无缝钢管超声探伤报告
无缝钢管检测报告
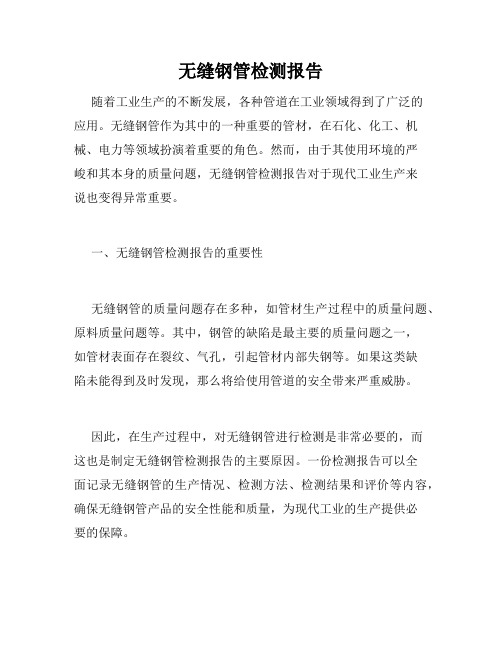
无缝钢管检测报告随着工业生产的不断发展,各种管道在工业领域得到了广泛的应用。
无缝钢管作为其中的一种重要的管材,在石化、化工、机械、电力等领域扮演着重要的角色。
然而,由于其使用环境的严峻和其本身的质量问题,无缝钢管检测报告对于现代工业生产来说也变得异常重要。
一、无缝钢管检测报告的重要性无缝钢管的质量问题存在多种,如管材生产过程中的质量问题、原料质量问题等。
其中,钢管的缺陷是最主要的质量问题之一,如管材表面存在裂纹、气孔,引起管材内部失钢等。
如果这类缺陷未能得到及时发现,那么将给使用管道的安全带来严重威胁。
因此,在生产过程中,对无缝钢管进行检测是非常必要的,而这也是制定无缝钢管检测报告的主要原因。
一份检测报告可以全面记录无缝钢管的生产情况、检测方法、检测结果和评价等内容,确保无缝钢管产品的安全性能和质量,为现代工业的生产提供必要的保障。
二、无缝钢管检测报告的检测方法无缝钢管检测报告的检测方法有很多种,如钢管外观检测、尺寸检测、材质成分检测、物理性能检测等。
其中,超声波探伤和射线探伤是无缝钢管检测中最常用的两种方法。
超声波探伤是利用超声波在材料中传播时的声波特性,通过探伤头对材料的内部进行检测。
这种方法可以检测出管道内部的各种缺陷,如气孔、裂纹、夹杂等,具有很高的检测精度和可靠性。
射线探伤是利用射线通过被检测管道后,通过照片进行分析来判断管道内部存在的缺陷。
该方法可以检测出管道内部的各种缺陷,如气孔、裂纹、夹杂等,具有极高的灵敏度和可靠性。
三、无缝钢管检测报告的内容要素无缝钢管检测报告应该包含的内容要素十分重要,主要包括破坏性试验结果、无损检测结果、化学成分、金相结构以及技术性能等各方面的内容,全面详实地反映出无缝钢管的质量情况,为无缝钢管的使用提供保障。
其中,破坏性试验结果反映出管道的奇强抗压、抗拉等性能,是管道质量的重要评价指标。
无损检测结果反映出管道内部的缺陷情况,是管道质量的重要检测指标。
化学成分和金相结构反映出管道材料的成分和组织结构,是管道质量的重要技术参数。
无缝管探伤报告

无缝管探伤报告1. 引言无缝管是一种常见的管道材料,在工业生产领域中广泛应用。
为了确保管道的安全和可靠性,对无缝管进行探伤是至关重要的。
本报告将介绍对无缝管进行探伤的方法和结果。
2. 探伤方法无缝管的探伤方法主要包括磁粉探伤和超声波探伤两种。
2.1 磁粉探伤磁粉探伤是一种使用磁场和铁粉的方法来检测管道表面和内部缺陷的技术。
首先,将磁粉涂布在无缝管的表面,然后施加磁场。
如果管道上存在裂纹、缺陷等问题,磁粉会被吸附在缺陷处,形成可见的指示。
2.2 超声波探伤超声波探伤是一种利用超声波在材料中传播和反射的原理来检测管道内部缺陷的方法。
通过向无缝管内部发送超声波,并监听返回的信号,可以确定管道中是否存在问题。
超声波探伤可以检测到更小的缺陷,并且可以提供更准确的缺陷位置和尺寸信息。
3. 探伤结果对于本次无缝管的探伤,使用了磁粉探伤和超声波探伤两种方法进行检测。
以下是探伤结果的总结:•样品1:经过磁粉探伤和超声波探伤,未发现任何缺陷或问题。
•样品2:磁粉探伤检测到管道表面存在少量的裂纹,经过超声波探伤确认裂纹小于0.5mm。
•样品3:经过磁粉探伤和超声波探伤,未发现任何缺陷或问题。
4. 结论通过本次无缝管的探伤,可以得出以下结论:•样品1符合探伤要求,可以使用于工业生产。
•样品2存在少量的裂纹,但尺寸较小,可以采取相应补救措施。
•样品3符合探伤要求,可以使用于工业生产。
5. 建议基于本次探伤结果,对无缝管的生产和使用提出以下建议:•对生产过程进行质量检查,以减少可能导致裂纹产生的因素。
•对样品2进行进一步的检测和修复,确保裂纹的尺寸符合安全要求。
