Nm干气制氢
炼厂干气制甲醇技术简介
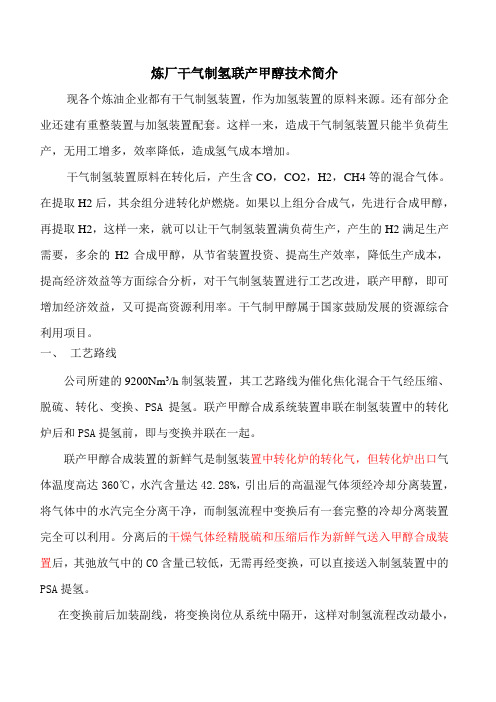
炼厂干气制氢联产甲醇技术简介现各个炼油企业都有干气制氢装置,作为加氢装置的原料来源。
还有部分企业还建有重整装置与加氢装置配套。
这样一来,造成干气制氢装置只能半负荷生产,无用工增多,效率降低,造成氢气成本增加。
干气制氢装置原料在转化后,产生含CO,CO2,H2,CH4等的混合气体。
在提取H2后,其余组分进转化炉燃烧。
如果以上组分合成气,先进行合成甲醇,再提取H2,这样一来,就可以让干气制氢装置满负荷生产,产生的H2满足生产需要,多余的H2合成甲醇,从节省装置投资、提高生产效率,降低生产成本,提高经济效益等方面综合分析,对干气制氢装置进行工艺改进,联产甲醇,即可增加经济效益,又可提高资源利用率。
干气制甲醇属于国家鼓励发展的资源综合利用项目。
一、工艺路线公司所建的9200Nm3/h制氢装置,其工艺路线为催化焦化混合干气经压缩、脱硫、转化、变换、PSA提氢。
联产甲醇合成系统装置串联在制氢装置中的转化炉后和PSA提氢前,即与变换并联在一起。
联产甲醇合成装置的新鲜气是制氢装置中转化炉的转化气,但转化炉出口气体温度高达360℃,水汽含量达42.28%,引出后的高温湿气体须经冷却分离装置,将气体中的水汽完全分离干净,而制氢流程中变换后有一套完整的冷却分离装置完全可以利用。
分离后的干燥气体经精脱硫和压缩后作为新鲜气送入甲醇合成装置后,其弛放气中的CO含量已较低,无需再经变换,可以直接送入制氢装置中的PSA提氢。
在变换前后加装副线,将变换岗位从系统中隔开,这样对制氢流程改动最小,且能充分利用现有设备,另外一旦氢气需求量增大,甲醇合成装置弛放气量无法满足要求时,可以很方便地将变换岗位并入系统恢复原制氢流程。
原制氢装置工艺流程与制氢装置联产甲醇新工艺路线流程方框图比较如下:二、甲醇生产方案2.1路线原理因汽、柴油加氢装置需要足够的氢气,因此联产甲醇方案是以制氢装置生产原料氢为主,联醇装置生产甲醇产品为辅的原则。
即在保证加氢装置所需要的氢气量的前提下,尽可能多生产甲醇。
炼厂干气制氢工艺流程介绍

干气制氢工艺流程(一)造气单元1、进料系统来自装置外的焦化干气进入原料气缓冲罐,经原料气压缩机压缩至3.2MPa(G)后进入原料气脱硫部分。
2、脱硫部分进入脱硫部分的原料气经原料气-中变气换热器或开工加热炉(开工时用)升温到230℃左右进入加氢反应器,在其中原料中的不饱和烃通过加氢转化为饱和烃类,床层温度升至380℃左右,此外通过加氢反应,原料中的有机硫转化为无机硫,然后进入氧化锌脱硫反应器脱除硫化氢和氯化氢。
经过精制后的气体总硫含量小于0.5PPm,氯化氢含量小于1 PPm,进入转化部分。
3、转化部分精制后的原料气按水碳比3.5与自产的3.5MPa水蒸汽混合,再经转化炉对流段予热至500℃,进入转化炉辐射段。
在催化剂的作用下,发生复杂的水蒸汽转化反应。
整个反应过程是吸热的,所需热量由分布在转化炉顶部的气体燃料烧嘴提供,出转化炉840℃高温转化气经转化气蒸汽发生器换热后,温度降至360℃,进入中温变换部分。
4、变换部分来自转化气蒸汽发生器约360℃的转化气进入中温变换反应器,在催化剂的作用下发生变换反应,将变换气中CO含量降至3%左右。
中变气经原料气-中变气换热器、中变气蒸汽发生器、中变气-脱氧水换热器、中变气-除盐水换热器进行热交换回收大部分余热后,再经中变气空冷器冷却至40℃,并经分水后进入中变气PSA单元。
5、热回收及产汽系统来自装置外的脱盐水与来自酸性水气提塔的净化水混合并经中变气-除盐水换热器预热后进入除氧器。
除氧水经锅炉给水泵升压后,再经中变气-脱氧水换热器预热后进入中压汽包。
锅炉水通过自然循环的方式分别经过转化炉对流段的产汽段及转化气蒸汽发生器产生中压蒸汽。
所产生的中压蒸汽在转化炉对流段蒸汽过热段过热至440℃离开汽包。
一部分蒸汽作为工艺蒸汽使用;另一部分进入全厂中压蒸汽管网。
(二)中变气PSA单元来自造气单元压力约2.1MPa(G)、温度40℃中变气进入界区后,自塔底进入吸附塔中正处于吸附工况的塔(始终同时有两台),在其中多种吸附剂的依次选择吸附下,一次性除去氢以外的几乎所有杂质,获得纯度大于99.9 的产品氢气,经压力调节系统稳压后送出装置。
国内首套100000Nm3h的制氢装置的技术特点及节能措施

国内首套100000Nm3/h的制氢装置的技术特点及节能措施方友(中国海油惠州炼化公司)摘要:本文主要论述国内首套100000Nm3/h的烃类蒸汽转化制氢装置的一些技术特点及节能措施。
关键字:催化剂预转化节能措施1.前言随着环保法规的日益严格以及对油品质量要求的不断提高和含硫原油、重质原油数量的不断增加,使得加氢精制、加氢裂化等深加工技术成为各炼厂重要加工工艺,进而促使对氢气的需求量迅速增长,新建和拟建的制氢装置的能力大大超过以往任何一个时期。
我公司正是顺应这一趋势新建了目前全国年加工能力最大的炼厂(1200吨/年),其中以加氢为主:400万吨/年蜡油加氢裂化装置(目前全国最大的高压加氢装置)、360万吨/年煤柴油加氢裂化装置、200万吨/年汽柴油加氢装置。
为了满足加氢需要本公司新建了两套100000Nm3/h 的制氢装置。
为了充分考虑制氢装置能耗大问题,有效降低制氢成本。
本装置以天然气和饱和炼厂气为原料,采用德国Uhde公司的工艺技术,烃类蒸汽转化法造气、PSA法提纯氢气的工艺路线。
生产符合高压加氢裂化装置新氢要求的高纯氢气,同时副产9.8MPa(g)高压过热蒸汽。
装置设计满足在计划停工间隔内连续操作4年的要求,按年开工8400h计算年产99.99%的工业氢气15万吨。
