OQA作业规范
样机出货管理规范

样机出货管理规范编制/日期审核/日期批准/日期1.目的规范样机出货流程,确保样机出货受到管控,客户同意接收已知 Bug。
2.适用范围本规范适用于公司及工厂样机出货的管理。
3.定义3.1样机: 一般分为初样和正样,初样是指公司为实施研制合同、研发合同、内部定制化订单等而研发制作生产的产品,也称为研制产品;正样是公司为实施生产试制合同、内部试产等而制作生产的产品,也称为试制产品。
4.权责4.1销售工程师:提出样机需求。
4.2产品经理:根据样机需求编制产品配置表及客制化需求 Check List 等资料给到研发进行设计。
4.3项目经理:负责依照产品工程师的需求组织研发人员进行设计并完成样机的制作与出货管理。
4.4中试工程师(品质工程师):负责结合产品经理提供的资料、客户其它需求等制定试验与出货检验规范主导检验与试验,输出测试报告与结论。
5.程序内容5.1销售工程师将收集到的客户新需求经评审通过后以样机需求的形式提交产品经理,产品经理结合客户的实际需求编制配置表与客制化需求 Check List,适用时编制《立项报告》经评审通过后转研发进行设计开发。
研发完成设计经试组、调试后转中试工程师依相应的试验(检验)规范进行试验(检验)后给出试验(检验)报告。
相关报告在中试经理签核后提交项目工程师。
5.2项目工程师在接到试验(检验)报告后对其中的 Bug 跟进改进并将改进后的样机交中试验证。
相关 Bug 的改进在超出项目进度允许的范围而客户要求出货时,由中试工程师填写《样机出货风险评估单》,产品经理组织评估后启动特采流程,特采通过后方可出货。
项目经理对最终出货把关,严禁存在 Bug 的问题样机不办理任何审批手续出货。
5.3出货后样机未解的 Bug 由项目经理继续跟进解决。
5.4出货的样机由产品经理跟进客户端在应用及测试中发现的问题并反馈到内部给予解决。
5.5在工厂装配后直接出货的样机由工厂品质把关,依照 OQA 检验规范相关规定作业。
公司OQA检验作业指导书

OQA作业指导书
1.0目的:
明确质量部对生产包装成品检验对的流程,确保成品质量符合客户要求和相关规定。
2.0适用范围:
本指引适用生产成品入库的质量控制。
3.0术语和定义:
无
4.0职责:
4.1质量部:负责对包装成品进行抽检,对抽检不合格成品开《成
品(半成品)不合格处理单》,跟进成品不合格改善结果。
4.2 生产部:负责成品的包装,及不合格批成品的处理。
4.3 工程部:负责对抽检不合格成品的分析,及出具返工工艺。
4.4 PMC:负责编制返工计划。
5.0工作程序:
5.1 质量部对生产包装的成品进行抽检,以每100-150PCS为1个
抽检批,按成品检验标准或签样样品进行检验,抽检结果记录《OQA检验报告》中,报告主要记录抽检产品的序号,不良品的序号及缺陷描述,及批次检验结论。
5.2 OQA按GB2828.1-2012 LevelⅡ来抽样,CRI=0;MAJ=0.65;MIN=1.5。
第 1 页共2 页。
oqa检查内容
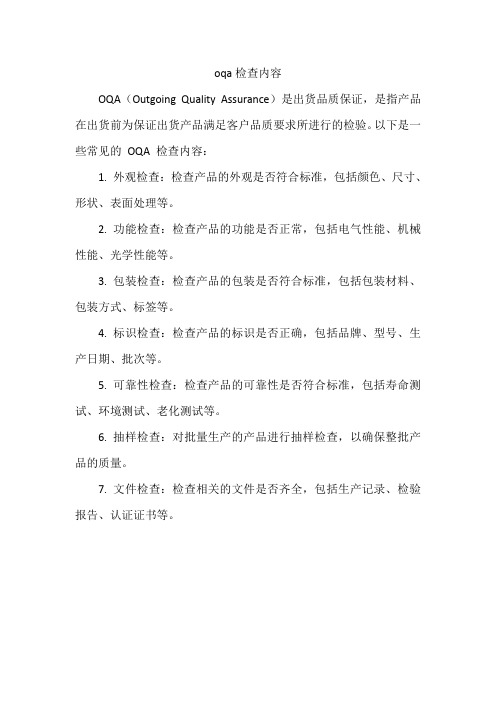
oqa检查内容
OQA(Outgoing Quality Assurance)是出货品质保证,是指产品在出货前为保证出货产品满足客户品质要求所进行的检验。
以下是一些常见的OQA 检查内容:
1. 外观检查:检查产品的外观是否符合标准,包括颜色、尺寸、形状、表面处理等。
2. 功能检查:检查产品的功能是否正常,包括电气性能、机械性能、光学性能等。
3. 包装检查:检查产品的包装是否符合标准,包括包装材料、包装方式、标签等。
4. 标识检查:检查产品的标识是否正确,包括品牌、型号、生产日期、批次等。
5. 可靠性检查:检查产品的可靠性是否符合标准,包括寿命测试、环境测试、老化测试等。
6. 抽样检查:对批量生产的产品进行抽样检查,以确保整批产品的质量。
7. 文件检查:检查相关的文件是否齐全,包括生产记录、检验报告、认证证书等。
OQA作业规范

3. 权责 权责:
3.1 OQA 检验员:负责对制造部门送检入库的成品或半成品进行出货检验。 3.2 OQA 领班:及时安排检验员对送检产品进行检验并监督检验员按照规范正确作业,对检验数据进行统 计整理,定期发放产品出货品质报告,并监督确认因此产生的矫正预防措施执行性和有效性。 3.3 组长: 负责 OQA 检验作业指导书的制定,修改,指导和确认检验员作业,对异常进行追踪和确认。 3.4 制造: 负责成品和半成品的送检,对 OQA 判退品执行矫正预防措施。 3.5 PE: 负责对 OQA 检验发现的电性不良板进行分析,并依据分析结果拟定矫正预防措施。
轩敏电子(深圳) 轩敏电子(深圳)有限公司
Plexton Electronics(Shenzhen)Limited OQA 作业规范
版本 V1.0 新发行 修订内容 修订页次 文件编号 生效日期 版本 V1.0 修订日期 页次 修订者
NO
1
2
3
4
5
6
7
8
9
10
11
12
13
14
15
16
17
18
分 发 单 位
施行正常检 验 10 批中, 无 1 批被拒收 则用减量检 验
严格检验
减量检验
抽样转换图 抽样转换图
6.15:抽样计划调整转换只针对同一机种,如客户有特殊要求则依客户提供之抽样计划与允收 标准执行.
