RAMS LCC 工程培训讲义
《RAMS培训教程》课件

总结
RAMS培训内容回顾
总结培训课程的重点内容, 加强学习效果。
RAMS在实际工程中的 应用展望
展望RAMS在未来实际工程 中的应用前景,引发思考。
Q&A
提供问答环节,解答学员的 疑问。
RAMS基础知识
可靠性分析
了解可靠性指标和定义,学习可 靠性分析的方法。
维护性分析
掌握维护性指标和定义,探索维 护性分析的方法。
安全性分析
研究安全性指标和定义,了解安 全性分析的方法。
RAMS实践案例分析
1
航空电气系统
探讨航空电气系统的可靠性、维护性和 安全性。
铁路信号系统
深入分析铁路信号系统的可靠性、维护 性和安全性。
《RAMS培训教程》PPT课件
在这个PPT课件中,我们将深入介绍RAMS(可靠性、可维护性、可用性和安 全性)的培训教程,让您轻松学习这一重要领域的知识和应用。
课程概述
RAMS是什么?
RAMS是可靠性、可维护性、可用性和安全性的 缩写,是一种综合性的工程管理方法。
RAMS在工程领域中的应用
RAMS被广泛应用于各种工程项目,包括铁路和 航空等。
1-RAMS基本概念

7
内容安排
1
RAMS/LCC 是什么? RAMS/LCC 的工作意义 RAMS/LCC 的现状和发展 RAMS/LCC 的概念解释
2 3 4 5
RAMS/LCC 的标准体系
8
购买一辆私家车
购买费用
性价比 ?
费用
使用费用
维修费用 马力 舒适性 适用性
外观
OUT
RAMS
性能
性能维持 能力
9
权衡因素
•
• •
RAMS/LCC 里程碑设定 (Creat-Update-Close)
RAMS/LCC 阶段成果确认(拒收-有条件接收-接收) RAMS/LCC 数据审查
3. 风险分析 4. 系统要求
10. 系统验收
5. 系统要求分配
9. 系统确认
6. 设计和实现
8. 安装
* From EN50126
20
7. 制造
完善的培训体系
RAMS专业咨询公司的辅助
22
国内铁路行业的RAMS/LCC 现状
• 国内轨道交通装备各企业的RAMS工程尚处于起步或初步发展阶段, 局部建立了质量与可靠性信息系统,利用各研发、生产和使用单位提 供的质量与可靠性信息进行分析和评价 • 新车型的技术合同中普遍提出了RAMS/LCC要求
国外铁路产品先进的RAMS/LCC特点
具有系统化的RAMS/LCC 标准体系 RAMS/LCC 要求是重要的设计输入 对研发的全过程进行RAMS管理 RAMS/LCC 信息化程度较高 丰富的RAMS专业资源
• •
完善的故障信息数据库 RAMS与产品设计信息的有效融合
•
可靠性预计、FMEA、FTA、LCC等软件工具得以广
1-RAMS基本概念

9. 系统确认
6. 设计和实现
8. 安装
* From EN50126
7. 制造
20
国外铁路产品先进的RAMS/LCC特点
具有系统化的RAMS/LCC 标准体系 RAMS/LCC 要求是重要的设计输入 对研发的全过程进行RAMS管理 RAMS/LCC 信息化程度较高 丰富的RAMS专业资源
• 完善的故障信息数据库 • RAMS与产品设计信息的有效融合 • 可靠性预计、FMEA、FTA、LCC等软件工具得以广
整车 信号系统
IEC 标准 EN 标准(CENELET) IRIS(国际铁路工业标准) 其他支持标准
其他分系统 设备
17
IRIS-国际铁路工业标准
ALSTOM
阿尔斯通
BOMBARDIER 庞巴迪
SIEMENS 西门子
Ansaldo Breda 安萨多布 雷达 (意大利)
EN50129
EN50126
权衡因素
购车费用 使用费用 保养费用 维修费用
10
210000 330000 264000 150000
产品的RAMS
产品特性
RAMS=可靠性+维修性+可用性+安全性
11
RAMS 的工程意义
效能
能力 可用性
12
效能
设备性能 人的能力
可靠性 维修性 保障性
RAM的目标-提高运营能力
可靠性
贮存 待命 工作
可靠性建模 可靠性预计 可靠性评估
FMECA
27
可靠性
解决问题
• 可靠性建模 • 可靠性预计 • 可靠性评估 • FMECA
可靠性分析
可靠性试验
• 可靠性研制试验 • 可靠性增长试验
编号9—3 可靠性(RAMS)培训大纲

可靠性(RAMS)培训大纲课程简介:此课程培训,学员能够全面了解铁路设施-可靠性、有效性、维修性和安全性(RAMS)的规范和认证要求,全面掌握IRIS标准中关于RAMS的要求,并帮助企业培养铁路行业RAMS技术人员和管理人员,帮助企业提升产品的可靠性、有效性、维修性和安全性研究开发水平,提高产品质量,赢得客户满意和忠诚.课程特色:1.全面了解铁路设施-可靠性、有效性、维修性和安全性(RAMS)的规范和认证要求;2.全面掌握IRIS标准中关于RAMS的要求,并帮助企业培养铁路行业RAMS技术人员和管理人员;3.帮助企业提升产品的可靠性、有效性、维修性和安全性研究开发水平,提高产品质量,赢得客户满意和忠诚.课程大纲:第一部分:RAMS 技术基础第一章:RAMS 基本概念——可靠性——故障——可用性——维修性——安全性——RAMS的关联性第二章:RAMS 工程意义——产品特性——效能——寿命周期费用——现代设计思想的转变——国外背景——国内背景——开展RAMS的急迫性第三章:RAMS 标准体系——CENELEC——其他标准第二部分:RAMS 技术要求第一章:RAMS 指标要求一、铁路产品可靠性参数体系——平均故障间隔时间-MTBF——故障率——平均首次故障时间——可靠度二、铁路产品维修性参数体系——平均修复时间——平均维修时间——平均维修间隔时间三、铁路产品可用性参数体系——可用度——固有可用度——可达可用度——工作可用度四、铁路产品安全性参数体系——平均危险故障间隔时间——平均安全系统故障间隔时间第二章:RAMS 风险控制要求——危险来源——危险的类别——危险和故障——主要概念(风险、危险严重性、危险可能性、)——风险的计算——风险控制准则——控制措施的优先次序第三章:RAMS 安全完整性要求——安全完整性等级(SIL)——EN50129 给出的SIL表第四章:故障导向安全要求——定义——应用范围第三部分:RAMS 体系框架第一章:RAMS 工程管理平台——RAMS 管理组织——RAMS 工作体系——RAMS 工作资源——RAMS大纲和计划第二章:RAMS 工作项目——RAMS 管理——RAMS 设计与分析——RAMS 试验——RAMS 验证第三章:RAMS 工作程序——产品寿命周期14步骤——寿命阶段和RAMS 任务第四章:RAMS 数据管理——FRACAS (故障报告、分析及纠正措施系统)——FRACAS 说明——RAMS 数据管理——FRACAS用途——FRACAS代表两个系统——FRACAS 流程——FRACAS故障信息的利用第五章:RAMS 实施建议第四部分:RAMS 关键技术——可靠性建模(RBD)——可靠性预计——维修性预计——可用性计算——故障模式影响与危害性分析(FMECA)——初步危险分析 (PHA)——故障树分析 (FTA)——事件树分析 (ETA)。
RAMS和LCC的培训讲义
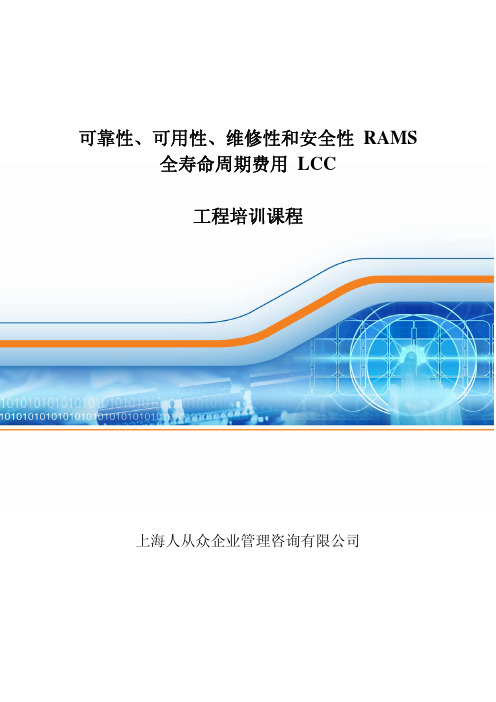
维修性 Maintainability 通过维修性工程技术在产品设计开发、生产制造、使用维护过程的应用,降低列车运 营过程中修复、维护活动 时间 和停运时间;
安全性 Safety 通过一系列的安全工程技术和管理措施,降低 事故 发生的严重性和可能性,提高运 营安全。
电话 : (8621)3368137 2
工务工程 牵引供电
远程监控系统
通信信号
调度集中系统 集中监测系统
车辆
列车网络系统
运营调度
客运服务
旅客服务系统 市场营销策划 客运组织管理
接触网系统
电话 : (8621)3368137 2
电话 : (8621)3368137 2
路基工程
现实 RAMS 差距
比较项目 RAMS 发展阶段 RAMS 标准体系 RAMS 管理体系 较为先进 系统的行业标准 完整高效的工作体系 先进的设计分析技术 RAMS 工程技术 有效的分析验证技术 稳定的持续改进能力 RAMS 应用情况 应用至产品研制、生产、运用过程 提高了产品质量保证能力 先进国家、地区 起步阶段 缺乏行业标准、指导性文件 工作体系建立阶段 设计开发仅从功能、性能考虑; 欠缺RAMS分析、验证方法、手段; 缺乏事前预防,事后改进不彻底; 部分企业建立了RAMS管理体系; 多数企业RAMS工作“两张皮”; 缺乏行业RAMS信息数据库; 其他 缺乏RAMS专业人才; 产品运营故障率高; 国内
RAMS 主要标准
Railway applications – the Specification and demonstration of EN 50126 Reliability, Availability, maintainability and Safety (RAMS) 轨道交通-可靠性、可用性、维修性和安全性规范及示例 Railway applications – Software for railway control and protection EN 50128 systems 轨道交通-铁路控制和保护系统软件 Railway applications – Safety related electronic systems for signaling 轨道交通-与安全性相关的信号传送电子系统
RAMS与LCC培训资料

生命周期成本LCC1、生命周期成本(IEC300-3,IEC60300-3-3 ):根据LCC 模型,一个产品在其生命周期内累计的模型成本。
2、生命周期成本过程:根据LCC模型,对购买和使用一个产品的总成本进行经济分析的过程。
这个分析为决定产品的设计、开发和使用提供了重要的输入。
产品供应商可以通过评估不同方案和进行比较分析研究,优化产品的设计。
也可以评估不同的运行和维修策略以优化LCC。
3、LCC由若干方面组成:-投资列车的购置成本需要的专用工具备品备件(LRU:Line Replaceable Unit)培训文件化……页脚内容1-维修预防性维修(PM:Preventive maintenance)纠正性维修(CM:Corrective maintenance)-运行成本能源(电或燃料)轨道的使用(*)运行人员(*)-生命结束成本处置成本(*)注:(*)- 这些项目一般不包括在LCC的合同中。
页脚内容23、LCC的作用:-投标-比较不同的方案-项目控制页脚内容3-成本预测-……页脚内容4可靠性Reliability1、定义(IEC50 191-02-06)可靠性指的是一个部件履行要求的功能的能力:-在给定的条件下和-在给定的时间内。
2、测量方法1)R(t), 可靠性概率: 一个部件在给定条件下、在给定的时间间隔内能够履行要求的功能的概率。
