大型齿轮箱结构设计与分析虚拟仿真实验
轨道交通齿轮箱的仿真测试与验证研究

轨道交通齿轮箱的仿真测试与验证研究随着城市化进程的加快和人们对高效、便捷交通需求的不断增长,轨道交通作为一种快速、环保的交通工具,受到了广泛的关注和应用。
而在轨道交通系统中,齿轮箱作为传动系统的重要组成部分,对保证列车运行的能力和稳定性发挥着重要作用。
因此,对轨道交通齿轮箱的仿真测试与验证进行研究,对确保列车运行的安全性和可靠性有着重要的意义。
一、轨道交通齿轮箱仿真测试的意义1. 验证设计方案的可行性轨道交通齿轮箱是由许多精密的齿轮、轴承和润滑系统组成的复杂机械系统。
在设计齿轮箱时,通过仿真测试,能够验证设计方案的可行性和合理性,提前发现潜在的问题,并对设计进行优化。
2. 评估齿轮箱的工作性能通过仿真测试,可以评估齿轮箱在实际工作条件下的性能表现,包括传动效率、噪音和振动等指标。
根据仿真结果,可以对齿轮箱的设计参数进行调整和优化,以达到更好的工作性能。
3. 提高产品质量和可靠性轨道交通齿轮箱的故障会对列车的正常运行造成严重影响,甚至可能引发事故。
通过仿真测试,可以预测齿轮箱在各种工况下的工作状态,并评估其可靠性。
在测试中发现的问题可以在设计阶段进行修正,从而提高产品的质量和可靠性。
二、轨道交通齿轮箱仿真测试与验证的方法1. 基于多体动力学仿真的方法多体动力学仿真是一种常用的仿真测试方法,通过对齿轮箱的结构和工作原理建立数学模型,考虑各种外部载荷、齿轮传动和润滑条件等因素的影响,模拟齿轮箱在不同工况下的运动和受力情况,从而评估其工作性能和可靠性。
该方法具有高度的灵活性和适应性,可以模拟齿轮箱在不同速度、负载和润滑条件下的工作情况,为设计和优化提供依据。
2. 流体动力学仿真方法轨道交通齿轮箱中的润滑系统在传动中起到了重要的作用,但也容易受到振动、温度变化等因素的影响。
通过流体动力学仿真方法,可以对润滑系统进行仿真分析,考虑润滑油膜的厚度、温度和压力等因素,评估润滑系统的性能和稳定性,以避免因润滑不良而引发的故障和损坏。
基于SolidWorks的齿轮箱虚拟设计

煤矿机械Coal Mine Machinery Vol.32No.01 Jan.2011第32卷第01期2011年01月0前言虚拟设计(Virtual Design)是将VR技术和CAD 技术相结合的一个应用于多领域的新技术。
近年来,商业CAD软件及工具的兴起,例如:PTC公司的产品SolidWorks,Pro/Engineer,SDRC的产品I-DEAS Master Series、UGS公司的产品Unigraphics 等,推动了虚拟设计的发展[4]。
虚拟设计指的是设计者可以在虚拟的设计环境中,通过友好的计算机界面,建立虚拟的三维模型,根据零部件的配合关系,进行虚拟装配,爆炸视图的仿真,并可以进行修改。
一个虚拟设计系统应该具备以下3个功能:数据表达与双向数据传输;三维建模用户界面;参数化选择。
1虚拟设计的特点1.1虚拟设计与传统设计的比较传统设计,需要从设计开始,然后试制,试制的过程中要投入原料、人员和厂房等,如果评价不通过,还要反复循环进行制造,可见这个过程需要投入大量的物力和人力,降低了生产效率。
虚拟设计,它的设计、制造、装配和评价均在计算机内进行,只有实际制造过程中才投入原料和人员,从而缩短的时间,降低了成本,提高了生产效率,并可以对市场的需求作出迅速的反应。
1.2虚拟设计的优点随着市场的开放性和全球化,用户在追求高质量低价格和短交货期的同时,会缩短产品的更新换代周期,这就要求设计人员去改变传统设计模式,最大限度地利用虚拟设计技术。
设计者通过虚拟装配检查各零部件尺寸以及可装配性,即时修改错误;通过虚拟原型进行虚拟试验,而不用再去做更多的实物试验。
这样,既节省了时间又节约了费用。
SolidWorks软件在产品性能优化和仿真(运动和干涉检查、整机运动分析、零部件设计优化等)、结构特征建模、分析评价等方面具有独到的优势。
故以SolidWorks软件作为虚拟设计平台,对JMY240机车车轴齿轮箱进行虚拟设计,齿轮箱箱体由52种零部件所组成,通过对主要零部件进行建模,然后进行组装形成装配体,现对车轴齿轮箱零部件进行建模,并经行装配的虚拟设计。
基于Pro E齿轮减速器虚拟样机构建及性能仿真研究
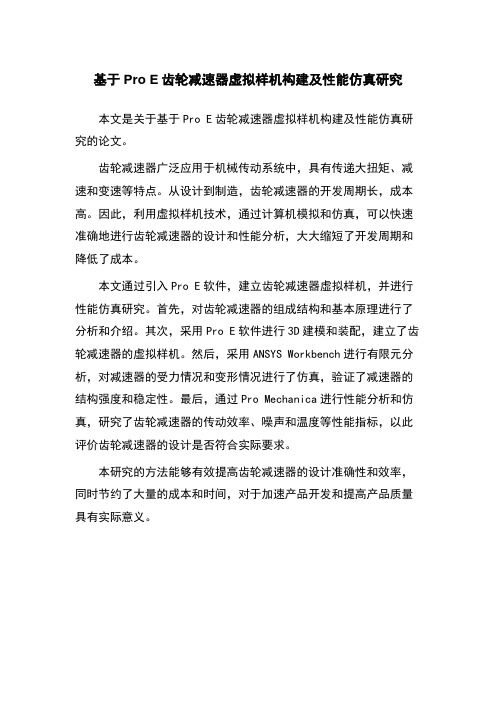
基于Pro E齿轮减速器虚拟样机构建及性能仿真研究
本文是关于基于Pro E齿轮减速器虚拟样机构建及性能仿真研究的论文。
齿轮减速器广泛应用于机械传动系统中,具有传递大扭矩、减速和变速等特点。
从设计到制造,齿轮减速器的开发周期长,成本高。
因此,利用虚拟样机技术,通过计算机模拟和仿真,可以快速准确地进行齿轮减速器的设计和性能分析,大大缩短了开发周期和降低了成本。
本文通过引入Pro E软件,建立齿轮减速器虚拟样机,并进行性能仿真研究。
首先,对齿轮减速器的组成结构和基本原理进行了分析和介绍。
其次,采用Pro E软件进行3D建模和装配,建立了齿轮减速器的虚拟样机。
然后,采用ANSYS Workbench进行有限元分析,对减速器的受力情况和变形情况进行了仿真,验证了减速器的结构强度和稳定性。
最后,通过Pro Mechanica进行性能分析和仿真,研究了齿轮减速器的传动效率、噪声和温度等性能指标,以此评价齿轮减速器的设计是否符合实际要求。
本研究的方法能够有效提高齿轮减速器的设计准确性和效率,同时节约了大量的成本和时间,对于加速产品开发和提高产品质量具有实际意义。
齿轮仿真耦合实验报告(3篇)
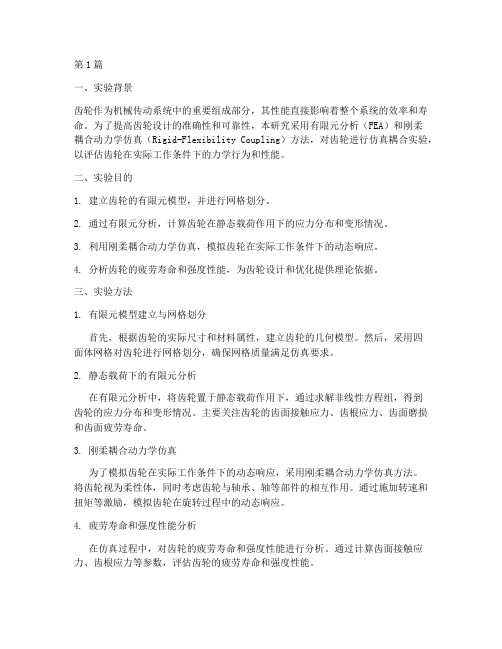
第1篇一、实验背景齿轮作为机械传动系统中的重要组成部分,其性能直接影响着整个系统的效率和寿命。
为了提高齿轮设计的准确性和可靠性,本研究采用有限元分析(FEA)和刚柔耦合动力学仿真(Rigid-Flexibility Coupling)方法,对齿轮进行仿真耦合实验,以评估齿轮在实际工作条件下的力学行为和性能。
二、实验目的1. 建立齿轮的有限元模型,并进行网格划分。
2. 通过有限元分析,计算齿轮在静态载荷作用下的应力分布和变形情况。
3. 利用刚柔耦合动力学仿真,模拟齿轮在实际工作条件下的动态响应。
4. 分析齿轮的疲劳寿命和强度性能,为齿轮设计和优化提供理论依据。
三、实验方法1. 有限元模型建立与网格划分首先,根据齿轮的实际尺寸和材料属性,建立齿轮的几何模型。
然后,采用四面体网格对齿轮进行网格划分,确保网格质量满足仿真要求。
2. 静态载荷下的有限元分析在有限元分析中,将齿轮置于静态载荷作用下,通过求解非线性方程组,得到齿轮的应力分布和变形情况。
主要关注齿轮的齿面接触应力、齿根应力、齿面磨损和齿面疲劳寿命。
