薄壁件深腔加工
薄壁深腔零件上小螺孔的数控加工技术

6 ) 如果深腔薄壁类的零件有盒体和盒盖 , 由于盖板和盒体 进 行装 配的时候往往使用沉头螺钉进行联结 , 需要保证 螺纹孔 和沉孔保持 同轴 , 位置度公 差一般 为 ± 0 3 0 5 m m 左右 。因此 , 盒体上 的小螺孔加工完成 以后 , 对盒盖上 的沉孔进 行加工的 时
候, 需要使用铣夹具来保证 和盒体上小螺孔 的位置度的要求。
3 小 螺 纹 加 工 实 验
的时候丝锥在空中受到的负荷作用不稳定 。除此之外 , 薄壁深
腔 的 零 件 在 钳 口装 夹 的 过程 中 , 如果用力过大就会使得 型腔 内 部 的装 夹 产 生 形 变 , 如果 装夹不 牢 固, 那 么 加 工 螺 孔 的 整 个 型 腔 更 加 容 易 发 生 振 动 的 现象 。其 次 , 对 于 薄 壁 深 腔 零 件 的 制 造 材料一般都是热轧板料 , 经常会存在一些 比较硬 的质点。而且
d o i : 1 0 . 3 9 6 9 / j . i s s n . 1 0 o 6—8 5 5 4. 2 0 1 5 . 0 9 . 1 1 7
1 小螺孔 ̄ j u ' r 问题
在 加 工 的 过程 中 , 在 薄 壁 深 腔零 件上 小 螺 孔 的 加 工 经 常 出 现很多问题 , 我们经过认 真的研究 , 得 出 了可 能 导 致 问 题 的几 种原因。 首先 , 在薄壁深腔的零 件上进 行加工 小螺孔 时 , 由于 型腔 的内壁很薄 , 攻丝过程 中很 容易 产生振动 , 尤 其是在 进行高 速 攻丝 的时候 , 这种震动现 象会变得 更加 明显 , 这就 使得在攻 丝
对此进行确定。
对加工 中心小螺孔 的工艺加工方案进 行合理 的确定 , 对于 螺孔 的加工是很关键 的要素。 由于上面 已经对 于加工过 程 中 的一 些原 因进行 了分析 , 我们 在此基 础上 , 对 于小螺孔 的加工 提 出来 了 如下 加 工 方 案 。 1 )在薄壁深腔零件上加工螺孔时 , 进行两次装 夹。其中 ,
薄壁深腔零件数控铣削加工技术探究
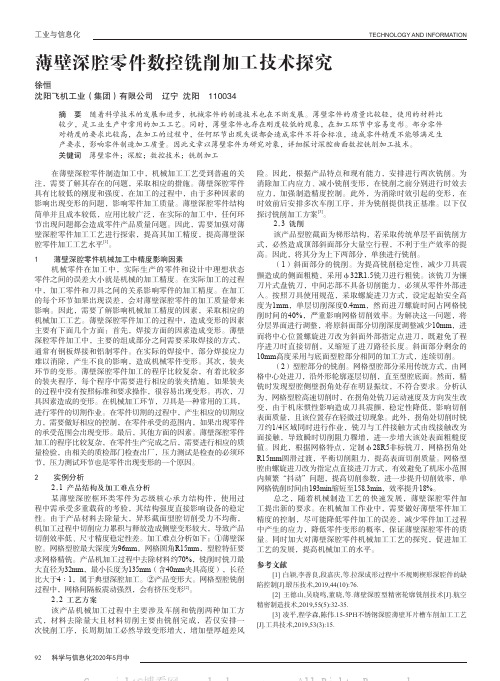
TECHNOLOGY AND INFORMATION
薄壁深腔零件数控铣削加工技术探究
徐恒 沈阳飞机工业(集团)有限公司 辽宁 沈阳 110034
摘 要 随着科学技术的发展和进步,机械零件的制造技术也在不断发展。薄壁零件的质量比较轻,使用的材料比 较少,是工业生产中常用的加工工艺。同时,薄壁零件也存在刚度较低的现象,在加工环节中容易变形。部分零件 对精度的要求比较高,在加工的过程中,任何环节出现失误都会造成零件不符合标准,造成零件精度不能够满足生 产要求,影响零件制造加工质量。因此文章以薄壁零件为研究对象,详细探讨深腔曲面数控铣削加工技术。 关键词 薄壁零件;深腔;数控技术;铣削加工
在薄壁深腔零件制造加工中,机械加工工艺受到普遍的关 注,需要了解其存在的问题,采取相应的措施。薄壁深腔零件 具有比较低的刚度和强度,在加工的过程中,由于多种因素的 影响出现变形的问题,影响零件加工质量。薄壁深腔零件结构 简单并且成本较低,应用比较广泛,在实际的加工中,任何环 节出现问题都会造成零件产品质量问题。因此,需要加强对薄 壁深腔零件加工工艺进行探索,提高其加工精度,提高薄壁深 腔零件加工工艺水平[1]。
2 实例分析 2.1 产品结构及加工难点分析 某薄壁深腔框环类零件为芯级核心承力结件,使用过
程中需承受多重载荷的考验,其结构强度直接影响设备的稳定 性。由于产品材料去除量大,异形截面型腔切削受力不均衡, 机加工过程中切削应力累积与释放造成侧壁变形较大,导致产品 切削效率低、尺寸精度稳定性差。加工难点分析如下:①薄壁深 腔。网格型腔最大深度为96mm,网格圆角R15mm,型腔特征要 求网格精铣。产品机加工过程中去除材料约70%,铣削时铣刀最 大直径为32mm,最小长度为135mm(含40mm夹具高度),长径 比大于4∶1,属于典型深腔加工。②产品变形大。网格型腔铣削 过程中,网格间隔板震动强烈,会有挤压变形[2]。
薄壁深腔零件上小螺孔的数控加工技术

摘
要 : 用数控 加工 中心在深腔 薄壁零件上 利
薄 , 丝时 易引起 振 动 , 其在 高 速 攻丝 时 , 动更 攻 尤 振 显著 , 这样 , 攻丝 时丝 锥 在 孔 中受 到 了变 负 荷 作用 。
此外 , 薄壁深 腔零 件 在 钳 口上 装 夹 时 , 力 稍 大 , 用 型 腔便 会产生 装夹 变形 , 装夹 不牢 , 若 则加工 螺孔 时整 个 型腔更 易产生 振动 。 2 )薄 壁深 腔 类 零 件 的制 造 材 料 一般 是 热 轧 板 料, 常会存 在一些 较硬 的质点 。 3 )攻 丝 时 , 内切 削 条件 恶 劣 , 孔 内部 无法 及 时 供给 切削液 。
把百余 元 的进 口丝锥 , 一般 仅能攻 1 0个 螺孔左 右 。 0 且需经 多次退 刀排 屑 , 加工 效率较 低 。若 发生 断锥 , 大多会 报废 工件 。若 采用 钳 工 加工 时 , 把 国产 丝 一 锥可 平均 加 工 20 0多个 螺 孑 。相 比之 下 , 很 多 0 L 使 企业对 M6以下 螺孑 的加工 放 弃 了数 控 攻 丝 , 不 极 致使 小螺孔 加 工成 本增
加, 无法进行正常生产 。针对该 问题 , 从工 艺角度进
行 了具 体 分析 , 定 了合 理 的 加 工 工 艺路 线 , 计 了 确 设
必要的 夹具, 确定 了合理 的切 削工艺参数 , 并采 用 了
挤 压丝锥 , 避免 了非正常断锥和螺 纹烂 牙, 大幅度提
生 断锥 。 1 2 小 螺孔加 工工艺 方案 .
