高精度、不锈钢、细长轴的磨削加工
不锈钢的平面磨床磨削方法
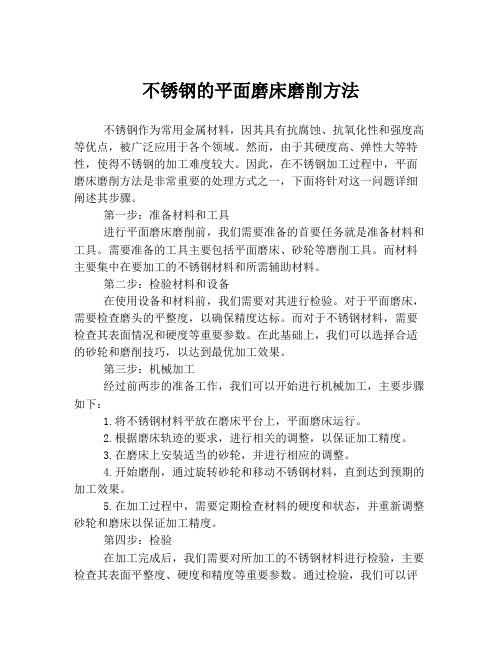
不锈钢的平面磨床磨削方法不锈钢作为常用金属材料,因其具有抗腐蚀、抗氧化性和强度高等优点,被广泛应用于各个领域。
然而,由于其硬度高、弹性大等特性,使得不锈钢的加工难度较大。
因此,在不锈钢加工过程中,平面磨床磨削方法是非常重要的处理方式之一,下面将针对这一问题详细阐述其步骤。
第一步:准备材料和工具进行平面磨床磨削前,我们需要准备的首要任务就是准备材料和工具。
需要准备的工具主要包括平面磨床、砂轮等磨削工具。
而材料主要集中在要加工的不锈钢材料和所需辅助材料。
第二步:检验材料和设备在使用设备和材料前,我们需要对其进行检验。
对于平面磨床,需要检查磨头的平整度,以确保精度达标。
而对于不锈钢材料,需要检查其表面情况和硬度等重要参数。
在此基础上,我们可以选择合适的砂轮和磨削技巧,以达到最优加工效果。
第三步:机械加工经过前两步的准备工作,我们可以开始进行机械加工,主要步骤如下:1.将不锈钢材料平放在磨床平台上,平面磨床运行。
2.根据磨床轨迹的要求,进行相关的调整,以保证加工精度。
3.在磨床上安装适当的砂轮,并进行相应的调整。
4.开始磨削,通过旋转砂轮和移动不锈钢材料,直到达到预期的加工效果。
5.在加工过程中,需要定期检查材料的硬度和状态,并重新调整砂轮和磨床以保证加工精度。
第四步:检验在加工完成后,我们需要对所加工的不锈钢材料进行检验,主要检查其表面平整度、硬度和精度等重要参数。
通过检验,我们可以评估加工的效果,确定是否需要进行相关的修正或二次加工。
总体来说,平面磨床磨削方法是加工不锈钢材料最为常用的一种方式。
通过上述步骤的详细介绍,我们可以更好地了解和掌握其操作技巧和加工流程,以更好地应用于实际工作中,提高加工效率和精度。
分析不锈钢的机械加工方法

分析不锈钢的机械加工方法不锈钢是一种耐腐蚀的金属材料,广泛应用于制造行业中。
机械加工是对不锈钢进行形状加工和表面处理的重要方法之一,本文将分析常用的不锈钢机械加工方法。
1.铣削加工:铣削是将刀具在工件上旋转切削的一种加工方法。
不锈钢的硬度相对较高,因此在铣削过程中需要选用高硬度的刀具,并采用适当的切削速度和进给速度。
对于精密加工,还可采用数控铣床进行精确控制。
2.车削加工:车削是通过旋转车刀将工件宽度修整到设计尺寸的加工方法。
不锈钢的硬度高,具有很高的切削难度。
为了保证加工质量,需要选用刀具的刀片材料具有良好的切削性能,经常更换刀片,并且适当选择进给速度和切削速度。
3.钻削加工:钻削是通过旋转刀具在工件上切削孔洞的加工方法。
在不锈钢的钻削中,由于工件硬度高,钻头容易损坏。
因此,应选择硬质合金钻头,采用较低的切削转速,并进行冷却润滑剂的切削润滑。
4.磨削加工:磨削是通过磨料颗粒对工件进行磨削的一种加工方法。
不锈钢硬度高,适合采用砂轮进行磨削。
在磨削过程中,应选用适当的磨具和磨削磨粒,并保证切削液的良好冷却和润滑。
5.锻造加工:锻造是通过对不锈钢材料施加压力,使其发生塑性变形并改变形状的一种加工方法。
不锈钢具有较好的锻造性能,适合进行锻造加工。
通过锻造可以获得高强度和良好的耐腐蚀性能的零件。
6.激光切割:激光切割是通过高能激光束对不锈钢表面进行烧蚀,达到切割的目的。
激光切割具有高精度、高速度的特点,可用于制造复杂形状的零件。
7.电火花加工:电火花加工是通过电脉冲在工件表面产生高能量火花,使工件表面产生微小的氧化腐蚀,从而实现对不锈钢进行精细加工和切割的一种方法。
以上是常见的不锈钢机械加工方法,每种方法都具有适用的情况和要求。
在实际应用中,需要根据具体的加工需求和工件材料特性进行选择,以获得最佳的加工效果。
浅谈细长轴类工件的磨削加工
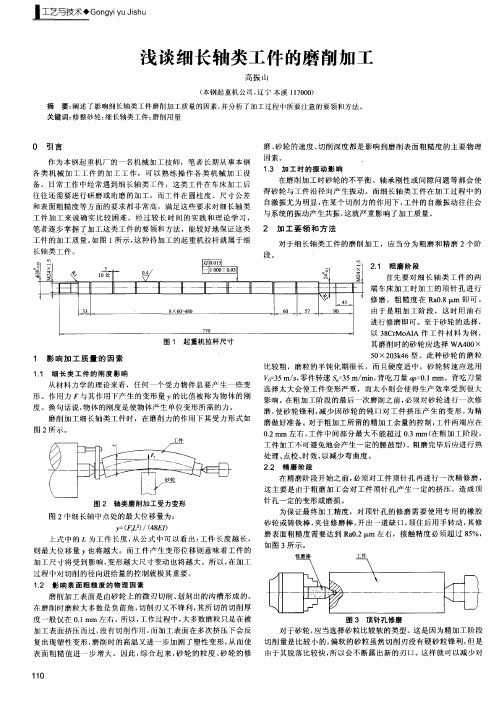
2. 精 磨 阶 段 2
往 往 还需 要进 行 研 磨或 珩 磨 的加工 ,而 工 件在 圆柱 度 、尺 寸 公 差 和 表 面粗 糙度 等 方 面 的要 求都 非常 高 ,满 足这 些要 求 对 细长 轴 类
磨、 砂轮 的速度 、 切削 深度 都 是影 响 到磨 削 表面 粗 糙度 的主要 物 理
因素 。
13 加 工 时 的 振 动 影 响 .
