加工高含硫原料对装置的影响和对策
加工高含硫原油设备管道腐蚀及相应措施

20 0 0年 以来 安 庆炼 油 厂 原油 及 主要 生 产 装 置 原 料硫含 量等 基 本情 况见 表 3和 表 4所示 。如 常 减 压装 置 工套 平 均 为 0 9 % , 高 达 1 2 ; 化 .2 最 .% 焦 装置 实 际 进 料 平 均 硫 含 量 为 1 3 % , 高 达 1 .5 最 . 5 % 。两 套装 置均超 过原 料设 计 的硫 含量 值 , 蚀 6 腐
钛材
0 C2 1 R N —P镀 9 rAMo e i
涂料
电化学保护
随着 加工 高 含硫 、 酸值 原 油 , 蚀介 质 变 得 高 腐 越来 越 复杂 , 防腐 蚀 工作增 加 了难 度 。安庆炼 油 给 厂狠抓 防 腐 蚀 措 施 落 实 工 作 , 取 得 了 一定 的 成 并
效。
值上 升 , 次加 工 的硫 腐 蚀 问题 愈来 愈 严 重 , 其 二 尤
是 焦化装 置 ( 表 5 ,00年 至今 , 如 ) 20 己更 换 了 2 0台
管束 , 其泄 漏点 多 在 换 热管 与 管 板 的焊 缝处 , 现 表
为点蚀 、 冲蚀 和裂纹 。 主要原 因为 :
①换 热管 与管板 焊缝 内有 缺 陷 , 在腐 蚀 介质 和 液体 冲刷作 用 下 , 层金 属 冲蚀 , 孑 ( 为针 孔 ) 表 气 L多
收 稿 日期 : 0 —1 —3 2 1 0 0 0 作 者 简介 : 长 青 ,92年 毕 业 于 浙 江 大 学 材 料 系 。 高 级 郑 18 工程 师 。
第 3期
郑 长 青 等 . 工 高 含硫 原 油设 备 管道 腐 蚀 及 相 应 措 施 加
相 当严重 。
表 3 原 油 含硫 情 况
( 庆 石 化 分 公 司炼 油 厂机 动 科 , 安 安徽 安 庆 260 ) 40 1
加工高硫高酸原油注意事项

加工高硫、高酸原油注意事项常减压装置单独加工马瑞油,硫含量高达2.9%并含有硫化氢,给储运、装置加工带来很大安全隐患,并且严重影响产品质量,各生产环节要注意防止硫化氢中毒,装置要24小时不间断巡检。
对加工高硫、高酸原油安全注意事项重申如下:高硫高酸原油对装置的影响:高硫、高酸原油中的比重大、硫含量和重金属含量高,深度脱盐较为困难。
加工这类原油能够造成设备腐和催化剂中毒以及环境污染。
如电脱盐装置会因原油乳化而影响脱盐效果,从而造成分馏塔顶腐性,还会造成分馏塔、加热炉等设备高温部位的腐蚀。
加工高酸原油带来的腐性问题主要集中在蒸馏装置,而加工高硫原油带来的腐性问题,贯穿于整个原油加工过程中。
高温硫化物的腐性是指240℃以上的部位元素硫、硫化氢和硫醇等形成的腐蚀。
典型的高温硫化物腐蚀存在于常、减压塔的下部及塔底管线,常压渣油和减压渣油换热器,催化裂化装置分馏塔的下部,以及焦化装置高温部位等。
在高温条件下,活性硫与金属直接反应它出现在与物流接触的各个部位,表现为均匀腐性,其中以硫化氢的腐位性最强。
燃料重油中通常含有1%-3%的硫及硫化物,在燃烧中大部分生成SO2,其中约有1%-5%在一定条件下反应生成SO3,对设备几乎不发生腐性,但当它与烟气中的水蒸汽结合形成硫酸蒸汽时,在装置的落点部位发生凝结,严重腐蚀设备。
环烷酸腐蚀经常发生在酸值大于0.5mgKOH/g, 温度在270-400℃之间高流速介质中。
它与金属表面或硫化铁膜直接反应生成环烷酸铁,环烷酸铁是油溶性的,再加上介质的流动,使金属表面不断暴露并受到腐性,故环烷酸腐蚀的金属表面清洁,光滑无垢。
在物料的高温高流速区域,环烷酸腐呈顺流向产生的尖锐边缘的流线沟槽,在低流速区域,则呈边缘锐利的凹坑状。
环烷酸腐蚀都发生在塔盘、塔壁、转油线等部位。
另外由于环烷酸盐具有表面活性,会造成油品乳化,从而引起装置操作波动,并造成塔顶腐蚀。
装置在加工此类原油时要做好安全防范措施并从生产工艺上进行调整,保证产品质量合格和污水处理合格。
加工含硫原油的设备腐蚀问题与对策

