300mm半导体工厂的AMHS系统合集
Interbay物料运输系统实时调度方法

夏蓓鑫等:Interbay物料运输系统实时调度方法
65
Interbay物料运输系统实时调度方法
夏蓓鑫 高 雅 曹建斌 陈甜甜
(上海大学管理学院,上海 200072;上海大学机电工程与自动化学院,上海 200444)
摘 要:自动物料运输系统(AMHS)的运行效率对晶圆制造系统有影响。本文提出了一种有效的多目标动态调度方法。首先,建立多目标成 本模型,并提出了一种基于模糊理论的改进方法,动态调整成本模型中的权值。采用匈牙利算法对模型进行求解。仿真实验结果表明,与其他 调度方法相比,该方法具有更好的综合性能。 关键词:半导体制造系统;AMHS;模糊理论 中图分类号:O313 文献标识码:A 国家标准学科分类代码:4604030 DOI:10.15988/j.cnki.1004-6941.2019.5.018
Real-timeSchedulingMethodforInterbayMaterialHandlingSystem
搬运机器人

简单介绍一下半导体工厂AMHS系统的搬运机器人fosb是wafer做好以后送给客户时用的盒子(因为AMD 采用了“前开口运装箱”(FOSB),这样就保证了在大多数加工制作过程中,晶片都是处于密封)。
foup是12寸厂内部生产线上的装lot的盒子(在台湾8吋SMIF晶圆盒(POD)的需求量约有新台币3~5亿元的市场,未来12吋SMIF晶圆盒(FOUP) 的需求量预估为每年6万个)。
在超净环境中,晶圆被密封在称作FOUP(front-opening unified pods)的容器中。
带有彩色编码的容器代表晶圆将进入不同的制程。
每个FOUP有一个序列号以识别晶圆,写得不好,请大家多多指教。
OHS(Over Head Shuttle )可以在安装在天井下轨道上高速移动的自动搬运装置。
一般是用于成膜、洗浄等各个保管设备间FOUP搬运。
OHT(Overhead Hoist Transfer )是安装在天井下轨道下高速移动的自动搬运小车。
由升降装置马达驱动BELT,使GRIPPER自动抓取设置在port的foup。
这是300mm晶圆厂运用最广泛的搬运工具。
GRIPPER有不同的类型可以搬运不同类型的foup。
从第一代10几年前只能低速走行单线轨道,移载设置于其正下方port的foup,到第二代可以高速走行在分歧轨道,第三代不仅可以走行在分歧轨道,还可以左右移载设置在STS,UTS上的FOUP,再到第四代450mm搬运小车,更新速度可谓非常之快。
中国国内半导体厂商使用第一代,第二代自动搬运小车,目前国内还没有使用第三代自动搬运小车的客户。
AGV (Automated Guided Vehicle)车上安装了多关节手臂机器人,用于搬运保管设备和制造设备之间的foup。
本搬运小车由于安装了大容量的电池,可以自动走行在工厂的地板上,并按照程序设置,可以走行比较复杂的路径。
台湾,韩国有半导体厂商很多使用这种小车的案例。
ASYST推出AMHS新方案增加晶圆厂的生产力

ASYST推出AMHS新方案增加晶圆厂的生产力具有竞争力的晶圆厂必须一方面做到高设备利用率,一方面又使处于制程中的晶圆量维持在最低,同时还必须让晶圆生产周期压缩到最短。
这两项要求可能互相抵触。
而解决的关键是不要让简称为「AMHS」的「自动物料处理系统」成为晶圆处理过程中的瓶颈,限制了晶圆厂的表现。
为半导体及平面显示器制造厂提供整合式自动化解决方案领导供货商ASYST 今天宣布推出Agile Automation,这是一种在半导体晶圆厂新的自动化物料处理(Automated Material Handling)方式。
Agile Automation 是开创业界先例的解决方案. 它大幅增加晶圆厂的生产力,通过模块化增强现有AMHS 制度。
Agile Automation 具有并行加载和卸载几项工具的功能,同时大幅度减少对搭载置顶输送工具(Overhead Transport Vehicles, OHV)的依赖. 这样造成显著缩短且更可预测前开式芯片传送盒(FOUP)运输时间和巨幅地改善吞吐量和工具的使用.由于其灵活和模块化结构,Agile Automation 可简单地与标准工厂自动化系统整合,不论是在现有或新建的环境。
这有助于提高晶圆厂生产力的管理及低风险方法。
使用Agile Automation 方案,晶圆厂可以得到额外的节省,通过减少地面空间的需求,可能性较少工具和降低功率消耗。
Agile Automation 整合ASYST 先进的硬件,软件和服务的能力,及允许定制透过业界标准界面与晶圆厂环境整合的应用。
ASYST 整合若干新技术成为Agile Automation 解决方案的一部份.这包含为悬吊式搬运车系统(OHT)独立工具装载的DLT Lifting Loadport™. 这是ASYST 关键技术,这技术允许工具的自动装卸不受搬运车(vehicle)支配.其它新技术及产品包含: ASYSTS 新Satellite StockerTM,,它提供高效率的近工具的缓冲; 适用于高速,高通量材料处。
