塑料件设计指导《PlasticDesignGuide》资料重点
塑胶件设计指南之简洁优美版

塑胶件设计指南之简洁优美版关注上方公众号“降本设计”,获取更多原创产品设计知识!均匀壁厚均匀壁厚,这是塑胶件设计最重要的原则。
避免壁厚急剧变化,保证平滑过渡。
局部过厚处掏空并使用加强筋补强局部过厚的区域会导致塑胶件发生缩水和翘曲等缺陷,需要进行掏空的设计,并使用加强筋补强。
避免尖角塑胶件的任意部位(分模线处除外)都需要避免尖角。
加强筋的设计加强筋常用于提高塑胶件的强度,其厚度一般在壁厚的0.5~0.7倍,加强筋厚度过厚会造成缩水,高度一般在壁厚的3倍以下。
脱模斜度在可能的情况下,设计至少2度的脱模斜度,特征高度越高,脱模斜度越大。
支柱当塑胶件需要使用螺纹连接时,推荐使用自攻螺丝,并在塑胶件上设计支柱。
不推荐螺牙注塑成型,这是因为直接成型的螺牙会在脱模时造成倒扣;也不推荐在塑胶件上直接攻牙,因为二次加工成本高。
螺纹嵌件当需要反复的拆卸时,可以使用螺纹嵌件。
螺纹嵌件可以通过热熔、超声波和模内注塑等方式加工。
卡扣紧固卡扣是最简单、最经济以及最快速的塑胶件紧固工艺。
干涉筋干涉筋是指塑胶件上的局部凸起特征,当其它零件例如轴承等装配到塑胶件之中时,干涉筋因为受力变形而把轴承卡紧。
干涉筋是轴、轴承类零件进行紧配合时常用的一种方法。
干涉量为0.25mm,干涉筋不必添加脱模斜度。
活铰链活铰链是塑胶件上较薄较有弹性的一部分,把一个塑胶件的两部分较硬实体连接为一个整体,并允许两部分实体绕着活动铰链旋转一定角度甚至180度以上。
倒扣尽量避免倒扣,倒扣会增加模具复杂度和模具成本。
强脱当塑料具有足够的弹性时,可以使用强脱。
强脱常用于加工杯盖中的螺纹。
避免对玻纤增强塑料使用强脱。
一般来说,PP、HDPE和PA可以承受直径大小5%的强脱。
滑块当塑胶件中存在倒扣时,由于美观或技术的原因,必须使用侧向的抽芯机构即滑块。
在塑胶件设计时,需要为滑块的运动提供预留空间;另外,滑块的运动方向应当与开模方向垂直,非垂直方向会使得模具复杂。
一些降本建议o避免倒扣。
塑胶设计指南
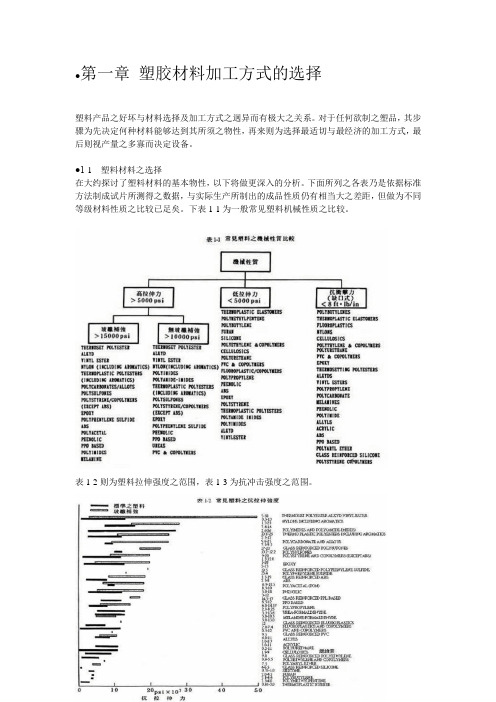
●第一章塑胶材料加工方式的选择塑料产品之好坏与材料选择及加工方式之迥异而有极大之关系。
对于任何欲制之塑品,其步骤为先决定何种材料能够达到其所须之物性,再来则为选择最适切与最经济的加工方式,最后则视产量之多寡而决定设备。
●1-1塑料材料之选择在大约探讨了塑料材料的基本物性,以下将做更深入的分析。
下面所列之各表乃是依据标准方法制成试片所测得之数据,与实际生产所制出的成品性质仍有相当大之差距,但做为不同等级材料性质之比较已足矣。
下表1-1为一般常见塑料机械性质之比较。
表1-2则为塑料拉伸强度之范围,表1-3为抗冲击强度之范围。
表1-4及表1-5,则为塑料之其它性质。
参考以上各表,即大约可知塑品用何种材料可达到其用途之所须性质要求。
一般而言加了玻纤后,可增加拉伸力、减少拉伸量、抗磨耗力降低、挠曲力增高、热变形温度增加、热膨胀降低及较不透明,而耐冲击力则不一定。
但是硬度(除非高填充)、电气性质、抗化学性及抗天候性则甚无影响。
表1-6则为一般材料之机械性质之定性趋势表。
若是依各种用途来分,所使用之塑料大概可列表如1-7所示。
●1-2塑料加工方式之选择塑料之加工方式五花八门,随着材料及成品而有极大之差异。
以下对一般常见的加工方式,作一番简介:1. 射出成形(injection molding)在所有之塑料加工成形方法上,射出成形最为被广泛使用。
其法为热塑性塑料或热固性塑料导入于射出成形机的加热筒中,俟其完全熔融后,藉由柱塞或螺杆之压力,产生热能及摩擦热能,将其注入于闭合模具之模穴中,固化后,再开启模具取出成品。
此种加工技术因材料、机械设计及制品要求而衍生出其它之方法,如预嵌入金属零件之插件成形、多色及混色的射出成形,结构发泡的射出成形、气体辅助射出成形(gas assisted injection molding)、共射出成形(coinjection)、射出中空成形及利用液态单体或液态预聚合物为原料之反应射出成形(RIM)等方法。
塑胶产品设计要点
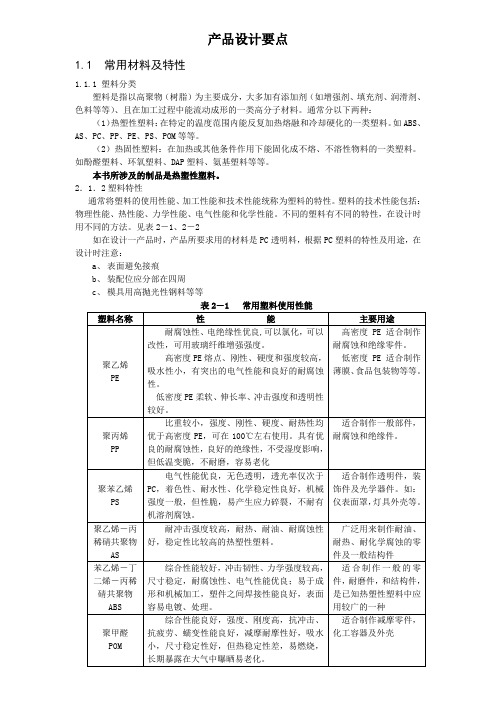
产品设计要点1.1 常用材料及特性1.1.1 塑料分类塑料是指以高聚物(树脂)为主要成分,大多加有添加剂(如增强剂、填充剂、润滑剂、色料等等)、且在加工过程中能流动成形的一类高分子材料。
通常分以下两种:(1)热塑性塑料:在特定的温度范围内能反复加热熔融和冷却硬化的一类塑料。
如ABS、AS、PC、PP、PE、PS、POM等等。
(2)热固性塑料:在加热或其他条件作用下能固化成不熔、不溶性物料的一类塑料。
如酚醛塑料、环氧塑料、DAP塑料、氨基塑料等等。
本书所涉及的制品是热塑性塑料。
2.1.2塑料特性通常将塑料的使用性能、加工性能和技术性能统称为塑料的特性。
塑料的技术性能包括:物理性能、热性能、力学性能、电气性能和化学性能。
不同的塑料有不同的特性,在设计时用不同的方法。
见表2-1、2-2如在设计一产品时,产品所要求用的材料是PC透明料,根据PC塑料的特性及用途,在设计时注意:a、表面避免接痕b、装配位应分部在四周c、模具用高抛光性钢料等等表2-1 常用塑料使用性能1.2 塑胶制品常用设计工艺塑料件结构的工艺性,直接关系到其成形模具结构、类型、生产周期与成本。
只有符合模塑工艺要求的塑件设计,才能顺利成形,确保内在与外观质量,达到高效率的生产和低成本的目的。
塑件设计的工艺性,自然与其成形方法密切关联。
塑件的几何形状与成形方法、模具结构、能否顺利成形与脱模、以及与制品质量等均有密切关系。
塑件几何形状设计必须满足其成形工艺要求。
1.1.1避免侧孔与侧凹塑件的内外表面形状应设计得容易成形与脱模,以防止采用复杂得瓣合模和侧抽芯机构,因此塑件设计应尽量避免有侧孔与侧凹。
不是所有的设计都能制作生产出来或者容易生产出来的,应尽可能的了解产品的生产制作过程,避免设计与现实脱离,见表2-3若干典型示例。
表2-3 带有侧孔与侧凹的塑件设计示例2.2.2脱模斜度为了便于塑件从模腔顺利脱模或抽芯,塑件设计时必须考虑到内外壁面应有足量的脱模斜度。
塑胶产品结构设计重点
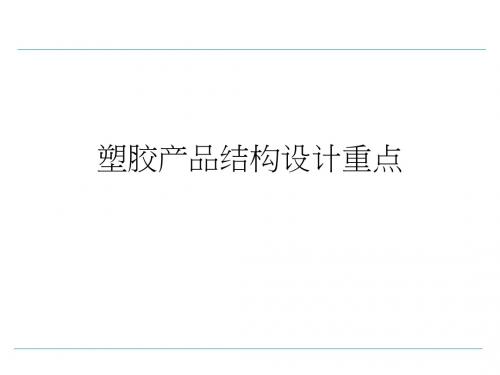
孔离边位或内壁边之要点 :
confidential
18
四、塑胶产品结构设计-洞孔 (Hole)
盲孔设计要点: 盲孔是靠模具上的镶针形成,而镶针的设计只能单边支撑在模具上,因此很容易 被溶融的塑料使其弯曲变形,造成盲孔出现椭圆的形状,所以镶针的长度不能过长。 盲孔深度最大是直径的3倍,考虑模具镶针强度要求直径最小0.8mm。 外观件上的各种凹槽,如雕刻文字等,要求棱线分明,导致过渡太急,易产生气
的刚性及强度有所不足时再适当地增加。
confidential
10
二、塑胶产品结构设计-加强筋
加强筋被置於塑胶部件边缘的基本尺寸建议:
因肋骨在冷却时会在背面造 成凹痕(或色差),对策可在加强 筋对应的後面,设置一些小肋 骨或凹槽,用那些肋骨和凹槽 可以作装饰用途而消除缩水的
缺陷。
confidential
B. 最理想的壁厚分布是切面在任何一个地方都是均一的厚度。当因 功能上的需求以致壁厚有所改变时,由厚胶料的地方过渡到薄胶 料的地方应尽可能顺滑。太突然的壁厚过渡转变会导致因冷却速 度不同和产生乱流而造成尺寸不稳定和表面问题。
采用射出成型的生产方法时,流道、浇口和部件的设计应使塑料 由厚胶料的地方流向薄胶料的地方。这样使模腔内有适当的压力 以减少在厚胶料的地方出现缩水及避免模腔不能完全充填的现象。
confidential
14
三、塑胶产品结构设计-支柱 ( Boss )
