纺丝工艺参数
静电纺丝评价标准

静电纺丝评价标准全文共四篇示例,供读者参考第一篇示例:静电纺丝技术是一种通过高电压静电场将高分子流体加工成纤维的方法。
它具有快速、高效、省时、易操作的特点,广泛应用于纺织、医疗、生物材料等领域。
由于静电纺丝技术的复杂性,评价其性能的标准也相对复杂。
本文将介绍静电纺丝技术的评价标准,希望能为相关领域的研究人员和工程师提供一些帮助。
一、纤维质量评价标准1. 纤维直径纤维的直径是评价静电纺丝产品质量的一个重要指标。
通常情况下,纤维直径越细,产品的性能越好。
通过测量纤维直径的分布情况,可以评估产品的均匀性和稳定性。
3. 纤维形态纤维的形态包括直线度、曲率等。
直线度越好的纤维产品,其使用性能和品质也就越好。
测量纤维的形态参数可以评估产品的加工性能和使用寿命。
4. 纤维结构纤维的结构包括表面形貌、孔隙率、结晶度等。
这些参数直接影响产品的力学性能、透气性和吸湿性等性能。
评估静电纺丝产品的结构特征是评价其质量的重要依据。
二、工艺参数评价标准1. 电场强度静电纺丝技术是通过高电压静电场将高分子流体加工成纤维的方法,因此电场强度是影响产品性能的一个重要参数。
合适的电场强度可以提高纤维的质量和产量,同时避免产品出现缺陷。
2. 喷丝速度喷丝速度是指高分子流体从喷嘴中喷出的速度。
过高或过低的喷丝速度都会影响纤维的形态和质量。
通过调节喷丝速度,可以获得理想的纤维产品。
3. 收集器距离收集器的距离是指纺丝喷嘴与纤维收集器之间的距离。
调节收集器的距离可以改变纤维的拉伸程度和排列密度,从而影响产品的性能和外观。
4. 加热温度加热温度是指高分子流体在静电场中受热之后的温度。
合适的加热温度可以使得高分子流体更容易被拉伸成纤维,并且有助于改善纤维的结晶度和强度。
三、应用性能评价标准1. 机械性能静电纺丝产品的机械性能包括拉伸强度、弹性模量等参数。
通过测量这些参数,可以评估产品的耐磨性、拉伸性和抗拉断性等性能。
2. 吸湿性能吸湿性能是一种评价纤维产品适用性的重要性能之一。
聚乙烯醇湿法纺丝 天津工业大学

实验参数设计第一纺丝盘纤度的计算由于喷丝头拉伸率应为1030选取20为本实验喷丝头拉伸率喷丝头拉伸率第一纺丝盘线速度喷出速率110002因为第一纺丝盘的线速度12m15s48mmin代入上述公式所以喷丝头速度6mmin因为每分钟喷出量等于供料量所以10000041066081063768rmin所以供料量3768rmin08mlr3014mlmin第一纺丝盘纤度100003014102016481000102dtex拉伸倍数的计算拉伸倍数第一纺丝盘纤度经拉伸后纤度62因为根据实验要求第一导丝盘拉伸一般在室温空气介质中进行拉伸率控制在80以下拉伸倍数18
因为 每分钟喷出量等于供料量 所以 1000*∏*(0.04)2*10-6*6/0.8*10-6=37.68 r/min 所以 供料量=(37.68 r/min)*(0.8ml/r)=30.14ml/min 第一纺丝盘纤度=10000*(30.14*1.02*0.16/4.8*1000)=10.2dtex
52[1].5dtex36f锦纶6POY试纺工艺
![52[1].5dtex36f锦纶6POY试纺工艺](https://img.taocdn.com/s3/m/ddde7d661ed9ad51f01df2ec.png)
! 统计数据#
世界产业用纺织品的最终消费预测
用 途
汽车用 产业用 家庭用 医疗用 建设用 农业用 衣料用 包装用 土木用 体育用 环境用 保护用 合 计
消费量 k t
1995 年
2005 年