300mm半导体工厂的AMHS系统

300mm半导体工厂的AMHS系统在半导体制造技术高度发达的今天,300mm的半导体工厂已经成为全球半导体行业的主流。
由于300mm半导体生产线的巨额投入,人们不得不尽可能的挖掘300mm工厂的生产效率,以期得到更大的晶圆产出。
一个功能强大且性能稳定的AMHS系统在300mm工厂里扮演了一个非常重要的角色。
AMHS系统不仅可以有效的利用宝贵的洁净室的生产空间,并且还可以提高生产设备的利用率,缩短在制品WIP的Cycle Ti me,所以在很多的300mm的半导体工厂里,AMHS都被视为可以快速提升产能,增加生产效率的尖兵利器。
AMHS系统在300mm半导体工厂的应用特点ﻫ和200mm晶圆相比,更大的晶圆尺寸使得单批Lot的晶圆重量变得更大,仅凭在200mm工厂Intrabay内的人工搬运已经远远无法满足300mm工厂的生产要求。
因此,在300mm的半导体工厂里,生产方式的巨大变化也给AMHS系统提出了更高的要求。
搬送方式的巨大进化首先,是AMHS搬送方式从200mm工厂的SEMI Auto方式到300mm工厂FullAuto方式的转变。
如图1红色轨道所示:在200mm工厂所采用的Semi Auto生产方式中的Wafer搬送,只包括中央区域Interbay的AMHS搬送。
而Wafer到生产设备的部分需要人工搬送来完成。
而在300mm工厂里,由于wafer自身重量的增加,导致人工搬送异常困难,故由AMHS系统取而代之直接将wafer搬送到生产设备,如图1中的蓝色轨道,这即是FullAuto的作业方式。
这种方式极大减轻了生产一线操作人员的工作强度,同时又避免了因人为事故而造成的损失。
更为重要的是,在工厂产能迅速提升的过程中,可以满足大规模搬送量的AMHS系统的巨大优势可以完全呈现。
其次,是ToolTo Tool直接搬送的全厂性应用。
为了进一步的节省FOUP的搬送时间,300mm晶圆厂的AMHS系统必须支持Tool To Tool的直接搬送。
半导体制程高度的输送系统逻辑MCS
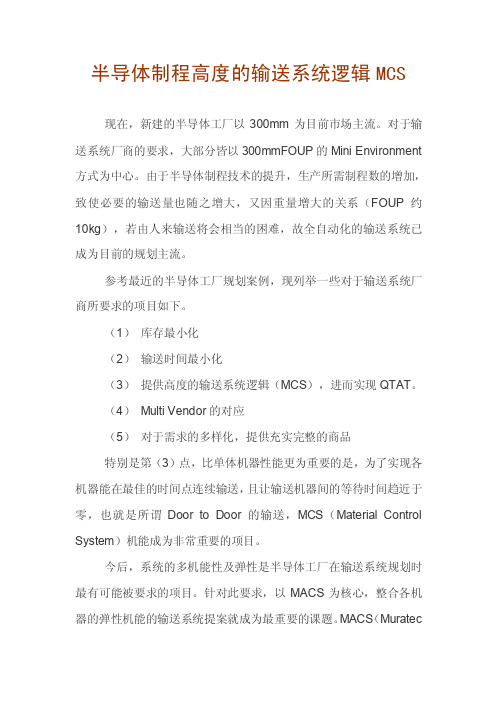
半导体制程高度的输送系统逻辑MCS现在,新建的半导体工厂以300mm为目前市场主流。
对于输送系统厂商的要求,大部分皆以300mmFOUP的Mini Environment 方式为中心。
由于半导体制程技术的提升,生产所需制程数的增加,致使必要的输送量也随之增大,又因重量增大的关系(FOUP约10kg),若由人来输送将会相当的困难,故全自动化的输送系统已成为目前的规划主流。
参考最近的半导体工厂规划案例,现列举一些对于输送系统厂商所要求的项目如下。
(1)库存最小化(2)输送时间最小化(3)提供高度的输送系统逻辑(MCS),进而实现QTAT。
(4)Multi Vendor的对应(5)对于需求的多样化,提供充实完整的商品特别是第(3)点,比单体机器性能更为重要的是,为了实现各机器能在最佳的时间点连续输送,且让输送机器间的等待时间趋近于零,也就是所谓Door to Door的输送,MCS(Material Control System)机能成为非常重要的项目。
今后,系统的多机能性及弹性是半导体工厂在输送系统规划时最有可能被要求的项目。
针对此要求,以MACS为核心,整合各机器的弹性机能的输送系统提案就成为最重要的课题。
MACS(MuratecControl System)是针对Clean输送的管理及控制用所开发的MCS。
现将系统的机能列举如下:•Local Level的输送控制及相关输送管理的控制•输送物管理情报及系统全体的追踪(Tracking)•HOST(如MES)与Local Level输送控制的中继界面•资料收集及对HOST与Operator的报告(GUI)输送最佳化(JIT Transport)•特急Lot(Hot Lot)输送管理Web使用(GUI)•远距离操作及维护•Cluster方式控制,系统无中断现象(Down Time最小化)Local对应容易,简单的Layout变更可能•Email方式资料讯息报告(警告,Alarm等)当然,为了实现整体性的输送系统,多种多样化的机器单体也是相当重要的要因。
dmps-300-c-dtp

| 800.237.2041
DMPS-300-C
DigitalMedia™ 演示系统 300
DMPS-300-C - 后视图
DigitalMedia 8G+™ 集成 DM 8G+ 输入和输出实现了极致的简洁性,为远程信 集成 DM 8G+ 输入和输出实现了极致的简洁性,为远程信 号源和显示设备提供了一个真正的单线接口。只需轻松地添 加最多两个 DM 8G+ 发送器就能在会议桌或展示台上连接 高清 AV 信号源或者计算机。连接两个 DM 8G+ 接收器即可 为两个单独的投影仪或平板显示器提供独立的信号路由和控 制。DM 8G+支持长达 330 英尺(100 米)的缆线,还可在 较大型的多房间或者房间组合系统中为中央 DigitalMedia 切 换器提供一个理想的接口。
