ASME工艺流转卡
压力容器工艺过程流转卡

件号
第
3
页
1
共 13
页
控制 标记
序 号
工序
工艺内容及技术要求
R
1
核查
看 清
有裂纹、凹凸、分层、表面无锈蚀。检验员签字确认后划线下料
2
划线
毛 坯 标
W
3 4 5
检验 定位
记 检 验 对
焊 焊接
拼 对 拼 笔
标
φ
划
2
线
1±1㎜ 错边量
W
6 7
检验
检 验 委
托
H
8
检验
1 )
内表面形状偏差:外凸≤1.25% Di 即≤ 25.00 mm
坡口表面不得有裂纹、分层、夹渣等缺陷,清理坡口两侧不小于20㎜范围内污物,打磨见金属光
泽。
6 滚圆 按要求对钢板进行卷筒制作,要求筒节内径Φ444mm。
7
定位 焊
对卷筒完毕后的件进行定位焊,焊道长度10~20mm,间隔50mm,要求错边量b≤3mm,对接间隙
1±1㎜;
W
8
焊接
对筒节的纵焊缝分别进行焊接,清除焊接熔渣及飞溅物,焊接参数见对应的焊接工艺卡,焊接完 成后,
进行标识移植。
W 4 检验 按图纸及工艺检查下料几何尺寸。
W 5 坡口 进行坡口加工,要求按图加工单边V型坡口,坡口角度35°±2°,钝边高度:1±1mm。 坡口表面不得有裂纹、分层、夹渣等缺陷,清理坡口两侧不小于20㎜范围内污物,打磨见金属光 泽。
6 卷制 按要求对钢板进行卷筒制作,要求卷制零件内径Φ2036mm。
文件编号:ZB2005
产品编号 R20-01
管口位置 共
工艺流转卡填写管理制度范文

工艺流转卡填写管理制度范文工艺流转卡填写管理制度第一章总则第一条为了规范和统一工艺流转卡的填写管理工作,提高工艺流转卡的使用效率和准确性,保证生产过程中的工艺资料的准确传递,制定本制度。
第二条工艺流转卡是企业生产过程中的一种重要工具,用来记录和传递工艺技术资料。
填写工艺流转卡是生产作业人员和管理人员的基本职责之一。
第三条工艺流转卡填写管理制度适用于所有生产部门的工艺流转卡的填写工作。
第二章工艺流转卡的分类和用途第四条工艺流转卡分为生产工艺流转卡和维修工艺流转卡两类。
第五条生产工艺流转卡用于传递产品的生产工艺资料,包括产品的加工工艺流程、工艺参数、工艺标准等。
第六条维修工艺流转卡用于传递设备的维修工艺资料,包括设备的维修流程、维修方法、维修步骤等。
第三章工艺流转卡的填写管理要求第七条工艺流转卡的填写由生产作业人员或维修人员负责,并经过相关部门的审核和批准。
第八条工艺流转卡必须按照规定的格式填写,确保填写的内容准确无误。
第九条工艺流转卡的填写内容包括但不限于以下几个方面:1. 产品或设备的基本信息,如名称、规格、型号等;2. 加工或维修工艺的流程,包括各个工段的操作内容、顺序和所需时间;3. 工艺参数,包括各个工段的温度、压力、速度等参数;4. 工艺标准,包括加工或维修的质量要求和检验标准;5. 特殊注意事项,包括注意安全、环保、节能等方面的要求。
第十条工艺流转卡的填写必须认真细致,确保信息全面、准确、可靠。
第四章工艺流转卡的流转管理第十一条工艺流转卡的流转必须按照规定的程序进行,严禁乱丢乱放。
第十二条工艺流转卡的流转必须经过相关部门的审核和批准。
第十三条工艺流转卡的流转必须按照规定的时间节点进行,确保传递及时。
第十四条工艺流转卡的流转必须做好记录,包括接收人、发放人、流转时间等。
第五章工艺流转卡的存档管理第十五条工艺流转卡必须按照规定的时间保留备查,一般不少于两年。
第十六条工艺流转卡的存档必须按照规定的要求进行分类、整理和归档。
生产工序流转卡
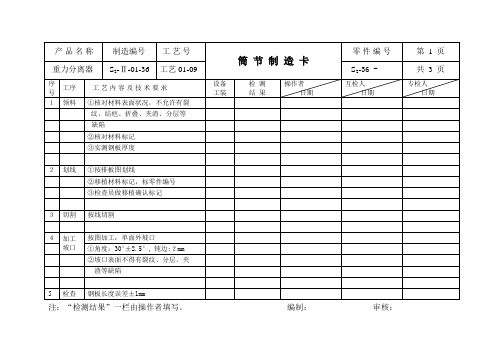
注:“检测结果”一栏由操作者填写。
编制:审核:注:“检测结果”一栏由操作者填写。
编制:审核:注:“检测结果”一栏由操作者填写。
编制:审核:注:“检测结果”一栏由操作者填写。
编制:审核:注:“检测结果”一栏由操作者填写。
编制:审核:注:“检测结果”一栏由操作者填写。
编制:审核:注:“检测结果”一栏由操作者填写。
编制:审核:注:“检测结果”一栏由操作者填写。
编制:审核:注:“检测结果”一栏由操作者填写。
编制:审核:注:“检测结果”一栏由操作者填写。
编制:审核:注:“检测结果”一栏由操作者填写。
编制:审核:注:“检测结果”一栏由操作者填写。
编制:审核:注:“检测结果”一栏由操作者填写。
编制:审核:注:“检测结果”一栏由操作者填写。
编制:审核:注:“检测结果”一栏由操作者填写。
编制:审核:注:“检测结果”一栏由操作者填写。
编制:审核:注:“检测结果”一栏由操作者填写。
编制:审核:注:“检测结果”一栏由操作者填写。
编制:审核:注:“检测结果”一栏由操作者填写。
编制:审核:注:“检测结果”一栏由操作者填写。
编制:审核:注:“检测结果”一栏由操作者填写。
编制:审核:注:“检测结果”一栏由操作者填写。
编制:审核:注:“检测结果”一栏由操作者填写。
编制:审核:注:“检测结果”一栏由操作者填写。
编制:审核:注:“检测结果”一栏由操作者填写。
编制:审核:。
ASME规范产品焊接管理的探讨