1 918 1 523 1 439 1 177
849 741 647 423 251 237
2 483 2 344 2 259 1 652 1 266 1 021
速 0. 35 m s。
表 1 两种产品的纺丝组件压力及喷丝板对比
2 结果与讨论
2. 1 切片质量 由于在纺制多孔细旦锦纶 6 PO Y 时, 应相应提高纺
丝温度, 切片中可萃取物含量偏高时, 会严重影响板面清
规格 毛细孔径 (dtex f) mm
52. 5 12 0. 35 52. 5 36 0. 20
(长沙锦纶厂, 湖南, 410013)
摘 要: 介绍了在进口锦纶高速纺生产线上试纺锦纶 6 多孔细旦 PO Y 的生产工艺, 试生产证明调整和 稳定切片质量, 提高纺丝温度, 适当缩短喷丝板与上油嘴之间的距离, 采用合适的组件装配方式, 降低侧 吹风速度, 提高纺丝上油量等是生产锦纶 6 细旦丝的工艺技术关键。 主题词: 聚己内酰胺纤维 细旦纤维 预取向丝 纺丝
项 目
纤维原料 对苯二甲酸 乙二醇 对苯二甲酸二甲酯 己内酰胺 己二胺 丙烯腈 纤维聚合物 聚酯 聚酰胺 聚乙烯醇 合成纤维 涤纶 腈纶 丙纶
1997 年产量 k t
2 316 1 180
535 235
52 38 270 930 793 12 81 707 377 273 21
b. 严格控制锦纶 6 切片质量, 纺丝温度相应提高 5℃, 采取较低的侧吹风风速, 适当提高上油量, 缩短喷油 嘴与喷丝板之间的距离, 降低卷绕张力, 可以改善 PO Y 质量及卷绕成形。
静电纺丝技术

静电纺丝技术静电纺丝技术是利用高压静电作用使聚合物溶液或熔体带电并发生形变,在喷头末端处形成悬垂的锥状液滴,当液滴表面静电斥力大于其表面张力时,液滴表面就会喷射出高速飞行的射流,并在较短的时间内经电场力拉伸、溶剂挥发、聚合物固化形成纤维。
所获得的静电纺纤维直径小、比表面积大,同时纤维膜还具有孔径小、孔隙率高、孔道连通性好等优势,在过滤、传感、医疗卫生以及自清洁等领域具有广泛的应用。
1静电纺丝的起源与发展静电纺丝起源于200多年前人们对静电雾化过程的研究。
1745年,Bose通过对毛细管末端的水表面施加高电势,发现其表面将会有微细射流喷出,从而形成高度分散的气溶胶,并得出该现象是由液体表面的机械压力与电场力失衡所引起的。
1882年,Rayleigh指出当带电液滴表面的电荷斥力超过其表面张力时,就会在其表面形成微小的射流,并对该现象进行理论分析总结,得到射流形成的临界条件。
1902年,Cooley与Morton申请了第一个利用电荷对不同挥发性液体进行分散的专利。
随后Zeleny研究了毛细管端口处液体在高压静电作用下的分裂现象,通过观察总结出几种不同的射流形成模型,认为当液滴内压力与外界施加压力相等时,液滴将处于不稳定状态。
基于上述的基础研究,1929年,Hagiwara公开了一种以人造蚕丝胶体溶液为原料,通过高压静电制备人造蚕丝的专利。
1934年,Formhals设计了一种利用静电斥力来生产聚合物纤维的装置并申请了专利,该专利首次详细介绍了聚合物在高压电场作用下形成射流的原因,这被认为是静电纺丝技术制备纤维的开端。
从此,静电纺丝技术成为了一种制备超细纤维的有效可行方法。
1966年,Simons发明了一种生产静电纺纤维的装置,获得了具有不同堆积形态的纤维膜。
20世纪60年代,Taylor在研究电场力诱导液滴分裂的过程中发现,随着电压升高,带电液体会在毛细管末端逐渐形成一个半球形状的悬垂液滴,当液滴表面电荷斥力与聚合物溶液表面张力达到平衡时,带电液滴会变成圆锥形;当电荷斥力超过表面张力时,就会从圆锥形聚合物液滴表面喷射出液体射流。
