ISO9001:2015仪器设备校准程序英文版
ISO 9001-2015 中英文对照

ISO 9001:20151 ScopeThis International Standard specifies requirements for a quality management system when an organization:a)needs to demonstrate its ability toconsistently provide product or servicethat meets customer and applicablestatutory and regulatory requirements,andb)aims to enhance customer satisfactionthrough the effective application of thesystem, including processes forimprovement of the system and theassurance of conformity to customer and applicable statutory and regulatoryrequirements.All requirements of this International Standard are generic and are intended to be applicable to all organizations, regardless of type, size and product and service provided.NOTE 1 In this International Standard, the terms “product” or “service” only apply to products and services intended for, or required by, a customer.NOTE 2 Statutory and regulatory requirements can be expressed as legal requirements. 1範圍本國際標準所訂的品質管理系統要求,當一個組織:a)必須展現其提供一致地符合顧客要求和符合適用法令和法規要求之產品或服務的能力。
ISO9001:2015全套文件英文版(含质量手册及全套程序文件)

Ningbo XXX Material TechnologyCo.,LtdISO9001:2015 Quality ManualRevision [A/0] - [2018/3/1](c) [Copyright Year Of 2018] [Ningbo XXX Material Technology Co.,Ltd]; all rights reserved. This document may contain proprietary information and may only be released to third parties with approval of management. Document is uncontrolled unless otherwise marked; uncontrolled documents are not subject to update notification.Revision [A/0] - [2018/3/1]Page 1 of 19TABLE OF CONTENTS0.0 Revision History and Approval ...................................................................................................................... 3 1.0 Welcome to Ningbo XXX Material Technology Co.,Ltd ................................................................................ 4 2.0 XXX Material: Who We Are ........................................................................................................................... 4 2.1 Determining Our Strategic Direction ......................................................................................................... 4 2.2 Scope of the Management System ........................................................................................................... 4 2.2.1 Scope Statement ............................................................................................................................... 4 2.2.2 Facilities Within the Scope ................................................................................................................ 4 2.2.3 Permissible Exclusions ..................................................................................................................... 5 2.2.4 Scope of the ISO9001:2015 Quality Manual ..................................................................................... 5 3.0 Quality Policy................................................................................................................................................. 5 4.0 Management System Structure and Controls ............................................................................................... 5 4.1 Process Approach .................................................................................................................................... 5 4.1.1 Process Identification ........................................................................................................................ 5 4.1.2 Process Controls & Objectives .......................................................................................................... 6 4.1.3 Outsourced Processes ...................................................................................................................... 7 4.2 Documentation & Records ....................................................................................................................... 7 4.2.1 General .............................................................................................................................................. 7 4.2.2 Control of Documents ....................................................................................................................... 7 4.2.3 Control of Records ............................................................................................................................ 7 4.3 Change Management ................................................................................................................................ 8 4.4 Risks and Opportunities ............................................................................................................................ 8 5.0 Management & Leadership ........................................................................................................................... 8 5.1 Management Leadership and Commitment .............................................................................................. 8 5.2 Customer Focus ........................................................................................................................................ 9 5.3 Quality Policy ............................................................................................................................................. 9 5.4 Organizational Roles Responsibilities & Authorities ................................................................................. 9 5.5 Internal Communication ............................................................................................................................ 9 5.6 Management Review .............................................................................................................................. 10 6.0 Resources ................................................................................................................................................... 10 6.1 Provision of Resources ........................................................................................................................... 10 6.2 Human Resources .................................................................................................................................. 10 6.3 Infrastructure ........................................................................................................................................... 11 6.4 Work Environment ................................................................................................................................... 11 6.5 Organizational Knowledge ...................................................................................................................... 11 7.0 Operation ..................................................................................................................................................... 11 7.1 Operational Planning and Control ........................................................................................................... 12 7.2 Customer-Related Activities .................................................................................................................... 12 7.2.1 Capture of Customer Requirements ............................................................................................... 12 7.2.2 Review of Customer Requirements ................................................................................................ 12 7.2.3 Customer Communication ............................................................................................................... 12 7.3 Design and Development ........................................................................................................................ 13 7.4 Purchasing .............................................................................................................................................. 13 7.5 Provision of [Production of adhesive tape] .............................................................................................. 13 7.5.1 Control of Provision of [Production of adhesive tape] ..................................................................... 13 7.5.2 Identification and Traceability .......................................................................................................... 14 7.5.3 Property Belonging to Third Parties ................................................................................................ 14 7.5.4 Preservation .................................................................................................................................... 14 7.5.5 Post-Delivery Activities .................................................................................................................... 14 7.5.6 Process Change Control ................................................................................................................. 15 7.5.7 Measurement and Release of [Production of adhesive tape] ......................................................... 15 7.5.8 Control of Nonconforming Outputs .. (15)Revision [A/0] - [2018/3/1]Page 2 of 198.0 Improvement ............................................................................................................................................... 15 8.1 General .................................................................................................................................................... 15 8.2 Customer Satisfaction ............................................................................................................................. 15 8.3 Internal Audit ........................................................................................................................................... 16 8.4 Corrective and Preventive Action ............................................................................................................ 16 Appendix A: Overall Process Sequence & Interaction ........................................................................................ 17 Appendix B: ISO 9001:2015 Cross Reference . (18)Revision [A/0] - [2018/3/1] 0.0 Revision History and ApprovalRev. Nature of changes Approval DateA/0 Original release. XXX 2018/3/1Page 3 of 19Revision [A/0] - [2018/3/1] 1.0 Welcome to Ningbo XXX Material Technology Co.,LtdNingbo XXX Material Technology Co., Ltd. Was established in 2000, with the UAE businessmen to build the joint venture company; 2004 Ming Shan founded Nissin special adhesive tape and adhesive tape company; 2008 due to the strategic adjustment of 3 company merger and reorganization, the establishment of Ningbo letter mountains adhesive products Manufacturing Co., Ltd..PVC insulation tape is one of China’s national standard drafting unit, the field of adhesive products governing unit of China, Ningbo, adhesives and related products Industry Association, honorary president of the unit.We produce more than 1000 varieties of products of 11 categories. The annual throughput more than 100,000,000 square of the adhesive and 10,000 ton of the adhesive.Our company located in Ningbo which the city of the east China sea, beside 500 kilometers of shanghai, 20 kilometers from Ningbo list airport and 50 kilograms of the Ningbo seaport. The transport is very convenient (Easy to ship to everywhere on the world).2.0 XXX Material: Who We Are2.1 Determining Our Strategic DirectionXXX Material has reviewed and analyzed key aspects of itself and its stakeholders to determine the strategic direction of the company. This involves:∙Understanding our core products and services, and scope of management system (see 2.2 below).