铸造工艺设计说明书
法兰盘铸造工艺设计说明书
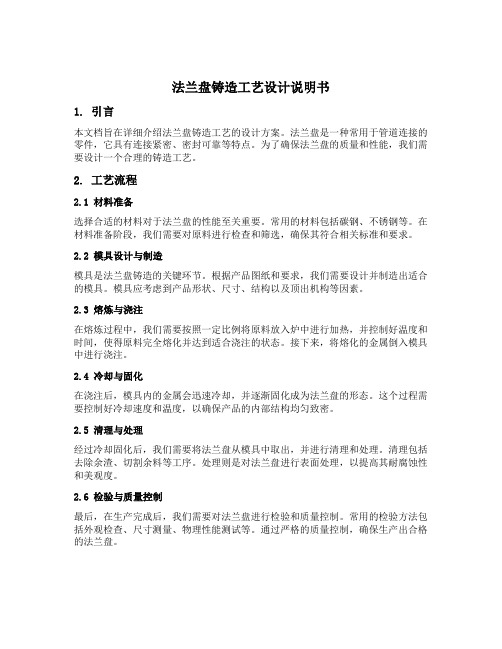
法兰盘铸造工艺设计说明书1. 引言本文档旨在详细介绍法兰盘铸造工艺的设计方案。
法兰盘是一种常用于管道连接的零件,它具有连接紧密、密封可靠等特点。
为了确保法兰盘的质量和性能,我们需要设计一个合理的铸造工艺。
2. 工艺流程2.1 材料准备选择合适的材料对于法兰盘的性能至关重要。
常用的材料包括碳钢、不锈钢等。
在材料准备阶段,我们需要对原料进行检查和筛选,确保其符合相关标准和要求。
2.2 模具设计与制造模具是法兰盘铸造的关键环节。
根据产品图纸和要求,我们需要设计并制造出适合的模具。
模具应考虑到产品形状、尺寸、结构以及顶出机构等因素。
2.3 熔炼与浇注在熔炼过程中,我们需要按照一定比例将原料放入炉中进行加热,并控制好温度和时间,使得原料完全熔化并达到适合浇注的状态。
接下来,将熔化的金属倒入模具中进行浇注。
2.4 冷却与固化在浇注后,模具内的金属会迅速冷却,并逐渐固化成为法兰盘的形态。
这个过程需要控制好冷却速度和温度,以确保产品的内部结构均匀致密。
2.5 清理与处理经过冷却固化后,我们需要将法兰盘从模具中取出,并进行清理和处理。
清理包括去除余渣、切割余料等工序。
处理则是对法兰盘进行表面处理,以提高其耐腐蚀性和美观度。
2.6 检验与质量控制最后,在生产完成后,我们需要对法兰盘进行检验和质量控制。
常用的检验方法包括外观检查、尺寸测量、物理性能测试等。
通过严格的质量控制,确保生产出合格的法兰盘。
3. 工艺参数3.1 熔炼温度熔炼温度是影响铸件质量和性能的重要参数之一。
根据材料特性和产品要求,选择合适的熔炼温度,以确保金属完全熔化且不产生过多的气体。
3.2 浇注温度浇注温度是指将熔化的金属倒入模具中的温度。
合适的浇注温度可以保证金属充分填充模具,并避免产生缺陷和气孔。
3.3 冷却速度冷却速度直接影响到铸件的组织结构和性能。
较快的冷却速度可以使得铸件结构更致密,但也容易产生应力集中和裂纹等问题。
因此,需要根据产品要求选择合适的冷却速度。
铸造工艺设计说明书

铸造⼯艺设计说明书铸造⼯艺设计说明书课程设计:机械⼯艺课程设计设计题⽬:底座铸造⼯艺设计班级:机⾃1103设计⼈:学号:指导教师:张锁梅、贾志新前⾔学⽣通过设计能获得综合运⽤过去所学过的全部课程进⾏机械制造⼯艺及结构设计的基本能⼒,为以后做好毕业设计、⾛上⼯作岗位进⾏⼀次综合训练和准备。
它要求学⽣全⾯地综合运⽤本课程及有关选修课程的理论和实践知识,进⾏零件加⼯⼯艺规程的设计和机床夹具的设计。
其⽬的是:(1)培养学⽣综合运⽤机械制造⼯程原理课程及专业课程的理论知识,结合⾦⼯实习、⽣产实习中学到的实践知识,独⽴地分析和解决机械加⼯⼯艺问题,初步具备设计中等复杂程度零件⼯艺规程的能⼒。
(2)培养学⽣能根据被加⼯零件的技术要求,运⽤夹具设计的基本原理和⽅法,学会拟订夹具设计⽅案,完成夹具结构设计,进⼀步提⾼结构设计能⼒。
(3)培养学⽣熟悉并运⽤有关⼿册、图表、规范等有关技术资料的能⼒。
(4)进⼀步培养学⽣识图、制图、运算和编写技术⽂件的基本技能。
(5)培养学⽣独⽴思考和独⽴⼯作的能⼒,为毕业后⾛向社会从事相关技术⼯作打下良好的基础。
⽬录⼀、⼯艺审核 (1)1.数量与材料 (1)2.图样 (1)3.零件的结构性 (1)⼆、成形⼯艺设计 (1)1.确定⼯艺⽅案 (1)(1)浇注位置的选择 (2)(2)分型⾯的选择 (2)2.确定铸造⼯艺参数 (4)(1)机械加⼯余量和铸出孔 (4)(2)浇注位置的选择 (5)(3)拔模斜度 (5)(4)铸造收缩率 (6)3.砂芯设计 (6)4.浇注系统的设计 (6)5. 冷铁的设置 (6)三、⼼得体会 (7)⼀、⼯艺审核1、数量与材料由零件图可知,该零件结构⽐较简单,但是形状不是很规则,⼯作条件⼀般以承受压⼒为主,故要求该零件有良好的刚性和强度。
另外,根据零件图的要求,该底座零件为单件⼩批量⽣产,另外材料选⽤灰铸铁HT200,流动性较好,适于铸造。
2、图样该零件图给出了主视图、左视图、俯视图3个视图。
带轮铸造工艺设计说明书

带轮铸造工艺设计说明书一、工艺分析1、审阅零件图仔细审阅零件图,熟悉零件图,而且提供的零件图必须清晰无误,有完整的尺寸和各种标记。
仔细审查图样。
注意零件图的结构是否符合铸造工艺性,有两个方面:(1)审查零件结构是否符合铸造工艺的要求。
