复合板轧制工艺流程
复合板的制造工艺

复合板的制造工艺一.复合板的制做:1. 制做工艺:采用基层和复层爆炸焊接热轧法复合而成。
2.型式2.1复合板是由基板和复材组成。
2.2复合钢板的形状为矩形、方形、圆形三种。
2.3尺寸规定:复合钢板的爆炸最大宽度为2000mm,最大长度8000mm,最大直径为4000mm,因此基板的规格尽量控制在上述尺寸内。
如遇特殊情况,特别提出。
2.4基板下料尺寸要求:在要求规格的基础上单边余量25mm。
板材超过4000mm,长度方向余量加30mm,宽度方向加余量25m m2.5复板下料要求:在基板加宽的基础上,再加余量25mm。
需要拼接的部分,不开坡口,但要求直口部分无熔渣飞溅。
2.6 基本和复板下料后质量要求:下料边缘必须平滑,无熔渣,豁口。
无论基板还是复板下料后必须宽窄均匀。
3.拼接要求3.1基层板拼接:允许采用焊条电弧焊,埋弧自动焊。
焊前必须彻底清理焊缝及两侧的油污,水锈等杂质。
如遇母材表面有较大凹坑,必须焊接补平,并且磨平。
焊接后必须进行X光检查,100%合格后将焊缝打磨与母材齐平。
3.2复层板焊接:焊接目的达到连接即可。
组对无间隙。
焊接方法:2-3mm板采用手工氩弧焊。
4-8mm板采用焊条电弧焊。
焊材选择:必须采用与母材匹配焊材。
不许乱用焊材。
焊材选用见表1焊接只需在其中一侧进行,另一侧不焊。
焊前在板面上喷洒防飞溅用品。
焊接时严格控制规范参数。
尽量采用小电流,小电压,快速焊。
焊接只需一层连续焊缝。
4.爆炸复合4.1复合板的结合率符合JB4733-1996 第5条要求。
4.2复合板尺寸偏差:复合板整平后复层表面不平度在板宽范围内小于3mm,板长范围内小于8 mm。
4.3复合板表面质量复合后表面不得有气泡、结疤、裂纹、夹杂、折迭等缺陷,且不允许有明显的凹凸不平,复合板经复合热处理、整平热处理后,要求波浪峰值〈1.6mm/m),其波浪度应<5mm/m且<1/50斜度。
4.4复层钢板焊道的修复复层在复合前的焊接状态仅限于连接,爆炸复合后,必须将原连接焊道用角磨机清除。
复合板公司生产工艺能力及主要应用

济钢集团有限公司
金属复合板
三、主要应用行业
(一)造纸行业:主要用于纸浆塔的制作,目前国内80%以上的纸浆塔全部用热轧复合板 制作。
(二)化工设备行业:化工压力容器机械加工中的储槽、储罐、反应釜及非标压力容器设
备等。前期与无锡公司实现了与中石油物资沈阳公司的合作,产品成功进入吉林油田。 (三)生物发酵及制药行业:医药化工设备中的玉米深加工和发酵设备,及医药中间体的 存储设备。 (四)热电行业:各大热电企业项目新建或改造中的水箱、煤斗、钛复合烟筒等设备。 (五)制糖行业:广西、云南地区的制糖新建项目,及设备加工厂家。 (六)路桥行业中的钢模板:国内钢模板企业。
(七)焦化行业:市场细分:国内焦化企业改造项目,及钢铁企业炼焦改造项目中的脱硫
设备等。 (八)管线钢:国内各大管厂。 (九)桥梁:桥梁滑道、桥面等。
济钢集团有限公司
Байду номын сангаас
济钢集团有限公司
金属复合板
(二)生产能力
复合板依托济钢2500mm中板生产线、3500mm厚板生产
线、4300mm宽厚板生产线生产,年生产能力达到3万吨。
基层厚度:3.0~39.5mm 覆层厚度:0.5~5.0mm 总 厚 度:3.5~40.0mm 交货宽度:≤2650mm
交货长度:≤13000mm
金属复合板
(二)工艺流程图
济钢复合板公司
工艺流程图
济钢集团有限公司
金属复合板
二、生产能力
(一)常规生产材质
基层材质:普锰系列(Q235、Q295、Q345等)、容器板系列(
Q245R、Q345R、Q370R、16MnDR等)、管线钢系列(L360[X52]、 L415[X60]、L450[X60]等)、耐候钢系列(Q450NQR1等)、船板系 列、高强钢系列等。 覆层材质:304(L)、310S、316(L)、 317(L) 、321、 1Cr13、镍基合金N08825及工业纯钛TA1、TA2等。
复合板的制造工艺