当= 常数时,t 可以是以下任何一种参数:-时间(日历时间, 车辆运行时间, 部件运行时间, 旅行时间) -运行的距离页脚内容5-工作循环或类似的.2) 故障概率F(t) = 1-R(t)3) 故障概率密度f(t) = d F(t) / d t4) 故障率= f(t) / R(t)当故障率为常数时, 即不随时间和行程变化时,= 1/MTTF, 对于不可修复部件;= 1/MTBF, 对于可修复部件;= 1/MDBF, 通常是对车辆.这里, MTTF: Mean Time To Failure到故障的平均时间MTBF: Mean Time Between Failures故障间的平均时间(指运行时间) MDBF: Mean Distance Between Failures故障间的平均行程页脚内容6注意: 一般情况下, 是随时间变化的, 譬如在运行初期和末期故障率都会比较高(浴盆曲线).MDBF是经常被作为规范使用的.MDBF = 在一段时间里的运行行程/ 这段时间总的故障次数3、故障分类(EN 50 126)1)特大故障(Significant, Immobilizing Failure)具有下列特征的故障:-产生危害和/或-列车无法移动或者导致服务延迟大于某一规定时间和/或引起成本高于某一规定水平.2)大故障(Major, Service Failure)具有下列特征的故障:-系统必须调整以达到规定的性能, 并且-不满足特大故障的条件.3)小故障(Minor)具有下列特征的故障:页脚内容7-不阻止系统达到规定的性能, 并且-不满足大故障或特大故障的条件.页脚内容8可靠性确定的例题:5辆机车在24个月内的故障情况如下表. 所有机车每月的行程为20 Tkm. 故障之后立即被修理好并返回到运行. 要求确定机车的MDBF.(24个月平均; 前12个月平均; 后12个月平均)页脚内容9页脚内容101. 用全部24个月数据: MDBF = 5*480 / 20 = 120 Tkm故障率= 1/MDBF = 0.83 次/ 100 Tkm2. 用前12个月数据:MDBF = 5*240 / 14 = 85.7 Tkm故障率= 1/MDBF = 1.17 次/ 100 Tkm3. 用后12个月数据:MDBF = 5*240 / 6 = 200 Tkm故障率= 1/MDBF = 0.5 次/ 100 Tkm4. 每辆机车的MDBF, 故障率= ?5. 行程-累计故障次数曲线页脚内容116. M(d)程序页脚内容12有效性Availability1. 定义(IEC50 191-02-05)一个部件在履行要求功能的状态的能力-在给定的条件下-在给定的时间内或在给定的时间间隔内-假定要求的外部资源已被提供.2. 有效性的测量A = 有效时间up time / (有效时间up time +无效时间down time) = up time / 总的时间total time= 1 - down time / total time有效时间up time: 部件在有效状态的时间间隔无效时间down time: 部件在无效状态的时间间隔1)固有有效性inherent availability (Ai)Ai = 纠正性维修时间/ 总的时间页脚内容13= MTBF / (MTBF + MTTR)MTBF: Mean Time Between Failure平均故障时间MTTR: Mean Time To Restoration 平均恢复时间纠正性维修时间corrective maintenance time (主动维修时间active maintenance time): -故障定位时间-零件更换时间(包括进入到更换位置)-修完后的复查时间但不包括: 服务时间, 路途时间, 休息时间和作决定的时间.2)技术有效性technical availability (At)At = (纠正性维修时间+ 预防性维修时间) / 总的时间预防性维修时间Preventive maintenance time:-维修计划中包括的安全措施和工作准备时间-纯维修时间-修完后的复查时间页脚内容14但不包括: 服务时间, 路途时间, 休息时间和作决定的时间.作为一个规则, 预防性和纠正性维修时间不包括在维修工场中修理, 大修或重新调试被更换零件的时间, 因为这不会影响到车辆的有效性. 但是如果被换下的零件修好后要被重新安装在原车辆中, 这个时间要被计入作为计算有效性.4)运行有效性Operational availability (Ao)除纠正性, 预防性维修时间之外, 还将物流和管理性延迟时间也计入无效时间.5)车辆有效性Fleet availability (Afleet)Afleet = 可运行的车辆数/ (可运行的车辆数+ 现在维修的车辆数)=可运行的车辆数/ 总的车辆数专用非有效性(special unavailability):由于纠正性维修而不有效的车辆数/ 总的车辆数一般, Ai, At, 专用非有效性会在合同中用到.页脚内容15例题:车辆每天运行18h (一年按365天计). 每年纠正性维修的时间为100h, 预防性维修的时间是200h. 请计算Ai, At.1.时间按h计算.2. 时间按天计算, 每天按24小时计.3. 时间按天计算, 每天按8小时工作时间计.页脚内容161. Ai = (18*365-100)/(18*365)=0.9848At = (18*365 -100 -200) / (18*365) = 0.95432. Ai = 1-100/24/365=0.9886At = 1- (100+200)/24/365 = 0.96573. Ai = 1-100/8/365=0.9658At = 1- (100+200)/8/365 = 0.8973页脚内容174. 如何改进车辆的有效性-改进可靠性-在合适时加大维修间隔-减少维修时间(用尽可能多的有用的工人人数, 用优化的程序)-改善可维修性(maintainability): 快速故障探测, 易进入, 很好诊断, 对更换频繁的部件很容易进入, 更换时不需重工或调整等)-将维修活动放在运行不太繁忙的时间里-将维修时间换到车辆不运行时.页脚内容18可维修性Maintainability1.定义(IEC50 191-02-07)一个部件的能力:-在给定的使用条件下-被维持在-或被恢复到-一个它能履行要求的功能的状态-当在给定的条件和使用规定的程序和资源执行维修时.2.可维修性的量测MTTR: Mean Time To Restoration平均恢复时间恢复时间具有统计分布特性, 一般用对数正态分布来表示.页脚内容19恢复Restoration: 通过更换缺陷件(LRU: Line Replaceable Unit在线可更换件)将车辆恢复到正常运行状态. 缺陷件随后在维修工场被修理.3. 恢复时间Restoration time, 主动维修时间Active maintenance time, 可维修性Maintainability可维修性可以被描述为在规定的维修和运行条件下易于服务程度和易修理程度的特性.其主要特点是:-可进入性(accessibility)-可测试性(testability)-可更换性(exchangeability)可进入性(accessibility): 要测量部件的特性或进行维修, 部件必须容易进入(人员和工具的空间, 尽可能页脚内容20少地移出其它部件).可测试性(testability): 故障之后要进行的检查要使用简单的, 不相互矛盾的测试(故障识别和定位, 即诊断的准确性).可更换性(exchangeability):故障发生后, 有缺陷的部件要用储存的备件去更换, 要没有调整和其它形式的重工.可测试性(testability): 更换缺陷部件后, 需要用另一个简单的测试去检查故障是否已被消除.因此, 可以用3个时间之和(故障定位, 更换, 复核)来表示检查和修理过程, 称为”主动维修时间” (Active maintenance time). 服务时间(可进入性)也被计入主动维修时间.主动维修时间:-故障定位时间, 包括进入-缺陷部件更换时间-复核时间页脚内容21主动维修时间也就是恢复时间, 具有统计分布特性, 一般用对数正态分布来表示. 其平均值就是MTTR(平均恢复时间) –可维修性的量测方法.4. 可维修性和维修(Maintainability & Maintenance)维修Maintenance: 所有技术性和行政性措施的组合, 包括管理措施, 其目的是维持部件在或将其恢复到能够履行要求的功能的状态.可维修性是一个部件的内在特性, 这个特性是部件制造商的职责.维修是由维修团队应用技能和资源来实施的一种活动, 这是维修者的职责.理想状况: 可维修性和维修应该彼此和谐.不理想: -差的可维修性可以被好的维修补偿掉(但有一定限度)-好的可维修性可以被差的维修所毁掉-内装式零件的好的可维修性可以被差的系统集成所毁掉页脚内容225. 可维修性的验证5.1 Sample analysis样本分析5.2 Test Restoration恢复测试可从FMEA分析中的故障里随即选取一些做试验.页脚内容23安全性Safety1.定义(IEC 50 126)Freedom from unacceptable risk. 安全性指的是免于不可接受的风险.风险: 故障后果的严重性和故障发生概率的组合.Combination of the severity of a failure consequence and the probability of occurrence of the failure.2.风险水平根据有害事件发生的严重性和其频率, 风险的水平可以分为: (IEC 50 126)-不可接受的Unacceptable-不希望的Undesirable-可忍受的Tolerable-可忽略的Negligible页脚内容24有害事件发生的频率风险水平有害事件发生的严重度低---------------------------------------------------------高风险会与下列因素相关:-乘客-运行和管理人员-铁路系统之外的人员(行人, 汽车司机)页脚内容25-维修人员-环境-铁路系统或子系统本身最基本的安全特性:-出轨-刹车和牵引力的控制-门的控制-结构损坏-碰撞(同其它车辆或铁路系统之外的东西)-防火-触电安全性不仅是一个技术问题, 也是一个运行和维修的安全程序问题. 实际上, 大部分安全问题是由于人员的错误或失误引起的.铁路系统的安全性目标是聚焦在事故预防(Error proof), 而不是减轻事故的后果.页脚内容263. 安全性的量测有害故障率(Hazarduous Failure Rate)页脚内容27预防性和纠正性维修Preventive & Corrective Maintenance1.