∙Identifying “interested parties” (stakeholders) who receive our [Production of adhesive tape], or who may be impacted by them, or those parties who may otherwise have a significant interest in our company. These parties are identified in the document [Requirements and expectations list of interested parties].∙Understanding internal and external issues that are of concern to XXX Material and its interested parties; also identified in the document [Requirements and expectations list of interested parties]. Many such issues are identified through an analysis of risks facing either XXX Material or the interested parties. Such issues are monitored and updated as appropriate, and discussed as part of management reviews.This information is then used by senior management to determine the company’s strategic direction. This is defined in records of management review, and periodically updated as conditions and situations change.2.2 Scope of the Management System2.2.1 Scope StatementBased on an analysis of the above issues of concern, interests of stakeholders, and in consideration of its products and services, XXX Material has determined the scope of the management system as follows:Production of adhesive tapePage 4 of 19Revision [A/0] - [2018/3/1]Page 5 of 192.2.2 Facilities Within the ScopeThe quality system applies to all processes, activities and employees within the company. The facility is located at: Factory Add :XXX Tel :XXX Fax :XXX XXX XXX2.2.3 Permissible ExclusionsThe following clauses of ISO 9001 were determined to be not applicable to XXX Material.∙ 8.3 Design and development of products and services 2.2.4Scope of the ISO9001:2015 Quality ManualThis manual is prepared for the purpose of defining the company’s interpretations of the ISO 9001:2015 international standard, as well as to demonstrate how the company complies with that standard.This manual does not follow the numbering structure of ISO 9001. Instead, Appendix B presents a cross reference between the sections of this manual and the clauses of ISO 9001:2015.This manual presents “Notes” which are used to define how XXX Material has tailored its management system to suit its purposes. These are intended to clarify implementation approaches and interpretations for concepts which are not otherwise clearly defined in ISO 9001:2015. Notes appear in italics, with gray background.Where subordinate or supporting documentation is reference in this manual, these are indicated by bold italics .∙ Quality PolicyThe Quality Policy of XXX Material is as follows:Quality first, customer satisfaction;Scientific management, continuous improvement. ∙ Management SystemStructure and Controls 4.1Process Approach4.1.1 Process IdentificationXXX Material has adopted a process approach for its management system. By identifying thetop-level processes within the company, and then managing each of these discretely, this reduces the potential for nonconforming [Production of adhesive tape] discovered during final processes or after delivery. Instead, nonconformities and risks are identified in real time, by actions taken within each of the top-level processes.Note: not all activities are considered “processes” – the term “process” in this context indicates the activity has been elevated to a higher level of control and management oversight.The controls indicated herein are applicable only to the top-level processes identified.。
ISO9001:2015全套程序文件英文版

ISO9001:2015全套程序文件英文版(本人辛苦原创)Code QM-COP-01Date2018.10.24Date2018.10.241.0 PurposeAll the documents required by the Company’s quality management system should be controlled to ensure the version applied by all the relevant departments is valid.2.0 ScopeIt is applicable to all the documents pertaining to the quality management system including external documents.3.0 Definition3.1 Controlled document: The document applied in and out of the Company is controlled in modifications, identities, versions, version numbers, formats, fonts, etc.3.2 DCC: Document Controlling Center3.3 External document: It refers to the document that has been handled by outside individuals like national/international standards, laws and regulations, documents provided by customers or suppliers, material certificates, amendment advice, etc.3.3.1 Administrative documents on quality management system or product, released from local government authorities and regulatory agencies such as the notices from Guangdong Food and Drug Administration.3.3.2 National laws and regulations such as Product Quality Law of the People’s Republic of China, Regulation on the Supervision and Administration of Medical Devices, 93/42/EEC, etc.3.3.3 International standards such as Medical devices—Quality management systems—Requirements for regulatory purposes.3.3.4 National standards such as Medical electrical equipment – Part 1: General requirements for safety.3.3.5 Regulations and standards provided by customers such as agreements and commitments signed with customers.3.3.6 Drawings provided by customers such as drawings, mold drawings provided by a certain customer.3.3.7 Other important external documents relating to the product, including official materials like customer’s notice.4.0 Duties4.1 General Manager: Responsible for approval of the Company’s quality manual.4.2 Management Representative: Responsible for the Company’s procedure files, quality plans and cross-department three-order files and approval of external documents.4.3 Principals of each department: Responsible for approval of three-order files and all kinds of tables as well as department-related external documents.4.4 Department: Responsible for compilation, number and review of the documents dominated by the department.Code QM-COP-01Date2018.10.24Date2018.10.244.5 Quality Management Department: Responsible for all the controlled documents of the Company to ensure the electronic document is the latest version, and responsible for the updating of the controlled document list of all the departments.5.0 Procedures5.1 Document classification: The management system documents includes four layers and external documents5.1.1The Quality Manual (including policies and goals) is a principle-based and master document guiding the implementation of the quality management system. As the first level document, it does not just explain the scope of application but also describe the interaction among all the procedures in the quality management system.5.1.2 The procedure document is the expansion and specification of the Quality Manual, providing the process, methods and controlling means for carrying out quality management. It belongs to the second level document.5.1.3 Supporting documents (operation/technical specifications, process/inspection standards, technical guidance and position description) specify the quality management goals, duties of the posts of all levels and specific operation methods. It belongs to the third level document.5.1.4 The table is applied to record the state and result of activities, belonging to the fourth level document.5.1.5 External document: It refers to the document directly obtained from outside and cited by the Company, including national/international standards, laws and regulations, documents provided by customers or suppliers, material certificates and amendment advice.5.1.6 The document is drawn up mainly in written or electronic form, and both shall be under control.5.2 Document compilation and approval5.2.1 The formats of the second and third level documents are the same as that of the document.5.2.2 The date of the document must be written in the form of “year month day”.5.2.3 Limits for examination and approving authority for documentsS/N Order Type ofdocumentPrepared byReviewedbyJointreviewed byApprovedbyRemark1 First ManagementManualQualityManagementDepartmentManagementRepresentativeSupervisorof eachdepartmentTopmanagement2 SecondProceduredocumentAlldepartmentDepartmentRelevantdepartmentManagementCodeQM-COP-01Date2018.10.24 Date2018.10.245.3 Document’s number and version/version number5.3.1 Number: The document compiler numbers the newly compiled documents according to the Basic Rules for Numbering the Controlled Documents and the document list of the department, and confirms the uniqueness of the numbers with the controlling center.5.3.2 Version/Version number: The version or version number of the controlled document is compiled insmanagermanagerRepresen tative3ThirdManagement documentAll department sDepartme nt managerRelevant department manager and Managemen tRepresentat iveManage ment Represen tativeJob Description of the personnel below the manager level is reviewed by the department manager and approved by the manager of HR Department.4ThirdProcess, inspection standarddocument and specification (including external document)All department sQuality Manageme nt Departme ntDepartm ent manager5Fourt hTablesAlldepartment sQualityManageme nt Departme ntDepartm entmanagerAdditional remarks: 1) The document can be compiled by the compilers or above the compiler level but must be approved by the personnel upper than the compiler.2) The relevant department refers to the departments having ties with others involved in this system. 3) When the approver of the above documents is absent, his agent or Management Representative can sign it up instead to make the document effective.Code QM-COP-01Date2018.10.24Date2018.10.24the form of 26 alphabets from A to Z. The initial version number is “A/0”, the next revised version is “A/1” and so on. Changing Arabic numbers is enough for minor revisions while changing alphabets, for instance, from “A” to “B”, is necessary in case of major revisions.5.4 Document distribution and storage5.4.1 The document compiler sends the copy of the approved document and its electronic version to the Quality Management Department where the document will be checked whether it has been approved by designated personnel. After that, the document will be registered, controlled with the controlled document list updated.5.4.2 The document controller determines the scope of distribution, makes copies of the electronic file ina required number according to the List of distributed controlled documents, add the watermarks of correspondent departments on these copies, save them to the folder for controlled documents of each department and notify the departments for making and using the documents by email.5.4.3 All the department are responsible for checking if the controlled document is correct or not.5.4.4 The authority for the controlled document folder of each department shall be set as follows:①Document controller is permitted to modify, delete the content or add new content to the document.②Each department can only read but cannot delete, modify or add the content of controlled documents.5.4.5 The document controller must copy the electronic document as a backup.5.4.6 Visual management of documentsAs for the documents which are frequently applied at production site, all the departments should take correspondent measures such as hanging them on the wall, beside the equipment or enveloping them with plastic so to make it easy for operators to use.5.5 Document reading5.5.1 In case of reading the documents, the relevant personnel can open the PDF file which are saved in the Company’s share disk.5.6 Document review, modification, recovery, invalidation and destruction5.6.1 Review①The documents of the quality management system should be reviewed once a year by the Quality Management Department and internal review team organized by the Management Representative along with the Company’s internal review and reviewed with the result put down in the internal review record.