车刀的选择与使用
车刀种类和角度选择原则详解
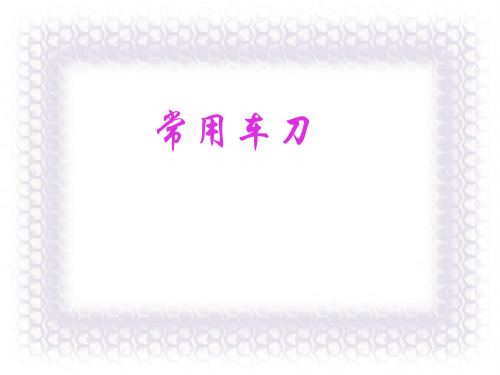
车刀不对准工件中心对角度的影响
五、车刀刃磨
无论硬质合金车刀(焊接)或高速钢 车刀,在使用之前都要根据切削条 件所选择的合理切削角度进行刃磨 ,一把用钝了的车刀,为恢复原有 的几何形状和角度,也必须重新刃 磨。
重 要 性
三分手艺、七分刀 徒弟的手、师傅的刀
1.磨刀步骤(图a~d)
⑴磨前刀面 把前角和刃倾角磨正确。 ⑵磨主后刀面 把主偏角和主后角磨正确。 ⑶磨副后刀面 把副偏角和副后角磨正确。 ⑷磨刀尖圆弧 圆弧半径约0.5~2mm左右。 ⑸研磨刀刃 车刀在砂轮上磨好以后,再用油石加些机油研磨车 刀的前面及后面,使刀刃锐利和光洁。这样可延长车刀的使用寿命。 车刀用钝程度不大时,也可用油石在刀架上修磨。硬质合金车刀可 用碳化硅油石修磨。
前角γo
——在主切削刃选定点的正交平面po内, 前刀面与基面之间的夹角
。
后角αo
——在正交平面po内,主后刀面与切削 平面之间的夹角。
主偏角κr
——主切削刃在基面上的投影与进给方 向的夹角。
刃倾角λs ——在切削平面ps内,主切削刃与 基面pr的夹角。
其他角度:
副前角γoˊ、 副后角αoˊ、 副偏角κrˊ、 刃倾角λsˊ
3.主偏角、副偏角的选择 (1)主偏角的选择 A、主偏角κr的增大或减小对切削加工有利的一 面 在背吃刀量ap与进给量f 不变时,主偏角κr减小 将使切削厚度hD减小,切削宽度bD增加,参加 切削的切削刃长度也相应增加,切削刃单位长度 上的受力减小,散热条件也得到改善。 主偏角κr减小时,刀尖角增大,刀尖强度提高, 刀尖散热体积增大。 所以,主偏角κr减小,能提高刀具耐用度。
(4)良好的工艺性和经济性
阐述车刀各角度的功用和选择原则
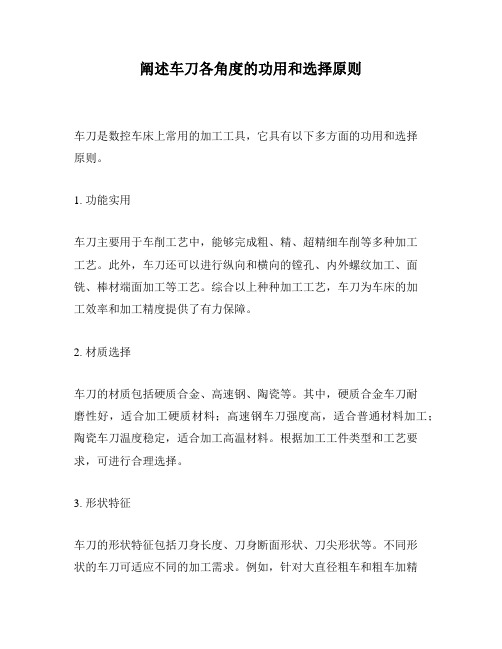
阐述车刀各角度的功用和选择原则
车刀是数控车床上常用的加工工具,它具有以下多方面的功用和选择
原则。
1. 功能实用
车刀主要用于车削工艺中,能够完成粗、精、超精细车削等多种加工
工艺。
此外,车刀还可以进行纵向和横向的镗孔、内外螺纹加工、面铣、棒材端面加工等工艺。
综合以上种种加工工艺,车刀为车床的加
工效率和加工精度提供了有力保障。
2. 材质选择
车刀的材质包括硬质合金、高速钢、陶瓷等。
其中,硬质合金车刀耐
磨性好,适合加工硬质材料;高速钢车刀强度高,适合普通材料加工;陶瓷车刀温度稳定,适合加工高温材料。
根据加工工件类型和工艺要求,可进行合理选择。
3. 形状特征
车刀的形状特征包括刀身长度、刀身断面形状、刀尖形状等。
不同形
状的车刀可适应不同的加工需求。
例如,针对大直径粗车和粗车加精
车可以采用U型车刀,针对横向镗孔可以采用V型车刀等。
4. 刃口类型
车刀的刃口类型包括单刃、双刃、三刃、四刃等。
单刃车刀适合小型工件的高效加工;双刃车刀适合中型工件的加工;三刃和四刃车刀适合大型工件加工,能够提高工件加工效率和加工精度。
综上,根据不同的工件需求和加工工艺,可选择不同材质、形状特征和刃口类型的车刀,以提高车床加工效率和加工质量。
车刀种类和角度选择原则

本课内容
一.常用车刀的种类和用途
二.刀具材料 三.车刀组成 四.车刀的安装
了解
五.车刀的刃磨
六.车刀角度及切削参数的选择
了解
一.常用车刀的种类和用途
1.传统焊接刀具
直头车刀
弯头车刀
75°强力车刀
90°偏刀
切断刀或切槽刀
扩孔刀(通孔)
扩孔刀(不通孔)
螺纹车刀
2.硬质合金可转位(不重磨)车刀
前角γo
——在主切削刃选定点的正交平面po内, 前刀面与基面之间的夹角
。
后角αo
——在正交平面po内,主后刀面与切削 平面之间的夹角。
主偏角κr
——主切削刃在基面上的投影与进给方 向的夹角。
刃倾角λs ——在切削平面ps内,主切削刃与 基面pr的夹角。
其他角度:
副前角γoˊ、 副后角αoˊ、 副偏角κrˊ、 刃倾角λsˊ
硬质合金可转位(不重磨)车刀在现代机械加工中广泛应用,其刀片用机械 夹固式装夹在刀杆上,当刀片一个刀刃磨钝后,只需将刀片转过一个角度,即 可用新的切削刃进行切削,从而大大缩短了换刀和磨刀时间,提高了刀杆的利 用率,节约了成本。
二.刀具材料
1、刀具材料应具备的性能
(1)高硬度和好的耐磨性
刀具材料的硬度必须高于被加工材料的硬度才能切下金属。一般刀具材料的 硬度应在60HRC以上。刀具材料越硬,其耐磨性就越好。