复合板的制造工艺一、复合板的制做:1.制做工艺:采用基层和复层爆炸焊接热轧法复合而成。
2.型式2.1复合板是由基板和复材组成。
2.2复合钢板的形状为矩形、方形、圆形三种。
2.3尺寸规定:复合钢板的爆炸最大宽度为2000mm,最大长度8000mm,最大直径为4000mm,因此基板的规格尽量控制在上述尺寸内。
如遇特殊情况,特别提出。
2.4基板下料尺寸要求:在要求规格的基础上单边余量25mm。
板材超过4000mm,长度方向余量加30mm,宽度方向加余量25mm2.5复板下料要求:在基板加宽的基础上,再加余量25mm。
需要拼接的部分,不开坡口,但要求直口部分无熔渣飞溅。
2.6基本和复板下料后质量要求:下料边缘必须平滑,无熔渣,豁口。
无论基板还是复板下料后必须宽窄均匀。
3.拼接要求3.1基层板拼接:允许采用焊条电弧焊,埋弧自动焊。
焊前必须彻底清理焊缝及两侧的油污,水锈等杂质。
如遇母材表面有较大凹坑,必须焊接补平,并且磨平。
焊接后必须进行X光检查,100%合格后将焊缝打磨与母材齐平。
3.2复层板焊接:焊接目的达到连接即可。
组对无间隙。
焊接方法:2-3mm板采用手工氩弧焊。
4-8mm板采用焊条电弧焊。
焊材选择:必须采用与母材匹配焊材。
不许乱用焊材。
焊接只需在其中一侧进行,另一侧不焊。
焊前在板面上喷洒防飞溅用品。
焊接时严格控制规范参数。
尽量采用小电流,小电压,快速焊。
焊接只需一层连续焊缝。
4.爆炸复合4.1复合板的结合率符合JB4733-1996第5条要求。
4.2复合板尺寸偏差:复合板整平后复层表面不平度在板宽范围内小于3mm,板长范围内小于8mm。
4.3复合板表面质量复合后表面不得有气泡、结疤、裂纹、夹杂、折迭等缺陷,且不允许有明显的凹凸不平,复合板经复合热处理、整平热处理后,要求波浪峰值〈1.6mm/m),其波浪度应<5mm/m且<1/50斜度。
4.4复层钢板焊道的修复复层在复合前的焊接状态仅限于连接,爆炸复合后,必须将原连接焊道用角磨机清除。
《Al-Mg-Al热轧复合板的制备及其微观组织和力学性能研究》范文

《Al-Mg-Al热轧复合板的制备及其微观组织和力学性能研究》篇一Al-Mg-Al热轧复合板的制备及其微观组织和力学性能研究一、引言随着现代工业的快速发展,对于具有优异性能的金属材料需求日益增长。
Al/Mg/Al热轧复合板作为一种新型的金属复合材料,具有轻质、高强、耐腐蚀等优点,被广泛应用于航空航天、汽车制造、电子包装等领域。
本文旨在研究Al/Mg/Al热轧复合板的制备工艺,探讨其微观组织结构及力学性能,为该类材料的实际应用提供理论依据。
二、制备工艺Al/Mg/Al热轧复合板的制备主要包括原料准备、合金熔炼、轧制及热处理等步骤。
首先,选用纯度较高的铝合金和镁合金作为原料;其次,将两种合金在高温下进行熔炼,以实现合金化;然后,将熔炼后的合金液进行轧制,形成复合板材;最后,对轧制后的板材进行热处理,以提高其性能。
三、微观组织研究(一)金相组织观察通过金相显微镜观察Al/Mg/Al热轧复合板的金相组织,可以发现在轧制过程中,铝合金与镁合金之间发生了良好的冶金结合,没有明显的界面反应产物。
此外,复合板中的晶粒尺寸较小,晶界清晰,这有利于提高材料的力学性能。
(二)扫描电镜及能谱分析利用扫描电镜对Al/Mg/Al热轧复合板进行观察,发现其界面处无明显的孔洞、裂纹等缺陷,表明两种金属之间具有良好的结合性能。
同时,通过能谱分析确定界面处的元素分布,发现铝合金和镁合金在界面处发生了元素扩散,形成了冶金结合。
(三)X射线衍射分析X射线衍射分析表明,Al/Mg/Al热轧复合板中主要包含铝、镁及其合金相。
在界面处未发现新的物相生成,说明两种金属在轧制过程中未发生明显的化学反应。
四、力学性能研究(一)硬度测试通过对Al/Mg/Al热轧复合板进行硬度测试,发现其硬度高于单一金属材料。
这主要是由于复合板中铝合金与镁合金的硬质相相互交错,提高了材料的硬度。
此外,热处理后,复合板的硬度得到进一步提高。
(二)拉伸性能测试拉伸性能测试表明,Al/Mg/Al热轧复合板具有较好的抗拉强度和延伸率。
