冲压件生产及工艺技术标准
冲压件技术要求范文

冲压件技术要求范文
一、性能要求
1、冲压件的材质应选用符合国家标准的冷轧材料,冲压件表面应满
足涂装的要求,在冲压过程中均匀性好。
2、冲压件表面不能有锈蚀、块状缺损、气孔、裂纹等缺陷,局部变
形不得超过规定值。
3、冲压件尺寸及形状应符合要求,尺寸公差不超过技术要求规定值,冲压件容易与被连接件密封的表面应光洁,平整,无明显的毛刺和激光焊
接痕迹等。
4、冲压件的表面涂装应保持均匀、美观,不得有漆斑或其它缺陷,
镀层厚度应符合国家标准。
5、冲压件的装配必须牢固可靠,不得发生移位、变形、断裂等现象,组成部件之间的联接点、螺纹丝孔应有完善的密封性能,绝不发生渗漏及
潮湿现象。
二、质量控制
1、冲压件的重复精度应满足设计要求。
2、对机械性能的检验应按照有关国家标准进行检测,并记录。
3、对冲压件的质量控制应有完善的检验制度,必要时可采用X射线
或放射性检测的方法检测内部结构的尺寸公差。
4、对冲压件抛光粗糙度应符合规定,实现冲压件的表面粗糙度,有
良好的光洁度。
5、在冲压件后的加工工序中,应采取有效的防锈措施,以免发生锈蚀现象。
冲压过程技术标准
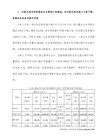
冲压工艺培训教材魏龙2004-5第一章绪论冷冲压是一种先进的金属加工方法,它是建立在金属塑性变形的基础上,利用模具和冲压设备对板料金属进行加工,以获得所需要的零件形状和尺寸。
冲压工艺应用范围十分广泛,在国民经济各个部门中,几乎都有冲压加工产品,如汽车、飞机、拖拉机、电机、电器、仪表、铁道、邮电、化工以及轻工日用产品中均占有相当大的比重。
冷冲压和切削加工比较,具有生产率高、加工成本低、材料利用率高、产品尺寸精度稳定、操作简单、容易实现机械化和自动化等一系列优点,特别适合大批量生产。
一、冲压工序的分类冷冲压工艺按其变形性质可分为分离工序和成形工序两大类。
分离工序又可分为落料、冲孔和切边等,如表1-1所示。
成形工序可分为弯曲、拉深、翻孔、翻边、胀形、扩口、缩口和旋压等,如表1-2所示。
根据产品零件的形状、尺寸精度和其他技术要求,可分别采用各种工序对板料毛坯进行加工,以获得满意的零件。
表1-1分离工序工序名称简图特点及应用范围第二章冲裁冲裁是利用模具使板料产生分离的冲压工序,包括落料、冲孔、切口、剖切、修边等。
用它可以制作零件或为弯曲、拉深、成形等工序准备毛坯。
一、落料从板料上冲下所需形状的零件(或毛坯)叫落料。
如图2-1所示。
图2-1落料图2-2冲孔二、冲孔在工件上冲出所需形状的孔(冲去的为废料)叫冲孔。
如图2-2所示。
三、冲裁的过程冲裁既是分离工序,工件受力时必然从弹、塑性变形开始,以断裂告终。
当凸模下降接触板料,板料即受到凸、凹模压力而产生弹性变形,板料产生弯曲,即从模具表面上翘起(图2-3-1)。
随着凸模下压,模具刃口压入材料,内应力状态满足塑性条件时,产生塑性变形(图2-3-2)。
塑性变形从刃口开始,随着刃口的深入,变形区向板料的深度方向发展、扩大,直到在板料的整个厚度方向上产生塑性变形,板料的一部分相对于另一部分移动。
当切刃附近材料各层中达到极限应变与应力值时,便产生微裂(图2-3-3),裂纹产生后,沿最大剪应变速度方向发展,直至上、下裂纹会合,板料就完全分离。
五金冲压件技术要求标准
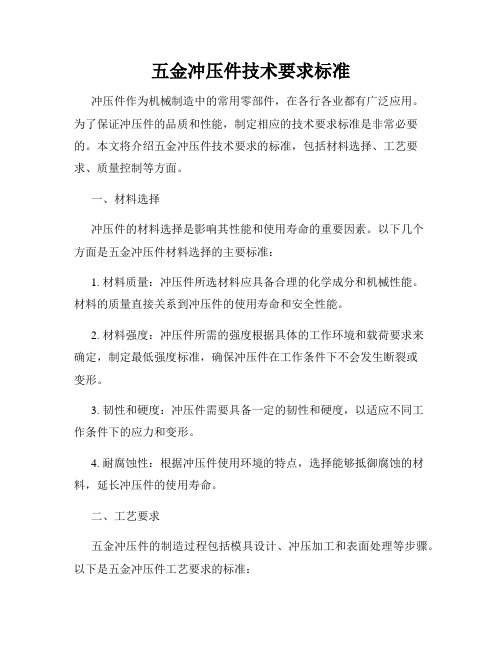
五金冲压件技术要求标准冲压件作为机械制造中的常用零部件,在各行各业都有广泛应用。
为了保证冲压件的品质和性能,制定相应的技术要求标准是非常必要的。
本文将介绍五金冲压件技术要求的标准,包括材料选择、工艺要求、质量控制等方面。
一、材料选择冲压件的材料选择是影响其性能和使用寿命的重要因素。
以下几个方面是五金冲压件材料选择的主要标准:1. 材料质量:冲压件所选材料应具备合理的化学成分和机械性能。
材料的质量直接关系到冲压件的使用寿命和安全性能。
2. 材料强度:冲压件所需的强度根据具体的工作环境和载荷要求来确定,制定最低强度标准,确保冲压件在工作条件下不会发生断裂或变形。
3. 韧性和硬度:冲压件需要具备一定的韧性和硬度,以适应不同工作条件下的应力和变形。
4. 耐腐蚀性:根据冲压件使用环境的特点,选择能够抵御腐蚀的材料,延长冲压件的使用寿命。
二、工艺要求五金冲压件的制造过程包括模具设计、冲压加工和表面处理等步骤。
以下是五金冲压件工艺要求的标准:1. 模具设计:在冲压件制造过程中,模具设计起到至关重要的作用。
模具设计应确保冲压件的精度和表面质量,减少废品率和生产成本。
2. 冲压加工:冲压加工要保证加工过程中冲片的精度和一致性。
加工过程中需要注意工艺参数的控制,避免冲压件的变形和损坏。
3. 表面处理:根据冲压件的用途和客户要求,选择合适的表面处理方法。
表面处理包括镀锌、喷漆、电镀等,旨在提高冲压件的耐腐蚀性和外观质量。
三、质量控制五金冲压件的质量控制是确保其性能和可靠性的关键环节。
以下是五金冲压件质量控制的标准:1. 材料检测:对冲压件所需材料进行磁粉检测、拉伸测试等,确保材料质量达到要求。
2. 产品检测:对冲压件进行外观质量检验、尺寸检测等,确保产品的准确度和一致性。
3. 产品性能测试:根据冲压件的使用要求,进行强度、韧性、硬度等性能测试,确保产品能够承受相应的工作条件。
4. 质量管理:建立和执行严格的质量管理体系,包括产品追溯、异常处理和质量持续改进等,以确保冲压件的质量稳定和可控。
五金冲压件技术要求标准

五金冲压件技术要求标准一、前言五金冲压件是指利用模具将金属板材进行切割、弯曲、拉伸等加工而形成的零件,在机械制造、汽车制造、电子设备等行业中广泛应用。
为了确保五金冲压件质量和生产效率,制定一套标准的技术要求对于企业的制造和质量管理具有重要意义。
本文旨在就五金冲压件的技术要求标准进行深入探讨。
二、材料要求1. 材料品种:五金冲压件所使用的金属材料应符合国家标准或相关行业标准,且应具有良好的可加工性和成形性。
2. 材料厚度:根据零件的设计要求和使用环境,决定冲压件所需金属材料的厚度范围。
3. 材料表面处理:五金冲压件在生产过程中需要确保其表面光洁度和防锈性,可进行镀锌、喷涂等表面处理。
三、工艺要求1. 模具设计:五金冲压件的模具设计应合理、精准,能够确保冲压件的尺寸精度和表面质量。
2. 冲压工艺参数:包括冲头尺寸、压力、冲裁速度等参数的设置,需根据材料性能和工件的几何形状进行科学合理的确定。
3. 冲裁设备:冲压设备应具备良好的稳定性和精度,确保批量生产时零件的一致性。
4. 补料和送料:对于复杂形状的五金冲压件,补料和送料系统应配备合适的辅助设备,确保生产效率和产品质量。
四、质量要求1. 尺寸精度:五金冲压件的尺寸公差应符合设计要求,并经过严格的尺寸检测。
2. 表面质量:冲压件的表面应不得有明显的划痕、氧化等缺陷,并符合相关行业标准规定的表面处理要求。