l圣
Ggyi 。yu h niJu s
浅谈 细长轴类工件 的磨 削加工
高振 山
( 本钢起 重机公司 , 宁 本溪 17 0 ) 辽 10 0
摘
要: 阐述 了影响细长轴类 工件磨削加工质量的 因素 , 并分析 了加 工过程中所要注意的要领和方法 。
关键词 : 整砂轮 ; 修 细长轴类工件; 磨削用量
从材 料 力学 的理 论 来看 ,任 何 一个 受 力物 件 总要 产 生一 些 变 形 。作 用 力 F与其 作 用下 产 生 的变 形量 Y的 比值被 称 为 物体 的刚
选 择太 大 会使 工 件变 形严 重 ,而 太 小则 会 使得 生产 效 率 受 到很 大
影 响 。 粗加 工 阶段 的最 后一 次磨 削之 前 , 在 必须 对砂 轮 进行 一 次修
在精 磨 阶段 开始 之 前 , 必须 对 工件 顶 针孔 再进 行 一 次精 修 磨 ,
这主 要 是 由于粗 磨 加工 会对 工 件 顶针 孔产 生 一 定 的挤 压 ,造成 顶
提高不锈钢细长轴(管)磨削加工质量的方法
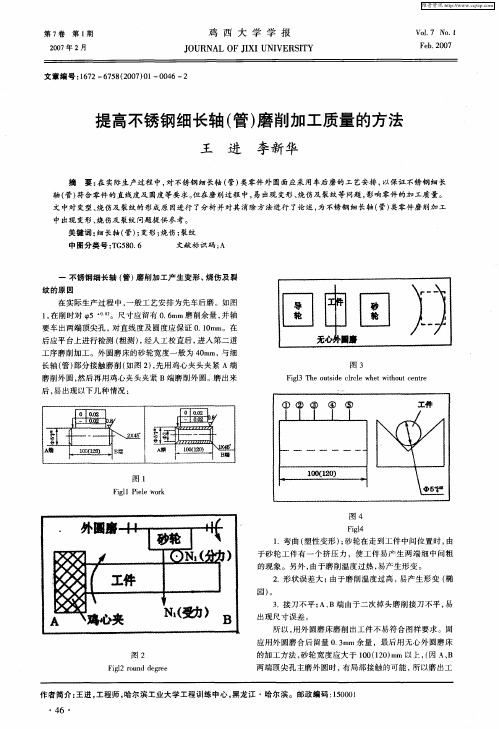
1 在削时对 q 02 , o - 5+0 0尺寸应 留有 0 6 m磨削余量 , .m 并轴
要 车 出两 端 顶 尖 孔 , 对直 线 度 及 圆 度应 保 证 0 1 m 。 在 .O m 后应 平 台上 进 行检 测 ( 测 ) 经 人 工校 直后 , 入第 二道 粗 , 进 工序 磨 削 加 工 。外 圆磨 床 的 砂 轮 宽 度一 般 为 4 m 与 细 0 m,
的加 工 方 法 , 轮 宽 度 应 大 于 10 10 ml以上 ,因 A、 砂 0 (2 ) i l ( B 两 端 顶 尖 孔 主磨 外 圆 时 , 局部 接 触 的可 能 , 以磨 出工 有 所
作者简介 : 进 , 王 工程 哈 尔 滨工 业 大 学 工 程训 练 中 心 , 币, 黑龙 江 ・哈尔 滨 。 邮 政 编码 :5 0 1 10 0
长轴 ( 部分接触磨削 ( 管) 如图 2 , )先用鸡心夹头夹紧 A端 磨削外 圆, 然后再用鸡 心夹 头夹紧 B端磨削外 圆。磨出来
后 , 出现 以下 几 种 情 况 : 易
图 3
Fil g3 Theousd ice wh twih u e r tie cr l e t o tc nte
图 1
Fg l Pil r il ee wok
图4
Fil g4
1 曲 ( 性 变 形 ) 砂 轮 在 走 到 工 件 中 间位 置 时 , .弯 塑 ; 由
于砂轮工 件有 一个挤压力 ,使工件易产 生两端细中间粗 的现象。另外 , 由于磨削温度过热 , 易产 生形 变。
2 状误差大 ; .形 由于 磨 削 温 度过 高 , 产 生形 变 ( 易 椭
维普资讯
第7 卷 第 1 期
20 0 7年 2月
磨削加工中的磨削精度

磨削加工中的磨削精度是指在磨削过程中所能达到的精度程度。
磨削加工是一种高精度的加工方法,可以制造出高精度零件,能够满足不同的制造需求。
磨削加工由于其高精度,广泛应用于航空、汽车、机床、电子、仪器仪表等领域,并成为制造业中不可或缺的工艺。
我国在磨削技术方面有着悠久的历史,早在汉代就已经出现了磨轮,磨削技术的发展可以追溯到数千年前。
随着工业的迅速发展,磨削技术也不断地得到提高、完善。
从最初的手工磨削,到机械化磨削,再到电脑化磨削,每一步的发展都提高了磨削加工的精度。
在实际的磨削加工中,要提高磨削精度,需要从多个方面入手。
首先,选择合适的磨削机床非常重要,不同类型的机床适用于不同的磨削任务。
其次,磨削工具的选择也是决定磨削精度的一个重要因素。
以磨削刃磨为例,磨削刃磨是指在磨削过程中利用磨削工具对刃口进行磨削,这要求磨削工具具有高精度、高效率、高耐磨性等特点。
此外,还需要注意磨削工具的材质选择,不同的材质对磨削效果会有很大的影响。
除了选择合适的磨削机床和磨削工具,磨削精度还与磨削的过程参数密切相关。
磨削的过程参数包括切削速度、进给速度、磨削深度、磨削力、冷却液等方面,这些参数的优化能够显著影响磨削加工质量。
例如在切削速度选择方面,通常情况下磨削速度越高,磨削效率越高,但是同时也会增加磨削热量,导致磨削过程变形和表面质量下降,因此需要根据实际情况,选择适当的切削速度。
此外,正确调整磨削加工中的磨削参数也是提高磨削精度的关键。
在实际工作中,可以采用计算机模拟的方法对磨削过程进行模拟和优化,这可以帮助工程师更好地了解磨削过程中的物理和化学机制,同时可以帮助工程师查找和解决磨削中可能遇到的问题。
总之,对零部件的质量和性能有着重要的影响,提高磨削精度是制造高精度零部件和产品的关键。
在磨削加工中要选择适当的机床和磨削工具,同时优化磨削过程参数和磨削参数的调整,这些都可以帮助工程师提高磨削精度,生产出更好质量的产品,使制造业在市场中更具竞争力。
细长轴磨削技巧

细长轴磨削技巧细长轴磨削技巧包括以下几点:1. 改进工件的装夹方法:粗加工时,由于切削余量大,工件受的切削力也大,一般采用卡顶法,尾座顶尖采用弹性顶尖,可以使工件在轴向自由伸长。
精车时,采用双顶尖法(此时尾座应采用弹性顶尖)有利于提高精度。
2. 采用跟刀架:跟刀架是车削细长轴极其重要的附件。
采用跟刀架能抵消加工时径向切削分力的影响,从而减少切削振动和工件变形,但必须注意仔细调整,使跟刀架的中心与机床顶尖中心保持一致。
3. 采用反向进给:车削细长轴时,常使车刀向尾座方向作进给运动(此时应安装卡拉工具),这样刀具施加于工件上的进给力方向朝向尾座,因而有使工件产生轴向伸长的趋势,而卡拉工具大大减少了由于工件伸长造成的弯曲变形。
