冲压模具组立测量记录表
冲压模具制造检查表

Construction Co. Rep
零件制造方代表:
Production Plant Rep.
冲压模具制造审核表(B)
DIE CONSTRUCTION REVIEW( B )
零件号:
Part Number
总成号:
Assembly Part#
工程更改号:
EWO#
零件名称:
Part Name
零件图纸号:
G D & T DWG #
零件图纸更改级别:
Part DWG E/C Level
年型/车型:
Year & Style
零件数模版本号:
Math Data Release #
模具编号:
Die Code
零件供应商:
Part Supplier
SQE ( SGM )
SQE ( SGM ):
电话:
Phone#
DUNS / Z编号:
DUNS / Z Code
模具工程师(供应商pplier)
电话:
D.冲孔头及引孔符合标准
Were the Pierce punch & punch entry as std.
E.斜锲操作平稳,回程装置安装正确
Camoperation is smooth, positive returns are fitted
14.模具的操作安全性
Is the safety cover installed properly
15.所有模具号标牌均正确固定,并按标准上漆
All die ID tags are fitted and painted as std.
注释:
Comments
冲压首末件检验记录表
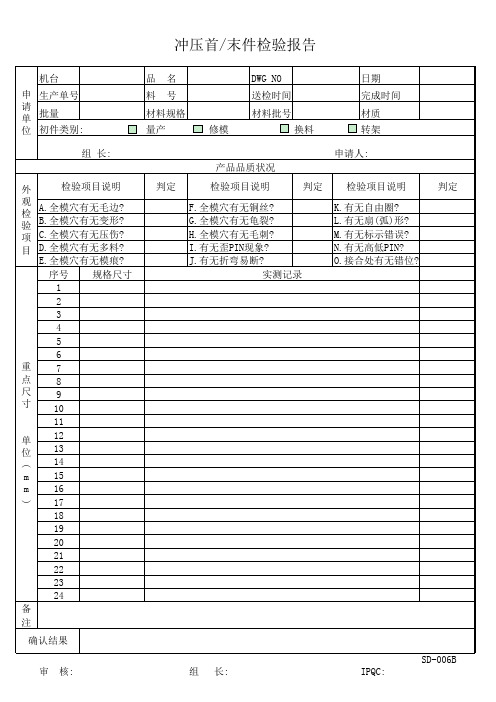
判定
组 长:
IPQC:
SD-006B
(
)
冲压首/末件检验报告
机台
申 生产单号 请 单 批量 位 初件类别:
品名 料号 材料规格 量产
修模
DWG NO 送检时间 材料批号
换料
日期 完成时间 材质 转架
组 长:
外
检验项目说明
观 检
A.全模穴有无毛边?
验 B.全模穴有无变形?
项 C.全模穴有无压伤?
目 D.全模穴有无多料?
E.全模穴有无模痕?
序号 规格尺寸
1
2
3
4
5
6
重
7
点
8
尺
9
寸 10
11
单 12 位 13
14
m
15
m 16
17
18
192021源自222324
备
注
确认结果
审 核:
产品品质状况
申请人:
判定
检验项目说明
判定 检验项目说明
F.全模穴有无铜丝? G.全模穴有无龟裂? H.全模穴有无毛刺? I.有无歪PIN现象? J.有无折弯易断?
实测记录
K.有无自由圈? L.有无扇(弧)形? M.有无标示错误? N.有无高低PIN? O.接合处有无错位?
