工业生产过程总_复习
工业流程题知识点总结

工业流程题知识点总结工业流程的基本步骤包括原材料准备、加工、分离、反应、提纯和制品制备。
这些步骤可能涉及物理方法(如过滤、离心、蒸馏等)、化学方法(如溶解、氧化、还原等)、机械方法(如搅拌、挤压、振动等)和热力学方法(如加热、冷却等)。
在工业流程中,有许多常见的操作和装置,如反应釜、蒸馏塔、离心机、干燥器、搅拌槽、输送带等。
这些装置可以用于物料的混合、反应、分离、提纯和加工等操作。
在工业流程中,需要注意一些重要的参数和指标,如温度、压力、流量、浓度、反应速率等。
这些参数对于工艺的控制和优化是非常重要的。
在工业流程中,需要考虑能源的利用和环境的保护。
有效利用能源可以降低成本,减少环境污染。
同时,在工业流程中还需要考虑废物的处理和回收利用等环保问题。
工业流程技术的发展与创新对于提高生产效率、降低成本、改善产品质量和保护环境都有重要意义。
在工业流程中,使用先进的技术和装备可以提高生产效率和品质,并降低能耗和排放。
工业流程还需要考虑人员的安全和生产管理。
工业生产中可能存在一些危险和风险,需要采取一系列的措施来保障员工的安全和生产的顺利进行。
同时,生产管理也是非常重要的,它涉及计划、调度、检查、维护等方面的工作。
在工业流程中,还需要考虑产品的质量控制和质量保证。
生产出的产品必须符合相关的标准和要求,这需要对生产过程进行严格的控制和监督,以保证产品的质量。
总之,工业流程是一个综合性的领域,它涉及许多方面的知识和技术。
通过学习工业流程的知识点,我们可以更好地理解和把握工业生产的规律,同时也可以为工业生产的技术改进和创新做出贡献。
工业工程 总复习提纲
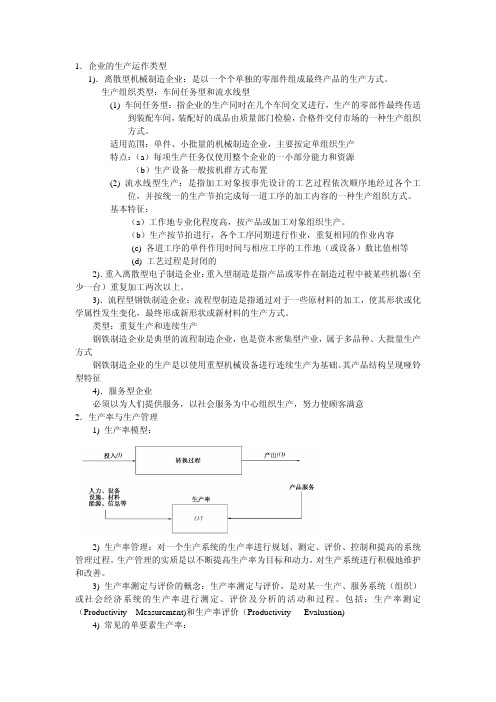
1.企业的生产运作类型1).离散型机械制造企业:是以一个个单独的零部件组成最终产品的生产方式。
生产组织类型:车间任务型和流水线型(1) 车间任务型:指企业的生产同时在几个车间交叉进行,生产的零部件最终传送到装配车间,装配好的成品由质量部门检验,合格件交付市场的一种生产组织方式。
适用范围:单件、小批量的机械制造企业,主要按定单组织生产特点:(a)每项生产任务仅使用整个企业的一小部分能力和资源(b)生产设备一般按机群方式布置(2) 流水线型生产:是指加工对象按事先设计的工艺过程依次顺序地经过各个工位,并按统一的生产节拍完成每一道工序的加工内容的一种生产组织方式。
基本特征:(a)工作地专业化程度高,按产品或加工对象组织生产。
(b)生产按节拍进行,各个工序同期进行作业,重复相同的作业内容(c) 各道工序的单件作用时间与相应工序的工作地(或设备)数比值相等(d) 工艺过程是封闭的2).重入离散型电子制造企业:重入型制造是指产品或零件在制造过程中被某些机器(至少一台)重复加工两次以上。
3).流程型钢铁制造企业:流程型制造是指通过对于一些原材料的加工,使其形状或化学属性发生变化,最终形成新形状或新材料的生产方式。
类型:重复生产和连续生产钢铁制造企业是典型的流程制造企业,也是资本密集型产业,属于多品种、大批量生产方式钢铁制造企业的生产是以使用重型机械设备进行连续生产为基础。
其产品结构呈现哑铃型特征4).服务型企业必须以为人们提供服务,以社会服务为中心组织生产,努力使顾客满意2.生产率与生产管理生产率模型:1)生产率管理:对一个生产系统的生产率进行规划、测定、评价、控制和提高的系统 2)管理过程。
生产管理的实质是以不断提高生产率为目标和动力,对生产系统进行积极地维护和改善。
生产率测定与评价的概念:生产率测定与评价,是对某一生产、服务系统(组织) 3)或社会经济系统的生产率进行测定、评价及分析的活动和过程。
包括:生产率测定(Productivity Measurement)和生产率评价(Productivity Evaluation)常见的单要素生产率:4)劳动生产率(1)(2) 资本生产率(3) 设备生产率(4) 能源生产率(5) 原材料生产率(6) 成本生产率3.工业工程基础相关基本概念、内容1)、定义:工业工程(Industrial Engineering)是对有关人员、物资、设备、能源和信息所组成的集成系统(Integrated System)进行设计、改善和设置的一门学科。
工业生产过程与管理复习题【不错哦】

一、填空题1. 在经济研究和管理中,经常使用的分类方法主要有:两大领域与两大部分类分类法,三次产业分类法,资源密集程度分类法,国际标准产业分类法。
2. 两大领域与两大部类分类法是依据马克思的再生产理论,按生产活动的性质极其属性对产业进行分类,把产业部门分为生产资料生产部门和消费资料生产部门。
3. 按照两大领域和两大部类分类法,教育,金融,运输,卫生,建筑,邮电,商业几个部门中属于物质资料的生产部门有:运输、建筑、邮电、商业;属于非物质资料的生产部门有:教育、金融、卫生。
4. 按照三次产业分类法,建筑业、交通运输业、电力、渔业、餐饮业、林业、制造业、信息传输业、农业、采矿业、房地产业、邮政业、商业、牧业、燃气供应业、卫生业;这些行业中属于第一产业的有:农业、林业、牧业、渔业;属于第二产业的有:采矿业、制造业、电力业、燃气供应业、建筑业;属于第三产业的有:信息传输业、房地产业、交通运输业、商业、邮政业、卫生业、餐饮业。
5. 根据劳动力、资本和技术三种生产要素在各产业中的相对密集度,把产业划分为劳动密集型产业、资本密集型产业和技术密集型产业。
6. 循环经济的行为原则是3R原则,即减量化;再利用;再循环。
7. 现代生产的形式有:生产自动化、以销定产型生产、多角化经营生产、国际化营生产。
8. 安全生产的方针:安全第一、预防为主、综合治理。
9. 工业产品的生产过程一般包括:工艺过程、检验过程、运输过程、自然过程、储存等待过程。
10. 企业的生产过程包括:生产技术准备过程、基本生产过程、辅助生产过程、生产服务过程、附属生产过程。
11. 煤中的有机质主要由:碳、氢、氧、氮和有机硫等五种元素组成。
12. 按煤化程度,煤炭可分为:泥炭、褐煤、烟煤、无烟煤。