车刀不对准工件中心对角度的影响
五、车刀刃磨
无论硬质合金车刀(焊接)或高速钢 车刀,在使用之前都要根据切削条 件所选择的合理切削角度进行刃磨 ,一把用钝了的车刀,为恢复原有 的几何形状和角度,也必须重新刃 磨。
车刀的选择与使用

关键 词: 车刀 材 料 车7 J / L , 何角度 车刀安装使 用 中图分类号 : T P 2 文献标 识码 : A
文章编号 : 1 6 7 4 —0 9 8 x( 2 0 1 3 ) 0 8 ( c ) 一0 0 2 0 —0 l
“ 三分 手艺 , 七分刀” 。 这句 俗语 很 形 象 的 说 明 了, 在 车床 加 工中, 最 重要 的部 分 是 刀具 。 随着社会的进步, 科 技的发展, 从 普 通 车 床 向精 密 数 控 加 工中 心 的 过 渡 、 越 来 越 多 的 原 材 料种 类 、 越 来 越 高 的 工 件 性 能 要求、 热 处 理 和 激 光 熔 覆 使 原材 料 的 硬 度 翻 倍 增加 。 在 机 床 加 工 过 程 中, 对 刀具 的 要 求 越 来越 高 。 在数 控机床 和普 通车床的使 用、 刀具 的 选 择 和 安 装 中, 碰 见过 很 多的 问题 。 在 翻 阅 书 籍 和请 问 老 师傅 后 , 获得 了很 多 经验 , 在 这里 写 出来 。 与大家共 同学 习, 共 同探讨 , 共同进 步 。
钨钛钻合金 ( 代号 YT) 、 钨 钴 钛合 金 ( 代号 Yw ) 、 钨 钻 铌 合金 ( 代 号Y A) 。 鉴 于 本 单 位 常 用 的 毛 胚 材 料 为 3 0 C r M n Ti 、 4 0 C r 、 2 7 Si M n类 塑 性 材 料 ,热 处 理 后 硬 度 能 达 到 H RC 3 5— 4 5 ( HB 2 4 0 — 3 0 0 ) , 所 以最 常 选 择 的 刀具 是 硬 质 合 金 中的 钨 、 钛、 钻合金 , 即 YT型 。 本 单 位 常 用 的YT1 5 、 Y T3 0 即属 于 钨 钛 钻
车刀的选择

普通钢刀杆作内孔镗削刀杆最大悬伸为 4倍杆径,做内螺纹车削为3倍杆径,做 内槽与仿形加工为2倍杆径,超出会有 振动发生;
刀杆悬伸在4倍到7倍杆径时,可以使用 重金属刀杆或者整体硬质合金刀杆,
推荐采用的夹持方式
非涂层牌号性能源自ZCC选择刀片几何槽型和牌号
YBC
YBD
YC YBM
ZCC
选择刀片尺寸
条件恶劣的工序应考虑选用厚刀片。 如果有效切削刃长度小于切削深度,就应该选择更大的刀
片,或减小切削深度。
ZCC
选择刀片尺寸
ZCC
选择刀尖圆弧半径
选择刀尖半径时要考虑 ---- 粗加工时的强度 ---- 精加工时的表面纹理
YC D 10 1 Y BC 10 1 Y 1D 10 Y 2D 10
2YB 3 5
YB 1C 5 1
YB 2C 15
YB 2 53
Y CB 53 1
YN 1G 5 1 YC D 10 1 YC 0B 1 1
YN G 50 1 Y 1C 0 YN G 51 1
Y 4C 0 Y 2D 10
YC 4 0
切削速度 韧性
车削刀片 T u rn i n g i n se rts
普 通车 削的 常用 切 削速 度和 进给 量 C a r b id e g r a d e s fo rg e n e r a ltu r n in g
01
10
20 钢,铸钢, 长切屑可锻铸铁。
30
80
40
50
10
钢,铸钢
锰钢,
YM20 YM30
ISO-K
1.6 数控车刀的选择与使用解析

2018/10/6
15
“确定刀片的断屑槽型代码或ISO断 屑范围代码”图标如前图所示。ISO标准 按切削深度aP和进给量的大小将断屑范 围分为A、B、C、D、E、F六个区,其中A、 B、C、D为常用区域,WALTER标准将断屑 范围分为图中各色块表示的区域,ISO标 准和WALTER标准可结合使用,如前图所 示。根据选用标准,按加工的切削深度 和合适的进给量来确定刀片的WALTER断 屑槽型代码或ISO分类范围。
2018/10/6 4
2018/10/6
5
1、机床影响因素
“机床影响因素”图标如图所示。为保 证加工方案的可行性、经济性,获得最佳加 工方案,在刀具选择前必须确定与机床有关 的如下因素: (1)机床类型:数控车床、车削中心; (2)刀具附件:刀柄的形状和直径,左切和右 切刀柄; (3)主轴功率; (4)工件夹持方式。