3. 刚柔耦合动力学仿真为了模拟齿轮在实际工作条件下的动态响应,采用刚柔耦合动力学仿真方法。
将齿轮视为柔性体,同时考虑齿轮与轴承、轴等部件的相互作用。
通过施加转速和扭矩等激励,模拟齿轮在旋转过程中的动态响应。
4. 疲劳寿命和强度性能分析在仿真过程中,对齿轮的疲劳寿命和强度性能进行分析。
通过计算齿面接触应力、齿根应力等参数,评估齿轮的疲劳寿命和强度性能。
四、实验结果与分析1. 静态载荷下的应力分布和变形通过有限元分析,得到齿轮在静态载荷作用下的应力分布和变形情况。
结果表明,齿轮的齿面接触应力主要集中在齿根附近,齿根应力较大。
同时,齿轮的变形主要集中在齿面和齿根处。
2. 刚柔耦合动力学仿真结果通过刚柔耦合动力学仿真,模拟齿轮在实际工作条件下的动态响应。
结果表明,齿轮的齿面接触应力、齿根应力等参数在旋转过程中发生变化,但总体上满足设计要求。
1mw风力发电机组pj10偏航齿轮箱设计与仿真分析图文
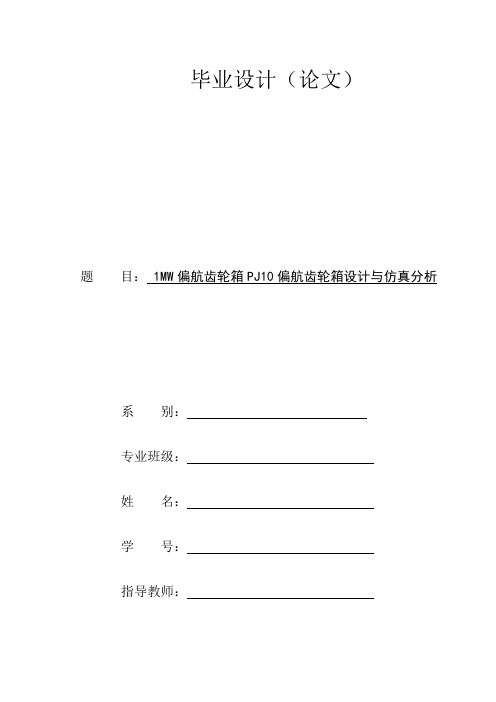
毕业设计(论文)题目:1MW偏航齿轮箱PJ10偏航齿轮箱设计与仿真分析系别:专业班级:姓名:学号:指导教师:二〇年月日毕业设计(论文)题目:1MW偏航齿轮箱PJ10偏航齿轮箱设计与仿真分析系别:专业班级:姓名:学号:指导教师:二〇年月日目录毕业设计(论文) ..................................................................................................... - 1 -毕业设计(论文) ...................................................................................................... - 2 -1MW风机偏航齿轮箱的设计.................................................................................... - 1 -摘要 .............................................................................................................................. - 1 -ABSTRACT ................................................................................................................. - 1 -第一章引言 .................................................................................................................. - 1 -1.1风力发电和风力发电机简介 (1)1.2风力发电技术的国内外发展现状 (1)1.2偏航齿轮箱简介 (2)1.3课题意义 (2)第2章偏航齿轮箱结构设计 ...................................................................................... - 4 -2.1偏航齿轮箱技术要求 (4)2.2主要设计参数 (5)2.3总体方案设计 (5)第3章行星轮传动设计计算 ...................................................................................... - 6 -3.1方案设计.. (6)3.2风力发电机组偏航结构 (7)3.3第一级行星齿轮传动 (8)3.3.1 传动比分配.................................................................................................................... - 8 -3.3.2 初步计算齿轮主要参数 ................................................................................................ - 9 -3.3.3 齿轮变位计算.............................................................................................................. - 10 -3.3.4 重合度计算.................................................................................................................. - 10 -3.3.5 啮合效率计算............................................................................................................ - 11 - 3.4第二级行星齿轮传动. (12)3.4.1 齿轮参数的确定.......................................................................................................... - 12 -3.4.2 初步计算齿轮主要参数 .............................................................................................. - 12 -3.4.3 齿轮变位计算.............................................................................................................. - 13 -3.4.4 重合度计算.................................................................................................................. - 13 -3.4.5 