专业音频数字信号处理器
DMPS-300-C 上的每一个模拟音频输出都自带数字信号处理 器,因此每个输出都能够通过优化向功放、编解码器、录音 器或辅助收听系统馈送。除了可实时调节的音量、低音、高 音和静音控制之外,每一个数字信号处理器还提供 10 波段 图形均衡、2 波段参数均衡和 80 ms 扬声器延迟调节。每路 输出都设置有硬件继电器静音功能,以防止上电"低频噪声 "。
> 支持灵活的音频信号混合以及 7 个单独输出的路由
> 支持所有输入的音频随视频或提取切换
> 支持 HDMI 音频信号提取和嵌入
> 提供 3 个立体声模拟输出,每路输出采用独立的数字 信号处理器
> 配有内置 40 W 功放,可针对 8 欧姆立体声或者 70/100 伏单声道工作选择
> 多通道 PCM、Dolby®和 DTS® 音频信号可路由至 HDMI 和 DM 8G+ 输出
mm半导体工厂的AMHS系统精编

m m半导体工厂的A M H S系统精编Document number:WTT-LKK-GBB-08921-EIGG-22986300mm半导体工厂的AMHS系统在半导体制造技术高度发达的今天,300mm的半导体工厂已经成为全球半导体行业的主流。
由于300mm半导体生产线的巨额投入,人们不得不尽可能的挖掘300mm工厂的生产效率,以期得到更大的晶圆产出。
一个功能强大且性能稳定的AMHS系统在300mm工厂里扮演了一个非常重要的角色。
AMHS 系统不仅可以有效的利用宝贵的洁净室的生产空间,并且还可以提高生产设备的利用率,缩短在制品WIP的Cycle Time,所以在很多的300mm的半导体工厂里,AMHS都被视为可以快速提升产能,增加生产效率的尖兵利器。
AMHS系统在300mm半导体工厂的应用特点和200mm晶圆相比,更大的晶圆尺寸使得单批Lot的晶圆重量变得更大,仅凭在200mm工厂Intrabay内的人工搬运已经远远无法满足300mm工厂的生产要求。
因此,在300mm的半导体工厂里,生产方式的巨大变化也给AMHS系统提出了更高的要求。
搬送方式的巨大进化首先,是AMHS搬送方式从200mm工厂的SEMI Auto方式到300mm工厂Full Auto方式的转变。
如图1红色轨道所示:在200mm工厂所采用的Semi Auto生产方式中的Wafer搬送,只包括中央区域Interbay的AMHS搬送。
而Wafer到生产设备的部分需要人工搬送来完成。
而在300mm工厂里,由于wafer自身重量的增加,导致人工搬送异常困难,故由AMHS系统取而代之直接将wafer搬送到生产设备,如图1中的蓝色轨道,这即是Full Auto的作业方式。
这种方式极大减轻了生产一线操作人员的工作强度,同时又避免了因人为事故而造成的损失。
更为重要的是,在工厂产能迅速提升的过程中,可以满足大规模搬送量的AMHS系统的巨大优势可以完全呈现。
大福(集团)公司 - Material handling and automation

世界知名运动品生产商的超大型物流网点专业商社存储特殊纸张的自动仓库大型食品批发商的物流中心第三方物流企业的自动分拣系统运输公司的物流中心韩国纸张文具仓储系统马来西亚机场行李输送系统中国总部东京总部滋贺事业所小牧事业所康泰克公司康泰克ems公司康泰克软件开发公司大福普拉司贸公司日新馆公司大福后勤服务公司大福制造技术公司菲律宾分公司大福中国有限公司大福中国物流设备有限公司大福中国自动化设备有限公司大福自动搬送设备苏州有限公司北京康泰克电子技术有限公司康泰克上海信息科技有限公司daifukuindiaprivatelimitedforgeproindiaprivatelimitedptdaifukuindonesiadaifukukoreaco
CAS300M12BM2
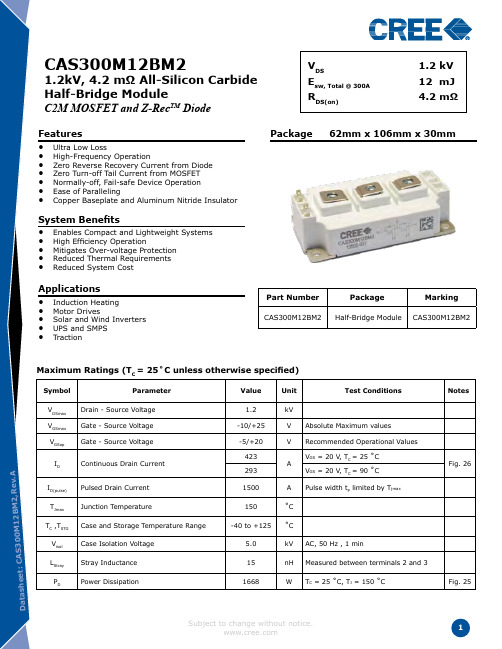
1.2kV, 4.2 mΩ All-Silicon Carbide Half-Bridge Module C2M MOSFET and Z-RecTM Diode
Features
Esw, Total @ 300A RDS(on)
VDS 1.2 kV
12 mJ 4.2 mΩ
