模具设计技术要求
模具的技术要求

装配过程中零件不允许磕、碰、划伤和锈蚀。
螺钉、螺栓和螺母紧固时,严禁打击或使用不合适的旋具和扳手。紧固后螺钉槽、螺母和螺钉、螺栓头部不得损坏。
规定拧紧力矩要求的紧固件,必须采用力矩扳手,并按规定的拧紧力矩紧固。
同一零件用多件螺钉(螺栓)紧固时,各螺钉(螺栓)需交叉、对称、逐步、均匀拧紧。
补焊前必须将缺陷彻底清除,坡口面应修的平整圆滑,不得有尖角存在。
根据铸钢件缺陷情况,对补焊区缺陷可采用铲挖、磨削,炭弧气刨、气割或机械加工等方法清除。
补焊区及坡口周围20mm以内的粘砂、油、水、锈等脏物必须彻底清理。
在补焊的全过程中,铸钢件预热区的温度不得低于350°C。
在条件允许的情况下,尽可能在水平位置施焊。
补焊时,焊条不应做过大的横向摆动。
铸钢件表面堆焊接时,焊道间的重叠量不得小于焊道宽度的1/3。
10.锻件要求:
每个钢锭的水口、冒口应有足够的切除量,一以保证锻件无缩孔和严重的偏折。
锻件应在有足够能力的锻压机上锻造成形,以保证锻件内部充分锻透。
锻件不允许有肉眼可见的裂纹、折叠和其他影响使用的外观缺陷。局部缺陷可以清除,但清理深度不得超过加工余量的75%,锻件非加工表面上的缺陷应清理干净并圆滑过渡。
轴承外圈与开式轴承座及轴承盖的半圆孔不准有卡住现象。
轴承外圈与开式轴承座及轴承盖的半圆孔应接触良好,用涂色检查时,与轴承座在对称于中心线120°、与轴承盖在对称于中心线90°的范围内应均匀接触。在上述范围内用塞尺检查时,0.03mm的塞尺不得塞入外圈宽度的1/3。
轴承外圈装配后与定位端轴承盖端面应接触均匀。
塑胶模具技术要求模板

塑胶模模具技术要求本技术要求从以下方面来要求: 1、 塑胶模要求塑胶模要求 2、 塑胶模设计技术要求塑胶模设计技术要求3、 塑胶模的检验和验收技术要求4、 塑胶模的设计审核塑胶模的设计审核5、 模具标识模具标识6、 备件备件7、 模具的包装、运输模具的包装、运输 8、 模具的使用规定模具的使用规定 9、 模具的维护、保养和贮存模具的维护、保养和贮存一、塑胶模要求 1、替换A.A. 除非得到甲方项目经理的书面授权及承认,任何替代或违背本份标准的任何要求都是不允许的。
2、要求模具制造的产品应与以下保证一致:a. a. 产品图面产品图面产品图面b.b. 形状尺寸及公差形状尺寸及公差c.c. 首件承认程序要求首件承认程序要求3、模具设计所有权、模具设计所有权根据设计及组装购买合同,甲方对应给甲方的模具设计具有所有权。
因此,供应商应无保留的供应所有的图纸及相关磁片和铜公。
图纸及相关磁片和铜公。
4、模具设计责任、模具设计责任1) 供应商对模具设计、组装、功能以及反复制造产品的能力负主要责任。
2) 任何在模具试模及接受过程中发现的错误应由供应商更正,任何相关费用与甲方无关。
5、模具性能、模具性能1)在模具设计及组装中应考虑由项目经理提出的最佳生产速率,在模具设计及组装中应考虑由项目经理提出的最佳生产速率,这个目的就是研究更新的技术去增加模具这个目的就是研究更新的技术去增加模具生产机床的速率。
这将转换为在更短的时间内获得更高的制造能力2) 2) 在模具最终接受前,所有生产甲方产品的模具必须获得首件承认以及产品生产速率在模具最终接受前,所有生产甲方产品的模具必须获得首件承认以及产品生产速率6、图纸审核确认、图纸审核确认1)乙方在设计方案完成之后,立即提供甲方审议,甲方认可后方可开始动工制造。
2)要求乙方在合同签定七天内提供模具加工进度表给甲方认可,并每周通报一次加工进度。
7、设变A. A. 甲方有权利在模具设计及组立过程中变更产品设计及模具设计。
模具技术要求
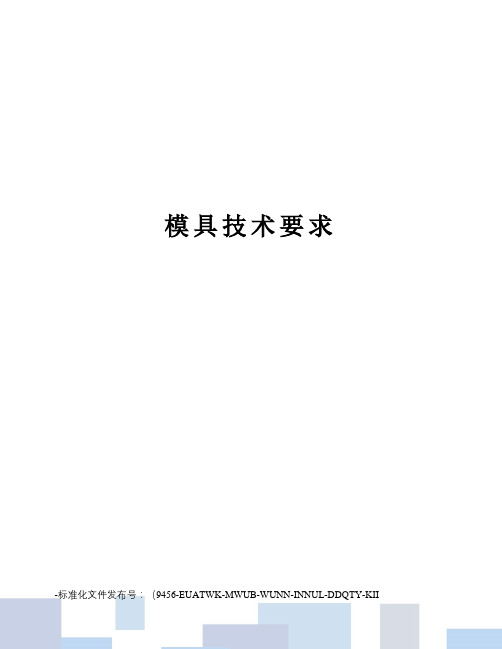
模具技术要求-标准化文件发布号:(9456-EUATWK-MWUB-WUNN-INNUL-DDQTY-KII模具技术要求一.模具材料及热处理要求1.拉延、成形类模具外板件拉延序凸模、凹模及压边圈使用GGG70L铸铁,淬火硬度HRC50-55;内板件凸模、凹摸及压边圈使用MoCr铸铁,淬火硬度HRC50-55。
特殊情况下须渗氮或TD处理(模具图纸会签时确认)。
变形剧烈及高强度钢板(抗拉强度≥350MPa)的制件应采用整体镶Cr12MoV;淬火硬度要达到HRC58—62。
基体采用HT300。
采用键槽与螺栓链接。
GGG70L铸件厂:天津虹岗或长城精工或经甲方认可的同等铸造品质铸造厂。
2.冲裁类模具普通板料零件料厚小于或等于1.2mm的刃口镶块可采用空冷钢(7CrSiMnMoV 或ICD-5),淬火硬度HRC55-60;料厚大于1.2mm的采用Cr12MoV材料,淬火硬度为HRC58~62。
料厚大于等于1.4mm的镶块采用波浪刃口。
高强度板的制件采用Cr12MoV材料,淬火硬度为HRC58~62。
所有凹模镶块、废料刀均采用背托,凹模采用镶块结构,凸模可采用整体结构。
模具基体采用HT300。
3.翻边、整形类模具中大型模具凹模镶块原则上应采用侧面固定式以便于调整;小型模具可采用整体式结构,料厚大于1.4mm的凹模采用镶块式。