(2 )在既定的零件结构条件下,考虑铸造过程中可能出现的主要缺陷,在工艺设计中采取措施避免。
零件名称:带轮零件材料:HT150生产批量:大批量生产2、零件技术要求铸件重要的工作表面,在铸造是不允许有气孔、砂眼、渣孔等缺陷.3、选材的合理性铸件所选材料是否合理,一般可以结合零件的使用要求、车间设备情况、技术状况和经济成本等,参考常用铸造合金(如铸钢、灰铸铁、球墨铸铁、可锻铸铁、蠕墨铸铁、铸造铝合金、铸造铜合金等)的种类、牌号、性能、工艺特点、价格和应用等,进行综合分析,判断所选的合金是否合理。
4、审查铸件结构工艺性铸件壁厚不小于最小壁厚5—6又在临界壁厚20-25以下.二、工艺方案的确定1、铸造方法的确定铸造方法包括:造型方法、造芯方法、铸造方法及铸型种类的选择(1)造型方法、造芯方法的选择根据手工造型和机器造型的特点,选择手工造型(2)铸造方法的选择根据零件的各参数,对照表格中的项目比较,选择砂型铸造.(3)铸型种类的选择根据铸型的特点和应用情况选用自硬砂.2、浇注位置的确定根据浇注位置选择的4条主要规则,选择铸件最大截面,即底面处。
3、分型面的选择本铸件采用两箱造型,根据分型面的选择原则,分型面取最大截面,即底面。
三、工艺参数查询1、加工余量的确定根据造型方法、材料类型进行查询。
查得加工余量等级为11~13,取加工余量等级为12.根据零件基本尺寸、加工余量等级进行查询.查得铸件尺寸公差数值为10.根据零件尺寸公差、公差等级进行查询。
查得机械加工余量为5.5。
2、起模斜度的确定根据所属的表面类型查得测量面高140,起模角度为0度25分(0。
42°)。
3、铸造圆角的确定根据铸造方法和材料,查得最小铸造圆角半径为3。
支架零件铸造工艺设计说明书

支架零件铸造工艺设计一、零件的生产条件、结构及技术要求1、生产性质:大批量生产2、材料:HT2003、零件加工方法:零件上有多个孔,除中间的大孔需要铸造以外,其他孔在考虑加工余量后不宜铸造成型,采用机械方法加工,均不铸出。
造型方法:机器造型;造芯方法:机器制芯4、主要技术要求:满足HT200的机械性能要求,去毛刺及锐边,铸件表面不允取有缺陷。
二、零件图及立体图结构分析1、零件图如下:零件主视图零件俯视图2、立体图如下:三、工艺设计过程1、铸造工艺设计方法及分析(1)铸件壁厚为了避免浇不到、冷隔等缺陷,铸件不应太薄。
铸件的最小允许壁厚与铸造的流动性密切相关。
在普通砂型铸造的条件下,铸件最小允许壁厚见表1。
表1. 铸件最小允许壁厚查得灰铁铸件在100~200mm的轮廓尺寸下,最小允许壁厚为5~6mm。
由零件图可知,零件中不存在壁厚小于设计要求的结构,在设计过程中,也没有出现壁厚小于最小壁厚要求的情况。
(2)造型、制芯方法造型方法:该零件需批量生产,为中小型铸件,因此,采用湿型粘土砂机器造型,模样采用金属模,采用技术先进的机器造型。
制芯方法:在造芯用料及方法选择中,如用粘土砂制作砂芯原料成本较低,但是烘干后容易产生裂纹,容易变形。
在大批量生产的条件下,由于需要提高造芯效率,且常要求砂芯具有高的尺寸精度,此工艺所需的砂芯采用热芯盒法生产砂芯,以增加其强度及保证铸件质量。
选择使用射芯工艺生产砂芯。
采用热芯盒制芯工艺热芯盒法制芯,是用液态固性树脂粘结剂和催化剂制成的一种芯砂,填入加热到一定的芯盒内,贴近芯盒表面的砂芯受热,其粘结剂在很短的时间内硬化。
而且只要砂芯表层有数毫米的硬壳即可自芯取出,中心部分的砂芯利用余热可自行硬化。
(3)砂箱中铸件数目的确定及排布初步确定一箱中放几个铸件,作为进行浇冒口设计的依据。
一箱中的铸件数目,应该是在保证铸件质量的前提下越多越好。
本铸件在一砂箱中高约130mm,长约200mm,宽约110mm,体积约99.7cm^3,密度7.2g/cm^3,重约0.8Kg。
铸造工艺设计说明书
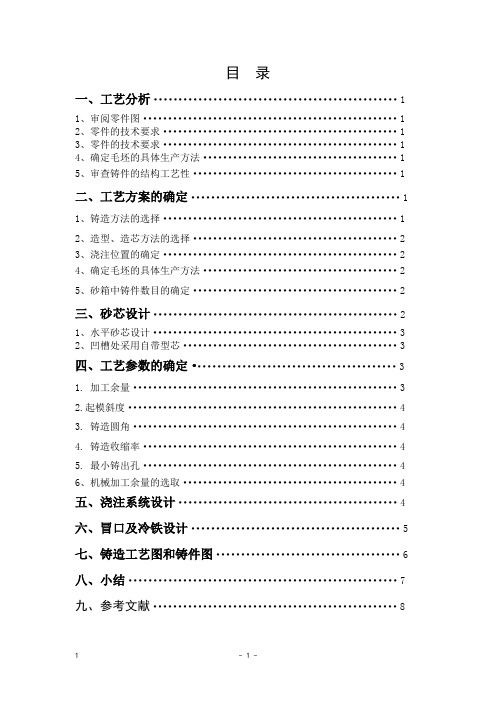
目录一、工艺分析 (1)1、审阅零件图 (1)2、零件的技术要求 (1)3、零件的技术要求 (1)4、确定毛坯的具体生产方法 (1)5、审查铸件的结构工艺性 (1)二、工艺方案的确定 (1)1、铸造方法的选择 (1)2、造型、造芯方法的选择 (2)3、浇注位置的确定 (2)4、确定毛坯的具体生产方法 (2)5、砂箱中铸件数目的确定 (2)三、砂芯设计 (2)1、水平砂芯设计 (3)2、凹槽处采用自带型芯 (3)四、工艺参数的确定 (3)1. 加工余量 (3)2.起模斜度 (4)3. 铸造圆角 (4)4. 铸造收缩率 (4)5. 最小铸出孔 (4)6、机械加工余量的选取 (4)五、浇注系统设计 (4)六、冒口及冷铁设计 (5)七、铸造工艺图和铸件图 (6)八、小结 (7)九、参考文献 (8)一、工艺分析1、审阅零件图查看零件图的具体尺寸与图纸绘制是否正确。
