薄壁工件加工的因素及方法
薄壁零件的机械加工工艺分析
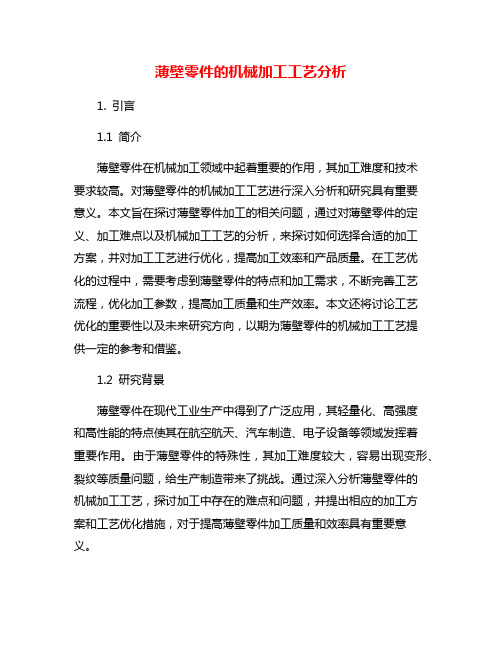
薄壁零件的机械加工工艺分析1. 引言1.1 简介薄壁零件在机械加工领域中起着重要的作用,其加工难度和技术要求较高。
对薄壁零件的机械加工工艺进行深入分析和研究具有重要意义。
本文旨在探讨薄壁零件加工的相关问题,通过对薄壁零件的定义、加工难点以及机械加工工艺的分析,来探讨如何选择合适的加工方案,并对加工工艺进行优化,提高加工效率和产品质量。
在工艺优化的过程中,需要考虑到薄壁零件的特点和加工需求,不断完善工艺流程,优化加工参数,提高加工质量和生产效率。
本文还将讨论工艺优化的重要性以及未来研究方向,以期为薄壁零件的机械加工工艺提供一定的参考和借鉴。
1.2 研究背景薄壁零件在现代工业生产中得到了广泛应用,其轻量化、高强度和高性能的特点使其在航空航天、汽车制造、电子设备等领域发挥着重要作用。
由于薄壁零件的特殊性,其加工难度较大,容易出现变形、裂纹等质量问题,给生产制造带来了挑战。
通过深入分析薄壁零件的机械加工工艺,探讨加工中存在的难点和问题,并提出相应的加工方案和工艺优化措施,对于提高薄壁零件加工质量和效率具有重要意义。
薄壁零件加工的难点主要包括材料轻薄、刚度低、易变形等特点,导致加工过程中容易出现振动、共振、切削变形等问题。
针对这些问题,现有研究主要集中在加工参数优化、刀具选择、切削力控制等方面进行探讨,但仍存在一定的局限性。
有必要对薄壁零件的机械加工工艺进行进一步深入的研究和分析,以期提出更有效的解决方案,实现薄壁零件加工质量的提升和成本的降低。
2. 正文2.1 薄壁零件的定义薄壁零件是指在加工过程中其壁厚相对较薄的零件。
薄壁零件通常用于各种工业领域,包括航空航天、汽车制造、电子设备等。
由于其壁厚较薄,薄壁零件在机械加工过程中常常面临一些特殊的挑战和难点。
薄壁零件的定义可以从几个方面来说明。
薄壁零件的壁厚通常小于其最小尺寸的10%,这就要求在加工过程中需要特别注意避免壁厚过薄导致变形或破裂的问题。
薄壁零件的结构通常比较复杂,需要高精度的加工,以保证零件的质量和性能。
航空薄壁件加工技巧
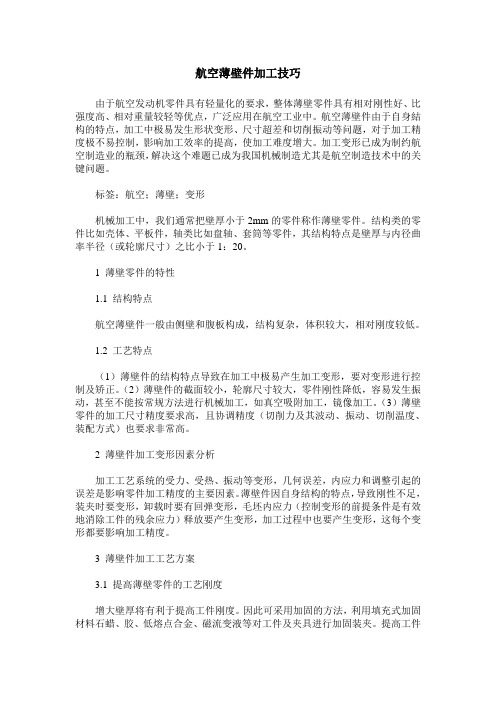
航空薄壁件加工技巧由于航空发动机零件具有轻量化的要求,整体薄壁零件具有相对刚性好、比强度高、相对重量较轻等优点,广泛应用在航空工业中。
航空薄壁件由于自身結构的特点,加工中极易发生形状变形、尺寸超差和切削振动等问题,对于加工精度极不易控制,影响加工效率的提高,使加工难度增大。
加工变形已成为制约航空制造业的瓶颈,解决这个难题已成为我国机械制造尤其是航空制造技术中的关键问题。
标签:航空;薄壁;变形机械加工中,我们通常把壁厚小于2mm的零件称作薄壁零件。
结构类的零件比如壳体、平板件,轴类比如盘轴、套筒等零件,其结构特点是壁厚与内径曲率半径(或轮廓尺寸)之比小于1:20。
1 薄壁零件的特性1.1 结构特点航空薄壁件一般由侧壁和腹板构成,结构复杂,体积较大,相对刚度较低。
1.2 工艺特点(1)薄壁件的结构特点导致在加工中极易产生加工变形,要对变形进行控制及矫正。
(2)薄壁件的截面较小,轮廓尺寸较大,零件刚性降低,容易发生振动,甚至不能按常规方法进行机械加工,如真空吸附加工,镜像加工。
(3)薄壁零件的加工尺寸精度要求高,且协调精度(切削力及其波动、振动、切削温度、装配方式)也要求非常高。
2 薄壁件加工变形因素分析加工工艺系统的受力、受热、振动等变形,几何误差,内应力和调整引起的误差是影响零件加工精度的主要因素。
薄壁件因自身结构的特点,导致刚性不足,装夹时要变形,卸载时要有回弹变形,毛坯内应力(控制变形的前提条件是有效地消除工件的残余应力)释放要产生变形,加工过程中也要产生变形,这每个变形都要影响加工精度。
3 薄壁件加工工艺方案3.1 提高薄壁零件的工艺刚度增大壁厚将有利于提高工件刚度。
因此可采用加固的方法,利用填充式加固材料石蜡、胶、低熔点合金、磁流变液等对工件及夹具进行加固装夹。
提高工件的工艺刚度还可以从下面几个方面着手,一是提高工件与工装接触定位面的加工精度和表面光洁度,二是提高接触刚度(增强接触面硬度或采用高弹性模量材料)。
典型薄壁零件数控铣削加工工艺

典型薄壁零件数控铣削加工工艺随着制造业的发展,数控加工技术逐渐成为最常用的加工方法之一。
而在数控加工领域中,数控铣削技术是常见的加工方法之一。
本文将介绍典型薄壁零件数控铣削加工工艺,包括工艺准备、加工流程、刀具选择和切削参数等方面的内容。
一、工艺准备1.1 材料选择因为薄壁零件通常是轻型结构件,所以材料一般选择铝合金、镁合金、不锈钢等轻质、高强度的材料。
1.2 工件夹紧在加工薄壁零件时,一定要保证工件夹紧牢固。
否则,易造成加工过程中工件的振动或位移,导致加工精度降低。
1.3 加工精度要求由于薄壁零件的厚度较小,所以在加工过程中要保证加工精度高,以防加工出错或造成损失。
二、加工流程2.1 预处理将所选材料进行预处理,包括去表面氧化层、去毛刺等。
2.2 下刀编制好数控加工程序后,进行下刀和切割。
2.3 清洗清洗零件,以便检查和测试。
2.4 检测检测零件的精度、结构、特性等。
