材料性能复习题(力学性能)
《工程材料力学性能》考试复习题

名词解释名词解释1,循环韧性:金属材料在交变载荷下吸收不可逆变形功的能力应力状态软性系数材料最大切应力与最大正应力的比值,记为α。
:2,缺口效应:缺口材料在静载荷作用下,缺口截面上的应力状态发生的变化。
3,缺口敏感度:金属材料的缺口敏感性指标,用缺口试样的抗拉强度与等截面尺寸光滑试样的抗拉强度的比值表示。
抗拉强度的比值表示。
4,冲击吸收功:冲击弯曲试验中试样变形和断裂所消耗的功5,过载损伤界:抗疲劳过载损伤的能力用过载损伤界表示。
6,应力腐蚀:材料或零件在应力和腐蚀环境的共同作用下引起的破坏7,氢蚀:,氢蚀: 由于氢与金属中的第二相作用生成高压气体,使基体金属晶界结合力减弱而导 8,金属脆化。
氢蚀断裂的宏观断口形貌呈氧化色,颗粒状。
微观断口上晶界明显加宽,呈沿晶断裂。
断裂。
9,磨损:机件表面相互接触并产生相对运动,表面逐渐有微小颗粒分离出来形成磨屑,使表面材料逐渐损失、造成表面损伤的现象。
1010,耐磨性:机件表面相互接触并产生相对运动,表面逐渐有微小颗粒分离出来形成磨屑,,耐磨性:机件表面相互接触并产生相对运动,表面逐渐有微小颗粒分离出来形成磨屑,使表面材料逐渐损失、造成表面损伤的现象。
论述论述1,影响屈服强度的因素:,影响屈服强度的因素:①内因:①内因:a a 金属本性及晶格类型b 晶粒大小和亚结构c 溶质元素d 第二相第二相②外因:②外因:a a 温度b 应变速率c 应力状态应力状态2,影响韧脆转变的因素:,影响韧脆转变的因素:①冶金因素:①冶金因素:a a 晶体结构,体心立方金属及其合金存在低温脆性。
b 化学成分化学成分,1,1,1)间隙溶质元素↑→韧脆转变温度↑)间隙溶质元素↑→韧脆转变温度↑2置换型溶质元素一般也能提高韧脆转变温度,但Ni 和一定量Mn 例外。
3杂质元素S 、P 、As As、、Sn Sn、、Sb 等使钢的韧性下降等使钢的韧性下降c 晶粒大小,细化晶粒提高韧性的原因有:晶界是裂纹扩展的阻力;晶界前塞积的位错数减少,有利于降低应力集中;晶界总面积增加,使晶界上杂质浓度减少,避免产生沿晶脆性断裂。
材料力学性能考试题与答案

07 秋材料力学性能一、填空:(每空1分,总分25分)1. 材料硬度的测定方法有、和。
2. 在材料力学行为的研究中,经常采用三种典型的试样进行研究,即、和。
3.平均应力越高,疲劳寿命。
4.材料在扭转作用下,在圆杆横截面上无正应力而只有 ,中心处切应力为 ,表面处。
5.脆性断裂的两种方式为和。
6.脆性材料切口根部裂纹形成准则遵循断裂准则;塑性材料切口根部裂纹形成准则遵循断裂准则;7.外力与裂纹面的取向关系不同,断裂模式不同,张开型中外加拉应力与断裂面,而在滑开型中两者的取向关系则为。
8.蠕变断裂全过程大致由、和三个阶段组成。
9.磨损目前比较常用的分类方法是按磨损的失效机制分为、和腐蚀磨损等。
10.深层剥落一般发生在表面强化材料的区域。
11.诱发材料脆断的三大因素分别是、和。
二、选择:(每题1分,总分15分)()1. 下列哪项不是陶瓷材料的优点a)耐高温 b) 耐腐蚀 c) 耐磨损 d)塑性好()2. 对于脆性材料,其抗压强度一般比抗拉强度a) 高b) 低c) 相等d) 不确定()3.用10mm直径淬火钢球,加压3000kg,保持30s,测得的布氏硬度值为150的正确表示应为a) 150HBW10/3000/30 b) 150HRA3000/l0/30c) 150HRC30/3000/10 d) 150HBSl0/3000/30()4.对同一种材料,δ5比δ10a) 大 b) 小 c) 相同 d) 不确定()5. 下列哪种材料用显微硬度方法测定其硬度。
a) 淬火钢件 b) 灰铸铁铸件c) 退货态下的软钢 d) 陶瓷()6.下列哪种材料适合作为机床床身材料a) 45钢 b) 40Cr钢 c) 35CrMo钢 d) 灰铸铁()7. 下列哪种断裂模式的外加应力与裂纹面垂直,因而它是最危险的一种断裂方式。
a) 撕开型 b) 张开型 c) 滑开型 d) 复合型()8. 下列哪副图是金属材料沿晶断裂的典型断口形貌a) b) c) d) ()9. 下列哪种材料中的弹性模量最高a) 氧化铝 b) 钢 c) 铝 d) 铜()10. 韧性材料在什么样的条件下可能变成脆性材料a) 增大缺口半径 b) 增大加载速度c) 升高温度 d) 减小晶粒尺寸()11.应力腐蚀门槛值正确的符号为a) K ISCC b) ΔK th c) K IC d) CF()12.σm=0 , R=-1 表示下列哪种循环应力a) 交变对称循环 b)交变不对称循环c) 脉动循环 d) 波动循环()13.为提高材料的疲劳寿命可采取如下措施a)引入表面拉应力 b) 引入表面压应力c) 引入内部压应力 d) 引入内部拉应力()14.工程上产生疲劳断裂时的应力水平一般都比条件屈服强度a) 高 b) 低 c) 一样 d) 不一定()15.下列曲线中哪种为脆性材料的应力-应变曲线a) b) c) d)三、判断:(每题1 分,总分15分)()1.材料的力学行为与材料的力学性能是同一概念。
(完整word版)金属材料力学性能练习题
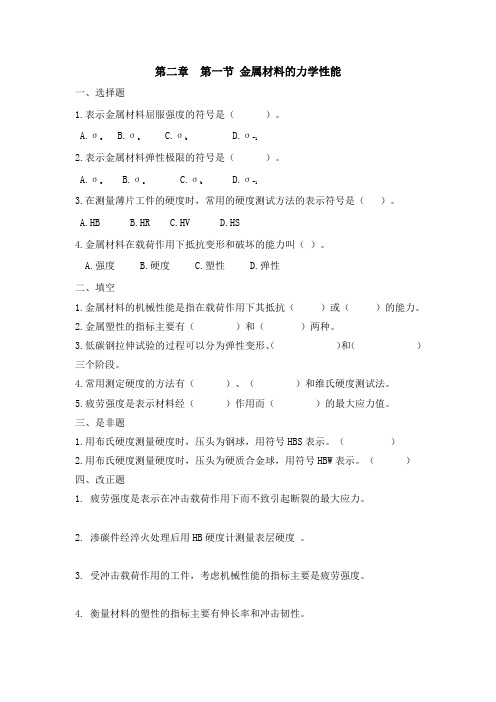
第二章第一节金属材料的力学性能一、选择题1.表示金属材料屈服强度的符号是()。
A.σe B.σsC.σbD.σ-12.表示金属材料弹性极限的符号是()。
A.σe B.σsC.σbD.σ-13.在测量薄片工件的硬度时,常用的硬度测试方法的表示符号是()。
A.HBB.HRC.HVD.HS4.金属材料在载荷作用下抵抗变形和破坏的能力叫()。
A.强度B.硬度C.塑性D.弹性二、填空1.金属材料的机械性能是指在载荷作用下其抵抗()或()的能力。
2.金属塑性的指标主要有()和()两种。
3.低碳钢拉伸试验的过程可以分为弹性变形、()和()三个阶段。