加工含硫原油的设备腐蚀问题与对策*摘要综述了加工含硫原油对设备的腐蚀问题和应采取的对策。
认为应提高原料油和产品的脱硫能力,和做好工艺防腐及设备的选材工作。
关键词含硫原油性质腐蚀与防护世界原油的硫含量在不断升高,目前硫含量在1%以上的原油占世界原油总产量的55%以上。
据预测原油平均相对密度将上升到 3 g/cm3,硫含量将上升到%。
2001年中国石油化工集团公司下发了《加工高含硫原油安全管理规定》,明确含硫量在1%以上的原油为高含硫原油。
随着我国沿海炼油厂加工含硫原油规模的不断扩大和我国环保要求的不断提高,加工含硫原油所面临的问题也越来越多。
含硫原油有两个比较突出的特点,一是硫含量高,如伊朗拉万原油的硫含量达%,其大于500℃的减压渣油硫含量高达%;二是轻馏分多,蜡油收率较高,如沙特拜里原油小于180℃轻馏分质量收率达%,而我国胜利原油小于180℃轻馏分质量收率只有%(几乎不含C3和C4)。
因此加工含硫原油带来了加工工艺的改动、设备的腐蚀与防护,以及环境保护等问题。
1 含硫原油的主要性质含硫原油主要来自中东,如沙特、伊朗、伊拉克、阿联酋、科威特、阿曼等国家,其主要性质见表1。
从中可见,含硫原油与中国胜利原油相比,轻馏分都较多,密度、粘度、酸值、胶质、凝点和闪点都较低,钒含量则普遍较高,各段馏分的硫含量都较高。
表1 含硫原油的主要性质原油种类伊朗拉万沙特轻质伊朗重质伊朗轻质沙特拜里加蓬曼吉美国北坡阿曼阿联酋穆尔班中国胜利评价日期1997-08-06 1995-03-061997-03-051995-08-271995-12-231997-06-231998-07-271997-07-171993-06-031998-05-20含量,% 0密度/()凝点/℃-22 <-30 <-30 -16 <-30 -15 <-30 <-30 -7 15 开口闪点<28 <21 <21 28 <18 <28 47 <25 <29 57●/℃50℃粘度/()酸值(KOH)/()残碳,%盐含量/()蜡含量,%硅胶胶4 质, %沥青质,%镍含量(×10-6)钒含量(×10-6)HK-180℃收率,%180~260℃收率,%260~360℃收率,%360~500℃收率,%>500℃收率,%汽油含硫,%煤油含硫,%柴油含硫,%蜡油含硫,%减渣含硫,%注:均油轮采样。
常减压装置改炼高含硫的危险分析及安全对策措施

常减压装置改炼高含硫的危险分析及安全对策措施引言常减压装置是炼油厂石脑油裂解工艺的重要组成部分,其中包含的脱汽、常减等设备是整个装置的核心设备。
在作业过程中,经常发生故障,而高含硫的石脑油是导致故障的主要因素之一。
本文将对常减压装置炼制高含硫的危险性进行分析,并提出相应的安全对策措施。
高含硫石脑油的危害性石脑油裂解产生的产品主要有轻质馏分和重质馏分,重质馏分中含有丰富的硫化氢和硫醇等硫化物。
高含硫的石脑油在运输过程中容易发生分解产生大量的硫化氢,对作业人员的身体健康造成极大的影响。
同时,高含硫的石脑油也会加速设备的腐蚀速度,对设备的寿命造成影响。
常减压装置中高含硫石脑油的危险性常减压装置是炼油厂石脑油裂解工艺的重要组成部分。
在常减压装置中,高含硫的石脑油很容易在蒸发器、换热器等部位留下残渣,影响设备的正常工作。
同时,高含硫的石脑油在常减压装置中也会加速设备的腐蚀速度,降低设备的寿命。
常减压装置改炼高含硫的安全对策措施为了避免常减压装置炼制高含硫石脑油带来的安全隐患,需要采取相应的安全措施,具体如下:1. 采用先进的炼制工艺在常减压装置中,应采用先进的炼制工艺,尽量避免石脑油中含有过多的硫化物。
此外,还应加强设备的清洁和维护工作,保证石脑油在设备中的流通畅通。
2. 加强设备的监测针对常减压装置中高含硫石脑油的危害性,需要加强设备的监测工作,及时发现和处理设备中的硫化物残留和腐蚀现象,保证设备的运作安全可靠。
3. 健全应急预案对于常减压装置中高含硫石脑油带来的设备故障和安全事故,应建立完善的应急预案,保证在发生突发事件时能够迅速有效地进行处置,减少损失。