如果不合格,要重新加工。
进行表面处理,包括抛光、喷漆、防锈等。
三、刀具选择在加工薄壁零件时,需要选用比较特殊的刀具。
常用的刀具主要包括切割刀具、削铣刀具、倒角刀具、钻头等。
3.1 切割刀具为了保证零件表面的质量和精度,需要选用切割刀具。
切割刀具的作用是将零件中的材料割离,形成所需的几何形状。
在进行倒角时,需要选用倒角刀具。
倒角刀具能够将薄壁零件边缘处的角进行倒角处理,使其具有更好的平滑度和美观度。
3.4 钻头在加工薄壁零件时,常常需要进行孔加工。
钻头是一种常用的刀具,在加工孔时经常被使用。
四、切削参数在加工薄壁零件时,需要注意切削参数的选择。
切削参数对加工质量起着重要的影响。
4.1 切削速度切削速度是指刀具在切割过程中移动的速度。
切削速度过快,容易导致刀具磨损、表面质量差等问题。
切削速度过慢,加工效率低下。
切削深度是指刀具在一次切削过程中切入材料的深度。
切削深度过大,会导致切屑对切削影响的加重,影响加工质量和效率。
总之,在加工薄壁零件时需要注意工艺准备、加工流程、刀具选择和切削参数等方面的内容。
薄壁类零件的车削工艺分析

薄壁类零件的车削工艺分析段立波一.引言薄壁类零件指的是零件壁厚与它的径向、轴向尺寸相比较, 相差悬殊, 一般为几十倍甚至上百倍的金属材料的零件,具有节省材料、结构简单等特点。
薄壁类零件已广泛地应用于各类石油机械部件。
但是薄壁类零件的车削加工是比较棘手的,具体的原因是因为薄壁类零件自身刚性差、强度弱,在车削加工中极容易变形,很难保证零件的加工质量。
如何提高薄壁类零件的加工精度是机械加工行业关心的话题。
二.薄壁类零件车削过程中常出现的问题、原因及解决办法我们在车削加工过程中,经常会碰到一些薄壁零件的加工。
如轴套薄壁件(图1),环类薄壁件(图2),盘类薄壁件(图3)。
本文详细分析了薄壁类零件的加工特点、防止变形的装夹方法、车刀材料、切削参数的选择及车刀几何角度。
进行了大量的实验,为以后更好地加工薄壁类零件,保证加工质量,提供了理论依据。
图1轴套薄壁件图2环类薄壁件图3盘类薄壁件1.薄壁类零件的加工特点1.1因零件壁薄,在使用通用夹具装夹时,在夹压力的作用下极易产生变形,而夹紧力不够零件又容易松动,从而影响零件的尺寸精度和形状精度。
如图4所示,当采用三爪卡盘夹紧零件时,在夹紧力的作用下,零件会微微变成三角形,车削后得到的是一个圆柱体。
但松开卡爪,取下零件后,由于零件弹性,又恢复成弧形三角形。
这时若用千分尺测量时,各个方向直径相同,但零件已变形不是圆柱体了,这种变形现象我们称之为等直径变形。
图4三爪卡盘装夹1.2因零件较薄,加工时的切削发热会引起零件变形,从而使零件尺寸难以控制。
对于膨胀系数较大的金属薄壁零件,如在一次安装中连续完成半精车和精车,由切削热引起零件的热变形,会对其尺寸精度产生极大影响,有时甚至会使零件卡死在芯轴类的夹具上。
1.3薄壁类零件加工内孔中,一般采用单刃镗刀加工,此时,当零件较长时,如果刀具参数及切削用量处理不当,将造成排屑困难,影响加工质量,损伤刀具。
1.4由于切削力和夹紧力的影响,零件会产生变形或振动,尺寸精度和表面粗糙度不易控制。
薄壁件铣削加工工艺
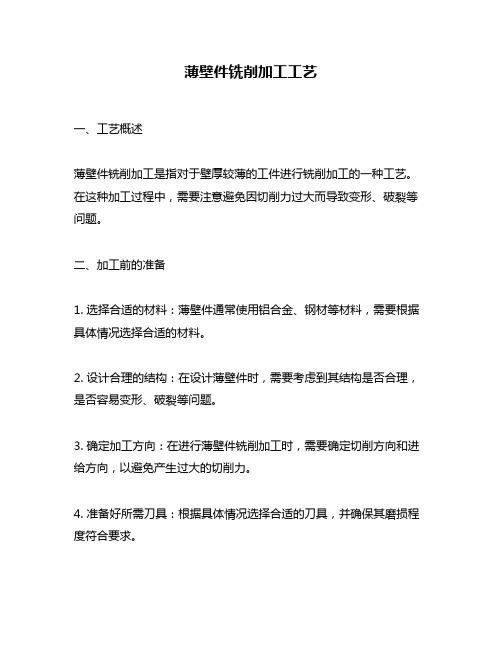
薄壁件铣削加工工艺一、工艺概述薄壁件铣削加工是指对于壁厚较薄的工件进行铣削加工的一种工艺。
在这种加工过程中,需要注意避免因切削力过大而导致变形、破裂等问题。
二、加工前的准备1. 选择合适的材料:薄壁件通常使用铝合金、钢材等材料,需要根据具体情况选择合适的材料。
2. 设计合理的结构:在设计薄壁件时,需要考虑到其结构是否合理,是否容易变形、破裂等问题。
3. 确定加工方向:在进行薄壁件铣削加工时,需要确定切削方向和进给方向,以避免产生过大的切削力。
4. 准备好所需刀具:根据具体情况选择合适的刀具,并确保其磨损程度符合要求。
三、加工过程1. 切割前处理:将薄壁件固定在机床上,并使用夹具固定好位置。
同时检查夹具是否牢固,以避免因夹具不牢导致的误差。
2. 粗铣:根据加工要求选择合适的切削速度和进给速度,并进行粗铣。
在粗铣时,需要注意切削深度和切削宽度的控制,以避免过大的切削力。
3. 半精铣:在粗铣完成后,进行半精铣。
在半精铣时,需要控制好刀具的磨损程度,并根据加工要求选择合适的切削参数。
4. 精铣:最后进行精铣。
在精铣时,需要控制好加工温度和表面质量,并使用合适的冷却液降低温度。
四、加工后处理1. 去毛刺:在加工完成后,需要去除薄壁件表面的毛刺,以保证其表面质量。
2. 洗净清理:将薄壁件洗净并清理干净,在检查其尺寸是否符合要求。
3. 包装运输:将薄壁件包装好,并妥善运输到指定地点。
五、注意事项1. 避免过大的切削力:在进行薄壁件铣削加工时,需要注意避免因切削力过大而导致变形、破裂等问题。
2. 选择合适的刀具:根据加工要求选择合适的刀具,并确保其磨损程度符合要求。
3. 控制好加工温度:在进行薄壁件铣削加工时,需要注意控制好加工温度,以避免因过高的温度导致变形、破裂等问题。
4. 检查夹具是否牢固:在进行薄壁件铣削加工时,需要检查夹具是否牢固,以避免因夹具不牢导致的误差。
数控车床薄壁件加工技巧和方法

