车刀刀片的合理选择
外圆车刀的用途
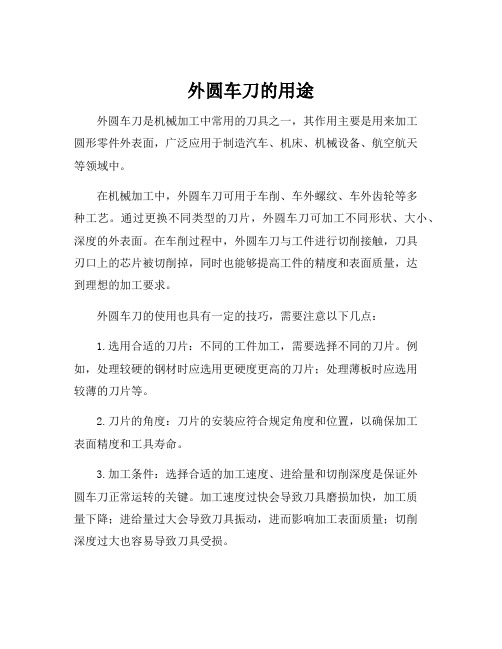
外圆车刀的用途
外圆车刀是机械加工中常用的刀具之一,其作用主要是用来加工
圆形零件外表面,广泛应用于制造汽车、机床、机械设备、航空航天
等领域中。
在机械加工中,外圆车刀可用于车削、车外螺纹、车外齿轮等多
种工艺。
通过更换不同类型的刀片,外圆车刀可加工不同形状、大小、深度的外表面。
在车削过程中,外圆车刀与工件进行切削接触,刀具
刃口上的芯片被切削掉,同时也能够提高工件的精度和表面质量,达
到理想的加工要求。
外圆车刀的使用也具有一定的技巧,需要注意以下几点:
1.选用合适的刀片:不同的工件加工,需要选择不同的刀片。
例如,处理较硬的钢材时应选用更硬度更高的刀片;处理薄板时应选用
较薄的刀片等。
2.刀片的角度:刀片的安装应符合规定角度和位置,以确保加工
表面精度和工具寿命。
3.加工条件:选择合适的加工速度、进给量和切削深度是保证外
圆车刀正常运转的关键。
加工速度过快会导致刀具磨损加快,加工质
量下降;进给量过大会导致刀具振动,进而影响加工表面质量;切削
深度过大也容易导致刀具受损。
4.刀具保养:外圆车刀的保养非常重要,切削前需要做好刀具检查,确保无损伤、松动现象;切削结束后要及时清理,以免污染加工表面。
在实际应用中,外圆车刀是一种高效、实用且不可或缺的切削工具。
随着科技的进步,外圆车刀也在不断改进,以适应更加复杂、精细的加工需求。
未来,外圆车刀将更加精进,成为更加智能化、高效的加工工具,为制造业的发展带来更大贡献。
车刀种类和角度选择原则详解
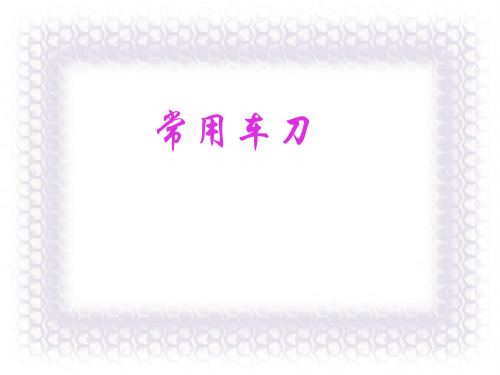
车刀不对准工件中心对角度的影响
五、车刀刃磨
无论硬质合金车刀(焊接)或高速钢 车刀,在使用之前都要根据切削条 件所选择的合理切削角度进行刃磨 ,一把用钝了的车刀,为恢复原有 的几何形状和角度,也必须重新刃 磨。
重 要 性
三分手艺、七分刀 徒弟的手、师傅的刀
1.磨刀步骤(图a~d)
⑴磨前刀面 把前角和刃倾角磨正确。 ⑵磨主后刀面 把主偏角和主后角磨正确。 ⑶磨副后刀面 把副偏角和副后角磨正确。 ⑷磨刀尖圆弧 圆弧半径约0.5~2mm左右。 ⑸研磨刀刃 车刀在砂轮上磨好以后,再用油石加些机油研磨车 刀的前面及后面,使刀刃锐利和光洁。这样可延长车刀的使用寿命。 车刀用钝程度不大时,也可用油石在刀架上修磨。硬质合金车刀可 用碳化硅油石修磨。
前角γo
——在主切削刃选定点的正交平面po内, 前刀面与基面之间的夹角
。
后角αo
——在正交平面po内,主后刀面与切削 平面之间的夹角。
主偏角κr
——主切削刃在基面上的投影与进给方 向的夹角。
刃倾角λs ——在切削平面ps内,主切削刃与 基面pr的夹角。
其他角度:
副前角γoˊ、 副后角αoˊ、 副偏角κrˊ、 刃倾角λsˊ
3.主偏角、副偏角的选择 (1)主偏角的选择 A、主偏角κr的增大或减小对切削加工有利的一 面 在背吃刀量ap与进给量f 不变时,主偏角κr减小 将使切削厚度hD减小,切削宽度bD增加,参加 切削的切削刃长度也相应增加,切削刃单位长度 上的受力减小,散热条件也得到改善。 主偏角κr减小时,刀尖角增大,刀尖强度提高, 刀尖散热体积增大。 所以,主偏角κr减小,能提高刀具耐用度。
(4)良好的工艺性和经济性
车刀的牌号及对应用途

车刀的牌号及对应用途车刀是一种用于车削加工的刀具,广泛应用于各种机械制造领域。
根据不同的加工要求和材料特性,车刀有多种不同的牌号和对应的用途。
下面将介绍几种常见的车刀牌号及其对应的应用领域。
1. TCMT(三角形刀片)TCMT刀片是一种常见的车刀,以其高效的切削性能和较长的使用寿命而受到广泛应用。
TCMT刀片的主要应用领域包括钢、铸铁、不锈钢、高温合金等材料的外圆车削和切槽加工。
其特点是刃翼角度合适,切削力稳定,可实现较高的切削速度,提高生产效率。
2. CCMT(菱形刀片)CCMT刀片是一种常用的车削刀片,适用于钢材、铸铁、不锈钢等材料的内外圆车削、切槽和纵切加工。
CCMT刀片具有较好的刚性和切削刃的稳定性,刃翼角度适中,可实现较高的切削深度和切削速度。
3. CNMG(菱形刀片)CNMG刀片是一种常见的车刀,适用于钢材、铸铁、不锈钢等材料的外圆车削和切槽加工。
CNMG刀片具有较强的硬度和刚性,可在较高的切削速度下实现较大的切削深度和切削力。
4. VNMG(菱形刀片)VNMG刀片是一种适用于加工铸件、钢铁和不锈钢的车刀刀片。
VNMG刀片具有较大的刃翼角度和较高的刚性,适合进行加工粗糙度要求较高的零件,如汽车发动机缸套等。