4. 员工的安全教育和培训为了保证员工的安全,需要加强员工的安全教育和培训,提高员工的安全意识和安全技能,确保员工能够正确处理石脑油中的硫化物,避免产生安全事故。
结论常减压装置改炼高含硫的石脑油会带来较大的安全隐患,需要采取一系列的安全对策措施来保证设备的安全运行。
影响硫磺回收装置高效运行的问题分析及解决措施

影响硫磺回收装置高效运行的问题分析及解决措施摘要:随着居民尤其是城镇居民环保意识的增强和国家环保执法力度的加大,硫磺回收装置的地位越来越重要。
硫磺回收装置能高效运行,是提高企业的经济效益和可持续发展的前提条件。
本文探讨分析了影响硫磺回收装置高效安全平稳运行的问题,并针对各问题提出了相应的策略。
关键词:硫磺;回收装置; 设备腐蚀; 制硫一、前言伴随着我国国民经济迅速增长的同时,石油加工高速发展。
高硫原油进口增加及大量含硫燃料油的深加工,释放的硫化物是对环境破环和对空气的严重污染的元凶。
硫磺回收是一件国计民生的大事,所以硫磺回收装置作为配套的环保装置越来越被重视。
二、影响硫磺回收装置高效运行的问题(一)硫磺回收装置工艺设备腐蚀( 1 )高温硫腐蚀。
高温为硫腐蚀制硫设备产生了条件。
一般在250℃左右的高温下,极其容易产生高温硫腐蚀这一现象。
高温硫腐蚀经常会发生在装置设备中的高温部分,如制硫炉内构件、高温掺合阀、废热锅炉、反应器内构件和尾气焚烧炉等部件。
硫化物、单质硫对设备的腐蚀,会随着温度的升高而加重。
(2)硫化氢腐蚀。
硫化氢的腐蚀作用极强。
强度极高的钢材合金产品会因受到硫化氢的腐蚀而产生裂痕,防护不当,会导致设备出现泄露等现象,从而影响整个硫磺回收的工作过程。
(3)二氧化碳腐蚀。
二氧化碳和铁在高温或者有水分的情况下,极容易发生化学反应,生成一种不坚硬的碳酸铁。
碳酸铁中的酸性成分含量较高,具有一定程度的腐蚀性,所以二氧化碳腐蚀也是硫磺回收装置工艺中很常见的腐蚀类型之一。
(4)?温度变化导致的露点腐蚀。
硫磺回收工艺流程中,系统设备管线中存在硫、硫化氢、二氧化硫及三氧化硫等腐蚀性介质及水蒸气,这些介质在低于露点时形成酸性冷凝液,造成低温露点腐蚀,从而对碳钢材质的设备装置造成腐蚀。
当温度低于150℃时易发生露点腐蚀,温度越高,腐蚀越轻,温度越低,腐蚀越严重。
露点腐蚀一般发生在温度低于露点装置的部位,如各种气管线、尾气管线、硫冷凝器管束出口、捕集器以及烟囱的顶部。
加工高硫原油对环保的影响和治理对策

作 者 简 介 : 晓 芹 , 程 师 ,9 7年 毕 业 于 南 京 化 工 动 力 专 科 张 工 18 学校热能工程专业, 现在 炼 油 厂 HS E科 从 事 环 境 保 护工 作
维普资讯
扬 子 石 油 化 工
20 0 6年 第 2 卷 第 6 1 期
时间。
油 罐切 水 ( 化物 2 0 0 / ) 焦 化 汽油罐 切 硫 0 . 0mg L 、
水 ( 化 物 20 1 0 / ) Ⅱ套 常减 压减 压 塔 硫 4 . 0mg L 、 顶 切水 ( 硫化 物 5 1 8 / ) 。 9 . 6mg L 等
表 2 加 工 高 硫 原 油 期 间废 水 污 染 源 调 查 情 况
出 水 硫 化 物 平 均 浓 度 由 非 高 硫 油 加 工 期 间 的
2 2 酸性 水汽提 装置情 况 . 炼 油 厂 有 2 套 酸 性 水 汽 提 处 理 装 置 (4 0 6 0 ) 设计 负 荷分 别 为 4 , 0th 3 0 ,2 0 , O 8 / 。2
高硫 原油 加工 , 污水 处理装 置进 水水 质变化
收 稿 日期 :0 6 2 4 2 0 —0 —2 。 2 0 —0 —2 ; 0 6 6 1
的环 保 问题 , 因此研究 和解 决加 工高硫 原油 的环 保 问题 已成为 炼油 厂面 临的重要 课题 。 1 高硫 原油加 工硫 分布 原油 经过 加工后 , 所含硫 最终 被转 移至产 其 品、 副产 品 、 气 、 体 、 渣 等 中 。 Ⅱ套 常减 压 大 水 废