3. 强度和硬度:冲压件应具有符合设计要求的机械性能,包括强度、硬度等方面的指标。
4. 成形性能:要求零件在正常使用情况下能够保持其成形性能,不易产生变形、开裂等现象。
五、其它要求1. 标识要求:五金冲压件应在产品上清晰标识材料、规格、批号等信息。
2. 环保要求:在生产过程中应符合国家环保法规,减少废料产生,做到资源合理利用。
3. 安全要求:对于生产过程中存在的安全隐患,应制定相应的安全措施和操作规程。
六、结语五金冲压件在各个行业起着重要的作用,其技术要求的制定对于提高零部件的质量、降低生产成本具有重要意义。
五金冲压件技术要求标准

五金冲压件技术要求标准一、引言五金冲压件是指利用模具对金属材料进行冲压加工,制作各种形状的零部件,广泛应用于汽车、家电、机械设备等领域。
为了确保五金冲压件的质量稳定和生产效率,制定一套严格的技术要求标准是十分必要的。
二、材料要求1. 材料应选用优质金属材料,如冷轧板材、热轧板材等,符合国家标准。
2. 材料的厚度、硬度和强度应满足设计要求,并能够确保冲压加工后的产品符合强度和耐久性要求。
三、设计要求1. 模具设计应符合产品的结构要求,确保冲压件的几何形状、尺寸和孔位精度满足设计要求。
2. 充分考虑材料的拉伸变形特性和冲压时的应力分布,避免产生裂纹、翘曲等缺陷。
四、冲压工艺要求1. 冲床设备应具备稳定的性能和精度,确保冲压件的加工精度和表面质量。
2. 合理确定冲压工艺参数,如冲头压力、冲头速度、冲头行程和冲座间距等,以确保产品的成型质量和生产效率。
3. 对于复杂工件,应采用逐级成形或多工位冲压工艺,以确保产品的成形质量和精度。
五、质量控制要求1. 制定严格的产品质量检验标准,包括外观质量、尺寸精度、表面平整度、材料硬度等项目,保证产品的质量稳定。
2. 引入先进的检测设备和工艺控制手段,如光学测量仪、数控冲床等,以实现产品质量的在线监测和控制。
3. 建立完善的产品质量追溯体系,确保每一批产品都可以进行追溯和溯源,对质量问题进行追踪和处理。
六、环境保护要求1. 在生产过程中,严格遵守环保法律法规,减少废水、废气和废固体的排放。
2. 推广清洁生产技术,降低资源消耗和能耗,减少对环境的影响。
3. 加强废品回收和利用,减少对自然资源的浪费,实现循环经济发展。
七、安全生产要求1. 坚持安全第一的原则,加强安全生产管理,确保生产过程中不发生安全事故。
2. 提高员工的安全意识,加强安全培训,提供必要的劳动防护设备,保障员工的人身安全。
八、结论五金冲压件技术要求标准是确保产品质量和生产安全的重要保障,对企业的技术水平和管理能力提出了更高要求。
冲压件技术要求

模具设计制造技术要求一、总体要求设计和制造K综合车架增加的冲压件模具。
生产纲领:年产3万辆,双班制。
模具使用寿命30万次。
二、模具规格1.模具结构形式(1)模具结构形式为钢板式结构或框架式结构,所有尺寸及零部件:选用及加工均采用公制。
模具本体为钢板式结构:参照《中国机械工业标准模具卷》钢板模架标准进行设计,应保证模具的强度、钢度和外观质量。
材质为45号钢。
模具本体为框架式结构:模板选用(汽车冲模标准汇编)模架标准,材质为ZG45。
(2)导柱,导套采用压入式结构。
选用(汽车冲模标准汇编)QM1201、QM1221标准。
拉延模可采用导板导向,导板采用自润滑式导板。
(3)所有模具凸凹模工作部位局部或整体淬火后,不允许出现软点、烧伤、裂纹。
(4)模具图中应反映模具的进、出料方向,气顶杆位置,闭合高度。
(5)模具定位要操作方便、可靠,模具上、下模前端标记处明显。
(6)修边废料可以人工收集,易于拿取;废料不能滑出工作台,原则上采用废料盒装置,装入量应不小于80件废料。
废料盒要取放方便。
(7)拉延模和整形模要设置到底标记,左右合模件设置左右标记L、R;标记安装在模具上模上。
(8)起吊装置采用(汽车冲模标准汇编)QM标准,便于模具的起吊、翻转;设置上、下连接板。
(9)模具结构设计要便于工人操作,保证操作者人身、设备及模具安全。
(10)以上所述内容及其它未说明内容参阅(汽车冲模标准汇编)、(中国机械工业标准模具篇)。
2. 模具工作部位材料(1)拉延模:凸、凹模及压边圈采用Cr12MoV,整体淬火,其硬度不低于HRC55。
(2)修边冲孔落料模:a.修边刃口采用T10A,整体淬火,其硬度为HRC60±2;b.冲头采用Cr12MoV,球锁式快换冲头,对于特殊结构由会签时确定。
c.凹模套采用Cr12MoV甲方认可的标准凹模套(保证同轴度且具有互换性)凹模套的防转方法采用甲方认可的Φ4mm的防转销。
(3)弯曲成形模:凸凹模采用Cr12MoV。
冲压过程技术标准

冲压工艺培训教材魏龙2004-5第一章绪论冷冲压是一种先进的金属加工方法,它是建立在金属塑性变形的基础上,利用模具和冲压设备对板料金属进行加工,以获得所需要的零件形状和尺寸。
冲压工艺应用范围十分广泛,在国民经济各个部门中,几乎都有冲压加工产品,如汽车、飞机、拖拉机、电机、电器、仪表、铁道、邮电、化工以及轻工日用产品中均占有相当大的比重。
冷冲压和切削加工比较,具有生产率高、加工成本低、材料利用率高、产品尺寸精度稳定、操作简单、容易实现机械化和自动化等一系列优点,特别适合大批量生产。
一、冲压工序的分类冷冲压工艺按其变形性质可分为分离工序和成形工序两大类。
分离工序又可分为落料、冲孔和切边等,如表1-1所示。
成形工序可分为弯曲、拉深、翻孔、翻边、胀形、扩口、缩口和旋压等,如表1-2所示。
根据产品零件的形状、尺寸精度和其他技术要求,可分别采用各种工序对板料毛坯进行加工,以获得满意的零件。
表1-1分离工序工序名称简图特点及应用范围第二章冲裁冲裁是利用模具使板料产生分离的冲压工序,包括落料、冲孔、切口、剖切、修边等。
用它可以制作零件或为弯曲、拉深、成形等工序准备毛坯。
一、落料从板料上冲下所需形状的零件(或毛坯)叫落料。
如图2-1所示。
图2-1落料图2-2冲孔二、冲孔在工件上冲出所需形状的孔(冲去的为废料)叫冲孔。
如图2-2所示。
三、冲裁的过程冲裁既是分离工序,工件受力时必然从弹、塑性变形开始,以断裂告终。
当凸模下降接触板料,板料即受到凸、凹模压力而产生弹性变形,板料产生弯曲,即从模具表面上翘起(图2-3-1)。
随着凸模下压,模具刃口压入材料,内应力状态满足塑性条件时,产生塑性变形(图2-3-2)。
塑性变形从刃口开始,随着刃口的深入,变形区向板料的深度方向发展、扩大,直到在板料的整个厚度方向上产生塑性变形,板料的一部分相对于另一部分移动。
当切刃附近材料各层中达到极限应变与应力值时,便产生微裂(图2-3-3),裂纹产生后,沿最大剪应变速度方向发展,直至上、下裂纹会合,板料就完全分离。
锻压、冲压工艺标准精选(最新)