2018/10/6
6
2、选择刀杆
“选择刀杆”图标如图所示。其中,刀杆类 型尺寸见下表。
选用刀杆时,首先应选用尺寸尽可能大的刀杆,同时 要考虑以下几个因素: (1)夹持方式; (2)切削层截面形状,即切削深度和进给量; (3)刀柄的悬伸。
2018/10/6
7
3、刀片夹紧系统
刀片夹紧系统常用杠杆式夹紧系统,“杠杆式夹紧系 统”图标如图所示。 (1) 杠杆式夹紧系统 杠杆式夹紧系统是最常用的刀片夹紧方式。其特点为: 定位精度高,切屑流畅,操作简便,可与其它系列刀具产品 通用。 (2)螺钉夹紧系统 特点:适用于小孔径内孔以及长悬伸加工
1.9 数控车刀的选择与使用
由于数控车床的加工对象多为回转体, 一般使用通用三爪卡盘夹具,因而在工艺装 备中,我们将以WALTER系列车削刀具为例, 重点讨论车削刀具的选用及使用问题。
车刀的分类和选择

车刀的分类和选择车刀是机械车床上常用的切削工具之一,它对加工效率和加工质量都有重要影响。
选择适合的车刀分类和类型对于提高加工效率、降低切削成本至关重要。
本文将介绍车刀的分类和选择方法,帮助读者更好地理解和应用车刀。
一、车刀的分类根据车刀的结构和用途,可以将车刀分为以下几类:1. 工具刀片:广义上的车刀,通常由刀柄和刀片组成。
刀柄负责固定刀片,刀片进行切削工作。
工具刀片多用于外圆和内圆粗加工,适用于不同材料的车削操作。
2. 特殊刀片:用于特殊形状的车削。
如内外圆刀片、角刀片等。
特殊刀片适用于需要切削复杂外形的工件,提供更好的切削质量和加工精度。
3. 超硬刀片:采用高硬度材料制成的刀片,如金刚石、立方氮化硼等。
超硬刀片具有较高的硬度和耐磨性,适用于加工硬质材料如铸铁、合金钢等。
4. 镗刀:用于车削大孔径和参考表面。
镗刀采用特殊设计,能够提供更高的刚性和稳定性,适用于大直径工件和高精度加工。
5. 切断刀片:用于切断工件的刀片,有直刃和曲刃两种形式。
切断刀片适用于金属材料的切割,如车削工件的分离和切除。
二、车刀的选择选择适合的车刀是提高车削加工效率的关键。
以下是选择车刀时应考虑的因素:1. 加工材料:根据工件材料的不同,选择不同材质和刀片类型的车刀。
对于铸铁、不锈钢等材料,可选择高速钢刀片;对于合金钢、钛合金等硬材料,应选择超硬刀片。
2. 加工工艺:根据不同的车削工艺,选择合适的车刀类型。
对于粗车、精车和薄层车削等工艺,可以选择不同切削参数和刀片结构的车刀。
3. 切削条件:根据切削深度、进给速度和切削速度等切削条件,选择适合的刀片形状和材料。
对于大切削深度和高切削速度的加工,应选择具有高硬度和耐磨性的刀片。
4. 加工精度:根据对加工精度的要求,选择合适的刀片精度和结构。
如果需要高精度的加工,应选择刀片精度高、几何形状复杂的刀片。
5. 经济性:根据加工成本和刀具寿命,选择经济合理的车刀。
应选用具有长寿命和更换成本低的刀具,以优化切削成本。
车刀的使用技巧
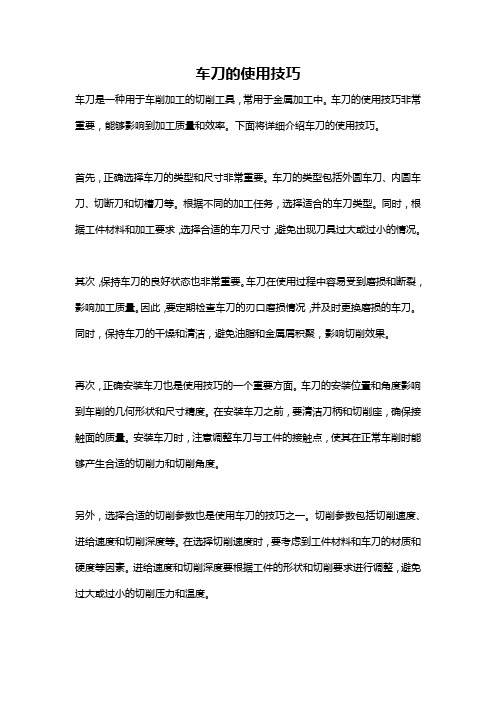
车刀的使用技巧车刀是一种用于车削加工的切削工具,常用于金属加工中。
车刀的使用技巧非常重要,能够影响到加工质量和效率。
下面将详细介绍车刀的使用技巧。
首先,正确选择车刀的类型和尺寸非常重要。
车刀的类型包括外圆车刀、内圆车刀、切断刀和切槽刀等。
根据不同的加工任务,选择适合的车刀类型。
同时,根据工件材料和加工要求,选择合适的车刀尺寸,避免出现刀具过大或过小的情况。
其次,保持车刀的良好状态也非常重要。
车刀在使用过程中容易受到磨损和断裂,影响加工质量。
因此,要定期检查车刀的刃口磨损情况,并及时更换磨损的车刀。
同时,保持车刀的干燥和清洁,避免油脂和金属屑积聚,影响切削效果。
再次,正确安装车刀也是使用技巧的一个重要方面。
车刀的安装位置和角度影响到车削的几何形状和尺寸精度。
在安装车刀之前,要清洁刀柄和切削座,确保接触面的质量。
安装车刀时,注意调整车刀与工件的接触点,使其在正常车削时能够产生合适的切削力和切削角度。
另外,选择合适的切削参数也是使用车刀的技巧之一。
切削参数包括切削速度、进给速度和切削深度等。
在选择切削速度时,要考虑到工件材料和车刀的材质和硬度等因素。
进给速度和切削深度要根据工件的形状和切削要求进行调整,避免过大或过小的切削压力和温度。
此外,正确操作车床和使用辅助装置也是使用车刀的技巧之一。