4. 采用车削细长轴的车刀:车削细长轴的车刀一般前角和主偏角较大,以使切削轻快,减小径向振动和弯曲变形。
粗加工用车刀在前刀面上开有断屑槽,使断屑容易。
精车用刀常有一定的负刃倾角,使切削流向待加工面。
5. 使用中心架支承细长轴:中心架直接支承在工件中间,当工件可以分段车削时,在毛坯中部车处一段支承中心架的沟槽,其表面粗糙度值小,同轴度公差小,保持与车床旋转中心同轴。
6. 使用跟刀架支承细长轴:两爪跟刀架,跟刀架跟随车刀移动,车刀给工件的切削抗力,使工件贴在跟刀架的两个支承爪上,减少变形。
7. 优化磨削参数:针对不同的材料和工件尺寸选择合适的磨削参数,如砂轮粒度、转速、磨削深度等。
8. 控制冷却液的使用:使用适量的冷却液可以减少热量产生和工件变形。
9. 遵循加工步骤:按照合理的加工步骤进行磨削,避免因重复定位或装夹导致误差。
10. 提高操作技能:操作员应具备熟练的操作技能和高度的责任心,避免因操作失误导致工件损伤或质量不合格。
以上是细长轴磨削的一些技巧和注意事项,供您参考。
如需了解更多信息,建议咨询专业技术人员或查阅专业书籍。
细长轴的加工工艺分析
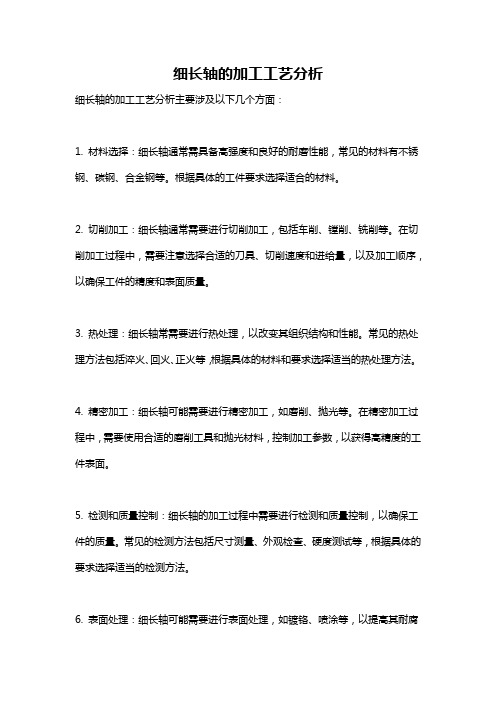
细长轴的加工工艺分析
细长轴的加工工艺分析主要涉及以下几个方面:
1. 材料选择:细长轴通常需具备高强度和良好的耐磨性能,常见的材料有不锈钢、碳钢、合金钢等。
根据具体的工件要求选择适合的材料。
2. 切削加工:细长轴通常需要进行切削加工,包括车削、镗削、铣削等。
在切削加工过程中,需要注意选择合适的刀具、切削速度和进给量,以及加工顺序,以确保工件的精度和表面质量。
3. 热处理:细长轴常需要进行热处理,以改变其组织结构和性能。
常见的热处理方法包括淬火、回火、正火等,根据具体的材料和要求选择适当的热处理方法。
4. 精密加工:细长轴可能需要进行精密加工,如磨削、抛光等。
在精密加工过程中,需要使用合适的磨削工具和抛光材料,控制加工参数,以获得高精度的工件表面。
5. 检测和质量控制:细长轴的加工过程中需要进行检测和质量控制,以确保工件的质量。
常见的检测方法包括尺寸测量、外观检查、硬度测试等,根据具体的要求选择适当的检测方法。
6. 表面处理:细长轴可能需要进行表面处理,如镀铬、喷涂等,以提高其耐腐
蚀性和装饰性。
在表面处理过程中,需要选择合适的表面处理方法和材料,控制加工参数,确保工件的表面质量。
总之,细长轴的加工工艺分析需要考虑材料选择、切削加工、热处理、精密加工、检测和质量控制,以及表面处理等方面的因素,以确保工件的加工质量和性能。
细长轴的加工方法

细长轴的加工方法细长轴的加工方法是指在机械加工过程中对于长度较长、直径相对较小的轴类工件所采取的一系列加工工艺和方法。
这类工件在许多领域中都有广泛的应用,比如汽车制造、航空航天、机械制造等。
细长轴的加工方法主要有以下几种:1. 切削加工:细长轴通常通过车床、铣床、钻床等机床进行切削加工。
在车床上,可以采用车削、车磨等方式进行加工,通过刀具不断地切削和磨削,逐步将粗加工的轴件加工成细长轴。
在铣床上,可以采用铣削、镗削等方式进行加工,通过刀具的旋转和移动,将工件表面的一定量材料切除,以达到加工精度和表面质量的要求。
2. 磨削加工:磨削是细长轴加工中常用的一种方法,通过磨削工具与工件表面的相对运动,将工件表面的一定量材料切除,以达到加工精度和表面质量的要求。
磨削加工分为外圆磨削和内圆磨削两种,分别适用于细长轴的外圆面和孔内面的加工。
常用的磨削加工方法有普通磨削、中心磨削、无心磨削和滚动磨削等。
3. 精密加工:细长轴的加工精度要求比较高,常常需要进行精密加工。
精密加工包括线切割、电火花加工、焊接等。
线切割是利用线切割机将工件切割成需要的形状,可以实现高精度的加工。
电火花加工是利用电火花放电烧蚀工件表面的加工方法,可以实现对轴件表面的高精度加工。
焊接是将两个或多个工件通过热源加热到熔融状态,使其熔合在一起的加工方法,通过焊接可以实现对细长轴的连接。
4. 其他加工方法:除了以上几种常规的加工方法外,还有一些特殊的加工方法可用于细长轴的加工。
比如深孔加工、滚压加工、冲压加工等。
深孔加工是通过刀具在细长轴上钻孔,可以实现对轴内腔的加工。
滚压加工是利用滚轮对工件表面施加压力,使其产生塑性变形,从而改善轴件的表面硬度和粗糙度。
冲压加工是将细长轴放置在冲压模具中,通过冲击力将轴件冲压成需要的形状。
细长轴的加工方法在实际应用中需要根据工件的具体要求和加工精度来选择,确保加工精度和表面质量的要求。
同时,在细长轴的加工过程中,还需要注意工艺参数的选择、刀具的使用和切削润滑的控制,以确保加工质量和工件的加工效率。
不锈钢细长轴磨削加工的工艺改进
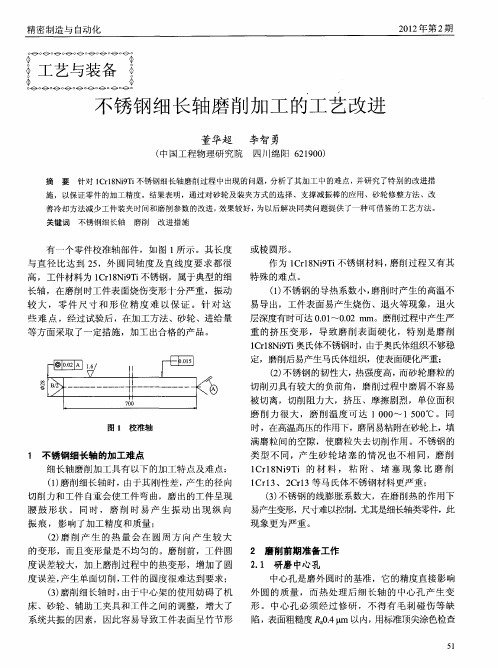
有 一个 零件 校准 轴部件 ,如 图 1 示 。其 长度 所 与 直 径 比达 到 2 ,外 圆 同轴度 及 直 线度 要 求 都 很 5
或棱 圆形 。
作为 1 r8 9 i C lNiT 不锈 钢材 料 , 削过程 又有 其 磨
特殊 的难 点 。 () 锈钢 的导热系 数小 , 削时产 生 的高温 不 1不 磨
工件 安装 时 的顶紧 力 。顶紧力 过 小时 ,工件 易产 生
轴 向窜动 ,过大 时易使 细长轴 产 生弯 曲变形 ,调 整
时应使 弹簧 项尖压 缩 1 为佳 。 ~2mm
图 2 加工示意图
2 3 采用双爪拨盘 .
