当前汽车覆盖件冲压工艺应用及其缺陷因素分析
汽车覆盖件成型过程中缺陷的产生原因和分析

汽车覆盖件成型过程中缺陷的产生原因和分析汽车覆盖件是指汽车外部的可移动或可拆卸的部件,如车门、引擎盖、后备箱盖等。
在汽车覆盖件的成型过程中,可能会出现一些缺陷,影响产
品的质量和性能。
下面将对汽车覆盖件成型过程中缺陷的产生原因和分析
进行详细阐述。
1.原材料问题:汽车覆盖件常用的材料有钢板、铝板、塑料等。
如果
原材料质量不好或存在焊接接头等问题,会导致成型过程中产生缺陷,如
裂纹、气泡等。
2.设计问题:不合理的设计会导致成型过程中产生缺陷。
比如,在覆
盖件的拐角处加强筋不够,容易发生变形或破裂;覆盖件连接处的设计不
合理,容易发生接缝开裂等。
3.成型工艺问题:成型工艺是影响覆盖件成型质量的重要因素。
如果
压力、温度、注射速度等参数不合理或控制不良,容易导致缺陷的产生。
例如,注塑成型时,塑料料筒温度不均匀、反应时间过短等,会导致覆盖
件的尺寸不一致或强度不足。
4.模具问题:模具是汽车覆盖件成型的关键工具,模具质量的好坏直
接影响成型质量。
如果模具的设计、制造不良或磨损严重,则会导致成型
中产生缺陷,如模具接缝处的破损、模具表面的划痕等。
针对以上问题,可以采取以下措施来减少缺陷的产生:
1.严格选择优质原材料,保证其质量稳定,避免原材料的问题对成型
过程造成影响。
2.合理设计覆盖件的结构,充分考虑材料的性能和力学特性,避免设计缺陷引起的问题。
3.优化成型工艺参数,确保温度、压力、速度等参数的准确控制,以提高成型质量。
4.保养和维护模具,定期检查和修复,避免模具质量问题对成型产生影响。
汽车覆盖件成形缺陷分析及控制措施
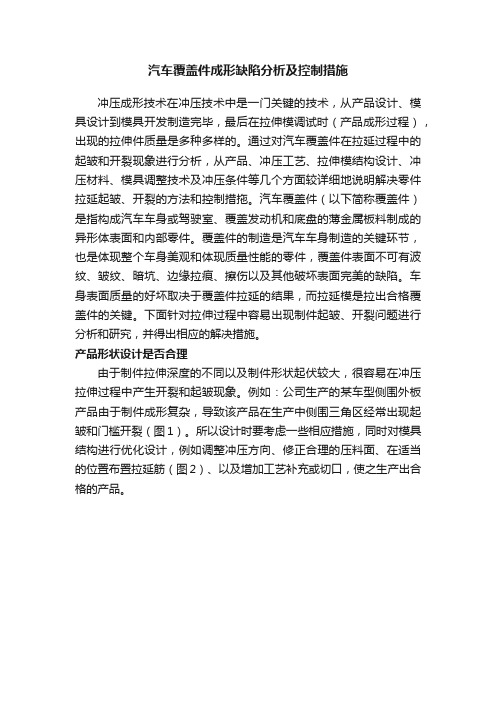
汽车覆盖件成形缺陷分析及控制措施冲压成形技术在冲压技术中是一门关键的技术,从产品设计、模具设计到模具开发制造完毕,最后在拉伸模调试时(产品成形过程),出现的拉伸件质量是多种多样的。
通过对汽车覆盖件在拉延过程中的起皱和开裂现象进行分析,从产品、冲压工艺、拉伸模结构设计、冲压材料、模具调整技术及冲压条件等几个方面较详细地说明解决零件拉延起皱、开裂的方法和控制措拖。
汽车覆盖件(以下简称覆盖件)是指构成汽车车身或驾驶室、覆盖发动机和底盘的薄金属板料制成的异形体表面和内部零件。
覆盖件的制造是汽车车身制造的关键环节,也是体现整个车身美观和体现质量性能的零件,覆盖件表面不可有波纹、皱纹、暗坑、边缘拉痕、擦伤以及其他破坏表面完美的缺陷。
车身表面质量的好坏取决于覆盖件拉延的结果,而拉延模是拉出合格覆盖件的关键。
下面针对拉伸过程中容易出现制件起皱、开裂问题进行分析和研究,并得出相应的解决措施。
产品形状设计是否合理由于制件拉伸深度的不同以及制件形状起伏较大,很容易在冲压拉伸过程中产生开裂和起皱现象。
例如:公司生产的某车型侧围外板产品由于制件成形复杂,导致该产品在生产中侧围三角区经常出现起皱和门槛开裂(图1)。
所以设计时要考虑一些相应措施,同时对模具结构进行优化设计,例如调整冲压方向、修正合理的压料面、在适当的位置布置拉延筋(图2)、以及增加工艺补充或切口,使之生产出合格的产品。
图1 门洞处开裂图2 更改双拉延筋解决拉延模设计工艺性是否合理覆盖件工艺性主要表现在冲压性能、焊接装配性能、操作安全性、材料消耗及性能的要求。
覆盖件的冲压性能,在多数情况下是以拉伸件为先决条件的。
拉伸过程中在设计拉延件时不但要考虑冲压方向、压料面形状、拉延筋形状及布置、工艺补充部分等设计,对于这些方面设计是相辅相成,也是成形技术的关键,所以覆盖件的拉伸模具工艺设计是非常重要的,这不但能决定产品拉伸好坏,而且给下道修边、翻边工序创造有利条件,对于覆盖件工艺设计一般应注意:⑴冲压方向的确定;⑵合理增加工艺补充部分;⑶压料面形状的确定;⑷工艺切口和工艺孔的设置。
汽车冲压常见质量问题及解决方法PPT课件

2019/9/19
20
2.1.3材料表面质量差-划痕引起应力集中、锈蚀增大后阻力。
2.1.4压料面的进料阻力过大-毛坯外形大、压料筋槽间隙小、凹 模圆角半径过小、外滑块调的过深、拉深筋过高、压料面和凹 模圆角半径光洁度差。
2.1.5局部拉深量太大,拉深变形超过了材料变形极限。
2.1.6在操作中,把毛坯放偏,造成一边压料过大,一边压料过小。 过大的一边则进料困难,造成开裂;过小的一边,进料过多, 易起皱,皱后进料困难,引起破裂。
b 模具装配误差-导向部分间隙大、凸凹模装配不同心等;
c 压力机精度差—如压力机导轨间隙过大,滑块底面与工作台表 面的平行度不好 ,或是滑块行程与压力机台面的垂直度不好, 工作台刚性差,在冲裁时产生挠度,均能引起间隙的变化;
d 安装误差—如冲模上下底板表面在安装时未擦干净或对大型冲 模上模的紧固方法不当,冲模上下模安装不同心(尤其是无导 柱模)而引起工作部分倾斜;
1.6 制件的工艺性差-形状复杂有凸出或凹入的尖角均
易因磨损过快而产生毛刺。
2019/9/19
6
小结:
毛刺的产生,不仅使冲裁以后的变形工序由于 产生应力集中而容易开裂,同时也给后续工序毛 坯的分层带来困难。大的毛刺容易把手划伤;焊 接时两张钢板接合不好,易焊穿,焊不牢;铆接 时则易产生铆接间隙或引起铆裂。
3.1 模具刃口尺寸制造超差
3.2 冲裁过程中的回弹、上道工序的制件形状与下道工序模具工 作部分的支承面形状不一致,使制件在冲裁过程中发生变形,冲 裁完毕后产生弹性回复,因而影响尺寸精度。
