数字工厂国内外应用分析
智能制造数字化技术的应用与前景

智能制造数字化技术的应用与前景智能制造是指通过应用先进的数字化技术和物联网技术,实现生产过程的智能化、自动化和高效化。
随着科技的不断发展和创新,智能制造在各个行业中得到了广泛应用。
本文将探讨智能制造数字化技术的应用情况,并展望其未来的前景。
一、智能制造数字化技术的应用1. 智能工厂智能工厂是智能制造的重要组成部分,它通过数字化技术将生产设备和工艺流程进行集成和优化,实现生产过程的自动控制和管理。
智能工厂能够提高生产效率,降低成本,并且提供更高质量的产品。
2. 人工智能人工智能在智能制造中发挥了重要作用。
通过机器学习和深度学习等技术,智能制造可以实现对生产数据和设备状态进行实时分析和预测,从而提前预知可能发生的问题,并采取相应的优化措施。
人工智能还可以实现智能化的产品设计和制造过程,提高产品质量和创新能力。
3. 物联网技术物联网技术是智能制造的基础,通过传感器和无线通信技术,将生产设备和产品连接成一个巨大的网络,实现信息的实时采集和传输。
物联网技术能够帮助企业实现对生产过程的全面监控和调度,以及对产品的追踪和管理。
4. 3D打印技术3D打印技术是一项革命性的数字化技术,它可以通过将数字模型转化为实体产品,实现个性化的定制生产。
3D打印技术可以大大缩短产品的生产周期和成本,并提供更多的创新可能性。
5. 虚拟现实技术虚拟现实技术可以模拟真实环境,通过虚拟现实头盔等设备,使用户可以身临其境地体验和操作数字化的生产设备和工厂。
虚拟现实技术可以帮助企业进行生产线的优化和故障诊断,提高生产效率和安全性。
二、智能制造数字化技术的前景1. 提高生产效率智能制造数字化技术的应用可以大大提高生产效率。
通过实时监控和数据分析,生产过程可以更加精确和高效地进行管理和调度,减少资源浪费和产能闲置,从而提高生产效率。
2. 降低生产成本智能制造数字化技术的应用可以有效地降低生产成本。
通过自动化和智能化的生产过程,可以减少人力成本和能源消耗,并优化供应链和物流管理,降低原材料的浪费和损耗,从而降低企业的生产成本。
数字工厂的应用

数字工厂的应用随着科技的不断进步,数字工厂成为了现代工业生产中的重要组成部分。
数字工厂利用先进的信息技术和智能化设备,实现了工厂生产过程的数字化、自动化和智能化,极大地提高了生产效率和质量。
本文将从数字工厂的定义、应用领域、优势以及未来发展趋势等方面进行探讨。
1. 数字工厂的定义数字工厂是指利用数字化技术,将传统工厂的生产过程转化为数字化的表达和管理,实现生产过程的可视化、智能化和自动化。
数字工厂通过采集、处理和分析生产过程中的各种数据,实现对生产过程的全面监控和精细管理,从而提高生产效率、降低成本、提升产品质量。
2. 数字工厂的应用领域数字工厂的应用领域非常广泛,涵盖了制造业的各个环节。
首先,在产品设计阶段,数字工厂可以通过虚拟样机技术,实现产品设计的可视化和优化,大大加快了产品开发的速度。
其次,在生产制造阶段,数字工厂可以实现生产过程的自动化和智能化,提高生产效率和生产质量。
再次,在供应链管理阶段,数字工厂可以实现对供应链的全程可视化和智能化管理,提高供应链的灵活性和响应速度。
最后,在售后服务阶段,数字工厂可以通过远程监控和预测维护技术,提供更加及时和精准的售后服务。
3. 数字工厂的优势数字工厂相比传统工厂具有许多优势。
首先,数字工厂可以实现生产过程的自动化和智能化,减少人力投入,提高生产效率。
其次,数字工厂可以实现生产过程的全面监控和精细管理,减少生产中的错误和浪费,提高产品质量。
再次,数字工厂可以实现生产过程的可视化和模拟仿真,减少生产试错成本,提高产品研发的效率。
最后,数字工厂可以实现供应链的全程可视化和智能化管理,提高供应链的灵活性和响应速度。
4. 数字工厂的未来发展趋势数字工厂在未来的发展中将继续呈现以下趋势。
首先,数字工厂将更加注重数据的采集和分析,通过大数据和人工智能技术,实现对生产过程的实时监控和预测分析,进一步提高生产效率和质量。
其次,数字工厂将更加注重与物联网技术的结合,实现设备之间的互联互通,实现智能制造和智能管理。
先进制造技术论文(数字化工厂)

先进制造技术论文(数字化工厂)数字化工厂发展现状及趋势摘要:目前,将数字与智能制造作为关键技术应用到数字化工厂,是现代工业化与信息化融合的应用体现,也是实现智能化制造的必经之路。
打造数字化工厂,是当前工业企业变革、突破的重要手段。
本文对数字化工厂发展现状及趋势进行了初步的研究,通过具体实例,分析了数字化工厂的特点,应用现状并展望了数字化工厂的发展趋势及其决定性意义。
发展数字化工厂对制造企业提升生产力,实现生产智能化和有效管理,推广数字化工厂的建设和发展,搭建智能制造技术和数字化工厂相结合的交流平台,为我国传统产业转型升级、工业与信息化深度融合的战略发展要求,都有着关键性的意义。
关键词:数字化工厂;虚拟仿真;数字制造;智能管理;产业转型升级一、引言现代工业经历了机械化、电气化革命,未来的第三次工业革命必然以机、电、信息相结合的智能化制造革命。
《经济学人》2012年4月发表的《第三次工业革命:制造业与创新》专题报告中阐述了目前由技术创新引发的制造业深刻变化,其中,数字化与智能化的制造技术是“第三次工业革命的核心技术”。
作为数字化与智能化制造的关键技术之一,数字化工厂是现代工业化与信息化融合的应用体现,也是实现智能化制造的必经之路。
数字化工厂借助于信息化和数字化技术,通过集成、仿真、分析、控制等手段,可为制造工厂的生产全过程提供全面管控的一种整体解决方案。