钢-铝复合板工艺和实验过程

钢-铝复合板复合工艺和实验过程1实验材料的选择钢。
实验用的钢为碳钢板,规格有H×B=(5.0~15.0)mm×(800~1250)mm,在厚比分配规律和结合强度和界面的研究中分别使用了两种钢板与铝板复合轧制,然后进行研究。
铝。
实验用的铝为铝板,规格为180mmx50mmxO.5mm,化学成分见表2.2。
1050纯铝板在本论文中主要用于钢-铝复合板的厚比分配的研究、钢-铝复合板结合强度和界面形貌的研究和热轧复合后的钢-铝复合板的轧后扩散退火处理的研究。
2轧制复合工艺的确定本文通过对爆炸焊接法、挤压复合法、铸轧法、电磁连铸复合法和轧制复合法等几种复合方法的优缺点、产能和投资情况的综合分析,选择轧制复合法作为钢-铝复合板的复合方法。
轧制方法成本低、产量高,而且工艺技术及装备较为成熟,作为一种金属层状复合的工艺方法在本世纪30年代就引起了一些研究者的关注。
轧制工艺不仅用于实现复合的坯料的进一步加工,而且也用来作为一种有效的复合制备技术。
轧制技术易于实现大规模工业化生产,同时不存在像电镀和物理化学方法覆层所带来的环境污染问题,是一种具有非常好的发展潜力的金属层状复合材料制备加工技术。
热轧复合可以在较小的轧制变形率下实现复合,是生产复合板材高速有效生产的方法;冷轧可以减少对钢-铝板的预热处理,节约能源降低成本,但是需要在较大的变形量下才能实现复合,同时板形的弯曲和跑偏比较严重。
在本文中采用了热轧和冷轧对比研究的方法。
2.2.1热轧复合的实验方案实验采用传统的四步骤工序,如图2.1所示,即试样表面处理一轧制前预热一轧制复合一轧后退火处理。
2.2.1.1表面处理在表面处理方面,不管是对钢板表面还是对铝板表面都是为了除去它们表面的氧化层,使其暴露处新鲜的金属和在金属表面表面上达到一定的粗糙度,从而使金属在轧制复合时能实现良好的结合。
本实验所采用的表面处理方法是热轧复合前,钢板表面采用10%HCl溶液浸泡,铝板采用10%NaOH溶液浸泡,然后在清水中除去表面的残余HCI和NaOH溶液和生成物,在空气中晾干,然后用钢刷将铝板试样表面打毛,用手提电动砂轮将钢板试样的结合面打毛,并尽可能使它们的打磨表面有一定的粗燥度,然后用丙酮溶液浸泡以除去表面打毛时留下的油污和磨削等,最后用无水乙醇擦洗表面,将刚才钢板和铝板打毛的表面对合即可进入下一步工艺。
不锈钢/碳钢层状结构复合板生产工艺

不锈钢/碳钢层状结构复合板生产工艺【摘要】介绍四种主要的不锈钢/碳钢层状结构复合板生产工艺和相应的工业化生产流程:爆炸复合,热轧复合,冷轧复合,粘接复合。
分析其各自的特点和市场适应性。
为工程技术人员选用各种不同的不锈钢复合材料实现工程目的提供参考。
【关键词】不锈钢/碳钢复合板;爆炸复合;热轧复合;冷轧复合;粘接复合;扩散退火1、基本概念复合材料是一个极其庞大的产品“家族”体系,本文讨论的仅为其中一个小小的分支。
为了便于理解,将本分支有关的“家谱”作一简单介绍。
1.1复合材料[1]复合材料(Composite materials),是由两种或两种以上不同性质的材料,通过物理或化学的方法,在宏观上组成具有新性能的材料。
各种材料在性能上互相取长补短,产生协同效应,使复合材料的综合性能优于原组成材料而满足各种不同的要求。
复合材料的基体材料分为金属和非金属两大类。
金属基体常用的有铝、镁、铜、钛及其合金。
非金属基体主要有合成树脂、橡胶、陶瓷、石墨、碳等。
增强材料主要有玻璃纤维、碳纤维、硼纤维、芳纶纤维、碳化硅纤维、石棉纤维、晶须、金属丝和硬质细粒等。
复合材料按其组成分为金属与金属复合材料、非金属与金属复合材料、非金属与非金属复合材料。
按其结构特点又分为:(1)纤维增强复合材料。
将各种纤维增强体置于基体材料内复合而成。
如纤维增强塑料、纤维增强金属等。
(2)夹层复合材料。
由性质不同的表面材料和芯材(基材)组合而成。
通常面材强度高、薄,且价格高;芯材质轻、强度低,但具有一定刚度和厚度,成本相对低。
分为实心夹层和蜂窝夹层两种。
(3)细粒复合材料。
将硬质细粒均匀分布于基体中,如弥散强化合金、金属陶瓷等。