合 理 确定 加 工 中 心 ( 数 控 铣 床 、 控 钻 攻 中 或 数
心) 加工 小 螺孔 的工 艺路 线 , 螺 孔 的 加 工 至 关 重 对 要 。根据 上述 断锥 原 因 的分 析 , 小 螺孔 的 加 工提 对 出采 取 以下工 艺技术措 施 。 1 )薄壁零 件加 工螺孔 时 , 行 2次装 夹 。 进 铣削 型腔 时的装 夹为第 1 次装 夹 , 其切 削力 大 ,
铝合金薄壁深腔的数控加工
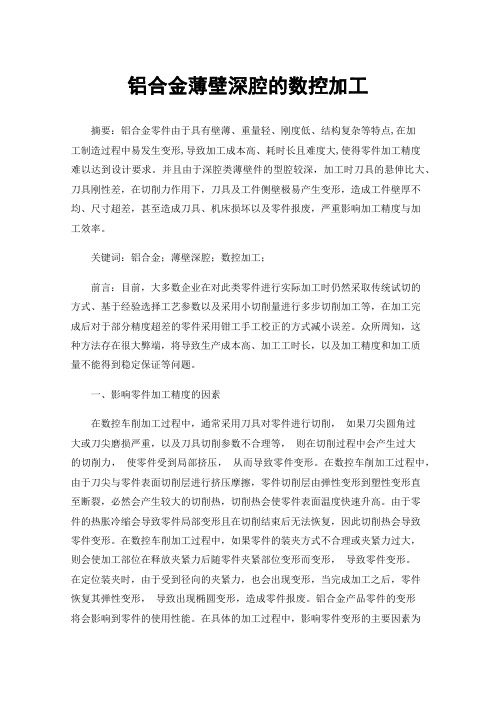
铝合金薄壁深腔的数控加工摘要:铝合金零件由于具有壁薄、重量轻、刚度低、结构复杂等特点,在加工制造过程中易发生变形,导致加工成本高、耗时长且难度大,使得零件加工精度难以达到设计要求。
并且由于深腔类薄壁件的型腔较深,加工时刀具的悬伸比大、刀具刚性差,在切削力作用下,刀具及工件侧壁极易产生变形,造成工件壁厚不均、尺寸超差,甚至造成刀具、机床损坏以及零件报废,严重影响加工精度与加工效率。
关键词:铝合金;薄壁深腔;数控加工;前言:目前,大多数企业在对此类零件进行实际加工时仍然采取传统试切的方式、基于经验选择工艺参数以及采用小切削量进行多步切削加工等,在加工完成后对于部分精度超差的零件采用钳工手工校正的方式减小误差。
众所周知,这种方法存在很大弊端,将导致生产成本高、加工工时长,以及加工精度和加工质量不能得到稳定保证等问题。
一、影响零件加工精度的因素在数控车削加工过程中,通常采用刀具对零件进行切削,如果刀尖圆角过大或刀尖磨损严重,以及刀具切削参数不合理等,则在切削过程中会产生过大的切削力,使零件受到局部挤压,从而导致零件变形。
在数控车削加工过程中,由于刀尖与零件表面切削层进行挤压摩擦,零件切削层由弹性变形到塑性变形直至断裂,必然会产生较大的切削热,切削热会使零件表面温度快速升高。
由于零件的热胀冷缩会导致零件局部变形且在切削结束后无法恢复,因此切削热会导致零件变形。
在数控车削加工过程中,如果零件的装夹方式不合理或夹紧力过大,则会使加工部位在释放夹紧力后随零件夹紧部位变形而变形,导致零件变形。
在定位装夹时,由于受到径向的夹紧力,也会出现变形,当完成加工之后,零件恢复其弹性变形,导致出现椭圆变形,造成零件报废。
铝合金产品零件的变形将会影响到零件的使用性能。
在具体的加工过程中,影响零件变形的主要因素为切削力、切削热和夹紧力。
切削过程中,产生的切削力大小直接影响到切削热和夹紧力,切削热引起铝合金材料的热变形;施加在零件上的夹紧力引起薄壁零件的冷变形;从而容易产生切削力下的振动变形。
铝合金薄壁深腔的数控加工
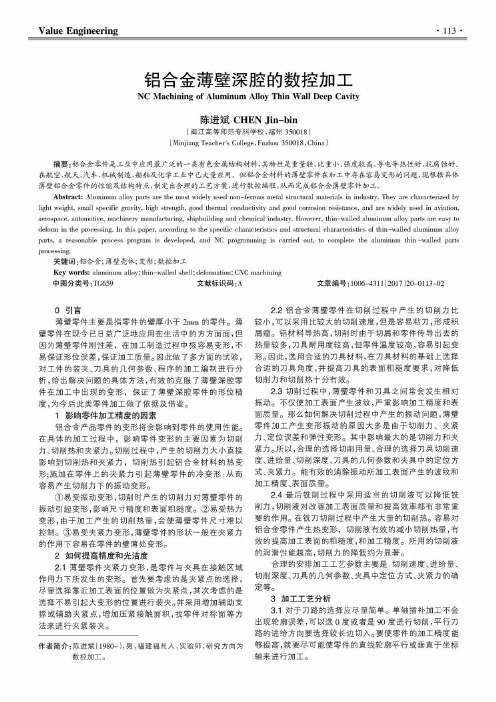
Value Engineering• 113 •铝合金薄壁深腔的数控加工NC Machining of Aluminum Alloy Thin Wall Deep Cavity陈进斌C H E N J i n-b i n(闽江高等师范专科学校,福州350018)(Minjiang Teacher's College, Fuzhou 350018, China )摘要:铝合金零件是工业中应用最广泛的一类有色金属结构材料,其特性是重量轻、比重小、强度较高、导电导热性好、抗腐蚀好。
在航空、航天、汽车、机械制造、船舶及化学工业中已大量应用。
但铝合金材料的薄壁零件在加工中存在容易变形的问题,现根据具体 薄壁铝合金零件的性能及结构特点,制定出合理的工艺方案,进行数控编程,从而完成铝合金薄壁零件加工。
Abstract:Aluminum alloy parts are the most widely used non-ferrous metal structural materials in industr^^. They are characterized by light weight, small specific gravity, high strength, good ther^nal conductivity and good corrosion resistance, and are widely used in aviation, aerospace, automotive, machinery manufacturing, shipbuilding and chemical industry. How,ever, thin-w,alled aluminum alloy parts are easy to defor^m in the processing. In this paper, according to the specific characteristics and structural characteristics of thin-w alled aluminum alloy parts, a reasonable process program is developed, and NC programming is carried out, to complete the aluminum thin -walled parts processing.