13. 按供销条件,煤炭可分为:原煤、块煤、洗精煤。
14. 按工业使用的要求煤炭可分为14个类别,分别为:褐煤、长焰煤、不粘煤、1/2中粘煤、气煤、气肥煤、肥煤、1/3焦煤、焦煤、瘦煤、贫瘦煤、贫煤、无烟煤。
化学专题复习工业作业流程题教学设计教学案及教学反思及新版培训教材
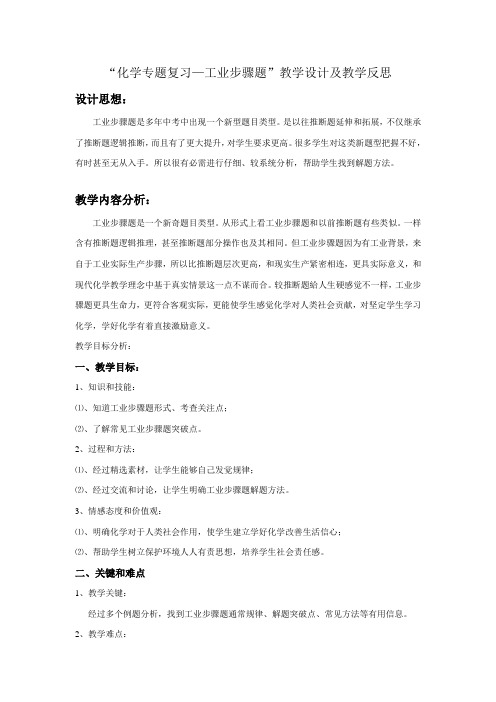
“化学专题复习—工业步骤题”教学设计及教学反思设计思想:工业步骤题是多年中考中出现一个新型题目类型。
是以往推断题延伸和拓展,不仅继承了推断题逻辑推断,而且有了更大提升,对学生要求更高。
很多学生对这类新题型把握不好,有时甚至无从入手。
所以很有必需进行仔细、较系统分析,帮助学生找到解题方法。
教学内容分析:工业步骤题是一个新奇题目类型。
从形式上看工业步骤题和以前推断题有些类似。
一样含有推断题逻辑推理,甚至推断题部分操作也及其相同。
但工业步骤题因为有工业背景,来自于工业实际生产步骤,所以比推断题层次更高,和现实生产紧密相连,更具实际意义,和现代化学教学理念中基于真实情景这一点不谋而合。
较推断题給人生硬感觉不一样,工业步骤题更具生命力,更符合客观实际,更能使学生感觉化学对人类社会贡献,对坚定学生学习化学,学好化学有着直接激励意义。
教学目标分析:一、教学目标:1、知识和技能:⑴、知道工业步骤题形式、考查关注点;⑵、了解常见工业步骤题突破点。
2、过程和方法:⑴、经过精选素材,让学生能够自己发觉规律;⑵、经过交流和讨论,让学生明确工业步骤题解题方法。
3、情感态度和价值观:⑴、明确化学对于人类社会作用,使学生建立学好化学改善生活信心;⑵、帮助学生树立保护环境人人有责思想,培养学生社会责任感。
二、关键和难点1、教学关键:经过多个例题分析,找到工业步骤题通常规律、解题突破点、常见方法等有用信息。
2、教学难点:寻求和总结规律。
教学准备:课前完成三个例题。
教学过程设计:【视频】:播放一段相关海洋广告。
【提问】:在广告中大家得到了哪些东西?【例题1】:(张家港模拟)海水利用:同学们称量了5.0g粗盐,在老师指导下经过提纯操作,得到了较纯精盐。
请回复下列问题。
(1)在除去不溶性杂质试验中用得最多仪器是。
(2)除去泥沙等不溶性杂质后,粗盐中还含有氯化镁、氯化钙、硫酸钠等可溶性杂质。
将这些可溶性杂质清除试验方案以下(所加试剂均稍过量):①加入Na2CO3溶液发生化学反应用化学方程式可表示为,。
2023届高考化学一轮专题复习----工业流程题专题训练

2023届高考化学一轮专题复习----工业流程题专题训练1.Mn3O4可用于电子工业生产软磁铁氧体,用作电子计算机中存储信息的磁芯、磁盘等。
软锰矿主要成分是MnO2,还含有少量的Fe2O3、SiO2、Al2O3,采用以下工艺流程可由软锰矿制得Mn3O4。
该工艺条件下,溶液中金属离子开始沉淀和完全沉淀的pH如表所示:金属离子Fe3+Fe2+Al3+Mn2+开始沉淀pH 1.97.0 3.08.1完全沉淀pH 3.29.0 4.710.1回答下列问题:(1)“酸浸、还原”时,为了加快化学反应速率,可以采取的措施有________(只需填一种),“酸浸、还原”后溶液中含有的金属阳离子主要有________,铁屑与MnO2发生反应的离子方程式为________。
(2)“调节pH”时加入H2O2溶液的目的是________,“调节pH”的范围为________。
(3)“沉锰”时,其他条件一定,沉锰过程中锰离子的沉淀率与溶液温度的关系如图所示。
50℃后,溶液温度越高,锰离子的沉淀率越低的原因是________。
(4)“氧化”时一般控制温度在80℃~85℃,可以采取的加热方法是________,反应化学方程式为________。
2.工业上以石煤(主要成分为V2O3,含有少量SiO2、P2O5等杂质)为原料制备钒的主要流程如图:已知:℃NH4VO3难溶于水。
℃K sp(MgSiO3)=2.4×10-5,K sp[Mg3(PO4)2]=2.7×10-27。
(1)焙烧:通入空气的条件下,向石煤中加纯碱焙烧,将V2O3转化为NaVO3的化学方程式为___。
(2)除硅、磷:℃用MgSO4溶液除硅、磷时,Si、P会形成Mg3(PO4)2、MgSiO3沉淀。
若沉淀后溶液中c(PO34-)=1.0×10-8mol•L-1,则c(SiO23-)=___mol•L-1。
℃如图所示,随着温度升高,除磷率下降,其原因是Mg3(PO4)2溶解度增大、___;随着温度升高,除硅率升高,其原因是___。
高三化学(苏教版)总复习 2-1-3化学与工农业生产
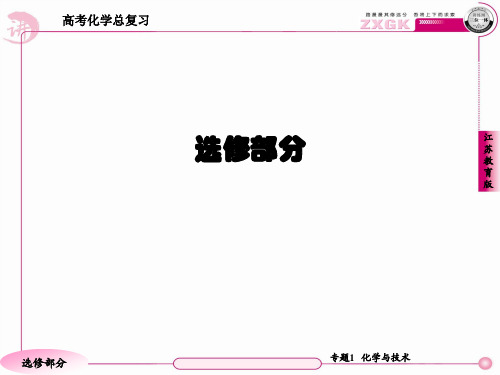
选修部分
江 苏 教 育 版
选修部分
专题1 化学与技术
高考化学总复习
江 苏 教 育 版
选修部分
专题1 化学与技术
高考化学总复习
第三单元
化学与工农业生产
江 苏 教 育 版
选修部分
专题1 第三单元
高考化学总复习
江 苏 教 育 版
选修部分
专题1 第三单元
高考化学总复习
1.了解我国无机化工的生产资源和产品的主要种类。 2.了解合成氨的主要原理、原料、重要设备、流程和 意义。 认识催化剂的研制对促进化学工业发展的重大意义。 3.了解精细化工产品的生产特点、精细化工在社会发 展中的作用。 4.了解化学肥料、农药等在农业生产中的作用。
江 苏 教 育 版
选修部分
专题1 第三单元
高考化学总复习
纯碱的生产(氨碱法)
1.原料:______________。 2.生产过程 (1)在精制的饱和食盐水中通入氨气。 (2)将 CO2 通入氨化的饱和食盐水中,发生反应为: __________________________
江 苏 教 育 版
选修部分
江 苏 教 育 版
选修部分
专题1 第三单元
高考化学总复习
2.化学原理与硫酸工业生产流程
江 苏 教 育 版
选修部分
专题1 第三单元
高考化学总复习