Symbol VDSS VGS(th) IDSS IGSS RDS(on) Parameter Drain - Source Blocking Voltage Gate Threshold Voltage Zero Gate Voltage Drain Current Gate-Source Leakage Current On State Resistance Min. 1.2 1.8 2.5 600 1500 1 4.2 7.7 156 144 19.3 2.57 0.12 5.8 6.1 3.0 166 475 1025 76 68 168 43 1.6 2.0 3.2 2.0 ns ns ns ns V μC nC mJ mJ Ω VDD = 600 V, VGS = -5V/+20V ID = 300 A, RG(ext) = 2.5 Ω Load = 77 μH, TJ = 150 ˚C Note: IEC 60747-8-4 Definitions f = 200 kHz, VAC = 25 mV VDD= 800 V, VGS = -5V/+20V, ID= 300 A, Per JEDEC24 pg 27 VDD = 600V, VGS = -5/+20V, ID = 300 A, RG(ext) = 2.5 Ω, Timing relative to VDS Note: IEC 60747-8-4, pg 83 Inductive load IF = 300 A, VGS = 0 IF = 300 A, TJ = 150 ˚C, VGS = 0 Fig. 15 Fig. 22 nF VDS = 600 V, f = 200 kHz, VAC = 25 mV Fig. 16, 17 100 5.3 mΩ nA 2000 Typ. Max. Unit kV V μA Test Conditions VGS, = 0 V, ID = 2 mA VDS = 10 V, ID = 15 mA VDS = 1.2 kV, VGS = 0V VDS = 1.2 kV,VGS = 0V, TJ = 150 ˚C VGS = 20 V, VDS = 0V VGS = 20 V, IDS = 300 A VGS = 20 V, IDS = 300 A, TJ = 150 ˚C VDS = 20 V, IDS = 300 A VDS = 20 V, ID = 300 A, TJ = 150 ˚C Fig. 4, 5, 6 Fig. 8 Fig 7 Note
300MW机组DEH、MEH系统说明书(ia)

汽轮机数字电调控制系统说明书图号:71.K156.35-01上海汽轮机有限公司2004.6300MW机组DEH、MEH系统DEH控制系统的组成DEH控制系统由下列几部分组成:1.1 DEH系统DEH控制器采用上海FOXBORO公司的I/A系统硬件,其组成及硬件配置详见传递图及有关硬件资料。
1.2 EH系统EH系统包括控制阀门的油动机及其向油动机提供高压抗燃油的EH供油系统,除此之外还包括控制油动机紧急关闭的危急遮断控制块(电磁阀)和隔膜阀等部件。
EH系统的功能是接受DEH输出指令,控制汽轮机进汽阀门开度,改变进入汽轮机的蒸汽流量,满足汽轮机转速及负荷调节的要求。
同时通过危急遮断控制块(电磁阀)接受危急遮断系统输出指令,通过隔膜阀接受保安系统信号,控制油动机的紧急关闭。
因此EH系统实际上是DEH控制器及危急遮断系统或保安系统的执行机构。
控制阀门的油动机共有:主汽门油动机2个,调节汽阀油动机4个,再热调节汽阀油动机2个,再热主汽门油动机2个。
其中再热主汽门油动机为二位式结构,主汽门、调节汽阀及再热调节汽阀油动机为连续控制式结构。
1.3 保安系统包括机械超速危急遮断器,危急遮断油门,手拍危急遮断装置以及危急遮断复位装置等保安部套。
保安系统以隔膜阀为媒体将停机信号传递到EH系统,控制油动机的紧急关闭。
一、DEH系统功能汽轮机组采用由纯电调和液压伺服系统组成的数字式电液控制系统(DEH),提供了以下几种运行方式:操作员自动控制∙汽轮机自启动∙自同期运行∙ DCS远控运行∙手动控制通过这几种运行方式,可以实现汽轮机控制的基本功能如转速控制、功率控制、工程师站和操作员站的画面是主机控制接口,它是用来传递指令给汽轮机和获得运行所需的资料。
正常运行时可以使用键盘、鼠标直接对CRT画面上的按键进行操作,画面可以通过画面主菜单调用,也可在画面之间相互切换。
1 基本系统图像所有基本系统图像将机组运行的重要资料提供给运行人员。
半导体工厂的毒性

半导体工厂的毒性作者:xxsavage 发表时间:2007-3-21 14:56:29在半导体厂设备单位一般包括Diff、Thin-film、CMP、Etch、Photo,各单位的主要性质介绍如下:(一)Diff 扩散设备单位(包括Kaijo、TEL、DNS、Applied 等)主要用到有毒、无毒的Process Gas、water、高电压、高电流、废气,Clean机台则使用强酸碱化学品、而有废酸液的生成。
(二)Thin-film 薄膜设备单位(包括Applied、Novellus 等)主要用到有毒、无毒的Process Gas、water、高电压、高电流、高频、废气。
(三)CMP 研磨设备单位(包括Applied、EBARA等)主要用到强碱slurry 化学液、water、而有废碱液的生成。