啮合效率计算.............................................................................................................. - 14 - 3.5第三级行星齿轮传动. (15)3.5.1 齿轮参数的确定.......................................................................................................... - 15 -3.5.2 初步计算齿轮主要参数 .............................................................................................. - 15 -3.5.3 齿轮变位计算.............................................................................................................. - 17 -3.5.4 重合度计算.................................................................................................................. - 18 -3.5.5 啮合效率计算.............................................................................................................. - 18 - 3.6第四级行星齿轮传动. (19)3.6.1 齿轮参数的确定.......................................................................................................... - 19 -3.6.2 初步计算齿轮主要参数 .............................................................................................. - 20 -3.6.3 齿轮变位计算.............................................................................................................. - 21 -3.6.4 重合度计算.................................................................................................................. - 22 -3.6.5 啮合效率计算.............................................................................................................. - 22 - 3.7行星齿轮传动设计汇总. (23)第4章行星齿轮强度校核 ........................................................................................ - 24 -4.1载荷的确定...............................................................................................错误!未定义书签。
基于仿真技术的轨道交通专用齿轮箱性能评估
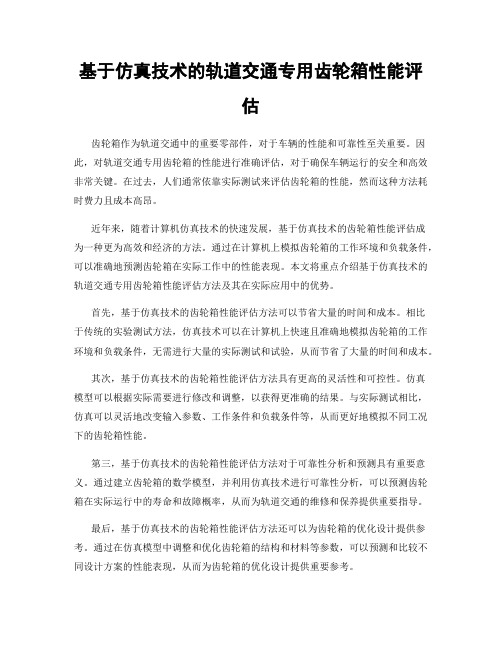
基于仿真技术的轨道交通专用齿轮箱性能评估齿轮箱作为轨道交通中的重要零部件,对于车辆的性能和可靠性至关重要。
因此,对轨道交通专用齿轮箱的性能进行准确评估,对于确保车辆运行的安全和高效非常关键。
在过去,人们通常依靠实际测试来评估齿轮箱的性能,然而这种方法耗时费力且成本高昂。
近年来,随着计算机仿真技术的快速发展,基于仿真技术的齿轮箱性能评估成为一种更为高效和经济的方法。
通过在计算机上模拟齿轮箱的工作环境和负载条件,可以准确地预测齿轮箱在实际工作中的性能表现。
本文将重点介绍基于仿真技术的轨道交通专用齿轮箱性能评估方法及其在实际应用中的优势。
首先,基于仿真技术的齿轮箱性能评估方法可以节省大量的时间和成本。
相比于传统的实验测试方法,仿真技术可以在计算机上快速且准确地模拟齿轮箱的工作环境和负载条件,无需进行大量的实际测试和试验,从而节省了大量的时间和成本。
其次,基于仿真技术的齿轮箱性能评估方法具有更高的灵活性和可控性。
仿真模型可以根据实际需要进行修改和调整,以获得更准确的结果。
与实际测试相比,仿真可以灵活地改变输入参数、工作条件和负载条件等,从而更好地模拟不同工况下的齿轮箱性能。
第三,基于仿真技术的齿轮箱性能评估方法对于可靠性分析和预测具有重要意义。
通过建立齿轮箱的数学模型,并利用仿真技术进行可靠性分析,可以预测齿轮箱在实际运行中的寿命和故障概率,从而为轨道交通的维修和保养提供重要指导。
最后,基于仿真技术的齿轮箱性能评估方法还可以为齿轮箱的优化设计提供参考。
通过在仿真模型中调整和优化齿轮箱的结构和材料等参数,可以预测和比较不同设计方案的性能表现,从而为齿轮箱的优化设计提供重要参考。
尽管基于仿真技术的齿轮箱性能评估方法具有许多优势,但仍然存在一些挑战。
首先,齿轮箱的数学建模需要准确地考虑各种参数和因素,如齿轮齿型、润滑和振动等。
其次,仿真模型的准确性和可靠性对于评估结果的准确性至关重要,因此需要依靠可靠的模型验证和实验数据进行校准。
采用VRML的齿轮变速箱虚拟模型的实现

一
三维 建模 软件主 要有 A tC uo AD、 G、 oiWok U Sl d r、 PoE I E R等 。每个 产品都 有着 自己的发展 r,NG N E
