腐蚀管道剩余寿命预测原则
油气管道腐蚀检测及剩余寿命预测
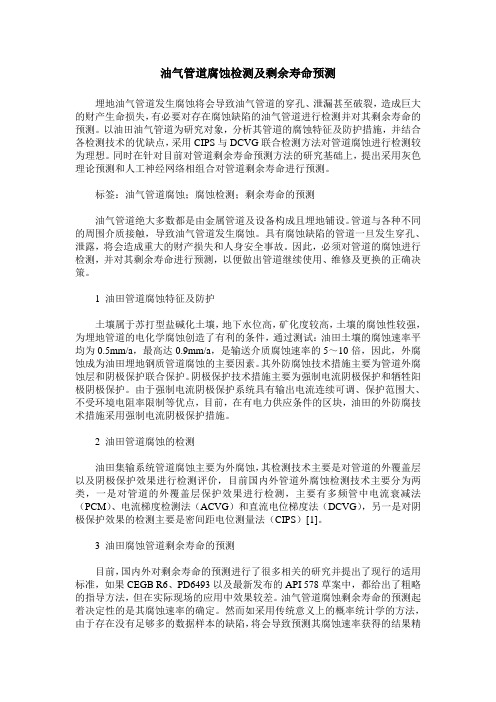
油气管道腐蚀检测及剩余寿命预测埋地油气管道发生腐蚀将会导致油气管道的穿孔、泄漏甚至破裂,造成巨大的财产生命损失,有必要对存在腐蚀缺陷的油气管道进行检测并对其剩余寿命的预测。
以油田油气管道为研究对象,分析其管道的腐蚀特征及防护措施,并结合各检测技术的优缺点,采用CIPS与DCVG联合检测方法对管道腐蚀进行检测较为理想。
同时在针对目前对管道剩余寿命预测方法的研究基础上,提出采用灰色理论预测和人工神经网络相组合对管道剩余寿命进行预测。
标签:油气管道腐蚀;腐蚀检测;剩余寿命的预测油气管道绝大多数都是由金属管道及设备构成且埋地铺设。
管道与各种不同的周围介质接触,导致油气管道发生腐蚀。
具有腐蚀缺陷的管道一旦发生穿孔、泄露,将会造成重大的财产损失和人身安全事故。
因此,必须对管道的腐蚀进行检测,并对其剩余寿命进行预测,以便做出管道继续使用、维修及更换的正确决策。
1 油田管道腐蚀特征及防护土壤属于苏打型盐碱化土壤,地下水位高,矿化度较高,土壤的腐蚀性较强,为埋地管道的电化学腐蚀创造了有利的条件,通过测试:油田土壤的腐蚀速率平均为0.5mm/a,最高达0.9mm/a,是输送介质腐蚀速率的5~10倍,因此,外腐蚀成为油田埋地钢质管道腐蚀的主要因素。
其外防腐蚀技术措施主要为管道外腐蚀层和阴极保护联合保护。
阴极保护技术措施主要为强制电流阴极保护和牺牲阳极阴极保护。
由于强制电流阴极保护系统具有输出电流连续可调、保护范围大、不受环境电阻率限制等优点,目前,在有电力供应条件的区块,油田的外防腐技术措施采用强制电流阴极保护措施。
2 油田管道腐蚀的检测油田集输系统管道腐蚀主要为外腐蚀,其检测技术主要是对管道的外覆盖层以及阴极保护效果进行检测评价,目前国内外管道外腐蚀检测技术主要分为两类,一是对管道的外覆盖层保护效果进行检测,主要有多频管中电流衰减法(PCM)、电流梯度检测法(ACVG)和直流电位梯度法(DCVG),另一是对阴极保护效果的检测主要是密间距电位测量法(CIPS)[1]。
7、剩余强度评估和剩余寿命预测计算过程
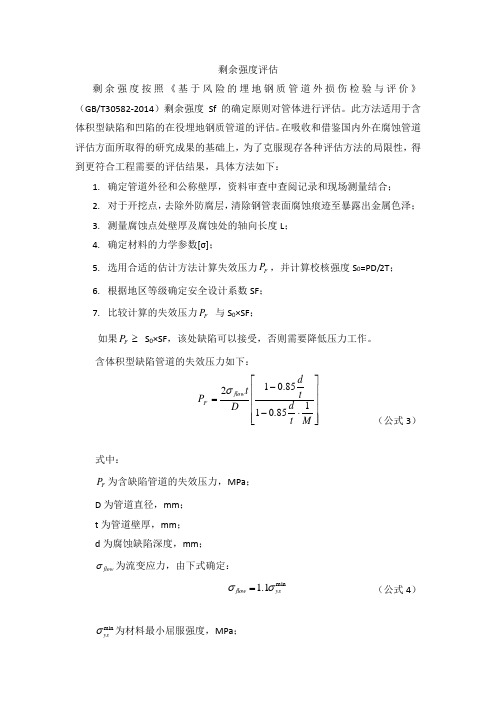
剩余强度评估剩余强度按照《基于风险的埋地钢质管道外损伤检验与评价》 (GB/T30582-2014)剩余强度Sf 的确定原则对管体进行评估。
此方法适用于含体积型缺陷和凹陷的在役埋地钢质管道的评估。
在吸收和借鉴国内外在腐蚀管道评估方面所取得的研究成果的基础上,为了克服现存各种评估方法的局限性,得到更符合工程需要的评估结果,具体方法如下:1. 确定管道外径和公称壁厚,资料审查中查阅记录和现场测量结合;2. 对于开挖点,去除外防腐层,清除钢管表面腐蚀痕迹至暴露出金属色泽;3. 测量腐蚀点处壁厚及腐蚀处的轴向长度L ;4. 确定材料的力学参数[σ];5. 选用合适的估计方法计算失效压力F P ,并计算校核强度S 0=PD/2T ;6. 根据地区等级确定安全设计系数SF ;7. 比较计算的失效压力F P 与S 0×SF ;如果≥F P S 0×SF ,该处缺陷可以接受,否则需要降低压力工作。
含体积型缺陷管道的失效压力如下:(公式3)式中:F P 为含缺陷管道的失效压力,MPa ;D 为管道直径,mm ;t 为管道壁厚,mm ;d 为腐蚀缺陷深度,mm ;flow σ为流变应力,由下式确定:(公式4)min ysσ为材料最小屈服强度,MPa ; ⎥⎥⎥⎥⎦⎤⎢⎢⎢⎢⎣⎡⋅--=M t d t d D t P flow F 185.0185.012σmin 1.1ys flow σσ=M 为Folias 膨胀系数,由下式确定: 50)/(2>Dt L (公式5) 50)/(2≤Dt L (公式6)L 为缺陷长度,mm 。
管道运行压力不得超过最大允许工作压力,最大允许工作压力为:F P K p ⋅=p 为管道最大允许工作压力,MPa ;K 为设计系数,应根据管道内的介质类型、缺陷及所在处的地区级别等确定。
本次受检埋地管道共发现防腐层漏电点21处。
受检单位对15个已打孔检漏处理的漏电点处进行了燃气泄漏检测,结果未发现燃气泄漏;对4处漏电点进行了开挖修复;其余2处漏电点处于水中,无法打孔检漏,观察水面未发现泄漏气泡。
腐蚀管道的失效概率和剩余寿命预测方法

对于埋地管道 ,腐蚀导致管壁减薄和引起局部 应力集中 ,是影响系统可靠性及使用寿命的关键因 素 ,由于存在着许多不确定因素 ,管道失效概率和腐 蚀剩余寿命的预测工作有很大难度 。最近的研究结 果表明 ,可靠性评估方法不失为一种理想的失效概 率和腐蚀剩余寿命的预测方法 。
-
n
∑
i=1
-
5g
5
∧
xi
P 3 ·x∧i3
+ g σ x∧13 x1 +μx1 , …, x∧n3σx n +μx n
=0
n
∑
i=1
5g
5
∧
xi
P3
2
n
∑
5g
i =1 5 xi
P3
2
(14)
式 (14) 第二项的绝对值即坐标原点 0′至切平 面的最短距离β, 点 P3 ( x∧13 , x∧23 …, x∧n3 ) 在极限状
+μx2
,
…,
σ ∧
x n xn
+μxn )
= 0 。该方程表示在
