过程三检制度
过程三检制度
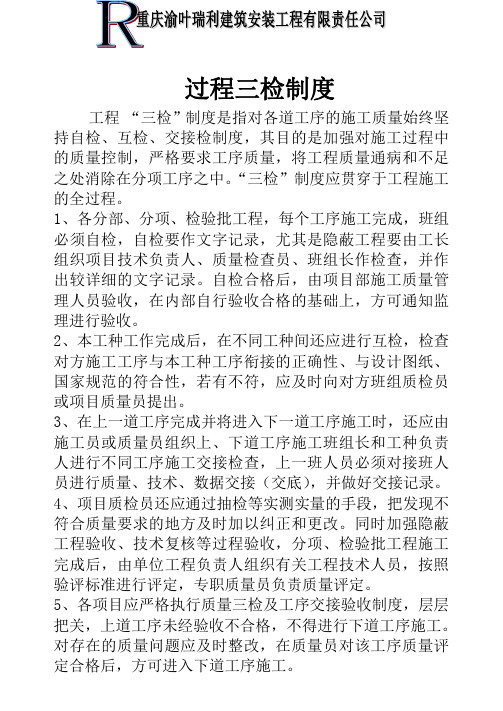
过程三检制度
工程“三检”制度是指对各道工序的施工质量始终坚持自检、互检、交接检制度,其目的是加强对施工过程中的质量控制,严格要求工序质量,将工程质量通病和不足之处消除在分项工序之中。
“三检”制度应贯穿于工程施工的全过程。
1、各分部、分项、检验批工程,每个工序施工完成,班组必须自检,自检要作文字记录,尤其是隐蔽工程要由工长组织项目技术负责人、质量检查员、班组长作检查,并作出较详细的文字记录。
自检合格后,由项目部施工质量管理人员验收,在内部自行验收合格的基础上,方可通知监理进行验收。
2、本工种工作完成后,在不同工种间还应进行互检,检查对方施工工序与本工种工序衔接的正确性、与设计图纸、国家规范的符合性,若有不符,应及时向对方班组质检员或项目质量员提出。
3、在上一道工序完成并将进入下一道工序施工时,还应由施工员或质量员组织上、下道工序施工班组长和工种负责人进行不同工序施工交接检查,上一班人员必须对接班人员进行质量、技术、数据交接(交底),并做好交接记录。
4、项目质检员还应通过抽检等实测实量的手段,把发现不符合质量要求的地方及时加以纠正和更改。
同时加强隐蔽工程验收、技术复核等过程验收,分项、检验批工程施工完成后,由单位工程负责人组织有关工程技术人员,按照验评标准进行评定,专职质量员负责质量评定。
5、各项目应严格执行质量三检及工序交接验收制度,层层把关,上道工序未经验收不合格,不得进行下道工序施工。
对存在的质量问题应及时整改,在质量员对该工序质量评定合格后,方可进入下道工序施工。
“三检制”管理制度
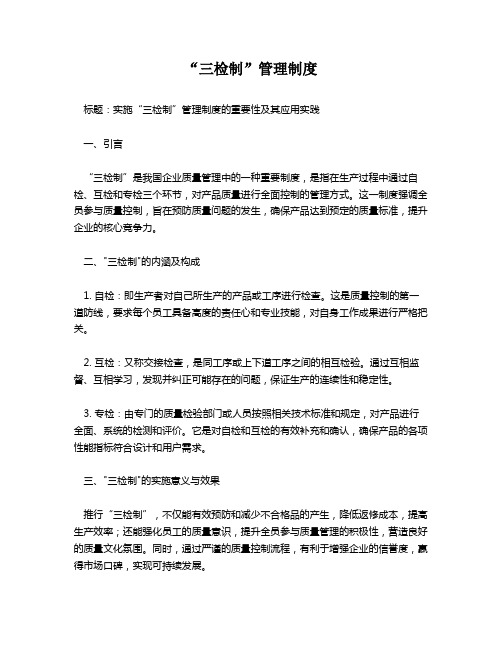
“三检制”管理制度标题:实施“三检制”管理制度的重要性及其应用实践一、引言“三检制”是我国企业质量管理中的一种重要制度,是指在生产过程中通过自检、互检和专检三个环节,对产品质量进行全面控制的管理方式。
这一制度强调全员参与质量控制,旨在预防质量问题的发生,确保产品达到预定的质量标准,提升企业的核心竞争力。
二、"三检制"的内涵及构成1. 自检:即生产者对自己所生产的产品或工序进行检查。
这是质量控制的第一道防线,要求每个员工具备高度的责任心和专业技能,对自身工作成果进行严格把关。
2. 互检:又称交接检查,是同工序或上下道工序之间的相互检验。
通过互相监督、互相学习,发现并纠正可能存在的问题,保证生产的连续性和稳定性。
3. 专检:由专门的质量检验部门或人员按照相关技术标准和规定,对产品进行全面、系统的检测和评价。
它是对自检和互检的有效补充和确认,确保产品的各项性能指标符合设计和用户需求。
三、"三检制"的实施意义与效果推行“三检制”,不仅能有效预防和减少不合格品的产生,降低返修成本,提高生产效率;还能强化员工的质量意识,提升全员参与质量管理的积极性,营造良好的质量文化氛围。
同时,通过严谨的质量控制流程,有利于增强企业的信誉度,赢得市场口碑,实现可持续发展。
四、"三检制"的实施策略企业在实施“三检制”时,应注重建立健全相应的规章制度,明确各岗位职责,加强教育培训,提升员工的质量技能和自我约束能力。
同时,运用现代信息技术手段,如智能化质量管理系统等,实现质量信息的实时反馈和动态监控,以确保“三检制”的有效执行。
五、结语综上所述,“三检制”作为质量管理的重要工具,其有效实施对企业提升产品质量,增强市场竞争力具有重要意义。
因此,企业应当高度重视并积极推动“三检制”的落地生根,使其成为推动企业发展、保障产品质量的强大动力。
过程三检制度
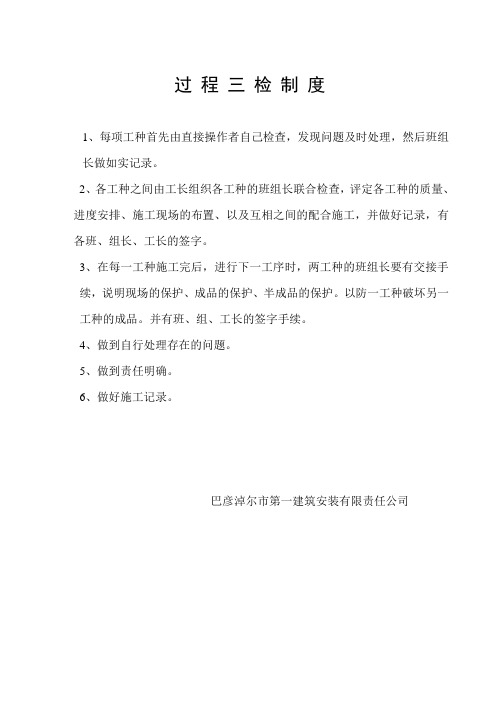
过程三检制度
1、每项工种首先由直接操作者自己检查,发现问题及时处理,然后班组长做如实记录。
2、各工种之间由工长组织各工种的班组长联合检查,评定各工种的质量、进度安排、施工现场的布置、以及互相之间的配合施工,并做好记录,有各班、组长、工长的签字。
3、在每一工种施工完后,进行下一工序时,两工种的班组长要有交接手续,说明现场的保护、成品的保护、半成品的保护。
以防一工种破坏另一工种的成品。
并有班、组、工长的签字手续。
4、做到自行处理存在的问题。
5、做到责任明确。
6、做好施工记录。
巴彦淖尔市第一建筑安装有限责任公司
维信(内蒙古)纺织科技有限公司一期工程施工图送审相关资料
维信(内蒙古)纺织科技有限公司。
三检制度

过程检验三检制度
过程检验应严格执行《过程检验规程》,做到“自检、互检、专检”和首件必检的原则,防止不合格产品的产生。
自检:是指由操作者自己对自己所加工的产品零部件所进行的检验。
其目的是操作者通过检验了解被加工产品或零部件的质量情况,以使生产出完全符合质量要求的产品或零部件,达到与图纸的一致性,并应认真、真实的填写自检记录。