零件名称: 套筒座工艺方法:铸造零件材料:HT250零件重量:3.1955kg毛坯重量:4.3303kg生产批量: 100件/年,为小批量生产2、零件的技术要求零件在铸造方面的技术要求:未铸造圆角半径:R=2~3 mm;时效处理。
3、选材的合理性套筒座选用的材料是HT250,为灰铸铁。
灰铸铁铸件的壁厚不应太薄,边角处应适当加厚,防止出现白口组织使该处既硬又难于加工。
此零件用于支承,只要求能够承受抗压即可,选择材料HT250可以满足要求。
4、确定毛坯的具体生产方法根据以上信息可知,由于零件属中型零件小批量生产,形状比较简单、壁厚比较均匀,且该材料为灰铸铁,所以确定毛坯的生产方法为砂型铸造,采用砂型铸造具有生产周期短,灵活性大、成本低的优点。
5、审查铸件的结构工艺性铸件轮廓尺寸为162x134x133mm,查表得砂型铸造的最小壁厚为6mm,套筒座的壁厚符合其要求。
在套筒座中最小壁厚为6mm,最大铸造壁厚为15mm。
二、工艺方案的确定1、铸造方法的选择由于套筒座的年产量为100件,属小批量生产,且零件结构简单,所以确定毛坯的生产方法为砂型铸造,由于铸件的高度为133mm,浇注位置上没有较大的壁厚、材料为HT250不需要冷铁。
铸造工艺设计说明书

铸造⼯艺设计说明书铸造⼯艺设计说明书⽬录1. 零件结构分析 (3)1.1. 零件信息 (3)1.2. 技术要求 (3)2. 铸造⼯艺⽅案分析 (5)2.1. 铸造⽅法的确定 (5)2.2. 分型⾯的选择 (5)2.3. 铸件浇注位置的确定 (7)3. 铸造⼯艺参数 (9)3.1. 铸件尺⼨公差 (9)3.2. 铸件重量公差 (9)3.3. 机械加⼯余量 (9)3.4. 铸造收缩率 (9)3.5. 起模斜度 (9)3.6. 最⼩铸出孔及槽 (10)3.7. ⼯艺补正量 (10)3.8. 分型负数 (10)3.9. 反变形量 (10)3.10. 砂芯负数 (11)3.11. ⾮加⼯壁厚的负余量 (11)3.12. 分型负数 (11)4. 砂芯设计 (12)4.1. 砂芯的概念 (12)4.2. 芯头设计 (12)5. 浇注系统设计 (16)5.1. 浇注系统设计原则 (16)5.2. 浇注系统位置确定 (17)5.3. 浇注系统类型确定 (17)5.4. 浇注系统尺⼨计算 (17)6. 冒⼝及冷铁 (22)6.1. 冒⼝补缩原则 (22)6.2. 冒⼝及冷铁位置个数的选择 (22)6.3. 冒⼝种类选择及参数计算 (23)6.4. 铸件成品率 (25)1. 零件结构分析1.1. 零件信息产品名称:⽀架材料:铸钢外形尺⼨:91×42×66cm 3 质量:463Kg g 463000cm 58983cm g 85.7v m 33=≈?=?=ρ⽣产批量:成批⼤量⽣产。
造型⽅法:⼿⼯造型其零件⽰意图如下图1.2. 技术要求铸件重要的⼯作表⾯,在铸造是不允许有⽓孔、砂眼、渣孔等缺陷。
2.铸造⼯艺⽅案分析2.1.铸造⼯艺的确定铸造⼯艺包括:造型⽅法、造芯⽅法、铸造⽅法及铸型种类的选择2.1.1.造型⽅法、造芯⽅法的选择根据⼿⼯造型和机器造型的特点,选择⼿⼯造型2.1.2.铸造⽅法的选择根据零件的各参数,对照表格中的项⽬⽐较,选择砂型铸造。
《铸造工艺》课程设计说明书

目录1绪言················································2铸造工艺设计···············2.1铸件结构的铸造工艺性·········2. 2铸造工艺方案的确定·················2.3参数的选择工艺2. 4砂芯设计2. 5浇注系统设计·············3铸造的工艺装备设计······3. 1模样设计·······3. 2模底板的设计·······················3. 3模样在模底板上的装配············4结束语·······参考文献1绪言我本次课程设计的任务是对灰铸铁支承座进行铸造工艺及工装设计。
铸造工艺设计说明书
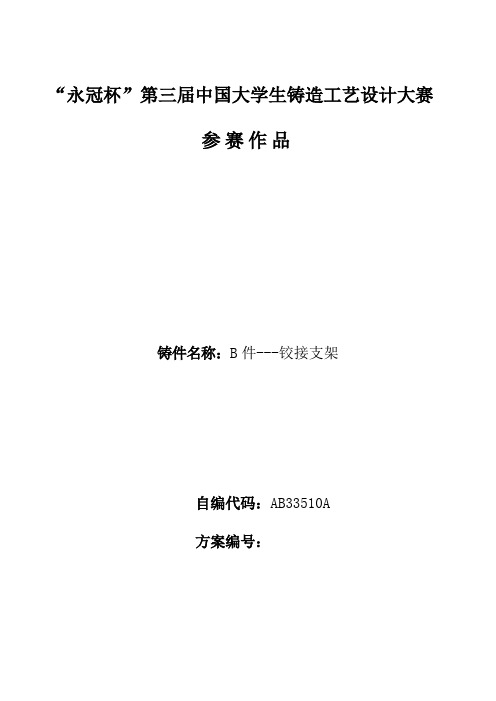