4.常用测定硬度的方法有()、()和维氏硬度测试法。
5.疲劳强度是表示材料经()作用而()的最大应力值。
三、是非题1.用布氏硬度测量硬度时,压头为钢球,用符号HBS表示。
()2.用布氏硬度测量硬度时,压头为硬质合金球,用符号HBW表示。
()四、改正题1. 疲劳强度是表示在冲击载荷作用下而不致引起断裂的最大应力。
2. 渗碳件经淬火处理后用HB硬度计测量表层硬度。
3. 受冲击载荷作用的工件,考虑机械性能的指标主要是疲劳强度。
4. 衡量材料的塑性的指标主要有伸长率和冲击韧性。
5. 冲击韧性是指金属材料在载荷作用下抵抗破坏的能力。
五、简答题1.说明下列机械性能指标符合所表示的意思:σS 、σ0.2、HRC、σ-1。
2.说明下列机械性能指标符合所表示的意思:σb 、δ5、HBS、akv。
2.2金属材料的物理性能、化学性能和工艺性能一、判断题1.金属材料的密度越大其质量也越大。
()2.金属材料的热导率越大,导热性越好。
()3.金属的电阻率越小,其导电性越好。
()二、简答题:1.什么是金属材料的工艺性能?它包括哪些?2.什么是金属材料的物理性能?它包括哪些?3.什么是金属材料的化学性能?它包括哪些?。
材料力学性能习题及解答库
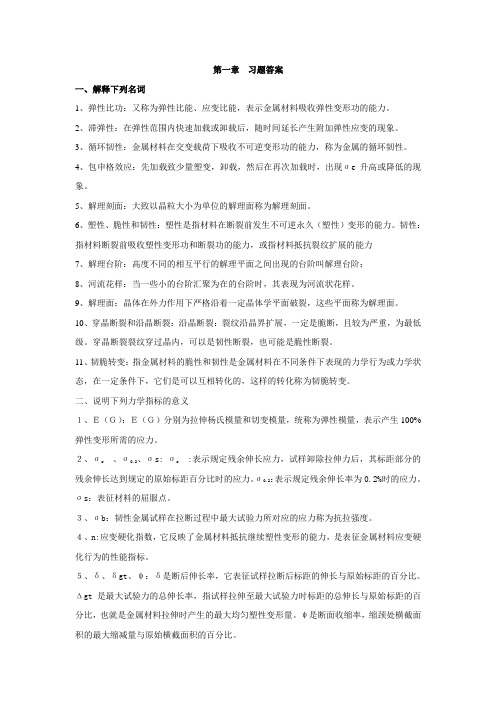
第一章习题答案一、解释下列名词1、弹性比功:又称为弹性比能、应变比能,表示金属材料吸收弹性变形功的能力。
2、滞弹性:在弹性范围内快速加载或卸载后,随时间延长产生附加弹性应变的现象。
3、循环韧性:金属材料在交变载荷下吸收不可逆变形功的能力,称为金属的循环韧性。
4、包申格效应:先加载致少量塑变,卸载,然后在再次加载时,出现σe升高或降低的现象。
5、解理刻面:大致以晶粒大小为单位的解理面称为解理刻面。
6、塑性、脆性和韧性:塑性是指材料在断裂前发生不可逆永久(塑性)变形的能力。
韧性:指材料断裂前吸收塑性变形功和断裂功的能力,或指材料抵抗裂纹扩展的能力7、解理台阶:高度不同的相互平行的解理平面之间出现的台阶叫解理台阶;8、河流花样:当一些小的台阶汇聚为在的台阶时,其表现为河流状花样。
9、解理面:晶体在外力作用下严格沿着一定晶体学平面破裂,这些平面称为解理面。
10、穿晶断裂和沿晶断裂:沿晶断裂:裂纹沿晶界扩展,一定是脆断,且较为严重,为最低级。
穿晶断裂裂纹穿过晶内,可以是韧性断裂,也可能是脆性断裂。
11、韧脆转变:指金属材料的脆性和韧性是金属材料在不同条件下表现的力学行为或力学状态,在一定条件下,它们是可以互相转化的,这样的转化称为韧脆转变。
二、说明下列力学指标的意义1、E(G):E(G)分别为拉伸杨氏模量和切变模量,统称为弹性模量,表示产生100%弹性变形所需的应力。
2、σr、σ0.2、σs: σr :表示规定残余伸长应力,试样卸除拉伸力后,其标距部分的残余伸长达到规定的原始标距百分比时的应力。
σ0.2:表示规定残余伸长率为0.2%时的应力。
σs:表征材料的屈服点。
3、σb:韧性金属试样在拉断过程中最大试验力所对应的应力称为抗拉强度。
4、n:应变硬化指数,它反映了金属材料抵抗继续塑性变形的能力,是表征金属材料应变硬化行为的性能指标。
5、δ、δgt、ψ:δ是断后伸长率,它表征试样拉断后标距的伸长与原始标距的百分比。
金属材料的力学性能考核试卷
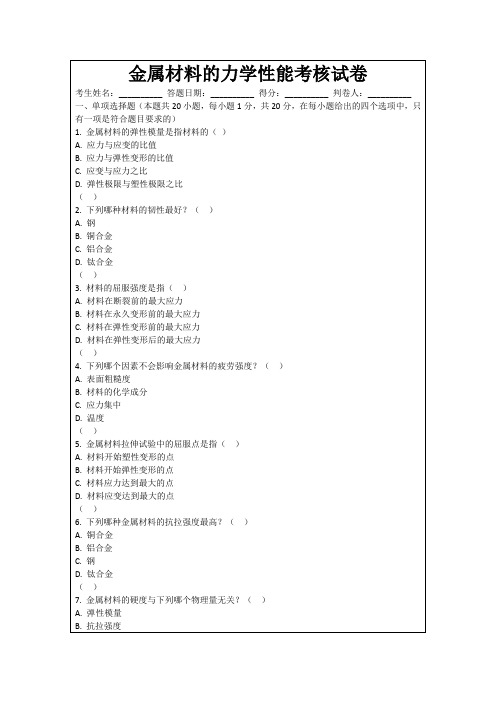
B.超声波探伤
C.磁粉探伤
D.渗透探伤
()
15.以下哪些情况下金属材料可能表现出非线性弹性特性?()
A.高应力水平
B.低应力水平
C.高温环境
D.材料内部缺陷
()
16.以下哪些是金属材料在高温环境下的主要失效模式?()
A.蠕变
B.疲劳
C.应力腐蚀开裂
D.热裂
()
17.以下哪些因素会影响金属材料的熔点?()
三、填空题
1.杨氏模量
2. MPa
3.塑性
4.硬度
5.应力水平和材料性能
6.晶粒大小和晶体缺陷
7.蠕变
8.镀层处理
9.延伸率
10.冲击韧性
四、判断题
1. ×
2. √
3. √
4. ×
5. ×
6. ×
7. ×
8. ×
9. ×
10. ×
五、主观题(参考)
1.弹性指材料受力后能恢复原状的能力,塑性指材料在断裂前能承受永久变形的能力,韧性指材料在断裂前能吸收能量的能力。它们在工程应用中至关重要,因为它们决定了材料在受到外力时的响应行为和失效模式。
10.所有金属材料的熔点都高于室温。()
五、主观题(本题共4小题,每题10分,共40分)
1.请简述金属材料的弹性、塑性和韧性的定义,并说明它们在工程应用中的重要性。
()
2.疲劳破坏是金属结构失效的主要原因之一。请描述导致金属材料疲劳破坏的主要因素,并提出减少疲劳破坏的几种方法。
()
3.试比较退火、正火、淬火和回火四种常见热处理工艺对金属材料性能的影响。
4.蠕变是由高温下的长时间应力作用导致的缓慢塑性变形。影响蠕变行为的因素包括温度、应力水平和时间。为减少蠕变,可以选用蠕变抗力更强的材料,降低工作温度,或减少应力水平。
1材料的力学性能(答案)
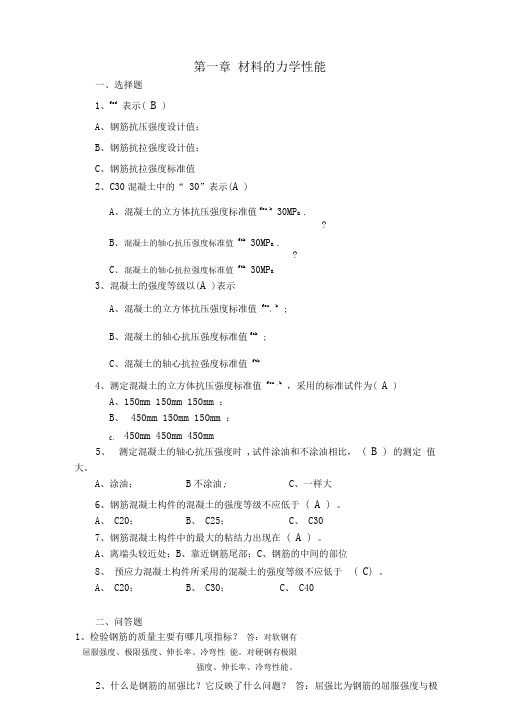
第一章材料的力学性能一、选择题1、fsd表示( B )A、钢筋抗压强度设计值;B、钢筋抗拉强度设计值;C、钢筋抗拉强度标准值2、C30混凝土中的“ 30”表示(A )A、混凝土的立方体抗压强度标准值fcu,k 30MP a .?B、混凝土的轴心抗压强度标准值fck 30MP a .?C、混凝土的轴心抗拉强度标准值ftk 30MP a3、混凝土的强度等级以(A )表示A、混凝土的立方体抗压强度标准值fcu,k;B、混凝土的轴心抗压强度标准值fck;C、混凝土的轴心抗拉强度标准值ftk4、测定混凝土的立方体抗压强度标准值fcu ,k,采用的标准试件为( A )A、150mm 150mm 150mm ;B、450mm 150mm 150mm ;450mm 450mm 450mmC、5、测定混凝土的轴心抗压强度时,试件涂油和不涂油相比,( B ) 的测定值大。