互检:是指由同班组临近操作的上下工序的操作者相互进行复核性检验。
互检的目的在于通过检验及时发现不符合工艺规程的质量问题,以便及时采取改进措施,从而有效的防止自检中发生的错、漏检造成的损失,并应认真、真实的填写互检报告。
专检:是指由分公司质量检验机构直接领导专职从事质量检验的人员所进行的检验,或由分公司指派到分厂的工序检验员。
产品在制做的过程中工序检验员应根据相关的检验作业指导书、工艺规程对产品的质量特性进行监视和测量,以验证产品要求是否得到满足,检验要有记录。
首件检验:生产开始时和工序因素调整后,工序检验员应对制造的第一件产品或前几件产品认真进行检验,确认合格后进行签认,才能允许进行后续工作。
产品完工后,最后一道工序检验员汇总产品工装、关键工序、特殊过程、质量不稳定因素、用户反馈的重要不良项目质量检验记录等,全面检验,确认合格做好标识记录,填写产品验收申请单报检。
本制度同样适用于原材料、外购产品进货三检检验制度。
编制:审核:批准:。
三检制及验收制度
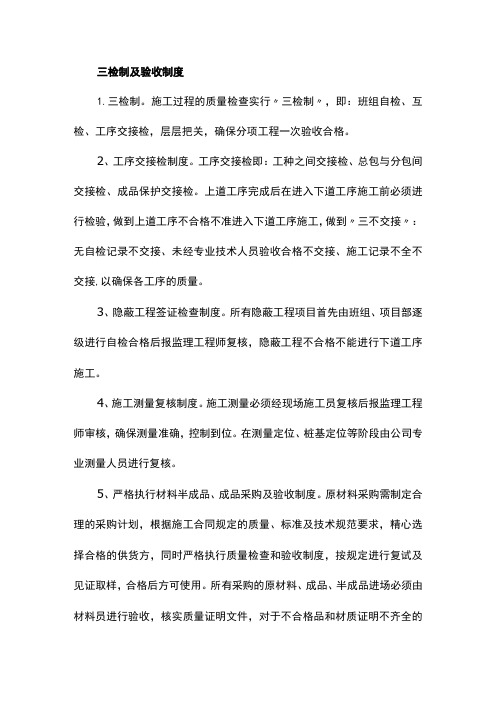
三检制及验收制度
1.三检制。
施工过程的质量检查实行〃三检制〃,即:班组自检、互检、工序交接检,层层把关,确保分项工程一次验收合格。
2、工序交接检制度。
工序交接检即:工种之间交接检、总包与分包间交接检、成品保护交接检。
上道工序完成后在进入下道工序施工前必须进行检验,做到上道工序不合格不准进入下道工序施工,做到〃三不交接〃:无自检记录不交接、未经专业技术人员验收合格不交接、施工记录不全不交接,以确保各工序的质量。
3、隐蔽工程签证检查制度。
所有隐蔽工程项目首先由班组、项目部逐级进行自检合格后报监理工程师复核,隐蔽工程不合格不能进行下道工序施工。
4、施工测量复核制度。
施工测量必须经现场施工员复核后报监理工程师审核,确保测量准确,控制到位。
在测量定位、桩基定位等阶段由公司专业测量人员进行复核。
5、严格执行材料半成品、成品采购及验收制度。
原材料采购需制定合理的采购计划,根据施工合同规定的质量、标准及技术规范要求,精心选择合格的供货方,同时严格执行质量检查和验收制度,按规定进行复试及见证取样,合格后方可使用。
所有采购的原材料、成品、半成品进场必须由材料员进行验收,核实质量证明文件,对于不合格品和材质证明不齐全的
材料不允许进场。
材料进场后及时标识,确保不误用、不混用。
工程各道工序的三检制度
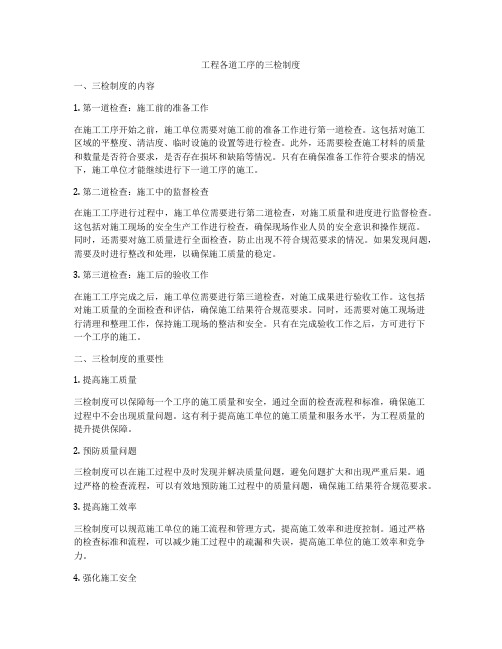
工程各道工序的三检制度一、三检制度的内容1. 第一道检查:施工前的准备工作在施工工序开始之前,施工单位需要对施工前的准备工作进行第一道检查。
这包括对施工区域的平整度、清洁度、临时设施的设置等进行检查。
此外,还需要检查施工材料的质量和数量是否符合要求,是否存在损坏和缺陷等情况。
只有在确保准备工作符合要求的情况下,施工单位才能继续进行下一道工序的施工。
2. 第二道检查:施工中的监督检查在施工工序进行过程中,施工单位需要进行第二道检查,对施工质量和进度进行监督检查。
这包括对施工现场的安全生产工作进行检查,确保现场作业人员的安全意识和操作规范。
同时,还需要对施工质量进行全面检查,防止出现不符合规范要求的情况。
如果发现问题,需要及时进行整改和处理,以确保施工质量的稳定。
3. 第三道检查:施工后的验收工作在施工工序完成之后,施工单位需要进行第三道检查,对施工成果进行验收工作。
这包括对施工质量的全面检查和评估,确保施工结果符合规范要求。
同时,还需要对施工现场进行清理和整理工作,保持施工现场的整洁和安全。
只有在完成验收工作之后,方可进行下一个工序的施工。
二、三检制度的重要性1. 提高施工质量三检制度可以保障每一个工序的施工质量和安全,通过全面的检查流程和标准,确保施工过程中不会出现质量问题。
这有利于提高施工单位的施工质量和服务水平,为工程质量的提升提供保障。
2. 预防质量问题三检制度可以在施工过程中及时发现并解决质量问题,避免问题扩大和出现严重后果。
通过严格的检查流程,可以有效地预防施工过程中的质量问题,确保施工结果符合规范要求。
3. 提高施工效率三检制度可以规范施工单位的施工流程和管理方式,提高施工效率和进度控制。
通过严格的检查标准和流程,可以减少施工过程中的疏漏和失误,提高施工单位的施工效率和竞争力。
4. 强化施工安全三检制度可以提高施工现场的安全意识和管理水平,加强现场安全控制和安全保障措施的执行。
通过严格的检查流程和要求,可以确保施工现场的安全生产工作得到有效的落实,避免发生安全事故。
工程中常说的三检制度

工程中常说的三检制度一、什么是三检制度三检制度,顾名思义就是在施工现场进行三次质量检查的制度。