6.2 OQA 检验作业: 检验作业:
6.2.1: 送检单位需按正常送检批量为单位将包装好的产品送至待验区, 并立即开送检单给 OQA 检验员检验. 6.2.2: 送检核对: 检验员根据生产单位所开的送检单首先进行资料核对, 核对内容: 产品客户, 规格,机种名称,工单号,数量,要与生管出货排程和客户出货要求相关资料相符才接受检验. 6.2.3: 资料准备: 对应机种的 PACK JOB-BOM, 验收规范, 生产通知单, 出货排程, PI, ECN, OTCN, SPEC 及客户要求的相关文件. 6.2.4:具体检验内容: 6.2.4.1:核对客户提供的备忘录,查看出货客户有无特别要求,逐行核对 JOB-BOM 料号是否 与包装实物相符,验收规范核对要素以从里到外的原则检验, 6.2.4.2:半成品出货工令/风扇是否与出货排程要求一致,频率贴纸/风扇贴纸内容需与生产通 知单/PI 内容一致。若不相符首先查看有无 ECN 更改。条码贴纸位置,条码编排格式,附件放置 位置,彩盒贴纸位置是否与规范一致,彩盒贴纸内容需与料号描述一致,条码内容必需与出货排 程、PI 要求一致。 6.2.4.3: 对半成品功能测试依据《OQA 检验报表》上的项目逐一进行检验,并填写记录。对 所配出货附件必须实装使用,确保其功能正常,检验到不良项目时,需在该项目上注明 NG。 6.2.4.4: 根据检验情况在送检单上注明检验判定结果,如合格在送检单上签字放行。
IPQA作业规范

5.1.8.1测试段IPQC根据《产品软件及流程图的联络单》确认产线的测试软件是否OK;
5.1.8.2测试段IPQC根据《各机型测试流程及校准项目确认表》和《产品软件及流程图的联络单》确认校准文件及参数是否正确;
5.1.8.3测试段IPQC确认点屏工位是否是按《功能测试项目表》进行测试。
a.每次更换机型、换线或执行ECN时执行(更换机型、换线或执行ECN时执行首件数量为8PCS)
b.正常生产过程中每隔2小时需进行一次(每2小时的首件数量为4PCS)
5.1.1.2每次更换机型、换线或执行ECN时执行的首件,必须经IPQC跟踪确认OK后产线方能正常进行生产,各段确认结果及时填写到《首件确认一览表》中。
5.1.7OQA外观检验
5.1.7.1 OQA根据《PCBA外观检验标准》对首件板进行外观检验,如有问题立即反应给生产、设备人员进行改善,确认合格后才通知物料员把板过往测试。
5.1.7.2每次更换机型、换线或执行ECN时执行的首件为节省产线停线待首件时间,OQA外观检验该步骤可以省略,外观部分就由炉后QC加严检验,并且分板也直接采用炉后手工分板。
5.2.3.4非同规格物料换料时IPQC需在BOM表、ECN或客户确认可以使用的异常单上核对清楚替代关系,对OK后在通知产线进行使用的同时需对换料后生产出来的前4-8PCS板做首件确认(炉前锡膏板确认→ OQA外观检验→功能测试)。首件过程中如有出现因此物料所导致的功能不良,产线IPQC需及时通知组长/SMT生产进行处理。
5.3.2.2散料上线使用时需确认散料的丝印是否与实物一致;方向是否与位号图标示方向一致。
5.4印锡厚度检查
5.4.1各线每2小时取GPX印刷机前、后刮刀各一片测量锡膏印刷厚度,将量测值及时记录在《锡厚初期制程能力CPK评估表》。量测完毕需在十分钟内将测量板还于SMT产线处理。量测时发现锡厚异常时应及时反映给线上组长和工程处理、改善。
OQA出货检验规范

通现象是否符合技术要求。
4.7、绝缘电阻检验需做绝缘电阻测试的产品,需抽取相应数产品使用校对合格的绝缘电阻仪检查各不相互接触的引脚绝缘承受度应否符合技术要求。
4.8耐电压检验需做耐电测试的产品,需抽取相应数产品使用校对合格的耐电压仪检查各不相互接触的引脚耐电压承受度应否符合技术要求。
4.9可焊性试验抽取相应数量放置于温度为180±5℃加热箱中进行焊前预热,时间为120min,加热后进行可焊性试验,将试件垂直置于锡液深度为2-4㎜中,温度255℃±5℃、时间2秒±0.5秒,快速取出检查表面焊锡面需达到浸入面积的90﹪以上,且表面平滑(有回流焊要求的做回流焊试验)。
以10倍率以上镜头对焊锡正反两面进行观察,视浸锡部位是否有峰孔状、块状、虚焊、浸锡不均匀、未上锡及试件是否出现严重变色等不良现象。
4.10回流焊检查抽取相应数量放置于PCB板,回流焊设备设定温度为第一段:240±5℃、第二段:270±5℃第三段:330±5℃、第四段:270±5℃、第五段:250±5℃,将PCB板放置于回流焊卷动链,转速为:470,待整个过程结束后将产品取出观察其插针表面是否有发黑、发黄、严重缩锡等不良。