零件料厚小于或等于1.2mm,材料可选用MoCr/7CrSiMnMoV;零件料厚大于1.2mm 的采用Cr12MoV或与之相当的材料(应取得甲方工艺认可,具体以会签为准)。
普通板料的制件凸模可采用合金铸铁,表面淬火硬度不低于HRC50;高强度板的制件采用Cr12MoV材料,淬火硬度为HRC58-62;如采用分体或镶块式基座(底板)可采用HT300的材料。
对于部分易拉毛部位,必要时需进行TD处理。
4.压料(退料)顶出器可采用铸造结构,但应根据其强度要求,决定用铸铁或球铁或铸钢材料(工艺会签时,甲方根据具体结构决定)。
冲压模具设计技术要求
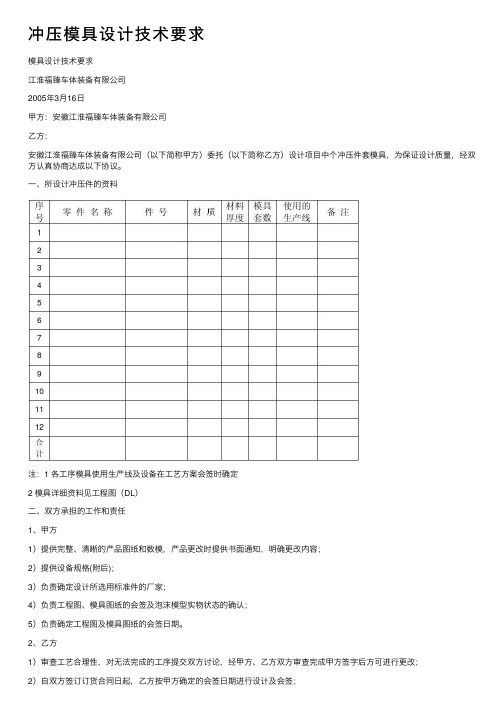
冲压模具设计技术要求模具设计技术要求江淮福臻车体装备有限公司2005年3⽉16⽇甲⽅:安徽江淮福臻车体装备有限公司⼄⽅:安徽江淮福臻车体装备有限公司(以下简称甲⽅)委托(以下简称⼄⽅)设计项⽬中个冲压件套模具,为保证设计质量,经双⽅认真协商达成以下协议。
⼀、所设计冲压件的资料注:1 各⼯序模具使⽤⽣产线及设备在⼯艺⽅案会签时确定2 模具详细资料见⼯程图(DL)⼆、双⽅承担的⼯作和责任1、甲⽅1)提供完整、清晰的产品图纸和数模,产品更改时提供书⾯通知,明确更改内容;2)提供设备规格(附后);3)负责确定设计所选⽤标准件的⼚家;4)负责⼯程图、模具图纸的会签及泡沫模型实物状态的确认;5)负责确定⼯程图及模具图纸的会签⽇期。
2、⼄⽅1)审查⼯艺合理性,对⽆法完成的⼯序提交双⽅讨论,经甲⽅、⼄⽅双⽅审查完成甲⽅签字后⽅可进⾏更改;2)⾃双⽅签订订货合同⽇起,⼄⽅按甲⽅确定的会签⽇期进⾏设计及会签;3)⼄⽅必须向甲⽅提供完整的电⼦版⼯程(DL)图(⼯序内容完整,图形表⽰清晰)和其他相关图纸、资料;4)⼄⽅必须对所设计的图纸进⾏认真校对和审核,电⼦版图纸上必须有设计⼈员、校对⼈员、审核⼈员的签名;5)所有结论前的产品及⼯艺更改,涉及到设计内容的则需要修改相应⼯程图、模具图及检具图。
对于⼯作量较⼤的,增加费⽤问题与甲⽅协商解决;6)按甲⽅清单注明的零件需做成型模拟分析的,提供模拟结果并对结果负责;7)⼄⽅所设计模具必须符合甲⽅⾃动化⽣产要求:机械⼿上下件、⽓动挺件、废料⾃动滑出等;8)如甲⽅在⽣产制造过程中对⼄⽅所设计的图纸存在疑问,⼄⽅有责任在24⼩时内派技术⼈员对现场进⾏解疑及指导。
三、模具寿命及冲压线分布1、开发模具⽣产纲领要求:总寿命万辆,(双、单)班万辆/年。
2、冲压设备流⽔分布图⽰:1) A线:2) B1线:3) B2线:4) C1线:5)C2线:四、制图标准的基本要求1、⼄⽅在进⾏⼯艺⽅案和模具设计时,应按本协议要求执⾏,如设计时有超出本协议的内容,可双⽅协商解决。
模具设计的几个要求

模具设计的几个要求第一篇:模具设计的几个要求青岛海培德模具加工厂模具设计的几个要求1.冲压工艺性分析冲压工艺性是指零件冲压加工的难易程度。
在技术方面,主要分析该零件的形状特点、尺寸大小(最小孔边距、孔径、材料厚度、最大外形)、精度要求和材料性能等因素是否符合冲压工艺的要求。
如果发现冲压工艺性差,则需要对冲压件产品提出修改意见,经产品设计者同意后方可修改。
.搜集必要的资料设计冷冲模时,需搜集的资料包括产品图、样品、设计任务书和参考图等,并相应了解如下问题:)了解最大限度采用标准件的可能性,以缩短模具制造周期。
)了解制件的生产性质是试制还是批量或大量生产,以确定模具的结构性质。
)了解适用的压力机情况和有关技术规格,根据所选用的设备确定与之相适应的模具及有关参数,如模架大小、模柄尺寸、模具闭合高度和送料机构等。
)了解提供的产品视图是否完备,技术要求是否明确,有无特殊要求的地方。
5)了解模具制造的技术力量、设备条件和加工技巧,为确定模具结构提供依据。
)了解制件的材料性质(软、硬还是半硬)、尺寸和供应方式(如条料、卷料还是废料利用等),以便确定冲裁的合理间隙及冲压的送料方法。
.确定合理的冲压工艺方案确定方法如下:)最后从产品质量、生产效率、设备占用情况、模具制造的难易程度、模具寿命、工艺成本、操作方便和安全程度等方面进行综合分析、比较,在满足冲件质量要求的前提下,确定适合具体生产条件的最经济合理的冲压工艺方案,并填写冲压工艺过程卡片(内容包括工序名称、工序数目、工序草图(半成品形状和尺寸)、所用模具、所选设备、工序检验要求、板料规格和性能、毛坯形状和尺寸等):;)根据工艺计算,确定工序数目,如拉深次数等。
)根据各工序的变形特点、尺寸要求确定工序排列的顺序,例如,是先冲孔后弯曲还是先4)根据生产批量和条件,确定工序的组合,如复合冲压工序、连续冲压工序等。
)根据工件的形状、尺寸精度、表面质量要求进行工艺分析,确定基本工序的性质,即落料、冲孔、弯曲等基本工序。
模具技术要求及验收标准
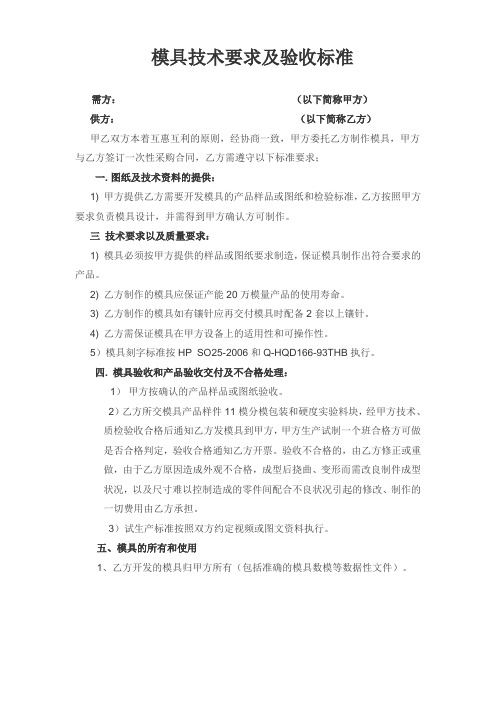
模具技术要求及验收标准
需方:(以下简称甲方)
供方:(以下简称乙方)