对于外观件,当有螺丝柱子,需要进行缩水验证,依照上页图示意,塑胶壁厚 1.5 ,螺丝柱子外径3.4,验证结果 NG:(1.8-1.5)/1.5*100%=20% >8%。 外观面有可能会有缩水痕迹。
塑胶件的结构设计(提纲)
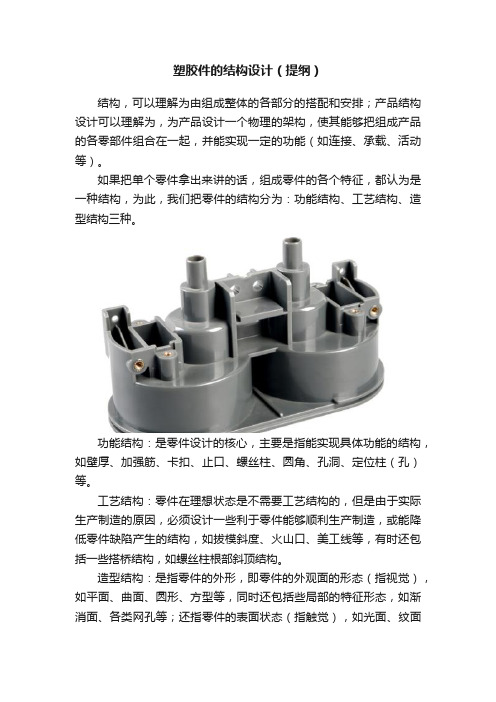
塑胶件的结构设计(提纲)结构,可以理解为由组成整体的各部分的搭配和安排;产品结构设计可以理解为,为产品设计一个物理的架构,使其能够把组成产品的各零部件组合在一起,并能实现一定的功能(如连接、承载、活动等)。
如果把单个零件拿出来讲的话,组成零件的各个特征,都认为是一种结构,为此,我们把零件的结构分为:功能结构、工艺结构、造型结构三种。
功能结构:是零件设计的核心,主要是指能实现具体功能的结构,如壁厚、加强筋、卡扣、止口、螺丝柱、圆角、孔洞、定位柱(孔)等。
工艺结构:零件在理想状态是不需要工艺结构的,但是由于实际生产制造的原因,必须设计一些利于零件能够顺利生产制造,或能降低零件缺陷产生的结构,如拔模斜度、火山口、美工线等,有时还包括一些搭桥结构,如螺丝柱根部斜顶结构。
造型结构:是指零件的外形,即零件的外观面的形态(指视觉),如平面、曲面、圆形、方型等,同时还包括些局部的特征形态,如渐消面、各类网孔等;还指零件的表面状态(指触觉),如光面、纹面等。
在之前文章有提到,本年度主要分享结构设计的知识多一些,以上就是需要介绍的主题提纲,即由功能结构、工艺介绍、造型结构组成的零件的结构设计。
需要声明的是,是以塑胶件的角度进行介绍,其他诸如压铸件,结构上虽与塑胶件有很大相似之处,但咱不做具体的分析介绍。
以上一些列的结构知识基本上囊括了一件塑胶零件的结构设计内容,(注意:特指结构,不包含CMF相关的内容)。
所以,大家可以随意拿出一件塑胶零件,仔细观察,零件的结构基本都可以从上面提到的三种结构分类找到具体的结构。
大家不要误解零件的结构就是产品的结构,实际上,产品的具体结构设计的内容不单单是零件的结构,还应包括零件之间的分配关系(即拆件)以及配合关系(即装配),这部分内容留到以后介绍,(注意:两个零件通过有些配合关系可视为一个零件,如双色件)。
可能有些小伙伴会问,这些内容太基础了,很多资料网上都有,甚至其他公众号都有相对应的介绍。
塑胶产品结构设计重点

塑胶产品结构设计重点一、材料选择塑胶产品的结构设计首先要考虑材料选择。
材料的选择直接关系到产品的性能、质量和成本,因此需要根据产品的具体要求和使用环境,选择适合的塑胶材料。
常见的塑胶材料有聚乙烯(PE)、聚丙烯(PP)、聚氯乙烯(PVC)、聚苯乙烯(PS)、聚酯(PET)等。
在选择材料时需要考虑产品的机械性能、耐热性、耐化学性、耐候性、电气性能、透明度等因素。
同时还需要考虑材料的加工性能,如流动性、热稳定性、收缩率等。
材料的选择不合理会导致产品性能不达标或加工工艺困难,因此需要在产品设计之前进行充分的材料筛选和试验。
二、结构设计塑胶产品结构设计主要包括外形设计和内部结构设计。
外形设计需要考虑产品的功能、美观和人机工程学等因素。
合理的外形设计可以提升产品的市场竞争力和用户体验。
内部结构设计需要考虑产品的强度、稳定性和装配性等因素。
合理的内部结构设计可以提高产品的性能和质量,减少生产和使用过程中的故障和损坏。
此外还需要考虑产品的可制造性和生产效率。
在进行结构设计时,需要采用CAD软件进行三维建模和仿真分析,以验证设计的可行性和优化设计。
三、模具设计塑胶产品的生产需要模具进行注塑成型。
模具设计是塑胶产品结构设计中非常重要的一部分,直接影响产品的质量和生产效率。
模具设计需要考虑产品的尺寸、形状和结构特点,选择合适的注塑工艺,确定模具的结构和加工工艺。
模具的设计要求高精度、高效率、长寿命和低成本,需要充分考虑模具的结构强度、冷却系统、顶出系统、塑胶流道等因素。
合理的模具设计可以提高产品的精度和表面质量,降低生产成本和生产周期。
四、加工工艺塑胶产品的加工工艺是塑胶产品结构设计的最后一步,直接影响产品的成型质量和效率。
常见的塑胶加工工艺有注塑成型、吹塑成型、挤出成型、压缩成型等。
在选择和优化加工工艺时,需要考虑产品的形状、尺寸、材料特性和生产要求等因素。
合理的加工工艺可以提高产品的质量和生产效率,降低生产成本和能耗。
塑胶件设计准则(一)
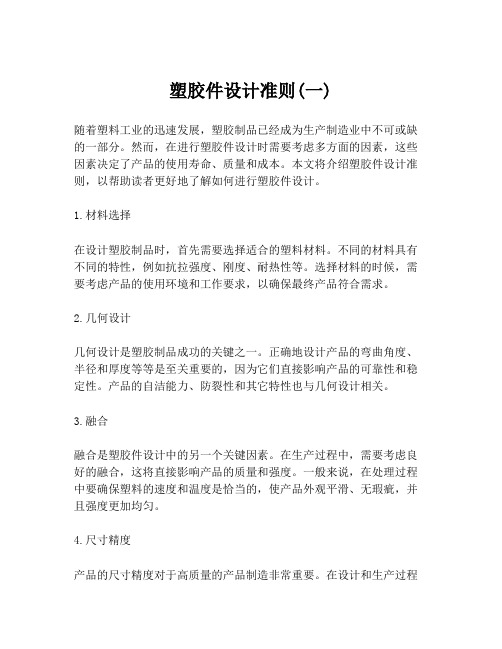
塑胶件设计准则(一)随着塑料工业的迅速发展,塑胶制品已经成为生产制造业中不可或缺的一部分。
然而,在进行塑胶件设计时需要考虑多方面的因素,这些因素决定了产品的使用寿命、质量和成本。
本文将介绍塑胶件设计准则,以帮助读者更好地了解如何进行塑胶件设计。
1.材料选择在设计塑胶制品时,首先需要选择适合的塑料材料。
不同的材料具有不同的特性,例如抗拉强度、刚度、耐热性等。
选择材料的时候,需要考虑产品的使用环境和工作要求,以确保最终产品符合需求。
2.几何设计几何设计是塑胶制品成功的关键之一。
正确地设计产品的弯曲角度、半径和厚度等等是至关重要的,因为它们直接影响产品的可靠性和稳定性。
产品的自洁能力、防裂性和其它特性也与几何设计相关。
3.融合融合是塑胶件设计中的另一个关键因素。
在生产过程中,需要考虑良好的融合,这将直接影响产品的质量和强度。
一般来说,在处理过程中要确保塑料的速度和温度是恰当的,使产品外观平滑、无瑕疵,并且强度更加均匀。
4.尺寸精度产品的尺寸精度对于高质量的产品制造非常重要。
在设计和生产过程中,必须严格控制尺寸精度。
如果精度过低,往往会影响产品的可靠性和性能。
5.模具设计加工模具的质量将直接影响成品的质量。
因此,在设计模具时,需要充分考虑产品的要求,并尽可能减少缺陷的可能性。
从模具材料的选择到处理方法的选定,都必须被考虑到。
综上所述,塑胶件设计准则是非常重要的,可以确保产品质量和性能。
设计师需要仔细考虑产品使用的工作条件,选择适合的材料,并采取正确的几何设计方法。
保证良好的融合、尺寸精度和模具设计,可以使塑料制品达到最高质量标准,从而满足用户的需求。
《塑料模设计指导》电子教案 塑料模设计指导3
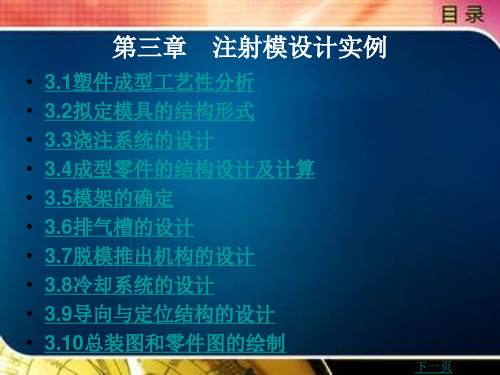
多型腔模具尽可能采用平衡式排列布置,且力求紧凑,并与浇口开设的 部位对称。由于该设计选择的是一模两腔,故采用直线对称排列,如图 3-3所示。
(3)模具结构形式的确定
从上面的分析可知,本模具设计为一模两腔,呈直线对称排列,根据塑 件结构形状,推出机构拟采用脱模板推出的推出形式。浇注系统设计时 ,流道采用对称平衡式,浇口采用侧浇口,且开设在分型面上。因此, 定模部分不需要单独开设分型面取出凝料,动模部分需要添加型芯固定 板、支撑板和脱模板。由以上综合分析可确定选用带脱模板的单分型面 注射模。
②吸湿性强。水的质量分数应小于0.3%,必须充分干燥,要求表面光 泽的塑件应要求长时间预热干燥。
③流动性中等。溢边料0. 04 mm左右。
④模具设计时要注意浇注系统,选择好进料口的位置、进料形式。当 推出力过大或机械加工时塑件表面易呈现白色痕迹。
(3) AIDS的主要性能指标
其性能指标见表3-2
上一页 下一页 返回
第三章 注射模设计实例
• 3.1塑件成型工艺性分析 • 3.2拟定模具的结构形式 • 3.3浇注系统的设计 • 3.4成型零件的结构设计及计算 • 3.5模架的确定 • 3.6排气槽的设计 • 3.7脱模推出机构的设计 • 3.8冷却系统的设计 • 3.9导向与定位结构的设计 • 3.10总装图和零件图的绘制
(1)外形尺寸 该塑件壁厚为3 mm塑件外形尺寸不大,塑料熔体流程不太长,适合 于注射成型,如图3-1所示。
(2)精度等级 每个尺寸的公差不一样,有的属于一般精度,有的属于高精度,就按 实际公差进行计算。
(3)脱模斜度 ABS属无定型塑料,成型收缩率较小,参考表3-1选择该塑件上型芯 和凹模的统一模斜度为1°。
塑胶件设计手册

塑胶件设计手册