锻压、冲压工艺标准精选(最新)G6402《GB/T 6402-2008 钢锻件超声检测方法》G8176《GB 8176-2012 冲压车间安全生产通则》G8541《GB/T 8541-2012 锻压术语》G12361《GB/T12361-2003 钢质模锻件通用技术条件》G12362《GB/T12362-2003 钢质模锻件公差及机械加工余量》G12363《GB/T 12363-2005 锻件功能分类》G13318《GB13318-2003 锻造生产安全与环保通则》G13320《GB/T 13320-2007 钢质模锻件金相组织评级图及评定方法》G13887《GB 13887-2008 冷冲压安全规程》G13914《GB/T 13914-2013 冲压件尺寸公差》G13915《GB/T 13915-2013 冲压件角度公差》G13916《GB/T 13916-2013 冲压件形状和位置未注公差》G14999.6《GB/T 14999.6-2010 锻制高温合金双重晶粒组织和一次碳化物分布测定方法》G15055《GB/T 15055-2007 冲压件未注公差尺寸极限偏差》G15825.1《GB/T 15825.1-2008 金属薄板成形性能与试验方法第1部分:成形性能和指标》G15825.2《GB/T 15825.2-2008 金属薄板成形性能与试验方法第2部分:通用试验规程》G15825.3《GB/T 15825.3-2008 金属薄板成形性能与试验方法第3部分:拉深与拉深载荷试验》G15825.4《GB/T 15825.4-2008 金属薄板成形性能与试验方法第4部分:扩孔试验》G15825.5《GB/T 15825.5-2008 金属薄板成形性能与试验方法第5部分:弯曲试验》G15825.6《GB/T 15825.6-2008 金属薄板成形性能与试验方法第6部分:锥杯试验》G15825.7《GB/T 15825.7-2008 金属薄板成形性能与试验方法第7部分:凸耳试验》G15825.8《GB/T 15825.8-2008 金属薄板成形性能与试验方法第8部分:成形极限图(FLD)测定指南》G15826《GB/T15826.1~9-1995 锤上自由锻自由锻件机械加工余量与公差》G16743《GB/T 16743-2010 冲裁间隙》G17107《GB/T17107-1997 锻件用结构钢牌号和力学性能》G20078《GB/T 20078-2006 铜和铜合金锻件》G20911《GB/T 20911-2007 锻造用半成品尺寸、形状和质量公差》G21469《GB/T 21469-2008 锤上钢质自由锻件机械加工余量与公差一般要求》G21470《GB/T 21470-2008 锤上钢质自由锻件机械加工余量与公差盘、柱、环、筒类》G21471《GB/T 21471-2008 锤上钢质自由锻件机械加工余量与公差轴类》G22131《GB/T 22131-2008 筒形锻件内表面超声波检测方法》G25134《GB/T 25134-2010 锻压制件及其模具三维几何量光学检测规范》G25135《GB/T 25135-2010 锻造工艺质量控制规范》G25136《GB/T 25136-2010 钢质自由锻件检验通用规则》G25137《GB/T 25137-2010 钛及钛合金锻件》G26030《GB/T 26030-2010 镍及镍合金锻件》G26036《GB/T 26036-2010 汽车轮毂用铝合金模锻件》G26637《GB/T 26637-2011 镁合金锻件》G26638《GB/T 26638-2011 液压机上钢质自由锻件复杂程度分类及折合系数》G26639《GB/T 26639-2011 液压机上钢质自由锻件通用技术条件》G29532《GB/T 29532-2013 钢质精密热模锻件通用技术条件》G29533《GB/T 29533-2013 钢质模锻件材料消耗工艺定额编制方法》G29534《GB/T 29534-2013 温锻冷锻联合成形锻件通用技术条件》G29535《GB/T 29535-2013 温锻冷锻联合成形工艺工艺编制原则》G30566《GB/T 30566-2014 GH4169合金棒材、锻件和环形件》G30567《GB/T 30567-2014 钢质精密热模锻件工艺编制原则》G30568《GB/T 30568-2014 锆及锆合金锻件》G30569《GB/T 30569-2014 直齿锥齿轮精密冷锻件结构设计规范》G30570《GB/T 30570-2014 金属冷冲压件结构要素》G30571《GB/T 30571-2014 金属冷冲压件通用技术条件》G30572《GB/T 30572-2014 精密冲裁件工艺编制原则》G30573《GB/T 30573-2014 精密冲裁件通用技术条件》G30895《GB/T 30895-2014 热轧环件》GJ904A《GJB904A-1999 锻造工艺质量控制要求》GJ1057《GJB 1057-1990 铝合金过时效锻件》GJ2351《GJB2351-1995 航空航天用铝合金锻件规范》GJ5154《GJB5154-2002 航空航天用镁合金锻件规范》GJ2744A《GJB2744A-2007 K 航空用钛及钛合金锻件规范》GJ5040《GJB5040-2001 航空用钢锻件规范》GJ5061《GJB 5061-2001 航空航天用超高强度钢锻件规范》GJ5911K《GJB 5911-2006 K 舰艇用15CrNi3MoV钢锻钢规范》HB0-19《HB0-19-2011 开口弯边》HB0-20《HB0-20-2011 皱纹弯边》HB0-22《HB0-22-2008 挤压型材下陷》HB0-35《HB0-35-2011 挤压型材倾斜角度极限值》HB199《HB/Z199-2005 钛合金锻造工艺》H283《HB/Z283-1996钢的锻造工艺》HB5224《HB5224-2011 航空发动机用钛合金盘模锻件规范》H5355《HB5355-1994 锻造工艺质量控制》H5402《HB5402-1997 锻件试制定型规范》HB6077《HB6077-2008 模锻件公差及机械加工余量》HB6587《HB 6587-1992 锤上自由锻件机械加工余量与尺寸公差》H7238《HB7238-1995 钛合金环形锻件》H7726《HB7726-2002 航空发动机用钛合金叶片精锻件规范》HB8401《HB 8401-2013 钣金成形工装设计要求》QJ262《QJ 262-1994 钣金冲压件通用技术条件》QJ502A《QJ 502A-2001 铝合金、铜合金锻件技术条件》QJ2141A《QJ2141A-2011 高温合金锻件规范》WJ2537《WJ2537-1999 兵器用冲压件规范》CB773《CB/T 773-1998 结构钢锻件技术条件》J1266《JB/T 1266-2014 25 MW~200 MW汽轮机轮盘及叶轮锻件技术条件》J1268《JB/T 1268-2014 汽轮发电机Mn18Cr5 系无磁性护环锻件技术条件》J1270《JB/T 1270-2014 水轮机、水轮发电机大轴锻件技术条件》J1271《JB/T 1271-2014 交、直流电机轴锻件技术条件》J1581《JB/T 