数控车床薄壁件加工技巧和方法一、概述薄壁件是指壁厚小于2mm的机械零件,具有重量轻、节省材料、结构紧凑等特点。
数控车床是现代加工制造业中应用广泛的设备,对于薄壁件的加工具有独特优势。
本文将重点介绍数控车床在薄壁件加工中的技巧和方法,以提高加工效率和产品质量。
二、材料选择与装夹方式1.材料选择:薄壁件常用的材料有铝合金、钛合金、不锈钢等,这些材料具有较好的塑性和切削性能。
在选择材料时,应充分考虑其物理性能和加工工艺性。
2.装夹方式:针对薄壁件易变形的特点,应采用合适的装夹方式,如真空吸附、专用夹具等,以保证工件在加工过程中保持稳定。
三、刀具选择与切削参数优化1.刀具选择:针对薄壁件的加工特点,应选用锋利、耐磨的刀具,如硬质合金刀具、涂层刀具等。
同时,刀具的几何参数对切削力、切削热等方面都有影响,应根据工件材料和加工要求进行合理选择。
2.切削参数优化:切削参数的合理选择对于薄壁件的加工至关重要。
应综合考虑切削深度、进给速度、切削速度等参数,以减小切削力、切削热对工件的影响,防止工件变形。
四、加工技巧1.轻切快走:在加工过程中,应采用轻切快走的加工方式,以减小切削力对工件的影响。
同时,合理使用切削液,降低切削温度。
2.分层加工:对于厚度较大的薄壁件,可以采用分层加工的方式,减小各层之间的切削力,避免工件变形。
3.工艺优化:在编制加工程序时,应充分考虑工件的形状、材料特性等因素,合理安排粗加工、半精加工和精加工的顺序,以提高加工效率和产品质量。
4.热处理:在加工过程中,可对工件进行适当的热处理,以提高其硬度和耐磨性。
同时,合理安排热处理工艺参数,防止工件变形或开裂。
5.检测与修正:在加工过程中,应定期检测工件的尺寸和形位公差,如有偏差应及时修正。
同时,对加工过程中出现的问题进行分析和总结,不断优化加工方法和工艺参数。
五、结论通过以上分析可知,数控车床在薄壁件加工中具有独特优势。
在实际生产中,应根据具体情况选择合适的材料、装夹方式、刀具和切削参数。
铝合金薄壁件加工中变形的因素分析与控制方法

铝合金薄壁件加工中变形的因素分析与控制方法一般认为,在壳体件、套筒件、环形件、盘形件、轴类件中,当零件壁厚与内径曲率半径(或轮廓尺寸)相比小于1:20时,称作为薄壁零件。
这一类零件的共同特点是受力形式复杂,刚度低,加工时极易引起误差变形或工件颤振,从而降低工件的加工精度。
薄壁零件因其制造难度极大,而成为国际上公认的复杂制造工艺问题。
一、薄壁件加工变形因素分析薄壁件由于刚度低,去除材料率大,在加工过程中容易产生变形,对装夹工艺要求高,使加工质量难以保证。
薄壁类零件在加工中引起变形的因素有很多,归纳总结有以下几个方面:1、工件材料的影响铝合金作为薄壁件最理想的结构材料,与其他金属材料相比,具有切削加工性好的特点。
但由于铝合金导热系数高、弹性模量小、屈强比大、极易产生回弹现象,大型薄壁件尤为显著。
因此,在相同载荷情况下,铝合金工件产生的变形要比钢铁材料的变形大,同时铝合金材料具有硬度小、塑性大和化学反应性高等性质,在其加工中极易产积屑瘤,从而影响工件的表面质量和尺寸精度。
2、毛坯初始残余应力的影响薄壁件加工中的变形与毛坯内部的初始残余应力有直接的关系,同时由于切削热和切削力的影响,使工件和刀具相接触处的材料产生不能回弹的塑性变形。
这种永久性的变形一旦受到力的作用就会产生残余应力,而在加工过程中,一旦破坏了毛坯的残余应力,工件内部为达到新的平衡状态而使应力重新分布,从而造成了工件的变形。
3、装夹方式的影响在加工中夹具对工件的夹、压而引起的变形直接影响着工件的表面精度,同时如果由于夹紧力的作用点选择不当而产生的附加应力,也将影响工件的加工精度。
其次,由于夹紧力与切削力产生的耦合效应,也将引起工件残余应力的重新分布,造成工件变形。
4、切削力和切削热的影响切削力是影响薄壁件变形的一个重要因素。
切削力会导致工件的回弹变形,产生不平度,当切削力达到工件材料的弹性极限会导致工件的挤压变形。
在切削加工过程中,刀具与工件之间的摩擦所作的功,材料在克服弹性、塑性变形过程中所做的功绝大部分转化为加工中的切削热,从而导致工件的各部分的温度差,使工件产生变形。
薄壁零件的加工工艺和夹具设计

摘要:本文系统设计了薄壁零件的数控车削加工工艺。
通过探讨薄壁零件在加工中存在的易变形、零件尺寸精度、位置精度及表面粗糙度不易保证等技术问题,对加工难点进行分析,给出了加工工艺路线和加工方案,通过优化、完善夹具设计和切削参数,防止了薄壁零件加工变形、保证了较好的尺寸精度和位置精度,从而有效解决薄壁零件的车削加工难题。
由于薄壁零件刚性差、强度弱,在加工中极易变形,是零件的形位公差增大,不易保证零件的加工质量。
因此对薄壁零件的装夹,切削加工过程中刀具的合理选用及切削量的选择,提出了严格要求。
在普通车床上加工形状较复杂、有一定精度要求、且需要多把刀具进行加工的批量零件时,不仅需要频繁换刀和装夹,花费大量的人力和时间,而且加工出来的零件质量取决于加工人员的技术水平, 产品质量得不到充分的保证。
而运用数控车床,结合传统的加工工艺,不但能大大缩短加工时间、提高加工精度,而且成品率高、产品质量稳定。
所以,在运用数控机床加工过程中为保证被加工薄壁件的必要的精度,有同轴度要求的内外圆柱面或有垂直度要求的外圆与端面,尽可能在一次装夹中完成;需要编制其加工路线、合理的选择个阶段的加工参数并编写高质量的数控加工程序。