②In case of special circumstances, some documents should be reviewed by the relevant department.③The review must take into account the influence of both the internal factors like the Company’s organization and position changes and the external factors like laws, regulations, relevant standards and market demands upon the sufficiency and applicability of the documents with the Review Record filled in.5.6.2 Revision/alteration①The director and executor of each unit should check the effect after implementing the documents. If the documents are not applicable or in doubt in addition to the opinions on the content of the documents from other units, the documents can be revised or modified by the department which revised or compiledCode QM-COP-01Date2018.10.24Date2018.10.24them last time after the discussion among the relevant departments. Relevant approval process is the same as that in 5.2.2.②All the modifications or alterations must be underlined (“___”). In case of version change, the previous underline should be substituted by the latest one.③The revision record should be written on the first page of the documents, containing the content of the revision, identification of the affected documents, signature of the approver, date of approval and effective time.④The relevant departments shall be notified of review and confirmation of the alteration, and personnel training will be provided if necessary.⑤In the following circumstances that there is any alteration to the documents of the quality management system or the documents relating to the Company’s medical device products, the top management or Management Representative of the Company should be notified of deciding whether to inform the competent authority or notified bodies about it. If it is necessary, the notification should be implemented in accordance with the local laws and administrative regulations.a. Major alterations to the Quality Manual.b. Major alterations to the product’s functions, performance, safety, reliability and electromagnetic compatibility, caused by altering product standards.c. Major alterations to the product’s functions, performance, safety, reliability and electromagnetic compatibility, caused by changing key components of products.d. Stipulated by laws and regulations.5.6.3 Once the new version of controlled document is distributed, the old one becomes invalid automatically. The document controller should delete the copies of invalid controlled documents in the controlled document folder, upload the latest version and keep the original documents printed with an “invalid” stamp at the document controlling center till the expiry date (at least five years) before destruction.5.6.4 As for the invalid original documents, the document controlling center should destruct them uniformly after Document/Record Destruction Registration Form filled in by the center is approved by the Management Representative.5.7 The non-controlled document is identified as the “Reference”. If a Company’s customer or other personnel need it for their jobs, they must have the copies of the Company’s controlled documents and get its copies approved by the Management Representative and stamped with the ‘Reference’ seal by the Quality Management Department. The ‘Reference’ documents will not be withdrawn or changed to the latest version.5.8 Temporary documentIt is not yet official for some reasons but needed by each department. Such document should have a ‘Temporarily Controlled’ stamp as well as the time limit and distribution department on them. The temporary document cannot be valid for more than 3 months.Code QM-COP-01Date2018.10.24Date2018.10.245.9 Management of external documents5.9.1 Each department of the Company can collect external documents through the following channels.a. National, provincial, municipal governments and their relevant functional departments.b. All kinds of meetings, professional newspapers, magazines, publishers and suppliers.c. Internet, telephone and fax.5.9.2 The external document collected by each department should be selected timely and delivered to the relevant department to recognize its contents and decide whether make it a controlled document.a. The collected technical standards on our products should be delivered to the Technical Department to recognize its year, version and applicable articles.b. The laws, regulations and rules that are issued by the state on the quality and safety of the product should be delivered to the Quality Management Department to identify the required department and scope.c. Policy documents issued by the superior should be delivered to the administration department for recognition.d. The technical documents provided by suppliers or customers should be delivered to the Technical Department and Quality Management Department for recognition.f. The design input documents provided by customers should be delivered by the Market Department to the R&D Department for recognition. Saved in DHF format, they don’t have to be controlled by document controller.5.9.3 Numbering of external documentsAs for the external documents on technology and standards as well as other external documents, the Quality Management Department should number them in accordance with the Basic rules on numbering controlled documents.5.9.4 Distribution of external documentsa. After being recognized, the external documents should be kept on a file and put down on a list.b. The external documents should be distributed after the distribution scope is confirmed according to 5.4 of this procedure.5.9.5 Updating of external documentsAs for the external documents which need updating, the new version should be distributed with the invalid ones withdrawn immediately.5.9.6 Preservation and destruction of external documentsThe preservation and destruction should be implemented according to 5.6.3 of this procedure.5.10 The Quality Management Department should supervise and inspect irregularly the controlling process implemented by each department.6.0 Records and Tables6.1 Controlled Document Directory。
ISO90012015记录控制程序英文版
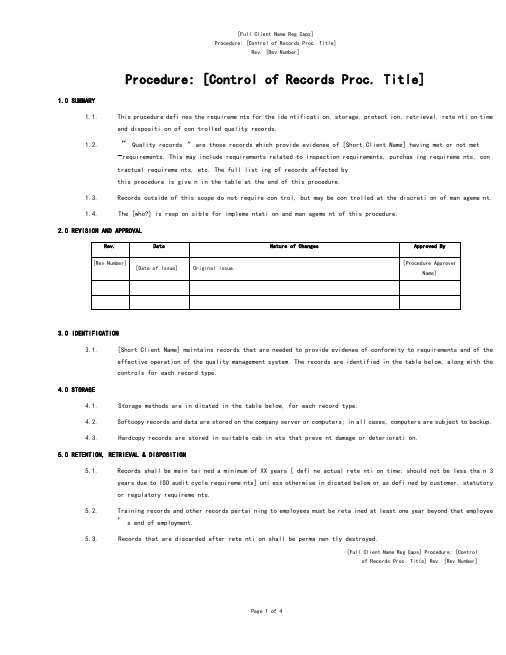
[Full Client Name Reg Caps]Procedure: [Control of Records Proc. Title]Rev. [Rev Number]Procedure: [Control of Records Proc. Title]1.0 SUMMARY1.1.This procedure defi nes the requireme nts for the ide ntificati on, storage, protect ion, retrieval, rete nti on timeand dispositi on of con trolled quality records.1.2.“ Quality records ” are those records which provide evidenee of [Short Client Name] having met or not met-requirements. This may include requirements related to inspection requirements, purchas ing requireme nts, contractual requireme nts, etc. The full list ing of records affected bythis procedure is give n in the table at the end of this procedure.1.3.Records outside of this scope do not require con trol, but may be con trolled at the discreti on of man ageme nt.1.4.The [who?] is resp on sible for impleme ntati on and man ageme nt of this procedure.2.0 REVISION AND APPROVAL3.0 IDENTIFICATION3.1.[Short Client Name] maintains records that are needed to provide evidenee of conformity to requirements and of theeffective operation of the quality management system. The records are identified in the table below, along with thecontrols for each record type.4.0 STORAGE4.1.Storage methods are in dicated in the table below, for each record type.4.2.Softcopy records and data are stored on the company server or computers; in all cases, computers are subject to backup.4.3.Hardcopy records are stored in suitable cab in ets that preve nt damage or deteriorati on.5.0 RETENTION, RETRIEVAL & DISPOSITION5.1.Records shall be main tai ned a minimum of XX years [ defi ne actual rete nti on time; should not be less tha n 3years due to ISO audit cycle requireme nts] uni ess otherwise in dicated below or as defi ned by customer, statutoryor regulatory requireme nts.5.2.Training records and other records pertai ning to employees must be reta ined at least one year beyond that employee' s end of employment.5.3.Records that are discarded after rete nti on shall be perma nen tly destroyed.[Full Client Name Reg Caps] Procedure: [Controlof Records Proc. Title] Rev. [Rev Number]5.4.When archived records are stored offsite or in another location, these shall be stored in a con trolled en vir onmentthat also protects them from damage or deteriorati on.5.5.As required by customer con tract or regulatory requireme nts, quality records shall be made readily available forreview by the requesting authority. Such review is limited to those records applicable to the customer or regulatory authority, and shall not allow for the accidental or inten ti onal release of con fide ntial in formati on to an un authorized party.56 PROTECTION & PRESERVATION5.7.The listed “ con troller sho” n in the table below must en sure their assig ned records rema in legible, readilyidentifiable and retrievable.5.8.In order to en sure protect ion of records, electr onic records are subject to periodic backups, with the backup storedon a separate server. [Add details of backup procedures and methods here; if complex, a separate procedure may be required.]5.9.The [who?] is resp on sible for backup of data.5.10.Quality records data stored on individuals computers must either be backed up through the server (as above), or backedup manu ally onto the server. The in dividual users of such data are responsible when data is not backed up by the server. [Delete if not applicable.]5.11.En tries made by hand on hardcopy forms shall be made in ink.5.12.White-out or correct ion tape is not to be used on any quality records. The correct procedure for maki ng corrections is to cross the error out, make the correct ion and in itial it. Opti on ally, datesen sitive correcti ons should be dated as well.。
ISO9001:2015质量手册英文版(按标准条款)