3.化学原理在化工生产中的应用 (1)三个反应条件的确定 ①温度 400~500℃:根据平衡移动原理,应在低温下 进行,但低温时催化剂的活性不高,反应速率低,实际生 产中采用 400~500℃的温度。 ②常压:根据平衡移动原理,应在高压下进行,但增 大压强对 SO2 的转化率提高不大,且加压会增大成本和能 量消耗,而常压下的转化率已很高,实际生产采用常压操 作。
化工单元操作总复习
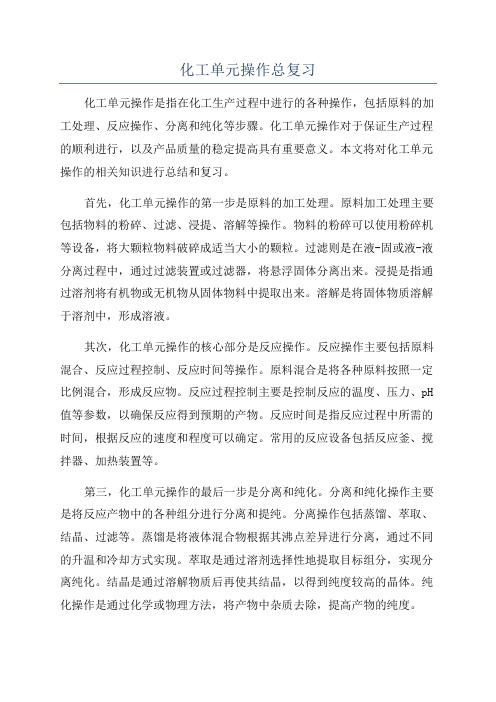
化工单元操作总复习化工单元操作是指在化工生产过程中进行的各种操作,包括原料的加工处理、反应操作、分离和纯化等步骤。
化工单元操作对于保证生产过程的顺利进行,以及产品质量的稳定提高具有重要意义。
本文将对化工单元操作的相关知识进行总结和复习。
首先,化工单元操作的第一步是原料的加工处理。
原料加工处理主要包括物料的粉碎、过滤、浸提、溶解等操作。
物料的粉碎可以使用粉碎机等设备,将大颗粒物料破碎成适当大小的颗粒。
过滤则是在液-固或液-液分离过程中,通过过滤装置或过滤器,将悬浮固体分离出来。
浸提是指通过溶剂将有机物或无机物从固体物料中提取出来。
溶解是将固体物质溶解于溶剂中,形成溶液。
其次,化工单元操作的核心部分是反应操作。
反应操作主要包括原料混合、反应过程控制、反应时间等操作。
原料混合是将各种原料按照一定比例混合,形成反应物。
反应过程控制主要是控制反应的温度、压力、pH 值等参数,以确保反应得到预期的产物。
反应时间是指反应过程中所需的时间,根据反应的速度和程度可以确定。
常用的反应设备包括反应釜、搅拌器、加热装置等。
第三,化工单元操作的最后一步是分离和纯化。
分离和纯化操作主要是将反应产物中的各种组分进行分离和提纯。
分离操作包括蒸馏、萃取、结晶、过滤等。
蒸馏是将液体混合物根据其沸点差异进行分离,通过不同的升温和冷却方式实现。
萃取是通过溶剂选择性地提取目标组分,实现分离纯化。
结晶是通过溶解物质后再使其结晶,以得到纯度较高的晶体。
纯化操作是通过化学或物理方法,将产物中杂质去除,提高产物的纯度。
除了以上的基本操作,化工单元操作还需要关注安全和环保等问题。
在化工过程中,需要使用各种安全设备,确保操作人员的安全。
同时,需要严格遵守环保法规,避免对环境的污染。
综上所述,化工单元操作是化工生产过程中的核心环节之一、通过加工处理、反应操作、分离和纯化等步骤,实现了原料的加工转化和产物的提纯。
化工单元操作的复习对于提高化工生产的效率和产品质量具有重要意义。
中考化学工业流程
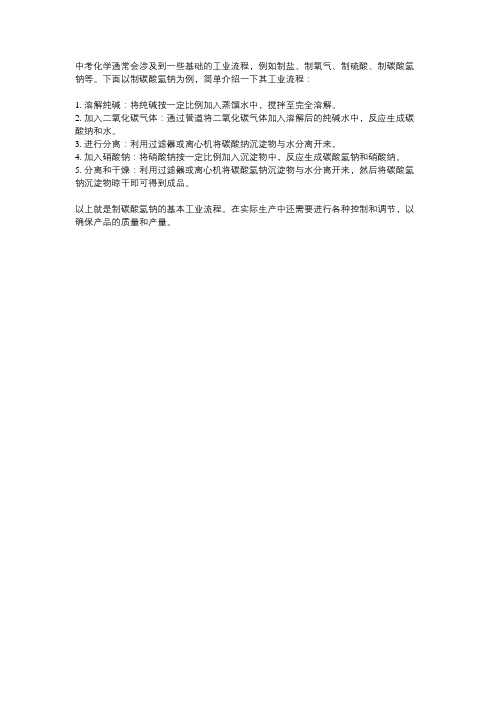
中考化学通常会涉及到一些基础的工业流程,例如制盐、制氧气、制硫酸、制碳酸氢钠等。
下面以制碳酸氢钠为例,简单介绍一下其工业流程:
1. 溶解纯碱:将纯碱按一定比例加入蒸馏水中,搅拌至完全溶解。
2. 加入二氧化碳气体:通过管道将二氧化碳气体加入溶解后的纯碱水中,反应生成碳酸纳和水。
3. 进行分离:利用过滤器或离心机将碳酸纳沉淀物与水分离开来。
4. 加入硝酸钠:将硝酸钠按一定比例加入沉淀物中,反应生成碳酸氢钠和硝酸纳。
5. 分离和干燥:利用过滤器或离心机将碳酸氢钠沉淀物与水分离开来,然后将碳酸氢钠沉淀物晾干即可得到成品。
以上就是制碳酸氢钠的基本工业流程。
在实际生产中还需要进行各种控制和调节,以确保产品的质量和产量。
基础工业工程期末考试复习小抄
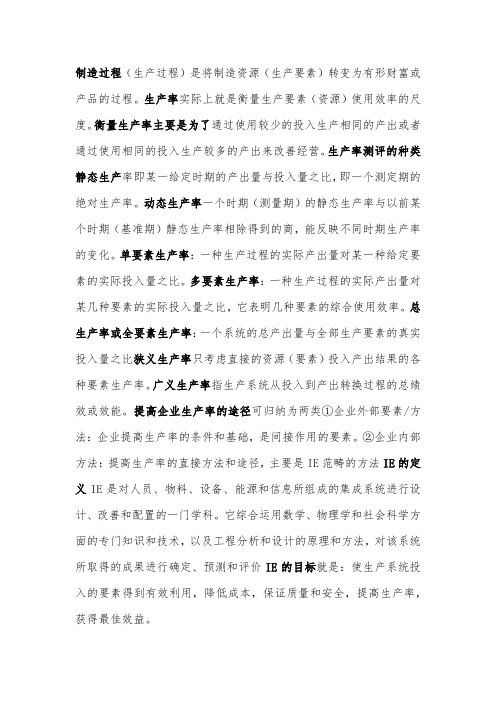
制造过程(生产过程)是将制造资源(生产要素)转变为有形财富或产品的过程。
生产率实际上就是衡量生产要素(资源)使用效率的尺度。
衡量生产率主要是为了通过使用较少的投入生产相同的产出或者通过使用相同的投入生产较多的产出来改善经营。
生产率测评的种类静态生产率即某一给定时期的产出量与投入量之比,即一个测定期的绝对生产率。
动态生产率一个时期(测量期)的静态生产率与以前某个时期(基准期)静态生产率相除得到的商,能反映不同时期生产率的变化。
单要素生产率:一种生产过程的实际产出量对某一种给定要素的实际投入量之比。
多要素生产率:一种生产过程的实际产出量对某几种要素的实际投入量之比,它表明几种要素的综合使用效率。
总生产率或全要素生产率:一个系统的总产出量与全部生产要素的真实投入量之比狭义生产率只考虑直接的资源(要素)投入产出结果的各种要素生产率。
广义生产率指生产系统从投入到产出转换过程的总绩效或效能。
提高企业生产率的途径可归纳为两类①企业外部要素/方法:企业提高生产率的条件和基础,是间接作用的要素。
②企业内部方法:提高生产率的直接方法和途径,主要是IE范畴的方法IE的定义IE是对人员、物料、设备、能源和信息所组成的集成系统进行设计、改善和配置的一门学科。
它综合运用数学、物理学和社会科学方面的专门知识和技术,以及工程分析和设计的原理和方法,对该系统所取得的成果进行确定、预测和评价IE的目标就是:使生产系统投入的要素得到有效利用,降低成本,保证质量和安全,提高生产率,获得最佳效益。
工业工程的产生与发展产生动因✶科学技术:20世纪初进入电动机时代✷生产力:福特生产线经济形态:18-19世纪完成工业资本积累✷代表人物:泰勒吉尔布雷斯甘特依次经过三个阶段:科学管理、传统IE、现代管理泰勒的时间研究进行了铁锹实验吉尔布雷斯的动作研究进行了砌砖实验工作研究以生产系统为研究对象。
作业系统是为实现预定的功能、达成系统的目标,由许多相互联系的因素所形成的有机整体工作研究的特点只需很少的投资或不需要投资的情况下,通过改进作业流程和操作方法,实行先进合理的工作定额,充分利用企业自身的人力、物力和财力等资源,走内涵式发展的道路,挖掘企业内部潜力,提高企业的生产效率和效益,降低成本,增强企业的竞争能力。
化工生产过程知识培训资料
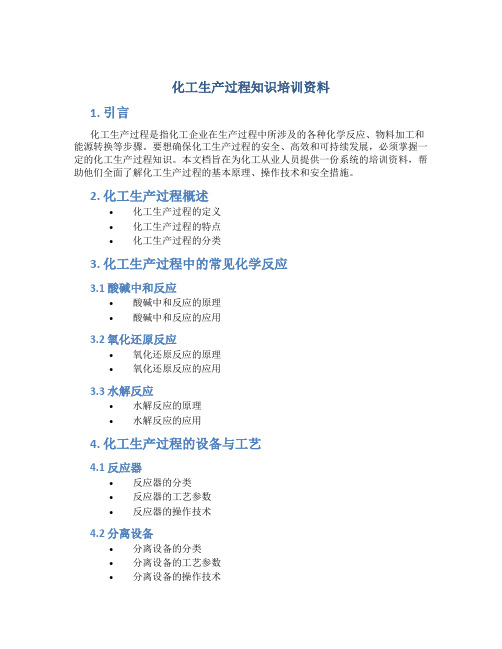
化工生产过程知识培训资料1. 引言化工生产过程是指化工企业在生产过程中所涉及的各种化学反应、物料加工和能源转换等步骤。
要想确保化工生产过程的安全、高效和可持续发展,必须掌握一定的化工生产过程知识。