“永冠杯”第三届中国大学生铸造工艺设计大赛参赛作品铸件名称:B件---铰接支架自编代码:AB33510A方案编号:目录摘要 (1)1 零件简介 (2)1.1零件名称及用途 (2)1.2零件的技术要求 (2)1.3零件的结构 (2)2铸造工艺方案 (3)2.1材料选择 (3)2.2工艺方案的选择 (3)2.3工艺参数的确定 (5)2.3.1铸件的尺寸公差 (5)2.3.2铸件的质量公差 (5)2.3.3机械加工余量 (5)2.3.4模样的起模斜度 (5)2.3.5铸造收缩率 (5)2.3.6最小铸出孔 (5)2.4浇注系统的设计 (6)2.4.1浇注系统的选择 (6)2.4.2浇注系统尺寸的计算 (6)2.4.3浇注系统设计的校核 (8)2.5砂芯设计 (9)2.5.1砂芯设计的要点 (9)2.5.21#砂芯 (10)2.5.32#砂芯 (11)2.6冒口设计 (12)2.6.1冒口设计的说明 (12)2.6.2冒口的尺寸计算 (12)2.7出气孔的设计 (13)3砂箱的设计 (13)4铸件充型及凝固过程数值模拟 (14)4.1ViewCast 模拟软件 (14)4.2充型过程模拟 (14)4.3铸造凝固过程数值模拟 (17)4.4铸造工艺改进方案 (18)结论 (19)参考文献 (20)附图1 ——铸造工艺图附图2 ——合箱图附图3 ——铸造工艺卡片附图4 ——砂箱图摘要该铸件为驾驶室右铰接支架,通过分析零件的结构特点和性能要求,选用粘土砂湿型手工造型方法,采用两箱造型,确定了浇注位置和分型面等工艺方案,使零件整体位于下箱。
确定了机械加工余量、起模斜度、铸件收缩率等工艺参数。
根据各铸造工艺参数用Pro/Engineer软件画出铸件的三维实体图。
根据零件的形状特征,选用两个竖直放置的砂芯,1#砂芯采用盖板砂芯的形式固定。
选用了封闭式底注式浇注系统,采用了两个内浇道,用奥赞公式计算了浇注系统各部分的截面面积和尺寸,根据工艺方案在铸件顶部放置了两个用于补缩的暗冒口。
法兰盘铸造工艺设计说明书

法兰盘铸造工艺设计说明书一、工艺概述法兰盘铸造工艺是一种通过将熔融的金属浇注进模具中,待其冷却凝固后获得所需形状和性能的金属构件的工艺方法。
本说明书将详细介绍法兰盘铸造工艺设计的各个方面,以确保生产出的法兰盘具有高质量和稳定性。
二、材料选择1. 铸钢:适用于制造承受较大载荷和冲击的法兰盘。
具有较好的强度、韧性和耐腐蚀性。
2. 铸铁:成本较低,适用于制造对强度要求不高的法兰盘。
具有较好的耐磨性和耐腐蚀性。
3. 铝合金:质量轻,适用于对重量有要求的场合。
具有良好的导热性和抗腐蚀性。
三、模具设计1. 根据产品要求,设计合理的模具结构,以确保法兰盘的形状和尺寸精度。
2. 考虑模具材料的热膨胀系数、耐热性、耐磨性和加工性能,选择合适的模具材料。
3. 设计合理的浇注系统和冷却系统,以确保金属液的充型和冷却凝固。
四、熔炼与浇注1. 根据选定的材料,进行熔炼制备金属液。
控制金属液的成分、温度和纯净度,以确保铸造质量。
2. 在浇注前对金属液进行除渣、过滤等处理,以提高铸件的质量。
3. 控制浇注温度和浇注速度,以确保金属液的充型效果和减少铸造缺陷。
五、凝固与冷却1. 确保金属液在模具内充分凝固,形成所需形状的法兰盘。
2. 控制冷却速度,以获得良好的铸件组织和性能。
3. 在冷却过程中,应避免产生较大的温度梯度和收缩应力,以减少铸件裂纹和变形。
六、热处理与精整1. 根据选定的材料和性能要求,进行必要的热处理,以调整铸件的组织和性能。
2. 进行表面处理和精整,以提高法兰盘的表面质量和尺寸精度。
3. 对铸件进行消除应力和稳定组织的处理,以提高其使用性能和寿命。
七、质量检测1. 对铸件进行外观质量检查,确保无明显的铸造缺陷。
2. 进行尺寸精度检测,确保符合图纸要求。
3. 根据需要,进行机械性能测试、金相组织分析和无损检测等,以确保铸件的质量和可靠性。
八、安全注意事项1. 在操作过程中,应穿戴防护用具,如防护服、手套、眼镜等,以防止烫伤、割伤等伤害。
法兰盘铸造工艺设计说明书

法兰盘铸造工艺设计说明书设计说明书:法兰盘铸造工艺一、工艺概述法兰盘是一种连接设备的重要元件,广泛应用于工业领域。
本文将介绍法兰盘的铸造工艺设计,包括模具设计、材料选用、铸造工艺参数等方面的内容。
二、模具设计1. 模具类型选择根据法兰盘的形状复杂度和生产批量,选取适当的模具类型。
常见的模具类型有砂型、金属型和陶瓷型等。
考虑到铸造成本和生产效率,本设计选择砂型作为模具类型。
2. 模具结构设计根据法兰盘的尺寸和形状特点,设计模具的结构。
模具应包括上模、下模、型芯和型腔。