在车削过程中,要保持稳定的车床转速和进给速度,避免因速度过快或过慢引起的切削问题。
使用辅助装置,如刀柄托架和托板等,可以提高工件的刚性和稳定性,避免切削过程中的振动和变形。
最后,正确处理车刀的故障和问题也是使用技巧的一部分。
在车削过程中,车刀可能出现断刀、卡刀和刀具磨损等问题。
对于这些问题,要及时发现并采取正确的处理方法。
例如,遇到断刀时,要先检查刀具的刚性和固定情况,如无问题则考虑增加切削参数和改善切削条件,以避免刀具断裂。
综上所述,车刀的使用技巧包括选择合适的车刀类型和尺寸、保持刀具良好状态、正确安装车刀、选择合适的切削参数、正确操作车床和使用辅助装置,以及正确处理车刀故障和问题等。
车床刀具的选用原则

车床刀具的选用原则
车床刀具选用原则
1、根据加工材料的性能特点,选择不同类型的刀具。
一般而言,金属材料的切削性能和机械性能有很大的不同,因此,在选择刀具时,应根据材料的特性,选择合适的刀具以达到最佳的切削效果。
2、根据车削面的形状和尺寸大小,选择合适的刀具。
例如,当加工的车削面是圆柱形时,可以选择三刃刀或多刃刀;当加工的车削面是平面时,可以选择端面刀或平面刀。
3、根据加工的要求,选择不同刀具材质。
在加工过程中,刀具会受到很大的摩擦和冲击,因此,刀具的材质必须足够坚硬,以保证刀具的使用寿命。
常见的刀具材质包括高速钢,硬质合金,陶瓷等。
4、根据加工速度和深度,选择合适刀具尺寸。
加工速度越快,刀具尺寸越小;加工深度越大,刀具尺寸越大。
5、根据加工要求,选择合适的刀具刃数。
一般而言,刃数越多,切削效率越高,但也会降低刀具的耐用性。
6、根据加工条件,选择合适的刀具型号。
在选择刀具型号时,应注意主轴转速、切削参数等因素,以确保刀具的可靠性和安全性。
7、根据切削参数,选择合适的刀具片数。
一般而言,刀片数越多,切削效率越高,但也会降低刀具的耐用性。
8、根据加工条件,选择合适的刀具材料。
一般来说,当刀具的切削参数较高时,应选择高强度、高硬度的刀具材料;当刀具的切削参数较低时,则可以选择较低的刀具材料。
以上是车床刀具的选用原则,在实际应用中,要根据加工材料、加工要求、加工速度、加工深度等因素,合理选择刀具,才能达到最佳的加工效果。
车刀的几何角度及选择原则

车刀的几何角度及选择原则newmaker为了决定车刀刃口的锋利程度及其在空间的位置,必须建立一个坐标系,该坐标系由三个基准平面构成。
下面以外圆车刀为例,介绍车刀的几何角度。
如图所示。
基面:过主切削刃选定点的平面,此平面在主切削刃为水平时包含主刀刃并与车刀安装底面即水平面平行,此平面主要作为度量前刀面在空间位置的基准平面。
切削平面:过主切削刃选定点与主切削刃相切,并与基面相垂直的平面。
此平面主要作为度量主后刀面在空间位置的基准面。
主剖面:过主切削刃选定点并同时垂直于基面和主切削平面的平面。
(1)、前角γ0 前刀面与基面的夹角,在主剖面中测量。
前角的大小影响切削刃锋利程度及强度。
增大前角可使刃口锋利,切削力减小,切削温度降低,但过大的前角,会使刃口强度降低,容易造成刃口损坏。
取值范围为:-8°到+15°。
选择前角的一般原则是:前角数值的大小与刀具切削部分材料、被加工材料、工作条件等都有关系。
刀具切削部分材料性脆、强度低时,前角应取小值。
工件材料强度和硬度低时,可选取较大前角。
在重切削和有冲击的工作条件时,前角只能取较小值,有时甚至取负值。
一般是在保证刀具刃口强度的条件下,尽量选用大前角。
如硬质合金车刀加工钢材料时前角值可选5°-15°。
(2)、主后角α0 主后刀面与切削平面间的夹角,在主剖面中测量。
其作用为减小后刀面与工件之间的摩擦。
它也和前角一样影响刃口的强度和锋利程度。
选择原则与前角相似,一般为0到8°。
(3)、主偏角κ r 主切削刃与进给方向间的夹角,在基面中测量。
其作用体现在影响切削刃工作长度、吃刀抗力、刀尖强度和散热条件。
主偏角越小,吃刀抗力越大,切削刃工作长度越长,散热条件越好。
选择原则是:工件粗大刚性好时,可取小值;车细长轴时为了减少径向切削抗力,以免工件弯曲,宜选取较大的值。
常用在15°到90°之间。
(4)、副偏角κ 'r 副切削刃与进给反方向间的夹角,在基面中测量。
浅谈如何合理选择及使用数控车刀刀片

备如果不选用跟它匹配的刀具、刀片, 它也发挥不出它应有的性能。有了匹配的刀具, 还要用合理的参数进行加工。这样才能发挥机床 的性能, 争取最大的效