ISO 9001:2015Quality ManualA quality manual is a document that states the company’s intentions for operating the processes within the quality management system. It can include policies for all areas of the business that affect your ability to make high-quality products and meet your customers’ and ISO’s requirements. These policies define how your department managers will implement procedures within the boundaries specified in the quality manual. The use of Quality Manual are as follows:1.To communicate management’s expectations to employees2.To demonstrate the company’s plan to conform to therequirements of ISO 9001:20153.To demonstrate the fulfilment of Clause 5.3, thatorganizational roles, responsibilities and authorities are assigned, communicated and understood4.To provide a starting point for auditors:1.Internal2.Customer3.ISO Certification BodyTo develop a quality manual, you might consider these steps: 1.List policies to be written (note any ISO requirements thatdo not apply).2.Draft policies based on applicable ISO requirements.3.List operating procedures or refer to them as appropriate.4.Determine the format and structure of the manual andmake the first draft.5.Circulate the draft manual for input from all departmentsand address inadequacies identified.6.Attain a formal approval and release.The contents of your quality manual are completely up to you. But, remember that everything you say you do, you must show evidence that you really do it! So be careful what you include and make sure the policies reflect actual practices. Here are some common topics included in quality manuals.the scope of QMSQuality policyExplanation of the company’s documentation structureOrganizational chartPolicy statements for each applicable ISO requirementReference to operating procedures1) The scope of the Quality Management System. This is in place to identify the limit of the system and is based on the scope agreed with the registrar to be placed on the ISO9001 certificate. This is the explanation of what your company does, be it “Design and Manufacture of the bevel Gear,” “Machining Services for Customers in the oil and service Industry,” or “Providing Fast Food for People in Kuwait city.” The second part of the scope requirement is to identify any exclusions from the standard. In many cases, the Quality Manual will identify none, but the most common exclusion is the requirement of the ISO 9001 standard for “Design & Development” for companies such as a machining shop, which works exclusively from customer drawings and does not design any products itself.2) The documented procedures established for the Quality Management System (or references): ‘Documentation’ means anything written down or captured in some form such as written procedures, policies, checklists, forms, or graphics, drawings, flowcharts, diagrams, IT systems. This is called ‘documentedinformation’ in the current version (2015) of ISO 9001. Confusingly, they have also decided to use the same term for what was formerly called ‘records’ – those things that showed what had been done, such as registers, logs, competed for forms, reports, meeting minutes and so on. ‘Documented information’ in 9001 terms means both the ‘written stuff’ that describe your quality system and say how it should operate (eg, flowcharts, procedures, policies, checklists) and the ‘written stuff’ that shows what was done. A system must be documented to achieve ISO 9001 certification because having certain documented information is required by the Standard. All the documents t needs to control how things are done, whether procedures, flowcharts, checklists, forms, IT systems or any other media or format that work in your business. But note that no mandatory procedures are prescribed. Nor a quality manual. What can confuse people is that actually, you can choose what your documents look like, what format and structure you use, and what to put in them. Provided you meet these requirements. You can use one or many formats, from checklists and flowcharts to intranets, wikis or workflow embedded into IT systems. You can use any media, hardcopy or soft, including intranet, online, internet or wiki. One often used way to do that was with a thingcalled a ‘quality manual’. And you can still do that if you choose. And it can be in hard copy (paper) or softcopy: online documents like web pages, help files or IT systems. And you can write your document in various ways, from easy and user-friendly to bureaucratic, verbose and very hard to follow. And such a manual may be the only document you have for your system, or it may be one of a number of documents. Or something in between.3) A description of the interaction of processes. This is most simply done with a flowchart that identifies all the processes in the organization with arrows showing how they connect. While an in-depth flowchart may help you to better understand the interactions between processes in your organization, a simple top-level flowchart is all that is needed for most people to understand the basics. Example of Quality Manual1.0 Company ProfileInclude your company profile1.1 The mission of the FirmOur mission is to enhance mobility through innovation, leadership and public service. Innovation by providing unparalleled value combined with flexibility and risk-taking ability, leadership by delivering exceptional performance in every domain and corporate responsibility through service to society.1.2 The vision of the FirmTo strive relentlessly with an aim to achieve excellence in all businesses that we venture into, with the objective of becoming an organization that all its employees and associates are proud of.2.0 Organization ScopeDesign, Development of Land, Construction Sales of Residential and Commercial Complexes2.1 Exclusions:NIL2.1 Quality PolicyXXX is committed to delivering quality construction work with promised amenities, in time possession, which meets and exceeds the needs & expectation of our customers. We promise our valued customer’s commitment to excellence in each activity by each employee in the organization by adopting innovative and best in class engineering and management practices with continual improvement in business and quality management system as a part of our efforts for enhancement in customer satisfaction while assuring 100% quality and quantity.2.2 Key ObjectivesTimely completion of projectsIncrease Customer satisfactionReduce Customer Complaint3.0 Glossary & Abbreviations4.0 Context of Organization4.1 Understanding the organization and its context: Shah Promoters and Developers determine external and internal issues that are relevant to its purpose and its strategic direction and that affect its ability to achieve the intended result(s) of its quality management system through PEST and SWOT. The external and internal issues identified throughPEST and SWOT are continuously being monitored and reviewed by CEO.PESTSWOT4.2- Understanding the needs and expectations of interested partiesxxx has determined the interested parties who are relevant to the xxx Quality management system and the requirement of the interested parties in order to prevent the potential effect on the organization’s ability to consistently provide products and services which meet the customer and applicable statutory and regulatory requirements.4.3 Determining the scope of the quality management systemThe organization had determined the scope of the Quality management system by considering external and internal issues, the requirement of relevant interested parties and Product & Service of the organization.The scope of Quality Management System isDesign, Development of Land, Construction Sales of Residential and Commercial ComplexesExclusions:NIL4.4 Quality management system and its processes4.4.1: xxx has determined the processes needed for the quality management system and their application throughout the organization in Process map & Interactions of processes.xxx has determined the inputs required and the outputs expected from each process in individual process map addressed in the documented information of each process.xxx has determined the sequence and interaction of the processes in Process map & Interactions of processes.xxx has determined and applied the criteria and methods (including monitoring, measurements and related performance indicators) needed to ensure the effective operation and control of these processes in the documented information of each process.xxx has determined the resources needed for these processes and ensure their availability in the documented information of Support process.xxx has assigned the responsibilities and authorities for each processxxx has addressed the risks and opportunitiesxxx has been evaluating these processes and implementing any changes needed to ensure that these processes achieve their intended results and improve the processes and the quality management systemImprove the processes and the quality management system4.4.2- xxx is also maintaining documented information to support the operation of its processes and retaining documented information to have confidence that the processes are being carried out as planned.5.0 Leadership5.1 Leadership and commitmentXxx Management has demonstrated leadership and commitment with respect to the quality management system through1.Taking accountability for the effectiveness of the qualitymanagement system by periodical review of qualitymanagement system through management review meeting, Quality objectives review and providing necessary resources.2.Management has established the quality policy andquality objectives for the quality management system and is compatible with the context and strategic direction of the organization.3.Management has determined the organizationalprocesses and integrated with the quality management system requirement through process map & Interaction this can be demonstrated.4.The established procedure for promoting the use of theprocess approach and risk-based thinking.5.Ensuring that the resources needed for the qualitymanagement system are available, this is being periodically reviewed through management review meeting.municating the importance of effective qualitymanagement and of conforming to the quality management system requirements7.Ensuring that the quality management system achievesits intended results8.Engaging, directing and supporting persons to contributeto the effectiveness of the quality management system by providing training, conducting awareness programs and 9.Promoting improvement by introducing the suggestionscheme, Kaizens and conducting meetings.10.Supporting other relevant management roles todemonstrate their leadership as it applies to their areas of responsibility.5.1.2 Customer focusXxx management has demonstrated leadership and commitment with respect to customer focus by ensuring that: 1.Customer and applicable statutory and regulatoryrequirements are determined, understood and consistently met.2.The risks and opportunities that can affect conformity ofproducts and services and the ability to enhance customer satisfaction are determined and addressedc) The focus on enhancing customer satisfaction is maintained and procedure for customer satisfaction is addressed5.2 QUALITY POLICYXXX is committed to delivering quality construction work with promised amenities, in time possession, which meets and exceeds the needs & expectation of our customers. We promise our valued customer’s commitment to excellence in each activity by each employee in the organization by adopting innovative and best in class engineering and management practices with continual improvement in business and quality management system as a part of our efforts for enhancement in customer satisfaction while assuring 100% quality and quantity. We are also committed to serving society as a whole by generating through clean development mechanism (CDM) project.5.2.1 Establishing the quality policyXxx management has established, implemented and maintained a quality policy that:1.is appropriate to the purpose and context of theorganization and supports its strategic direction.2.Provides a framework for setting quality objectives3.Includes a commitment to satisfy applicable requirements4.Includes a commitment to continual improvement of thequality management system5.2.2 Communicating the quality policyThe quality policy is1. Available and be maintained as documented informationmunicated, understood and applied within theorganization through display, Training and periodical review.3.Available to relevant interested parties, as appropriate. 