5. WNMG(菱形刀片)WNMG刀片是一种适用于加工钢、不锈钢和铸铁的车刀刀片。
WNMG刀片具有较大的刃翼角度和较高的刚性,适合进行中等加工精度要求的零件车削加工。
此外,还有其他一些牌号的车刀也有各自的应用领域,如:SNMG(正六角刀片)适用于加工高温合金和钢材,TNMG(三角形刀片)适用于加工铸件、钢材和不锈钢等。
综上所述,车刀的牌号和用途是根据不同的材料和加工要求而确定的。
不同牌号的车刀具有不同的刃翼角度、刚性和硬度等特点,可以满足不同工件加工的需求。
在选择车刀时,需要根据具体的加工工艺要求和材料特性来选择合适的车刀牌号,以提高加工效率和产品质量。
刀片的选择

1.影响数控刀具选择的因素在选择刀具的类型和规格时,主要考虑以下因素的影响:(1)生产性质在这里生产性质指的是零件的批量大小,主要从加工成本上考虑对刀具选择的影响。
例如在大量生产时采用特殊刀具,可能是合算的,而在单件或小批量生产时,选择标准刀具更适合一些。
(2)机床类型完成该工序所用的数控机床对选择的刀具类型(钻、车刀或铣刀)的影响。
在能够保证工件系统和刀具系统刚性好的条件下,允许采用高生产率的刀具,例如高速切削车刀和大进给量车刀。
(3)数控加工方案不同的数控加工方案可以采用不同类型的刀具。
例如孔的加工可以用钻及扩孔钻,也可用钻和镗刀来进行加工。
(4)工件的尺寸及外形工件的尺寸及外形也影响刀具类型和规格的选择,例如特型表面要采用特殊的刀具来加工。
(5)加工表面粗糙度加工表面粗糙度影响刀具的结构形状和切削用量,例如毛坯粗铣加工时,可采用粗齿铣刀,精铣时最好用细齿铣刀。
(6)加工精度加工精度影响精加工刀具的类型和结构形状,例如孔的最后加工依据孔的精度可用钻、扩孔钻、铰刀或镗刀来加工。
(7)工件材料工件材料将决定刀具材料和切削部分几何参数的选择,刀具材料与工件的加工精度、材料硬度等有关。
2.数控刀具的性能要求由于数控机床具有加工精度高、加工效率高、加工工序集中和零件装夹次数少的特点,对所使用的数控刀具提出了更高的要求。
从刀具性能上讲,数控刀具应高于普通机床所使用的刀具。
选择数控刀具时,首先要应优先选用标准刀具,必要时才可选用各种高效率的复合刀具及特殊的专用刀具。
在选择标准数控刀具时,应结合实际情况,尽可能选用各种先进刀具,如可转位刀具、整体硬质合金刀具、陶瓷刀具等。
在选择数控机床加工刀具时,还应考虑以下几方面的问题:(1)数控刀具的类型、规格和精度等级应能够满足加工要求,刀具材料应与工件材料相适应。
(2)切削性能好。
为适应刀具在粗加工或对难加工材料的工件加工时能采用大的背吃刀量和高进给量,刀具应具有能够承受高速切削和强力切削的性能。
车刀的分类和选择

车刀的分类和选择车刀是机械车床上常用的切削工具之一,它对加工效率和加工质量都有重要影响。
选择适合的车刀分类和类型对于提高加工效率、降低切削成本至关重要。
本文将介绍车刀的分类和选择方法,帮助读者更好地理解和应用车刀。
一、车刀的分类根据车刀的结构和用途,可以将车刀分为以下几类:1. 工具刀片:广义上的车刀,通常由刀柄和刀片组成。
刀柄负责固定刀片,刀片进行切削工作。
工具刀片多用于外圆和内圆粗加工,适用于不同材料的车削操作。
2. 特殊刀片:用于特殊形状的车削。
如内外圆刀片、角刀片等。
特殊刀片适用于需要切削复杂外形的工件,提供更好的切削质量和加工精度。
3. 超硬刀片:采用高硬度材料制成的刀片,如金刚石、立方氮化硼等。
超硬刀片具有较高的硬度和耐磨性,适用于加工硬质材料如铸铁、合金钢等。
4. 镗刀:用于车削大孔径和参考表面。
镗刀采用特殊设计,能够提供更高的刚性和稳定性,适用于大直径工件和高精度加工。
5. 切断刀片:用于切断工件的刀片,有直刃和曲刃两种形式。
切断刀片适用于金属材料的切割,如车削工件的分离和切除。
二、车刀的选择选择适合的车刀是提高车削加工效率的关键。
以下是选择车刀时应考虑的因素:1. 加工材料:根据工件材料的不同,选择不同材质和刀片类型的车刀。
对于铸铁、不锈钢等材料,可选择高速钢刀片;对于合金钢、钛合金等硬材料,应选择超硬刀片。
2. 加工工艺:根据不同的车削工艺,选择合适的车刀类型。
对于粗车、精车和薄层车削等工艺,可以选择不同切削参数和刀片结构的车刀。
3. 切削条件:根据切削深度、进给速度和切削速度等切削条件,选择适合的刀片形状和材料。
对于大切削深度和高切削速度的加工,应选择具有高硬度和耐磨性的刀片。
4. 加工精度:根据对加工精度的要求,选择合适的刀片精度和结构。
如果需要高精度的加工,应选择刀片精度高、几何形状复杂的刀片。
5. 经济性:根据加工成本和刀具寿命,选择经济合理的车刀。
应选用具有长寿命和更换成本低的刀具,以优化切削成本。