早在2000 年前后,上汽、海尔、华为和成飞等制造企业均已开始着手建立自己的数字化工厂。
今年来,随着国际竞争的不断加剧和我国制造业劳动力成本的不断上升,对设备效率、制造成本、产品质量等环节的要求不断提高,离散制造业中以汽车、工程机械、航空航天、造船为代表的大型企业已越来越重视数字化工厂的建设。
二、数字化工厂的研究热点根据在范围、阶段、视角上的关注点存在差异,对于数字化工厂也有不同提法,比如可视化工厂(Visual Factory)、智慧工厂(Smart Factory)、智能工厂图1典型数字化工厂提法的主要业务范围(Intelligence Factory)、数字化制造(Digital Manufacturing)、虚拟工厂(Virtual Factory)等。
国家数字化转型的战略规划与应用分析

国家数字化转型的战略规划与应用分析近年来,数字化转型已成为各国争相探讨和实践的重要议题,而在国家层面,数字化转型已逐渐成为一项重要的计划。
国家数字化转型计划旨在推动数字技术的广泛应用和数字经济的发展,促进国家经济实力和国际竞争力的提升。
一、国家数字化转型的意义数字化转型已经成为经济、社会、政治和文化发展中不可缺少的一项策略。
通过数字技术的运用,国家可将经济、政治、文化和社会发展的各个领域快速推向前所未有的发展高峰。
数字化转型推动了国家生产方式的升级换代,推动了数字化时代下新兴产业的蓬勃发展,同时也提高了国家公共服务的效率。
数字化转型远远不止于固定的硬件或软件。
它是一种全方位、全面的变革。
数字化转型的成功实现不仅仅意味着政府机构、企业和个人之间的数字化互通和互动,更是国家各个维度间的数字化整合,实现经济、政治、文化和社会发展的全方位、全面贯通。
二、国家数字化转型战略规划的重要性国家数字化转型战略规划是数字化转型的指南。
它作为国家发展的框架,不仅要对全社会的数字化排列进行重新整合,而且要固定将社会的发展纳入国家的数字化路线图之中。
只有适应数字化转型趋势,才能更好地保持国家经济、社会和政治的稳定发展。
要推进数字化转型,一个国家必须拥有清晰的战略和规划,该计划必须加强数字技术的应用,推动产业升级、促进经济社会创新发展,加强市场监管,强化数字安全保障等关键领域的管控能力。
三、数字化转型的应用分析数字化转型的应用涉及都社会的方方面面。
在工业领域,数字化转型已实现了从传统制造模式向数字化生产模式的转变。
通过工业物联网的技术支持,工厂可以实现数字化制造,实时数据监控、分析和处理,以及系统协同工作。
在教育领域,数字化转型促使政府、教育机构开展更加个性化、多元化的教育服务。
新兴技术如AI、智慧城市建设、虚拟现实等技术的推广和普及将有助于实现个性定制的学习体验,确保学生们能够获得与之匹配的技能和知识。
在医疗领域,数字化转型赋予了医疗行业人员更加高效地管理和利用数据的能力。
数字制造技术在工厂生产中的应用

数字制造技术在工厂生产中的应用现代工业生产已经走过了一个漫长的历程,随着科技的进步和数据技术的兴起,数字制造技术成为了未来工厂生产的重要趋势。
数字制造技术是工业信息化与数字化的核心内容和关键技术,具有很高的推广应用价值。
本文将从数字制造技术的概念、特点及其在工厂生产中的具体应用角度探讨数字制造技术在工厂生产中的应用。
数字制造技术是什么?在数字时代,数字制造技术便于理解,从字面上看,数字制造是指一个工厂从设计到生产再到管理,全程基于数字技术、数字数据来实现智能化和自动化的制造技术。
数字制造的主要思想是“数字化、模拟化、智能化和网络化”。
数字化是把实体生产过程转成数字的过程,并且利用这些数据进行分析和优化,优化而成的数字模型能深入到工厂每一个部件,支持对生产过程进行精细分析和优化;模拟化是把实际的生产过程用数字化的方法模拟出来,并对生产过程进行优化和测试,提前发现潜在问题,以减少生产的错误率;智能化是利用各种数字化技术和算法,让设备设施能智能化控制,产品质量能全程自动检测,生产过程能够实现自适应调控,从而为工厂提供全新的生产方式;网络化是指把生产各模块进行互联,并建立起有机的信息流动机制,实现生产过程的数字化协同,方便监管和管理。
数字制造技术的特点数字制造技术的特点就在于其实现了数字化、智能化、网络化、可持续和灵活的生产方式,具有以下几个特点:1.生产智能化:数字化、模拟化和智能化相结合的生产方式,能够实现自动化生产,提高生产效率和价格竞争力。
2.设备自动化运维:设备自动化运维可以在生产过程中进行预测性维护,减少停机时间,减少生产成本,提高生产效率。
3.生产过程协同:产品从 R&D,制造,生产、运营到维护的整个生命周期的全过程协同;4.数据智能化:数据智能化能够实现生产过程实时大数据监控和预判,有效降低生产风险。
5.环境友好:数字制造技术生产过程所造成的环境污染少、物料利用率高,从根本上做到了低碳、环保、可持续发展。
智能工厂市场分析

智能工厂市场分析随着科技的不断进步和应用,智能工厂作为工业领域的新兴概念,正迅速发展并引起了全球范围内的关注。
智能工厂利用先进的技术和自动化系统,通过数字化、网络化和智能化的方式,实现生产过程的智能化管理和运营控制。
本文旨在对智能工厂市场进行全面分析,并探讨其未来发展前景。
一、市场规模与发展趋势当前,全球范围内智能工厂市场规模呈现快速增长的趋势。
一方面,制造业转型升级的需求推动了智能工厂市场的不断扩大;另一方面,先进的技术和设备的不断发展,使得智能工厂的建设成本逐渐降低。
根据市场研究机构的数据显示,预计到2025年,全球智能工厂市场规模将达到5000亿美元。
