措施
根据评估结果,对培训内容和方式进行改进,以提高培训效果和质量。同时, 定期组织复训和更新培训课件,以适应制氢车间工艺和安全要求的变化。
制氢车间HAZOP培训课 件
• HAZOP简介 • HAZOP基本概念 • HAZOP分析方法 • HAZOP分析实践 • HAZOP培训与提升 • HAZOP应用与发展趋势
01
HAZOP简介
HAZOP的定义
是一种基于风险的评估方法,用于识别和评估工艺系统中的潜在危险和操 作问题。
通过分析工艺流程图和操作规程,HAZOP研究确定可能发生的偏离,并 评估这些偏离对人员、环境和设备的影响。
分析实施与记录
成立分析小组
组建具备HAZOP分析经验和制氢 车间知识的专业团队。
实施分析
按照HAZOP分析的步骤和方法, 对制氢车间的工艺流程、设备、 操作等进行全面分析,识别潜在 的危险和操作偏差。
记录分析结果
详细记录每个偏差及其潜在的风 险和后果,为后续评估和报告编 写提供依据。
水碳比的计算(干气制氢)

干气制氢水碳比的计算进转化炉水蒸汽和脱硫后原料气流量进行水/ 碳比的比值控制。
在正常生产情况下,控制好水蒸汽与原料气的水/ 碳比是转化操作的关键。
正常比值为3.5:1,水/ 碳比过高,不仅浪费水蒸汽,而且增加转化炉的热负荷;水/ 碳比过低,会引起催化剂积碳,使催化剂失活,甚至造成生产事故。
从安全生产与节能两方面综合考虑,工艺生产过程稳定时,要求水/ 碳比操作在低限;原料气增量时,先增水蒸汽后增原料气;减量时,先减原料气后减水蒸汽。
知道干气组成,怎们计算水碳比?公式:水/碳=水蒸气流量(Nm3h )/碳流量(Nm3h)水蒸气的流量如以kg/h表示时,则乘以22.4/18转化成Nm3/h,再带入公式;干气中碳流量以干起流量(Nm3/h )乘以干气平均分子式的碳原子个数,结果带入公式;油中碳流量=进料量kg/h X油平均分子式碳原子个数X 22.4油的平均相对分子质量,结果带入公式。
举例说明干气H2O/C 计算方式干气组分:H2 15% CH4 71% C2H6 10% C2H4 2% C3H8 2% C4H8 3总% 碳原=0.71+2*0.1+2*0.02+3*0.02+4*0.03 =0.71+0.2+0.04+0.06+0.12 =1.13 干气流量3600NM3/H 碳流量=3600*1.13=4068 配汽量12000KG/H=12000*22.4 4068*18)=3.67mol/h )/ mol/h 3~4.5的是表观水碳比,如果要计算实际水碳比,则要用{ (mol/h )+转化炉内生成的水的流量(mol/h ))/ 总mol/h )mol/h )=总碳元素mol/mol * (mol/h),mol/h )=水蒸气流量(kg/h )*1000/18H2O 与C 的mol 比,干气的单位是分可以计算出总碳元素的含量(mol/mol ),然后用,mol Nm3/H ,水蒸汽的单位是T/H0 122.4升, 1Nm3mol 量=1000/22.41Nm3 C mol =1000/22.4C mol 含摩尔量=质量/摩尔质量”量是18g/mol ,1吨水的摩尔量=1000000/18= 1000 22.4 / 18 / 干气中C 的mol= 1244.4 ( C 的molC 的mol。
制氢工艺技术PPT课件
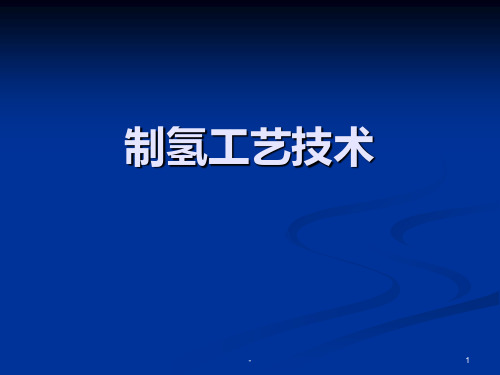
-
17
-
15
低变催化剂