车刀图解

刀杆的形状、尺寸及选择
刀杆:45钢 截面形状:矩形、正方形、圆形。常用矩形。 矩形和方形刀杆的截面尺寸,一般按机床中心高选取。 刀头尺寸:刀头有效长度l、刀尖偏距m
刀槽的形状、 刀槽的形状、尺寸及选择
刀槽形状:通式、半封闭式、封闭式、切口式
2.2 机夹式车刀
结构比较复杂 常用的两种结构形式:上压式、侧压式 上压式 多用螺钉和压板从上向下施力压紧刀片,结构简 单,使用方便可靠。 侧压式 利用楔形块和螺钉从刀片侧面将刀片压紧,刀片 上无障碍,排屑顺畅。
h = R ⋅ sin(γ + α ) 重磨前刀面时,必须保持h不变。为便是控制, H = R ⋅ sin α 刀具两端面上刻有刃磨检验园。半径(mm) 式中:R — 圆体成形车刀最大外圆
c 1 f f 1 f
钢料:rf=5°~10°,抗拉强度高的取小值,反之取大值; 铸铁: rf=0°~10°,硬度高的取小值,反之取大值; 成形车刀的后角取决于其种类。圆体形车刀:αf=10º ~12º 棱体形车刀:αf=12º ~15º
成形车刀的类型
按外形和结构分: 平体成形车刀 切削刃为成形刃,其它与普通刀具结构相似 棱体成形车刀 外形棱柱体,刚性好,寿命长 圆体成形车刀 带有刀孔的回转体 按进给方向分:进向成形车刀、切向成形车刀
成形车刀的前角、后角
成形车刀切削刃形状复杂,有直线部分,也有曲线部分, 各段的主剖面方向互不相同,为简便起见,规定:成形车 刀的前角、后角均在假定工作平面内度量,并以切削刃上 最外一点(工件上半径最小处的点)的侧前角、侧后角作 为刀具的名义前角、后角。 前角、后角的形成 只刃磨前刀面,预先磨出一定的角度,再相对工件装 夹成一定位置,分别形成需要的前角、后角。
2.3 可转位车刀
车刀片的选择

车刀片的选择2010-4-23 16:21:00 来源:精威深机械阅读:64次我要收藏【字体:大中小】车外圆的刀片:选用原则主要是根据加工工艺的具体情况决定。
一般要选通用性较高的及在同一刀片上切削刃数较多的刀片。
粗车时选较大尺寸,精、半精车时选较小尺寸。
S形:四个刃口,刃口较短(指同等内切圆直径),刀尖强度较高,主要用于75°、45°车刀,在内孔刀中用于加工通孔。
T形:三个刃口,刃口较长,刀尖强度低,在普通车床上使用时常采用带副偏角的刀片以提高刀尖强度。
主要用于90°车刀。
在内孔车刀中主要用于加工盲孔、台阶孔。
C形:有两种刀尖角。
100°刀尖角的两个刀尖强度高,一般做成75°车刀,用来粗车外圆、端面,80°刀尖角的两个刃口强度较高,用它不用换刀即可加工端面或圆柱面,在内孔车刀中一般用于加工台阶孔。
R形:圆形刃口,用于特殊圆弧面的加工,刀片利用率高,但径向力大。
W形:三个刃口且较短,刀尖角80°刀尖强度较高,主要用在普通车床上加工圆柱面和台阶面。
D形:两个刃口且较长,刀尖角55°刀尖强度较低,主要用于仿形加工,当做成93°车刀时切入角不得大于27°~30°;做成62.5°车刀时,切入角不得大于57°~60°,在加工内孔时可用于台阶孔及较浅的清根。
V形:两个刃口并且长,刀尖角35°刀尖强度低,用于仿形加工。
做成93°车刀时切入角不大于50°;做成72.5°车刀时切入角不大于70°;做成107.5°车刀时切入角不大于35°。
切槽刀片:一般切深槽用切断刀片,切浅槽用成型刀片,如以下几种:立装切槽刀片、平装切槽刀片、条状切槽刀片、清台阶圆弧根槽刀片,这些刀片切出的槽宽精度较高。
螺纹刀片:常用的是L形,这种刀片可重磨,价格也便宜,但不能切牙顶。
车刀的选择
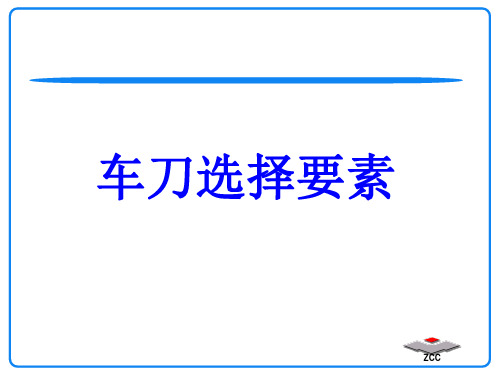
普通钢刀杆作内孔镗削刀杆最大悬伸为 4倍杆径,做内螺纹车削为3倍杆径,做 内槽与仿形加工为2倍杆径,超出会有 振动发生;
刀杆悬伸在4倍到7倍杆径时,可以使用 重金属刀杆或者整体硬质合金刀杆,
ZCC
选择切削参数
要考虑的因素
刀具寿命 工件材料类型,状态和硬度 刀片牌号和几何槽型 有关机床功率、主轴转速和稳定性等方面的能力 产生切削热及积屑瘤的倾向 有关断续切削和振动方面的加工状况 切削控制和表面粗糙度
ZCC
ZCC
选择刀杆类型、尺寸及刀片形状
ZCC
选择刀杆类型、尺寸及刀片形状
Kn min=5o
ZCC
选择刀杆类型、尺寸及刀片形状
大
小 小 机床刚性差 细长工件 稳定连续切削 精加工
Kr 刀刃强度 要求功率
应用
小 大
大 机床刚性好 粗短工件 粗加工 、硬材料
ZCC
选择刀杆类型、尺寸及刀片形状
选择尽可能最大的刀杆尺寸以提供最好的稳定 性和强度
•如果有震动倾向,选择小的刀尖半径。 •对于粗加工,常用的半径为R1.2-1.6.