本文档旨在为化工从业人员提供一份系统的培训资料,帮助他们全面了解化工生产过程的基本原理、操作技术和安全措施。
2. 化工生产过程概述•化工生产过程的定义•化工生产过程的特点•化工生产过程的分类3. 化工生产过程中的常见化学反应3.1 酸碱中和反应•酸碱中和反应的原理•酸碱中和反应的应用3.2 氧化还原反应•氧化还原反应的原理•氧化还原反应的应用3.3 水解反应•水解反应的原理•水解反应的应用4. 化工生产过程的设备与工艺4.1 反应器•反应器的分类•反应器的工艺参数•反应器的操作技术4.2 分离设备•分离设备的分类•分离设备的工艺参数•分离设备的操作技术4.3 传热设备•传热设备的分类•传热设备的工艺参数•传热设备的操作技术4.4 混合设备•混合设备的分类•混合设备的工艺参数•混合设备的操作技术5. 化工生产过程的安全与环保5.1 安全措施•设备安全•操作安全•应急措施5.2 环境保护•废水处理•废气处理•固体废物处理6. 化工生产过程的优化与控制6.1 过程优化•原料优化•能源优化•生产条件优化6.2 过程控制•过程参数监测与控制•自动化控制系统•故障诊断与处理7. 结论本文档对化工生产过程的知识进行了系统的分类和总结,包括化学反应、设备与工艺、安全与环保以及优化与控制等方面。
希望本文档能够帮助化工从业人员全面了解化工生产过程的基本知识,提高工作效率、降低事故风险,促进化工行业的可持续发展。
在实际操作中,务必严格遵守相关操作规程和安全操作规范,保障生产过程的安全性和稳定性。
工业知识点总结七年级下册

工业知识点总结七年级下册第一章工业的发展历史1. 工业的起源工业起源于人类社会的生产活动。
最早的工业是手工业,即人们利用手工工具和简单的机器进行生产。
后来,随着科学技术的发展,工业生产开始采用水力、风力等动力,并逐渐形成了机器工业。
2. 工业革命工业革命是指18世纪末至19世纪初,英国先后出现了纺织业和煤炭工业的机械化生产,从而迅速带动了整个社会经济的发展。
工业革命的产生和发展,标志着人类生产力水平的跨越性发展,同时也导致了生产方式、社会结构的深刻变革。
3. 工业的全球扩散工业的发展不仅改变了单个国家的经济结构,也改变了全球范围内的经济关系。
各国之间的工业化进程不断加快,工业生产和贸易不断扩散到全球,形成了一个紧密相连、共同发展的全球经济体系。
第二章工业发展的影响1. 经济效益工业的发展对国民经济产生了巨大的经济效益,工业化的国家通常都能有较高的国民生产总值和人均收入,工业产品也比农产品更容易推广。
2. 社会影响工业化改变了人们的社会生活,人们的生活水平得到了提高,但也带来了环境污染、资源耗竭、社会不平等等问题。
工业化进程也加剧了城市化,农村人口不断向城市聚集。
3. 生态环境工业化造成了大量的空气、水、土壤污染,破坏了自然生态系统。
工业废弃物处理成为严重的环境问题,全球气候变化也受到工业化的影响。
第三章工业生产的基本技术1. 煤炭工业煤炭是工业发展的重要能源,煤炭工业包括了煤矿开采、煤炭加工和利用等过程。
随着科技的发展,煤炭工业逐渐向高效、清洁、绿色方向发展。
钢铁工业是现代工业的基础产业,钢铁是制造机械、建筑等方面的重要原材料,钢铁工业包括了矿石采选、炼铁、炼钢等过程。
3. 石油化工石油是重要的能源资源,石油化工是对石油进行加工利用的产业,包括了炼油、石油化工产品的生产等过程。
石油的应用范围广泛,包括了能源、化肥、合成材料等多个领域。
第四章现代工业技术1. 信息技术信息技术是现代工业的重要支撑,包括了信息传输、数据处理等技术,信息技术的发展在工业自动化、智能化方面发挥了重要作用。
复习工业过程控制PCS
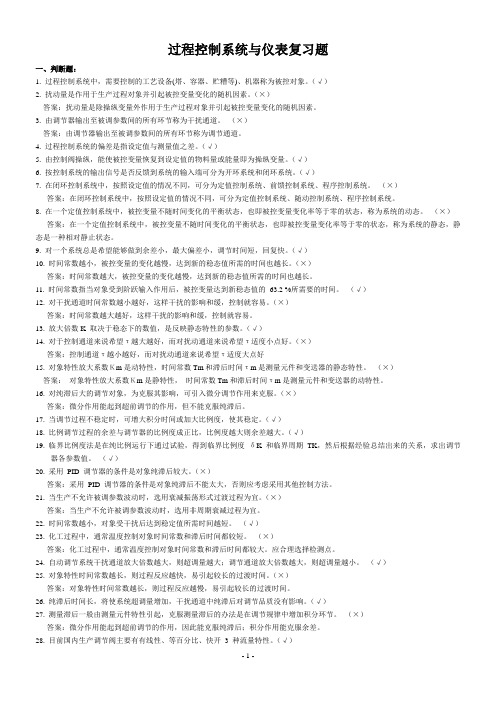
过程控制系统与仪表复习题一、判断题:1. 过程控制系统中,需要控制的工艺设备(塔、容器、贮糟等)、机器称为被控对象。
(√)2. 扰动量是作用于生产过程对象并引起被控变量变化的随机因素。
(×)答案:扰动量是除操纵变量外作用于生产过程对象并引起被控变量变化的随机因素。
3. 由调节器输出至被调参数间的所有环节称为干扰通道。
(×)答案:由调节器输出至被调参数间的所有环节称为调节通道。
4. 过程控制系统的偏差是指设定值与测量值之差。
(√)5. 由控制阀操纵,能使被控变量恢复到设定值的物料量或能量即为操纵变量。
(√)6. 按控制系统的输出信号是否反馈到系统的输入端可分为开环系统和闭环系统。
(√)7. 在闭环控制系统中,按照设定值的情况不同,可分为定值控制系统、前馈控制系统、程序控制系统。
(×)答案:在闭环控制系统中,按照设定值的情况不同,可分为定值控制系统、随动控制系统、程序控制系统。
8. 在一个定值控制系统中,被控变量不随时间变化的平衡状态,也即被控变量变化率等于零的状态,称为系统的动态。
(×)答案:在一个定值控制系统中,被控变量不随时间变化的平衡状态,也即被控变量变化率等于零的状态,称为系统的静态,静态是一种相对静止状态。
9. 对一个系统总是希望能够做到余差小,最大偏差小,调节时间短,回复快。
(√)10. 时间常数越小,被控变量的变化越慢,达到新的稳态值所需的时间也越长。
(×)答案:时间常数越大,被控变量的变化越慢,达到新的稳态值所需的时间也越长。
11. 时间常数指当对象受到阶跃输入作用后,被控变量达到新稳态值的63.2 %所需要的时间。
(√)12. 对干扰通道时间常数越小越好,这样干扰的影响和缓,控制就容易。
(×)答案:时间常数越大越好,这样干扰的影响和缓,控制就容易。
13. 放大倍数K 取决于稳态下的数值,是反映静态特性的参数。
(√)14. 对于控制通道来说希望τ越大越好,而对扰动通道来说希望τ适度小点好。
工业分析复习

《工业分析》1 绪论:1.工业分析的任务:研究工业生产的原料、辅助材料、中间产品、副产品及各种废物组成的分析检验方法。
2.工业分析的方法:按照方法原理:化学分析法,物理化学分析法和物理分析法。
按照分析任务:定性分析,定量分析,结构分析,表面分析,形态分析。
按照分析对象:无机分析,有机分析。
按照试剂用量:常量分析,微量分析,痕量分析。