ASME规范产品焊接管理的探讨摘要:ASME规范产品的建造是一项系统化的工作,焊接作为特殊工序是ASME规范产品中十分关键的控制环节。
本文对ASME规范产品建造过程中的焊接管理从质量体系建立、人员管理、焊接文件、焊材控制、焊接过程控制、焊缝返修等方面进行了分析和探讨。
关键词:ASME 钢印产品焊接管理质量控制1 ASME质量体系的建立公司根据ASME要求建立了ASME质量体系,编制了ASME质量手册及程序文件,首版2011年正式发布执行。
ASME质量控制手册是该质量控制体系的书面文字叙述,是ASME钢印产品质量控制的纲领性文件,公司员工在安装及制造规范产品时,必须严格遵照执行ASME规范、ASME质量手册和美国锅炉压力容器检验师总部检验规范的要求,不得违反。
ASME质量手册中包含“焊接管理”和“热处理”两个章节,程序文件中包含6个焊接相关的管理程序,内容涵盖了焊缝识别、缺陷返修、热处理、焊材管理、目视检验等工作。
工欲善其事必先利其器,ASME质量手册和程序文件的编制发布为钢印产品的建造奠定了坚实的管理基础。
2 人员管理ASME标准中对三种人员的有资质要求,即NDT检验人员、VT目视检验人员和焊工/焊接操作工。
NDT检验人员资质外部取证,VT检验人员的培训及授权由QC部负责。
焊工技能评定和焊工资质管理成为焊接管理的一项重要工作。
焊工技能评定需严格按照ASME IX执行。
ASME标准相对于国内标准而言焊工评定的适用范围是比较宽的,但是进行ASME焊工评定时需要注意焊接变素的限制。
在实际的焊工评定中,可依据规范要求,综合考虑各焊接变素及评定范围,合理的选取焊工评定(操作)方法、母材试件的尺寸、母材P-No.及焊材F-No.,尽可能的扩大焊工技能评定覆盖范围。
ASME规范产品的焊工资质管理是一项严谨而且持久的工作,焊工资质需严格控制并由专人进行管理维护。
每个合格焊工分配一个唯一焊工钢印号来识别。
依据焊工评定记录WPQ编制“已有资格焊工及焊接操作工一览表”,并定期根据焊工的实际操作活动更新和完善“焊工和焊接操作工资格连续操作记录”,以确保焊工资质有效。
工艺流转卡管理规定
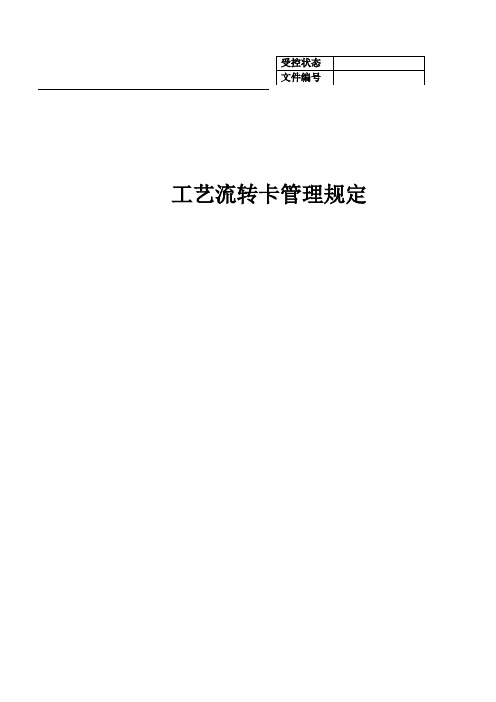
4.4对检验不合格的部件,经评审最终不予放行,按不合格品控制程序执行;检验不合格的部件由班长安排人员返工或返修;
4.5经检验合格的部件,生产者必须使用白色油漆笔将部件编号(见附件2)标识在部件上,<工艺流转卡>必须随合格部件一起转序或存放;质量部将检验合格的部件做好合格标识,不合格部件做好隔离;
3工作职责
3.1工艺员负责公司产品自制件<工艺流转卡>的编制、更新、发放;
3.2生产调度负责<工艺流转卡>班组、部件编号、使用部件编号、生产订单的填写和分发;
3.3生产者负责按<工艺流转卡>技术要求进行自检,填写自检项。班长负责填写自检结论,并签名确认;
3.4质检员负责按<工艺流转卡>技术要求进行专检,填写专检项和专检结论,并签名确认;
第三层:流水号。为“01、02……99”
第三层:年月。如2013年7月为“1307”
第二层:零部件代号。
第一层:工段班组代号。如“H1、H2、TL……”
3.工段班组代号:工段名称拼音首字母+班组名称拼音首字母+班组序号(无序号时以班组名称第二个字拼音首字母代替)。
表2 班组代号表
班组代号
名称
班组代号
4.6质检员在下一道工序检验过程中发现部件与<工艺流转卡>检验要求不相符时,应立即予以纠正,退回至上一道工序重新流转;避免乱流转现象;
4.7最终工序生产者要将所有部件<工艺流转卡>收集后送检,没有<工艺流转卡>或所有工序<工艺流转卡>不完整的不予总检。完成总检后,制造部负责对所有<工艺流转卡>收集、整理及保管;
ASME 取证(专业部分)

