先进线锯切割技术
先进线锯切割技术PPT课件

本文简要介绍线锯切割工艺及生产过程中面临的各种挑战,并且展示了能同时降 低硅锭切方与硅片切割成本的下一代线锯切割技术。
3
锯的历史
第一台可实际使用的光伏硅片切割机是以瑞士 HCT 成型系统公司(HCT Shaping Systems)的 创始人Charles Hauser 博士的开创性研究为基础 研制而成,于上个世纪八十年代投入使用。(如今 是应用材料公司的精密硅片切割系统部门。) 这类 设备使用携带研磨浆料的切割线,通过切割线运 动来切割硅片。即使到现在为止,大多数用来将 硅锭开方和切片的线锯仍然保留了与Hauser 博士 的原型机器相同的基本结构,但是载荷与切割速 度都得到了大幅提升。
4
线锯切割工艺
现代线锯的核心部分是缠绕在导轮上、直径为 110µm-140µm的单根切割钢线。这种导轮开槽精细 且槽距均匀,形成平行切割线的水平网状结构或网 (图3)。强大的驱动力使整张网在相对高速(每 秒10米到20米)下运行。浆料,一种由耐磨粒子加 冷却液制成的悬浮液,通过喷嘴输送到运动中的切 割线上。切割线将浆料传送到切割区。将要切割的 硅锭被固定在切割台上并且与切割头逆向垂直运动。 这一动作将硅锭推过切割线网,同时产生大量的硅 块或硅片。在使用浆料的多线锯切割系统中,切割 运动基本上是一种快速的三体磨损过程,其特点在 于使用了一种基于滚动及
12
应用
目前原材料费用占晶体硅太阳能电池总体成本相当大的一部 分,因此线锯技术对于降低每瓦成本并让太阳能光伏价格与 传统电力能源持平来说至关重要。线锯切割技术取得的三大 进步已经大幅减少了产生太阳能电力所要消耗的硅材料(每 瓦所需的硅材料克数)。 首先,实现切割更薄硅片的能力。历史趋势显示,每5年硅 片厚度就会减少50微米。从1995年至今,硅片厚度已经从 330µm 降低到了180µm。而这一趋势已经不可能再持续这一 速度:随着厚度的降低,硅片会变得越来越脆弱,这需要能 够在最小压力下处理超薄硅片的先进自动化技术 。这在将 硅片从切割后的堆叠结构中取出(这一过程也被称为“分 检”)以及在太阳能电池生产线加工时都是如此。同时,也 需要提高切割工艺来减少硅片的厚度变化并使其与厚度成比 例。
线锯工作原理
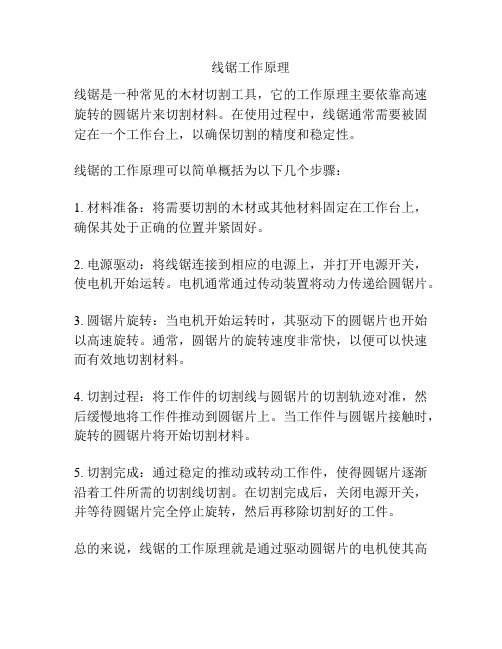
线锯工作原理
线锯是一种常见的木材切割工具,它的工作原理主要依靠高速旋转的圆锯片来切割材料。
在使用过程中,线锯通常需要被固定在一个工作台上,以确保切割的精度和稳定性。
线锯的工作原理可以简单概括为以下几个步骤:
1. 材料准备:将需要切割的木材或其他材料固定在工作台上,确保其处于正确的位置并紧固好。
2. 电源驱动:将线锯连接到相应的电源上,并打开电源开关,使电机开始运转。
电机通常通过传动装置将动力传递给圆锯片。
3. 圆锯片旋转:当电机开始运转时,其驱动下的圆锯片也开始以高速旋转。
通常,圆锯片的旋转速度非常快,以便可以快速而有效地切割材料。
4. 切割过程:将工作件的切割线与圆锯片的切割轨迹对准,然后缓慢地将工作件推动到圆锯片上。
当工作件与圆锯片接触时,旋转的圆锯片将开始切割材料。
5. 切割完成:通过稳定的推动或转动工作件,使得圆锯片逐渐沿着工件所需的切割线切割。
在切割完成后,关闭电源开关,并等待圆锯片完全停止旋转,然后再移除切割好的工件。
总的来说,线锯的工作原理就是通过驱动圆锯片的电机使其高
速旋转,从而实现对材料的切割。
通过合理的操作和保养,线锯可以有效地进行木材或其他材料的切割工作。
金刚石线锯切割加工实验报告
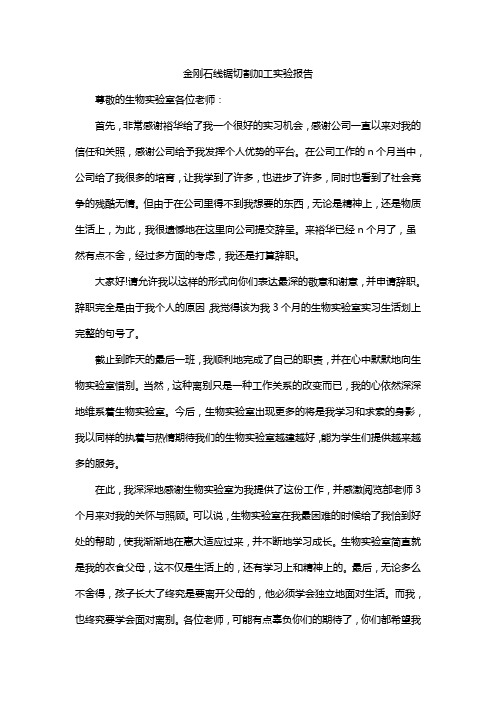
金刚石线锯切割加工实验报告尊敬的生物实验室各位老师:首先,非常感谢裕华给了我一个很好的实习机会,感谢公司一直以来对我的信任和关照,感谢公司给予我发挥个人优势的平台。
在公司工作的n个月当中,公司给了我很多的培育,让我学到了许多,也进步了许多,同时也看到了社会竞争的残酷无情。
但由于在公司里得不到我想要的东西,无论是精神上,还是物质生活上,为此,我很遗憾地在这里向公司提交辞呈。
来裕华已经n个月了,虽然有点不舍,经过多方面的考虑,我还是打算辞职。
大家好!请允许我以这样的形式向你们表达最深的敬意和谢意,并申请辞职。
辞职完全是由于我个人的原因,我觉得该为我3个月的生物实验室实习生活划上完整的句号了。
截止到昨天的最后一班,我顺利地完成了自己的职责,并在心中默默地向生物实验室惜别。
当然,这种离别只是一种工作关系的改变而已,我的心依然深深地维系着生物实验室。
今后,生物实验室出现更多的将是我学习和求索的身影,我以同样的执着与热情期待我们的生物实验室越建越好,能为学生们提供越来越多的服务。
在此,我深深地感谢生物实验室为我提供了这份工作,并感激阅览部老师3个月来对我的关怀与照顾。
可以说,生物实验室在我最困难的时候给了我恰到好处的帮助,使我渐渐地在惠大适应过来,并不断地学习成长。
生物实验室简直就是我的衣食父母,这不仅是生活上的,还有学习上和精神上的。
最后,无论多么不舍得,孩子长大了终究是要离开父母的,他必须学会独立地面对生活。
而我,也终究要学会面对离别。
各位老师,可能有点辜负你们的期待了,你们都希望我能做完这个学期,但我却在此时退出,为此我深感歉意。
实因一张张新的面孔的出现,一张张熟悉的面孔离开,生物实验室实习工作已经顺利地实现了级际替换,我也应该把机会留给更需要的人。