考虑到法兰盘的外形要求和便于脱模,本设计采用具有分型面和脱模斜度的模具结构。
三、材料选用1. 基础材料选择法兰盘通常用于高温、高压环境,要求具有良好的耐腐蚀性和耐磨性。
本设计选择了耐热铸铁作为基础材料,其具有良好的机械性能和耐蚀性。
2. 涂料选用为提高法兰盘铸件表面质量,减少缺陷率和气孔率,需选用适合的涂料。
本设计选择石英砂作为铸造涂料,石英砂具有良好的耐火性和流动性,能有效提高铸件表面光滑度。
四、铸造工艺参数1. 熔炼工艺根据法兰盘的尺寸和材料要求,确定适当的熔炼工艺参数。
包括熔炼温度、保温时间、炉内气氛等。
2. 浇注工艺根据模具的结构和法兰盘的形状特点,确定适当的浇注工艺参数。
包括浇注温度、浇注速度和浇注位置等。
3. 固化工艺根据法兰盘材料的凝固特性,确定适当的固化工艺参数。
包括冷却时间、扫砂时间和升温速率等。
五、质量控制1. 理化性能测试对铸造完成的法兰盘样品进行理化性能测试,包括硬度、抗拉强度和冲击韧性等指标。
确保法兰盘的材料性能符合设计要求。
2. 尺寸检验使用合适的测量工具对法兰盘进行尺寸检验,包括直径、孔距和孔径等参数。
确保法兰盘的尺寸精度符合设计要求。
3. 表面质量检验使用目视和触摸等方法对法兰盘的表面质量进行检验,确保无明显缺陷和粗糙度过高的情况。
六、安全措施1. 工人防护工人在进行铸造操作时应做好个人防护措施,包括戴好安全帽、防护眼镜和手套等。
(完整word版)铸造工艺课程设计说明书

铸造工艺课程设计说明书目录1 前言 (4)1。
1本设计的意义 (4)1.1.1 本设计的目的 (4)1.1。
2 本设计的意义 (5)1.2本设计的技术要求 (5)1。
3本课题的发展现状 (5)1.4本领域存在的问题 (6)1.5本设计的指导思想 (6)1。
6本设计拟解决的关键问题 (7)2 设计方案 (7)2。
1零件的材质分析 (8)2.2支座工艺设计的内容和要求 (9)2.3造型造芯方法的选择 (11)2。
4浇注位置的选择与分型面的选择 (12)2。
4.1 浇注位置的选择 (12)2.4.2 分型面的确定 (14)2.4.3 砂箱中铸件数目的确定 (15)3 设计说明 (17)3。
1工艺设计参数确定 (17)3。
1.1 最小铸出的孔和槽 (17)3.1.2 铸件的尺寸公差 (18)3。
1.3 机械加工余量 (19)3。
2铸造收缩率 (19)3。
2。
1 起模斜度 (20)3.2。
2 浇注温度和冷却时间 (21)3。
3砂芯设计 (22)3.3。
1 芯头的设计 (22)3。
3。
2 砂芯的定位结构 (23)3。
3.3 芯骨设计 (23)3.3.4 砂芯的排气 (23)3。
4浇注系统及冒口,冷铁,出气孔的设计 (24)3。
4.1 浇注系统的类型和应用范围 (24)3。
4。
2 确定内浇道在铸件上的位置、数目、金属引入方向 (24)3.5决定直浇道的位置和高度 (25)3.5.1 计算内浇道截面积 (25)3.5.2 计算横浇道截面积 (26)3。
5。
3 计算直浇道截面积 (27)3。
5.4 冒口的设计 (27)4 铸造工艺装备设计 (28)4。
1模样的设计 (28)4。
1.1 模样材料的选用 (28)4.1。
2 金属模样尺寸的确定 (29)4。
1。
3 壁厚与加强筋的设计 (29)4。
1。
4 金属模样的技术要求 (29)4.1。
5 金属模样的生产方法 (29)4.2模板的设计 (30)4。
2。
1 模底板材料的选用 (30)4.2。
铸造工艺说明书
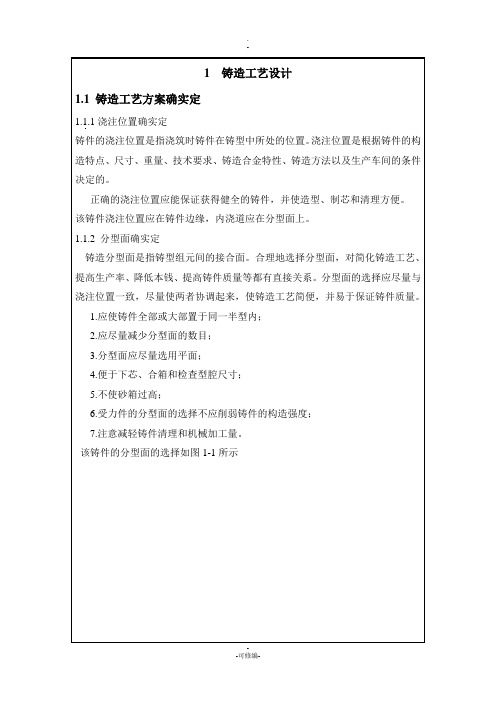
6.浇注系统构造应当简单、可靠,减少金属液消耗,便于清理。
1.4.2灰铸铁浇注系统尺寸确实定
浇注面积可由式(1-1)阻流截面法确定:
式(1-1)
式中: —浇注系统最小截面积 ;
—流经 截面的金属液总重量〔Kg〕;
—流量损耗系数;
—浇铸时间〔s〕;
—平均净压力头高度〔cm〕。
根据零件要求,起模斜度 。
1.2.4最小铸出孔槽
机械零件上往往有很多孔、槽和台阶,一般应尽可能在铸造时铸出。这样既可节约金属、减少机械加工量、降低本钱,又可使铸件壁厚比拟均匀,减少形成缩孔、缩松等铸造缺陷的倾向。但是当铸件上的孔、槽尺寸太小,而铸件的壁厚又较厚和金属压力较高时,反而会使铸件产生粘砂,造成清理和机械加工困难。有的孔、槽必须采用复杂而难度较大的工艺措施才能铸出,而实现这些措施还不如用机械加工的方法制出更为方便和经济。有时由于孔距要求很准确,铸出的孔如有偏心,就很难保证加工精度。因此在确定零件上的孔和槽是否铸出时,必须既考虑到铸出这些孔和槽的可能性,又要考虑到铸出这些孔和槽的必要性和经济性。