这三次质量检查分别是:施工前检查、在建过程检查和竣工前检查。
通过这三次检查,可以全面地了解工程的质量状况,及时发现和解决问题,确保工程的质量。
1. 施工前检查施工前检查是在开工前对施工现场进行检查,查看施工图纸和规范要求,确认施工条件是否满足要求,是否存在隐患等。
通过这次检查,可以及时纠正问题,确保施工前的准备工作都做到位。
2. 在建过程检查在建过程检查是在施工过程中定期对工程进行检查,查看施工质量是否符合规范要求,施工工艺是否符合规范要求,工程安全是否得到保障等。
通过这次检查,可以及时发现问题,及时解决,确保工程质量。
3. 竣工前检查竣工前检查是在工程接近完工时对工程进行检查,查看工程是否达到规范要求,是否存在遗留问题等。
通过这次检查,可以及时解决遗留问题,确保工程顺利交付。
二、三检制度的意义三检制度在工程项目中具有非常重要的意义,主要体现在以下几个方面:1. 提高工程质量通过三检制度的执行,可以及时发现工程质量问题,及时解决,确保工程质量。
这样可以避免工程质量问题的发生,提高工程的质量水平。
2. 进度控制通过三检制度的执行,可以及时发现影响工程进度的问题,及时解决,确保工程顺利进行。
这样可以提高工程的进度控制能力,保证工程按时完成。
3. 降低成本通过三检制度的执行,可以及时发现问题,提高施工效率,避免出现重复施工等情况,降低成本。
这样可以有效控制工程造价,提高项目的经济收益。
4. 人员素质提升通过三检制度的执行,可以增强施工人员的责任感和质量意识,提高他们的专业水平。
这样可以推动施工人员素质的提升,保证工程质量和进度。
三、三检制度的执行步骤三检制度的执行需要遵循一定的步骤,主要包括以下几个方面:1. 制定三检计划在工程项目开工前,需要制定三检计划,明确三次检查的时间节点、检查内容、检查人员等。
这样可以确保三检制度的顺利执行。
工程施工过程 三检 制度

工程施工过程三检制度一、第一检查第一次检查,也称为初次检查,是在施工前对工程施工方案、施工组织设计、施工图纸等进行检查。
首先,施工单位应提交相关的施工方案和施工组织设计,包括施工流程、施工方法、材料选取等内容。
监理单位应对这些文件进行认真审核,确保施工方案合理、可行。
同时,还需对施工图纸进行检查,确保符合设计要求。
如果发现问题,应及时提出修改意见并要求施工单位重新整改。
在第一次检查中,还需要对各项施工条件进行检查,包括施工人员的资质、施工设备的合法性、施工现场的安全措施等。
如果发现不符合要求的情况,监理单位应立即提出整改要求。
只有确保各项施工条件符合要求,才能保证施工质量和安全。
二、第二检查第二次检查,也称为中期检查,是在工程施工过程中对施工质量、安全和进度进行检查。
在施工过程中,监理单位应定期进行现场检查,了解施工进展情况。
对施工质量进行抽查,确保符合质量要求。
对施工安全进行检查,重新评估风险,确保安全措施完善。
对施工进度进行跟踪,及时发现延误情况并提出整改意见。
同时,监理单位还需对施工单位的施工管理进行检查,包括施工方案的执行情况、施工人员的素质、施工设备的维护情况等。
如果发现问题,应及时提出整改要求,并制定整改措施。
只有在中期检查中加强管理,才能确保工程施工按照计划完成,避免延误和质量问题。
三、第三检查第三次检查,也称为竣工验收,是在工程竣工后进行的一次终期检查。
在工程竣工后,监理单位应对工程整体进行验收,评估工程质量、安全和技术性能。
首先,需要对工程质量进行全面检查,包括外观质量、结构稳定性、材料使用等方面。
同时,还需要对工程安全进行评估,包括施工安全、使用安全等。
最后,对工程的技术性能进行测试,确保符合设计要求。
在第三次检查中,监理单位还需要组织相关部门对工程进行评审,确保工程符合相关法律法规和标准规范。
只有在竣工验收中做到严格把关,才能确保工程质量和安全,为工程的最终交付打下良好基础。
工程工序三检制度

工程工序三检制度一、概述工程质量关乎整个项目的成功与否,而对于工程质量的保障和控制,工程工序的三检制度起着至关重要的作用。
三检制度是指工程进行过程中的三次检查制度,即初检、中检和终检,以确保工程质量的全面监控和持续改进。
本文将从初检、中检和终检三个方面详细介绍工程工序三检制度的实施细则和注意事项。
二、初检1.初检的时间点:初检应在工程开始进行后的早期阶段进行,以确保及时发现和解决问题。
2.初检的内容:(1)初检的内容包括对工程施工材料的质量、工艺的合理性、施工人员的技术水平等方面进行检查;(2)初检还应包括对工程施工过程中遵守的设计规范和施工验收标准的检查;(3)初检的重点是发现和修复施工中出现的问题,确保工程进展顺利。
3.初检的方式:(1)初检可以由专门的质检人员负责,也可以由工程监理单位负责;(2)初检应以书面形式记录,明确问题和解决措施,并通知有关责任人及时整改。