塑胶件设计手册是一本主要介绍塑胶件设计原则、方法、工艺等内容的手册。
它的目的是帮助设计师在塑胶件的设计过程中能够正确应用相关知识和技术,提高设计质量和效率。
塑胶件设计手册通常包含以下内容:
1. 塑胶材料选型:介绍各种常用的塑胶材料的特性、性能以及选择原则,帮助设计师根据产品要求和制造工艺选择合适的材料。
2. 塑胶件设计原则:介绍塑胶件设计的基本原则,如尺寸设计、结构设计、壁厚设计等,帮助设计师避免一些常见的设计失误。
3. 注塑成型工艺:介绍塑胶件的注塑成型工艺,包括模具设计、注塑工艺参数设置、成型工艺控制等内容,帮助设计师在设计过程中考虑到制造工艺的要求。
4. 塑胶件结构设计:介绍塑胶件的结构设计方法和技巧,如缩减零件数量、减少接口、提高装配性等,以实现更简化和高效的设计。
5. 塑胶件表面处理:介绍塑胶件表面处理的方法和技术,如喷漆、镀铬、氧化等,以提高产品的外观和性能。
6. 塑胶件模具设计:介绍塑胶件模具设计的基本原理和方法,包括模具结构设计、模具材料选择、模具加工工艺等,以保证
模具能够满足产品的制造需求。
除了以上内容,塑胶件设计手册还可以包括一些设计实例和技术指导,以帮助设计师更好地理解和应用其中的知识。
总之,塑胶件设计手册是塑胶件设计过程中的一个重要参考资料,对设计师具有很大的指导和帮助作用。
塑胶件设计基础知识
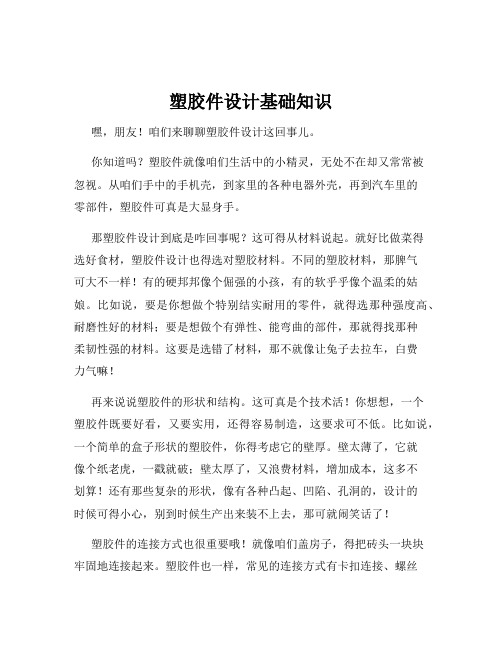
塑胶件设计基础知识嘿,朋友!咱们来聊聊塑胶件设计这回事儿。
你知道吗?塑胶件就像咱们生活中的小精灵,无处不在却又常常被忽视。
从咱们手中的手机壳,到家里的各种电器外壳,再到汽车里的零部件,塑胶件可真是大显身手。
那塑胶件设计到底是咋回事呢?这可得从材料说起。
就好比做菜得选好食材,塑胶件设计也得选对塑胶材料。
不同的塑胶材料,那脾气可大不一样!有的硬邦邦像个倔强的小孩,有的软乎乎像个温柔的姑娘。
比如说,要是你想做个特别结实耐用的零件,就得选那种强度高、耐磨性好的材料;要是想做个有弹性、能弯曲的部件,那就得找那种柔韧性强的材料。
这要是选错了材料,那不就像让兔子去拉车,白费力气嘛!再来说说塑胶件的形状和结构。
这可真是个技术活!你想想,一个塑胶件既要好看,又要实用,还得容易制造,这要求可不低。
比如说,一个简单的盒子形状的塑胶件,你得考虑它的壁厚。
壁太薄了,它就像个纸老虎,一戳就破;壁太厚了,又浪费材料,增加成本,这多不划算!还有那些复杂的形状,像有各种凸起、凹陷、孔洞的,设计的时候可得小心,别到时候生产出来装不上去,那可就闹笑话了!塑胶件的连接方式也很重要哦!就像咱们盖房子,得把砖头一块块牢固地连接起来。
塑胶件也一样,常见的连接方式有卡扣连接、螺丝连接、胶水连接等等。
每种连接方式都有它的优缺点。
卡扣连接简单方便,但是强度可能不够;螺丝连接牢固可靠,但是会影响外观;胶水连接密封性好,但是操作起来麻烦。
这可得根据具体情况来选择,就像选鞋子,得合脚才行!还有啊,塑胶件的表面处理也不能马虎。
你想要它光滑如镜,还是有磨砂质感?是要鲜艳的颜色,还是低调的纯色?这都得在设计的时候想好。
不然生产出来的塑胶件表面粗糙、颜色暗淡,那可就没人喜欢啦!在塑胶件设计的过程中,还得考虑模具的问题。
模具就像是塑胶件的“妈妈”,它决定了塑胶件的出生质量。
模具设计得好,生产出来的塑胶件尺寸精准、质量上乘;模具设计不好,那生产出来的塑胶件就可能有各种缺陷,这可就麻烦大了。
第5部分:塑胶件设计指南
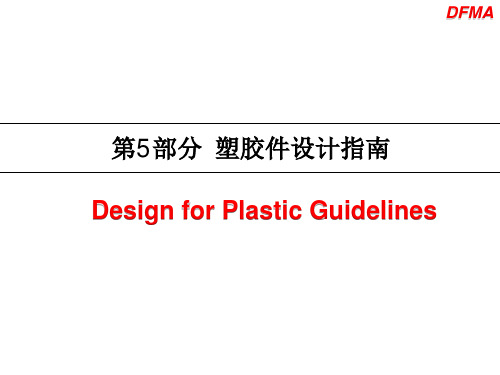
原始的设计
优化的设计
11
1.零件壁厚
C. 零件壁厚均匀
当壁厚不均匀时: 原始的设计
较好的设计a
较好的设计b
优化的设计
DFMA
12
2.避免尖角
A.避免零件外部尖角
DFMA
原始的设计
优化的设计
例外:零件分模线处直角的设计比较好
原始的设计
优化的设计
13
2.避免尖角
B.避免在塑胶熔料流动方向上产生尖角
39
8.提高塑胶件外观的设计
D.设计美工沟:
原始的设计 美工沟的设计之一 美工沟的设计之二
DFMA
40
8.提高塑胶件外观的设计
DFMA
E.避免外观零件表面出现熔接痕:
塑胶件表面咬花可以部分掩盖熔接痕,但并不能完全掩盖熔接痕; 喷漆可以掩盖熔接痕; 合理设置浇口的位置和数量,避免在零件重要外观表面产生熔接痕; 保证模具通风顺畅。
二.塑胶件设计指南
1. 零件壁厚 2. 避免尖角 3. 脱模斜度 4. 加强肋的设计 5. 支柱的设计 6. 孔的设计 7. 提高塑胶件强度的设计
DFMA
8. 改善塑胶件外观的设计 9. 降低塑胶件成本的设计 10. 注塑模具可行性设计
三.塑胶件的装配
1. 卡扣装配 2. 紧固件装配 3. 超声波焊接
分类非结晶塑胶结晶塑胶比重较低较高拉伸强度较低较高拉伸模量较低较高延展性较高较低抗冲击性较高较低最高使用温度较低较高收缩率和翘曲较低较高流动性较低较高耐化学性较低较高耐磨性较低较高抗蠕变性较低较高硬度较低较高透明性较高较低加玻璃纤维补强效果较低较高材料特性塑胶分类dfma一
DFMA
第5部分 塑胶件设计指南 Design for Plastic Guidelines
塑胶件设计指导
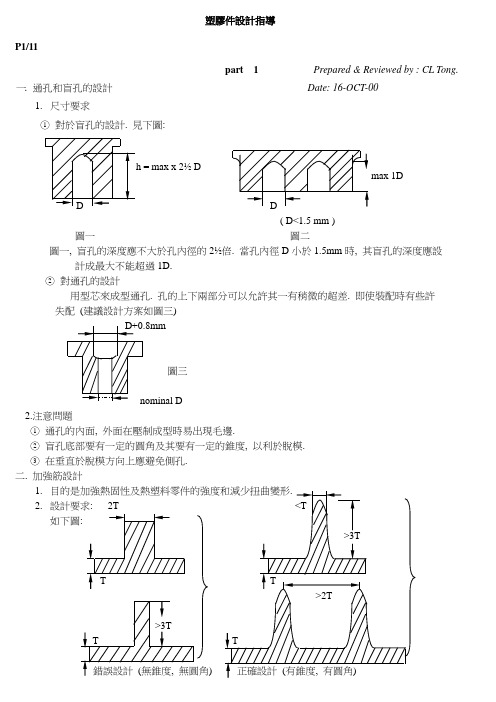
塑膠件設計指導P1/11part 1 Prepared & Reviewed by : CL Tong.一. 通孔和盲孔的設計 Date: 16-OCT-001. 尺寸要求○1 對於盲孔的設計. 見下圖:max 1D( D<1.5 mm ) 圖一圖二圖一, 盲孔的深度應不大於孔內徑的2½倍. 當孔內徑D 小於1.5mm 時, 其盲孔的深度應設計成最大不能超過1D.○2 對通孔的設計用型芯來成型通孔. 孔的上下兩部分可以允許其一有稍微的超差. 即使裝配時有些許 失配 (建議設計方案如圖三)圖三2.注意問題○1 通孔的內面, 外面在壓制成型時易出現毛邊. ○2 盲孔底部要有一定的圓角及其要有一定的錐度, 以利於脫模. ○3 在垂直於脫模方向上應避免側孔. 二. 加強筋設計1.2. 設計要求: 2T 如下圖)圖四P2/11 圖四中, 加強筋根部的厚度應不大於所要加強部分壁厚T, 筋高度應大於3T, 而筋與筋之間的距離(筋中心線與筋中心線之間) 應大於2T.3.注意問題○1多根加強筋設計其效果優於單根加強筋(即使你增大其厚度或高度)○2筋的根部要有一定的圓角, 要有一定的錐度, 以利於脫模.○3加強筋的方向應跟模壓, 成型, 熔料流動方向相一致.三.击台1.目的: 增強孔的穩固及強度或裝配附件之用.2.設計要求圖五圖六击台高度最大不超過击台根部尺寸D的二倍, 击台根部外徑與內徑之差的一半應為0.8T如圖五. 击台跟平面相裝配時, 击台須設計在成型件的四周. 且其高度如圖六所示應為0.4mm. 如果A外平面的平面度要求較高. 還需要打磨.3.注意問題○1击台根部要有一定的圓角和其要有一定的錐度, 以利於脫模.○2當击台高度過高時, 可在击台外部加加強筋, 不僅可以增大击台強度. 而且還有利於促進熔爐塑料的流動.四.錐度設計1.含義: 由於成型時零件內外表面收縮率不一致, 在設計時, 根據塑料對型蕊的粘附力要大於對型腔的粘附力, 設置內表面錐度大於外表面錐度.2.注意問題○1成型件設計要有一定錐度是有利於脫模.○2同樣有利於減少成型過程中瑕疵的形成.五.螺紋的設計(熱固性塑料)塑料螺紋包括螺紋孔和螺牙.1.如下圖○1螺牙要圓, 不宜尖.○2螺紋長度要短.2.如下圖P3/11, 螺紋的中心線位於分型面上.3.螺牙角選擇為32º4.採取成型後再加工螺紋方式去獲取塑料螺紋.5.當螺紋孔要多次裝配時, 建議使用內嵌件.六.嵌件1.要求:○1在塑膠件成型之後. 立即把嵌件壓制到膠件上. 讓包圍著嵌件的部分收縮而來緊嵌件.○2外部嵌件會因為合成物料的收縮而松軟, 內部嵌件會因它的收縮而破裂. 