•对无缝管的使用过程进行监测和维护,及时发现和处理可能出现的缺陷。
6. 总结本文报告了对无缝管进行探伤的方法和结果。
通过磁粉探伤和超声波探伤,可以有效地检测管道表面和内部的缺陷,并提供相关的缺陷信息。
根据探伤结果,可以对无缝管的生产和使用提出相应的建议,以确保管道的安全和可靠性。
无缝钢管探伤报告以及与直缝焊管的明显区别
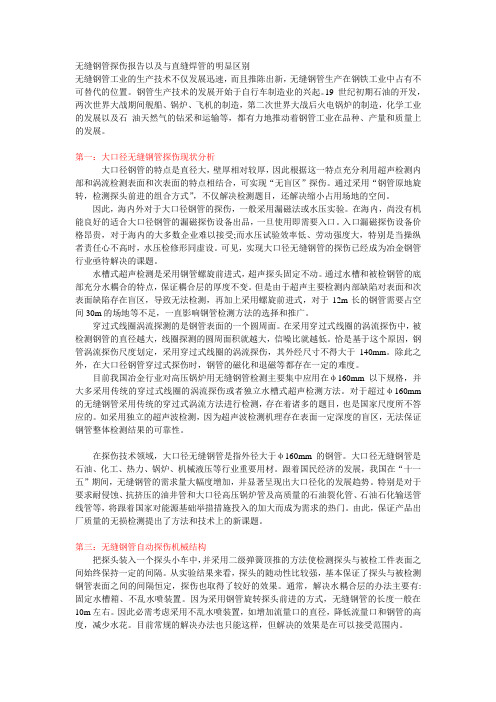
无缝钢管探伤报告以及与直缝焊管的明显区别无缝钢管工业的生产技术不仅发展迅速,而且推陈出新,无缝钢管生产在钢铁工业中占有不可替代的位置。
钢管生产技术的发展开始于自行车制造业的兴起。
19 世纪初期石油的开发,两次世界大战期间舰船、锅炉、飞机的制造,第二次世界大战后火电锅炉的制造,化学工业的发展以及石油天然气的钻采和运输等,都有力地推动着钢管工业在品种、产量和质量上的发展。
第一:大口径无缝钢管探伤现状分析大口径钢管的特点是直径大,壁厚相对较厚,因此根据这一特点充分利用超声检测内部和涡流检测表面和次表面的特点相结合,可实现“无盲区”探伤。
通过采用“钢管原地旋转,检测探头前进的组合方式”,不仅解决检测题目,还解决缩小占用场地的空间。
因此,海内外对于大口径钢管的探伤,一般采用漏磁法或水压实验。
在海内,尚没有机能良好的适合大口径钢管的漏磁探伤设备出品,一旦使用即需要入口。
入口漏磁探伤设备价格昂贵,对于海内的大多数企业难以接受;而水压试验效率低、劳动强度大,特别是当操纵者责任心不高时,水压检修形同虚设。
可见,实现大口径无缝钢管的探伤已经成为冶金钢管行业亟待解决的课题。
水槽式超声检测是采用钢管螺旋前进式,超声探头固定不动。
通过水槽和被检钢管的底部充分水耦合的特点,保证耦合层的厚度不变。
但是由于超声主要检测内部缺陷对表面和次表面缺陷存在盲区,导致无法检测,再加上采用螺旋前进式,对于12m长的钢管需要占空间30m的场地等不足,一直影响钢管检测方法的选择和推广。
穿过式线圈涡流探测的是钢管表面的一个圆周面。
在采用穿过式线圈的涡流探伤中,被检测钢管的直径越大,线圈探测的圆周面积就越大,信噪比就越低。
恰是基于这个原因,钢管涡流探伤尺度划定,采用穿过式线圈的涡流探伤,其外经尺寸不得大于140mm。
除此之外,在大口径钢管穿过式探伤时,钢管的磁化和退磁等都存在一定的难度。
目前我国冶金行业对高压锅炉用无缝钢管检测主要集中应用在φ160mm以下规格,并大多采用传统的穿过式线圈的涡流探伤或者独立水槽式超声检测方法。
无缝钢管检测报告
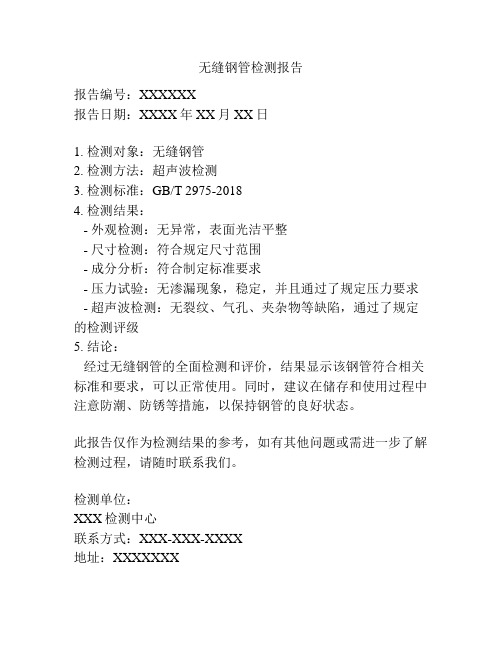
无缝钢管检测报告
报告编号:XXXXXX
报告日期:XXXX年XX月XX日
1. 检测对象:无缝钢管
2. 检测方法:超声波检测
3. 检测标准:GB/T 2975-2018
4. 检测结果:
- 外观检测:无异常,表面光洁平整
- 尺寸检测:符合规定尺寸范围
- 成分分析:符合制定标准要求
- 压力试验:无渗漏现象,稳定,并且通过了规定压力要求 - 超声波检测:无裂纹、气孔、夹杂物等缺陷,通过了规定的检测评级
5. 结论:
经过无缝钢管的全面检测和评价,结果显示该钢管符合相关标准和要求,可以正常使用。
同时,建议在储存和使用过程中注意防潮、防锈等措施,以保持钢管的良好状态。
此报告仅作为检测结果的参考,如有其他问题或需进一步了解检测过程,请随时联系我们。
检测单位:
XXX检测中心
联系方式:XXX-XXX-XXXX
地址:XXXXXXX。
钢管超声波探伤报告

V型坡口
补偿(dB)
4dB
缺陷总长
0
焊接方法
手工电弧焊
检查面状况
打磨良好
返修情况
无返修
探 伤 面
焊缝单面双侧
探伤时机
焊后24小时
检测结果
合格
焊缝宽度
12-14㎜
探头参数
2.5P8×12K2
实测m
Z1