采 用双 爪拨盘 和双 爪鸡 心夹 头 ,能使工 件在 旋 在 磨 削过程 中 的使用 方法 :支撑 棒 宽度 要 一 直 一 处在 工件 的磨 削部位 上 ,与砂轮 相对 ,当工 作 台作
易 导 出,工件 表面 易产 生烧 伤 、退火 等现 象 ,退火
层深度有 时可达 00 ~00 T。磨削过程 中产生严 .1 . ml 2 l
重 的挤 压 变 形 ,导 致 磨 削 表 面 硬 化 ,特 别 是 磨 削
1 r8 9 i 氏体不锈 钢时 ,由于奥 氏体组织不够稳 C lNiT 奥
床 、砂轮 、辅 助工夹 具 和工件 之 间 的调 整 ,增 大 了 系统 共振 的 因素 ,因此 容易 导致 工件表 面 呈竹节 形
陷 ,表面粗糙度 a.g 以 内, 0 m 4 用标准顶尖涂色检 查
51
精密 制造 与 自动化
接 触 面 大于 8 %,圆锥的圆度公差应在 00 2 0 . 以 0 mm 内,两端 中心 孔 同轴度 公差应 在 0 2 q 内,采 . 以 0 mn
细长轴的加工方法
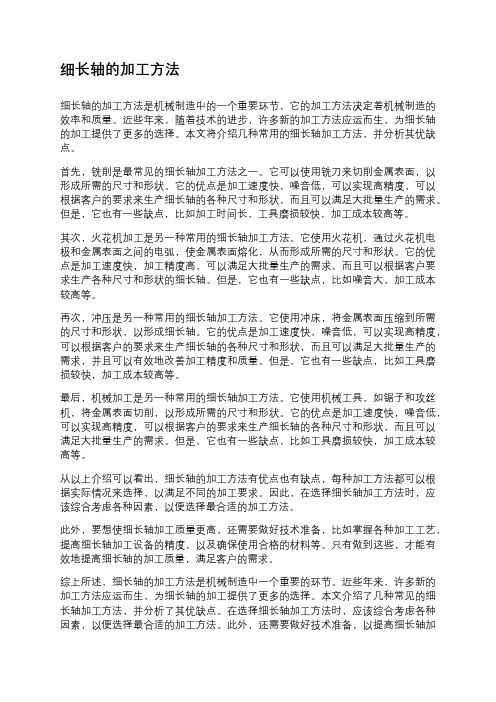
细长轴的加工方法细长轴的加工方法是机械制造中的一个重要环节,它的加工方法决定着机械制造的效率和质量。
近些年来,随着技术的进步,许多新的加工方法应运而生,为细长轴的加工提供了更多的选择。
本文将介绍几种常用的细长轴加工方法,并分析其优缺点。
首先,铣削是最常见的细长轴加工方法之一。
它可以使用铣刀来切削金属表面,以形成所需的尺寸和形状。
它的优点是加工速度快,噪音低,可以实现高精度,可以根据客户的要求来生产细长轴的各种尺寸和形状,而且可以满足大批量生产的需求。
但是,它也有一些缺点,比如加工时间长,工具磨损较快,加工成本较高等。
其次,火花机加工是另一种常用的细长轴加工方法。
它使用火花机,通过火花机电极和金属表面之间的电弧,使金属表面熔化,从而形成所需的尺寸和形状。
它的优点是加工速度快,加工精度高,可以满足大批量生产的需求,而且可以根据客户要求生产各种尺寸和形状的细长轴。
但是,它也有一些缺点,比如噪音大,加工成本较高等。
再次,冲压是另一种常用的细长轴加工方法。
它使用冲床,将金属表面压缩到所需的尺寸和形状,以形成细长轴。
它的优点是加工速度快,噪音低,可以实现高精度,可以根据客户的要求来生产细长轴的各种尺寸和形状,而且可以满足大批量生产的需求,并且可以有效地改善加工精度和质量。
但是,它也有一些缺点,比如工具磨损较快,加工成本较高等。
最后,机械加工是另一种常用的细长轴加工方法。
它使用机械工具,如锯子和攻丝机,将金属表面切削,以形成所需的尺寸和形状。
它的优点是加工速度快,噪音低,可以实现高精度,可以根据客户的要求来生产细长轴的各种尺寸和形状,而且可以满足大批量生产的需求。
但是,它也有一些缺点,比如工具磨损较快,加工成本较高等。
从以上介绍可以看出,细长轴的加工方法有优点也有缺点,每种加工方法都可以根据实际情况来选择,以满足不同的加工要求。
因此,在选择细长轴加工方法时,应该综合考虑各种因素,以便选择最合适的加工方法。
此外,要想使细长轴加工质量更高,还需要做好技术准备,比如掌握各种加工工艺,提高细长轴加工设备的精度,以及确保使用合格的材料等。
细长轴的加工方法

细长轴的加工方法细长轴是一种常见的机械零部件,广泛应用于各种机械设备中。
在机械加工过程中,对细长轴的加工要求较高,需要采用合适的加工方法和工艺,以确保加工质量和效率。
本文将介绍几种常见的细长轴加工方法,希望能对相关行业人士有所帮助。
首先,细长轴的车削加工是一种常见的加工方法。
在车床上进行细长轴的车削加工时,需要注意选择合适的刀具和切削参数,以保证加工表面的精度和光洁度。
此外,还需要合理设计夹具,以确保工件的稳定性和加工精度。
在车削加工过程中,操作人员需要严格按照工艺要求进行操作,确保加工质量。
其次,细长轴的磨削加工也是常用的加工方法之一。
磨削加工可以提高工件的精度和表面质量,适用于对细长轴的精密加工。
在磨削加工中,需要选择合适的砂轮和磨削液,控制磨削速度和进给量,以确保加工表面的精度和光洁度。
此外,还需要注意磨削过程中的冷却和润滑,以防止工件表面的热损伤和磨削热变形。
另外,电火花加工也是适用于细长轴加工的一种方法。
电火花加工可以实现对硬质材料的精密加工,适用于对细长轴的复杂轮廓和内腔加工。