甲乙双方本着互惠互利的原则,经协商一致,甲方委托乙方制作模具,甲方与乙方签订一次性采购合同,乙方需遵守以下标准要求;
一. 图纸及技术资料的提供:
1) 甲方提供乙方需要开发模具的产品样品或图纸和检验标准,乙方按照甲方要求负责模具设计,并需得到甲方确认方可制作。
三技术要求以及质量要求:
1) 模具必须按甲方提供的样品或图纸要求制造,保证模具制作出符合要求的产品。
2) 乙方制作的模具应保证产能20万模量产品的使用寿命。
3) 乙方制作的模具如有镶针应再交付模具时配备2套以上镶针。
4) 乙方需保证模具在甲方设备上的适用性和可操作性。
5)模具刻字标准按HP SO25-2006和Q-HQD166-93THB执行。
四. 模具验收和产品验收交付及不合格处理:
1)甲方按确认的产品样品或图纸验收。
2)乙方所交模具产品样件11模分模包装和硬度实验料块,经甲方技术、质检验收合格后通知乙方发模具到甲方,甲方生产试制一个班合格方可做是否合格判定,验收合格通知乙方开票。
验收不合格的,由乙方修正或重做,由于乙方原因造成外观不合格,成型后挠曲、变形而需改良制件成型状况,以及尺寸难以控制造成的零件间配合不良状况引起的修改、制作的一切费用由乙方承担。
3)试生产标准按照双方约定视频或图文资料执行。
五、模具的所有和使用
1、乙方开发的模具归甲方所有(包括准确的模具数模等数据性文件)。
模具开发技术要求
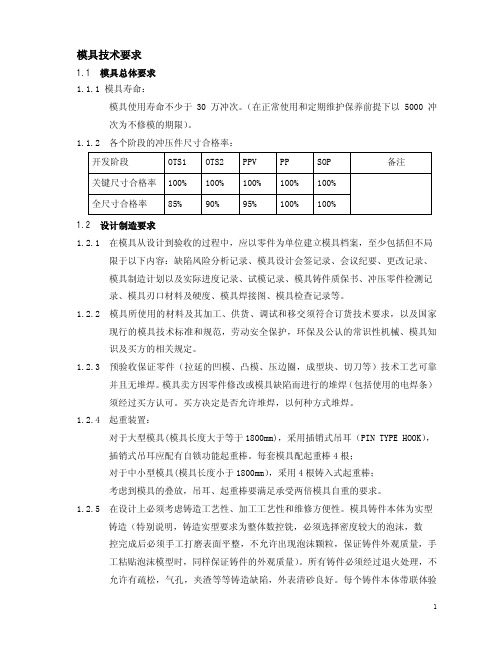
模具技术要求1.1 模具总体要求1.1.1 模具寿命:模具使用寿命不少于30万冲次。
(在正常使用和定期维护保养前提下以 5000 冲次为不修模的期限)。
1.1.2 各个阶段的冲压件尺寸合格率:开发阶段OTS1 OTS2 PPV PP SOP 备注关键尺寸合格率100% 100% 100% 100% 100%全尺寸合格率85% 90% 95% 100% 100%1.2 设计制造要求1.2.1 在模具从设计到验收的过程中,应以零件为单位建立模具档案,至少包括但不局限于以下内容:缺陷风险分析记录、模具设计会签记录、会议纪要、更改记录、模具制造计划以及实际进度记录、试模记录、模具铸件质保书、冲压零件检测记录、模具刃口材料及硬度、模具焊接图、模具检查记录等。
1.2.2 模具所使用的材料及其加工、供货、调试和移交须符合订货技术要求,以及国家现行的模具技术标准和规范,劳动安全保护,环保及公认的常识性机械、模具知识及买方的相关规定。
1.2.3 预验收保证零件(拉延的凹模、凸模、压边圈,成型块、切刀等)技术工艺可靠并且无堆焊。
模具卖方因零件修改或模具缺陷而进行的堆焊(包括使用的电焊条)须经过买方认可。
买方决定是否允许堆焊,以何种方式堆焊。
1.2.4 起重装置:对于大型模具(模具长度大于等于1800mm),采用插销式吊耳(PIN TYPE HOOK),插销式吊耳应配有自锁功能起重棒。
每套模具配起重棒4根;对于中小型模具(模具长度小于1800mm),采用4根铸入式起重棒;考虑到模具的叠放,吊耳、起重棒要满足承受两倍模具自重的要求。
1.2.5 在设计上必须考虑铸造工艺性、加工工艺性和维修方便性。
模具铸件本体为实型铸造(特别说明,铸造实型要求为整体数控铣,必须选择密度较大的泡沫,数控完成后必须手工打磨表面平整,不允许出现泡沫颗粒,保证铸件外观质量,手工粘贴泡沫模型时,同样保证铸件的外观质量)。
所有铸件必须经过退火处理,不允许有疏松,气孔,夹渣等等铸造缺陷,外表清砂良好。
模具设计总体要求
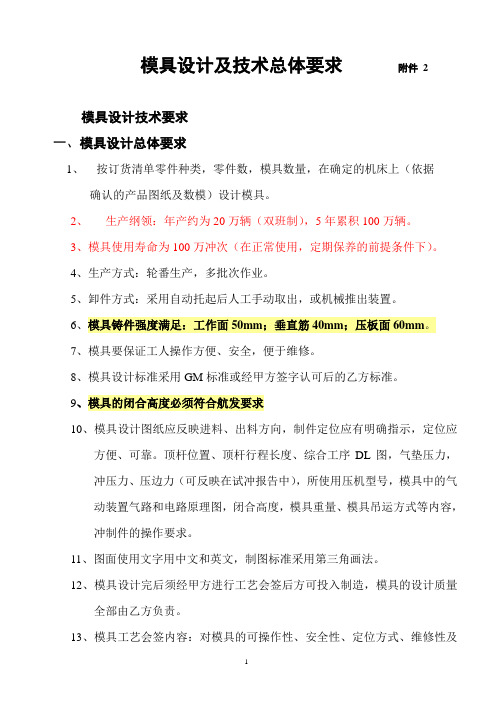
模具设计及技术总体要求附件 2模具设计技术要求一、模具设计总体要求1、按订货清单零件种类,零件数,模具数量,在确定的机床上(依据确认的产品图纸及数模)设计模具。
2、生产纲领:年产约为20万辆(双班制),5年累积100万辆。
3、模具使用寿命为100万冲次(在正常使用,定期保养的前提条件下)。
4、生产方式:轮番生产,多批次作业。
5、卸件方式:采用自动托起后人工手动取出,或机械推出装置。
6、模具铸件强度满足:工作面50mm;垂直筋40mm;压板面60mm。
7、模具要保证工人操作方便、安全,便于维修。
8、模具设计标准采用GM标准或经甲方签字认可后的乙方标准。
9、模具的闭合高度必须符合航发要求10、模具设计图纸应反映进料、出料方向,制件定位应有明确指示,定位应方便、可靠。
顶杆位置、顶杆行程长度、综合工序DL图,气垫压力,冲压力、压边力(可反映在试冲报告中),所使用压机型号,模具中的气动装置气路和电路原理图,闭合高度,模具重量、模具吊运方式等内容,冲制件的操作要求。
11、图面使用文字用中文和英文,制图标准采用第三角画法。
12、模具设计完后须经甲方进行工艺会签后方可投入制造,模具的设计质量全部由乙方负责。
13、模具工艺会签内容:对模具的可操作性、安全性、定位方式、维修性及模具对甲方压机规格的适应性等进行检查。
14、订货模具的图纸设计必须采用公制ISO标准。
15、模具的总体结构应便于直接安装、拆卸、使用,并有足够刚性。