低变催化剂主要组分为Cu0,添加Zn0、Al203,、Cr203等。 催化剂毒物主要是硫、氯,水、氨也有影响。硫主要来自 原料气,它会与催化剂活性表面的铜晶粒发生化学吸附和 反应而影响活性。研究表明,氯比硫的毒害严重,氯离子 来自蒸汽和原料气,对低变催化剂的毒害是与Cu、Zn0生 成了Cu7Cl4(OH)10(H2O)、ZnCl2·4Zn(OH)2等组成的低熔 点而有挥发性的表面化合物,使Zn0失去间隔体作用,铜 微晶迅速长大,破坏了催化剂的结构,使活性大大下降。 加之生成的氯化物易溶于水,在湿气条件下,氯化物会沿 床层迁移,毒害更多催化剂。凝聚水和氨可以使催化剂中 铜微晶生成铜氨络合物,使催化剂中毒和侵蚀
-
14பைடு நூலகம்
中温变换催化剂
中变催化剂化学组分为Fe2O3、Cr203、K2O, 使用时被还原为有活性的Fe3O4,催化剂
毒物为硫、磷、硅等。但中变催化剂受毒 物影响较小,如原料气硫含量达到0.1%时 才使Fe3O4转变为FeS,使活性稍有下降, 为新剂的70%~80%。工艺蒸汽中含杂质
过多时会与原料气组分反应,使催化剂结 皮而降低活性
-
5
氢气的化学性质
氢能与很多物质进行化学反应,在进行化学反 应形成化合物时其价键具有特征。氢原子失去 其ls电子就成为H+离子,实际上就是氢原子核 或质子。质子的半径比氢原子的半径要小许多 倍,使质子有相对很强的正电场。因此它总是 同别的原子或分子结合在一起形成新的物质。 如加氢反应就是将氢气加到各种化合物上的反 应。如甲烷化反应:
-
16
甲烷化催化剂
催化剂的主要化学组分为Ni0、Al203,使用时还原为金 属镍。主要毒物为硫、砷、钒、碳酸钾和羰基镍等。对 于甲烷化催化剂,硫是永久性毒物,这是因为操作温度 较低,活性镍一旦与硫化氢生成Ni2S3后,即使除去H2S, 也无法被氢气再还原为活性状态。研究表明,甲烷化催 化剂中吸硫达到0.15%~0.2%时活性丧失50%,若达到 0.5%则活性全部丧失。希望进甲烷化催化剂的原料气中 硫含量越低越好,一般要小于0.1ppm。甲烷化工序设在 脱碳之后,各种脱碳液带入均会造成不同的毒害。砷是 永久性毒物,催化剂中砷含量达到0.1%时便严重失活。 甲烷化催化剂在150℃以下操作时,活性镍与一氧化碳 会反应生成羰基镍Ni(CO)4,这是对人剧毒的挥发物, 还造成催化剂中镍的流失,严重降低活性。因此,在床 层降温至150℃以下时不能再通工艺气,应改用氮、氢 气氛
制氢系统ppt课件
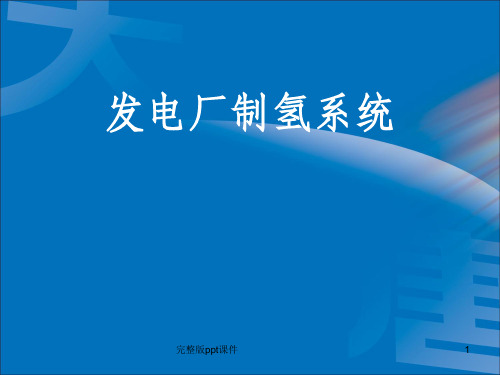
• 放在干燥器后面,滤去气体中所含的微尘。
完整版ppt课件
23
氢气干燥装置使用注意事项
• 1.干燥装置间严禁明火,操作人员严禁穿带钉的鞋入内。 • 2 .应注意观察氢气的含氧量应≤0.5%,若≥0.5%应停机。 • 3. 再生进气温度不得超过 350℃,再生加热终止温度不得超过 300℃。 • 4 .当没有氢气流过加热器时,禁止长时间开启加热器(不超过 15s),
• 捕滴器一般装在洗涤器的上顶部或是分离器(如卧式分离器)的气
体出口处,用于分离氢(氧)气中夹带的直径为 0 . 3 µm以上微液滴。
它是在一定直径的圆筒内装填一定规格和数量的不锈钢捕滴网。当进
入捕滴器的气体流速控制在一定范围内时,气体中夹带的液滴撞到丝
网并附在其上,水滴聚集到一定程度,在重力作用下沿丝网下流,达
• 3、故障及排除方法:
• 碱液循环量不断下降,槽体温度升高,或者分离器冷却正常而槽温 又难以下降,这说明过滤器的滤网堵塞,应取出滤芯进行清洗。
• 过滤器的清洗在停车状态下进行,清洗方法是:关闭过滤器进出口 截止阀,打开过滤器顶部排气阀,泄掉过滤器内压力。拆开过滤器法
兰螺拴,取下法兰盖,卸下滤筒进行清洗。
2H2O → 2H2↑+ O2↑
完整版ppt课件
3
工艺流程
完整版ppt课件
4
气液处理器典型流程图
完整版ppt课件
5
系统组成
2.1电解槽:
1)、单极性电解槽:
单极电解槽是由外部并联若干个电解槽组成的。而单元电解槽由若干 个彼此交替的、彼此平行的阳极版和阴极版组成。对于一个电极而言只 能做阳极或阴极。单极性电解槽安装、维修简便,效率低,体积大。