(4)混杂复合材料。
由两种或两种以上增强相材料混杂于一种基体相材料中构成。
与普通单增强相复合材料比,其冲击强度、疲劳强度和断裂韧性显著提高,并具有特殊的热膨胀性能。
分为层内混杂、层间混杂、夹芯混杂、层内/层间混杂和超混杂复合材料。
《TC4-6061复合板热轧复合工艺及有限元模拟》范文

《TC4-6061复合板热轧复合工艺及有限元模拟》篇一一、引言随着现代工业的快速发展,金属复合材料因其独特的物理和机械性能,在航空、航天、汽车、船舶等众多领域得到了广泛应用。
TC4和6061作为两种常用的金属材料,其结合形成的复合板具有优异的力学性能和耐腐蚀性。
本文旨在探讨TC4-6061复合板的热轧复合工艺及其有限元模拟。
二、TC4-6061复合板热轧复合工艺1. 材料准备首先,选取质量合格的TC4和6061金属板材,对板材进行表面处理,去除油污、氧化物等杂质,确保板材表面清洁,为后续的复合做好准备。
2. 复合工艺流程(1)预处理:将处理后的TC4和6061板材按照一定的叠层方式放置,进行预加热处理,以提高板材的塑性和表面活性。
(2)热轧:在一定的温度和压力下进行热轧复合。
热轧过程中要控制好温度、压力、时间等参数,以确保复合质量。
(3)后处理:热轧完成后,对复合板进行退火处理,以消除内应力,提高材料的力学性能。
三、有限元模拟有限元模拟是研究金属复合板热轧过程的重要手段。
通过建立合理的有限元模型,可以模拟热轧过程中的温度场、应力场等物理量的变化,为实际生产提供理论依据。
1. 模型建立根据TC4和6061金属的物理性能,建立热轧过程的有限元模型。
模型应包括材料模型、热传导模型、接触模型等。
其中,材料模型应准确反映TC4和6061金属的力学性能;热传导模型要考虑材料的热传导系数、比热容等参数;接触模型要准确描述板材之间的接触状态。
2. 模拟过程(1)温度场模拟:模拟热轧过程中温度的变化情况,包括预加热、热轧过程中的温度分布等。
(2)应力场模拟:模拟热轧过程中的应力分布情况,包括板材之间的接触压力、剪切力等。
(3)模拟结果分析:根据模拟结果,分析热轧过程中的温度场、应力场的变化规律,为实际生产提供指导。
四、实验结果与讨论通过实际生产与有限元模拟结果的对比分析,可以得出以下结论:1. 合理的热轧工艺参数对TC4-6061复合板的复合质量有着重要的影响。
不锈钢复合板的生产工艺方法
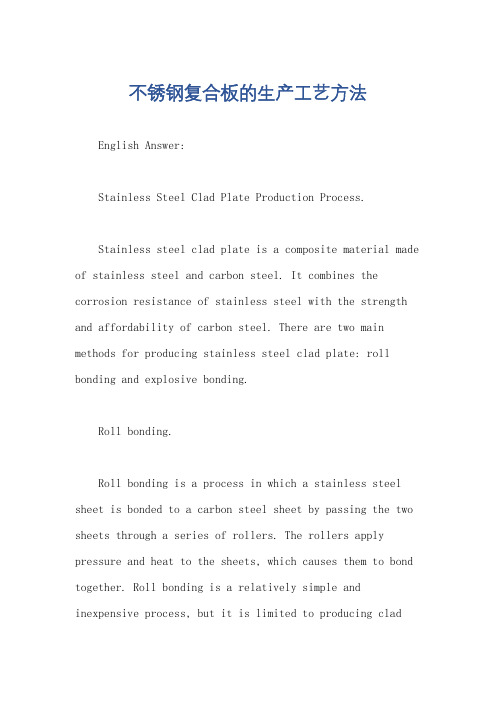
不锈钢复合板的生产工艺方法English Answer:Stainless Steel Clad Plate Production Process.Stainless steel clad plate is a composite material made of stainless steel and carbon steel. It combines the corrosion resistance of stainless steel with the strength and affordability of carbon steel. There are two main methods for producing stainless steel clad plate: roll bonding and explosive bonding.Roll bonding.Roll bonding is a process in which a stainless steel sheet is bonded to a carbon steel sheet by passing the two sheets through a series of rollers. The rollers apply pressure and heat to the sheets, which causes them to bond together. Roll bonding is a relatively simple and inexpensive