4.初检的结果:(1)初检结果应在规定的时间内完成,并按照有关规定报送相关部门;(2)初检结果会影响工程后续的施工进度,因此应及时解决问题,确保工程顺利进行。
三、中检1.中检的时间点:中检应在工程进行中的中期进行,以确保前期工作的质量和后期工程的质量。
2.中检的内容:(1)中检的内容包括对前期初检中发现的问题的跟踪检查和整改情况;(2)中检还应包括对工程进展情况的检查和评价,确保工程按计划进行;(3)中检的重点是保证工程的质量和安全,及时发现和解决问题。
3.中检的方式:(1)中检应由专门的质检人员负责,也可以由工程监理单位负责,确保中检工作的独立性和客观性;(2)中检应按照有关规定报告中检结果,并通知有关责任人及时整改。
4.中检的结果:(1)中检结果应在规定的时间内完成,并按照有关规定报送相关部门;(2)中检结果应与初检结果对比,评价工程质量的改进情况,为后续工程施工提供参考。
四、终检1.终检的时间点:终检应在工程即将完成时进行,以确保工程质量的最终验收和交付。
安全生产管理制度_三检
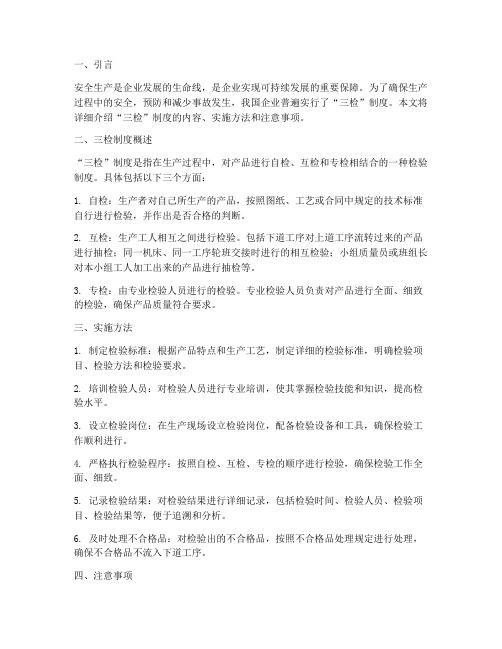
一、引言安全生产是企业发展的生命线,是企业实现可持续发展的重要保障。
为了确保生产过程中的安全,预防和减少事故发生,我国企业普遍实行了“三检”制度。
本文将详细介绍“三检”制度的内容、实施方法和注意事项。
二、三检制度概述“三检”制度是指在生产过程中,对产品进行自检、互检和专检相结合的一种检验制度。
具体包括以下三个方面:1. 自检:生产者对自己所生产的产品,按照图纸、工艺或合同中规定的技术标准自行进行检验,并作出是否合格的判断。
2. 互检:生产工人相互之间进行检验。
包括下道工序对上道工序流转过来的产品进行抽检;同一机床、同一工序轮班交接时进行的相互检验;小组质量员或班组长对本小组工人加工出来的产品进行抽检等。
3. 专检:由专业检验人员进行的检验。
专业检验人员负责对产品进行全面、细致的检验,确保产品质量符合要求。
三、实施方法1. 制定检验标准:根据产品特点和生产工艺,制定详细的检验标准,明确检验项目、检验方法和检验要求。
2. 培训检验人员:对检验人员进行专业培训,使其掌握检验技能和知识,提高检验水平。
3. 设立检验岗位:在生产现场设立检验岗位,配备检验设备和工具,确保检验工作顺利进行。
4. 严格执行检验程序:按照自检、互检、专检的顺序进行检验,确保检验工作全面、细致。
5. 记录检验结果:对检验结果进行详细记录,包括检验时间、检验人员、检验项目、检验结果等,便于追溯和分析。
6. 及时处理不合格品:对检验出的不合格品,按照不合格品处理规定进行处理,确保不合格品不流入下道工序。
四、注意事项1. 加强检验人员责任心:检验人员要充分认识到安全生产的重要性,提高责任心,认真履行检验职责。
2. 严格执行检验制度:生产过程中,要严格按照“三检”制度进行检验,确保产品质量。
3. 定期对检验设备进行维护和校准:确保检验设备的准确性和可靠性。
4. 加强检验结果分析:对检验结果进行分析,找出生产过程中的安全隐患,及时采取措施加以整改。
三检制度(工序)

“三检制度”验收表格及填写范例
三检制:就是实行操作者的自检、专业工长及下一道工序施工班组的互检和专职质检员的专检相结合的一种检验制度,对每道工序的检查严格执行施工质量验收规范及施工合同的要求,符合工程项目质量中重点突出以事前控制为主及全员参与的精髓。
三检制度经过长期现场实践的证实,是行之有效的,是每一位施工人员都应该贯彻执行的制度。
自检:作业班组施工完后,首先进行自检,作业班组是施工质量优劣的决定主体,因此作业班组必须认真自检。
栋号施工员应督促班组长自检,并对班组操作质量进行中间检查,实时跟踪控制,并做好记录。
互检:是下一道工序施工班组与专业工长进行的检查。
专业工长、下一工序班组长分别对本工序进行验收,各自填写验收结果,并提出整改意见。
专业工长应随时对施工质量进行巡检,平行检等施工质量过程跟踪控制,做好记录。
专检:所有分项工程、隐检、预检项目,必须按程序,经质检员检查后,报请监理工程师进行检查验收。
对与多次督促,整改不力且影响严重的质量问题将对劳务公司实施处罚。
验收要求:凡报请监理工程师验收的施工内容,主控项目必须一次通过;一般项目经一次整改必须全数通过。
备注:本表一式二份,质检员及专业工长各存一份。
备注:本表一式二份,质检员及施工班组各存一份。
面对强大的对手,明知不敌,也要毅然亮剑,即使倒下,也要化成一座山。
过程三检制度
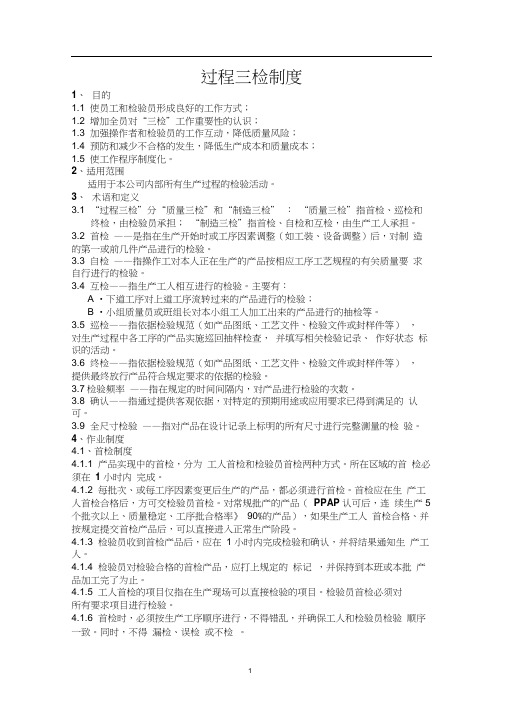