3.3 板形不好。
3.4 多工序的制件由于上道工序调整不当或圆角磨损,破坏了变 形时体积均等的原则,引起了冲裁后尺寸的变化。
汽车冲压覆盖件常见质量缺陷及处理措施
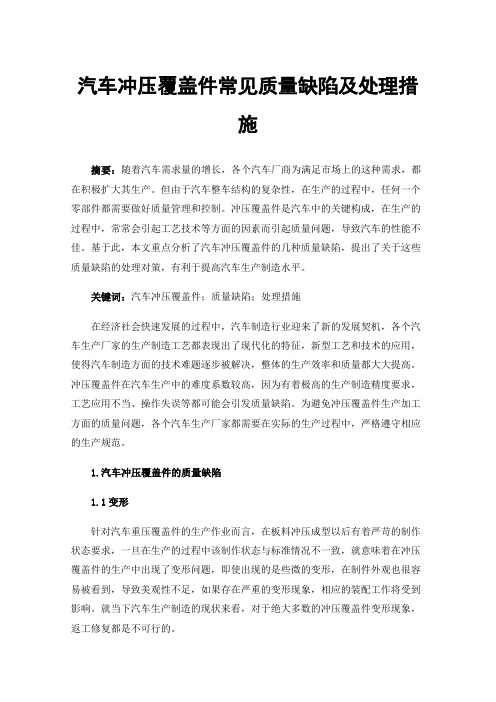
汽车冲压覆盖件常见质量缺陷及处理措施摘要:随着汽车需求量的增长,各个汽车厂商为满足市场上的这种需求,都在积极扩大其生产。
但由于汽车整车结构的复杂性,在生产的过程中,任何一个零部件都需要做好质量管理和控制。
冲压覆盖件是汽车中的关键构成,在生产的过程中,常常会引起工艺技术等方面的因素而引起质量问题,导致汽车的性能不佳。
基于此,本文重点分析了汽车冲压覆盖件的几种质量缺陷,提出了关于这些质量缺陷的处理对策,有利于提高汽车生产制造水平。
关键词:汽车冲压覆盖件;质量缺陷;处理措施在经济社会快速发展的过程中,汽车制造行业迎来了新的发展契机,各个汽车生产厂家的生产制造工艺都表现出了现代化的特征,新型工艺和技术的应用,使得汽车制造方面的技术难题逐步被解决,整体的生产效率和质量都大大提高。
冲压覆盖件在汽车生产中的难度系数较高,因为有着极高的生产制造精度要求,工艺应用不当、操作失误等都可能会引发质量缺陷。
为避免冲压覆盖件生产加工方面的质量问题,各个汽车生产厂家都需要在实际的生产过程中,严格遵守相应的生产规范。
1.汽车冲压覆盖件的质量缺陷1.1变形针对汽车重压覆盖件的生产作业而言,在板料冲压成型以后有着严苛的制作状态要求,一旦在生产的过程中该制作状态与标准情况不一致,就意味着在冲压覆盖件的生产中出现了变形问题,即使出现的是些微的变形,在制件外观也很容易被看到,导致美观性不足,如果存在严重的变形现象,相应的装配工作将受到影响。
就当下汽车生产制造的现状来看,对于绝大多数的冲压覆盖件变形现象,返工修复都是不可行的。
1.2毛刺制件在生产的过程中,存在有修边、切断、冲孔等各个工序,如果在这些工序的实施过程中存在断面平整度不够的现象,就是冲压覆盖件的毛刺问题,这种缺陷出现的频次是相对较高的。
当在冲压覆盖件的生产过程中发生了毛刺现象时,不仅无法保障产品的美观性,也难以满足产品的性能规定,在利用专有设备开展生产作业时,设备运行过程中的噪音偏大,长时间无法处理这种毛刺问题,将会增大生产设备的故障几率[1]。
浅谈冲压件制造工艺及质量缺陷

浅谈冲压件制造工艺及质量缺陷欧阳春生北汽福田汽车股份有限公司摘要:汽车制造中有60%-70%的金属零部件需经塑性加工成形,冲压加工是完成金属塑性成形的一种重要手段,它是最基本、最传统、最重要的金属加工方法之一。
汽车冲压工艺技术如车身上的各种覆盖件、车内支撑件、结构加强件,还有大量的汽车零部件,如发动机的排气弯管及消声器、空心凸轮轴、油底壳、发动机支架、框架结构件、横纵梁等等,都是经冲压成形技术正向精密、多功能、高效节能、安全清洁的生产方向发展,冲压工件的制造工艺水平及质量,在较大程度上对汽车制造质量和成本有直接的影响。
关键词:冲压工艺质量1汽车覆盖件的工艺过程概述汽车冲压件的加工过程大致如下:卷材——落料——堆垛——运输——(冲压线)仓储——清洗——冲压成型。
在落料过程中,由起重机将卷料放上卷料备料台,然后装载到上料小车上,上料小车运行到开卷机,上料小车回位后,完成卷料与整线的对中,穿带结束后,料带经过四辊式送料机组进行料头剪切,进入清洗机进行料带的清洗;经过清洗后的料带进入校平机组;被校平后的板料进入地坑,形成一个缓冲带(补偿环),以补偿卷材在开卷校平部分连续运行和进入落料切断冲模时的间歇动作的速度差。
在地坑的一侧,装有光电反射器,当卷材下落到地坑时,反射器给出信号使驱动开卷装置的电机停止工作,卷材进给中断;经过几次落料切断后,地坑中的卷材逐步上升到一定程度,光电反射器发出信号,使驱动开卷装置的电动机起动,恢复卷材进给,开卷校平;从地坑上来的板料进入落料压力机进给的装置;落料压机落料及堆垛。
在冲压成形过程中,钢板的成型都是借助模具对薄板施加外力所引起的结果。
一定力的作用方式和大小,都对应着一定的变形。
不论采用什么样的成形方式,冲压成形件所要求的几何形状,都是通过钢板在冲压成形过程中的塑性变形来完成的。
根据冲压成形过程中钢板变形区的应力、应变的不同,可将零件变形划分为拉伸、压缩、弯曲、扭转等多种成形方式。
汽车覆盖件冲压成型的典型缺陷分析

汽车覆盖件冲压成型的典型缺陷分析摘要:覆盖件作为汽车的主要组成部件,其设计、制造的速度对汽车工业的发展有着直接的影响作用。
汽车覆盖件的重要生产方式之一即板料冲压成型,这是一种非常关键的制造技术,已广泛的应用于汽车、航空、电器等工业领域,尤其是在汽车制造中更为重要。
本文对汽车覆盖件冲压成型过程中的出现的缺陷进行分析,有着重要的现实意义。
关键词:冲压成型;缺陷;分析1、汽车覆盖件概述所谓的汽车覆盖件,指的是构成汽车车身或者驾驶室、覆盖发动机和底盘的异形体表面和汽车零件。
汽车覆盖件不仅仅有着很强的装饰性,同时还承担着一定的冲击力,所以说汽车覆盖件的功能是十分复杂的。
汽车覆盖件除了我们经常能看见的车门外板、侧围外板、机盖等外覆盖件外,还包括一些隐藏在车内的地板面板和左右纵梁等内覆盖件。
2、覆盖件冲压工艺的特征在对汽车车身进行设计的时候,必须要从整体的造型和结构功能来进行设计,而汽车的覆盖件是完成汽车造型和结构功能的重要配件,所以往往汽车的设计者对其十分重视。