CAD s fwa e o t r .Th n i ua s e l a d k n mai smu a i n a e c o ls e v e v r l a s mb y n i e tc i l to a c mp ih d b VRM L t r f n to t r ai e h s ai a i n o h s it g a r c s .Th it a u c i ns o e l t e viu lz to f t e h fi z ng e r p o e s e v ru l mod l a e esc n b a c s e d o e ae ntr c i e y o e n e ne,ofe i f ce tWa o e l a e a r mo e c e s d a p r t d i e a tv l v rI tr t f rng a e n n i i n y t vau t e t d sgn tr ug e wo k. ei o hn t r h Ke wor :c mp e pp i ai n;v rua mo e o e rbo y ds o utr a lc to i t l d l f g a — x;VRM L;vru l a s mbl ; i a se t y k n ma c smu ai n i e t i l to i
听觉、运动等行为的人机界面技术 。目前市场
齿轮箱有限元模态分析及试验研究报告

齿轮箱有限元模态分析及试验研究报告齿轮箱是现代机械设备中重要的组成部分,它广泛用于各种机械传动系统中,如车辆、工程机械等。
因此研究齿轮箱的动力学特性对于机械传动系统的设计、优化和性能提升具有重要意义。
本文通过有限元模态分析和试验研究,对齿轮箱的动力学特性进行了分析和研究。
首先进行有限元模态分析,使用ANSYS软件建立了三维齿轮箱模型,并对其进行了固有频率和模态分析。
在分析过程中,设定了模型的约束和加载条件,确保模型模拟的真实性与可靠性。
通过模态分析,得到了齿轮箱的固有频率和模态形态,并且确定出了前几个重要频率的数值。
结果表明,齿轮箱的固有频率主要集中在数百Hz的高频段。
为了验证有限元模态分析结果的准确性,本文设计了试验验证方案。
首先,使用激光精密测量仪对齿轮箱的位移进行测量,并将测试数据存储为动态位移序列。
然后,基于FFT算法对动态位移序列进行频谱分析,得到齿轮箱的频响函数。
最后,通过对比有限元模态分析结果与试验结果,验证模型的准确性和可靠性。
试验结果表明,模型的预测结果与试验结果相符,二者的误差在可接受范围内。
综上所述,本文采用有限元模态分析和试验验证两种方法,对齿轮箱的动力学特性进行了研究。
结果表明,齿轮箱具有较高的固有频率,且主要分布在数百Hz的高频段。
通过试验验证,证明了有限元模态分析方法的准确性和可靠性。
这些结果对于齿轮箱的优化设计、结构改进和性能提升具有重要参考价值。
齿轮箱的有限元模态分析和试验研究,采用了多项相关数据。
在本文中,我们主要关注以下数据:1. 齿轮箱模型的材料性质2. 模型的约束和加载条件3. 模型的固有频率和模态形态4. 齿轮箱的位移测试数据5. 齿轮箱的频响函数6. 模型预测结果与试验结果的误差对于第一项数据,齿轮箱的材料性质是有限元模型分析的关键。
正确的材料参数可以确保分析结果的准确性和可靠性。
在本文中,我们将齿轮箱的材料定义为铸铁,其杨氏模量为169 GPa,泊松比为0.27。
大模数齿轮虚拟制造的齿形设计1
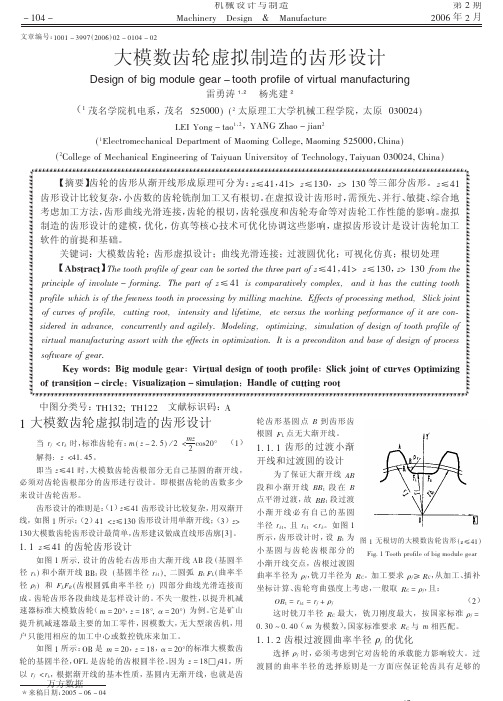
【摘要】 齿轮的齿形从渐开线形成原理可分为: !D(!, (!O !D!+$,!O !+$ 等三部分齿形。 !D(! 齿形设计比较复杂, 小齿数的齿轮铣削加工又有根切。 在虚拟设计齿形时, 需预先、 并行、 敏捷、 综合地 考虑加工方法, 齿形曲线光滑连接, 齿轮的根切, 齿轮强度和齿轮寿命等对齿轮工作性能的影响。 虚拟 制造的齿形设计的建模, 优化, 仿真等核心技术可优化协调这些影响, 虚拟齿形设计是设计齿轮加工 软件的前提和基础。 关键词:大模数齿轮;齿形虚拟设计;曲线光滑连接;过渡圆优化;可视化仿真;根切处理 【 !"#$%&’$】 "#$ %&&%# ’(&)*+$ &) ,$-( .-/ 0$ 1&(%$2 %#$ %#($$ ’-(% &) !D(!, (!O !D!+$, !3 !+$ )(&4 %#$ ’(*/.*’+$ &) */5&+6%$ 7 )&(4*/,8 "#$ ’-(% &) ! D (! *1 .&4’-(-%*5$+9 .&4’+$:; -/2 *% #-1 %#$ .6%%*/, %&&%# ’(&)*+$ <#*.# *1 &) %#$ )$</$11 %&&%# */ ’(&.$11*/, 09 4*++*/, 4-.#*/$8 =))$.%1 &) ’(&.$11*/, 4$%#&2; >+*.? @&*/% &) .6(5$1 &) ’(&)*+$; .6%%*/, (&&%; */%$/1*%9 -/2 +*)$%*4$; $%. 5$(161 %#$ <&(?*/, ’$()&(4-/.$ &) *% -($ .&/A 1*2$($2 */ -25-/.$; .&/.6(($/%+9 -/2 -,*+$+98 B&2$+*/,; &’%*4*!*/,; 1*46+-%*&/ &) 2$1*,/ &) %&&%# ’(&)*+$ &) 5*(%6-+ 4-/6)-.%6(*/, -11&(% <*%# %#$ $))$.%1 */ &’%*4*!-%*&/8 C% *1 - ’($.&/2*%&/ -/2 0-1$ &) 2$1*,/ &) ’(&.$11 1&)%<-($ &) ,$-(8 ()* +,%-#. /01 2,-34) 1)&%;50%$3&4 -)#016 ,7 $,,$8 9%,704);:40’; <,06$ ,7 ’3%=)# >9$020?061 ,7 $%&6#0$0,6 @ ’0%’4);50#3&40?&$0,6 @ #0234&$0,6;A&6-4) ,7 ’3$$061 %,,$ 中图分类号:GP!+#Q GP!## 文献标识码:5
750kW风力机组齿轮箱动力学仿真分析
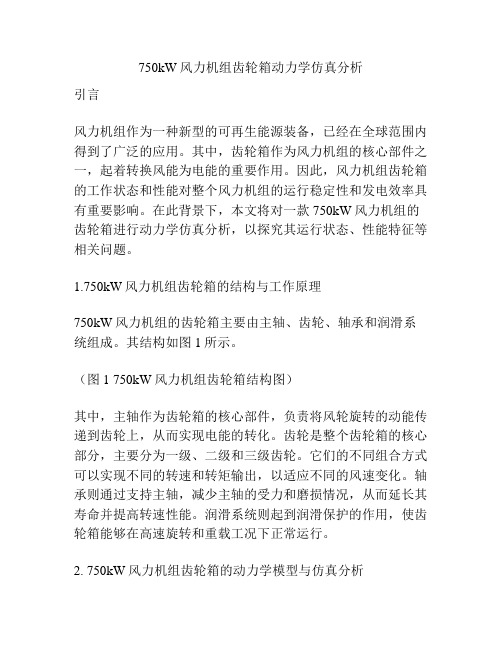
750kW风力机组齿轮箱动力学仿真分析引言风力机组作为一种新型的可再生能源装备,已经在全球范围内得到了广泛的应用。
其中,齿轮箱作为风力机组的核心部件之一,起着转换风能为电能的重要作用。
因此,风力机组齿轮箱的工作状态和性能对整个风力机组的运行稳定性和发电效率具有重要影响。
在此背景下,本文将对一款750kW风力机组的齿轮箱进行动力学仿真分析,以探究其运行状态、性能特征等相关问题。
1.750kW风力机组齿轮箱的结构与工作原理750kW风力机组的齿轮箱主要由主轴、齿轮、轴承和润滑系统组成。
其结构如图1所示。
(图1 750kW风力机组齿轮箱结构图)其中,主轴作为齿轮箱的核心部件,负责将风轮旋转的动能传递到齿轮上,从而实现电能的转化。