新坐标系下的极限状态超曲面中 ( 见图 1) , 该曲面
将
∧
xi
空间分为安全区和失效区
。
图 1 可靠度与极限状态曲面的关系
由新坐标系的原点 0′向极限状态曲面引一条
垂线 ,交曲面上一点
P3
∧∧
( x1 , x2 ,
…,
∧
xn
)
, 该交点称
图 3 可靠性指标与管道服役时间的关系
图 2 一阶二次矩方法求解β程序框图
三 、工程实例
我国北方某管道钢管为 16Mn 螺旋焊管 ,屈服 强度为 353 M Pa ,管径为 529 mm ,壁厚为 7 mm ,已 运行近 30 年 。根据工程的需要 ,对该管道进行了安
埋地输油管道腐蚀原因分析及剩余寿命预测方法概述
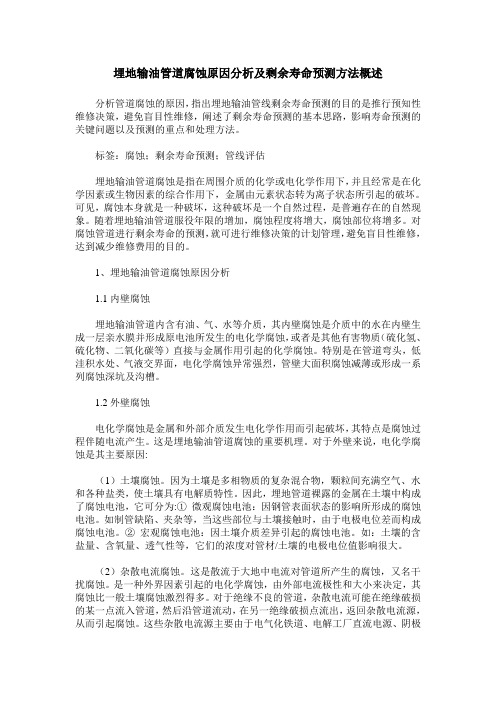
埋地输油管道腐蚀原因分析及剩余寿命预测方法概述分析管道腐蚀的原因,指出埋地输油管线剩余寿命预测的目的是推行预知性维修决策,避免盲目性维修,阐述了剩余寿命预测的基本思路,影响寿命预测的关键问题以及预测的重点和处理方法。
标签:腐蚀;剩余寿命预测;管线评估埋地输油管道腐蚀是指在周围介质的化学或电化学作用下,并且经常是在化学因素或生物因素的综合作用下,金属由元素状态转为离子状态所引起的破坏。
可见,腐蚀本身就是一种破坏,这种破坏是一个自然过程,是普遍存在的自然现象。
随着埋地输油管道服役年限的增加,腐蚀程度将增大,腐蚀部位将增多。
对腐蚀管道进行剩余寿命的预测,就可进行维修决策的计划管理,避免盲目性维修,达到减少维修费用的目的。
1、埋地输油管道腐蚀原因分析1.1内壁腐蚀埋地输油管道内含有油、气、水等介质,其内壁腐蚀是介质中的水在内壁生成一层亲水膜并形成原电池所发生的电化学腐蚀,或者是其他有害物质(硫化氢、硫化物、二氧化碳等)直接与金属作用引起的化学腐蚀。
特别是在管道弯头,低洼积水处、气液交界面,电化学腐蚀异常强烈,管壁大面积腐蚀减薄或形成一系列腐蚀深坑及沟槽。
1.2外壁腐蚀电化学腐蚀是金属和外部介质发生电化学作用而引起破坏,其特点是腐蚀过程伴随电流产生。
这是埋地输油管道腐蚀的重要机理。
对于外壁来说,电化学腐蚀是其主要原因:(1)土壤腐蚀。
因为土壤是多相物质的复杂混合物,颗粒间充满空气、水和各种盐类,使土壤具有电解质特性。
因此,埋地管道裸露的金属在土壤中构成了腐蚀电池,它可分为:①微观腐蚀电池:因钢管表面状态的影响所形成的腐蚀电池。
如制管缺陷、夹杂等,当这些部位与土壤接触时,由于电极电位差而构成腐蚀电池。
②宏观腐蚀电池:因土壤介质差异引起的腐蚀电池。
如:土壤的含盐量、含氧量、透气性等,它们的浓度对管材/土壤的电极电位值影响很大。
(2)杂散电流腐蚀。
这是散流于大地中电流对管道所产生的腐蚀,又名干扰腐蚀。
是一种外界因素引起的电化学腐蚀,由外部电流极性和大小来决定,其腐蚀比一般土壤腐蚀激烈得多。
腐蚀管道剩余寿命预测原则
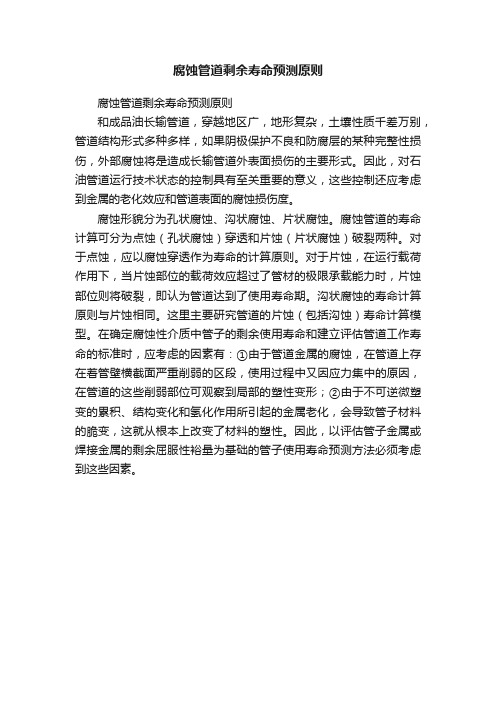
腐蚀管道剩余寿命预测原则
腐蚀管道剩余寿命预测原则
和成品油长输管道,穿越地区广,地形复杂,土壤性质千差万别,管道结构形式多种多样,如果阴极保护不良和防腐层的某种完整性损伤,外部腐蚀将是造成长输管道外表面损伤的主要形式。
因此,对石油管道运行技术状态的控制具有至关重要的意义,这些控制还应考虑到金属的老化效应和管道表面的腐蚀损伤度。
腐蚀形貌分为孔状腐蚀、沟状腐蚀、片状腐蚀。
腐蚀管道的寿命计算可分为点蚀(孔状腐蚀)穿透和片蚀(片状腐蚀)破裂两种。
对于点蚀,应以腐蚀穿透作为寿命的计算原则。
对于片蚀,在运行载荷作用下,当片蚀部位的载荷效应超过了管材的极限承载能力时,片蚀部位则将破裂,即认为管道达到了使用寿命期。
沟状腐蚀的寿命计算原则与片蚀相同。
这里主要研究管道的片蚀(包括沟蚀)寿命计算模型。
在确定腐蚀性介质中管子的剩余使用寿命和建立评估管道工作寿命的标准时,应考虑的因素有:①由于管道金属的腐蚀,在管道上存在着管壁横截面严重削弱的区段,使用过程中又因应力集中的原因,在管道的这些削弱部位可观察到局部的塑性变形;②由于不可逆微塑变的累积、结构变化和氢化作用所引起的金属老化,会导致管子材料的脆变,这就从根本上改变了材料的塑性。
因此,以评估管子金属或焊接金属的剩余屈服性裕量为基础的管子使用寿命预测方法必须考虑到这些因素。
石油集输管道腐蚀剩余预测研究
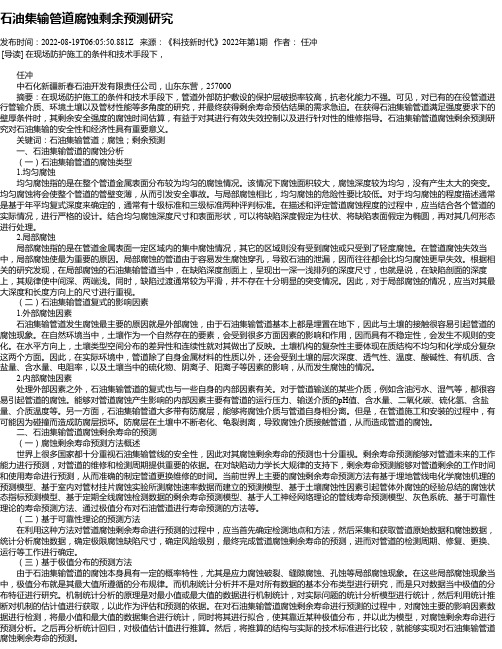
石油集输管道腐蚀剩余预测研究发布时间:2022-08-19T06:05:50.881Z 来源:《科技新时代》2022年第1期作者:任冲[导读] 在现场防护施工的条件和技术手段下,任冲中石化新疆新春石油开发有限责任公司,山东东营,257000摘要:在现场防护施工的条件和技术手段下,管道外部防护敷设的保护层破损率较高,抗老化能力不强。
可见,对已有的在役管道进行管输介质、环境土壤以及管材性能等多角度的研究,并最终获得剩余寿命预估结果的需求急迫。
在获得石油集输管道满足强度要求下的壁厚条件时,其剩余安全强度的腐蚀时间估算,有益于对其进行有效失效控制以及进行针对性的维修指导。
石油集输管道腐蚀剩余预测研究对石油集输的安全性和经济性具有重要意义。