但是虽然覆盖件是汽车的重要配件,由于受到设计人员专业知识的限制,可能在一些制造工艺方面的考虑还不是很深入,所以就导致了覆盖件制造工艺存在一定的问题。
而覆盖件的冲压工艺对于覆盖件的制造又有着非常重要的意义,所以说必须对其引起足够的重视,在进行覆盖件的设计时,必须要考虑冲压的工艺性。
3、汽车覆盖件冲压成型过程中的典型缺陷分析板材冲压成型过程可以被看作是板材经过塑性变形变为想要获得的形状的过程。
板材成型过程包括成型材料选择、成型工序制定、模具设计制造、成型操作以及后续处理等,其中,比较关键的是成型工序的制定,包括弯曲、胀形、拉延和翻边等几道工序。
由于板料尺寸、材料特性和环境条件使冲压成型过程的预测性和可重复性变得困难,一般要通过多次试验才能使成型工序与工艺参数确定出来。
板材冲压成型过程中的任何一道工序都会直接影响到产品质量和价格。
材质不当、模具形状不合适或加工失误,都容易产生成型件拉裂、回弹或起皱等形状不良问题。
汽车冲压件成形及其缺陷分析
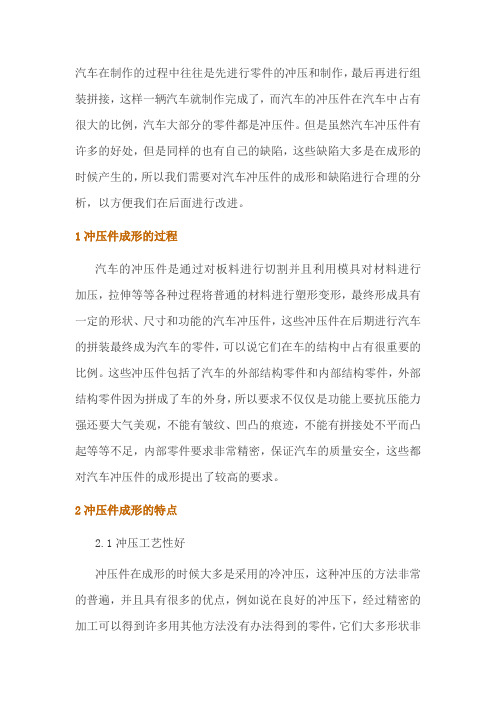
汽车在制作的过程中往往是先进行零件的冲压和制作,最后再进行组装拼接,这样一辆汽车就制作完成了,而汽车的冲压件在汽车中占有很大的比例,汽车大部分的零件都是冲压件。
但是虽然汽车冲压件有许多的好处,但是同样的也有自己的缺陷,这些缺陷大多是在成形的时候产生的,所以我们需要对汽车冲压件的成形和缺陷进行合理的分析,以方便我们在后面进行改进。
1冲压件成形的过程汽车的冲压件是通过对板料进行切割并且利用模具对材料进行加压,拉伸等等各种过程将普通的材料进行塑形变形,最终形成具有一定的形状、尺寸和功能的汽车冲压件,这些冲压件在后期进行汽车的拼装最终成为汽车的零件,可以说它们在车的结构中占有很重要的比例。
这些冲压件包括了汽车的外部结构零件和内部结构零件,外部结构零件因为拼成了车的外身,所以要求不仅仅是功能上要抗压能力强还要大气美观,不能有皱纹、凹凸的痕迹,不能有拼接处不平而凸起等等不足,内部零件要求非常精密,保证汽车的质量安全,这些都对汽车冲压件的成形提出了较高的要求。
2冲压件成形的特点2.1冲压工艺性好冲压件在成形的时候大多是采用的冷冲压,这种冲压的方法非常的普遍,并且具有很多的优点,例如说在良好的冲压下,经过精密的加工可以得到许多用其他方法没有办法得到的零件,它们大多形状非常的复杂,或者说很小巧精致,这些都是其他制作方法无法很好的做到的。
2.2质量得到保证利用冲压制作的零件和汽车部件一般质量都比较高,因为它是采用机器进行的加工,所以它在大小尺寸上精确度很高,并且不会出现第一个冲压得到的部件质量高,形状好且尺寸精确,但是下一个冲压得到的部件却缺胳膊少腿,尺寸和要求的不符合的现象,质量比较稳定,一致性较高。
汽车的冲压件多是对金属材料进行塑性变形,把普通的金属材料通过冲压制作成汽车的零件,保证了汽车的零件都是金属材质,汽车的质量也得到了保证。
2.3成件效率高在对金属材料进行冲压制作汽车冲压件时,材料大多是整块的金属材料,只要我们进行好规划,利用压力机进行冲压的时候可以合理的利用几乎所有的金属材料,可以避免人为操作的时候因为裁割的大小不符合要求需要进行再次切割而导致的材料浪费。
汽车覆盖件的冲压工艺优化分析
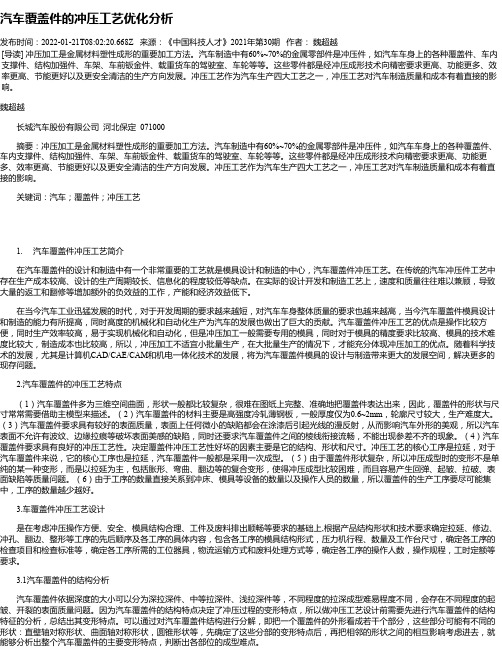
汽车覆盖件的冲压工艺优化分析发布时间:2022-01-21T08:02:20.668Z 来源:《中国科技人才》2021年第30期作者:魏超越[导读] 冲压加工是金属材料塑性成形的重要加工方法。
汽车制造中有60%~70%的金属零部件是冲压件,如汽车车身上的各种覆盖件、车内支撑件、结构加强件、车架、车前钣金件、载重货车的驾驶室、车轮等等。
这些零件都是经冲压成形技术向精密要求更高、功能更多、效率更高、节能更好以及更安全清洁的生产方向发展。
冲压工艺作为汽车生产四大工艺之一,冲压工艺对汽车制造质量和成本有着直接的影响。
魏超越长城汽车股份有限公司河北保定 071000摘要:冲压加工是金属材料塑性成形的重要加工方法。
汽车制造中有60%~70%的金属零部件是冲压件,如汽车车身上的各种覆盖件、车内支撑件、结构加强件、车架、车前钣金件、载重货车的驾驶室、车轮等等。
这些零件都是经冲压成形技术向精密要求更高、功能更多、效率更高、节能更好以及更安全清洁的生产方向发展。
冲压工艺作为汽车生产四大工艺之一,冲压工艺对汽车制造质量和成本有着直接的影响。
关键词:汽车;覆盖件;冲压工艺1. 汽车覆盖件冲压工艺简介在汽车覆盖件的设计和制造中有一个非常重要的工艺就是模具设计和制造的中心,汽车覆盖件冲压工艺。
在传统的汽车冲压件工艺中存在生产成本较高、设计的生产周期较长、信息化的程度较低等缺点。
在实际的设计开发和制造工艺上,速度和质量往往难以兼顾,导致大量的返工和翻修等增加额外的负效益的工作,产能和经济效益低下。
在当今汽车工业迅猛发展的时代,对于开发周期的要求越来越短,对汽车车身整体质量的要求也越来越高,当今汽车覆盖件模具设计和制造的能力有所提高,同时高度的机械化和自动化生产为汽车的发展也做出了巨大的贡献。
汽车覆盖件冲压工艺的优点是操作比较方便,同时生产效率较高,易于实现机械化和自动化,但是冲压加工一般需要专用的模具,同时对于模具的精度要求比较高、模具的技术难度比较大,制造成本也比较高,所以,冲压加工不适宜小批量生产,在大批量生产的情况下,才能充分体现冲压加工的优点。
汽车覆盖件常见质量缺陷及对策