1581-2014 汽轮机、汽轮发电机转子和主轴锻件超声检测方法》J1582《JB/T 1582-2014 汽轮机叶轮锻件超声检测方法》J3733《JB/T 3733-2006 大型锻造合金钢热轧工作辊》J4120《JB/T 4120-2006 大型锻造合金钢支承辊》J4129《JB/T4129-1999 冲压件毛刺高度》J4201《JB/T4201-1999 直齿锥齿轮精密热锻件技术条件》J4290《JB/T4290-1999 高速工具钢锻件技术条件》J4378《JB/T4378.1~2-1999 金属冷冲压件》J4381《JB/T 4381-2011 冲压剪切下料未注公差尺寸的极限偏差》J4385《JB/T4385.1~2-1999 锤上自由锻件》J5109《JB/T5109-2001 金属板料压弯工艺设计规范》J6052《JB/T 6052-2005 钢质自由锻件加热通用技术条件》J6053《JB/T6053-2004 钢制锻件热锻工艺燃料消耗定额计算方法》J6054《JB/T6054-2001 冷挤压件工艺编制原则》J6056《JB/T 6056-2005 冲压车间环境保护导则》J6395《JB/T 6395-2010 大型齿轮、齿圈锻件技术条件》J6396《JB/T 6396-2006 大型合金结构钢锻件技术条件》J6397《JB/T 6397-2006 大型碳素结构钢锻件技术条件》J6398《JB/T 6398-2006 大型不锈、耐酸、耐热钢锻件》J6402《JB/T 6402-2006 大型低合金钢铸件》J6405《JB/T 6405-2006 大型不锈钢铸件》J6541《JB/T6541-2004 冷挤压件形状和结构要素》J6957《JB/T6957-2007 精密冲裁件工艺编制原则》J6958《JB/T6958-2007 精密冲裁件通用技术条件》J6959《JB/T 6959-2008 金属板料拉深工艺设计规范》J6979《JB/T 6979-1993 大中型钢质锻模模块质量分级》J7023《JB/T 7023-2014 水轮发电机镜板锻件技术条件》J7025《JB/T 7025-2004 25MW以下汽轮机转子体和主轴锻件技术条件》J7026《JB/T 7026-2004 50MW以下汽轮发电机转子锻件技术条件》J7027《JB/T 7027-2002 300MW以上汽轮机转子体锻件技术条件》J7028《JB/T 7028-2004 25MW以下汽轮机转盘及叶轮锻件技术条件》J7029《JB/T 7029-2004 50MW以下汽轮发电机无磁性护环锻件技术条件》J7030《JB/T 7030-2014 汽轮发电机Mn18Cr18N 无磁性护环锻件技术条件》J7032《JB/T7032-2001 大型全纤维曲轴锻件》J7531《JB/T 7531-2005 旋压件设计规范》J7532《JB/T 7532-2005 旋压工艺编制原则》J7535《JB/T7535-1994 锻件工艺质量控制规范》J8421《JB/T8421-1996 钢质自由锻件检验通用规则》J8466《JB/T 8466-2014 锻钢件渗透检测》J8467《JB/T 8467-2014 锻钢件超声检测》J8468《JB/T 8468-2014 锻钢件磁粉检验》J8705《JB/T 8705-2014 50 MW以下汽轮发电机无中心孔转子锻件技术条件》J8706《JB/T 8706-2014 50 MW~200 MW汽轮发电机无中心孔转子锻件技术条件》J8707《JB/T8707-1998 300MW以上汽轮无中心孔转子锻件技术条件》J8708《JB/T 8708-2014 300 MW~600 MW汽轮发电机无中心孔转子锻件技术条件》J8888《JB/T8888-1999 环芯法测量汽轮机,汽轮发电机转子锻件残余应力的试验方法》J8930《JB/T8930-1999 冲压工艺质量控制规范》J9020《JB/T9020-1999 大型锻造曲轴的超声波检验》J9021《JB/T 9021-2010 汽轮机主轴和转子锻件的热稳定性试验方法》J9174《JB/T9174-1999 模锻件材料消耗工艺定额编制方法》J9175.1《JB/T 9175.1-2013 精密冲裁件第1部分:结构工艺性》J9175.2《JB/T 9175.2-2013 精密冲裁件第2部分:质量》J9176《JB/T9176-1999 冲压件材料消耗工艺定额编制方法》J9177《JB/T9177-1999 钢制模锻件结构要素》J9178.1《JB/T9178.1-1999 水压机上自由锻件通用技术条件》J9178.2《JB/T9178.2-1999 水压机上自由锻件复杂程度分类及折合系数》J9179《JB/T9179.1~8-1999 水压机上自由锻件机械加工余量与公差》J9180.1《JB/T 9180.1-2014 钢质冷挤压件第1部分:公差》J9180.2《JB/T 9180.2-2014 钢质冷挤压件第2部分:通用技术条件》J9181《JB/T9181-1999 直齿锥齿轮精密热锻件结构设计规范》J10138《JB/T10138-1999 渗碳轴承钢锻件》J10265《JB/T 10265-2014 水轮发电机用上下圆盘锻件技术条件》J10663《JB/T 10663-2006 25MW及25MW以下汽轮机无中心孔转子和主轴锻件技术条件》J10664《JB/T 10664-2006 25MW~200MW汽轮机无中心孔转子和主轴锻件技术条件》J11017《JB/T 11017-2010 1000MW及以上火电机组发电机转子锻件技术条件》J11018《JB/T 11018-2010 超临界及超超临界机组汽轮机用Cr10型不锈钢铸件技术条件》J11019《JB/T 11019-2010 超临界及超超临界机组汽轮机用高中压转子锻件技术条件》J11020《JB/T 11020-2010 超临界及超超临界机组汽轮机用超纯净钢低压转子锻件技术条件》J11021《JB/T 11021-2010 大型高铬锻钢支承辊技术条件》J11022《JB/T 11022-2010 大型高铬铸钢热轧工作辊技术条件》J11023《JB/T 11023-2010 大型高铬铸铁热轧工作辊技术条件》J11024《JB/T 11024-2010 大型核电机组汽轮机用焊接转子锻件技术条件》J11026《JB/T 11026-2010 大型核电机组四极汽轮发电机转子锻件技术条件》J11028《JB/T 11028-2010 汽轮发电机集电环锻件技术条件》J11030《JB/T 11030-2010 汽轮机高低压复合转子锻件技术条件》J11032《JB/T 11032-2010 燃气轮机压气机轮盘不锈钢锻件技术条件》J11033《JB/T 11033-2010 燃气轮机压气机轮盘合金钢锻件技术条件》J11760《JB/T 11760-2013 直齿锥齿轮精密冷锻件技术条件》J11761《JB/T 11761-2013 