ASME取证试题(专业部分)一、设计方面(压力容器UG、UW与UCS)1.常规压力容器强度计算书应该包含哪些基本内容?筒体得强度计算应该考虑哪些要求?椭圆封头得强度计算应该考虑哪些要求?2.如何确定压力容器设计过程中引用标准得版本?如何考虑单位制统一得问题,规范怎么要求得?3.如何考虑规范中没有提到得计算,比如支座计算?4.压力容器得腐蚀裕量就是由设计工程师指定吗?设计工程师如何审核用户设计规范?5.对于锅炉与压力容器,静压头就是否都一定要考虑?6.压缩空气储罐得受压件最小要求壁厚就是多少?7.哪些材料可以允许用于制造压力容器得受压件?允许得螺栓,螺母材料就是哪些?压力容器非受压件就是否需要就是ASME材料?8.压力容器人孔得设计方面得有什么要求?容器排污孔得位置有什么要求?计算书中得所有得尺寸就是腐蚀前还就是腐蚀后?9.判定压力容器就是否需要焊后热处理得因素有哪些?公称厚度得定义?10.什么情况下压力容器必须拍片?如果规范不强制拍片,那么由谁决定拍片得比例?11.如果容器接管开孔在焊缝上,接管满足UG-36(c)(3)得要求不需要计算开孔补强,对这样得开孔处得焊缝有没有RT得要求?12.判定压力容器就是否需要冲击试验得因素有哪些?就是否只就是受压件需要考虑低温冲击?考虑低温冲击时,控制厚度得定义?设计工程师请熟悉附录JJ!13.对于压力容器,免除开孔补强计算得开孔应满足什么条件?14.就是不就是所有尺寸得补强圈都可以完整得考虑为补强得范围内,即补强得范围?15.压力容器接管厚度得计算需满足那些要求?16.针对容器,考虑冲击试验时,SA-105,SA-516 Gr70 正火, SA-106B 分别属于哪一种曲线?17.一台容器打了RT-3标记,封头与筒体焊接用Type 1得接头形式,封头计算时得焊接接头系数为多少?18.一台容器封头为无缝,筒体纵缝RT抽拍,封头与筒体得环缝抽拍并同时满足UW-11(a)5(b)得要求,计算封头壁厚时得焊接接头系数为多少?筒体接头系数为多少?容器打RT-1,RT-2,RT-3还就是RT-4?19.SA 106B 与 A106B什么区别?能等同得材料吗?20.针对容器,封头成型后如何判定就是否需要成型后热处理?如何判定就是否需要带成型试板?21.如何判定焊缝强度就是否需要计算?22.压力容器得水压试验压力值如何确定?水压试验温度就是指介质温度还就是金属温度?具体得温度值有何要求?23.压力容器铭牌得要求有哪些?24.如果容器得铭牌直接装在设备上,铭牌可以装在与设备相连得支架上,这种情况下,铭牌与容器得距离有无具体得要求?二、材料方面1.SA-516 Gr70得质保书有哪些要求?SA-106 GrB质保书有哪些要求?2.SA-516 Gr70 ,20mm厚,允许得尺寸变差就是多少?板材原始标记得要求就是哪些?3.B16、5法兰,材料SA-105要求得标记有哪些?质保书要求哪些内容?就是否需要作入厂验收?4.SA-106B要求得标记有哪些?要求哪些性能试验,允许得尺寸偏差为多少?5.N, QT, Ceq就是什么意思?6.ASME材料如何进行验收?就是否需要复验?就是否一定需要质保书?哪些材料需要质保书?ASME焊材如何进行验收?就是否一定需要质保书?第I 卷与VIII-1卷对材料质保书方面得要求就是否一样?7.材料入厂验收得基本流程就是怎样得?每一过程需要哪些文件?验收合格得材料由谁指定材料追踪号?如何指定?8.谁负责登记材料追踪号得台帐?9.如果材料验收不合格,如何处理?如果需要对母材进行补焊,应该如何操作?10.如果外购得无缝封头,应该如何进行验收?采取什么样得方式追踪其材料追踪号?三、焊接方面1.手工焊,自动焊,机器焊得定义?2.哪些焊接方法能用于焊接VIII-1卷得容器?3.WPS,PQR都应该分别包含哪些变素?4.WPS里得非重要变素发生变化时,如何处理?5.P-No、,F-No、A-No、分别含义?6.WPS中得焊材不属于任何一个A-No、,如何处理?7.焊工考试试样得试验有哪些项目?哪些焊接方法可以用RT替代力学性能试验?RT评定合格得依据就是第五卷吗?这种情况下对焊缝长度有要求吗?8.PQR机械性能包含哪些试验项目?合格依据就是什么?可以用RT代替力学性能试验吗?9.管接头与筒体得焊接接头采用骑座式,管接头尺寸为1’’, 那么焊这条焊缝得焊工应该如何进行考试?如果接头形式为插入式呢?焊工应该具有什么位置得资格?10.焊接非受压件与受压件得焊工就是否需要评定合格得焊工?就是否需要评定合格得WPS,允许进行焊接得最低温度就是多少?11.非受压件就是否一定需要就是ASME材料?非受压件与受压件得焊缝要求在哪一章节?12.如果WPS评定P-NO、1材料并合格,那么这个WPS能覆盖哪些材料?13.如果焊工考试有F-NO、3 带垫板,那么这个焊工焊接哪些F-No、?14.如何维持焊工得资格?15.焊接工艺评定试板材料为SA-516 Gr 70,厚度为9mm,那么弯曲半径为多少?如果试样厚度为40mm,那么做拉伸实验时如何处理?16.低氢焊条得烘培温度,烘培时间依据就是什么?能够回收几次?如何标识回收焊条?如何控制回收得焊条?四、检验方面1.检验员如何进行装配检查?点焊检查?焊缝检查?如果就是RT抽拍,由谁指定抽拍得位置?2.错边量得要求在哪一章节?焊缝余高要求在哪一章节?3.检验员在焊接前应该检查什么?焊接中检查什么?焊接后检查什么?4.如果在检验过程中出现NCR, 应该采取怎样得步骤?5.检验接管与筒体得角焊缝尺寸时,图纸规定得尺寸就是就是仅值沿筒体纵向得焊脚尺寸还就是针对整个焊缝焊脚?6.热处理工程师在准备焊后热处理工艺卡时,保温温度,升温速度,降温速度,如炉温度,出炉温度,保温时间依据在那一章节?7.热处理分包前与分包后如何控制?8.容器在水压试验之后,打U钢印之前,在受压件上焊接非受压件,就是否需要重新进行水压试验?9.MDR就是什么?如何选用相应格式得MDR? 请质检部经理负责熟悉并填写MDR。
ASME 取证(专业部分)
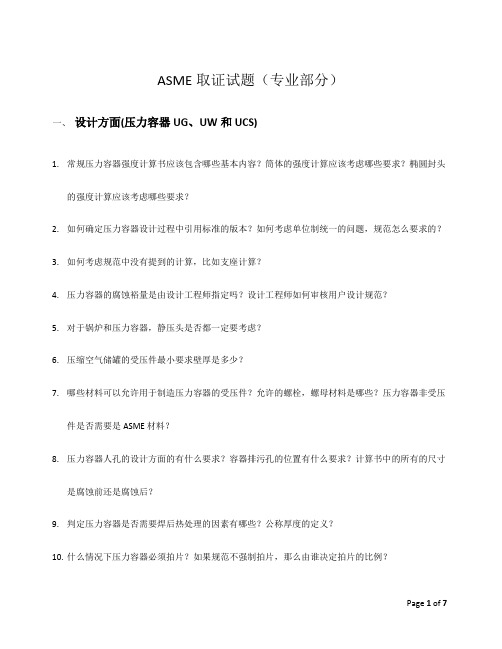
ASME取证试题(专业部分)一、设计方面(压力容器UG、UW和UCS)1.常规压力容器强度计算书应该包含哪些基本内容?筒体的强度计算应该考虑哪些要求?椭圆封头的强度计算应该考虑哪些要求?2.如何确定压力容器设计过程中引用标准的版本?如何考虑单位制统一的问题,规范怎么要求的?3.如何考虑规范中没有提到的计算,比如支座计算?4.压力容器的腐蚀裕量是由设计工程师指定吗?设计工程师如何审核用户设计规范?5.对于锅炉和压力容器,静压头是否都一定要考虑?6.压缩空气储罐的受压件最小要求壁厚是多少?7.哪些材料可以允许用于制造压力容器的受压件?允许的螺栓,螺母材料是哪些?压力容器非受压件是否需要是ASME 材料?8.压力容器人孔的设计方面的有什么要求?容器排污孔的位置有什么要求?计算书中的所有的尺寸是腐蚀前还是腐蚀后?9.判定压力容器是否需要焊后热处理的因素有哪些?公称厚度的定义?10.什么情况下压力容器必须拍片?如果规范不强制拍片,那么由谁决定拍片的比例?11.如果容器接管开孔在焊缝上,接管满足UG-36(c)(3)的要求不需要计算开孔补强,对这样的开孔处的焊缝有没有RT的要求?12.判定压力容器是否需要冲击试验的因素有哪些?是否只是受压件需要考虑低温冲击?考虑低温冲击时,控制厚度的定义?设计工程师请熟悉附录JJ!13.对于压力容器,免除开孔补强计算的开孔应满足什么条件?14.是不是所有尺寸的补强圈都可以完整的考虑为补强的范围内,即补强的范围?15.压力容器接管厚度的计算需满足那些要求?16.针对容器,考虑冲击试验时,SA-105,SA-516 Gr70 正火, SA-106B 分别属于哪一种曲线?17.一台容器打了RT-3标记,封头和筒体焊接用Type 1的接头形式,封头计算时的焊接接头系数为多少?18.一台容器封头为无缝,筒体纵缝RT抽拍,封头与筒体的环缝抽拍并同时满足UW-11(a)5(b)的要求,计算封头壁厚时的焊接接头系数为多少?筒体接头系数为多少?容器打RT-1,RT-2,RT-3还是RT-4?19.SA 106B 和 A106B 什么区别?能等同的材料吗?20.针对容器,封头成型后如何判定是否需要成型后热处理?如何判定是否需要带成型试板?21.如何判定焊缝强度是否需要计算?22.压力容器的水压试验压力值如何确定?水压试验温度是指介质温度还是金属温度?具体的温度值有何要求?23.压力容器铭牌的要求有哪些?24.如果容器的铭牌直接装在设备上,铭牌可以装在与设备相连的支架上,这种情况下,铭牌与容器的距离有无具体的要求?二、材料方面1.SA-516 Gr70的质保书有哪些要求?SA-106 GrB质保书有哪些要求?2.SA-516 Gr 70 ,20mm厚,允许的尺寸变差是多少?板材原始标记的要求是哪些?3.B16.5 法兰,材料SA-105 要求的标记有哪些?质保书要求哪些内容?是否需要作入厂验收?4.SA-106B要求的标记有哪些?要求哪些性能试验,允许的尺寸偏差为多少?5.N, QT, Ceq是什么意思?6.ASME 材料如何进行验收?是否需要复验?是否一定需要质保书?哪些材料需要质保书?ASME焊材如何进行验收?是否一定需要质保书?第I 卷和VIII-1卷对材料质保书方面的要求是否一样?7.材料入厂验收的基本流程是怎样的?每一过程需要哪些文件?验收合格的材料由谁指定材料追踪号?如何指定?8.谁负责登记材料追踪号的台帐?9.如果材料验收不合格,如何处理?如果需要对母材进行补焊,应该如何操作?10.如果外购的无缝封头,应该如何进行验收?采取什么样的方式追踪其材料追踪号?三、焊接方面1.手工焊,自动焊,机器焊的定义?2.哪些焊接方法能用于焊接VIII-1卷的容器?3.WPS,PQR都应该分别包含哪些变素?4.WPS里的非重要变素发生变化时,如何处理?5.P-No.,F-No. A-No.分别含义?6.WPS中的焊材不属于任何一个A-No.,如何处理?7.焊工考试试样的试验有哪些项目?哪些焊接方法可以用RT替代力学性能试验?RT评定合格的依据是第五卷吗?这种情况下对焊缝长度有要求吗?8. PQR 机械性能包含哪些试验项目?合格依据是什么?可以用RT代替力学性能试验吗?9.管接头与筒体的焊接接头采用骑座式,管接头尺寸为1’’, 那么焊这条焊缝的焊工应该如何进行考试?如果接头形式为插入式呢?焊工应该具有什么位置的资格?10.焊接非受压件与受压件的焊工是否需要评定合格的焊工?是否需要评定合格的WPS, 允许进行焊接的最低温度是多少?11.非受压件是否一定需要是ASME材料?非受压件与受压件的焊缝要求在哪一章节?12.如果WPS 评定P-NO. 1材料并合格,那么这个WPS能覆盖哪些材料?13.如果焊工考试有F-NO.3 带垫板,那么这个焊工焊接哪些F-No.?14.如何维持焊工的资格?15.焊接工艺评定试板材料为SA-516 Gr 70,厚度为9mm,那么弯曲半径为多少?如果试样厚度为40mm,那么做拉伸实验时如何处理?16.低氢焊条的烘培温度,烘培时间依据是什么?能够回收几次?如何标识回收焊条?如何控制回收的焊条?四、检验方面1.检验员如何进行装配检查?点焊检查?焊缝检查?如果是RT抽拍,由谁指定抽拍的位置?2.错边量的要求在哪一章节?焊缝余高要求在哪一章节?3.检验员在焊接前应该检查什么?焊接中检查什么?焊接后检查什么?4.如果在检验过程中出现NCR, 应该采取怎样的步骤?5.检验接管与筒体的角焊缝尺寸时,图纸规定的尺寸是是仅值沿筒体纵向的焊脚尺寸还是针对整个焊缝焊脚?6.热处理工程师在准备焊后热处理工艺卡时,保温温度,升温速度,降温速度,如炉温度,出炉温度,保温时间依据在那一章节?7.热处理分包前和分包后如何控制?8.容器在水压试验之后,打U钢印之前,在受压件上焊接非受压件,是否需要重新进行水压试验?9.MDR 是什么?如何选用相应格式的MDR? 请质检部经理负责熟悉并填写MDR。
C5 ASME 检查和检验程序