process, but it is limited to producing cladplates with a relatively thin stainless steel layer.Explosive bonding.Explosive bonding is a process in which a stainless steel sheet is bonded to a carbon steel sheet by using an explosive charge. The explosive charge is detonated between the two sheets, which causes them to bond together under extreme pressure and heat. Explosive bonding produces a stronger bond than roll bonding, and it can be used to produce clad plates with a thicker stainless steel layer.Applications of stainless steel clad plate.Stainless steel clad plate is used in a wide range of applications, including:Chemical processing equipment.Food processing equipment.Pharmaceutical equipment.Marine equipment.Architectural components.Advantages of stainless steel clad plate.Stainless steel clad plate offers a number of advantages over other materials, including:Corrosion resistance.Strength.Affordability.Durability.Disadvantages of stainless steel clad plate.Stainless steel clad plate also has some disadvantages, including:Weight.Complexity of fabrication.Cost.Overall, stainless steel clad plate is a versatile and durable material that is well-suited for a wide range of applications.中文回答:不锈钢复合板的生产工艺。
轧制复合生产特厚板工艺

1 100 ~ 1 050
1 130 ~ 1 120
1 100 ~ 1 050
Ⅱ阶段
开轧温度 /℃
终轧温度 /℃
880 ~ 860
830 ~ 820
—
—
冷阶段
终冷温度 / ℃ 冷却速度 / ( ℃·s - 1 )
650 ~ 600
20650 ~ 600Fra bibliotek20表 3 道次压下规程 Table 3 Reduction schedule for the rolling
Vol. 33 No. 11 Nov. 2011
轧制复合生产特厚板工艺
余 伟 张烨铭 何春雨 徐立善 蔡庆伍
北京科技大学高效轧制国家工程研究中心,北京 100083 通信作者,E-mail: yuwei@ nercar. ustb. edu. cn
摘 要 采用 Q345 连铸坯料,经过表面清理、焊接组坯和抽真空至 1 × 10 -3 Pa 后密封,分别采用两阶段控轧和再结晶型控轧 两种轧制工艺进行轧制. 用剪切、拉伸和冷弯试验检验复合板的力学性能,利用扫描电镜观察分析复合板的组织与结合面. 结果表明: 两种轧制工艺生产出的钢板各项力学性都能达标; 再结晶控轧工艺比两阶段控轧工艺复合效果更好,并生产出的 钢板厚向性能更加均匀. 试验条件下的轧制复合包含机械啮合与再结晶两种机制. 关键词 钢板; 轧制复合; 力学性能; 组织; 超声波探伤 分类号 TG 335. 1