如果因为我的离开而给各位老师带来什么不便的话,也只好敬请各位老师的原谅,我只能抱歉地说一声“老师辛苦了!”,我会在心中一直感谢你们的,感谢你们在我的人生旅途中,送给了我那么多。
线锯的使用方法
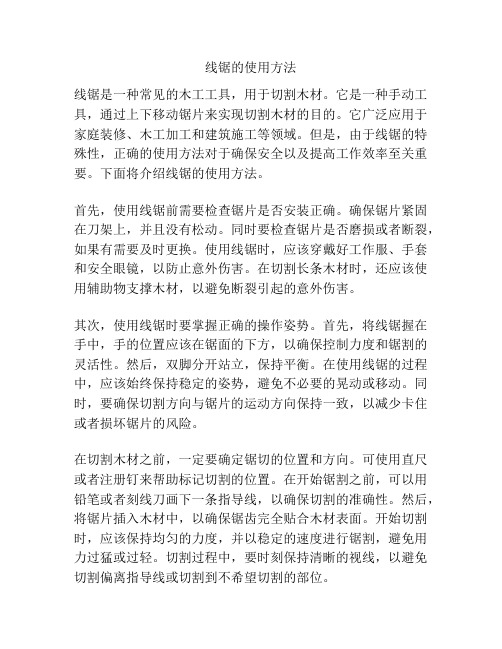
线锯的使用方法线锯是一种常见的木工工具,用于切割木材。
它是一种手动工具,通过上下移动锯片来实现切割木材的目的。
它广泛应用于家庭装修、木工加工和建筑施工等领域。
但是,由于线锯的特殊性,正确的使用方法对于确保安全以及提高工作效率至关重要。
下面将介绍线锯的使用方法。
首先,使用线锯前需要检查锯片是否安装正确。
确保锯片紧固在刀架上,并且没有松动。
同时要检查锯片是否磨损或者断裂,如果有需要及时更换。
使用线锯时,应该穿戴好工作服、手套和安全眼镜,以防止意外伤害。
在切割长条木材时,还应该使用辅助物支撑木材,以避免断裂引起的意外伤害。
其次,使用线锯时要掌握正确的操作姿势。
首先,将线锯握在手中,手的位置应该在锯面的下方,以确保控制力度和锯割的灵活性。
然后,双脚分开站立,保持平衡。
在使用线锯的过程中,应该始终保持稳定的姿势,避免不必要的晃动或移动。
同时,要确保切割方向与锯片的运动方向保持一致,以减少卡住或者损坏锯片的风险。
在切割木材之前,一定要确定锯切的位置和方向。
可使用直尺或者注册钉来帮助标记切割的位置。
在开始锯割之前,可以用铅笔或者刻线刀画下一条指导线,以确保切割的准确性。
然后,将锯片插入木材中,以确保锯齿完全贴合木材表面。
开始切割时,应该保持均匀的力度,并以稳定的速度进行锯割,避免用力过猛或过轻。
切割过程中,要时刻保持清晰的视线,以避免切割偏离指导线或切割到不希望切割的部位。
另外,在使用线锯时,还需要注意一些维护保养的问题。
首先,使用完线锯后应该及时清理锯末和灰尘,以保持锯刃的锐利度和工作效率。
清理时可以使用刷子或者压缩空气去除锯末。
其次,线锯不宜长时间连续使用,需要适当停歇,以减少锯片的磨损,并防止锯机过热。
如果发现锯片磨损或者松动,应该及时更换或者调整。
此外,线锯需要储存在干燥通风的地方,远离潮湿和腐蚀性物质,以延长线锯的使用寿命。
综上所述,线锯是一种常见的木工工具,使用方法的正确与否直接关系到工作效率和工作安全。
金刚石线切割技术简析

金刚石线切割技术简析技术简介以生产工艺划分,金刚石线可以分为电镀金刚石线和树脂金刚石线。
金刚石切割线是通过一定的方法,将金刚石镀覆在钢线上制成,通过金刚石切割机,金刚石切割线可以与物件间形成相对的磨削运动,从而实现切割的目的。
金刚石线是用复合电镀的方法将高硬,高耐磨性的金刚石微粉固结在钢丝基体上,而制成固结磨料金刚石锯线。
在切割过程中90%的抗拉强度来自钢丝线,因此钢丝线对金刚石线至关重要。
在自由磨料线锯切割过程中,研磨液由喷嘴直接喷到钢丝线与硅晶体上,由线网的钢丝线带动游离磨料对硅晶体进行切割。
与游离磨料不同,金刚石线将金刚石微分固结到钢丝线上,钢丝线往复移动对硅晶体进行切割。
图:金刚石线构成轴剖面图技术优势传统砂浆的利用钢丝的快速运动将含磨料的液体带入到工件切缝中,产生切削作用。
在切割过程中,碳化硅被冲刷下来,唯有持续进行滚动磨削,而减少切割效率。
碳化硅的硬度9.5(莫氏),而金刚石硬度在10(莫氏)。
金钢线切割线速度基本在15m/s,正常切割的砂浆线速度基本在9-11.5m/s。
而若金钢线再做突破的话,就应该是要更硬,同时兼有更好的自锐性(多晶金刚石),更稳定的固结方式,更快的线速度。
金刚石切割线相比传统工艺有三大优势:1)金刚石线切割漏损少,寿命长,切割速度快,切割效率高,提升产能;2)品质受控,单片成本低,金刚石线切割造成的损伤层小于砂浆线切割,有利于切割更薄的硅片;3)环保,金刚石线使用水基磨削液(主要是水),有利于改善作业环境,同时简化洗净等后道加工程序。
添加剂原理随着金刚石线切割技术的发展及单多晶竞争的日益激烈,多晶硅片将全部由砂浆线切割转变为金刚石线切割。
不过由于金刚石线切割多晶硅片的损伤层浅、线痕明显等问题,常规砂浆线的酸制绒难以在其表面刻蚀出有效的减反射绒面。
目前,针对金刚石线多晶硅片制绒的难题,主要解决办法包括:金刚石线直接添加剂法、干法黑硅(RIE)及湿法黑硅(MCCE)等,由于RIE和MCCE成本及工艺等原因,目前大多数企业以金刚石线直接添加剂法制备金刚石线切割多晶硅片的减反射绒面,当然由于添加剂法制备的电池转换效率低等因素,决定其只是金刚石线切割多晶硅片全面推广的一个过渡阶段。
金刚石绳锯切割工艺介绍
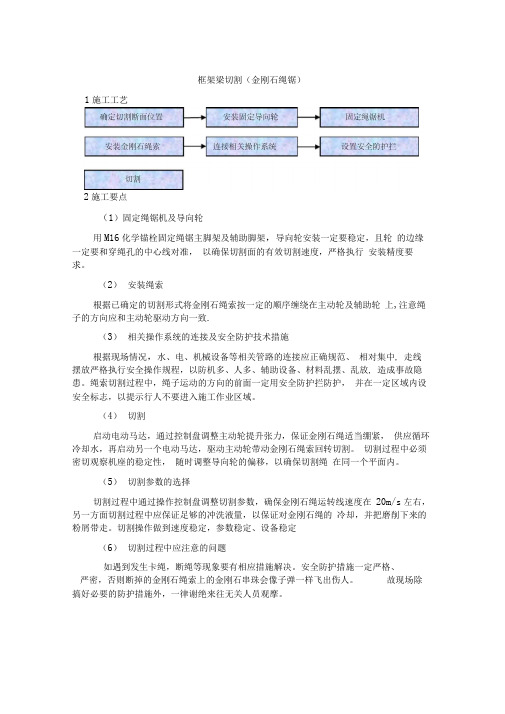
框架梁切割(金刚石绳锯)1施工工艺2施工要点(1)固定绳锯机及导向轮用M16化学锚栓固定绳锯主脚架及辅助脚架,导向轮安装一定要稳定,且轮的边缘一定要和穿绳孔的中心线对准,以确保切割面的有效切割速度,严格执行安装精度要求。
(2)安装绳索根据已确定的切割形式将金刚石绳索按一定的顺序缠绕在主动轮及辅助轮上,注意绳子的方向应和主动轮驱动方向一致.(3)相关操作系统的连接及安全防护技术措施根据现场情况,水、电、机械设备等相关管路的连接应正确规范、相对集中, 走线摆放严格执行安全操作规程,以防机多、人多、辅助设备、材料乱摆、乱放, 造成事故隐患。
绳索切割过程中,绳子运动的方向的前面一定用安全防护拦防护,并在一定区域内设安全标志,以提示行人不要进入施工作业区域。