所以在設計嵌件時應考慮配套零件的壁厚,嵌件包圍部分壁厚設計參考表6.1-3.(略)2.注意問題○1用模具壓制嵌件時, 易出現嵌件由於圍壁出現收縮而松動又或者壁易出現斷裂現象.七.平面度由於在成型時易混入氣泡等使熱固性塑料出現收縮現象. 要獲得良好的平面度十分不易的. 通常要求表面留有0.3%的余量.八.零件圖:最終零件圖要指出, 哪一個地方不可以出現分型線. 不可以出現澆口痕, 哪一個地方需要印上模號和模具標記. 哪一個表面出現缺點不能接受等等. 使用SPI/SPE的配套完模工具作為指導.這樣做的目的是易於發現問題和解決問題.九.尺寸因素熱固性塑料成型件尺寸精度可以達到要求公差. 但是, 其精度難以跟加工金屬零件相提並論.造成這樣的原因是:1.塑膠料的收縮率(在成型中).2.成型後塑膠料的收縮率.3.時間, 溫度, 壓力(成型條件)4.模具類型.5.射出及預成型尺寸.6.熔料的流量變異.7.塑膠料種類.十.公差尺寸公差表參考表6.1.4(略)P4/11PART 2一. 注射成型過程○1粒狀塑膠料加入到料斗在180℃高溫下隔熔成液體狀. (熔化的溫度同塑膠料的種類和成型條件有關) 進入鋼模, 被水冷卻成固體狀(水在模外) 取零件.○2整個過程周期為45秒. 壓力為70,000Kpa, 大部分時間用於冷卻.二. 注射成型件的典型特徵及發展趨勢.注射成型適用於大批量複雜零件的生產. 雖然其仍然有極多局限性, 但由於一個注射成型產品可以代替裝配出來的產品, 所以, 其經濟性很好, 另外, 由於顏色, 形狀可以一次性成型做到, 免去二次加工.○1主要特徵:I. 廣泛應用於薄壁零件, 但也可以成型大塊及不同壁厚的零件.II. 強度低, 適用於外殼, 連接桿等受力較小的場合.○2發展超勢熱塑性材料強度會變得越來越大, 機械特性越來越好, 一些類似尼龍, 複合碳酸鹽等,其強度可以同鐵, 鋁, 甚至鋼相比美.PART 3 P5/11一. 收縮率的影響1.啤模時會產生許多不規則或拗曲的形狀, 常見的有夾水紋, 縮水等, 它們常發生在零件較厚的部位.(如圖七)圖七2.另一種經常產生的缺限就是“U”型楔面收縮(如圖八). 第三種情況就是在左右平面收縮變形. (如圖九) 方向易產生平面出現固收縮而引起的曲線.圖八圖九二. 經濟的生產數量注射模適用於量生產的, 一般不會用此方式, 除非有上萬或者更多零件要生產. 之所以有此限製是因為每種零件都需做一個自己獨有的模.只有大量生產開模的經費才能在批量生產中收回, 即便是很小的零件都要花幾千元的開模費. 那些較大較複雜的零件就更會花上萬乃甚至十萬元的經費.三. 合適的原料多種合適的熱熔膠可用於注射模生產. 常用的有聚乙烯﹑PVC﹑尼龍﹑ABS﹑等.注射模在熱塑模市場有很重要的地位, 因此工程人員必須設法使之更利於生產. 物理特性及價格常是選擇這些材料時比加工性能更為重要的因素.通常, 高性能的工程塑料往往比日常使用的塑料像PE料, PP料, PS料等之類更難開模, 特別是PVC雖具有價廉和高性能的優點, 但卻比一般塑膠更難注塑, 最主要的缺點是它的熔點到凝固溫度範圍太窄.表6-2-2列出了一些常用的注塑材料及其特性, 價格和使用範圍. (略)四. 設計指南1.水口及頂針位:設計者須考慮它們的方位, 因為它們會對表面成型產生影響. 如果注件有內外側的話, 水口常開在下側. 水口一般的方位見圖6-2-6(略) 圓形或圓柱型注件的中央水口或者近於中央水口(較大面積的注件)在注塑時是最理想的安全模塑頂料方式.2.注件厚度:表6-2-3 列出了注件厚度的正常值及下限(略), 表明了塑料在注塑完工以前它在模件中冷卻和固化的趨勢, 塑料流動愈緩慢, 則注件厚度要求愈窄, 當然注件的厚度要盡可能的一致. 即便是不得已要改動厚度, 最好變動要舒緩, 不突變.(如圖十)圖十P6/11錯誤設計 正確設計錯誤設計 稍好設計 最好設計3. 孔的設計● 注塑件開孔雖可行卻是開模最複雜的一個因素. 孔周圍易產生飛邊以及 “夾紋” 或是 “夾水weld line圖十一●兩孔間距或是孔到邊的距離至少要有一個孔徑. (如圖十二)錯誤設計 正確設計 圖十二●為避免外應力的影響,單孔必須開在距注件邊緣三個或以上孔徑的地方.(如圖十三)P7/11正確設計錯誤設計圖十三●通孔較盲孔好, 因為做孔所用到的頂針可以在兩頭加以固定, 這樣做出的孔位置尺寸很標準而且可以避免彎曲或折斷.●在注件底部開孔較在邊上開孔好, 因為後者須要可折卸頂針.●盲孔深度須小於兩孔徑之和, 若孔徑為1.5mm或更小, 那麼其深度最小應有一個孔徑. (如圖十四)大孔小孔圖十四●利用击台可以增加盲孔深度, 這須用到較硬的頂針(型蕊). (如圖十五)錯誤設計正確設計圖十五●切去通孔零件兩端的部分可縮短頂針(型蕊)的長度. (如圖十六)錯誤設計正確設計(此設計可降低心棒受損危險性)圖十六4.加強筋●加強筋必須比注件的厚度薄一些, 防止注件表面縮水. 比較好的方法是保證加強的寬度為注件厚度的一半或更少.P8/11●同樣為避免縮水, 加強筋高度須不大於壁厚的1.5倍.●如果有必要, 可以用兩個筋位去加強注件強度用以代替一個更高的筋位的作用.這些筋位須以兩個或以上壁厚的距離分散開來.●為使注件順利地從模中取出, 加強筋必須與注件方位垂直.●由加強筋引起的縮水可以通過在其對面增加凹槽的方法加以減輕和去除. (如圖十七)蝕紋錯誤正確正確正確圖十七●加強筋的設計規則如圖十八.錯誤設計正確設計5.击台: 主要用於塑件的表面突起.●它必須有較大的半徑和圓角.●在加強筋中說明過的原則同樣適用於击台一節. 圖十九表明了固體击台的最大高度和寬度.圖十九●如果可能, 將击台做至邊角處可有助於充模時塑料的流動, 若有必要, 在做可拆裝的击台時,加個聯接筋位將有助於塑膠充模.●如果可能, 盡力避免在罐上部做击台, 因為這將會產生更多氣泡.P9/11●在击台上採用5°錐度, 其設計與加強筋相同.●如果較大的击台要用到, 那必須是中空, 且與塑件厚保持一致.6.凹槽凹槽在注塑中同樣會用到, 只是他們要用到滑動型蕊和分模方式, 凹槽可開在注件的分型線或其延長線方向上, 以避免型心的拉力作用. 凹槽可以不依靠型蕊的拉力即可較容易的脫模. 如果凹槽被移除, 則另一半模必定會保持完好. 那麼頂針(型蕊)將被用於脫模. 凹槽的一般設計尺寸如圖二十.7.螺紋設計螺紋成型盡管很複雜, 但卻是可以辦到的可使用以下三個方法:●螺紋成型後使用旋轉型蕊. 可以使模件順利地從模中取出.●令螺絲軸線與分型面一致. 這樣可避免用到旋轉型蕊, 且可以在模型間得到更好的配合以減少螺紋上的流痕. 這種方案僅用於外部螺紋制作, 且成本昂貴, 除非螺紋可以遠離分型面,而通常這也是可行的. 如果這種方法不適用, 另一種可能的方式將被要求用來移除分型面在螺紋上產生的流痕.●減少螺紋齒數, 降低螺牙高度, 零件可以直接從模腔中脫出而不須從製品中擰下來. 螺牙未端不宜延長到與垂直底面相接處, 否則易使脆性塑料件發生斷裂, 螺紋的始端均不應突然開始和結束, 而應有過渡部分. 因為它方便取出而且避免了多余的飛邊, 以致模件很難配合,甚至生成流痕. 如果是剛性螺紋, 必須使用金屬模蕊.P10/11PART 4原始設計改善設計(增強強度)有時候為了確保產品具有足夠的強度有必要修改設計方案. 防止縮水方法之一是在部件易於受影響的表面加鋸齒狀的骨位.標準的外形為模具工業的發展所需要, 因為它便宜, 且易於採購. 如果有仍何可能我們寧可用標準件, 這對於大現模生產尤其顯得重要.※擠出材料熱熔物的選擇非常重要, 特別是對一種新技術, 新產品. 高強度的苯乙烯是一種最易擠出的塑膠, 纖維與丙烯居其次, 最難擠出的材料為尼龍. 軟塑料不如硬塑料易於擠出到一個細小公差, 快速冷卻會產生內應力並導致裂紋生成. 透明材料(如: PE; 尼龍; VC和PP)常在冷水中冷卻.通過不平衡壓模ABS和PS較PE, PP料易擠出成型. 