装置 单炼 沙特 轻 油期 间各 相 关 装置 加 工 原 料 中 平均 硫含量 1 5 , .2 见表 1 。
注: HGO 为 重 柴 油 ; AGO 为 常 压 瓦 斯 油 ; VGO 为 减 压 瓦
炼油厂加工高硫高酸值原油遇到的问题及对策
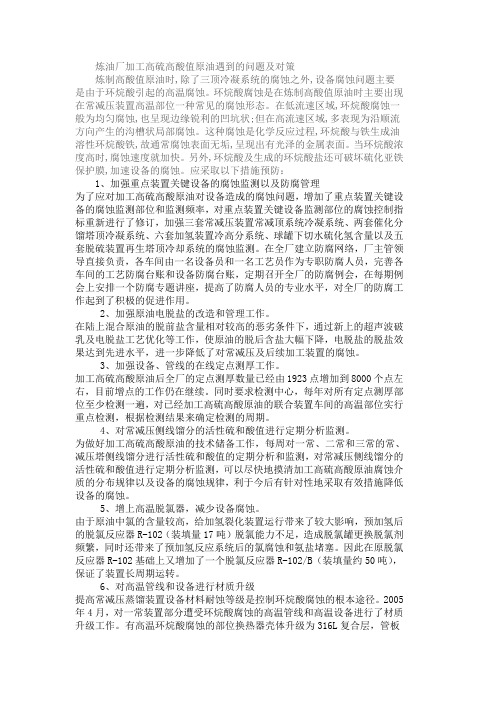
炼油厂加工高硫高酸值原油遇到的问题及对策炼制高酸值原油时,除了三顶冷凝系统的腐蚀之外,设备腐蚀问题主要是由于环烷酸引起的高温腐蚀。
环烷酸腐蚀是在炼制高酸值原油时主要出现在常减压装置高温部位一种常见的腐蚀形态。
在低流速区域,环烷酸腐蚀一般为均匀腐蚀,也呈现边缘锐利的凹坑状;但在高流速区域,多表现为沿顺流方向产生的沟槽状局部腐蚀。
这种腐蚀是化学反应过程,环烷酸与铁生成油溶性环烷酸铁,故通常腐蚀表面无垢,呈现出有光泽的金属表面。
当环烷酸浓度高时,腐蚀速度就加快。
另外,环烷酸及生成的环烷酸盐还可破坏硫化亚铁保护膜,加速设备的腐蚀。
应采取以下措施预防:1、加强重点装置关键设备的腐蚀监测以及防腐管理为了应对加工高硫高酸原油对设备造成的腐蚀问题,增加了重点装置关键设备的腐蚀监测部位和监测频率,对重点装置关键设备监测部位的腐蚀控制指标重新进行了修订,加强三套常减压装置常减顶系统冷凝系统、两套催化分馏塔顶冷凝系统、六套加氢装置冷高分系统、球罐下切水硫化氢含量以及五套脱硫装置再生塔顶冷却系统的腐蚀监测。
在全厂建立防腐网络,厂主管领导直接负责,各车间由一名设备员和一名工艺员作为专职防腐人员,完善各车间的工艺防腐台账和设备防腐台账,定期召开全厂的防腐例会,在每期例会上安排一个防腐专题讲座,提高了防腐人员的专业水平,对全厂的防腐工作起到了积极的促进作用。
2、加强原油电脱盐的改造和管理工作。
在陆上混合原油的脱前盐含量相对较高的恶劣条件下,通过新上的超声波破乳及电脱盐工艺优化等工作,使原油的脱后含盐大幅下降,电脱盐的脱盐效果达到先进水平,进一步降低了对常减压及后续加工装置的腐蚀。
3、加强设备、管线的在线定点测厚工作。
加工高硫高酸原油后全厂的定点测厚数量已经由1923点增加到8000个点左右,目前增点的工作仍在继续。
同时要求检测中心,每年对所有定点测厚部位至少检测一遍,对已经加工高硫高酸原油的联合装置车间的高温部位实行重点检测,根据检测结果来确定检测的周期。
原料性质对渣油加氢装置的影响及控制效果
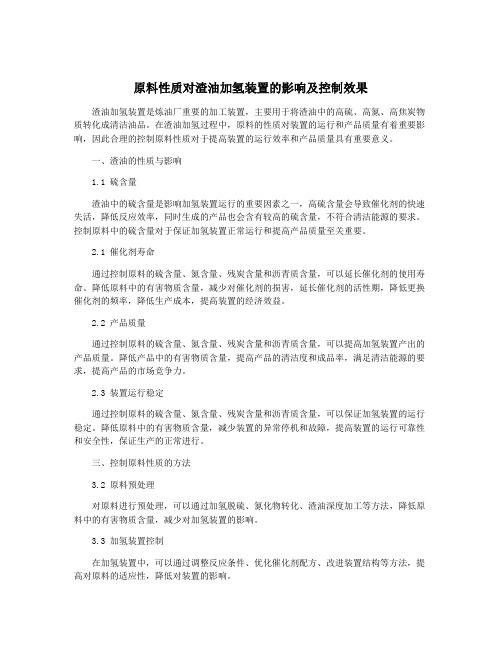
原料性质对渣油加氢装置的影响及控制效果渣油加氢装置是炼油厂重要的加工装置,主要用于将渣油中的高硫、高氮、高焦炭物质转化成清洁油品。
在渣油加氢过程中,原料的性质对装置的运行和产品质量有着重要影响,因此合理的控制原料性质对于提高装置的运行效率和产品质量具有重要意义。
一、渣油的性质与影响1.1 硫含量渣油中的硫含量是影响加氢装置运行的重要因素之一,高硫含量会导致催化剂的快速失活,降低反应效率,同时生成的产品也会含有较高的硫含量,不符合清洁能源的要求。
控制原料中的硫含量对于保证加氢装置正常运行和提高产品质量至关重要。
2.1 催化剂寿命通过控制原料的硫含量、氮含量、残炭含量和沥青质含量,可以延长催化剂的使用寿命。
降低原料中的有害物质含量,减少对催化剂的损害,延长催化剂的活性期,降低更换催化剂的频率,降低生产成本,提高装置的经济效益。
2.2 产品质量通过控制原料的硫含量、氮含量、残炭含量和沥青质含量,可以提高加氢装置产出的产品质量。
降低产品中的有害物质含量,提高产品的清洁度和成品率,满足清洁能源的要求,提高产品的市场竞争力。
2.3 装置运行稳定通过控制原料的硫含量、氮含量、残炭含量和沥青质含量,可以保证加氢装置的运行稳定。
降低原料中的有害物质含量,减少装置的异常停机和故障,提高装置的运行可靠性和安全性,保证生产的正常进行。