齿轮是整个齿轮箱的核心部分,主要分为一级、二级和三级齿轮。
它们的不同组合方式可以实现不同的转速和转矩输出,以适应不同的风速变化。
轴承则通过支持主轴,减少主轴的受力和磨损情况,从而延长其寿命并提高转速性能。
润滑系统则起到润滑保护的作用,使齿轮箱能够在高速旋转和重载工况下正常运行。
2. 750kW风力机组齿轮箱的动力学模型与仿真分析为了对750kW风力机组齿轮箱的运行状态和性能进行深入了解,我们需要基于可靠的动力学模型进行仿真分析。
具体来说,我们可以采用以下步骤实现:2.1. 几何建模和参数定义首先,需要对750kW风力机组齿轮箱进行几何建模和参数定义。
这包括齿轮箱的三维模型、材料参数、尺寸参数、接口参数等。
在定义材料参数时,需要考虑到其弹性模量、泊松比、密度等因素,以反映材料的物理特性。
在定义尺寸参数时,需要根据实际设计要求指定齿轮箱的各种尺寸参数和工作状态参数,如齿轮啮合度、轴向载荷、径向载荷等。
2.2. 运动学分析与求解完成几何建模和参数定义后,我们需要进行运动学分析和求解,以获得齿轮箱的运动状态和动力特征。
这包括运动学约束方程、位置、速度和加速度等参数的计算。
同时,为了更加准确地描述齿轮箱的运动状态,我们还可以考虑增加一些约束,如位移约束、角速度约束、加速度约束等。
毕业设计--齿轮测试实验台结构设计与建模
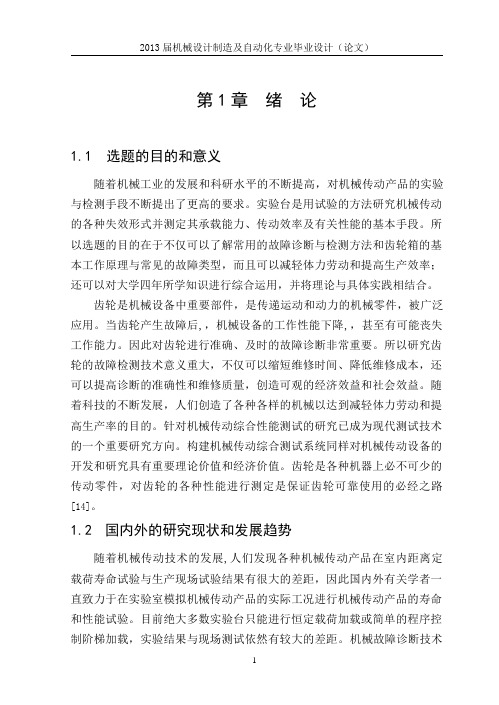
开诊断仪器与诊断系统,因此,体积小、高精度、操作简单的诊断与分析 仪器和大型综合诊断系统的研发一直是故障诊断学面向应用的研究重点。 目前这方面的研究主要有:便携式振动仪器、检测仪器、分析与诊断仪器 以及集中式、分布式的大型在线检测与诊断系统。 展望今后齿轮故障诊断技术发展方向,当前机械故障诊断学的发展趋 势集中在以下几方面: (1)传统的频谱分析技术将日趋完善。 (2)专家系统,神经网络,小波分析等新技术将从实验室研究阶段, 逐步走向实际应用阶段。 (3) 目前, 齿轮故障诊断技术多集中于采用振动监测手段, 可以预见, 在今后几年里,铁谱技术、油样光谱技术及声发射技术将会占有一席之地。
故障诊断的关键环节,直接关系到故障诊断结果的准确性。故障诊断学的 发展是以故障信息的提取与处理技术的革新为标志。早期,人们只能依靠 感觉(如听觉、触觉等) ,凭经验提取故障信息并判断故障的原因。这种故 障信息的提取与分析手段是最原始的故障诊断技术。随着传感器技术和信 号处理技术发展,人们借助简单仪器和传统的信号分析技术,能够完成较 为复杂的诊断工作,在一定程度上可以预防突发事故的发生,随着科学技 术的发展和多学科之间相互交叉于渗透,特别是计算机技术和现代信号处 理技术的发展,人们对故障信息的提取与处理能力显著增强,可以更准确 地判断故障原因,更可靠地预测故障发展的趋势,做到对设备科学管理, 新的故障信息提取技术有:模式识别、信息熵、高阶统计量、人工智能、 专家系统等。还有许多现代分析方法如:人工神经元网络、遗传算法、小 波分析、全息普、高阶谱分析等。借助计算机技术和现代分析方法可以提 高诊断的自动化程度和分析精度。 (3)诊断仪器与诊断系统的开发与研究 机械故障诊断的实现离不
3
2013 届机械设计制造及自动化专业毕业设计(论文)
风电齿轮箱的数字化仿真与优化设计
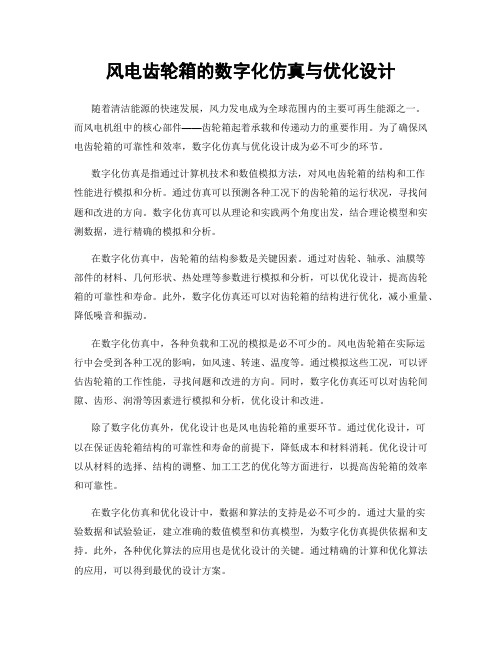
风电齿轮箱的数字化仿真与优化设计随着清洁能源的快速发展,风力发电成为全球范围内的主要可再生能源之一。
而风电机组中的核心部件——齿轮箱起着承载和传递动力的重要作用。
为了确保风电齿轮箱的可靠性和效率,数字化仿真与优化设计成为必不可少的环节。
数字化仿真是指通过计算机技术和数值模拟方法,对风电齿轮箱的结构和工作性能进行模拟和分析。
通过仿真可以预测各种工况下的齿轮箱的运行状况,寻找问题和改进的方向。
数字化仿真可以从理论和实践两个角度出发,结合理论模型和实测数据,进行精确的模拟和分析。
在数字化仿真中,齿轮箱的结构参数是关键因素。
通过对齿轮、轴承、油膜等部件的材料、几何形状、热处理等参数进行模拟和分析,可以优化设计,提高齿轮箱的可靠性和寿命。
此外,数字化仿真还可以对齿轮箱的结构进行优化,减小重量、降低噪音和振动。
在数字化仿真中,各种负载和工况的模拟是必不可少的。
风电齿轮箱在实际运行中会受到各种工况的影响,如风速、转速、温度等。
通过模拟这些工况,可以评估齿轮箱的工作性能,寻找问题和改进的方向。
同时,数字化仿真还可以对齿轮间隙、齿形、润滑等因素进行模拟和分析,优化设计和改进。
除了数字化仿真外,优化设计也是风电齿轮箱的重要环节。
通过优化设计,可以在保证齿轮箱结构的可靠性和寿命的前提下,降低成本和材料消耗。
优化设计可以从材料的选择、结构的调整、加工工艺的优化等方面进行,以提高齿轮箱的效率和可靠性。
在数字化仿真和优化设计中,数据和算法的支持是必不可少的。
通过大量的实验数据和试验验证,建立准确的数值模型和仿真模型,为数字化仿真提供依据和支持。
此外,各种优化算法的应用也是优化设计的关键。
通过精确的计算和优化算法的应用,可以得到最优的设计方案。
值得注意的是,数字化仿真和优化设计是相辅相成的。
数字化仿真可以为优化设计提供依据和支持,而优化设计可以通过实际验证,不断改进和优化数字化仿真模型。
数字化仿真和优化设计需要密切配合,不断进行循环验证和改进。
HXN3型机车齿轮箱模拟仿真研究
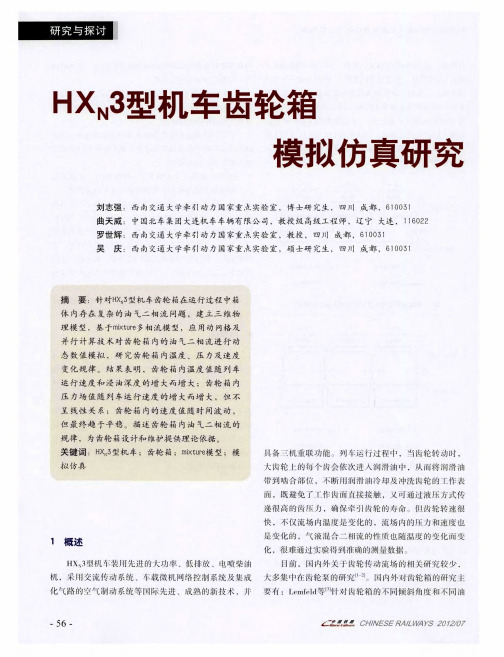
主 动 齿 轮 和 从 动 齿 轮 及 工 作 的 润 滑 油 是 在 箱 体 和 比较 复 杂 ,采 用 基 于 O t e 术 生成 非 结 构 化 网格 。 cr 技 e 轴 、齿 轮 之 间 形 成 的半 密 封 空 间 里 _ 作 ,模 型 可 以省 略 f =
计算域 出 口采用压力 出 口条件 ,齿 轮和齿轮箱体 均
可能把齿轮箱 的全部部件都体 现 出来 ,要 对模型进行 简 值 模拟结果起着 很重要 的作 用 ,网格质量 好坏直接关 系 化 。简化后 的模 型要尽可 能真实反 映实 际工作情况 ,确 到数值模 拟结 果的正确性 ,尽量减小 网格质量对计算精
保计算结果准确 。 度 的影 响 。 由于 进 行 并 行 计 算 ,考 虑到 齿 轮 箱 几 何 模 型
场 、压 力 场 和 速 度 场 的分 布 状 况 与 特 点 , 以及 各 种 因 素 于齿轮箱 内含油气二相 流的数 值计算 。 的 影 响 。 齿 轮 箱 的设 计 及 维 护 有 非 常 重 要 的工 程 应 用 价 油 气 二 相 流 模 型 的连 续 方 程 :
a
一
值 。基于 以上情况考虑 ,以H 型机 车传 动齿轮箱为研 X3