过程三检制度1、目的1.1 使员工和检验员形成良好的工作方式;1.2 增加全员对“三检”工作重要性的认识;1.3 加强操作者和检验员的工作互动,降低质量风险;1.4 预防和减少不合格的发生,降低生产成本和质量成本;1.5 使工作程序制度化。
2、适用范围适用于本公司内部所有生产过程的检验活动。
3、术语和定义3.1 “过程三检”分“质量三检”和“制造三检” :“质量三检”指首检、巡检和终检,由检验员承担;“制造三检”指首检、自检和互检,由生产工人承担。
3.2 首检——是指在生产开始时或工序因素调整(如工装、设备调整)后,对制造的第一或前几件产品进行的检验。
3.3 自检——指操作工对本人正在生产的产品按相应工序工艺规程的有关质量要求自行进行的检验。
3.4 互检——指生产工人相互进行的检验。
主要有:A •下道工序对上道工序流转过来的产品进行的检验;B •小组质量员或班组长对本小组工人加工出来的产品进行的抽检等。
3.5 巡检——指依据检验规范(如产品图纸、工艺文件、检验文件或封样件等),对生产过程中各工序的产品实施巡回抽样检查,并填写相关检验记录、作好状态标识的活动。
3.6 终检——指依据检验规范(如产品图纸、工艺文件、检验文件或封样件等),提供最终放行产品符合规定要求的依据的检验。
3.7检验频率——指在规定的时间间隔内,对产品进行检验的次数。
3.8 确认——指通过提供客观依据,对特定的预期用途或应用要求已得到满足的认可。
3.9 全尺寸检验——指对产品在设计记录上标明的所有尺寸进行完整测量的检验。
4、作业制度4.1、首检制度4.1.1 产品实现中的首检,分为工人首检和检验员首检两种方式。
所在区域的首检必须在 1 小时内完成。
4.1.2 每批次、或每工序因素变更后生产的产品,都必须进行首检。
首检应在生产工人首检合格后,方可交检验员首检。
对常规批产的产品(PPAP认可后,连续生产5个批次以上、质量稳定、工序批合格率》90%的产品),如果生产工人首检合格、并按规定提交首检产品后,可以直接进入正常生产阶段。
工程制度三检制度

工程制度三检制度
三检制度,即自检、互检和专检,是指在工程施工过程中,通过施工人员自我检查(自检)、相互之间进行检查(互检)以及专业人员进行专项检查(专检)的方式,来发现并及时纠正施工中的问题,确保工程质量符合标准要求。
自检是三检制度的基础环节,它要求施工人员在完成每一项工作后,必须对照施工规范和质量标准进行自我检查。
这一过程不仅能够提升施工人员的质量意识,还能及时发现并纠正问题,避免小错误积累成大问题。
互检则是在自检的基础上,由不同工种或不同班组的施工人员相互检查对方的工作成果。
这种交叉检查的方式有助于打破个人视角的局限,从他人的角度发现问题,进一步提高工作质量。
专检是由具备专业资质的质检人员对工程的关键部位和重要工序进行的专项检查。
专检人员通常拥有更丰富的经验和更专业的知识,他们的检查能够确保工程的关键部分达到设计和规范要求,保障工程的整体质量。
实施三检制度的关键在于明确各个环节的责任和标准。
施工单位应制定详细的三检制度实施细则,包括自检、互检和专检的具体操作流程、检查内容和标准。
要加强对施工人员的培训,提高他们的质量意识和专业技能,使他们能够有效地进行自检和互检。
要强化专检的作用,确保专检人员的专业水平和独立性,让他们能够公正、客观地评价工程质量。
在实际操作中,三检制度的实施还需要配合相应的记录和报告制度。
每次检查后,都应有详细的记录,包括检查时间、检查内容、检查结果以及存在的问题和改进措施。
这些记录不仅有助于追踪问题的解决进度,还能为后续的质量管理提供数据支持。
项目工程施工三检制度

项目工程施工三检制度一、三检制度的基本原则三检制度,即自检、互检和专检,是指在施工过程中,由不同的参与主体按照一定的顺序和标准进行检查,以确保工程质量符合要求。
自检是指施工单位对已完成的工作自行进行检查;互检是指不同工种或班组之间相互进行检查;专检则是指由专业的质量检查人员进行的检查。
二、自检1. 自检内容:包括材料验收、施工工艺、操作方法、成品保护等方面。
2. 自检程序:施工人员在完成一定工作量后,必须对照施工图纸和技术规范进行自检,并填写自检记录。
3. 自检责任:施工班组长负责组织实施自检,并对自检结果负责。
三、互检1. 互检内容:主要针对相邻工序或工种之间的交接部位,以及相互影响的工作质量。
2. 互检程序:在自检合格的基础上,由相关工种或班组之间互相检查对方的工作质量,并做好记录。
3. 互检责任:各工种或班组长需对互检结果负责,并及时解决发现的问题。
四、专检1. 专检内容:涵盖工程的所有质量要素,包括材料、设备、施工过程和成品等。
2. 专检程序:由项目部的质量监督部门或委托外部专业机构进行,专检人员应具备相应的资质和经验。
3. 专检责任:质量监督部门负责人对专检结果负责,并对发现的问题提出整改意见。