三、控制原料性质的方法3.2 原料预处理对原料进行预处理,可以通过加氢脱硫、氮化物转化、渣油深度加工等方法,降低原料中的有害物质含量,减少对加氢装置的影响。
3.3 加氢装置控制在加氢装置中,可以通过调整反应条件、优化催化剂配方、改进装置结构等方法,提高对原料的适应性,降低对装置的影响。
3.4 产品升级通过产品升级,可以改变原料中的有害物质含量,提高产品的附加值,调整原料的来源和使用,减少对加氢装置的影响。
四、结语原料的性质对渣油加氢装置的运行和产品质量有着重要影响,合理的控制原料性质可以延长催化剂寿命、提高产品质量、保证装置运行稳定、达到环保效果。
连续重整装置进料硫含量的影响及控制对策
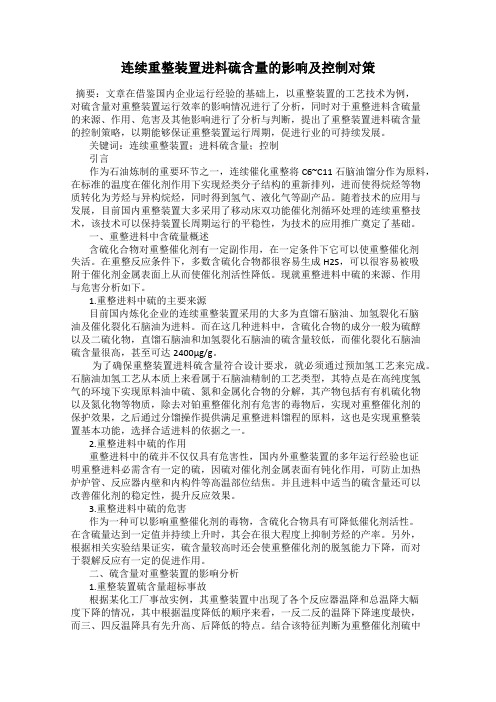
综上所述,与普通重整装置相比,连续重整装置对于含硫量的要求更高,一旦出现催化剂的硫中毒就会影响整个生产过程。在生产中,需要加强进料硫含量的控制工作,做好分析,一旦出现异常问题需要及时进行调控,确保整体硫含量在预期的范围内,以此来提升反应稳定性,降低重整部分运行风险。
参考文献:
[1]张东升.炼厂连续重整装置操作条件优化研究[D].内蒙古大学,2016.
为了确保重整装置进料硫含量符合设计要求,就必须通过预加氢工艺来完成。石脑油加氢工艺从本质上来看属于石脑油精制的工艺类型,其特点是在高纯度氢气的环境下实现原料油中硫、氮和金属化合物的分解,其产物包括有有机硫化物以及氮化物等物质,除去对铂重整催化剂有危害的毒物后,实现对重整催化剂的保护效果,之后通过分馏操作提供满足重整进料馏程的原料,这也是实现重整装置基本功能,选择合适进料的依据之一。
2.重整催化剂中毒
在常规条件下,连续重整工艺对于进料时的硫含量要求为不大于0.5μg/mg,如果经预处理后的精制油仍不能满足重整进料的要求,那么就会导致一些潜在的安全隐患与生产危害。在重整反应器内,硫化物会转变为H2S以及烃类化合物,此时H2S会被催化剂吸附并与其发生化学反应,出现金属中心活性减弱的问题,此时催化剂酸性功能增强裂化反应加剧,出现反应放热量和氢耗增加的情况,C4-组分也会持续增加。硫含量高还会降低催化剂机械强度和比表面积,催化寿命也会减少。
二、硫含量对重整装置的影响分析
1.重整装置硫含量超标事故
根据某化工厂事故实例,其重整装置中出现了各个反应器温降和总温降大幅度下降的情况,其中根据温度降低的顺序来看,一反二反的温降下降速度最快,而三、四反温降具有先升高、后降低的特点。结合该特征判断为重整催化剂硫中毒。经过事故分析,该装置的进料缓冲罐进行切罐时出现了误操作,将含硫量很高的混有蜡油的重原油罐当做进料罐,导致了重整进料硫含量严重超标的结果。结合分析的实际情况来看,经过预加氢单元处理后的精制石脑油的硫含量都已经增加到10倍左右。由于此时进料硫含量严重超标,导致催化剂中毒,并且催化剂出现结焦失活,严重影响后期的生产。
常减压装置改炼高含硫的危险分析及安全对策措施.docx

常减压装置改炼高含硫的危险分析及安全对策措施摘要:随着人类对自然资源的开发,原油价格逐年上涨,很多炼油厂开始以常减压装置改炼高含硫原油,期望以此降低成本。
然而高含硫原油的炼制存在很多危险因素,往往造成很多危险事故,不但威胁到了工作人员的生命健康,而且造成了很大的经济损失。
有鉴于此,本文对常减压装置改炼高含硫的危险因素进行分析,并提出了一些旨在解决问题的对策措施,希望能为高含硫炼油厂的安全运行提供参考。
关键词:常减压装置,高含硫,危险分析,对策措施引言随着原油量逐年减少,其价格也逐年升高,在此形势下,我国不得不从国外原油丰富的市场进口越来越多的原油,然而出于对成本的考虑,这些原油中往往含有很多硫,高含硫原油在进口原油中占的比例越来越大。
一方面低含硫原油越来越少,另一方面其价格攀升,两方面的原因使得国内很多炼制低含硫原油的炼油厂开始改炼高含硫原油。
而用常减压装置改炼高含硫原油存在很多安全隐患,对高含硫炼制能否安全进行构成了威胁。
高含硫炼制过程中主要可能出现的危险事故有:炼油、储运设备泄露以及火灾。