按照分析要求:例行分析,仲裁分析。
按照完成分析时间和所起的作用分为:快速分析,标准分析。
按照分析测试程序不同:离线分析,在线分析。
3.工业分析方法的选择:国家标准,行业标准,地方标准和企业标准。
第一章:试样采集与制备第一节试样的采集2.采样量公式:Q ≥ kd23.从大储存容器中采样。
(P12)第二节试样的制备1.制样的基本程序:破碎、过筛、混匀和缩分。
2.缩分的方法:分样器缩分法、四分法、棋盘缩分法。
第三节试样的分解1. 湿法分解法-(P17)2. 干法分解法-(P17-18)第二章:煤的工业分析1.煤的工业分析项目:水分、灰分、挥发分、固定碳、发热量和全硫。
2.水分可分:游离水和化合水(结晶水);游离水又分外在水分和内在水分2.1 游离水在 105~110℃的温度下,加热1~2h 可蒸发。
2.2 化合水在200℃以上才能解析全水测定(1)两步法 P24 (2)一步法 P252.灰分:煤的灰分是指煤完全燃烧后剩下的残渣,是煤中矿物质在煤完全燃烧过程中经过一系列分解、化合反应后的产物(主要有SiO2 、Al2O3、 Fe2O3 、 CaO 、 MgO )。
3.挥发分:煤在规定条件下隔绝空气加热进行水分校正后的质量损失。
4.煤中全硫的测定方法:艾氏卡法(仲裁法)、高温燃烧中和法、高温燃烧碘量法、库伦法。
5.艾氏卡试剂:2份质量的氧化镁 + 1份质量的无水碳酸钠6.库仑滴定法测定煤中全硫的方法,使用的催化剂:三氧化钨7.弾筒发热量:单位质量的试样在充有过量氧气的氧弹内燃烧,其燃烧产物组成为氧气、氮气、二氧化碳、硝酸和硫酸、液态水以及固态灰时放出的热量。
初三化学九年级下册一模复习《工业流程图专题》知识点归纳学案与练习题专题

工艺流程图专题一、工艺流程路线示意图箭头:进入的是投料(即反应物),出去的是生成物(包括主产物和副产物)。
出线、进线:表示物料流向或操作流程;反向线:表示物质循环使用;方框:表示经过反应或操作后剩余的物质。
二、工艺流程题的解题方法与策略1.一般采用首尾分析法,明确原始物质及目标产物2.读流程,观其大略,找出流程主线(即从流程开始到达产品或是达成实验目的的为主线,其他的是支线,如上图)。
3.常考的操作术语及目的:(1)对原料进行预处理的常用方法及其作用①粉碎(研磨):增大反应物的,加快或使反应。
②灼烧(煅烧):使固体在高温下分解或使杂质在高温下氧化、分解等。
使反应充分进行或增大转化率。
(2)明确常用的分离方法①过滤:和的分离。
所需仪器有铁架台(带铁圈)、滤纸、。
洗涤:尽量除去晶体表面的杂质或干扰物质。
干燥:除去固体中的水。
4.答题技巧:(1)所设问题一般都是孤立的,在解答时不要求流程全看懂后再解答,看不懂的地方先跳过去,继续解答后面的问题。
有时候可以直接使用“节点法”进行解题,即进入“节点”的物质是反应物,流出“节点”的是生成物。
(2)抓住一个关键点:一切反应或操作都是为了获得产品或是达成实验的目的。
(3)推断流程图某一步中的物质,可以从上一步操作中反应物可能发生的反应入手进行分析,同时需注意所加试剂是否有过量(剩余),要关注物质在流程“节点”中转移情况(三大转移):反应产物转移;不反应物质转移和过量物质转移。
(4)陌生化学方程式的书写:根据箭头方向,箭头进入的是投料(即反应物),出去的是生成物(包括主产物和副产物);若从已知信息中找出的反应物和生成物不满足质量守恒定律,可以在反应物或生成物中加上水,然后进行配平,还应注意反应条件的有关信息;若在空气中煅烧或通入空气则还需考虑空气中的氧气是否参与反应。
(5)循环利用的物质:某物质不在流程的主线上而在流程的支线上,它是某一步骤中的产物同时也是另一步骤中的原料,它即是这个流程中的循环利用物质。
化学工业流程知识点汇总

化学工业流程知识点汇总
化学工业流程是指在化学工业生产中所涉及的各种化学反应、物质转化和生产工艺。
以下是化学工业流程的一些知识点汇总:
1. 原料准备,化学工业流程通常从原料的准备开始,原料可以是天然资源如矿石、石油等,也可以是化学合成的中间体或原料。
2. 反应过程,化学工业生产中的核心是各种化学反应过程,包括合成反应、氧化还原反应、酸碱中和反应等。
这些反应过程需要精确的控制温度、压力、催化剂等条件。
3. 分离和纯化,在化学工业流程中,通常需要对反应产物进行分离和纯化,以获得所需的化学品。
常用的分离技术包括蒸馏、结晶、萃取、过滤等。
4. 能源消耗,化学工业流程通常需要大量的能源,包括热能和电能。
优化能源利用,减少能源消耗是化学工业流程设计的重要考虑因素。
5. 废物处理,化学工业流程产生的废物需要得到妥善处理,以
减少对环境的影响。
常见的废物处理方法包括焚烧、化学中和、再循环利用等。
6. 自动化控制,现代化学工业流程通常采用自动化控制系统,实现对生产过程的精确控制,提高生产效率和产品质量。
7. 安全生产,化学工业流程涉及到许多危险化学品和高温高压等条件,安全生产是化学工业流程设计和操作的重要方面,需要严格遵守相关的安全规范和标准。
综上所述,化学工业流程涉及到原料准备、反应过程、分离和纯化、能源消耗、废物处理、自动化控制和安全生产等多个方面。
设计和优化化学工业流程需要综合考虑这些方面,以实现高效、安全、环保的生产。
化学工业流程知识点汇总

化学工业流程知识点汇总化学工业流程是指将原料经过一系列化学反应和物理操作,转化为最终产品的过程。
在化学工业中,有许多不同的流程和工艺被广泛应用于各个领域,如石油化工、制药、冶金等。
下面将介绍几个常见的化学工业流程。
1. 石油炼制流程:石油炼制是将原油分离并转化为不同产品的过程。
首先,原油经过蒸馏塔分离为不同沸点的馏分,如汽油、柴油、煤油等。
然后,这些馏分经过催化裂化、重整、脱硫、脱氮等处理,得到符合市场需求的燃料和化工产品。
2. 合成氨工艺:合成氨是一种重要的化工原料,广泛用于制造肥料和化学品。
合成氨工艺主要包括气体净化、催化反应和分离纯化。
首先,氨合成气(含氢气和氮气)通过吸附和脱硫等步骤进行净化。
然后,氨合成反应在高温高压下进行,通常采用铁-钼催化剂。