在电火花加工中,需要根据工件材料和加工要求选择合适的电极和工艺参数,控制放电能量和加工速度,以确保加工精度和表面质量。
此外,还需要注意工作液的清洁和循环,以确保加工质量和稳定性。
最后,激光加工也是一种新型的细长轴加工方法。
激光加工可以实现对细长轴的高速、高精度加工,适用于对薄壁、薄膜和高硬度材料的加工。
在激光加工中,需要选择合适的激光源和光束参数,控制激光功率和加工速度,以确保加工精度和表面质量。
此外,还需要注意激光束的对准和稳定,以确保加工质量和稳定性。
综上所述,细长轴的加工方法有多种选择,每种方法都有其适用的工件和加工要求。
在实际生产中,需要根据具体情况选择合适的加工方法和工艺,以确保加工质量和效率。
希望本文对相关行业人士有所帮助,谢谢阅读。
不锈钢细长薄壁管轴的磨削加工

式中
, ——振动力 (0 N ; 1 ) m ——平衡质量 ( ) g;
高工件 的质量也起到极为重要的作用 。下面结合工作实 践,主要将在普通外 圆磨床上,不用 中心架磨 削不锈钢
细长薄壁管轴的一些特点作一介绍。
r ——不平衡量距 回转轴线的距离 ( t) i ; n o
— —
砂轮回转角速度 (a/ ) r s。 d
圜
. l 三
不 锈 钢 细 长 薄 壁 管 轴 的磨 削 加 工
秦 皇岛烟草机械有限责任公 司 ( 河北 06 0 ) 张立业 杨江涛 60 1
不锈钢材料具有较大的韧性 ,进行磨 削加工时砂轮 表面容易被磨屑嵌塞和粘 附,由于砂轮堵塞 ,使磨粒切
②进行超精磨时因加大 了顶尖与中心孑 的接 触面,提高 L
所选择的技术参数 。
技 术 参数 表
锐 性 好 、硬 度 稍 低 、组 织 疏 松 的 砂 轮 ,建 议 使 用
WA 6 5 4 K V。
( )金刚石笔 的调整 2
~
金 刚石笔 的顶角一般取 7 。 0
、\
内容
工步
\
粗磨
5 0
4 0
~
半精 磨
2 5
2 5~3 O
精磨
2 5
1 2 0~ 0
8。 0 ,在修整 过程 中,应 保证其 尖角锋 利 ,为此它 的
工件转i|( mn ) 壹 r・ i /
不锈钢的平面磨床磨削方法
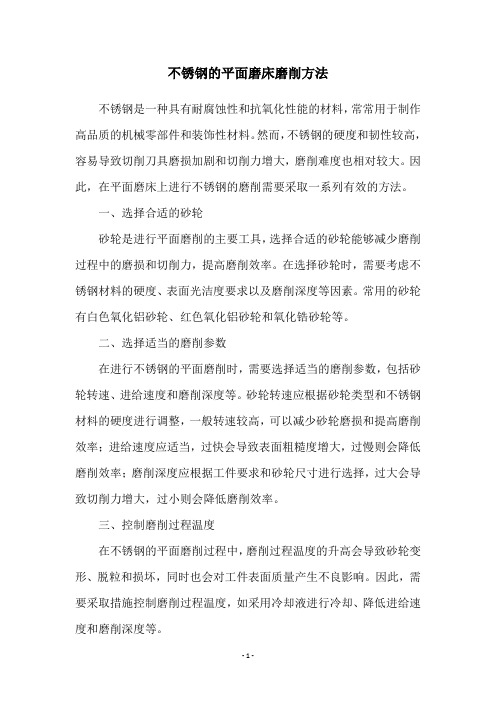
不锈钢的平面磨床磨削方法
不锈钢是一种具有耐腐蚀性和抗氧化性能的材料,常常用于制作高品质的机械零部件和装饰性材料。
然而,不锈钢的硬度和韧性较高,容易导致切削刀具磨损加剧和切削力增大,磨削难度也相对较大。
因此,在平面磨床上进行不锈钢的磨削需要采取一系列有效的方法。
一、选择合适的砂轮
砂轮是进行平面磨削的主要工具,选择合适的砂轮能够减少磨削过程中的磨损和切削力,提高磨削效率。
在选择砂轮时,需要考虑不锈钢材料的硬度、表面光洁度要求以及磨削深度等因素。
常用的砂轮有白色氧化铝砂轮、红色氧化铝砂轮和氧化锆砂轮等。
二、选择适当的磨削参数
在进行不锈钢的平面磨削时,需要选择适当的磨削参数,包括砂轮转速、进给速度和磨削深度等。
砂轮转速应根据砂轮类型和不锈钢材料的硬度进行调整,一般转速较高,可以减少砂轮磨损和提高磨削效率;进给速度应适当,过快会导致表面粗糙度增大,过慢则会降低磨削效率;磨削深度应根据工件要求和砂轮尺寸进行选择,过大会导致切削力增大,过小则会降低磨削效率。
三、控制磨削过程温度
在不锈钢的平面磨削过程中,磨削过程温度的升高会导致砂轮变形、脱粒和损坏,同时也会对工件表面质量产生不良影响。
因此,需要采取措施控制磨削过程温度,如采用冷却液进行冷却、降低进给速度和磨削深度等。
四、定期更换砂轮
砂轮的磨损程度会影响磨削效率和工件表面质量,因此需要定期更换砂轮,以保证磨削效率和磨削质量。
同时,在更换砂轮时也需要注意选择合适的砂轮规格和类型。
不锈钢的平面磨床磨削方法需要综合考虑多种因素,采取有效的措施进行控制和调整,方可达到理想的磨削效果和工件表面质量。
细长轴加工工艺

细长轴加工工艺一、工艺概述细长轴是指长度大于直径10倍的轴类零件,广泛应用于机械、航空、航天等领域。
其加工难度较大,需要经过多道工序才能完成。
本文将详细介绍细长轴的加工工艺。
二、材料准备1.选择合适的材料。
常用的材料有碳素钢、合金钢等。
2.对材料进行切割。
根据长度要求,将材料切割成相应长度。
三、车削加工1.粗车。
将材料放入车床上,进行粗车加工。
首先要确定好中心线,并进行装夹固定。
2.精车。
在粗车基础上,进行精车加工。