16、修边、冲孔、翻边、整形等模具的侧面,上平面开观察检验窗口。
修边刃口与制件夹角小于75°时要充分考虑避免毛刺产生的措施。
17、冲孔凹模尽量采用镶件结构,并符合快卸式易更换原则。
18、导向润滑采用自润滑结构。
19、交付验收时的模具必须与模具设计图、冲压工序工程图保持一致,要求实物和图纸相符。
20、乙方所选用的试冲压机,必须是机械压力机,其压力机的性能及吨位应考虑与甲方选用的压力机相对应(拉深模必须在机械压力机上试压)。
压铸模具的技术要求文档

压铸模具的技术要求文档压铸模具是现代工业生产中常用的一种模具,用于制造各种金属制品。
压铸模具的技术要求非常高,对模具的设计、制造、使用等方面都有相应的要求。
本文将从几个方面详细介绍压铸模具的技术要求。
一、设计要求1.模具结构设计要合理,要考虑到产品的结构特点、工艺要求等因素,并保证在模具使用中有较高的稳定性和精度。
2.模腔的设计要充分考虑充型性、冷却性、顶出性等要素,确保产品成型质量稳定。
3.模具的开口方式、进料方式等设计要符合产品要求,并能保证模具的安全操作。
二、材料要求1.模具材料应具有良好的刚性、韧性和耐磨性,能够承受较大的冲击负荷和高温环境,如工具钢、合金钢等。
2.模具的热处理要求良好,能够使模具硬度均匀、稳定,延长使用寿命。
三、制造要求1.模具加工要求高精度、高质量,要保证模具的尺寸精度和表面质量。
2.维修和保养要定期进行,及时处理模具的磨损、损伤等问题,确保模具的正常使用和寿命。
四、使用要求1.模具的操作人员要具备一定的技能和经验,严格按照操作规程进行操作,保证操作的安全和准确性。
2.模具的使用环境要保持清洁、干燥,避免灰尘、水汽等对模具的损坏。
3.模具的顶出装置、冷却装置等要保持良好的工作状态,及时进行维修和更换。
五、质量控制要求1.模具的尺寸精度、表面质量等要进行严格的检测和控制,保证产品的准确性和一致性。
2.定期对模具进行检测和维修,及时发现并解决模具的问题,防止因模具问题引起的产品质量问题。
总结:压铸模具的技术要求非常高,对模具的设计、制造、使用等方面都有严格要求。
只有合理的设计,良好的材料和制造工艺,正确的使用和维护,才能保证模具的高质量和长寿命,从而保证产品的质量和生产效率。
因此,在实际应用中,需要充分重视压铸模具的技术要求,综合考虑各方面因素,确保模具的高效稳定运行。
模具技术的详细要求
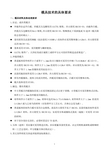
模具技术的具体要求一.模具材料及热处理要求1.拉延、成形类模具●外板件拉延序凸模、凹模及压边圈使用GGG70L铸铁,淬火硬度HRC50-55;内板件凸模、凹摸及压边圈使用MoCr铸铁,淬火硬度HRC50-55。
特殊情况下须渗氮或TD处理(模具图纸会签时确认)。
●变形剧烈及高强度钢板(抗拉强度≥350MPa)的制件应采用整体镶Cr12MoV;淬火硬度要达到HRC58—62。
●基体采用HT300。
采用键槽与螺栓链接。
●GGG70L铸件厂:天津虹岗或长城精工或经甲方认可的同等铸造品质铸造厂。
2.冲裁类模具●普通板料零件料厚小于或等于1.2mm的刃口镶块可采用空冷钢(7CrSiMnMoV 或ICD-5),淬火硬度HRC55-60;料厚大于1.2mm的采用Cr12MoV材料,淬火硬度为HRC58~62。
料厚大于等于1.4mm的镶块采用波浪刃口。
●高强度板的制件采用Cr12MoV材料,淬火硬度为HRC58~62。
●所有凹模镶块、废料刀均采用背托,凹模采用镶块结构,凸模可采用整体结构。
●模具基体采用HT300。
3.翻边、整形类模具●中大型模具凹模镶块原则上应采用侧面固定式以便于调整;小型模具可采用整体式结构,料厚大于1.4mm的凹模采用镶块式。
●零件料厚小于或等于1.2mm,材料可选用MoCr/7CrSiMnMoV;零件料厚大于1.2mm 的采用Cr12MoV或与之相当的材料(应取得甲方工艺认可,具体以会签为准)。
●普通板料的制件凸模可采用合金铸铁,表面淬火硬度不低于HRC50;高强度板的制件采用Cr12MoV材料,淬火硬度为HRC58-62;如采用分体或镶块式基座(底板)可采用HT300的材料。
●对于部分易拉毛部位,必要时需进行TD处理。
4.压料(退料)顶出器可采用铸造结构,但应根据其强度要求,决定用铸铁或球铁或铸钢材料(工艺会签时,甲方根据具体结构决定)。
5.其它部件材质及热处理按国家标准执行。
二.模具结构及技术要求1.模具结构1.1模具结构采用单动式,原则上按甲方认可的乙方提供的结构式样(模具需满足自动化线要求)。
模具设计技术要求
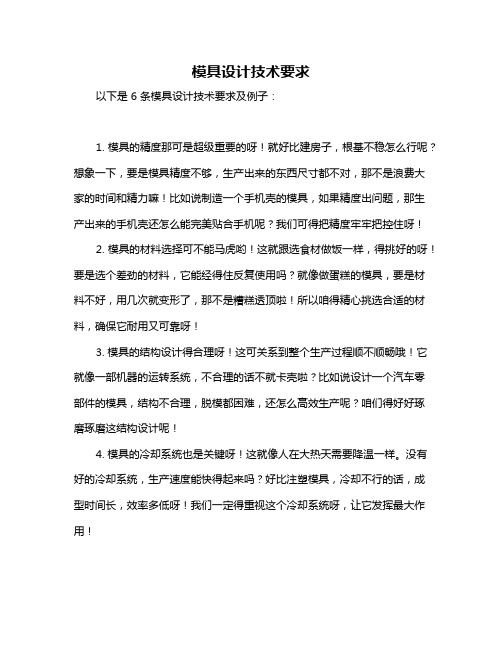
模具设计技术要求
以下是 6 条模具设计技术要求及例子:
1. 模具的精度那可是超级重要的呀!就好比建房子,根基不稳怎么行呢?想象一下,要是模具精度不够,生产出来的东西尺寸都不对,那不是浪费大家的时间和精力嘛!比如说制造一个手机壳的模具,如果精度出问题,那生产出来的手机壳还怎么能完美贴合手机呢?我们可得把精度牢牢把控住呀!