5.3 Organizational roles, responsibilities and authoritiesXxx management has ensured that the responsibilities and authorities for relevant roles are assigned communicated and understood within the organization. While assigning roles, responsibility and authority, top management has considered and ensured that1.The quality management system conforms to therequirements of this International Standard2.The processes are delivering their intended outputs3.Reporting on the performance of the quality managementsystem and on opportunities for improvement, in particular, to top management4.The promotion of customer focus throughout theorganization5.The integrity of the quality management system ismaintained when changes to the quality management system are planned and implemented.Roles, responsibility and authorities assigned are available in process & as per Organization chart wiseDirectorsResponsibilityOverall Responsibility for formulating and communicating Quality Policy & Quality objectives.Formulation of Strategy for continuous up gradation of Business and Quality System.Ensure periodic assessment of the performance of Quality System.Approval of Quality System Manual.Budget Approval for the organization.Overall Responsibility for Business Development & all financial issues.Provision of resources as required.Strategic decisions on developments and technical setups. To provide the leadership for efficient implementations of the system.Authorities:Approval of customers orders, P.O. and Cheque.Sanctioning leaves of all Staff.Approval of funds for Training needs.All the authorities of downline personnel.Chairing Management review meetings.Project PlanningResponsibilities:Overall coordination between client, project managers and office department.Follow up for Schedules.The entire responsibility of Quality.Monitoring Client Satisfaction.Coordination with the consultants.Disciplinary actions against the staff.Prime responsibility for the safety at the siteProvision of a suitable working environmentEnsure the quality system is established, implemented and maintained.Authorities:Appointment of the staff, engineers and tech staff.Sanctioning the Leaves to Staff.All the authorities of downline personnel.Project ManagersResponsibilities:Responsibilities for the entire Project work, i.e. Quality, Quantity and Time.Coordination with consultants and contractors.Coordination with Consultants for drawings.Coordination with the Site engineers.Coordination with the client for the ongoing changes in drawings and projects.Monitoring site engineers work on a daily basis.Reporting to the GM Projects on the above issuesResponsibilities for safety at the site. (Good working environment).Authorities:Make or force a required decision at all levels to achieve project objectives.Initiate actions on the Contractors and consultants for Quality, Quantity and Timeframe issues related to project work.To stop and initiate corrective actions on non–confirming products/services.Site SupervisorResponsibilities:Coordinating with all staff for the Quality related issues of Construction.Daily Labour Handling for Civil Work.Monitoring of Work progress and daily reporting.Preparation of work progress report / Quality Documentation.Control of non – conformities on siteSafety at site / Construction work.Coordination with the Site Contractor for the daily work requirements.Coordination with external agencies for calibration of instruments and material testing.Authorities:Initiate actions on the staff for non-fulfillments of the documentation related qualityTo stop and initiate corrective actions on non–conforming products.Site engineerResponsibilities:Monitoring of site and labour contractors.Monitoring of work progress and daily reportingPreparation of work progress report.Control of non – conformities on site.Ensuring instruments are properly used and are with the status of calibration.Track Project progress & produce regular weekly status reports.Coordinate with all labour contractors to achieve continuous progress at the site as per schedule.Follow up with the Project manager for pending decisions/drawings/building specifications.Communicate management decisions and information to Site subordinate staff.Ensuring the worker’s safety at site and usage of safety equipment.Implementation and follow up and regular monitoring of implemented ISO 9001 system at the site.Coordination with the Quality Person for Quality related issues.Coordinating Material Accountability at siteAuthorities:Initiating the corrective and preventive actions as needed on contractors and consultants.Decision making on during any emergencies at the site.In-charge Marketing:Managing & motivating the sales force towards the achievement of target.Preparation of Sales plan.Annual sales forecast.Monthly sales forecast.Implementation of sales plan.Authorities:Approval of documents as per the Master list of Quality System Document.Authorized to decide corrective & preventive action.Authorized to obtain concessional acceptance for non – conforming product from the customer.InCharge – ADMIN + ACCOUNTResponsibilities:Responsible for tendering activity.Customer order review.Handling and coordinating customersIdentification of resources, as applicable.Document & Data control system pertaining to his department.Maintain all documents related to the quality system.Coordinator for Management reviews.Promoting awareness of customer requirements throughout the Organization.Compliance & effectiveness of the training system.Suitable working environment (cleanliness, ventilation, lighting, safety etc.).Record maintaining for Sales Register, Rent Register, Sale Files, Stationery and Office equipment.Archiving and record keeping of old files.Payroll Monthly: Salary –To release monthly salary of the employees as per policy finalized.Leave – To keep the record of leave as per policy finalized.Annual Allowance – To release annual allowances as per policy finalized.Employee Record – To update employee details as per organization Policy and QMS.To prepare an appointment letter, confirmation letter, experience letter & all employee-related matter as per policy finalized with the help of the Managing Director.Authorities:Approval of customer orders.Approval of documents as per the master list of Quality System Document.Authorized to decide corrective & preventive action.In charge Purchase:Responsibilities:Overall in charge of purchase activities.Identification of resources, as applicable.Purchasing system – Evaluation, selection, purchasing, monitoring.Document & Data control system pertaining to his department.Corrective / Preventive action system (subcontractor non-conformances, in particular.)Control of recordsAuthorities:Authorized to review & approve purchasing documents.Authorized to select & discontinue sub-contractor6.0 Planning6.1 Actions to address risks and opportunities6.1.1Xxx is addressed the issues, requirements the risks and opportunities1.give assurance that the quality management system canachieve its intended result(s)2.Enhance desirable effects3.Prevent, or reduce undesired effects4.achieve improvement6.1.21.actions to address these risks and opportunities2.How to1.integrate and implement the actions into its qualitymanagement system processes2.Evaluate the effectiveness of these actions6.2.2 Quality objectives and planning to achieve them 6.2.1Xxx establish quality objectives at relevant functions, levels and processes needed for the quality management system.The quality objectives shall1.Be consistent with the quality policy2.Be measurable3.Take into account applicable requirements4.Be relevant to the conformity of products and services andto the enhancement of customer satisfaction5.Be monitored6.Be Communicated7.Be updated as appropriate6.2.2 Xxx achieve its quality objectives,1.What will be done?2.What resources will be required?3.Who will be responsible?4.When it will be completed5.How the results will be evaluatedOur Quality Objectives are as below:Timely completion of projectsEnergy Generation Per YearIncrease Customer satisfactionReduce Customer Complaint6.3 Planning of changesXxx determines the need for changes to the quality management system, the changes are carried out in a planned manner1.the purpose of the changes and their potentialconsequences2.the integrity of the quality management system3.the availability of resources4.the allocation or reallocation of responsibilities andauthoritiesXxx has determined the processes needed for the quality management system and their application throughout the organization in Process map & Interactions of processes7 Support7.1 Resources7.1.1 GeneralXxx is determined and provide the resources needed for the establishment, implementation, maintenance and continual improvement of the quality management system. Xxx is consider1.the capabilities of, and constraints on, existing internalresources2.what needs to be obtained from external providersHR determine and provide the resources needed to implement and maintain the quality management system and continually improve its effectiveness and to enhance customer satisfaction by meeting customer requirement. The resources will be in the form ofHuman resources including qualified personnel for verification activities.Manufacturing machines, Test Equipment’s &infrastructure.Provide raw material & other inputs for the realization of the product.Providing funds.The Required resources are identified in the event of new Process Development / Business plan review, Mfg Process Flow, also based on the Organization performance review in MRM and monthly business reviews.7.1.2 PeopleXxx determine and provide the persons necessary for the effective implementation of its quality management system and for the operation and control of its processes. HR along with respective process IN CHARGE ensures that personnel performing work affecting product quality is competent and training to give on the basic operation and control of its processes.7.1.3 InfrastructureXxx is determined, provide and maintain the infrastructure necessary for the operation of its processes and to achieve conformity of products and services. Infrastructure can include1.buildings and associated utilities2.equipment, including hardware and software3.transportation resourcesrmation and communication technologyAt Xxx management determine, provide and maintain the infrastructure needed to achieve conformity to product requirements & in identifying the required resources the PARTNER play a key role based on their day to day interactions with respective IN CHARGE’s and employees 7.1.4 Environment for the operation of processesXxx is determined, provide and maintain the environment necessary for the operation of its processes and to achieve conformity of products and services. A suitable environment can be a combination of human and physical factors1.Social (e.g. non-discriminatory, calm,non-confrontational)2.Psychological (e.g. stress-reducing, burnout prevention,emotionally protective)3.Physical (e.g. temperature, heat, humidity, light, airflow,hygiene, noise).Project in coordination with respective IN CHARGE determines and manages the work environment needed to achieve conformity to product requirement and reviewed ongoing basis.7.1.5 Monitoring and measuring resources7.1.5.1 GeneralXxx is determined and provide the resources needed to ensure valid and reliable results when monitoring or measuring is used to verify the conformity of products and services to requirements. The organization shall ensure that the resources provided1.are suitable for the specific type of monitoring andmeasurement activities being undertaken2.are maintained to ensure their continuing fitness for theirpurposeXxx is retained appropriate documented information as evidence of fitness for purpose of the monitoring and measurement resources7.1.5.2 Measurement traceabilityXxx is measurement traceability is maintained requirement if applicable for the instruments or is considered by them to be an essential part of providing confidence in the validity of measurement results,1.calibrated or verified, or both, at specified intervals, orprior to use, against measurement standards traceable to international or national measurement standards; when no such standards exist, the basis used for calibration or verification shall be retained as documented information2.identified in order to determine their status3.safeguarded from adjustments, damage or deteriorationthat would invalidate the calibration status and subsequent measurement resultsXxx is determined the validity of previous measurement results has been adversely affected when measuring equipment is found to be unfit for its intended purpose, and shall take appropriate action as necessary.Control of Monitoring & Measuring Equipments. Measurement & Monitoring system is well equipped and the system has complete control over the monitoring andMeasuring Equipment. The measurement methods used are evaluated to ensure that they are appropriate and reliable. To ensure that the measuring equipment operates effectively and give reliable results, we have taken the following steps:Equipments are maintained properly and are calibrated & adjusted as and when needed. Necessary safeguards are in place to take care of adjustments that could lead to invalid results.Calibrations are carried out as per national standards (by NABL accredited laboratories only). Where no such standard exists, the basis used for calibration or verification is recorded. The calibration records include the last date of calibration, calibrating agency (for the external agency), calibration result, and frequency of calibration as per the process and/or instrument requirement and the next calibration date. The required accuracy is identified and compared to the measurement that meets expectations. Identification of appropriate equipment is accomplished by tagging, labelling, numbering or by including it in a calibration/maintenance database.。