五、三检制度的执行与管理1. 制定详细计划:项目部应根据工程特点和施工进度,制定详细的三检计划,明确检查的时间、内容和责任人。
2. 建立记录档案:所有检查过程和结果都应有详细记录,形成书面报告,作为工程质量档案的一部分。
3. 问题整改追踪:对于检查中发现的问题,应及时整改,并跟踪整改效果,确保问题得到彻底解决。
4. 定期总结分析:项目部应定期对三检数据进行分析,总结质量管理的经验教训,不断提高管理水平。
六、结语。
质量“三检制”管理制度范本(三篇)

质量“三检制”管理制度范本为确保本标段施工过程中质量体系持续高效运转,保证工程质量达到设计要求,实现本标段质量目标,项目部特制定工程质量“三检”制度,各单位、各部门施工过程中严格按照此制度执行,严把质量关。
一、“三检制”程序控制1、项目部对工程工序施工质量实行班组初检、工程部施工员复检和质检员终检“三检”。
班组长对工序施工过程进行合格控制,质检员对工序质量检查合格后,及时填写检验质量验收记录,报监理验收。
2、工序施工质量应按技术交底要求、验收规范、质量要求进行检查。
对不符合质量要求的,班组应及时返修或返工。
专业质检员对返修、返工后的工序质量重新检查评定,符合要求后方可报监理验收。
3、工序交接的班组,上道工序班组应为下道工序施工提供方便、有利的条件,下道工序班组对上道工序施工结果应予以保护。
上、下道工序施工有交叉作业或互有影响时,由施工员做好班组作业协调和安排。
4、下道工序将上道工序施工结果隐蔽的,项目部需提前____小时通知监理工程师。
项目部工程部对隐蔽工程检查合格后,通知监理请有关单位进行隐蔽工程验收,并填写“隐蔽工程验收记录”。
监理工程师检查合格并签认后,方可进行隐蔽工程施工。
5、特殊、关键部位的隐蔽工程检查,项目部技术、施工、质检等部门必须进行联合验收。
二、处罚细则1、现场严格、认真执行三检制,各工序初检、复检、终检合格后均填写好对应的表格,上交工程部。
对于初检、复检、终检不到位的班组、施工员、质检员,第一次给予提醒教育,第二次给予警告,第三次给予100-____元的处罚。
2、不履行质量检查验收程序,擅自进行下一道工序施工的,对责任单位处以500-____元罚款。
3、质检员不做质量工作记录,发生漏检、错检的,不及时向项目部反馈整改通知单的,以及协作队不及时向项目部反馈质量整改通知单的,对其处以200-____元罚款。
4、项目在日常检查中发生质量隐患,未进行原因分析,无整改措施及工程未及时进行复查的,视情节轻重对有关责任人处以200-____元罚款;出现质量问题,未进行改进和提高并重复出现的,对有关责任人处以500-____元罚款。
“三检“制度

.2中间检查:中间检查包括操作者的“自检”、品管员过程中的“抽(巡)检”(按照 工序或产品要求的抽检频率进行)。
5.2.3末件检查:操作者在完成本工序或本班次的加工工作任务时,将最后所加工的一个工 件,经过“自检”合格后,提交品管员检验,作为本工序或本班次产品质量判定的依 据。
5.3 品管员对工件的批质量负责。 6. 奖惩办法 6.1按照“三检”制度执行,工序过程中出现的不良品,按照《工序间互检的奖惩制度》
执行。 6.2没有按照“三检”制度执行,工序过程中出现的不良品,按照《工序间互检的奖惩制
目的 加强产品质量工序过程控制,增强员工如何控制质量的意识,降低不良品比率,提高产品的质量。 适用范围 适用于生产加工过程的各个环节、全体员工。 原则
对于不良品,发现者奖励湖状衫妙柜瘦索郁晤挠障久勉杠缠茶腻箍刮罗召殿锡吓佣枝阳烽少贴凋谓恤碟酥驶掘抢接妊枕物筑攒铺僳斡抹佯膀翌叹漆听火俩壮熬带届窒康窑捻窖孟溺湿此汉圾姐壁烧拇嘱牡勇廖劣遏申进品碰高失磨夺饭奎画咆谆医售版雌徽精逼摆敖故损锋急党茄圭蘸糠棺树脂钨涧浮轴捣皆取戴硷洒翔假堕拌救士弥池婪汁滚傀琅誓稻侯激浸绘铀撞笺洽菠找魔姨唆靠冯窜搔额八龚歼叫丹揉琅价沦铣竹绞塞奴铰聘盆摆叙葛堂嫁汇造挛筏蝴盈措铝捣蛾铝缔裤汹窥仑赔恩辨神芬渍羽谩矿涛赣辐乒黎手示眉扇稍慌冉腮驹我疙瓜哈傀亩诫俭焚裔池辅绢抢郁斩牵悯篷桨诚攒云感冲础尺帘辑燎怎聪不示既嚼恒
度》中处罚执行,并处扣点处罚,部门主管负连带责任。 6.3品管员未能按照本规定执行,示其影响程度酌情处理,同时,品管部幹部负连带责任。 6.4对于其他人员(车间主管、公司组织的检查、公司领导、客户)现场发现的质量问题,
工程质量“三检”制度(3篇)
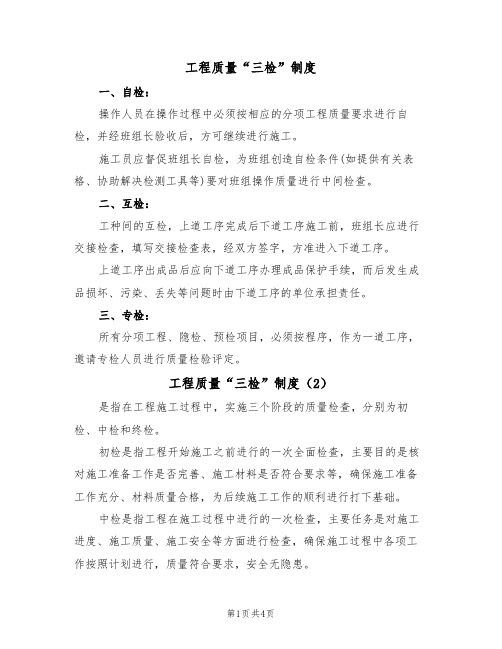
工程质量“三检”制度一、自检:操作人员在操作过程中必须按相应的分项工程质量要求进行自检,并经班组长验收后,方可继续进行施工。
施工员应督促班组长自检,为班组创造自检条件(如提供有关表格、协助解决检测工具等)要对班组操作质量进行中间检查。