关键词:石油集输管道;腐蚀;剩余预测一、石油集输管道的腐蚀分析(一)石油集输管道的腐蚀类型 1.均匀腐蚀均匀腐蚀指的是在整个管道金属表面分布较为均匀的腐蚀情况。
该情况下腐蚀面积较大,腐蚀深度较为均匀,没有产生太大的突变。
均匀腐蚀将会使整个管道的管壁变薄,从而引发安全事故。
与局部腐蚀相比,均匀腐蚀的危险性要比较低。
对于均匀腐蚀的程度描述通常是基于年平均复式深度来确定的,通常有十级标准和三级标准两种评判标准。
在描述和评定管道腐蚀程度的过程中,应当结合各个管道的实际情况,进行严格的设计。
结合均匀腐蚀深度尺寸和表面形状,可以将缺陷深度假定为柱状、将缺陷表面假定为椭圆,再对其几何形态进行处理。
2.局部腐蚀局部腐蚀指的是在管道金属表面一定区域内的集中腐蚀情况,其它的区域则没有受到腐蚀或只受到了轻度腐蚀。
在管道腐蚀失效当中,局部腐蚀使最为重要的原因。
局部腐蚀的管道由于容易发生腐蚀穿孔,导致石油的泄漏,因而往往都会比均匀腐蚀更早失效。
根据相关的研究发现,在局部腐蚀的石油集输管道当中,在缺陷深度剖面上,呈现出一深一浅排列的深度尺寸,也就是说,在缺陷剖面的深度上,其规律使中间深、两端浅。
同时,缺陷过渡通常较为平滑,并不存在十分明显的突变情况。
腐蚀管道剩余寿命预测方法

中 图 分 类 号 :E 8 T 8 文 献 标 识 码 : A 文 章 编 号 :04 64 20 )5 0 7 0 10 —9 1(060 —0 3 — 3
Ab ta t B s d o e rl b ly te r , rs n e e to rte rmann f rdcin o o rd d p p l e T e meh d s r c : a e n t ei it h o y p ee td a n w meh d f e iig l ep e it fc r e i ei . h t h a i o h i o o n o
icu e s bi ig tel t a efn t n o or d d p p l e h r b b ly ds iu i d l f aibe u h a o rs n v lc n l s e t l hn mi d s t ci f r e iei ,tep o a i t it b t n mo e o r lss c sc r i e . d a s h i e l u o c o n i r o s v a oo o i n h al ep o a i t r eibl yv r e 8 lie t fc r d d pp l e h e iig le p n o o rd d pp l e( 3 b t a d te fi r r b b ly o l i t es t  ̄'e me o or e iei .T e rmann fs a f ro e iei  ̄ 1 e y u i r a i e h v i o n i c n 8 c luae . sln s te a c pa l alr rb bl y O ag t eibly i d tr n d a c r ig t h n io me tlc n i o s a d ac ltd a g a h c e tbe fi e p o a i t r tre l i t s e mie c o dn o t e e vrn na o dt n n o u i r a i e i
输油管道腐蚀缺陷评估与剩余寿命预测

蚀 速 率计 算 公 式 。 结合 容 限尺 寸模 型对 腐蚀 缺 陷部位 的剩 余 强度 进 行 了评 价 ,采 用概 率 的 方 法
对局部管道进行 了失效概率的预测计算。结果表 明:该输 油管道 的腐蚀较 为严重 ,在 目前的工 作压力下,管段 上的中度缺 陷有一定的安全余量 ,对管道的安全操作不构成威胁 ;但在设 计压 力下 ,一 些 中度 缺 陷 的剩余 强度 不 能满 足要 求 ,需要 进一 步评 估 。
第3 4 卷第 8 期 ( 2 0 1 5 . 0 8 )( 试验 研 究)
输油管道腐蚀缺陷评估与剩余寿命预测
代辉 ’ 杨磊 李涛。 田知 密 徐 方
1长庆 油 田采油 八 厂 2新 疆 油 田分 公 司 陆梁油 田作 业 区 3新疆 油 田分公 司石西 服极 限 ( MP a ) 。
2 腐蚀缺 陷的评估
2 . 1 剩 余强 度评 估 方法
2 . 2 容 限尺 寸 曲线
管道设计压力为 6 MP a ,当前工作 压力为 4 . 6 MP a ,
管道的腐蚀主要受环境和结构因素的影 响,缺 比设 计压力低 。图 2 为建立 的管 道 的容 限尺寸 曲 陷 的长 度 和 深度 是 估 算 失 效 程 度 的两 个 关 键 参 数 。 线 ,在 曲线 下 方为 安全 区域 ,如 果 缺 陷位置 在 曲线 图1 所示为理想缺陷的截面示意图闭 。 以下 ,说明该缺陷可在管道容忍 的位置上 ,即正常
式 中 为 管 材 的流 变应 力 ( MP a ) ; D为 直 径 也就是在管道 的上顶部附近 ;绝大部分缺陷集 中在 ( mm) ;t 为壁 厚 ( mm) ; d为 缺 陷深 度 ( m i l 1 ) ;Z 中 间 ,即管 道 下 部 4  ̄ 7 时钟 点位 置 ,这是 由于底 部 为 缺 陷长度 ( mm) ; M 为 鼓胀 因子 ; S MY S为对 管 的管道容易积水 ,从而导致电化学腐蚀的缘故 。