为完全保证零件的形位公差需要设计其装夹的夹具,为此,对零件图纸、零件加工及时效处理等方面都认真地进行了分析和研究。
图1-1由图1-1可看出,?64mm的外圆对?60mm的内孔的同轴度,?64的外圆的圆度和表面质量以及内孔尺寸精度的加工是该薄壁零件最主要的加工难点。
因为该零件刚性差、强度弱,在加工中极易变形,表面质量、垂直度及同轴度难以保证。
镗削内孔时应一次装夹中加工出来,以保证该零件的尺寸精度。
针对薄壁零件壁薄、刚性差、易变形的特点,可设计该薄壁零件专用夹具装夹,以保证零件的尺寸精度和形位公差达到图纸技术要求。
这些加工难点的存在,使得加工过程中刀具选择、加工工艺路线安排、工艺装夹方式确定等对于该零件是否合格非常关键。
典型薄壁零件数控铣削加工工艺

典型薄壁零件数控铣削加工工艺一、加工工艺概述在现代机械加工中,数控铣削技术已经成为广泛采用的一种加工方式。
它具有高效率、高精度、高稳定性等诸多优点,能够满足各种复杂形状的零部件加工需求。
而在制造业中,薄壁零件的加工一直以来都是一个难点,因为它们具有较大的面积,容易发生振动和变形,导致加工质量不佳。
因此,采用数控铣削加工工艺来生产薄壁零件,显得尤为重要。
1. 材料准备首先需要选定适合薄壁零件加工的材料,一般采用铝合金、镁合金、钛合金等轻合金材料。
然后进行材料的切割、碾磨等预处理工作,以优化后续加工的效果。
2. CAD制图在进行数控铣削加工前,需要对零件进行三维模型设计,以制定详尽的加工工艺方案。
在CAD制图过程中,需要考虑加工精度、表面质量、加工时间等多个因素,确定好各种加工参数,包括加工路径、刀柄发生器等。
3. CAM编程在CAD制图完成后,需要进行CAM编程,将机器指令和实际加工过程相一致。
在CAM编程中,需要考虑加工路径,以及刀柄进给速度、切削进给速度等参数,调整加工节奏和刀具尺寸等。
4. 加工调试CAM编程完成后,需要先进行一次加工调试。
调试过程中,需要不断调整加工参数,以充分发挥数控铣削加工的优势,并保证加工精度和表面光洁度达到标准要求。
5. 实际加工过程综合考虑加工条件、切削速度、进给速率等因素,进行实际的数控铣削加工。
在加工过程中,需要密切关注加工状态,调整加工参数,以保证产品精度和表面质量。
三、关键问题控制1.加工稳定性的控制薄壁零件加工面积较大,容易发生振动和变形,因此需要掌握加工稳定性的控制方法。
首先要选择合适的工件夹持方式,确保工件在加工过程中不产生任何变形。
同时,合理设计加工刀具尺寸和结构,采用具有高刚性的刀具,以提高加工精度和稳定性。
2.表面光洁度的控制薄壁零件加工表面质量要求较高,表面光洁度是一个很关键的指标。
因此,在加工过程中需要选用具有高刚度、高切削能力的刀具,并适当降低装夹紧密度,避免过度压缩,从而保证零件表面光滑克服表面氧化和氧化皮的形成。
车床加工薄壁工件方法

车床加工薄壁工件方法车床加工薄壁工件是一项具有一定难度和挑战性的工程任务,需要在制作过程中充分考虑工件的材料、几何形状以及切削条件等因素,以确保工件的加工质量和精度。
在本文中,我将介绍一种常用的车床加工薄壁工件的方法,并详细说明其中的关键步骤和注意事项。
车床加工薄壁工件的方法主要包括以下几个步骤:材料准备、工件夹紧、切削参数选择、切削策略设计、切削工具选择、车削操作步骤以及加工质量检验。
下面我将逐一介绍这些步骤。
首先是材料准备。
薄壁工件通常使用具有较高的强度和刚度的材料,如铝合金、钛合金等。
在选择材料时,需要根据工件的具体要求和使用环境,选用适当的材料。
另外,要根据工件的几何形状和尺寸,确定所需的原材料形状和尺寸,并对原材料进行切割和修整。
接下来是工件夹紧。
薄壁工件在车床上的加工过程中,需要使用适当的夹具将其稳定地固定在车床上。
夹具应具有足够的刚度和稳定性,以确保工件在切削过程中不会发生变形或脱离夹紧。
可以使用机械夹具、气动夹具等多种夹紧方式,具体选择根据工件的形状和尺寸而定。
然后是切削参数选择。
切削参数包括切削速度、进给量、切削深度等。
对于薄壁工件的加工,切削速度一般选择较低的值,以避免过大的切削力和切削温度造成工件的变形或损坏。
进给量和切削深度应根据工件的材料和几何形状,选择适当的数值,以充分保证切削效率和加工质量。
接下来是切削策略设计。
根据工件的几何形状和加工要求,设计合理的切削策略是确保工件加工质量的关键。
对于薄壁工件,一般采用多次轻微切削的方法,以避免一次性过大的切削力造成工件的变形。
可以通过合理安排切削路径和切削方向,控制切削力的大小和方向,以达到最优的切削效果。
然后是切削工具选择。
薄壁工件的加工通常需要选择具有较高硬度和强度的刀具,以保证切削质量和寿命。
常用的刀具有硬质合金刀具、刚性刀具等。
在选择刀具时,要根据工件的材料和几何形状,选择合适的刀具类型和规格,并进行刀具的合理刃磨和涂层处理,以提高切削效率和刀具寿命。
薄壁类零件加工装夹技术研究
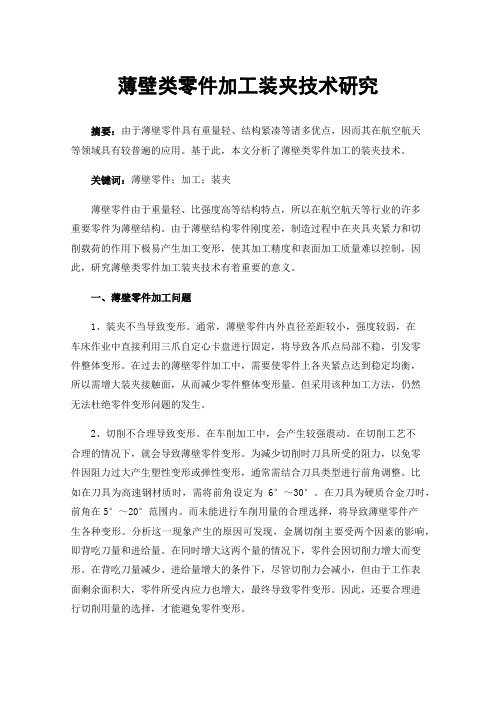
薄壁类零件加工装夹技术研究摘要:由于薄壁零件具有重量轻、结构紧凑等诸多优点,因而其在航空航天等领域具有较普遍的应用。