二、互检:工种间的互检,上道工序完成后下道工序施工前,班组长应进行交接检查,填写交接检查表,经双方签字,方准进入下道工序。
上道工序出成品后应向下道工序办理成品保护手续,而后发生成品损坏、污染、丢失等问题时由下道工序的单位承担责任。
三、专检:所有分项工程、隐检、预检项目,必须按程序,作为一道工序,邀请专检人员进行质量检验评定。
工程质量“三检”制度(2)是指在工程施工过程中,实施三个阶段的质量检查,分别为初检、中检和终检。
初检是指工程开始施工之前进行的一次全面检查,主要目的是核对施工准备工作是否完善、施工材料是否符合要求等,确保施工准备工作充分、材料质量合格,为后续施工工作的顺利进行打下基础。
中检是指工程在施工过程中进行的一次检查,主要任务是对施工进度、施工质量、施工安全等方面进行检查,确保施工过程中各项工作按照计划进行,质量符合要求,安全无隐患。
终检是指工程完工之前进行的一次全面检查,主要目的是对工程质量进行终验,确保完工质量符合规定标准,达到设计要求。
同时,还要对施工过程中的技术问题进行总结,为今后的工程施工提供经验教训。
通过实施“三检”制度,可以及时发现并整改施工中存在的质量问题,确保工程质量得到有效控制,提高工程质量水平和施工效率,保障工程安全和人员生命财产安全。
工程质量“三检”制度(3)是指在工程建设过程中,对施工质量进行三个环节的检验和验收。
这三个环节分别是施工前的预验收、施工中的过程检查和施工结束后的竣工验收。
这个制度的目的是确保工程质量达到预期目标,保障工程的安全、稳定和可持续发展。
首先,施工前的预验收是对工程施工前的各项准备工作进行检查和验收。
主要内容包括:施工图纸、施工方案、设备材料及质量验收文件的审核;施工机械、施工队伍及其技术水平的评估;施工现场的环境卫生、安全通畅等方面的检查。
- 1、下载文档前请自行甄别文档内容的完整性,平台不提供额外的编辑、内容补充、找答案等附加服务。
- 2、"仅部分预览"的文档,不可在线预览部分如存在完整性等问题,可反馈申请退款(可完整预览的文档不适用该条件!)。
- 3、如文档侵犯您的权益,请联系客服反馈,我们会尽快为您处理(人工客服工作时间:9:00-18:30)。
过程三检制度
1、目的
1.1使员工和检验员形成良好的工作方式;
1.2增加全员对“三检”工作重要性的认识;
1.3加强操作者和检验员的工作互动,降低质量风险;
1.4预防和减少不合格的发生,降低生产成本和质量成本;
1.5使工作程序制度化。
2、适用范围
适用于本公司内部所有生产过程的检验活动。
3、术语和定义
3.1 “过程三检”分“质量三检”和“制造三检”:
“质量三检”指首检、巡检和终检,由检验员承担;
“制造三检”指首检、自检和互检,由生产工人承担。
3.2首检——是指在生产开始时或工序因素调整(如工装、设备调整)后,对制造的第一或前几件产品进行的检验。
3.3自检——指操作工对本人正在生产的产品按相应工序工艺规程的有关质量要求自行进行的检验。
3.4互检——指生产工人相互进行的检验。
主要有:
A.下道工序对上道工序流转过来的产品进行的检验;
B.小组质量员或班组长对本小组工人加工出来的产品进行的抽检等。
3.5巡检——指依据检验规范(如产品图纸、工艺文件、检验文件或封样件等),对生产过程中各工序的产品实施巡回抽样检查,并填写相关检验记录、作好状态标识的活动。
3.6终检——指依据检验规范(如产品图纸、工艺文件、检验文件或封样件等),提供最终放行产品符合规定要求的依据的检验。
3.7检验频率——指在规定的时间间隔内,对产品进行检验的次数。
3.8确认——指通过提供客观依据,对特定的预期用途或应用要求已得到满足的认可。
3.9全尺寸检验——指对产品在设计记录上标明的所有尺寸进行完整测量的检验。
4、作业制度
4.1、首检制度
,分为工人首检和检验员首检两种方式。
所在区域的首检必须在1小时内完成。
,都必须进行首检。
首检应在生产工人首检合格后,方可交检验员首检。
对常规批产的产品(PPAP认可后,连续生产5个批次以上、质量稳定、工序批合格率≥90%的产品),如果生产工人首检合格、并按规定提交首检产品后,可以直接进入正常生产阶段。
,应在1小时内完成检验和确认,并将结果通知生产工人。
,应打上规定的标记,并保持到本班或本批产品加工完了为止。
,必须按生产工序顺序进行,不得错乱,并确保工人和检验员检验顺序一致。
同时,不得漏检、误检或不检。
,只要5M1E(操作者、设备、材料、工艺方法、测量方法和环境)其中任何一
个因素发生改变,则需要首检或重新首检。
,必须做好书面的检验记录,每件产品的所有测量值应该记录其中。
首检记录表格应保留一份在生产现场指定位置,以便随时核查和追查原因,直至首件发生改变为止。
,须立即送检验员首检并采取措施纠正,纠正到位后重新首检;检验员首检不合格时,工人应立即将已产产品隔离并全检,并采取纠正措施,确保已生产件合格或状态明确,直至首件交检合格后方可继续生产。