2.装置特点综述本装置两个独立的系列构成,确保在其中一个系列有问题时,另一系列能保证供氢;装置原料适应性强,能单独天然气进料,也可以天然气、炼厂气任何比例进料;装置催化剂采用Johnson Matthey公司的进口催化剂,其中的国内首次使用的深度脱硫剂能使原料中的毒物脱除指标达到:总硫:<0.02ppm,总氯:<0.01ppm;装置还采用的预转化工艺、工艺冷凝液有效回用技术、以及转化炉烟气多段换热系统等诸多措施以尽可能降低能耗。
2.1 制氢原料与催化剂的优化选择2.1.1本装置制氢原料的优化构成本装置的原料为炼厂饱和干气和天然气。
制氢供氢技术及氢管理

1.4 炼化副产氢气
以国内某一大型炼化一体化企业为例,在其全厂氢源的组成中 ,炼化副产氢的比例高达68.52%,且该部分氢源的成本仅为9 000 元/吨左右。具体氢源组成如下表2所示。
表 2 某炼化企业氢源组成
制氢
资源量,Nm3/h 比例,% 45315 30.32
回收
1736 1.16
重整
43298 28.97
制氢供氢技术及氢管理
上海石化
二〇一二年九月
前
言
由于环保的要求越来越高,对燃油中硫、氮、烯烃等含量的控制越
来越严格,炼油厂只能用加氢处理来减少它们的含量,提供更清洁的燃 料;而且,由于轻质原料短缺,炼油厂要把重质原料加氢裂化,变成价 值更高的轻烃类,也需要大量氢气。 炼厂的唯一出路就是必须注重石油资源深加工,提高轻质、优质产
乙烯
59128 39.55
合计
149477 100
1.4 炼化副产氢气
随着炼油轻烃资源利用深度的不断提高,炼厂干气中所含有的 氢气组分也越来越受到人们的重视,在依次回收干气中的液化气和 碳二组分等后,干气中的氢气浓度得到不断的提升,使得回收其中 的氢气成为可能。表3为某炼化企业碳二回收装臵在回收催化干气中 碳二组分后的干气组成。
表 3 某炼化企业碳二回收装置原料及吸附废气组成
物流名称 原料气 吸附废气
氢气,vol% 27.33 38.32
甲烷,vol% 30.83 39.14
碳二,vol% 25.50 5.59
其它,vol% 16.34 16.95
第二部分
氢气提纯工艺
变压吸附(PSA)工艺
膜分离工艺
深冷分离工艺
氢气回收组合工艺
企业的氢网络系统,通常可以分为三个部分:产氢过程、耗氢过 程和净化回收单元。这三要素间的相互作用决定了企业氢分配网络以 及氢需求量。
不同原料制氢成本分析
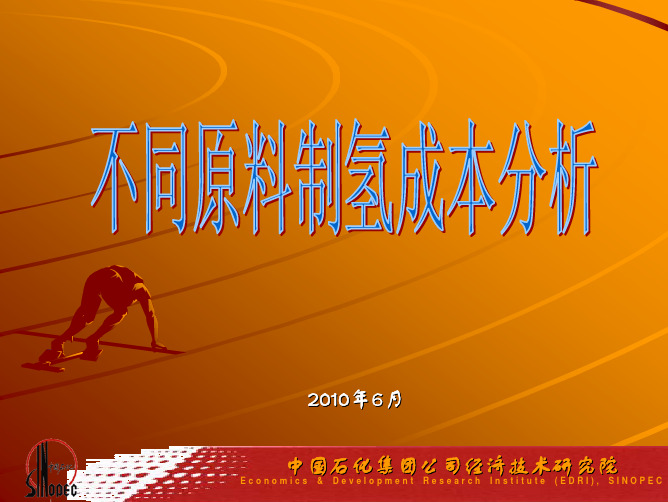
元/吨 9000 11000 13000 15000 17000 19000 21000 23000 25000 27000
中国石化集团公司经济技术研究院
Economics & Development Research Institute (EDRI), SINOPEC
4000
180
6.5 6.0
3500
3000
煤制氢 干气制氢 天然气制氢
5.5 5.0 4.5 4.0 3.5 3.0 2.5
140 120
原煤价格(元/吨)
2500 100 2000 80 1500
2.75元/Nm3
2.0 1.5 1.0
60美元/桶 885元/吨 40美元/桶
60 40 20
1000
1.94元/Nm3
495元/吨
中国石化集团公司经济技术研究院
Economics & Development Research Institute (EDRI), SINOPEC
• 干气制氢成本与天然气制氢成本对比: • 当原油价格为60美元/桶时,干气制氢成本加 回报值约为15609元/吨,相同成本下对应天然气 制氢的天然气价格为2.75元/Nm3。 • 当油价在60美元/桶左右时,天然气制氢与干气制 氢相比成本相当。当原油价格处于高价位 (80~100美元/桶)时,相同成本对应天然气价格 为3.6~4.3元/Nm3,此时天然气制氢与干气制氢相 比具有一定的竞争力。
中国石化集团公司经济技术研究院
Economics & Development Research Institute (EDRI), SINOPEC
• 煤制氢投资强度大大高于干气制氢装置,考虑到 投资的机会成本,比较分析时采用成本加投资回 报(ROI)的方法进行对比,投资回报率按10% 考虑。 • 制氢完全成本+回报每增加1000元/吨时,煤制氢 对应原料煤价增加130元/吨,天然气制氢对应天 然气价格增加0.26元/M3,干气制氢对应原油价格 增加6.8美元/桶,重油制氢对应原油价格增加6.1 美元/桶。
干气制氢

干气制氢1.工艺原理以催化干气为原料(轻石脑油为临时备用原料),采用加氢技术将原料中的烯烃饱和为烷烃,并将有机硫、有机氯等杂质转化为无机硫、无机氯,再通过脱氯、脱硫反应器脱除HCl和H2S,使精制后的气体硫含量小于0.5ppm,氯含量小于1ppm,烯烃含量小于0.1%(v)。
精制后的原料采用水蒸汽转化工艺将烃类转化为H2、CO、CO2,转化气中的CO采用中温变换,使其反应生成H2和CO2,变换气中的残余CO、CO2和CH4等杂质,采用变压吸附(PSA)的净化技术进行清除,从而得到纯度为99.9%(v)、CO+CO2<20ppm的产品氢气1.1干气(轻烃)蒸汽转化法制氢过程分为原料的净化,烃蒸汽转化,CO中温变换等工艺。
1.1.1原料净化时原料气在一定的温度、氢气压力和空速条件下,借助加氢催化剂作用,把原料气中硫化物、氯化物脱出,使原料气含硫流量降至0.2ppm,含氯量降直1ppm,以保护好后续催化剂的正常运行。
1.1.2当烃类蒸汽转化的精制原料气在一定压力、温度、空速、水碳比和催化剂作用下,烃和蒸汽进行反应,转化成气体氢和一氧化碳,同时伴生CO2和少量的残余CH4。