其原因体现在含硫腐蚀,硫化氢毒性和硫化亚铁等腐蚀产物的自燃等三方面的内容上。
本文正是在分析改炼前后原油变化的基础上对三方面的危险因素进行研究,并从防腐、防中毒、防自燃三方面提出了一些应对措施。
1.改炼前后的原油性质对比常减压装置改炼高含硫前后原油性质存在多处不同,这也是其危险因素出现的原因。
常减压装置改炼之前大多采用的是国产原油,其性质主要有①密度大,从密度上看国产原油大多在0.86至0.98g/cm3,密度大小反应了原油化学组成上的差别,密度大的原油轻油产率较低,因此炼油成本相对较高;②含蜡量高,以我国南海原油来说,其含蜡量达到30.3%。
含蜡量与原油的凝点直接相关,南海原油的凝点高达45摄氏度,而大庆原油的含蜡量为26.2%,其凝点也相应降低为30摄氏度,新疆低凝原油含蜡量仅有1.5%,因此其凝点降低至零下58摄氏度;③粘性较大,因此造成国产原油输送成本较高;④含硫量较低,对装置的腐蚀性较小,炼制过程中发生中毒以及爆炸、燃烧等意外事故的可能性也较小。
焦化装置硫腐蚀危害及对策
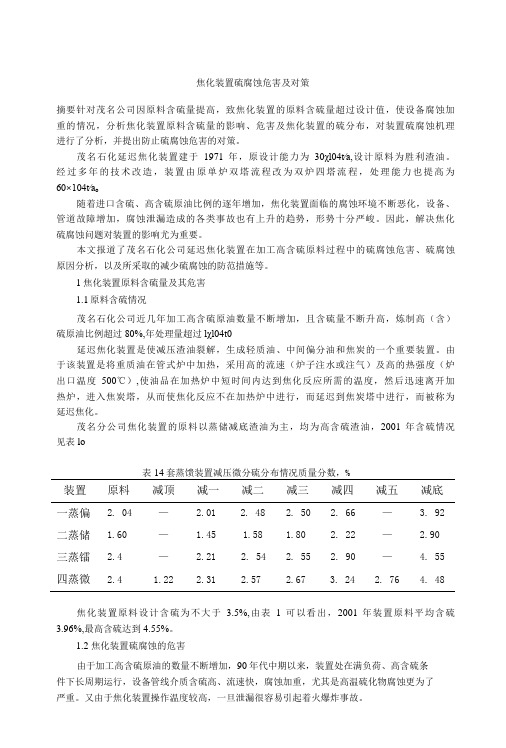
焦化装置硫腐蚀危害及对策摘要针对茂名公司因原料含硫量提高,致焦化装置的原料含硫量超过设计值,使设备腐蚀加重的情况,分析焦化装置原料含硫量的影响、危害及焦化装置的硫分布,对装置硫腐蚀机理进行了分析,并提出防止硫腐蚀危害的对策。
茂名石化延迟焦化装置建于1971年,原设计能力为30χl04t∕a,设计原料为胜利渣油。
经过多年的技术改造,装置由原单炉双塔流程改为双炉四塔流程,处理能力也提高为60×104t∕a o随着进口含硫、高含硫原油比例的逐年增加,焦化装置面临的腐蚀环境不断恶化,设备、管道故障增加,腐蚀泄漏造成的各类事故也有上升的趋势,形势十分严峻。
因此,解决焦化硫腐蚀问题对装置的影响尤为重要。
本文报道了茂名石化公司延迟焦化装置在加工高含硫原料过程中的硫腐蚀危害、硫腐蚀原因分析,以及所采取的减少硫腐蚀的防范措施等。
1焦化装置原料含硫量及其危害1.1原料含硫情况茂名石化公司近几年加工高含硫原油数量不断增加,且含硫量不断升高,炼制高(含)硫原油比例超过80%,年处理量超过lχl04t0延迟焦化装置是使减压渣油裂解,生成轻质油、中间偏分油和焦炭的一个重要装置。
由于该装置是将重质油在管式炉中加热,采用高的流速(炉子注水或注气)及高的热强度(炉出口温度500℃),使油品在加热炉中短时间内达到焦化反应所需的温度,然后迅速离开加热炉,进入焦炭塔,从而使焦化反应不在加热炉中进行,而延迟到焦炭塔中进行,而被称为延迟焦化。
茂名分公司焦化装置的原料以蒸储减底渣油为主,均为高含硫渣油,2001年含硫情况见表lo表14套蒸馈装置减压微分硫分布情况质量分数,%装置原料减顶减一减二减三减四减五减底一蒸偏 2. 04 — 2.01 2. 48 2. 50 2. 66 — 3. 92 二蒸储 1.60 — 1.45 1.58 1.80 2. 22 — 2.90 三蒸镭 2.4 — 2.21 2. 54 2. 55 2. 90 — 4. 55 四蒸微 2.4 1.22 2.31 2.57 2.67 3. 24 2. 76 4. 48焦化装置原料设计含硫为不大于 3.5%,由表1可以看出,2001年装置原料平均含硫3.96%,最高含硫达到4.55%。
高硫原料油对乙烯装置的影响分析及对策

0 5 一20 的称 为 含硫 石 油 。我 国原 油 大 部 分 .% .% 属 于低硫 石 油 和含 硫 石 油 , 庆 原 油 即 是 低 硫 石 大
作者简介 : 杜春梅( 9 6一) 女 ,9 3年毕业 于北京燕化公 司 16 , 19
职工大学石油化工安全专业 , 现从事 乙烯安全生产管理工 作,
量 的 6% , 0 最大投 用量 为 2 4 2th 1 . 。因此 , 含 量 / 硫
×
6 0 0 0
宝 50 0 0
、 4( 啪
,o o o
t'
.