(4)切割启动电动马达,通过控制盘调整主动轮提升张力,保证金刚石绳适当绷紧,供应循环冷却水,再启动另一个电动马达,驱动主动轮带动金刚石绳索回转切割。
切割过程中必须密切观察机座的稳定性,随时调整导向轮的偏移,以确保切割绳在同一个平面内。
(5)切割参数的选择切割过程中通过操作控制盘调整切割参数,确保金刚石绳运转线速度在20m/s左右,另一方面切割过程中应保证足够的冲洗液量,以保证对金刚石绳的冷却,并把磨削下来的粉屑带走。
切割操作做到速度稳定,参数稳定、设备稳定(6)切割过程中应注意的问题如遇到发生卡绳,断绳等现象要有相应措施解决。
安全防护措施一定严格、严密,否则断掉的金刚石绳索上的金刚石串珠会像子弹一样飞出伤人。
故现场除搞好必要的防护措施外,一律谢绝来往无关人员观摩。
322金刚石绳锯机工作性能采用型号DSM-10A (见下图)绳锯机,具体性能参数如下所述:金刚石绳锯机DSM-10A 型绳锯机主要技术参数:驱动轮:© 600 mm额定功率:10KV ;额定电压:400V-50/60HZ ;钢丝线速度:0— 27m/s ; 缠绳容量: 最大9.0米; 外型尺寸:1370X 557X( 1840-2054) mm 防护等级: TP65液压泵量:40-100L/min ;最大工作压力:21MPa最大切割面积:20m2 设备重量:150kg (主机)+190 kg (高压油泵)(1)金刚石绳锯切割的原理金刚石绳锯切割是金刚石绳索在液压马达驱动下绕切割面高速运动研磨切割体,完成切割工作。
拉花线锯使用方法

拉花线锯使用方法
拉花线锯是一种常用的木工工具,主要用于对木材进行精密的切割和雕刻。
下面是一些关于拉花线锯的使用方法:
1. 确定锯齿的方向:拉花线锯的锯齿一般是向下切割的,因此在使用前需要确认锯齿的方向,并将其置于正确的位置。
2. 选择合适的锯条:拉花线锯的锯条一般有不同的粗细和材质。
使用时需要根据需要选择合适的锯条,并将其安装到拉花线锯上。
3. 定位好要切割的位置:在使用拉花线锯进行切割前,需要先用笔在木材上标记好要切割的位置,并用工具将其固定好。
4. 调整锯条的张力:在使用拉花线锯进行切割前,需要先调整锯条的张力,使其达到合适的松紧程度。
5. 开始切割:在调整好锯条张力后,可以用拉花线锯开始切割。
切割时需要保持手部稳定,缓慢地移动锯条,并注意安全。
6. 磨削锯齿:在使用拉花线锯一段时间后,锯齿会变得钝,需要及时进行磨削,以保证切割效果和使用寿命。
总之,使用拉花线锯需要注意安全,熟练掌握使用技巧,并进行适当的保养和维护,以确保其长期高效地使用。
- 1 -。
绳锯切割技术介绍

绳锯切割技术介绍绳锯切割技术的工作原理是通过绳锯切割刃的高速旋转,将金属材料进行切割。
绳锯切割刃通常由超硬合金制成,具有较高的硬度和耐磨性。
在切割过程中,绳锯切割刃以高速旋转的方式与金属材料接触,通过摩擦和冲击力将金属材料切割开。
1.切割设备:绳锯切割设备是绳锯切割技术的关键设备,通常由切割机、绳锯切割刃、电机等组成。
切割机通过控制电机的转速和切割刃的进给速度,实现对金属材料的精确切割。
2.切割材料:绳锯切割技术适用于各种金属材料的切割,如钢材、铝材、铜材等。
不同的材料对切割刃的选择有所差异,一般情况下,硬度较高的材料需要使用质量较好的切割刃。
3.切割参数:切割参数是绳锯切割技术中需要考虑的重要因素,包括切割刃的转速、切割速度、进给速度等。
不同的材料和切割要求需要调整不同的切割参数,以达到最佳的切割效果。
4.切割精度:绳锯切割技术具有较高的切割精度,可以满足大部分切割要求。
切割精度的影响因素主要包括切割刃的质量、切割设备的性能和切割参数的选择等。
1.机械加工:在机械加工领域,绳锯切割技术可以用于加工各种金属零部件。
由于切割精度高,可以满足工程要求,被广泛应用于汽车、航天、航空等行业。
2.金属加工:绳锯切割技术可以用于金属板材的切割,可以实现对不同尺寸和形状的板材进行切割。
在金属加工领域,绳锯切割技术的应用可以提高生产效益和产品质量。
3.建筑:绳锯切割技术可以用于建筑领域的金属结构切割,可以满足各种复杂形状的切割需求。
在建筑领域,绳锯切割技术的应用可以提高施工效率和工程质量。
总之,绳锯切割技术是一种高效、精确的金属切割技术,被广泛应用于各个领域。
随着科技的不断进步和创新,绳锯切割技术将进一步发展,为工业生产和社会发展提供更好的服务。
线锯钢线断线续切技术研究

-
线锯钢 线 断线续切 技术研 究
马 玉通 , 杨 士 超 ( 中国 电子 科 技 集 团公 司 第 四十 六研 究 所 , 天津 3 0 0 2 2 0 )
摘 要 : 根 据 切 割 线 的特 性 , 分析 了在 多 线切 割过 程 中铜 丝 断 线 的各 种 原 因 ; 在 生产 中 , 有 效控
喷 灌提 供 稳 定 的砂 浆 流 量 。钢 丝 绕 过 线 网 后 再通
过 滑 轮 和 张 力 回 到 收 线轮 上 , 在切 割 时 高速 运 动
的 钢 线 携 带 附着 在钢 丝上 的 S i C 磨 料对 硅 棒进 行
研 磨 从 而 达 到 切 割 的 效 果 。 在 切 割 过程 中钢 线通
过滑 轮 的 引导 , 在 导轮 上 形 成 一 张 线 网 , 而 待 加 工 硅棒 通 过 工 作 台 的 下 降 或 上 升 实现 供 给 ,把 硅 晶
棒 按 一 定 晶 格 方 向切 割 成 片 …。 随 着 硅 料 价 格 的