油气管道腐蚀剩余寿命的预测方法
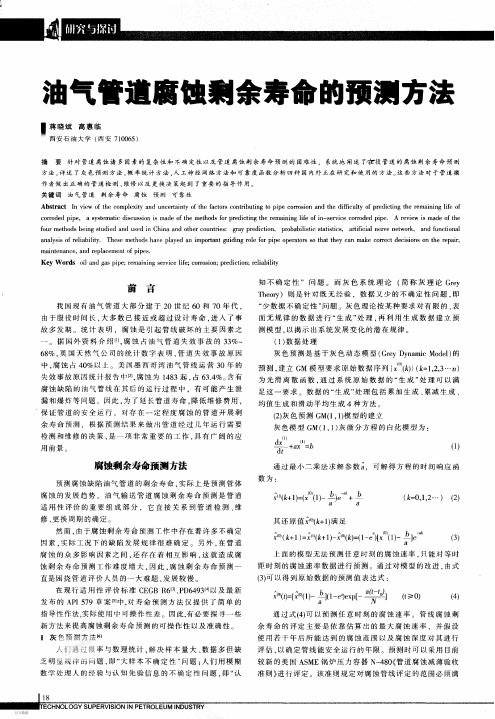
一介
一 1‘. }
件 、 一
一 、 l一
\
\
介
气
厂一. 卜
公
}
/
尸
、
卞
尹
卜
、护
对于管道腐蚀这样的复杂系统 , 采用概率论的方法在一 定程度上有一定的准确性。同时采用概率统计方法可以得 到管线表面上最大蚀坑深度 ,这种实测加统计的方法具有 较高的科学性 ,可为管道腐蚀剩余寿命的评估提供可靠的
足以下条件:
「
0 t - 0 7t ., t . 5 3- , 8 _ , ; 式中, , t w为正常时管道的壁厚 , 即原设计时无腐蚀的壁
久 -
厚,为 t 评定寿 , 命时的 最大腐蚀坑深度剩余壁厚。 根据灰色
预测方法计算所得的任意时刻的腐蚀速率 ,就能确定出任 意时刻的最大腐蚀坑深度剩余壁厚 , 同时采用提供的准则 , 我们就能很清晰地评判腐蚀油气管道剩余寿命 , 做出检测 、 维修或更换等决策。此方法能够评价出各种腐蚀因素对应 于管道的腐蚀程度 , 对腐蚀因素进行筛选 , 选取主要的影响 腐蚀的因素 ,配合人工神经网络方法使用能够达到较好的
人们通过概率与数理统计, 解决样本量大、 数据多但缺 乏明显规律的问题, 大样本不确定性” 即“ 问题; 人们用模糊 数学处理人的经验与认知先验信息的不确定性问题 , 认 即“
万方数据
I i '+ I "IIY I I I +l. IAe1II I I .1h /I'lYY 娜 g./II I WP I a ? lAL 1 a - . ti:tl l tJ.0I " . I ll } y 1 . .¥ l 巍 " P
(灰色预测G (, 模型的建立 M11 2 ) )
预测压力管道腐蚀剩余寿命的可靠性方法
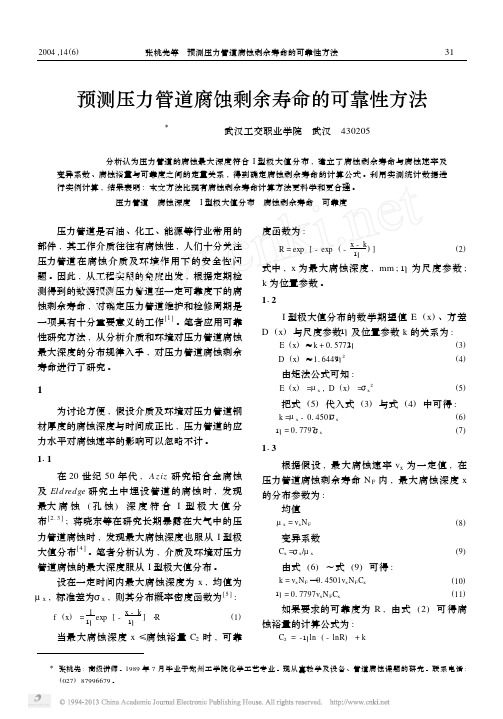
E (x) ≈k + 015772η
(3)
D (x) ≈116449η2
(4)
由矩法公式可知 :
E (x) =μx , D (x) =σx2
(5)
把式 (5) 代入式 (3) 与式 (4) 中可得 :
k =μx - 014501σx
(6)
η= 017797σx
(7)
113 腐蚀剩余寿命的计算公式
根据假设 , 最大腐蚀速率 vx 为一定值 , 在 压力管道腐蚀剩余寿命 N F 内 , 最大腐蚀深度 x 的分布参数为 :
(13)
114 可靠度与腐蚀剩余寿命
由于影响腐蚀速率的因素很多 , 因此可将压 力管道的安装地段分为低度 、中度和高度风险等
3 种 , 在不同风险地段的可靠度要求见表 1[1 ] 。
表 1 不同风险地段可接受的可靠度
地段类别 可靠度 Rσ, %
低风险 9717
中风险 9919
高风险 991999
均值
μx = vxNF
(8)
变异系数
Cx =σx/μx
(9)
由式 (6) ~式 (9) 可得 :
k = vxNF —014501vxNFCx
(10)
η= 017797vxNFCx
(11)
如果要求的可靠度为 R , 由式 (2) 可得腐
蚀裕量的计算公式为 :
C2 = - ηln ( - lnR) + k
输油管道的公称尺寸为 <273 ×6 (7) , 设计 压力 6128M Pa , 操作压力 510 ~518M Pa , 运行 温度为 56 ℃, 腐蚀裕量为 C2 = 412mm 。经过大 量的实测数据进行统计 , 得到腐蚀速率的均值 vx = 013968mm/ a , 标准差σx = 01141mm/ a 。下 面用压力管道安装在低 、中 、高风险地段中的可 靠度对腐蚀剩余寿命进行计算 。
管道剩余使用寿命的预测和评估_李桂杰
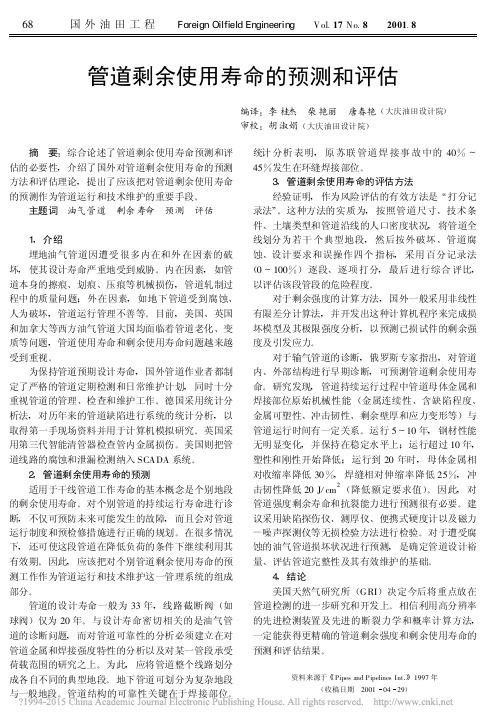
管道剩余使用寿命的预测和评估 编译:李桂杰 柴艳丽 唐春艳(大庆油田设计院)审校:胡淑娟(大庆油田设计院) 摘 要:综合论述了管道剩余使用寿命预测和评估的必要性,介绍了国外对管道剩余使用寿命的预测方法和评估理论,提出了应该把对管道剩余使用寿命的预测作为管道运行和技术维护的重要手段。
主题词 油气管道 剩余寿命 预测 评估1,介绍埋地油气管道因遭受很多内在和外在因素的破坏,使其设计寿命严重地受到威胁。
内在因素,如管道本身的擦痕、划痕、压痕等机械损伤,管道轧制过程中的质量问题;外在因素,如地下管道受到腐蚀、人为破坏,管道运行管理不善等。
目前,美国、英国和加拿大等西方油气管道大国均面临着管道老化、变质等问题,管道使用寿命和剩余使用寿命问题越来越受到重视。
为保持管道预期设计寿命,国外管道作业者都制定了严格的管道定期检测和日常维护计划,同时十分重视管道的管理、检查和维护工作。
德国采用统计分析法,对历年来的管道缺陷进行系统的统计分析,以取得第一手现场资料并用于计算机模拟研究。
英国采用第三代智能清管器检查管内金属损伤。
美国则把管道线路的腐蚀和泄漏检测纳入SCADA系统。
2,管道剩余使用寿命的预测适用于干线管道工作寿命的基本概念是个别地段的剩余使用寿命。
对个别管道的持续运行寿命进行诊断,不仅可预防未来可能发生的故障,而且会对管道运行制度和预检修措施进行正确的规划。