(四)Etch 蚀刻设备单位(包括Lam、TEL、Applied、Kaijo、Mattson、Axcelis 机台)蚀刻机台的制程主要用到有毒特殊气体(Cl2,HBr,氟化物等)、无毒的气体(N2,Ar….)、water(冷却循环水,去离子水….)、高电压、高频、高电流在真空中反应,且在生产过程会有废气、辐射、废水的生成物。
(五)Photo 黄光设备单位(包括Nikon stepper\Scanner、TEL track及其它相关量测或检视机台)主要用到紫外线光源HMDS、thinner、光阻等有机溶剂,且有高电流、高电压、紫外线的应用,生产过程会有废气、废液的生成。
综合一般无尘室内常见的工业安全伤害,可分为化学性、物理性的伤害,而伤害也分布身体的各部位。
以下就将各单位较易发生及机台维修的安全事项说明如下:(一)Diff 扩散设备单位1、Furnace tools and CVD tools(1)机械方面:robot 的夹伤、撞伤、chamber 毒气外泄、plasma 辐射伤害、gatedoor 的夹伤,高温烫伤。
化学供应系统届介绍

300mm半导体代工厂的化学供应系统探讨ppy1014 发表于: 2007-12-10 17:21 来源: 半导体技术天地搜集的资料,大家一起学习,如有重复还请见谅。
300mm半导体代工厂的化学供应系统探讨张云秀,黄其煜(上海交通大学微电子学院,上海200030)1引言进入2005年以来,随着大陆半导体行业的继续发展,300mm芯片生产线在大陆也已开始上马。
中芯国际已建一条300mm生产线,在建两条300mm生产线;华虹NEC在建一条300mm芯片生产线;海力士意法在建一条300mm生产线等[1]。
相对于传统的200mm或150mm生产线,300mm芯片生产线由于晶圆面积很大,是200mm的2.25倍,可以进一步降低每个芯片单元的生产成本,但是也由于面积的因素,生产线的任何问题都有可能造成极大的损失。
同时,由于制程的不断发展,线宽越来越窄,工艺的要求也越来越高,这些因素都对厂务各系统的无故障运行能力提出了更高的要求。
厂务的气体、化学(包括研磨浆料系统)和纯水系统为整条生产线提供气体(特气和大宗气体)、化学品和纯水,它们与芯片直接接触,所以这些系统被称为制程相关系统。
制程相关系统的稳定与否直接关系到生产线制造是否正常。
本文将重点介绍300mm厂务化学系统的分类、架构、品质控制、安全设计并且将对设计进行探讨。
2定义和分类厂务化学系统是为生产线提供一年365天无中断化学品供应的系统。
本文所定义的化学供应系统包括研磨浆料系统,简而言之,是由厂务化学课(气化课)负责的系统。
厂务化学系统所供应的化学品一是要达到一定量(大量的机台使用该化学品或单个机台用量很大),二是要具有长距离(如100m)输送不易变质的特点。
一般供应到湿法清洗、黄光、CMP、零部件清洗等部门。
按照所供应的化学品的种类不同,厂务化学系统一般可分为三大类,即化学研磨液系统、有机溶剂系统和酸碱系统。
(1)化学研磨液系统。
供应到CMP去的、用于研磨的化学浆料称为化学研磨液。
300mm离子注入机靶室晶圆传输控制系统设计

300mm离子注入机靶室晶圆传输控制系统设计谢均宇;杨亚兵;孙勇【摘要】在实现了高效晶圆传输全自动控制的基础上,阐述了靶室晶圆传送系统运动部件的结构和各自的功能;介绍了整个晶圆传输控制系统的设计思路,在采用高性能多轴运动控制卡和机械手模块的硬件基础上,引用了有限状态机对系统软件进行了智能化模型设计.【期刊名称】《电子工业专用设备》【年(卷),期】2010(039)005【总页数】5页(P26-29,37)【关键词】晶圆传送系统;自动控制;机械手;Turbo PMAC;有限状态机【作者】谢均宇;杨亚兵;孙勇【作者单位】北京中科信电子装备有限公司,北京,101111;北京中科信电子装备有限公司,北京,101111;北京中科信电子装备有限公司,北京,101111【正文语种】中文【中图分类】TN305.3离子注入机是半导体离子掺杂工艺线的关键设备之一[1],随着市场上对半导体器件的要求的提高,对离子注入机的综合要求也越来越高。
要求离子注入机具有:整机可靠性好、生产效率高、多种电荷态离子宽能量范围注入、精确控制束注入能量精度、精确控制束纯度、低尘粒污染、整机全自动控制、注片均匀性和重复性好等多种功能和特征。
这一切都直接受控制技术的影响,而其中的靶室晶圆传输控制系统,是整机控制系统一个重要组成部分,直接决定了整机的生产效率和可靠性。
目前,300mm离子注入机已经成为国际高端集成电路生产线采用的主流机型,北京中科信电子装备有限公司作为国内离子注入机制造的领航者,为适应大规模生产线工艺要求率先成功研制出300mm大角度中束流离子注入机。
本文要介绍的就是这台离子注入机上的300mm靶室晶圆传送控制系统,包括各个运动部件、硬件模块的选用及软件模块的设计。