ABSTRACT After surface cleaning,weld combining and vacuumizing to 1 × 10 -3 Pa,Q345 continuous casting slabs were processed by conventional control rolling ( CCR) and recrystallization control rolling ( RCR) . The mechanical properties of the clad rolling plates were tested by shear,tensile and cold bending tests,and the microstructures and combining boundaries were observed by scanning electron microscope ( SEM) . The results show that the mechanical properties of the clad rolling plates produced by the two rolling processes are all qualified. Compared with CCR process,RCR process provides a better bonding effect and the plate has better property homogeneity in the thickness direction. The clad rolling process in the experimental condition involves the mechanical meshing mechanism and the recrystallization mechanism. KEY WORDS plates; clad rolling; mechanical properties; microstructure; ultrasonic testing
复合翅片轧制过程
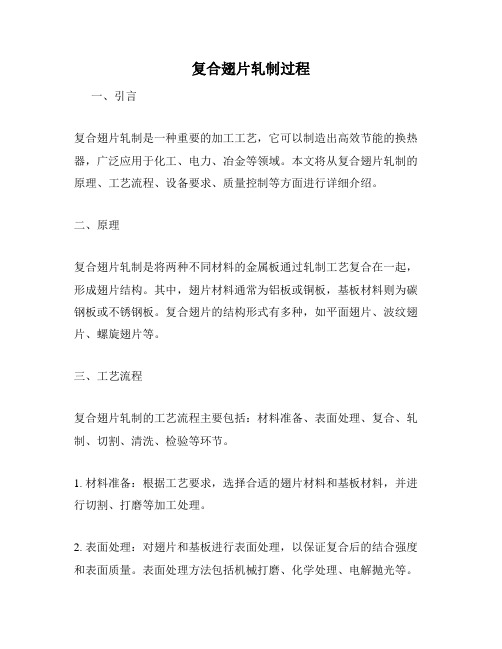
复合翅片轧制过程一、引言复合翅片轧制是一种重要的加工工艺,它可以制造出高效节能的换热器,广泛应用于化工、电力、冶金等领域。
本文将从复合翅片轧制的原理、工艺流程、设备要求、质量控制等方面进行详细介绍。
二、原理复合翅片轧制是将两种不同材料的金属板通过轧制工艺复合在一起,形成翅片结构。
其中,翅片材料通常为铝板或铜板,基板材料则为碳钢板或不锈钢板。
复合翅片的结构形式有多种,如平面翅片、波纹翅片、螺旋翅片等。
三、工艺流程复合翅片轧制的工艺流程主要包括:材料准备、表面处理、复合、轧制、切割、清洗、检验等环节。
1. 材料准备:根据工艺要求,选择合适的翅片材料和基板材料,并进行切割、打磨等加工处理。
2. 表面处理:对翅片和基板进行表面处理,以保证复合后的结合强度和表面质量。
表面处理方法包括机械打磨、化学处理、电解抛光等。
3. 复合:将翅片和基板按照一定的排列方式复合在一起,形成复合板材。
4. 轧制:将复合板材通过轧制机进行轧制,使翅片与基板紧密结合,形成翅片结构。
5. 切割:将轧制好的板材按照要求进行切割,形成所需的尺寸和形状。
6. 清洗:对切割好的板材进行清洗,去除表面的油污和杂质。
7. 检验:对清洗好的板材进行检验,检查其表面质量、结合强度等指标是否符合要求。
四、设备要求复合翅片轧制需要使用一系列专用设备,包括:切割机、表面处理设备、轧制机、清洗设备、检验设备等。
其中,轧制机是复合翅片轧制的核心设备,其性能和精度对产品质量有着重要影响。