[2].王文清,李魁盛.铸造工艺学.机械工业.2002
[3].?砂型铸造工艺及工装设计?联合编写组.砂型铸造工艺及工装设计..1980
2.芯盒必须具有足够的强度、刚度和耐磨性,在正常操作下,到达要求的使用寿命;
3.确保芯盒的何形状和尺寸精度到达工艺要求;
4.尽可能减轻芯盒的重量,以降低能耗和工人的劳动强度;
5.适用放便、制造简单、降低本钱;
6.应满足选用的制芯设备的装配和操作要求。
金属芯盒的设计依据是产品零件图、铸造工艺图〔包括芯头的形状尺寸、芯盒中砂芯的数量、通气针的尺寸及同期方式等〕、生产批量、制芯设备的技术规格以及工装加工条件等。
铸造工艺学课程设计说明书
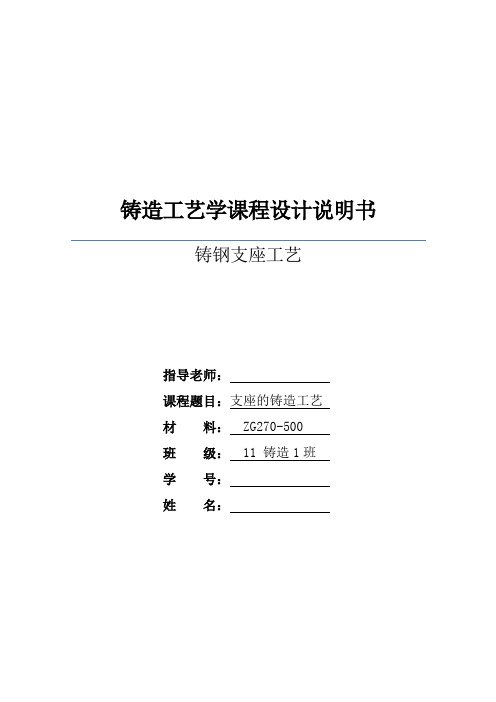
铸造工艺学课程设计-铸钢支座工艺
设计要求: 1 用 CAD 绘制符合国家制图标准的铸件零件二维三视图,经过指导老师检 查合格打印出图,图纸采用 A0 图幅; 2 在 A0 铸件图样上用红蓝铅笔做铸造工艺设计,包括分型面、加工余量、 分型(芯)负数、拔模斜度、铸造体(线)收缩率、补正量、冷铁,浇注系统设 计、冒口设计、砂芯设计、工艺说明等;必须设计 3 种分型方案,从中选取一种 合适的方案做铸造工艺设计, 设计中冒口及浇注系统等设计须有详细的计算过程 和计算依据; 3 铸造工艺图设计完成后,根据铸造工艺图设计金属模板装配图、金属芯盒 装配图(中等难度砂芯) ,用 A2 图幅打印出图;
表22铸件质量公差数值323机械加工余量铸造工艺学课程设计铸钢支座工艺420铸件为保证其加工面尺寸和零件精度应有加工余量即在铸件工艺设计时预先增加的而后在机械加工时又被加工去的金属层厚度称为机械加工余量简称加工余量
铸造工艺学课程设计说明书
铸钢支座工艺
指导老师: 课程题目:铸钢支座的铸造工艺 课程题目:支座的铸造工艺 材 料: 材 料: ZG270-500 班 学 姓 级: 号: 名: 11 铸造 1 班
图 1.1 零件图
1 / 20
铸造工艺学课程设计-铸钢支座工艺
1 零件分析 1.1 零件结构分析 零件为支座,其零件结构如图 1.1 所示。该件结构复杂,壁厚较为均匀,长、 宽和高相差大,结构上的铸造工艺性能较为合理。 1.2 零件化学成分分析 零件为支座,其零件结构如图 1.1 所示。材料为 ZG270-500,对材料的化学 成分和机械性能要求见下表 1.1 和表 1.2。 表 1.1 ZG270-500 化学成分(%) 元素 C≤ 0.40 Si≤ 0.50 Mn≤ 0.90 S≤ 0.04 P≤ 0.04 Ni 0.30 残余元素≤ Cr Cu Mo 0.30 0.30 0.25 V 0.05
阀盖铸造工艺设计说明书

阀盖铸造工艺设计说明书
1. 工艺流程
开始>模具制造>材料准备>熔炼铸造>去毛刺>抛光>喷涂>质检>包装>完成
2. 模具制造
制作阀盖铸造所需模具,包括上、下模和中心柱。
模具要求精度高,尤其是中心柱的精度需要准确。
3. 材料准备
选用优质的高温合金材料,按照合适的比例混合,并进行称重和计量。
4. 熔炼铸造
将混合好的合金材料放入电弧炉中进行熔炼。
进行熔炼时需要加入合适的合金元素,以提高合金的性能和耐用性。
5. 去毛刺
将阀盖从模具中取出,去除表面的毛刺和凸起。
6. 抛光
对阀盖的表面进行抛光,使用不同颜色的研磨材料进行多次抛光,直到达到合适的表面光洁度。
7. 喷涂
将阀盖进行喷涂处理,使用合适的涂料,并按照要求进行喷涂厚度和油漆的颜色。
8. 质检
对阀盖进行质检,包括尺寸、表面光洁度、颜色、材料性能等方面的检查。
9. 包装
对质量合格的阀盖进行包装打包,以便运输和使用。
10. 完成
工艺流程结束,产品正式完成,准备投入使用。
铸造工艺说明书
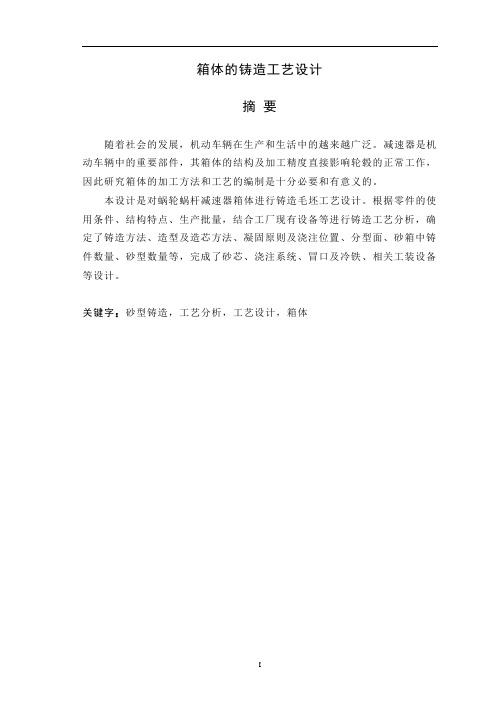
箱体的铸造工艺设计摘要随着社会的发展,机动车辆在生产和生活中的越来越广泛。
减速器是机动车辆中的重要部件,其箱体的结构及加工精度直接影响轮毂的正常工作,因此研究箱体的加工方法和工艺的编制是十分必要和有意义的。
本设计是对蜗轮蜗杆减速器箱体进行铸造毛坯工艺设计。
根据零件的使用条件、结构特点、生产批量,结合工厂现有设备等进行铸造工艺分析,确定了铸造方法、造型及造芯方法、凝固原则及浇注位置、分型面、砂箱中铸件数量、砂型数量等,完成了砂芯、浇注系统、冒口及冷铁、相关工装设备等设计。