2. 模具的材料选择可不能马虎哟!这就跟选食材做饭一样,得挑好的呀!要是选个差劲的材料,它能经得住反复使用吗?就像做蛋糕的模具,要是材料不好,用几次就变形了,那不是糟糕透顶啦!所以咱得精心挑选合适的材料,确保它耐用又可靠呀!
3. 模具的结构设计得合理呀!这可关系到整个生产过程顺不顺畅哦!它就像一部机器的运转系统,不合理的话不就卡壳啦?比如说设计一个汽车零部件的模具,结构不合理,脱模都困难,还怎么高效生产呢?咱们得好好琢磨琢磨这结构设计呢!
4. 模具的冷却系统也是关键呀!这就像人在大热天需要降温一样。
没有好的冷却系统,生产速度能快得起来吗?好比注塑模具,冷却不行的话,成型时间长,效率多低呀!我们一定得重视这个冷却系统呀,让它发挥最大作用!
5. 模具的维护保养可不能忘啊!这就像爱护自己的宝贝一样。
不保养它,它能一直好用吗?你想啊,一个长期不保养的模具,各种问题都会冒出来,那不是给自己找麻烦嘛!所以呀,要定期给模具做个检查、保养护理啥的,让它一直健健康康的呀!
6. 模具的设计创新多重要呀!这就像给自己的生活加点新花样一样。
一直守着老一套,能有进步吗?看看人家那些厉害的模具设计,多么有创意呀!咱也不能落后呀,要大胆去尝试新的设计思路,说不定就能做出让人惊艳的模具呢!
总之,模具设计技术要求可多了去了,每一条都得认真对待,这样才能做出好的模具,生产出高质量的产品呀!。
模具设计制造及验收技术要求

技术协议附件三模具设计制造及验收技术要求1.大体技术条件1.1.模具设计的大体技术条件1.1.1.工法图设计和模具结构设计必需按用户确认的《钣金件模具设计标准》及提供的《冲压设备技术参数》和冲压生产布线要求。
用户将对冲压工艺方案、冲压设备选用情形、模具结构方案进行认可性会签。
1.1.2.所需卖方开发模具的零件:W=2490车身的驾驶室总成(包括仪表板总成和流水槽)、需要制作弯曲成形类模具的型材和前保险杠总成等与驾驶室同时过油漆线的零件。
1.1.3.按A级标准开发模具的钣金件是:全数外覆盖件(包括:左/右车门外板、前保险杠、顶盖、左/右后侧围外板、左/右前柱外板和后围外板等)、大型或复杂钣金件(包括:后围内板、左/右车门内板、左/右边围内板、地板鼓包等)、t≥的厚板料钣金件(包括:左/右前纵梁、左右后纵梁等);其余钣金件、滚压件和型材按B级标准开发模具。
1.1.4.卖方提供给用户的模具冲出制件的材料利用率必需达到车门为70%,地板为90%,平均为80%以上。
如卖方在冲压工艺要领图设计时,如有发觉材料利用率不能达到要求时,应进行CAE分析,提供出科学准确的材料利用率数据供用户确认。
1.1.5.模具工作部份的材料选用原那么及热处置要求:1.1.6.模具的安装应方便快捷,中大型模具采纳托杆快速定位,应能利用快速安装夹紧装置。
1.1.7.所有模具应考虑得手工操作的平安合理性(如:良好的视野,足够的操作空间和操作区域),便于操作、维修、搬运与寄存,坯件的送进掏出方便,坯件的定位靠得住,废料的排出平安通畅;模具的零部件应考虑防松、防崩、防脱落、防冲击等方法;活动零部件应有平安方法,应有行程限位器、寄存限位器、平安块、防护板、防护罩等。
1.1.8.模具的导柱均安装在下模座上,模具的起重和翻转应在设计时考虑。
1.1.9.模具的气动接头采纳快换接头,接头的安放位置及尺寸规格与压机匹配,并应备有堵塞和换向阀及调压阀;接头插座的顺序排列为定位装置升起、下降、托料装置升起、下降。
冲压模具制作技术要求
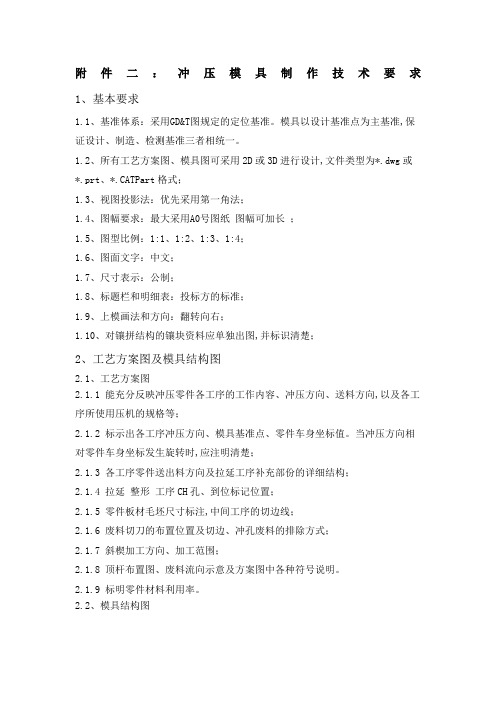
附件二:冲压模具制作技术要求1、基本要求1.1、基准体系:采用GD&T图规定的定位基准。
模具以设计基准点为主基准,保证设计、制造、检测基准三者相统一。
1.2、所有工艺方案图、模具图可采用2D或3D进行设计,文件类型为*.dwg或*.prt、*.CATPart格式;1.3、视图投影法:优先采用第一角法;1.4、图幅要求:最大采用A0号图纸图幅可加长;1.5、图型比例:1:1、1:2、1:3、1:4;1.6、图面文字:中文;1.7、尺寸表示:公制;1.8、标题栏和明细表:投标方的标准;1.9、上模画法和方向:翻转向右;1.10、对镶拼结构的镶块资料应单独出图,并标识清楚;2、工艺方案图及模具结构图2.1、工艺方案图2.1.1 能充分反映冲压零件各工序的工作内容、冲压方向、送料方向,以及各工序所使用压机的规格等;2.1.2 标示出各工序冲压方向、模具基准点、零件车身坐标值。
当冲压方向相对零件车身坐标发生旋转时,应注明清楚;2.1.3 各工序零件送出料方向及拉延工序补充部份的详细结构;2.1.4 拉延整形工序CH孔、到位标记位置;2.1.5 零件板材毛坯尺寸标注,中间工序的切边线;2.1.6 废料切刀的布置位置及切边、冲孔废料的排除方式;2.1.7 斜楔加工方向、加工范围;2.1.8 顶杆布置图、废料流向示意及方案图中各种符号说明。