5、判定/处理依据检验卡对检验结果参照主次缺点允收水准接收值进行综合判定,完全符合要求则在送检上判定为合格,若产品状况出现4-10项任一条件不相符超过主次缺点允收水准接收值,应判定为不合格处理,并将不合格品进行标识,立即开立《品质异常处理单》报上级进行审批处理,描述不合格原因并附不合格样品,并对各项检验状况记录于《成品最终逐批检记录单》报上级审批后存档。
附表:OQA检验规范(详见下页)。
IQC、PQC、OQA工作流程与工作要求

品质部
• 1、IQC,PQC,OQA的定义及作用 • 2、IQC,PQC,OQA工作职责及内容 • 3、检验工作要求
IQC定义
• IQC:英文全称为:Incoming Quality Control,意思为来料质量控制。IQC的工作 方向是从被动检验转变到主动控制,将质 量控制前移,把质量问题发现在最前端, 减少质量成本,达到有效控制,并协助供 应商提高内部质量控制水平。IQC不仅影响 到公司最终产品的品质,还影响到各种直 接或间接成本
IQC工作内容
1、进料检验又称验收检验,是控制不让不良物料进 入物料仓库的控制点,也是评鉴供料厂商主要的资 讯来源。 2、所进物料,因供料厂商的品质信赖度及物料的数 量、单价、体积等,加以规划为全检、抽检、免检 。 a、全检:数量少,单价高; b、抽检:数量多,或经常性的物料;
c、免检:数量多,单价低或一般性补助或经认证为 免检厂商或局限性的物料; 3、检验项目 (1) 外观检验; (2) 尺寸、结构特性检验; (3) 电气特性检验; (4) 化学特料检验; (5) 物理特性检验; (6) 机械特性检验;
(3)破坏性检验。
PQC岗位职责
• 1、根据每天生产,严格按照检验标准来检查生产首件、 巡检产品;
• 2、将检查后的首件品盖上合格的印章,并摆放在相应的 位置;
• 3、不合格情况出现时,应立即通知相关人员改善,避免 造成批量性的不良品;
• 4、对品质不稳定的产品要进行跟踪、有问题时应及时汇 报上级或相关人员,并找出解决方法,及时解决问题;
• 6.新产品、新员工是否重点巡查,特采、代用、试产、让 步放行的必须重点稽核、记录情况及结果反馈
4、检验方法 (1)外观检验:一般用目视、手感、限度样本。 (2)尺寸检验:如游标、分厘卡、投影仪、高度规及三次 元。 (3)结构特性检验:如拉力计、扭力计。 (4)特性检验:使用检测仪器或设备。 5、抽样检验 5.1 抽样计划 5.2 品质特性: 分一般特性与特殊特性。 一般特性:如外观特性。 (1)检验工作容易;如外观特性,生产品质有直接重要影 响。 (2)品质特性变异太高。
OQA出货检验作业规范书

3.3 膠量檢驗: 針對出貨達創成品每批抽檢 5PCS 確認膠量(包含確認鐵芯是否有松動不良)。 4. 允收水準﹕AC = 0 RE = 1 5. 檢驗依據﹕
5.1 抽樣依據《抽樣檢驗作業指導書》進行抽樣作業﹔ 5.2 外觀檢驗﹕依據出貨《成品外觀檢驗標准》進行作業﹔ 5.3 尺寸(機構)檢驗﹕依據《外觀 SOP》進行作業﹔
5.4 電氣功能檢驗﹕依據《測試規格書》進行作業﹔ 5.5 包裝檢驗﹕依據《包裝作業規範》進行作業﹔ 5.6 出貨查核﹕依據《出貨通知單》《包裝作業規範》進行作業。 6. 檢驗方法﹕
6.1 外觀﹕以放大鏡﹑顯微鏡﹑目視(距離 30cm) 檢驗。 6.2 尺寸﹕以數顯卡尺﹑千分尺﹑塞規﹑投影機﹑模具等量具檢驗。 6.3 機構: 依相關之規定、指導書等進行檢驗。 6.4 電氣功能:以儀器設備依各產品之功能需求進行測試檢驗。 7. 檢驗設備﹕ 依《測試規格書》所規範之儀器、設備。
10.2 檢驗結果為拒收 開具《不合格品處理單》 → 經品保課長簽核(外觀與機構不良) → 工程部工程師簽核(尺寸與電氣不良) → 品保經理
判定處理方式 → 相關責任單位處理 → OQA 重檢 → 重復規定之檢驗流程
核准﹕
審核﹕
編制﹕
日Q A 出貨檢驗
流
程
圖
版本/次
10. 檢驗流程﹕ 10.1 資材發出《出貨通知單》通知出貨 → 倉庫依據《出貨通知單》進行數量及產品備貨 → 依據相關資料﹑規定進行 拼箱﹑貼標簽 → OQA 依據相關資料﹑規定對出貨產品進行檢驗 → OQA 蓋章(PASS﹑日期﹑檢驗員代碼等) → OQA 填寫《出貨檢驗報告表》及《出貨查檢表》→ 品保課長核准 → 出貨
9.4 《特采出貨申請單》
9.4.1 遇檢驗異常但需特采放行時填寫此單。 9.4.2 由出貨責任單位(資材)提出申請。 9.4.3 經由資材﹑工程﹑品保單位確認﹐管理者代表核准。
最新《OQA检验作业指引》
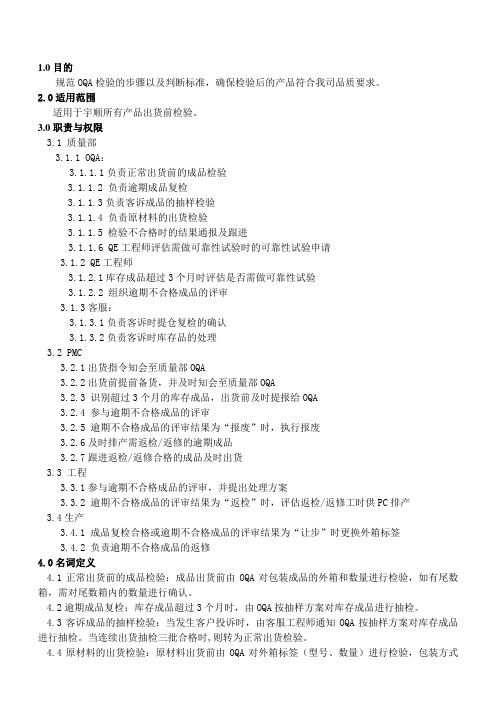