A、涂油;B不涂油;C、一样大6、钢筋混凝土构件的混凝土的强度等级不应低于( A ) 。
A、C20;B、C25;C、C307、钢筋混凝土构件中的最大的粘结力出现在( A ) 。
A、离端头较近处;B、靠近钢筋尾部;C、钢筋的中间的部位8、预应力混凝土构件所采用的混凝土的强度等级不应低于( C) 。
A、C20;B、C30;C、C40二、问答题1、检验钢筋的质量主要有哪几项指标?答:对软钢有屈服强度、极限强度、伸长率、冷弯性能。
对硬钢有极限强度、伸长率、冷弯性能。
2、什么是钢筋的屈强比?它反映了什么问题?答:屈强比为钢筋的屈服强度与极限强度的比值。
它反映结构可靠性的潜力及材料的利用率。
3、如何确定混凝土的立方体抗压强度标准值?它与试块尺寸的关系如何?答:按标准方法制作、养护的边长为150mm勺立方体在28天龄期用标准试验方法测得的具有95%保证率的抗压强度。
试件尺寸越小,抗压强度值越高。
4、为什么要有混凝土棱柱体抗压强度这个力学指标?它与混凝土立方体抗压强度有什么关系?答:钢筋混凝土受压构件中棱柱体多于立方体,所以棱柱体抗压强度比立方体抗压强度能更好地反映受压构件中混凝土的实际强度。
材料力学性能复习

材料⼒学性能复习第⼆章材料在静载荷下的⼒学性能1.连续塑性变形强化材料和⾮连续塑性形变强化材料曲线、变形过程、屈服强度。
2.指出以下应⼒应变曲线与哪些典型材料相对应,并对其经历的变形过程做出说明。
3.拉伸断裂前,发⽣少量塑性变形,⽆颈缩,在最⾼载荷点处断裂;4.断裂前先发⽣弹性变形,然后进⼊屈服阶段,之后发⽣形变强化+均匀塑性变形,有颈缩现象,再发⽣⾮均匀塑性变形直⾄断裂;5.应⼒状态软性系数的定义及其意义、应⼒状态图的应⽤。
6.画出低碳钢的应⼒应变曲线,并说明获得该材料的强度和塑性指标?⽐例极限弹性极限屈服极限强度极限断裂强度延伸率断⾯收缩率7.⼯程应⼒、⼯程应变、真应⼒和真应变之间有什么关系?8.为什么灰⼝铸铁的拉伸断⼝与拉伸轴垂直,⽽压缩断⼝却与压缩⼒轴成45o⾓?9.材料为灰铸铁,其试样直径d=30mm,原标距长度h。
=45mm。
在压缩试验时,当试样承受到485kN压⼒时发⽣破坏,试验后长度h=40mm。
试求其抗压强度和相对收缩率。
10.布⽒、洛⽒、维⽒硬度的试验原理、特点、应⽤。
11.现有如下⼯件需测定硬度,选⽤何种硬度试验⽅法为宜? (1) 渗碳层的硬度分布;(2)灰铸铁;(3)淬⽕钢件;(4)氮化层;(5)双相钢中的铁素体和马⽒体;(6)⾼速钢⼑具;(7)硬质合⾦;(8)退⽕态下的软钢。
第三章材料的变形12.⾦属的弹性模量主要取决于什么?材料的弹性模量可以通过材料热处理等⽅式进⾏有效改变的吗?为什么说它是⼀个对结构不敏感的⼒学性能?弹性也称之为刚度,都是表征材料变形的能⼒?特点:单值性,可逆性,变形量⼩;物理本质:克服原⼦间⼒(双原⼦模型)组织不敏感:E主要取决于材料的本性,与晶格类型和原⼦间距有关,合⾦中固溶原⼦、热处理⼯艺、冷塑性变形,温度、加载⽅式等都对弹性模量影响不⼤;刚度:弹性与刚度是不同的,弹性表征材料弹性变形的能⼒,刚度表征材料弹性变形的抗⼒。
13.弹性变形的不完整性?灰⼝铸铁可以⽤作机床机⾝,为什么?对理想弹性体,在应⼒作⽤下产⽣的应变,与应⼒间存在三个关系:线性、瞬时和唯⼀性。
材料力学性能考试题与答案

07 秋材料力学性能一、填空:(每空1分,总分25分)1. 材料硬度的测定方法有、和。
2. 在材料力学行为的研究中,经常采用三种典型的试样进行研究,即、和。
3. 平均应力越高,疲劳寿命。
4. 材料在扭转作用下,在圆杆横截面上无正应力而只有 ,中心处切应力为 ,表面处。
5. 脆性断裂的两种方式为和。
6. 脆性材料切口根部裂纹形成准则遵循断裂准则;塑性材料切口根部裂纹形成准则遵循断裂准则;7. 外力与裂纹面的取向关系不同,断裂模式不同,张开型中外加拉应力与断裂面,而在滑开型中两者的取向关系则为。
8.蠕变断裂全过程大致由、和三个阶段组成。
9.磨损目前比较常用的分类方法是按磨损的失效机制分为、和腐蚀磨损等。
10.深层剥落一般发生在表面强化材料的区域。
11.诱发材料脆断的三大因素分别是、和。
二、选择:(每题1分,总分15分)()1. 下列哪项不是陶瓷材料的优点a)耐高温 b) 耐腐蚀 c) 耐磨损 d)塑性好()2. 对于脆性材料,其抗压强度一般比抗拉强度a) 高 b) 低 c) 相等 d) 不确定()3.用10mm直径淬火钢球,加压3000kg,保持30s,测得的布氏硬度值为150的正确表示应为a) 150HBW10/3000/30 b) 150HRA3000/l0/30c) 150HRC30/3000/10 d) 150HBSl0/3000/30()4. 对同一种材料,δ5比δ10a) 大 b) 小 c) 相同 d) 不确定()5. 下列哪种材料用显微硬度方法测定其硬度。
a) 淬火钢件 b) 灰铸铁铸件c) 退货态下的软钢 d) 陶瓷()6. 下列哪种材料适合作为机床床身材料a) 45钢 b) 40Cr钢 c) 35CrMo钢 d) 灰铸铁()7. 下列哪种断裂模式的外加应力与裂纹面垂直,因而它是最危险的一种断裂方式。