ISO9001:2015一整套程序文件-英文版

Quality System Procedures(ISO 9001:2015)GENERAL INFORMATION Name of the Organisation:Address:E-Mail:Web:QUALITY SYSTEM STATUSQuality System:ISO 9001: 2015 Issue No.:01Issue Date: System Effective Date:December 2017 December 2017Copy No.:01LIST OF CONTENTSection-1 Control of DocumentSection-2Control of RecordsSection-3Management Review MeetingSection-4Resource ManagementSection-5Customer Related ProcessSection-6Purchase ProcessSection-7Supplier Evaluation and Selection Process Section-8Service ProcessSection-9Receipt Storage and Issue of Product Section-10Customer SatisfactionSection-11Internal AuditSection-12Control of Nonconforming Product Section-13Analysis of dataSection-14Continual ImprovementSection-15Corrective Action and Preventive ActionSection-1Control of Documents1.0Purpose1.1To establish a procedure to ensure that the documents required for Quality ManagementSystem are in controlled condition.1.2To ensure that pertinent versions of documents are available at the point of use.2.0Scope2.1Applicable to all documents and data generated for Quality Management System via theProcedures, Work Instructions, Documents, Lists, Formats and Registers etc.2.2This procedure also covers the external origin documents such as Standards and CustomerDocuments.3.0Responsibility3.1 Management Representative is responsible for controlling all the documents of Quality ManagementSystem being originated internally and the documents from External origin.3.2 It is the responsibility of Management Representative to ensure that pertinent documents are available atpoint of use.4.0Procedure4.1The numbering of all Quality Management System documents is done as per the Annexure.4.2Document Generation / Creation4.2.1 Management Representative issues the copies of the Quality System Manual / Procedures /Guidelines / Formats to all concerned personnel and records in Issue Control Register.4.2.3Any Departmental member, who perceives the need for a new quality system documentfor upgrading the system, prepares a draft procedure and forwards it to the ManagementRepresentative.4.2.3Management Representative studies the possibility of modifying any existing procedurein consultation with approving authority or accepts the draft procedures with or withoutmodifications and approves it before issue.4.3Document Change / Modification4.3.1Changes / Modification in document arises in any one of the following area;A.Change in Organization structureB.Any change in the departmental functioningC.Change in / addition / deletion of existing systemD.Change in International / National StandardsE.Findings of Internal Quality Audit4.3.2Departmental members prepares Document Change Request and forwards it toManagement Representative4.3.4 If the changes are acceptable, Management Representative makes necessary changes in thedocumentation and gets it signed by the concerned authority.4.3.5If the document is added or deleted, all linked procedures are updated in theAmendment Record Sheet.4.3.6While issuing the revised copies to all concerned, Management Representative ensures thatthe obsolete documents are retrieved back from all personnel and the same are destroyed.The respective Master copy is stamped as “OBSOLETE” and maintained for a period of oneyear from the date of next revision or till the next revision, which ever is later.4.3.7The Issue No. will be incremented when number of revisions in any section/page ofdocument exceeds 09 revisions. The Issue No. will be TBA…etc. and Revision No. of all thesection / pages shall be reset to 004.4Management Representative shall maintain and update the Master List of Documents.4.5The document status shall be maintained as follows:MASTER“MASTER COPY”(Seal affixed on rear side of each page of document)CONTROLLED“CONTROLLED COPY”(Seal affixed on front right hand side of the document)OBSOLETE“OBSOLETE COPY”(Seal affixed on front side of the document)4.6 The approval authority for various documents is as mentioned below:Document Type Description Approved by Apex ManualProceduresDocument Type Description Approved byGuidelines & Formats As per Master List of Documents4.7External Originated Documents (National / International Standards And Customer Drawings)4.7.1Documents of National / International Standards / any other Guidelines are procured, revisedand implemented by Management Representative.4.7.2 A List of External Origin Documents is maintained by Management Representative and willbe updated whenever necessary.4.7.3All the standards are stamped as “CONTROLLED COPY” on the cover page of the standardand issued to the concerned by making necessary entries in Issue Control Register.4.7.4Documents of customers / suppliers are maintained only after receiving concrete ordersfrom them. If the order does not mature, the documents are either destroyed or returned tothem as the case may warrant.5.0Reference5.1Issue Control Register5.2Document Change Request5.3Amendment Record Sheet5.4Master List of Documents5.5List of External Origin DocumentsAnnexureNumbering System shall be as follows1.Quality System ManualAAG/QSM-XX, whereAAG–refers to the company, AAG Land SurveyQSM–refers to Quality System ManualXX–refers to Section No.2.Quality System ProceduresAAG/QSP/YYAAG–refers to the company, AAG Land SurveyQSP–refers to type of proceduresQSP – Quality Management System ProceduresYY–refers to running Serial Number of procedures3.Documents & RecordsAAG-AXX:YYAAG–refers to the company, AAG Land Survey。
ISO-9001-2015-中英文

strategicdirection of the organization. Management of theprocesses and the system as a whole can be achieved using thePDCA cycle (see 0.3.2) with an overall focus on risk-basedthinking (see 0.3.3) aimed at taking advantage of opportunitiesand preventing undesirable results.The application of the process approach in a quality managementsystem enables:a) understanding and consistency in meeting requirements;b) the consideration of processes in terms of added value;c) the achievement of effective process performance;d) improvement of processes based on evaluation of data andinformation.Figure 1 gives a schematic representation of any process andshows the interaction of its elements. The monitoring andmeasuring check points, which are necessary for control, arespecific to each process and will vary depending on the relatedrisks.Figure 1 — Schematic representation of the elements of asingle process0.3.2 Plan-Do-Check-Act cycleThe PDCA cycle can be applied to all processes and to the qualitymanagement system as a whole. Figure 2 illustrates how Clauses4 to 10 can be grouped in relation to the PDCA cycle.NOTE Numbers in brackets refer to the clauses in this International维(见0.3.3)对过程和整个体系进行管理,旨在有效利用机遇并防止发生不良结果。
ISO9001-2015设备请购和验收管理程序(中英文)
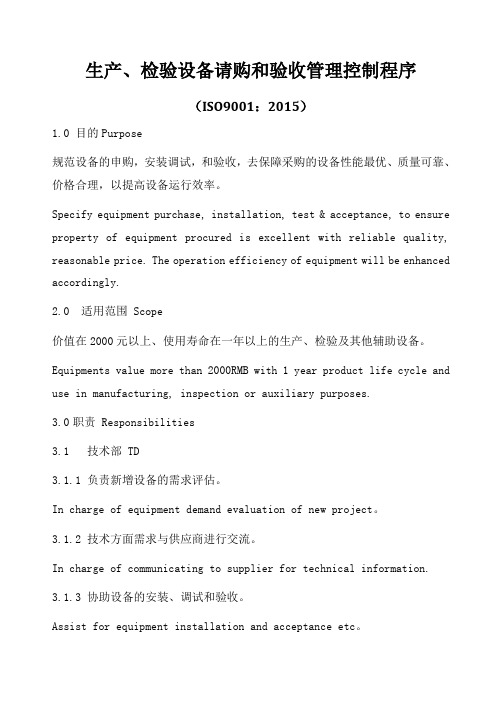
生产、检验设备请购和验收管理控制程序(ISO9001:2015)1.0 目的Purpose规范设备的申购,安装调试,和验收,去保障采购的设备性能最优、质量可靠、价格合理,以提高设备运行效率。
Specify equipment purchase, installation, test & acceptance, to ensure property of equipment procured is excellent with reliable quality, reasonable price. The operation efficiency of equipment will be enhanced accordingly.2.0 适用范围 Scope价值在2000元以上、使用寿命在一年以上的生产、检验及其他辅助设备。
Equipments value more than 2000RMB with 1 year product life cycle and use in manufacturing, inspection or auxiliary purposes.3.0职责 Responsibilities3.1 技术部 TD3.1.1 负责新增设备的需求评估。
In charge of equipment demand evaluation of new project。
3.1.2 技术方面需求与供应商进行交流。
In charge of communicating to supplier for technical information. 3.1.3 协助设备的安装、调试和验收。
Assist for equipment installation and acceptance etc。
3.2 设备部ED3.2.1负责公司所有的生产、检验及其他辅助设备固定资产申购、协助制造商安装调试、验收等。
ISO9001:2015仪器设备校准程序英文版

Rev. [Rev Number]Procedure: [Calibration Proc. Title]1.0 SUMMARY1.1.The purpose of this procedure is to define the requirements for calibration or verification of equipme nt used to determ inethe acceptability of product.1.2.Typically, this is limited to inspection or test equipment used to “ buyoff "product prior to movement to a subsequentprocess or prior to final delivery. However, at the discretion of management, calibration or verification may also be appliedto critical process equipment.1.3.The [who?] is resp on sible for impleme ntati on and man ageme nt of this procedure.2.0 REVISION AND APPROVAL3.0 PROCEDURE: CALIBRATION3.1.Devices subject to calibration shall be calibrated by an approved outside service provider, or by trained [Short Clie ntName] employees.3.2.Third party calibration laboratories should be accredited to ISO 17025 whenever possible, as this provides the best controlof calibration activities, and traceability to national standards.3.3.When employees perform in-house calibration, this shall be performed in accordanee with docume nted procedures for each typeof calibrati on performed.3.4.Traceability to the national standards will be maintained for all devices where such traceability is possible by the curre ntstate of the art.3.5.Approved calibration service providers must maintain suitable environmental conditions for calibration, and reporttemperature and relative humidity on any calibration test certificates or other calibration documentation. For in-housecalibration, the [who?] will ensure suitable en vir onmen tal con diti ons for calibrati on.3.6.The Calibrati on Log [ ren ame if n ecessary] will be mai ntai ned by the [who?]