汽车覆盖件常见质量缺陷及对策【摘要】随着社会和经济的快速发展,汽车的使用量在不断增加,从而对汽车覆盖件的表面质量提出了更高的要求。
本文对暗坑、波浪、破裂、回弹、毛刺、棱线不清、拉毛等常见质量缺陷进行分析,阐述了相应处理措施,并简单介绍了缺陷检查方法。
【关键词】汽车;覆盖件;质量缺陷;处理措施汽车车身主要是由很多轮廓尺寸比较大并具有空间曲面形状的覆盖件连接而成的,汽车覆盖件的表面质量直接决定着车身的质量,要求汽车覆盖件的表面平整、清晰,并且不允许存在裂缝、划伤等表面缺陷。
下面将对覆盖件常见质量缺陷产生原因以及处理措施进行详细地阐述。
1.覆盖件常见质量缺陷及其分析1.1暗坑暗坑是指覆盖件上连续凸出的曲面在局部出现的轻微凹陷或者凸起。
直接目视观察是很难发现这种缺陷的,只有将车身油漆之后并经过光线照射才能表现出来,所以将其称为暗坑。
暗坑产生的原因包括:在板料形成的过程中,板料的变形是由弹性变形以及塑性变形组成的,当外力消失之后,弹性变形成为了塑性变形的限制,无法完全恢复,从而在冲压件中形成了残余应力,通过冲压件的形状以及尺寸可以综合体现板料的弹性变形以及塑性变形。
弯曲的弹性变形导致该处的曲率半径发生变化,最终形成了暗坑。
1.2波浪波浪是一些极轻微的皱纹,与一定区域中连续出现的暗坑比较相似,其主要出现在零件的边缘附近,比如,翼子板的轮罩上方,或者是车门的翻边线附近。
波浪产生的原因是在板料成形的过程中,法兰面部分受到切向压应力的影响,因为失稳从而产生起皱的板料,主要是通过凸模和凹模之间的间隙将其保留在冲压件的表面,从而形成了表面波浪。
另外,在进行翻边的过程中,由于材料出现弯曲变形,材料的完全部分的外侧受到拉应力作用,内侧受到压应力作用,由于这些应力具有力矩作用,卸载之后出现的轻微翘曲变形也是表面波浪的具体表现。
产品的形状、材料的性能以及模具的结构等因素都对波浪的产生具有重要的影响,尤其是在进行拉延时,压边圈设计与模具之间的间隙不合理则会导致波浪的产生。
汽车外覆盖件冲压表面缺陷的产生原因及预防措施

万方数据
Die and Mould Technology No.5 2012
度不一致,造成压边圈的压料力不均匀,局部位 置的压料力大,拉深时零件局部出现变薄、拉裂。 ’:j■‘二4
+:4
造成模具的压料力不均匀,零件成形时压料紧 的部位材料流人模具型腔困难造成变薄、拉裂, 压料松的部位因压不住材料造成起皱。(5)落
预防冲压生产中汽车外覆盖件表面产生凹 坑的措施如下。(1)拉深时保证压机滑块的成 形力大小稳定。(2)拉深时保证压机的气垫压 力大小稳定。(3)拉深时托杆的顶起高度要相 同,且顶起高度的大小要保持定值。(4)模具使 用一段时间后要根据氮气弹簧的压力指示表中 指示值的大小变化或零件外观的质量判断向氮 气弹簧中充氮气。(5)要保证落料毛坯的尺寸 大小。
图1 一款SI TX’车型的右侧围外板
表面擦干净。(4)在模具表面及材料表面干净 的情况下,如果拉深时零件表面仍出现严重星 目,则这种材料不能用于外覆盖件的生产,需要
2.1星目产生的原因及预防措施 表面星目是指汽车外覆盖件在冲压生产中 表面出现的微小凸包,用油石检查冲压件的外 观质量时可以看到表面的微小亮点。这些微小 的缺陷会在涂装后引起光的杂乱不规则反射而 影响外观质量。 产生表面星目的主要原因如下。(1)材料 表面清洗不干净或清洗油不干净导致的原材料 表面脏。(2)开卷落料后的材料清洗后保存不 善或长期存放导致的原材料表面脏。(3)模具 清洗不干净或模具没有及时清洗导致的模具表 面脏。(4)原材料在热镀锌前母材表面脏。(5) 模具长期生产后表面镀铬层破坏,拉深时模具 与材料表面摩擦导致的材料表面脱锌。(6)生 产车间的防尘条件不好,生产现场有灰尘进入 材料表面和模具表面。(7)在人工线进行搬运 生产时,工人戴普通的防护手套作业时,普通防 护手套与板料摩擦产生的毛屑掉人材料表面和 模具表面。(8)修边冲孔工序中产生的切粉进 入模具中。 零件在冲压生产过程中出现表面星目的位 置点一般不固定,表面星目问题是冲压生产中 的难点问题。我公司委托外加工加工的几种外 覆盖件在人工线进行生产,车间的防尘条件不 好,加上曾因原材料脏,在冲压生产过程中出现 表面星目最严重的情况是1个零件表面出现20
分析冲压件成型存在的缺陷及解决对策

分析冲压件成型存在的缺陷及解决对策摘要:随着我国经济水平的不断的提高,加工制造业水平也在飞速发展,尽管其工艺已日趋成熟和完善,但还是存在一定问题尤其是冲压成型的工艺。
汽车工业是世界上最大的几个制造产业之一,汽车的需求量随着世界经济的快速发展迅速增加,这就要求汽车制造技术也要随之提高。
关键词:汽车冲压件;冲压成形;缺陷分析冷冲压是汽车制造过程的一个重要环节,外覆盖件作为车身外表面零件,表面不允许有皱纹、凹痕等缺陷,骨架件形状复杂,用于提高车身的刚性,并连接或固定内饰件及其它零件。
可以说,汽车覆盖件既是外观装饰性的零件,又是封闭薄壳状的受力零件。
由于车身的美观性和功能性等特殊需要,很多覆盖件整体轮廓内部带有局部形状特征,这对成形控制技术提出更多更高的要求。
分析拉伸过程中的应力应变状态,有助于分析拉伸过程中出现的工艺问题和质量问题。
1 汽车冲压件的运用冲压成可以说是一种有着悠久历史的生产加工工艺,有着生产效率高以及零件一致性等方面的优点,板材成形技术也得到汽车等加工制造业的高度重视。
研究显示80%左右的汽车零件是使用板材;中压制造的。
所以;中压成型技术水平的坏,会直接影响到加工制造业产品制造的成本、质量以及新产品开发的周期。