DTY生产工艺及参数设定
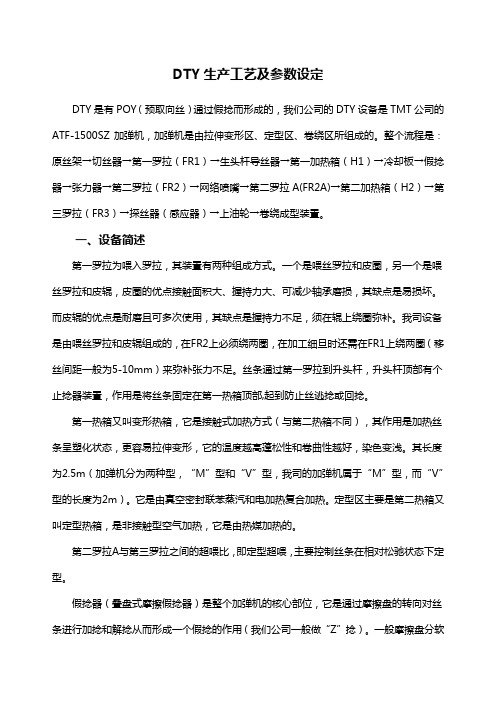
DTY生产工艺及参数设定DTY是有POY(预取向丝)通过假捻而形成的,我们公司的DTY设备是TMT公司的ATF-1500SZ加弹机,加弹机是由拉伸变形区、定型区、卷绕区所组成的。
整个流程是:原丝架→切丝器→第一罗拉(FR1)→生头杆导丝器→第一加热箱(H1)→冷却板→假捻器→张力器→第二罗拉(FR2)→网络喷嘴→第二罗拉A(FR2A)→第二加热箱(H2)→第三罗拉(FR3)→探丝器(感应器)→上油轮→卷绕成型装置。
一、设备简述第一罗拉为喂入罗拉,其装置有两种组成方式。
一个是喂丝罗拉和皮圈,另一个是喂丝罗拉和皮辊,皮圈的优点接触面积大、握持力大、可减少轴承磨损,其缺点是易损坏。
而皮辊的优点是耐磨且可多次使用,其缺点是握持力不足,须在辊上绕圈弥补。
我司设备是由喂丝罗拉和皮辊组成的,在FR2上必须绕两圈,在加工细旦时还需在FR1上绕两圈(移丝间距一般为5-10mm)来弥补张力不足。
丝条通过第一罗拉到升头杆,升头杆顶部有个止捻器装置,作用是将丝条固定在第一热箱顶部,起到防止丝逃捻或回捻。
第一热箱又叫变形热箱,它是接触式加热方式(与第二热箱不同),其作用是加热丝条呈塑化状态,更容易拉伸变形,它的温度越高蓬松性和卷曲性越好,染色变浅。
其长度为2.5m(加弹机分为两种型,“M”型和“V”型,我司的加弹机属于“M”型,而“V”型的长度为2m)。
它是由真空密封联苯蒸汽和电加热复合加热。
定型区主要是第二热箱又叫定型热箱,是非接触型空气加热,它是由热媒加热的。
第二罗拉A与第三罗拉之间的超喂比,即定型超喂,主要控制丝条在相对松驰状态下定型。
假捻器(叠盘式摩擦假捻器)是整个加弹机的核心部位,它是通过摩擦盘的转向对丝条进行加捻和解捻从而形成一个假捻的作用(我们公司一般做“Z”捻)。
一般摩擦盘分软盘(聚氨酯PU盘等)和硬盘(陶瓷盘、砂盘等),软盘摩擦系数高、表面柔软、对丝条损伤小、“雪花少”但使用寿命短成本贵;而硬盘与软盘反之。
化纤公司纺丝部纺丝主要的工艺参数
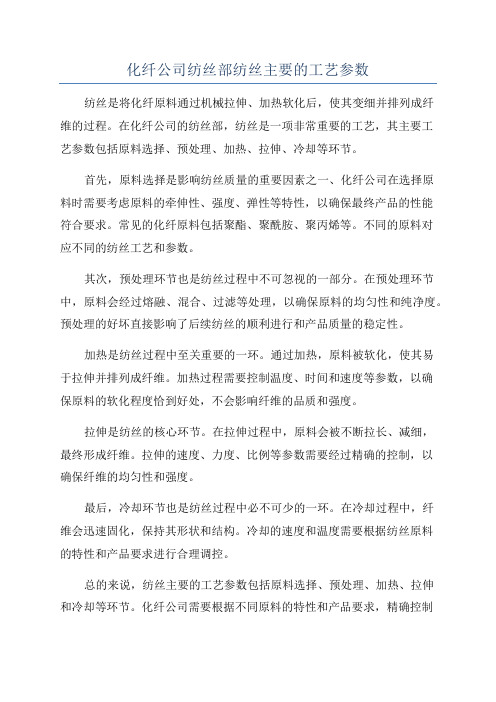
化纤公司纺丝部纺丝主要的工艺参数纺丝是将化纤原料通过机械拉伸、加热软化后,使其变细并排列成纤维的过程。
在化纤公司的纺丝部,纺丝是一项非常重要的工艺,其主要工艺参数包括原料选择、预处理、加热、拉伸、冷却等环节。
首先,原料选择是影响纺丝质量的重要因素之一、化纤公司在选择原料时需要考虑原料的牵伸性、强度、弹性等特性,以确保最终产品的性能符合要求。
常见的化纤原料包括聚酯、聚酰胺、聚丙烯等。
不同的原料对应不同的纺丝工艺和参数。
其次,预处理环节也是纺丝过程中不可忽视的一部分。
在预处理环节中,原料会经过熔融、混合、过滤等处理,以确保原料的均匀性和纯净度。
预处理的好坏直接影响了后续纺丝的顺利进行和产品质量的稳定性。
加热是纺丝过程中至关重要的一环。
通过加热,原料被软化,使其易于拉伸并排列成纤维。
加热过程需要控制温度、时间和速度等参数,以确保原料的软化程度恰到好处,不会影响纤维的品质和强度。
拉伸是纺丝的核心环节。
在拉伸过程中,原料会被不断拉长、减细,最终形成纤维。
拉伸的速度、力度、比例等参数需要经过精确的控制,以确保纤维的均匀性和强度。
最后,冷却环节也是纺丝过程中必不可少的一环。
在冷却过程中,纤维会迅速固化,保持其形状和结构。
冷却的速度和温度需要根据纺丝原料的特性和产品要求进行合理调控。