经验法则 F粗=0.5X刀尖半径
精加工时
•可根据公式计算出合适的r值,或r选定时, 计算出f值。 •不宜选择过大的刀尖圆弧半径。
Ry=(fn2 /8r)X1000
ZCC
镗刀杆的选择
基本原则
选择尽可能大的直径 选择尽可能小的镗杆悬伸 选择刚性尽可能大的夹紧,以
车刀选择要素
ZCC
车刀选择的主要因素
刀具的夹持方法 刀杆类型、尺寸及刀片形状 刀片几何槽型和牌号 刀片尺寸 刀尖圆弧半径 切削参数 经济性及产量
刀具合理几何参数的选择

刀具的几何参数包括刀具的切削角度,刀面的形式(如平前刀面,带卷屑断屑槽的前刀面、波形刀面等)以及切削刃的形状(直线形、折线形、圆弧形等)。
刀具的几何参数对切屑变形、切削力、切削温度和刀具磨损都有显著影响,从而影响切削加工生产率、刀具耐用度、加工质量和加工成本。
刀具的合理几何参数.是指在保证加工质量的前提下,能够获得最高刀具耐用度,从而能达到提高切削效率,降低加工成本目的的几何参数。
选择刀具合理几何参数主要取决于工件材料、刀具材料、刀具类型,也与切削用量、工艺系统刚性和机床功率等因素有关。
第一节前角及前刀面形状的选择一、前角的功用及选择前角是刀具上重要的几何参数之一,它的大小决定切削刃的锋利程度和强固程度,直接影响切削过程。
前角有正前角和负前角之分。
取正前角的目的是为了减小切屑被切下时的弹塑性变形和切屑流出时与前面的摩擦阻力,从而可减小切削力和切削热,使切削轻快,提高刀具寿命,并提高已加工表面质量。
但前角过大时,楔角过小,会削弱切削刃部的强度并降低散热能力,反而会使刀具寿命降低。
由图可知,加工不同材料时,前角太大或太小,刀具耐用度都较低。
在一定加工条件下,存在一个耐用度为最大的前角,即合理前角。
取负前角的目的在于改善刃部受力状况和散热条件,提高切削刃强度和耐冲击能力。
负前角刀具通常在用脆性刀具材料加工高强度高硬度工件材料而当切削刃强度不够、易产生崩刃时才采用。
前角的合理数值选取原则刀具合理前角的选择主要取决于刀具材料、工件材料的种类与性质:1.刀具材料:强度和韧性较高时可选择较大的前角。
高速钢的强度高,韧性好;硬质合金脆性大,怕冲击,易崩刃。
因此,高速钢刀具的前角可比硬质合金刀具选得大一些,可大5°~10°。
陶瓷刀具的脆性更大,故前角应选择得比硬质合金还要小一些。
选择要充分注意增加切削刃强度,常取负值(多在-4°~-15°范围)以改善刀具受力时的应力状态,并选负的刃倾角(取0°~-10°)与之配合以改善切入时承受冲击的能力。
浅谈如何合理选择及使用数控车刀刀片

备如果不选用跟它匹配的刀具、刀片, 它也发挥不出它应有的性能。有了匹配的刀具, 还要用合理的参数进行加工。这样才能发挥机床 的性能, 争取最大的效
益, 本文 针对 如 何正 确 了解 和 使用 数控 的现 代化 车 刀刀 片进 行 了详 尽 的论述 。 [ 词] 关键 数控 车削 加 工材料 刀 片材质 切 削参 数 切 削速度 相应措 施 中图分类 号 :G5 T6 9 文 献标识 码 : A 文章编 号 :099 4 2 1) 30 1— 2 10 — 1X(00 0 —1 20
刀片的掼伤状描麓况刀其材料切削蘩件刀兵参敷降佳协劓毫度丈暑后砸量惯位带性蔓好曲辨辩遗喜毫夫辩麓膏太刀虫举赴铸避嚣协聃性麓好舫羹鼻稿略彘研村毫度太麓前面膏掼琶用射一性鼍虾的研辩最小毫络量遗霉鼍亳的刀片旰量佳埘削毫度量太麓撮度量横鼍麻琳诖蔓婷的辩蕞小蠢蛤量天囊蕞小麓硪小遵培量蛙高纛虞埘劓刀矗曩糟丈囊刀位席锅性曩妊辩知太斛擒蕞小切撵太套囊量丘犬刀辑叶蕞小麓膏哦小迓拾遗辱高甓度切舯再曩一糟小囊玎龅蔫栩性好的向太斛按降低饼州毫度太夯靛期大刀辩叶蕞十者培量蕞十麓膏剽落使用栩缝蔓好豹舯辩者夫盘太斛援睁俄埘劓蠢度太屠角蕞小蠢鳍蔓大麓囊塑性变形龅用甜挂蔓好的埘辩罐小嚣虫任半桎蕞小忻蒜翩挎却蕞小囊稿建量埘挂囊妊的刀片一蠢蹙用与触芏褂辩囊翱餐矗埘啊连度丈麓熔敷力小豹增大连始矗研村性蠢好的刀斗夤蠢膏慑切嗣度熟龟裂芷用翻挂量好的村蠢小连络矗霉嘲一谴蠢妊的刀斗纛蠹蠢犬羹囊翩睁柏聩量科技博克物理涂层本涂层以硬质合金做基体用物理涂层方法在基体表面涂上等弱的有害层并能保持涂层前的形状精度也适合整体刀具
如何针对 零件 的材 料选择合 理的刀 片以及正确 使用刀 片, 首先要 了解刀 片 材料 的组 成及相应性 能 : 其次要 了解刀 具的相关 参数 以及 相关 的切削加 工参数 的设 定 : 最后 要根 据 刀具 的实 际磨 损 情况 适 当的 调整 加 工参 数及 加 工条 件 。 本文 针 对 以- 三 方面 进 行论 述 。 上