在很多情况下,还可使这段管道在降低负荷的条件下继续利用其有效期。
因此,应该把对个别管道剩余使用寿命的预测工作作为管道运行和技术维护这一管理系统的组成部分。
管道的设计寿命一般为33年,线路截断阀(如球阀)仅为20年。
与设计寿命密切相关的是油气管道的诊断问题,而对管道可靠性的分析必须建立在对管道金属和焊接强度特性的分析以及对某一管段承受荷载范围的研究之上。
为此,应将管道整个线路划分成各自不同的典型地段。
地下管道可划分为复杂地段与一般地段。
管道结构的可靠性关键在于焊接部位。
集输管道腐蚀期限预测方法研究
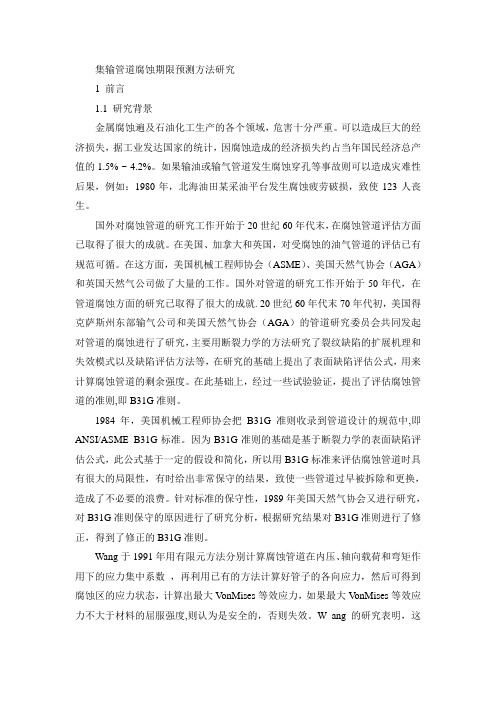
集输管道腐蚀期限预测方法研究1 前言1.1 研究背景金属腐蚀遍及石油化工生产的各个领域,危害十分严重。
可以造成巨大的经济损失,据工业发达国家的统计,因腐蚀造成的经济损失约占当年国民经济总产值的1.5% ~ 4.2%。
如果输油或输气管道发生腐蚀穿孔等事故则可以造成灾难性后果,例如:1980年,北海油田某采油平台发生腐蚀疲劳破损,致使123人丧生。
国外对腐蚀管道的研究工作开始于20世纪60年代末,在腐蚀管道评估方面已取得了很大的成就。
在美国、加拿大和英国,对受腐蚀的油气管道的评估已有规范可循。
在这方面,美国机械工程师协会(ASME)、美国天然气协会(AGA)和英国天然气公司做了大量的工作。
国外对管道的研究工作开始于50年代,在管道腐蚀方面的研究已取得了很大的成就. 20世纪60年代末70年代初,美国得克萨斯州东部输气公司和美国天然气协会(AGA)的管道研究委员会共同发起对管道的腐蚀进行了研究,主要用断裂力学的方法研究了裂纹缺陷的扩展机理和失效模式以及缺陷评估方法等,在研究的基础上提出了表面缺陷评估公式,用来计算腐蚀管道的剩余强度。
在此基础上,经过一些试验验证,提出了评估腐蚀管道的准则,即B31G准则。
1984年,美国机械工程师协会把B31G准则收录到管道设计的规范中,即ANSI/ASME B31G标准。
因为B31G准则的基础是基于断裂力学的表面缺陷评估公式,此公式基于一定的假设和简化,所以用B31G标准来评估腐蚀管道时具有很大的局限性,有时给出非常保守的结果,致使一些管道过早被拆除和更换,造成了不必要的浪费。
针对标准的保守性,1989年美国天然气协会又进行研究,对B31G准则保守的原因进行了研究分析,根据研究结果对B31G准则进行了修正,得到了修正的B31G准则。
Wang于1991年用有限元方法分别计算腐蚀管道在内压、轴向载荷和弯矩作用下的应力集中系数,再利用已有的方法计算好管子的各向应力,然后可得到腐蚀区的应力状态,计算出最大V onMises等效应力,如果最大V onMises等效应力不大于材料的屈服强度,则认为是安全的,否则失效。
腐蚀管道剩余寿命预测方法
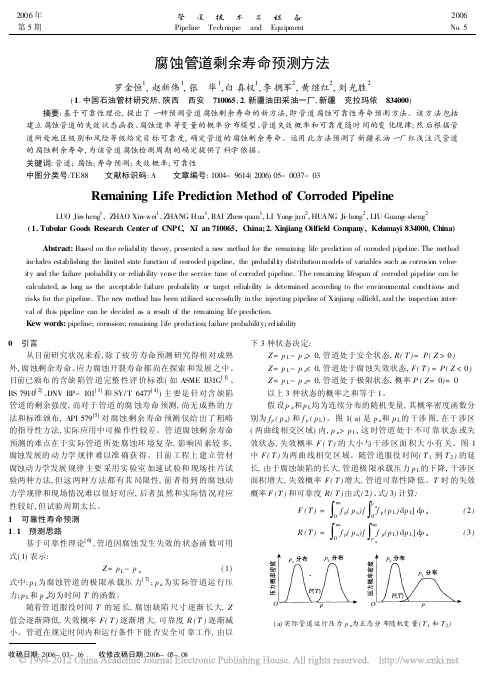
收稿日期:2006-03-16 收修改稿日期:2006-05-08腐蚀管道剩余寿命预测方法罗金恒1,赵新伟1,张 华1,白真权1,李拥军2,黄继红2,刘光胜2(1.中国石油管材研究所,陕西 西安 710065;2.新疆油田采油一厂,新疆 克拉玛依 834000)摘要:基于可靠性理论,提出了一种预测管道腐蚀剩余寿命的新方法,即管道腐蚀可靠性寿命预测方法。
该方法包括建立腐蚀管道的失效状态函数、腐蚀速率等变量的概率分布模型、管道失效概率和可靠度随时间的变化规律;然后根据管道所处地区级别和风险等级给定目标可靠度,确定管道的腐蚀剩余寿命。
运用此方法预测了新疆采油一厂红浅注汽管道的腐蚀剩余寿命,为该管道腐蚀检测周期的确定提供了科学依据。
关键词:管道;腐蚀;寿命预测;失效概率;可靠性中图分类号:TE88 文献标识码:A 文章编号:1004-9614(2006)05-0037-03Remaining Life Prediction Method of Corroded PipelineLUO Jin -heng 1,ZHAO Xin -wei 1,ZHANG Hua 1,BAI Zhen -quan 1,LI Yong -jun 2,HUANG J-i hong 2,LIU Guang -sheng 2(1.Tubular Goods Research Center of C NPC ,Xi .an 710065,C hina;2.Xinjiang Oilfield C om pany,Kelamayi 834000,China)Abstract:Based on the reliability theory,presented a new method for the remaini ng life prediction of corroded pipeline.The method includes establishing the limited state function of corroded pipeline,the probabili ty distribution models of variables such as corrosion veloc -ity and the failure probabili ty or reliability verse the service