《制氢技术简介》PPT课件

3. 水分解制氢
利用光化学、热化学和电化学方法制氢。然而,太阳能的收集、 高品质热能和电能的产生方法,都是首先要解决的问题。
全球年产氢: 5000亿Nm3 化石燃料制氢 占96%
合成氨:50% 石油精练:37% 甲醇合成:8%
五、制氢技术简介
1、化石燃料制氢 (1) 甲烷重整(Steam Methane (2) 天然气热解制氢
2、光电转换
Fuels CO2
O2
H2
e
a) 光伏电池
Sugar
b) 光电化学电池
c) 染料敏化光电化学电
H 2O
池
O2
sc
M
H2O
3、光-化学能转换
Photosynthesis Semiconductor/Liquid Junctions
太阳能 + 水 = 氢?
三、氢能经济的缘起
氢能经济的设想
Chrysler Natrium 车(2001)
2、电解水制氢 0.401V
负极: 2H2O + 2e 2OH- + H2 φ =- 理论分解电压10.2.832V8,V每1Kg氢电耗为 32.9 KWh 。实际为~
46.8KWh。
(1) 碱性水溶液电解
(2) 质子膜电解水发生器
2OH- H2O+ ½O2+2e
2H2O+2e 2OH- + H2
五、制氢技术简介
4、光催化制氢体系
半导体光 催化制氢
Z-型体系 光催化法
悬浮体系 光催化法
光电化学 体系制氢
M.Gratzel, et al, Nature, 1991, 353: 737; Nature,et al, Science, et al., Nature, 2001, 414, 625.
- 1、下载文档前请自行甄别文档内容的完整性,平台不提供额外的编辑、内容补充、找答案等附加服务。
- 2、"仅部分预览"的文档,不可在线预览部分如存在完整性等问题,可反馈申请退款(可完整预览的文档不适用该条件!)。
- 3、如文档侵犯您的权益,请联系客服反馈,我们会尽快为您处理(人工客服工作时间:9:00-18:30)。
5
制氢的工艺原理
烃类蒸汽转化制氢过程分为转化和变换两个阶段。
转化:本装置采用烃-水蒸汽转化法生产工业氢。转化是整个制氢 的核心部分。 转化的实质是轻质烃类按一定的比例与水蒸汽混合后,在较高 温度条件下,在装有转化催化剂的转化炉管中发生反应,使烃类转 化成氢气及一氧化碳和二氧化碳,转化反应是一种强吸热反应。 CH4+H2O=CO+3H2 吸热 CH4+2H2O=CO2+4H2 吸热 CO+ H2O= CO2+H2 放热 变换:转化气中除了目的产物氢气外,还有大量的副产物一氧化碳 、二氧化碳及少量未转化完的甲烷。转化气在一定的工艺条件下及 变换催化剂的作用下,其一氧化碳将与转化气中的过剩水蒸汽发生 如下变换反应: CO + H2O = CO2 + H2 变换后的结果是一来提高了产氢率,二来将难以从转化气中分 离的一氧化碳气体转变成了较易脱除的二氧化碳。
焦化干气制氢工艺流程
中温变换部分 由转化气蒸汽发生器(E1001)来的360-380℃转化气 进入中温变换反应器,在催化剂的作用下发生变换 反应,将变换气中CO降至3%左右。中变气经锅炉给 水第二预热器预热锅炉给水,锅炉给水第一预热器 预热锅炉给水,除盐水预热器预热除盐水回收大部 分预热后,在经中变器水冷器降温至40℃,并经分 水后进入PSA部分。
焦化干气制氢工艺流程
脱硫部分 进入脱硫部分的原料气,进入加氢反应器(R1001),先在 加氢催化剂的作用下,发生烯烃饱和反应同时发生有机硫 转化反应和有机氯的转化反应,使有机硫转化为无机硫, 有机氯转化为无机氯被脱除。然后在进入氧化锌脱硫反应 器(R1002A/B),在此氧化锌与硫化氢发生脱硫反应,脱除 原料中的硫,精制后的气体硫含量小于0.5PPm。