後者比前者具有更低的熔解強度和更易改變的條件(測試條件易控制).如果採用“雙料擠塑”的材料不同, (除外)那它們之間的結合可能是不完整的. 完全不同的材料連接在一起要通過凹槽. 燕尾槽或機械連接. 當要對不同的塑料作雙料擠塑時一定要考慮材料間的相容性.例如: 增型擠塑乙烯基就與PS不相容.※材料的特點:1.ABS--- 硬性好, 易出模可調任何顏色. 可塑出任何複雜外形. 公差控制水平較高. 用於房屋, 門柱手柄等.2.CA--- 價廉, 通用硬性要求高或較高產品. 顏色可任何意調製. 耐氣候性差, 須涂上防護油, 汽油和大量清潔液體. 易清洗, 斷面較薄.3.CAB--- 與2 類同,但有更好的耐熱與氣候浸蝕性氣味難聞. 顏色可隨意配製, 用於標志倍存.4.CP--- 與3相似只是沒有怪味.5.EC--- 硬性彈性好, 易出模. 公差易控制. 低溫下穩定. 用於膠管刀刃及裝飾部件.6.EV A--- 柔性好, 可配製任何顏色. 外形單調. 用於低性能小五金. 印章, 墊圈等.7.尼龍--- 體輕, 很高的延伸性, 僅用於較單一的外形產品. 對公差要求不高. 凝固速度快. 很好的吸水性. 用於膠管, 路標, 摩擦溝道等.8.PC--- 最好的整體平衡性. 用於製造標準的外形. 公差控制容易. 較貴. 須特別處理, 但其吸水性,導熱性差. 用於燈罩, 消毒櫃等.9.PE--- (高密度)比低密度的PE更加堅硬, 公差難控制. 用於皮帶, 棍棒等.10.PE--- (低密度)較軟, 難以成型. 很好的非導電性,室溫下即能溶解. 用於膠管, 手柄, 緩沖器等.11.PP--- 很輕,標準公差控制. 不適用於複雜的外形. 可調多種顏色. 用於高性能絞鏈樞扭, 滑動導架等.12.PS--- 價廉, 適用於任何顏色, 易碎, 擠塑有限製. 用於燈罩等.13.PS--- 高彈性, 堅硬, 低價. 用於複雜外形. 標準公差控制. 顏色不限. 用於滑動門的導架等.14.PVC--- (柔軟) 通用於各種硬度. 標準的複雜外形. 標準的公差控制.用於各種顏色, 常用於進氣口, 密封圈.P11/1115.PVC--- (硬) 易出模, 可用於複雜外形, 優良的非導電性特性.公差控制容易. 有顏色限製. 常用於導電體的殼和蓋.16. PN--- 可用於各種硬性可調出, 用於各種顏色. 耐磨性好, 常用於傳送帶.17. VD--與15相似. 其非導電特性比PVC(硬)更加好. 複雜的外形, 優良的公差控制特性. 可擠塑出任何顏色. 用於製做熱水管, 高溫涂藥器等.PART 5一.影響尺寸的因素:盡管模塑零件能夠保證這種變異的緊配合公差, 但是對可獲得一定精度的金屬零件之尺寸卻不能保證原因有以下幾種:1.材料收縮力, 包括材料收縮過程中的均勻和不確定性.2.塑料有高的熱膨脹系數, 因此, 如果公差定得過大或過小, 設計者就應定出溫度並采取測量措施.3.盡管有對壓力, 溫度, 時間設定作自動調節的設備, 但這些因素在從一次注塑到另一次注塑間都會有一些變化, 這些變化的結果導致模塑零件輕微的尺寸變化.4.塑料零件通常較金屬零件有較大的柔軟性.由於柔軟因素的存在使得塑膠零件的緊配合無多大必要. 裝配時, 如果有必要去確保一個好配合常可通過零件輕微的變形達到. 如有必要, 明智的設計者可利用設計塑膠零件的击台和击緣去確保與相配零件表面的對稱.與其它過程相比, 緊配合會大大的增加注塑模零件的成本, 精密(公差)模具比粗製(公差) 模具的成本更高, 正如當零額外的緊配合時就會導致加工成本的增加, 例如, 須為壓力, 溫度和循環時間增加相關過程控制, 因而也許會增加循環時間或需要膠件出模後的熱套裝置, 廢品率也更高.不同的塑料材料有不同的公差特性, 低收縮率材料能以相應公差被恆定的注塑, 玻璃或礦物填充材料的注塑比非填充材料更精確. 更多模腔數的使用導致降低所注塑零件控制尺寸的精確. 根據以往經驗, 對每個模腔在第一次啤塑之後的尺寸允差都應增加5%, 例台, 一單模腔在某一尺寸具有±0.1mm的允差;在模腔長為10應有±0.15mm (0.006in) 的允差(公差增加10x5percent=50%).表 6.2.4(略)及6.2.5(略)為不同塑料材料的尺寸公差的建儀值, 這些表格數據, 是由塑膠工業行業提供數據所歸納出的. 代表了以往和現在塑膠模工業的發展成果, 個別模廠的合同形式和協議所規定的也許有變化.。
塑件设计指南

目录第一章塑件设计的一般程序和原则 (1)1.1 塑件设计的一般程序 (1)1.2 塑件设计的一般原则 (1)第二章塑件的收缩 (1)第三章拔模斜度 (4)3.1拔模斜度确定要点 (4)3.2 制品拔模斜度设计 (5)第四章制品壁厚 (7)4.1制品壁厚的作用 (7)4.2 制品壁厚的设计 (7)第五章加强筋(含凸台、角撑) (12)5.1 加强筋的作用 (12)5.2 加强筋的形状及尺寸 (12)第六章支承面 (17)第七章圆角 (18)第八章孔 (19)8.1 制品孔的形式及成型方法 (19)8.2 孔的模塑成型 (20)8.3 孔的设计要点 (23)第九章侧面凸凹和侧孔 (26)9.1 制品的侧凸凹 (26)9.2 侧凸凹的设计与成型方法 (27)第十章螺纹 (31)10.1 塑件螺纹的类型与选用(图2—54) (31)10.2塑件螺纹的模塑成型方法 (32)10.3 塑件螺纹设计要点 (32)第十一章塑件中的嵌件 (35)11.1 嵌件的结构形式 (36)11.2 嵌件在塑件中的固定 (38)11.3 嵌件在模具中的安放与定位 (40)11.4 嵌件周围塑料的裂纹和联接强度 (42)11.5 装配式嵌件(制品模塑后再装入嵌件) (43)11.6 塑料嵌件(嵌件的外插注射模塑) (44)第十二章塑件的凸凹纹(滚花) (45)第十三章标记、符号 (47)第十四章制品的尺寸精度 (47)14.1 尺寸精度的组成及影响因素 (47)14.2 塑件尺寸公差 (49)附录一:塑料的基本概念及其常用工程塑料的性能特点 (52)附录二:塑料的成型工艺 (55)塑件设计指南塑件的结构设计又称塑件的功能特性设计或塑件的工艺性。
第一章 塑件设计的一般程序和原则1.1 塑件设计的一般程序1. 详细了解塑件的功能、环境条件和载荷条件2. 选定塑件品种3. 制定初步设计方案,绘制制品草图(形状、尺寸、壁厚、加强筋、孔的位置等)4. 样品制造、进行模拟试验或实际使用条件的试验5. 制品设计、绘制正规制品图纸6. 编制文件,包括塑件设计说明书和技术条件等。
塑料设计基础知识点

塑料设计基础知识点塑料设计是当今工业中广泛应用的一门技术与艺术,它涵盖了塑料材料的特性、加工工艺、模具设计以及产品设计等多个方面。
本文将介绍一些塑料设计的基础知识点,帮助读者更好地理解和应用塑料设计。
一、塑料材料的特性1. 物理特性:塑料材料通常具有较低的密度、良好的延展性和可塑性,还具有较好的电绝缘性和耐水性。
2. 化学特性:不同种类的塑料材料对溶剂和化学品的抵抗能力各不相同,需要根据实际使用环境来选择合适的材料。
3. 热学特性:塑料材料的热膨胀性较大,熔化温度和热变形温度也不同,需要在设计时考虑其热学特性以防止变形。
4. 机械特性:塑料材料的力学性能如强度、刚度、韧性等都具有明显的差异,需要根据产品的具体要求选择合适的材料。
二、塑料加工工艺1. 注塑成型:注塑成型是最常用的塑料加工工艺,通过将熔化的塑料注入模具腔中,冷却后得到所需形状的产品。
2. 吹塑成型:吹塑成型主要用于生产中空的塑料制品,如瓶子、桶,通过将加热的塑料挤出并在模具腔内吹气,使其与模具表面接触形成产品的空腔。
3. 挤出成型:挤出成型适用于生产条状、管状或异形截面的产品,通过将塑料加热熔化后挤出模具,冷却后得到产品。
4. 压塑成型:压塑成型适用于制作薄壁产品或具有较大面积的产品,通过将塑料加热软化后压入模具中,冷却后得到产品。
三、模具设计1. 模具材料:模具材料应选择具有良好的耐磨性和导热性能的材料,例如合金工具钢或精密合金等。