a) 撕开型 b) 张开型 c) 滑开型 d) 复合型()8. 下列哪副图是金属材料沿晶断裂的典型断口形貌a) b) c) d) ()9. 下列哪种材料中的弹性模量最高a) 氧化铝 b) 钢 c) 铝 d) 铜()10. 韧性材料在什么样的条件下可能变成脆性材料a) 增大缺口半径 b) 增大加载速度c) 升高温度 d) 减小晶粒尺寸()11.应力腐蚀门槛值正确的符号为a) K ISCC b) ΔK th c) K IC d) CF()12.σm=0 , R=-1 表示下列哪种循环应力a) 交变对称循环 b)交变不对称循环c) 脉动循环 d) 波动循环()13.为提高材料的疲劳寿命可采取如下措施a)引入表面拉应力 b) 引入表面压应力c) 引入内部压应力 d) 引入内部拉应力()14.工程上产生疲劳断裂时的应力水平一般都比条件屈服强度a) 高 b) 低 c) 一样 d) 不一定()15.下列曲线中哪种为脆性材料的应力-应变曲线a) b) c) d)三、判断:(每题1 分,总分15分)()1.材料的力学行为与材料的力学性能是同一概念。
材料力学性能复习题基本概念1抗拉强度18韧性金属试样拉

材料力学性能复习题一、基本概念1、抗拉强度(18):韧性金属试样拉断过程中最大应力所对应的应力。
2、弹性模量(3):弹性模量是产生100%弹性变形所需要的应力。
3、弹性比功(4):弹性比功又称弹性比能、应变比能,表示金属材料吸收弹性变形功的能力。
4、包申格效应(6):金属材料经过预先加载产生少量塑性变形,卸载后再同向加载,规定残余伸长应力增加;反向加载,规定残余伸长应力降低的现象,称为包申格效应。
5、屈服强度(10):用应力表示的屈服点或下屈服点就是表征材料对微量塑性变形的抗力,即屈服强度。
6、低温脆性(59):体心立方晶体金属及合金或某些密排六方晶体金属及其合金,特别是工程上常用的中、低强度结构钢,在试验温度低于某一温度k t 时,会由韧性状态变为脆性状态,冲击吸收功明显下降,断裂机理由微孔聚集型变为穿晶解理型,断口特征由纤维状变为结晶状,这就是低温脆性。
7、蠕变断裂(162):由蠕变变形而最后导致金属材料的断裂称为蠕变断裂。
8、疲劳极限南国梨(98):当循环应力水平降低到某一临界值时,试样可以经无限次应力循环也不发生疲劳断裂,故将对应的应力称为疲劳极限。
9、松弛稳定性(167):金属材料抵抗应力松弛的性能。
10、应变硬化(15):金属材料有一种阻止继续塑性变形的能力,这就是应变硬化性能。
11、断裂韧度(70):I K 是决定应力场强弱的一个复合力学参量,当I K 增大达到临界值时,也就是在裂纹尖端足够大的范围内应力达到了材料的断裂强度,裂纹便失稳抗展而导致材料断裂。
这个临界或失稳状态的I K 值记作IC K 或C K ,称为断裂韧度。
12、过载持久值(102):金属材料抵抗疲劳过载损伤的能力,用过载损伤界或过载损伤区表示,过载损伤界与疲劳曲线高应力区直线段各应力水平下发生疲劳断裂的应力循环周次称为过载持久值。
13、蠕变(162):所谓蠕变,就是金属在长时间的恒温、恒载荷作用下缓慢地产生塑性变形的现象。
工程材料力学性能考试题.doc

解释下列名词。
弹性比功:1弹性比功:金属材料吸收弹性变形功的能力,一般用金属开始型性变形前单位体积吸收的最大弹性变形功表示。
2.滞弹性:金属材料在弹性范围内快速加载或卸载后,随时间延长产生附加弹性应变的现象称为滞弹性,滞弹性:也就是应变落后于应力的现象。
3.循环韧性:金属材料在交变载荷下吸收不可逆变形功的能力称为循环韧性。
循环韧性:4.包申格效应:金属材料经过预先加载产生少量型性变形,卸载后再同1侃加载,规定残余伸长应力增加;包申格效应:反向加载,规定残余伸长应力降低的现象。
5.解理刻面:这种大致以晶粒大小为单位的解理面称为解理刻面。
6.型性:金属材料断裂前发生不可逆永久(塑性)变形的能力。
塑性:韧性:韧性:指金属材料断裂前吸收索性变形功和断裂功的能力。
7.解理台阶:当解理裂纹与螺型位错相遇时,便形成一个高度为b的台阶。
解理台阶8. 河流花样:8.河流花样:河流花样解理台阶沿裂纹前端滑动而相互汇合,同号台阶相互汇合长大,当汇合台阶高度足够大时,便成为河流花样。
是解理台阶的一种标志。
9.解理面:9.解理面:是金属材料在一定条件下,当外加正应力达到一定数值后,以极快速率沿一-定品体学平面产生解理面的穿晶断裂,因与大理石断裂类似,故称此种晶体学平面为解理面。
10.穿晶断裂:10.穿晶断裂:穿晶断裂的裂纹穿过晶内,可以是韧性断裂,也可以是脆性断裂。
穿晶断裂沿晶断裂:沿晶断裂:裂纹沿晶界扩展,多数是脆性断裂。
11.切脆转变:11 .韧脆转变:具有一定韧性的金属材料当低于某一温度点时,冲击吸收功明显下降,断裂方式由原来的韧韧脆转变性断裂变为脆性断裂,这种现象称为韧脆转变1何谓拉伸断曰三要素?影响宏观拉伸断口性态的因素有哪些?答:宏观断口呈杯锥形,由纤维区、放射区和剪切唇三个区域组成,即所谓的断曰特征三要素。
上述断口三区域的形态、大小和相对位置,因试样形状、尺寸和金属材料的性能以及试验温度、加载速率和受力状态不同而变化。
钢筋混凝土材料的力学性能试题及答案

钢筋混凝土材料的力学性能试题及答案第一章钢筋混凝土的材料力学性能一、填空题:1、《混凝土规范》规定以强度作为混凝土强度等级指标。
2、测定混凝土立方强度标准试块的尺寸是。
3、混凝土的强度等级是按划分的,共分为级。
4、钢筋混凝土结构中所用的钢筋可分为两类:有明显屈服点的钢筋和无明显屈服点的钢筋,通常称它们为和。
5、钢筋按其外形可分为、两大类。
6、HPB235、 HRB335、 HRB400、 RRB400表示符号分别为。
7、对无明显屈服点的钢筋,通常取相当于于残余应变为时的应力作为名义屈服点,称为。
8、对于有明显屈服点的钢筋,需要检验的指标有、、、等四项。
9、对于无明显屈服点的钢筋,需要检验的指标有、、等三项。
10、钢筋和混凝土是两种不同的材料,它们之间能够很好地共同工作是因为、、。
11、钢筋与混凝土之间的粘结力是由、、组成的。
其中最大。
12、混凝土的极限压应变cu ε包括和两部分,部分越大,表明变形能力越,越好。
13、钢筋冷加工的方法有、、三种。
14、有明显屈服点的钢筋采用强度作为钢筋强度的标准值。
15、钢筋的屈强比是指,反映。
二、判断题:1、规范中,混凝土各种强度指标的基本代表值是轴心抗压强度标准值。