3089mm
Z2 H1
2700mm
焊缝编号
缺陷深度
MDJ7
MDJ4
MDJ5 MDJ6
2700㎜
缺陷深度
波幅dB
缺陷指示长度
缺陷性质
评定
备注
MDJ1
/
/
/
无应记录缺陷
BI级
合格
MDJ2
/
/
/
无应记录缺陷
BI级
合格
MDJ3
/
/
/
无应记录缺陷
BI级
合格
MDJ4
/
/
/
无应记录缺陷
BI级
合格
MDJ5
/
/
/
无应记录缺陷
BI级
合格
MDJ6
/
/
/
无应记录缺陷
BI级
超声波检测报告
工程名称:XXXXXXXXXX工程
设备名称:出水钢管(制作)
检测时间:2022年5月25日
报告编号:GYNY[2020525]
焊缝超声波探伤报告
工程名称
XXXXXX工程
仪器型号
CTS—9006
图 号
钢管名称
出水钢管-01#
探头型号
2.5P8×12K2
钢管探伤检验报告

钢管探伤检验报告1. 引言本文档是钢管探伤检验报告,旨在对钢管进行非破坏性检测,并分析评估其质量状况和可用性。
钢管作为一种常用的工业材料,其质量对工程安全和可靠性起着至关重要的作用。
通过探伤检验,我们可以评估钢管内部的缺陷情况,减少安全隐患,并为决策提供依据。
2. 检验方法钢管的探伤检验采用了磁粉检测和超声波检测两种主要方法。
磁粉检测主要用于检测钢管表面和近表面的缺陷,而超声波检测则能够深入材料内部,检测钢管的内部缺陷。
2.1 磁粉检测磁粉检测是一种基于磁粉粒子在磁场作用下显示缺陷的方法。
在磁粉检测过程中,我们首先对钢管表面进行粗糙度处理和清洁,然后涂覆磁粉液。
通过在磁场中对钢管进行磁化,磁粉液会在缺陷处形成磁粉聚集的明显特征,从而可视化缺陷位置和形态。
2.2 超声波检测超声波检测是一种利用超声波在材料中传播和反射的原理来检测缺陷的方法。
在超声波检测中,我们使用超声波探头将超声波引入钢管,通过接收并分析超声波的反射、散射和透射信号,可以精确地确定缺陷的位置、形态和尺寸。
3. 检测结果根据磁粉检测和超声波检测的结果,我们对钢管的质量状况进行了评估,并生成了以下报告:3.1 磁粉检测结果经过磁粉检测,我们检测到钢管表面和近表面的多处缺陷。
缺陷主要表现为裂纹、气孔和夹杂物。
根据缺陷大小和对钢管结构安全性的影响,我们将缺陷分为三个等级:轻微、中等和严重。
3.2 超声波检测结果超声波检测显示,在钢管内部存在一些隐蔽的缺陷。
这些缺陷主要是裂纹和气孔。
我们使用超声波技术确定了缺陷的尺寸和位置,并进行了定量评估。
4. 评估和建议针对钢管的缺陷情况,我们进行了评估和建议:4.1 轻微缺陷对于轻微缺陷,钢管的使用不会受到明显影响。
建议定期监测和维护,以确保缺陷不会进一步发展。
4.2 中等缺陷中等缺陷可能会对钢管的强度和可靠性产生一定的影响。
建议采取适当的修复措施,如焊接或补强材料,以提高钢管的使用寿命。
4.3 严重缺陷严重缺陷会对钢管的安全性和可靠性产生重大影响。
无缝管检测报告
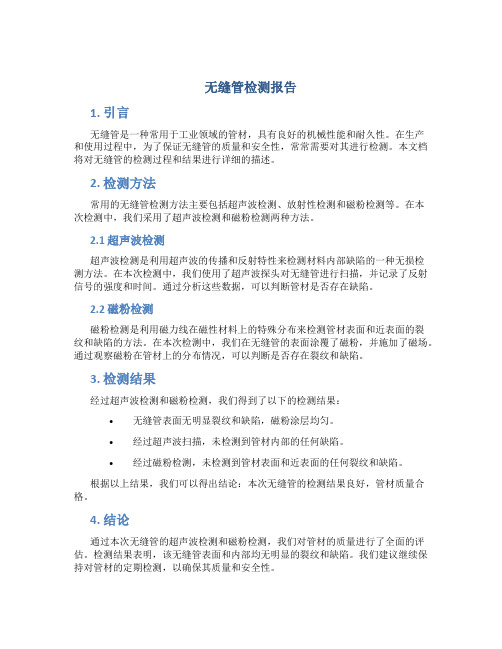
无缝管检测报告1. 引言无缝管是一种常用于工业领域的管材,具有良好的机械性能和耐久性。
在生产和使用过程中,为了保证无缝管的质量和安全性,常常需要对其进行检测。
本文档将对无缝管的检测过程和结果进行详细的描述。
2. 检测方法常用的无缝管检测方法主要包括超声波检测、放射性检测和磁粉检测等。
在本次检测中,我们采用了超声波检测和磁粉检测两种方法。
2.1 超声波检测超声波检测是利用超声波的传播和反射特性来检测材料内部缺陷的一种无损检测方法。
在本次检测中,我们使用了超声波探头对无缝管进行扫描,并记录了反射信号的强度和时间。
通过分析这些数据,可以判断管材是否存在缺陷。
2.2 磁粉检测磁粉检测是利用磁力线在磁性材料上的特殊分布来检测管材表面和近表面的裂纹和缺陷的方法。