2. 模具结构:模具结构应合理设计,包括模腔、模芯、顶出机构等,以确保产品的几何形状和尺寸的精度。
3. 模具寿命:模具寿命受到多种因素的影响,如材料选择、加工工艺和使用环境等,需要在设计时考虑这些因素以延长模具的使用寿命。
四、产品设计1. 结构设计:塑料制品的结构设计应符合力学原理和工艺要求,以确保产品的强度和稳定性。
2. 外观设计:塑料制品的外观设计应考虑产品的使用功能和美观性,同时要兼顾材料的可塑性和成型工艺的要求。
塑胶件结构设计手册(精华板)

1.0 选择材料的考虑因素任何一件工业产品在设计的早期过程中,一定牵涉考虑选择成形物料。
因为在产品生产时、装配时、和完成的时间,物料有着相互影响的关系。
除此之外,品质检定水平、市场销售情况和价格的厘定等也是需要考虑之列.所以这是无法使用概括全面的考虑因素而定出一种系统性处理方法来决定所选择的材料和生产过程是为最理想。
1。
1 不同材料的特性1。
ABS•用途:玩具、机壳、日常用品•特性:坚硬、不易碎、可涂胶水,但损坏时可能有利边出现设计上的应用:多数应用于玩具外壳或不用受力的零件。
2.PP•用途:玩具、日常用品、包装胶袋、瓶子•特性:有弹性、韧度强、延伸性大、但不可涂胶水。
•设计上的应用:多数应用于一些因要接受drop test(跌落测试)而拆件的地方.3.PVC•用途:软喉管、硬喉管、软板、硬板、电线、玩具•特性:柔软、坚韧而有弹性。
•设计上的应用:多数用于玩具figure(人物),或一些需要避震或吸震的地方。
4.POM•用途:机械零件、齿轮、摃杆、家电外壳•特性:耐磨、坚硬但脆弱,损坏时容易有利边出现(Fig. 1。
1。
6)。
•设计上的应用:多数用于胶齿轮、滑轮、一些需要传动,承受大扭力或应力的地方。
5。
Nylon (尼龙)•用途:齿轮、滑轮•特性:坚韧、吸水、但当水份完全挥发后会变得脆弱。
•设计上的应用:因为精准度比较难控制,所以大多用于一些模数较大的齿轮。
6。
Kraton (克拉通)用途: 摩打垫特性:柔软,有弹性,韧度高,延伸性强。
设计上的应用:多数作为摩打垫,吸收摩打震动,减低噪音。
Table 1.1.1 一般胶料的特性与用途2.0 壁厚 [Wall Thickness]壁厚的大小取决于产品需要承受的外力、是否作为其它零件的支撑、承接柱位的数量、伸出部份的多少以及选用的塑料材料而定。
一般的热塑性塑料的壁厚设计应以4mm为限.从经济角度来看,过厚的产品设计不但增加物料成本,延长生产周期(冷却时间),增加生产成本。
塑料产品设计指南
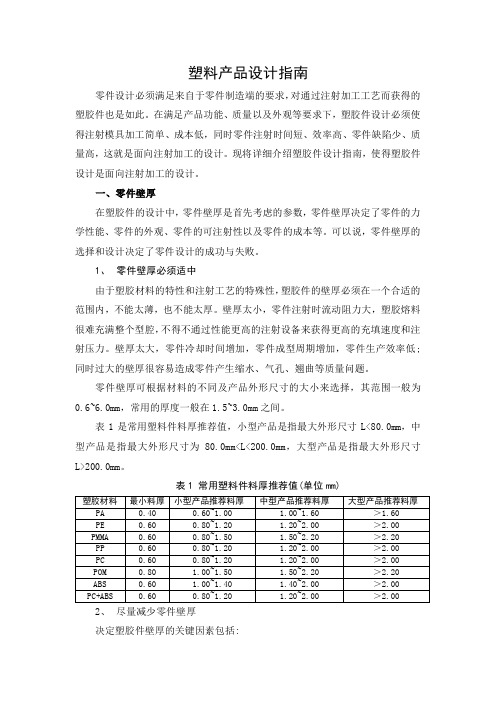
塑料产品设计指南零件设计必须满足来自于零件制造端的要求,对通过注射加工工艺而获得的塑胶件也是如此。
在满足产品功能、质量以及外观等要求下,塑胶件设计必须使得注射模具加工简单、成本低,同时零件注射时间短、效率高、零件缺陷少、质量高,这就是面向注射加工的设计。
现将详细介绍塑胶件设计指南,使得塑胶件设计是面向注射加工的设计。
一、零件壁厚在塑胶件的设计中,零件壁厚是首先考虑的参数,零件壁厚决定了零件的力学性能、零件的外观、零件的可注射性以及零件的成本等。
可以说,零件壁厚的选择和设计决定了零件设计的成功与失败。
1、零件壁厚必须适中由于塑胶材料的特性和注射工艺的特殊性,塑胶件的壁厚必须在一个合适的范围内,不能太薄,也不能太厚。
壁厚太小,零件注射时流动阻力大,塑胶熔料很难充满整个型腔,不得不通过性能更高的注射设备来获得更高的充填速度和注射压力。
壁厚太大,零件冷却时间增加,零件成型周期增加,零件生产效率低;同时过大的壁厚很容易造成零件产生缩水、气孔、翘曲等质量问题。
零件壁厚可根据材料的不同及产品外形尺寸的大小来选择,其范围一般为0.6~6.0mm,常用的厚度一般在1.5~3.0mm之间。
表1是常用塑料件料厚推荐值,小型产品是指最大外形尺寸L<80.0mm,中型产品是指最大外形尺寸为80.0mm<L<200.0mm,大型产品是指最大外形尺寸L>200.0mm。
表1 常用塑料件料厚推荐值(单位mm)2、尽量减少零件壁厚决定塑胶件壁厚的关键因素包括:1)零件的结构强度是否足够。
一般来说,壁厚越大,零件强度越好。
但零件壁厚超过一定范围时,由于缩水和气孔等质量问题的产生,增加零件壁厚反而会降低零件强度。
2)零件成型时能否抵抗脱模力。
零件太薄,容易因顶出而变形。
3)能否抵抗装配时的紧固力。
4)有金属埋入件时,埋入件周围强度是否足够。
一般金属埋入件与周围塑胶材料收缩不均匀,容易产生应力集中,强度低。
5)零件能否均匀分散所承受的冲击力。
塑胶模具设计指引
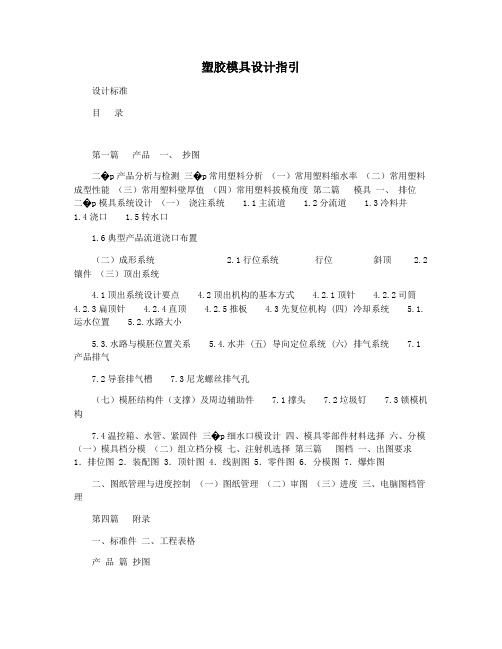
塑胶模具设计指引设计标准目录第一篇产品一、抄图二�p产品分析与检测三�p常用塑料分析(一)常用塑料缩水率(二)常用塑料成型性能(三)常用塑料壁厚值(四)常用塑料拔模角度第二篇模具一、排位二�p模具系统设计(一)浇注系统 1.1主流道 1.2分流道 1.3冷料井1.4浇口 1.5转水口1.6典型产品流道浇口布置(二)成形系统 2.1行位系统行位斜顶 2.2镶件(三)顶出系统4.1顶出系统设计要点 4.2顶出机构的基本方式 4.2.1顶针 4.2.2司筒4.2.3扁顶针 4.2.4直顶 4.2.5推板 4.3先复位机构 (四) 冷却系统5.1.运水位置 5.2.水路大小5.3.水路与模胚位置关系 5.4.水井 (五) 导向定位系统 (六) 排气系统 7.1产品排气7.2导套排气槽 7.3尼龙螺丝排气孔(七)模胚结构件(支撑)及周边辅助件 7.1撑头 7.2垃圾钉 7.3锁模机构7.4温控箱、水管、紧固件三�p细水口模设计四、模具零部件材料选择六、分模(一)模具档分模(二)组立档分模七、注射机选择第三篇图档一、出图要求1.排位图 2.装配图 3.顶针图 4.线割图 5.零件图 6.分模图 7.爆炸图二、图纸管理与进度控制(一)图纸管理(二)审图(三)进度三、电脑图档管理第四篇附录一、标准件二、工程表格产品篇抄图一.抄图前,先要看懂,看透产品线图,然后班顺思路,特别是外形面的画法。
抄好产品图要转为2D线图与设计部提供的平面线图套。
要保证主要的视图和边界线完全重合一致。
若有不重合、不一致的情况,首先分析是2D线图本身表达有问题,还是抄图时造成的。
若为2D线图表达问题则应及时标明,并与设计部沟通、反映;若为抄图问题,及时修改。
二.一个产品通常要多次转图与标题栏对上几次逐步确认(看版本),避免最后的问题堆积。
三.在抄图的整个过程中,最为重要的是基体外形面的控制和核对。
四.抄好的UG尽可能保证可以再生,以实现UG的参数设计功能。
塑料制品设计师指南

塑料制品设计师指南基本资料塑料制品设计师指南作者:唐志玉出版社:出版年: 1993年09月第1版页数:定价: 21.1装帧:ISAN:内容简介本书包括聚合物结构特征与性能、填料对塑料性能的影响、蠕变与断裂、结构件设计等20章。