2.1.9 标明零件材料利用率。
2.2、模具结构图2.2.1 模具图应充分表达模具的工作状态,反映零件的送出料方向、所用的压机型号、顶杆位置与顶杆行程等。
2.2.2 模具图应准确注明模具中心、机床中心。
模具中心应加注车身坐标系坐标值。
2.2.3 每工序模具图应有工序内容简图。
2.2.4 模具结构中含弹簧/氮气缸的应有弹力工作示意图。
2.2.5 模具使用斜楔机构的应做出斜楔行程图及斜楔断面图。
2.2.6 模具如果配备气缸顶出机构,模具图中应附加气路图。
2.2.7 工艺方案图、模具图及数模文件的命名规则如下:×××项目代号 -×××零件代号 -×××零件版本– OPx/y x表示10、20…;y表示总工序数,如共五序则为50 。
模具设计制造技术要求
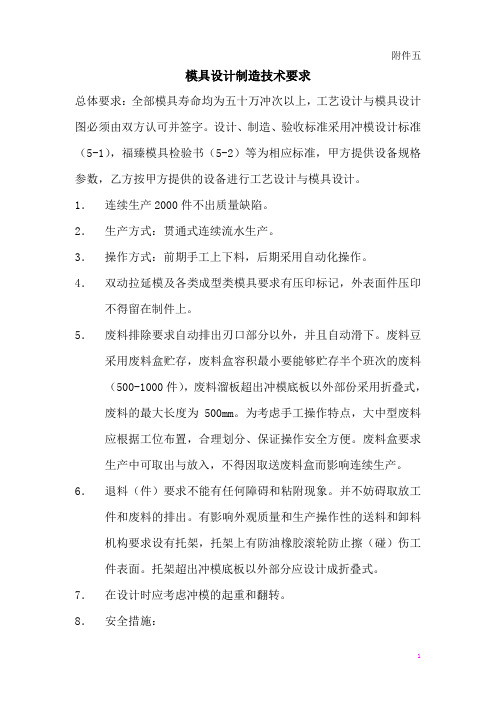
附件五模具设计制造技术要求总体要求:全部模具寿命均为五十万冲次以上,工艺设计与模具设计图必须由双方认可并签字。
设计、制造、验收标准采用冲模设计标准(5-1),福臻模具检验书(5-2)等为相应标准,甲方提供设备规格参数,乙方按甲方提供的设备进行工艺设计与模具设计。
1.连续生产2000件不出质量缺陷。
2.生产方式:贯通式连续流水生产。
3.操作方式:前期手工上下料,后期采用自动化操作。
4.双动拉延模及各类成型类模具要求有压印标记,外表面件压印不得留在制件上。
5.废料排除要求自动排出刃口部分以外,并且自动滑下。
废料豆采用废料盒贮存,废料盒容积最小要能够贮存半个班次的废料(500-1000件),废料溜板超出冲模底板以外部份采用折叠式,废料的最大长度为500mm。
为考虑手工操作特点,大中型废料应根据工位布置,合理划分、保证操作安全方便。
废料盒要求生产中可取出与放入,不得因取送废料盒而影响连续生产。
6.退料(件)要求不能有任何障碍和粘附现象。
并不妨碍取放工件和废料的排出。
有影响外观质量和生产操作性的送料和卸料机构要求设有托架,托架上有防油橡胶滚轮防止擦(碰)伤工件表面。
托架超出冲模底板以外部分应设计成折叠式。
7.在设计时应考虑冲模的起重和翻转。
8.安全措施:8.1冲模上的活动部件应有安全措施,并设置安全区。
8.2应有限位器、安全块、防护板、防护罩等。
8.3冲模零部件应考虑防松、防崩、防脱落、防反、防冲击等措施。
8.4冲模的布置应考虑到安全、合理,便于操作及压床的安装。
8.5 部分梁类、柱类及中小型件的模具要求设计时装模高度一致可以进行采用联合安装。
8.6冲模的设计应考虑手工操作的安全,如:良好的视野,足够的操作空间和操作区域。
9、冲模安装采用螺钉安装,模板定位方式采用定位销定位。
10、中大型模具上模采用侧销及安全侧销(二段式)。
11、工法图必须经会签后方可投入设计制造。
12、调试中不得使用拉延油,调试用料甲方提供100辆份,复杂件提供150辆份,超过部份由乙方自己解决;在甲方工厂最终验收用料由甲方提供。
冲压模具制作技术要求

冲压模具制作技术要求冲压模具是冲压工艺中使用的重要工具,其质量直接影响到冲压件的精度和质量。
因此,冲压模具制作技术要求较高,主要包括以下几个方面:一、模具设计要求:1.合理性原则:模具设计应考虑到冲压件的材料性质、形状、尺寸等因素,使模具结构合理、工作稳定。
2.精度要求:模具设计应考虑到冲压件的精度要求,合理设置定位、导向装置,并确保模具的定位精度以及冲压件的位置和尺寸精度。
3.可靠性要求:模具设计应考虑到使用寿命、可靠性等要求,并采用高强度、高耐磨材料制作。
4.便于加工和调试:模具设计应考虑到加工工艺、制造难度,以及调试和维修的便捷性。
二、模具制造要求:1.材料选用:模具材料应具有好的热处理性能、硬度、耐磨性和韧性,常用的材料有工具钢、合金钢等。
2.加工工艺:模具制造过程中应采用先进的加工工艺,包括车、铣、磨、电火花等工艺。
尤其是模具的加工精度和表面粗糙度要求较高。
3.系统模具加工:对于大型、复杂的模具,应采用CNC加工、数控加工等系统模具加工工艺,提高加工精度和效率。
4.热处理工艺:模具经过车削、铣削等加工后应进行热处理,以获得所需的硬度和韧性。
热处理过程要控制温度、时间等参数,并进行合理的淬火和回火处理。
5.表面处理:模具表面应进行合适的处理,以提高其耐磨性和抗腐蚀性。
常用的表面处理方法包括氮化、镀铬等。
三、模具调试和测试要求:1.模具调试:模具制造完成后,需要进行调试工作,包括模具的总装和零件的调试,以确保模具的正常使用和冲压件的质量。
2.测试和检验:模具制作完成后,需进行各项性能测试和质量检验,包括模具的尺寸测量、冲压件的检验等,以确保模具的性能和质量达到设计要求。
四、模具维护和保养要求:1.定期保养:模具在使用中需要定期进行维护和保养,包括润滑、清洁等,以延长模具使用寿命。
2.磨损修复:模具在使用中可能出现磨损和损坏,需要进行修复工作,包括砂轮修复、电火花修复等,保证模具的尺寸精度和使用寿命。