()2、混凝土强度等级是由一组立方体试块抗压后的平均强度确定的。
()3、采用边长为100mm 的非标准立方体试块做抗压试验时,其抗压强度换算系数为0.95。
()4、采用边长为200mm 的非标准立方体试块做抗压试验时,其抗压强度换算系数为1.05。
()5、对无明显屈服点的钢筋,设计时其强度标准值取值的依据是条件屈服强度。
()6、对任何类型钢筋,其抗压强度设计值y y f f '=。
()7、钢筋应在焊接前冷拉。
()8、混凝土的收缩和徐变对钢筋混凝土结构都是有害的。
()9、冷拉后的钢筋不可以作受压钢筋。
()10、钢材的含C量越大,钢材的强度越高,因此在建筑结构选钢材时,应选用含C 量较高的钢筋。
材料力学性能题库
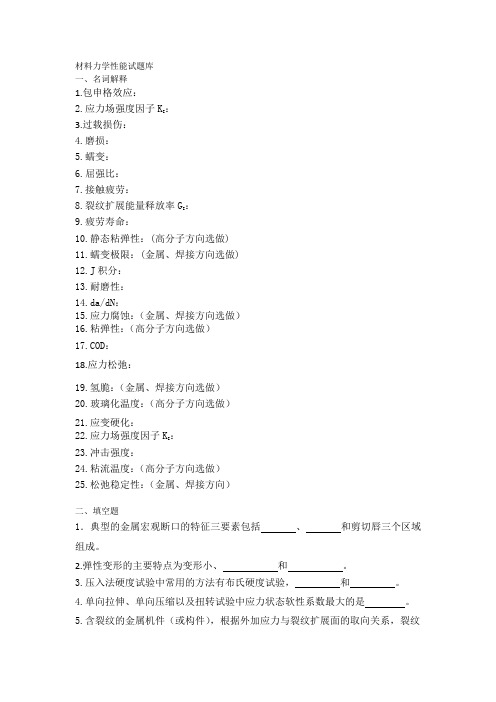
材料力学性能试题库一、名词解释1.包申格效应::2.应力场强度因子KI3.过载损伤:4.磨损:5.蠕变:6.屈强比:7.接触疲劳::8.裂纹扩展能量释放率GI9.疲劳寿命:10.静态粘弹性:(高分子方向选做)11.蠕变极限:(金属、焊接方向选做)12.J积分:13.耐磨性:14.da/dN:15.应力腐蚀:(金属、焊接方向选做)16.粘弹性:(高分子方向选做)17.COD:18.应力松弛:19.氢脆:(金属、焊接方向选做)20.玻璃化温度:(高分子方向选做)21.应变硬化::22.应力场强度因子KI23.冲击强度:24.粘流温度:(高分子方向选做)25.松弛稳定性:(金属、焊接方向)二、填空题1.典型的金属宏观断口的特征三要素包括、和剪切唇三个区域组成。
2.弹性变形的主要特点为变形小、和。
3.压入法硬度试验中常用的方法有布氏硬度试验,和。
4.单向拉伸、单向压缩以及扭转试验中应力状态软性系数最大的是。
5.含裂纹的金属机件(或构件),根据外加应力与裂纹扩展面的取向关系,裂纹扩展有型裂纹扩展、撕开型裂纹扩展、滑开型裂纹扩展三种基本形式。
6.机件正常运行的磨损过程一般分为、稳定磨损阶段、剧烈磨损三个阶段。
7.解理裂纹的河流花样特征中,“河流”的流向与裂纹扩展方向,按“河流”流向的方向去寻找裂纹源。
8.金属材料中常见的塑性变形方式主要为和。
9.冲击试验中,标准试样一般有两种,分别是和。
10.常用的金属断裂韧度包括、ICG、和COD四种。
11.按磨损机理进行分类,磨损类型有黏着磨损、、冲蚀磨损、疲劳磨损、腐蚀磨损和微动磨损。
12.疲劳过程包括:、及最后失稳扩展三个阶段。
13.金属材料常用的塑性指标为和。
14.氢脆是由于和的共同作用而导致金属材料产生脆性断裂的现象。
15.50HRC表示硬度,此测试方法中压头是。
16.金属材料的缺口敏感性指标用和的比值表示。
17.当测出后,还可以借助公式间接换算出KIC 以代替大试样的KIC,然后再按K判据即解决工程中中、低强度钢大型件的断裂问题。
材料的力学性能1

试题内容:直径为d的拉伸比例试样,其标距长度l只能为10d。
( ) 试题答案:答:非试题内容:直径为d的拉伸比例试样,其标距长度l只能为5d。
()试题答案:答:非试题内容:圆柱形拉伸试样直径为d,常用的比例试样其标距长度l是5d或10d。
()试题答案:答:是试题内容:直径为d的拉伸非比例试样,其标距长度l和d无关。
()试题答案:答:是试题内容:Q235钢进入屈服阶段以后,只发生弹性变形。
()试题答案:答:非试题内容:低碳钢拉伸试验进入屈服阶段以后,只有塑性变形。
()试题答案:答:非试题内容:低碳钢拉伸试验进入屈服阶段以后,只发生线弹性变形。
()试题答案:答:非试题内容:试题内容:低碳钢拉伸应力-应变曲线的上、下屈服极限分别为1s σ和2s σ,则其屈服极限s σ为1s σ。
( ) 试题答案: 答:非试题内容:低碳钢拉伸应力-应变曲线的上、下屈服极限分别为1s σ和2s σ,则其屈服极限s σ为2s σ。
( ) 试题答案: 答:是试题内容:拉伸试验测得材料的上、下屈服极限分别为1s σ和2s σ,则材料的屈服极限s σ为22s 1s σσ+。
( ) 试题答案: 答:非试题内容:拉伸试验测得材料的上、下屈服极限分别为1s σ和2s σ,则材料的屈服极限S σ为22s 1s σσ-。
( ) 试题答案: 答:非试题内容:铸铁的强度指标是s σ。
( ) 试题答案: 答:非试题内容:铸铁的强度指标是b σ。
( )试题内容:铸铁的极限应力是s σ和b σ。
( ) 试题答案: 答:非试题内容:铸铁的强度指标是δ和s σ。
( ) 试题答案: 答:非试题内容:材料的塑性指标有s σ和b σ。
( ) 试题答案: 答:非试题内容:材料的塑性指标有s σ和ε。
( ) 试题答案: 答:非试题内容:材料的塑性指标有δ和ψ。
( ) 试题答案: 答:是试题内容:材料的塑性指标有s σ、ε和ψ。
( ) 试题答案: 答:是工程上通常把伸长率%5≥δ材料称为塑性材料。
材料力学性能试题

一、名词解释1、滞弹性:在弹性范围内快速加载或卸载后,随时间延长产生附加弹性应变的现象2、弹性比功:表示金属材料吸收弹性变形功的能力。
一般用金属开始塑性变形前单位体积吸收的最大弹性变形功。
3、包申格效应:材料经过预先加载并产生少量塑性变形,卸载后,再同向加载,规定残余伸长应力增加,反向加载规定残余伸长应力降低的现象,称为包申格效应。
4、河流花样:裂纹跨越若干相互平行的而且位于不同高度的解理面;解理裂纹与很多螺型位错相遇,汇合台阶高度足够大时,便成为在电镜下可以观察到的河流花样。
5、穿晶断裂:金属断裂时裂纹穿过晶内。
穿晶断裂可以是韧性断裂(如室温下的穿晶断裂),也可以是脆性断裂(如低温下的穿晶断裂)。
6、沿晶断裂:金属断裂时裂纹沿晶界扩展。
沿晶断裂多为脆性断裂。
断口形貌呈冰糖状7、韧脆转变温度:体心立方或密排六方金属及合金,在温度低于tk时,会由韧性状态转变为脆性状态,冲击吸收功明显下降,断裂机理由微孔聚集型变为穿晶解理型,断口特征由纤维状变为结晶状,这就是低温脆性。