未来智能工厂市场发展的主要趋势有以下几点:1. 自动化水平提升:智能工厂将进一步实现全面自动化,工业机器人和自动化设备将广泛应用于生产线上,提高生产效率和质量。
2. 数据驱动决策:智能工厂通过大数据分析和人工智能技术,实时收集、监控和分析生产数据,为企业提供智能化的决策支持,帮助企业优化生产过程和管理效率。
3. 灵活生产模式:智能工厂采用模块化设计,能够快速调整生产线,适应客户需求的个性化生产,实现产能的高效利用和灵活生产。
4. 人机协同合作:智能工厂通过人机协同合作,将工人与智能设备紧密结合,提高工作效率和生产安全,同时减轻工人的劳动强度。
二、市场竞争格局与主要企业智能工厂市场竞争激烈,国内外众多知名企业积极投入其中,形成了一定的市场竞争格局。
以下是一些主要的智能工厂企业:1. 西门子(Siemens)作为全球领先的工业自动化解决方案提供商之一,西门子在智能工厂领域拥有雄厚的技术和经验优势。
其产品和解决方案广泛应用于机械制造、汽车工业和电子工业等领域。
2. ABBABB是一家全球知名的电力和自动化技术公司,在智能工厂市场中具有较高的市场份额。
该公司的智能工厂解决方案涵盖了生产过程控制、电气设备和自动化设备等多个方面。
3. 三菱电机(Mitsubishi Electric)作为日本领先的电气设备制造商,三菱电机在智能工厂领域拥有广泛的应用和市场份额。
简述数字工厂的概念及典型应用

简述数字工厂的概念及典型应用数字工厂是指利用数字技术和智能化手段,将传统工厂的生产过程进行数字化和智能化改造的一种生产模式。
通过数字工厂的建设,企业可以实现生产过程的数字化管理、数据的实时监控和分析,从而提高生产效率、降低成本,提升产品质量和竞争力。
数字工厂的典型应用可以包括以下几个方面:1. 设备连接和监控:通过数字工厂,可以实现生产设备的连接与监控。
传感器和物联网技术可以将设备所产生的数据实时传输至数字工厂平台,实现对设备状态的监控和远程控制。
这样可以提前发现设备故障,并进行预防性维护,减少设备故障停机时间,提高设备利用率。
2. 数据分析和优化:数字工厂可以对生产过程中产生的大量数据进行采集、分析和优化。
通过对生产数据的深度挖掘和分析,可以发现潜在的优化点,提高产线的稳定性、效率和质量。
通过分析生产设备的数据,可以调整生产参数,优化生产效率和质量。
3. 虚拟仿真与优化:数字工厂可以通过虚拟仿真技术对生产过程进行模拟和优化。
借助数字双胞胎技术,可以将实际生产线与虚拟仿真模型进行对比,分析并优化生产过程中的瓶颈与问题,提高生产线的运行效率和产能。
4. 智能调度与协同:数字工厂可以实现生产过程的智能调度和协同。
通过整合供应链、生产计划和库存管理等各环节的数据,实现生产过程的协同与优化。
从而减少生产中的浪费,提高生产资源的利用率,降低企业的运营成本。
5. 智能质量控制:数字工厂可以结合视觉识别、传感器和机器学习等技术,实现对产品质量的智能检测和控制。
通过对产品质量数据的分析和反馈,可以及时调整生产参数,确保产品质量的稳定。
总结起来,数字工厂通过数字化、智能化和数据化的手段,实现整个生产过程的优化和协同。
它的典型应用包括设备连接和监控、数据分析和优化、虚拟仿真与优化、智能调度与协同以及智能质量控制等方面。
数字工厂的建设可以提高生产效率、降低成本、提升产品质量和竞争力,对于企业的可持续发展具有重要意义。
制造业数字化工厂智能制造解决方案
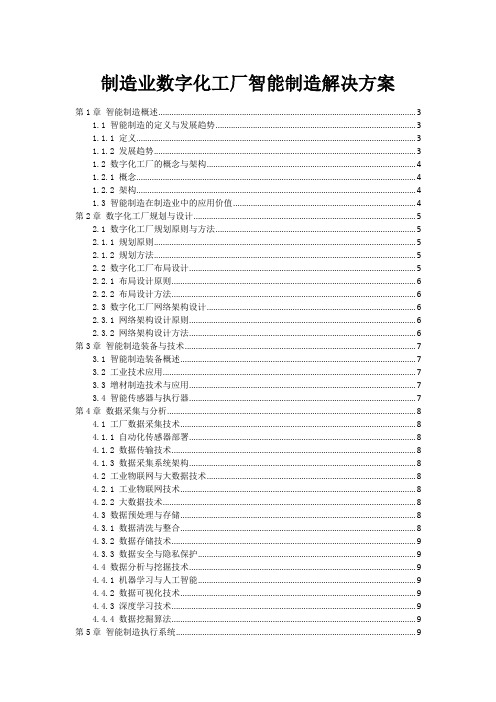
制造业数字化工厂智能制造解决方案第1章智能制造概述 (3)1.1 智能制造的定义与发展趋势 (3)1.1.1 定义 (3)1.1.2 发展趋势 (3)1.2 数字化工厂的概念与架构 (4)1.2.1 概念 (4)1.2.2 架构 (4)1.3 智能制造在制造业中的应用价值 (4)第2章数字化工厂规划与设计 (5)2.1 数字化工厂规划原则与方法 (5)2.1.1 规划原则 (5)2.1.2 规划方法 (5)2.2 数字化工厂布局设计 (5)2.2.1 布局设计原则 (6)2.2.2 布局设计方法 (6)2.3 数字化工厂网络架构设计 (6)2.3.1 网络架构设计原则 (6)2.3.2 网络架构设计方法 (6)第3章智能制造装备与技术 (7)3.1 智能制造装备概述 (7)3.2 工业技术应用 (7)3.3 增材制造技术与应用 (7)3.4 智能传感器与执行器 (7)第4章数据采集与分析 (8)4.1 工厂数据采集技术 (8)4.1.1 自动化传感器部署 (8)4.1.2 数据传输技术 (8)4.1.3 数据采集系统架构 (8)4.2 工业物联网与大数据技术 (8)4.2.1 工业物联网技术 (8)4.2.2 大数据技术 (8)4.3 数据预处理与存储 (8)4.3.1 数据清洗与整合 (8)4.3.2 数据存储技术 (9)4.3.3 数据安全与隐私保护 (9)4.4 数据分析与挖掘技术 (9)4.4.1 机器学习与人工智能 (9)4.4.2 数据可视化技术 (9)4.4.3 深度学习技术 (9)4.4.4 数据挖掘算法 (9)第5章智能制造执行系统 (9)5.2 生产调度与优化 (9)5.2.1 生产计划制定与调整 (10)5.2.2 资源分配与任务指派 (10)5.2.3 调度算法研究与应用 (10)5.2.4 生产过程监控与实时调整 (10)5.3 生产线自动化控制 (10)5.3.1 生产线自动化设备选型与布局 (10)5.3.2 控制系统设计与实现 (10)5.3.3 传感器与执行器应用 (10)5.3.4 设备间通信与协同控制 (10)5.4 智能质量管理与设备维护 (10)5.4.1 质量管理体系构建与实施 (10)5.4.2 在线检测与实时质量控制 (10)5.4.3 设备故障预测与健康监测 (10)5.4.4 维护策略制定与执行 (10)第6章数字化工厂仿真与优化 (10)6.1 数字化工厂仿真技术 (10)6.1.1 数字化工厂仿真原理 (10)6.1.2 数字化工厂仿真关键技术 (11)6.1.3 数字化工厂仿真应用 (11)6.2 生产过程优化与调度 (11)6.2.1 生产过程优化方法 (11)6.2.2 生产过程调度方法 (11)6.2.3 生产过程优化与调度应用 (12)6.3 设备功能分析与优化 (12)6.3.1 设备功能分析方法 (12)6.3.2 设备功能优化方法 (12)6.3.3 设备功能分析与优化应用 (12)6.4 能耗管理与优化 (12)6.4.1 能耗分析方法 (13)6.4.2 能耗优化方法 (13)6.4.3 能耗管理与优化应用 (13)第7章智能仓储与物流系统 (13)7.1 智能仓储系统设计 (13)7.1.1 设计原则与目标 (13)7.1.2 系统构成要素 (13)7.2 自动化物流设备与技术 (13)7.2.1 自动化物流设备 (14)7.2.2 相关技术 (14)7.3 仓储物流信息系统 (14)7.3.1 系统功能 (14)7.3.2 系统架构 (14)7.3.3 关键技术 (14)7.4.1 供应链协同管理概述 (15)7.4.2 智能仓储与物流在供应链协同管理中的应用 (15)第8章智能制造与工业互联网 (15)8.1 工业互联网平台概述 (15)8.2 设备联网与数据集成 (15)8.2.1 设备联网技术 (15)8.2.2 数据集成方法 (15)8.3 工业APP与微服务架构 (15)8.3.1 工业APP开发 (16)8.3.2 微服务架构 (16)8.4 工业互联网安全体系 (16)8.4.1 安全体系架构 (16)8.4.2 安全技术 (16)8.4.3 安全管理 (16)第9章智能制造人才培养与技能提升 (16)9.1 智能制造人才培养策略 (16)9.2 数字化工厂技能培训体系 (17)9.3 跨界融合与创新 (17)9.4 企业大学与产业学院 (17)第10章案例分析与未来发展 (18)10.1 国内外智能制造案例分析 (18)10.2 智能制造发展趋势与挑战 (18)10.3 我国智能制造政策与产业布局 (18)10.4 未来制造业发展展望 (18)第1章智能制造概述1.1 智能制造的定义与发展趋势1.1.1 定义智能制造是指通过集成先进的信息技术、自动化技术、网络通信技术、人工智能等手段,对制造过程进行智能化改造,实现制造系统的高效、灵活、绿色、个性化生产。
数字化智能制造技术在工业生产中的应用分析
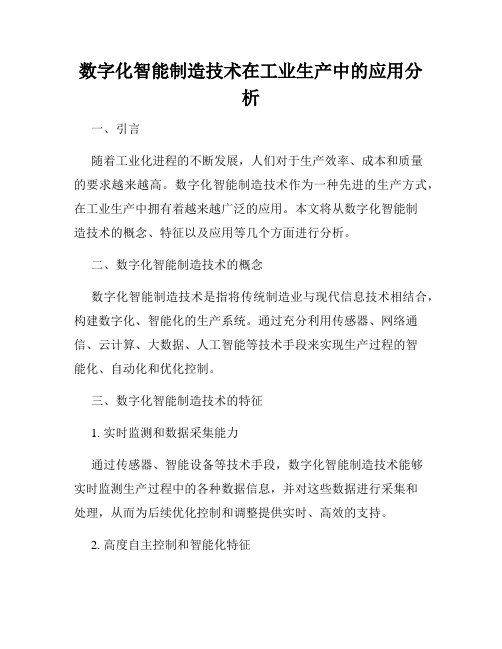
数字化智能制造技术在工业生产中的应用分析一、引言随着工业化进程的不断发展,人们对于生产效率、成本和质量的要求越来越高。
数字化智能制造技术作为一种先进的生产方式,在工业生产中拥有着越来越广泛的应用。
本文将从数字化智能制造技术的概念、特征以及应用等几个方面进行分析。
二、数字化智能制造技术的概念数字化智能制造技术是指将传统制造业与现代信息技术相结合,构建数字化、智能化的生产系统。
通过充分利用传感器、网络通信、云计算、大数据、人工智能等技术手段来实现生产过程的智能化、自动化和优化控制。
三、数字化智能制造技术的特征1. 实时监测和数据采集能力通过传感器、智能设备等技术手段,数字化智能制造技术能够实时监测生产过程中的各种数据信息,并对这些数据进行采集和处理,从而为后续优化控制和调整提供实时、高效的支持。
2. 高度自主控制和智能化特征数字化智能制造技术基于人工智能和自动化技术,通过大数据分析、机器学习和模型优化等手段,实现了自主控制和智能化,使生产系统更加高效、稳定和可靠。
3. 模块化和可定制化特征数字化智能制造技术采用模块化的设计理念,生产系统中的各个模块可以自由组合和调整,以适应不同的生产需求和生产环境。
同时,数字化智能制造技术支持定制化生产,满足用户特定的生产要求和个性化需求。
4. 网络化和跨平台特征数字化智能制造技术构建了一个网络化的生产系统,不同机器、设备和工厂之间可以进行数据共享和协作,实现整个生产过程的自动化。
同时,数字化智能制造技术支持跨平台的应用,可以在不同的设备和终端上进行操作和控制。
四、数字化智能制造技术在工业生产中的应用1. 生产线自动化数字化智能制造技术可以对生产过程中的各个环节进行实时监测和自动控制,实现生产线的自动化和智能化。
该技术可以有效提高生产效率和产品质量,同时降低人力和资源成本。
2. 工厂整体优化数字化智能制造技术可以实现对整个工厂生产过程的数据采集和分析,通过大数据的分析和处理,找到生产过程中的瓶颈和障碍,从而实现整体的生产优化。
数字化制造技术的应用案例

数字化制造技术的应用案例数字化制造技术应用案例数字化制造技术,简称为DPM,是一种以数字化技术为基础,集成物联网、云计算、大数据等技术,为制造业的生产管理、制造流程、产品设计及制造测试等提供数字化支持的一种新型制造技术。
数字化制造技术的应用案例现已遍及世界各地。
本文就介绍以下几个国内外典型的数字化制造技术应用案例,以便更好地理解数字化制造技术在实际应用中的应用优势。
一、沃尔沃重型卡车公司数字化制造改造沃尔沃重型卡车公司是一家生产重型卡车、轮胎、汽车部件和发动机的国际化公司。
2015年,它启动了数字化制造改造计划,利用数字化技术来优化制造流程和提高生产效率。