time of corroded pipeline.The remaining lifespan of corroded pipeline can be calculated,as long as the acceptable failure probability or target reliability is determined according to the environmental condi tions and risks for the pipeline.The new method has been utilized successfully in the injecting pipeline of Xinjiang oilfield,and the inspection inter -val of this pipeline can be decided as a result of the remaining life prediction.Kew words:pipeline;corrosion;remaining life prediction;failure probability;reliability 0 引言从目前研究状况来看,除了疲劳寿命预测研究得相对成熟外,腐蚀剩余寿命、应力腐蚀开裂寿命都尚在探索和发展之中。
集输管道腐蚀评价及剩余寿命预测
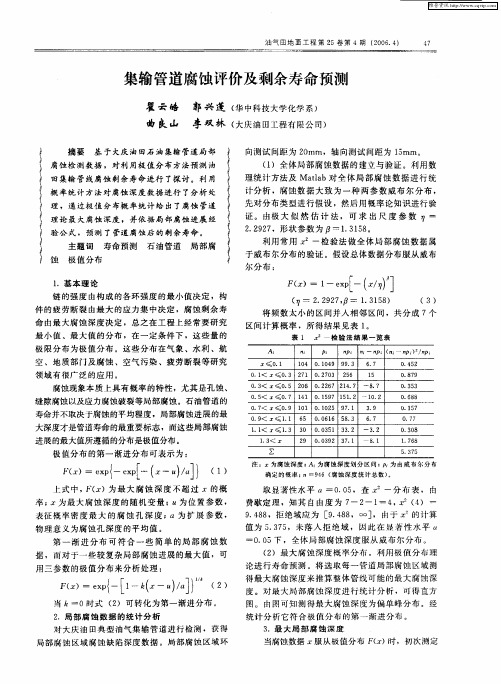
( )全 体局部 腐蚀数 据 的建立与验 证 。利 用数 1 理统 计方法 及 Malb对 全 体局 部 腐蚀 数 据 进行 统 t a
计分 析 ,腐 蚀数据 大 致 为 一种 两 参数 威 布尔 分 布 , 先 对分布类 型进行 假设 ,然后 用概率论 知识 进行验 证 。 由极 大 似 然 估 计 法 ,可 求 出 尺 度 参 数 刁一 2 2 2 ,形状参 数为 口一1 3 5 。 . 97 . l 8 利用 常 用
取 显著性水 平 a一0 0 ,查 。一分 布 表 ,由 .5 费歇定 理 ,知 其 自由度 为 7 2 1 ,2 4 : — — =4 . 7 ) 。( 948 . 8 ,拒绝 域应 为 [ . 8 ,。 ] 9 4 8 。 ,由于 的计 算
值为 5 3 5 . 7 ,未 落入 拒 绝域 ,凼此 在 著 性 水平 “
~ L 、 一 ,
确 定 的 概率 ; n=96 ( 蚀 深 度 统 计 总数 ) 4 腐 。
上式 中 , )为 最 大腐 蚀 深 度 不 超过 z 的概 F( 率 ; 为最 大 腐蚀 深度 的随 机变 量 ;“为位 置参 数 ,
表征 概率 密度 最 大 的腐 蚀 孑 深 度 ; L “为 扩 展 参 数 .
物理 意义 为腐 蚀孑 深度 的平均值 。 L
第 一 渐 进分 布 可 符 合 一 些 简 单 的 局部 腐 蚀 数 据 ,而对 于一些较 复杂局 部腐蚀 进展 的最大 值 ,可
=O0 F,全体 局部腐 蚀深度 服从威 布尔 分布 。 . 5一
( )最大 腐蚀深 度概 率分布 。利用极 值分 布理 2 论进 行寿命 预测 。将 选取 每一管 道局部 府蚀 区域测 得最 大腐蚀 深度来 推算整 体管线 可能 的最大腐 蚀深 度 。对最大 局部腐蚀 深度进 行 统计 分析 ,可得 直方 图。 由图可知测得 最大腐蚀 深 度为偏单 峰分布 。经 统计 分 析它符合 极值 分布 的第 一渐 进分布 。
天然气长输管道腐蚀缺陷评估与剩余寿命预测

因此,开展适合于天然气长输管道的腐蚀缺陷评估
(4)
和剩余寿命预测方法日益迫切。
本文针对某天然气长输管道腐蚀缺陷内检测数
(5)
据,对管道整体腐蚀状况进行了分析,采用Modified
B31G评价方法和Kastner评价方法,分析管道在不同
(6)
压力和厚度下剩余强度的变化,并预测管道的剩余
寿命,定制了管道修复计划。
method; kastner evaluation method
作者简介:庞洪晨 (1989-) ,男,山东临沂人,工程师,本科,主要从事天然气管道完整性管理 工作。
108
TOTAL CORROSION CONTROL VOL.33 No.12 DEC. 2019
腐蚀研究 Corrosion Research
相关信息,在不同压力和壁厚上,采用Modified B31G和Kastner评价方法计算了管道的剩余强度,
并进行了剩余寿命预测。结果表明:基于Modified B31G 评价方法,在评价维修;基于Kastner 评价方法,在评价压力3.9MPa下,没有金属
M = 0.032 L2 + 3.3, L2 > 50
(3)
Dt
Dt
1.2 Kastner评价方法 Modified B31G评价方法主要是分析缺陷长度
对管道的影响,为了解缺陷宽度对管道安全的影 响,British Gas(英国燃气公司)进行了大量水压 试验,试验结果表明Kastner法是分析此类问题的最 佳模型之一[6]。该方法的主要计算公式(4):
腐蚀研究 Corrosion Research
天然气长输管道腐蚀
缺陷评估与剩余寿命预测
庞洪晨1 杨立君2
输油管道腐蚀剩余寿命的预测
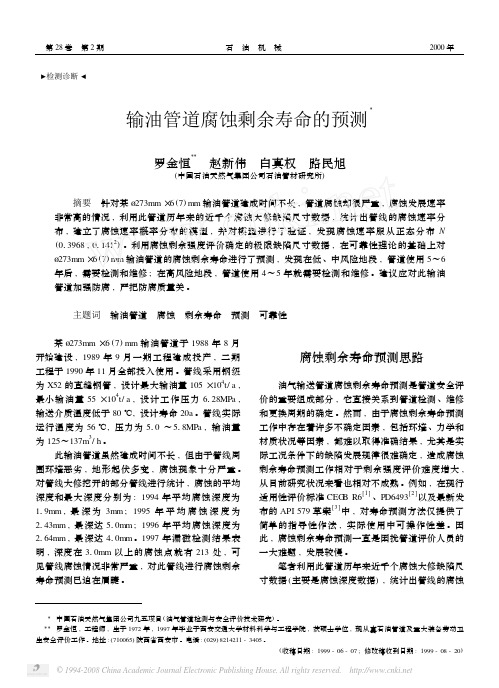