齿轮轴毛坯楔横轧技术条件》J12028《JB/T 12028-2014 涡旋压缩机铝合金精锻涡旋盘通用技术条件》J50196《JB/T50196-2000 3~600MW发电机无磁性护环合金钢锻件质量分等》J50197《JB/T50197-2000 3~600MW汽轮机转子和主轴锻件锻件质量分等》J53485《JB/T53485-2000 50MW以下发电机转子锻件质量分等》J53488《JB/T53488-2000 25MW以下汽轮机转盘及叶轮锻件产品质量分等》J53495《JB/T53495-2000 特大型轴承钢锻件产品质量分等》J53496《JB/T53496-2000 50~600MW发电机转子锻件质量分等》YB091《YB/T 091-2005 锻(轧)钢球》YS479《YS/T 479-2005 一般工业用铝及铝合金锻件》YS686《YS/T 686-2009 活塞裙用铝合金模锻件》TB2944《TB/T 2944-1999 铁道用碳素钢锻件》TB3014《TB/T 3014-2001 铁道用合金钢锻件》SJ10726《SJ/T10726-1996 冲压件一般检验原则》SJ10538《SJ/T10538-1994 冲压生产技术经济指标计算方法》A788《ASTM A788 -2004a 钢锻件通用要求的标准技术条件》(中文版)JB/T4129-1999 冲压件毛刺高度JB/T4201-1999 直齿锥齿轮精密热锻件技术条件JB/T4290-1999 高速工具钢锻件技术条件JB/T4378.1-1999 金属冷冲压件结构要素JB/T4378.2-1999 金属冷冲压件通用技术条件JB/T4381-1999 冲压剪切下料未注公差尺寸的极限偏差JB/T 4385.1-1999 锤上自由锻件通用技术条件JB/T 4385.2-1999 锤上自由锻件复杂程度分类及折合系数JB/T8930-1999 冲压工艺质量控制规范JB/T9174-1999 模锻件材料消耗工艺定额编制方法JB/T 9175.1-1999 精密冲裁件结构工艺性JB/T 9175.2-1999 精密冲裁件质量JB/T9176-1999 冲压件材料消耗工艺定额编制方法JB/T9177-1999 钢质模锻件结构要素JB/T9178.1-1999 水压机上自由锻件通用技术条件JB/T9178.2-1999 水压机上自由锻件复杂程度分类及折合系数JB/T 9179.1-1999 水压机上自由锻件机械加工余量与公差一般要求JB/T 9179.2-1999 水压机上自由锻件机械加工余量与公差圆轴、方轴和矩形截面类JB/T 9179.3-1999 水压机上自由锻件机械加工余量与公差台阶轴类JB/T 9179.4-1999 水压机上自由锻件机械加工余量与公差圆盘和冲孔类JB/T 9179.5-1999 水压机上自由锻件机械加工余量与公差短圆柱类JB/T 9179.6-1999 水压机上自由锻件机械加工余量与公差模块类JB/T 9179.7-1999 水压机上自由锻件机械加工余量与公差筒体类JB/T 9179.8-1999 水压机上自由锻件机械加工余量与公差圆环类JB/T 9180.1-1999 钢质冷挤压件公差JB/T 9180.2-1999 钢质冷挤压件通用技术条件JB/T9181-1999 直齿锥齿轮精密热锻件结构设计规范JB/T9194-1999 辊锻模结构形式及尺JB/T9195-1999 辊锻模通用技术条件JB/T10138-1999 渗碳轴承钢锻件。
五金冲压件技术要求标准

五金冲压件技术要求标准一、引言五金冲压件是制造业中常见的零部件,广泛应用于汽车、航空航天、家电、机械设备等行业。
为了保证五金冲压件的质量和性能,制定了一系列的技术要求标准,从材料选取、工艺流程、设备要求等方面进行规范。
二、材料要求1. 材料选择:五金冲压件的材料应符合相关国家标准,如GB/T 1220、GB/T 3077等。
应根据零部件的使用环境和要求选择适当的材料,包括钢材、铝合金、铜合金等。
2. 材料性能:五金冲压件材料应具有良好的机械性能,包括强度、硬度、塑性等指标。
应对材料进行严格的化学成分检测和力学性能测试。
3. 表面处理:对五金冲压件的表面进行防锈、防腐、涂装等处理,以保证产品的表面质量和使用寿命。
三、工艺流程要求1. 冲压工艺:应根据产品的结构和要求确定合理的冲压工艺,包括模具设计、模具加工、成型工艺参数的选择等。
2. 成型精度:五金冲压件的成型精度应符合相关标准要求,包括尺寸精度、形位公差、表面质量等。
3. 工艺控制:对冲压工艺进行严格的控制和检测,确保产品的质量稳定和一致性。
四、设备要求1. 冲压设备:应选用先进的数控冲床、冲压机等设备,确保产品的生产效率和质量。
2. 模具设备:应具备高精度、高耐磨的模具加工设备,保证模具的精度和寿命。
3. 检测设备:应配置相应的检测设备,包括三坐标测量机、硬度计、拉力试验机等,对产品进行全面的检测。
五、质量控制要求1. 品质管理体系:应建立完善的品质管理体系,包括从材料采购、工艺控制、产品检测等各个环节的管理和控制。
2. 出厂检验标准:制定五金冲压件的出厂检验标准,包括外观检验、尺寸检验、力学性能检验等。
3. 不良品处理:建立完善的不良品处理流程,及时发现和处理不合格品,保证产品的合格率和稳定性。
六、环保要求1. 废水、废气处理:五金冲压件生产过程中应注意废水、废气的处理,达到环保要求。
2. 资源利用:在生产过程中应尽量节约资源,减少能源消耗和废弃物产生。
五金冲压件技术要求标准

五金冲压件技术要求标准一、引言五金冲压件是一种常见的金属制品,广泛应用于机械、汽车、电子、家电等领域。
为了确保五金冲压件的质量和安全性,制定了以下的技术要求标准。
二、材料要求1. 材料应符合国家相关标准,如材料牌号、化学成分、力学性能等应满足规定。
2. 材料应无裂纹、气孔、夹杂等缺陷,表面应光洁、无明显划痕。
3. 对于特殊要求的五金冲压件,如耐高温、耐腐蚀、导电等,应选择相应特殊材料。
三、设计要求1. 五金冲压件的设计应符合相关标准和规范,包括尺寸、形状、结构等。
2. 避免设计过于复杂或过于薄弱,应尽量减少锐角、薄壁等容易产生变形或开裂的形状。
3. 对于需要进行后续加工或表面处理的五金冲压件,应在设计阶段考虑后续工艺的可行性。
四、工艺要求1. 冲压模具的选材和制造应符合相关标准,保证模具寿命和精度。
2. 冲床设备应定期检测,保证冲压过程中的动态平衡和精度。
3. 冲床应配置合适的上模和下模,保证五金冲压件在冲压过程中的形状保持正确。
4. 冲床及模具的冷却系统应合理设计,保证冲压过程中温度的控制,避免因过热导致的变形或缺陷。
五、表面处理要求1. 表面处理应根据五金冲压件的使用环境和要求进行选择,如镀锌、喷涂、电镀等。
2. 表面处理应保证均匀、牢固,符合相关标准的耐腐蚀、耐磨损要求。
3. 表面处理后的五金冲压件应进行质量检测,包括涂层厚度、附着力等。