关键字:砂型铸造,工艺分析,工艺设计,箱体目录前言................................................................. 错误!未定义书签。
第一章铸造工艺设计.. (4)§1.1 零件概述 (4)§1.1.1 零件信息 (4)§1.1.2 技术要求 (4)§1.2 铸造工艺方案的确定 (5)§1.2.1 造型、造芯方法及铸型种类的确定 (5)§1.2.2 浇注位置和分型面的确定 (5)§1.2.3 砂箱中铸件数目的确定......... 错误!未定义书签。
§1.3工艺参数的选择 (7)§1.3.1 铸造收缩率 (8)§1.3.2 机械加工余量 (8)§1.3.3 拔模斜度的确定 (8)§1.3.4 铸造圆角的确定 (8)§1.3.5 最小铸出口 (8)§1.4 浇注系统的设计 (8)§1.4.1 浇注系统的概述 (8)§1.4.2 浇注系统类型的选择 (9)§1.4.3 浇注系统的设计与计算 (10)§1.4.4 出气孔的设计 (10)§1.5 砂芯的设计 (11)§1.5.1 砂芯的概述 (11)§1.5.2 砂芯数量的确定 (11)§1.5.3 芯头的设计 (11)§1.5.4 壳芯的制备 ............................ 错误!未定义书签。
铸造工艺设计说明书

铸造工艺设计说明书一、铸造工艺设计的目的和意义铸造是将液态金属浇注到与零件形状、尺寸相适应的铸型型腔中,待其冷却凝固,以获得毛坯或零件的生产方法。
铸造工艺设计则是根据零件的结构特点、技术要求、生产批量等因素,确定铸造方法、铸型分型面、浇注系统、冒口和冷铁等工艺参数,以保证获得高质量的铸件,并提高生产效率、降低成本。
良好的铸造工艺设计具有重要意义。
首先,它能够保证铸件的质量,减少铸造缺陷的产生,如气孔、缩孔、夹渣等。
其次,合理的工艺设计可以提高生产效率,降低生产成本,缩短生产周期。
此外,还能为后续的机械加工提供良好的基础,减少加工余量,提高材料利用率。
二、零件分析1、零件结构对需要铸造的零件进行结构分析,包括形状、尺寸、壁厚均匀性等。
例如,形状复杂的零件可能需要采用复杂的分型面和浇注系统;壁厚不均匀的零件容易产生缩孔、缩松等缺陷,需要合理设置冒口和冷铁。
2、技术要求明确零件的技术要求,如材质、力学性能、表面质量等。
不同的材质和性能要求会影响铸造工艺的选择和参数的确定。
3、生产批量生产批量的大小直接影响铸造方法的选择。
大批量生产时,通常采用金属型铸造、压力铸造等高效率的铸造方法;小批量生产则多采用砂型铸造。
三、铸造方法的选择1、砂型铸造砂型铸造是应用最广泛的铸造方法,其优点是成本低、适应性强,可生产各种形状和尺寸的铸件。
但砂型铸造的生产效率较低,铸件的表面质量相对较差。
2、金属型铸造金属型铸造的生产效率高,铸件的精度和表面质量好,但模具成本高,适用于大批量生产形状简单、尺寸较小的铸件。
3、压力铸造压力铸造能生产出形状复杂、薄壁的高精度铸件,但设备投资大,主要用于生产大批量的有色金属铸件。
4、熔模铸造熔模铸造适用于生产形状复杂、精度要求高、难以机械加工的小型零件。
根据零件的结构、技术要求和生产批量,综合考虑选择合适的铸造方法。
四、铸型分型面的选择分型面的选择直接影响铸型的制造、造型操作的难易程度以及铸件的质量。
盖铸造工艺设计说明书

盖铸造工艺设计说明书1铸件构造工艺性分析1.1铸件根本情况:铸件材料为ZG310—570,铸件属半圆环厚壁零件,最大直径780mm,最小直径490mm,加工后最大壁厚210mm,最小145mm,加工后净重238Kg,铸件尺寸精度CT14,质量需符合GB/T6414—1999标准,允许深度不大的短小裂纹补焊,加工面不允许有肉眼看见的缩孔、缩松和裂纹等缺陷。
铸件属于中型铸件,属单件小批量生产性质类型。
根据零件三视图,画出铸件三维图如图1-1所示。
图1-1 铸件三维图1.2铸件构造工艺性分析铸件壁厚的适宜性分析铸件壁过薄,铸件将产生浇缺乏、冷隔、浇注流痕等铸造缺陷,铸件壁过厚,将使铸件由于冷却过慢晶粒粗大,也影响铸件的机械性能,因此对于一个具体的铸件,根据其材料与铸造方法,必须有一个最小临界壁厚才能保证其铸造工艺的实施。
由于零件属单件小批量生产类型,因此适宜的铸造方法为砂型铸造,根据材料的类型与铸件最大尺寸,查阅资料[1],从铸件尺寸来看,临界壁厚必须小于39mm,而本铸件最小壁厚为145mm,远远大于临界壁厚,所以本铸件属厚壁件,因此在铸造过程中应想法使金属液快速冷却。