共3页,第1页5.0 检查和检验程序本章规定按照ASME规范和用户技术条件制造规范产品的检查和检验程序。
5.1总则5.1.1 质检部主管应负责提供规范产品的检查和检验程序,并符合ASME规范和QC手册的要求。
5.2 工艺检验流转卡(COL)5.2.1 工艺工程师应按照图纸、规范和用户技术条件编制COL(样表5-1A,B&C)。
COL应包含所有需要的检查、检验和试验,并有质检员和AI对应签字和注明日期的栏目,以验证上述的质量活动。
COL应经质检工程师审核、计划部主管批准,以确保所有需要的检查、检验和试验均是合理、恰当的,并满足规范和用户技术条件的要求。
需要修改时,工艺工程师应准备新的COL或在原版上修改,新修改的内容须经和初版一样的审查和批准,插入原COL以取代需要更改内容,封面应升版,签字确认。
替换下来的内容也要附在后面。
5.2.2在制造开始之前,质保工程师负责将COL与相应的图纸、工艺或说明一并提交AI审核。
AI审核后,在COL上指明AI检验点,并在COL封面页上签字和注明日期。
5.3 AI检验5.3.1 AI检验点为AI在COL上签字和注明日期的检验点。
AI检验点分成停止点(H)、见证点(W)和审核点(R),定义如下:a) H:停止点是AI不到场,工序不得继续进行的检验点;b) W:见证点是AI不到场,但已事先经AI许可,本公司质检员认可后,工序可继续进行的检验点。
AI的事先许可由经济运行管理部主管写在相应的COL上。
此检查、检验或试验记录应在AI下一次到访时,提交AI认可。
如果AI不能到场指定RT抽拍位置,并且已经被告知,质检工程师负责代表AI指定抽拍点。
c) R:审核点是AI不在场,工序仍可以继续进行的检验点。
此检查、检验或试验记录要在最终检验和试验前,提交AI审核和认可。
5.3.2质保工程师应负责工序进行到“停止点(H)”和“见证点(W)”检验点之前、在合理的时间内通知AI。
5.4 制造过程检查、检验或试验5.4.1当接近过程检验工序时,车间班长负责要求质检员进行或见证检查、检验或试验。
ASME文件管理(101)