六、质量管理要求1. 五金冲压件在生产过程中应进行全程质量控制,包括原材料的检测、生产过程的监控和成品的检验。
2. 质量管理体系应符合ISO9001等相关认证标准,保证产品的质量稳定性和可追溯性。
3. 对于批量生产的五金冲压件,应进行抽样检验,确保产品的合格率稳定在可接受的范围内。
七、检测要求1. 五金冲压件的检测应包括尺寸、形状、力学性能、表面质量等方面的检验。
2. 对于关键性能的五金冲压件,如安全零部件、工程机械零部件等,应进行可靠性测试和耐久性测试。
冲压件中的行业标准与规范

冲压件中的行业标准与规范在制造业中,冲压件是一种常见的零部件,广泛应用于汽车、电子、家电等领域。
为了保证冲压件的质量和可靠性,行业标准和规范被广泛使用和遵循。
本文将介绍冲压件中常见的行业标准和规范,以及它们在冲压件制造中的重要性。
一、ISO/TS 16949标准ISO/TS 16949标准是汽车行业质量管理体系的国际标准,也是冲压件行业中常用的标准之一。
它要求冲压件制造商实施全面的质量管理体系,包括质量方针、质量目标的设定和达成,以及持续改进等。
ISO/TS 16949标准的遵循确保了冲压件的质量稳定和满足汽车制造商的要求,从而提高了产品的竞争力和市场认可度。
二、国家标准除了ISO/TS 16949标准外,每个国家都有一套适用于本国制造业的标准和规范。
这些国家标准通常包括产品设计、材料选择、工艺要求和尺寸容差等方面的规定。
冲压件制造商需要熟悉并遵循国家标准,以确保生产的冲压件符合国内相关法规和技术要求。
三、材料标准在冲压件制造过程中,材料的选择对产品的质量和性能有着重要影响。
各种金属材料如钢、铝、铜等都有各自的标准,包括材料的化学成分、力学性能、热处理要求等。
冲压件制造商需要根据产品的具体要求选择合适的材料,并确保符合相应的材料标准,以确保产品的可靠性和持久性。
四、尺寸和容差标准冲压件的尺寸和容差对于产品的装配和性能至关重要。
制定统一的尺寸和容差标准有助于保证冲压件的互换性和一致性。
国际上常用的尺寸和容差标准包括ISO2768和ISO 286。
冲压件制造商需要按照这些标准进行产品设计和制造,以确保产品的尺寸和容差在可接受范围内。
五、模具制造标准在冲压件制造过程中,模具是不可或缺的工具。
模具的质量和精度直接影响到冲压件的加工质量。
因此,模具制造需要遵循相应的标准和规范,包括模具材料的选择、设计和加工要求等。
常用的模具制造标准有ISO 9001和ISO 14001等。
冲压件制造商需要选择合适的模具制造商并确保其符合相应的标准,以保证模具的质量和使用寿命。
与冲压加工有关的国家标准
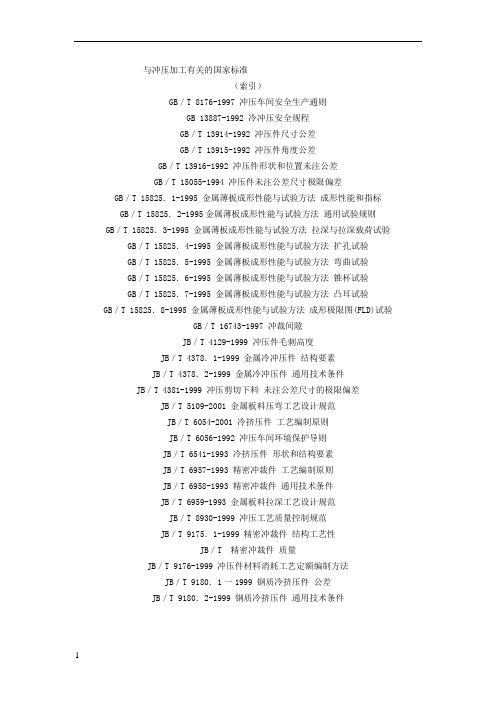
与冲压加工有关的国家标准(索引)GB/T 8176-1997 冲压车间安全生产通则GB 13887-1992 冷冲压安全规程GB/T 13914-1992 冲压件尺寸公差GB/T 13915-1992 冲压件角度公差GB/T 13916-1992 冲压件形状和位置未注公差GB/T 15055-1994 冲压件未注公差尺寸极限偏差GB/T 15825.1-1995 金属薄板成形性能与试验方法成形性能和指标GB/T 15825.2-1995金属薄板成形性能与试验方法通用试验规则GB/T 15825.3-1995 金属薄板成形性能与试验方法拉深与拉深载荷试验GB/T 15825.4-1995 金属薄板成形性能与试验方法扩孔试验GB/T 15825.5-1995 金属薄板成形性能与试验方法弯曲试验GB/T 15825.6-1995 金属薄板成形性能与试验方法锥杯试验GB/T 15825.7-1995 金属薄板成形性能与试验方法凸耳试验GB/T 15825.8-1995 金属薄板成形性能与试验方法成形极限图(FLD)试验GB/T 16743-1997 冲裁间隙JB/T 4129-1999 冲压件毛刺高度JB/T 4378.1-1999 金属冷冲压件结构要素JB/T 4378.2-1999 金属冷冲压件通用技术条件JB/T 4381-1999 冲压剪切下料未注公差尺寸的极限偏差JB/T 5109-2001 金属板料压弯工艺设计规范JB/T 6054-2001 冷挤压件工艺编制原则JB/T 6056-1992 冲压车间环境保护导则JB/T 6541-1993 冷挤压件形状和结构要素JB/T 6957-1993 精密冲裁件工艺编制原则JB/T 6958-1993 精密冲裁件通用技术条件JB/T 6959-1993 金属板料拉深工艺设计规范JB/T 8930-1999 冲压工艺质量控制规范JB/T 9175.1-1999 精密冲裁件结构工艺性JB/T 精密冲裁件质量JB/T 9176-1999 冲压件材料消耗工艺定额编制方法JB/T 9180.1一1999 钢质冷挤压件公差JB/T 9180.2-1999 钢质冷挤压件通用技术条件1。
冲压过程技术标准
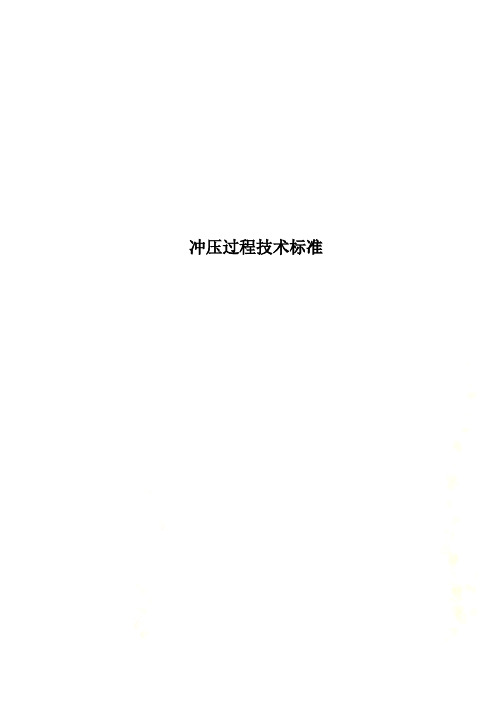
冲压过程技术标准冲压工艺培训教材魏龙2004-5第一章绪论冷冲压是一种先进的金属加工方法,它是建立在金属塑性变形的基础上,利用模具和冲压设备对板料金属进行加工,以获得所需要的零件形状和尺寸。
冲压工艺应用范围十分广泛,在国民经济各个部门中,几乎都有冲压加工产品,如汽车、飞机、拖拉机、电机、电器、仪表、铁道、邮电、化工以及轻工日用产品中均占有相当大的比重。
冷冲压和切削加工比较,具有生产率高、加工成本低、材料利用率高、产品尺寸精度稳定、操作简单、容易实现机械化和自动化等一系列优点,特别适合大批量生产。
一、冲压工序的分类冷冲压工艺按其变形性质可分为分离工序和成形工序两大类。
分离工序又可分为落料、冲孔和切边等,如表1-1所示。
成形工序可分为弯曲、拉深、翻孔、翻边、胀形、扩口、缩口和旋压等,如表1-2所示。
根据产品零件的形状、尺寸精度和其他技术要求,可分别采用各种工序对板料毛坯进行加工,以获得满意的零件。
表1-1 分离工序工序名称简图特点及应用范围落料废料零件用冲模沿封闭轮廓曲线冲切,冲下部分是零件。
用于制造各种形状的平板零件。
冲孔废料零件用冲模沿封闭轮廓曲线冲切,冲下部分是废料。
切边将成形零件的边缘修切整齐或切成一定形状。
表1-2 成形工序工序名称简图特点及应用范围弯曲将板料沿直线弯成各种形状,可以加工形状极为复杂的零件。
拉深将板料毛坯成形制成各种空心的零件。
翻孔在预先冲孔的板料半成品上或未经冲孔的板料冲制成竖立的边缘。
第二章冲裁冲裁是利用模具使板料产生分离的冲压工序,包括落料、冲孔、切口、剖切、修边等。
用它可以制作零件或为弯曲、拉深、成形等工序准备毛坯。
一、落料从板料上冲下所需形状的零件(或毛坯)叫落料。
如图2-1所示。
废料零件图2-1 落料废料零件图2-2 冲孔二、冲孔在工件上冲出所需形状的孔(冲去的为废料)叫冲孔。
如图2-2所示。
三、冲裁的过程冲裁既是分离工序,工件受力时必然从弹、塑性变形开始,以断裂告终。