车削刀具选择

卧式数控车床选刀目录一机卡车刀的选用 (1)二孔加工刀具的选用 (9)三切断和切槽刀 (12)四螺纹车刀 (13)五刀具材料 (16)六刀具厂商 (17)七刀具干预图 (18)八刀具允许的最大转动惯量 (19) (21)数控车床刀具系统比卧车复杂。
要求安装数量多,安装可靠,自动换刀,装卸方便迅速还要求切削时间短以提高生产率。
因此普遍采用机卡车刀。
机卡车刀是把压制有合理的几何参数,在一定的切削用量范畴内保证卷屑,断屑并有几个刀刃的刀片,用机械卡固方式装卡在标准刀体上的一种新型刀具。
它防止了硬质合金刀片在焊接中产生的种种不良后果,因此能充分发挥刀片材料原有的切削性能,提高了车刀的耐用度和切削加工的生产率.另外刀体可重复使用,能节约大量制造刀体的钢材.还便于使刀具标准化和集中生产,同一型号刀片的几何形状较一致切削效果稳定.有利于提高零件加工质量,简化了刀具的管理工作.使用时,当刀刃磨损后,只需松开卡紧机构将刀片转一个角度,不必重磨,大大缩短了换刀.磨刀.装刀的辅助时间,而且可以防止刀片由于重磨而造成的缺陷.因此机卡车刀也叫不重磨车刀或可转位车刀。
除不可防止的情况外,为用户选用的都应该是机卡车刀。
一机卡车刀的选用侧重外外表车刀的选用。
内孔车刀大体相同,其特殊性问题另做表达。
ISO对外外表车刀型号是如下表示的,它是国内外刀具厂商的统一标准。
选刀工作也就是确定型号中的各项内容,按选刀时考虑问题的大体顺序分叙如下:(一)刀片形状的选择:外内外表车刀刀片形状关系车刀类型,它取决于加工部位的形状,是选刀的最重要内容。
它主要涉及刀具的主偏角,刀尖角和有效刃数等。
一般来讲刀尖角愈大刀尖强度愈高,应尽量采用。
但刀尖角小干预现象少,适用于复杂型面,开挖沟槽及下坡的型面。
刀片形状甚多,某些厂家列出十几种,本厂实际只用过图1所示七种,也正是ISO规定的七种基本类型。
图1 图280°菱型刀片C,目前是我厂选用最多的。
车刀参数资料[大全]
![车刀参数资料[大全]](https://img.taocdn.com/s3/m/e416a3d54128915f804d2b160b4e767f5acf8012.png)
车刀参数资料车刀种类和用途车刀是应用最广的一种单刃刀具。
也是学习、分析各类刀具的基础。
车刀用于各种车床上,加工外圆、内孔、端面、螺纹、车槽等。
车刀按结构可分为整体车刀、焊接车刀、机夹车刀、可转位车刀和成型车刀。
其中可转位车刀的应用日益广泛,在车刀中所占比例逐渐增加。
二、硬质合金焊接车刀所谓焊接式车刀,就是在碳钢刀杆上按刀具几何角度的要求开出刀槽,用焊料将硬质合金刀片焊接在刀槽内,并按所选择的几何参数刃磨后使用的车刀。
三、机夹车刀机夹车刀是采用普通刀片,用机械夹固的方法将刀片夹持在刀杆上使用的车刀。
此类刀具有如下特点:(1)刀片不经过高温焊接,避免了因焊接而引起的刀片硬度下降、产生裂纹等缺陷,提高了刀具的耐用度。
(2)由于刀具耐用度提高,使用时间较长,换刀时间缩短,提高了生产效率。
(3)刀杆可重复使用,既节省了钢材又提高了刀片的利用率,刀片由制造厂家回收再制,提高了经济效益,降低了刀具成本。
(4)刀片重磨后,尺寸会逐渐变小,为了恢复刀片的工作位置,往往在车刀结构上设有刀片的调整机构,以增加刀片的重磨次数。
(5)压紧刀片所用的压板端部,可以起断屑器作用。
四、可转位车刀可转位车刀是使用可转位刀片的机夹车刀。
一条切削刃用钝后可迅速转位换成相邻的新切削刃,即可继续工作,直到刀片上所有切削刃均已用钝,刀片才报废回收。
更换新刀片后,车刀又可继续工作。
1.可转位刀具的优点与焊接车刀相比,可转位车刀具有下述优点: (1)刀具寿命高由于刀片避免了由焊接和刃磨高温引起的缺陷,刀具几何参数完全由刀片和刀杆槽保证,切削性能稳定,从而提高了刀具寿命。
(2)生产效率高由于机床操作工人不再磨刀,可大大减少停机换刀等辅助时间。
(3)有利于推广新技术、新工艺可转位刀有利于推广使用涂层、陶瓷等新型刀具材料。
(4)有利于降低刀具成本由于刀杆使用寿命长,大大减少了刀杆的消耗和库存量,简化了刀具的管理工作,降低了刀具成本。
2.可转位车刀刀片的夹紧特点与要求(1)定位精度高刀片转位或更换新刀片后,刀尖位置的变化应在工件精度允许的范围内。
如何选择刀具和切削参数
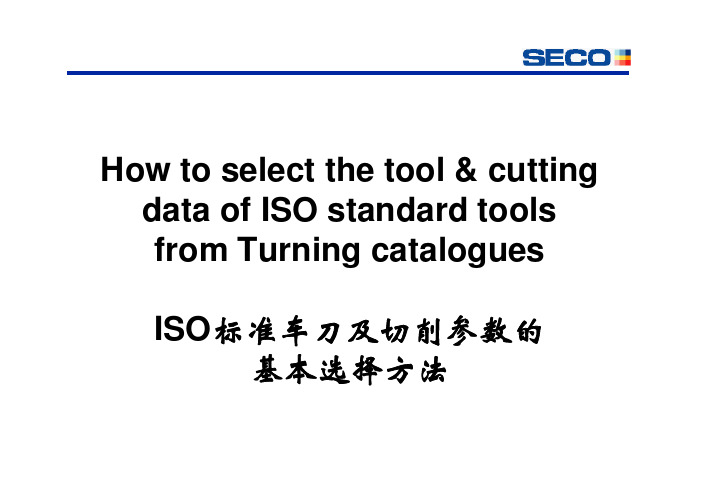
205