定义(IEC50)维修: 所有技术性和行政性措施的组合, 包括管理措施, 其目的是维持部件在或将其恢复到能够履行要求的功能的状态.纠正性维修: 故障之后所实施的维修, 目的是将部件恢复到其能履行要求的功能的状态.预防性维修: 按照预先确定的间隔或根据预先定义的准则实施维修, 其目的是降低故障发生或部件功能降低的概率.2. 按照VOV6.7的维修流程图页脚内容283.维修的量测页脚内容29维修费用. 可以有多种形式:-每车每年的维修成本-每车每km的维修成本-每座每km的维修成本维修费用可分为人员成本(或man.hours)和设备成本. 维修成本是LCC的重要组成部分.注意: 维修费用在不同的运行年份可能是不同的, 如大修年份预防性维修费用可能很高; 对老的车辆的纠正性维修成本可能要远高于初始高峰故障已经过去的车辆.4. 纠正性维修成本(CM Cost)的计算是LCC分析中的重要部分.一般, 两阶段维修模型在LCC分析中被用于计算CM Cost:1)故障元件被从储存在仓库里的好的备件替换掉, 以便使车辆可以尽快地工作.2)可修理的元件(LRU)将在修理工场(CWS)中被修理; 对于不可修理的LRU, 损坏的将被处置掉, 同时备件库中增加一个LRU.页脚内容30因此, 对于可修理的LRU, 有两部分进入CM Cost:-更换有缺陷的LRU的人工成本(可维修性, 主动维修时间的成本)-在修理工场修好有缺陷的LRU的成本.对于不可修理的LRU, 下面两部分进入CM Cost:-更换有缺陷的LRU的人工成本(可维修性, 主动维修时间的成本)-新的备件的成本(适用时, 还包括处置有缺陷的LRU的成本).在LCC模型中, 每个LRU的CM Cost可以用下式计算:CMcost = 故障率*(更换时间*单位时间人工成本+ 在修理工场修理的成本包括人员成本和材料费用)这里: 故障率: 故障次数/百万km,更换时间: Man.hours,单位时间人工成本: 元/h,在修理工场修理的成本指的是-对于不可修理的LRU, 新的LRU的价格;-对于可修理的LRU, 修好有缺陷的LRU的价格.因此一个LRU每年的CM Cost为:页脚内容31CMcost,yearly = CMcost * 车辆每年的运行距离(百万km)页脚内容32例题:1.不可修理的LRU. 故障率= 4 / 百万km; 更换时间: 0.75h, 2个人; 单位时间人工成本: 50元/h; 新的LRU的价格: 480元/个; 车辆每年运行的距离: 0.08 百万km/年. 计算: 该LRU每年的纠正性维修成本(CM Cost).2. 可修理的LRU. 故障率= 2.5 / 百万km; 更换时间: 1.5h, 1个人; 单位时间人工成本: 50元/h; 新的LRU 的价格: 2500元/个; 修理费用:估计为新部件价格的15%; 车辆每年运行的距离: 0.3 百万km/年. 计算: 该LRU每年的纠正性维修成本(CM Cost).页脚内容33答案:1. CMcost,yearly = 4*(2*0.75*50 + 480) *0.08 = 177.6元/年.2. CMcost,yearly = 2.5*(1.5*50 + 2500*15%) *0.3 = 337.5元/年.注意: 维修的成本是很难准确确定的. 因为故障的类型是很多的, 尤其是在投标阶段, 很难准确了解故障类型, 修理时间. 相对来说, 更换时间可以比较准确地确定. 因此, 纠正性维修成本只能是粗略的.纠正性维修成本要在实际的运营中加以确认.页脚内容34预防性维修成本(PM Cost)的计算相对来说, 预防性维修成本的计算要简单一些. 它是基于时间间隔或行程间隔而安排的维修活动. 如: -周维修-季度维修-年度维修-每5年一次的大修-每15年一次的大修一般来说, 更长时间间隔的维修项目包括了小一些时间间隔的维修项目.平衡性维修Balanced maintenance: 指的是某个维修活动被分为几个小的部分, 每个部分在车辆不太繁忙时被实施.状态维修Condition-based maintenance(CBM): 指的是维修活动根据磨损的准则来实施. 以此维修策略制订出的预防性维修将更为经济.以可靠性为中心的维修Reliability-centred maintenance(RCM): 它是一种通过成本/性能的比较分析为基础页脚内容35的优化的成本有效性维修系统的技术. 譬如比较一个维修活动的成本和无此维修时导致的故障的成本, 从而决定维修的策略.RCM包括了功能分解, FMECA(Failure Mode Critical Effect Analysis, 故障模式关键影响分析)和决定树, 考虑了不同被选因素的相对重要性, 如安全, 故障类别, 有效性, 与CM相比较的PM的成本和CBM的有效性.页脚内容36例题车辆转向架的季度维修项目如下: (每30 Tkm)单位时间人工成本: 50元/h.计算: 一个转向架每年的预防性维修成本(PM Cost).页脚内容37答案:每季度每个预防性维修项目的成本:目视检查地刷的成本: 0.25*1*50*2=25元润滑轮轴承的成本: (0.15*1*50+2)*4=38元目视检查刹车块的成本: 0.1*1*50*4=20元因此, PMcost, yearly = (25 + 38 +20)*4 = 332元.页脚内容38LCC分析用于设计比较的例子比较两种不同设计方案的LCC.第一种方案: 现有的已在运行的情况. 部件由LRU A(1个), LRU B(2个), LRU C(2个), LRU D(1个), LRU E(3个)插接在一起组成. 各种LRU的故障率, 价格见表1. 这些LRU均是可修复的, 其修复成本均为新的备件的价格的20%.表1:第二种方案: 由于SMD技术的发展, 可以将这些LRU集成成一个LRU X. 据粗略估计, LRU X的价格约为6000元, 故障率大约为20次/(10**6h). LRU X也是可修复的, 其修复成本初步估计为新的备件的5%.请比较这两种方案的LCC(仅考虑购置成本和CM成本), 以判定新方案(第二种)是否应该研发.部件的整个生命周期在50km/h时为10百万km行程. 各种LRU(A, B, C, D, E, X)的平均故障修复时间均为0.5h, 1人. 单位时间人工成本为30元/h.页脚内容39第三种情况: 现在新的方案研发出来了, 并在实际中得到了运用. 虽然价格保持在了原来的目标(6000元), 但实际运行表明, 其故障率和故障修复成本均比预计的要高, 分别达到30次/(10**6h)和新备件价格的8%(即实际的可靠性指标和可维修性指标未能达到预期的水平). 请计算实际研发出来的LRU X的LCC.页脚内容40答案:在整个生命周期里的总的运行时间: 10*10**6 / 50 = 0.2* 10**6 h每次更换故障的LRU的成本: 0.5*1*30 = 15元第一种情况:CMcost, life cycle, LRU A = 故障率*总的运行时间*(每次更换故障LRU的成本+ 每次修好故障的LRU的成本) *部件中LRU A的数目= 6 * 0.2 * (15 + 2500*20%) * 1= 618元.CMcost, life cycle, LRU B = 4.5 * 0.2 * (15 + 750*20%) * 2= 297元.CMcost, life cycle, LRU C = 3 * 0.2 * (15 + 300*20%) * 2= 90元.CMcost, life cycle, LRU D = 5 * 0.2 * (15 + 900*20%) * 1= 195元.CMcost, life cycle, LRU E = 4 * 0.2 * (15 + 550*20%) * 3= 300元.CMcost, life cycle,整个部件= CMcost, life cycle, LRU A + CMcost, life cycle, LRU B + CMcost, life cycle, LRU C + CMcost, life cycle, LRU D + CMcost, life cycle, LRU E = 618 + 297 + 90 + 195 + 300 =1500元.部件的购置成本=2500*1 + 750*2 + 300*2 + 900*1 + 550*3 = 7150元页脚内容41整个部件的LCC = 7150 + 1500 = 8650 元.第二种情况:整个部件的LCC = 6000*1 + 20*0.2*(15 + 6000*5%)*1 = 6000 + 1260 = 7260 元< 8650元(第一种方案的LCC)因此, 应该研制新的方案.第三种情况:整个部件的LCC = 6000*1 + 30*0.2*(15 + 6000*8%)*1 = 6000 + 2970 = 8970 元> 8650元(第一种方案的LCC) > 7260元(新研制方案预估的LCC)为了准确预测故障情况, 应当使用FMEA或FTA(Fault Tree Analysis,故障树分析)分析, 以尽量降低风险. (在这个例子中是可靠性和可维修性风险).页脚内容42问题讨论:LCC方法的局限性有哪些?页脚内容43RAMS和LCC工作程序1. 作用RAMS/LCC过程的作用有三个:1) 研究故障的后果以及它们对用在风险评估中有害和其它不希望事件的影响, 以确定减少风险的措施;2) 以我们产品的可靠性性能和可维修性性能为基础计算在确定的产品生命周期内维修(纠正性维修和预防性维修)的成本.3) 用来检查在这个领域客户的要求是否被满足, 以及用于确认要求的/同意的可靠性数值, 修复时间和维修成本.2. 过程页脚内容44页脚内容45页脚内容46页脚内容47页脚内容48页脚内容493. 定义和公式(略)4. 变更EHD负责设计和验证/确认过程的变更对RAMS/LCC的影响将被检查, 并就下列方面进行评估: -针对内部和外部危害的防护机械进入电气进入过热过压火和烟环境损害-故障识别指示故障信息-功能部件的变更页脚内容50。
RAMS技术基础培训

第*页
可达可用度Aa(Achieved Availability)考虑到故障修复和预防性情况,没有考虑备件和管理延迟。 可达可用度也称为技术可用度(Technical Availability)。 有时也用作采购时合同规定的要求。
可用性参数
第*页
运行可用度Ao(Operational Availability)考虑到故障修复性和预防性情况,并考虑保障延迟。 评估机车在实际使用条件下的可用性。 运行可用度( Ao)不是制造商可控的因素。
1
次/百万公里
临修率
10
次/百万公里
千万不能搞混
例如:
寿 命: 产品能有价值存活的时间长度,是时间特性。 MTBF: 它体现了在寿命期内的发生故障的强度,是概率特性。
MTBF 不是寿命 !