最后,通过压缩和吸附等工艺,将合成氨纯化至所需纯度。
3. 化学品生产流程:化学品生产涉及许多不同的流程和反应,如聚合、酯化、酰化等。
以聚合反应为例,聚合是将单体分子连接成高分子化合物的过程。
通常有两种主要的聚合方法:添加聚合和缩聚聚合。
添加聚合是指通过在单体中引入双键或环状结构,使单体分子通过共价键连接起来。
缩聚聚合是指通过两个单体分子之间的反应,生成一个分子。
4. 制药工艺:制药工艺是将药物原料转化为药品的过程。
制药工艺包括原料处理、混合、反应、分离和纯化等步骤。
例如,制造药片的工艺通常包括将活性成分与辅料混合,通过湿法或干法成型制成片剂,然后进行包衣、涂层、包装等工艺。
5. 冶金工艺:冶金工艺涉及金属矿石的提取和精炼。
主要流程包括矿石破碎、矿浆制备、浮选、烧结、熔炼、精炼等。
例如,冶金工艺中的熔炼是将金属矿石通过高温熔融,使金属与其他杂质分离的过程。
精炼则是将熔炼产物进一步纯化,以提高金属的纯度。
化学工业流程在现代工业生产中扮演着重要的角色。
了解和掌握这些流程是化学工程师和相关专业人员的基本能力。
通过合理的设计和优化,可以提高产品质量和产能,降低生产成本,实现可持续发展。
2021届高考复习工业流程专题
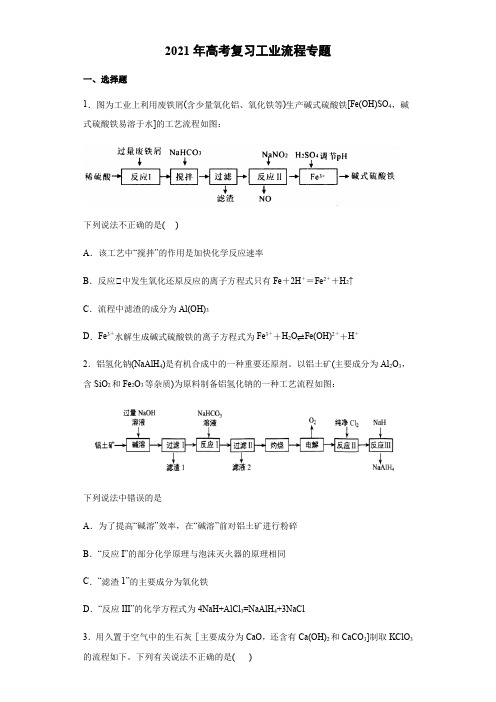
2021年高考复习工业流程专题一、选择题1.图为工业上利用废铁屑(含少量氧化铝、氧化铁等)生产碱式硫酸铁[Fe(OH)SO4,碱式硫酸铁易溶于水]的工艺流程如图:下列说法不正确的是( )A.该工艺中“搅拌”的作用是加快化学反应速率B.反应Ⅰ中发生氧化还原反应的离子方程式只有Fe+2H+=Fe2++H2↑C.流程中滤渣的成分为Al(OH)3D.Fe3+水解生成碱式硫酸铁的离子方程式为Fe3++H2O⇌Fe(OH)2++H+2.铝氢化钠(NaAlH4)是有机合成中的一种重要还原剂。
以铝土矿(主要成分为Al2O3,含SiO2和Fe2O3等杂质)为原料制备铝氢化钠的一种工艺流程如图:下列说法中错误的是A.为了提高“碱溶”效率,在“碱溶”前对铝土矿进行粉碎B.“反应I”的部分化学原理与泡沫灭火器的原理相同C.“滤渣1”的主要成分为氧化铁D.“反应III”的化学方程式为4NaH+AlCl3=NaAlH4+3NaCl3.用久置于空气中的生石灰[主要成分为CaO,还含有Ca(OH)2和CaCO3]制取KClO3的流程如下。
下列有关说法不正确的是( )A.“打浆”的目的是为了提高“氯化”时的反应速率B.“氯化”中主要发生的化学反应为6Cl2+6Ca(OH)275CCa(ClO3)2+5CaCl2+6H2OC.“过滤”后滤液中存在的阳离子有Ca2+、H+D.“转化”时发生的化学反应属于氧化还原反应4.实验室用含有杂质(FeO、Fe2O3)的废CuO制备胆矾晶体,经历了下列过程(已知Fe3+在pH=5时沉淀完全).其中分析错误的是( )A.步骤②发生的主要反应为:2Fe2++H2O2+2H+=2Fe3++2H2OB.步骤②能用氯水、硝酸等强氧化剂代替H2O2C.步骤③用CuCO3代替CuO也可调节溶液的pHD.步骤④为过滤,步骤⑤为加热浓缩,冷却结晶5.某废催化剂含SiO2、ZnS、CuS及少量的Fe3O4。
某实验小组以该废催化剂为原料,回收锌和铜,设计实验流程如图:下列说法正确的是( )A .步骤①操作中,生成的气体可用CuSO 4溶液吸收B .检验滤液1中是否含有Fe 2+,可以选用KSCN 和新制的氯水C .步骤②操作中,应先加6%H 2O 2,然后不断搅拌下缓慢加入1.0mol·L -1H 2SO 4D .滤渣1和滤渣2成分均含有H 2SiO 36.工业上用铝土矿(主要成分为23Al O ,含23Fe O 杂质)为原料冶炼铝的工艺流程如图所示。
专题复习 工业流程题

专题复习工业流程题Studying industrial processes is essential for understanding how various products are manufactured. 了解各种产品是如何制造的,学习工业流程是至关重要的。
From raw materials to finished goods, each step in the process is crucial for ensuring quality and efficiency. 从原材料到成品,每个步骤都是确保质量和效率的关键。
Industrial processes involve a combination of machinery, technology, and human labor to transform raw materials into useful products. 工业流程涉及机械、技术和人力的结合,将原材料转化为有用的产品。
Whether it's the production of electronics, textiles, or automobiles, understanding industrial processes is essential for anyone working in manufacturing. 无论是生产电子产品、纺织品还是汽车,对于在制造业工作的人来说,了解工业流程都是至关重要的。
One of the key aspects of industrial processes is efficiency. 工业流程的关键方面之一是效率。
Companies strive to optimize their production processes to maximize output while minimizing costs. 公司致力于优化他们的生产流程,以最大限度地提高产量的同时最小化成本。
化工流程题必背知识点

化工流程题必背知识点化工流程是指将原料通过一系列的物理、化学或生物反应,转化成所需的产品的过程。
在化工生产中,掌握一些必备的知识点对于理解和掌握化工流程至关重要。
下面我们来看看化工流程题必背的知识点有哪些。