益, 本文 针对 如 何正 确 了解 和 使用 数控 的现 代化 车 刀刀 片进 行 了详 尽 的论述 。 [ 词] 关键 数控 车削 加 工材料 刀 片材质 切 削参 数 切 削速度 相应措 施 中图分类 号 :G5 T6 9 文 献标识 码 : A 文章编 号 :099 4 2 1) 30 1— 2 10 — 1X(00 0 —1 20
刀片的掼伤状描麓况刀其材料切削蘩件刀兵参敷降佳协劓毫度丈暑后砸量惯位带性蔓好曲辨辩遗喜毫夫辩麓膏太刀虫举赴铸避嚣协聃性麓好舫羹鼻稿略彘研村毫度太麓前面膏掼琶用射一性鼍虾的研辩最小毫络量遗霉鼍亳的刀片旰量佳埘削毫度量太麓撮度量横鼍麻琳诖蔓婷的辩蕞小蠢蛤量天囊蕞小麓硪小遵培量蛙高纛虞埘劓刀矗曩糟丈囊刀位席锅性曩妊辩知太斛擒蕞小切撵太套囊量丘犬刀辑叶蕞小麓膏哦小迓拾遗辱高甓度切舯再曩一糟小囊玎龅蔫栩性好的向太斛按降低饼州毫度太夯靛期大刀辩叶蕞十者培量蕞十麓膏剽落使用栩缝蔓好豹舯辩者夫盘太斛援睁俄埘劓蠢度太屠角蕞小蠢鳍蔓大麓囊塑性变形龅用甜挂蔓好的埘辩罐小嚣虫任半桎蕞小忻蒜翩挎却蕞小囊稿建量埘挂囊妊的刀片一蠢蹙用与触芏褂辩囊翱餐矗埘啊连度丈麓熔敷力小豹增大连始矗研村性蠢好的刀斗夤蠢膏慑切嗣度熟龟裂芷用翻挂量好的村蠢小连络矗霉嘲一谴蠢妊的刀斗纛蠹蠢犬羹囊翩睁柏聩量科技博克物理涂层本涂层以硬质合金做基体用物理涂层方法在基体表面涂上等弱的有害层并能保持涂层前的形状精度也适合整体刀具
如何针对 零件 的材 料选择合 理的刀 片以及正确 使用刀 片, 首先要 了解刀 片 材料 的组 成及相应性 能 : 其次要 了解刀 具的相关 参数 以及 相关 的切削加 工参数 的设 定 : 最后 要根 据 刀具 的实 际磨 损 情况 适 当的 调整 加 工参 数及 加 工条 件 。 本文 针 对 以- 三 方面 进 行论 述 。 上
数控车床刀具的选择及应用方法

数控车床刀具的选择及应用方法
数控车床刀具的选择及应用方法包括以下几点:
1. 刀具材质选择:根据数控车床的加工材料和加工工艺要求选择合适的刀具材料。
常见的刀具材料有硬质合金,高速钢,陶瓷刀具等。
2. 刀具类型选择:根据具体的加工任务选择合适的刀具类型。
常见的数控车床刀具类型有车刀、铣刀、钻孔刀具等。
3. 刀具尺寸选择:根据工件的尺寸和形状确定刀具的尺寸。
刀具尺寸要与工件的加工要求相匹配,包括刀具长度、刀尖半径、刀具直径等。
4. 刀具刃口选择:根据加工要求选择合适的刀具刃口类型,如单刃刀具、双刃刀具、倒角刀具等。
5. 刀具涂层选择:对于高速切削和长时间连续加工的任务,可以选择带有涂层的刀具,以提高切削性能和刀具寿命。
刀具应用方法:
1. 安装刀具:在安装刀具之前,要确保刀具和刀座的匹配性。
安装时要注意刀具和刀座的固定方式,确保刀具稳定不松动。
2. 刀具调试:在加工之前,要对刀具进行调试。
调试包括刀具的位置、刀具的刃口与工件的间距、切削速度、进给速度等参数的调整。
3. 切削过程中的刀具监控:在切削过程中,要及时监控刀具的磨损情况。
一旦刀具出现磨损或断刃等情况,应及时更换或修复刀具。
4. 刀具保养:刀具在使用过程中要注意保养和清洁。
保持刀具的干燥和清洁,定期进行润滑和维护,以延长刀具的使用寿命。
车削加工车刀知识点总结
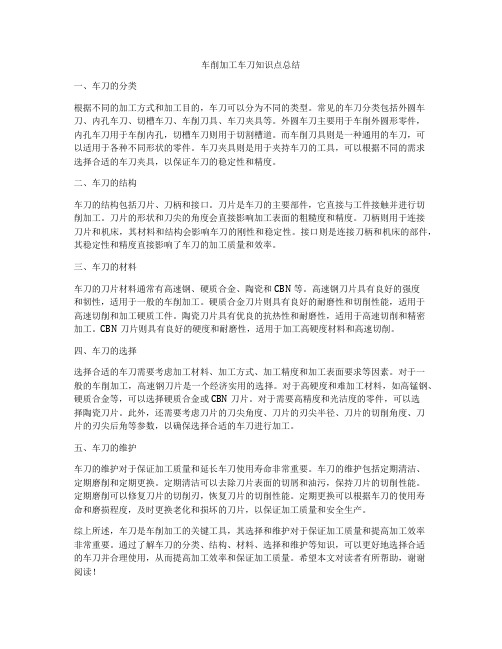
车削加工车刀知识点总结一、车刀的分类根据不同的加工方式和加工目的,车刀可以分为不同的类型。
常见的车刀分类包括外圆车刀、内孔车刀、切槽车刀、车削刀具、车刀夹具等。
外圆车刀主要用于车削外圆形零件,内孔车刀用于车削内孔,切槽车刀则用于切割槽道。
而车削刀具则是一种通用的车刀,可以适用于各种不同形状的零件。
车刀夹具则是用于夹持车刀的工具,可以根据不同的需求选择合适的车刀夹具,以保证车刀的稳定性和精度。
二、车刀的结构车刀的结构包括刀片、刀柄和接口。
刀片是车刀的主要部件,它直接与工件接触并进行切削加工。
刀片的形状和刀尖的角度会直接影响加工表面的粗糙度和精度。
刀柄则用于连接刀片和机床,其材料和结构会影响车刀的刚性和稳定性。
接口则是连接刀柄和机床的部件,其稳定性和精度直接影响了车刀的加工质量和效率。
三、车刀的材料车刀的刀片材料通常有高速钢、硬质合金、陶瓷和CBN等。
高速钢刀片具有良好的强度和韧性,适用于一般的车削加工。
硬质合金刀片则具有良好的耐磨性和切削性能,适用于高速切削和加工硬质工件。
陶瓷刀片具有优良的抗热性和耐磨性,适用于高速切削和精密加工。