1.0目的规范OQA检验的步骤以及判断标准,确保检验后的产品符合我司品质要求。
2.0适用范围适用于宇顺所有产品出货前检验。
3.0职责与权限3.1 质量部3.1.1 OQA:3.1.1.1负责正常出货前的成品检验3.1.1.2 负责逾期成品复检3.1.1.3负责客诉成品的抽样检验3.1.1.4 负责原材料的出货检验3.1.1.5 检验不合格时的结果通报及跟进3.1.1.6 QE工程师评估需做可靠性试验时的可靠性试验申请3.1.2 QE工程师3.1.2.1库存成品超过3个月时评估是否需做可靠性试验3.1.2.2 组织逾期不合格成品的评审3.1.3客服:3.1.3.1负责客诉时提仓复检的确认3.1.3.2负责客诉时库存品的处理3.2 PMC3.2.1出货指令知会至质量部OQA3.2.2出货前提前备货,并及时知会至质量部OQA3.2.3 识别超过3个月的库存成品,出货前及时提报给OQA3.2.4 参与逾期不合格成品的评审3.2.5 逾期不合格成品的评审结果为“报废”时,执行报废3.2.6及时排产需返检/返修的逾期成品3.2.7跟进返检/返修合格的成品及时出货3.3 工程3.3.1参与逾期不合格成品的评审,并提出处理方案3.3.2 逾期不合格成品的评审结果为“返检”时,评估返检/返修工时供PC排产3.4生产3.4.1 成品复检合格或逾期不合格成品的评审结果为“让步”时更换外箱标签3.4.2 负责逾期不合格成品的返修4.0名词定义4.1正常出货前的成品检验:成品出货前由OQA对包装成品的外箱和数量进行检验,如有尾数箱,需对尾数箱内的数量进行确认。
4.2逾期成品复检:库存成品超过3个月时,由OQA按抽样方案对库存成品进行抽检。
4.3客诉成品的抽样检验:当发生客户投诉时,由客服工程师通知OQA按抽样方案对库存成品进行抽检。
当连续出货抽检三批合格时,则转为正常出货检验。
4.4原材料的出货检验:原材料出货前由OQA对外箱标签(型号、数量)进行检验,包装方式不做管控,如有尾数不需拆箱检验。
OQA作业检验规范
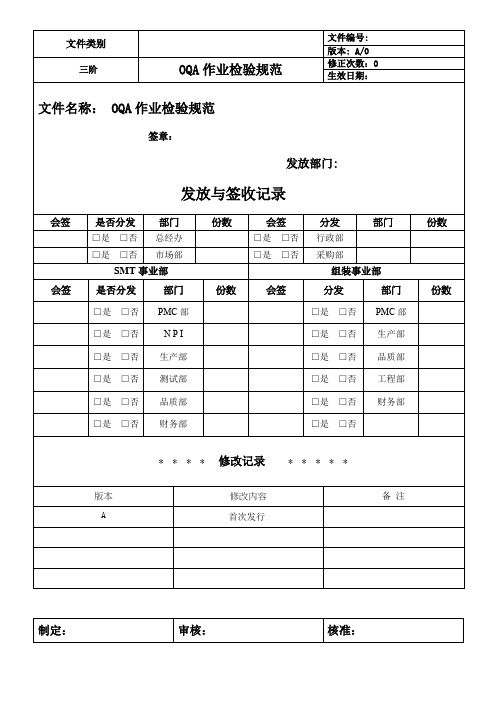
5.2.5检验复议:产线对功能不稳定品质问题批次要求复议时,由工程部对不良机进行分析确认,分析结果知会客户工程部。经客户同意后,可不上线返工,否则必须执行品质判定结果。
6.记录单:
6.1《批退通知单》
6.2《成品抽样检验报告》
5.2成品机的检验
5.2.1成品抽样:抽检按《MIL-STD-105E抽样标准》,一般Ⅱ级水平抽样进行。
5.2.2成品的检验:
A.QA检验员按《成品检验标准》,检验生产部报检批次成品机。对不合格报检批次成品,填写《批退通知单》,通知生产部产线负责人(拉长或助拉)。检验合格成品,通知货仓成品仓管员入库。
份数
□是□否
总经办
□是□否
行政部
□是□否
市场部
□是□否
采购部
SMT事业部
组装事业部
会签
是否分发
部门
份数
会签
分发
部门
份数
□是□否
PMC部
□是□否
PMC部
□是□否
N P I
□是□否
生产部
□是□否
生产部
□是□否
品质部
□是□否
测试部
□是□否
工程部
□是□否
品质部
□是□否
财务部
□是□否
财务部
□是□否
* * * *修改记录* * * * *
B.检验记录:品质部OQA对每周生产部各产线判退批次进行记录《OQA成品批退记录表》;对每天生产部各产线报检批情况记录《成品抽样检验报告》。
5.2.3成品的判定:检验员抽检结果,按《成品检验标准》检验项目AQL值进行判定。
OQA作业流程规范指引

OQA作业流程规范指引1.目的:确保公司所有待出货产品和客户返回产品都被有效检验及控制。
2.范围:本程序适用于品质部OQA内部所有检验员、工程师的作业指导。
3.职责:3.1生产部:负责将已生产好的产品及填写好送检通知单送至QA检查;3.2品质部:负责对送检产品及时进行检验,记录检查有关情况和结果并返馈给相关部门。
4.管理规范:4.1 对于待检的产品, QA首先要核对产品送检通知单上以下内容是否填写且填写内容是否与实际相符:工段、客户、产品名称 (或P/N)、订单号(WO#/KIT#)、送检时间、计划出货时间、送检类别、送检次数及送检数量等。
其中送检类别包括正常送检、新产品、维修品、返修品、QA拒收产品等。
另外,送检单上要有送检人签名及该工段领班以上管理人员签名确认,QA才可对此产品进行检验,且在产品送检通知单上签名并注明接收时间,放上“QA在检”状态牌,QA人员根据产品送检通知单上计划出货时间来进行优先检查。
4.2 一般客户产品的抽样检验抽样标准使用ANSI/ASQC-Z1.4-1993,采用正常加严转换单次检验水平II 级。