基于此,本文分析了薄壁类零件加工的装夹技术。
关键词:薄壁零件;加工;装夹薄壁零件由于重量轻、比强度高等结构特点,所以在航空航天等行业的许多重要零件为薄壁结构。
由于薄壁结构零件刚度差,制造过程中在夹具夹紧力和切削载荷的作用下极易产生加工变形,使其加工精度和表面加工质量难以控制,因此,研究薄壁类零件加工装夹技术有着重要的意义。
一、薄壁零件加工问题1、装夹不当导致变形。
通常,薄壁零件内外直径差距较小,强度较弱,在车床作业中直接利用三爪自定心卡盘进行固定,将导致各爪点局部不稳,引发零件整体变形。
在过去的薄壁零件加工中,需要使零件上各夹紧点达到稳定均衡,所以需增大装夹接触面,从而减少零件整体变形量。
但采用该种加工方法,仍然无法杜绝零件变形问题的发生。
2、切削不合理导致变形。
在车削加工中,会产生较强震动。
在切削工艺不合理的情况下,就会导致薄壁零件变形。
为减少切削时刀具所受的阻力,以免零件因阻力过大产生塑性变形或弹性变形,通常需结合刀具类型进行前角调整。
比如在刀具为高速钢材质时,需将前角设定为6°~30°。
在刀具为硬质合金刀时,前角在5°~20°范围内。
而未能进行车削用量的合理选择,将导致薄壁零件产生各种变形。
分析这一现象产生的原因可发现,金属切削主要受两个因素的影响,即背吃刀量和进给量。
在同时增大这两个量的情况下,零件会因切削力增大而变形。
在背吃刀量减少、进给量增大的条件下,尽管切削力会减小,但由于工作表面剩余面积大,零件所受内应力也增大,最终导致零件变形。
因此,还要合理进行切削用量的选择,才能避免零件变形。
3、刀具不合适导致变形。
薄壁零件在车削时,选取合理的刀具至关重要,尤其是对刀具几何角度的选择,不仅会影响切削力的大小,也会影响车削中产生的热变形程度,需关注的是,在薄壁零件的工作表面微观质量的把握也很重要。
典型薄壁零件数控铣削加工工艺
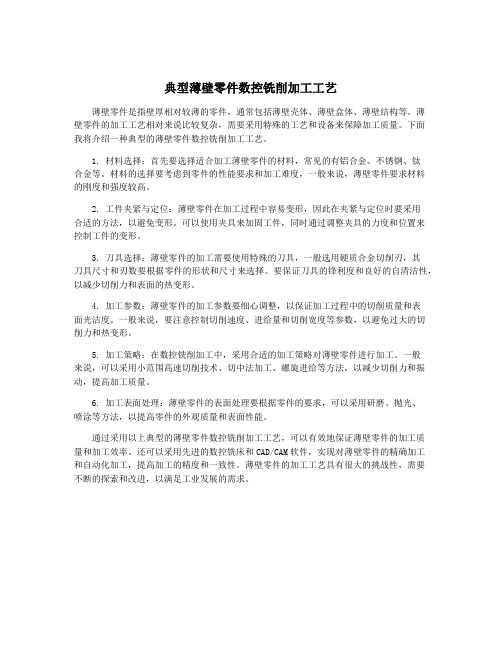
典型薄壁零件数控铣削加工工艺薄壁零件是指壁厚相对较薄的零件,通常包括薄壁壳体、薄壁盒体、薄壁结构等。
薄壁零件的加工工艺相对来说比较复杂,需要采用特殊的工艺和设备来保障加工质量。
下面我将介绍一种典型的薄壁零件数控铣削加工工艺。
1. 材料选择:首先要选择适合加工薄壁零件的材料,常见的有铝合金、不锈钢、钛合金等。
材料的选择要考虑到零件的性能要求和加工难度,一般来说,薄壁零件要求材料的刚度和强度较高。
2. 工件夹紧与定位:薄壁零件在加工过程中容易变形,因此在夹紧与定位时要采用合适的方法,以避免变形。
可以使用夹具来加固工件,同时通过调整夹具的力度和位置来控制工件的变形。
3. 刀具选择:薄壁零件的加工需要使用特殊的刀具,一般选用硬质合金切削刃,其刀具尺寸和刃数要根据零件的形状和尺寸来选择。
要保证刀具的锋利度和良好的自清洁性,以减少切削力和表面的热变形。
4. 加工参数:薄壁零件的加工参数要细心调整,以保证加工过程中的切削质量和表面光洁度。
一般来说,要注意控制切削速度、进给量和切削宽度等参数,以避免过大的切削力和热变形。
5. 加工策略:在数控铣削加工中,采用合适的加工策略对薄壁零件进行加工。
一般来说,可以采用小范围高速切削技术、切中法加工、螺旋进给等方法,以减少切削力和振动,提高加工质量。
6. 加工表面处理:薄壁零件的表面处理要根据零件的要求,可以采用研磨、抛光、喷涂等方法,以提高零件的外观质量和表面性能。
通过采用以上典型的薄壁零件数控铣削加工工艺,可以有效地保证薄壁零件的加工质量和加工效率。
还可以采用先进的数控铣床和CAD/CAM软件,实现对薄壁零件的精确加工和自动化加工,提高加工的精度和一致性。
薄壁零件的加工工艺具有很大的挑战性,需要不断的探索和改进,以满足工业发展的需求。
铝合金薄壁零件的机械加工工艺分析

铝合金薄壁零件的机械加工工艺分析[摘要]铝合金薄壁零件应用领域较为广泛,但其自身性能较为特殊,在加工过程中需要注意工艺与方法。
基于此,本文分析了铝合金薄壁零件性能与特点,并提出提高铝合金薄壁零件机械加工质量的有效对策。
[关键词]铝合金薄壁零件;机械加工;工艺特点与其他零件相比,铝合金薄壁零件结构复杂,并且在尺寸方面要求较高,因此,在加工过程中难度较大。
为了加工出符合工艺标准的机械设备零件,需要不断提高相关加工人员的工作能力与操作水平。
一、铝合金薄壁零件的性能及工艺特点第一,铝合金材料本身具有较强的可塑性与韧性,并且其粘附性较大,容易出现切屑粘连的情况,加工人员在进行切削操作时,切屑容易粘附在刀刃上,对切削刀日后使用会造成影响。
第二,铝合金薄壁零件刚性较弱,在进行加工过程中,需要把握好对铝合金薄壁力的大小,如果加工人员用力过大,极易导致铝合金薄壁零件形状发生变化,从而达不到质量要求。
第三,线膨胀系数大,通常情况下,铝的线膨胀系数要远超于钢的线膨胀系数,因此加工人员在进行切削作业时会使温度上升,造成零件变形。
第四,铝合金材料硬度较差,在进行加工时,加工面容易出现划伤的现象。
因此,在进行铝合金薄壁零件加工时,要达到设备对零件表面粗糙度的要求,加工人员需要熟练掌握加工设备,保证操作水平。
第五,通常情况下,加工人员会应用数控机床对铝合金薄壁零件进行加工操作,但是由于有些零件厚度较薄,在操作时,要注意切削作业会产生切削力,加之薄板本身存在弹性,因此容易出现切削面震动的现象,零件的厚度尺寸是控制不了的,并且表面的粗糙程度也会有所增加。