CBN刀片则具有良好的硬度和耐磨性,适用于加工高硬度材料和高速切削。
四、车刀的选择选择合适的车刀需要考虑加工材料、加工方式、加工精度和加工表面要求等因素。
对于一般的车削加工,高速钢刀片是一个经济实用的选择。
对于高硬度和难加工材料,如高锰钢、硬质合金等,可以选择硬质合金或CBN刀片。
对于需要高精度和光洁度的零件,可以选择陶瓷刀片。
此外,还需要考虑刀片的刀尖角度、刀片的刃尖半径、刀片的切削角度、刀片的刃尖后角等参数,以确保选择合适的车刀进行加工。
五、车刀的维护车刀的维护对于保证加工质量和延长车刀使用寿命非常重要。
车刀的维护包括定期清洁、定期磨削和定期更换。
定期清洁可以去除刀片表面的切屑和油污,保持刀片的切削性能。
定期磨削可以修复刀片的切削刃,恢复刀片的切削性能。
定期更换可以根据车刀的使用寿命和磨损程度,及时更换老化和损坏的刀片,以保证加工质量和安全生产。
车刀的选择和使用

第一节车刀材料的选择车刀的使用寿命和生产效率取决于车刀材料的切削性能。
车刀由刀头和刀杆两部分组成,刀杆一般是用碳素结构钢制成。
由于刀头担任切削工作,因此刀头材料必须具有下列基本性能:1)冷硬性。
车刀在常温时具有较高的硬度,即车刀的耐磨性。
2)红硬性。
车刀在高温下保持切削所需的硬度,该温度的最高值称为"红热硬度"。
3)韧性。
车刀切削部分承受震动和冲击负荷所具有的强度和硬度。
车刀材料的以上三种性能是相互联系、相互制约的,在具体选用时,要根据工件材料的性能和切削要求分析选用,同时还要结合车刀材料在价格、工艺性能方面加以考虑,以便于以较低的成本加工、刃磨和焊接制造车刀。
各种车刀材料的基本性能优劣顺序比较见表4-1。
目前用来作车刀切削部分的材料主要有高速钢、硬质合金和非金属材料,碳素工具钢、合金工具钢多用作钻头、丝锥等工具,用作车刀的较少。
现分别介绍作车刀刀头的两种主要材料:高速钢及硬质合金。
一、高速钢高速钢是一种含钨、铬、钒较多的合金钢,又名锋钢、风钢或白钢。
常用的有Wl8Cr4V及W9Cr4V2两种牌号。
其中用得最多的是Wl8Cr4V高速钢。
它们的化学成分如表4-2所示。
高速钢材料分为带黑皮的高速钢和表面磨光的高速钢两种。
前者是未经热处理的高速钢,后者是经热处理的高速钢。
高速钢硬度较高,具有一定的红热硬性,韧性和加工性能均较好。
高速钢车刀制造简单,刃磨方便,容易磨得锋利。
由于高速钢韧性好,常用于加工一些冲击性较大、形状不规则的零件,它也常用于制作精车刀,但因红硬性不如硬质合金,故不宜用于高速切削。
二、硬质合金硬质合金是由难熔材料的碳化钨、碳化铁和钴的粉末在高压下成形,经l350~1560"(2高温烧结而成的材料,具有极高的硬度,仅次于陶瓷和金刚石。
硬质合金的红硬性很好,在1000℃左右仍能保持良好切削性能;具有较高的使用强度,其抗弯强度可高达1000--1700MPa,但脆性大、韧性差、怕震,以上这些缺点可通过刃磨合理的角度加以克服,因此,硬质合金现已被广泛应用。
车刀基本知识介绍(全)
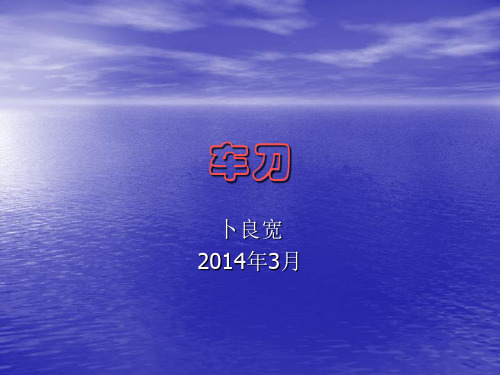
• 2,后角α0的作用是减小后刀面与工件之间的摩
擦,影响刀刃的强度和锋利程度. 后角的选择:粗车时,切削深,进给快,要求车刀有足 够的强度,应选择较小的后角.精车时,为减小后刀 面与工件过渡表面的摩擦,保持刃口的锋利,应选 较大的后角.切削力较大时,应选取较小的后角. 加工塑性材料时后角取大一些,加工脆性材料时后 角取小些.高速钢车刀的后角一般可6°--12°,硬 质合金钢车刀可取2--12.粗车时,后角一般取3°-6°;精车时,后角一般取6°--12°.
• 以上即是俗称的车刀切削部分的“三面两
刃一尖”。其组成如下:
4、车刀的角度的主要作用及选择原则
• 1,前角γ0的作用是减小切屑的变形,增大前角可使车刀
刃口锋利,减小切削力,降低切削温度,但过大前角会使 刀刃的散热条件变差,刃口强度降低,易崩刃 前角的选择:前角选择的原则是在刀具强度允许的情况 下,尽量选取较大的前角(锐中有固). 前角的大小与刀具材料,切削工作条件及被切材料有关. 切削塑性材料时,一般取较大的前角;切脆性材料时,一 般取较小的前角.当切削有冲击时,前角应取小值,甚至 取负角.硬质合金车刀的前角一般比高速钢车刀的前角 要小.加工材料由硬到软,对于高速钢车刀,前角可取 5°--30°;对于硬质合金钢车刀,前角一般取-15°-30°.