对ISO/TS16949产品采用零缺陷抽样检验标准。
具体参考: 抽样计划使用说明Q-OP-MR-008.品质允收水平(AQL):根据客户的要求不同而有所不同,具体参考该客户产品的《QA出货检查标准》。
致命缺陷(CR):可能影响产品的安全使用或导致产品主要性能失效的缺陷;严重缺陷:(MA):可能影响产品性能失效或降低性能或影响产品形象的缺陷;轻微缺陷:(MI):任何不符合既定要求又不严重影响产品外观或性能的缺陷;检验程序采用正常检验、加严检验、停检检验三种程序,依照标准采用转换原则进行状态的检验。
正常加严,在正常检验状态下,如果连续5批中有2批被拒收,则由正常检验转换为加严检验;加严正常,在加严检验状态下,如果连续5批被允收,则由加严检验转为正常检验;停止检验:在加严检验状态下,如果退货批数累积到3批或连续2批被拒收将停止检验,直至责任方作出书面改善报告并且措施已被执行方恢复检验,检验从正常开始。
OQA作业指导书

5.2.7OQA将检验结果记录及送检单交本部组长确认后,OQA与测试部当班组长进行交接。
5.2.8当判定拒收时,由OQA开出重工通知单,给相关单位进行重工处理。
5.2.9待相关单位处理完毕后由相关单位通知品质部,品质部再进行抽检,直到合格为止。
份数
□是□否
PMC部
□是□否
PMC部
□是□否
N P I
□是□否
生产部
□是□否
生产部
□是□否
品质部
□是□否
测试部
□是□否
工程部
□是□否
品质部
□是□否
财务部
□是□否
财务部
□是□否
* * * *修改记录* * * * *
版本
修改内容
备注
A
首次发行
制定:
审核:
核准:
1.目的
1.1为确保产品出货的品质水准,以达到客户之允收范围内。
5
5
26-50
8
8
8
51-90
13
13
13
91-150
20
0 1
20
0 1
20
151-280
32
32
32
281-500
50
50
50
0 1
501-1200
80
12
80
80
1201-3200
125
23
125
12
125
3201-10000
200
34
200
23
200
12
10001-35000
OQA出货检验作业规范书

核准
審核
制表
檢驗作業規範書
OQA 出貨檢驗
日期
版本/次
A0
頁
碼
第 3 頁共 5 頁
標准進行檢驗作業﹐有特殊要求項目或檢驗項目變更時﹐需經權責主管核准﹐并按要求保存 相關檢驗記錄。 9.7 遇客戶有特殊品質要求者﹐依客戶要求進行相應作業。 9.8 對出貨零數箱產品數量及其標識等作全檢。 9.9 倉庫呆滯品出貨檢驗﹐按<<產品防護管理程序>>執行。 9.10. 每箱出貨產品外箱需蓋”QA PASS”標示﹐且符合各客戶之要求標示。 9.10 當交付給客戶的產品﹐在廠內發現有 HS 項不良時﹐品保需在 24 小時內(除節假日外)通知業 務部聯系客戶并及時處理防止擴散。 10.相關表單﹕ 10.1 <出貨查檢表>(附件一)<QC 檢驗記錄表>(附件五) 10.1.1 每次出貨檢驗結果均需填寫。 10.1.2 同一型號﹑不同周期之產品可記錄在表上。 10.1.3 此單作為出貨品質的記錄追溯。 10.2 <出貨檢驗報告表>(附件二) 10.2.1 此報告表根據產品測試條件進行填寫。 10.2.2 此報告表需經品保主管做最終判定。 10.2.3 此報告表附屬每批出貨產品箱內(或依客戶要求方式)。 10.3 <出貨檢驗周﹑月報表>(附件四) 10.3.1 用于統計每周﹑月出貨檢驗狀況。 10.3.2 品質周﹑月報中 OQA 的附屬統計表。 10.3.3 制式表單﹐使用電子檔。 12. 檢驗流程﹕
檢驗作業規範書
版本/次
A0
OQA 出貨檢驗
頁
碼
第 1 頁共 5 頁
1. 目的﹕使出貨檢驗作業規範化﹐確保產品出貨品質﹐符合客戶要求。
OQA抽样检验作业规范

6.附件
6.1 IPQA 稽核日報表(表 QA-INS-14) 6.2 品質問題反映速報(表 QA-INS-03) 6.3 IPQA ROVING CHECK LIST(表 QA-INS-21) 6.4 IPQA ROVING CHECK LIST REPORT(表 QA-INS-22) 6.5 成型廠首件確認表(表 IP-INS-05 6.6 噴塗廠首件確認表(表 PP-INS-27) 6.7 組裝廠首件確認表(表 AP-INS-02)
5.1.作業流程 開始
首件確認
NG
OK,簽名
量
產
開品質問 不合格品 處理 題反映速 報
NG
制程巡檢
OK
統計分析