1. 总则1.1 本规程规定了ASME 规范产品的质量控制手册、质量管理规程、设计文件、工艺文件的编号、编制、审批、修改发放及保存的责任和 要求。
2. 质量控制手册2.1 质量控制手册编码规定2.1.1质量控制手册的文件号:QCM1 -07 2.1.2质量控制手册的编号:決決为自然顺序号0 1、02、03质量控制手册的编号和《在控手册发放表》上所示的编号相同,即每 一个手册持有者有一本相应编号的手册。
2.1.3质量控制手册所附样表的文件编号-k -k -k _____________ -k -k -k -k ______________ -k -k' 顺序号(01、02、03产品的工号或年份后两位数(03) 每张表的指示标志(已经标注在各表上)2.1.4质量控制手册所列样表的表号•k 士 * _________ -k _______-k ( "k \I —按样表页数的先后次序排列(A 、 " 序号(1、2…)样表所在手册的章节号EXHIBIT样表的表号已经在样表上注明。
质量控制手册的编制、审批、发放、修改按质量控制手册第一章 ASME 质量管理规程ASME 质量管理规程编码规定XXXX文件的管理规程文件编号QCP101--07版本 第二版 第1页共5页修改标记2.2行。
3.3.13.1.1ASME质量管理规程的文件编号*** ______________ -J V-J V-J V-J V ________ -J V-J VU 年份后两位数(06、07…)——顺序号(01、02、03规程所在手册章节的章节号QCP3.1.2除了NDE的规程外其它ASME管理规程所附样表的文件编号,和表号与2.1.3、2.1.4规定相同。
3.2管理规程的编制、审批3.2.1材料管理规程、材料标记规程由质控工程师编制,质控部长审核,质保部长批准。
3.2.2封头压制管理规程,筒体冷卷规程,水压试验规程,热处理管理规程由工艺工程师编制,技术部长审核,质保部长批准。
ASME 热处理工艺卡(模拟).pptx

3. The strips are fixed and tightened
by bolts.Threeheads of the armoued 备注:
thermocouple shall be placed and Remark:
fixed at upper,middle and lower of 编制(热处理工程师)
the vessel separately by one
Prepared by
strip.See the sketch on right.
(H.T Eng.)
批准(技术部长) Approved by
(Manager of TechnologyDept.)
认可 Accepted by
(Form No. 9-1 Rev. 0)
Heating as a whole in closed furnace
Procedure No.
09
Sketch
3. 窄条由螺栓锁紧和固定,每个窄条上所 安装的3个铠装热电偶头,被紧固在容
器的上、中和下部,如右图所示。
1. The heat treatment is Performed in compliance with XXX0901-2009(Heat
Product Name
箱
NA
规格 Dimension
219×16
数量 Quantity
1
重 量 kg Weight
506.035
12
热处理类型
制造后热处理 Post
Type of H.T. Fabrication H.T.
热处理方法 Method of H.T.
整体炉内 工艺规程编号 HZWY0903-20
工序流转卡实施细则

车间现场管控之《工序流转卡》管理细则《工序流转卡》是公司生产管控过程中最重要的业务单据,由制造部依据《生成订单》生成打印后签章下发,从第一道工序切割下料开始至最后一道工序总检包装结束,再办理完工入库,《工序流转卡》必须紧紧跟随整装工位器具实物一同流转。
《工序流转卡》是一线操作工加工后报工的唯一真实、有效的单据,为确保操作工计件薪资准确、及时计算,车间管理数据统计实时、准确,操作工、质检员、车间主管必须高度重视,确保《工序流转卡》在车间流转过程中不得涂改、污损、损毁。
为此,特制定如下管理细则:1、操作工当班加工前请认真核对上一道工序交付的整装工位器具实物数量与《工序流转卡》中的“转移数量”是否完全一致,上道工序报工后才能转移至下一道工序进行加工,否则将影响正常报工和整装工位器具实物的正常流转。
2、操作工当班加工完成整装工位器具产品后,应确保工位器具实物与《工序流转卡》中的“转移数量”完全一致,填写“完工日期”并签字,报质检员进行现场工序完工检验。
3、质检员依据检验结果填写《工序流转卡》表体中的“转移数量”“合格”“返工”“报废”“报废原因”,填写的数据逻辑关系正确且不得随意涂改,否则处罚该笔记录对应的质检员2元。
说明:《工序流转卡》表头右下角“订单数量”=表体第一行“转移数量”;本行“转移数量”=“合格”+“返工”+“报废”。
下一行的“转移数量”=上一行的“合格”。
4、质检员检验出需要前续工序加工返工的产品,按公司质量管理办法执行,各车间主管应协调返工操作工首先加工处理,确保返工品随同整装工位器具实物和《工序流转卡》完整流转;如返工品当班不能返回,该工序操作工则无法正常报工,该整装工位器具和《工序流转卡》不得继续流转,停留超过2个工作日由质检员在《工序流转卡》中记录返工品数量,同时交由制造部计划员办理《生产订单改制》,ERP系统新增一张新的《生产订单》,计划员依据新的《生产订单》生成并打印新增的《工序流转卡》随附返工品单独流转,该工序操作工才能正常报工继续流转,否则下道工序操作工拒绝接受以及核算员有权拒绝报工。
ASME压力容器-工艺评定-试板--取样尺寸解读