冲压件首件检验记录(表格模板、格式)
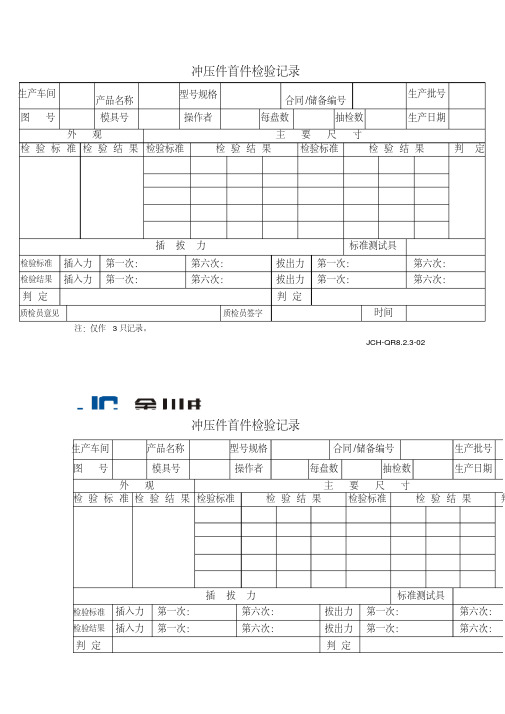
冲压件首件检验记录
生产车间
产品名称型号规格
合同/储备编号
生产批号
图号模具号操作者每盘数抽检数生产日期
外观主要尺寸
检验标准检验结果检验标准检验结果检验标准检验结果判定
插拔力标准测试具
检验标准插入力第一次:第六次:拔出力第一次:第六次:
检验结果插入力第一次:第六次:拔出力第一次:第六次:
判定判定
质检员意见质检员签字时间
注:仅作3只记录。
JCH-QR8.2.3-02
冲压件首件检验记录
生产车间产品名称型号规格合同/储备编号生产批号
图号模具号操作者每盘数抽检数生产日期
外观主要尺寸
检验标准检验结果检验标准检验结果检验标准检验结果判
插拔力标准测试具检验标准插入力第一次:第六次:拔出力第一次:第六次:
检验结果插入力第一次:第六次:拔出力第一次:第六次:
判定判定
质检员意见质检员签字时间注:仅作3只记录。
冲压模具检查记录表范例
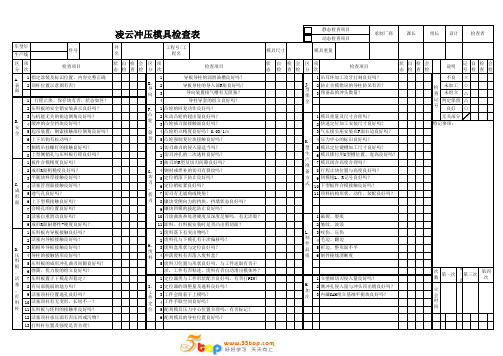
3 预备品的冲头数量?
全
1 模具重量及尺寸合理吗?
2 快速定位加工安装尺寸良好吗?
3 气压接头座安装在F面右边良好吗?
K. 4 压力中心的标识良好吗? 型 5 模具定位键槽加工尺寸良好吗?
生 6 模具锁付用U型槽位置、宽高良好吗?
产 准
7 模具闭合高度合理吗?
备 8 行程止块位置与高度良好吗?
方 9 闭模钮L、R记号良好吗? 式 10 下型板件合模接触良好吗?
12 活塞顶杆承压面有否压凹或污物?
13 打料杆位置及强度是否合理?
1 E. 2 导 向3
4
导板导柱的润滑油槽良好吗? 导板导柱的导入部R角良好吗?
导向装置排气槽有无阻塞? 导柱导套的组立良好吗?
F. 1 凸轮的回复动作良好吗?
凸 2 从动凸轮的超出量良好吗?
轮 、
3 凸轮插刀面接触面良好吗?
斜 4 凸轮组立精度良好吗?0.03/1m
凌云冲压模具检查表
静态检查项目 动态检查项目
承制厂商
课长
组长 设计
检查者
车型年 生产线
件号
件 名
工程号/工 程名
模具尺寸
模具重量
区项 分次
检查项目
状自检会 区项 态检查检 分次
检查项目
状 自 检会 区项 态 检 查检 分次
检查项目
状自检会 态检查检
说明
记自检会 号检查检
A. 1 指定涂装及标识位置、内容完整正确 表 2 顶杆位置示意图有否? 面
11 顶料机构形状、动作、装配良好吗?