总的来说,纺丝主要的工艺参数包括原料选择、预处理、加热、拉伸和冷却等环节。
化纤公司需要根据不同原料的特性和产品要求,精确控制这些参数,以确保纺丝过程的顺利进行和产品质量的稳定性。
只有做到这些,才能生产出符合市场需求的高质量化纤产品。
化纤公司纺丝部纺丝主要的工艺参数

化纤公司纺丝部纺丝主要的工艺参数化纤公司的纺丝部是进行化纤纺丝生产的重要部门之一,其主要工艺参数包括纺丝温度、纺丝速度、纺丝压力、纺丝张力、喷丝气压等。
下面将详细介绍这些工艺参数。
首先,纺丝温度是纺丝工艺中的一个关键参数。
纺丝温度的控制能够影响纺丝质量和纺丝速度。
通常情况下,纺丝温度较高可以提高纺丝速度,但过高的温度会引起纤维熔化或起糊化现象,降低纺丝质量。
因此,在确定纺丝温度时需要进行适当的调整和控制。
其次,纺丝速度是指纺丝过程中纤维经过纺丝机头的速度。
纺丝速度对纺丝质量和产量起着重要的影响。
纺丝速度较高时,可以提高生产效率,但也容易产生纤维断裂或其他质量问题。
因此,纺丝速度需要在一定范围内进行调整和控制。
纺丝压力是纺丝过程中纤维在纺丝机头内部受到的压力。
纺丝压力的大小决定了纤维在纺丝机头内部的受力情况,进而影响纤维的拉伸程度和纺丝质量。
通常情况下,纺丝压力较高可以提高纤维的拉伸程度,但过高的压力会导致纤维断裂或其他质量问题。
因此,在确定纺丝压力时需要进行适当的调整和控制。
纺丝张力是指纺丝过程中纤维受到的张力大小。
纺丝张力对纺丝质量和产量也有重要的影响。
纺丝张力较大时,可以提高纤维的拉伸程度,但过大的张力会导致纤维断裂或其他质量问题。
因此,在确定纺丝张力时需要进行适当的调整和控制。
喷丝气压是指喷丝装置通过喷嘴向纺丝机头注入的气体压力。
喷丝气压的大小会影响纤维在纺丝机头内部的流动情况和纺丝质量。
通常情况下,喷丝气压较大可以提高纤维的流动性,但过大的气压会引起纺丝乱流或其他质量问题。
因此,在确定喷丝气压时需要进行适当的调整和控制。
综上所述,化纤公司纺丝部的纺丝主要工艺参数包括纺丝温度、纺丝速度、纺丝压力、纺丝张力、喷丝气压等。
这些参数的合理控制和调整,对于保证化纤纺丝质量和提高生产效率具有重要意义。
芳纶纺丝关键技术
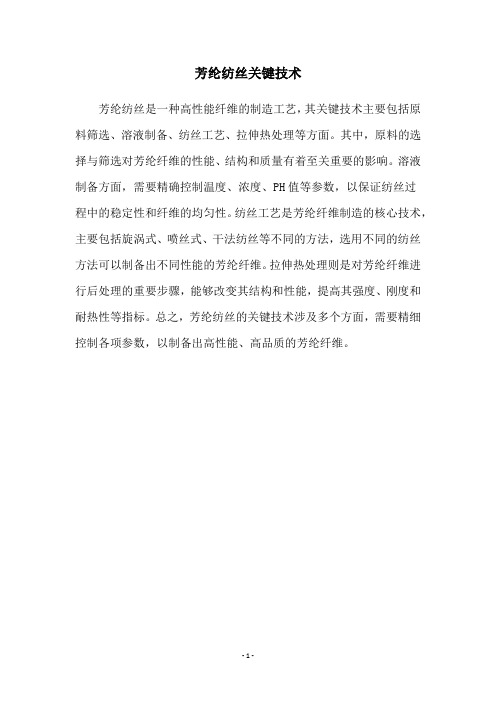
芳纶纺丝关键技术
芳纶纺丝是一种高性能纤维的制造工艺,其关键技术主要包括原料筛选、溶液制备、纺丝工艺、拉伸热处理等方面。
其中,原料的选择与筛选对芳纶纤维的性能、结构和质量有着至关重要的影响。
溶液制备方面,需要精确控制温度、浓度、PH值等参数,以保证纺丝过
程中的稳定性和纤维的均匀性。
纺丝工艺是芳纶纤维制造的核心技术,主要包括旋涡式、喷丝式、干法纺丝等不同的方法,选用不同的纺丝方法可以制备出不同性能的芳纶纤维。
拉伸热处理则是对芳纶纤维进行后处理的重要步骤,能够改变其结构和性能,提高其强度、刚度和耐热性等指标。
总之,芳纶纺丝的关键技术涉及多个方面,需要精细控制各项参数,以制备出高性能、高品质的芳纶纤维。
- 1 -。
静电纺丝技术的工艺原理及应用

静电纺丝技术的工艺原理及应用静电纺丝技术是目前制备纳米纤维最重要的基本方法。
这一技术的核心是使带电荷流体在静电场中流动与变形,最终得到纤维状物质,从而为高分子成为纳米功能材料提供了一种新的加工方法。
由于纳米纤维具有许多特性,例如纤维纤度细、比表面积大、孔隙率高,因而具有广泛的应用。
1、静电纺技术静电纺是一项简单方便、廉价而且对环境无污染的纺丝技术。
早在20世纪30年代,Formals A就已经在其专利中报道了利用高压静电纺丝,但是直到近些年,由于对纳米科技研究的迅速升温,激起了人们对这种可制备纳米尺寸纤维的纺丝技术进行深入研究的浓厚兴趣。