二、薄壁零件机械加工过程及主要工艺(一)选择合适的切削刀在进行加工时,要选择合适的刀具,充分考虑刀具的形状、切削用量等特点,规划好加工任务,注意加工过程中的镜像切削力,对薄壁零件的变形情况加以重视。
切削刀具的前角要综合刀具的形状及切削变形等特点决定,如果切削前角过大,则在切削过程中摩擦力会变小,可见,在确定刀具前角大小时需要综合各项影响因素。
典型薄壁零件数控铣削加工工艺

典型薄壁零件数控铣削加工工艺
随着数控技术的不断发展和普及,传统的机械加工方式已逐渐被数控加工所取代。
具
有复杂形状的零件加工越来越受到重视,薄壁零件的加工也成为数控铣削加工中的一个重
要领域。
本文将介绍几种常见的典型薄壁零件数控铣削加工工艺。
一、空间曲面薄壁零件的加工
1. 先导铣削法:先导铣削法是指在进行数控铣削之前,通过手工或其他加工方式,
先将工件的主要外形进行加工,以便在数控铣削中能够准确定位和定位,确保加工精度。
这种方法通常适用于工件的结构单一,不涉及过多曲面的薄壁零件。
2. 内壁铣削法:对于空间曲面薄壁零件的加工,往往会涉及到一些内壁的加工。
内
壁铣削法是指利用特殊形状的刀具进行内壁加工,通常采用搅拌刀或球头刀进行加工。
这
种方法相比传统的刀具在内壁加工过程中更容易掌握,提高加工质量和效率。
3. 全固定装夹法:对于薄壁零件的加工来说,固定装夹是一个非常关键的环节,直
接关系到加工精度和质量。
全固定装夹法是指在加工过程中,将工件的切削力用于装夹上,使其实现稳定加工。
这种方法适用于一些形状复杂、精度要求高的薄壁零件。
典型薄壁零件的数控铣削加工工艺有很多种,根据不同的零件形状和要求,选择合适
的加工工艺能够提高加工效率和质量,满足工程的需求。
随着数控技术的不断发展和应用,相信在将来的发展中,还会出现更多的创新加工工艺,以适应各种需要。
薄壁零件车削加工中热变形分析及对策

薄壁零件车削加工中热变形分析及对策薄壁零件在车削加工过程中容易受到热变形的影响,影响产品的加工精度和表面质量。
对薄壁零件车削加工中的热变形进行分析并提出对策是非常必要的。
本文将从热变形的原因、分析方法以及对策措施等方面进行深入探讨,以期为相关行业提供一些有益的参考。
一、热变形的原因1.1 刀具和工件之间的摩擦在车削加工中,刀具和工件之间的摩擦会产生大量的热量,导致工件局部升温。
当工件表面发生热变形时,其形状和尺寸都会发生变化,从而影响产品的加工精度。
1.2 切削温度的影响1.3 切削速度和进给速度对热变形的影响切削速度和进给速度的选择直接影响着切削过程中的热变形情况。
如果选择不当,容易引起工件的热变形,进而影响产品的加工质量。
二、热变形的分析方法2.1 数值模拟分析通过数值模拟分析的方法,可以对车削过程中的热变形情况进行较为准确的预测。
数值模拟分析可以方便地获取刀具和工件间的摩擦热源以及切削温度等信息,从而为热变形的分析和对策提供科学依据。
2.2 实验测量分析三、对策措施3.1 采用合适的刀具材料为了减少车削过程中的热变形,可以选择较高的热导率和热稳定性较好的刀具材料,如硬质合金等,以提高刀具的散热性能,从而减少切削时的热量积累。
3.2 优化切削参数针对薄壁零件的车削加工,可以通过优化切削速度、进给速度和切削深度等参数,以减少切削时的热量积累,从而减少热变形的产生。
3.3 冷却液的应用在车削加工过程中,适当地应用冷却液可以有效地降低工件的表面温度,从而减少热变形的产生。
冷却液还可以有效地冷却刀具,减少刀具的磨损和延长使用寿命。
3.4 加强工件的支撑在薄壁零件的车削加工过程中,应加强对工件的支撑,以减少工件的挠曲和变形,从而降低热变形的影响。
薄壁零件加工方法和工艺分析.pdf

薄壁零件的工艺分析及加工方法单位名称:陕西长岭电子科技有限责任公司作者:安小康2017年3月 2 日薄壁零件的工艺分析及加工方法作者:安小康职业技能鉴定等级:二级单位名称:陕西长岭电子科技有限责任公司单位地址:宝鸡市渭滨区清姜璐75号2017年3月2 日目录摘要 (1)关键词 (1)1工艺方案分析 (2)1.1薄壁零件图 (2)1.2零件图分析 (2)1.3确定加工方法 (2)2工件装夹 (3)2.1定位基准选择 (3)2.2确定零件定位基准 (3)2.3装夹方式选择 (3)2.4确定装夹方式 (3)3刀具和切削用量选择 (3)4零件加工 (5)5加工注意事项 (7)5.1安全文明生产 (7)5.2刀具的选择 (7)5.3削用量的要求 (7)6影响薄壁加工因素及解决方法 (8)6.1受力变形 (8)6.2受热变形 (9)6.3振动变形 (9)总结 (10)参考文献 (11)摘要薄壁工件因为具有重量轻、节约材料、结构紧凑等特点,薄壁零件已日益广泛地应用在各工业部门。
但薄壁零件的加工是比较棘手的,原因是薄壁零件刚性差、强度弱,在加工中极容易变形,不易保证零件的加工质量。
薄壁零件的加工问题,一直是较难解决的。
薄壁件目前一般采用数控车削的方式进行加工,为此要对工件的装夹、刀具几何参数、程序的编制等工艺分析方面进行试验,合理的选择加工方法从而有效地克服了薄壁零件加工过程中出现的变形,保证加工精度。