1 破裂、裂痕
2 皱纹、波浪
L. 3 咬伤、压伤 制 4 毛边、翻边 件 品 5 折边、整形面不平 质 6 制件棱线清晰度
冲压点检记录
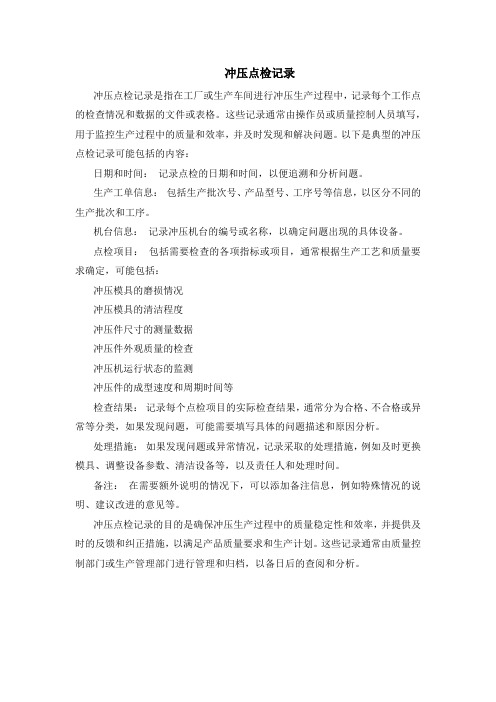
冲压点检记录
冲压点检记录是指在工厂或生产车间进行冲压生产过程中,记录每个工作点的检查情况和数据的文件或表格。
这些记录通常由操作员或质量控制人员填写,用于监控生产过程中的质量和效率,并及时发现和解决问题。
以下是典型的冲压点检记录可能包括的内容:
日期和时间:记录点检的日期和时间,以便追溯和分析问题。
生产工单信息:包括生产批次号、产品型号、工序号等信息,以区分不同的生产批次和工序。
机台信息:记录冲压机台的编号或名称,以确定问题出现的具体设备。
点检项目:包括需要检查的各项指标或项目,通常根据生产工艺和质量要求确定,可能包括:
冲压模具的磨损情况
冲压模具的清洁程度
冲压件尺寸的测量数据
冲压件外观质量的检查
冲压机运行状态的监测
冲压件的成型速度和周期时间等
检查结果:记录每个点检项目的实际检查结果,通常分为合格、不合格或异常等分类,如果发现问题,可能需要填写具体的问题描述和原因分析。
处理措施:如果发现问题或异常情况,记录采取的处理措施,例如及时更换模具、调整设备参数、清洁设备等,以及责任人和处理时间。
备注:在需要额外说明的情况下,可以添加备注信息,例如特殊情况的说明、建议改进的意见等。
冲压点检记录的目的是确保冲压生产过程中的质量稳定性和效率,并提供及时的反馈和纠正措施,以满足产品质量要求和生产计划。
这些记录通常由质量控制部门或生产管理部门进行管理和归档,以备日后的查阅和分析。
冲压模具检查表

10 凹模镶块及废料刀的空刀部分与铸件安装面平齐 11 保证刃口的切入量(有效刃口高度≥8mm)空刀1-2mm 12 压料板、顶出器与凹模镶块间隙<0.5mm,没有油污和刮痕 淬火后模具刃口部位硬度符合图纸要求,不允许有软点、烧伤及 13 裂纹 14 异形凹模及带形状处凹模应有防转装置,并符合图纸要求 15 镶块与窝座、止退键之间不能有间隙 16 凸模的废料刀刃口高度应低于凸模刃口的高度≥4mm 17 凸模废料刀的宽度应符合图纸(冲压件宽+10mm) 18 相邻处的凹模刃口与废料刀刃口相接触的高度应低于t+4mm 19 反侧类模具,接触面深确保进入20mm后工作,接触面无间隙 1 2 3 斜锲的固定应符合图纸,检查定位销松紧及挡块的贴合情况 回程键和回程钩起始部位的圆角及安装应符合图纸 斜锲滑动面的间隙<0.03mm 斜锲弹簧应有预压缩,复位良好 滑动压板的间隙<0.03mm以下无摆动 暴露的斜锲弹簧或其它弹顶器,均应有安全护板 安 装 部 分
斜 锲
其 它
4 5 6