转变温度tk称为韧脆转变温度,也称冷脆温度。
8、应力场强度因子:在线弹性断裂力学中,表示带初始裂纹构件的裂纹尖端处应力场奇异性性态的一个参数。
或者反映裂纹尖端弹性应力场强弱的物理量称为应力强度因子。
9、缺口敏感度:用缺口试样的抗拉强度σbn与等截面尺寸光滑试样的抗拉强度σb的比值表示,记为NSR。
是安全性力学性能指标。
NSR = σbn/σb10、裂纹扩展能量释放率:把裂纹扩展单位面积时系统释放势能的数值称为裂纹扩展能量释放率,简称能量释放率或能量率。
11、驻留滑移带:金属在循环应力长期作用下,形成永久留或再现的循环滑移带称为驻留滑移带,具有持久驻留性.12、疲劳条带:电镜断口分析表明,第二阶段的断口特征是具有略呈弯曲并相互平行的沟槽花样,称为疲劳条带(疲劳条纹,疲劳辉纹)。
13、应力腐蚀断裂:金属在拉应力和特定的化学介质共同作用下,经过一段时间后所产生的低应力脆断现象,称为应力腐蚀断裂。
材料力学性能复习资料

一、说明下列力学性能指标的意义 1) P σ 比例极限 2) e σ 弹性极限 3) b σ抗拉强度 4) s τ扭转屈服强度 5) bb σ抗弯强度6) HBW 压头为硬质合金球时的布氏硬度7) HK 显微努氏硬度8) HRC 压头为顶角120︒金刚石圆锥体、总试验力为1500N 的洛氏硬度 9) KV A 冲击韧性 10) K IC 平面应变断裂韧性 11) R σ应力比为R 下的疲劳极限 12) ∆K th 疲劳裂纹扩展的门槛值13) ISCC K 应力腐蚀破裂的临界应力强度因子14) /Tt εσ给定温度T 下,规定试验时间t 内产生一定的蠕变伸长率δ的蠕变极限 15) T t σ给定温度T 下,规定试验时间t 内发生断裂的持久极限二、单向选择题1)在缺口试样的冲击实验中,缺口越尖锐,试样的冲击韧性( b )。
a ) 越大; b) 越小;c ) 不变;d) 无规律2)包申格效应是指经过预先加载变形,然后再反向加载变形时材料的弹性极限( b )的现象。
a ) 升高 ;b ) 降低 ;c ) 不变;d ) 无规律可循3)为使材料获得较高的韧性,对材料的强度和塑性需要( c )的组合。
a ) 高强度、低塑性 ;b) 高塑性、低强度 ;c) 中等强度、中等塑性;d ) 低强度、低塑性4)下述断口哪一种是延性断口(d )。
a) 穿晶断口;b ) 沿晶断口;c) 河流花样 ;d ) 韧窝断口 5) 5)HRC 是( d )的一种表示方法.a) 维氏硬度;b ) 努氏硬度;c ) 肖氏硬度;d ) 洛氏硬度6)I 型(张开型)裂纹的外加应力与裂纹面(b );而II 型(滑开型)裂纹的外加应力与裂纹面( )。
a) 平行、垂直;b) 垂直、平行;c) 成450角、垂直;d) 平行、成450角 7)K ISCC 表示材料的( c )。
a) 断裂韧性; b) 冲击韧性;c ) 应力腐蚀破裂门槛值;d ) 应力场强度因子 8)蠕变是指材料在( B )的长期作用下发生的塑性变形现象。
最新材料力学性能期试卷和答案

答:韧性断裂是金属材料断裂前产生明显宏观塑性变形的断裂,这种断裂有一个缓慢
的撕裂过程,在裂纹扩展过程中不断地消耗能量。典型的韧性断裂宏观断口呈杯锥形, 由纤维区、放射区和剪切唇三个区域组成。(2.5分)
2、简述c-1和厶Kth的异同点,并画出疲劳裂纹扩展速率曲线。
答:相同:表征材料无限寿命疲劳性能(2分)
不同:c-1(疲劳强度)代表的是光滑试样的无限寿命疲劳强度,适用于传统的疲 劳强度设计和校核(1.5分);△Kth(疲劳裂纹扩展门槛值)代表的是裂纹试样的无限 寿命疲劳性能,适于裂纹件的设计和疲劳强度校核。(1.5分)(画图2.5分)
3、简述缺口的两个效应,并画出厚板缺口拉伸时弹性状态下的应力分布图。
A、塑性变形功;B、弹性变形功;
C、弹性变形功和塑性变形功;D、冲击变形功
8、金属具有应变硬化能力,表述应变硬化行为的Hollo mon公式,目前得到比较广
泛的应用,它是针对真实应力-应变曲线上的()阶段。
A、弹性;B、屈服;C、均匀塑性变形;D、断裂。
9、 因相对运动而产生的磨损分为三个阶段:()、稳定磨损阶段和剧烈磨损阶 段。
4、简述氢脆的类型及其特征。
六、综合计算题:(每题10分,20分)
已知平面应变修正公式为:K(丫也,Ro1(―)2
耳10.056Y2(/s)2^2s
1、一块含有长为16mm中心穿透裂纹[K】=«na)1/2]的钢板,受到350MPs垂直于裂 纹平面的应力作用。(1)如果材料的屈服强度分别是1400Mpa和385MPa求裂纹 顶端应力场强度因子值;(2)试比较和讨论上述两种情况下,对应力场强度因子进 行塑性修正的意义。
5、根据剥落裂纹起始位置及形态的差异,接触疲劳破坏分为点蚀、浅层剥落和
材料力学性能试题集

判断1•由内力引起的内力集度称为应力。
(X )2•当应变为一个单位时,弹性模量即等于弹性应力,即弹性模量是产生100%弹性变形所需的应力。
(V )3•工程上弹性模量被称为材料的刚度,表征金属材料对弹性变形的抗力,其值越大,则在相同应力条件下产生的弹性变形就越大。
(X )4•弹性比功表示金属材料吸收弹性变形功的能力。
(V )5•滑移面和滑移方向的组合称为滑移系,滑移系越少金属的塑性越好。
(X )6•高的屈服强度有利于材料冷成型加工和改善焊接性能。
(X )7•固溶强化的效果是溶质原子与位错交互作用及溶质浓度的函数,因而它不受单相固溶合金(或多项合金中的基体相)中溶质量所限制。
(X )8•随着绕过质点的位错数量增加,留下的位错环增多,相当于质点的间距减小,流变应力就增大。
(V)9•层错能低的材料应变硬度程度小。
(X )10. 磨损、腐蚀和断裂是机件的三种主要失效形式,其中以腐蚀的危害最大。
(X )11. 韧性断裂用肉眼或放大镜观察时断口呈氧化色,颗粒状。