堰 20 0 0
. 一
‘
…
.^ 几
—
U 1I l l ' f l 。‘ l
—‘ |
l 一
摘
要 : 对 乙烯 装 置 裂 解 原 料 石 脑 油 中硫 含 量 偏 高 的情 况 , 析 了使 用 高硫 油在 工 艺 、 备 和 安 全 针 分 设
环 境 方 面对 乙烯 装 置 的 影 响 , 并从 实 际 出发 , 出 了选 择 合 理 的 原 油 炼 制 方 案 来 降 低 石 脑 油 中硫 含 量 , 提 从 根 本 上 解 决硫 含 量 偏 高的 问题 。 另 外 , 可 以从 改进 工 艺操 作 、 强监 测 、 设 备 材 料 进 行 升 级 处理 等 角 还 加 对 度 考 虑 如 何 减 少 高硫 原 料 油对 乙烯 装 置 的 影 响 。 关 键 词 :石 脑 油 ; ;乙烯 装 置 硫
中国石 油化 工 股份 有 限公 司北 京燕 山分公 司 化工 一厂 ( 以下简称燕 化 ) 乙烯 装置 是我 国 2 0世 纪 7 0年代 从 国外 引进 的第 一 套年 产 30k 乙烯 的石 0 t
加工高含硫原油防腐工作经验总结归纳

精心整理[资料]加工高含硫原油防腐工作经验总结含硫原油,经验总结,加工,防腐近几年,加工高含硫原油不断增加,大部分装置的原料含硫超过设计值,设备腐蚀加重,给设备安全运行造成威胁。
针对加工高含硫原油造成的设备腐蚀情况,我们应加强设备防腐管理,开展全面的腐蚀调查,采取各种有效的防腐措施,现对近年1、加工高含硫原油存在的腐蚀问题:1.1加工高含硫原油情况1.2加工高含硫原油后设备腐蚀情况含硫油指含硫0.5-2.0%,表2加热炉腐蚀主要发生在对流段冷进料炉管及软化水管。
二蒸馏装置2000年2月,炉1、炉2、炉3对流段软化水管及冷进料管腐蚀穿孔,于同年5月份大修,3台炉对流段整体更换。
主要原因是瓦斯和燃料油含硫较高,烟气露点上升,管子受烟气露点腐蚀减薄。
塔器腐蚀主要发生在常、减压塔碳钢内构件,腐蚀形态为高温段(>300℃)的均匀减薄,低温段(<120℃)的减薄和坑蚀。
三蒸馏装置2000年底大修检查发现常、减压塔碳钢内件腐蚀较重。
常压塔7-26、43-48层塔盘支梁减薄近一半,部分受液盘穿孔。
主要原因是碳钢受高温硫腐蚀和低温H2O+HCL+H2S腐蚀。
冷换设备腐蚀主要发生在:1高温硫腐蚀;21、三蒸馏、四蒸馏常顶冷却器18-8管束2、三蒸馏装置渣油一次换热器(换度由14mm减至9mm 1.7mm/a。
管线阀门1、19979、10)平衡管腐蚀穿孔;减压塔底流控阀及法兰腐蚀穿孔;常压炉(炉-1)转油线低速蒸汽入口腐蚀穿孔;减四线压力表碳钢接管腐蚀穿孔。
2、1998年减压渣油泵出口Cr5Mo三通腐蚀穿孔。
二蒸馏装置:1、减底渣油线原用20#钢,渣油泵(泵30)出口至换11渣油线腐蚀穿孔,1998年6月和99年5月将泵进出口管更换为Cr5Mo,检查旧管内表面腐蚀严重。
2、渣油泵30出口碳钢弯头腐蚀减薄至3mm,2000年2月7日更换。
三蒸馏装置:1、换13/1C壳程进口短管(20#钢)2000年2月18日因高温硫腐蚀减薄穿孔,测厚为1.5mm。
加氢裂化装置炼制高含硫原油腐蚀状况及对策

近年来 , 工进 口高 含 硫原 油 量 不 断增 加 , 加 致
使 加氢 裂化 装 置原 料硫 含量 也 出现 较 大 幅度 的增 长( 见图 1 。原 料硫 含量 增 加 , ) 导致 脱 丁烷 塔脱 硫 12系统硫 分布 变化情 况 .