与以往的国产机型相比,这套系统除了达到全自动运行基本的功能要求外,还能够针对单晶圆注入方式,改良了结构设计,优化了运动流程,大大提高了生产效率,同时稳定性和运动精度也得到了提高,达到了国外先进机型的水平。
300mm半导体代工厂Slurry供应系统设计中的品质管理
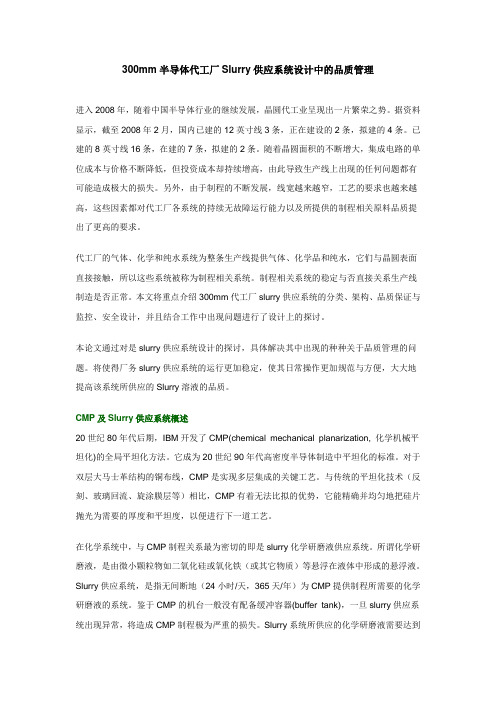
300mm半导体代工厂Slurry供应系统设计中的品质管理进入2008年,随着中国半导体行业的继续发展,晶圆代工业呈现出一片繁荣之势。
据资料显示,截至2008年2月,国内已建的12英寸线3条,正在建设的2条,拟建的4条。
已建的8英寸线16条,在建的7条,拟建的2条。
随着晶圆面积的不断增大,集成电路的单位成本与价格不断降低,但投资成本却持续增高,由此导致生产线上出现的任何问题都有可能造成极大的损失。
另外,由于制程的不断发展,线宽越来越窄,工艺的要求也越来越高,这些因素都对代工厂各系统的持续无故障运行能力以及所提供的制程相关原料品质提出了更高的要求。
代工厂的气体、化学和纯水系统为整条生产线提供气体、化学品和纯水,它们与晶圆表面直接接触,所以这些系统被称为制程相关系统。
制程相关系统的稳定与否直接关系生产线制造是否正常。
本文将重点介绍300mm代工厂slurry供应系统的分类、架构、品质保证与监控、安全设计,并且结合工作中出现问题进行了设计上的探讨。
本论文通过对是slurry供应系统设计的探讨,具体解决其中出现的种种关于品质管理的问题。
将使得厂务slurry供应系统的运行更加稳定,使其日常操作更加规范与方便,大大地提高该系统所供应的Slurry溶液的品质。
CMP及Slurry供应系统概述20世纪80年代后期,IBM开发了CMP(chemical mechanical planarization, 化学机械平坦化)的全局平坦化方法。
它成为20世纪90年代高密度半导体制造中平坦化的标准。
对于双层大马士革结构的铜布线,CMP是实现多层集成的关键工艺。
与传统的平坦化技术(反刻、玻璃回流、旋涂膜层等)相比,CMP有着无法比拟的优势,它能精确并均匀地把硅片抛光为需要的厚度和平坦度,以便进行下一道工艺。
在化学系统中,与CMP制程关系最为密切的即是slurry化学研磨液供应系统。
所谓化学研磨液,是由微小颗粒物如二氧化硅或氧化铁(或其它物质)等悬浮在液体中形成的悬浮液。
ASYST推出AMHS新方案增加晶圆厂生产力
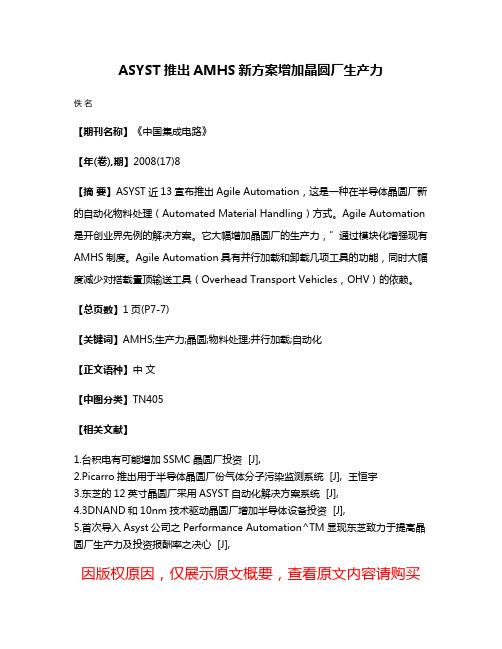
ASYST推出AMHS新方案增加晶圆厂生产力
佚名
【期刊名称】《中国集成电路》
【年(卷),期】2008(17)8
【摘要】ASYST近13宣布推出Agile Automation,这是一种在半导体晶圆厂新的自动化物料处理(Automated Material Handling)方式。
Agile Automation 是开创业界先例的解决方案。
它大幅增加晶圆厂的生产力,”通过模块化增强现有AMHS制度。
Agile Automation具有并行加载和卸载几项工具的功能,同时大幅度减少对搭载置顶输送工具(Overhead Transport Vehicles,OHV)的依赖。
【总页数】1页(P7-7)
【关键词】AMHS;生产力;晶圆;物料处理;并行加载;自动化
【正文语种】中文
【中图分类】TN405
【相关文献】
1.台积电有可能增加SSMC晶圆厂投资 [J],
2.Picarro推出用于半导体晶圆厂份气体分子污染监测系统 [J], 王恒宇
3.东芝的12英寸晶圆厂采用ASYST自动化解决方案系统 [J],
4.3DNAND和10nm技术驱动晶圆厂增加半导体设备投资 [J],
5.首次导入Asyst公司之Performance Automation^TM显现东芝致力于提高晶圆厂生产力及投资报酬率之决心 [J],
因版权原因,仅展示原文概要,查看原文内容请购买。
- 1、下载文档前请自行甄别文档内容的完整性,平台不提供额外的编辑、内容补充、找答案等附加服务。
- 2、"仅部分预览"的文档,不可在线预览部分如存在完整性等问题,可反馈申请退款(可完整预览的文档不适用该条件!)。
- 3、如文档侵犯您的权益,请联系客服反馈,我们会尽快为您处理(人工客服工作时间:9:00-18:30)。
300mm半导体工厂的AMHS系统在半导体制造技术高度发达的今天,300mm的半导体工厂已经成为全球半导体行业的主流。
由于300mm半导体生产线的巨额投入,人们不得不尽可能的挖掘300mm工厂的生产效率,以期得到更大的晶圆产出。
一个功能强大且性能稳定的AMHS系统在300mm工厂里扮演了一个非常重要的角色。
AMHS系统不仅可以有效的利用宝贵的洁净室的生产空间,并且还可以提高生产设备的利用率,缩短在制品WIP的Cycle Time,所以在很多的300mm的半导体工厂里,AMHS都被视为可以快速提升产能,增加生产效率的尖兵利器。