关键词:铝合金;薄壁壳体;变形;数控加工Key words:aluminum alloy; thin-walled shell; deformation; CNC machining中图分类号:TG659 文献标识码:A 文章编号= 1006-4311(2017)20-0113-02〇引言薄壁零件主要是指零件的壁厚小于2m m的零件。
薄壁深孔零件的数控加工

薄壁深孔零件的数控加工摘要:在机械产品加工中会碰到薄壁深孔不规那么盲孔零件加工,装夹难,常规加工方式是难以完成的。
为此,本文制定相应加工工艺,提出专用夹具的设计方案。
并进一步介绍夹具的制造和利用。
经实践证明,该工装是行之有效的,完全达到了形位公差的精度要求,并提高了生产效率。
关键词:专用夹具工艺进程设备生产效率前言:随着科学技术和社会生产的迅速进展,机械产品日趋复杂,加工困难。
如薄壁深孔件,在夹紧力和切削力的作用下,容易产生变形、振动,阻碍工件精度,工件尺寸不容易操纵,若是不规那么又是盲孔,加倍难以加工。
由于单一机械设备是不能一次装夹把工件加工出来,也存在着多次装夹的重复定位的精度误差,还存在效率和本钱的问题。
为此,设计和制造加工薄壁深孔不规那么盲孔零件的专用夹具,利用夹具,在多种机械设备上高质量、高效加工该工件,不失为一种有效的方式论文内容:一、薄壁深孔不规那么盲孔零件加工装夹难从图1伸缩筒分析:(1)薄壁装夹受力易变形伸缩筒为薄壁深孔筒状盲孔零件,最薄壁厚单边只有,零件单薄;外圆上有凸台带键槽,键槽内6-φ80+ mm孔,厚度不均匀,而且盲孔排屑困难。
常规夹具装夹受力容易变形,使尺寸难于操纵。
(2)伸缩筒带外圆凸台,装夹难车加工时用三爪卡盘装夹卡爪会跟零件上的外圆上凸台产生干与。
若是用四爪装夹零件的精度很难保证,而且校正费时。
铣床常规的夹具用平口钳装夹,平口钳夹紧圆柱体很产生容易松动,凸台铣键槽和钻孔,孔底跟轴心有 mm等公差和尺寸得不到保证。
凸台上的键槽和孔跟零件的轴心对称度会误差较大。
(3)加工工序内容多,重复装夹。
伸缩筒要用到的多种机械设备加工,多次装夹必然带来装夹误差,耗时长,效率低。
这与要求相矛盾。
如Ø,内孔有 mm公差,光洁度要求,用数车精加工很难保证,考虑在加工中心上用绞刀来加工。
整个伸缩筒结构是薄壁孔深且是盲孔的不规那么零件,按常装夹加工困难,质量难保证,效率低。
批量生产还增加本钱。
薄壁零件的加工精度及注意事项
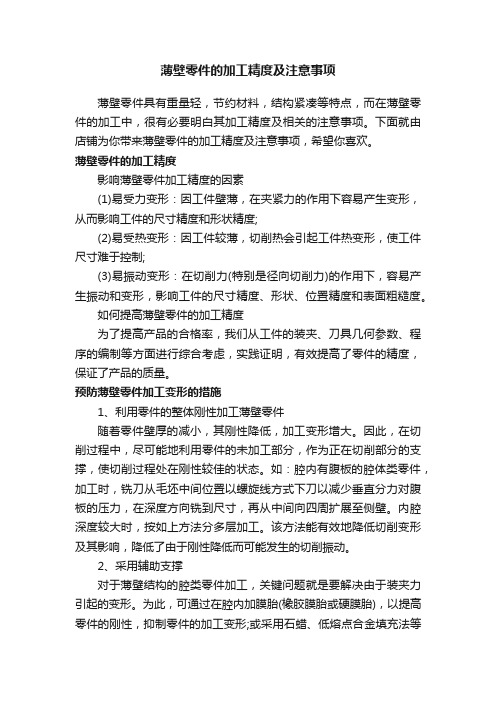
薄壁零件的加工精度及注意事项薄壁零件具有重量轻,节约材料,结构紧凑等特点,而在薄壁零件的加工中,很有必要明白其加工精度及相关的注意事项。
下面就由店铺为你带来薄壁零件的加工精度及注意事项,希望你喜欢。
薄壁零件的加工精度影响薄壁零件加工精度的因素(1)易受力变形:因工件壁薄,在夹紧力的作用下容易产生变形,从而影响工件的尺寸精度和形状精度;(2)易受热变形:因工件较薄,切削热会引起工件热变形,使工件尺寸难于控制;(3)易振动变形:在切削力(特别是径向切削力)的作用下,容易产生振动和变形,影响工件的尺寸精度、形状、位置精度和表面粗糙度。
如何提高薄壁零件的加工精度为了提高产品的合格率,我们从工件的装夹、刀具几何参数、程序的编制等方面进行综合考虑,实践证明,有效提高了零件的精度,保证了产品的质量。
预防薄壁零件加工变形的措施1、利用零件的整体刚性加工薄壁零件随着零件壁厚的减小,其刚性降低,加工变形增大。
因此,在切削过程中,尽可能地利用零件的未加工部分,作为正在切削部分的支撑,使切削过程处在刚性较佳的状态。
如:腔内有腹板的腔体类零件,加工时,铣刀从毛坯中间位置以螺旋线方式下刀以减少垂直分力对腹板的压力,在深度方向铣到尺寸,再从中间向四周扩展至侧壁。
内腔深度较大时,按如上方法分多层加工。
该方法能有效地降低切削变形及其影响,降低了由于刚性降低而可能发生的切削振动。
2、采用辅助支撑对于薄壁结构的腔类零件加工,关键问题就是要解决由于装夹力引起的变形。