产品 典型设计寿命 典型MTBF 继电器 15,000 次 55,000 次 按钮 3 million 12 million 电视机 15 years 68 years 人 (71,74)年 39年
EN50126 1999年
IEC62278 2002年
GB/T 21562 2008年
EN50126-2 2006年
EN50126-3 2004年,2007年
IRIS 2010
EN50128 2001年
EN50129 2001年
方 针
要 求
指 南
RAMS 是产品质量的核心
IRIS ALSTOM 阿尔斯通 BOMBARDIER 庞巴迪 SIEMENS 西门子 Ansaldo Breda 安萨多布雷达 (意大利)
临修故障
相邻两次检修期间,机车运用过程中发生事故或零部件出现故障,没有造成机破,但不得不进行修理的故障。
RAMS与LCC培训资料
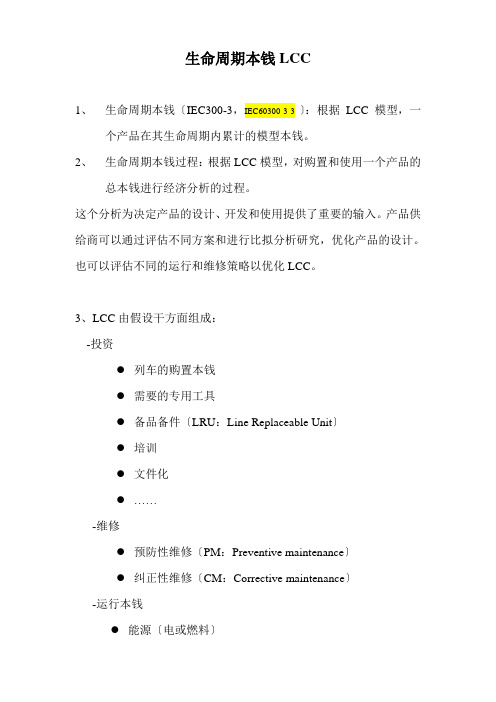
生命周期本钱LCC1、生命周期本钱〔IEC300-3,IEC60300-3-3 〕:根据LCC模型,一个产品在其生命周期内累计的模型本钱。
2、生命周期本钱过程:根据LCC模型,对购置和使用一个产品的总本钱进行经济分析的过程。
这个分析为决定产品的设计、开发和使用提供了重要的输入。
产品供给商可以通过评估不同方案和进行比拟分析研究,优化产品的设计。
也可以评估不同的运行和维修策略以优化LCC。
3、LCC由假设干方面组成:-投资●列车的购置本钱●需要的专用工具●备品备件〔LRU:Line Replaceable Unit〕●培训●文件化●……-维修●预防性维修〔PM:Preventive maintenance〕●纠正性维修〔CM:Corrective maintenance〕-运行本钱●能源〔电或燃料〕●轨道的使用〔*〕●运行人员〔*〕-生命结束本钱●处置本钱〔*〕注:〔*〕- 这些工程一般不包括在LCC的合同中。
3、LCC的作用:-投标-比拟不同的方案-工程控制-本钱预测-……可靠性Reliability1、定义〔IEC50 191-02-06〕可靠性指的是一个部件履行要求的功能的能力:-在给定的条件下和-在给定的时间内。
2、测量方法1)R(t), 可靠性概率: 一个部件在给定条件下、在给定的时间间隔内能够履行要求的功能的概率。
当= 常数时,t 可以是以下任何一种参数:-时间(日历时间, 车辆运行时间, 部件运行时间, 旅行时间)-运行的距离-工作循环或类似的.2) 故障概率F(t) = 1-R(t)3) 故障概率密度f(t) = d F(t) / d t4) 故障率= f(t) / R(t)当故障率为常数时, 即不随时间和行程变化时,= 1/MTTF, 对于不可修复部件;= 1/MTBF, 对于可修复部件;= 1/MDBF, 通常是对车辆.这里, MTTF: Mean Time To Failure到故障的平均时间MTBF: Mean Time Between Failures故障间的平均时间(指运行时间)MDBF: Mean Distance Between Failures故障间的平均行程注意: 一般情况下, 是随时间变化的, 譬如在运行初期和末期故障率都会比拟高(浴盆曲线).MDBF是经常被作为标准使用的.MDBF = 在一段时间里的运行行程/ 这段时间总的故障次数3、故障分类(EN 50 126)1)特大故障(Significant, Immobilizing Failure)具有以下特征的故障:-产生危害和/或-列车无法移动或者导致效劳延迟大于某一规定时间和/或引起本钱高于某一规定水平.2)大故障(Major, Service Failure)具有以下特征的故障:-系统必须调整以到达规定的性能, 并且-不满足特大故障的条件.3)小故障(Minor)具有以下特征的故障:-不阻止系统到达规定的性能, 并且-不满足大故障或特大故障的条件.可靠性确定的例题:5辆机车在24个月内的故障情况如下表. 所有机车每月的行程为20 Tkm. 故障之后立即被修理好并返回到运行. 要求确定机车的MDBF. (24个月平均; 前12个月平均; 后12个月平均)1. 用全部24个月数据:MDBF = 5*480 / 20 = 120 Tkm故障率= 1/MDBF = 0.83 次/ 100 Tkm2. 用前12个月数据:MDBF = 5*240 / 14 = 85.7 Tkm故障率= 1/MDBF = 1.17 次/ 100 Tkm3. 用后12个月数据:MDBF = 5*240 / 6 = 200 Tkm故障率= 1/MDBF = 0.5 次/ 100 Tkm4. 每辆机车的MDBF, 故障率= ?5. 行程-累计故障次数曲线6. M(d)程序有效性Availability1. 定义(IEC50 191-02-05)一个部件在履行要求功能的状态的能力-在给定的条件下-在给定的时间内或在给定的时间间隔内-假定要求的外部资源已被提供.2. 有效性的测量A = 有效时间up time / (有效时间up time +无效时间down time)= up time / 总的时间total time= 1 - down time / total time有效时间up time: 部件在有效状态的时间间隔无效时间down time: 部件在无效状态的时间间隔1)固有有效性inherent availability (Ai)Ai = 纠正性维修时间/ 总的时间= MTBF / (MTBF + MTTR)MTBF: Mean Time Between Failure平均故障时间MTTR: Mean Time To Restoration 平均恢复时间纠正性维修时间corrective maintenance time (主动维修时间active maintenance time):-故障定位时间-零件更换时间(包括进入到更换位置)-修完后的复查时间但不包括: 效劳时间, 路途时间, 休息时间和作决定的时间.2)技术有效性technical availability (At)At = (纠正性维修时间+ 预防性维修时间) / 总的时间预防性维修时间Preventive maintenance time:-维修方案中包括的平安措施和工作准备时间-纯维修时间-修完后的复查时间但不包括: 效劳时间, 路途时间, 休息时间和作决定的时间.作为一个规那么, 预防性和纠正性维修时间不包括在维修工场中修理, 大修或重新调试被更换零件的时间, 因为这不会影响到车辆的有效性. 但是如果被换下的零件修好后要被重新安装在原车辆中, 这个时间要被计入作为计算有效性.4)运行有效性Operational availability (Ao)除纠正性, 预防性维修时间之外, 还将物流和管理性延迟时间也计入无效时间.5)车辆有效性Fleet availability (Afleet)Afleet = 可运行的车辆数/ (可运行的车辆数+ 现在维修的车辆数)=可运行的车辆数/ 总的车辆数专用非有效性(special unavailability):由于纠正性维修而不有效的车辆数/ 总的车辆数一般, Ai, At, 专用非有效性会在合同中用到.例题:车辆每天运行18h (一年按365天计). 每年纠正性维修的时间为100h, 预防性维修的时间是200h. 请计算Ai, At.1.时间按h计算.2. 时间按天计算, 每天按24小时计.3. 时间按天计算, 每天按8小时工作时间计.1. Ai = (18*365-100)/(18*365)=0.98484. 如何改良车辆的有效性-改良可靠性-在适宜时加大维修间隔-减少维修时间(用尽可能多的有用的工人人数, 用优化的程序)-改善可维修性(maintainability): 快速故障探测, 易进入, 很好诊断, 对更换频繁的部件很容易进入, 更换时不需重工或调整等)-将维修活动放在运行不太繁忙的时间里-将维修时间换到车辆不运行时.可维修性Maintainability1.定义(IEC50 191-02-07)一个部件的能力:-在给定的使用条件下-被维持在-或被恢复到-一个它能履行要求的功能的状态-当在给定的条件和使用规定的程序和资源执行维修时.MTTR: Mean Time To Restoration平均恢复时间恢复时间具有统计分布特性, 一般用对数正态分布来表示.恢复Restoration: 通过更换缺陷件(LRU: Line Replaceable Unit在线可更换件)将车辆恢复到正常运行状态. 缺陷件随后在维修工场被修理.3. 恢复时间Restoration time, 主动维修时间Active maintenance time, 可维修性Maintainability可维修性可以被描述为在规定的维修和运行条件下易于效劳程度和易修理程度的特性.