(X )12. 脆性断裂的断裂面一般与正应力垂直,断口平齐而光亮,长呈放射状或结晶状。
(V )13. 决定材料强度的最基本因素是原子间接合力,原子间结合力越高,则弹性模量、熔点就越小。
(X )14. 脆性金属材料在拉伸时产生垂直于载荷轴线的正断,塑性变形量几乎为零。
(V)15. 脆性金属材料在压缩时除产生一定的压缩变形外,常沿与轴线呈45。
方向产生断裂具有切断特征。
(V )16. 弯曲试验主要测定非脆性或低塑性材料的抗弯强度。
(x )17. 可根据断口宏观特征,来判断承受扭矩而断裂的机件性能。
(V)18. 缺口截面上的应力分布是均匀的。
(x )19. 硬度是表征金属材料软硬程度的一种性能。
(V)20. 于降低温度不同,提高应变速率将使金属材料的变脆倾向增大。
(X )21•低温脆性是材料屈服强度随温度降低急剧下降的结果。
(X )22. 体心立方金属及其合金存在低温脆性。
- 1、下载文档前请自行甄别文档内容的完整性,平台不提供额外的编辑、内容补充、找答案等附加服务。
- 2、"仅部分预览"的文档,不可在线预览部分如存在完整性等问题,可反馈申请退款(可完整预览的文档不适用该条件!)。
- 3、如文档侵犯您的权益,请联系客服反馈,我们会尽快为您处理(人工客服工作时间:9:00-18:30)。
材料性能复习题(力学性能)第一章 单向静拉伸力学性能一.名词解释1. 弹性极限(σe ):以后,材料便开始产生塑性变形。
其表达式为2. 弹性模数(E):E=σ/ε G= τ/ γ 值,表面原子间结合力大小。
3. 弹性比功(a e ):材料拉伸时的弹性比功可用应力 a e =4. 规定非比例伸长应力(σp ): 0.05%时的应力。
5. 屈服强度(σs ):的屈服强度或屈服点,用σs 表示.6. 规定残余伸长应力:σr r0.1、σr0.2,常用的为σr0.2。
7. 应变硬化指数(n ):S=ke n ,材料的n 值高低与其层错能的大小有关。
物理意义:抵抗均匀塑性变形的能力。
技术意义:对加工硬化敏感,n 越大,应变硬化效益越高,根据n 值选 工程材料。
8. 断后伸长率(δ):指试样拉断后,标距的伸长与原始标距百分比。
δ=ΔL K (L 1-L 0)/L 0 × 100%9. 断面收缩率(Ψ):断面收缩率是试样拉断后, 缩颈处横截面积的最大减缩量与原始横截面积的百分比, 用符号Ψ表示, 即Ψ=(Ao-A1)/Ao × 100%,式中:Ao 为试样原始横截面积;A1 为缩颈处最小横截面积.10. 韧性断裂:断裂前有明显的宏观塑性变形,吸收的能量大,断口呈纤维状,发暗,看的出塑性变形后的痕迹。
11. 脆性断裂:断裂前不发生明显的宏观塑性变形,即断裂发生在弹性变形阶段、吸收的能量很小。
断口与正应力垂直,宏观上比较平齐光亮,常呈放射状或结晶状。
12. 剪切断裂:剪切断裂是材料在切应力作用下沿着滑移面滑移分离而造成断裂。
剪切断裂的另一种形式为微孔聚集型断裂,微孔聚集型断裂是材料韧性断裂的普通方式。
13. 解理断裂:在正应力作用下,由于原子间结合键的破坏引起的沿特定晶面发生的脆性穿晶断裂称为解理断裂。
(沿着一定结晶学平面发生的断裂的现象叫解理。
)14. 理论断裂强度(σm ):将晶体两个原子面沿垂直于外力方向拉断所需最小应力。
(使得原子间引力达到最大值时所受到的拉应力。
)a E m γσ= (一般金属σm =10000MPa ;实际金属强度:铝合金:200-300MPa ,低碳钢:400-500MPa ,合金钢:1000MPa )15. 静力韧度:金属材料在静拉伸时单位体积材料断裂前所吸收的功。
通常将静拉伸的σ-ε曲线下包围的面积减去试样断裂前吸收的弹性能定义为静力韧度。
静力韧度的数学表达式可用材料拉断后的真应力-真应变曲线求得。
表达式:二.判断题 正确用√,错误用× 1. 材料的弹性模数越大,其弹性越好。
(×)解释:弹性模数是表征材料对弹性变形的抗力,即材料的刚度,其值越大,则在相同应力下产生的弹性变形就越小。
反应的是材料抵御变形的能力,不能反映材料的弹性。
模量大说明材料不易变形,反之则表示材料很容易发生变形。
弹性是指材料发生变形后回复原始形状的能力,和模量没有必然的联系。
2. 金属材料的显微组织对其弹性模数的影响较小。
(×)解释:金属材料,在合金成分不变的情况下,显微组织对弹性模数的影响较小,晶粒大小对E值无影响;钢经过淬火后E值虽有所下降,但回火后又恢复到退火状态的数值;第二相对E值的影响视其体积比例和分布状态而定,大致可按两相混合物体积比例的平均值计算。
3. 材料的理论断裂强度愈高,其抗拉强度也愈高。
(×)?解释:抗拉强度( Rm )指材料在拉断前承受最大应力值。
理论断裂强度指将晶体两个原子面沿垂直于外力方向拉断所需最小应力。
二者没有必然联系。
4. 材料在韧性断裂过程中都要产生明显的宏观塑性变形。
(√)解释:韧性断裂的特征:断裂前有明显的宏观塑性变形,吸收的能量大,断口呈纤维状,发暗,看的出塑性变形后的痕迹。
5. 微孔聚集型断裂不是金属材料韧性断裂的普遍方式。
(×) 解释:韧性断裂的主要机制就是微孔集合型剪切,在断口上其微观特征表现为韧窝。
分别表示(杨氏)模量和(切变)模量,它们都是表征材料)变形的抗力,其值越大,在相同应力下产生的(弹性变形)就越小。
材料拉伸屈服时,所对应的应力值称为(屈服点),用(σs )表示,试样发生屈服而力首),屈服伸长对应的水平或曲折线段称为(屈服平台)低碳钢试棒静拉伸断裂后,断口一般为杯锥状,由(纤维区)、(放射区)和(剪切唇)3材料发生韧性断裂时,裂纹的扩展过程一般(较慢),要消耗大量的(塑性)变形功,断)。
而脆性断裂多为突然发生的(快速)断裂过程,具有很),常呈放射状或(结晶)状。
n=1时,表示材料为完全理想的(弹n 值在(0.1-0.5)之间。