5.2 作業說明 5.2.1 記錄“稽核日報表”要遵循以下原則: 及時准确,全面詳細,真實可靠,工整清晰 DATE REV A NEW ISSUE CHANGES Approved by
Prepared by
7.保存記錄
7.1.IPQA 稽核日報表: 三個月 7.2 品質問題反映速報: 三個月 7.3 IPQA ROVING CHECK LIST: 三個月 7.4 IPQA ROVING CHECK LIST REPORT: 三個月 7.5 成型廠首件確認表: 三個月 7.6 噴塗廠首件確認表: 三個月 7.7 組裝廠首件確認表: 三個月
及時准确全面詳細真實可靠工整清晰daterevchangesapprovedbyanewissue首件確認量產制程巡檢不合格品處理統計分析開品質問題反映速報開始ngokngok簽名preparedbyapprovedbyauthorizedbyeffectivedate漢達精密電子科技順德有限公司塑膠制造中心制程檢驗作業規范編號1
OQA作业指导书
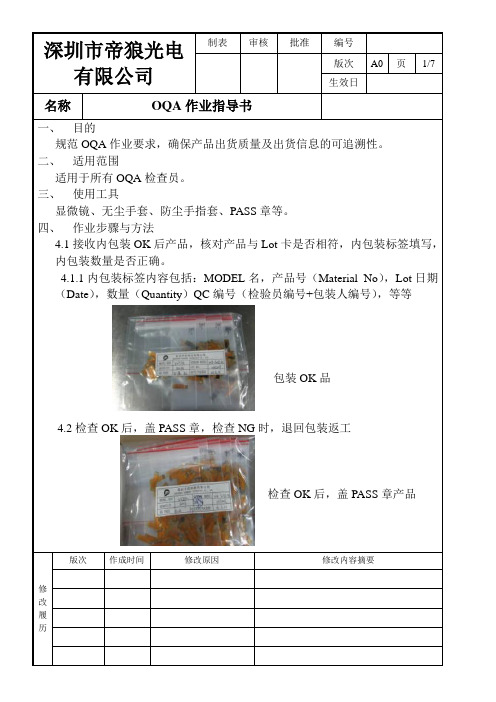
制表
审核
批准
编号
版次
A0
页
1/7
生效日
名称
OQA作业指导书
一、目的
规范OQA作业要求,确保产品出货质量及出货信息的可追溯性。
二、适用范围
适用于所有OQA检查员。
三、使用工具
显微镜、无尘手套、防尘手指套、PASS章等。
四、作业步骤与方法
4.1接收内包装OK后产品,核对产品与Lot卡是否相符,内包装标签填写,内包装数量是否正确。
4.3.4外包装标签内容包括:MODEL名、产品号(Material No)、收注号(Series No)、LOT号、日期(Date)、数量(Quantity)\QC编号(检查员编号+包装人编号)等等。
4.3.5OQA检查NG时,开启返品通知单返回包装工序重新进行包装或装箱。
外包装OK后产品
4.4对外包装检查OK后产品在外箱标签上盖PASS章,在包装箱内入入《出货检查成绩书》通知外包装人员进行封箱入库,对外包装NG产品退回包装返工处理。
4.1.1内包装标签内容包括:MODEL名,产品号(Material No),Lot日期(Date),数量(Quantity)QC编号(检验员编号+包装人编号),等等
包装OK品
4.2检查OK后,盖PASS章,检查NG时,退回包装返工
检查OK后,盖PASS章产品
修改履历
版次
作成时间
修改原因
修改内容摘要
OQA查外包装OK后盖PASS章产品
五、相关记录
5.1《出货检查成绩书》
5.2《产品包装要求一览表》
深圳市帝狼光电有限公司
编号
版次
生效日
OQC,OQA作业办法 A版

品管課版次:A制作日期:2005/6/19OQC/OQA作業辦法目錄1.目的2.QC的定義3.檢驗依據4.檢驗方式5.檢驗設備6.檢驗項目7.缺點判定定義8.成品數量檢驗抽樣箱數9.成品檢驗作業內容▪一目的:▪為讓全體OQC/OQA人員了解自己的工作職權及范圍,從而熟練地運作,減少品質失敗率,以滿足客戶的需求.▪二.OQC的定義:▪QC:品質管制:是為了要達成,維持與改進生產品所使用的統計技巧與活動.▪OQC:成品檢驗:是管制不讓不良品流出至客戶處. ▪OQA:出貨檢驗也就是成品管制.▪三.檢驗依據:▪工程藍圖,包裝規範,成品檢驗規範,產品缺點判定標准,抽樣檢驗計划,客戶特殊要求.▪四.檢驗方式:▪ 1.依據[成品檢驗規範]對成品進行抽樣檢驗,客戶有要求依客戶要求執行.▪ 2.待檢物置于合适之亮度下,受檢面与檢驗者成45度,距离約300mm,亮度500LUX,接受檢驗.不得在反光下檢驗,而強化表面可能出現之瑕疵.▪ 3.尺寸及机械性能:抽樣5PCS并將實際量測所得的尺寸,將實測數据(或數據MAX/MIN)記錄, 有標示重點之尺寸( ) 須記錄.▪ 4. 電氣 :100%檢驗▪ 1.應先确認測試線是否校正并在管制期限內,測試線的正确性及功能是否良好.▪ 2.測試前,應先确認線位與線位圖是否相符.▪ 3.電氣測試時須以一手握CONNECTOR,另一手握CABLE處作搖擺,▪搖擺條件如下表所示:▪CONNECTOR 類型搖擺距離(mm) 搖擺角度(度)▪ MINDIN 約60 上下左右90▪ D-SUB (不含CORE) 約120 上下左右45▪ D-SUB (含CORE) 約150 上下左右30▪ HOUSING 約50-100 上下60▪ DC PIUG/RCA 約60 上下左右90▪ ADAPTER 輕微振動▪USB (未鎖鐵片/不含CORE) 約60 上下左右90▪ USB (鎖鐵片/含CORE) 約60 上下左右45▪ FLAT CABLE 不作搖擺▪ MINI USB (成型) 約60 上下左右90▪ MINI USB (組裝) 上下45▪ SATA (組裝) 不作搖擺▪ SATA (成型) 約60 上下45搖擺條件▪客戶有要依客戶耍求執行,搖擺的力量以自然為原則.