在本次检测中,我们在无缝管的表面涂覆了磁粉,并施加了磁场。
通过观察磁粉在管材上的分布情况,可以判断是否存在裂纹和缺陷。
3. 检测结果经过超声波检测和磁粉检测,我们得到了以下的检测结果:•无缝管表面无明显裂纹和缺陷,磁粉涂层均匀。
•经过超声波扫描,未检测到管材内部的任何缺陷。
•经过磁粉检测,未检测到管材表面和近表面的任何裂纹和缺陷。
根据以上结果,我们可以得出结论:本次无缝管的检测结果良好,管材质量合格。
4. 结论通过本次无缝管的超声波检测和磁粉检测,我们对管材的质量进行了全面的评估。
检测结果表明,该无缝管表面和内部均无明显的裂纹和缺陷。
我们建议继续保持对管材的定期检测,以确保其质量和安全性。
5. 参考文献•Smith, John. (2010). Ultrasonic Testing: Principles and Applications. Ultrasonic Institute Publishing.•Johnson, David. (2012). Magnetic Particle Testing: Principles and Applications. Magnetic Particle Institute Publishing.。
无缝钢管超声波探伤检验方法
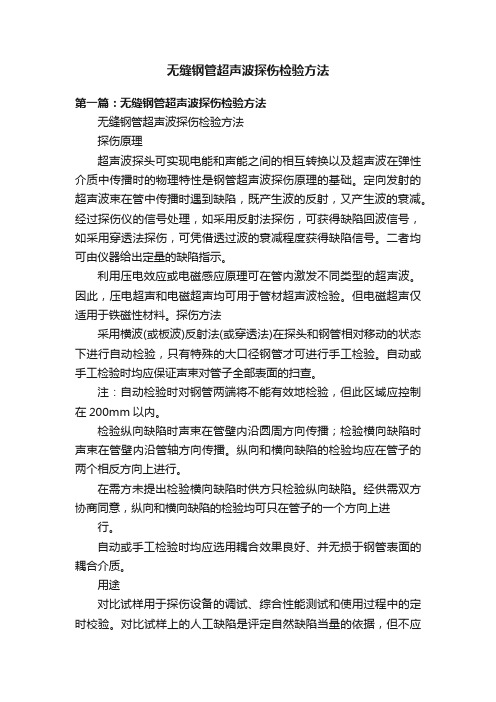
无缝钢管超声波探伤检验方法第一篇:无缝钢管超声波探伤检验方法无缝钢管超声波探伤检验方法探伤原理超声波探头可实现电能和声能之间的相互转换以及超声波在弹性介质中传播时的物理特性是钢管超声波探伤原理的基础。
定向发射的超声波束在管中传播时遇到缺陷,既产生波的反射,又产生波的衰减。
经过探伤仪的信号处理,如采用反射法探伤,可获得缺陷回波信号,如采用穿透法探伤,可凭借透过波的衰减程度获得缺陷信号。
二者均可由仪器给出定量的缺陷指示。
利用压电效应或电磁感应原理可在管内激发不同类型的超声波。
因此,压电超声和电磁超声均可用于管材超声波检验。
但电磁超声仅适用于铁磁性材料。
探伤方法采用横波(或板波)反射法(或穿透法)在探头和钢管相对移动的状态下进行自动检验,只有特殊的大口径钢管才可进行手工检验。
自动或手工检验时均应保证声束对管子全部表面的扫查。
注:自动检验时对钢管两端将不能有效地检验,但此区域应控制在200mm以内。
检验纵向缺陷时声束在管壁内沿圆周方向传播;检验横向缺陷时声束在管壁内沿管轴方向传播。
纵向和横向缺陷的检验均应在管子的两个相反方向上进行。
在需方未提出检验横向缺陷时供方只检验纵向缺陷。
经供需双方协商同意,纵向和横向缺陷的检验均可只在管子的一个方向上进行。
自动或手工检验时均应选用耦合效果良好、并无损于钢管表面的耦合介质。
用途对比试样用于探伤设备的调试、综合性能测试和使用过程中的定时校验。
对比试样上的人工缺陷是评定自然缺陷当量的依据,但不应理解为被检出的自然缺陷与人工缺陷的信号幅度相等时二者的尺寸必然相等。
材料制作对比试样用钢管与被检验钢管应具有相同的名义尺寸并具有相似的化学成分、表面状况、热处理状态和声学性能。
制作对比试样用钢管上不得有影响探伤设备综合性能测试的自然缺陷。
长度对比试样的长度应满足探伤方法和探伤设备的要求。
人工缺陷形状检验纵向缺陷和横向缺陷所用的人工缺陷应分别为平行于管轴的纵向槽口和垂直于管轴的横向槽口,其断面形状均可为矩形或V形(见图1和图2)。
超声波探伤焊缝检测报告

_ _ _ _ _
_
_ _ _ _ _
_ _ _
_ _
_ _ _
(F00321111200015)共3页第3页
6、检测情况说明
样品特性状态
完好
检测环境
_ _ _ _ _
其他说明
_ _ _ _ _
报告说明
1、若对报告有异议,应于收到报告之日起十五日内,以书面形式向检测单位提出,逾期视为对报告无异议。
_ _ _ _