AMHS系统在300mm半导体工厂的应用特点和200mm晶圆相比,更大的晶圆尺寸使得单批Lot的晶圆重量变得更大,仅凭在200mm工厂Intrabay内的人工搬运已经远远无法满足300mm工厂的生产要求。
因此,在300mm的半导体工厂里,生产方式的巨大变化也给AMHS系统提出了更高的要求。
搬送方式的巨大进化首先,是AMHS搬送方式从200mm工厂的SEMI Auto方式到300mm工厂Full Auto 方式的转变。
如图1红色轨道所示:在200mm工厂所采用的Semi Auto生产方式中的Wafer搬送,只包括中央区域Interbay的AMHS搬送。
而Wafer到生产设备的部分需要人工搬送来完成。
而在300mm工厂里,由于wafer自身重量的增加,导致人工搬送异常困难,故由AMHS系统取而代之直接将wafer搬送到生产设备,如图1中的蓝色轨道,这即是Full Auto的作业方式。
这种方式极大减轻了生产一线操作人员的工作强度,同时又避免了因人为事故而造成的损失。
更为重要的是,在工厂产能迅速提升的过程中,可以满足大规模搬送量的AMHS系统的巨大优势可以完全呈现。
其次,是Tool To Tool直接搬送的全厂性应用。
为了进一步的节省FOUP的搬送时间,300mm晶圆厂的AMHS系统必须支持Tool To Tool的直接搬送。
这种搬送模式可以使得FOUP不必经过存储设备Stocker的中转,而直接从上一站的加工设备搬送到下一站的加工设备。
如图1所示:在没有Tool To Tool直接搬送的工厂内,从Tool A到Tool B的搬送路径为Tool A→Stocker01—>Stocker02→Tool B。
但是在具备Tool To Tool直接搬送功能的工厂内,如图2所示,从Tool A到Tool B的搬送路径为Tool A→Tool B。
为了实现这种Tool To Tool的搬送功能,在AMHS系统设计的时候,必须要考虑到Interbay和Intrabay的整合,工厂布局,搬送车辆和Stocker的选择等多种因素。
AMHS系统整体性能的要求稳定性:由于全厂都在大规模地应用AMHS系统进行Wafer的搬送,所以一旦AMHS 系统发生故障将导致全厂性的生产设备因没有可供生产的Wafer而停止生产,进而严重影响正常的生产运营。
考虑到在300mm半导体工厂内,AMHS系统的稳定性将直接关系到工厂的生产效率,工厂的管理者对于AMHS系统稳定性也提出了极其苛刻的要求。
高效性:与200mm半导体工厂的AMHS系统相比,300mm工厂的AMHS搬送量有了十倍以上的增长。
在面对巨大搬送量的时候,如何确保全厂的搬送效率,在更短的时间内完成Wafer的搬送,对于AMHS系统而言是一个巨大的挑战。
同时,AMHS系统搬送效率的高低,也将直接影响到生产设备的利用率,故在300mm半导体工厂的搬送时间都是以秒为单位进行计算,且每一秒钟的减少,都需要付出更多的精心设计才可实现。
最大化的利用生产空间在300mm工厂的生产车间内,洁净室的空间是极其昂贵的。
而AMHS系统为了解决生产线上所有在制品WIP的存储保管问题,不得不占用大量的面积和空间。
如何在满足存储和搬送要求的前提下,最大化的节省所占用的面积空间,是AMHS系统必须面对的一个难题。
在200mm半导体工厂的AMHS系统中,为了尽可能的利用洁净室的面积,提高单位占地面积的Wafer存储量,比较经常采用的方式是提升Stocker中央区域的天花板高度,并采用更高的Stocker型号,这种方式一般可以增加20%~30%的wafer存储量。
在300mm半导体工厂的AMHS系统中,比较常用的方式是使用UTS(Under Track Storage),一种可以将Wafer存放在天花板下方空中的装置,由于UTS可以不占用洁净室的地面面积,有效地利用了洁净室的空中区域,所以这种解决方案在300mm半导体工厂里的应用非常广泛,如图3所示。
AMHS系统的柔性设计在300mm半导体工厂内,搬送轨道遍布整个车间,构成了巨大且复杂的网络拓扑结构。
虽然单个车辆个体或单一合分流的节点发生故障,对于轨道控制系统不会产生大的影响,但是这种单点故障若发生在交通繁忙的路段,或者较长时间不能解决的时候,将会产生严重的交通拥塞,并导致整体搬送效率急速下降,从而影响到整个工厂的生产。
因此,300mm的AMHS轨道控制系统必须具备故障自我侦测和自我调整的柔性特点。
当某单一的轨道节点发生故障,轨道控制系统可以自动调节系统的运行参数,动态响应故障激励,及时调整所有搬送车辆的运行路线,并通知系统管理人员进行紧急故障处理等功能。
AMHS系统的性能分析和影响因素由于AMHS系统属于较复杂的多元非线性系统,传统的控制理论很难对其进行准确的分析和性能优化。
为了对AMHS系统进行优化改善,首先需要确定可以准确反映AMHS 系统性能的指标参数,并在此基础上对那些关键性因素进行模拟分析得出优化方向,进而在AMHS系统的实际运行中加以验证,从而得到预期的优化效果。