顶出器及活动部位须加装防护板 模块重量超过15公斤时应设起重孔,孔位确保起吊时模 3 块保持平衡 气缸与托料杆之间的连接部分要安全、牢固,运动时平 4 稳 5 平衡块安装面应设有加强筋 U形槽的厚度、宽度、个数、位置及托杆孔位置误差≤ 6 ±0.5mm 7 螺纹深度,应符合图纸和国标要求,同时满足强度要求 翻转孔、起重孔,孔径、孔距应符合图纸(应能满足强 8 度要求) 侧销应保证在3根以上,并应使限位板开口向下,锁板 9 厚度5.0mm,要求用2-M10螺钉紧固 10 在存放状态时,应确保导柱或导板的配合量≥40mm 1 气源固定装置及管接规格是否符合图纸 进气、出气管接头应用颜色来区分,进气红色,出气兰 色,软管应夹头固定不能悬空、缠绕及破裂 2 所有调整垫片的大小应合适,并固定在底板上 3 模具应清洗(模具无切屑、废料、油污、红丹粉等) 4 模具加工基准必须保留,并在底板上刻印出坐标值 铭牌的安装、底板铸字区标识(F标识、送料方向箭头 5 、图号、材料)及镶块的图号、材料与底板安装座对应 的件号 6 模具非工作部位倒角2X45° 模具所有部位须按规定色、涂色,涂色要求参照技术 7 协议
中日文冲压模具检查表
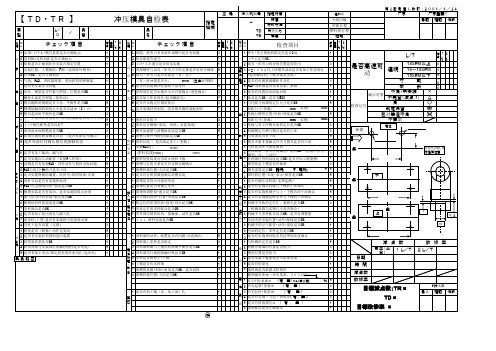
5 mm
3
4 机械侧定位销与模具是否有干涉
3
取 5 与设备是否有干涉
5
L/T
是否高速可 动
連続
18SPM以上 16~18SPM 15SPM以下
寸 動
中 断
减点对象
不良・未安装 不完全(減点 1)
× △
检查记号
良 判定保留
○
○保
已对策但不良
○
不要紧
定位
换模
減1 2 点 L/ L/
TT
0
-
TD
板厚 材料寸法 气垫压力
夹紧内幅 夹紧行程 弹料块行程
承認 確認 作成
TR 模高
送距
分N 类o
检查项目
1 冲头・导正销座的销定位是否2处
減自 1 2 点 主 L/ L/
TT
1
(中心定位NG)
2 切刃・折弯刀的分割位置是否恰当
3
模 具
3
w=10kg以上的模具部品是否有加工作业用孔
1
保 (起吊螺纹孔)(嵌合部品全部)
1 间隙、折弯刀R形状在试模中是否有问题
2 咬合量是否适当
3 2次・3次避让是否切实实施
切
4
背撑钢性与切刃・折弯刀下的支撑是否有充分确保
刃 5 切刃・折弯刀是否有悬挂(有,无)
(有)时⇒量是多少: ・
mm (立会时判断)
6 是否有安装侧冲孔强制下落零件
曲 7 补焊部位是否实施淬火后开裂确认(着色确认)
确 7 防误夹的安装位置・动作・配线是否OK 认 8 机械手的空气配管・动作・强度是否OK
9 空站的定位、零件定位是否OK
1 0
是否有实施相对取出传送带的高度确认
冲压模具验收记录(多工位版)
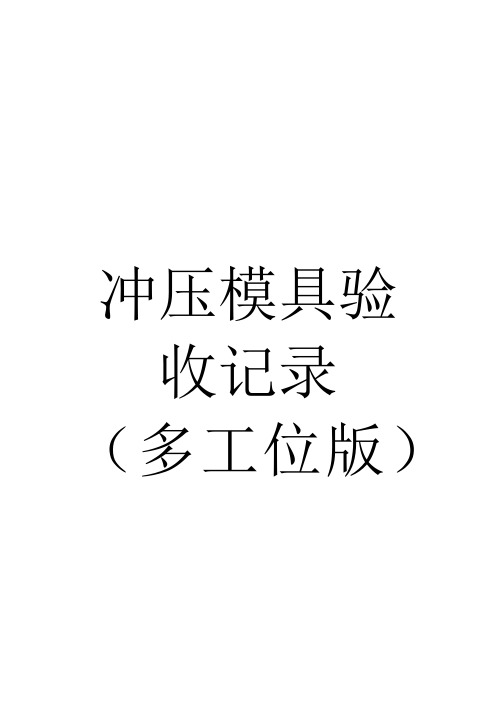
冲压模具验
收记录(多工位版)
➢静态验收检查项-后工序(拉延)
备注:
①模具上用来调整的(钢)垫片(除平衡块)只能为1片。
②模具零件的连接、固定要使用内六角螺钉。
③定位块、气缸要有定位柱销来确定位置。
④对照图纸确认侧销支承座强度,止动板过孔直径。
⑤所有图纸指示的螺钉、定位柱销要装配齐全。
⑥模具使用内六角螺钉拧入深度:铸件要达到螺钉直径1.5倍;钢件要达到螺钉直径1倍。
⑦定位块要有调整余量,如果会引起强度、成形方面的问题则不受此范围限制
⑧模具主要零件要有加工基准并刻印坐标。
⑨按图纸确认压板槽,快速定位,定位键槽,上
模定位孔的技术指标(数量、厚度、位置、形状等)。