为此,可通过在腔内加膜胎(橡胶膜胎或硬膜胎),以提高零件的刚性,抑制零件的加工变形;或采用石蜡、低熔点合金填充法等工艺方法,加强支撑.进而达到减小变形、提高精度的目的。
3、设计工艺加强筋,提高刚性对于薄壁零件,增加工艺筋条,以加强刚性,是工艺设计常用的手段之一。
4、对称分层铣削,让应力均匀释放毛坯初始残余应力对称释放,可以有效减小零件的加工变形。
对厚度两面需进行加工的板类零件,采用上下两面去除余量均等的原则,进行轮流加工,即在上平面去除δ余量,然后翻面,将另一面也去除δ余量。
薄壁不锈钢类零件加工工艺探讨
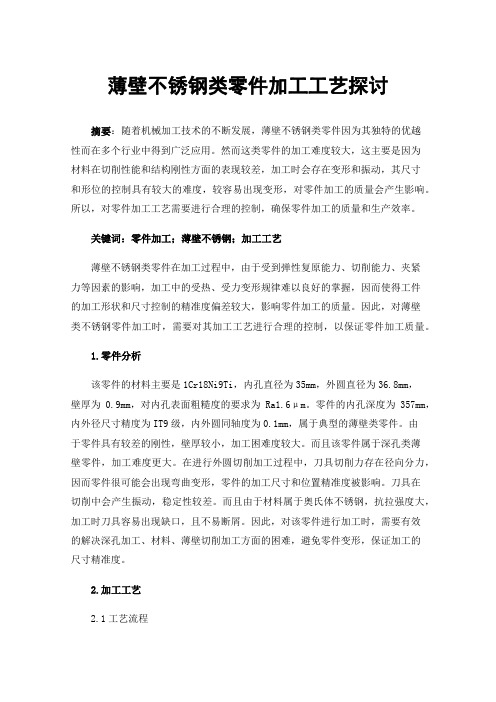
薄壁不锈钢类零件加工工艺探讨摘要:随着机械加工技术的不断发展,薄壁不锈钢类零件因为其独特的优越性而在多个行业中得到广泛应用。
然而这类零件的加工难度较大,这主要是因为材料在切削性能和结构刚性方面的表现较差,加工时会存在变形和振动,其尺寸和形位的控制具有较大的难度,较容易出现变形,对零件加工的质量会产生影响。
所以,对零件加工工艺需要进行合理的控制,确保零件加工的质量和生产效率。
关键词:零件加工;薄壁不锈钢;加工工艺薄壁不锈钢类零件在加工过程中,由于受到弹性复原能力、切削能力、夹紧力等因素的影响,加工中的受热、受力变形规律难以良好的掌握,因而使得工件的加工形状和尺寸控制的精准度偏差较大,影响零件加工的质量。
因此,对薄壁类不锈钢零件加工时,需要对其加工工艺进行合理的控制,以保证零件加工质量。
1.零件分析该零件的材料主要是1Cr18Ni9Ti,内孔直径为35mm,外圆直径为36.8mm,壁厚为0.9mm,对内孔表面粗糙度的要求为Ra1.6μm。
零件的内孔深度为357mm,内外径尺寸精度为IT9级,内外圆同轴度为0.1mm,属于典型的薄壁类零件。
由于零件具有较差的刚性,壁厚较小,加工困难度较大。
而且该零件属于深孔类薄壁零件,加工难度更大。
在进行外圆切削加工过程中,刀具切削力存在径向分力,因而零件很可能会出现弯曲变形,零件的加工尺寸和位置精准度被影响。
刀具在切削中会产生振动,稳定性较差。
而且由于材料属于奥氏体不锈钢,抗拉强度大,加工时刀具容易出现缺口,且不易断屑。
因此,对该零件进行加工时,需要有效的解决深孔加工、材料、薄壁切削加工方面的困难,避免零件变形,保证加工的尺寸精准度。
2.加工工艺2.1工艺流程对该零件进行加工时,工艺流程为:粗车外圆将多数的切削量去掉,将外圆作为基准进行内孔加工。
接着再以内孔为基准对外圆进行加工,对工艺方法进行合理的控制,将加工中切削力、装夹产生的影响降低,有效的控制加工过程的变形量。
薄壁件加工注意事项

薄壁件加工注意事项薄壁件加工是现代制造业中常见的一种加工方法,其特点是工件壁厚相对较薄,常用于汽车、电子、航空等领域。
在进行薄壁件加工时,需要注意以下几个方面。
材料的选择非常重要。
薄壁件通常使用的材料有铝合金、不锈钢、钛合金等,这些材料具有良好的可塑性和强度,能够满足薄壁件的使用要求。
在选择材料时,需要考虑工件的使用环境、力学性能要求等因素,确保选择的材料具有足够的耐腐蚀性和机械强度。
加工工艺要合理。
薄壁件加工过程中,常用的工艺包括冲压、拉伸、剪切等。
在进行冲压加工时,需要控制好冲头的形状和尺寸,避免产生过大的应力集中,导致工件变形或破裂。
在进行拉伸加工时,需要控制好拉伸速度和温度,以避免材料的过度延展和变形。
剪切加工时,要注意切割刀具的选择和刀口的尺寸,以确保切割线的质量和工件的精度。
加工设备的选用也是关键。
薄壁件加工对设备的要求比较高,需要使用高精度的数控机床或冲床。
在使用机床时,要控制好切削参数,避免过大的切削力和热量对工件造成损伤。
同时,要定期检查和维护设备,确保其正常运行和精度稳定。
在加工过程中,还要注意工件的夹紧和支撑。
由于薄壁件的壁厚较薄,容易产生变形和振动。
因此,在夹紧工件时,要选择合适的夹具和夹持方式,确保工件能够稳定固定,避免在加工过程中发生移位和变形。
同时,在加工过程中,要提供足够的支撑,避免工件发生弯曲或塌陷。
质量控制是薄壁件加工中的关键环节。
在加工过程中,要密切关注工件的尺寸精度、表面质量和力学性能等指标。
可以采用光学测量、三坐标测量等方法对工件进行检测,确保工件符合设计要求。
同时,要建立完善的质量控制体系,对加工过程进行全面监控和记录,及时发现和纠正问题,提高产品的合格率和一致性。
薄壁件加工是一项复杂的工艺,需要在材料选择、加工工艺、设备选用、夹紧和支撑以及质量控制等方面都加以注意。
只有科学合理地进行薄壁件加工,才能保证产品的质量和性能,满足市场的需求。
薄壁零件机加工工艺及方法分析