在此计划中,公司利用数字化模拟技术为新产品设计提供更快速、更准确的制造流程和测试方法,从而缩短研发周期、提高产能;利用物联网和云计算技术,建立了多种生产数据的实时监控和控制系统,以更好地调整各生产环节的生产计划和资源分配,从而提高生产效率和质量控制;在生产流程中加入了机器人操作、3D打印技术等数字化生产装备,为生产流程提供柔性化支持,实现了智能、自动化、数字化制造。
二、国内汽车生产厂商数字化制造应用案例在汽车生产方面,国内一些大型汽车生产厂商也开始逐步实施数字化制造技术。
比如,广汽乘用车公司在其新厂区的生产车间中应用数字化制造技术,建立了智能化生产流程和现代化生产资源分配系统。
通过建立生产车间的数字化模型,实现了生产现场的虚拟化,提高了生产资源的利用率和生产效率,节约了生产成本。
同样,上汽通用汽车也在其全球首个数字化工厂-上汽雪佛兰数字工厂中全面应用数字化制造技术。
在这个数字化工厂中,上汽通用汽车利用物联网和大数据分析技术,实现了生产流程的全程跟踪、在线大数据分析和数据共享平台,提高了生产效率和质量控制效果。
三、数字化制造技术在机床行业的应用案例除了在汽车行业中,数字化制造技术在机床行业也存在着广泛的应用。
以京东方科技集团为例,该公司在其数控机床生产基地中广泛应用了数字化制造技术,从生产计划和管理、设备制造和装配、设备维护和保养等方面实现了数字化技术的全面应用。
先进制造技术在企业中的应用分析
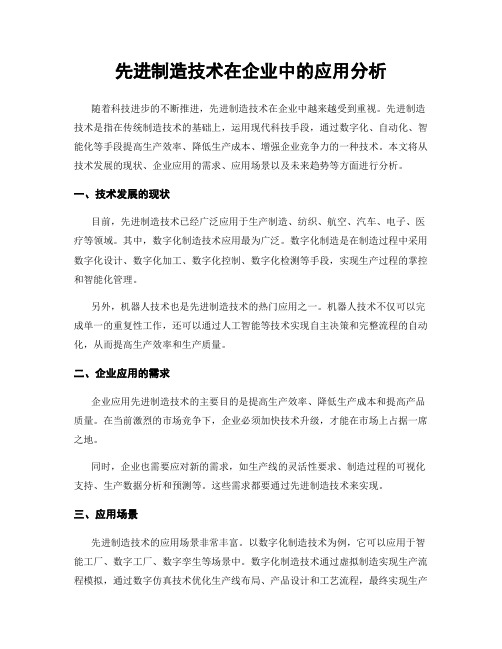
先进制造技术在企业中的应用分析随着科技进步的不断推进,先进制造技术在企业中越来越受到重视。
先进制造技术是指在传统制造技术的基础上,运用现代科技手段,通过数字化、自动化、智能化等手段提高生产效率、降低生产成本、增强企业竞争力的一种技术。
本文将从技术发展的现状、企业应用的需求、应用场景以及未来趋势等方面进行分析。
一、技术发展的现状目前,先进制造技术已经广泛应用于生产制造、纺织、航空、汽车、电子、医疗等领域。
其中,数字化制造技术应用最为广泛。
数字化制造是在制造过程中采用数字化设计、数字化加工、数字化控制、数字化检测等手段,实现生产过程的掌控和智能化管理。
另外,机器人技术也是先进制造技术的热门应用之一。
机器人技术不仅可以完成单一的重复性工作,还可以通过人工智能等技术实现自主决策和完整流程的自动化,从而提高生产效率和生产质量。
二、企业应用的需求企业应用先进制造技术的主要目的是提高生产效率、降低生产成本和提高产品质量。
在当前激烈的市场竞争下,企业必须加快技术升级,才能在市场上占据一席之地。
同时,企业也需要应对新的需求,如生产线的灵活性要求、制造过程的可视化支持、生产数据分析和预测等。
这些需求都要通过先进制造技术来实现。
三、应用场景先进制造技术的应用场景非常丰富。
以数字化制造技术为例,它可以应用于智能工厂、数字工厂、数字孪生等场景中。
数字化制造技术通过虚拟制造实现生产流程模拟,通过数字仿真技术优化生产线布局、产品设计和工艺流程,最终实现生产自动化、智能化和可视化控制。
数字孪生则是通过数字采集、传感器网络、真实生产环境的数据模拟等手段建立虚拟化管理模型,实现生产过程掌握和优化。
机器人技术的应用场景也广泛。
它可以应用于工厂生产、仓储物流、航空维修等领域。
通过机器人技术实现生产过程中的重复性工作自动化,使生产线更加高效。
在物流方面,机器人技术可以代替人工完成物料搬运、储存等任务,提高物流效率。
四、未来趋势先进制造技术的发展趋势是数字化、自动化、智能化、协同化。
2021国内外本地化技术研究现状与技术应用范文2
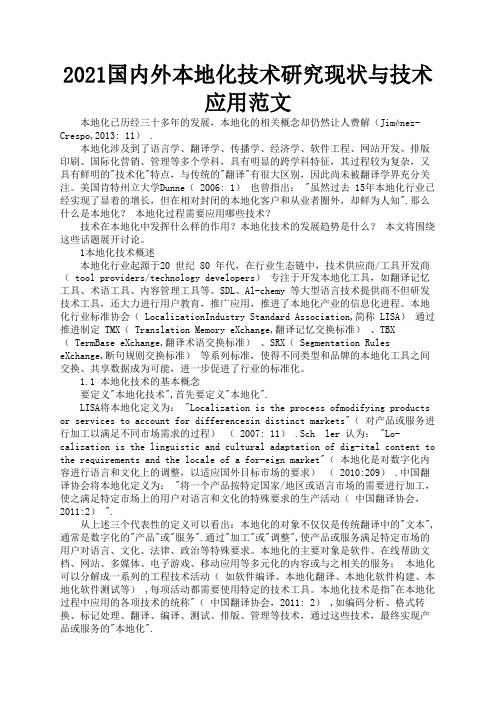
Austermühl( 2006) 在 Training translatorto localize 一文中提出应该在传统 的翻译教学中整合本地化教学,他的模型包括四个层次: 本地化概况、软件和网站翻 译、技术工具、理论。Kosaka &Itagaki( 2003 ) 在 Building a curriculum for Japaneselocalization translators 一文中描述了作者在美国蒙特雷国际研究学院教 授的本地化课程的内容,包括技术写作、软件本地化和网站本地化三门课程。Koby& Brian( 2003) 在 Task-based instruction and the newtechnology: training translators for the modern lan-guage industry 一文中提出在真实的翻译项目中 进行翻译技术工具的教学。也有学者对技术工具和本地化进行了深入的纯理论思考, Michael Cronin( 2013)在 Translation in the Digital Age 中讨论了数字技术对 于翻译实践及本地化实践的深刻影响。AnthonyPym 在 The Moving Text: localization,translation anddistribution ( 2004 ) 和 Exploring Translation Theories( 2010) 两部着作中以本地化产业为背景,探讨了信息技术 条件下"Text"的嬗变,以及由此对翻译理论体系造成的冲击,进而提出了 "Localization as a para-digm"这一命题( 刘明,2013: 150) . 国内的本地化技术研究也可按研究主体划分为从业者实践总结和学界研究。