主要是为了提高表面平整度和精度。
3.修整端面。
在端面处进行修整,以保证端面平整度和垂直度。
四、磨削加工1.外圆磨削。
采用外圆磨床对轴身进行磨削,以提高尺寸精度和表面质量。
2.内孔磨削。
对于有内孔的轴类零件,在内孔处采用内圆磨床进行磨削。
3.端面磨削。
采用平面磨床对端面进行磨削,以保证平整度和垂直度。
五、齿轮加工1.车削齿轮。
将轴类零件放入数控车床上,进行齿轮车削加工。
2.滚齿。
在车削基础上,采用滚齿机进行滚齿加工,提高齿轮精度和耐磨性。
六、淬火处理1.淬火前准备。
在淬火前,需要对轴类零件进行清洗和预热处理。
2.淬火。
将轴类零件放入油池中进行淬火处理,提高硬度和耐磨性。
3.回火。
在淬火后,需要对零件进行回火处理,以提高强度和韧性。
七、表面处理1.抛光。
采用抛光机对表面进行抛光处理,提高表面质量。
2.镀层。
根据使用要求,在表面涂覆一层保护性涂料或金属镀层。
八、检验1.外观检验。
对于表面质量要求较高的细长轴,需进行外观检验,如裂纹、气泡等。
2.尺寸检验。
对轴类零件的尺寸进行检验,以保证精度和质量。
九、包装运输1.包装。
根据轴类零件的大小和重量,选择合适的包装材料进行包装。
2.运输。
选择合适的运输方式,将轴类零件送到客户手中。
以上就是细长轴加工的详细工艺流程,通过多道工序的加工处理,可以保证细长轴的精度和质量,达到客户要求。
轴类零件加工工艺的过程
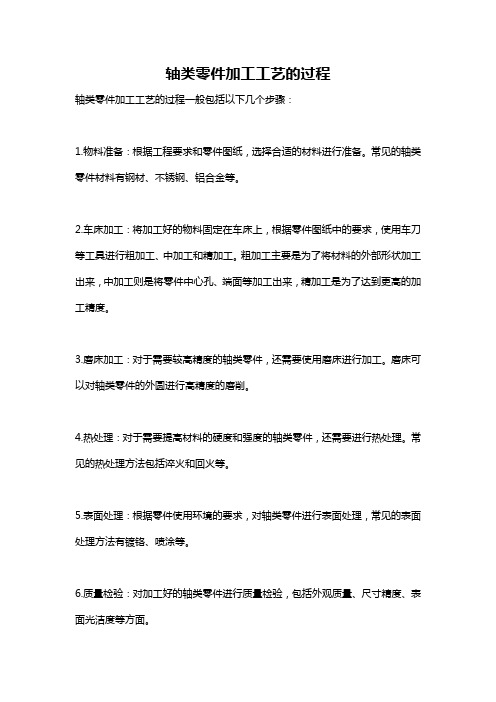
轴类零件加工工艺的过程
轴类零件加工工艺的过程一般包括以下几个步骤:
1.物料准备:根据工程要求和零件图纸,选择合适的材料进行准备。
常见的轴类零件材料有钢材、不锈钢、铝合金等。
2.车床加工:将加工好的物料固定在车床上,根据零件图纸中的要求,使用车刀等工具进行粗加工、中加工和精加工。
粗加工主要是为了将材料的外部形状加工出来,中加工则是将零件中心孔、端面等加工出来,精加工是为了达到更高的加工精度。
3.磨床加工:对于需要较高精度的轴类零件,还需要使用磨床进行加工。
磨床可以对轴类零件的外圆进行高精度的磨削。
4.热处理:对于需要提高材料的硬度和强度的轴类零件,还需要进行热处理。
常见的热处理方法包括淬火和回火等。
5.表面处理:根据零件使用环境的要求,对轴类零件进行表面处理,常见的表面处理方法有镀铬、喷涂等。
6.质量检验:对加工好的轴类零件进行质量检验,包括外观质量、尺寸精度、表面光洁度等方面。
7.包装出库:将通过质量检验的轴类零件进行包装,并进行出库准备,便于交付给客户或下一道工序使用。
以上是轴类零件加工工艺的基本过程,实际操作中还需要根据具体情况进行调整和改进。
同时,为了确保加工质量和效率,还需要合理选择和使用适当的加工设备和工具。
磨削加工的特点和应用范围
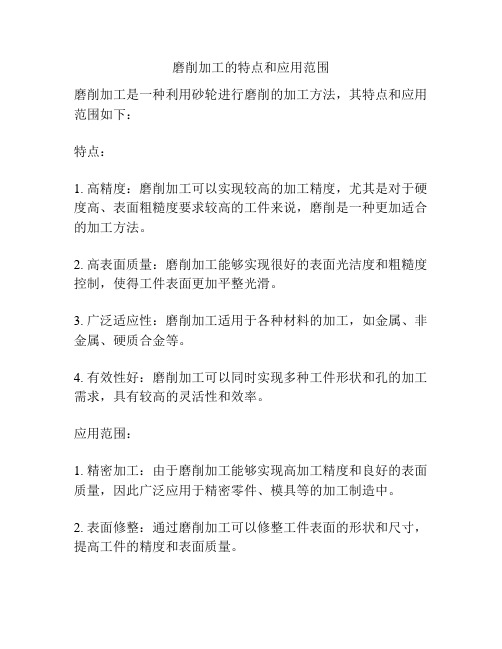
磨削加工的特点和应用范围
磨削加工是一种利用砂轮进行磨削的加工方法,其特点和应用范围如下:
特点:
1. 高精度:磨削加工可以实现较高的加工精度,尤其是对于硬度高、表面粗糙度要求较高的工件来说,磨削是一种更加适合的加工方法。
2. 高表面质量:磨削加工能够实现很好的表面光洁度和粗糙度控制,使得工件表面更加平整光滑。
3. 广泛适应性:磨削加工适用于各种材料的加工,如金属、非金属、硬质合金等。
4. 有效性好:磨削加工可以同时实现多种工件形状和孔的加工需求,具有较高的灵活性和效率。
应用范围:
1. 精密加工:由于磨削加工能够实现高加工精度和良好的表面质量,因此广泛应用于精密零件、模具等的加工制造中。
2. 表面修整:通过磨削加工可以修整工件表面的形状和尺寸,提高工件的精度和表面质量。
3. 刀具制造:磨削加工可以用于刀具的加工和修整,提高刀具的刃口质量和效率。
4. 零件修复:对于已经磨损或损坏的零件,可以通过磨削加工进行修复和修整,使其恢复到正常使用状态。
总之,磨削加工是一种高精度、高表面质量的加工方法,广泛应用于精密加工、表面修整、刀具制造和零件修复等领域。
细长轴的加工与设计

摘要
细长轴是机械加工中比较重要的部分,本文针对细长轴 的自身特点进行了研究。发现细长轴在机械加工中刚性差, 易变形,振动大等特点。并针对切削热引起的热变形伸长, 增加细长轴刚性,减小车削时的振动等方面介绍了车削加工 中预防细长轴变形的措施
Summary.