其主要特点是:-可进入性(accessibility)-可测试性(testability)-可更换性(exchangeability)可进入性(accessibility): 要测量部件的特性或进行维修, 部件必须容易进入(人员和工具的空间, 尽可能少地移出其它部件).可测试性(testability): 故障之后要进行的检查要使用简单的, 不相互矛盾的测试(故障识别和定位, 即诊断的准确性).可更换性(exchangeability):故障发生后, 有缺陷的部件要用储存的备件去更换, 要没有调整和其它形式的重工.可测试性(testability): 更换缺陷部件后, 需要用另一个简单的测试去检查故障是否已被消除.因此, 可以用3个时间之和(故障定位, 更换, 复核)来表示检查和修理过程, 称为〞主动维修时间〞(Active maintenance time). 效劳时间(可进入性)也被计入主动维修时间.主动维修时间:-故障定位时间, 包括进入-缺陷部件更换时间-复核时间主动维修时间也就是恢复时间, 具有统计分布特性, 一般用对数正态分布来表示. 其平均值就是MTTR(平均恢复时间) –可维修性的量测方法.4. 可维修性和维修(Maintainability & Maintenance)维修Maintenance: 所有技术性和行政性措施的组合, 包括管理措施, 其目的是维持部件在或将其恢复到能够履行要求的功能的状态.可维修性是一个部件的内在特性, 这个特性是部件制造商的职责.维修是由维修团队应用技能和资源来实施的一种活动, 这是维修者的职责.理想状况: 可维修性和维修应该彼此和谐.不理想: -差的可维修性可以被好的维修补偿掉(但有一定限度)-好的可维修性可以被差的维修所毁掉-内装式零件的好的可维修性可以被差的系统集成所毁掉5. 可维修性的验证5.1 Sample analysis样本分析5.2 Test Restoration恢复测试可从FMEA分析中的故障里随即选取一些做试验.平安性Safety1.定义(IEC 50 126)Freedom from unacceptable risk. 平安性指的是免于不可接受的风险.风险: 故障后果的严重性和故障发生概率的组合.Combination of the severity of a failure consequence and the probability of occurrence of the failure.根据有害事件发生的严重性和其频率, 风险的水平可以分为: (IEC 50 126)-不可接受的Unacceptable-不希望的Undesirable-可忍受的Tolerable-可忽略的Negligible有害事件发生的频率风险水平有害事件发生的严重度低---------------------------------------------------------高风险会与以下因素相关:-乘客-运行和管理人员-铁路系统之外的人员(行人, 汽车司机)-维修人员-环境-铁路系统或子系统本身最根本的平安特性:-出轨-刹车和牵引力的控制-门的控制-结构损坏-碰撞(同其它车辆或铁路系统之外的东西)-防火-触电平安性不仅是一个技术问题, 也是一个运行和维修的平安程序问题. 实际上, 大局部平安问题是由于人员的错误或失误引起的.铁路系统的平安性目标是聚焦在事故预防(Error proof), 而不是减轻事故的后果.3. 平安性的量测有害故障率(Hazarduous Failure Rate)预防性和纠正性维修Preventive & Corrective Maintenance1.定义(IEC50)维修: 所有技术性和行政性措施的组合, 包括管理措施, 其目的是维持部件在或将其恢复到能够履行要求的功能的状态.纠正性维修: 故障之后所实施的维修, 目的是将部件恢复到其能履行要求的功能的状态.预防性维修: 按照预先确定的间隔或根据预先定义的准那么实施维修, 其目的是降低故障发生或部件功能降低的概率.维修费用. 可以有多种形式:-每车每年的维修本钱-每车每km的维修本钱-每座每km的维修本钱维修费用可分为人员本钱(或man.hours)和设备本钱. 维修本钱是LCC的重要组成局部.注意: 维修费用在不同的运行年份可能是不同的, 如大修年份预防性维修费用可能很高; 对老的车辆的纠正性维修本钱可能要远高于初始顶峰故障已经过去的车辆.4. 纠正性维修本钱(CM Cost)的计算是LCC分析中的重要局部.一般, 两阶段维修模型在LCC分析中被用于计算CM Cost:1)故障元件被从储存在仓库里的好的备件替换掉, 以便使车辆可以尽快地工作.2)可修理的元件(LRU)将在修理工场(CWS)中被修理; 对于不可修理的LRU, 损坏的将被处置掉, 同时备件库中增加一个LRU.因此, 对于可修理的LRU, 有两局部进入CM Cost:-更换有缺陷的LRU的人工本钱(可维修性, 主动维修时间的本钱) -在修理工场修好有缺陷的LRU的本钱.对于不可修理的LRU, 下面两局部进入CM Cost:-更换有缺陷的LRU的人工本钱(可维修性, 主动维修时间的本钱)-新的备件的本钱(适用时, 还包括处置有缺陷的LRU的本钱).在LCC模型中, 每个LRU的CM Cost可以用下式计算:CMcost = 故障率*(更换时间*单位时间人工本钱+ 在修理工场修理的本钱包括人员本钱和材料费用)这里: 故障率: 故障次数/百万km,更换时间: Man.hours,单位时间人工本钱: 元/h,在修理工场修理的本钱指的是-对于不可修理的LRU, 新的LRU的价格;-对于可修理的LRU, 修好有缺陷的LRU的价格.因此一个LRU每年的CM Cost为:CMcost,yearly = CMcost * 车辆每年的运行距离(百万km)1.不可修理的LRU. 故障率= 4 / 百万km; 更换时间: 0.75h, 2个人; 单位时间人工本钱: 50元/h; 新的LRU的价格: 480元/个; 车辆每年运行的距离: 0.08 百万km/年. 计算: 该LRU每年的纠正性维修本钱(CM Cost).2. 可修理的LRU. 故障率= / 百万km; 更换时间: 1.5h, 1个人; 单位时间人工本钱: 50元/h; 新的LRU的价格: 2500元/个; 修理费用:估计为新部件价格的15%; 车辆每年运行的距离: 0.3 百万km/年. 计算: 该LRU每年的纠正性维修本钱(CM Cost).注意: 维修的本钱是很难准确确定的. 因为故障的类型是很多的, 尤其是在投标阶段, 很难准确了解故障类型, 修理时间. 相对来说, 更换时间可以比拟准确地确定. 因此, 纠正性维修本钱只能是粗略的.纠正性维修本钱要在实际的运营中加以确认.预防性维修本钱(PM Cost)的计算相对来说, 预防性维修本钱的计算要简单一些. 它是基于时间间隔或行程间隔而安排的维修活动. 如:-周维修-季度维修-年度维修-每5年一次的大修-每15年一次的大修一般来说, 更长时间间隔的维修工程包括了小一些时间间隔的维修工程.平衡性维修Balanced maintenance: 指的是某个维修活动被分为几个小的局部, 每个局部在车辆不太繁忙时被实施.状态维修Condition-based maintenance(CBM): 指的是维修活动根据磨损的准那么来实施. 以此维修策略制订出的预防性维修将更为经济.以可靠性为中心的维修Reliability-centred maintenance(RCM): 它是一种通过本钱/性能的比拟分析为根底的优化的本钱有效性维修系统的技术. 譬如比拟一个维修活动的本钱和无此维修时导致的故障的本钱, 从而决定维修的策略.RCM包括了功能分解, FMECA(Failure Mode Critical Effect Analysis, 故障模式关键影响分析)和决定树, 考虑了不同被选因素的相对重要性, 如平安, 故障类别, 有效性, 与CM相比拟的PM的本钱和CBM 的有效性.例题车辆转向架的季度维修工程如下: (每30 Tkm)单位时间人工本钱: 50元/h.计算: 一个转向架每年的预防性维修本钱(PM Cost).答案:每季度每个预防性维修工程的本钱:目视检查地刷的本钱: 0.25*1*50*2=25元润滑轮轴承的本钱: (0.15*1*50+2)*4=38元目视检查刹车块的本钱: 0.1*1*50*4=20元因此, PMcost, yearly = (25 + 38 +20)*4 = 332元.LCC分析用于设计比拟的例子比拟两种不同设计方案的LCC.第一种方案: 现有的已在运行的情况. 部件由LRU A(1个), LRU B(2个), LRU C(2个), LRU D(1个), LRU E(3个)插接在一起组成. 各种LRU的故障率, 价格见表1. 