➢静态验收检查项-后工序(切边冲孔、整形)
备注:
①模具上用来调整的(钢)垫片(除平衡块)只能为1片。
②模具零件的连接、固定要使用内六角螺钉。
③定位块、气缸要有定位柱销来确定位置。
④对照图纸确认侧销支承座强度,止动板过孔直径。
⑤所有图纸指示的螺钉、定位柱销要装配齐全。
⑥模具使用内六角螺钉拧入深度:铸件要达到螺钉直径1.5倍;钢件要达到螺钉直径1倍。
⑦定位块要有调整余量,如果会引起强度、成形方面的问题则不受此范围限制
⑧模具主要零件要有加工基准并刻印坐标。
⑨按图纸确认压板槽,快速定位,定位键槽,上
模定位孔的技术指标(数量、厚度、位置、形状等)。
➢动态验收检查项-(拉延)
➢动态验收检查项-后工序(切边、整形)
参数记录表:。
冲压日常点检表

1
操作盘和各灯点状态确认
日 良好/不良
/
/
/
/
/
/
/
/
/
/
/
/
/
/
/
/
2
超负荷压力表确认
日
/
/
/
/
/
/
/
/
/
/
/
/
/
/
/
/
3
平衡缸气压表确认
日 4.0~6.0
/
/
/
/
/
/
/
/
/
/
/
/
/
/
/
/
4
离合器气压表确认
日
kg/㎠
/
/
/
/
/
/
/
/
/
/
/
/
/
/
/
/
5
模垫压力表确认
日
/
/
/
/
/
/
/
/
/
/
/
/
/
/
/
/
/
/
/
/
/
/
/
/
/
/
/
/
/
/
/
/
11
送料机 正常作动 确认
日 良好/不良
/
/
/
/
/
/
/
/
/
/
/
/
/
/
/
/
12
模高数显器状态确认
日 良好/不良
/
/
/
/
/
冲压件首件检验记录表格模板、doc格式)
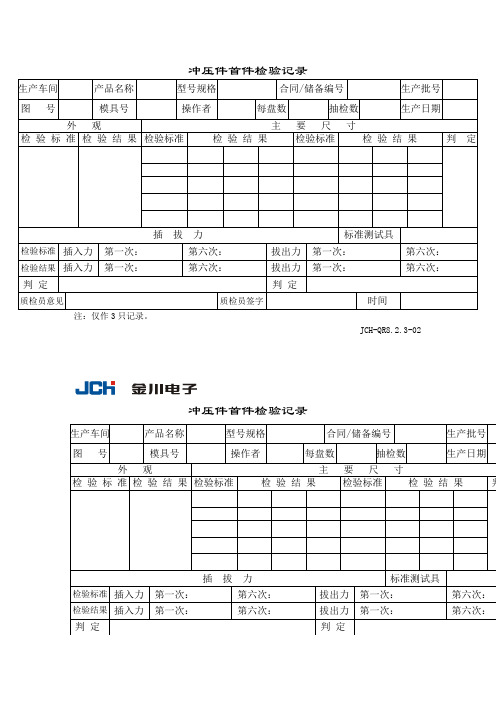
时间
注:仅作3只记录。
JCH-QR8.2.3-02
冲压件首件检验记录
生产车间
产品名称
型号规格
合同/储备编号
生产批号
图号
模具号
操作者
每盘数
抽检数
生产日期
外观
主要尺寸
检验标准
检验结果
检验标准
检验结果
检验标准
检验结果
判定
插 拔 力
标准测试具
检验标准
插入力
第一次:第六次:拔出力来自第一次:第六次:
检验结果
冲压件首件检验记录
生产车间
产品名称
型号规格
合同/储备编号
生产批号
图号
模具号
操作者
每盘数
抽检数
生产日期
外观
主要尺寸
检验标准
检验结果
检验标准
检验结果
检验标准
检验结果
判定
插 拔 力
标准测试具
检验标准
插入力
第一次:
第六次:
拔出力
第一次:
第六次:
检验结果
插入力
第一次:
第六次:
拔出力
第一次:
第六次:
判定
判定
质检员意见
插入力
第一次:
第六次:
拔出力
第一次:
第六次:
判定
判定
质检员意见
质检员签字
时间
注:仅作3只记录。
模具点检表

生产班组:
时段 点检项目 1、检查模具的产品号及工序号与生产计划是 否相符 点检方法 目视 测量/目视 目视 目视/手感 目视 目视 目视 目视 目视/手感 目视 操作/目视 判断标准 计划与模具实物相符,符合 生产计划 能正常安装,符合《冲压作 业指导书》 无杂质、无异物、无突起 安全销无晃动、丢失 无损坏、断裂 无杂质、无异物、无突起 送料取件正常/与工作台中心 线重合 存放垫平稳支撑模具 安装支点稳定,无晃动 模具外观完好、导向部位清 洁并加注润滑油 安全墩、模具存放块已取 下,无缺失 模具型腔内、上下表面无异 物 无脱落、松动 光滑,清洁/上下行程到位, 无异常 完好 废料滑落顺畅 无异常 6S标准 无异常,无缺损,无晃动 存放垫平稳支撑模具 1 2 3 4 5 6
生 3、检查模具型腔内、上下表面是否清洁,螺栓 产 目视/手感 是否松动、缺失 前 4、检查模具紧固装置状况(如螺栓)导向装 目视/手感 置状况(如导板) 定位装置状况(如定位 块) 5、棉布清理模具型面,涂润滑油,开动寸动 目视/手感 行程空车运行三次 1、检查模具五大装置(工作、紧固、导向、 定位、顶出装置)是否正常 目视 目视 目视/听觉 目视 目视/手感 目视
填写顺序
1
3
2
年 月
12 13 14 157891011
安 2、检查压力机的滑块高度或最大行程是否适 装 合模具的封闭高度及加工行程 前 3、清理压力机的工作台及滑块表面 4、检查模具安全销又没有松动,缺失 5.检查吊装棒及防脱链是否损坏、断裂 1、检查模具上下表面有没有废屑或杂质 2、检查模具安装方向是否正确,安装位置是 安 否对中 装 时 3、检查模具存放垫是否齐备 4、检查模具装模压板或螺钉有没有缺陷,检 查模具是否锁紧 1、检查模具外观与导向部位 2、检查安全墩及模具存放块
冲压各项表单填写

_
磷青铜Βιβλιοθήκη C5210__
120-150 100-160 150-170 140-205 170-190 _ 190-210 185-235 210-230 210-260 _
_
黃銅
C2680 R
_
_
_
75-125
_
85-145
_
95-165
_
105-175
_ 145-UP _
_
铍铜
C17200
_
90-160
_
_
_
洋白铜
C7521
_
70-UP
_
80-120
_
120-180
_
_
_
160-UP
_
_
_
_
SECC
_ 95-130(8D) _ 115-150(4D) _ 135-185(2D) _ 170(1D) _
_
_
_
_
_
SPCC-SD
_ 95-130(1/8H) _
115-150
_
135-185
_
_
_ 170-235 _
20
材料图片
21
22
16
533WD
17
科莱蒙特重负荷冲压油(S-805)
18
冲压切屑油(S-800)
19
常用金属与非金属材质表
金属材质硬度对照表-HV
质别/参照标准
O
1/4H
1/2H
3/4H
H
EH
FH
JIS材质/牌号
GB
JIS
GB
JIS
GB
JIS
冲压模具点检表

凸凹模表 面无裂纹 、无杂物
漏料部位 清洁无积
料
导柱顶部 、导套内 部、导板 表面干净
无异物
气动装置无 限位及支
感应器装 漏气、无明 撑套(支
置可靠、 显变形,橡 撑块)无
无松动 胶部位无严 变形、缺
重磨损
损、
废料滑料 板无变形
安全侧销 、安全螺