上涨 以及 硅 片 向越 来 越 薄 的方 向发 展 ,降 本 增 收 成 为企 业 发 展 的 关键 , 多线 切 割 中屡 次 断 线 事 故 , 会对 单 位 的生 产 成 本 产 生 极 大 的 影 响 ,平 均 每 次 断线 都 将 造 成 1 ~l 0万 元 不 等 的损 失 , 为此 , 我们 对 钢 线 的 断线 原 因进 行 了研 究 ,找 出 问题 出现 的 原因, 从 而 找 到解 决 问题 、 预 防 问题 发 生 的方 法 。
多线 切 割 机 的原 理 是 通 过 伺 服 电机 控 制 的放 线 轮 拉 出 的 镀 铜 拉 丝 绕 过 几 个 起 转 向 作 用 的滑 轮, 然 后 经 过 张 力控 制 器 , 在 切 割 室 内连 续 缠绕 在 2 ~4个 主 导 轮 上 , 形 成 一 个 在 水 平 面 上 弥 补 的 平 行线 网。 而在 线 网 的上 方 , 单 晶 的两 侧 布 置 有 砂浆
金刚石线切割的原理、特点及其在精密超精密加工领域的应用

1金刚石线切割20世纪90年代,国际上为了解决大尺寸硅片的加工问题,采用了线锯加工技术将硅棒切割成片。
早期的线锯加工技术是采用裸露的金属线和游离的磨料,在加工过程中,将磨料以第三者加入到金属线和加工件之间产生切削作用[1]。
这种技术被成功地用于对硅和碳化硅的加工。
为了进一步缩短加工时间,以及对其它坚硬物质和难以加工的陶瓷进行加工,人们将金刚石磨料以一定的方式固定到金属线上,从而产生了固定金刚石线锯。
3.1金刚石线切割的原理图3.1金刚石线切割原理图如图3.1高速往复运动的切割线带动砂浆到切割区,使砂浆中的研磨颗粒(SiC颗粒)与硅棒表面高速磨削,由于研磨颗粒有非常锐利的棱角,并且硬度远大于硅棒的硬度,所以硅棒与线锯接触的区域逐渐被砂浆磨削掉,进而达到切割的效果,同时砂浆也可以带走磨削中产生的大量热[2]。
在对金刚石线锯切割机理的认识过程中,许多研究者认为,金刚石磨粒的微观切削运动是一个滚动、嵌入过程,提出了“滚动 -嵌入”模型。
Li 等人提出锯丝施加在磨粒上的力带动磨粒沿切削表面滚动,同时压挤磨粒嵌入切削表面,从而形成剥落片屑和表面裂缝,形成宏观的切割作用。
重点研究了磨粒嵌入工件时的应力分布和作用,发现磨粒对材料的最大剪切应力发生在微观切削表面之下,据此对磨料的选择进行优化。
Kao 等人指出在“滚动 - 嵌入”模型中,磨粒的运动除滚动和嵌入外,还包括刮擦,三者共同形成切削作用。
Bhagavat等人则在这个模型中考虑了磨浆的作用并认为,在锯丝带动游离磨料切割硅锭的小区域内,锯丝与磨浆的运动构成了一个弹性流体动力学环境,用有限元方法分析锯丝与硅锭间的磨浆弹性流体动力学模型,得到磨浆薄膜厚度和压力分布关于走丝速度、磨浆粘度和切割条件的函数,还得出结论:磨浆薄膜厚度大于平均磨粒尺寸,是磨粒的流动产生了切削[3]。
3.2 金刚石线切割的导线轮根据切割材料直径不同和设备制造厂家的技术考虑导线轮有2轮、3轮、4轮不等,安装方法有2轮平行、等边三角形或梯形,如图3.2所示。
电镀金刚石线锯制造及切割技术研究

液 的游离磨 料切 割方 式 。但 是 : 工 艺 存 在 的 主要 问 该 题是锯 口损耗 大 , 易造成 硅 片表层较 深 的损伤 层 , 且表 面粗糙 度和 面形精 度难 以控制 ; 磨浆 消耗 大 , 作业 环境 恶劣 ; 因使用 游离磨 粒钢 丝移 动速度 难 于提高 , 割效 切 率 的改善 受 到限制 。
维普资讯
Thl d 工艺与检测 enga C0yn 0
电镀金 刚石线锯制造及切割技术研究
高 玉飞 葛培琪 侯 志坚 李 绍杰
( 山东 大 学机械 学院 , 山东 济 南 2 06 ) 50 1
摘 要 : 介绍 了几种 电镀 金刚石 线锯 的制 造方 法 , 介绍 了往 复式和 环 形 两种 金 刚 石线 锯 切片 方 法 的原 理 。 并 对 锯切 硅片 时各 工艺参 数对 切片 表面质 量 的影 响规律 进行 了理 论研 究 。适 当提 高锯 丝 的张紧 力 , 在
为了解决 上述 问题 , 电镀 金 刚石 线 锯 切割 技 术 正
为解决 电沉 积速 率低 导致线 锯 生产效 率低 这个缺 点 , 采用毡 刷辅 助 电镀 的超 高 速 电 镀 工艺 制 造 电镀 可
金 刚石 线锯 … 。这种工 艺 采 用 氨基 磺 酸 镍 镀 液 , 把金
逐渐发展起来 。将高硬度 、 高耐磨性 的金刚石微粉用 复合 电镀 的方法 固结在 钢丝基 体上 而制 成 的电镀金 刚
石 线锯 , 具有 耐热性 和 耐 磨性 高 , 切缝 窄 , 切割 面形 精
度好 等优 点 。电镀 金刚石 线锯 切割 技术应 用 于工业 上 硅 片切割 具有 良好 的发展 前景 , 也适 用 于切割 宝石 、 玛 瑙、 陶瓷 、 晶等 贵重 硬脆 材料 。 水 本文 介绍 了几种 电镀 金 刚 石线 锯 的制 造 方 法 , 介 绍 了往复 式和 环形两 种线 锯切 割技术 的原 理 。不考 虑
金刚石线锯切割硬脆材料的表面形貌仿真和实验

金刚石线锯切割硬脆材料的表面形貌仿真和实验硬脆材料具有高强度、高硬度、隔热性好和化学稳定性好等优点,同时也耐高温和腐蚀,因此它的应用越来越广泛,对脆性材料的晶片表面质量要求也越来越高。
但由于脆性高、塑性和断裂韧性低等原因,导致脆性材料的加工非常困难。
金刚石线锯切割是一种新兴的、能有效切割硬脆材料的加工方法,其具有较低的成本、锯口损耗与环境污染,同时可以获得更窄的切缝,因此已经成为发展最快、被使用最多的一种硬脆材料切割方法。