Slender shaft are machined in the more important part, this paper focuses on researching the
characteristics of slender shaftFound slender shaft in the rigid difference in mechanical processing, easy deformation, vibrations, and other
characteristics.Forcutting heat and thermal deformation caused by extension, increase the slender shaft stiffness, cutting vibration when car introduced in areas such as the reduction in turning of slender shaft deformation prevention measure
与顶尖的配合,车床尾座锥孔与麻花钻柄的配合。 1.转动小滑板法 转动小滑板法,是把刀架小滑板按工件的圆锥半角 a∕2 要求转 动一个相应的角度, 使车刀的运动轨迹与所要求加工的圆锥素线平行。 转动小滑板操作简便,调试范围广。 2.偏移尾座法 采用偏移尾座法车外圆锥面,必须工件装夹在两顶尖间,巴尾座上滑 板向里(是用在车正外圆锥面)或者向外(用于车外倒圆锥面)横向 移动一端距离 S 后,使工作回转轴线与车床主轴轴线相交一个角度, 并使其大小等于圆锥半角 a∕2。由于床鞍进给是沿平行于主轴轴线 移动的。当尾座横向移动一端距离 S 后,工件就成了一个圆锥体。 3.仿形法车外圆锥面 仿形法车外圆锥面是刀具按照仿形装置(靠模)进给对工件进行 加工的方法,在卧式车床上安装一套装置,该装置能使刀具作纵向进 给的同时,又作横向进给,从而使车刀的运动轨迹与与圆锥的素线平 行,加工出所需的圆锥面. 4. 宽刃刀车削法 宽刃刀车外圆锥面,实质上也属于成形法车削,即使用成行刀具 对工件进行加工。它是在车刀安装后,使主切削刃与主轴轴线夹角等 于工件的圆锥半角 a∕2,采用横向进给的方法加工出外圆锥面。 三、 成形面加工方案 1. 双手控制法
细长轴的加工方法
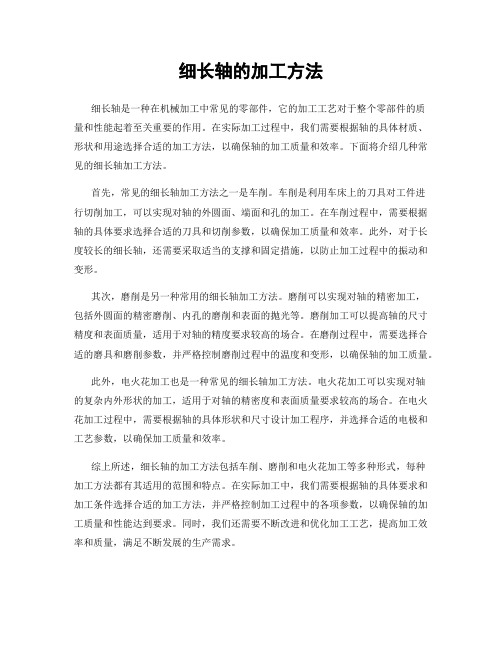
细长轴的加工方法细长轴是一种在机械加工中常见的零部件,它的加工工艺对于整个零部件的质量和性能起着至关重要的作用。
在实际加工过程中,我们需要根据轴的具体材质、形状和用途选择合适的加工方法,以确保轴的加工质量和效率。
下面将介绍几种常见的细长轴加工方法。
首先,常见的细长轴加工方法之一是车削。
车削是利用车床上的刀具对工件进行切削加工,可以实现对轴的外圆面、端面和孔的加工。
在车削过程中,需要根据轴的具体要求选择合适的刀具和切削参数,以确保加工质量和效率。
此外,对于长度较长的细长轴,还需要采取适当的支撑和固定措施,以防止加工过程中的振动和变形。
其次,磨削是另一种常用的细长轴加工方法。
磨削可以实现对轴的精密加工,包括外圆面的精密磨削、内孔的磨削和表面的抛光等。
磨削加工可以提高轴的尺寸精度和表面质量,适用于对轴的精度要求较高的场合。
在磨削过程中,需要选择合适的磨具和磨削参数,并严格控制磨削过程中的温度和变形,以确保轴的加工质量。
此外,电火花加工也是一种常见的细长轴加工方法。
电火花加工可以实现对轴的复杂内外形状的加工,适用于对轴的精密度和表面质量要求较高的场合。
在电火花加工过程中,需要根据轴的具体形状和尺寸设计加工程序,并选择合适的电极和工艺参数,以确保加工质量和效率。
综上所述,细长轴的加工方法包括车削、磨削和电火花加工等多种形式,每种加工方法都有其适用的范围和特点。
在实际加工中,我们需要根据轴的具体要求和加工条件选择合适的加工方法,并严格控制加工过程中的各项参数,以确保轴的加工质量和性能达到要求。
同时,我们还需要不断改进和优化加工工艺,提高加工效率和质量,满足不断发展的生产需求。
细长轴磨削加工工艺与技术分析

细长轴磨削加工工艺与技术分析作者:彭冬梅来源:《速读·上旬》2019年第07期在普通外圆磨床上超精磨削细长轴一直是老大难问题,特别是,当工件的长径比超过30(L/D>30)时,尤为困难。
美国中小型机械修造公司(厂)的长期实践表明,只要检修、调整好普通外圆磨床,合理地选择砂轮、磨削用量和工艺过程,就能满足细长轴的技术要求。
1磨削前的几项准备工作1.1校直细长轴校直方法有热校和冷校两种方法,热校比冷校理想。
校直后的彎曲度应控制在工件每1000mm长度,其弯曲度在0.15mm以内。
1.2中心孔中心孔是细长轴的基准、细长轴经过热处理后,中心孔将会产生变形,应对中心孔进行研磨,使其60°锥孔和圆度达到标准要求。
1.3检修机床保证检修后的外圆磨床各项精度达到出厂时指标。
1.4调整机床主要是调整头架与尾架间的中心距离。
将工件顶在两顶尖间,用手旋转工件。
感觉不松不紧为好,如果尾座顶尖是弹簧式的,可使弹簧顶尖压缩0.5~2mm,再顶住工件中心孔。
1.5检查工件两顶尖顶住工件,先用百分表对细长轴的全长作径向跳动检查,特别是对中间弯曲度最大的地方,观察其跳动量方向是否一致。
然后再用千分尺检查工件的磨削余量和各项尺寸。
细长轴的磨削余量取较小值为宜。
2砂轮及磨削用量的选择2.1砂轮的选择根据细长轴材料的不同,选择不同磨料、硬度、粒度的砂轮,这是很重要的。
磨细长轴的砂轮硬度应稍软,粒度应稍粗。
砂轮的形状中间呈凹形,因为中凹形砂轮不但可减少砂轮与工件的接触面积,而且砂轮整体宽度不变,可以减少细长轴在旋转中产生自激振动。
2.2切削用量的选择数控机床加工中的切削量,是表示机床主运动和进给运动大小的重要参数,主要包括切削深度、主轴转速和进给速度。
在加工程序的编制工作中,应把各种加工用量编入工序单内。
零件的加工方法不同,切削用量的选择也会有区别,粗加工时一般以提高生产效率为主,但也要考虑经济性和加工成本。
半精加工和精加工时,应在保证加工质量的前提下,兼顾切削效率、经济性和加工成本。
细长轴的磨削加工

关检测系统等。这些检测方法都存在其各 自的优 势,但同时也都存在着各 自的不足。 激光测试方法的优点在于车辆与检测系统之
间为非接触关系 ,设备可靠性高,受外界干扰小。 缺点是设备成本高,且空间位置布局 困难。尽管
激光发射 系统还 可以用光学 的分光系统所替代 ,
即在发射系统 中放置一定频率的点光源,经分光 后 ,形成符合要求的光束 ,但 由于光束的发散性 , 它们相互干涉 ,很难实现与接收装置的一一对应
的磨 削加 工 的 方 法和 技 巧 。
【 关键词】细 轴; 加 磨 ; 轮 长 磨削 工; 粒 砂
中图分类 号 :T 5 06 G 8 . 文献 标识 码 :C
我校的实习工厂有车床 4 台,因此细长轴和 2 丝杠在厂的磨削生产 中占有很大 比例。因为细长 轴的磨削加工是很典型的 ,见图 1 、图 2 。 磨削是细长轴生产的最后一道工 序,其加工
图2
・
15 20 4 ・ O8年 1 0月
农 业 与 技 术
要 选择合 适 的砂轮硬 度及粒 度 。若砂 轮太硬 、
砂轮修整时,必需在砂 轮右方进刀 ,这样可 以使
磨钝的砂粒不易脱掉 , 若继续磨削、磨削力会不
断增大 ,不仅使工件变形 ,而且还会产生磨削热、 烧伤加工表 面。因此使用太硬的砂轮时 ,要经常 修磨 ,这样影响工作效率;砂轮太软 ,则磨粒在 未变钝前 即已脱落,砂轮很快地变小 ,失去其原 有的形状,也需要经常修磨 ,同样影响工效。磨 削细长轴所用砂轮硬度宜采用 中等硬度即 “ Y Z” ( 棕刚玉) 。粒度应根据工件情况来确定 ,若工件 表面粗糙 度、尺寸精度要求高 ,则采用细磨粒的 砂轮。工件及砂轮尺寸愈大、则磨粒应 愈粗 ,一
- 1、下载文档前请自行甄别文档内容的完整性,平台不提供额外的编辑、内容补充、找答案等附加服务。
- 2、"仅部分预览"的文档,不可在线预览部分如存在完整性等问题,可反馈申请退款(可完整预览的文档不适用该条件!)。
- 3、如文档侵犯您的权益,请联系客服反馈,我们会尽快为您处理(人工客服工作时间:9:00-18:30)。
高精度、不锈钢、细长轴的磨削加工
作者:张新建, 朱文莅
作者单位:总公司第七研究所第七零九研究所
1.期刊论文金奎文.JIN Kui-wen高精度不锈钢尖角方矩形管的生产技术-焊管
2008,31(4)
根椐直缝方矩形焊管的变形规律、特点及影响质量的主要因素提出了高精度不锈钢尖角方矩形管的变形机制,形成了一整套的方矩形尖角管的工艺设计方法,提出了计算公式.该方法利用管坯的塑性变形填充方矩形管角部形成尖角,共使用两架土耳其头,各土耳其头轧辊之间相互定位,相互制约,以提高方矩形管的精度和生产过程的稳定性.在钢管纵向,利用定径机组的圆形管坯直接推进两架被动的土耳其头而形成尖角管.第一道土耳其头的主要作用是轧制出角(压角),第二道土耳其头的主要作用是轧制出平面(压面),这种方法较大地提高了方矩形管的尺寸精度,改善了方矩形管的角部形状,使用普通焊管机组能生产出高精度的方矩形管,用于装饰结构工程、体育器材、厨房装修等高品质工程.