关键词:薄壁工件工艺分析程序编制加工方法1工艺方案分析1.1薄壁零件图1.2零件图分析该零件图是薄壁套类零件由外圆、内孔、外螺纹组成。
尺寸标注完整,表面粗糙度为1.6,选用毛坯是45号钢。
毛坯尺寸Φ35mm×50mm,表面无热处理等要求。
1.3确定加工方法确定加工方法的原则是保证加工表面加工精度和表面粗糙度。
薄壁类零件应按粗、精加工工序。
薄壁件通常需要加工工件的内、外表面。
内表面的粗加工和精加工都会导致工件变形,所以应按粗精加工分序。
薄壁零件的数控车削加工探讨

薄壁零件的数控车削加工探讨一、薄壁零件在数控车削加工中的问题1. 变形问题:薄壁零件在数控车削加工中容易受到刀具切削力的影响,从而产生变形。
尤其是在加工过程中,由于热变形效应的存在,薄壁零件更容易出现变形现象。
变形不仅会影响零件的尺寸精度和几何形状,还会降低零件的使用寿命和性能。
2. 振动问题:由于薄壁零件的结构特点,容易受到切削力的作用而产生振动现象。
振动不仅会影响加工质量,还会加剧刀具磨损、降低加工精度、影响加工表面质量等问题。
3. 切屑问题:薄壁零件在数控车削加工中,由于切削力的作用,容易产生大量的切屑,而这些切屑往往会对加工表面造成损坏,同时也会对工件和刀具造成损伤。
以上问题对薄壁零件的加工质量和加工效率都会产生较大的影响。
如何解决这些问题,提高薄壁零件的加工质量和效率,是当前数控车削加工中的一个重要课题。
二、解决问题的方法和技术1. 刀具选择和切削参数的优化:在数控车削加工中,合理选择刀具和优化切削参数对薄壁零件的加工具有重要意义。
选择合适的刀具材料和刀具几何形状对降低切削力、延长刀具使用寿命非常重要。
通过优化切削速度、进给量、切削深度等切削参数,可以有效地减少切削力、降低振动,从而保证薄壁零件的加工质量。
2. 支撑技术:薄壁零件在数控车削加工中,可以采用支撑技术来减少变形和振动。
支撑技术可以通过在零件上设置支撑点、改变切削路线等方式,有效地提高零件的刚度和稳定性,减少变形和振动。
可以在薄壁零件的内部设置支撑件,以增加结构的刚性,减少振动和变形。
3. 刀轴倾角补偿技术:在数控车削加工中,刀轴倾角对薄壁零件的加工具有重要影响。
合理地设置刀轴倾角可以有效地减少切削力和振动,避免因为切削力对零件产生的变形。
通过刀轴倾角补偿技术,可以实现对零件的精密加工,提高加工质量。
4. 加工路径优化技术:在数控车削加工中,通过优化加工路径,可以减少切屑对加工表面的损害,同时也可以减少切削力和振动。
在薄壁零件的加工中,通过合理设置加工路径和切削方向,可以减少切屑的产生,提高加工表面的光洁度和平整度。
铝薄壁工件的加工方法有

铝薄壁工件的加工方法有铝薄壁工件的加工方法有很多种,包括冲压、剪切、弯曲、焊接、钻孔等。
下面将详细介绍几种常见的加工方法。
冲压是一种常见的铝薄壁工件加工方法。
冲压是通过模具对铝板进行压制,使其在一次或多次冲击下获得所需形状的方法。
冲压技术广泛应用于汽车、电子、航空航天等领域。
冲压的优点是加工速度快、批量生产能力强,同时还可以实现复杂的外形和精度要求。
但是冲压的缺点是成本较高,需要专业的设备和技术。
剪切是将铝板切割成所需形状的加工方法。
剪切主要依靠剪切机械设备,通过将刀具对铝板进行快速切割来达到加工目的。
剪切可以实现简单的形状,如直线边缘,但是对于复杂的内外轮廓剪切会比较困难。
剪切的加工精度较低,一般用于对加工精度要求不高的工件。
弯曲是将铝板弯曲成所需形状的加工方法。
弯曲通常需要通过弯曲机进行,通过对铝板的不同部分施加压力,使其产生弯曲现象。
弯曲可以实现各种不同角度和半径的曲线,适用于形状复杂的工件。
弯曲的加工精度较高,但是对设备和操作者的要求也较高。
焊接是将不同铝板部分连接在一起的方法。
焊接可以通过多种方式进行,包括氩弧焊、激光焊、电阻焊等。
焊接可以实现不同形状的工件的连接,同时也可以用于修复和加固。
焊接对设备和操作者的要求较高,同时还需要注意热变形等问题。
钻孔是在铝板上通过钻头制作孔洞的方法。
钻孔可以实现不同大小和深度的孔洞,以适应不同的需求。
钻孔的加工速度较快,但是需要注意保持稳定和一致的加工质量。
总结起来,铝薄壁工件的加工方法有冲压、剪切、弯曲、焊接和钻孔等。
不同的加工方法可以根据具体的需求和工件形状选择。
对于需要高精度和复杂形状的工件,冲压和弯曲是较常用的加工方法。
而对于简单形状和低精度要求的工件,剪切和钻孔是较为适合的选择。
而焊接则适用于工件的连接和修复。
薄壁套类零件数控车削加工工艺分析

薄壁套类零件数控车削加工工艺分析摘要:随着加工制造业的发展,薄壁类零件的应用范围越来越广泛,技术要求越来越高。
但是在薄壁套类零件的数控车削加工中还存在很多问题,影响到了加工的效率以及零件的质量,因此需要不断改进数控车削加工工艺,提高加工质量。
关键词:薄壁套类零件数控;车削加工工艺;前言:在实际生产过程中,经常会遇到加工各种不同类型的薄壁零件,因为它具有结构小、质量轻、材料省、结构紧凑等优点,所以应用在各行各业,特别是在航空航天业应用更加广泛。
薄壁件加工时由于振动、夹紧力、切削热、内应力、车削力对变形的影响,使工件产生大幅度的形状变形,导致零件尺寸精度、形状精度和位置精度超差。