这些LRU均是可修复的, 其修复本钱均为新的备件的价格的20%.表1:第二种方案: 由于SMD技术的开展, 可以将这些LRU集成成一个LRU X. 据粗略估计, LRU X的价格约为6000元, 故障率大约为20次/(10**6h). LRU X也是可修复的, 其修复本钱初步估计为新的备件的5%.请比拟这两种方案的LCC(仅考虑购置本钱和CM本钱), 以判定新方案(第二种)是否应该研发.部件的整个生命周期在50km/h时为10百万km行程. 各种LRU(A, B, C, D, E, X)的平均故障修复时间均为0.5h, 1人. 单位时间人工本钱为30元/h.第三种情况: 现在新的方案研发出来了, 并在实际中得到了运用. 虽然价格保持在了原来的目标(6000元), 但实际运行说明, 其故障率和故障修复本钱均比预计的要高, 分别到达30次/(10**6h)和新备件价格的8%(即实际的可靠性指标和可维修性指标未能到达预期的水平). 请计算实际研发出来的LRU X的LCC.答案:在整个生命周期里的总的运行时间: 10*10**6 / 50 = 0.2* 10**6 h每次更换故障的LRU的本钱: 0.5*1*30 = 15元第一种情况:CMcost, life cycle, LRU A = 故障率*总的运行时间*(每次更换故障LRU的本钱+ 每次修好故障的LRU的本钱) *部件中LRU A的数目= 6 * 0.2 * (15 + 2500*20%) * 1= 618元.CMcost, life cycle, LRU B = 4.5 * 0.2 * (15 + 750*20%) * 2= 297元. CMcost, life cycle, LRU C = 3 * 0.2 * (15 + 300*20%) * 2= 90元. CMcost, life cycle, LRU D = 5 * 0.2 * (15 + 900*20%) * 1= 195元. CMcost, life cycle, LRU E = 4 * 0.2 * (15 + 550*20%) * 3= 300元.CMcost, life cycle,整个部件= CMcost, life cycle, LRU A + CMcost, life cycle, LRU B + CMcost, life cycle, LRU C + CMcost, life cycle, LRU D + CMcost, life cycle, LRU E = 618 + 297 + 90 + 195 + 300 =1500元.部件的购置本钱=2500*1 + 750*2 + 300*2 + 900*1 + 550*3 = 7150元整个部件的LCC = 7150 + 1500 = 8650 元.第二种情况:整个部件的LCC = 6000*1 + 20*0.2*(15 + 6000*5%)*1 = 6000 + 1260 = 7260 元< 8650元(第一种方案的LCC)因此, 应该研制新的方案.第三种情况:整个部件的LCC = 6000*1 + 30*0.2*(15 + 6000*8%)*1 = 6000 + 2970 = 8970 元> 8650元(第一种方案的LCC) > 7260元(新研制方案预估的LCC)为了准确预测故障情况, 应当使用FMEA或FTA(Fault Tree Analysis,故障树分析)分析, 以尽量降低风险. (在这个例子中是可靠性和可维修性风险).问题讨论:LCC方法的局限性有哪些?RAMS和LCC工作程序1. 作用RAMS/LCC过程的作用有三个:1) 研究故障的后果以及它们对用在风险评估中有害和其它不希望事件的影响, 以确定减少风险的措施;2) 以我们产品的可靠性性能和可维修性性能为根底计算在确定的产品生命周期内维修(纠正性维修和预防性维修)的本钱.3) 用来检查在这个领域客户的要求是否被满足, 以及用于确认要求的/同意的可靠性数值, 修复时间和维修本钱.2. 过程,3. 定义和公式(略)4. 变更EHD负责设计和验证/确认过程的变更对RAMS/LCC的影响将被检查, 并就以下方面进行评估:-针对内部和外部危害的防护●机械进入●电气进入●过热●过压●火和烟●环境损害-故障识别●指示●故障信息-功能部件的变更●供给商●型式●备件价格-变更(设计, 零件)对可维修性的影响●进入●可互换性●修复的时间检查和评估的结果必须被记录在〞图纸修改通知〞上.如果有影响, 相关的RAMS文件必须被更新, 必要的措施必须被方案并实施.。
RAMS培训讲义之三
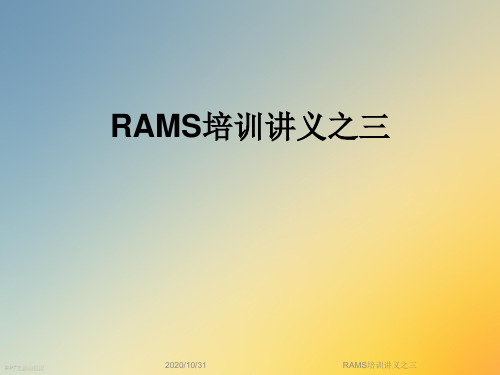
•Automatic conversion of reliability metrics
•(l)(•R = t)
e •Ln(R l= )
•-t
PPT文档演模板
•Component •Comp Rel = f (Failure Modes)
•Block-Sim Reliability Model or Scorecard Simple Series Calculation
PPT文档演模板
RAMS培训讲义之三
•可靠性预计方法
电子元器件的应力分析法
电子元器件的应力分析法已有成熟的预计标准和手册。对 于国产电子元器件,可采用国家军用标准GJB/Z299B-98 《电子设备可靠性预计手册》进行预计;而对于进口电子 元器件,可采用美国军用手册MIL-HDBK-217F《电子设备 可靠性预计》进行预计。
PPT文档演模板
RAMS培训讲义之三
串联模型举例
PPT文档演模板
RAMS培训讲义之三
•1
可靠性模型
可靠性框图为:
其数学模型为:
•EXAMPLE :
•R = 0.95 •R = 0.95 •R = 0.95
PPT文档演模板
•并联模型
RAMS培训讲义之三
并联模型的举例和特点
举例:
• 发动机四个点火器只要同时点火,其中一个点火就行 • 电路保护:两个保险丝串接(保护的角度)
•System Level
•Power supply •F/LY = 0.0031
•Control Card •F/LY = 0.0005
•Subsystem Level
•Motor •R = 0.97 •F/LY = 0.0015
[自然科学]轨道交通RAMS基本概念和参数体系
![[自然科学]轨道交通RAMS基本概念和参数体系](https://img.taocdn.com/s3/m/8f4cda89866fb84ae45c8ddd.png)
RAMS/LCC 培训教材:二〇一一年二月内容安排1 2参数及指标影响RAMS的因素3铁路产品可靠性参数体系4铁路产品维修性参数体系5 6铁路产品可用性参数体系铁路产品安全性参数体系RAMS参数体系—①参数及指标¾对于铁路产品的“系统要求”阶段,需要提出并确定系统RAMS技术要求,并形成文档,随后将系统要求分配到分系统和设备中去。
¾铁路产品各级产品的RAMS 活动都是围绕RAMS要求进行的,包括定义、分配、实现、评估和验证等活动。
¾RAMS要求分类:¾定性要求-提出了应当开展的RAMS 工作项目和工作要求,通常采用评审的方法进行确认;¾定量要求-是基于RAMS的技术参数提出的,一般通过评估和验证的方法进行确认。
RAMS参数体系—①参数及指标¾RAMS 参数是产品RAMS定量化描述的数学属性,RAMS 参数体系是某种产品RAMS 的参数的集合;¾RAMS指标是产品某一RAMS 参数的要求值,RAMS指标体系是所有RAMS 参数的要求值。
内容安排1 2参数及指标影响RAMS的因素3铁路产品可靠性参数体系4铁路产品维修性参数体系5 6铁路产品可用性参数体系铁路产品安全性参数体系RAMS参数体系—②影响RAMS的因素¾系统状态-System Conditions在系统寿命的任何阶段在系统内部引入的故障源;¾工作条件-Operating Condition在运用中施加到系统上的故障源;¾维修条件-Maintenance Condition在维护活动中施加到系统上的故障源。
RAMS 参数体系—②影响RAMS 的因素系统内故障的影响铁路应用环境干扰威胁反作用影响可靠性反作用影响安全性铁路系统功能性状态故障状态安全相关的故障模式RAMS参数体系—②影响RAMS的因素环境越恶劣可靠性越差!¾温度应力会提高产品的故障率¾振动应力会加速产品的疲劳¾湿度和化学应力会缩短产品的寿命¾环境应力和可靠性一般是指数关系:¾温度-Arrhenius¾振动-Coffin-Manson¾湿度和其他-Eyring¾因此可以根据此特性有意施加恶劣的环境应力进行试验,用以高效地暴露产品缺陷。
RAMSLCC介绍

RAMS L设C计C 质量
15
16
8
二、RAMS/LCC的意义
RAMS好,质量就好,那么质量意味着……
市场? 形象?