液 黏 度 对 其 内部 流 场 进 行 研 究 ;赵 宁 等 利 用 齿 轮 啮 合
( 2)列 车 运 行 时 轮 对 角 速 度 和 从 动 轮 角 速 度 相 同 ,不 存 在 瞬 时 角 速 度 差 ; ( 3)主 动 齿 轮 和 从 动 齿 轮 转 速 在 工 作 中 保 持 不
( 4)主 动 齿 轮 和 从 动 齿 轮 没 有 完 全 接 触 ,两 者 之
了 简 化 的 啮合 齿 轮 模 型 ,并 求 出 温 度 场 的解 析 解 ,提 出 间 留 有 几 毫 米 间 隙 , 目的是 为 了减 少 网格 数 量 ,提 高计 在 温 度 场 存 在 与 应 力 场 圣 唯 南 原 理 相 类 似 的 原 理 ,使 用 算 速 度 ; 该 原 理 对 齿 轮 温 度 场 进 行 修 正 ,得 到 的结 果 与 有 限元 法 ( 5)齿 轮 箱 功 率 损 失 全 部 转 化 为 大 小 齿 轮 的发 热
齿轮传动中仿真系统的分析

1.内平动齿轮传动的建模传统的齿轮传动设计方法相当复杂,设计周期长,工作量大。
设计过程重复,工作效率低。
在齿轮装配环节,也是仅仅在理论上进行可行性装配计算。
对于装配过程中可能出现的问题无法预知,可视性差;当齿轮的某一参数改变时,整个设计过程都要跟着改变,设计智能化低。
因此,利用计算机技术实现齿轮的参数化、智能化设计和虚拟装配是非常必要的。
比较流行的3D设计软件有,SOLID-WORKS、PRO/E、UG等。
笔者就利用PRO/E软件进行齿轮虚拟设计。
对在虚拟环境下实现齿轮的精确建模与装配方法进行了研究。
1.1外齿轮精确建模首先在Pro/E中新建一个零件模块。
在模板的选用中注意应选择“mmns_part_so-lid”。
并且各零件模型和装配模型应一致,否则会造成单位上的不一致,使装配无法进行。
在主菜单中依次选择“工具”,“关系”选项,系统将自动弹出“关系”对话框。
在对话框中将齿轮的各参数依次添加到参数列表框中。
绘制齿轮基本圆,在草绘状态下,绘制出分度圆,齿顶圆,齿根圆。
创建齿轮关系式。
在主菜单中依次选择“工具”,“关系”选项,在关系对话框中添加齿轮的几何尺寸关系。
创建齿轮齿廓线。
在菜单中依次选择“曲线选项”,“从方程”,“完成”选项,系统弹出“曲线:从方程”对话框。
根据系统提示,在模型窗口中选择“PRT_CSYS_DEF”坐标系,并定义为笛卡儿坐标。
创建齿廓镜像平面。
渐开线建立之后,为保证所建立齿轮的对称性,建立一个镜像平面就尤为重要了。
对于非变位齿轮它在分度圆处的齿厚和槽宽是相等的。
所以镜像平面的旋转角度等于三百六十度除以二倍的齿数。
镜像渐开线。
在工作区中选择创建的渐开线齿廓曲线,以DTM2为镜像平面。
完成另一侧轮廓线的创建。
通过创建的轮廓线建立轮齿的草图,利用拉伸特征创建第一个齿槽。
通过圆周阵列操作生成其余齿槽。
最后生成外齿轮。
1.2内齿轮精确建模在Pro/E中新建一个零件模块,模板选用“mmns_part_solid”。
大型风力发电机齿轮箱全柔体动力学建模与仿真分析
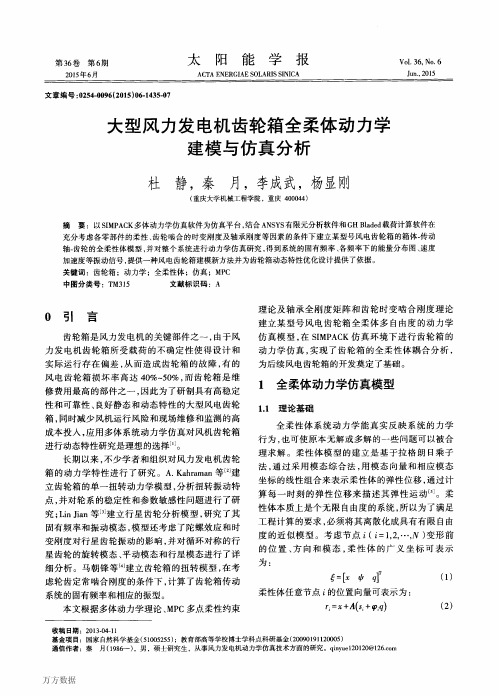
过花键连接,其余各轴通过齿轮副传递作用力。最
终将作用力输出给联轴器。
式中,g——重力加速度矢量。则重力正表示为:
万方数据
6期
杜静等:大型风力发电机齿轮箱全柔体动力学建模与仿真分析
1437
式中,咖——模态向量矩阵,中=[咖。,咖:,…,咖。】,
Ⅳ为模态向量数,通常Ⅳ远小于物体的自由度数; q.=g。@——模态坐标。对式(12)求一阶导数,便 可求的P点的速度向量:
后曲J
式中,s一¨——轴承内外圈的相对位移,S吣.。=
l
I}
| I J l。 | ¨ l l l’ , } 、。1 | \
l
lx,Y。彳。0。P,。P,l|lI风幽。——轴承所受力㈤,
FB。dy'。=IF;。F,。Fd M,。鸩,M。11;K“。咖——轴
承刚度矩阵;S吣,,——轴承内外圈的相对位移。 由于轴承的力学特性是轴承6个方向不同自 由度之间的相互耦合,所以轴承的刚度矩阵中非对
z z’
坐标作为广义坐标来减缩系统的自由度,降低求解
规模阳]。
FEMBS模块作为有限元分析软件和SIMPACK 软件之间的接口,此模块生成了柔性体动力学仿真 所需要的参数,有限元分析软件用来分析柔性体的 应力、应变及模态振型等参数,最终通过此接口在
SIMPACK中生成完整的柔性体模型n引。 在齿轮箱全柔性体模型中轴承、齿轮、花键与 轴之间的力和力矩通过弹簧阻尼系统来传递,本文
(5)
E=圭J:∥’勘dy2圭姜mi";q+∞jt∞t
=告P膨(f)亭
1.2齿轮箱动力学模型的建立 对齿轮箱动力学模型的仿真要求所建立的 模型能准确反映出齿轮箱真实的动力学特性,
Jan
式中,rn。——节点i的模态质量;P——物体的密 度;V——物体的体积;Ii——物体的转动惯量; M(手)——质量矩阵,为三阶方阵,其矩阵形式可表
基于Romax的风电齿轮箱齿轮修形仿真分析_李瑞亮

Wt烌 . 0 4 Δ 1 u =5+0 . 0 4 Wt 烍 Δ 2 u =0 烎
F t ; 式中 , Wt 为单位齿宽载荷 , Wt= ( ) F t 为齿轮切向 bN
力, b 为齿轮有效宽度 , N; mm。 根据会田俊夫 推 荐 的 方 法
[ 7]
1 0 2 5 1 6 6 2 1
, 长 修 形 长 度 为 1=
Hale Waihona Puke 中心距) , 短 修 形 长 度 为 1= ε p b( -1 mm。
1 ( ) , 单位为 p b ε -1 2
常用的修形曲线有直线和抛物线 。 1. 2 齿向修形 进行齿轮修 形 的 目 的 就 是 使 齿 向 载 荷 分 布 趋 于 均匀 , 同时齿面上不产生应力集中 。 如果齿面上接触线一直 延 伸 到 轮 齿 端 部 , 将导致 轮齿的转角处局部应力过 大 , 从而引起齿面剥落或疲 劳损伤 , 所以 我 们 在 齿 向 修 形 方 面 , 对高速级小齿轮 采用齿端修薄 + 鼓形修形 + 螺 旋 角 修 形 的 综 合 方 法 , 如图 1。
5] 。齿廓修形是指将齿轮副啮合的 会出现啮 合 干 涉 [
风力发电机关键部件之一 , 功率等级从几百千瓦级到
3-4] , 如 何 提 高 齿 轮 箱 的 性 能、 兆瓦级 [ 延长寿命一直
是风力发电 领 域 的 热 点 问 题 。 齿 轮 修 形 正 是 一 种 可 有效改善齿 轮 啮 合 性 能 , 避 免 出 现 偏 载 等 不 良 现 象, 提高齿轮承载能力 , 延长齿轮箱寿命的方法 。 本文借助 R 对 a x W i n d 出色的 仿真 分 析 功 能 , o m 得 2. 5 MW 风电齿轮箱高 速 级 小 齿 轮 进 行 仿 真 分 析 ,