1.1.3转化气进行中温变换在一定的温、压力、空速、水气比和催化剂作用下,将CO与水反应生成氢气和CO2。
2.制氢的化学反应机理2.1原料烃中的硫化物以多种形态存在,一般分为无机硫化物和有机硫化物,有机硫化物不能在氧化锌脱硫剂上直接反应被脱除,必须经加氢生成无机硫化物方可被氧化锌脱硫及吸附脱除,有机硫化物在原料中一般由硫醇、硫醚、二硫化物和环状硫化物等,原料气中的硫化物绝大部分是有机硫化物。
加氢过程同样是有机氯转变为无机氯,采用高活性的金属氧化物为活性组分,脱氯剂与氯化氢反应,被固定载体上,达到脱出氯化物目的。
硫醇加氢:R-SH+H2=RH+H2S硫醚加氢:R-S-R’+H2=RH+R’H+H2S噻吩加氢:C4H4S+4H4=C4H10+H2S二硫化碳加氢:CS2+H2=CH4+H2S氧化锌脱硫:H2S+ZnS+H2O2.2烃类的蒸汽转化是将烃类与蒸汽转化为H2和CO少量残余CH4CH4+H2O=CO+H2CO+H2O=CO2+H22.3 CO中温变换是将转化气中的CO与水蒸气继续反应生成CO2和氢气。
水碳比的计算(干气制氢)

干气制氢水碳比的计算进转化炉水蒸汽和脱硫后原料气流量进行水/ 碳比的比值控制。
在正常生产情况下,控制好水蒸汽与原料气的水/ 碳比是转化操作的关键。
正常比值为3.5:1,水/ 碳比过高,不仅浪费水蒸汽,而且增加转化炉的热负荷;水/ 碳比过低,会引起催化剂积碳,使催化剂失活,甚至造成生产事故。
从安全生产与节能两方面综合考虑,工艺生产过程稳定时,要求水/ 碳比操作在低限;原料气增量时,先增水蒸汽后增原料气;减量时,先减原料气后减水蒸汽。
知道干气组成,怎们计算水碳比?公式:水/碳=水蒸气流量(Nm3h )/碳流量(Nm3h)水蒸气的流量如以kg/h表示时,则乘以22.4/18转化成Nm3/h,再带入公式;干气中碳流量以干起流量(Nm3/h )乘以干气平均分子式的碳原子个数,结果带入公式;油中碳流量=进料量kg/h X油平均分子式碳原子个数X 22.4油的平均相对分子质量,结果带入公式。
举例说明干气H2O/C 计算方式干气组分:H2 15% CH4 71% C2H6 10% C2H4 2% C3H8 2% C4H8 3总% 碳原=0.71+2*0.1+2*0.02+3*0.02+4*0.03 =0.71+0.2+0.04+0.06+0.12 =1.13 干气流量3600NM3/H 碳流量=3600*1.13=4068 配汽量12000KG/H=12000*22.4 4068*18)=3.67mol/h )/ mol/h 3~4.5的是表观水碳比,如果要计算实际水碳比,则要用{ (mol/h )+转化炉内生成的水的流量(mol/h ))/ 总mol/h )mol/h )=总碳元素mol/mol * (mol/h),mol/h )=水蒸气流量(kg/h )*1000/18H2O 与C 的mol 比,干气的单位是分可以计算出总碳元素的含量(mol/mol ),然后用,mol Nm3/H ,水蒸汽的单位是T/H0 122.4升, 1Nm3mol 量=1000/22.41Nm3 C mol =1000/22.4C mol 含摩尔量=质量/摩尔质量”量是18g/mol ,1吨水的摩尔量=1000000/18= 1000 22.4 / 18 / 干气中C 的mol= 1244.4 ( C 的molC 的mol。
以催化干气的制氢工艺特点
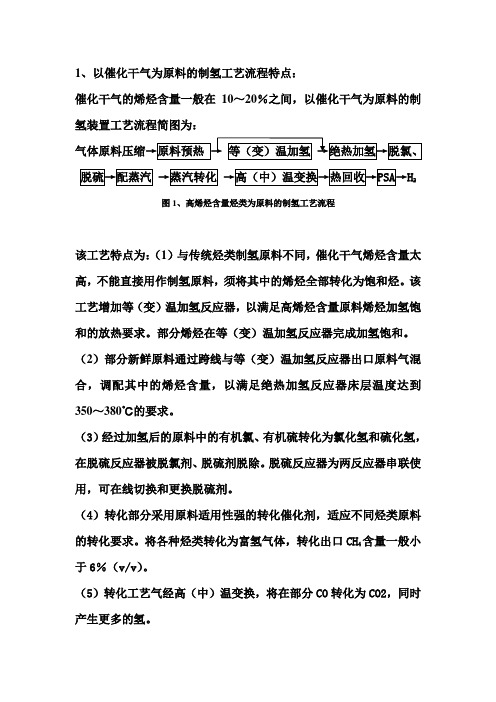
1、以催化干气为原料的制氢工艺流程特点:催化干气的烯烃含量一般在10~20%之间,以催化干气为原料的制氢装置工艺流程简图为:H2图1、高烯烃含量烃类为原料的制氢工艺流程该工艺特点为:(1)与传统烃类制氢原料不同,催化干气烯烃含量太高,不能直接用作制氢原料,须将其中的烯烃全部转化为饱和烃。
该工艺增加等(变)温加氢反应器,以满足高烯烃含量原料烯烃加氢饱和的放热要求。
部分烯烃在等(变)温加氢反应器完成加氢饱和。
(2)部分新鲜原料通过跨线与等(变)温加氢反应器出口原料气混合,调配其中的烯烃含量,以满足绝热加氢反应器床层温度达到350~380℃的要求。
(3)经过加氢后的原料中的有机氯、有机硫转化为氯化氢和硫化氢,在脱硫反应器被脱氯剂、脱硫剂脱除。
脱硫反应器为两反应器串联使用,可在线切换和更换脱硫剂。
(4)转化部分采用原料适用性强的转化催化剂,适应不同烃类原料的转化要求。
将各种烃类转化为富氢气体,转化出口CH4含量一般小于6%(v/v)。
(5)转化工艺气经高(中)温变换,将在部分CO转化为CO2,同时产生更多的氢。
(6)中变气经过多级热回收及冷却,降温至40℃以下,满足PSA进料要求。
(7)通过PSA制得纯度99.5%以上的工业氢,解吸气作为低热值燃料返回转化炉作燃料。
2 装置开工过程提要烃类蒸汽转化制氢装置的开工过程,就是将各种催化剂活化的过程,其中原料加氢催化剂需要预硫化处理,转化及中变催化剂需要还原处理。
脱硫、脱氯剂要进行适当的干燥脱水处理。
以下分别论述。
2.1 加氢催化剂预硫化制氢原料加氢催化剂投入正常使用前,一般需要将氧化态的活性组分先变成具有催化活性的金属硫化态形态,称为预硫化,本文不对加氢催化剂的详细预硫化过程进行论述,各用户可参考催化剂供应商提供的催化剂硫化方案,本文主要介绍硫化介质及硫化过程的流程控制。
硫化介质硫化介质是指催化剂硫化所需的气体氛围,一般由N2、H2、H2S组成。
工业上一般不直接采用H2S作硫化介质,而是采用液态的CS2、DMDS (二甲基二硫)等作为硫化剂。
炼厂干气作为制氢原料的技术探讨与工业应用