各个制造业厂商目前已经先后运用仿真技术用来指导产品设计以及制造,并目随着理论技术方面的不断完善,冲压成形仿真分析站在汽车等制造业的生产过程中应用越来越广泛,冲压成形的仿真分析为冲压生产也提供有力的条件,在早期设计阶段评价覆盖件以及模具的设计可行性,在试冲阶段则做好故障分析并解决问题,批量生产的阶段则可以进一步用来分析潜在的缺陷分析,从而进一步改善覆盖件的生产质量,从不断调整材料的等级。
可以说冲压件的运用对于汽车等机械制造行业的发展有着不可或缺的重要意义。
2 冲压成型过程产生缺陷的影响因素2.1 材料参数。
通常用成型极限曲线(FLD)来反映钣金的成型质量,对于该曲线拟合影响最大的参数包括硬化指数n和厚向异性系数r。
覆盖件冲压表面缺陷的产生原因及预防措施

覆盖件冲压表面缺陷的产生原因及预防措施1 引言大型覆盖件是指汽车的左/右侧围外板、左/右前翼子板、顶盖、左/右前门外板、左/右后门外板、后背门外板、发动机盖外板等冲压零件,组装后构成车身的外部形状。
大型覆盖件具有材料薄、形状复杂(多为立体曲面),结构尺寸大,尺寸精度高,表面质量要求高等特点。
大型覆盖件的冲压生产是汽车车身制造的关键环节,在冲压生产中常见的表面缺陷有:①表面星目;②表面凹坑;③表面局部变薄、拉裂;④表面局部起皱;⑤零件刚性差;⑥表面划伤。
2 表面缺陷的产生原因及预防措施图1所示为一款SUV车型的右侧围外板,材料为SP782AUJQ,料厚0.75 mm。
现以该零件为例对汽车大型覆盖件在冲压生产中常见表面缺陷的产生原因及预防措施进行探讨。
2.1 冲压生产中表面星目的原因及预防措施表面星目是指大型覆盖件在冲压生产中表面出现的微小凸包,用油石检查冲压件的外观质量时可以看到表面的微小亮点。
这些微小的缺陷会在涂装后引起光的杂乱、不规则反射而影响外观质量。
产生表面星目的主要原因有:①材料表面清洗不干净或清洗油不干净导致的原材料表面脏;②开卷落料后材料清洗后保存不善或长期存放导致的原材料表面脏;③模具清洗不干净或模具没有及时清洗导致模具表面脏;④原材料在热镀锌前母材表面脏;⑤模具长期生产后表面镀铬层破坏,拉延时模具与材料表面摩擦导致的材料表面脱锌;⑥生产车间的防尘条件不好,生产现场有灰尘落入材料表面和模具表面;⑦在进行搬运生产时,工人戴普通的防护手套作业时,普通防护手套与板料摩擦产生的毛屑掉入材料表面和模具表面;⑧修边冲孔工序中产生的切粉进入模具中。
大型覆盖件在冲压生产过程中出现表面星目的位置点一般不固定,表面星目问题是冲压生产中的难点,生产过程中出现表面星目最严重的情况是1个零件表面出现20多个星目,返修工时为10 min/件。
减少和消除冲压生产中的表面星目问题,从而降低返修率及返修工时是冲压生产中的重点管控项目。
汽车覆盖件冲压工艺常见缺陷
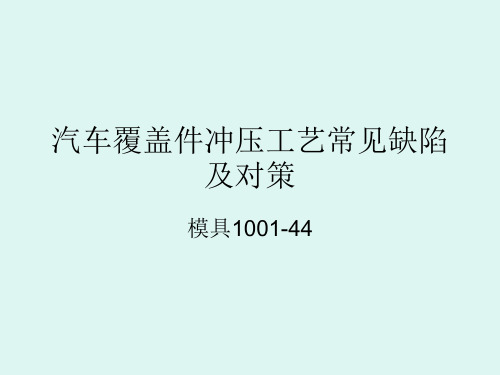
1.6起皱
拉伸件产生凸缘起皱和侧壁起皱主要是由于拉 伸时板料受压缩变形而引起的,通常采用提高板内 径向拉应力来消除皱纹,可通过增加拉伸筋、减小凹 模圆角半径、调整压料面的间隙和拉伸间隙来增大 压边力,避免起皱的发生。 日本薄钢板成形技术研究会对汽车覆盖件拉延 成型中的起皱现象进行了分类。该分类法把汽车覆 盖件拉延成形中的起皱分为4类,即法兰起皱、凹模 口圆角处起皱、侧壁起皱和凸模底部起皱等。根据 生产实践中零件皱纹发生的部位及其产生的力学原 因,还可将起皱按部位分为法兰起皱、悬空侧壁起皱 和凸模底部起皱;按应力原因则可分为压应力起皱、 剪应力起皱和不均匀拉应力起皱_3 J。
1.8压痕、麻点、磕碰、划伤
压痕、麻点、磕碰、划伤是车身覆盖件中最易发 生的表面质量缺陷。压痕、麻点是因为模具表面有 缺陷以及模具的压料面或毛坯表面不清洁,存在沙 土颗粒或其他异物,在冲压过程中形成覆盖件表面 的非正常痕迹,经油石打磨表面后反映出亮点、亮痕 等;磕碰、划伤的产生则可能发生在从钢板下料到焊 接装配的每一个环节,特别是容易发生在这些环节 的人工操作过程中。从概率上讲,工艺流程中零件 周转次数越多发生磕碰划伤的机会就越多。 另外,覆盖件材料的选用对覆盖件的质量也起 着重要作用
1.3棱线不清晰
棱线不清晰主要是因为模具形状、尺寸精度差,模具未压到底,工件定位不 准确等原因造成,而拉毛 主要是因为凹模圆角处状态不好以及润滑不良或模 具硬度不够等原因造成…。
1.4回弹
产生回弹的主要原因是因工艺方法不当和模具 结构不合理引起零件变形区的材料塑性变形不足。
克服回弹,可通过采用合理的工艺方法来改善板材 在成形过程中的应力状态,还可通过选用合理的回 弹角、回弹半径、模具间隙等模具工艺参数解决。
另外,拉伸温度和润滑状态对成形质量也有影 响。如果温度较低,板料成形性能较差,不利于拉出 理想的拉伸件。在拉伸过程中,金属材料与模具的 表面直接接触,相互作用力很大,使材料在凹模表面 滑动时产生根大的摩擦力,增加了拉伸所需的压力 和材料内的拉应力,这也是工件破裂的原因之一。 造成零件开裂的原因很多,在调整时应仔细检 查开裂状况、产生的部位,确定产生开裂的拉伸行程 位置,根据具体情况分析判断产生开裂的原因,从而 制定出解决开裂的具体方案。
汽车覆盖件成型过程中缺陷的产生原因和分析

控制回弹的方法
①选用屈服强度小的材料
②增加防回弹筋 ③热处理法 ④补偿法 ⑤多次成型法
⑥内侧圆角硬化法
⑦成型硬化加工法
参考文献