在金刚石线锯切割加工中,影响脆性材料晶片表面质量的因素很多,如线锯速度、工件的进给即线锯的张力等。
本文以固结金刚石磨粒线锯的往复式切割过程为背景,分析晶片表面形貌的生成,进行仿真和实验研究。
分析了金刚石线锯的往复式切割过程,为了简化仿真过程,将单颗磨粒简化成圆锥体,将在线锯上分布无规律的磨粒简化为磨粒磁盘;分析了晶片表面形貌产生的机理,并建立了相应的数学模型,对线锯换向而导致的晶片表面波纹进行了仿真。
根据线锯换向周期,获得了晶片表面波纹的变化规律;用线锯上最终形成工件表面的微弧来解释表面的成因并预测其形状;结合磨粒磁盘运动特点,推导出磨粒运动的数学表达式,使用Matlab软件模拟线锯上磨粒的运动轨迹,建立切割过程中磨粒轨迹的数学模型。
仿真与实验结果的对比,获得了线锯速度和工件进给速度对工件表面形貌的影响。
在线锯速度不变的情况下,表面的波纹宽度会随着工件进给速度的增大而增加;而波纹的深度会随着线锯速度的增大而增大,并分析了仿真和实验之间的误差。
证明了仿真方法能有效的预测表面形貌随加工参数的变化趋势。
分析了往复式线锯切割硬脆材料时这些因素对成品表面质量和形貌的影响。
再使用响应曲面法(RSM)对多个加工因素建立模型,通过相关试验数据拟合模型系数,得到了响应函数的具体表达式并验证了模型的可靠性。
通过研究与探讨加工参数对表面质量的影响,进一步优化了工艺参数。
金刚石线锯简介
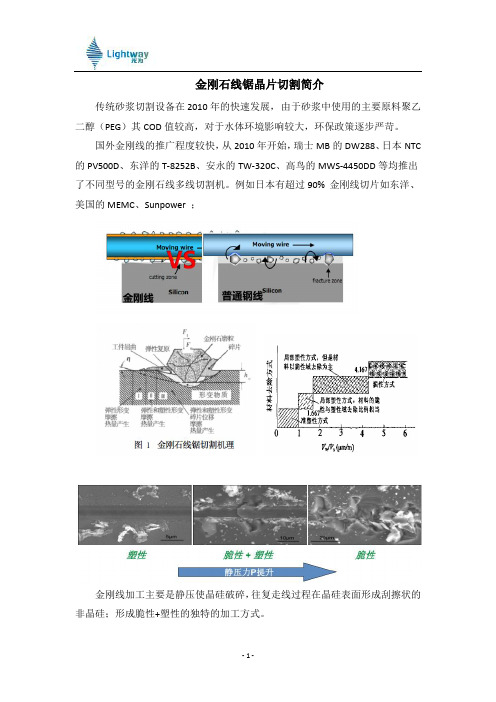
金刚石线锯晶片切割简介传统砂浆切割设备在2010年的快速发展,由于砂浆中使用的主要原料聚乙二醇(PEG)其COD值较高,对于水体环境影响较大,环保政策逐步严苛。
国外金刚线的推广程度较快,从2010年开始,瑞士MB的DW288、日本NTC 的PV500D、东洋的T-8252B、安永的TW-320C、高鸟的MWS-4450DD等均推出了不同型号的金刚石线多线切割机。
例如日本有超过90% 金刚线切片如东洋、美国的MEMC、Sunpower ;金刚线加工主要是静压使晶硅破碎,往复走线过程在晶硅表面形成刮擦状的非晶硅;形成脆性+塑性的独特的加工方式。
国内2012年随着环保政策的要求及金刚石线成本的降低,以及切割技术的进步,硅片厚度已经逐步从超过200um的水平逐步下降至180、160um的水平,硅片实验室切割水平硅片厚度已经可以达到140um,甚至更低的水平。
P型单晶普通电池和P型多晶PERC电池成本相当,单晶电池竞争力回升,多晶市场主导地位受到挑战。
多晶硅光伏产品行业目前也在加速推进金刚线切割多晶硅及制绒技术的研究与应用。
伴随电池技术进步,硅片薄片化是未来必然的发展趋势,通过薄片化可以降低硅片硅耗,提高硅片产量,进而降低硅片切割的硅成本。
金刚线切片技术在单晶加工领域获得了巨大的推广。
在成本和环保的双重压力下,国内多家单晶硅片生产公司如西安隆基、内蒙古中环、锦州阳光、卡姆丹克、申和热磁、晶龙等行金刚线切片。
多晶金刚线方面上海卡姆丹克、浙江昱辉、保利协鑫、晶科等公司进行传统砂浆切割设备的改造,有改造成功案例。
金刚线简介:目前日本厂商凭借先发优势,并依靠在金刚石工具制造行业积累的技术优势,在高端市场占据较大份额,代表企业包括旭金刚石(AsahiDiamond)、中村超硬(nakamura)等。
日本的旭金刚石(AsahiDiamond)2007年6月就推出了成熟产品;美国Diamond Wire Technology (Meyer Burger AG)主要和梅耶博格公司合作。
锯条的切割技巧

锯条的切割技巧
锯条是一种常见的切割工具,特别是在木工、金属加工和建筑行业中。
掌握正确的锯条切割技巧可以提高工作效率和切割质量,同时还可以保证工作安全。
下面介绍几种常用的锯条切割技巧。
1. 选择正确的锯条类型
不同材质需要不同类型的锯条,因此在选择锯条时必须注意。
例如,钢材需要用金属锯条,木材则需要木工锯条。
如果使用不正确的锯条,将会影响切割质量和切割速度,并且可能会损坏锯条。
2. 控制锯条的速度和压力
在使用锯条时,应该掌握正确的切割速度和压力。
切割速度不能太快,否则会容易让锯条卡住或者损坏锯条。
压力也不能太大,否则可能会导致锯条变形或者断裂。
3. 保持锯条垂直于工件
在切割时,锯条必须保持垂直于工件。
如果倾斜或者偏移,会导致切割线不准确,影响切割质量。
同时还会导致锯条损坏或者变形。
4. 使用合适的润滑剂
使用润滑剂可以减少锯条的磨损和摩擦,同时还可以提高切割速度和切割质量。
例如,在切割金属时,可以使用润滑油或者切削液来降低摩擦和热量。
5. 定期维护锯条
定期对锯条进行清洁和维护可以延长锯条的寿命和保持切割质量。
如果锯条出现损坏,必须及时更换。
同时,要注意锯条的存放和
保养,避免锯条受潮、生锈等问题。
总之,掌握正确的锯条切割技巧可以提高工作效率和切割质量,同时还可以保证工作安全。
在使用锯条时,必须严格按照操作规程进行操作,避免因操作不当而导致的安全事故。
线锯切割机工作原理

线锯切割机工作原理宝子们!今天咱们来唠唠线锯切割机这个超酷的家伙的工作原理,可有意思啦!线锯切割机呢,它有一根细细长长的锯线,这锯线就像是一个超级小却超级厉害的小战士。
这锯线可不是普通的线哦,它一般是用很坚韧的材料做的,像钢丝之类的。
为啥要用这么坚韧的材料呢?这就和它的工作有关啦。
想象一下,你要切割一些硬邦邦的东西,像石材啊,金属啊之类的。
如果是普通的线,那肯定一下子就断啦。