1.1 静电纺技术的基本原理静电纺丝技术(Electrospinning fiber technique)是使带电的高分子溶液(或熔体)在静电场中流动变形,经溶剂蒸发或熔体冷却而固化,从而得到纤维状物质的一种方法。
对聚合物纤维电纺过程的图式说明见图1。
静电纺丝机的基本组成主要有3个部分:静电高压电源、液体供给装置、纤维收集装置。
静电高压电源根据电流变换方式可以分成DC/DC和AC/DC两种类型,实验中多用IX;/DC电源。
液体供给装置是一端带有毛细管的容器(如注射器),其中盛有高分子溶液或熔体,将一金属线的一端伸进容器中,使液体与高压电发生器的正极相连。
纤维收集装置是在毛细管相对端设置的技术收集板,可以是金属类平面(如锡纸)或者是旋转的滚轮等。
收集板用导线接地,作为负极,并与高压电源负极相连。
另外随着对实验要求的提高,液体流量控制系统也被渐渐的采用,这样可以将液体的流速控制得更准确。
电场的大小与毛细管口聚合物溶液的表面张力有关。
由于电场的作用,聚合物溶液表面会产生电荷。
电荷相互排斥和相反电荷电极对表面电荷的压缩,均会直接产生一种与表面张力相反的力。
当电场强度增加时,毛细管口的流体半球表面会被拉成锥形,称为Taylor锥。
进一步增加电场强度,是用来克服表面张力的静电排斥力到达一个临界值,此时带电射流从Taylor锥尖喷射出来。
高速纺丝主要工艺参数

一、高速纺丝主要工艺参数1、纺丝温度:包括螺杆温度,箱体温度,联苯温度等。
一般在275~295℃之间。
2、熔体压力:包括滤前压,滤后压力和组件压力;滤后压力一般疫定在80~100BAR之间;组件压力一般在80~150BAR之间。
3、侧吹风:包括风速成(风压),风湿。
风速在0、3~ 0。
5m/s左右;风温20±2℃左右;风湿65±5﹪左右。
4、集束上油们置:一般根据纺制品种和所需纺丝张力迁当调节上油们置。
通常集束上尚未位置离喷丝板面的垂直距离控制在130~160cm左右;水平位于控制在离侧吹风网面22~23cm左右。
5、计量泵和油剂泵转速:计量泵转速根椐年纺品种的规格计算而得;油剂泵转速则根据丝条所需上油率而定,P0Y上油控制在0。
3~0。
7。
另外:纺间的温度、湿度、室内空气气流等环境对纤维成形也有一定的影响,一般要求温度25左右;湿度65﹪左右,室内空气无紊流干扰。
二、高速纺丝采用何种方式上油?高速成纺丝纺速高,必须使用油嘴上油方式才能保证计量准确各个部位上油量比较一致。
无油丝不但影响纺丝成型,而且直接后加工的正常进行,造成无法退绕,断头和无强力丝的出现,要杜绝无油丝产生。
三、POY含油一般以0.3~0.7﹪左右较为适当。
丝条含油率低会使纤维松散,摩擦阻力增大,发生毛丝;若含油量过高,会造成油污染增加。
四、造成纺丝细丝的原因有哪些?主要原因是组件原因:1、喷丝板镜检不干净;2、分配板不干净;3、组件组装不合格;4、铲板不及时等,出现这种情况,应立即铲板或更换组件。
五、在什么情况下需要紧急更换组件?1、纺丝发生细丝,硬头丝、竹节丝等不正常丝,经板面清理后仍不能清除;2、组件漏浆严重,无法正常生产;3、卷绕毛丝、断头多,检查导丝器,丝道无损伤。
六、熔体压力有哪三种?怎样设定熔体压力?熔体压力通常有螺杆出口压力(一般系过滤器前压)、滤后压力和组件压力三种。
滤后压力的确定一般是减去熔体管道的压力损失,保证熔体进入计量泵前的工作压力(一般不低于3.0MPa),不致使各计量泵吐出量有差异。
涤纶短纤维纺丝工艺及其影响因素.