!检测诊断#输油管道腐蚀剩余寿命的预测Ξ罗金恒ΞΞ 赵新伟 白真权 路民旭(中国石油天然气集团公司石油管材研究所)摘要 针对某 273mm×6(7)mm输油管道建成时间不长,管道腐蚀却很严重,腐蚀发展速率非常高的情况,利用此管道历年来的近千个腐蚀大修缺陷尺寸数据,统计出管线的腐蚀速率分布,建立了腐蚀速率概率分布的模型,并对模型进行了验证,发现腐蚀速率服从正态分布N (013968,011412)。
利用腐蚀剩余强度评价确定的极限缺陷尺寸数据,在可靠性理论的基础上对 273mm×6(7)mm输油管道的腐蚀剩余寿命进行了预测,发现在低、中风险地段,管道使用5~6年后,需要检测和维修;在高风险地段,管道使用4~5年就需要检测和维修。
建议应对此输油管道加强防腐,严把防腐质量关。
主题词 输油管道 腐蚀 剩余寿命 预测 可靠性 某 273mm×6(7)mm输油管道于1988年8月开始建设,1989年9月一期工程建成投产,二期工程于1990年11月全部投入使用。
管线采用钢级为X52的直缝钢管,设计最大输油量105×104t/a,最小输油量55×104t/a,设计工作压力6128MPa,输送介质温度低于80℃,设计寿命20a。
管线实际运行温度为56℃,压力为510~518MPa,输油量为125~137m3/h。
此输油管道虽然建成时间不长,但由于管线周围环境恶劣,地形起伏多变,腐蚀现象十分严重。
对管线大修挖开的部分管线进行统计,腐蚀的平均深度和最大深度分别为:1994年平均腐蚀深度为119mm,最深为3mm;1995年平均腐蚀深度为2143mm,最深达510mm;1996年平均腐蚀深度为2164mm,最深达410mm。
1997年漏磁检测结果表明,深度在310mm以上的腐蚀点就有213处,可见管线腐蚀情况非常严重,对此管线进行腐蚀剩余寿命预测已迫在眉睫。
腐蚀剩余寿命预测思路油气输送管道腐蚀剩余寿命预测是管道安全评价的重要组成部分,它直接关系到管道检测、维修和更换周期的确定。
基于智能内检测的腐蚀海底管道剩余寿命评估

基于智能内检测的腐蚀海底管道剩余寿命评估张东卫,孙国民,翁强,吕建伟(海洋石油工程股份有限公司, 天津 300452)[摘 要] 腐蚀是海底管道最常见的失效形式。
本文以渤海某海底管道为例,介绍了基于多次智能内检测的腐蚀海底管道剩余强度和剩余寿命评估,对管道腐蚀原因进行了分析,对生产运行和检测提出了切实可行的建议,可有效指导油田生产。
[关键词] 海底管道;腐蚀;智能内检测;剩余强度;剩余寿命作者简介:张东卫(1985—),男,河北保定人,硕士,工程师。
研究方向为海洋工程结构设计与评估。
在现代海洋开发事业中,海洋石油开发最引人注目。
我国拥有广阔的大陆架,含有较丰富的油气资源,现已开发的海上油气田包括渤海、黄海、东海和南海的所有中国海域。
伴随着我国海上油气田的开发,海底输送管道的建设取得了长足进步。
海底管道放置在海底或埋藏在海底土壤中,会受到来自内部和外部的许多因素的破坏。
海底管道本身的擦痕、划痕、金属材料自身缺陷以及焊接缺陷是影响海底管道安全的先天缺陷。
土壤、海水、细菌和杂散电流等因素是海底管道腐蚀的外在因素。
随着海底管道使用年限的增加,管道发生腐蚀的可能性增加。
一旦发生穿孔、泄漏,将会给油田作业者带来重大经济损失和社会影响[1]。
目前,国内外已经出台了相关的腐蚀管道剩余强度评价标准和评价体系,如ASME B31G 准则、修正的B31G 准则、RSTRENG 方法、DNV-RP-F101准则以及中国石油天然气行业标准SY/T 10048《腐蚀管道评估推荐做法》等[2]。
另外,随着智能内检测技术的发展,国内海底管道的完整性管理逐渐成熟,海底管道的检测逐渐规范化。
基于内检测结果的腐蚀海底管道剩余强度和剩余寿命评估的需求日益增多。
本文以ASME B31G 规范[3][4]为基础,对渤海某海管进行了基于多次智能内检测结果的腐蚀海底管道的剩余强度和剩余寿命评估。
1 评估标准1.1 ASME B31G 准则1984年美国机械工程师协会出台了最早的腐蚀管道剩余强度评估标准ASME B31G-1984,它是评价标准的基础[2]。
腐蚀管线的剩余寿命预测

收稿日期:2003 02 17基金项目:中国石油天然气集团公司中青年创新基金项目(CX1998 27)作者简介:帅健(1963-),男(汉族),湖北黄梅人,教授,博士,博士生导师,从事工程力学及油气储运系统安全工程研究。
文章编号:1000 5870(2003)04 0091 03腐蚀管线的剩余寿命预测帅 健(石油大学机电工程学院,北京102249)摘要:预测管线的腐蚀变化趋势及腐蚀对管线结构完整性的危害是评价管线剩余寿命的关键步骤。
将影响管线剩余寿命的各种因素看成是分布各异的随机变量,建立了预测管线失效的概率数学模型。
利用这一模型,研究了腐蚀速率、缺陷深度、管道壁厚和工作压力等因素对管线可靠性的影响。
结果表明,各参数的不确定性越大,管线的可靠性越低;缺陷深度在腐蚀缺陷形成初期,对管线的可靠性有很大影响,而随着时间的推移,腐蚀速率将对管线的可靠性有较大影响。
对一条输油管线,基于管线腐蚀检测数据,对1km 长度的管道进行失效概率统计分析得到的腐蚀速率能够对管线全线的安全状况做出合理预测,从而为管线的进一步维修与检测提供参考资料。