[1]李少岩.汽车覆盖件冲压成型过程中常见的缺陷[A].公路运输,2009(01) [2]施雄飞.车身外板冲压缺陷B].汽车与配件,2012(46) [3]赵栋.冲压件缺陷分析[A].理论与研究,2012(66) [4]王玉峰.冲压件调试生产常见缺陷分析及改进[B].汽车与配件,2013(27) [5]王玉峰.冲压制件翻边缺陷分析[B].汽车与配件,2013(02) [6]赵金升.冲压制件回弹研究[B].模具制造,2013(08) [7]韩宗斌.汽车表面覆盖件常见冲压缺陷及处理措施[B].装备制造技术,2012(8) [8]李淑慧.车身覆盖件冲压成形面畸变缺陷形成机理研究[J].机械工程学报,2013(03) [9]江东海.汽车覆盖件拉伸站中起皱、拉裂、回弹的分析[A].民营科技,2013(03) [10]郭瑞景.浅谈汽车冲压件成形及其缺陷分析[A].工程技术与产业经济,2010(02) [11] Liu Yuqi.QUANTITATIVE PREDICTION FOR SPRINGBACK OF UNLOADING AND TRIMMING IN SHEET METAL STAMPING FORMING[J]. Chinese Journal of Mechanical Engineering ,2003(16)
阳东永 工硕136班
一、前言
中国是汽车使用大国,据有关资料统计,中国汽车在 2013年销量将达到约1935万辆,而保有量更是将突破一亿。 对于汽车来说,其中一个重要组成部分就是冲压而成的车身 覆盖件,其表面质量尤为重要,除了考虑车身冲压件的一般 工艺特点外,其表面不允许有缺陷,棱线应清晰、平直、曲 线应圆滑、过渡均匀。另外,汽车覆盖件还需具有很高的尺 寸精度,以保证焊接和组装的准确性要求。因此,冲压成型 过程中缺陷的控制,是汽车工业中一个重要的环节。
浅谈汽车覆盖件冲压成型过程中的缺陷

浅谈汽车覆盖件冲压成型过程中的缺陷作者:孙倬来源:《科技探索》2013年第03期摘要:覆盖件是汽车的主要组成部件,板料冲压成型作为汽车覆盖件的一种关键加工技术,在汽车制造中有着至关重要的作用。
本文详细介绍了钣金冲压过程中常见的几种缺陷,并对缺陷成因及影响因素进行了分析,以期提高覆盖件的生产质量,降低生产成本,使其满足使用要求。
关键词:汽车覆盖件冲压成型缺陷分析覆盖件作为汽车的主要组成部件,其设计、制造的速度对汽车工业的发展有着直接的影响作用。
汽车覆盖件的重要生产方式之一即板料冲压成型,这是一种非常关键的制造技术,已广泛的应用于汽车、航空、电器等工业领域,尤其是在汽车制造中更为重要。
本文对汽车覆盖件冲压成型过程中的出现的缺陷进行分析,有着重要的现实意义。
1.汽车覆盖件冲压成型过程中常见的缺陷成型工序的制定是板材成形过程中的关键环节,其基本工序主要涉及到弯曲、胀形、拉延以及翻边。
板材成形是一个较为复杂的工艺过程,需要通过多次试验才能确定其成形工序以及工艺参数。
冲压件的材料以及加工过程的控制、覆盖件的模具设计和制造都会对产品的质量和价格造成不同程度的影响。
由于冲压成形过程的复杂性,其设计和控制难度较大,常会出现各种缺陷。
1.1拉裂深冲工艺中常见的缺陷之一即拉裂。
按照程度的不同,可将拉裂分为两种,分别为微观拉裂、宏观拉裂。
其中,微观拉裂是指工艺中产生无法用肉眼看清的裂纹,虽然裂纹有着较浅的深度,但部分材料已经失效;宏观拉裂则是指工件出现的裂纹或断裂可用肉眼看清。
一般来说,宏观拉裂是因过度拉胀所引起的,而微观拉裂则是因单纯的拉胀或单纯的弯曲所致。
无论是哪一种拉裂都是因局部拉应变过大所造成的。
就单纯的弯曲构建,相对来说,拉裂较为容易避免,可以采用简单的方法对弯曲区的最大拉应变作出准确的计算;就复杂的拉深件而言,要想对给定条件下的材料塑性流动情况作出准确的计算,采用传统的方法是很难做到的,这样以来就不容易判别出拉深工序是否存在拉裂缺陷。
分析冲压件成型存在的缺陷及解决对策

分析冲压件成型存在的缺陷及解决对策摘要:目前,汽车行业在加工制造冲压件中均能够使用冷冲压技术,但就具体而言,在冲压件的成型过程中会出现起皱、回弹以及毛刺等多种缺陷。
这些问题的出现会严重影响到生产的效益。
因此一旦在冲压件的成型中发生缺陷,就需要根据不同的情况针对性给予解决。
我国的重卡汽车行业得到了快速发展,其产销量也呈现出上升趋势,而且对于这一类型的汽车要求也愈发增高,其不但需要能够多拉和快跑,还在一定程度上对驾驶室的要求提出了美观大方的需求。
所以在冲压件的成型中更要注意存在的缺陷,从而及时给予解决,以便让重卡汽车行业得到进一步的发展。
关键词:冲压件成型;缺陷;解决对策汽车行业作为一个较大的制造产业,由于经济的快速发展,使得汽车需求量也在逐渐增长,尤其是重卡汽车这一类型。
其中钢铁以及化工等行业均能够到重卡汽车。
就冲压件来说,在汽车构成件中占比较大,如汽车外壳以及底盘等等。
同时因从车身功能性以及美观性等方面的需要,许多覆盖件的轮廓内部中具备局部形状的特点,这在一定程度上对冲压件的成型提出了较高的要求。
因此需要分期其成型中的缺陷,给予有效的解决对策。
一、冲压件的应用和成型过程第一,应用方面。
就冲压件成型来说,其是一种较为悠久的加工工艺,存在效率高和零件具备一致性等多种优势,引起了汽车行业的重视。
研究表明,大部分的汽车零件是采用板材冲压进行制造而来的。
在冲压件的成型中通过使用仿真技术,可以有效分析模具中的可行性,而且还可借助模拟来获取冲压件,但是会在一定程度上出现缺陷。