• (2)风湿: 65~85%;风湿对卷绕丝双折射率和纺丝稳定性 影响大 影响:冷却风带湿度→卷绕丝在纺丝甬道中的带电↓→飘丝↓
→空气比热和热焓↑→纺丝甬道中冷却风和丝束温度恒定
8
• (三)丝条冷却固化条件 • (3)风速(风量) :0.3~0.7m/s,与熔体吐出量有 关 • (4)吹出距离(缓冷区):吹风窗(环)与板面距 离 ,15cm;吹风面距丝束外缘距离1cm;高度20cm;环吹 头内经比喷丝板直径大2cm;风经倾斜多孔板到阻尼 层(由金属网、金属毡等材料制成)再送入纺丝筒 • (5)纺丝甬道:保护纤维并继续冷却。3.2-7m,圆 管Φ280mm。一般3.5m,甬道长,气流紊乱,湍流 严重,丝的摆动幅度大,碰撞摩擦
线密度波动
组件结构
13
7
• (孔分配板-纺 丝筒 • 2.工艺控制: • (1)风温:范围:20~30℃,±1 ℃,组件调换率、卷绕丝 双折射率、卷绕丝条干不匀率最低
影响: 风温↑→熔体丝条冷却不充分→并丝、粘结丝↑→卷绕丝条干不匀率↑ 风温↓→熔体在喷丝孔处快速冷却→拉伸应力↑→初生纤维预取向度↑,径向 双折射率差异大→纺丝性↓→能耗大
4
• 3.熔体均匀性 • (1)粘度:切片结构不匀或有凝胶粒子使粘
度不匀,从而使丝条结构不匀,出现硬头丝, 导致拉伸不匀 • (2)杂质:会阻塞喷丝孔,造成滤层压力升 高和使用周期缩短
• 熔体粘度不匀或存在胶粒会导致纺丝断头、线密度 不匀、产生硬头丝、后拉伸困难、染色不匀等缺陷
• 原因: • 原料差异;干燥均匀;熔融和纺丝过程杜绝与 氧气接触,防止氧化降解;控制加热区温度, 减少波动
10
• 2.纺丝(卷绕)速度:指牵引辊1000m/min • 影响:纺速↑→纺丝线上速度梯度↑、丝束与冷空气的摩擦阻 力↑→ 卷绕丝预取向度↑(双折射↑)、后拉伸倍数↓(初生 纤维内应力增大,沸水收缩率增大) 纺速↓→丝束张力↓→卷绕时发生跳动→纺丝稳定性↓、并丝↑ 喂入轮的速度:约提高1% • 3.喷丝头拉伸比:第一导丝盘速度与熔体喷出速度之比 • 影响:喷丝头拉伸比↑→后拉伸倍数↓→对卷绕丝预取向度影 响小 • 4.卷绕车间温湿度:夏20~27℃,冬20℃ ;相对湿度 60~75%
FDYPA6纺丝工艺设计

40d/34f半消光FDY PA6 纺丝工艺的设计1、引言聚酰胺(PA,俗称尼龙)是美国DuPont公司最先开发用于纤维的树脂,于1939年实现工业化。
20世纪50年代开始开发和生产注塑制品,以取代金属满足下游工业制品轻量化、降低成本要求。
尼龙系列是最重要的工程塑料,品种繁多,主要品种是尼龙6和尼龙66,从性能和价格综合考虑,PA6和PA66的市场用量占PA总量的90%左右,占绝对主导地位。
PA是历史悠久、用途广泛的通用工程塑料,2000年世界工程塑料市场分配为PA 35%。
2001年世界PA6的消费量为68万吨。
欧洲消费结构为PA6占50%,PA66占40%,美国PA66用量超过其它品种,日本则聚酰胺PA6消费居首位,为52%。
PA工程塑料以注射成型为主,注塑制品占PA制品的90%左右,PA6与PA66的成型加工工艺不尽相同,PA66基本都采用注塑加工,占95%,挤出成型仅占5%;PA6的注塑制品占70%,挤出成型占30%。
PA6由于其优异的耐热性能、耐磨擦和耐腐蚀性能,被广泛应用于工程塑料和纤维材料领域。
特别是PA6纤维染色性能较强,因此被大量用来生产服装面料,是仅次于涤纶的第二大纤维品种。
以PA6材料制成的合成纤维称为聚酰胺纤维。
我国称聚酰胺纤维为“锦纶”,锦纶6切片通常呈白色,柱形或圆球形颗粒状。
PA6切片是以己内酰胺(CPL)为原料,水为开环剂以及消光剂二氧化钛和稳定剂的调配液的作用下发生加成和缩聚反应产生的。
2、总论以PA6材料制成的纤维称为聚酰胺纤维,又称“锦纶”,锦纶6切片通常呈白色,柱形颗粒状,熔点为210—220℃,分解温度为300℃左右,可溶于苯酚和浓硫酸中。
一般的聚合装置生产切片都是采用己内酰胺水解开环工艺,即己内酰胺在有水的情况下生成ε氨基己酸,再由ε氨基己酸与单分子己内酰胺分迅速发生加成反应和缩聚反应,链不断增长并最终达到所要求的分子量。
PA6这种纤维具有优异的耐磨性,回弹性和耐多次变形性能,广泛用于制做袜子、内衣、运动衣、轮胎帘子线、工业带材、渔网、军用织物等。