6:依切削参数的优化 • 根据刚才选择的刀片,您可以很方便地选得适用的切削参数推荐值。 线速度Vc=200m/min,每齿进给fz=0.25mm/z,因为刀盘直径我们已 经知道是D=100mm,所以转速N=636rpm,刀盘齿数为Z=7,所以实 际的工作进给量F=636*7*0.25=1110mm/min。 实际每转的进给量为Fr=7*0.25=1.75mm>1.5mm的修光刃实际有效 宽度,所以可以预计加工的光洁度不是很好,要提高光洁度您认为应 该采用什么措施? 正确的办法应该是加用修光刃刀片而不是简单地降低每齿进给量。
Plunging Plunging 插铣 插铣
3:确定最适合的首选刀片 • 如我们以加工45钢为例,即山高第4组材料,根据被加工材料在样本的 相应组别中您可以非常容易地找到首选刀片的推荐。 XOMX090308TR-ME06 T350M
4:您也可以在样本中了解 到有关刀盘的其它信息
• 这些信息包括: 刀盘的有效工作直径、杆式 刀的柄直径、刀盘高度、齿 数、重量、盘式刀盘安装孔 径、备用板手、适用的刀柄 规格、安全最大切深等等。
1:确定被加工工件的材料组别 • 依据国际ISO标准的规定,常见的 工件材料被分为六类: 钢件类(P类)--山高组别1-6 不锈钢类(M类)--山高组别7-11 铸铁类(K类)--山高组别12-15 有色金属类(N类)--山高组别16-17 耐热合金类(S类)--山高组别20-22 淬硬钢类(H类)--山高组别7 我们最常用的45号钢为第3 组材料,不 锈钢( 316 )属于第9组材料,铸铁HT25 ( GG25 )属于第12组, 铝合金属于第 16组,钛合金( Ti6Al4V )属于20组,镍 基合金( 718 )属于第22组。
数控机床刀具的选择

第二章数控机床刀具的选择机械加工自动化生产可分为以自动生产线为代表的刚性专用化自动生产和以数控机床为主的柔性通用化自动生产。
就刀具而言,在刚性专用化自动生产中,是以提高刀具专用复合化程度来获得最佳经济效益的。
而在柔性自动化生产中,为适应随机多变加工零件的需求,尽可能通过提高刀具及其工具系统的标准化、系列化和模块化程度来获得最佳经济效益。
本章简述对数控刀具的特殊要求:车削类、镗铣类数控刀具系统;刀具预调、磨损与破损的自动监测。
2.1 对数控刀具的要求刀具的选择是数控加工工艺中的重要内容之一,它不仅影响机床的加上效率,而是直接影响加上质量。
编程时,选择刀具通常要考虑机床的加工能力、工序内容、工件材料等多方面的因素。
以数控机床为主的柔性自动化加工是按预先编好的程序指令自动地进行加工。
应适应加工品种多、批量小的要求,刀具除应具备普通机床用刀具应有的性能外,还应满足下列要求:1)刀具切削性能应稳定可靠,避免刀具过早地损坏,而造成频繁地停机。
由于刀具和工件材料性能的分散性,以及刀具制造工艺和工作条件控制不言,有相当一部分刀具的切削性能远低于平均性能,使刀具切削性能稳定可靠性差。
因此必须严格控制刀具材料的质量,严格贯彻刀具制造工艺,特别是热处理和刃磨工序。
严格检查刀具质量,确保刀具切削性能稳定可靠。
2)刀具寿命应有较高的寿命。
应选用切削性能好、耐磨性高的涂层刀片以及合理地选择切削用量。
3)保证可靠地断屑、卷屑和排屑。
加工时,应不产生紊乱的带状切屑,缠绕在刀具、工件上;不易断屑的刀具应保证切屑顺利的卷曲和排出;避免形成细碎的切屑;精加工是切屑不划伤已加工表面;切屑流出时不妨碍切削液浇注。
为了确保可靠地断屑、卷屑和排屑,可采取一下措施:合理选用可转位刀片的断屑槽槽形;合理地调整切削用量;在刀体中设置切削液通道,将切削液直接输送至切削区,有助于清除切屑;利用高压切削液强迫断屑。
4)能快速地换刀或自动换刀。
5)能迅速、精确地调整刀具尺寸。
车刀基本知识介绍(全)
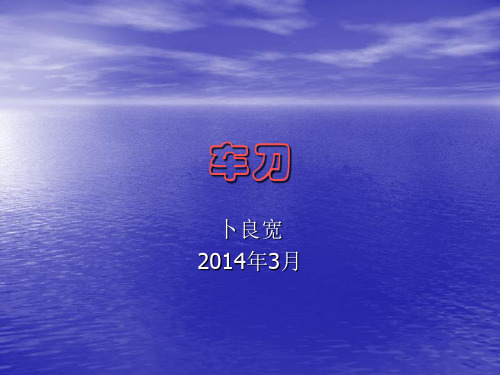
• 2,后角α0的作用是减小后刀面与工件之间的摩
擦,影响刀刃的强度和锋利程度. 后角的选择:粗车时,切削深,进给快,要求车刀有足 够的强度,应选择较小的后角.精车时,为减小后刀 面与工件过渡表面的摩擦,保持刃口的锋利,应选 较大的后角.切削力较大时,应选取较小的后角. 加工塑性材料时后角取大一些,加工脆性材料时后 角取小些.高速钢车刀的后角一般可6°--12°,硬 质合金钢车刀可取2--12.粗车时,后角一般取3°-6°;精车时,后角一般取6°--12°.
• 以上即是俗称的车刀切削部分的“三面两
刃一尖”。其组成如下:
4、车刀的角度的主要作用及选择原则
• 1,前角γ0的作用是减小切屑的变形,增大前角可使车刀