这时通过借助有关技术来解决存在的缺陷,可以显著提高冲压件质量,并且还可以对制造材料的等级进行明显提高。
所以,就需要提升冲压件成型的工艺水平,这样可以将重卡汽车部件的质量进行增强,确保其整体质量[1]。
第二,成型过程。
就实际情况来说,冲压件作为一种裁剪板材,通过采用拉伸以及成形等来获取想要的形状和规格等,是重卡汽车中一种非常重要的汽车零件和重要组成,而且还会在一定程度上能够影响到整体车辆的装配质量。
汽车覆盖件冲压成型过程中的常见缺陷及分析

Abstrac:t This paper describes meta l shee t ramming fo rming, w hich is the key manufacture technology of automotive cover pane ls, and its mi po rtant position. It p resents the causes of the de fects (frac turing, th inning, w rinkling), and the influenc ing factors (materia l parame ters, d -ie surface pa rameters, manufacture p rocess parameters). Through an ana lysis of parameter smi ula tion of the scro ll o f a certa in type ca r engine, a more in tu itive unde rstand ing of the factors in pressing forming is made and the suggestions are g iven for solving the defects. Key Words: Meta l shee;t Ramm ing fo rming; De fects; Ana lysis; Solve
3 冲压件拉深仿真模拟
车身冲压覆盖件高点、凹坑面品不良问题探讨

2.8轴承注油工艺的研究与改进以往轴承润滑用的是手工涂抹方式,油脂只能涂在轴承的外端面。
油脂无法进入轴承内部,轴承无法得到有效润滑。
因此我们改进轴承注油方式,保障其轴承油脂的填充量和良好的润滑效果。
经过对非密封式轴承的研究和分析,结合现场铁水车运行距离较短,停时较长、运行速度较低,轴承发热量小的特点,研究了轴承密封注油工艺,并设计了轴承注油机。
通过实施对铁水车轴承注油,满足了其轴承的润滑要求。
如轴承注油示意图1所示:通过设计注油小车,制作轴承注油模具,将注油模具卡在轴承端面上。
这样油脂通过注油管道进入到轴承内部,满足了轴承的润滑要求。
图1轴承注油示意图采用封闭式注油方式,可以使油脂充满轴承内腔。
①采用密闭式注油的轴承,由于自身的运用特点在运用过程中不会因油脂多而产生较大热量导致燃轴。
②在注油过程中,轴承前端面进入的油脂在压力的作用下能够将旧油脂挤出,解决了旧油脂驱除难的技术难题,提高了注油效率的同时保证了轴承润滑质量。
由于设计的注油卡盘紧固后紧贴于轴承外侧,虽然注油过程中轴承内腔填充满了油脂,但车辆运行后油脂即可有部分进入轴箱,使轴承室内油脂填充保持在1/2~2/3,能够充分满足轴承正常工作的需要。
2.9研制全功能轴承压装机现有的Wy 型滚动轴承压装机能够实现352226X2-2RZ型轴承的标准压装,即:定位、顶起、快进、夹紧、工进、保压、退回、降下,这八个工步按程序设定自动运行,从而完成轴承压装工作。
但是352230-2Z/YA 、22330CA 、22328CA 等其他五种轴承外形尺寸各异,所以不能自动完成定位等工序。
因此我们联合厂家对该设备进行改造,使得能够实现现有轴承的全自动压装。
3结束语运用实践表明冶金企业铁道车辆轮对综合检修技术研究与应用项目实施效果良好,不仅轮对检修项目全面,而且轮轴检修质量极大的提高了,并且增强了冶金铁道车辆运行的安全可靠性。
1技术背景为满足车身外覆盖件面品要求,大多数厂家会投入大量资金改善车间环境,或投入人力对制件进行返修,同样会造成大量资金投入,尤其镀锌板手修会造成制件防腐能力下降,从而导致售后三包问题产生,既造成成本损失、又造成企业品牌形象受损。
- 1、下载文档前请自行甄别文档内容的完整性,平台不提供额外的编辑、内容补充、找答案等附加服务。
- 2、"仅部分预览"的文档,不可在线预览部分如存在完整性等问题,可反馈申请退款(可完整预览的文档不适用该条件!)。
- 3、如文档侵犯您的权益,请联系客服反馈,我们会尽快为您处理(人工客服工作时间:9:00-18:30)。
当前汽车覆盖件冲压工艺应用及其缺陷因素分析
摘要本文主要从汽车覆盖件冲压工艺的概述出发,探讨了汽车覆蓋件的冲压工艺设计应用,并提出了若干影响冲压成形过程缺陷产生的因素,以期促进汽车工业的健康发展。
关键词汽车;覆盖件;冲压工艺
1 汽车覆盖件冲压工艺的概述
所谓汽车覆盖件,主要指构成汽车车身或者驾驶室、覆盖发动机和底盘的异形体表面和汽车零件。
通常,汽车覆盖件包括外覆盖件和内覆盖件,外覆盖件如车门外板、顶盖等,内覆盖件如车门内板和发动机盖内板等。
在汽车车身设计时,要从汽车整体造型和结构功能角度进行覆盖件设计,高度重视覆盖件的制造工艺性。
通常,覆盖件的冲压工艺性主要涉及以下几方面要求:
1.1 覆盖件分块尺寸的可行性