▪ 4.絕緣測試不作任何搖擺動作,顯示值大於規格值即判定合格,當顯示值不穩定時,若十秒內能達到要求即判定合格.▪ 5.抽樣方式: 正常/加嚴/減量/免檢/全檢.▪ 6.抽驗后判定方式:合格/退貨/特采/挑選.▪五.檢驗設備:▪ 1.外觀/結構/包裝: 目視.▪ 2.尺寸: 游標卡尺,分厘卡尺,線規,直尺,卷尺,投影機.▪ 3.電氣: CIRRIS西力思 1000H+/絕緣/耐壓測試儀/RT-9000 / CT-8681等測試儀.▪ 4.機械性能: 磅力計,搖擺機,鹽水噴霧試驗機,插撥機,硬度計,色差儀,网絡分析儀,吊重架與砝碼等,其它工程藍圖所要求設備. ▪ 5.重金屬測試:ICP測試儀.▪六.檢驗項目:▪ 1. 外觀/包裝.▪ 2.尺寸:零件圖上所有標示之尺寸.▪ 3.電氣一般檢驗項目包括如下:▪短路,斷路,錯位,電阻大,閃爍,PIN對PIN,PIN對鐵殼之絕緣阻抗等不良現象.▪ 4.各不良項目之定義:▪ 4.1.短路: 任意相鄰之獨立回路中,其中間介質有互相導通之情形;斷路: 各個獨立回路中,有斷開之情形.▪ 4.2.絕緣不良:任意兩相鄰之獨立回路中,其中間介質之抗阻與工程圖面規定不符;▪ 4.3.耐壓不良: 耐壓/高壓測試絕緣狀況與工程圖面規定不符;▪ 4.4.錯位: 兩個(含)以上獨立回路頭尾互相連接線位互相導通之現象;▪ 4.5.閃爍: a. 任意兩相鄰之獨立回路有瞬間導通的情形(瞬間為1/100秒);▪ b. 各個獨立回路內,有瞬間斷路之情形.▪七. 缺點判定定義:▪ 1.嚴重缺點(CRI):不良缺點是使產品完全失去功能或特殊限定之缺點,為客戶無法接受.▪ 2.主要缺點(MAJ): 不良缺點是使產品失去部分功能或嚴重外觀之缺點,為客戶拒絕接受.▪ 3.次要缺點(MIN): 不良缺點不影響產品功能而有明顯外觀之缺點,為客戶不接受.▪ 4.一級表面:使用者持續見到的所有外表.(產品的頂部或正面) ▪ 5.二級表面:使用者隨時見到的一點缺失但不危及品質的外表.(產品部或隱藏的外表)▪ 6.三級表面:使用在使用產品時看不見外表.(產品的內部,或由於其他零件混合的隱藏的外表)▪八.成品數量檢驗抽樣箱數:▪交驗箱(包)數 2-8 9-15 16-25 26-50 51-90 91-150 151-280▪應開箱(包)數 3 5 8 13 20 32 50▪九.成品檢驗作業內容:▪ 1.OQC在成品檢驗前先確認工程藍圖,包裝規範,成品檢驗規範;新機種是否有客戶承認OK之承認書/標准樣品;”進貨驗收單”后之附件是否齊全(件檢驗記錄/LOT管制單/COC材質報告/特採單/特採單累加數量管制表等) .▪ 2.依出貨通知單先后順序檢驗成品,依”進貨驗收單”核對成品入庫數量/線別/料號(確認成品標簽是否正確:确認產線標簽時須与藍圖及合格証核對),成品是否有管制燈點或印章;依[抽樣檢驗計划]選定抽樣方式及允收水准進行抽樣,針對異常常發之成品/新成品/新產線生產之成品/產線制程不良高之成品須加嚴檢驗.▪ 3.依[工程藍圖]/[成品檢驗規範]/ [BOM表]/[規格書]/標准樣品對抽樣之成品進行檢驗(外觀/尺寸/電氣/色差/機械性能/包裝/印字內容/成品單PCS重量等) ,針對異常常發之不良現象/新成品/新產線生產之成品/產線制程不良高之成品須重點檢驗.▪ 4.檢驗后將檢驗結果記錄(進貨驗收單,檢驗日報表, 矯正與預防措施追蹤表,品質異常處理單,含單PCS重量,誤差+/-5%,記錄在”品質履歷表”上),檢驗OK之成品在每一外箱上貼對應顏色之合格標簽(1/7月為淺橙色,2/8月為淺綠色,3/9月為淡黃色,4/10月為黃色,5/11月為桔色,6/12月為草綠色);檢驗NG 退貨之成品在外箱上貼紅色的拒收標簽(重金屬超標之成品貼色的拒收標簽),須在退貨標簽上注明成品料號,檢驗日期/單號,不良現象,稽核退貨處理結果.退貨及時知會生管,生管依客戶交貨需求時間,如為急出貨,來不及重工,在不影響產品功能情況下,需由業務與客戶協調(工訂單則由生管負責)客戶書面特採.▪ 5.批量小(300PCS)之產品須全檢,保証品質,并且零箱須100%點數.(新開產線之成品須視狀況全檢, 品質差之產品須跟線全檢,協助其品質穩定.)▪ 6.產線之”品質異常處理單”跟催(48H內提出改善措施)及結案,當成品有異常時,OQC對產線改善后之成品須追蹤第二,三批交貨是否OK.再結案.▪新開發之機種依[工程藍圖]/標准樣品對進行檢驗(外觀/尺寸/電氣/色差/機械性能/包裝/印字內容等)▪ 8.