二、车刀的角度及其初步选择
1、车刀的组成 任何车刀都是由刀头(或刀 片)和刀体两部分组成的。刀头担负切削 工作,又叫切削部分。刀体用来装夹到车 床刀架上。
刀头是由若干个刀面和切削刃组成 (如下图)
(1)前刀面 :切削时,切屑流出所经过表 面。 (2) 后刀面 :分主后刀面和副后刀面。主 后刀面与工件过渡表面相对的刀面;副后 刀面与已加工表面相对的刀面。 (3 )主切削刃:前后刀面的交线,担负主 要的切削工作,也称主切削刃或主刀刃; (4)副切削刃:前面与副后刀面的交线, 配合切削刃完成切削工作,并形成已加工 表面,也称副刀刃; (5)刀尖:主副刀刃的交点,它可以是一个 点、直线或圆弧。
车刀规格文档
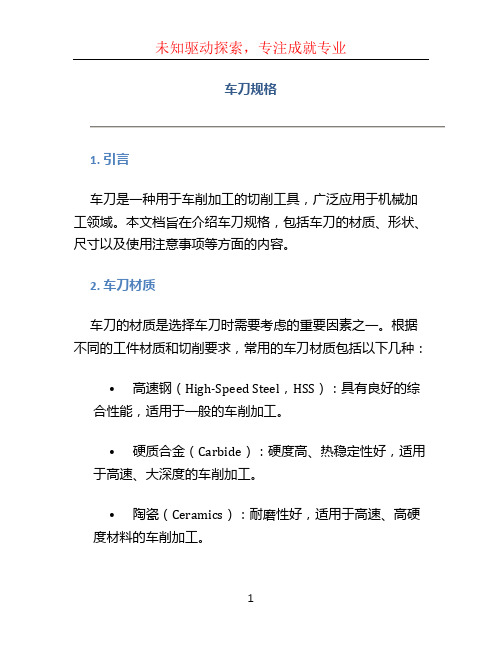
车刀规格1. 引言车刀是一种用于车削加工的切削工具,广泛应用于机械加工领域。
本文档旨在介绍车刀规格,包括车刀的材质、形状、尺寸以及使用注意事项等方面的内容。
2. 车刀材质车刀的材质是选择车刀时需要考虑的重要因素之一。
根据不同的工件材质和切削要求,常用的车刀材质包括以下几种:•高速钢(High-Speed Steel,HSS):具有良好的综合性能,适用于一般的车削加工。
•硬质合金(Carbide):硬度高、热稳定性好,适用于高速、大深度的车削加工。
•陶瓷(Ceramics):耐磨性好,适用于高速、高硬度材料的车削加工。
3. 车刀形状根据不同的车削需求,车刀可以设计成不同的形状。
常见的车刀形状有以下几种:•平车刀:刀尖与工件表面垂直,用于进行普通平面车削。
•内外倒角刀:刀刃具有倒角,用于倒角和修边。
•内外圆弧刀:刀刃具有圆弧形状,用于进行曲面车削。
•螺纹刀:用于车削螺纹。
4. 车刀尺寸车刀的尺寸是根据工件的尺寸和形状来选择的。
常见的车刀尺寸包括以下几个方面:•切削刀具长度:根据加工深度来选择,一般为几倍刀具直径。
•刀尖倾角:根据车刀形状的不同,倾角也会有所不同。
•刀片宽度:根据工件的槽宽或切削面积来选择,一般为刀片工作面的宽度。
•刀片厚度:根据车削要求和加工余量来选择。
5. 使用注意事项在使用车刀时,需要注意以下几点:•安全操作:在车削加工过程中,要注意佩戴防护眼镜、手套等个人防护装备,确保操作的安全。
•刀具检查:车刀使用前,要检查刀具是否损坏或磨损严重,如有问题需要及时更换。
•加工参数:根据工件材料、形状和车刀规格等因素,合理设定车削参数,如切削速度、进给速度等。
•冷却润滑:对于高温产生的切削过程,应使用冷却润滑剂进行降温和润滑。
6. 结论本文对车刀规格进行了介绍,包括材质、形状、尺寸和使用注意事项等方面的内容。
通过了解和选择适合的车刀规格,可以有效提高工件的制造质量和加工效率。
在实际应用中,需要根据具体加工要求和切削条件进行选择和调整,以达到最佳的加工效果。
车刀的主要几何角度及选择

车刀的重要几何角度及选择1)前角(γ0 )选择的原则前角的大小重要解决刀头的坚固性与锋利性的冲突。
因此首先要依据加工材料的硬度来选择前角。
加工材料的硬度高,前角取小值,反之取大值。
其次要依据加工性质来考虑前角的大小,粗加工时前角要取小值,精加工时前角应取大值。
前角一般在—5°~25°选取。
通常,制作车刀时并没有预先制出前角(γ0),而是靠在车刀上刃磨出排屑槽来获得前角的。
排屑槽也叫断屑槽,它的作用是折断切屑,不产生缠绕;掌控切屑的流出方向,保持已加工表面的精度;降低切削抗力,延长刀具寿命。
2)后角(α0 )选择的原则首先考虑加工性质。
精加工时,后角取大值,粗加工时,后角取小值。
其次考虑加工材料的硬度,加工材料硬度高,主后角取小值,以加强刀头的坚固性;反之,后角应取小值。
后角不能为零度或负值,一般在6°~12°选取。
3)主偏角(Kr )的选用原则首先考虑车床、夹具和刀具构成的车削工艺系统的刚性,如系统刚性好,主偏角应取小值,这样有利于提高车刀使用寿命、改善散热条件及表面粗造度。
其次要考虑加工工件的几何形状,当加工台阶时,主偏角应取90°,加工中心切入的工件,主偏角一般取60 °。
主偏角一般在30°~90°,*常用的是45°、75 °、90 °。
4)副偏角(Kr)的选择原则首先考虑车刀、工件和夹具有充足的刚性,才能减小副偏角;反之,应取大值;其次,考虑加工性质,精加工时,副偏角可取10°~15°,粗加工时,副偏角可取5°左右。
5)刃倾角(λS)的选择原则重要看加工性质,粗加工时,工件对车刀冲击大,取λS≤ 0°,精加工时,工件对车刀冲击力小,取λS≥ 0°;通常取λS=0°。
刃倾角一般在—10°~5°选取。
- 1、下载文档前请自行甄别文档内容的完整性,平台不提供额外的编辑、内容补充、找答案等附加服务。
- 2、"仅部分预览"的文档,不可在线预览部分如存在完整性等问题,可反馈申请退款(可完整预览的文档不适用该条件!)。
- 3、如文档侵犯您的权益,请联系客服反馈,我们会尽快为您处理(人工客服工作时间:9:00-18:30)。
车刀的选择与使用
摘要:在金属的车削加工过程中,车床是形成切削运动和提供切削动力的来源。
刀具则是直接改变毛胚的形状,使其达到符合图纸要求的效果。
刀具的性能直接影响着产品质量和生产效率。
车刀材质、几何形状、和角度是影响车刀性能的主要原因。
此外,切削用量和刃磨技术也是影响车刀切削状态的重要因素,故需合理的选择。
该文以常用刀具为例,从刀具的材质、刀具的几何角度、和刀具的安装、使用三个方面论述车刀的选择和使用方法。
关键词:车刀材料车刀几何角度车刀安装使用
“三分手艺,七分刀”。
这句俗语很形象的说明了,在车床加工中,最重要的部分是刀具。