静电纺丝工艺

静电纺丝工艺
一、溶液制备
静电纺丝工艺的第一步是制备纺丝溶液。
这一过程涉及到将聚合物溶解在适当的溶剂中,形成均一的溶液。
为了获得最佳的纺丝效果,需要控制溶液的粘度、浓度以及溶剂的蒸发速率。
通常,聚合物在溶剂中的溶解度越高,溶液的粘度越低,越有利于纺丝。
二、静电纺丝
在制备好纺丝溶液后,通过静电纺丝设备进行纺丝。
静电纺丝过程中,高压电场施加在喷嘴和收集器之间,使得溶液形成细流并射出。
在电场的作用下,细流会逐渐拉伸、细化,最终形成纤维。
这一过程中,可以通过调整电场强度、溶液流量以及喷嘴到收集器的距离等参数来控制纤维的形貌和直径。
三、收集与处理
纺出的纤维会落在收集器上,形成非织造布状的纤维膜。
为了获得实用的纤维材料,通常需要对收集到的纤维进行后处理。
这包括洗涤以去除残留的溶剂和杂质,以及热处理或化学处理以改善纤维的性能。
四、应用与性能测试
静电纺丝工艺制备的纤维材料在许多领域都有广泛的应用,如过滤、增强、生物医学等。
对于不同的应用,纤维材料的性能要求也不同。
因此,需要对制备的纤维材料进行性能测试,以满足实际需求。
常见的性能测试包括纤维直径、形貌、力学性能、热性能、电性能等。
总之,静电纺丝工艺是一种简单、环保的制备纤维材料的方法。
通过合理的工艺参数选择和控制,可以制备出具有优异性能的纤维材料,满足各种应用需求。
纺丝各工序要求及原理

一、【涤纶长丝的物理指标】1、线密度是表示长丝粗细的指标,用分特(dtex)表示。
10000m长纤维的重量克数为分特数。
也有用特数(tex)表示的。
1特等于10分特。
2、断裂强度是反映长丝质量的一项重要指标。
断裂强度高,长丝在加工过程中不易断头、绕辊,最终做成的纱线和织物的强力也高。
但断裂强度太高,纤维刚性增加,纱线和织物的手感变差。
3、断裂伸长率断裂伸长率是一种反映纤维韧性的指标。
对于衣着长丝,伸长率愈大,手感愈柔软,后加工毛丝、断头较少,但过大时,织物易变形。
4、条干不匀率是一种表示长丝条干均匀度的指标。
这项指标对预取向丝的拉伸丝尤为重要。
长丝条干不匀,在加工过程中容易产生毛丝和染色不匀。
5、沸水收缩率定长的长丝放在沸水中煮沸一定时间后,其收缩的长度与原来长度的比值称为沸水收缩率。
用百分数表示。
沸水收缩率是一种反映长丝热定型程度和尺寸稳定性的指标,与染色性能有一定关系。
二、【长丝对切片质量的要求】特性粘数为了使产品具有适当的物理机械性能,又能顺利纺丝,要求聚酯切片有适当的分子量。
而测定分子量及其分布的方法烦杂,故用特性粘数表示其分子量的大小。
凝聚粒子如氧化凝胶物、二氧化钛凝聚物以及在反应釜壁上生成的高熔点物、碳化物等,这些杂质不仅加重了熔体预过滤器或组件过滤层的负荷,而且还极易导致毛丝和断头。
端羧基含量端羧基含量高,说明分子量分布宽,可纺性差。
制得的成品在热态使用条件下,会导致聚酯大分子的降解加剧。
二氧化钛含量在能取得较好的消光效果的前提下,二氧化钛的含量应尽量低,并分布均匀、粒子细。
铁质含铁量高,会使纤维发黄,色泽变差。
三、【可纺性表现特征】预过滤器或纺丝组件的升压速率曰升压速率,高速纺丝应小于10%,常规纺丝应小于6%,否则,易出现染色不匀和毛丝、断头等问题。
拉伸断头率和绕辊率在拉伸张力下,纤维内部的缺陷最容易暴露。
可纺性好的切片,拉伸时,断头率和绕辊率均较低。
四、【长丝对切片干燥的要求】除去切片中的水分,可避免聚酯高分子在纺丝过程中剧烈的水解,剧烈的水解使分子量降低,丝的质量下降,甚至无法纺丝。
熔融纺丝法简介

熔体从喷丝孔高速挤出时,随着纺丝流体粘弹性和挤出条件 的不同,挤出细流的类型分为液滴型、慢流型、胀大型和破 裂型。
• 胀大型是高聚物熔体纺丝的正常现象,是由于高聚物熔体 的粘弹性中的弹性决定的,只要控制好纺丝工艺条件,尽 量减小胀大比,不应性纺丝过程的正常进行。其它三种类 型细流是纺丝不稳定性的表现,应该避免发生。
• 液滴型不能成为连续细流,纤维无法成形;液滴型出现的 条件首先与纺丝流体的性质有关。流体表面张力α越大, 则细流缩小其表面积成为液滴的倾向也越大。此外,粘度 η的下降也促使液滴的生成。 • 漫流型虽已形成连续细流,但纺丝流体在流出喷丝孔后, 迅即沿喷丝板表面漫流。这种细流很不稳定,纺丝往往因 而中断;为避免漫流型细流的出现,应设法提高η和R0 或 降低界面张力