注塑模具技术要求
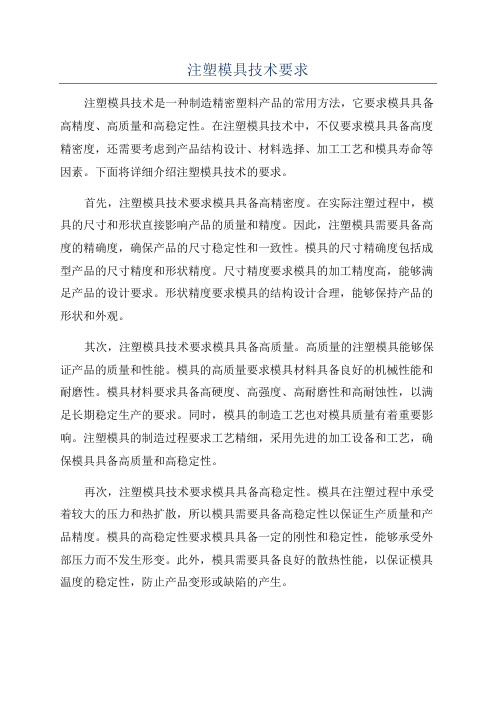
注塑模具技术要求注塑模具技术是一种制造精密塑料产品的常用方法,它要求模具具备高精度、高质量和高稳定性。
在注塑模具技术中,不仅要求模具具备高度精密度,还需要考虑到产品结构设计、材料选择、加工工艺和模具寿命等因素。
下面将详细介绍注塑模具技术的要求。
首先,注塑模具技术要求模具具备高精密度。
在实际注塑过程中,模具的尺寸和形状直接影响产品的质量和精度。
因此,注塑模具需要具备高度的精确度,确保产品的尺寸稳定性和一致性。
模具的尺寸精确度包括成型产品的尺寸精度和形状精度。
尺寸精度要求模具的加工精度高,能够满足产品的设计要求。
形状精度要求模具的结构设计合理,能够保持产品的形状和外观。
其次,注塑模具技术要求模具具备高质量。
高质量的注塑模具能够保证产品的质量和性能。
模具的高质量要求模具材料具备良好的机械性能和耐磨性。
模具材料要求具备高硬度、高强度、高耐磨性和高耐蚀性,以满足长期稳定生产的要求。
同时,模具的制造工艺也对模具质量有着重要影响。
注塑模具的制造过程要求工艺精细,采用先进的加工设备和工艺,确保模具具备高质量和高稳定性。
再次,注塑模具技术要求模具具备高稳定性。
模具在注塑过程中承受着较大的压力和热扩散,所以模具需要具备高稳定性以保证生产质量和产品精度。
模具的高稳定性要求模具具备一定的刚性和稳定性,能够承受外部压力而不发生形变。
此外,模具需要具备良好的散热性能,以保证模具温度的稳定性,防止产品变形或缺陷的产生。
最后,注塑模具技术要求模具具备较长的使用寿命。
模具作为生产工具,一般需要经历较多的注塑周期才能收回成本。
因此,模具需要具备较长的使用寿命以减少更换频率和生产成本。
模具的使用寿命受到多种因素的影响,包括模具材料、模具设计、模具加工工艺和使用条件等。
因此,注塑模具的制造要求模具具备高硬度、高耐磨性和高抗腐蚀性,同时要注意模具的设计合理性和使用条件的控制,以延长模具的使用寿命。
总之,注塑模具技术在市场中非常重要,对产品质量和生产效率有着直接的影响。
冲压模具设计技术要求
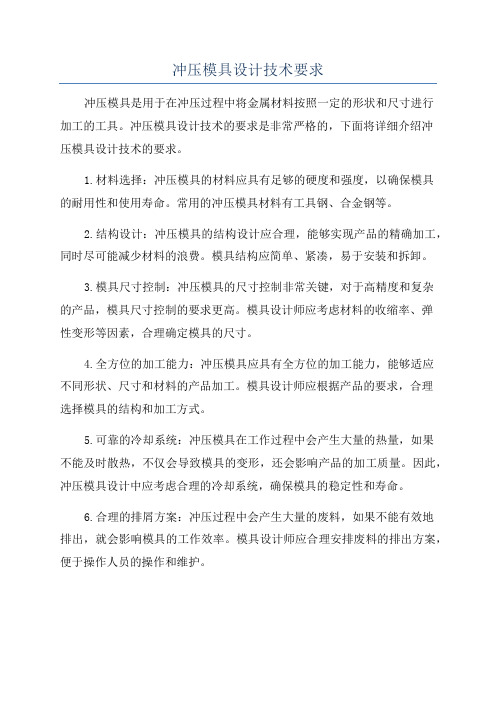
冲压模具设计技术要求冲压模具是用于在冲压过程中将金属材料按照一定的形状和尺寸进行加工的工具。
冲压模具设计技术的要求是非常严格的,下面将详细介绍冲压模具设计技术的要求。
1.材料选择:冲压模具的材料应具有足够的硬度和强度,以确保模具的耐用性和使用寿命。
常用的冲压模具材料有工具钢、合金钢等。
2.结构设计:冲压模具的结构设计应合理,能够实现产品的精确加工,同时尽可能减少材料的浪费。
模具结构应简单、紧凑,易于安装和拆卸。
3.模具尺寸控制:冲压模具的尺寸控制非常关键,对于高精度和复杂的产品,模具尺寸控制的要求更高。
模具设计师应考虑材料的收缩率、弹性变形等因素,合理确定模具的尺寸。
4.全方位的加工能力:冲压模具应具有全方位的加工能力,能够适应不同形状、尺寸和材料的产品加工。
模具设计师应根据产品的要求,合理选择模具的结构和加工方式。
5.可靠的冷却系统:冲压模具在工作过程中会产生大量的热量,如果不能及时散热,不仅会导致模具的变形,还会影响产品的加工质量。
因此,冲压模具设计中应考虑合理的冷却系统,确保模具的稳定性和寿命。
6.合理的排屑方案:冲压过程中会产生大量的废料,如果不能有效地排出,就会影响模具的工作效率。
模具设计师应合理安排废料的排出方案,便于操作人员的操作和维护。
7.安全性和可维护性:冲压模具设计应考虑到操作人员的安全,避免因操作不当导致事故发生。
同时,冲压模具应具备可维护性,便于检修和更换损坏的部件。
8.尽量减少模具的使用成本:在冲压模具设计中,应尽量减少模具的使用成本,包括原材料成本、制造成本和维护成本等。
通过合理的结构设计和材料选择,可以有效降低模具的使用成本。
总之,冲压模具设计技术要求严格,设计师需要综合考虑材料、结构、尺寸控制、加工能力、冷却系统、废料排出、安全性和可维护性等多个因素,以确保模具的质量和使用寿命。
只有具备专业的技术知识和丰富的实践经验,才能设计出高质量、高效率的冲压模具。
关于压铸模具设计制作技术标准要求

关于压铸模具设计制作技术标准要求ADC-03-版本A0 实施日期2020-1-1编制人更改记录标记处数更改依据更改人更改日期审核人批准人1、目的标准化压铸模具,达到提高模具寿命,减少装拆模浪费,提高产品质量,降低产品制造成本。
2、适用范围公司所用压铸模具。
3、内容3.1 产品孔由压铸模具保证,切边冲孔后无后处理工序的要求:对不需要后续加工直接压铸成型,经过切边冲孔就直接交货的产品,压铸模具设计时,孔内销子孔分型面尽量选择在孔的中间段,两边销子在分型面留隔皮间隙0.1-0.2mm。
目的是防止单边销子,隔皮在孔口,切边毛刺不净或蹦口,需要后续补充加工来保证,增加了制造成本。