书目:举报失效目录超星目录第一章总论§1.1塑料特性与用途§1.2设计内容§1.3设计程序1.3.1设计思想1.3.2设计步骤第二章聚合物结构特征与性能§21 塑料的分类2.1.1接塑料的物理化学性能分2.1.2按塑料用途分2.1.3按塑料成型方法分2.1.4按塑料半成品和制品分§2.2高聚物的结构与性能2.2.1 高聚物分子运动特性2.2.2高聚物的力学状态和热转变2.2.3高聚物的玻璃化转变2.2.4聚合物的结晶2.2.5高聚物的取向2.2.6高聚物的静电效应参考文献第三章塑料的应力-应变行为§3.1模量、柔量与泊松比§3.2虎克弹簧与牛顿粘壶§3.3 Maxwell和Voigt模型3.3.1 Maxwell模型3.3.2 Maxwell模型在动态力场中的应用 3.3.3 Maxwell-Weichert模型3.3.4 Voigt模型3.3.5 Voigt模型在动态力场中的应用 3.3.6四元件组合模型3.3.7 Voigt-Kelvin模型§3.4应力-应变-时间的三维图§3.5 Bo1tzman叠加原理第四章填料对塑料性能的影响§4.1填料定义与分类§4.2填料品种及属性§4.3填料聚集状态及性能的影响 4.3.1 填料几何形状4.3.2填料粒度分布4.3.3填料的表面积4.3.4填料的堆砌系数4.3.5化学组成对性能的影响§4.4填料的表面处理§4.5填料的改性作用4.5.1模量和抗张强度4.5.2抗压强度4.5.3蠕变及其伸长4.5.4改善热性能4.5.5改进电性能§4.6填料的增强作用4.6.1玻璃纤维增强塑料4.6.2增强机理及纤维临界长度 4.6.3影响增强性的因素§4.7填料对塑料加工性能的影响 4.7.1粘度变化4.7.2流变行为的改变4.7.3填料的选择第五章蠕变与断裂§5.1蠕变行为5.1.1蠕变数据5.1.2温度对应变的影响 5.1.3其它应变形式5.1.4应变的回复5.1.5间歇应力下的蠕变§5.2断裂现象5.2.1脆性断裂5.2.2韧性断裂5.2.3温度的影响§5.3断裂与蠕变参考文献第六章结构件设计§6.1设计过程及特点6.1.1工作要求与失效形式 6.1.2 材料选择6.1.3计算过程§6.2构件设计实例6.2.1 柱体设计6.2.2 叶片轮设计6.2.3悬臂梁设计6.2.4圆管计算§6 3应变回复的计算第七章刚性设计§7.1 夹芯板7.1.1夹芯板的刚性分析7.1.2技术性能指标7.1.3材料选用7.1.4制造与固定7.1.5 设计实例§7.2波纹板7.2.1波纹板特征7.2.2屋顶设计§7.3塑料曲面结构参考文献第八章动态载荷分析§8.1交变载荷与疲劳强度 8.1.1 交变应力8.1.2疲劳试验8.1.3疲劳强度§8.2滞后热效应8.2.1滞后热现象8.2.2防止滞后热软化的方法 8.2.3滞后热平衡分析§8.3减振特性8.3.1塑料的阻尼特性8.3.2减振计算8.3.3阻尼对应力和疲劳的影响§8 4冲击载荷8.4.1 冲击强度8.4.2半波正弦脉冲载荷8.4.3抗冲保护计算参考文献第九章成型方法对塑件设计的影响§9.1常用的成型方法9.1.1熔体成型9.1.2固相成型§9.2模具的限制9.2.1避免侧孔、侧凹9.2.2脱模斜度9.2.3 分型线9.2.4 浇口痕9.2.5制品公差9.2.6壁厚9.2.7 筋与凸台9.2.8圆弧与倒角9.2.9表面处理9.2.10孔与嵌件§9.3成型方法的限制9.3.1挤出成型9.3.2 吹塑成型9.3.3反应注射成型9.3.4热成型9.3.5 浇注成型参考文献第十章成型过程对制品性能的影响§10.1型腔模中所出现的问题 10.1.1充模问题10.1.2缩孔与收缩应力10.1.3熔体流动受阻10.1.4各向异性10.1.5浇口区取向10.1.6熔接缝10.1.7碳化与焦斑10.1.8制品内应力10.1.9表面缺陷10.1.10收缩率波动§10.2挤出成型中所遇到的问题 10.2.1取向与内应力10.2.2记忆效应10.2.3截面变形10.2.4 尺寸变化§10.3热成型中存在的问题10.3.1取向与冻结应力10.3.2截面厚薄不均10.3.3解模塑趋向10.3.4双重削弱作用§10.4吹塑成型中的问题§10.5浇铸成型给制品带来的问题参考文献第十一章环境因素的危害§11.1塑料制品的老化现象§11.2热环境老化11.2.1 热裂解11.2.2热氧化§11.3光氧环境老化11.3.1光氧老化机理11.3.2防止光老化方法§11.4化学介质老化11.4.1耐腐蚀性与评定标准11.4.2不同塑料的耐腐蚀性能11.4.3防腐塑料选用特性§11.5其它老化形式与环境试验 11.5.1臭氧环境老化11.5.2水解老化11.5.3生物老化11.5.4电晕老化11.5.5环境应力开裂11.5.6低温脆裂11.5.7环境试验§11.6常用塑料光热老化特性11.6.1聚烯烃塑料11.6.2卤代烯烃塑料11.6.3 ABS塑料和丙烯酸酯类塑料 11.6.4聚醚塑料11.6.5聚酰胺塑料11.6.6聚酯、聚砜塑料11.6.7热固性塑料参考文献第十二章塑料制品设计过程§12.1设计准备12.1.1设计思想12.1.2调查研究12.1.3设想方案§12.2设计步骤12.2.1功能设计12.2.2材料选择12.2.3结构设计12.2.4尺寸设计12.2.5性能估算12.2.6模型、制样及绘图12.2.7试生产及定型§12.3设计师的责任12.3.1不断更新产品结构12.3.2质量与价格兼顾参考文献第十三章CAD与塑件设计§13.1 CAD概述13.1.1CAD的概念13.1.2 CAD系统的规模13.1.3 CAD技术的核心13.1.4 CAD系统的配置13.1.5 CAD的意义和作用§13.2 CAD在塑件设计中的应用 13.2.1塑件设计的一般过程13.2.2塑件设计目录的编制13.2.3塑件设计方法诸要素§13.3注塑流动的计算机模拟 13.3.1注塑流动模拟的基本原理 13.3.2注塑流动的有限元分析 13.3.3 Moldflow软件的使用参考文献第十四章联接件设计§14.1卡夹联接14.1.1联接原理与分类14.1.2设计实例§14.2铰链联接§14.3常用联接实例§14.4压力装配联接参考文献第十五章轴承和齿轮设计§15.1塑料的摩擦和磨损性能 15.1.1摩擦15.1.2磨损§15.2轴承设计15.2.1轴承材料15.2.2轴承类型15.2.3设计考虑15.2.4橡胶轴承§15.3齿轮设计15.3.1齿轮模塑成型15.3.2齿轮几何参数计算15.3.3齿轮失效形式15.3.4齿轮弯曲疲劳强度计算 15.3.5齿面接触疲劳强度计算 15.3.6材料选择参考文献第十六章电工塑件设计§16.1塑料的电学性能16.1.1塑料的绝缘性16.1.2塑料的导电性16.1.3塑料的高电压性能§16.2接插件设计16.2.1 概述16.2.2接插件的技术要求1 6.2.3接插件用塑料材料§16.3印刷线路板16.3.1工艺过程16.3.2技术要求§16.4线缆包覆层设计16.4.1概述16.4.2 电缆用塑料材料16.4.3电缆绝缘层计算16.4.4 电缆料使用要求参考文献第十七章光学塑件设计§17.1 塑料的光学性质17.1.1透光性和透明性17.1.2折射和反射17.1.3光弹性17.1.4持久性和稳定性§17.2光管效应及其应用§17.3透镜和菲涅尔透镜§17.4光学领域其它应用17.4.1 镜片制造17.4.2光栅复制17.4.3其它用途§17.5光学塑料材料参考文献第十八章泡沫塑料及其制品设计§18.1泡沫塑料分类18.1.1按泡孔结构分18.1.2按软硬程度分18.1.3按密度大小分§18.2泡沫塑料结构18.2.1 泡孔形状18.2.2泡孔尺寸18.2.3开孔系数18.2.4 泡沫密度§18.3泡沫塑料性能18.3.1力学性能18.3.2热学性能18.3.3尺寸稳定性18.3.4 电学性能18.3.5 漂浮性能18.3.6吸水性和透湿性18.3.7声学性能18.3.8缓冲减震性能18.3.9阻燃性能18.3.10化学性能18.3.11生物性能§18.4结构泡沫18.4.1结构泡沫的结构与特性 18.4.2结构泡沫成型方法18.4.3增强结构泡沫18.4.4组合泡沫§18.5耐高温泡沫18.5.1有机硅泡沫18.5.2聚异氰脲酸酯泡沫18.5.3聚苯并咪唑泡沫18.5.4聚酰亚胺泡沫§18.6泡沫塑料应用18.6.1包装用制品设计18.6.2绝热和建筑用制品设计18.6.3交通运输用制品设计18.6.4海运和海洋事业用制品18.6.5家具和日常生活用制品18.6.6医疗技术材料18.6.7军事和航空航天技术应用参考文献第十九章表面装饰与着色§19.1表面绘画技术19.1.1模塑花纹技术19.1.2热固性塑料制品的绘画技术 19.1.3热塑性塑料制品的绘画技术 