关键词:油气管线;腐蚀;剩余寿命;失效概率;预测;数学模型中图分类号:T E 988.2,O 211.9 文献标识码:A引 言确保服役输油气管线的安全运营是实现管线高效、节能输油的关键。
然而,随着管线使用年限的增加,管线的腐蚀现象越来越严重,给管线的安全运行带来威胁。
为了预测整个管线的腐蚀情况,确知腐蚀对管线结构完整性的危害程度,有必要对腐蚀趋势进行预测,以了解管线的剩余寿命,确保管线的安全使用。
但是,由于管线腐蚀的复杂性,很难掌握各因素对腐蚀的影响规律。
采用概率统计的方法预测管线腐蚀有一定的合理性[1]。
因此,笔者建立管线失效预测的概率数学模型,对管线可靠性的影响因素进行分析。
1 数学模型描述管线腐蚀缺陷的两个基本参数是缺陷的深度和长度,腐蚀缺陷在周向的宽度对管线的承压能力影响不大,一般不须考虑。
埋地管道外腐蚀两阶段模型及其剩余寿命预测
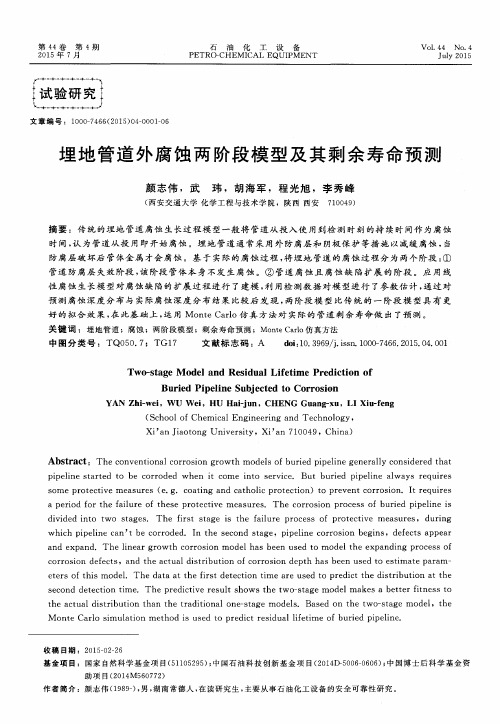
YAN Zh i — we i ,w U We i ,HU Ha i - j u n,CHENG Gu a n g - x u ,LI Xi u - f e n g
( S c h o o l o f Ch e mi c a l En g i n e e r i n g a n d Te c h n o l o g y,
时 间, 认 为 管道从 投 用即 开始腐蚀 。埋地 管道 通 常采用 外 防腐层 和 阴极 保 护等措 施 以减缓 腐蚀 , 当
防腐层破 坏后 管体 金属 才会 腐蚀 。基 于实 际的腐蚀 过程 , 将埋 地 管道 的腐蚀 过程 分 为 两个阶段 : ①
管道 防腐层 失效 阶段 , 该阶段 管体 本 身不发 生 腐蚀 。② 管道 腐蚀 且 腐 蚀 缺 陷扩 展 的 阶段 。应 用线
腐蚀管线的剩余寿命预测
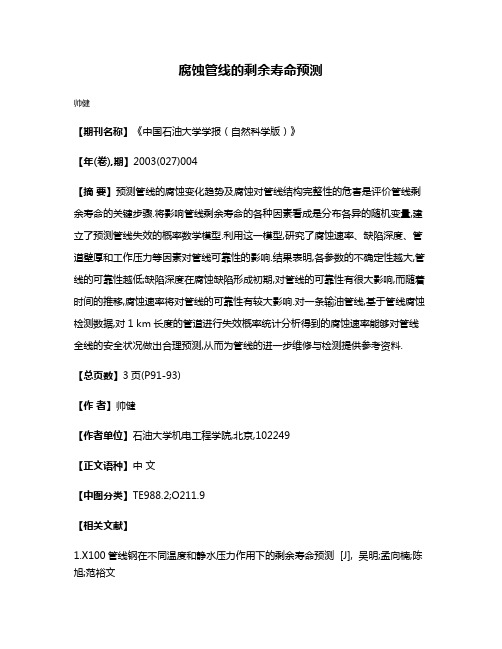
腐蚀管线的剩余寿命预测
帅健
【期刊名称】《中国石油大学学报(自然科学版)》
【年(卷),期】2003(027)004
【摘要】预测管线的腐蚀变化趋势及腐蚀对管线结构完整性的危害是评价管线剩余寿命的关键步骤.将影响管线剩余寿命的各种因素看成是分布各异的随机变量,建立了预测管线失效的概率数学模型.利用这一模型,研究了腐蚀速率、缺陷深度、管道壁厚和工作压力等因素对管线可靠性的影响.结果表明,各参数的不确定性越大,管线的可靠性越低;缺陷深度在腐蚀缺陷形成初期,对管线的可靠性有很大影响,而随着时间的推移,腐蚀速率将对管线的可靠性有较大影响.对一条输油管线,基于管线腐蚀检测数据,对1 km长度的管道进行失效概率统计分析得到的腐蚀速率能够对管线全线的安全状况做出合理预测,从而为管线的进一步维修与检测提供参考资料.【总页数】3页(P91-93)
【作者】帅健
【作者单位】石油大学机电工程学院,北京,102249
【正文语种】中文
【中图分类】TE988.2;O211.9
【相关文献】
1.X100管线钢在不同温度和静水压力作用下的剩余寿命预测 [J], 吴明;孟向楠;陈旭;范裕文
2.油气管线腐蚀剩余寿命预测研究现状分析 [J], 白真权;路民旭;赵新伟
3.基于无偏灰色马尔可夫链组合模型的管线腐蚀剩余寿命预测 [J], 王庆锋;雷兴国
4.输气管线腐蚀原因分析及剩余寿命预测 [J], 朱忠伟;李稳宏;李冬;淡勇;李俊苑;范峥;吕江;乔玉龙
5.基于改进神经网络腐蚀管线剩余寿命预测 [J], 李颜;谢飞
因版权原因,仅展示原文概要,查看原文内容请购买。
- 1、下载文档前请自行甄别文档内容的完整性,平台不提供额外的编辑、内容补充、找答案等附加服务。
- 2、"仅部分预览"的文档,不可在线预览部分如存在完整性等问题,可反馈申请退款(可完整预览的文档不适用该条件!)。
- 3、如文档侵犯您的权益,请联系客服反馈,我们会尽快为您处理(人工客服工作时间:9:00-18:30)。
腐蚀管道剩余寿命预测原则
和成品油长输管道,穿越地区广,地形复杂,土壤性质千差万别,管道结构形式多种多样,如果阴极保护不良和防腐层的某种完整性损伤,外部腐蚀将是造成长输管道外表面损伤的主要形式。
因此,对石油管道运行技术状态的控制具有至关重要的意义,这些控制还应考虑到金属的老化效应和管道表面的腐蚀损伤度。
腐蚀形貌分为孔状腐蚀、沟状腐蚀、片状腐蚀。
腐蚀管道的寿命计算可分为点蚀(孔状腐蚀)穿透和片蚀(片状腐蚀)破裂两种。
对于点蚀,应以腐蚀穿透作为寿命的计算原则。
对于片蚀,在运行载荷作用下,当片蚀部位的载荷效应超过了管材的极限承载能力时,片蚀部位则将破裂,即认为管道达到了使用寿命期。
沟状腐蚀的寿命计算原则与片蚀相同。
这里主要研究管道的片蚀(包括沟蚀)寿命计算模型。
在确定腐蚀性介质中管子的剩余使用寿命和建立评估管道工作寿命的标准时,应考虑的因素有:①由于管道金属的腐蚀,在管道上存在着管壁横截面严重削弱的区段,使用过程中又因应力集中的原因,在管道的这些削弱部位可观察到局部的塑性变形;②由于不可逆微塑变的累积、结构变化和氢化作用所引起的金属老化,会导致管子材料的脆变,这就从根本上改变了材料的塑性。
因此,以评估管子金属或焊接金属的剩余屈服性裕量为基础的管子使用寿命预测方法必须考虑到这些因素。