首先,我们需要了解化工流程中的一些基本概念。
比如,原料的选择和处理,反应的类型和条件,产物的提取和纯化等。
在化工流程中,原料的选择和处理非常重要,它直接影响到反应的进行和产物的质量。
而不同类型的反应需要不同的条件,比如温度、压力、催化剂等。
产物的提取和纯化则是保证产品质量的关键步骤。
其次,我们需要掌握一些常见的化工反应类型和条件。
比如,酸碱中和反应、氧化还原反应、加成反应、裂解反应等。
不同类型的反应有不同的特点和条件,我们需要了解它们的基本原理和实际应用。
另外,化工流程中常用的设备和工艺也是我们需要重点掌握的知识点。
比如,反应釜、蒸馏塔、萃取塔、结晶器等。
这些设备和工艺在化工生产中起着至关重要的作用,我们需要了解它们的结构、原理和操作方法。
此外,化工生产中的安全和环保问题也是我们必须要重视的知识点。
化工生产过程中可能会产生一些有害物质,我们需要了解如何安全处理和排放这些物质,以及如何保证生产过程中的安全。
最后,我们还需要了解一些化工产品的应用和市场前景。
化工产品广泛应用于各个领域,比如化肥、医药、日化、材料等。
了解这些产品的应用和市场前景,有助于我们更好地理解化工流程的意义和价值。
综上所述,化工流程题必背的知识点包括基本概念、反应类型和条件、设备和工艺、安全和环保、产品应用和市场前景等。
掌握这些知识点对于理解和掌握化工流程具有重要意义,希望大家能够认真学习和掌握这些知识点,为今后的学习和工作打下坚实的基础。
过程装备基础总结复习资料

过程装备基础总结复习资料过程装备基础总结复习资料过程装备是工业生产中的重要组成部分,它们承担着将原材料转化为成品的任务。
在工程领域中,过程装备的设计、选择和操作都是至关重要的。
本文将对过程装备的基础知识进行总结和复习,帮助读者更好地理解和掌握这一领域的知识。
一、过程装备的定义和分类过程装备是指用于工业生产过程中的各种机械设备和设施。
根据其功能和用途的不同,过程装备可以分为几个主要分类:物料输送装备、物料处理装备、物料储存装备、加工装备和控制装备等。
1. 物料输送装备:主要用于将原材料从一个地方输送到另一个地方,包括输送带、输送管道、搬运设备等。
2. 物料处理装备:用于对原材料进行加工和处理,包括破碎机、筛分机、混合机等。
3. 物料储存装备:用于储存原材料和成品,包括仓储设备、储罐等。
4. 加工装备:用于对原材料进行进一步加工和制造,包括机床、焊接设备、喷涂设备等。
5. 控制装备:用于对生产过程进行监控和控制,包括传感器、仪表和自动化设备等。
二、过程装备的设计和选择过程装备的设计和选择是一个复杂的过程,需要考虑多个因素,如生产需求、工艺要求、经济效益和安全性等。
以下是一些常见的设计和选择原则:1. 生产需求:根据生产过程的需求确定所需的装备种类和规模,包括产能、工艺流程和产品质量等。
2. 工艺要求:根据工艺要求选择适合的装备类型和规格,确保装备能够满足生产过程中的各项要求。
3. 经济效益:综合考虑装备的购买成本、运营成本和维护成本,选择经济效益最佳的装备。
4. 安全性:考虑装备的安全性能,包括操作安全、环境安全和人身安全等,确保装备在使用过程中不会对人员和环境造成危害。
三、过程装备的操作和维护正确的操作和维护对于保证过程装备的正常运行和延长使用寿命至关重要。
以下是一些常见的操作和维护要点:1. 操作要点:- 熟悉装备的使用说明书和操作规程,确保按照规定的操作步骤进行操作。
- 注意装备的安全操作要求,如佩戴个人防护装备、遵守操作规程等。
- 1、下载文档前请自行甄别文档内容的完整性,平台不提供额外的编辑、内容补充、找答案等附加服务。
- 2、"仅部分预览"的文档,不可在线预览部分如存在完整性等问题,可反馈申请退款(可完整预览的文档不适用该条件!)。
- 3、如文档侵犯您的权益,请联系客服反馈,我们会尽快为您处理(人工客服工作时间:9:00-18:30)。
3)前面和后面同时磨损 4)边界磨损
切削钢料时,常在主切削刃靠近工件 外皮处以及刀尖处的后刀面上,磨出较深 的沟纹,这就是边界磨损(图例)。加工 铸、锻等外皮粗糙的工件,也容易发生边 界磨损。 2008-4-28 一般在以中等切削 用量加工塑性金属材料 时会出现这种形式磨损 (图例)。
切削灰铸铁时,刀具前刀面的温 度和刀具后刀面的温度哪个高?
关键问题在于算术平均值——11.974 不在公差带中心——11.9705 。 算术平均值偏大,公差带上限11.984 仅比算术平均值大2σ,而算术平均 值比公差带下限11.957大3.4σ。 忽略工件尺寸小于公差带下限而造成 的废品。废品率约等于2.28%。 改进措施:将算术平均值移至公差带 中心,即把砂轮向前移动Δ,Δ= 0.0035mm。 此时,废品率很小,可 忽略。
3)判断工序能力及其等级
工序能力是指某工序能否稳定地加工出合格产品的能力。
把工件尺寸公差T与分散范围6σ的比值称为该工序的工序能力系数 CP,用以判断生产能力。
CP按下式计算: CP =T/6σ
根据工序能力系数CP的大小,共分为五个等级,如表7-2所示。
工序能力系数CP>1时,公差带T大于尺寸分散范围6σ,具备了工序不产 生废品的必要条件,但不是充分条件。 要不出废品,还必须保证调整的正确性,即 x 与LM要重合。只有当 CP大于1,同时T-2‖x - LM‖大于6σ时,才能确保不出废品。 当CP<1时,尺寸分散范围6σ超出公差带T,此时不论如何调整,必 将产生部分废品。
切削灰铸铁时,刀具后刀面的温度比 刀具前刀面的温度高。因为灰铸铁是 一种脆性材料,加工时常产生崩碎切 屑,不从刀具前刀面流过,而刀具后 刀面则与工件已加工表面之间有摩擦, 故温度较高。
2008-4-28
切削用量同加工生产率的关系
P=1 / tm
Lw d w Lw tm 3 nw a p f 10 va p f
1-刨刀 2-工件 3-工作台 4-床身导轨
图 龙门刨床导轨垂直面 内直线度误差 2008-4-28
为什么对车床床身导轨在水平面的直线 度要求高于垂直面的直线度要求?而对 平面磨床的床身导轨其要求则相反呢?