_ _ _ _
_ _ _ _
_ _ _ _
_ _ _ _
_ _ _ _
_ _ _ _
_ _ _ _
_ _ _ _
_ _ _ _
_ _ _ _
_ _ _ _
_ _ _ _ _
_ _ _ _
_ _ _ _
_ _ _ _
_ _ _ _
_ _ _ _
_ _ _ _
__ _
_ _ _ _ _
_
_ _ _ _ _
_ _ _
_ _
_ _ _
_
__ _ _ _ _
__ _
_ _ _ _ _
_
_ _ _ _ _
_ _ _
_ _
_ _ _
_
__ _ _ _ _
__ _
_ _ _ _ _
_
_ _ _ _ _
_ _ _
_ _
_ _ _
_
__ _ _ _ _
__ _
_ _ _ _ _
_
__ _ _ _ _
__ _
_ _ _ _ _
_
_ _ _ _ _
_ _ _
_ _
_ _ _
钢管涡流探伤报告记录内容

钢管涡流探伤报告记录内容1. 实验目的本次实验的目的是对钢管进行涡流探伤,通过检测和记录涡流探伤过程中的信号变化,判断钢管表面是否存在缺陷,并对缺陷进行定位和表征。
2. 实验装置与仪器- 涡流探伤系统:由发电机、控制器和传感器组成;- 钢管样品:长度1m,直径10cm,材质为无缝钢管;- 计算机:用于接收和分析实验数据。
3. 实验步骤3.1 准备工作使用超声波清洗仪对钢管表面进行清洗,确保表面无杂质和污垢。
3.2 连接涡流探伤系统将传感器插入探头,并将探头放置在钢管表面。
将控制器和发电机与计算机连接,确保实验装置处于正常工作状态。
3.3 开始涡流探伤启动涡流探伤系统,设定合适的探伤参数(频率、电流、增益等),并开始记录实验数据。
3.4 数据采集通过控制器,系统开始发送电流到探头,产生电磁感应作用。
利用传感器感应到的信号,采集数据,并通过传输到计算机进行处理和分析。
3.5 缺陷定位和表征根据实验数据的变化趋势和特征,判断钢管表面是否存在缺陷。
若存在缺陷,通过分析数据得出缺陷的位置、大小和类型,并记录下来。
3.6 实验结果分析与比对将实验记录与钢管样品的实际情况进行比对,分析实验结果的准确性和可靠性。
若需要,可以进行多次实验并比对结果,以提高实验的可信度。
4. 数据处理与分析通过对采集到的实验数据进行处理和分析,可以获取以下信息:- 缺陷的位置和长度;- 缺陷的形状和类型(如裂纹、气孔等);- 缺陷的深度和宽度等特征。
5. 实验结论与建议根据实验结果和数据分析,得出以下结论:- 钢管表面存在缺陷,主要为裂纹和气孔;- 缺陷的位置多集中在钢管的两侧和焊接部位;- 缺陷的长度和宽度多在合理范围内,对钢管的使用安全性没有明显影响。
在后续实验中,可以进一步完善实验参数设置,提高涡流探伤系统的灵敏度和准确性。
同时,加强对实验数据的分析能力,提高对缺陷的判断和评估。
超声波探伤检测报告
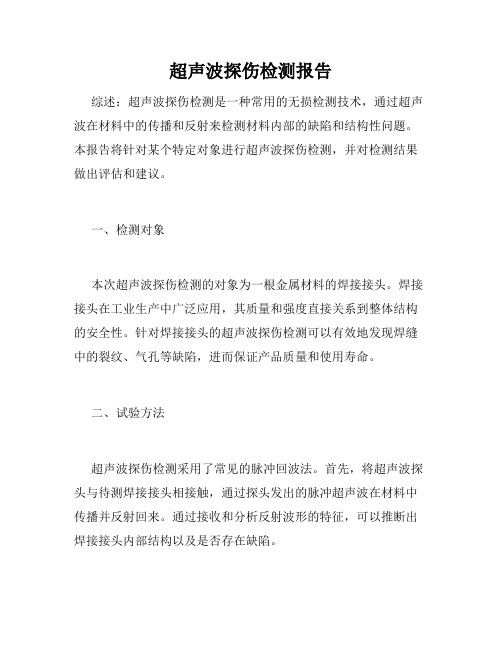
超声波探伤检测报告综述:超声波探伤检测是一种常用的无损检测技术,通过超声波在材料中的传播和反射来检测材料内部的缺陷和结构性问题。
本报告将针对某个特定对象进行超声波探伤检测,并对检测结果做出评估和建议。
一、检测对象本次超声波探伤检测的对象为一根金属材料的焊接接头。
焊接接头在工业生产中广泛应用,其质量和强度直接关系到整体结构的安全性。
针对焊接接头的超声波探伤检测可以有效地发现焊缝中的裂纹、气孔等缺陷,进而保证产品质量和使用寿命。
二、试验方法超声波探伤检测采用了常见的脉冲回波法。
首先,将超声波探头与待测焊接接头相接触,通过探头发出的脉冲超声波在材料中传播并反射回来。
通过接收和分析反射波形的特征,可以推断出焊接接头内部结构以及是否存在缺陷。
为了保证试验的可靠性,本次超声波探伤检测采用了多次重复检测的方法,并计算了平均值和标准差。