主要步骤: 高聚物纺丝熔体的制备 熔体自喷丝孔挤出/纺丝 挤出的熔体细流的冷却和拉伸成形 成形的纤维长丝铺网与固网
熔体纺丝工艺主要包 括:成纤聚合物在螺杆挤 出机中加热熔融,熔体通 过计量泵从喷丝孔挤出形 成细流,熔体细流冷却固 化,丝条经上油和卷绕, 被拉伸变细而得纤维。
熔体粘度和温度是熔体纺丝的主要工艺参数。在一定 温度下,熔体粘度主要取决于成纤聚合物的分子量。熔体 粘度过高,则流动不均匀,使出生纤维拉伸时易产生毛丝、 断头;熔体温度可利用螺杆挤出机各段的温度来控制,熔 体温度过高,会导致聚合物降解和形成气泡;温度过低, 则熔体粘度过高;两者均使纺丝过程不能正常进行
?高聚物流体通过喷丝孔的流动有明显的流场变的流动有明显的流场变化而包括毛细孔入口区的收敛流场毛细孔区的管道流动以及毛细孔出口区向拉伸流动的流场过渡?形变区也称冷凝区这是纺丝成形过程中最重要的区域
熔融纺丝
合成纤维的生产首先是将单体经聚合反应制 成成纤高 聚物,这些聚合反应原理、生产过程及设备与合成树脂、 合成橡胶的生产大同小异,不同的是合成纤维要经过纺丝 及后加工,才能成为合格的纺织纤维。 溶液纺丝又分为湿法纺丝和干法纺丝两种。
- 1、下载文档前请自行甄别文档内容的完整性,平台不提供额外的编辑、内容补充、找答案等附加服务。
- 2、"仅部分预览"的文档,不可在线预览部分如存在完整性等问题,可反馈申请退款(可完整预览的文档不适用该条件!)。
- 3、如文档侵犯您的权益,请联系客服反馈,我们会尽快为您处理(人工客服工作时间:9:00-18:30)。
纺丝工艺参数
1. 1 熔体输送温度
涤纶长丝生产的可纺性要求熔体黏度降越小越好, 所以熔体输送温度不能控制得太高, 太高会形成较大的黏度降, 影响纺丝生产;但纺制超粗旦丝熔体流量较大, 输送温度太低会使熔体输送管内层与外层温度差异增大, 影响熔体输送的流动均匀性, 从而会影响纺丝加工及产品质量。
所以要在保证熔体输送良好的前提下, 尽量降低熔体输送温度, 控制熔体黏度降。
可以通过降低熔体输送管线及热交换器的保温热媒温度来降低熔体输送温度, 达到减小黏度降的目的。
1. 2 纺丝温度
对于超粗旦纤维, 纺丝温度的控制至关重要。
可以通过纺丝温度的调节来有效改变熔体的流变性能, 同时纺丝温度对可纺性影响也较明显。
较高的温度有利于纺丝, 但会增加纺丝的毛丝和断头。
在工艺调试中发现, 在纺丝温度高于287 ℃时, 纺丝飘丝会增加, 铲板困难( 粘板严重) 。
同时组件压力的大小也会影响到熔体的流变性能, 所以纺丝温度要结合组件压力的情况调整。
较高的组件压力可适当降低黏度, 改善熔体的流变性能。
本工艺就是选择较高的组件压力( 17MP a ) 进行生产。
试验证明, 在较高的组件压力下, 纺丝温度控制在284 ℃较为合理。
1. 3 冷却条件和集束点的确定
冷却条件对超粗旦涤纶长丝影响较大, 粗旦纤维要求冷却均匀。
而超粗纤维DP F 较大, 冷却太快会使单丝冷却产生差异, 造成皮芯结构, 染色均匀性变差, 影响产品质量。
超粗旦纤维采用侧吹风冷却, 靠近整流屏的纤维冷却较快,
远离整流屏的纤维冷却较慢, 纤维之间会形成差异。
本工艺在纺丝缓冷区采用弧形板技术, 有效地减少了野风对缓冷区的干扰, 同时使丝层内外冷却更均匀一致。
超粗旦纤维冷却相对较慢, 所以集束点不应靠上, 防止丝条未完全冷却而过早集束, 从而影响纺丝生产及产品质量。
经过试验论证, 集束点选在1 500 mm较为理想。
1. 4 上油
由于纤维总纤度较大, 需要上油量较大, 生产时发现油嘴处会出现滴油、溅油等现象, 同时还发现油嘴发烫, 影响上油的均匀性。
经过查找发现, 在线使用的油嘴宽度较小, 出油孔较小,造成了上述异常。
更换大油嘴( 京瓷、杜塞拉姆等) 进行试验, 解决了难题。
1. 5 合股位置的选择
加工合股丝, 合股位置是关键。
本工艺调试时进行了多次实验, 丝束过了第二导丝盘合股,加工稳定, 毛丝等外观降等少。
但由于是单股网络后合股, 两束丝间抱合不好, 后加工时容易分散, 影响产品质量。
丝束在第一导丝盘前合股时, 会产生少量毛丝等外观异常情况, 但纤维抱合性较好, 能形成较好的预网络, 退绕成功率高。