《软 件本地化---本地化行业透视与实务指南》(王华伟、崔启亮,2005) 、《翻译与本 地化工程技术实践》( 崔启亮、胡一鸣,2011) 、《本地化与翻译导论》( 杨颖 波、王华伟、崔启亮,2011) 、《翻译项目管理实务》( 王华伟、王华树,2013) 等着作中都有大量的篇幅用于总结技术操作流程。苗菊、朱琳( 2009) 、王传英 ( 2011) 、崔启亮( 2012) 、冷冰冰( 2012) 主要从课程体系角度探讨了本地 化译者培养,李广荣( 2012) 论述了国内外本地化翻译学术话语的构建。国内翻译 学界对于本地化技术尚未进行深入研究。 3本地化的业务流程 Esselink(2000: 17-18) 在 A Practical Guide to Lo-calization 中概括了 本地化项目的典型流程: 售前阶段、启动会议、源资料分析、制定计划和预算、术语 准备、源资料准备、软件翻译、在线帮助和文档翻译、软件工程处理和测试、屏幕截 图、帮助文档工程处理和文档排版、工程处理更新、产品质量保证和提交、项目结束 等 14 个环节。仅软件本地化流程,就可以分为: 评估与准备、抽取资源文件、标识 资源文件、检查资源文件、调整用户界面尺寸、编译本地化软件、修正软件缺陷等 7 个环节( 杨颖波等,2011: 27) .若将本地化流程简化,基本上包括项目准备、翻 译、工程处理、本地化排版、质量保证和测试等环 节( Schaefer & Koh,2010: 19) .Schler ( 2011: 209-214) 将其简化为分析、准备、翻译、工程处理和测 试、审阅等环节。相对于传统翻译项目来说,本地化项目的流程相对复杂,是多种活 动的集合和优化。 按照现代项目管理的理念,本地化流程可以分为启动阶段、计划阶段、执行阶 段、监控阶段和收尾阶段,每个阶段又可分为不同的环节和若干任务。本地化项目千 变万化,却遵循普遍的流程。图2 是本地化项目一般的运作流程,从源语文档到输出 本地化后的产品,这个过程涵盖了十多个环节,同时又涉及到项目部、翻译部、工程 技术部、排版部、测试部等多个部门之间的协作。 当前,本地化行业处于蓬勃发展时期,新型本地化内容层出不穷,本地化企业面 临更加激烈的竞争和更加多变的外部环境,技术创新和流程优化成为本地化企业获取 竞争优势的重要战略途径。本地化技术的创新推动本地化流程不断优化,诸如SAP、 DELL、IBM 等语言服务大客户已经部署全球化管理系统,将本地化业务管理、定制化
离散制造业数字工厂模型构建与应用研究
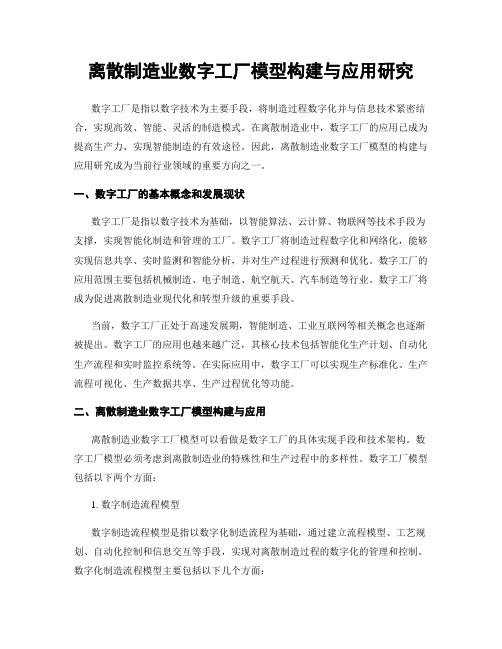
离散制造业数字工厂模型构建与应用研究数字工厂是指以数字技术为主要手段,将制造过程数字化并与信息技术紧密结合,实现高效、智能、灵活的制造模式。
在离散制造业中,数字工厂的应用已成为提高生产力、实现智能制造的有效途径。
因此,离散制造业数字工厂模型的构建与应用研究成为当前行业领域的重要方向之一。
一、数字工厂的基本概念和发展现状数字工厂是指以数字技术为基础,以智能算法、云计算、物联网等技术手段为支撑,实现智能化制造和管理的工厂。
数字工厂将制造过程数字化和网络化,能够实现信息共享、实时监测和智能分析,并对生产过程进行预测和优化。
数字工厂的应用范围主要包括机械制造、电子制造、航空航天、汽车制造等行业。
数字工厂将成为促进离散制造业现代化和转型升级的重要手段。
当前,数字工厂正处于高速发展期,智能制造、工业互联网等相关概念也逐渐被提出。
数字工厂的应用也越来越广泛,其核心技术包括智能化生产计划、自动化生产流程和实时监控系统等。
在实际应用中,数字工厂可以实现生产标准化、生产流程可视化、生产数据共享、生产过程优化等功能。
二、离散制造业数字工厂模型构建与应用离散制造业数字工厂模型可以看做是数字工厂的具体实现手段和技术架构。
数字工厂模型必须考虑到离散制造业的特殊性和生产过程中的多样性。
数字工厂模型包括以下两个方面:1. 数字制造流程模型数字制造流程模型是指以数字化制造流程为基础,通过建立流程模型、工艺规划、自动化控制和信息交互等手段,实现对离散制造过程的数字化的管理和控制。
数字化制造流程模型主要包括以下几个方面:(1)数字化工艺规划:通过对部件进行三维建模和模拟,建立数字化的生产工艺规划,对生产过程进行模拟和验证。
(2)数字化生产过程控制:通过将受控品质、生产数据、尺寸测量等数据点实时更新到系统中,实现生产过程的实时监测和控制。
(3)数字化生产资源管理:通过对机器人、生产设备、生产工具等进行数字化管理,实现生产过程中资源的自动配置和优化。
数字化制造技术的发展及应用

第6期机电技术169浅谈数字化制造技术的发展及应用*钟明灯 张颜艳(闽南理工学院,福建石狮 362700)摘 要:数字化制造技术作为一项专业技术,与传统的制造业有很大的不同,能极大地提升企业的创新能力。
文中从数字化制造技术的定义出发,分析了数字化制造技术国内外的研究现状,阐明了数字化制造技术的关键技术和核心技术,最后对数字化制造技术应用进行实例展示。
关键词:数字化制造技术;关键技术;核心技术;应用实例中图分类号:TH164 文献标识码:A 文章编号:1672-4801(2012)06-169-03数字化时代来临的标志是信息技术的越来越普及,现在信息技术应用于我们生活的方方面面,特别是在智能领域的应用越来越多。
数字化技术是软件和智能技术的基础,是高科技公司赖以生存的核心技术。
先进制造技术的应用,拓展了许多制造的新方法和新工艺。
数字化技术和先进制造技术的结合,给中国的制造业带来巨大的冲击,前景无限光明。
本文从数字化制造技术的定义出发,分析了数字化制造技术国内外的研究现状。