工艺评定试样加工(按ASME IX卷)一、取样位置:力学性能和弯曲性能试验的取样要求:a)试件允许避开缺陷制取试样。
b)试样去除焊缝余高前允许对试样进行冷校平。
c)板材对接焊缝试件上试样取样位置见下图:注:晶间腐蚀及其它试样取样位置见工艺评定试板流转卡。
二、板对接拉伸试样取样和加工要求:a)试样的焊缝余高应以机械方法去除,使之与母材齐平。
试样厚度应等于或接近试件母材厚度T。
b)厚度小于或等于25mm的试件,采用全厚度试样进行试验。
c)当试验机受能力限制不能进行全厚度的拉伸试验时,则可将试件在厚度方向上均匀分层取样,等分后制取试样厚度应接近试验机所能试验的最大厚度。
等分后的两片或多片试样试验代替一个全厚度试样的试验(当工艺评定试板流转卡拉伸试样数量要求大于2时则需分层取样)。
注:S——试样厚度,mm;hk——焊缝最大宽度,mm;h—夹持部分长度,根据试验机夹具而定,mm。
三、板对接弯曲试样试样加工要求:试样的焊缝余高应采用机械方法去除,面弯、背弯试样的拉伸表面应齐平,去除余高前允许采用冷校平。
试样形式:a)面弯和背弯试样1.材料为P-No.23,F-No.23或P-No.35时试件厚度T ≤3mm 时,试样厚度T 与y 相等;T >3mm 时,y =3mm ,从试样受压面加工去除多余厚度;2.其它所有材料厚度T ≤10mm 时,试样厚度T 与y 相等;T >10mm 时,y =10mm ,从试样受压面加工去除多余厚度;面弯试样 背弯试样注:1 试样长度L ≈160mm ;2 板材试样宽度B=38mm ;3 试样拉伸面棱角R ≤3mm 。
) b)横向侧弯试样。
1.当试件厚度T 为10~38mm 时,试样宽度等于试件厚度。
当试件厚度T大 于38mm 时,允许沿试件厚度方向分层切成宽度为19—38mm 等宽的两片 或多片试样的试验代替一个全厚度侧弯试样的试验(详见工艺流转卡)。
2.材料为P-No.23,F-No.23或P-No.35时试样宽度W =3mm ,T=t ;3.除上述2所述材料,其它所有材料试样W =10mm ,从试样受压面加工去除 多余厚度;横向侧弯试样注:3.试样长度L ≈160mm ;4.试样拉伸面棱角R ≤3mm 。
ASME压力容器-工艺评定-试板--取样尺寸
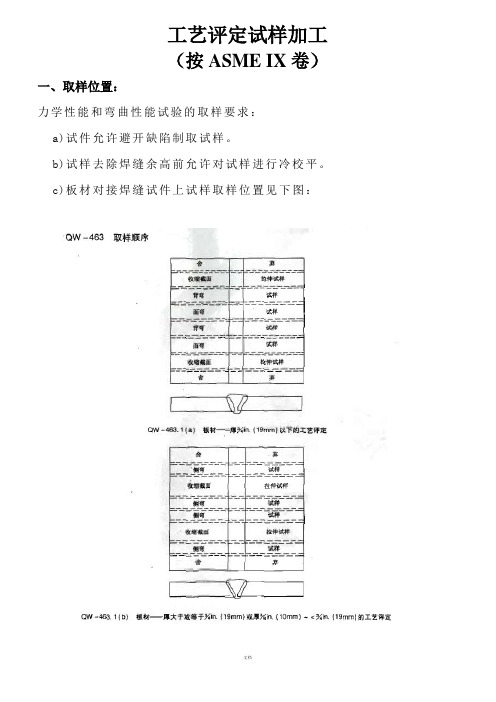
工艺评定试样加工(按ASME IX卷)一、取样位置:力学性能和弯曲性能试验的取样要求:a)试件允许避开缺陷制取试样。
b)试样去除焊缝余高前允许对试样进行冷校平。
c)板材对接焊缝试件上试样取样位置见下图:注:晶间腐蚀及其它试样取样位置见工艺评定试板流转卡。
二、板对接拉伸试样取样和加工要求:a)试样的焊缝余高应以机械方法去除,使之与母材齐平。
试样厚度应等于或接近试件母材厚度T。
b)厚度小于或等于25mm的试件,采用全厚度试样进行试验。
c)当试验机受能力限制不能进行全厚度的拉伸试验时,则可将试件在厚度方向上均匀分层取样,等分后制取试样厚度应接近试验机所能试验的最大厚度。
等分后的两片或多片试样试验代替一个全厚度试样的试验(当工艺评定试板流转卡拉伸试样数量要求大于2时则需分层取样)。
注:S——试样厚度,mm;hk——焊缝最大宽度,mm;h—夹持部分长度,根据试验机夹具而定,mm。
三、板对接弯曲试样试样加工要求:试样的焊缝余高应采用机械方法去除,面弯、背弯试样的拉伸表面应齐平,去除余高前允许采用冷校平。
试样形式:a)面弯和背弯试样1.材料为P-No.23,F-No.23或P-No.35时试件厚度T≤3mm时,试样厚度T与y相等;T>3mm时,y=3mm,从试样受压面加工去除多余厚度;试余面弯试样背弯试样注:1 试样长度L≈160mm;2 板材试样宽度B=38mm;b)横向侧弯试样。
1.当试件厚度T为10~38mm时,试样宽度等于试件厚度。
当试件厚度T 大于38mm时,允许沿试件厚度方向分层切成宽度为19—38mm 等宽的两片或多片试样的试验代替一个全厚度侧弯试样的试验(详见工艺流转卡)。
2.材料为P-No.23,F-No.23或P-No.35时试样宽度W=3mm,T=t;3.除上述2受压面加工去除横向侧弯试样注:3.试样长度L≈160mm;四、板对接冲击试样a)试样取向:试样纵轴应垂直于焊缝轴线,缺口轴线垂直于母材表面。
asme样表册资料汇编