炼厂干气作为制氢原料的技术探讨与工业应用彭成华(北京海顺德钛催化剂有限公司北京100176)摘要:对炼厂干气作为制氢装置原料的可行性进行了分析,针对焦化干气和催化干气作为制氢原料中存在有机硫和烯烃等问题提出了不同加氢处理工艺以及与此相配套的低温性能良好的加氢催化剂。
工业运转数据表明,北京海顺德钛催化剂有限公司研发的新一代加氢催化剂T205A-1/T205,具有初活性温度低、烯烃饱和性能好、抗结炭性能好等优点,可以很好的处理焦化干气和/或催化干气,使之满足水蒸气转化催化剂对原料的要求。
关键词:制氢原料炼厂干气加氢精制工业应用1.前言随着世界石油资源重质化、劣质化趋势的加剧以及各项环保法规的日益严格,加氢技术在原油二次加工过程中的应用日益广泛,相应的氢气需求也迅速增加。
而在加氢装置的加工成本中,氢气成本约占50%,因此降低加氢成本,提供更多廉价的氢气已经成为发展加氢技术,提高炼油企业综合经济效益的关键。
目前,蒸汽转化制氢工艺由于其技术可靠、流程简单、投资低廉、操作简便,而在制氢装置中占主导地位。
对此工艺来讲,原料消耗在制氢成本中占有很大比例,因此如何选用合适的原料以降低氢气生产成本,成了制氢装置首要考虑的问题。
本文探讨了炼油企业中常常作为燃料用的低廉的炼厂干气作为制氢原料的可行性,并列举了相应的工业运转实例。
2.炼厂干气作为制氢原料的技术探讨2.1炼厂干气性质比较与分析炼厂干气是指原油加工过程中副产的各种尾气,包括催化裂化干气、焦化干气、催化重整气、热裂解气、高压加氢裂化尾气等。
各种炼厂干气的组成变化较大,表1列出了炼厂干气的典型性质。
从表1数据可以看出,加氢裂化干气、加氢精制干气和重整干气基本不含有机硫和烯烃,经过湿法脱硫后硫化氢的含量一般也小于20μg·g-1,是制氢的良好原料。
焦化干气和催化裂化干气中烯烃和有机硫的含量较高,必须经过加氢处理,降低烯烃和硫含量,才能作为制氢装置的原料。
天然气制3000Nm3H氢工程的物料衡算和热量平衡一段转化炉的主要
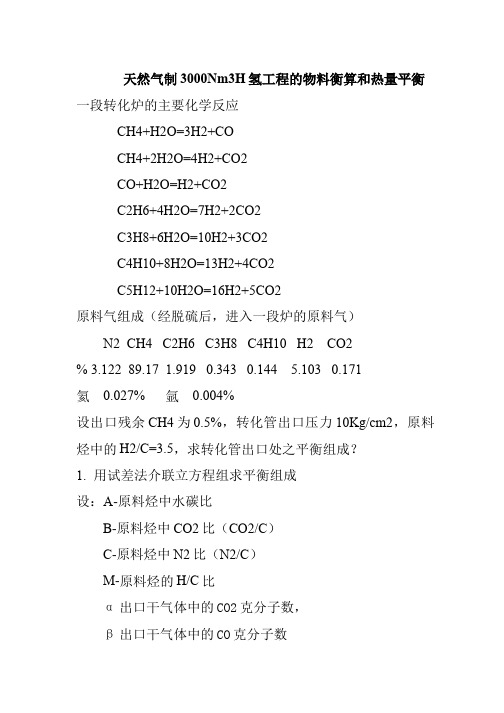
天然气制3000Nm3H氢工程的物料衡算和热量平衡一段转化炉的主要化学反应CH4+H2O=3H2+COCH4+2H2O=4H2+CO2CO+H2O=H2+CO2C2H6+4H2O=7H2+2CO2C3H8+6H2O=10H2+3CO2C4H10+8H2O=13H2+4CO2C5H12+10H2O=16H2+5CO2原料气组成(经脱硫后,进入一段炉的原料气)N2 CH4 C2H6 C3H8 C4H10 H2 CO2% 3.122 89.17 1.919 0.343 0.144 5.103 0.171氦 0.027% 氩 0.004%设出口残余CH4为0.5%,转化管出口压力10Kg/cm2,原料烃中的H2/C=3.5,求转化管出口处之平衡组成?1.用试差法介联立方程组求平衡组成设:A-原料烃中水碳比B-原料烃中CO2比(CO2/C)C-原料烃中N2比(N2/C)M-原料烃的H/C比α出口干气体中的CO2克分子数,β出口干气体中的CO克分子数γ出口干气体中的H2克分子数δ被转化了H2O的克分子数x出口干气体中CH4的百分含量V出口干气体总克分子数以100克分子原料烃为计算基准:按C平衡:M=∑H%/∑C%=4V CH4+4VC2H6+4*V C3H8…/V CH4+2V C2H6+V CO2+……=4*0.8917+4*0.01919+4*0.00343+4*0.00144+0.05103/0.8917+2*0.01919+3*0.00343+4*0.00144+O.OO171=3.5668+0.007676+0.01372+0.00576+0.05103/0.8917+0.03838+0.01029+0.00576+0.00171=3.645/0.94784=3.845M=3.845原料烃中之H2O/气为:A=3.5(0.8917+0.03838+0.01029+0.00576+0.00171)=3.5*0.94784=3.317A=3.3174将上述条件代入式得:按碳平衡式 ∑nCnHm+B=α++XV0.94784(为总碳量)=α+β+0.005V (1)0.005-为出转化炉的剩余CH4量按氧平衡 B+1/2A=α+1/2β+1/2(A-δ)0.00162+1/2*3.3174=α+1/2β+1/2(3.3174-δ)0.00171=α+0.5β-0.5δ (2)按氢平衡A+1/2(∑nCnHm+B)=γ+2XV+(A-δ)3.3174+1/2*(0.8917*4+0.01919*4+0.00343*4+0.00144*4.)=γ+2*0.005*V+(3.31744-δ)3.3174+1/2*(3.567+0.07676+0.0137+0.00576+0.05103)=γ+0.01V+3.31744-δ3.3174+3.645/2=γ+0.01V-δ+3.31741.8225-γ-0.01V=δδ=γ+0.01V-1.8225 (3)V=α+β+γ+0.005V+0.03122 (4)先假设出口温度为850℃,查变換反应平衡常数KP2=0.8552 KP2=CO2*H2/CO*H2O=α*γ/β(A-δ)α*γ/β(3.31744-δ)=0.8552 (5)由(1)减(4)得:0.94784-V=α-α+β-β+0.005V-γ-0.005V-0.0329γ= V-0.981 (6)代(6)入(3)得:δ=V-0.981+0.01V-1.8225δ=1.01V-2.804 (7)由(1)减(2)得:0.94784-0.00171=α-α+β-0.5β+0.5δ+0.005V0.9461=0.5β+0.5δ+0.005V (8)代(7)入(8)得0.9461=0.5β+0.5(1.01V-2.804)+0.005V0.9461=0.5β+0.505V-1.402+0.005V0.5β=0.51V-2.348β=4.696-1.02V (9)代(6)(9)入(4)得V=α+V-0.981+4.696-1.02V+0.005V+0.03122α=1.015V-3.74622 (10)代(6)(7)(9)(10)入(5)得〈1.015V-3.7489〉(V-0.981)/(4.696-1.02V)(3.31744-〈1.01V-2.804〉)=0.85521.015V2-3.7489V-0.996V+3.678/(4.696-1.02V)(〈3.3174〉-〈1.01V-2.804)=0.85521.015V2-4.745V+3.678/ 1.03V2-10.986V+28.744=00.85521.015V2-4.745V+3.678=0.7.63V2-8.14V+21.300.252V2+3.395V-17.622=0V2+13.47V-69.93=0V2+13.47V+(13.47/2)2=69.93+(13.47/2)2(V+13.47/2)2=69.93+(6.735)2V+6.737=√ 69.93+45.36V=10.735-6.735=4.0003α=1.015*4.0003-3.7489=0.3114β=4.696-1.02*4.0003=0.615γ=V-0.981=4.0003-0.981=3.0193δ=1.01V-4.0003=4.0403-4.0003=0.04出口水:H2O=3.3174-δ=3.3174-(1.01V-2.804)=2.081 CH4=0.005N2=0.03122出口湿基总和为:6.45795出口湿转化气组成为:CO2 CO H2 CH4 N2 H2O ∑0.0482 0.0952 0.4675 0.0619 0.0048 0.3222 0.9998出口干基总和0.3114+0.615+3.0193+0.005+0.03122=3.98129 CO2 CO H2 CH4 N2 ∑7.82 15.445 75.8252 0.1256 0.784 99.9998计算甲烷蒸汽转化平衡常数K1值:K1=Vco*V3H2/V CH4*V H2O*P2=0.0952*(0.4675)3 /0.0619*0.3222*(15)2=0.009727/0.019944*225=109.736查出平衡温度为780℃<850℃,计算符合要求。
10000m3小时制氢装置工艺介绍
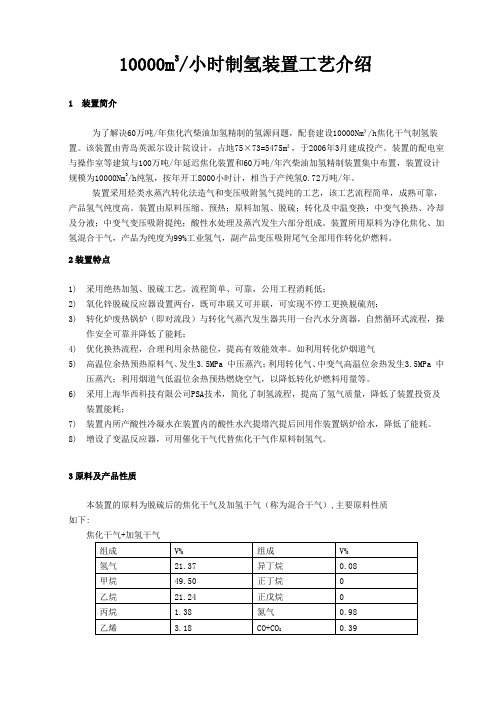
10000m3/小时制氢装置工艺介绍1 装置简介为了解决60万吨/年焦化汽柴油加氢精制的氢源问题,配套建设10000Nm³/h焦化干气制氢装置。
该装置由青岛英派尔设计院设计,占地75³73=5475m²,于2006年3月建成投产。
装置的配电室与操作室等建筑与100万吨/年延迟焦化装置和60万吨/年汽柴油加氢精制装置集中布置,装置设计规模为10000Nm3/h纯氢,按年开工8000小时计,相当于产纯氢0.72万吨/年。
装置采用烃类水蒸汽转化法造气和变压吸附氢气提纯的工艺,该工艺流程简单,成熟可靠,产品氢气纯度高。
装置由原料压缩、预热;原料加氢、脱硫;转化及中温变换;中变气换热、冷却及分液;中变气变压吸附提纯;酸性水处理及蒸汽发生六部分组成。
装置所用原料为净化焦化、加氢混合干气,产品为纯度为99%工业氢气,副产品变压吸附尾气全部用作转化炉燃料。
2装置特点1)采用绝热加氢、脱硫工艺,流程简单、可靠,公用工程消耗低;2)氧化锌脱硫反应器设置两台,既可串联又可并联,可实现不停工更换脱硫剂;3)转化炉废热锅炉(即对流段)与转化气蒸汽发生器共用一台汽水分离器,自然循环式流程,操作安全可靠并降低了能耗;4)优化换热流程,合理利用余热能位,提高有效能效率。
如利用转化炉烟道气5)高温位余热预热原料气、发生3.5MPa 中压蒸汽;利用转化气、中变气高温位余热发生3.5MPa 中压蒸汽;利用烟道气低温位余热预热燃烧空气,以降低转化炉燃料用量等。
6)采用上海华西科技有限公司PSA技术,简化了制氢流程,提高了氢气质量,降低了装置投资及装置能耗;7)装置内所产酸性冷凝水在装置内的酸性水汽提塔汽提后回用作装置锅炉给水,降低了能耗。
8)增设了变温反应器,可用催化干气代替焦化干气作原料制氢气。
3原料及产品性质本装置的原料为脱硫后的焦化干气及加氢干气(称为混合干气),主要原料性质如下:在焦化停工时用催化干气作原料工业氢气温度40℃压力2.0MPa(G)组成如下表:注 * 其中纯氢10000Nm3/h,相当于0.72 万吨/年纯氢。
神华煤液化干气与天然气共制氢影响浅析及对策

第 9期
化
工
技
术
与
开
发
Vo. 0 No9 14 . S p2 e . 01 1
2 1 年 9月 01
T c n l g & De e o me to h mia n u t e h oo y v lp n fC e c lI d sr y
神华煤液化干气与天然气共制氢影响浅析及对策
曾 吉 来
( 华煤 制 油化 工有 限公 司鄂 尔 多斯煤 制 油分 公 司 , 神 内蒙 古 鄂尔 多斯 0 7 0 ) 12 9 摘 要: 介绍 了神华 煤直 接 液化项 目利用 富余 的煤 液化 干气 与 天然 气共 制氢 试生 产运 行情 况 . 针对 煤 液
化 干气 与天 然气 共 制氢对 现 有天 然气 制氢 装 置造 成 的各种 影 响 , 分析 了其 中 的原 因 , 出 了一 些应 对 的办 法 提
幅度波动 。
2 影 响分 析
2 1 对 原 料 气 压 缩 机 的影 响 .