一、薄壁套类零件概述薄壁套类零件有着径向刚度差、外圆及内孔有着不规则变形导致壁厚不均匀、圆度不易控制等特点。
套类零件在机械结构中主要起支撑和导向作用,为此零件需具有较高的同轴度,端面与孔轴线或与外圆有较高的垂直度要求,除了尺寸的精度要求外还对零件的几何形状精度、表面粗糙度也要求较高。
在数控车削加工中急需解决的问题是控制零件装夹变形以及车削变形。
二、薄壁套类零件加工质量的影响因素①夹紧力对加工质量的影响:零件加工对装夹刚度有较高的要求,如果零件装夹的力度过小不仅会造成脱夹导致零件的报废,甚至会引发安全事故。
②工件材料的状态对切削力的影响:材料的状态会直接影响到切削力大小,随着材料硬度、强度增高切削力增大,同时还会涉及到加工硬化等问题,加工硬化不仅会使材料产生变形还会给材料的进一步加工带来困难。
③刀具角度对工件的影响:前角大时,切削变形量和摩擦力减小,切削力减小,表面粗糙度好;前角过大,刀具楔角减小,刀具强度降低,散热能力差,磨损速度快,刀具使用寿命降低;后角大,与工件切削表面间隙大,摩擦力小,切削力也相应的减小;后角过大,会形成刀具刃部变薄,强度不足,磨损速度快,刀具使用寿命降低。
④吃刀量与进给速度对切削力的影响:背吃刀量与切削速度对切削力的交互影响当背吃刀量为常数时,切削速度增大时,切削力变化的幅度不是很大;而当切削速度为常数时,背吃刀量增大,切削力增大较明显[3]。
- 1、下载文档前请自行甄别文档内容的完整性,平台不提供额外的编辑、内容补充、找答案等附加服务。
- 2、"仅部分预览"的文档,不可在线预览部分如存在完整性等问题,可反馈申请退款(可完整预览的文档不适用该条件!)。
- 3、如文档侵犯您的权益,请联系客服反馈,我们会尽快为您处理(人工客服工作时间:9:00-18:30)。
摘要:薄壁零件已广泛地应用在各种机械设备中,因为它结构紧凑,质量轻,主要是用来支撑轴上的零件及起导向作用的,此种零件刚性低、强度弱、产生振动大量的切削热,加工中易产生变形,从而影响工件的尺寸精度和形状精度。
针对以上问题,文章提出从薄壁件加工工序安排、刀具的几何参数、切削用量的选用及装夹工艺方面进行优化。
关键词:薄壁件工件精度加工优化
一、影响薄壁件加工因素
1.工件薄壁,在夹紧力的作用下易变形,从而影响工件的尺寸精度和形状度。
2.在加工中产生切削热引起薄壁件热变形,影响尺寸精度。
3.在切削背向力的作用下,易产生振动和变形,影响工件尺寸精度、表面粗糙度及形位精度。
二、减少薄壁工件变形的方法
1.采用粗精车分序加工:在粗车时考虑到切削余量较大和提高加工效率,相应的夹紧力稍大些。
精车前适当释放卡爪,消除粗车时因切削力过的引起的变形,精车时夹紧力可稍小些,加工完成。
2.刀具的几何参数:刀具参数的合理选择是反映切削过程中多因素综合效果的重要标志。
切削角度、刃口的形状在切削中都是相互影响的,侧重于保持刀刃的锋利和切削过程的稳定,从而减小切削力,应选较大的前角,较小的刀尖角。
从减小振动方面应采用较小的刀具后角增大刀具后面与工件的接触面积,达到消振的目的。
3.精车薄壁工件时,要求刀柄的刚度高,车刀的修光刃不宜过长(一般取0.15mm―0.3mm),刃口要锋利。
4.切削用量的选择:切削力与背吃刀量、切削速度、进给量密切相关,当背吃刀量和进给量同时加大,切削力就大,工件变形也大;减少背吃刀量、增大进给量(0.6-0.8mm/r),切削力虽然有所下降,但工件的表面残余面积大,粗糙度增加,同时导致零件变形。
一般粗加工时背吃刀量和进给量可以大些,精加工时背吃刀量在0.3―0.5mm左右,进给量应在0.15mm/min左右,精车时选用高的切削速度,三者要选用合适,可以提高加工精度。
5.装夹工艺的选择:使用开缝套筒或特制的软爪,增大装夹时的接触面积,使夹紧力均布在薄壁工件上,从而减少夹紧产生的变形。
在切削时浇注充分的切削液,是防止和减少薄壁工件变形的有效方法。
使用吸振材料,用软橡胶管、棉纱、泡沫等填充或包裹薄壁工件,能起到减少振动和消除噪声的作用,也可填充低熔点物质的方法车削薄壁套,减少工件的变形。
另外,车床的间隙调整到合适的程度也是提高机床刚性的重要手段。
[加工实例]
图1所示为我校企合作单位一薄壁工件,采用设备是沈阳数控机床配备广州数控系统gsk980ta的数控机床。
为能提高零件合格率,我们改进了工装,优化了刀具的几何参数和切削用量,保证了工件质量。
件1为内孔尺寸加工完成外圆待加工的工件,左端为卡盘夹持的部位,直径100mm,长度50mm,件2为开口的锥度涨胎,锥度比为1:30,件3为芯轴,相同的锥度,利用螺纹的锁紧使件2锥度开口处与工件充分接触,使工件在夹具能够良好的定位和传递切削力,既防止了振动,又有利于切削加工,在件2和件3配合面处涂抹润滑油有利于拆卸。
[刀具和切削参数]
外圆粗精车均用主偏角93度,刀尖角55度的机夹车刀,刚性强,减少振动,红硬性好,耐磨损,无需刃磨刀具。
外圆粗车主轴转速为800-900r/min-左右,进给速度f100-f120,预留精车余量0.3mm
左右。
精车时主轴转速在1000-1100r/min,进给速度f40左右。
切削时充分浇注冷却液,能带走大量切削热,防止工件变形保证加工精度。
以上几种加工方法在生产实践中经常接触到,在上述论述中难免有纰漏之处,敬请原谅并指正。