刃口锋利,减小切削力,降低切削温度,但过大前角会使 刀刃的散热条件变差,刃口强度降低,易崩刃 前角的选择:前角选择的原则是在刀具强度允许的情况 下,尽量选取较大的前角(锐中有固). 前角的大小与刀具材料,切削工作条件及被切材料有关. 切削塑性材料时,一般取较大的前角;切脆性材料时,一 般取较小的前角.当切削有冲击时,前角应取小值,甚至 取负角.硬质合金车刀的前角一般比高速钢车刀的前角 要小.加工材料由硬到软,对于高速钢车刀,前角可取 5°--30°;对于硬质合金钢车刀,前角一般取-15°-30°.
二、车刀的角度及其初步选择
1、车刀的组成 任何车刀都是由刀头(或刀 片)和刀体两部分组成的。刀头担负切削 工作,又叫切削部分。刀体用来装夹到车 床刀架上。
刀头是由若干个刀面和切削刃组成 (如下图)
(1)前刀面 :切削时,切屑流出所经过表 面。 (2) 后刀面 :分主后刀面和副后刀面。主 后刀面与工件过渡表面相对的刀面;副后 刀面与已加工表面相对的刀面。 (3 )主切削刃:前后刀面的交线,担负主 要的切削工作,也称主切削刃或主刀刃; (4)副切削刃:前面与副后刀面的交线, 配合切削刃完成切削工作,并形成已加工 表面,也称副刀刃; (5)刀尖:主副刀刃的交点,它可以是一个 点、直线或圆弧。
车刀刀片的槽型选择及刀杆选择

1、车刀刀杆的选用 2、车刀刀片槽型的选用
车刀刀杆的选用
1、车刀的分类(按车削类型):
外圆车刀
内孔车刀
2、车刀的分类(按加工类型):
粗车
半精车
精车
外圆刀
外圆刀选用时注意事项
1、车床的类型 :
根据不同才车床类型选用不同的刀杆
2、加工类型:
区分粗加工和精加工,粗加工时尽量选用CN
或WN型刀杆(特别是重型切削,切削力量大),
刀杆上压紧刀片的方式一般采用E型压紧或是犀牛
刀的形式,小型机床的粗加工也可以考虑TN刀杆。
精加工一般各种刀杆都通用,主要在选刀片上。
特殊情况
1、有些客户在加工过程中必须要用到外圆刀尖在外圆 面上挖不规则形状或是出现干涉(凸圆弧),必须使 用尖刀(如装VN刀片型刀杆EVQNR-2525M16)
2、注意在加工过程中有的必须用反刀
刀具干涉,要用到反刀
外圆刀需要向工件外圆面 上进刀
内孔刀
内孔刀选用时注意事项
1、内孔孔径的大小 内孔的都有一个 最小加工直径,要加工的孔径必须大 于内孔刀的最小加工直径
2、有些产品是外边孔大,里边还有个 小孔(台阶孔),过渡面还必须是平 面的话,选用时一定要注意选用的内 孔刀的最小加工直径必须小于里边小 孔的直径,只有这样才最安全
2、半精车和精车 负型刀片,槽型有 FA EA FG等,刀尖圆弧一般都比较 小;正型刀片一般只用于半精车和精 车,根据不同材料选用不同的槽型
刀片材质的选用
根据加工材料的材质特性选用应 材质的刀片
注:PCD刀片不能加工含碳的材 料,因为PCD刀片的材质就是 碳晶体
车刀的选择、进给路线选择

课时授课教案/ 学年第期课程名称:数控加工工艺授课班级:(三专)数控01-1、2授课时间:第周星期第节课题:车刀的选择、进给路线选择教学目的:掌握刀具的选择了解进给路线选择掌握切削用量的选择重点、难点:车刀的选择、进给路线选择使用教具:课件课后作业: 1课后记录:年月日授课主要内容一、刀具的选择1.车刀和刀片的种类由于工件材料、生产批量、加工精度以及机床类型、工艺方案的不同,车刀的种类也异常繁多。
根据与刀体的联接固定方式的不同,车刀主要可分为焊接式与机械夹固式两大类。
l)焊接式车刀将硬质合金刀片用焊接的方法固定在刀体上称为焊接式车刀。
这种车刀的优点是结构简单,制造方便,刚性较好。
缺点是由于存在焊接应力,使刀具材料的使用性能受到影响,甚至出现裂纹。
另外,刀杆不能重复使用,硬质合金刀片不能充分回收利用,造成刀具材料的浪费。
根据工件加工表面以及用途不同,焊接式车刀又可分为切断刀、外圆车刀、端面车刀、内孔车刀、螺纹车刀以及成形车刀等。
2)机夹可转位车刀如图所示,机械夹固式可转位车刀由刀杆l、刀片2、刀垫3以及夹紧元件4组成。
刀片每边都有切削刃,当某切削刃磨损钝化后,只需松开夹紧元件,将刀片转一个位置便可继续使用。
焊接式车刀的种类1—切断刀2—90°左偏刀3—90°右偏刀4—弯头车刀5—直头车刀6—成形车刀7—宽刃精车刀8—外螺纹车刀9—端面车刀10—内螺纹车刀11—内槽车刀12—通孔车刀13—盲孔车刀机械夹固式可转位车刀的组成1—刀杆2—刀片3—刀垫4—夹紧元件刀片是机夹可转位车刀的一个最重要组成元件。
按照国标GB2076-87,大致可分为带圆孔、带沉孔以及无孔三大类。
形状有:三角形、正方形、五边形、六边形、圆形以及菱形等共17种。