铸件壁的连接过渡圆角铸件的过渡圆角过小,将使连接处产生较大的铸造应力,并有可能造成铸件开裂,对于本铸件来说,铸件尺寸大,铸件收缩亦大,从而铸造应力更大,铸件壁连接转角更易开裂,因此对铸造圆角的大小进展分析具有重要意义。
从图1-2可知,其过渡圆角查阅资料[2]可知,铸造适宜的圆角应在R50较为适宜,本铸件的过渡圆角在图中为R20,此处圆角过小,易在此处产生较大的铸造应力,导致铸件在此处开裂,因此,与厂家协商后,铸造工艺设计中按铸造圆角R50进展设计模样与芯盒。
1.3铸件可能产生的铸造缺陷本铸件属于中型半圆环厚壁铸件,对于此类铸件,铸件由于壁太厚,铸造完成后容易使晶粒粗大,以至于达不到厂家所要求的力学性能,为消除与防止这些缺陷的产生,铸件除快速浇注外,还需采用加冷铁等方法方法。
- 1、下载文档前请自行甄别文档内容的完整性,平台不提供额外的编辑、内容补充、找答案等附加服务。
- 2、"仅部分预览"的文档,不可在线预览部分如存在完整性等问题,可反馈申请退款(可完整预览的文档不适用该条件!)。
- 3、如文档侵犯您的权益,请联系客服反馈,我们会尽快为您处理(人工客服工作时间:9:00-18:30)。
铸造工艺设计说明书
一、引言
铸造工艺设计是针对特定铸件的生产过程进行规划和安排的过程。
本文旨在详细介绍铸造工艺设计的内容,确保读者能够全面理解并掌握该过程的要点。
二、铸造工艺设计的目标
铸造工艺设计的目标是实现高质量的铸件生产。
具体而言,主要包括以下几个方面:
1. 确定适宜的材料:根据铸件的要求和使用环境,选择合适的铸造材料,确保其具备良好的机械性能和耐腐蚀性能。
2. 设计合理的结构:在铸造工艺设计中,需要考虑到铸件的结构特点,合理设计铸件的形状和尺寸,以确保在铸造过程中易于铸造和冷却。
3. 确定适宜的工艺参数:通过合理选择浇注温度、保温时间、浇注速度等工艺参数,以确保铸件的成形质量。
4. 确保铸件的表面质量:通过采用适当的除砂、除气和清洁工艺,确保铸件表面的光洁度和平整度符合要求。
三、铸造工艺设计的步骤
铸造工艺设计的步骤可以分为以下几个阶段:
1. 铸件设计分析:在铸造工艺设计之前,需要对铸件的结构和形状进行分析。
通过对铸件进行结构强度分析、模具结构分析以及热力学分析等,确定铸造工艺的基本要求和技术指标。
2. 模具设计:根据铸件的形状和尺寸要求,进行模具设计。
包括模具的整体结构设计、分型面设计、模腔和冷却系统的设计等。
3. 工艺参数确定:根据铸件的特点和模具设计,确定适宜的浇注温度、浇注速度、保温时间等工艺参数。
这些参数对于保证铸件成形质量和提高生产效率具有重要作用。
4. 检验和调整:在铸造工艺设计结束后,需要进行试验验证和工艺调整。
通过对铸件进行质量检验,查找潜在问题并进行相应的调整,以确保最终生产的铸件质量达到要求。
四、铸造工艺设计的注意事项
在铸造工艺设计的过程中,需要特别注意以下几个方面:
1. 材料特性:铸造工艺设计需要充分了解所选材料的特性和性能,确保其适用于特定的铸件要求。
同时,需要根据材料的熔化温度和流动性,合理选择浇注温度和浇注系统。
2. 模具设计:模具设计需要兼顾铸件的结构特点和生产效率。
合理的模具结构和冷却系统设计,能够提高铸件的成形质量和生产效率。
3. 温度控制:在铸造过程中,需要严格控制浇注温度、保温时间和冷却速度等工艺参数。
合理的温度控制可以避免铸件产生缩孔、疏松等缺陷。
4. 质量控制:铸造工艺设计需要注重质量控制。
通过对铸件的表面质量、尺寸精度和力学性能等进行检验,确保产品质量的稳定性和一致性。
五、总结
铸造工艺设计是实现高质量铸件生产的关键环节。
通过合理的工艺参数选择和模具设计,能够确保铸件的成形质量和表面质量。
同时,质量控制和工艺调整也是铸造工艺设计中不可或缺的一部分。
只有全面理解和合理运用铸造工艺设计的原理和方法,才能有效提高铸件的生产质量和生产效率。
六、参考资料
1. 铸造工艺学. 许树基,杨兆年. 中国冶金工业出版社,2007。
2. 铸造工艺与材料. 王权,鲁俊,窦红水. 机械工业出版社,2013。
3. 铸造工艺设计与实习指导. 孙秀义,李新民,王震. 中国冶金工业出版社,2014。
以上为铸造工艺设计说明书的内容,希望能对读者理解铸造工艺设计的要点和步骤有所帮助。
通过全面把握各个环节,合理运用相关知识和技术,能够提高铸件生产的质量和效率,推动铸造行业的发展。