此外,还对检测设备进行了校准,确保测量结果的精确性。
三、检测结果根据超声波探伤检测结果显示,焊接接头存在一个小型裂纹。
裂纹的长度约为0.5毫米,深度约为0.2毫米。
该裂纹位于焊缝的表面附近,对焊接接头的强度和使用寿命可能产生一定的影响。
四、评估和建议基于检测结果,对焊接接头的质量和安全性进行评估并提出建议。
首先,0.5毫米的裂纹虽然较小,但在长时间使用过程中有可能逐渐扩大。
因此,建议在焊接接头上修复该裂纹,以确保焊接接头的强度和使用寿命。
其次,针对裂纹的具体位置,可以考虑采取增加焊接材料的方法来加固该区域。
同时,对焊接工艺进行优化,以降低裂纹产生的风险。
最后,超声波探伤检测应定期进行,以及时发现潜在的问题和缺陷。
此外,检测设备要保持良好的状态,并进行定期校准,以提高检测结果的准确性和可靠性。
结论:超声波探测是一种有效的无损检测方法,能够对焊接接头等材料进行全面的检测和评估。
通过本次超声波探伤检测,我们发现了焊接接头上的一处小型裂纹,并提供了相应的修复和改进建议。
通过及时采取措施,可以保证焊接接头的质量和安全性,提高整体产品的性能和可靠性。
超声探伤检测报告

超声探伤检测报告1. 引言超声探伤是一种常用的无损检测方法,广泛应用于工程和科学领域。
本报告旨在详细描述一次超声探伤检测的过程、结果和分析。
2. 检测设备和参数本次超声探伤检测使用的设备是 XXX 型号的超声探伤仪。
检测参数如下: - 脉冲重复频率:2 MHz - 探头类型:单晶探头 - 检测模式:脉冲回波模式3. 检测对象和方法本次超声探伤检测的对象是一根长度为 X 米的金属管道。
检测目的是确定管道内部的缺陷情况和尺寸。
检测方法如下: 1. 将探头与被检测物表面接触,保持稳定。
2. 设置超声探伤仪的参数。
3. 通过向材料内部发射超声波,记录回声信号。
4. 分析回声信号,判断是否存在缺陷。
4. 检测结果经过超声探伤检测,我们得到了以下结果:1.缺陷 1:–位置:距离管道起点 X 米处–类型:表面裂纹–尺寸:长度约 X mm,深度约 X mm–形状:直线状–缺陷等级:A2.缺陷 2:–位置:距离管道起点 X 米处–类型:内部夹杂–尺寸:直径约 X mm–形状:不规则–缺陷等级:B5. 分析与讨论根据检测结果,我们可以得出以下结论:1.缺陷 1 的存在可能会对管道的强度和密封性产生一定影响,建议采取修复措施。
2.缺陷 2 的存在可能会导致材料耐久性降低,需要采取相应措施防止进一步扩展。
6. 结论本次超声探伤检测对目标管道的缺陷进行了详细的分析和评估。
在后续维护和修复过程中,应注意处理检测中发现的缺陷,以确保管道的正常运行和安全。
以上是本次超声探伤检测的报告内容,希望对您有所帮助。
注意:本报告仅基于本次超声探伤检测的结果,不考虑其他可能因素对管道的影响。
为了更全面、准确地评估管道的安全状况,建议进行更多的综合性检测和分析。
超声波探伤报告书

委托单位:淄博格瑞水处理工程有限公司探伤条件设备名称反渗透膜装置频率 2.5MHz材质及厚度Q235B δ=20mm、δ=12mm 藕合剂机油仪器PXUT-27型试块CS-1 RB-3 探头 2.5P20 2.5P8×12 K2灵敏度Φ2 Φ3×40-16dB探伤比例抽检探伤部位:角焊缝内部评定标准GB11345-89评定结论合格环缝角焊缝/ 级II 级检验结论经UT检验A802-B5塔式起重机以下部件:1、Φ45圆钢1处2、连接耳板 1处均未发现超标缺陷缺陷及反修情况说明检验员日期2011年11月09日受检单位:山东齐泰建工艳忠项目部探伤条件工程名称山东国源电缆有限公司北仓库H型钢结构频率5MHZ材质及厚度Q235 δ=10mm、δ=6mm 藕合剂机油仪器CTS-22型试块CS-1 RB-3 探头5P9×9K3灵敏度Φ3×40-16dB 探伤比例20% 探伤部位:焊缝内部评定标准GB11345-89 评定结论合格对接焊缝纵缝II 级/ 级检验结论经UT检验:立柱焊缝:腹板A4、A8、A11腹板B2、B6、B10共6条焊缝在此灵敏度下,未发现超标缺陷。