图示为常见的几种刀片形状及角度。
2.车刀类型和刀片的选择1)数控车削常用刀具的类型 数控车削用的车刀一般分为三类,即尖形车刀、圆弧形车刀和成型车刀。
(l )尖形车刀 以直线形切削刃为特征的车刀一般称为尖形车刀。
- 1、下载文档前请自行甄别文档内容的完整性,平台不提供额外的编辑、内容补充、找答案等附加服务。
- 2、"仅部分预览"的文档,不可在线预览部分如存在完整性等问题,可反馈申请退款(可完整预览的文档不适用该条件!)。
- 3、如文档侵犯您的权益,请联系客服反馈,我们会尽快为您处理(人工客服工作时间:9:00-18:30)。
Wiper
Optimization
Difficult materials
CP grades
Safety
TP2000
Multi-directional
MDT
High Vc/dry
TP1000
17/18
Questions?
18/18
steel – SS – GCI - etc.
加工方法
roughing - 1/2 rough - finishing
切削速度 Vc
切深 ap
进给 f
刀片材质
刃口形状
优化的刀片
3/18
选择刀片的形态
尽量使用强度最好的刀片(刀具形状决 定)
刀片的强度
刀片的强度 VS 通用性
通用性
4/18
刀片尺寸的选择
6/18
刀片刀尖圆弧的选择
• 提高线速度减小进给可得到小的Ra 。
– 需要合适的刀片: TP1000 , CM… – 不是绝对的: 速度, 工件,振动...
• 提高进给量减小进给可得到小的Ra.
– 使用修光刀片
7/18
刀片刀尖圆弧的选择 修光刀片—大进给量的精加工
(Typical example ) 8/18
钢
ISO-P
不锈钢
ISO-M
铸铁
ISO-K
P01 P10 P20 P30 P40 P50 M10 M20 M30 M40 K01 K10 K20 K30 K40
11/18
Secolor
精加工 普通加工 粗加工
3 种不同的颜色,代表三种加工方法
3 colours to determine the material to be machined
刀片刀尖圆弧的选择
• 高的效率 - wiper
– 半精加工和精加工 – 小的切深
• 好的表面质量 - wiper
– Feed x 2 = the same surface finish – The same feed = Ra / 2
WNHale Waihona Puke G080408W-M39/18
10/18
Secolor, a Seco system (often copied)
刀片的选择
1/18
选择优化的刀片
• 刀片的基本形态是由刀柄的决定的. • 切削刃的几何形状和刀片的材质等级是由加工性质决定的。
- 国际标准的材质决定选择什么样的刀片等几。 - 加工方法(粗加工/精加工)决定刀具刃口形状。 - 切削状态 (ap, f, vc) 是可变的因素
2/18
选择优化的刀片
被加工材料
(Typical example )
f
15/18
Secolor
6
5
4
ap (mm)
3
2
1
0
0,1
0,2
0,3
0,4
0,5
0,6
0,7
f (mm/tr)
(Typical example )
进给量由刃口形状决定,切深由刀具的强度决定,参考此图表 ,正确的选择理想的切削用量。
16/18
Secolor
Finishing
S
V
刀具的形态/尺寸/主偏角决定刀具的最大切深
5/18
刀片刀尖圆弧的选择
参考建议
Internal External Roughing Finishing 0,8 mm 0,4 mm 1,2 mm 0,8 mm
Theoretical
Reality
尽量使用大的刀尖圆弧,它能得到大的进给量,更好的刀尖强度,较好的表面质量. 不利的因素是大的切削力。
Steel ISO P
SS ISO M
Cast iron ISO K
12/18
Secolor
13/18
Secolor
(Typical example )
当刀具寿命较短时,选择更硬的材质 当刀具出现断裂时选择韧性好的材质
14/18
Secolor
ap
Harder Basic Stronger
当切屑很长时选择靠左的槽型。 When there is insert breakage (chips too short), select a chipbreaker geometry to the right of that currently used.