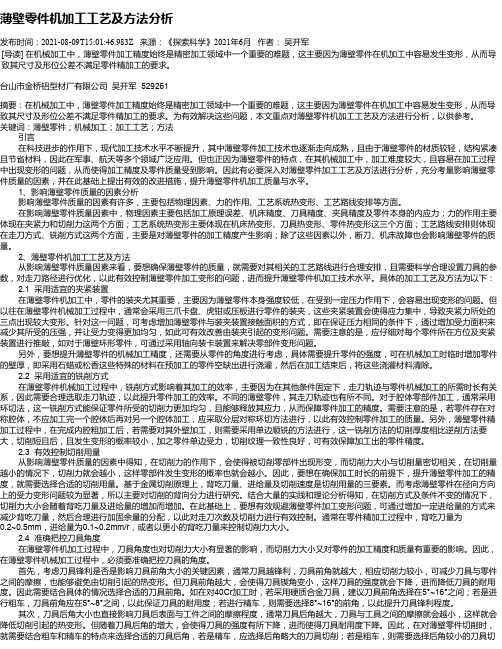
薄壁零件机加工工艺及方法分析发布时间:2021-08-09T15:01:46.983Z 来源:《探索科学》2021年6月作者:吴开军[导读] 在机械加工中,薄壁零件加工精度始终是精密加工领域中一个重要的难题,这主要因为薄壁零件在机加工中容易发生变形,从而导致其尺寸及形位公差不满足零件精加工的要求。
台山市金桥铝型材厂有限公司吴开军 529261摘要:在机械加工中,薄壁零件加工精度始终是精密加工领域中一个重要的难题,这主要因为薄壁零件在机加工中容易发生变形,从而导致其尺寸及形位公差不满足零件精加工的要求。
为有效解决这些问题,本文重点对薄壁零件机加工工艺及方法进行分析,以供参考。
关键词:薄壁零件;机械加工;加工工艺;方法引言在科技进步的作用下,现代加工技术水平不断提升,其中薄壁零件加工技术也逐渐走向成熟,且由于薄壁零件的材质较轻,结构紧凑且节省材料,因此在军事、航天等多个领域广泛应用。
但也正因为薄壁零件的特点,在其机械加工中,加工难度较大,且容易在加工过程中出现变形的问题,从而使得加工精度及零件质量受到影响。
因此有必要深入对薄壁零件加工工艺及方法进行分析,充分考量影响薄壁零件质量的因素,并在此基础上提出有效的改进措施,提升薄壁零件机加工质量与水平。
1、影响薄壁零件质量的因素分析影响薄壁零件质量的因素有许多,主要包括物理因素、力的作用、工艺系统热变形、工艺路线安排等方面。
在影响薄壁零件质量因素中,物理因素主要包括加工原理误差、机床精度、刀具精度、夹具精度及零件本身的内应力;力的作用主要体现在夹紧力和切削力这两个方面;工艺系统热变形主要体现在机床热变形、刀具热变形、零件热变形这三个方面;工艺路线安排则体现在走刀方式、铣削方式这两个方面,主要是对薄壁零件的加工精度产生影响;除了这些因素以外,断刀、机床故障也会影响薄壁零件的质量。
2、薄壁零件机加工工艺及方法从影响薄壁零件质量因素来看,要想确保薄壁零件的质量,就需要对其相关的工艺路线进行合理安排,且需要科学合理设置刀具的参数,对走刀路径进行优化,以此有效控制薄壁零件加工变形的问题,进而提升薄壁零件机加工技术水平。
薄壁零件加工工艺方法分析

薄壁零件加工工艺方法分析摘要:为解决薄壁零件在机械加工中易变形、尺寸公差、形位公差难于保证的问题,文章通过合理安排工艺路线、高速铣、对称分层铣削、增加工艺加强筋的加工方法,有效地降低了零件在机械加工过程中的变形,提高了零件精度,为类似薄壁件的加工提供了参考。
关键词:高速铣;对称分层铣;加强筋薄壁零件以质量轻、节约材料、结构紧凑等优点,已广泛应用于航空航天工业。
但该类刚度较低,易变形,加工精度难以保证,直接影响到产品的加工质量。
1 引起薄壁件变形的因素分析引起薄壁件变形的因素,如图1所示。
对影响薄壁件加工精度的因素有所了解后,我们通过对工艺参数进行合理设置,对工艺路线进行合理安排刀具参数、走刀路径与方式等方面进行考虑及优化,控制影响变形的可控因素,从而减小零件变形。
2 装夹方式的合理选择对于薄壁件而言,零件的装夹是一个非常重要的问题。
在选择定位基准进行装夹时,通常选用面积较大、精度较高的面,装夹点应尽可能对称。
常用装夹方式有:虎钳、压板、三爪卡盘。
对于铣加工来说,通常时采用虎钳在工件两端施加作用力而夹紧,但对于薄板类来说容易造成装夹变形,如图2所示,压板装夹如图3所示。
而压板装夹不仅可以解决受夹紧力装夹变形的问题,而且四周铣削后,切断前,零件与毛坯之间有0.1~0.2 mm的粘接,所以内应力的产生不会造成零件有较大变形。
现在对于精度特别高的零件采用真空吸盘直接吸附零件,不需要额外的外力夹紧工件,从而能有效的减小零件变形。
3 数控铣削方式的合理选择零件加工中,在其它条件不变,加工时间的长短取决走刀轨迹的长短。
因此合理选择走刀轨迹对提高加工效率有很大影响。
对于腔体类零件一般走刀轨迹有行切法和环切法两种,如图4所示。
与行切法相比,零件受对称切削力,应力释放均匀,可一定程度上提高零件的加工精度。
同时,当零件上有对称腔体时,不宜一个腔体加工完再加工另一个腔体,采用分层对称环切可有效控制产品的质量。
精加工时,一般内腔已经进行了粗加工,这时再加工腔体外壁时,尤其由于薄而长的零件。
薄壁筒类零件加工浅析
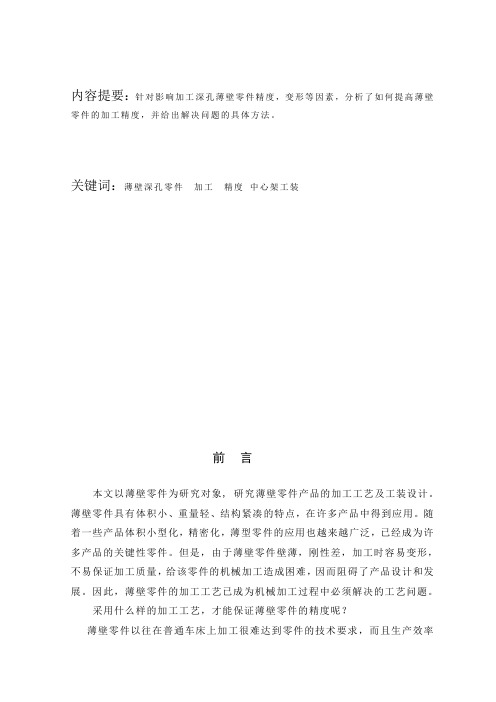
内容提要:针对影响加工深孔薄壁零件精度,变形等因素,分析了如何提高薄壁零件的加工精度,并给出解决问题的具体方法。
关键词:薄壁深孔零件加工精度中心架工装前言本文以薄壁零件为研究对象, 研究薄壁零件产品的加工工艺及工装设计。