冲压工艺通用技术要求

1 范围本标准规定了金属冷冲压件在原材料、形状和尺寸、表面质量、热处理、检验规则、包装等方面的通用技术要求。
本标准适用于冷冲压方法生产的板料厚度大于0.1mm的金属冷冲压件。
2 引用标准GB/T 710-1991 优质碳素结构钢热轧薄钢板和钢带GB/T 716-1991 碳素结构钢冷轧钢带GB/T 2517-1981 一般结构用热连轧钢板和钢带GB/T 2521-1996 冷轧晶粒取向、无取向磁性钢带(片)3 定义本标准采用下列定义。
3.1 平冲压件指经平面冲裁工序加工而成平面形状的冲压件。
3.2 成形冲压件经弯曲,拉深和其他成形工序加工而成的冲压件。
3.3 孔组间距同一零件上一组孔的中心线和另一组孔的中心线间的距离。
3.4 毛刺冲裁时存留在冲压件断面上突起的锋利的材料。
3.5 冲裁断面粗糙度指冲裁断面上剪裂带的粗糙度。
3.6 表面质量冲压件在成形过程中,由非冲裁断面形成的零件表面产生的各种物理现象。
4 技术要求冲压件应按经规定程序批准的产品图样和技术文件制造,产品图样和技术文件中未规定的要求,应符合本标准的规定。
4.1 原材料4.1.1 冲压件使用的原材料,需符合GB/T 710、GB/T 716、GB/T 2517、GB/T 2521等有关金属材料的标准规定,并符合对材料的供货状态或其他方面的要求。
4.1.2 冲压件的原材料应有关质量证明书,它保证材料符合规定的技术要求。
当无质量证明书或其他原因,冲压件生产厂可按需要选择原材料进行复检。
复检的主要项目和内容:4.1.2.1 外观检验:检验材料表面缺陷、污痕、外廓尺寸、形状和厚度以及表面粗糙度。
4.1.2.2 化学分析、金相检验:分析材料总化学元素的含量;判定材料晶粒度级别和均匀程度;评定材料中游离渗碳体、带状组织和非金属夹杂物的级别;检查材料缩孔、疏松等缺陷。
4.1.2.3 力学性能检验:检验材料的抗拉强度δb、屈服强度δs、屈强比δs/δb、伸长率δ、断面收缩率ψ及洛氏硬度HRB等。
五金冲压件技术要求标准

五金冲压件技术要求标准五金冲压件作为一种常见的零部件,广泛应用于汽车、家电、机械设备等各个领域,因此其技术要求标准显得尤为重要。
下面就五金冲压件的技术要求标准进行详细的阐述。
一、原材料选择五金冲压件的原材料选择对其质量起着决定性作用。
通常情况下,五金冲压件所选用的原材料应具有良好的塑性变形能力和焊接性能,能够满足强度要求,并具有良好的表面质量。
常见的五金冲压件原材料包括冷轧钢板、镀锌钢板、不锈钢板、铝合金板等。
在原材料的选择上,应根据产品的具体使用场景和要求来合理选择,以确保产品性能的稳定性和可靠性。
二、冲压工艺要求1.模具设计:五金冲压件的模具设计应考虑到冲压件的结构、尺寸精度、表面质量等因素,确保产品的一致性和稳定性。
2.冲压设备:应配备高精度、高稳定性的冲床设备,并保持设备的良好状态,确保冲压速度、压力等参数符合要求。
3.冲压工艺控制:应建立冲压工艺流程并进行严格控制,包括送料、定位、冲压、脱模等工序均应符合要求,以确保产品的尺寸精度和表面质量。
4.件型结构:五金冲压件的结构设计应合理,以确保产品的安装和使用性能,避免因工艺导致的变形或断裂等缺陷。
5.材料回弹控制:在冲压过程中要合理控制材料的回弹变形,确保产品尺寸精度和表面要求。
三、表面处理要求五金冲压件在生产过程中往往需要进行表面处理,以满足不同的使用要求。
常见的表面处理工艺包括镀锌、喷涂、电镀等。
在表面处理过程中,应确保处理层的厚度、附着力、耐腐蚀性等指标满足产品的要求。
四、质量检测要求1.尺寸检测:应建立尺寸检测标准,采用高精度的检测设备进行尺寸检测,确保产品的尺寸精度。
2.表面质量检测:应建立表面质量标准,采用目视、手感等方式对产品表面进行检测,并可借助检测仪器进行表面粗糙度、平整度等指标的检测。
3.力学性能检测:对五金冲压件的拉伸强度、屈服强度、延伸率等力学性能进行检测,以确保产品的使用性能。
4.包装运输:应建立包装标准,并对产品包装进行检测,以确保产品在运输过程中不受损。
五金冲压件技术要求标准
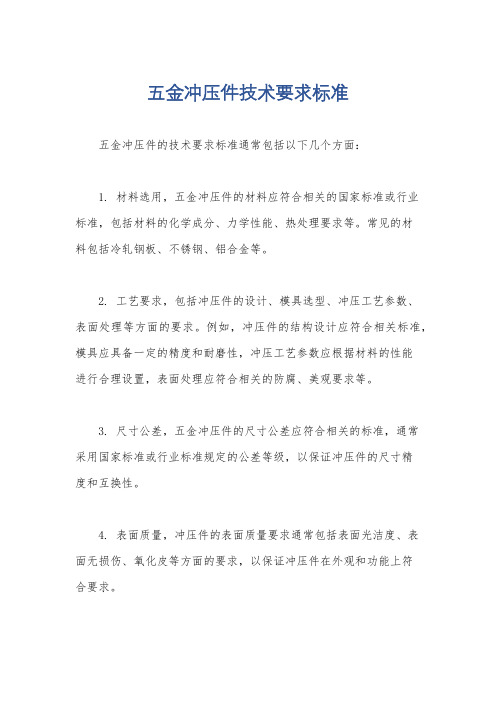
五金冲压件技术要求标准
五金冲压件的技术要求标准通常包括以下几个方面:
1. 材料选用,五金冲压件的材料应符合相关的国家标准或行业
标准,包括材料的化学成分、力学性能、热处理要求等。
常见的材
料包括冷轧钢板、不锈钢、铝合金等。
2. 工艺要求,包括冲压件的设计、模具选型、冲压工艺参数、
表面处理等方面的要求。
例如,冲压件的结构设计应符合相关标准,模具应具备一定的精度和耐磨性,冲压工艺参数应根据材料的性能
进行合理设置,表面处理应符合相关的防腐、美观要求等。
3. 尺寸公差,五金冲压件的尺寸公差应符合相关的标准,通常
采用国家标准或行业标准规定的公差等级,以保证冲压件的尺寸精
度和互换性。
4. 表面质量,冲压件的表面质量要求通常包括表面光洁度、表
面无损伤、氧化皮等方面的要求,以保证冲压件在外观和功能上符
合要求。
5. 检测要求,冲压件的检测通常包括外观检查、尺寸检测、材料性能检测等,要求符合相关的检测标准,以保证冲压件的质量。
总的来说,五金冲压件的技术要求标准是为了保证冲压件的质量、性能和可靠性,同时也是为了满足客户的需求和相关的法律法规要求。
具体的要求会根据不同的产品、行业和国家而有所不同。
冲压件生产及工艺技术规范
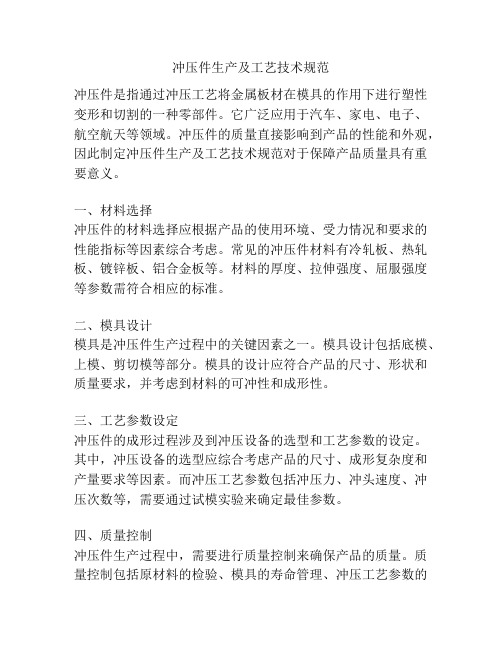
冲压件生产及工艺技术规范冲压件是指通过冲压工艺将金属板材在模具的作用下进行塑性变形和切割的一种零部件。
它广泛应用于汽车、家电、电子、航空航天等领域。
冲压件的质量直接影响到产品的性能和外观,因此制定冲压件生产及工艺技术规范对于保障产品质量具有重要意义。
一、材料选择冲压件的材料选择应根据产品的使用环境、受力情况和要求的性能指标等因素综合考虑。
常见的冲压件材料有冷轧板、热轧板、镀锌板、铝合金板等。
材料的厚度、拉伸强度、屈服强度等参数需符合相应的标准。
二、模具设计模具是冲压件生产过程中的关键因素之一。
模具设计包括底模、上模、剪切模等部分。
模具的设计应符合产品的尺寸、形状和质量要求,并考虑到材料的可冲性和成形性。
三、工艺参数设定冲压件的成形过程涉及到冲压设备的选型和工艺参数的设定。
其中,冲压设备的选型应综合考虑产品的尺寸、成形复杂度和产量要求等因素。
而冲压工艺参数包括冲压力、冲头速度、冲压次数等,需要通过试模实验来确定最佳参数。
四、质量控制冲压件生产过程中,需要进行质量控制来确保产品的质量。
质量控制包括原材料的检验、模具的寿命管理、冲压工艺参数的精确控制、产品尺寸的检测等。
对于质量不合格的冲压件,应及时进行修复或重新生产。
五、安全防护冲压件生产过程中存在着一定的安全隐患,如设备的挤压、机械手的夹紧等。
因此,必须加强对工人的安全教育和培训,并设立相应的安全防护措施,如安全栏杆、防护罩等,以降低事故的发生概率。