如下图示例。
3.2 模芯材料:模芯材料用国际知名品牌材料的优质模具钢,保证量产过程中模具质量稳定,减少反复修模造成浪费。
3.3模具浇注系统设计:合适的浇注口大小影响模具型腔注满的时间和压射力大小、速度高低、填充时间。
A、流道设计应符合流体力学原理,尽量各分流道做到铝液能同时到达各内浇口。
B、流道截面积从料柄分出到内浇口应逐步收紧变小,不可突然变大,造成喷射卷气。
C、流道不能小90°突然转急弯。
如因条件限制必须急弯,应采用大圆弧过渡,以减低压铸铸造压力和速度,避免压力速度过大产生飞边、涨模。
D、料筒选择:填充率30-50%.3.4 模具冷却系统:A、模具冷却主要是控制模具温度高低,同时使模具温度均匀,不均匀的模具温度将影响:产品有严重的缺陷,如开裂、冷隔、变形、压铸气孔、缩孔等。
温度过低,铸件冷隔,温度过高,铸件缩孔。
B、模具冷却水管要做成拔插式快换接头。
C、模具冷却水管理进水、出水管要有颜色区分,进水管蓝色,出水管红色。
D、模具定模侧上方集水器高度必须小于250mm,以避免与喷雾机干涉。
E、从模具内部接出来的水管要与图纸一致的编号标识,以利于根据模具温度要求调整冷却水的流量大小(开关开度)。
3.5 模具顶出系统:A、顶杆位置布置应使顶出力量均匀、平衡,防止因顶出力量不平衡,造成顶出变形。
- 1、下载文档前请自行甄别文档内容的完整性,平台不提供额外的编辑、内容补充、找答案等附加服务。
- 2、"仅部分预览"的文档,不可在线预览部分如存在完整性等问题,可反馈申请退款(可完整预览的文档不适用该条件!)。
- 3、如文档侵犯您的权益,请联系客服反馈,我们会尽快为您处理(人工客服工作时间:9:00-18:30)。
级进模设计要求
1、用该模具所冲出的零件应该满足产品质量要求;
2、优化排样设计,使材料材料的利用率尽可能高;
3、强度和刚性较差的小冲裁凸模必须有护套加导向;
4、镶块、凸模安装方便,正确可靠,冲裁凸模修模后,高度调节要方便;
5、单边冲裁凸模,尽可能加导向部分;单侧弯曲时,模具上要有防止材料流动的对策;
6、间隙的均匀程度要到达70%以上;
7、模具安装平稳性好,调整方便,工作安全;模具结构应便于制造与维修;
8、压力中心偏移量不能超过凹模1/6;
9、各工作系统坚固可靠,活动部分灵活平稳,动作互相协调。
定位起止正确,卸料板、顶块不倾斜,有足够的卸料、顶出件力,卸料安全可靠。
进料、定料、出件、清理废料畅通、方便,没有废料上浮、漏料孔堵塞、叠件现象。
保证稳定正常工作;
10、上模座沿导柱上、下移动平稳、无滞住现象。
11、级进模用四角滚珠导柱导套钢模,弹性卸料,小凸模用护套,卸料板用小导柱导套导向,凹模做成分段拼合或组合式,冲裁凸模修模后,高度要能调节,前后工位排废料、出工件方案合理,毛坯定位准确可靠,送料方便无阻碍,废料切断后回收。
工作量:图纸(1:1),装配图1张0号图纸;零件图,凸模、凹模、护套,其他工作零件必须画,其次按卸料板、凸模固定板、凹模固定板等顺序,画够2张以上0号图纸。
说明书:要求30页以上。
图纸和说明书质量按学校要求做。
冲压件要求(大批量生产)
一、零件附加说明
零件的形状和要求见附图,尺寸从图纸上量取
二、合格的制件应满足的要求
1.尺寸、形状符合图纸要求;
2.冲裁断面不允许有夹层,毛刺最好在一面、毛刺高度小于10%t;
3. 冲压件平整、形状无明显翘曲、畸形、扭曲、歪斜等形状缺陷;
4. 光面的均匀程度要求大于70%;
5. 搭接口不能出现错位、不平直、毛刺现象;
6. 成形部分平整、光滑,无起皱、裂纹、显著变薄、明显的刮痕现象;
7. 制件必须不能被模具的伤痕、划痕、表面块陷所影响;
8.保证制件质量稳定。
冲压模具设计要求
1、用该模具所冲出的零件应该满足产品质量要求;
2、优化排样设计,使材料材料的利用率尽可能高;
3、强度和刚性较差的小冲裁凸模必须有护套加导向;
4、镶块、凸模安装方便,正确可靠;
5、单边冲裁凸模,尽可能加导向部分;单侧弯曲时,模具上要有防止材料流动的对策;
6、间隙的均匀程度要到达70%以上;
7、模具安装平稳性好,调整方便,工作安全;模具结构应便于制造与维修;
8、压力中心偏移量不能超过凹模1/10;
9、各工作系统坚固可靠,活动部分灵活平稳,动作互相协调。
定位起止正确,卸料板、顶块不倾斜,有足够的卸料、顶出件力,卸料安全可靠。
进料、定料、出件、清理废料畅通、方便,没有废料上浮、漏料孔堵塞、叠件现象。
保证稳定正常工作;
10、上模座沿导柱上、下移动平稳、无滞住现象。
11、最好用软件预测成形过程中可能会产生的质量问题,并提出解决质量问题的可行性方案;要求设计成形工序的成形模具。
工作量:图纸(最好1:1),装配图;所有非标准零件图零件图全画。
说明书:在说明书中必须包含冲压工艺过程卡,预测成形过程中可能会产生的质量问题,并提出解决质量问题的可行性方案,其他按要求做。
要求30页以上。
图纸和说明书质量按学校要求做。