高负载增速齿轮箱结构设计及运动学仿真

高负载增速齿轮箱结构设计及运动学仿真[摘要]利用Solidworks三维软件建立增速齿轮箱三维模型,并利用Admas软件对齿轮进行运动仿真分析,最后对齿轮箱的主要零部件进行了应力应变分析,通过这些方式方法,更加直观地了解了齿轮箱的运动机理,掌握了齿轮箱工作过程中各零部件的应力状态,为后续的优化设计提供了参考依据,降低了生产成本,提高了设计效率。
[关键词]三维设计;运动仿真;应力应变;齿轮箱0 引言随着近代工业技术的高度发展,齿轮箱正朝着高速、高效和强力方向发展,传动系统传递的功率不断增大,齿轮箱要求能在高速、高负载的环境下平稳工作,对齿轮箱的强度以及稳定性要求大大提高,特别是在大型工程机械和航天航空等机械工业中应用广泛[1]。
但是在实际工作过程中,很难掌握齿轮箱的运动动态及受力情况,因此利用三维设计软件、admas等[2-4]对齿轮箱的运行过程进行仿真,分析齿轮箱工作过程的受力情况、啮合状态,并以此为基础修改齿轮箱参数,对齿轮箱进行优化设计,提高了设计效率,降低了设计成本,具有重大的意义。
1 增速齿轮箱模型的建立及虚拟装配本文所研究的高负载齿轮箱参数如表1所示。
表1 齿轮参数模型建立采用Solidworks三维软件。
通过拉伸,切除,旋转等命令及相关工具箱建立齿轮箱三维模型并进行虚拟装配,增速齿轮箱装配体如图1所示,爆炸图如图2所示。
图1增速器装配体的模型图2增速齿轮箱装配体的爆炸视图2 增速齿轮箱的运动仿真2.1 模型的导入及约束添加将齿轮模型导入Admas运动仿真软件中,导入后的模型如图3所示。
图3导入Admas中的齿轮副模型之后,给齿轮副添加旋转副,定义齿轮的材料属性,包括密度(Density)、杨氏模量(Young’s Modulus)、泊松比(Poisson’ratio)等各类参数,为齿轮副添加运动与负载扭矩,将转速1000rpm设在输出端。
定义动作为MOTION_1,加载于Jiont_2,Type为Rotational。
采用VRML的齿轮变速箱虚拟模型的实现
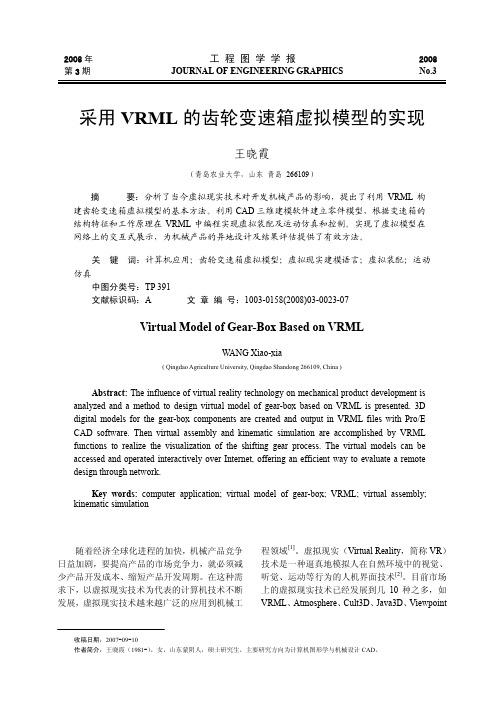
随着经济全球化进程的加快,机械产品竞争日益加剧,要提高产品的市场竞争力,就必须减少产品开发成本、缩短产品开发周期。
在这种需求下,以虚拟现实技术为代表的计算机技术不断发展,虚拟现实技术越来越广泛的应用到机械工程领域[1]。
虚拟现实(Virtual Reality,简称VR)技术是一种逼真地模拟人在自然环境中的视觉、听觉、运动等行为的人机界面技术[2]。
目前市场上的虚拟现实技术已经发展到几10种之多,如VRML、Atmosphere、Cult3D、Java3D、Viewpoint2008年 工 程 图 学 学 报2008第3期 JOURNAL OF ENGINEERING GRAPHICS No.3采用VRML的齿轮变速箱虚拟模型的实现王晓霞(青岛农业大学,山东青岛 266109)摘要:分析了当今虚拟现实技术对开发机械产品的影响,提出了利用VRML构建齿轮变速箱虚拟模型的基本方法。
利用CAD三维建模软件建立零件模型,根据变速箱的结构特征和工作原理在VRML中编程实现虚拟装配及运动仿真和控制。
实现了虚拟模型在网络上的交互式展示,为机械产品的异地设计及结果评估提供了有效方法。
关键词:计算机应用;齿轮变速箱虚拟模型;虚拟现实建模语言;虚拟装配;运动仿真中图分类号:TP 391文献标识码:A 文章编号:1003-0158(2008)03-0023-07Virtual Model of Gear-Box Based on VRMLWANG Xiao-xia( Qingdao Agriculture University, Qingdao Shandong 266109, China )Abstract: The influence of virtual reality technology on mechanical product development is analyzed and a method to design virtual model of gear-box based on VRML is presented. 3D digital models for the gear-box components are created and output in VRML files with Pro/E CAD software. Then virtual assembly and kinematic simulation are accomplished by VRML functions to realize the visualization of the shifting gear process. The virtual models can be accessed and operated interactively over Internet, offering an efficient way to evaluate a remote design through network.Key words: computer application; virtual model of gear-box; VRML; virtual assembly;kinematic simulation收稿日期:2007-09-10等。
- 1、下载文档前请自行甄别文档内容的完整性,平台不提供额外的编辑、内容补充、找答案等附加服务。
- 2、"仅部分预览"的文档,不可在线预览部分如存在完整性等问题,可反馈申请退款(可完整预览的文档不适用该条件!)。
- 3、如文档侵犯您的权益,请联系客服反馈,我们会尽快为您处理(人工客服工作时间:9:00-18:30)。
线上虚拟仿真实习报告
一、实验目的:
大型齿轮箱集成度高、结构复杂、性能要求高,受资金、场地的限制,实物实验成本高、箱体内部结构不易见、动态运行参数不易测,难以开展系统级传动系统结构设计能力训练。
依托重庆大学机械工程双一流学科、机械传动国家重点实验室和国家级机械基础实验教学示范中心、机械基础及装备制造国家虚拟仿真实验教学中心等国家级教学科研平台,与行业、企业合作共建、共享,将国家级科研成果转化为实验教学内容,充分运用信息技术开展虚拟仿真实验教学,有效解决了教学难题,提升学生机械传动系统综合设计能力和解决复杂工程问题的能力,满足产业发展对人才知识结构需求。
实验目的:
(1)通过交互式减速箱结构分析实验软件,了解减速器箱体内部结构,学习掌握减速器箱体结构如何综合设计满足功能要求、强度刚度要求、加工工艺要求、装配定位要求,学习减速器辅助部件的选择和设计;