1 数字化制造技术的定义相对于传统的制造业,有人会把它和先进制造业相混淆,认为数字化制造就是NC(数控)或CNC(计算机数控),更有甚者,有人会说数字化制造就是CAD(计算机辅助设计)/CAM(计算机辅助制造)的集成、FMS(柔性化制造系统)、CIMS(计算机集成制造系统)等等。
数字化制造的术语性定义:数字化制造就是指在虚拟现实、计算机网络、快速原型、数据库和多媒体等支撑技术的支持下,根据用户的需求,迅速收集资源信息,对产品信息、工艺信息和资源信息进行分析、规划和重组, 实现对产品设计和功能的仿真以及原型制造,进而快速生产出达到用户要求性能的产品整个制造全过程[1]。
从数字化制造的术语性定义中,可以发现,数字化制造定义的内涵包括以下三方面:1) 设计数字化。
在虚拟环境中,可以实现装配过程仿真,数字预装配,CAM,以及结构分析、管路分析、强度分析等等;2) 制造装备数字化。
智能工厂建设的主要模式

智能工厂建设的主要模式及国内外发展现状2018-08-21智能工厂是实现智能制造的重要载体,主要通过构建智能化生产系统、网络化分布生产设施,实现生产过程的智能化。
智能工厂已经具有了自主能力,可采集、分析、判断、规划;通过整体可视技术进行推理预测,利用仿真及多媒体技术,将实境扩增展示设计与制造过程。
系统中各组成部分可自行组成最佳系统结构,具备协调、重组及扩充特性。
已系统具备了自我学习、自行维护能力。
因此,智能工厂实现了人与机器的相互协调合作,其本质是人机交互。
一、智能工厂主要建设模式由于各个行业生产流程不同,加上各个行业智能化情况不同,智能工厂有以下几个不同的建设模式。
第一种模式是从生产过程数字化到智能工厂。
在石化、钢铁、冶金、建材、纺织、造纸、医药、食品等流程制造领域,企业发展智能制造的内在动力在于产品品质可控,侧重从生产数字化建设起步,基于品控需求从产品末端控制向全流程控制转变。
因此其智能工厂建设模式为:一是推进生产过程数字化,在生产制造、过程管理等单个环节信息化系统建设的基础上,构建覆盖全流程的动态透明可追溯体系,基于统一的可视化平台实现产品生产全过程跨部门协同控制;二是推进生产管理一体化,搭建企业CPS 系统,深化生产制造与运营管理、采购销售等核心业务系统集成,促进企业内部资源和信息的整合和共享;三是推进供应链协同化,基于原材料采购和配送需求,将CPS系统拓展至供应商和物流企业,横向集成供应商和物料配送协同资源和网络,实现外部原材料供应和内部生产配送的系统化、流程化,提高工厂内外供应链运行效率;四是整体打造大数据化智能工厂,推进端到端集成,开展个性化定制业务。
第二种模式是从智能制造生产单元(装备和产品)到智能工厂。
在机械、汽车、航空、船舶、轻工、家用电器和电子信息等离散制造领域,企业发展智能制造的核心目的是拓展产品价值空间,侧重从单台设备自动化和产品智能化入手,基于生产效率和产品效能的提升实现价值增长。
制造业智能化生产模式的国内外对比
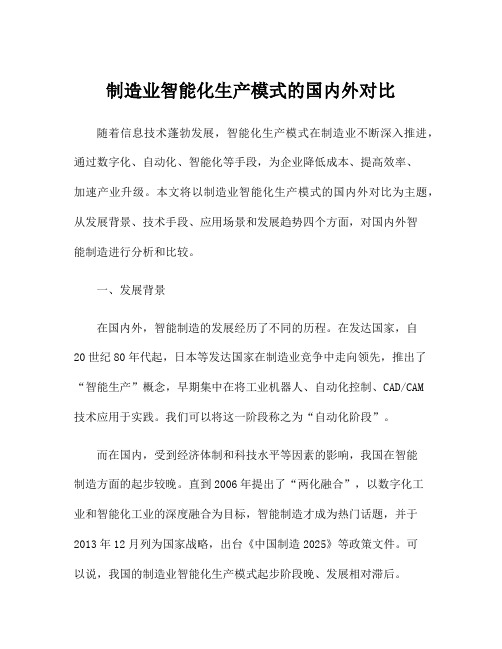
制造业智能化生产模式的国内外对比随着信息技术蓬勃发展,智能化生产模式在制造业不断深入推进,通过数字化、自动化、智能化等手段,为企业降低成本、提高效率、加速产业升级。
本文将以制造业智能化生产模式的国内外对比为主题,从发展背景、技术手段、应用场景和发展趋势四个方面,对国内外智能制造进行分析和比较。
一、发展背景在国内外,智能制造的发展经历了不同的历程。
在发达国家,自20世纪80年代起,日本等发达国家在制造业竞争中走向领先,推出了“智能生产”概念,早期集中在将工业机器人、自动化控制、CAD/CAM技术应用于实践。
我们可以将这一阶段称之为“自动化阶段”。
而在国内,受到经济体制和科技水平等因素的影响,我国在智能制造方面的起步较晚。
直到2006年提出了“两化融合”,以数字化工业和智能化工业的深度融合为目标,智能制造才成为热门话题,并于2013年12月列为国家战略,出台《中国制造2025》等政策文件。
可以说,我国的制造业智能化生产模式起步阶段晚、发展相对滞后。
二、技术手段智能化生产模式的核心在于智能化,其核心技术包括传感器技术、机器视觉技术、数据采集技术和智能算法等。
在国外,智能制造技术落地应用的进展相对快速,多采用了现成的成熟技术,如工业机器人、自动化控制、GIS技术、ERP、MES等。
最近几年,日本等国家也在加快研发基于人工智能技术的生产流程优化系统,更是在数字化生产,自动化生产的领域积累了大量的成功经验,并逐渐突破了困难,最近逐步推进到认知智能阶段,智能化制造技术正在被传统制造业广泛应用,成为制造业数字化、网络化、智能化发展的重要引擎。
在国内,虽然我国的制造业规模巨大,但智能制造技术水平与国际市场仍有差距。
需要提升的技术主要有:传感器速度和分辨率、机器视觉技术、大数据采集和处理技术、智能算法及应用技术等。
三、应用场景智能制造技术的应用,实现了制造业的数字化、智能化和网络化,应用场景也十分广泛。
在国外,智能制造技术广泛应用于汽车、电子、食品等工业制造领域,在制造、装配、物流、售后服务等方面实现了管理和协同。
数字工厂应用场景

数字工厂应用场景
1、智能生产线:数字工厂可以实现生产线全面数字化和智能化,通过数据采集、传输和分析,实现生产过程的监控和优化,提高生产效率和产品质量。
2、虚拟仿真:数字工厂还可以通过虚拟仿真技术对产品的设计、生产和测试进行模拟和优化,降低产品的开发成本和生产风险。
3、智能物流:数字工厂可以通过智能物流系统实现生产线的自动化控制和物流管理,提高物流效率和减少成本。