6
原料及产品
原料——焦化干气、除氧水 产品——氢气
7
焦化干气制氢工艺流程
制氢工艺过程可分为如下几个步骤: 钴-钼加氢转化脱有机硫; 脱氯; 氧化锌脱无机硫; 烃类——水蒸汽转化; 一氧化碳变换; PSA提纯。
焦化干气制氢工艺流程
9
焦化干气制氢工艺流程
原料气压缩部分 来自装置外的焦化干气进入原料油缓冲罐(V1001), 经原料气压缩机(C1001)升压后进入原料预热炉 (F1001),预热至300℃进入脱硫部分。本装置的备 用原料为来自装置外的石脑轻油,进入原料缓冲罐 (V1009),经原料泵升压后与装置外来的循环氢混合 进料原料预热炉(F1001),回收及产汽系统 1.除盐水除氧系统 自装置外来的除盐水经调节阀调节后经除盐水预 热器(E1004)预热至105℃左右,进入除氧器用蒸汽的 流量来控制除氧器的压力。除氧水经过锅炉给水泵 (P1001/ABCD)升压后送至中压产汽系统。 2.中压产汽系统 来自中压锅炉给水泵P1001/ABCD的除氧水经过锅炉给 水第一预热器E1003,锅炉给水第二预热器E1002预热 至饱和温度后进入中压气水分离器(V1005)中,饱和水 通过自然循环方式进入转化炉对流段的蒸发段及转化 蒸汽发生器(E1001)发生饱和蒸汽。该过热蒸汽一部分 供造汽系统自用,其余减压至1.0Mpa送出装置至 1.0Mpa蒸汽管网。
11
焦化干气制氢工艺流程
转化部分 精制后的原料气在进入转化炉(F1002)之前,按一定 的水碳比与3.5Mpa的水蒸气混合,在进转化炉对流段 (原料预热段)预热到500℃,由上集合管进入转化 炉辐射段。转化炉管内装有催化剂,在催化剂的作用 下,原料气与水蒸气发生复杂的转化反应,整个反应 过程表现为强吸热过程,反应所需热量由转化炉燃烧 气提供。出转化炉的高温转化气经转化蒸汽发生器发 生中压蒸汽后,温度降至360-380℃进入中温度变换 部分.
焦化干气制氢工艺流程
PSA部分 来自中温变换部分的中变气压力2.45Mpa温度40℃,进 入界区后自塔底进入吸附塔T2001A ~ H中正处于工况 塔(始终同时有两台)在其中多种吸附剂的一次选自吸 附下,一次性除去氢以外的几乎所有杂质,获得纯度 大于99.9%的氢气,经压力调节系统稳压后出界区。 当吸附剂吸附饱和后,通过程控阀切换至其他吸附塔 ,吸附饱和的塔则转入再生过程。在再生过程中,吸 附塔首先经过连续四次均压,降压尽量回收塔内死空 间的氢气,然后通过顺放步序,将剩余的大部分氢气 放入顺放气罐,(用作以后冲洗步序的冲洗气源), 在通过逆放和冲洗两个步序使被吸附杂质解析出来, 逆放解析气进入解析罐(V2002),冲洗气进入解析罐 (V2003),然后经调节阀混合稳后送往造气工段用作燃 料气。
焦化干气装置介绍
侯增敏
2013年9月
1
海科公司焦化干气制氢装置概况
2005年由华西石化设计院设计装置建设 规模为年产3000m3n/焦化干气制氢装置。 2009年更换转化催化剂一次。
2012年更换转化催化剂一次。
2
制 氢 转 化 炉
3
焦化干气制氢装置
内容安排
1、制氢的工艺原理
2、原料及产品
3、制氢工艺流程
4
制氢的工艺原理
轻烃蒸汽转化法制氢过程分为原料的净化,烃蒸汽转 化,CO中温度变换等工艺。 原料气在一定的温度、氢气压力和空速条件下,借助 加氢催化剂作用,把原料气中硫化物、氯化物脱除, 使原料气含硫量降至0.5PPm,含氯量降至1PPm,以保 护好后续催化剂的正常运行。 烃类蒸汽转化的精制原料气在一定压力、温度、空速 、水碳比和催化剂作用下,烃和蒸汽进行反应,转化 成气体氢和一氧化碳,同时伴生CO2和少量的残余CH4. 转化气进行中温变换在一定的温度、压力、空速、水 气比和催化剂作用下,将CO与水反应生成氢气和CO2.