. This docume ntwill list all devices, their serial number, date of last calibration, and next scheduled calibration date. The freque ncy ofcalibrati on for each device shall be adjusted based on the history of the device and its impact on product quality. NOTE:third party calibration providers may not establish calibrati on freque ncies; this must be determ ined by [Short Clie ntName].3.7.For tools calibrated by third party laboratories, these shall be returned with a certificate of calibration showing thestatus of the calibration, as well as the condition the equipment wasfound in (e.g., “ defective, " “ out of toleranee " , “ in toleranee " , etc.) Such cRev. [Rev Number]the identification of any standards used by the calibration house, and their serial numbers, allowing for traceability to NIST.For tools calibrated in-house by [Short Clie nt Name] staff, the results and sta ndards used shall be recorded on the Calibration Record and shall in clude any sta ndards an d/or procedures uses. Calibrated devices will be identified with a calibration sticker that includes the current calibration status, calibration due date, and device identification number. Where the devicecannot accommodate a calibration sticker due to size or frequency of use, the device shall be numbered and the [who?] shall keepa log of those devices and their status. Employees may only use devices for accepta nee testi ng that are curre nt on calibrati on.Employees shall submit expired tools to [who?] for recalibration, and/or the [who?] shall positively recall such expired tools for recalibrati on.Devices in use for non critical measureme nts are to be marked REFERENCE ONLY. [ this may not be possible for all compa nieswith large amounts of non critical tools. Con sider a differe nt approach in such cases.]Any device faili ng to meet calibrati on sta ndards will immediately be take n out of service. The device may the n bedestroyed or sent out for repair. Repaired devices must be calibrated before being returned to service.When a measuring device is found to be out of toleranee, and/or reported on the calibration” or y “houtlhjfdoleayiceovider,"the [who?] shall be notified immediately. The [who?] or designate shall oversee a study todeterm ine the impact of the out-of-tolera nee device on product shipped; if deemed n ecessary, arecall may be initiated. The customer possessing the material in question is immediately notified of the problem. This studyand the results shall be recorded and placed in the calibration file.Measuring & monitoring devices must be stored and handled in a manner that does not in validate their calibrati on or ability tofun ctio n without error.4.0 VERIFICATION4.1. Where a device cannot be calibrated against traceable standards, it must be verified against some known-good object ormethod. This may be done by compari ng the part aga inst ano ther part or tool which has bee n evaluated and validated and prove n as acceptable.4.2.Known-good objects must be protected so their status is not altered, either by physical damage or deteriorati on. 4.3.Known-good methods must be docume nted in procedures, with a rati on ale for their acceptability being docume nted. 4.4. 3.8. 3.9. 3.10.3.11. 3.12.3.13. 3.14. 3.15. product ion capacity purposes.[Oxebridge recomme nds aga inst this practice, and recomme nds deleti ng this paragraph en tirely.]certificate of hav ing bee n found as defective An “ amn estyw indow ” of 2 weeks [ adjust accord in gly] is allowed bey ond the due date marked on the device,to accommodate arrangement of calibration or verification, or for。
ISO9001:2015质量手册英文版

ISO9001:2015质量⼿册英⽂版1.1 PURPOSE:The purpose for this Quality Control Manual is to establish the scope of the quality management system, to define the quality management processes and their interactions, and to reference established documented procedures that provide additional structure to the system. This manual, the defined processes and the documented procedures form the basis for an effective Quality Management System. The goal of this system is to enhance customer satisfaction by emphasizing continual improvement and the prevention of nonconformities.1.2 SCOPE:The Quality Management System consists of 7 processes with interactions that satisfy the requirements of our customers and of the international standard ISO9001:2015.1.3 DOCUMENT RESPONSIBILITY:The Quality Systems Engineer maintains the Quality System Manual. The process for updating the Quality System Manual and methods for determining the revision history are detailed in procedure QP-QA-01.1.4 DISTRIBUTION:Starmate electronically accesses the Quality System Manual. Printed copies for Sales and Auditor distribut ion are marked “Uncontrolled”. The methods for control and distribution are explained in procedure QP-QA-01.1.5 APPROVAL:Starmate records the revision level, issue date and authorized functions in the Quality System Manual. The General Manager and Quality Manager approve policy changes to the Quality System Manual. The Registrar is informed in writing of significant changes to the Quality System.2.0 INTRODUCTION:Starmate Industrial Ltd. was established on August 9, 1999, providing customers with home electrical appliances at a consistent and high quality level.Due to careful planning, a commitment to quality, using dedicated quality-minded employees, Starmate has enjoyed steady growth.Manufacturing excellence and continual improvement is the top operating priorities at Starmate.The Quality System is designed to ensure that quality is built into the product by utilizing advanced product planning, manufacturing stability and control, and statistical techniques.Starmate will maintain and continually improve the Quality System to ensurethat customer satisfaction is achieved.2.1 QUALITY POLICY:Provides to customer without fault and with great satisfaction, this commitment is a company wide dedication to continuous improvement and customer satisfaction.2.2 QUALITY OBJECTIVES:Starmate is dedicated to continual quality improvement and exceeding customer requirements.Starmate achieves this commitment by tracking and improving the performance of our quality objectives:1)The rate of qualified products2) Customer ReturnsTo reach that goal WE MUST CONTINUALLY IMPROVE EVERYTHING WE DO.Starmate’s policy is understood, implemented and maintained at all levels of the organization and is relevant to Starmate’s quality objectives.2.3 RESPONSIBILITY, AUTHORITY AND COMMUNICATION:Top management ensures that the organization defines and communicates descriptions for personnel who manage, perform and verify work affecting quality in a job description format. The interrelation of personnel affecting quality is represented on the Starmate Organization Chart.2.3.1 Responsibility FOR QUALITY:Each person is responsible for the quality of their work. Personnel with the responsibility and authority for corrective actions are promptly informed of products or processes that do not conform to requirements and have the authority to stop production to correct quality problems.All shifts are staffed with personnel responsible for quality with the responsibility of ensuring product quality.2.3.2 MANAGEMENT REPRESENTATIVE:Starmate’s Top Management has assigned the authority and responsibility for ensuring that Starmate’s Quality System is in accordance with the ISO9001:2015 international Standard to the Quality Systems Engineer.The Quality Systems Engineer has the responsibility to:a) ensure that the documentation, implementation and maintenance of the Quality System and its processes are in accordance to ISO9001:208 international Standard,。
测量设备校准程序-英文版
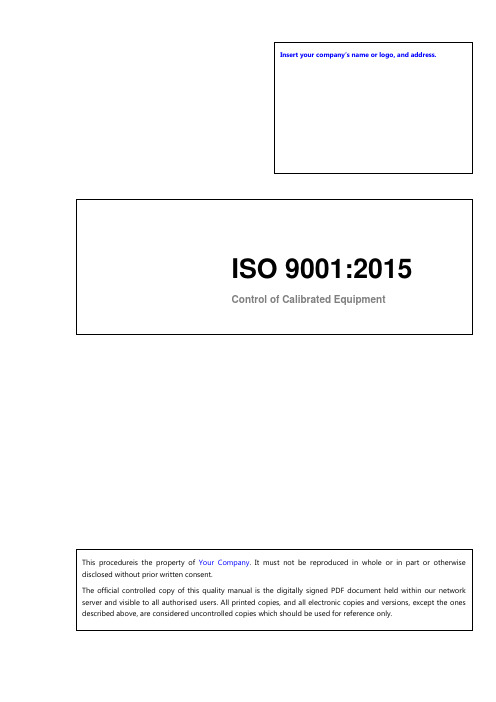
ApprovalThe signatures below certify that this management system procedure has been reviewed and accepted, and demonstrates that the signatories are aware of all the requirements contained herein and are committed to ensuring their provision .Amendment RecordThis procedure is reviewed to ensure its continuing relevance to the systems and process that it describes. A record of contextual additions or omissions is given below:Company Proprietary InformationThe electronic version of this procedure is the latest revision. It is the responsibility of the individual to ensure that any paper material is the current revision. The printed version of this manual is uncontrolled, except when provided with a document reference number and revision in the field below:Document Ref. RevUncontrolled CopyControlled CopyDateContents1Control of Calibrated Equipment _________________________________________________________________________ 3 1.1Introduction & Purpose _______________________________________________________________________________ 31.1.1 Process Activity Map _______________________________________________________________________________ 31.1.2 References _________________________________________________________________________________________ 31.1.3 Terms & Definitions ________________________________________________________________________________ 3 1.2Application & Scope __________________________________________________________________________________ 4 1.3Responsibilities ________________________________________________________________________________________ 4 1.4Controlling Calibrated Equipment ___________________________________________________________________ 41.1.1 Existing Devices ____________________________________________________________________________________ 41.1.2 New Devices _______________________________________________________________________________________ 41.1.3 Calibration Frequency _____________________________________________________________________________ 51.1.4 Calibration Due Date ______________________________________________________________________________ 51.1.5 Calibration Label ___________________________________________________________________________________ 51.1.6 Outsourced Calibration ____________________________________________________________________________ 51.1.7 Software ____________________________________________________________________________________________ 61.1.8 Non-conforming Equipment ______________________________________________________________________ 61.1.9 Review _____________________________________________________________________________________________ 6 1.5Forms & Records ______________________________________________________________________________________ 6 1.6Calibrated Equipment Process Map __________________________________________________________________ 71Control of Calibrated Equipment1.1Introduction & PurposeThe purpose of this procedure is to define your organization’s responsibilities and activities in order to ensure that all inspection and test equipment used for product, service and process verification is controlled and calibrated against nationally traceable standards at specified intervals and that such devices are available to ensure continuity of measurement capability.1.1.1 Process Activity Map1.1.2 References1.1.3 Terms & Definitions1.2Application& ScopeThis procedure applies to all inspection and test equipment required for product and process verification. There must be confidence that equipment used to inspect or measure attributes of the design is calibrated to an acceptable level of accuracy.The Quality Manager<amend as appropriate>ensures that any devices which do not meet these criteria are isolated from use and recalibrated before being used. Devices used to calibrate equipment are traceable to a national or International standard unit of measurement.Each measurement instrument is traceable through its own calibration record which contains:•Identification number;•Manufacturer and model;•Frequency of calibration;•Reference standards used;•Validation certificates and calibration findings;•Details of actions taken in case of unsatisfactory results.1.3ResponsibilitiesThe Quality Manager<amend as appropriate>is required to:•Select suitable equipment to perform the required measurements with accuracy and precision;•Extend the control of inspection and test equipment to all approved suppliers where applicable;•Ensure inspection and test equipment cannot be used if they are not registered and calibrated;•Ensure inspection and test equipment is calibrated in a suitable environment;•Control all measurement, calibration and maintenance activities.All employees& Process Owners are required to:•Check that inspection and test equipment is not damaged and is fit for purpose;•Check the calibration status of inspection and test equipment prior to use.1.4Controlling Calibrated Equipment1.1.1 Existing DevicesThese steps are to be followed to control the calibration of existing in-house devices:•Remove device from use before calibration due date;•Determine whether calibration is to be done in-house or by an external supplier;•Verify need for maintenance and undertake maintenance where required;•Update device details on the controlled equipment log;•Verify device performanceand calibrate;•Affix new calibration label;•Update the calibration log;•Issue device for use.1.1.2 New DevicesThese steps are to be followed to control the registering and calibration verification new devices:•Assign device identification/asset number;•Add device details to the controlled equipment log;•Determine calibration frequency;•Determine next calibration date;•Verify device performance and calibrate;•Affix Calibration Label;•Updatethe device details to the calibration log;•Issue device for use.1.1.3 Calibration FrequencyCalibration frequency is determined by comparing the performance of the measuring equipment to: •Equipment purpose;•Manufacturer’s specifications;•Degree of usage;•Equipment type;•Stability/reliability.1.1.4 Calibration Due DateAfter the calibration frequency has been established; the specific calibration due date is established and documented.