成本?
17
18
9
19
20
10
1 : 10 : 100 规则
1
10
100
如果未进行预防活动,那么流到下一个阶段发生的损失费用会更大. 如果在工程上检出到不良时,所损失的费用只有1USD 在顾客处发现时损失的费用会增加到10USD 最终顾客消费者处发生不良时其损失费用会上升到 100USD.
》 当前产品的可靠性水平是多少 ? 新产品的可靠性水平 又是多少?
》 对于一个未来的新产品,每年需要多少人力和资金来 处理突发故障?
》 故障处理是否有预定的流程,按流程走了吗?闭环率 是多少?
33
二、RAMS/LCC的意义
》 产品在设计评审阶段能控制风险吗?依靠“人”的因 素来控制还是依靠“程序”控制?
关键件重要件清单 工艺质量控制计划 产品验证试验计划
产品维护/修手册 产品备件清单
以后,我们该这样回答…
提出RAMS要求 RAMS协同设计 RAMS要求验证
产品设计方案 强度分析 疲劳分析 工艺分析
RAMS
可靠性分析 设计 FMECA 工艺 FMEA
RCMA 维修任务分析 保障资源分析
29
关键件重要件清单 产品验证试验计划 工艺质量控制计划 产品维护/修手册
21
第1部分 引言 (三)解决途径
22
11
23
24
12
二、RAMS/LCC的意义
RAMS/LCC
RAMS
LCC
经典RAMS技术基础培训课件

机车LCC包括初始配置费用、维护保养费用、故障维修费 用三大项。
12 10 8 6 4 2 0 飞机 汽车 机床 军事装备 轨道装备
运用维护费与购置费之比
现代设计思想的转变
性能向效能的延伸
研制费用向寿命周期费用的延伸
过去, 我们是这样回答的…
产品设计
不符合
产品设计方案
关键件重要件清单
仿真/试验
符合
强度分析
工艺质量控制计划
疲劳分析
产品验证试验计划
设计定型
工艺分析
产品维护/修手册
产品备件清单
以后,我们该这样回答…
RAMS
提出RAMS要求
可靠性分析
产品设计方案
关键件重要件清单
设计 FMECA
产品验证试验计划 强度分析
RAMS协同设计
疲劳分析
工艺 FMEA 工艺质量控制计划 RCMA
产品维护/修手册
EN50129
EN50126
IRIS的 RAMS
设计、质量、RAMS
RAMS 设计
质量
可靠性是产品质量的核心,但是质量工作不能代替可靠性工作
产品的可靠性主要是由产品的设计决定的,设计决定了产品的固有可靠性 产品可靠性工作的核心是可靠性管理 产品的可靠性是设计出来的、生产出来的、管理出来的。 ------钱学森
RAMS
RAMS/LCC
RAMS
LCC
合理的费用
RAM
高的可用性
S
高的安全性
高的效能
轨道交通产品的RAMS
RAMS
针对使用 需要定期维护吗? 多长时间需要更换? 维护的步骤是什么? 需要什么工具、消耗品? 针对故障 多长时间发生一次?
RAMS培训教材之一RAMS概念及参数

、评估和验证等活动。
RAMS要求分类:
• 定性要求-提出了应当开展的RAMS 的工作项目和工作要求,通常采用评审的方法进 行确认;
• 定量要求-是基于RAMS的技术参数提出的,一般通过评估和验证的方法进行确认。
第32页,共54页。
Reliability Center Maintainability),相当于容易发生故障的地方容易修复。
第6页,共54页。
维修性要素
可修
可修产品 - 故障 不可修产品 - 失效
能修
能检测 能定位 能到达 能更换
易修
修得快 - 定位快、维修快、确认快 修得好 - 修如旧、修如新
第二,与国际先进水平接轨的需要。
Þ 我国大量引进国外的轨道装备产品和技术;伴 随着引进,南北车集团的下属企业开始了与国 际领先公司的技术合作与配套供应,合作过程 中,作为供应链上游的国外厂商,分别对我国 内企业提出了相应的RAMS要求,强制要求进行
第28页,共54页。
现代设计思想的转变
性能向效能的延伸 采购费用向寿命周期费用的延伸
第16页,共54页。
影响RAMS的因素
系统状态-System Conditions 工作条件-Operating Condition 维修条件-Maintenance Condition
第17页,共54页。
第18页,共54页。
1.1 可靠性与环境
环境越恶劣可靠性越差
Þ 温度应力会提高产品的故障率 Þ 振动应力会加速产品的疲劳 Þ 湿度和化学应力会缩短产品的寿命
故障是危险的主要来源,危险性故障是全部故障的子集。
第11页,共54页。
RAMS系统培训

3
RAMS与质量的关系?
• 质量是一组固有特性满足要求的程度。 • 一组固有特性包括专用质量特性与通用质量特性。 • 专用质量特性:
产品的功能、性能等一组技术参数,如:机车速 度、牵引力、制动距离、能耗、噪音等。 • 通用质量特性: 保证专用质量特性有效发挥的一组共有技术特性, 如:可靠性、维修性、保障性、安全性、测试性、 环境适应性等。
GJB/Z 99-1997《系统安全工程手册》对安全的定义:不发生可能造成人 员 伤亡、职业病、设备损坏、财产损失或环境损害的状态
危险:可能导致事故的状态 GJB900 风险:用危险可能性和危险严重性表示发生事故的可能程度 风险规避方法:设计时进行风险分析,量化风险并采取措施
15
什么是危险分析?
危险分析是对产品设计、使 用以及环境有关的所有危险 进行系统化分析
RAMS知识系统性培训
1
培训内容
1
RAMS概述
2 可靠性设计准则
3
RAMS/LCC工作开展过程和管控
4
可靠性预计和分配方法
5 可靠性框图、故障树分析及DFME(C)A分析
6 后续培训内容
2
第1部分: RAMS概述
RAMS是什么?
➢ Reliability - 可靠性 ➢ Availability - 可用性 ➢ Maintainability -维修性 ➢ Safety - 安全性
于设计 + 预防性维修策略;使用可用性Ao取决于设计 + 预防性维修策 略 + 运营管理,见P15)
维修分类:1.修复性维修;2.预防性维修
8
维修性设计要求:
1.良好可达性 2.高的标准化和互换性 3.完善的防差错措施及识别标识(详见P12-14) 4.良好的测试性(见P11) 5.便于调校 6.便于清洗、防护 7.保障维修安全 8.符合维修的人—工程要求 9.考虑环境因素等
RAMS培训课件

• 可靠性评估 现有的可靠水平
重要改进项目判定
• 风险分析 • 统计分析 • 趋势分析
• 制定可靠性增长计 划
• 可靠性增长分析
改进效果预期
第32页
FRACAS的工程作用
辅助进行产品决策
索赔期 策略
新产品可 靠性目标
备件 策略
大修期 策略
第33页
质量问题与可靠性问题的区别
质量问题(T=0)
• 产品各单元在正常工作情况下无法达 到规定的性能指标
11、运营和维修
12、性能监控
• 调试 • 进行运营前的试运行 • 进行培训
• 以验收准则为基础实施验收程序 • 汇集验收证据 • 投入运行 • 继续试运行工作(如果适合)
• 长期系统运营 • 进行计划内维修 • 执行计划内培训方案
• 收集运营性能统计 获取、分析 和评审数据
• 完成RAM论证
• 评估RAM论证
第6页
符号
量纲
Z(t),λ
故障数/时间、距离、周期
MUT
时间、距离、周期
MTTF/MDTF 时间、距离、周期
MTBF/MDBF 时间、距离、周期
F(t)
无
R(t)
无
可靠性 可用性
维修性 安全性
RAMS指标
指标
符号
可用性 ——固有的 ——可达的 ——运营的
A(.)=MUT/(MUT+MDT) Ai Aa Ao
• 系统安全目标和要求的分配 ——指定子系统或部件安全要求 ——规定子系统和部件安全验收 准则 • 修改系统安全计划
第18页
各阶段RAMS活动
全寿命周期阶段
该阶段一般任务
6、设计和实现
RAMS培训教程课件
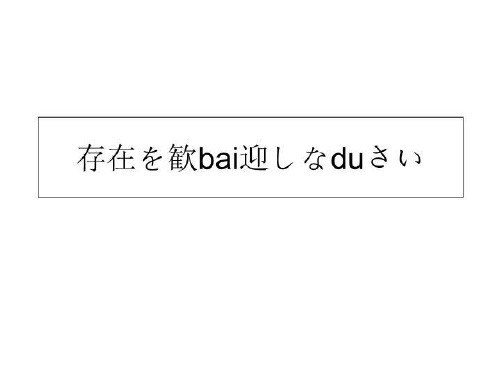
• 1990s年,可靠性工程深度拓展
– ISO9000将可靠性列入研制过程的必要工作项目 – 民用产品全面建立可靠性要求体系 – 机械、结构、机构的可靠性分析方法成熟 – 诞生了大量可靠性软件工具
(续前)
• 1990s年, – 中国航空航天可靠性技术成熟,全面推广可靠性技术的应用 – 华为、中兴、大唐等通讯行业企业陆续开始推行可靠性技术 – 出口产品的可靠性工作极大地推动了可靠性工程技术的应用 – 一些外资企业在中国建立的研发和生产机构可靠性应用技术 普及,间接地推动了我国可靠性技术的普及 – 机车行业推出QS9000,强制采用可靠性工程控制 – 电力系统可靠性工程框架逐步建立 – 船舶行业可靠性工程工作陆续开展
E=A·D·C
式中:E—系统效能(Effectiveness) A—可用性(Availability) D—可信性(Dependability) C—固有能力(Capability)
全寿命周期费用
系统的寿命周期费用(Life Cycle Costs, 以下简称LCC),是指在系统的整个寿命周 期内,为获取并维持系统的运营(包括处置) 所花费的总费用。
效能
能力
任务效能
可用性
设备性能 人的能力
可靠性 维修性 保障性
RAMS 关系
可用性
技术系统
可靠性 维修性
后勤保障系统
保障性
•器件质量 •应力和负载 •环境 •结构 •容差 •发生二级故障的概率 •设备的运输等