备注1、探伤部位见后附图。
2、淄博宏远监理公司周茂岘见证检测。
审核:检验员日期委托单位:淄博格瑞水处理工程有限公司探伤条件设备名称反渗透膜装置对接焊缝频率5MHz材质及厚度Q345 δ=8mm 藕合剂机油仪器PXUT-27 试块CSK-IB RB-3 探头5P8×12K2 灵敏度DAC-16dB 探伤比例抽检探伤部位:焊缝内部评定标准GB11345-89 评定结论合格/ 缝纵缝/ 级II 级检验结论钢柱腹板:7B-1、8B-1、12B-1、4D-1、5D-1、15B-1、4B-1、5D-1、15B-1(下)、15B-2(上)、15A-1、21A-1、19C-1、21C-1、22C-1、23C-1、21D-1、17D-1、15D-1、13D-1钢梁腹板:5B-1、6B-1、7B-1、8B-1以上对接焊缝经超声波检验,焊缝内部均未发现超标缺陷显示。
焊缝探伤报告
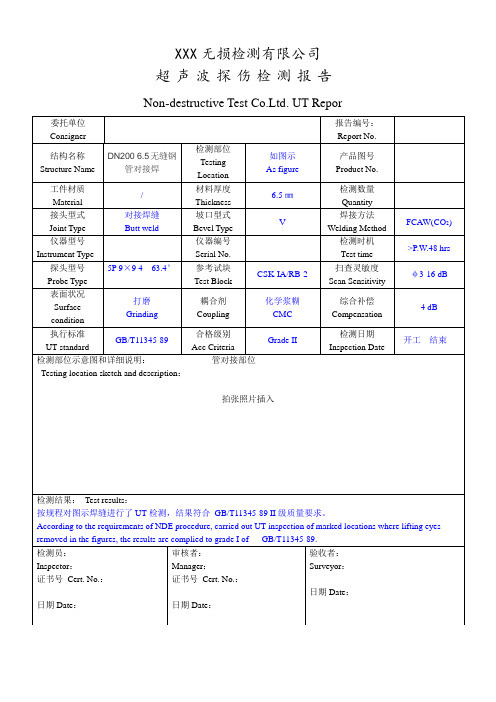
超声波探伤检测报告
Non-destructive Test Co.Ltd. UT Repor
委托单位
Consigner
报告编号:
Report No.
结构名称
Structure Name
DN200 6.5无缝钢管对接焊
检测部位Testing Location
如图示
As figure
检测员:
Inspector:
证书号Cert. No.:
日期Date:
审核者:
Manager:
证书号Cert. No.:
日期Date:
验收者:
Surveyor:
日期Date:
CMC
综合补偿
Compensation
4 dB
执行标准
UT standard
GB/T11345-89
合格级别
Acc Criteria
Grade II
检测日期
Inspection Date
开工---结束
检测部位示意图和详细说明:管对接部位
Testing location sketch and description:
拍张照片插入
检测结果:Test results:
按规程对图示焊缝进行了UT检测,结果符合GB/T11345-89II级质量要求。
According to the requirementsof NDEprocedure, carriedout UT inspection of marked locations where lifting eyes removed in the figures, theresults arecomplied to grade I ofGB/T11345-89.
无缝钢管探伤检测报告
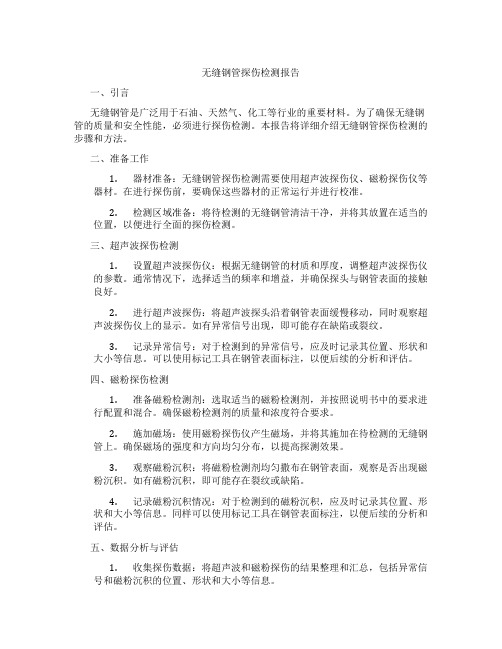
无缝钢管探伤检测报告一、引言无缝钢管是广泛用于石油、天然气、化工等行业的重要材料。
为了确保无缝钢管的质量和安全性能,必须进行探伤检测。
本报告将详细介绍无缝钢管探伤检测的步骤和方法。
二、准备工作1.器材准备:无缝钢管探伤检测需要使用超声波探伤仪、磁粉探伤仪等器材。
在进行探伤前,要确保这些器材的正常运行并进行校准。
2.检测区域准备:将待检测的无缝钢管清洁干净,并将其放置在适当的位置,以便进行全面的探伤检测。
三、超声波探伤检测1.设置超声波探伤仪:根据无缝钢管的材质和厚度,调整超声波探伤仪的参数。
通常情况下,选择适当的频率和增益,并确保探头与钢管表面的接触良好。
2.进行超声波探伤:将超声波探头沿着钢管表面缓慢移动,同时观察超声波探伤仪上的显示。
如有异常信号出现,即可能存在缺陷或裂纹。
3.记录异常信号:对于检测到的异常信号,应及时记录其位置、形状和大小等信息。