但是线锯切割机的锯线就不一样,它就像一个倔强的小硬汉。
当机器开始工作的时候,这锯线就开始高速地运动起来。
它的运动方式就像是在跳一种超级快的舞蹈,来来回回地穿梭。
这个锯线在切割的时候,其实是靠着摩擦力来干活的。
你看啊,当它高速地在被切割的材料表面移动的时候,就会产生摩擦力。
这个摩擦力可不得了,就像是一双双小手,一点点地把被切割材料的那些分子啊、原子啊给推开。
就好比你要把一群紧紧挨在一起的小蚂蚁分开,这个摩擦力就是那个把蚂蚁分开的力量。
而且哦,线锯切割机在工作的时候,还会给锯线施加一定的压力。
这个压力就像是在后面给锯线加油打气的小伙伴。
锯线有了这个压力,就更能紧紧地咬住被切割的材料啦。
就像你用手去捏一块橡皮泥,如果轻轻捏,可能就只能留下一点印子,但是用力捏呢,就能把橡皮泥捏出个形状来。
锯线也是这样,有了压力,就能更深入地切入到材料里面去。
在切割一些比较厚的材料的时候,线锯切割机的锯线还会不断地调整自己的角度呢。
它可聪明啦,就像一个会自己找路的小探险家。
如果一直按照一个角度切割,可能到后面就会卡住,或者切割得歪歪扭扭的。
但是锯线会根据材料的厚度和质地,灵活地改变自己的角度,这样就能保证切割出来的东西又平整又漂亮。
还有啊,线锯切割机里面还有一些小装置是专门用来控制锯线的速度的。
这个速度的控制也很有讲究呢。
如果速度太快,锯线可能会因为过热而坏掉,就像一个人跑得太快会累倒一样。
如果速度太慢呢,又会影响切割的效率。
所以这个速度的控制就像是在给锯线找一个最舒服的节奏,让它能欢快地工作,又不会累垮。
曲线锯抬刀档工作原理
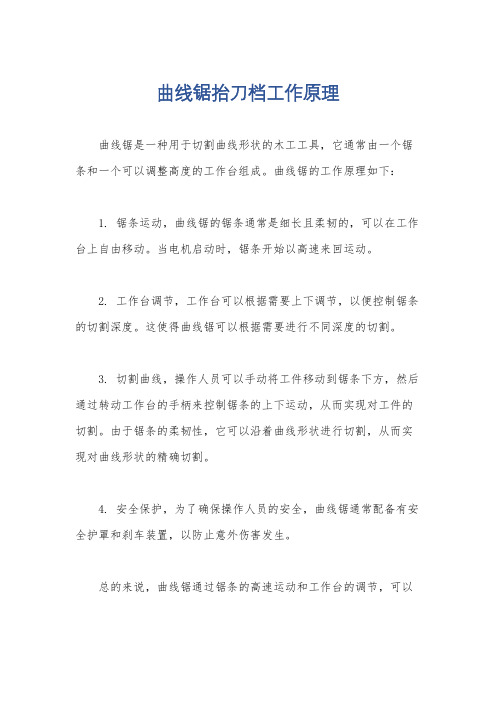
曲线锯抬刀档工作原理
曲线锯是一种用于切割曲线形状的木工工具,它通常由一个锯条和一个可以调整高度的工作台组成。
曲线锯的工作原理如下:
1. 锯条运动,曲线锯的锯条通常是细长且柔韧的,可以在工作台上自由移动。
当电机启动时,锯条开始以高速来回运动。
2. 工作台调节,工作台可以根据需要上下调节,以便控制锯条的切割深度。
这使得曲线锯可以根据需要进行不同深度的切割。
3. 切割曲线,操作人员可以手动将工件移动到锯条下方,然后通过转动工作台的手柄来控制锯条的上下运动,从而实现对工件的切割。
由于锯条的柔韧性,它可以沿着曲线形状进行切割,从而实现对曲线形状的精确切割。
4. 安全保护,为了确保操作人员的安全,曲线锯通常配备有安全护罩和刹车装置,以防止意外伤害发生。
总的来说,曲线锯通过锯条的高速运动和工作台的调节,可以
实现对木材等材料进行精确的曲线切割,是一种常用的木工加工工具。
东成曲线锯ff85方法

东成曲线锯ff85方法
东成曲线锯FF85方法是一种高精度金属加工工艺,通过特殊设计的切割工具和曲线运动模式,实现对金属材料的快速、精确切割。
该方法已广泛应用于航空航天、汽车制造、电子设备等领域,成为提高生产效率和产品质量的重要工艺。
东成曲线锯FF85方法的核心是曲线运动模式。
与传统的直线锯切不同,东成曲线锯FF85方法采用曲线运动轨迹,使刀具能够按照预定曲线进行切割。
这种曲线运动模式可以实现更加复杂的切割形状,提高金属材料的切割精度和表面质量。
此外,东成曲线锯FF85方法还采用了特殊设计的切割工具。
这些工具通常由高硬度的材料制成,如硬质合金。
刀具的设计与曲线运动模式相匹配,能够更好地适应切割曲线,并保持高速旋转的稳定性。
通过优化刀具的形状和材质,东成曲线锯FF85方法能够提高切割效率和工具寿命。
东成曲线锯FF85方法具有许多优点。
首先,它可以实现高精度的切割,尤其适用于复杂曲线形状的切割需求。
其次,这种方法切割速度快、效率高,能够提高生产效率和降低生产成本。
此外,东成曲线锯FF85方法还能够实现无需后续加工的切割,减少生产流程和工艺环节。
总之,东成曲线锯FF85方法是一种应用广泛的高精度金属加工工艺。
通过特殊设计的切割工具和曲线运动模式,可以实现对金属材料的快速、精确切割,提高生产效率和产品质量。
这种方法在众多领域都有着重要的应用前景,并为工业制造带来了巨大的发展机遇。
电锯锯木头的技巧和方法
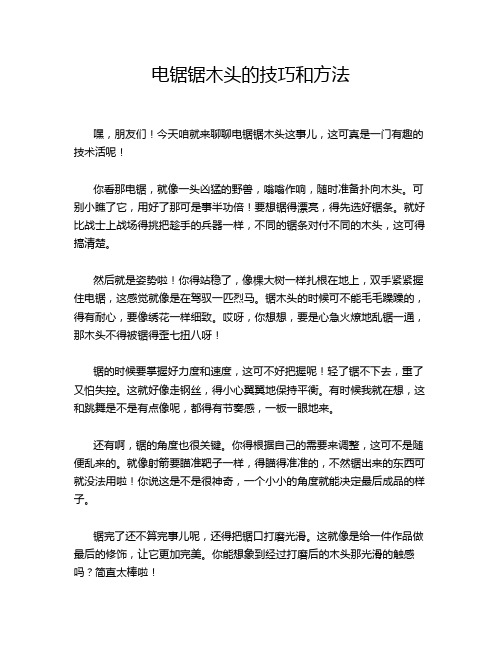
电锯锯木头的技巧和方法
嘿,朋友们!今天咱就来聊聊电锯锯木头这事儿,这可真是一门有趣的技术活呢!
你看那电锯,就像一头凶猛的野兽,嗡嗡作响,随时准备扑向木头。
可别小瞧了它,用好了那可是事半功倍!要想锯得漂亮,得先选好锯条。
就好比战士上战场得挑把趁手的兵器一样,不同的锯条对付不同的木头,这可得搞清楚。
然后就是姿势啦!你得站稳了,像棵大树一样扎根在地上,双手紧紧握住电锯,这感觉就像是在驾驭一匹烈马。
锯木头的时候可不能毛毛躁躁的,得有耐心,要像绣花一样细致。
哎呀,你想想,要是心急火燎地乱锯一通,那木头不得被锯得歪七扭八呀!
锯的时候要掌握好力度和速度,这可不好把握呢!轻了锯不下去,重了又怕失控。
这就好像走钢丝,得小心翼翼地保持平衡。
有时候我就在想,这和跳舞是不是有点像呢,都得有节奏感,一板一眼地来。
还有啊,锯的角度也很关键。
你得根据自己的需要来调整,这可不是随便乱来的。
就像射箭要瞄准靶子一样,得瞄得准准的,不然锯出来的东西可就没法用啦!你说这是不是很神奇,一个小小的角度就能决定最后成品的样子。
锯完了还不算完事儿呢,还得把锯口打磨光滑。
这就像是给一件作品做最后的修饰,让它更加完美。
你能想象到经过打磨后的木头那光滑的触感吗?简直太棒啦!