Exhibit No. List of Exhibits Rev. No. DateIV-1 CODE EDITION/ REVIEW CHECK LIST规范核实表0 Apr.08, 2012 IV-2 LIST OF MANUAL HOLDER 手册持有人清单0 Apr.08, 2012 2-1 Letter of Transmittal传送函0 Apr.08, 2012 2-2 Deliver & Receiving Note文件发放接收单0 Apr.08, 2012 3-1 Requisition of Material材料采购申请单0 Apr.08, 2012 3-2 Requisition of Welding Material焊接材料采购申请单0 Apr.08, 2012 3-3 Material Substitute Requisition材料代用申请单0 Apr.08, 2012 3-4 Label for Inspection待检标签0 Apr.08, 2012 3-5 Accepted Label合格标签0 Apr.08, 2012 3-6 Unaccepted Label不合格标签0 Apr.08, 2012 Material Receiving Inspection Record (Steel Plate)3-7 (a)0 Apr.08, 2012材料(钢板)进厂检验记录Material Receiving Inspection Record (Steel Pipe)0 Apr.08, 2012 3-7 (b)材料(钢管)进厂检验记录Material Receiving Inspection Record (Welding Material)0 Apr.08, 2012 3-7 (c)材料(焊材)进厂检验记录Material Receiving Inspection Record (Flange)0 Apr.08, 2012 3-7 (d)材料(法兰)进厂检验记录3-8 Material Request材料领料单0 Apr.08, 2012 3-9 Requisition Form of In-stock Material使用库存材料征询单0 Apr.08, 2012 3-10 Head Forming Inspection Record封头成型检验记录0 Apr.08, 2012Pressure Test Report (Hydrostatic, Pneumatic)0 Apr.08, 20124-1压力试验检验报告(水压、气压)4-2 Check Off List 工艺流转卡0 Apr.08, 2012 4-3 Name Plate 铭牌0 Apr.08, 2012 4-4 Visual and Dimensional Examination Report 外观及尺寸检验报告0 Apr.08, 2012 5-1 Non-conformity Report (NCR) 不合格品报告(NCR)0 Apr.08, 2012 5-2 Waiting for Disposition待处理0 Apr.08, 2012 6-1(a) Weld Summary Sheet焊接汇总表0 Apr.08, 20126-1(b) Welding Work Continuously Record焊接连续工作记录表0 Apr.08, 2012 6-2(a) Qualified Welder List合格焊工人员名单0 Apr.08, 2012 6-2(b) Qualified Welding Operator List合格焊接操作工名单0 Apr.08, 2012 6-3 Joint Identification Card焊缝分布图0 Apr.08, 2012 6-4 Welding Material Request焊材领用单0 Apr.08, 2012 6-5 Welding Repair Process Chart补焊返修工艺卡0 Apr.08, 2012 7-1 NDE Examiner Qualification Record无损检测人员资格鉴定记录0 Apr.08, 2012 7-2 List of Certified NDE personnel已有人员资格表0 Apr.08, 2012 7-3 Vision Examination Record 视力检查记录0 Apr.08, 2012 8-1 Heat Treatment Process Instruction热处理工艺卡0 Apr.08, 2012 8-2 Heat Treatment Report热处理报告0 Apr.08, 2012 9-1 Master List of Calibrated Instruments校正仪表总清单0 Apr.08, 2012 9-2 DO NOT USE禁用标签0 Apr.08, 2012 9-3 Calibration Sticker校正标签0 Apr.08, 2012 10-1 ASME Products List ASME产品清单0 Apr.08, 2012 10-2 NB Number Log NB编号登记表0 Apr.08, 2012Quality Control Manual Exhibit: IV-1 Rev: 0规范核实表CODE EDITION REVIEW CHECK LISTASME规范章节ASME CODESECTION 版本EDITIONLIST NO: 文件号是否修改REVISIONYES / NO有关文件DOCUMENT CONCERNEDⅡPART A PART B PART C PART D ⅤⅧ, DIV.1ⅨCOMMENTS备注:签发人PREPARED BY QA Manager签发日期ISSUED DATEQuality Control Manual Exhibit: IV-2 Rev:0手册持有人清单LIST OF MANUAL HOLDER签发日期Issued Date:签发人Prepared by QA Manager文件名称Document Name 版本号/修改号Ed./Rev.文件号Document No:版本(中文/英文)Version (Chinese/English)文件持有人清单(Signature List)分发号DistributionNo持有人姓名Holder’s Name持有人职务Title of Holder签名Signature日期Date回收Return*一旦收到新版本,控制副本的旧版本应退回。
压力容器制造工序流转卡
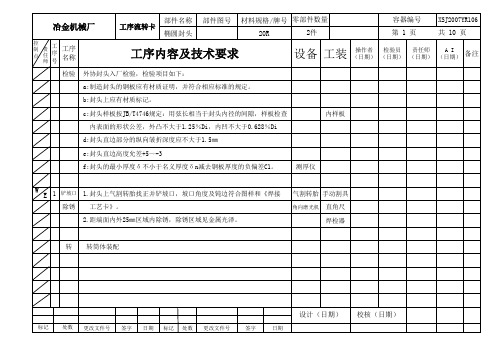
工序 名称
部件名称 部件图号 工序流转卡
附件
工序内容及技术要求
容器编号 第9页
XSJ2007YR106 共 10 页
设备 工装 操作者 (日期)
检验员 (日期)
责任师 (日期)
AI (日期)
备注
1 备料 领取经检验合格的管座 DN50、DN20、DN40、DN25、DN80接管, 铭牌,
支座等集中到装配现场。
5.定位焊缝长30~50㎜,间距50~200㎜,定位焊缝无气孔、夹渣、
裂纹等缺陷,且表面一致。
6.筒节端面倾斜度≤ 2 ㎜
7.筒节长度偏差2000±1.5㎜、 1000±1.5㎜。
8.同一截面上最大内径与最小内径之差随筒体直径的大小确定。
W E 6 装配 1.在筒节纵缝的一端装焊100×100㎜的引弧板,另一端装焊600×300㎜ 电焊机 定位焊 产品焊接试板一块及100×100㎜引弧板一块。 (焊条J427/φ3.2) 2.收、引弧板与筒节板等厚。 3.收、引弧板与筒节组对边缘偏差≤1.0㎜。 4.产品焊接试板焊缝与筒节纵缝应在同一直线上。
容器编号 第 10 页
XSJ2007YR106 共 10 页
设备 工装 操作者 (日期)
检验员 (日期)
责任师 (日期)
AI (日期)
工序流转卡
筒体
δ=8、20R
2节
容器编号 第5页
XSJ2007YR106 共 10 页
控
制 点
责 任 师
工 序 号
工序 名称
工序内容及技术要求
设备 工装 操作者 (日期)
检验员 (日期)
责任师 (日期)
AI (日期)
备注
W E 11 组对 1.筒节与筒节、筒节与封头,按焊缝排版图进行组对。
ASME质量管理工作流程图解

5
14 热处理记录包括:
3
曲线图和试验结果
15 焊后热处理记录
3
资料员 质保工程师
文 件 到 期 处 理 之 前, 质 保 部 部 长 和 设 计 部 部 长 核 定 保 管 期 限 已 满
ASME工作流程图解相关说明
大
厂
首 钢
其它相关工作流程及要求
机
电 有
参见《质量管理规程》中相关规定
限
公
司
团队精神的“三心二意”:信心、恒心、决心;创意、愿意。
批准
审核
质保工程师
电 有 限 公 司
检 查 与
工艺检验 流转卡COL
附加图纸和工艺单
编制 工艺工程师 送审 工艺部部长
批准
送审
质保经理
AI
审核
AI检验 停止点(H)、见证点(W)和审核点(R)
检
验
制造过程检查、检验或实验
工段长
检验员
程
生产试验
焊接工程师+质保部部长负责
序 最终 压力 检验
工段长
质保工程师
物资保管员
材料收发台账
材料发放卡 (样表4-5)
工艺工程师 送审
工艺部部长
工段长
批准
送审
车间主任
批准
材料的识别 标记与追踪
材料的代用
库存材料 的使用
第5章:检查与检验程序流程图解
大
依据ASME规范第Ⅷ卷第1册,QC手册和用户技术条件的要求
厂 首
工艺流程图PFC
编制 工艺工程师 送审
工艺部部长
钢 机
工艺部部长分发唯一的焊工代号 焊接工程师填写“已有资格焊工表”(样表7-1 A&B) “已有资格焊工表”由工艺部部长批准,焊接工程师保管。
ASME与GB制造方面的不同点