五、质量控制复合翅片轧制的质量控制主要包括:材料质量控制、表面处理质量控制、复合质量控制、轧制质量控制、切割质量控制、清洗质量控制、检验质量控制等。
其中,复合质量控制和轧制质量控制是关键环节,需要严格控制轧制压力、轧制速度、轧制温度等参数,以保证产品的结合强度和表面质量。
六、结论复合翅片轧制是一种重要的加工工艺,其制造的换热器具有高效节能、结构紧凑、使用寿命长等优点。
在实际生产中,需要严格控制各个环节的质量,以保证产品的质量和性能。
金属复合轧制

金属复合轧制概述金属复合板的生产方法有复合轧制法、挤压法、爆炸复合法、和钎焊法等。
复合轧制法是指两种或两种以上不同物理、化学性能的金属(基体材料与复层材料)通过轧制使它们在整个接触表面上,相互牢固地结合在一起的加工方法。
复合轧制生产的板带材,具有比组成材料更好的特殊性能。
复合板的轧制,其坯料的组合结构形式大体分为夹层型和表面复合型两种。
复合轧制法可采用冷轧或热轧,冷轧是将多层金属板直接叠合轧制。
热轧则多经组合后焊合边部缝隙,在进行加热轧制。
挤压法是采用组合的双金属坯料进行挤压生产复合料的方法。
爆炸复合法是由爆炸提供能量,使金属在很高的冲击压力下结合。
此法不受结合金属熔点和塑性差别限制,但生产的制品长度和产量有限,技术要求很高。
钎焊法是利用凝固时,能使两金属板焊合在一起的侵润液态金属相,将两种金属板结合在一起的方法。
复合轧制生产的双金属复合材料有钢-钢、铜-钢、铝-铝合金、铝-铜、钢-钛、铝-锌,等。
复合轧制法具有生产灵活,工艺简单,产品尺寸精度高,性能稳定,质量好,可实现机械化、自动化及连续化生产。
生产效率高,成本低,节约贵重金属等优点。
复合板带材主要用于航天、航空的结构材料;交通运输,如铝锡合金=钢双金属汽车轴瓦材料;军事与核工业,如包层弹头及复合装甲板,高能加速器用大型铜-钢复合板;电气、仪表、建筑及化工材料等。
目前,国外双金属复合板的生产,大多采用成卷带张力的连续生产方法,自动化程度高,生产稳定,产品质量容易控制,生产率高。
轧制生产技术的发展:国外已经采取多道次小压下率,实现冷复合轧制,这对改善厚料咬入,或减少压下量防止边部开裂,减少轧机功率和粘辊等效果明显;使用大小辊复合轧制,生产双金属轴瓦材料,即铝锡合金与小辊,钢层与大辊接触(主动辊),可消除钢带层的加工硬化;两层同种金属与一层异种金属的复合轧制,实现以薄带代替厚度进行成卷连续复合生产;并采取先热轧后冷轧,再烧结的工艺生产双金属,可降低复合轧制的压下率,提高结合强度。
- 1、下载文档前请自行甄别文档内容的完整性,平台不提供额外的编辑、内容补充、找答案等附加服务。
- 2、"仅部分预览"的文档,不可在线预览部分如存在完整性等问题,可反馈申请退款(可完整预览的文档不适用该条件!)。
- 3、如文档侵犯您的权益,请联系客服反馈,我们会尽快为您处理(人工客服工作时间:9:00-18:30)。
复合板轧制工艺流程
复合板轧制工艺是一种重要的金属加工工艺,用于生产各种复合板材料,例如铝复合板、钢铝复合板等。
该工艺流程通常包括以下几个主要步骤:
1. 材料准备,首先需要准备用于制作复合板的原材料,通常是铝板和钢板。
这些原材料需要经过清洗、涂层等预处理工艺,以确保表面清洁并具有良好的附着力。
2. 堆叠组合,在复合板轧制工艺中,铝板和钢板通常会被堆叠在一起,形成一个复合结构。
这个过程需要精确的对齐和叠放,以确保最终复合板的质量和性能。
3. 热轧压制,堆叠好的复合板材料被送入热轧机中进行轧制。
在高温和高压下,铝和钢板会发生塑性变形,从而实现两种材料的结合。
热轧过程中需要控制温度、压力和轧制速度,以确保复合板的厚度和表面质量符合要求。
4. 冷轧整平,经过热轧后的复合板可能存在一定的变形和不平整,因此需要进行冷轧整平处理。
这个步骤可以使复合板的厚度和
平整度达到设计要求。
5. 切割和成型,最后,经过轧制和整平处理的复合板会被切割成所需的尺寸,并进行成型加工,以满足最终产品的要求。
总的来说,复合板轧制工艺流程涉及材料准备、堆叠组合、热轧压制、冷轧整平以及切割成型等多个环节。
这些步骤需要精密的设备和严格的工艺控制,以确保最终生产出高质量的复合板材料。