2.学位论文付君彪不锈钢自动化酸洗线的设计及应用2006
不锈钢在化工、石化、航空航天、能源、轻纺等部门有着广泛的应用,近年来,随着经济的不断发展,不锈钢的消费领域不断拓展,特别是在建筑装饰、餐饮、食品等行业得到广泛的应用。
不锈钢因其具有良好的耐腐蚀性能、可加工性、外形美观等特点,在社会发展和人们生活消费领域发挥着越来越重要的作用。
该论文针对大连金牛股份有限公司的高精度高合金棒线材连轧机在生产不锈钢时酸洗时出现的问题,如:污染大、生产效率低、酸洗表面质量差等,通过调研了解企业中酸洗方面所存在的问题和缺陷,以及对国内外的酸洗情况的分析,做了以下几方面的研究,并提出了几点改进的意见。
首先对国内外的酸洗情况进行了调查,对酸洗方面的有关问题加以说明,包括:不同情况下所产生氧化皮的性质、酸洗原理、各种酸洗溶液的配制和选择、酸洗过程以及影响酸洗速度的因素等有关问题。
再结合大连金牛股份有限公司的实际情况,提出了针对不锈钢的自动化酸洗生产线方案,并且针对该厂存在的问题,进行试验及效益分析,提出改进意见。
其次,为了提高不锈钢盘条的酸洗质量和生产效率,公司提出了建设国际先进的自动化酸洗生产线的建设项目。
通过对国际上先进的自动化酸洗生产线的调研,结合大连金牛公司的搬迁改造整体方案,提出了新的生产线整体设计方案。
方案的主要内容包括具体的酸洗流程、自动化控制系统、自动化分析系统、以及一套完备的废水处理系统。
该自动化酸洗生产线方案经过不断的改进和试运行已经通过了初步审核,并在实际生产中显现出良好的效果。
通过对高精度高合金棒线材连轧机生产线的生活核算,体现出自动化酸洗生产线方案的很多优点:提高生产效率和人力资源的利用,同时节省了企业的成本。
而且该方案对改善工作环境、提高工人的自身安全及环境保护也有重要的作用。
3.期刊论文张斌.ZHANG Bin浅谈用直径较小刀具加工一不锈钢零件的加工工艺
-电子机械工程2006,22(6)
针对有高精度要求的不锈钢零件,通过实例,运用改进加工工艺的方法和使用一定的编程技巧,来保证其高精度的要求.为今后用直径较小的刀具加工此类材料的零件提供参考.
4.期刊论文郭小玲.陈怀奇.任红军.Guo Xiaoling.CHEN Huaiqi.Ren Hongjun高
精度内凸台加工工艺和测量技术-制造技术与机床2005,""(6)
介绍一种不锈钢高精度内凸台的加工和测量方法.通过精心规划和巧妙构思,设计出数套专用刀具和量具,切实解决了某零件批量生产时的加工和测量问题.
5.学位论文吴丹宇不锈钢管道内壁的磁性磨料研磨的实验及机理研究1996
该文所研究是是磁性磨料磁力研磨技术,该方法是一种高精度、高表面质量的精加工方法,具有能够加工复杂外形工件和各种内壁内腔表面的优势,同时易于控制,工作环境清洁,设备简单.
6.期刊论文郭小玲.陈怀奇.任红军高精度内凸台的加工和测量-机械制造
2004,42(11)
介绍一种不锈钢高精度内凸台零件的加工和测量方法.通过精心规划和巧妙构思,设计出数套专用刀具和量具,解决了零件批产时的加工和测量问题.
7.会议论文张海鸥.王桂兰熔射快速制作高精度不锈钢和碳化钨合金注塑模具
1998
熔射以快速。
使用材料自由度高等特点受到高度关注。
然而,由快速原型或天然素材原型熔射制模受到原型耐热性和熔射金属的限制,目前尚限于制作低熔点合金模具。
该研究采用复合材料制作耐热型被熔射原型,创制出不锈钢和碳化钨合金模具熔射表层,大幅度提高了模具的耐久性,使熔射快速制作大批量生产用注塑模具成为可能。
8.期刊论文刘晓岩.张洪超.Liu Xiao-yan.Zhang Hong-chao高精度轮对组装工
艺的开发及夹具的设计-机车车辆工艺2010,""(3)
针对出口到澳大利亚双层不锈钢车,由于两国铁路轨距不同,造成运输困难.为了节省成本,采用了不折轮对的运输方式,为此需要提高轮对的组装精度.文中介绍了高精度轮对组装工艺及夹具的设计.
9.会议论文程效军.周德意.鲍峰工业自动化生产线轴线检测及精度分析2002
工业自动化生产线上的感应滚筒是进行产品厚度快速自动检测的重要设备,特别是对于不锈钢冷轧生产线尤其重要,它直接决定着不锈钢板的加工精度,从而影响产品的质量.对于冷轧前后的两个感应滚筒厂方要求其轴线垂直于轧机纵轴线的偏差小于0.08mm,采用常规的测量仪器运用特殊的精密工程测量手段成功地实现以轴线检测与调整,经过对产品检验达到了厂房提出的精度要求.
10.期刊论文吴凤照.夏琴香.张学惠高强超高精度7A04超硬铝合金导轨型材的研
制-轻合金加工技术2001,29(9)
概述了高档电子机柜用超高精度高强7A04超硬铝合金导轨型材的研制过程,并对导轨的材质、结构、成形方案、挤压模具以及挤压、拉矫工艺的选择进行了深入探讨.结果表明,与机加不锈钢导轨相比,此新型导轨重量轻、加工成本低、装配性能优良、载荷能力也毫不逊色,完全可取代机加不锈钢导轨,实现以铝代钢、以压加取代机加不锈钢导轨的预定目标.
本文链接:/Conference_102014.aspx
授权使用:湖南大学(hunandx),授权号:5519bb4e-1710-4630-8726-
9df400b140dc
下载时间:2010年9月17日。