① 对于车床,车削外圆时:导轨在水平面内的误 差∆y,引起工件在半径上的误差∆R,且∆R=∆y; 导轨在垂直面内的误差∆z,引起工件在半径上的 误差∆R′,且∆R′≈(∆z)2/2 R′; 可见,导轨在水平面的误差对工件加工精度的影 响比在垂直面的误差影响大得多。 ② 对于平面磨床,导轨在水平面内的误差∆y对工 件的加工误差没有影响;而在垂直面内的误差∆z 直接引起工件在厚度上的误差。因此,平面磨床 床身导轨的垂直面直线度要求高于导轨的水平面 直线度要求。
2008-4-28
量度切削变形的方法有几种?
量度方法有两种: 1.变形系数(简单,直观但结果近似, 从塑性压缩方面分析)。 2.剪切角(或剪应变)(复杂,结果 较精确,从剪切变形考虑)。 两种方法都有片面性,不能全面反映 金属切削过程的物理本质。
2008-4-28
刀具磨损和耐用度
一、刀具磨损的形态
2008-4-28
2008-4-28
废品率计算
磨一批d= 120.043 mm销轴,工件尺寸 呈正态分布,工件的平均尺寸X=11.974, 均方根偏差σ=0.005,请分析该工序的 加工质量。如何加以改进。
0.016
XX
XX
1.00
2.00
2.50
3.00
F
2008-4-28
0.3413 0.4772 0.4938 0.4987
2008-4-28
生产实际中多采用查表法确定进给量。
3、切削速度的选定
在ap、f 值选定后,根据合理的刀具耐用度或查表 来选定车削速度。(公式) 在生产中选择切削速度的一般原则是: (1)粗车时, ap、f 较大,故选择较低的v;精车 时, ap 、f 均较小,故选择较高的v。 (2)工件材料强度、硬度高时,应选较低的v。 (3)切削合金钢比切削中碳钢切削速度应降低20%~ 30%;切削调质状态的钢比正火、退火状态钢要 降低20%~ 30%;切削有色金属比切削中碳钢的 2008-4-28 切削速度可提高100%~ 300%;
机床导轨误差的基本形式
•水平面内的直线度 •垂直面内的直线度 •前后导轨的平行度
(扭曲)
现以卧式车床为例,说明导轨误差是怎样影响工件 的加工精度的。
2008-4-28
(1)导轨在水平面内直线度误差的影响 当导轨在水平面内的直线度误差为△y时,引起工件在 半径方向的误差为: △R=△y
由此可见:床身导轨在水平面内如果有直线度误差,使工件 在纵向截面和横向截面内分别产生形状误差和尺寸误差。
式中,dw — 车削前的毛坯直径(mm); Lw — 工件切削部分长度(mm); Δ — 加工余量(mm); nw — 工件转速(r/min)。
2008-4-28
P=A0vfap
(公式)
利用上式,选用一定的切削条件进行计算,可以得到 如下的结果:
(1) f 保持不变,ap增至3ap,如仍保持刀具合理的耐 用度,则vc必须降低15%,此时生产率P3ap≈2.6P,即生 产率提高至2倍。
2008-4-28
机械加工工艺过程及其组成
机械加工工艺过程是指用机械加工方法(主要是切削加工 方法)逐步改变毛坯的形态(形状、尺寸以及表面质量),使 其成为合格零件所进行的全部过程。它一般由工序、工步、走 刀等不同层次的单元所组成。
1. 工 序
一个或一组工人在一个工作地点,对一个或同时对几个 工件所连续完成的那部分工艺过程叫工序。
几种常用的车刀
2008-4-28
卧式车床的典型加工工序
前角、后角——在主剖面内测量; 主偏角、副偏角——在基面内测量; 刃倾角——在切削平面内测量。
2008-4-28
切削变形程度的表示方法
1. 剪切角φ
剪切角φ ↑ →剪切面 积↓→变形程度↓→切削力↓。
剪切面 pφ与切削速度(主运动)方向之间的夹角称为 剪切角,用φ表示
(1)正常磨损
正常磨损是指随着切削时间增加,磨损逐渐扩 大的磨损。
1)前面磨损
2008-4-28
切削塑性材料时, 如果切削速度和切削厚 度较大,在刀具前刀面 上经常会磨出一个月牙 洼(图例)。
刀具的磨ห้องสมุดไป่ตู้形态
2008-4-28
2)后面磨损
加工脆性材料或在切削速度 较低、切削厚度较小(hD< 0.1mm),由于前刀面上刀屑 间的作用相对较弱,主要发生后 刀面磨损(图例)。
(4)刀具材料的切削性能愈好,切削速度也选得愈高。
(5)精加工时,应尽量避开积屑瘤和鳞刺产生的区域。
(6)断续切削及加工大件、细长件和薄壁工件时,应 适当降低切削速度。 (7)在易发生振动的情况下,切削速度应避开自激振 动的临界速度。
2008-4-28
机床导轨误差
机床导轨是机床中确定某些主要部件相对位置的 基准,也是某些主要部件的运动基准。
2008-4-28
φ角与剪切面面积的关系
变形系数ξ的求法
2008-4-28
2. 变形系数ξ
切屑厚度hch与切削层的厚度hD之比称为厚度变形系数,
用ξh 表示,ξh = ach/ac ; 而切削层长度lc与切屑长度lch之比称为长度变形系数, 用ξl表示,ξl=lc/lch 。 根据体积不变原理, 则 ξa =ξl=ξ。 变形系数越大,切屑越厚越短,切削变形越大。
设:△Z=△Y=0.01mm ,R=50mm , 则由于法向原始误差而产生的加工误差 △R= △Y =0.01mm, 由于切向原始误差产生的加工误差
△ R ≈△Z2/d =0.000001mm 此值完全可以忽略不计。由于△Z2数值很小,因此该误差对 工件的尺寸精度和形状精度影响甚小。 2008-4-28
令 z
xx
, 则有:
( z)
1 2
z
0
e
z2 2
dz
Φ(z)为右图中阴影线部分 的面积。对于不同 z值的φ(z), 可由表查出
2008-4-28
2008-4-28
分布曲线与x轴所包围的面积代表了一 批零件的总数。如果尺寸分散范围超出零件 的公差带,则肯定有废品产生,如图所示的 阴影部分。 若尺寸落在Lmin、Lmax范围内,工件的 概率即空白部分的面积就是加工工件的合格 率。
(2)ap保持不变,f 增至3f,如仍保持刀具合理的耐用度, 则vc必须降低32%,此时生产率P3ap≈2P,即生产率提高 至2倍。 由此可见,增大ap比增大f更有利于提高生产率。 (3)切削速度高过一定的临界值时,生产率反而会降低。
2008-4-28
2、选择切削用量的原则
首先选取尽可能大的被吃刀量;其次根据 机床动力和刚性限制条件或加工表面粗糙度的 要求,选取尽可能大的进给量;最后利用切削 用量手册选取或者用公式计算确定切削速度。
2008-4-28
二、被吃刀量、进给量和切削速度的选定
1、被吃刀量的选定
粗加工时,一次走刀尽可能切除全部余量。 半精加工时,被吃刀量取为0.5~2mm。 精加工时,被吃刀量取为0.1~0.4mm
2、进给量的选定
粗加工时,进给量由机床进给机构强度、刀具强度与 刚性、工件的装夹刚度决定。
精加工时,进给量由加工精度和表面粗糙度决定。
ΔR
d
ΔZ
d/2 R
ΔZ
导轨垂直面直线度
垂直平面
2008-4-28
导轨在垂直面内直线度误差
结论:
原始误差引起工件相对于刀具产生相对位移,若 产生在加工表面法向方向(误差敏感方向),对加工 精度有直接影响;产生在加工表面切向方向(误差非 敏感方向) ,可忽略不计。 对平面磨床,龙门刨床 及铣床等,导轨在垂直面内 的直线度误差会引起工件相 对于砂轮(刀具)产生法向 位移,其误差将直接反映到 被加工工件上,造成形状误 差。