总之,电锯锯木头可真是一门大学问。
它需要技巧,需要耐心,更需要我们对它的热爱。
只有真正热爱这门技术,才能把木头锯得漂亮,锯得精彩!这就是我的看法,你们觉得呢?。
曲线锯的原理

曲线锯的原理曲线锯是一种常用的木工工具,它可以用来切割各种形状的曲线,因此在家具制作和木工加工中被广泛使用。
曲线锯的原理是通过锯片的旋转和上下移动,将木材进行切割。
下面我们将详细介绍曲线锯的原理。
首先,曲线锯的核心部分是锯片。
锯片通常由金属材料制成,表面有着锋利的锯齿。
当曲线锯启动时,锯片会以高速旋转,锯齿会不断地切入木材表面,从而实现切割的目的。
锯片的旋转速度和锯齿的形状会直接影响到切割效果,因此选择合适的锯片对于曲线锯的工作效率和切割质量至关重要。
其次,曲线锯的上下移动也是实现切割的重要原理。
曲线锯的锯片通常是固定在一个可以上下移动的平台上。
当木材被放置在工作台上并启动曲线锯时,平台会根据操作者的控制上下移动,从而使锯片能够沿着木材的纵向进行切割。
这种上下移动的设计使得曲线锯能够灵活地适应不同厚度的木材,并且能够切割出各种复杂的曲线形状。
另外,曲线锯还配备有一台电机,这台电机提供了锯片旋转和平台上下移动所需的动力。
电机的功率和稳定性会直接影响到曲线锯的工作效率和安全性。
因此,选择一台性能稳定的电机对于曲线锯的工作质量至关重要。
除此之外,曲线锯还需要配备一套完善的安全保护装置。
例如,防护罩可以有效地防止操作者因为接触到旋转的锯片而受伤。
此外,紧急停止按钮也是必不可少的,一旦发生意外情况,操作者可以立即按下紧急停止按钮,以确保人身安全。
总的来说,曲线锯的原理是通过锯片的旋转和上下移动,配合稳定的电机和完善的安全保护装置,实现对木材的切割。
这种原理使得曲线锯成为了木工加工中不可或缺的工具,它不仅能够提高工作效率,还能够实现各种复杂曲线形状的切割,为木工加工提供了便利和灵活性。
saw工艺技术

saw工艺技术Saw工艺技术是一项常用于金属加工和木材加工中的技术,旨在通过使用锯子将材料切割成所需的形状和尺寸。
这项技术广泛应用于建筑、制造业和家具制作等领域,因其高效、精确和经济的特点而备受青睐。
在saw工艺技术中,最常见的工具是电动锯和手动锯。
电动锯通常由电动机和切割刃组成,可以快速高效地完成切割任务。
而手动锯则需要操作者手动推拉进行切割,适用于一些小块的加工。
在进行saw工艺技术时,首先需要选择合适的锯刃。
不同的锯刃适用于不同的材料,如金属、木材和塑料等。
一般来说,较粗的锯齿适用于粗糙的切割,而较细的锯齿则适用于更精细的切割。
锯刃的材质也很重要,通常有高速钢、硬质合金和钨钛合金等。
接下来,在进行切割之前,需要确定合适的工作台和夹具来保持材料的稳定。
这可以在切割中确保准确度和安全性。
同时,悬挂数量和位置也需要根据材料的尺寸和形状进行调整。
然后,操作者需要将材料放置在工作台上,并使用锯子沿着预定的切割线进行切割。
在进行锯切时,要保持稳定的手部动作,并适当加压,以确保切割的稳定和准确。
如果材料较大或切割较困难,可使用引导器或支撑物来增加稳定性。
在进行saw工艺技术时,操作者需要保持警惕,遵守安全规定。
必须佩戴护眼镜和手套,以防止碎片或切割物进入眼睛或手部。
此外,不得擅自更换或维修锯刃,以免引发危险。
在saw工艺技术中,切割后的材料常常需要进行进一步加工和处理,如打磨、抛光和焊接等。
这些步骤可以提高材料的表面质量和加工精度。
虽然saw工艺技术在金属和木材加工中非常常见,但它也面临一些挑战。
例如,切割过程中可能会产生热量和振动,需要在设计和操作中加以控制。
此外,由于锯切是一种物理切割过程,切割线可能不够平滑,需要进行进一步加工和修整。
总的来说,saw工艺技术作为一种快速高效的切割方法,具备广泛的应用前景。
随着技术的不断发展,saw工艺技术将会更加智能化和自动化,为工艺加工提供更多可能性。
同时,为了确保安全和质量,操作者需要具备专业的技能和知识。
- 1、下载文档前请自行甄别文档内容的完整性,平台不提供额外的编辑、内容补充、找答案等附加服务。
- 2、"仅部分预览"的文档,不可在线预览部分如存在完整性等问题,可反馈申请退款(可完整预览的文档不适用该条件!)。
- 3、如文档侵犯您的权益,请联系客服反馈,我们会尽快为您处理(人工客服工作时间:9:00-18:30)。
先进线锯切割技术在太阳能光伏电池制造中的应用应用材料公司外部使用先进线锯切割技术在太阳能光伏电池制造中的应用简介为了使太阳能电池能够最终在取决于每瓦成本的能源供应市场上具有竞争力,光伏价值链中每个生产步骤的总体拥有成本(图1)都至关重要。
晶体硅片的生产也不例外:处理一片硅片的总体拥有成本是降低其总体成本的主要动力。
图1: 晶体硅太阳能光伏硅片切割价值链图2: Applied HCT 切方机硅片切割工艺始于由单晶硅或多晶硅材料制成的实心硅锭。
线锯将硅锭裁成方块(图2),然后再切割成很薄的硅片。
这些晶体硅片就被用作制造光伏电池的衬底。
如今的线锯切割大多数是通过多线切割技术(MWS )实现的。
本文简要介绍线锯切割工艺及生产过程中面临的各种挑战,并且展示了能同时降低硅锭切方与硅片切割成本的下一代线锯切割技术。
线锯的历史第一台可实际使用的光伏硅片切割机是以瑞士HCT 成型系统公司(HCT Shaping Systems )的创始人Charles Hauser 博士的开创性研究为基础研制而成,于上个世纪八十年代投入使用。
(如今是应用材料公司的精密硅片切割系统部门。
) 这类设备使用携带研磨浆料的切割线,通过切割线运动来切割硅片。
即使到现在为止,大多数用来将硅锭开方和切片的线锯仍然保留了与Hauser 博士的原型机器相同的基本结构,但是载荷与切割速度都得到了大幅提升。
线锯切割工艺现代线锯的核心部分是缠绕在导轮上、直径为110µm-140µm 的单根切割钢线。
这种导轮开槽精细且槽距均匀,形成平行切割线的水平网状结构或网(图3)。
强大的驱动力使整张网在相对高速(每秒10米到20米)下运行。
浆料,一种由耐磨粒子加冷却液制成的悬浮液,通过喷嘴输送到运动中的切割线上。
切割线将浆料传送到切割区。
将要切割的硅锭被固定在切割台上并且与切割头逆向垂直运动。
这一动作将硅锭推多晶硅- 单晶硅硅锭生长 硅砖裁切硅锭生长 /晶体化硅砖加工 (研磨 + 倒角)硅砖切割 晶体硅片晶体硅片清洁度量过切割线网,同时产生大量的硅块或硅片。
在使用浆料的多线锯切割系统中,切割运动基本上是一种快速的三体磨损过程,其特点在于使用了一种基于滚动及压入的切割机制[1]。
图3: 多线锯系统示意图。
硅锭被推过过切割线网。
线锯切割的原理浅显易懂,但是真正的挑战来自于实际操作。
线锯必须准确地平衡切割线的直径、切割速度以及切割总面积,这样才能既不造成切割线断裂又能保证精确的形状控制和高成品率。
降低成本多线切割系统在进行硅片切割时的总体拥有成本取决于4个关键因素(按照重要性递减顺序):多晶硅的市场价格、硅片成品率、切割耗材的成本以及生产率。
提高成品率可以在降低硅片切割成本方面带来极大的改进,而对于原材料成本来说,能做的事情并不多或者根本没有办法。
硅片成品率,即每单位原材料所制成硅片的可用面积,受两大因素的影响:切割过程中原材料的损耗(“锯末”或锯缝损失)以及切割过程中产生的未达标硅片。
硅原料的利用率可通过减少锯缝损失或在保证切割质量的同时降低硅片厚度来加以提高。