4、数字化质量控制:数字工厂可以实现生产过程全面数字化和智能化,通过数据采集和分析实现质量控制和异常检测,提高产品质量和供应链效率。
5、智能维护:数字工厂可以通过智能维护系统实现设备的自动化检测和维护,提高设备的可靠性和降低维护成本。
总之,数字工厂应用场景非常广泛,是未来智能制造的重要发展方向。
- 1 -。
- 1、下载文档前请自行甄别文档内容的完整性,平台不提供额外的编辑、内容补充、找答案等附加服务。
- 2、"仅部分预览"的文档,不可在线预览部分如存在完整性等问题,可反馈申请退款(可完整预览的文档不适用该条件!)。
- 3、如文档侵犯您的权益,请联系客服反馈,我们会尽快为您处理(人工客服工作时间:9:00-18:30)。
“数字化工厂”
国内外案例分析
制造业在技术领域已经发生了巨大的进步,这种进步刺激了成本的节约和品质的提高。
反映国家的基础制造业技术发展水平和影响着基础制造业经济命脉的汽车业尤其如此,国内外汽车产品设计工程师已经做了很多了不起的工作来加速设计时间,缩短产品上市时间,并且储存优秀的设计方案以备将来的使用;西方汽车制造工程师们早在十九世纪中期就着手在此方面的研究,随着计算机技术的发展和多年应用实践的研究,最终研究出了一套科学实用先进的数字化制造解决方案-也称“数字化工厂”,这些先进技术的作用非常显著并在行业上得到了广泛的认可。
国内汽车行业,首先是一些合资企业,如南北大众,通用等,在十九世纪九十年代就纷纷开始效仿和学习国外的先进制造技术-“数字化工厂”,使在制造技术上得到了很大提升,并获取了很大的利益;其次是国内自主品牌的汽车业,如奇瑞,福田,长城等,从开始在产品设计领域的埋头苦干,已逐步开始重视制造环节,并已成立各大工程院或技术中心,着手对“数字化工厂”技术的研究和尝试性的应用;
案例一:通用-GM
用户需求:缩短生产准备时间并加速产品投放市场
用户感言:GM 使用了 Tecnomatix eMPower 解决方案,它向我们提供了用于制造过程管理的全方位的解决方案,使我们大大缩短了将新产品从设计,制造到投放市场的时间。
我们认为 eMPower 解决方案的应用在生产制造过程中起着极为重要的作用,它使我们减少了生产准备时间,加速了产品面市, 并使我们的产品拥有完美的品质和可信的服务。
案例二:宝马-BMW
应用效益体现总结图:
BMW将数字化制造技术应用到了汽车制造各个专业领域,尤其在生产线制造的虚拟验证,以及和供应商的工作协调上,获得了很大效益,以下为他们部分效益的总结:案例三:奥迪-AUDI
应用历程:
“数字化工厂”-物流规划仿真在Audi的应用分析,应用工具eM-Plant,Audi制造工程师的项目总结如下:
▪以前奥迪的物流规划依靠各种分散的表单,数据很离散;
▪在新的 A3 Sportback Audi 项目上,不仅应用了数字化的产品设计和工艺过程的规划,而且在物流规划中也全面应用了数
字化的物流仿真工具;
▪Markus Schneider, -Audi数字化物流
系统的负责人 in Ingolstadt, 总结出:
“应用数字化物流规划软件工具后,
物流规划的质量大大提高了。
”;
▪在生产开始前,整个生产物流供应
链:从供应商、入库、仓储、上线的
各个物流过程都全面应用了数字化
的物流规划仿真系统;
▪在数字化物流规划系统中,零件BoM 表上的每个零件都被分配了相应的工位器具,根据零件的几何尺寸和工位器具的数据,物流规划员就可定义各个零件应使用标准的器具或须特殊定制新的器具;
▪在生产的早期,包装供应商可通过确认零件的尺寸和其容器的尺寸,为零部件的包装做好准备;
▪ 现在Audi 的专家可在生产的早期阶段对物流系统进行检验,以前是在生产开始后才能发现存在的问题,这样就可对物流方案进行先期评估和可行性检验。
案例五:马自达-MAZDA
节省了时间和成本, 提高了产品质量、工作效率和产量;
现在Mazda 通过在每个车型项目SOP (投产)前进行约20000项的数字化仿真研究,已经把项目周期从30个月减少到18个月, Mazda 的目标是今后每个车型项目在SOP 前做约30000项数字化预研究来把项目周期缩短到14个月。
所有部门的工作数据都储存在一个 eMServer 中: 1) 没有数据冗余; 2) 不会发生丢失的数据; 3) 没有重复数据; 4) 访问数据快捷简便; 5) 工作流程清晰; 6) 可靠性强; 应用发动机解决方案的分析 ▪ Mazda RX8
– 转子发动机 - 16 种不同的零件 – 13 种机型
– 9周的生产准备时间
▪ 应用发动机解决方案后生产准备周期缩短到3周 ▪ 在新机加工线上应用数字化仿真工具把机床从54台减少到42台,节约了大量设备投资。
▪ 每个加工特征的投资从5400000日圆(36000美圆)减少到3860000日圆(25733美圆),整个生产线上共节约投资四百万美圆 案例六:上海大众-SVW
下图描述了“数字化工厂”技术在德国大众-VW 的应用领域:
15
45
10
20
30
40
50
New
Old Days
上海大众在学习和参考德国大众的成功应用经验的基础之上,已成功的应用到部分领域,尤其在上海大众的焊装领域,在此之前,每款车型的制造工艺设计,都需要国外专家的支持,并为此支付几千万的技术支持费,在焊装成功应用了“数字化工厂”之后,实现了完全自主规划,在制造技术和质量上都有了大幅度的提升;2007年,上海大众着手开始在发动机和总装领域的应用,并在发动机线的物流和人工工时核定方面,再次应证了“数字化工厂”技术在汽车制造领域发挥着举足轻重的作用,下图描述上海大众焊装领域的应用模式:。