从 表 1天 然 气 与 煤 液 化 干 气 组 分 数 据 表 计 算 得 出 。 液 化 干 气 平 均 分 子 量 为 l ., 设 计 提 煤 27 而
从 天 然气 工况 到煤液 化 干气 与 天 然气 共 制
收 稿 日期 : 0 10 . 3 2 1 - 6 1
化
工
技
术
与
开
发
第4 0卷
表 1 天 然 气 与 煤 液 化 干 气 组 分 数 据 表
现 有 系 统 内装 填 的未 使 用 到 期 限 的 铁 锰 加 氢/ 氧
化锌脱硫催 化剂和 Z 1Q 4 3 4 2 / 1Q转化催化剂进行 反 应 , 们 跟 踪 分 析 数 据 、 要 工 艺 参 数 和 其 他 我 主
制氢化工工艺培训工作总结

第二十三届制氢年会交流总结本次制氢年会共收到与制氢有关的工艺、催化剂、设备、原料净化、烃类转化制氢、煤气化制氢、甲醇制氢、氢产品提纯、操作技术及安全、事故处理等方面的论文近五十篇。
另外联络站还组织专业人员翻译了去年美国炼油工程师协会会议的制氢方面的七篇工艺、设计方面的综合性论文。
现将年会交流心得总结如下:一、炼油厂氢气网络设计优化技术日益严格的环保法规要求炼油厂在生产硫含量更低、规格更高的车用燃料的同时,还要实现清洁生产,降低二氧化硫和温室气体的排放;并且,炼油厂为了更有效的利用原油资源,获得更好的经济效益,并在激烈的竞争中求得生存,炼油厂在重油加工工艺选择上,从传统的选择脱碳工艺转向更多的选择加氢工艺,同时选择加工的原油也更加重质、劣质化,硫、氮含量也更高,这些都驱使炼油厂不断增加加氢装置的能力,从而导致氢气用量的大幅增加。
由于能源价格的不断提高,制氢的成本也不断上升,不论采用何种工艺技术的制氢装置,都要耗用大量的资源,并排放大量的温室气体;因此,优化氢气网络,合理利用氢气资源,对炼油厂的节能降耗,降低成本具有十分重要的意义。
通过氢气网络优化,达到最少使用新氢和最低排放废氢到燃料气管网的目的.炼厂氢网络优化技术主要分为两类:一是基于图形分析方式的夹点分析方法;二是基于数学模型的线性或非线性规划算法。
夹点分析方法可迅速诊断氢系统关键位置,确定系统最小用氢目标;而各种数学算法则可帮助用户设计实际可行的流程方案。
两类方法都有各自的优势和局限性。
因此,在实际氢网络设计和改造项目中将两方面技术相结合是非常必要的。
以m企业为例,原油综合加工能力为1350万吨/年,乙烯生产能力为100万吨/年。
通过对该企业的氢气网络进行优化,可使m企业节省氢气使用成本6620万元,经济效益显著,应在国内炼油厂的规划、改造设计中推广应用。
在氢网络设计中应分析制氢装置、氢气净化装置的规模、原料、工艺操作对氢气产率、氢纯度以及消耗、氢气成本、装置投资的影响.氢网络优化技术是一项炼油厂氢气网络优化的先进技术,其中基于图形法的氢夹点分析技术可有效识别炼油厂氢气网络中的瓶颈,科学指导氢气系统的优化方向,而基于数学模型的数学规划算法可优化氢网络的流程布局和操作条件,实现氢气的最佳利用方案。
制氢工艺基础简介

制氢工艺基础简介1.1制氢装置概况1.1.1 制氢装置简介本装置是12000Nm3/h制氢装置,由中石化北京设计院设计,2004年投入正式生产。
装置以油田气为主要原料,采用烃类水蒸气转化法造气,PSA法净化提纯的工艺路线制取氢气,设计产氢规模为年产99.9%(V)的工业氢气0.9万吨,年开工8000小时,相当于每小时产纯氢12000标准立方米。
所产的氢气中,供90万吨柴油加氢装置使用,其余部分送入公司氢气管网。
1.1.1.1设计概况中国石油天然气股份有限公司克拉玛依石化分公司稠油集中加工技术改造及配套工程可行性研究报告(BQOD-225-1、2.1、2.2、2.3);克拉玛依石化分公司关于稠油集中加工技术改造及配套工程基础设计/详细设计的委托书[KSHG(2003)38CS];中国石油天然气股份有限公司关于本项目可行性研究报告的批复文件(石油计字[2003]227号)。
1.1.1.2设计原则采用技术先进、成熟可靠的工艺方案,在降低能耗,减少环境污染的同时为下游装置提供稳定的高纯度氢源。
严格执行国家、中国石化集团公司及当地有关环保法规或标准。
1.1.1.3工艺概况1)装置的组成制氢装置共分为六个部分:(1)原料气压缩部分;(2)原料气加氢精制、干法脱硫部分;(3)转化及中温变换部分;(4)中变气换热及冷却部分;(5)变压吸附氢提纯部分;(6)酸性冷凝水汽提及蒸汽发生部分。
2)装置的特点(1)优化换热流程,提高能量利用效率加强对中变气热能的回收,利用中变气先后与原料气(去精制部分)、脱氧水(锅炉给水)进行热交换,充分回收了中变气的热能,降低装置能耗。
利用转化炉烟道气高温位预热原料气,利用烟道气和转化气高温余热发生并过热3.5MPa中压蒸汽,利用转化炉烟道气低温位余热预热燃烧用空气,降低转化炉的燃料消耗。
(2)回收工艺冷凝水,减少除盐水的用量。
在中变气冷却的过程中,产生大量的冷凝水。
水中含有微量的CO2、有机物,金属离子的含量很低,经酸性水汽提塔汽提后,经检验合格由凝结水泵(P-2101A/B)升压后,送出装置。
水碳比的计算(干气制氢)
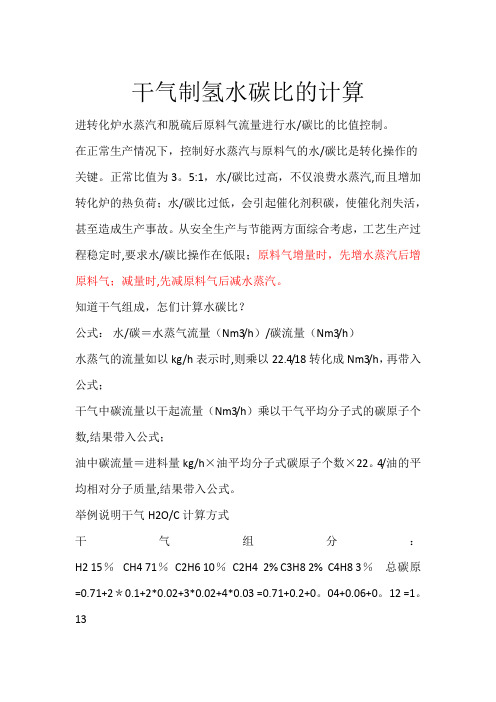
干气制氢水碳比的计算进转化炉水蒸汽和脱硫后原料气流量进行水/碳比的比值控制。
在正常生产情况下,控制好水蒸汽与原料气的水/碳比是转化操作的关键。
正常比值为3。
5:1,水/碳比过高,不仅浪费水蒸汽,而且增加转化炉的热负荷;水/碳比过低,会引起催化剂积碳,使催化剂失活,甚至造成生产事故。
从安全生产与节能两方面综合考虑,工艺生产过程稳定时,要求水/碳比操作在低限;原料气增量时,先增水蒸汽后增原料气;减量时,先减原料气后减水蒸汽。
知道干气组成,怎们计算水碳比?公式:水/碳=水蒸气流量(Nm3/h)/碳流量(Nm3/h)水蒸气的流量如以kg/h表示时,则乘以22.4/18转化成Nm3/h,再带入公式;干气中碳流量以干起流量(Nm3/h)乘以干气平均分子式的碳原子个数,结果带入公式;油中碳流量=进料量kg/h×油平均分子式碳原子个数×22。
4/油的平均相对分子质量,结果带入公式。
举例说明干气H2O/C计算方式干气组分:H2 15% CH4 71% C2H6 10% C2H4 2% C3H8 2% C4H8 3%总碳原=0.71+2*0.1+2*0.02+3*0.02+4*0.03 =0.71+0.2+0。
04+0.06+0。
12 =1。
13干气流量3600NM3/H 碳流量=3600*1。
13=4068 配汽量12000KG/H 水碳比=12000*22。