19.1.4发泡装饰技术19.1.5其它花纹技术§19.2表面涂饰技术19.2.1涂饰的功能19.2.2涂料的种类19.2.3涂料的选用19.2.4涂饰预处理19.2.5涂饰工艺19.2.6涂饰对制品的设计要求§19.3表面金属化19.3.1金属喷镀19.3.2真空镀膜19.3.3化学镀金与电镀19.3.4电镀塑料制品的设计要求§19.4表面印刷技术19.4.1表面烫印19.4.2丝网印刷(绢印)19.4.3其它印刷技术§19.5塑料着色19.5.1着色剂简介19.5.2着色剂选择19.5.3塑料着色技术参考文献第二十章塑料性能与鉴别§20.1性能规范与标准20.1.1物理性能20.1.2热学性能20.1.3力学性能20.1.4 电学性能20.1.5化学性能20.1.6老化性能§20.2塑料鉴别20.2.1燃烧鉴别法20.2.2溶解性试验法20.2.3元素检定法20.2.4最后鉴定法20.2.5现代鉴定法§20.3聚合物分子结构 20.3.1聚烯烃树脂20.3.2 乙烯基树脂20.3.3丙烯酸树脂20.3.4聚酰胺树脂20.3.5聚醚树脂20.3.6含氟树脂30.3.7芳杂环树脂20.3.8纤维素塑料20.3.9聚醚酯树脂20.3.10其它热固性树脂参考文献1。
- 1、下载文档前请自行甄别文档内容的完整性,平台不提供额外的编辑、内容补充、找答案等附加服务。
- 2、"仅部分预览"的文档,不可在线预览部分如存在完整性等问题,可反馈申请退款(可完整预览的文档不适用该条件!)。
- 3、如文档侵犯您的权益,请联系客服反馈,我们会尽快为您处理(人工客服工作时间:9:00-18:30)。
Gate
Engineering Polymers / DuPont (Korea) Inc.
16
Gate Location & Shrinkage
Flow Steps
Engineering Polymers / DuPont (Korea) Inc.
17
Shrinkage & Warpage Glass reinforced materials
Gate
Engineering Polymers / DuPont (Korea) Inc.
18
Shrinkage & Warpage
Effect of Machine Settings on Shrinkage
Engineering Polymers / DuPont (Korea) Inc.
7
Gate Location & Shrinkage
Mineral Reinforced
Flow Direction
Gate
Transverse Direction
Mineral Resists Shrinkage More Uniformly in All Directions
Engineering Polymers / DuPont (Korea) Inc.
6
Gate Location & Shrinkage
Glass Reinforced
Flow Direction
Gate
Transverse Direction
Glass Fiber Resists Shrinkage in Direction of Alignment/Flow
Engineering Polymers / DuPont (Korea) Inc.
S in flow
S Thick S
Engineering Polymers / DuPont (Korea) Inc.
14
Shrinkage & Warpage Unreinforced materials
Deformation trend
b
Байду номын сангаас
Shrinkage [%]
a
Transverse
In Flow
Gate
Flow Tranverse
4
Gate Location & Shrinkage
Flow Direction
Gate
Transverse Direction
Material Flow Affects Orientation
Engineering Polymers / DuPont (Korea) Inc.
Engineering Polymers / DuPont (Korea) Inc.
12
Shrinkage & Warpage Case on a ‘plate + rib’ profile
b
a
Gate L
h w
Gate
Flow angle Isochrones
Engineering Polymers / DuPont (Korea) Inc.
1 1.5 2
3
4
Wall thickness [mm]
Shrinkage (S)
S Thin
S in flow
S Thick S
Engineering Polymers / DuPont (Korea) Inc.
15
Gate Location & Shrinkage
Bad Gate Location
Engineering Polymers / DuPont (Korea) Inc.
3
Gate Location & Strength
300 250 200
MPa
150 100
50 0
Tension
Compression
Tensile Strength ZYTEL 70G33 23 C, DAM
Engineering Polymers / DuPont (Korea) Inc.
8
Shrinkage & Warpage
Shrinkage Increases with Wall Thickness
Higher Shrinkage
Lower Shrinkage
Engineering Polymers / DuPont (Korea) Inc.
9
Shrinkage & Warpage Uneven Shrinkage
13
Shrinkage & Warpage
Glass reinforced materials
Deformation trend
b
Shrinkage [%]
a
Transverse to flow
In flow
1 1.5 2
3
4
Wall thickness [mm]
Shrinkage (S)
S Thin
Design Concept
CAE
CAD
Engineering Polymers / DuPont (Korea) Inc.
2
Typical Wall Thickness
For Engineering Polymers
millimetric scale
3 0 1 2 4 5 6 7
General applications Special applications
Engineering Polymers / DuPont (Korea) Inc.
10
Shrinkage & Warpage
Bad Flatness
Engineering Polymers / DuPont (Korea) Inc.
11
Shrinkage & Warpage
Good Flatness
5
Gate Location & Shrinkage
Unreinforced
Flow Direction
Gate
Transverse Direction
Higher Shrinkage in Direction of Molecular Orientation/Flow
Engineering Polymers / DuPont (Korea) Inc.
Design Guidelines
Version 1.0
Nov . 24 . 2004
Technical Center / Engineering Polymers
DuPont (Korea) Inc.
Engineering Polymers / DuPont (Korea) Inc.
1
Design Flow