(2)通过学习在线学习环节,学习应用现代先进设计方法和手段进行机械传动系统性能仿真分析的方法,了解传动系统参数对机械传动系统性能的影响,学习机械传动系统零部件强度和疲劳寿命分析的方法;
(3)通过工程案例虚拟仿真分析和虚拟装配实验环节,了解工程问题的复杂性,学习和掌握机械传动系统综合设计能力和解决复杂工程问题的能力。
(4)根据教师发布的创新应用题目,进行机械传动系统方案设计和评估,获得满足要求的机械传动系统设计方案。
二、实验原理:
实验教学系统采用交互式虚拟仿真实验软件与工程软件的集成,学生从交互式减速器结构认知到复杂齿轮箱工程案例分析实践,训练机械传动系统设计分析能力,实现知识与能力渐进提升。
按照机械传动系统设计认知规律,构建了层次化、模块化的实验教学系统:从减速器结构分析→单级圆柱齿轮减速器虚拟仿真分析→双级圆柱齿轮减速器虚拟仿真分析→复杂工程案例虚拟装配→复杂工程案例仿真分析。
减速器结构分析模块:通过问题导向,学习齿轮箱箱体结构如何满足功能要求、强度刚度要求、加工工艺要求、装配定位要求。
了解轴系结构和功能特点,油面指示器、放油孔、定位销、吊装、加强筋、密封部件等辅助部件的选择和设计。
单级圆柱齿轮减速器虚拟仿真分析模块:建立单级圆柱齿轮减速器分析模型,并进行齿轮、轴的受力、应力、接触斑点、轴承的损伤分析,为二级圆柱齿轮分析奠定基础。
此模块用于非机类、近机类专业的实验教学。
双级圆柱齿轮减速器虚拟仿真分析模块:建立双级圆柱齿轮减速器分析模型,并进行齿轮、轴的受力、应力、接触斑点、错位量、轴承的损伤分析,齿轮修形、箱体的变形影响分析,为工程问题求解奠定基础。
此模块用于机类、近机类专业的实验教学。
工程案例虚拟装配模块:以2MW风电机组齿轮箱对象,通过交互装配练习,使学生熟悉轴系结构的装配顺序和装配工艺,拓宽学生的思路,丰富学生的知识储备。
工程案例仿真分析模块:通过问题导向,对 2MW风电机组齿轮箱工程案例,完成仿真分析,获得润滑油温升与轴承油膜厚度的关系、各轴承的损伤度分析、部件(齿轮、轴承和轴)的错位量、耐久性、箱体的变形对传动系统性能的影响。
本实验对象为机类、近机类、非机类专业大三学生,教师可以根据不同的教学要求进行模块组合,实验内容可拓展,柔性好,有效提升了实验效果。
三、实验仪器(装置或软件等):
减速器结构分析虚拟实验软件
ROMAX机械传动系统性能分析软件
虚拟装配虚拟实验软件
单级圆柱齿轮减速器(虚拟)、双级圆柱齿轮减速器(虚拟)、2MW风电齿
轮箱(虚拟)。
四、实验步骤及方法(包括实验过程记录、实验现象及原始数据记录等):
(1)实验方法描述:
用交互式减速器结构分析虚拟仿真实验,有效解决齿轮箱箱体内部结构复
杂、不可见,学生学习掌握困难问题。
用行业一流软件ROMAX进行减速器性能虚
拟仿真分析,有效解决解决受资金、场地的限制,系统性能参数不易测量、系统
级知识集成应用能力训练和设计验证缺乏问题。
用“2MW风电机组齿轮箱”工程
案例做仿真分析和虚拟装配实验,将工程问题的复杂性主动融入实验教学内容
中,培养学生解决复杂工程问题能力。
(2)学生操作步骤说明:
1)登录实验教学门户网站,点击实验分类下各栏目,了解各专业实验教学
要求和实验环节。
2)点击实验预习,查看实验指导书、ppt课件、实验报告等。
3)单击减速器结构分析虚拟实验“操作实验”,进入减速器结构分析虚拟
实验页面。
单击“开始实验”按钮,即可开始实验。
实验主体内容包括减速器概述、箱
体结构、附件结构和轴系结构四部分内容,通过人机交互完成减速器结构分析虚
拟实验任务。
由于篇幅限制,详细操作步骤可参考《减速器结构分析虚拟仿真实验指导书》。
4)单击在线测试按钮“在线测试”,完成减速器结构分析在线测试题,系统自动批改。
5)单击图示齿轮箱系统设计仿真分析操作实验按钮,进入虚拟实验列表,单击二级圆柱齿轮仿真分析进入实验页面。
单击“操作演示”按钮,打开二级圆柱齿轮减速器仿真分析任务录屏,学习应用ROMAX软件进行二级圆柱齿轮减速器建模与仿真分析方法:
a)新建一个模型,添加齿轮箱装配,并选择空齿轮箱。
b)建立两个概念齿轮对。
c)建立高速轴、中间轴、低速轴装配。
d)添加低速级概念齿轮和刚度轴承,生成概念齿轮箱模型,定义功率载荷及工况。
e)对概念齿轮对进行细化设计,通过定义齿轮的精度等级、材料和轮齿的表面粗糙度等把概念齿轮对转化成细节齿轮对。
f)选择轴承型号。
g)生成详细减速器模型。
h)添加各种不同的工况,进行系统仿真分析。
i)轴变形及强度分析。
j)轴承损伤分析。
k)齿轮啮合错位分析。
7)单击门户网站在线测试按钮,键入在线测试页面,学生完成减速器仿真分析在线测试题,系统自动批改。
8)学习工程案例—风电齿轮箱虚拟仿真分析。
因篇幅限制,具体不再一一详述,参照录屏步骤学习并完成2MW风电齿轮箱建模与仿真分析。
9)完成工程案例—风电齿轮箱虚拟仿真分析在线测试题。
10)完成工程案例虚拟装配实验。
通过交互,完成工程案例的背景知识学习、虚拟装配实验和在线虚拟装配测试。
11)创新应用研讨
学生通过线上学习,具备运用现代设计方法进行齿轮箱系统方案设计和评估能力。
线下开展项目式实验教学,学生以小组为单位,根据教师发布的创新应用题目,进行齿轮箱传动系统方案设计和分析评估。
通过问题导向,研讨质疑,培养学生发现问题、解决问题的能力,促进机械传动综合设计能力养成,有效提升实验教学效果。
五、实验结果与讨论(包括数据处理及实验结果分析等)
减速器的作用:
减速器的类型
轴上传动件的布置:
箱体的成型工艺:
箱体的附件结构作用:
窥视孔和窥视孔盖:窥视孔通常在上箱盖顶部并能够直接观察到齿轮啮合部位处。
窥视孔大小以手能伸入进行操作为准。
通气器:使箱体内热涨空气能够自由排出,保持箱内外压平衡,提高箱体缝隙处的密封性
放油螺塞:放有孔的位置位于油池最低处,安装在减速器不与其他部件靠近的一侧。
油标尺:用来检查箱内油面高度,常被安装在便于观测油面和油面稳定之处。
六、实验总结及心得体会:
通过这次的大型齿轮箱结构设计与分析虚拟仿真实验,在教学视频的分析和
讲解下,让我能够学到更多的理论知识,同时也增加自己对大型齿轮箱结构有了
进一步的认识和了解。
对今后遇到大型齿轮箱结构提供了很大的帮助。
线上实习让每一位热爱学习的人可以随时随地的学习,不受时间地点的限
制。
本实验大型齿轮箱结构设计与分析虚拟仿真实验,让我在线上就可以充分的
了解其原理和整个流程系统的流程信息,我体会到,我们将大学里所学的知识和
日常中的实践所结合在一起,用实践来检验真理。
更好的取学习和了解更多的知
识。
XXXX学院
日期:XXXX年XX月XX日。