4除以(4068*18)=3.67公式:水/碳=水蒸气流量(mol/h)/总碳元素的流量(mol/h)一般控制在3~4.5这样计算出来的是表观水碳比,如果要计算实际水碳比,则要用{加入的水蒸气流量(mol/h)+转化炉内生成的水的流量(mol/h))/总碳原素的流量(mol/h)知道干气的组分可以计算出总碳元素的含量(mol/mol),然后用,总碳元素的流量(mol/h)=总碳元素的含量(mol/mol)*干气的流量(mol/h),水蒸气流量(mol/h)=水蒸气流量(kg/h)*1000/18根据工艺要求计算水碳比是计算H2O与C的mol比,干气的单位是Nm3/H,水蒸汽的单位是T/H,一定注意量纲的统一.物质的mol量计算:0℃ 1个大气压下,每摩尔气体的体积大约为22。
制氢有关计算

第五章生产有关计算5.1 烃类蒸汽转化制氢的原料的选择适用于蒸汽转化的烃类原料大体分为气态和液态。
5.1.1 气态烃包括天然气、液化石油气和各种炼厂气天然气一般包括油田伴生气和气田气。
天然气主要成分是甲烷、乙烷、丙烷等低级烃类,含有一定的氮的二氧化碳等惰性气体和有害杂质硫化氢,其中气田天然气是以甲烷为主含微量杂质的气体。
液体石油气是由丙烷、丁烷为主要成分的烃类,来源有两种,一种是油田和天然气油伴生出来的天然液化气,另一种是炼油厂和石油化工厂生产的液化石油气。
炼厂气是指原油加工过程中副产的各种尾气,包括催化裂化气、焦化干气、热裂解气、高压加氢裂化尾气等,其组成变化较大,其中含有烯烃的炼厂气不宜直接应用,一般需经过环烷化或除掉烯烃才能做制氢原料。
而不含烯烃的加氢干气可以作为蒸汽转化制氢原料,但因为氧气含量一般>60%故单位产氢率小。
5.2原料物料的计算5.2.1原料烃的虚拟分子式的计算烃类的虚拟分子式:因为烃类原料都是有多种有机物和一些杂质组成。
为了便于进行工艺的物料衡算,人们把烃类混合物用一种所谓虚拟分子式Cm Hn代替,即代表混合物一个分子所含碳原子的平均数,m为混合物一个分子所含的平均氢原子数,而分子量也即是混合物的一个分子的平均分子量,有了虚拟分子式后,对以后工艺的计算就简化,方便多了。
以加裂干气为例,求法如下:加裂干气的n, mn=∑C=∑ViCi=(17.87×1+2.03×2+4.58×3+5.46×4+2.23×4+0.417×5+0.13×5)÷100=0.6916m=∑Hi=(66.75×2+17.87×4+2.03×6+4.58×8+5.46×10+0.417×120.13×12) ÷100=3.373故加裂干气虚拟分子式为:C0.6916H3.3735.2.2 原料总碳:烃类混合物每一分子所含的碳元素的平均个数我们示例中加裂干气的总碳n=0.6916,因为加裂干气虚拟分子式为:C0.6916H3.373总碳∑C=n=0.69165.2.3 氢碳化H/C=m/n=3.373/0.6916=4.877加裂干气虚拟分子式为:C0.6916H3.373平均分子量M=0.6916×12.01+3.373×2.016/2=11.706总碳∑C=n=0.6916H/C=m/n=3.373/0.6916=5.4755.2.4 什么是绝对碳原(总碳)?碳原的定义是指100Nm3原料气中所含的烃类中的碳都折算成气态C1时所占有的体积立方米数,写作∑C ,也叫做总碳。
- 1、下载文档前请自行甄别文档内容的完整性,平台不提供额外的编辑、内容补充、找答案等附加服务。
- 2、"仅部分预览"的文档,不可在线预览部分如存在完整性等问题,可反馈申请退款(可完整预览的文档不适用该条件!)。
- 3、如文档侵犯您的权益,请联系客服反馈,我们会尽快为您处理(人工客服工作时间:9:00-18:30)。
10000Nm3/h制氢装置一、概述********有限公司焦化装置配套建设60万吨/年加氢装置,因此需要配套建设制氢装置以供给加氢装置工业新氢。
(一)装置组成本装置由造气和中变气PSA两个单元组成。
投资约4654万元。
(二)装置规模根据全厂总流程安排,新建制氢装置的公称规模为10000Nm3/h工业氢。
装置年操作时数8000小时。
(三)工艺技术路线造气单元的工艺技术方案采用轻烃蒸汽转化技术;中变气PSA单元工艺方案采用变压吸附(PSA)净化技术。
造气单元主要包括:原料气压缩、脱硫、蒸汽转化和一氧化碳变换等。
(四)主要设备简况见表4-3-1。
表4-3-1主要设备简况表注:以上台数不含压缩机组配套设备。
(五)占地面积装置占地4620m2。
(六)装置定员本装置按四班三倒,共计16人,其中班长4人,操作人员12人。
二、原料及产品性质(一)原料性质焦化干气的规格进装置温度:40℃进装置压力:0.6MPa(G)。
表4-3-2原料性质表(二)产品方案产品-工业氢规格出装置温度:40℃出装置压力:2.0MPa(G)表4-3-3产品组成表三、装置物料平衡表4-3-3物料平衡表四、工艺技术方案(一)工艺方案选择以轻烃为原料制取工业氢,国内外均认为蒸汽转化法为最佳方案。
大型合成氨厂以及炼油厂的制氢装置,其造气工艺大多为水蒸气转化法。
该工艺技术具有投资省、能耗低、操作可靠性、灵活性高等优点,经过多年的生产实践,目前已积累了许多成功的工程设计及操作经验。
因此制氢装置造气单元拟采用蒸汽转化技术。
国内外蒸汽转化制氢装置的净化工艺主要可分为两种流程,即化学净化法(常规净化法)和变压吸附净化法(PSA净化法)。
两种流程在国内均已有成功的操作经验,两种净化方法的选择主要取决于原料和燃料价格及技术经济比较结果。
由于造气单元采用价格较低而且产氢量高的焦化干气为原料,因此采用PSA净化法的氢气成本要比采用化学净化法的氢气成本低。
而且采用PSA净化法制氢装置还具有流程简单,便于生产经管,产品氢纯度高(PSA净化法生产的工业氢纯度大于99.99%)等特点,有利于减少加氢装置的投资和消耗。
因此,推荐采用PSA净化法。
(二)工艺流程特点1、造气单元(1)采用焦化干气为装置原料,原料产氢率高,原料和燃料消耗低。
(2)优化装置设计,合理选择工艺参数,采用较高的转化出口温度(840℃),增加转化深度,提高单位原料的产氢率,从而降低原料和燃料消耗;选用较低的水碳比(3.5),进一步降低转化炉的燃料消耗。
(3)氧化锌脱硫反应器设置两台,即可串联又可并联,可实现不停工更换脱硫剂。
(4)一氧化碳变换部分仅采用中温变换流程,不采用低温变换流程,以降低装置投资,简化制氢流程,缩短开工时间。
(5)采用二合一的产汽流程(即烟道气、转化气的产汽系统共享一台汽包),简化了余热回收流程,降低了装置投资。
(6)优化换热流程,合理利用余热能位,提高有效能效率。
a.利用转化炉烟道气高温位余热预热原料气,利用烟道气和转化气的高温位余热发生3.5MPa中压蒸汽。
所产蒸汽一部分作为工艺用汽,多余部分外输至工艺蒸汽管网。
b.利用中变气高温位余热预热锅炉给水,以增加中压蒸汽产量。
c.利用烟道气低温位余热预热燃烧空气,以降低转化炉的燃料用量。
d.在维持合理传热温差的前提下,降低排烟温度,提高转化炉的热效率,以降低燃料消耗。
(7)为提高装置的可靠性,确保装置长周期安全运行,制氢装置的催化剂选用国内成熟可靠的催化剂。
其中转化催化剂建议选用国内制氢装置普遍采用的由齐鲁石化研究院研制生产的水蒸汽转化制氢催化剂。
(8)回收工艺冷凝水,减少装置脱盐水用量。