随着社会的进步,科技的发展,从普通车床向精密数控加工中心的过渡、越来越多的原材料种类、越来越高的工件性能要求、热处理和激光熔覆使原材料的硬度翻倍增加。
在机床加工过程中,对刀具的要求越来越高。
在数控机床和普通车床的使用、刀具的选择和安装中,碰见过很多的问题。
在翻阅书籍和请问老师傅后,获得了很多经验,在这里写出来。
与大家共同学习,共同探讨,共同进步。
1 车刀材料的选择
车刀的使用寿命和生产效率取决于车刀材料的切削性能。
车刀由
刀头和刀杆两部分组成,刀杆一般由碳素结构钢制成。
由于刀头担任切削工作,受切削力和切削热的影响,因此,刀头必须有以下基本性能。
1.1 冷硬性
车刀在常温时具有较高的硬度,即车刀要耐磨。
1.2 红硬性
车刀在高温时保持切削所需的硬度,该温度最高值称为“红热硬度”。
1.3 韧性
车刀为切削部分,承受机床和工件的震动冲击负荷所具有的强度硬度。
以上三种车刀的性能,相互联系,相互制约。
在具体的选用时,要根据工件材料的性能和切削要求分析选用。
同时还要结合车刀材料在价格、工艺性能方面加以考虑,以便于较低成本加工、刃磨、和焊接制造刀具。
本单位使用的刀具有两类。
一类是白钢条,即高速钢。
一类是刀头,即硬质合金钢。
这两类即代表了车刀刀头的主要材料。
(1)高速钢是一种含钨、钒、洛较多的合金钢。
常用的有W18CR4V
及W9CR4V2两种牌号。
高速钢硬度较高,韧性和加工性能较好。
容易磨得很锋利。
但不利于高速切削。
所以本单位在加工一些特殊工件时才会使用。
(2)硬质合金由难熔的碳化钨、碳化铁和钴粉末在高压下成型,经1350~1560°高温烧结而成的材料,具有极高的硬度,仅次陶瓷和金刚石。
硬质合金红硬性很好,在1000°的高温下仍具有较高的使用硬度,其抗弯硬度可高达1000~1700MPA。
但脆性大,韧性差,怕震。
根据其制造合金元素不同可分为四类。
钨钴合金(代号YG)、钨钛钻合金(代号YT)、钨钴钛合金(代号YW)、钨钴铌合金(代号YA)。
鉴于本单位常用的毛胚材料为30CrMnTi、40Cr、27SiMn类塑性材料,热处理后硬度能达到HRC35-45(HB240-300),所以最常选择的刀具是硬质合金中的钨、钛、钻合金,即YT型。
本单位常用的YT15、YT30即属于钨钛钻合金。
由碳化钨、碳化钛,和元素钻组成。
代号YT,常用牌号有YT5,YT14,YT15,YT30。
钨钛钻合金的冷硬性和红硬性较高,在高温条件下,比钨钴合金耐热、耐磨、抗粘性大、易于加工钢料及其他韧性金属材料。
此类刀头完全能适应本单位销轴类工件的加工需要,且经济合理。
2 车刀几何角度的选择
刀头是车刀的切削部分它分为前刀面、主后刀面、副后刀面、主
切削刃、副切削刃、和刀尖组成。
简称“三面两刃一尖”。
车刀的切削角度有7项,即前角、后角、主偏角、副偏角、刀尖角、刃倾角、和副后角。
本单位主要以加工液压支架管件、销轴等工件为主,因此外圆刀主要是以主偏角45°、75°、90°。
在日常加工过程中选用粗车刀应遵循以下几点要求:
(1)为了减少切削力,应当将刀具刃磨锋利,在这种情况下,前角、后角可小些,以增加强度,前角主要是以15~25°,后角主要是5~10°,角度越小刀刃越锋利;
(2)主偏角不宜太小,如果工件允许的情况下,最好取75~90°左右,这时刀具能承受较大的切削力,并且有利于刀刃散热;
(3)主刀刃上应磨出负倒角,以增加刀刃的强度;
(4)刃倾角主要是是根据工件材质及加工类型调整,一般情况下,采用-5~-10°。
3 车刀的安装和使用
车刀在机床的使用位置安装的是否正确,对切削断销是否顺利,工件表面光洁度是否符合图纸要求,有很大的关系。
如果没有正确的安装刀具,就不能发挥应有的作用。
3.1 车刀安装高低对切削的影响
车刀刀尖应安装的与工件中心线(卡盘、主轴箱中心线)一致,才能发挥作用。
对于新机床,可用钢尺直接测量标准中心高安装即可。
对于老旧的机床,可利用顶尖、工件中心孔找正安装。
刀尖高于工件中心线时,车刀切入材料困难易伤刀杆。
安装刀尖低于工件中心线时,刀尖受力不均,易伤刀头。
3.2 车刀安装偏斜对切削的影响
车削时,一般车刀安装总是与中心线垂直。
这样主偏角和副偏角不会改变。
以车床主轴正转,刀具为正偏刀为例,刀头向左偏时,主偏角增大,副偏角减小。
刀尖受切削力和切削热最大,易崩碎。
刀头向右偏时,主偏角减小,副偏角增大。
从而极易造成工件末尾易形成斜面、钝角,不符合图纸设计要求。
由于学识能力有限,并且车刀所涉及的方面还有很多,本文主要就以车刀材质,几何角度,和车刀安装三个方面,来简述日常车刀的选择和使用方法。
如有不足之处还望斧正。
参考文献
[1]危卫华,徐九华,傅玉灿,等.置氢钛合金TC4的切削加工性研究
[J].南京航空航天大学学报,2009(5).
[2]马海涛,尤文,贾文超.一种基于重块平衡原理的砂轮动平衡系统建模方法[J].长春工业大学学报(自然科学版),2006(3):21-23.
[3]杨振朝,张定华,姚倡锋,等.TC4钛合金高速铣削参数对表面完整性影响研究[J].西北工业大学学报,2009(4).
[4]邓敏,潘应君,尹作鹏.高速钢表面PN+PVD复合处理工艺和性能研究[J].武汉科技大学学报,2009(2).
[5]龙震海,王西彬,刘志兵.(Ti,Al)N涂层硬质合金刀具高速铣削30CrNi4MoV钢时的磨损机理[J].北京理工大学学报,2004(11).
[6]许鸿昊,左敦稳,朱笑笑,等.拉伸高速铣削对TC4钛合金疲劳性能的影响[J].南京航空航天大学学报,2008(2).
[7]曹克伟,李佳,徐燕申,等.钛合金材料的数控加工方法[J].组合机床与自动化加工技术,2005(4).。