薄壁零件具有体积小、重量轻、结构紧凑的特点,在许多产品中得到应用。
随着一些产品体积小型化,精密化,薄型零件的应用也越来越广泛,已经成为许多产品的关键性零件。
但是,由于薄壁零件壁薄,刚性差,加工时容易变形,不易保证加工质量,给该零件的机械加工造成困难,因而阻碍了产品设计和发展。
因此,薄壁零件的加工工艺已成为机械加工过程中必须解决的工艺问题。
采用什么样的加工工艺,才能保证薄壁零件的精度呢?薄壁零件以往在普通车床上加工很难达到零件的技术要求,而且生产效率低,不能适应大批量加工的要求。
因此,研究薄壁零件的加工工艺,对于保证产品质量具有重要意义。
根据薄壁零件的工艺特征,通过理论分析和试验确定一种利用数控车床加工该零件的合理的工艺方法,并设计其专用工装夹具。
经过多次试验,我们采用的这种在数控机床上加工的工艺方法和设计的专用工装夹具,较好地解决薄壁零件的加工问题,。
由于数控车床按照预定的加工程序自动加工,加工过程中避免了由于操作人员造成的人为误差,提高了零件加工精度,对于保证产品质量的稳定起到重要作用。
而数控车削技术的应用,极大的提高了生产效率。
同时,由于设计和采用了专用的夹具,解决了零件薄壁易变形,加工性能差的难题。
本设计的意义在于,通过对该薄壁零件加工工艺以及工装夹具的设计,总结利用数控技术和专用夹具加工薄壁零件的经验,并从理论上加以分析和提高,给制造薄壁零件加工工艺提供依据。
薄壁零件的加工问题,一直是较难解决的。
薄壁件目前一般采用数控车削的方式进行加工,为此要对工件的装夹、刀具几何参数、程序的编制等方面进行试验,从而有效地克服了薄壁零件加工过程中出现的变形,保证加工精度。
影响薄壁零件加工精度的因素有很多,但归纳直来主要有以下三个方面:(1)受力变形因工件壁薄刚性很差,车削是装夹不当在夹紧力的作用下容易产生变形,从而因为切削力及重力影响使工件发生弯曲变形从而影响工件的尺寸精度和形状精度。
盘件狭窄深腔的加工技术研究

Ch i n a Ne w Te c h n o l o g i e s a n d Pr o d u c t s !! 占2 源自一 工 业 技 术
盘件狭 窄深腔 的加工技术研究
于 洁 史前 凯
( 沈阳黎 明航 空发动机 ( 集 团 )有限责任 公司 ,辽 宁 沈 阳 1 1 0 0 3 4 )
中图分 类 号 :T H 1 3
1概 述
文 献标 识码 :A
对 于 狭 窄 腔 体结 构而 言 ,须 使用 非 止 振 刀 或 打 刀 的现 象 ,加 工参 数 选 定 恒
随着 我 国航 空 业 的 发 展 ,发 动 机 的 标 刀杆 加 工 。 因研 制 条 件 有 限 ,本案 在 线速 度 为 ¥ 5 0 m / m i n , 进 给量 f = 0 . 0 8 m m / r ,
研 制 已成 为我 们 生 产 中 的重 点 ,该 零 件 是 发 动 机 上 的关 键 件 ,零件 材 料 为 高 温 合 金 。该 零 件 外 圆尺 寸 小 ,结 构 复 杂 , 其 辐 板 与 斜 面构 成 的深 腔 结 构 给加 工 带 来 困 难 。通 过 对 该 零 件 机 械 加 工 研 究 , 从 刀 具 结 构 、切 削 用 量 、模 拟加 工 和数 控 程 序 控 制 等 方 面 进 行 分 析 、研 究 。 掌 握 这 种 小 直 径 深 腔结 构 盘 类 件 的 加 工技 术, 提 升航 空发 动机 盘类件 的制造水 平 。 2零件 简介 2 . 1 零件 结构 特点 该 零 件 是 位 于 鼓筒 组 件 中最 后 一 级 盘件 ,零 件 结 构 较 特殊 ,在 研 制 过 程 中 深 腔 的数 控 加 工 控 制 和 薄 壁 内腔 转 接 R 的加 工是 研制 中难 点 。 2 I 2 零 件 的加工难 点分 析 ( 1 )从 零件 的材 料分 析 ,属 于镍 基 高 温 合 金 ,在 切 削 过程 中 ,钼 、铌 、钛 等 金 属 元 素使 刀具 产 生 磨 损 、破 损 等 现 象 ;材料 中 的镍 、铬 等 金属 元 素 使 切 屑 不 易 被 断 开 ,切 屑 容 易 划 伤 零 件 ,影 响 零 件 加 工 表 面 的质 量 ;材料 的导 热 性 能 较 差 ,加 工 过 程 产 生 的 切 削 热量 不 易 散 去 ,加 工 过 程 中硬 化 现 象 较 严 重 ,导 致 切 削 时 刀 具 的 粘 接 现象 较 为 严 重 ,刀具 的磨损 现象严 重 ,耐 用程度 很低 。 ( 2 )从 零 件 的设 计 结 构 及 尺 寸 精 度 分 析 ,该零 件 属 小直 径 深 内腔 结构 薄 壁 零 件 ,其 外 径 直 径 仅 为 3 4 6 . 2 m m, 零 件辐 板 与 安 装 边 斜 壁 形成 一 个 狭 窄 腔 体 ,腔 深 为 3 4 m m, 最 窄 处 为 4 . 5 m m, 腔 体 开 口尺 寸 为 1 8 m m,安 装 边 直 径 为 2 4 6 . 7 6 mm,辐 板 与 轮 毂 交 点 处 直 径 为 1 6 7 . 8 m m,开 口处 距 离 交 点 处 位 置 3 9 m m,且 零 件辐 板 和深 腔 内斜 壁 都是 理 论 直 径 轴 向控 制 点 约 束 的 ,尺寸 公 差 约 束较 严格 。因此 对刀具 结构 、刀杆强 度 、 加 工 轨 迹 等 方 面 均提 出 了较 大 挑 战 。深 腔 内加 工 余 量 大 ,腔体 深 ,敞 开 性 差 , 不 利 用 排 屑 和 加 工 中散 热 ,对 腔 内深 处 加 工表 面质 量有 一定 影响 。 3 零 件 的数 控加 工 3 . 1 刀具 结构 的选 择
薄壁深腔零件的机械加工工艺探讨
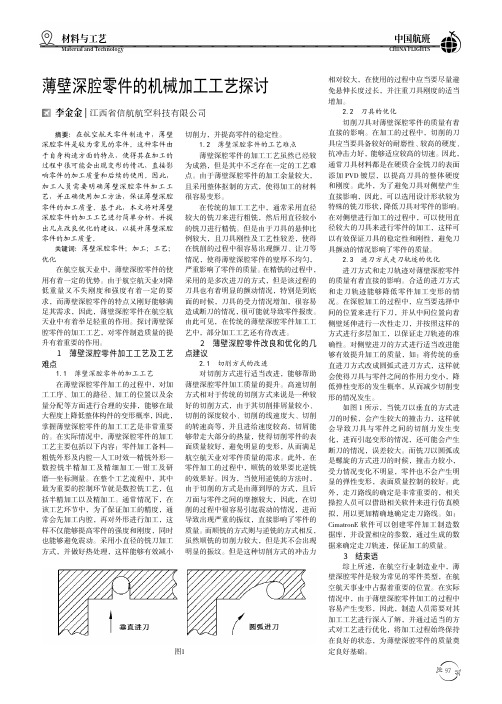
97中国航班材料与工艺Material and TechnologyCHINA FLIGHTS 薄壁深腔零件的机械加工工艺探讨 李金金|江西省信航航空科技有限公司摘要:在航空航天零件制造中,薄壁深腔零件是较为常见的零件。
这种零件由于自身构造方面的特点,使得其在加工的过程中很可能会出现变形的情况,直接影响零件的加工质量和后续的使用。
因此,加工人员需要明确薄壁深腔零件加工工艺,并正确使用加工方法,保证薄壁深腔零件的加工质量。
基于此,本文将对薄壁深腔零件的加工工艺进行简单分析,并提出几点改良优化的建议,以提升薄壁深腔零件的加工质量。
关键词:薄壁深腔零件;加工;工艺;优化在航空航天业中,薄壁深腔零件的使用有着一定的优势。
由于航空航天业对降低重量又不失刚度和强度有着一定的要求,而薄壁深腔零件的特点又刚好能够满足其需求,因此,薄壁深腔零件在航空航天业中有着举足轻重的作用。
探讨薄壁深腔零件的加工工艺,对零件制造质量的提升有着重要的作用。
1 薄壁深腔零件加工工艺及工艺难点1.1 薄壁深腔零件的加工工艺在薄壁深腔零件加工的过程中,对加工工序、加工的路径、加工的位置以及余量分配等方面进行合理的安排,能够在最大程度上降低整体构件的变形概率,因此,掌握薄壁深腔零件的加工工艺是非常重要的。
在实际情况中,薄壁深腔零件的加工工艺主要包括以下内容:零件加工备料—粗铣外形及内腔—人工时效—精铣外形—数控铣半精加工及精细加工—钳工及研磨—坐标测量。
在整个工艺流程中,其中最为重要的控制环节就是数控铣工艺,包括半精加工以及精加工。
通常情况下,在该工艺环节中,为了保证加工的精度,通常会先加工内腔,再对外形进行加工,这样不仅能够提高零件的强度和刚度,同时也能够避免震动。
采用小直径的铣刀加工方式,并做好热处理,这样能够有效减小切削力,并提高零件的稳定性。
1.2 薄壁深腔零件的工艺难点薄壁深腔零件的加工工艺虽然已经较为成熟,但是其中不乏存在一定的工艺难点。
高精度薄壁深腔零件的加工方法

(19)中华人民共和国国家知识产权局
(12)发明专利申请
(10)申请公布号
CN104015016A
(43)申请公布日 2014.09.03(21)申请号CN201410286000.2
(22)申请日2014.06.25
(71)申请人西安北方光电科技防务有限公司
地址710043 陕西省西安市长乐中路35号
(72)发明人刘涛;孙婙;陈贞奇;蔡永斌
(74)专利代理机构西安智萃知识产权代理有限公司
代理人方力平
(51)Int.CI
权利要求说明书说明书幅图
(54)发明名称
高精度薄壁深腔零件的加工方法
(57)摘要
本发明属于高精度薄壁型腔体零件的加工
技术领域,具体涉及到一种高精度薄壁深腔零件
的加工方法,包括以下步骤:步骤一,粗加工;
步骤二,热处理去应力;步骤三,精加工基准
面;步骤四,精加工深腔。
采用该方法实现了加
工薄壁高精度型腔体零件的平面度、平行度、垂
直度、壁厚、深度等各项要求,满足了该类高精
度零件的加工要求。
法律状态
法律状态公告日法律状态信息法律状态2014-09-03公开公开
2014-10-08实质审查的生效实质审查的生效2016-09-28授权授权
权利要求说明书
高精度薄壁深腔零件的加工方法的权利要求说明书内容是....请下载后查看
说明书
高精度薄壁深腔零件的加工方法的说明书内容是....请下载后查看。
薄壁件壳体上,深孔加工也没那么难!