硅片的厚度由导轮的槽距决定,而锯缝损失取决于钢线直径与磨料颗粒的大小。
在过去十年中,光伏硅片的厚度已经从330µm减少到如今常见的180µm ,而且未来这一趋势还会继续。
线锯切割系统的切割线直径最初在180µm至160µm之间,如今已经缩小到常见的130µm至100µm之间。
晶体硅太阳能光伏电池生产商对硅片质量要求极高,要求硅片没有任何表面损伤或只有极少的表面损伤(微小裂痕和锯痕),极少的外貌缺陷(扭曲、弯曲以及厚度不匀)并且基本无需额外的下游处理。
如下所述,钢线直径和磨料颗粒的大小是保证硅片表面质量的重要因素。
最后,耗材成本及生产率改进为降低成本提供了更多的渠道。
浆料消耗、切割线磨损、浆料回收以及切割线更换耗时等方面的改进都能发挥一定的作用。
在硅片切割工厂中,提高回收是一种十分强大、有效的降低成本的手段。
从这种技术最初于二十一世纪初期进入市场直至今天,以机械和化学分离原理为基础的回收技术稳定而显著地降低了浆料成本,同时也带来了一定的环保效益。
如今,大多数终端用户在切割硅片时所使用的浆料由70%到80%的回收成分(例如,液态冷却剂和研磨碳化硅颗粒)和全新的材料组成。
主要工艺变量硅片切割工艺的目标在于提高产量同时保证一流的成品率。
产量即指定时间内所生产出的硅片数量,主要取决于以下几个因素:1) 切割台速度(或进料速度)指固定待切割硅锭的切割台通过运动中的切割线网的速度。
硅锭通过切割线网开始接受切割时,切割线和硅原料之间的压力会逐渐增加。
两者之间的研磨浆料通过一种被称为“滚动与压入”的研磨机制开始切开硅原料。
在压力增加与原料开始移除之间的延迟会导致切割线网出现弯曲。
一旦原料移除速度和切割台下移速度匹配,切割就达到了运动平衡。
在指定的切割台速度和载荷下,这种平衡很大程度上取决于切割线速度、浆料切割能力以及切割线张力。
2) 载荷——指每次运行的总切割面积,即硅片面积乘以硅块数量然后再乘以每个硅块能生产的硅片数量。
每个硅块可生产的硅片数量由硅块/硅锭的长度除以导轮的槽距所得数值决定。
3) 钢线直径——较小的钢线直径意味着更低的锯缝损失。
然而,钢线直径较小的切割线容易断裂,而且在切割过程中会受到更多的磨损。
这种钢线直径的变化会增加切割线断裂的风险并影响硅片质量。
优化切割线损耗的方法包括在切割线磨损和断裂风险之间找到最佳平衡点:一种能承受更多切割线磨损的系统虽然可以减少切割线的用量,但是却面临着更为频繁的切割线断裂风险。
在特定应用中(载荷、硅片厚度等),切割台速度(进料速度)与切割线速度之比越高 (v T/v w),则切割线磨损就越快。
4) 可维护性或切换时间——在两次切割运行过程中,线锯被服务的速度越快,包括更换切割线和浆料,则整体生产率越高。
在理想状态下,生产商希望载荷尺寸能够最大化。
同时切割更多的硅料可在规定时间内生产出更多的硅片,从而实现生产率的最大化。
Applied HCT B5 (图4)是市场上唯一具备处理较大载荷(2米)能力的系统,为生产商提供了优化载荷的灵活性,在不牺牲成品率的前提下实现生产率的最大化。
图4: Applied HCT B5型线锯图5、图6及图7显示了0.85米载荷和1.73米载荷的测量数据,证实了提高载荷能极大地提高生产率并确保硅片的成品率。
在1.73米载荷及每分钟210µm的切割台速度下,98%的硅片可达到总厚度变化(TTV)30µm、厚度变化(TV)20µm以及20µm锯痕的规格要求。
图5: 厚度变化对比图表图6: 总厚度变化对比图表图7:锯痕对比图表先进的线锯切割技术为了满足市场对更低成本的要求,线锯平台架构必须不仅可以进行载荷优化,而且还要能够适应线锯技术的进步。
B5系统是经过实践证明可进行大规模生产的硅片切割系统,不仅能够使用细钢线,而且还可以方便地升级到其它先进的技术,例如结构线和金刚线。
图8: 结构线图10:金刚线结构线(图8)是一种革命性的切割线技术。
由于这种技术能够更有效地传输浆料并实现更快的切割速度,因而能大幅提高生产率。
Applied HCT在硅片切割和开方方面首先应用结构线技术。
实践证明,在Applied HCT开方机上,具有专利保护的粗结构线可将生产率提高70%、将拥有成本降低25%(图9)。
Applied HCT正致力于开发结构线在硅片切割中的应用。
结构线面临的最大挑战在于由于降低切割线断裂载荷而导致的切割线网管理难度。
然而,我们预期最终可以在不影响硅片质量的前提下实现更快的切割速度。
BKM比较标准结构线250µm 粗结构线300µm每个硅锭的锯缝损失(GEN 5 x 250 mm)每块2.05公斤每块2.34公斤生产率100%170%拥有成本100%75%硅块规格±0.25mm @ 95% ±0.25mm @ 95%图9: 结构线在多切割线切方中的应用新一代金刚线(图10)专门用于在通过减少浆料损耗降低成本的同时进一步提高切割速度。
金刚线是线锯切割工艺的一项关键变革。
金刚线实际上是一种表面嵌有钻石颗粒的切割线。
金刚线的磨料颗粒大小和集中度随应用而变化,例如,是切割多晶硅还是单晶硅材料。
钻石颗粒起到了研磨剂的作用,这样无需使用碳化硅磨料,使整个工艺更加清洁、更加环保。
和结构线一样,金刚线技术也同时适合于硅片切割和硅锭开方应用。
Applied HCT开方机和B5平台通过硬件升级可扩展到使用金刚线,这使客户能以更低的成本费用切换到金刚线技术,因为客户不用投资购买新的系统。
最近,Applied HCT金刚线开方机项目已经在实验室中成功实现了在4000µm/分钟的速度下有100%硅块符合规格。
同时,Applied HCT正在积极地研发使用金刚线进行硅片切割的解决方案。
初期结果显示,使用PEG冷却剂能容易地实现单晶硅切割。
而下一个挑战就是优化多晶硅材料载荷的长度以及使用水性冷却剂,这样一方面能完全消除PEG回收成本,而另一方面仍然可以实现高切割速度。
结论目前原材料费用占晶体硅太阳能电池总体成本相当大的一部分,因此线锯技术对于降低每瓦成本并让太阳能光伏价格与传统电力能源持平来说至关重要。
线锯切割技术取得的三大进步已经大幅减少了产生太阳能电力所要消耗的硅材料(每瓦所需的硅材料克数)。
首先,实现切割更薄硅片的能力。
历史趋势显示,每5年硅片厚度就会减少50微米。
从1995年至今,硅片厚度已经从330µm 降低到了180µm。
而这一趋势已经不可能再持续这一速度:随着厚度的降低,硅片会变得越来越脆弱,这需要能够在最小压力下处理超薄硅片的先进自动化技术。
这在将硅片从切割后的堆叠结构中取出(这一过程也被称为“分检”)以及在太阳能电池生产线加工时都是如此。
同时,也需要提高切割工艺来减少硅片的厚度变化并使其与厚度成比例。
其次,使用颗粒更小的磨料。
磨料颗粒大小不仅在通过减少锯缝损失来实现原料节约方面,而且还在通过切割线的单向运动来降低“楔”效应方面起到了重要的作用:硅片在切割线切入硅块的一端比切割线切离开硅块的一端要厚。
(这种厚度变化含糊地被称为“总厚度变化”,缩写为TTV。
) 与粗糙的磨料相比,颗粒更小的磨料在切割时还能让表面损伤更浅,因此在下游太阳能电池生产线上所需的锯痕消除工作也就更少。
减少损伤还能提高硅片的机械强度,减少处理中发生的损耗。
最后,多年来钢线直径的减少有助于节省硅料。
钢线直径已经从上个世纪九十年代中期的180µm降低到今天常见的120µm(有些生产中使用钢线直径规格为110µm甚至100µm的切割线,而在研发领域,钢线直径已经降低到了80µm)。