1. 材料的弹性模数主要取决于什么因素?通过热处理是否可以大幅度提高钢铁材料的弹性模数?答:影响弹性模数的因素:键合方式和原子结构、晶体结构、化学成分、微观组织、温度、加载条件和负荷持续时间。
金属材料的弹性模量与热处理有关系,但影响不大。
所以 通过热处理不可以大幅度提高钢铁材料的弹性模数。
(钢铁材料,在合金成分不变的情况下,显微组织对弹性模数的影响较小。
如经过淬火后E值虽有所下降,但回火后又恢复到退火状态的f k e S a 22.0σ+=数值,因此热处理无法大幅度提高钢铁材料的弹性模数。
)(具体解释)(1)键合方式和原子结构①无机非金属材料:大多由共价键或离子键以及两种键合方式共同作用而成,有较高弹性模数。
金属及其合金:为金属键合,有较高弹性模数。
高分子聚合物:分子键结合,结合力较弱,弹性模数较低。
②金属元素的弹性模数大小还与其在周期表中的位置有关,金属弹性模量主要取决于金属原子本身的性质,金属弹性模量随原子半径增大而减小,同时也表明弹性模量随原子间距的增加而下降。
(2)晶体结构①单晶体材料的弹性模数在不同晶体学方向上是各向异性,即沿原子排列最密的晶向上弹性模量较大,反之则小。
②多晶体材料的弹性模数为各晶粒的统计平均值,表现为各向同性,但这种各向同性称为伪各向同性。
③非晶态材料,如非晶态金属、玻璃等,弹性模量是各向同性的。
(3)化学成分材料化学成分变化将引起原子间距或键结合方式的变化,因此影响材料弹性模数。
与纯金属相比,合金的弹性模数将随组成元素的相对含量、结晶结构和组织状态的变化而变化。
①对于固溶体合金,弹性模数主要取决于溶剂元素的性质和晶体结构。
随着溶质元素浓度的增加,虽然可以改变固溶体的弹性模数,但在溶解度较小的情况下一般变化不大,例如碳钢与合金钢的弹性模数相差不超过 5%。
②在两相合金中,弹性模数的变化比较复杂,它与合金成分、第二相的性质、数量、尺寸及分布状态有关。
(4)微观组织①金属材料,在合金成分不变的情况下,显微组织对弹性模数的影响较小,晶粒大小对 E 值无影响。
经过淬火后E值虽有所下降,但回火后又恢复到退火状态的数值;第二相对 E 值的影响视其体积比例和分布状态而定,大致可按两相混合物体积比例的平均值计算。
②工程陶瓷弹性模数的大小受构成陶瓷的相种类、粒度、分布、比例及气孔率有无有关。
一般是通过实际测量而获得。
气孔率对陶瓷的弹性模数的影响大致可用下式表示,E=E 0 (1-1.9p+0.9p²)式中 E 0为无气孔时的弹性模数,p 为气孔率。
可见随着气孔率的增加,陶瓷的E 值下降。
(5)温度①一般说来,随着温度升高,原子振动加剧,体积膨胀,原子间距增大,结合力减弱,使材料的弹性模数降低。
例如,碳钢加热时,温度升高 100℃E 值下降(3~5)%。
另外,随着温度的变化,材料发生固态相变时,弹性模数将发生显著变化。
②高分子聚合物的物理性质与温度和时间有关。
随着温度的变化,在一些特定的温度区间,某些力学性质会发生突然的改变,这种变化称为高聚物的力学状态转变。
随着高聚物力学状态的转变,其弹性模数也相应产生很大变化。
(6)加载条件和负荷持续时间①加载方式(多向应力)、加载速率和负荷持续时间对金属,陶瓷类材料的弹性模数几乎没有影响。
②高分子聚合物材料的弹性模数与时间的关系与其对温度的关系相似,一般说来,随着负荷时间的延长,E 值逐渐下降。
在此情况下把高聚物的弹性模数称为松弛模数。
高分子聚合物的弹性模数常用加载一段时间后的数值 E(t)表示,称为 t 秒松弛模数,如 10 秒模数等。
2.举出3种提高金属材料屈服强度的方法,并说明其使材料强化的理由。
答:1 )细晶强化。
在常温下的细晶粒金属比粗晶粒金属有更高的强度、硬度、塑性和韧性。
这是因为细晶粒受到外力发生塑性变形可分散在更多的晶粒内进行,塑性变形较均匀,应力集中较小;此外,晶粒越细,晶界面积越大,晶界越曲折,越不利于裂纹的扩展。
晶粒越细小,位错集群中位错个数(n)越小,根据,应力集中越小,所以材料的强度越高;2 )固溶强化。
融入固溶体中的溶质原子造成晶格畸变,晶格畸变增大了位错运动的阻力,使滑移难以进行,从而使合金固溶体的强度与硬度增加。
在溶质原子浓度适当时,可提高材料的强度和硬度,而其韧性和塑性却有所下降。
3 )第二相强化。
复相合金与单相合金相比,除基体相以外,还有第二相得存在。
当第二相以细小弥散的微粒均匀分布于基体相中时,将会产生显著的强化作用。
第二相强化的主要原因是它们与位错间的交互作用,阻碍了位错运动,提高了合金的变形抗力。
4 )加工硬化(形变强化)。
金属在塑性变形时,晶粒发生滑移,出现位错的缠结,使晶粒拉长、破碎和纤维化,金属内部产生了残余应力等,因而继续塑性变形就变得困难,引起加工硬化。
( (1) 固溶强化; (2) 形变强化; (3) 沉淀强化和弥散强化; (4) 晶界和亚晶强化。
沉淀强化和细晶强化是工业合金中提高材料屈服强度的最常用的手段。
在这几种强化机制中,前三种机制在提高材料强度的同时,也降低了塑性,只有细化晶粒和亚晶,既能提高强度又能增加塑性。
)3.屈服强度在工程技术上有何用途?答:屈服强度的工程意义:①作为防止因材料过量塑性变形而导致机件失效的设计和选材依据;②根据屈服强度与抗拉强度之比(屈强比)的大小,衡量材料进一步产生塑性变形的倾向,作为金属材料冷塑性变形加工和确定机件缓解应力集中防止脆断的参考依据。
因为提高材料的屈服强度, 虽然可以减轻机件质量,不易使机件产生塑性变形失效, 但如果材料屈服强度与抗拉强度的比值增大,则不利于某些应力集中部位通过局部塑性变形使应力重新分布、缓解应力集中, 从而可能导致脆性断裂。
因此, 对于具体机件, 应选择具有多大数值的屈服强度的材料, 还应根据机件的形状、尺寸及服役条件而定,不一定一味追求高的屈服强度。
4.金属材料的应变硬化有何实际意义?答:应形变硬化标志金属继续塑性变形的抗力,是金属极为可贵的性质之一。
可以这样说,如果金属不具有形变硬化性质,金属材料就不可能得到现在这样广泛的运用。