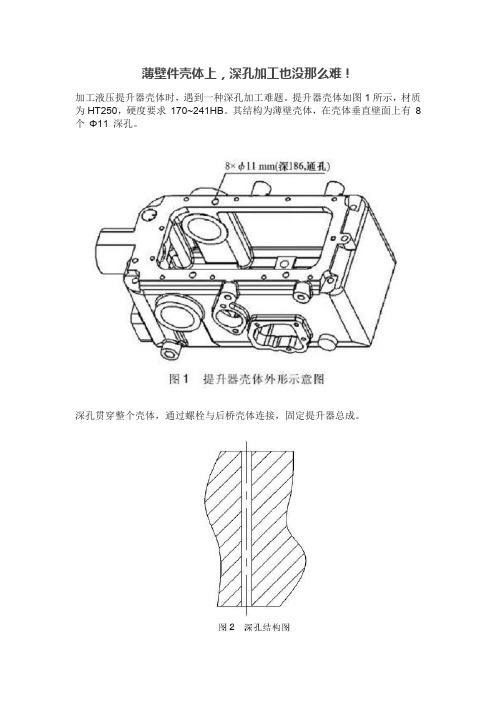
薄壁件壳体上,深孔加工也没那么难!加工液压提升器壳体时,遇到一种深孔加工难题。
提升器壳体如图1所示,材质为HT250,硬度要求170~241HB。
其结构为薄壁壳体,在壳体垂直壁面上有8 个Φ11 深孔。
深孔贯穿整个壳体,通过螺栓与后桥壳体连接,固定提升器总成。
提升器工作时同时承受螺栓预紧力及剪切力,因此,对其位置度要求相对较高。
本提升器壳体加工难点在于8 个贯穿深孔的加工,钻孔深度与钻头直径比值达到17,加工难度较大。
加工思路结合现有生产条件和提升器壳体深孔结构特点,采用的加工方案是: 对深孔加工进行有效分解,将深孔加工分成两道工序,分别从壳体底面和顶面两端对钻。
▲深孔钻加工视频这样避免了加工中刚性差、易引偏的问题,需要解决的重点问题是: 如何保证两端加工时的同轴度问题,深孔同轴度通过定位夹具和加工中心精度保证。
加工方法采用的加工方法如表所示:刀具采用Φ11mm的中心冷却钻头,转速1000r/min,切削速度34.5 r/min,精镗对角两个孔作为10序定位销孔(见图3) 。
夹具方面,为保证10序8个孔能够准确地与前道工序对接,采用一面两销定位,利用5序精镗出来的2个Φ11mm孔为定位销孔,复制5序的加工刀具和切削参数,钻深95mm至通。
加工调试中崩刀此方案的加工精度主要靠设备及夹具精度来保证,在此基础上两次加工,只要中心重合即可实现完美对接。
在实际调试过程中,加工10序与5序孔对接时,出现钻头断裂损坏的情况,如图4所示。
崩刀问题的分析解决4.1 定位问题首先分析夹具对加工精度的影响。
对5序定位孔的尺寸精度和位置精度以及10序定位销的设计及制造精度进行了检测及计算,均在设计要求内。
排除了夹具两次定位不同心的问题。
加工中可能有铁屑或其他杂质依附在夹具表面从而使零件装夹不到位。
利用三坐标,测试了6件产品,测试的内容为5序加工后的其余6个直径11mm孔相对定位孔的位置度,测量结果如表所示。
表2 孔位置度从以上数据可以看出,CV1200B立式加工中心对于位置度的保证精度相对较高,排除了机床、刀具、夹具的影响因素。
[薄壁,零件,工艺]大型薄壁深腔端框零件的车加工工艺分析
![[薄壁,零件,工艺]大型薄壁深腔端框零件的车加工工艺分析](https://img.taocdn.com/s3/m/e69127d7de80d4d8d05a4f93.png)
大型薄壁深腔端框零件的车加工工艺分析1 引言某新型运载火箭为我国最新研制的大型运载火箭,整体直径为 5m,该型号关键结构件卫星支架为倒 F 型结构。
其结构特点为:深腔、大倾斜角和薄壁结构等。
受其自身复杂的结构特点制约,实际加工中存在以下几个工艺问题:装夹困难,装夹位置及压边数量较难选取,装夹位置、数量及装夹方式的选择会严重影响零件加工精度;易变形,该支架为典型的薄壁结构件,加工中随着材料的去除,内应力及热应力导致变形,且在加工过程中让刀严重,加工精度难以保证;排屑困难,由于倾斜深槽的存在,切刀倾斜安装存在困难,并随着切槽深度的增加,将导致排屑不顺畅,以及切屑挤压已加工型面导致结构变形甚至槽底开裂;测量困难,由于设计所给多个尺寸为尖点尺寸,加工过程中不易测量。
本文以该新型运载火箭卫星支架为研究对象,根据该结构件的加工特性,提出了一系列的工艺优化方法,并最终在保证设计精度的前提下实现该零件的加工。
2 工艺技术方案零件材料为铝锻件(2219/T852),零件结构为倒F 型角度框,工艺要求保证内径尺寸为(50360.2)mm,薄壁倾角 5615,壁厚 2mm,整体高度 72mm,槽宽 8mm,深 33mm,槽底存在R2mm 圆角,外圆圆度要求 0.5mm,端面平面度要求 0.5mm。
产品三维结构如图 1 所示,从中可以看出,该产品主要加工难点在于工件装夹、排屑、尺寸测量和减小工件变形等方面,进而保证产品设计要求。
2.1 零件装卡为保证零件在加工过程中均匀受力,防止径向变形,装卡采用轴向下压方式。
根据以往加工经验,当定位点距离大于 350mm 时,倒压板后的工件的圆度都会大于 0.25mm,由此可见,只有让定位点距离小于 350mm ,才能使变形量不大于公差的一半(0.2mm),进而保证壁厚公差要求(0.2mm)及倾斜角度公差要求(15)。
2.2 刀具选择根据零件材料特点,该零件材料具有良好的抗疲劳强度、塑性和韧性,车削时,切屑和刀具表面摩擦力大,容易造成粘刀,且根据零件加工直径大、走刀时间长、材料去除量大的特点,刀具需能够实现较大切深,并具有较好的耐磨性。