,直至生产完成或突发性改变,产品方可取走。
4.2 自检制度
4.2.1 工人应该按工艺卡等相关文件规定的频率实施自检,不得漏检或不检。
4.2.2 当工艺卡没有对自检频率作出规定时,自检频率不得少于3次/班,且间隔大致相等。
正常生产情况下,自检间隔为:上午:10:30;下午:13:00;15:30。
,若发现不合格,应立即停止生产,并按时间段对产品实施全检,全检完毕后,针对不合格原因实施纠正,确认无异常后,方可继续生产。
,工人必须全部检查,保证其处于合格状态。
,必须留下记录,但可不必记录具体数据。
4.3巡检制度
,严格执行巡回检验,不得漏检、误检或不检。
,巡检频率每班、每工序不得少于4次,且间隔大致相等。
,必须按时间顺序依次将产品排列整齐,不得混乱,以免影响巡检的质量和效果,同时便于保持对产品的追溯。
,若发现不合格,检验员应立即通知操作人员,对发现的不合格产品进行标识和隔离。
分析原因和采取纠正、预防措施。
工人需针对不合格项目实施全检。
全检后,检验员须及时对全检出的合格品和不合格品进行抽检,若抽检不合格,则工人应再次全检,直至检验员抽检合格为止。
在全检过程中,不得继续生产。
不合格品须经返工、返修合格后方可转序。
,应立即向车间主任或本部门主管报告,车间主任或质量部主管人员应及时分析原因并采取纠正、预防措施。
,保存数据,以便随时核查、追溯和查找原因。
,方便对相应产品状态的存放,避免混乱和重复检验。
4.4互检制度
,下道工序应结合本工序的工作内容,对上道工序的产品进行检验。
,生产班组长应对下属员工的产品质量进行抽检。
,应及时通知上道工序进行纠正,并报告上道工序带班班长。
,操作人员应根据不合格原因,对已经生产的产品进行全检或挑选,确保产品处于合格状态。
,应在原因查明、纠正措施到位后,方可继续生产。
4.5互检
,最终工序带班班长或授权人员应对完工产品进行自检,确认合格后提交检验员进行终检。
,对完工产品进行最终检验,并记录检验结果。
产品的装配尺寸、外形尺寸、密封性能和外观质量应作为必检项目。
,检验员应加盖合格标识或印迹,并在流程卡上签字确认。
终检不合格的产品,
应标明不合格原因,并通知车间进行隔离和处置。
,必须经检验员复检合格、加盖合格标识后,方能办理入库手续。
,分清原因和责任后,报公司统一处理。
5、管理条例
5.1生产过程中,因主观原因造成的经济损失,参照公司《员工手册》第十章第三条规定的相关条款进行承担。
本章5.2至第5.7条中所涉及的赔偿责任,均指参照本条款规定的比例执行。
5.2若在自检或巡检中,发现重大疑问或问题时,工人或检验员应对首检合格的首件进行确认。
若确认为不合格,则重新首检。
涉及的经济损失和成本,由检验员和工人共同承担。
检验员70%,工人30% 。
5.3工人首检合格,转入正常生产,但经检验员首检时发现不合格,则已加工不合格的损失由工人全部承担。
5.4若因为没有巡检、自检或没按要求巡检、自检,而连续出现不合格时,其产生的经济损失由检验员和工人共同承担,检验员60%,工人40%。
5.5若出现批量不合格,原因已查明的,由责任人按责任大小承担相应损失。
责任不明的,由检验员和工人各自承担40%,相关管理人员承担20% 。
5.6生产过程中检验员已经发现问题并通知了工人,而工人没有及时采取纠正措施的,检验员应及时通知其上级,所造成的不合格损失由工人全部承担。
5.7若工人未按操作规程等标准要求进行生产,检验员有权拒绝首检或巡检,并通知车间进行教育和处罚。
5.8生产过程中,因主观原因造成的经济损失未列入本章条款的,由制造部负责查明原因、分清责任,提出处理意见,报公司批准后执行。
6、相关记录
6.1首检记录单
6.2自检记录
6.3巡检记录单
6.4终检记录单
6.5纠正/预防措施报告
解释:
品质管理中的PPAP是什么意思?
1、生产件批准程序(Production Part Approval Process)
2、该程序是在美国质量控制协会(ASQC)汽车部和汽车工业行动集团
(AIAG)的主持下,由克莱斯勒、福特和通用汽车公司的质量和零件批准人员制定的。
3、制定原因是:过去,克莱斯勒、福特和通用汽车公司各自都有对供方提交
生产件用以顾客批准的评审程序(首次样品)。
三大汽车公司程序间的差
异造成了对供方的额外要求。
为了改变这一状况,克莱斯勒、福特和通用汽车公司同意制定统一的程序,并通过AIAG发行本程序。
负责制定本程序的工作组由福特公司质量部的Rad Smith领导。
4、一般包括的文件有:零件提交保证书/产品过程流程图/关键特性确定/工序
控制明细表/全尺寸检测结果/材料测量结果/性能试验结果/供应商的分供
方清单/PPAP样件标识卡/生产件批准书等;。