钉无松 动; 冲孔废料 道无卡滞
班长确认
压前 压后 压前 压后 压前 压后 压前 压后 压前 压后 压前 压后 压前 压后 压前 压后 压前 压后 压前 压后 状态 状态 状态 状态 状态 状态 状态 状态 状态 状态 状态 状态 状态 状态 状态 状态 状态 状态 状态 状态
压前
压后
发生时间
确认人
异常描述
发生时间
异常处置
确认人
1、模具名称及编号栏填写如:“前车门外板”、“K1-8402111-1/5”。 2、检查内容填写时,完好请打“○”;发现异常请打“×”;处理完“×”, 然后在异常记录栏填写,并由班长确认。 3、此表保存期限为1年。
冲压模具点检表生产线体使用设备点检项目模具主体合模标记工作型面辅助装置班长确认点检方法目视目视目视擦拭目视手感目测目测目测目测目测点检基准序号模具编号模具名称点检人日期101112异常描述发生时间确认人异常描述发生时间异常处置确认人模具上下安装面无裂纹料豆等异上下模f标或侧面标指向同向凸凹模表面无裂纹无杂物漏料部位清导柱顶部导套内部导板表面干净无异物感应器装置可靠无松气动装置无漏气无明显变形橡胶部位无严重磨损限位及支撑套支撑块无变形缺损废料滑料板无变形安全侧销安全螺钉无松动
生产线体
使用设备
序 号
模具编号
1
模具名称
模具点检记录表范本
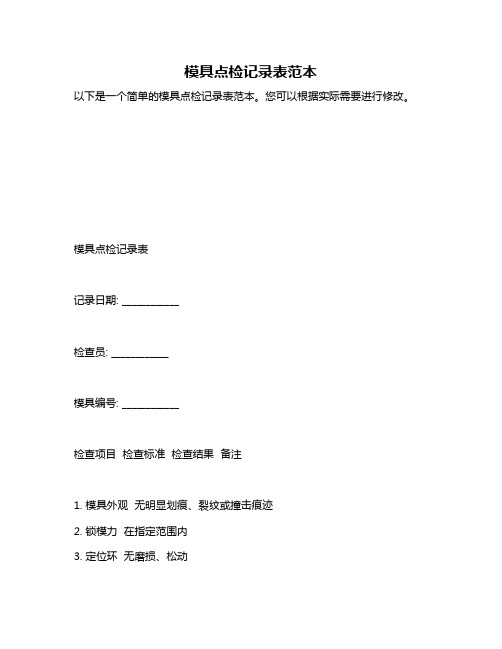
模具点检记录表范本
以下是一个简单的模具点检记录表范本。
您可以根据实际需要进行修改。
模具点检记录表
记录日期: ____________
检查员: ____________
模具编号: ____________
检查项目检查标准检查结果备注
1. 模具外观无明显划痕、裂纹或撞击痕迹
2. 锁模力在指定范围内
3. 定位环无磨损、松动
4. 冷却水道畅通无堵塞
5. 喷嘴状态无磨损、堵塞
6. 顶针状态无弯曲、断裂
7. 模腔表面无杂质、烧伤
8. 安全防护装置完好无损、有效
9. 润滑系统正常工作,无泄漏
10. 其他特殊要求如温度、湿度等
总体评价: ____________ (优、良、中、差)
建议措施: ________________________________________。
冲压件首检记录表.doc.td

冲压件首检记录表
NO:产名名称材质规格型号
机床编号检验数量检验日期
序号检验项
目
技术要
求
检测方式
实测记录判定
1 2 3 4 5 6
合格
数
不合
格数
1 外观无压印目测
2 无批锋目测
3 尺寸卷尺
4 卡尺/角度尺
5 卡尺/角度尺
6 卡尺/角度尺
7 卡尺/角度尺
结论:符合要求
检验员:注:无定量要求项符合要求记“√”,不符合要求记“×”
冲压件首检记录表
NO:
产名名称材质规格型号
机床编号检验数量检验日期
序号检验项
目
技术要
求
检测方式
实测记录判定
1 2 3 4 5 6
合格
数
不合
格数
1 外观无压印目测
2 无批锋目测
3 尺寸卷尺
4 卡尺/角度尺
5 卡尺/角度尺
6 卡尺/角度尺
7 卡尺/角度尺
结论:符合要求
检验员:注:无定量要求项符合要求记“√”,不符合要求记“×”。