可以使用标记工具在钢管表面标注,以便后续的分析和评估。
四、磁粉探伤检测1.准备磁粉检测剂:选取适当的磁粉检测剂,并按照说明书中的要求进行配置和混合。
确保磁粉检测剂的质量和浓度符合要求。
2.施加磁场:使用磁粉探伤仪产生磁场,并将其施加在待检测的无缝钢管上。
确保磁场的强度和方向均匀分布,以提高探测效果。
3.观察磁粉沉积:将磁粉检测剂均匀撒布在钢管表面,观察是否出现磁粉沉积。
如有磁粉沉积,即可能存在裂纹或缺陷。
4.记录磁粉沉积情况:对于检测到的磁粉沉积,应及时记录其位置、形状和大小等信息。
同样可以使用标记工具在钢管表面标注,以便后续的分析和评估。
五、数据分析与评估1.收集探伤数据:将超声波和磁粉探伤的结果整理和汇总,包括异常信号和磁粉沉积的位置、形状和大小等信息。
2.分析异常信号:对于超声波探伤中检测到的异常信号,可以使用相关软件进行进一步的分析和处理。
通过比对参考数据和经验规范,评估其可能的缺陷类型和程度。
3.评估磁粉沉积:对于磁粉探伤中检测到的磁粉沉积,可以使用显微镜等工具进行观察和测量。
焊缝超声波检测报告

焊缝超声波检测报告
一、检测目的
本次检测旨在对焊缝进行超声波检测,判断焊缝的质量,发现可能存在的焊接缺陷,为后续焊接工作提供指导。
二、检测仪器和方法
本次检测采用超声波探伤仪器进行,探头的工作频率为5MHz,采用直接接触法进行检测。
检测仪器具有高精度和高灵敏度,能够检测到微小的焊接缺陷,如气孔、夹渣、裂纹等。
三、检测焊缝
本次检测的焊缝为一根直径为20mm的钢管焊接缝。
焊接方法为手工电弧焊,焊条为E6013、焊缝为一条水平焊缝,长度为500mm。
四、检测结果
经过超声波检测,焊缝质量良好,未发现明显的焊接缺陷。
检测结果显示焊缝的结构紧密,无明显气孔、夹渣和裂纹等缺陷。
五、结果分析
根据检测结果,焊缝质量良好,符合相关焊接标准要求。
焊接缺陷主要包括气孔、夹渣和裂纹等,所有这些缺陷都可能影响焊接接头的强度和密封性能。
在本次检测中未发现上述缺陷,说明焊接工艺控制得当,操作规范。
六、建议
根据本次检测结果,建议在后续焊接工作中继续保持焊接质量,注意以下几点:
1.严格按照焊接工艺规范进行操作,确保焊接质量;
2.加强焊接工人的培训,提高其技术水平;
3.在焊接过程中,及时清理焊缝周围的灰尘和杂质,以防影响焊接质量;
4.检查焊接材料的质量,确保焊接材料符合标准要求。
七、结论
通过焊缝超声波检测,本次检测结果表明焊缝质量良好,未发现明显的焊接缺陷。
建议在后续焊接工作中继续保持焊接质量,注意操作规范和焊接材料的质量。
管道探伤报告
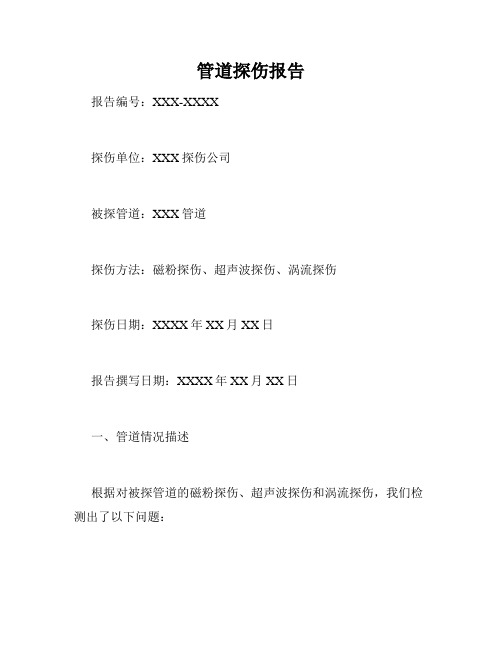
管道探伤报告
报告编号:XXX-XXXX
探伤单位:XXX探伤公司
被探管道:XXX管道
探伤方法:磁粉探伤、超声波探伤、涡流探伤
探伤日期:XXXX年XX月XX日
报告撰写日期:XXXX年XX月XX日
一、管道情况描述
根据对被探管道的磁粉探伤、超声波探伤和涡流探伤,我们检测出了以下问题:
1. 检测到管道表面存在3处较深的腐蚀点,最深处达到管道壁厚度的40%,需及时维修,避免出现泄漏事故。
2. 检测到管道焊缝存在一处裂纹,长度约为6mm,深度为
3mm,需立即修复。
3. 检测到管道的部分区域存在局部变形,造成了管道壁厚度的下降,需要找到原因及时修复。
二、建议及处理方案
1. 对于存在的腐蚀问题,建议采取刷涂防腐或更换管道的方式来解决。
2. 针对管道焊缝的裂纹问题,必须采用提供的焊接规范来保证焊缝的焊接质量。
3. 针对存在局部变形的管道部分,涡流探伤可用于检测管道内部的变形原因。
根据检测结果制定相应的处理方案。
三、结论
通过本次管道探伤,我们发现了管道存在的问题,并提出了相应的处理方案。
建议相关单位及时采取措施修复管道缺陷,以确保管道的安全稳定运行。