每日所有量具/儀器之清潔/保養,工作區所有物品之整理/清潔/標示/區隔.每日所有記錄/資料的歸位,表單記錄真實,不可涂改.▪ 9.依生管出貨通知單查核所有已驗OK成品.▪ 9.1.所有表單是否齊全/正確/完整/整潔.(進貨驗收單/出貨檢驗報告/材質報告/LOT管制單/初件檢驗記錄單/重金屬測試報告/機械性能測試報特/特採單累加數量管制表.)▪ 9.2.外箱標簽與合格標簽是否正確(可以比對的方式作業),環保標示是否正確.▪ 9.3.所有零箱數量之確認,成品總數與進貨驗收單是否一致. ▪ 9.4.外箱是否破損,整潔,正確.▪ 9.5.所有查核狀況如實記錄.▪ 9.6.若出貨時同時出一個出貨單號必須在報表上記錄所有檢驗單號.▪ 10.合格標簽依工程藍圖打印(注意不同客戶之檢驗單號).。
- 1、下载文档前请自行甄别文档内容的完整性,平台不提供额外的编辑、内容补充、找答案等附加服务。
- 2、"仅部分预览"的文档,不可在线预览部分如存在完整性等问题,可反馈申请退款(可完整预览的文档不适用该条件!)。
- 3、如文档侵犯您的权益,请联系客服反馈,我们会尽快为您处理(人工客服工作时间:9:00-18:30)。
OQA作业规范
编制/日期
审核/日期
批准/日期
1.目的
规范OQA作业程序,使OQA作业规范化、合理化、流程化,保障出货品质达到客户需求。
2.适用范围
适用于所有出货产品检验。
3.定义
3.1 OQA: Out-going Quality Assurance, 出货品质保证
3.2 IPQA: In-Process Quality Audit, 制程品质稽核
3.3 QE: Quality Engineer, 品质工程师
3.4 FAI: First Artistic Inspection, 首件检验
3.5 AQL:Acceptable Quality Level品质允收水平
4.职责
4.1 QE:对OQA检验作出相应指导。
4.2 OQA:负责出货产品检验确认及相关品质数据的记录,收集及存档工作,不合格品改善效果的确认以及检验
中发现的品质问题做出判断、并协调跟踪。
5.规范内容
5.1 OQA根据相关产品检验规范对产线成品进行功能和外观检验。
依据BOM, Check List或工程,QE等部门正式
发行的注意事项进行配置等检验。
5.2最终出货品质检验:
5.2.1 OQA负责最终出货品质检验,负责对产品的外观,功能,包装等方面进行检验。
5.2.2 产品生产完成后,生产部将待检产品开出《成品送检通知单》一式二份交于品质部OQA检验。
由OQA到产
品待检区进行随机抽样,按产品检验规范中要求的抽样水准对批量取样并取回到OQA待检区。
5.2.3 检验过程中产品缺陷的分类依《产品检验规范》进行判定。
5.2.4 针对OQA 发现之功能,少漏件及外观,包装等整批次不良现象,班组长需对不良现象进行判定,以判定
是否是治具因素或其他原因造成的不良,OQA 班组长不能判定之不良,通知负责机种品质工程师进行判定。
5.2.5 不良现象最终判定之后由OQA 班组长通知QE、相关工程部门工程师及产线主管,然后由负责工程师或生
产部分析不良原因;
5.2.5 各工程师确认不良现象后由OQA班组长开出在RDM 生产异常管理系统上开立异常通报的电子流,要求描述
清楚机型、不良现象、不良机台的数量、不良机台序列号、共检验机台数量等信息并由OQA依据检验结果决定批次货物是否拒收;
5.3 样机的检验
5.3.1 出给OEM 客户及送其他客户作测试、参展等使用的样机,必须达到出货标准良品入库方可出货,如果样
机处在DVT\PVT阶段存在瑕疵,则OQA需将问题描述记录清楚,以特采形式出货,具体操作参照5.4之规定;5.3.2 公司研发等部门作测试使用的样机由样机申请人提供样机要求,OQA 依此要求进行检验;
5.4 特采出货
5.4.1 所有不符合出货品质要求的机台都不可正常出货,必须经特采后方可出货;
5.4.2 针对需特采出货的成品,由PMC 依据不符合标准之问题点提出特采出货申请,并注明特采数量,不符合
标准之问题点等,并由相关工程部门、研发部门(研发部门根据实际情况决定是否需要签核)及品质部门给出特采意见,经经公司副总经理签核后方可出货;
5.4.3 OQA依据签核之后的特采单的特采数量Pass 成品出货,并针对特采单编号作保留,以作出货后之品质追溯。
6.支持文件:
6.1《不合格品控制程序》CZC-MP-023
7.质量记录:
7.1《OQA检验记录表》CZC-QR-PA-M-010
7.2《成品送检通知单》CZC-QR-PA-M-099。