在变换气冷却过程中将产生大量的冷凝水,这部分冷凝水如直接排放,将会污染环境或增加污水处理场负担。
本设计将工艺冷凝液经汽提塔汽提后直接进入除氧器,除氧后作为锅炉给水。
这样既保护了环境,又减少了脱盐水用量。
(9)采用U型管双壳程换热器,加深换热深度,提高热效率。
(10)采用高效分水器,降低了设备投资。
2、中变气PSA单元(1) PSA方案建议采用8-2-4 PSA工艺,在0.05MPa(G)压力下完成吸附剂再生,具有流程简单、无需动力设备、能耗低的特点。
(2)本方案较传统流程多一次均压过程,可更有效地回收产品氢气,提高了产品氢回收率。
(可达90%)(3)增加一台顺放气缓冲罐,解决了传统流程在冲洗再生过程中存在的二次污染问题,因而吸附剂再生效果更好。
(4)变压吸附工艺过程采用DCS控制系统,具有运转平稳,操作可靠的特点。
并且具有事故状态下,能自动或手动由八床操作切换至七床、六床、五床操作的功能, 因而大大地提高了装置的可靠性。
五、主要工艺过程操作条件(一)加氢反应温度: 230~380℃反应压力: 2.92MPa(G)(二)脱氯反应温度: 320~380℃反应压力: 2.89MPa(G)出口气中氯含量: ≤1ppm wt穿透氯容: 10kg/100kg催化剂(三)脱硫反应温度: 320~380℃反应压力: 2.88MPa(G)入口硫含量: ≤200ppm(wt)出口硫含量: ≤0.5ppm(wt)饱和硫容: 30kg/100kg催化剂(四)转化反应温度: 入口 480~520℃出口 800~850℃反应压力: 入口 2.80MPa(G)出口 2.50MPa(G)水碳比 3.5(H2O mol/c atom) (五)中变反应温度: 入口 340~360℃出口 400~420℃反应压力: 2.45MPa(G)(六)变压吸附H2回收率≥90%出口氢纯度≥99.9V%尾气压力≥0.05MPa(G)出口氢气压力 2.0MPa(G)六、工艺流程简述本装置由造气单元和中变气PSA单元组成。
(一)造气单元1、进料系统来自装置外的焦化干气进入原料气缓冲罐,经原料气压缩机压缩至3.2MPa(G)后进入原料气脱硫部分。
2、脱硫部分进入脱硫部分的原料气经原料气-中变气换热器或开工加热炉(开工时用)升温到230℃左右进入加氢反应器,在其中原料中的不饱和烃通过加氢转化为饱和烃类,床层温度升至380℃左右,此外通过加氢反应,原料中的有机硫转化为无机硫,然后进入氧化锌脱硫反应器脱除硫化氢和氯化氢。
经过精制后的气体总硫含量小于0.5PPm,氯化氢含量小于1 PPm,进入转化部分。
3、转化部分精制后的原料气按水碳比3.5与自产的3.5MPa水蒸汽混合,再经转化炉对流段予热至500℃,进入转化炉辐射段。
在催化剂的作用下,发生复杂的水蒸汽转化反应。
整个反应过程是吸热的,所需热量由分布在转化炉顶部的气体燃料烧嘴提供,出转化炉840℃高温转化气经转化气蒸汽发生器换热后,温度降至360℃,进入中温变换部分。
4、变换部分来自转化气蒸汽发生器约360℃的转化气进入中温变换反应器,在催化剂的作用下发生变换反应,将变换气中CO含量降至3%左右。
中变气经原料气-中变气换热器、中变气蒸汽发生器、中变气-脱氧水换热器、中变气-除盐水换热器进行热交换回收大部分余热后,再经中变气空冷器冷却至40℃,并经分水后进入中变气PSA单元。
5、热回收及产汽系统来自装置外的脱盐水与来自酸性水气提塔的净化水混合并经中变气-除盐水换热器预热后进入除氧器。
除氧水经锅炉给水泵升压后,再经中变气-脱氧水换热器预热后进入中压汽包。
锅炉水通过自然循环的方式分别经过转化炉对流段的产汽段及转化气蒸汽发生器产生中压蒸汽。
所产生的中压蒸汽在转化炉对流段蒸汽过热段过热至440℃离开汽包。
一部分蒸汽作为工艺蒸汽使用;另一部分进入全厂中压蒸汽管网。
(二)中变气PSA单元来自造气单元压力约2.1MPa(G)、温度40℃中变气进入界区后,自塔底进入吸附塔中正处于吸附工况的塔(始终同时有两台),在其中多种吸附剂的依次选择吸附下,一次性除去氢以外的几乎所有杂质,获得纯度大于99.9 的产品氢气,经压力调节系统稳压后送出装置。
当吸附剂吸附饱和后,通过程控阀门切换至其它塔吸附,吸附饱和的塔则转入再生过程。
在再生过程中,吸附塔首先经过连续四次均压降压过程尽量回收塔内死空间氢气,然后通过顺放步序将剩余的大部分氢气放入顺放气罐(用作以后冲洗步序的冲洗气源),再通过逆放和冲洗两个步序使被吸附杂质解吸出来。
逆放解吸气进入解吸气缓冲罐,冲洗解吸气进入解吸气缓冲罐,然后经调节阀调节混合后稳定地送往造气单元的转化炉作为燃料气。
七、自控水平(一)工艺装置对自动控制的要求制氢装置采用以微计算机技术为基础的集散控制系统(DCS),对全装置进行集中经管,数据处理,相对分散控制,以增强系统的适应性、可靠性,有利于装置顺利完成正常生产时的操作调优,长周期、安全、平稳操作。
制氢装置的造气单元与PSA单元共用一套DCS控制系统。
自动保护联锁功能和变压吸附(PSA)顺序控制功能也由DCS完成。
大部分仪表回路采用本安回路,变送器以智能型为主,并在装置内独立设置可燃气体监测系统,其中PSA单元的控制软件采用PSA专利商提供的“切塔控制和参数优化软件”。
(二)生产过程的自控水平以及控制、检测仪表选型原则1、生产过程的自控水平采用分散控制系统(DCS),对全装置工艺过程进行集中控制、监测、记录和报警。
DCS显示全面、直观、精确、控制可靠、操作方便,并为全厂实现计算机数据处理和生产经管创造条件。
设有安全联锁或紧急事故处理安全仪表系统(SIS),该系统与DCS共为一套系统,其机柜放置在中心控制室机柜室内,操作站放置于中心控制室操作间。
本装置与焦化、加氢、硫磺回收等装置共用一个中心控制室。
2、自控仪表选型原则(1)控制室仪表控制室内采用DCS,为了便于操作、经管、资源共享、节省投资,本装置与焦化、加氢装置采用一种DCS系统。
本装置DCS硬件配置如下:CRT操作站: 4台(其中1台专用于PSA)报表及报警打印机: 1 台(报表打印机与焦化、加氢装置共用)冗余的控制模件、机柜、隔离安全栅柜及相应的设备。
(2)现场仪表根据工艺条件及其要求,选用先进、可靠并且安装、使用方便的仪表。
电动仪表选用符合工艺场所防爆等级的本安型或隔爆型仪表,凡与腐蚀介质接触的仪表,均选用耐腐蚀材质。
本装置的变送器和信号转换类仪表选用本质安全型,配用隔离式安全栅构成本质安全防爆系统;开关类仪表选用防爆等级相当的隔爆型仪表。
a.流量仪表流量测量仪表以节流装置为主,配以差压变送器送入DCS,对于小流量的测量选用电远传金属管浮子流量计。
部分气体和蒸汽流量的测量选用气体质量流量计。
进出装置的汽、气、水均设置计量仪表并送入DCS进行计量累积。
b.液位仪表一般选用远传式双法兰液位变送器或电动导波雷达液位变送器。
现场指示的液位计一般选用磁性翻板式液面计或石英管式彩色液位计。
原则上液位开关的设置选用音叉式或浮球式开关,开关的接点应为双刀双掷式(DPDT)。