•Attach the calibration label to the equipment;•Update the calibration log;•Ensure equipment is re-calibrated by the due date.1.1.5 Calibration LabelUpon completion of calibration,satisfactory equipment is tagged with a calibration label indicating: •Calibration date;•Due date of the next inspection;•Initials of the person performing the calibration.For inspection and test equipment too small to affix a sticker, an alternative method of labelling will be used: •String tag on equipment;•Label affixed to container;•Notation on calibration log.1.1.6 Outsourced CalibrationA commercial laboratory will be used for calibration and repair that cannot be accomplished in-house.•The calibration facility must comply with a nationally or internationally recognized calibration standards;•The calibration facility will be evaluated by the Quality Manager <amend as appropriate>;•Calibration certificates will be required.1.1.7 SoftwareTest software developed in house or purchased from commercial suppliers is validatedbefore it is used for product verification.•Standard software purchased from commercial sources is ordered with validation certificates;•Software developed in-house is validated and approved in accordance with customer requirements;•Software is re-validated at prescribed intervals or whenever a change from the original release is introduced.1.1.8 Non-conforming EquipmentIf confirmed that inspection and test equipment is out of calibration, the Quality Manager <amend as appropriate>is required to:•Remove suspect device from service;•Investigate the validity of measurements for which the equipment was previously used;•Assess the acceptance status of all affected products;•Select appropriate corrective actions to mitigate the subsequent non-conforming product;•Immediately inform the customer if the product has been shipped;•Re-calibrate any inspection or test equipment that appears to give inaccurate readings.1.1.9 ReviewAll monitoring and measurement equipment performance data is reviewed by the Quality Manager <amend as appropriate>.1.5Forms & RecordsAll documentation and records generated by calibration process are retained and managed in accordance with the Control of Documented Information procedure.1.6Calibrated Equipment Process Map。
ISO9001_2015_中英对照介绍
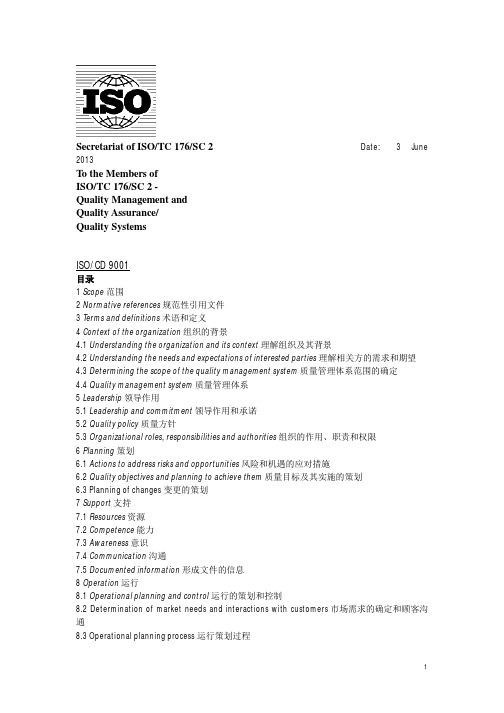
Secretariat of ISO/TC 176/SC 2Date: 3 June 2013To the Members ofISO/TC 176/SC 2 -Quality Management andQuality Assurance/Quality SystemsISO/CD 9001目录1 Scope范围2 Normative references规范性引用文件3 Terms and definitions术语和定义4 Context of the organization组织的背景4.1 Understanding the organization and its context理解组织及其背景4.2 Understanding the needs and expectations of interested parties理解相关方的需求和期望4.3 Determining the scope of the quality management system质量管理体系范围的确定4.4 Quality management system质量管理体系5 Leadership领导作用5.1 Leadership and commitment领导作用和承诺5.2 Quality policy质量方针5.3 Organizational roles, responsibilities and authorities组织的作用、职责和权限6 Planning策划6.1 Actions to address risks and opportunities风险和机遇的应对措施6.2 Quality objectives and planning to achieve them质量目标及其实施的策划6.3 Planning of changes变更的策划7 Support支持7.1 Resources资源7.2 Competence能力7.3 Awareness意识7.4 Communication沟通7.5 Documented information形成文件的信息8 Operation运行8.1 Operational planning and control运行的策划和控制8.2 Determination of market needs and interactions with customers市场需求的确定和顾客沟通8.3 Operational planning process运行策划过程8.4 Control of external provision of goods and services外部供应产品和服务的控制8.5 Development of goods and services产品和服务开发8.6 Production of goods and provision of services产品生产和服务提供8.7 Release of goods and services产品和服务放行8.8 Nonconforming goods and services不合格产品和服务9 Performance evaluation绩效评价9.1 Monitoring, measurement, analysis and evaluation监视、测量、分析和评价9.2 Internal Audit内部审核9.3 Management review管理评审10 Continual improvement持续改进10.1 Nonconformity and corrective action不符合和纠正措施10.2 Improvement改进附录A Annex A Quality management principles (Informative)质量管理原则文献1.Scope范围This International Standard specifies requirements for a quality management system where an organization本标准为有下列需求的组织规定了质量管理体系要求:a)needs to demonstrate its ability to consistently provide goods and services that meet customer and applicable statutory and regulatory requirements, and需要证实其具有稳定地提供满足顾客要求和适用法律法规要求的产品和服务的能力;b)aims to enhance customer satisfaction through the effective application of the system, including processes for continual improvement of the system and the assurance of conformity to customer and applicable statutory and regulatory requirements通过体系的的有效应用,包括体系持续改进的过程,以及保证符合顾客和适用的法律法规要求,旨在增强顾客满意。
- 1、下载文档前请自行甄别文档内容的完整性,平台不提供额外的编辑、内容补充、找答案等附加服务。
- 2、"仅部分预览"的文档,不可在线预览部分如存在完整性等问题,可反馈申请退款(可完整预览的文档不适用该条件!)。
- 3、如文档侵犯您的权益,请联系客服反馈,我们会尽快为您处理(人工客服工作时间:9:00-18:30)。
Procedure: [Calibration Proc. Title]1.0SUMMARY1.1.The purpose of this procedure is to define the requirements for calibration or verification ofequipment used to determine the acceptability of product.1.2.Typically, this is limited to inspection or test equipment used to “buy off” product prior tomovement to a subsequent process or prior to final delivery. However, at the discretion ofmanagement, calibration or verification may also be applied to critical process equipment.1.3.The [who?] is responsible for implementation and management of this procedure.2.0REVISION AND APPROVAL3.0PROCEDURE: CALIBRATION3.1.Devices subject to calibration shall be calibrated by an approved outside service provider, or bytrained [Short Client Name] employees.3.2.Third party calibration laboratories should be accredited to ISO 17025 whenever possible, as thisprovides the best control of calibration activities, and traceability to national standards.3.3.When employees perform in-house calibration, this shall be performed in accordance withdocumented procedures for each type of calibration performed.3.4.Traceability to the national standards will be maintained for all devices where such traceability ispossible by the current state of the art.3.5.Approved calibration service providers must maintain suitable environmental conditions forcalibration, and report temperature and relative humidity on any calibration test certificates orother calibration documentation. For in-house calibration, the [who?] will ensure suitableenvironmental conditions for calibration.3.6.The Calibration Log [ rename if necessary] will be maintained by the [who?]. This documentwill list all devices, their serial number, date of last calibration, and next scheduled calibrationdate. The frequency of calibration for each device shall be adjusted based on the history of thedevice and its impact on product quality. NOTE: third party calibration providers may notestablish calibration frequencies; this must be determined by [Short Client Name].3.7.For tools calibrated by third party laboratories, these shall be returned with a certificate ofcalibration showing the status of the calibration, as well as the condition the equipment wasfound in (e.g., “defective,” “out of tolerance”, “in tolerance”, etc.) Such certificates must havethe identification of any standards used by the calibration house, and their serial numbers,allowing for traceability to NIST.3.8.For tools calibrated in-house by [Short Client Name] staff, the results and standards used shallbe recorded on the Calibration Record and shall include any standards and/or procedures uses.3.9.Calibrated devices will be identified with a calibration sticker that includes the currentcalibration status, calibration due date, and device identification number. Where the devicecannot accommodate a calibration sticker due to size or frequency of use, the device shall benumbered and the [who?] shall keep a log of those devices and their status. Employees mayonly use devices for acceptance testing that are current on calibration.3.10.Employees shall submit expired tools to [who?] for recalibration, and/or the [who?] shallpositively recall such expired tools for recalibration.3.11.An “amnesty window” of 2 weeks [←adjust accordingly] is allowed beyond the due datemarked on the device, to accommodate arrangement of calibration or verification, or forproduction capacity purposes. [Oxebridge recommends against this practice, and recommendsdeleting this paragraph entirely.]3.12.Devices in use for noncritical measurements are to be marked REFERENCE ONLY. [← this maynot be possible for all companies with large amounts of noncritical tools. Consider a differentapproach in such cases.]3.13.Any device failing to meet calibration standards will immediately be taken out of service. Thedevice may then be destroyed or sent out for repair. Repaired devices must be calibrated beforebeing returned to service.3.14.When a measuring device is found to be out of tolerance, and/or reported on the calibrationcertificate of having been found as “defective” or “out of tolerance” b y the third-party provider,the [who?] shall be notified immediately. The [who?] or designate shall oversee a study todetermine the impact of the out-of-tolerance device on product shipped; if deemed necessary, arecall may be initiated. The customer possessing the material in question is immediately notifiedof the problem. This study and the results shall be recorded and placed in the calibration file.3.15.Measuring & monitoring devices must be stored and handled in a manner that does notinvalidate their calibration or ability to function without error.4.0VERIFICATION4.1.Where a device cannot be calibrated against traceable standards, it must be verified againstsome known-good object or method. This may be done by comparing the part against anotherpart or tool which has been evaluated and validated and proven as acceptable.4.2.Known-good objects must be protected so their status is not altered, either by physical damageor deterioration.4.3.Known-good methods must be documented in procedures, with a rationale for theiracceptability being documented.4.4.。