这些是冲压件生产及工艺技术规范中的一部分内容,通过制定规范并严格执行,可以提高冲压件生产的效率和质量,减少事故的发生。
同时,规范的执行也有助于促进冲压工艺的技术进步和产品质量的提高。
最终,有助于提升企业的竞争力和市场地位。
冲压模具标准及技术要求

第14章冲压模具标准及技术要求冲模标准是指在冲模设计与制造中应该遵循和执行的技术规范和标准。
制订冲模标准的意义有以下几个方面:1.可以缩短模具设计与制造周期因为模具结构及制造精度与冲压件的形状、尺寸精度以及生产的批量有关,所以冲模的种类繁多而且结构十分的复杂。
比如精密级进模的模具零件有时上百个(甚至更多),这样使得模具的设计与制造周期很长。
而实现模具标准化后,所有的标准件都可以外购,从而减化了模具的设计、减少了模具零件的制造工作量,最终的结构就是缩短了模具的制造周期。
2.有利于保证质量可以稳定和保证模具设计质量和制造中必须达到的质量规范,以保证冲压件的质量。
3.有利于模具的计算机辅助设计与制造模具技术标准使实现模具计算机辅助设计与制造的基础,可以这样说:没有模具标准化就没有模具的计算机辅助设计与制造。
4.有利于国际国内的交流与合作技术名词术语、技术条件的规范化、标准化将有利于国内、国际的商业贸易和技术交流,增强企业、国家的技术经济实力。
我国在模具行业中推广使用的模具标准是经国家技术监督局批准的国家标准(GB)和机械行业标准(JB)。
另外还有国际模具标准化组织ISO/TC29/SC8制订的冲模和成形模标准。
除此之外,由于我国一些企业从国外引进了大量级进模与汽车覆盖件模具,随着模具的引进,国外冲模标准也在我国一些企业中引用,如日本三住商事株式会议(MISUMI)的Face 标准,德国STRACK公司标准,美国DANLY公司标准等。
由于篇幅的原因,本篇只介绍常用的GB、JB及部分日本的Face标准。
14.1设计冲模时常用的标准我国已颁布的冲模技术标准见表14-1。
表14-1表14-1我国已颁布的冲模标准分类标准名称标准代号基础工艺质量1)冲模术语2)冲压件尺寸公差3)冲压件角度公差4)冲压件形状和位置未注公差5)冲压件未注公差尺寸极限偏差6)冲裁间隙7)冲模技术条件8)金属冷冲压件结构要素9)金属冷冲压件通用技术条件10)精密冲裁件通用技术条件GB/T8845-2006GB/T13914-2002GB/T13915-2002GB/T13196-2002GB/T15055-2007GB/T16743-1997GB/T14662-2006JB/T4378.1-1999JB/T4378.2-1999JB/T6958-1993设计冲压模具还应该执行和采用国家基础标准有:公差与配合标准;形状与位置公差;表面粗糙度标准;机械制图标准;尺寸及尺寸系列。
冲压过程技术标准

冲压工艺培训教材魏龙2004-5论绪第一章.冷冲压是一种先进的金属加工方法,它是建立在金属塑性变形的基础上,利用模具和冲压设备对板料金属进行加工,以获得所需要的零件形状和尺寸。
冲压工艺应用范围十分广泛,在国民经济各个部门中,几乎都有冲压加工产品,如汽车、飞机、拖拉机、电机、电器、仪表、铁道、邮电、化工以及轻工日用产品中均占有相当大的比重。
冷冲压和切削加工比较,具有生产率高、加工成本低、材料利用率高、产品尺寸精度稳定、操作简单、容易实现机械化和自动化等一系列优点,特别适合大批量生产。
一、冲压工序的分类冷冲压工艺按其变形性质可分为分离工序和成形工序两大类。
分离工序又可分为落料、冲孔和切边等,如表1-1所示。
成形工序可分为弯曲、拉深、翻孔、翻边、胀形、扩口、缩口和旋压等,如表1-2所示。
根据产品零件的形状、尺寸精度和其他技术要求,可分别采用各种工序对板料毛坯进行加工,以获得满意的零件。
分离工序1-1 表.工序名称简图特点及应用范围用冲模沿封闭轮廓线冲切,冲下部分落零件。
用于制造各零废形状的平板零件用冲模沿封闭轮廓冲线冲切,冲下部分废零废料将成形零件的边缘切切整齐或切成一定状表1-2 成形工序工序名称简图特点及应用范围将板料沿直线弯成各种形弯曲状,可以加工形状极为复杂的零件。
将板料毛坯成形制成各种拉深空心的零件。
在预先冲孔的板料半成翻上或未经冲孔的板料冲成竖立的边缘第二章冲裁冲裁是利用模具使板料产生分离的冲压工序,包括落料、冲孔、切口、剖切、修边等。
用它可以制作零件或为弯曲、拉深、成形等工序准备毛坯。
一、落料从板料上冲下所需形状的零件(或毛坯)叫落料。
如图2-1所示。
零件废料图2-1 落料废料零件图2-2 冲孔二、冲孔在工件上冲出所需形状的孔(冲去的为废料)叫冲孔。
如图2-2所示。
三、冲裁的过程冲裁既是分离工序,工件受力时必然从弹、塑性变形开始,以断裂告终。
当凸模下降接触板料,板料即受到凸、凹模压力而产生弹性变形,板料产生弯曲,即从模具表面上翘起(图2-3-1)。
- 1、下载文档前请自行甄别文档内容的完整性,平台不提供额外的编辑、内容补充、找答案等附加服务。
- 2、"仅部分预览"的文档,不可在线预览部分如存在完整性等问题,可反馈申请退款(可完整预览的文档不适用该条件!)。
- 3、如文档侵犯您的权益,请联系客服反馈,我们会尽快为您处理(人工客服工作时间:9:00-18:30)。
冲压件生产及工艺技术标准
冲压件是指通过模具将板材进行冲压变形、切割、折叠、拉伸等加工工艺,制成规定形状和尺寸的金属件。
冲压件具有尺寸精确、形状复杂、质量稳定、生产效率高等优点,广泛应用于汽车、航空航天、电子、家电等行业。
冲压件的生产过程包括工艺设计、模具制造和冲压加工三个环节。
首先,根据产品的形状和需求,进行工艺设计,确定材料的选择、厚度的测量和模具的设计。
其次,制造模具,模具的制作需要考虑产品的形状、尺寸、材料等因素,模具一般由上模和下模组成。
最后,进行冲压加工,将制作好的模具放入冲压机中,通过冲压机的力量,使模具对板材进行压缩、切割、折叠等操作,最终得到所需的冲压件。
冲压件的工艺技术标准主要包括以下几个方面:
1. 材料选择和精度要求:冲压件的材料选择应根据产品的要求和使用环境来确定,通常选用金属材料,如钢板、铝板等。
同时,冲压件的尺寸精确度要求较高,达到产品设计要求。
2. 模具设计和制造:模具的设计应符合产品的形状、尺寸和材料要求,确保冲压件的质量和生产效率。
模具的制造一般采用数控加工等先进工艺,确保模具的精度和稳定性。
3. 冲压工艺参数:包括冲击力、压缩力、冲头行程、冲压速度等参数的设定,这些参数决定了冲压件的成形过程和质量。
4. 表面处理:冲压件在成形过程中,可能会产生裂纹、毛刺等问题,需要进行表面处理,如研磨、打磨、抛光等,提高冲压件的质量。
5. 检测和质量控制:对冲压件进行尺寸、形状、质量等方面的检测,确保产品符合标准要求。
同时,建立完善的质量控制体系,监控生产过程,及时发现和纠正问题。
冲压件生产和工艺技术标准的制定,可以确保产品的质量和稳定性,提高生产效率,减少生产成本。
同时,还可以推动行业的发展和创新,提高冲压件在各个领域的应用和竞争力。