ASME 与 GB 制造中的不同点
GB Code
ASME
流转卡上的控制点由公司控制,产品投 产品投产前必须交 AI 设立控制点
产时不需监检
后方可投产
棱角度 错边量 余高
δn/10+2,且不大于 5 mm
不允许
小于等于 12 mm,≤1/4δn 12 到 20 mm,纵缝为 3 mm,环缝为≤ 1/4δn
δn≤1/2(12.7mm) ≤1/4δn
1/2<δn≤11/2 ≤1/8(3.2mm)
单面坡口:15%板厚且小于 4 mm(外 焊缝)
内焊缝≤1.5mm 双面坡口:单面坡口:15%板厚且小于
4 mm
δn≤3/32(2.4mm) ≤1/32(0.8mm) 3/32<δn≤3/16 ≤1/16(1.6mm) 3/16(4.8mm)<δn≤1(25.4mm) ≤3/32(2.4mm)
内件装配
―――
伸入筒体内的接管要导角
焊工钢印
一条焊缝一个钢印
每米长度必须要有焊工钢 1.25×设计压力 气压: 1.15×设计压力
压力表范围
1.5 到 3 倍的压力
不需要
液压: 1.3×设计压力 气压: 1.1×设计压力
1.5 到 4 倍的压力
提交客户资料 质量证明书、合格证、监督检验证书等
除客户特别要求,否则仅提供 MDR
ASME压力容器工艺评定试板取样尺寸

工艺评定试样加工(按ASME IX卷)一、取样位置:力学性能和弯曲性能试验的取样要求:a)试件允许避开缺陷制取试样。
b)试样去除焊缝余高前允许对试样进行冷校平。
c)板材对接焊缝试件上试样取样位置见下图:注:晶间腐蚀及其它试样取样位置见工艺评定试板流转卡。
二、板对接拉伸试样取样和加工要求:a)试样的焊缝余高应以机械方法去除,使之与母材齐平。
试样厚度应等于或接近试件母材厚度T。
b)厚度小于或等于25mm的试件,采用全厚度试样进行试验。
c)当试验机受能力限制不能进行全厚度的拉伸试验时,则可将试件在厚度方向上均匀分层取样,等分后制取试样厚度应接近试验机所能试验的注:S——试样厚度,mm;hk——焊缝最大宽度,mm;h—夹持部分长度,根据试验机夹具而定,mm。
三、板对接弯曲试样试样加工要求:试样的焊缝余高应采用机械方法去除,面弯、背弯试样的拉伸表面应齐平,去除余高前允许采用冷校平。
试样形式:从试余面弯试样背弯试样注:1 试样长度L≈160mm;2 板材试样宽度B=38mm;3 试样拉伸面棱角R≤3mm。
)b)横向侧弯试样。
1.当试件厚度T为10~38mm时,试样宽度等于试件厚度。
当试件厚度T大于为19—38mm等宽的两试验(详见工艺流转2.材料为T=t;3.除上述2受压面加工去除横向侧弯试样注:3.试样长度L≈160mm;4.试样拉伸面棱角R≤3mm。
四、板对接冲击试样a)试样取向:试样纵轴应垂直于焊缝轴线,缺口轴线垂直于母材表面。
b)取样位置:在试件厚度上的取样位置(厚度小于等于38mmnn情况)见下图,不锈钢复合板冲击试样只对基层焊缝区及热影响区取冲击试样。
注:l T ≤38mm 时,t1<1.5mm(仅限焊缝区)。
2 厚度大于38mm 时 取3组(每组仍为3个)试样 一组取焊缝热影响区(与T ≤38mm 时相同取样尽可能包括更多的热影响区)另一组取距焊缝表面 1.2mm 处 另一组取焊缝的另一表面至中心的中间部分.AST M 、ASME 材料的冲击试样:(a) 标准全尺寸试样试样尺寸要求(a)允许偏差如下:45°L(b)标准小尺寸试样(b)对小尺寸试样,除上面所示宽度改变外公差是1%, 标准试样的所有尺寸和公差保持不变。
加工工序流转卡

流转周期:工作日(年月日至年月日)批号:
产品
名称
产品
图号
投产
数量
pcs
投产
日期
工序
数量
工序
编号
工序名称
完成
日期
合格品
数量
不合格品分类数量(pcs)
操作者
检验员
备注
A
BCBiblioteka DEYZ
不合格品分类
A开机调试失控B原物料不合格C上序加工失控D本序加工失控E技术更改Y不合格品处理合格Z不合格品让步接收
加工工序流转卡
流转周期:工作日(年月日至年月日)批号:
产品
名称
产品
图号
投产
数量
pcs
投产
日期
工序
数量
工序
编号
工序名称
完成
日期
合格品
数量
不合格品分类数量(pcs)
操作者
检验员
备注
A
B
C
D
E
Y
Z
不合格品分类
A开机调试失控B原物料不合格C上序加工失控D本序加工失控E技术更改Y不合格品处理合格Z不合格品让步接收
加工工艺方案(筒体流转卡-3+80)

×××××
产 品 编 号
×××××
产 品 名 称
×××××
零(部)件名称
筒 节
共 5页
第 2页
件号
材 料 牌 号
Monel400+16MnR
材 料 规 格
δ=3+80
毛坯尺寸
数 量
工
序
号
工 序
名 称
工 序 内 容
设备或
工 种
工装图号或编号
工时(时)
操作者
检验员
备 注
单件
准结
筒节单块宽度刨边至L+30mm尺寸,不加工坡口,上下棱角倒圆角R≥
②每件筒节在基层表面标示筒节号、焊缝标记、两端口实际周长尺寸。
编制
(日期)
审 核
(日期)
标记
处数
更改文件号
签字
日期
标记
处数
更改文件号
签字
日期
3~5mm。
5
探伤
拼接坡口表面进行100%MT检测,按JB/T 4730.4标准规定的Ⅰ级合格。
6
拼接
将筒节单块进行拼板并组合产品焊接试板,拼板时控制复层对口错边量
铆 工
b≤0.8㎜。
拼缝V型坡口侧基层应焊满并用卡板固定,组焊吊耳后才允许拼接板翻
面。
7
焊接
按焊接工艺要求进行基层、过渡层和复层的焊接。
②备好干净无污染的扫帚、拖布、帆布等。
③复合板翻面时复层表面加垫洁净不锈钢板,确保复层表面不受污染和机
械损伤。
备好清理卷板机上辊轴用的打磨工具。
二、拼板
2
划线
按筒节零件图和筒体拼板图划筒节单块两长边、一短边下料线并标示。