分析AMHS系统性能的重要指标在对AMHS系统进行性能分析的时候,一般会从以下两个方面进行判断:稳定性:MTBF和MTTR是在衡量系统稳定性方面最常用到的两个参数。
MTBF(Mean Time Between Failure)表示系统硬件的故障频率,这个数据越低,表示系统的硬件越稳定,故障率越低。
而MTTR(Mean Time To Repair)表示系统硬件发生故障时候的修复时间,这个数据越低,表示系统硬件的可修复能力越高,可在线使用的能力越高。
高效性:在衡量AMHS系统的搬送效率的时候,平均搬送时间和三西格玛的搬送时间是最常用到的两个指标。
平均搬送时间是指在某单位时间段内完成的所有搬送任务的平均搬送时间,而三西格玛的搬送时间则是借用了统计学上的一个概念:即在三西格玛的搬送时间内完成的搬送任务的数量占到总体搬送量的三西格玛(99.97%)。
在Full Auto 作业模式下的这两个指标将直接关系到生产设备能否保证较高的生产利用率,甚至会影响到Wafer的Cycle Time。
因此,大部分300mm工厂的管理者对于这个性能指标都会设定极其严格的标准。
影响AMHS系统搬送性能的主要因素通常,影响AMHS系统搬送性能的因素可以从AMHS系统的硬件特性和系统控制软件两方面去分析。
首先,系统的硬件因素主要考虑以下几点:OHT行走速度和加速度:OHT的行走速度和加速度是影响AMHS系统整体运行效率的重要参数。
更高的行走速度和加速度可以有效地降低单次搬送的时间;但是当AMHS 系统的搬送任务过于频繁的时候,OHT本身会遇到经常性的临时停车,这个时候过高的速度和加速度反而会增加OHT车体本身的负担,加快OHT车体的磨损。
因此,大部分的AMHS系统制造商都会根据实际情况设定最佳的行车速度,而不是盲目的追求更高的行走速度。
OHT的升降马达的运行速度:OHT的升降马达主要是用来将FOUP从轨道高度的位置下降放置于生产设备的Port上或者反之将FOUP从设备的Port上传送到OHT上。
因此,升降马达的运行速度也会影响AMHS系统整体的搬送时间,但考虑到生产设备操作人员的安全问题,升降马达的速度一般不会设置过高。
轨道的设计和布局:轨道的设计模式和拓扑布局是影响AMHS系统搬送效率的关键因素。
在设计轨道拓扑布局的时候,需要考虑到OHT行走路线的优化、最短路径的设计、轨道通行的冗余能力、OHT交汇路口的设计等问题。
一个优秀的轨道布局设计,不仅可以缩短OHT的行走路程,还可以提高轨道整体的冗余能力,增加在单点发生故障时候轨道系统的健壮性。
其次,系统的软件方面主要考虑以下几个因素:OHT行走路径的选择:OHT在出发至目的地之前需要确定最优的行走路线,以便尽可能的减少搬送时间。
在分析比较各种不同行走路径的时候,通常需要考虑每条行走路径实际的行走距离;路途障碍物的数量;中途交汇路口的数量;路径中途有无单点故障发生等因素。
同时,当OHT行走路径确定后出发的时候,如果有影响到路径选择的意外事件发生,OHT可以重新计算最优路径,并动态改变之前的行走路径。
最佳OHT的搜索逻辑:OHT的搜索逻辑是用来确定当某一个站点有搬送请求发生的时候,AMHS系统如何选择最优的OHT来完成这个搬送任务。
一般而言,如果仅仅认为只要是距离最近的没有任务的空车就是最优的OHT,那是不完全正确的。
若考虑到更加复杂的情况,即当多个站点都发生了搬送请求事件的时候,如何确定多站点的最优OHT,并且加上允许改变之前有搬送指令的空车的搬送指令的条件,则需要一个复杂算法的帮助才能真正确定系统整体的最优选择。
不过可惜的是,复杂算法通常会消耗控制系统大量的CPU资源,且更易导致控制系统的不稳定。
故在实际工厂的应用中,无法确定对于系统整体搬送最优的OHT。
轨道交通的控制逻辑:交通控制主要是解决在OHT行走至交汇路口时的优先通行问题。
使排队等待通过交汇路口的所有OHT车辆有序且高效的通行是轨道交通控制最主要的目的。
但在大部分情况下,考虑到控制程序的稳定性,设计人员通常仍会舍弃更为智能化的控制逻辑而采用逻辑简单容易操作的交通控制程序。
AMHS系统所面临的挑战和未来的发展趋势在2007 SEMICON Taiwan的高峰论坛上,TSMC发表了未来五年内建设启用450mm 半导体工厂的豪言壮语。
随着更多的半导体制造商的积极投入,450mm半导体工厂似乎将不再遥远。
到那时,AMHS系统在450mm半导体工厂的生产过程中将发挥更加重要的作用,同时也会面临更为严峻的挑战。
AMHS系统的使用者和管理人员提出的每一个近乎于苛刻的要求,对于AMHS系统的设计开发人员来说,都将是技术进步的动力来源和未来的挑战方向。
1)在450mm半导体工厂内,虽然Wafer尺寸仅仅增加 1.5倍,但Wafer重量却增加2.25倍。
为了适应重量更重的Wafer的搬送,AMHS的制造商将不得不对OHT的负载能力,轨道强度,厂房结构等多方面进行重新计算评估,并相应的提高AMHS系统的硬件性能。