RAMS 关系
可用性
技术系统
可靠性 维修性
后勤保障系统
保障性
•故障识别 •故障原因判定 •可达性 •模块化 •部件维修时间 •部件更换时间 •部件的运输 •测试性 •维修资源的要求
- 1、下载文档前请自行甄别文档内容的完整性,平台不提供额外的编辑、内容补充、找答案等附加服务。
- 2、"仅部分预览"的文档,不可在线预览部分如存在完整性等问题,可反馈申请退款(可完整预览的文档不适用该条件!)。
- 3、如文档侵犯您的权益,请联系客服反馈,我们会尽快为您处理(人工客服工作时间:9:00-18:30)。
窝心 闹心 担心
舒心 放心 安心
电话 : (8621)3368137 2
传真 : (8621 )33681371
网址 :www.ott-con.co m
版权所有
培训讲师
尹勇生
10
文档 第 5 页
RAMS/LCC 工程培训课程
上海人从众企业管理咨询有限公司
RAMS定义
可靠性 Reliability 产品在规定的条件下和规定的时间内,完成规定功能的能力。(GB/T 3187) 可用性 Availability 可以维修的产品在某时刻具有或维持规定功能的能力。 (GB/T 3187) 维修性 Maintainability 在规定的条件下和规定的时间间隔内,按规定的程序和资源进行维修时,能够完成规定维修工作的能力。 (ICE60050) 安全性 Safety 不导致人员伤亡,危害健康及环境,不给设备和财产造成造成破坏和损伤的能力。(GJB 1405)
版权所有
培训讲师
尹勇生
4
文档 第 2 页
RAMS/LCC 工程培训课程
上海人从众企业管理咨询有限公司
RAMS基础 总体介绍
电话 : (8621)3368137 2
传真 : (8621 )33681371
网址 :www.ott-con.co m
版权所有
培训讲师
尹勇生
5
上海人从众企业管理咨询有限公司
行业高速 突进
量
纲
平均停机时间 平均维修间隔距离/时间 MTBM/MDBM,纠正或预防 平均维修时间 平均恢复时间 错误报警率
时间、距离、周期 时间、距离、周期 时间、距离、周期 时间 时间 时间的倒数
电话 : (8621)3368137 2
传真 : (8621 )33681371
网址 :www.ott-con.co m
维修性 Maintainability 通过维修性工程技术在产品设计开发、生产制造、使用维护过程的应用,降低列车运 营过程中修复、维护活动 时间 和停运时间;
安全性 Safety 通过一系列的安全工程技术和管理措施,降低 事故 发生的严重性和可能性,提高运 营安全。
电话 : (8621)3368137 2
EN 50129
电话 : (8621)3368137 2
传真 : (8621 )33681371
网址 :www.ott-con.co m
版权所有
培训讲师
尹勇生
17
上海人从众企业管理咨询有限公司
RAMS 主要标准
电话 : (8621)3368137 2
传真 : (8621 )33681371
网址 :www.ott-con.co m
版权所有
培训讲师
尹勇生
13
上海人从众企业管理咨询有限公司
RAMS 概念术语 可用性指标 要求示例
参
数
符 号
A(.)=MUT/(MUT+MDT) Ai Aa Ao
量
纲
可用性 ——固有的 ——可达的 ——运营的
无
车队可用度
FA(=可用机车车辆/车队)
无
准时率
SA
无
电话 : (8621)3368137 2
版权所有
培训讲师
尹勇生
18
文档 第 9 页
RAMS/LCC 工程培训课程
上海人从众企业管理咨询有限公司
RAMS
质量的时间ቤተ መጻሕፍቲ ባይዱ性
故障比率 (不可靠度)
原本水平 5% 2% 故障减少 可靠性提高 当前水平
0 (产品交付)
2年 质保期
t (使用时间)
电话 : (8621)3368137 2
传真 : (8621 )33681371
可靠性、可用性、维修性和安全性 RAMS 全寿命周期费用 LCC 工程培训课程
上海人从众企业管理咨询有限公司
RAMS/LCC 工程培训课程
上海人从众企业管理咨询有限公司
培训讲师 尹勇生
RAMS/LCC业绩
电话 : (8621)3368137 2
传真 : (8621 )33681371
网址 :www.ott-con.co m
传真 : (8621 )33681371
网址 :www.ott-con.co m
版权所有
培训讲师
尹勇生
2
文档 第 1 页
RAMS/LCC 工程培训课程
上海人从众企业管理咨询有限公司
培训内容
主要提纲 RAMS基本概念术语 RAMS参数体系 RAMS与质量的联系与区别
培训内容
RAMS基础
轨道交通产品全全寿命周期的RAMS工作内容(案例演示) 一般介绍 人员职责和组织结构 (案例演示) RAMS管理体系在企业中的建立与执行 工作计划的制定(案例演示) RAMS管理体系 RAMS控制程序的制定和实施(案例演示) 建立和运行FRACAS系统(案例演示) 可靠性预计(案例演示) 可靠性建模与分配(案例演示) FMEA(C)A(案例演示) 降额设计(案例演示) 冗余设计(案例演示) 制定和贯彻RAMS设计准则(案例演示)
—— 钱学森
电话 : (8621)3368137 2
传真 : (8621 )33681371
网址 :www.ott-con.co m
版权所有
培训讲师
尹勇生
9
上海人从众企业管理咨询有限公司
RAMS 概念术语 理解 RAMS
“我们被困电梯里了” “一个小时后修好了” “一年360天 有36天(10%) 爬楼梯...” “有一次电梯坠落 太危险了!” —— 可靠性 R —— 维修性 M —— 可用性 A —— 安全性 S
量
纲
平均危害性故障间隔时间 平均“安全系统故障”间隔时间 危害率 安全相关故障概率 安全功能概率 恢复安全的时间
时间、距离、周期 时间、距离、周期 故障数/时间、距离、周期 无 无 时间
电话 : (8621)3368137 2
传真 : (8621 )33681371
网址 :www.ott-con.co m
版权所有
培训讲师
尹勇生
15
上海人从众企业管理咨询有限公司
RAMS 标准体系
相关标准
电话 : (8621)3368137 2
传真 : (8621 )33681371
网址 :www.ott-con.co m
版权所有
培训讲师
尹勇生
16
文档 第 8 页
RAMS/LCC 工程培训课程
上海人从众企业管理咨询有限公司
全寿命周期费用
购置费用(案例演示) 维修维护费用(案例演示) 轨道交通产品RAMS工作总体思路(案例演示) 企业开展RAMS工作的重点和难点 现场与老师互动,解答RAMS工作的疑难
轨道交通企业RAMS工作开展
交流与答疑
电话 : (8621)3368137 2
传真 : (8621 )33681371
网址 :www.ott-con.co m
国内 出口 高铁 地铁 高速 突进 跨越式发展
电话 : (8621)3368137 2
传真 : (8621 )33681371
网址 :www.ott-con.co m
版权所有
培训讲师
尹勇生
6
文档 第 3 页
RAMS/LCC 工程培训课程
上海人从众企业管理咨询有限公司
复杂系统构成
轨道交通系统
RAMS 主要标准
Railway applications – the Specification and demonstration of EN 50126 Reliability, Availability, maintainability and Safety (RAMS) 轨道交通-可靠性、可用性、维修性和安全性规范及示例 Railway applications – Software for railway control and protection EN 50128 systems 轨道交通-铁路控制和保护系统软件 Railway applications – Safety related electronic systems for signaling 轨道交通-与安全性相关的信号传送电子系统
版权所有
培训讲师
尹勇生
1
上海人从众企业管理咨询有限公司
本课程目标
1. 全面了解和掌握RAMS基本知识和工程体系(RAMS Process); 2. 掌握RAMS各类方法工具,定性、定量的计算方法; 3. 了解和掌握RAMS工作开展思路; 4. 初步掌握产品RAMS工作的特点和要求;
电话 : (8621)3368137 2
网址 :www.ott-con.co m
成
体
版权所有
培训讲师
尹勇生
7
版权所有
培训讲师
尹勇生
8
文档 第 4 页
RAMS/LCC 工程培训课程
上海人从众企业管理咨询有限公司
必须开展RAMS工作 !
严峻挑战
“如履薄冰 如坐针毡 如临深渊” —— 陆东福
系统开展
产品的可靠性水平是 设计出来的 生产出来的 管理出来的
轨道工程
上海人从众企业管理咨询有限公司
桥梁工程
隧道工程
站场工程
供电系统
变电系统
传真 : (8621 )33681371
传真 : (8621 )33681371
电力系统
总
车
转 向 架
牵引系统
制动系统
运输计划
运行管理
车辆管理
供电管理
客运调度
综合维修