覆盖件分块不同决定零件的轮廓尺寸和结构形状,从设计制造角度考虑分块尺寸应越大越好,不仅可减少整车零件的数量和车身表面可见焊缝,提高车身结构制造精度与外观完整性,且还可减少冲压模具的数量和车身生产过程中工装与人力资源的投入。
但由于工艺手段和生产条件限制,就需根据现有条件和技术来分析覆盖件分块尺寸的可行性。
1.2 一次拉延成型的可能性
由于覆盖件结构尺寸大、形状复杂、材料薄及精度高等决定了需一次拉延成型。
因此,在覆盖件设计时要注意:①覆盖件轮廓形状尽量简单匀称,使拉延应力均布;②覆盖件形面变化尽量均匀,以保证拉延凸模能顺利进入拉延凹模;③拉延底面的形状尽量平顺,避免出现尖底和凸模接触不到的负角区域。
1.3 翻边整形的简易性
如果覆盖件达不到一次拉延成型的工艺性要求,就要增加翻边整形工序。
因此,需注意的是:①翻边尽量设计成垂直方向且翻边方向相同,以简化模具结构;
②不同方向翻边在交接处应有适当的距离,以利于翻边刃口的布置;③避免曲面翻边,特别是压缩型翻边;④翻边线尽量直,以减小修边的复杂程度,提高模具寿命。
总之,在覆盖件设计中,要综合考虑上述冲压工艺性要求,在保证覆盖件美观和功能前提下加强冲压工艺的优化,以达到用最少模具、最低材料的消耗生产出合格覆盖件产品。
2 汽车覆盖件的冲压工艺设计应用
汽车覆盖件的冲压工艺设计是十分重要的工作,覆盖件冲压工艺设计合理性,直接影响覆盖件成形质量,高质量的覆盖件冲压工艺设计,能提高覆盖件冲压质量,避免破裂、起皱和回弹等严重质量问题,进而提高驾驶舒适性和车身的疲劳耐久性能。
2.1 坯料设计
在冲压工艺设计中,板料毛坯设计十分重要。
在确定坯料材料情况下,坯料设计主要指毛坯的形状和尺寸设计。
合适的毛坯形状和尺寸设计,可以改变板料在成形过程中的流动阻力,提高覆盖件的成形性能;有时在其他参数不变的情况下,仅仅通过改变毛坯的形状大小,就可以消除覆盖件的成形缺陷。
2.2 冲压方向设计
在覆盖件拉伸成形时,冲压方向设计的合理与否,不仅影响凸模能否顺利进入凹模型腔,也决定了板料成形后的最大变形程度及塑性应变是否充分,同时合理的冲压方向设计还有利于防止开裂起皱等冲压缺陷的产生,一般而言,冲压方向的设计要考虑以下几条原则:
(1)保证凸模能够全部进入凹模,使零件的全部空间形状能够一次拉伸成形出来。
(2)确保毛坯与凸模具有良好的初始接触条件,避免毛坯和凸模间的相对串动,有利于毛坯的塑性变形,并提高冲压件的表面质量。
(3)有利于后续的模具结构设计,尽量保证后续能够采用垂直修边、垂直翻边和整形。
2.3 拉延筋设计
拉延筋对汽车覆盖件拉深的结果有很大影响。
在拉伸过程中,为了促进板料的塑性变形,板材必须在坯料周围产生拉应力。
一般说来,只有在压边力作用下,压力机表面与材料之间的摩擦力才足以控制板的流动。
因此,为了提供足够的流动阻力以满足坯料塑性变形和塑性流动的要求,必须在压力机表面上设置拉伸杆。
2.4 汽车覆盖件工艺补充面的设计
添加工艺补充面是为了顺利实现拉延,但是在后续修边工序中,工艺补充面需要被切除,成为工艺废料。
所以在保证覆盖件顺利拉延的前提下,尽量减小工艺补充面,以提高板料的材料利用率。
在大批量生产中,对大中型冲压件而言,原材料成本占冲压件成本的60%~70%,因此,提高材料利用率具有十分重要的
意义。
3 影响冲压成形过程缺陷产生的因素分析
3.1 材料参数因素
材料自身相关参数对覆盖件成形也具有重要的影响,因此,可从成形极限曲线的走向方面进行分析。
当硬化指数n增加时,不仅会使破裂成形极限曲线得以提高,还会使材料拉延的均匀性也提高。
胀形变形也是随着硬化指数n的增大,极限曲线向右移动,从而获得更大的等效应变;随着厚向异性系数r值的不断增长,破裂极限曲线与变形路径交点值也随之增大,当r值比1大时,板厚方向的变形较平面内更为困难,拉深难以变薄,压缩也很难增厚,从而可以有效避免破裂和起皱问题。
3.2 模具型面参数因素
凹模口圆角半径的取值是拉延成功与否的一个关键因素,半径过大、过小都对成形有直接影响。
在常压边力控制下,如果采用均一圆角来进行凹模设计,为确保板料拉延成功,要求圆角半径不得小于4mm,否则会引起板材拉裂。
为了提高成形质量,保证后拉伸的方便性,必须改变传统的均匀圆角的设计。
模具的拐角值取决于变形材料的流动条件,模具的角度应逐渐转移。
对于更复杂的覆盖件的数值模拟,该方法通常不提倡,因为工作量大,但通过使用模具口的均匀拐角半径和使用其他方法,例如涂层,提高了材料的流速的均匀性。
3.3 工艺过程参数因素
所谓工艺过程参数是指除模具的几何参数以及拉延板料的材料性能外,一般在成形时方出现并起作用的过程参数,主要包括摩擦力、压边力、成形阻力、成形速度以及变形路径等。
其中,拉延筋的布置和成形阻力尺寸的确定对板的成形设计有着重要的意义。
拉延筋的布置主要遵循以下原则:首先,在压边圈内轮线设置拉延筋,不仅增加了进料给阻力,而且增加了材料的变形程度。
其次,局部短拉延筋布局容易起皱,从而防止纸张起皱。
最后,为了更好地调节进给阻力和进给量,宜在拉延深度大的直线部位进行拉延筋设置,而不宜在拉延深度大的曲线部位进行拉延筋设置。
4 结束语
总之,随着我国汽车工业的快速发展,对于汽车覆盖件冲压工艺的要求也越来越高,由于汽车覆盖件冲压工艺是一项复杂的工作,往往在冲压过程中容易受到诸多因素的影响,导致产生缺陷。
因此,在汽车覆盖件冲压过程中,不仅要加强其冲压工艺的应用,同时还要加强缺陷的分析,进而提升覆盖件的生产质量,促进汽车工业的健康发展。