化 氢效 果不 理想 , 丁烷塔 的腐蚀 加速 。腐蚀 产物 脱 FS在 床 层 的沉 积 , 压 力 下 降 过快 , e 使 增加 撇 头 停 工 次数 。腐 蚀 的加 速使 脱 丁烷 塔 重 沸炉 系统 设 备 壁 面减 薄 , 响装 置 的安全操 作 。硫化 氢含 量的升 影
%
量 由 0 6 %提 升 至 3 , 因 高压换 热 器 E 0A B .8 % 但 12 / 和 E0 l3没有 更 换 和其 它 因 素 的影 响 , 料 含硫 未 原
能提至 3 %改造 指标 , 只能 提 至 15 , 艺流程 改 .% 工 全 循 环为部 分循 环 。
19 9 7年 19 98年 19 99年 20 0 0年 20 年 上 半 年 01
(. 1石化股份有限公司茂名 分公 司设备监测研究中心 , 广东茂名 55 1 ; 20 l 2 茂名分公司炼化股份有限公司 , . 广东茂名 5 0 1 5 2 1) 摘 要: 对茂名加氢裂化装置炼高 含硫原料后装置 出现的腐蚀情况进 行了概述 , 在总结经 验与不足 的同
硫 腐 蚀
时, 从工艺及材料升级等方面提 出了相应的对策。
单 程转 化率 约 6 v , 料 为 胜 利减 压 蜡 油 ( G ) 0% 原 V O 和焦化蜡 油 ( G 的混 合 油 , G C O=9: ( C O) V O: G 1 质 11 . 原料硫 含量 变化情 况 装 置 19 年 1 ~20 年 6月 间 原料 硫 含 量 97 月 01 变 化 的统 计数 据 ( 表 1 表 明 , 氢裂 化 装 置原 料 见 ) 加 硫 含量 大幅度 上升 。
加工高含硫原油的防范措施

加工高含硫原油的防范措施
随着工业化的加速以及对能源依赖的不断增加,对于能源需求
的供应也在逐渐增加,因此精炼工厂对于高含硫原油的需求也在逐
渐增加,然而这也带来了一些新的挑战和问题,比如高含硫原油的
加工会产生大量的污染物,造成环境的污染,同时也会对工人的身
体健康产生负面影响,因此在加工高含硫原油的过程中需要采取一
系列的防范措施来降低影响。
首先,应该进行原油的预处理。
在加工之前,应该对原油进行
预处理,包括脱水、脱盐、脱蜡等等,以提高原油质量,并且减少
其中的杂质含量,从而降低加工过程中的环境污染,同时也可以减
少设备的磨损和腐蚀。
其次,在加工过程中应该采取先进的技术和设备,比如应用渣
油催化裂化技术,可以降低生产中的硫排放,从而减少对环境的影响。
此外,使用一些先进的化工技术,如高温加氢裂化技术,也可
以在加工高含硫原油的过程中有所帮助。
第三,提高废气处理的技术水平。
在生产过程中,废气是产生
最多的污染物之一,因此需要采取先进的废气处理技术,比如采用
尾气净化器、吸附器等设备,降低硫酸盐等有害气体的含量,从而
使产生的废气满足环境保护要求。
最后,加强生产过程的监管。
在加工高含硫原油的过程中,需
要对生产过程进行全方位的监测和管理,比如加强生产过程的现场
安全监测,加强技术培训和环保意识教育,严格控制硫含量的排放,降低对环境的影响。
加工高含硫原油是一个挑战性很大的任务,在这个过程中需要采取一系列的防范措施,从而降低对环境的影响,提高加工质量,保护生产工人的身体健康,达到可持续发展的目标。
硫磺装置腐蚀分析及对策

硫磺装置腐蚀分析及对策近年来,随着进口高含硫原油炼制的增加,为了适应生产的需要和环保要求,山东汇丰石化硫磺装置于2008年建成投产。
如何认识和解决设备腐蚀问题已成为保证硫磺装置安全生产的关键,根据相关资料和同行交流发现硫磺装置腐蚀有以下特点:制硫过程腐蚀的主要形态在制硫装置过程气中含有SO3、SO2、H2S、CS2、水蒸汽、硫蒸汽等高温气体,以及从加氢反应器出来的高温气体进入急冷塔水洗后形成的酸水,对设备产生的腐蚀,其中主要的腐蚀是酸水电离腐蚀、电化学腐蚀、高温硫腐蚀、低温SO3露点腐蚀和低温SO2露点腐蚀。
一、设备腐蚀分析1、酸水电离腐蚀SCOT加氢反应器出来的高温过程气中含有H2S、SO2、S等介质,进入急冷塔(C-201)冷却。
该过程气主要成分是硫化氢,硫化氢本身就是一种弱酸,不稳定,有剧毒,常温下一体积水能溶4.65体积硫化氢气体。
硫化氢在水中溶解的电离平衡如下:H2S = H+ + HS- K1=1.1×10-7HS-= H+ + S- K2 =1.1×10一15硫化氢与金属反应生成硫化物H2S+Fe=FeS↓+H2↑这就是硫化氢腐蚀钢材的机理。
但是在制硫燃烧炉生产操作过程中出现配风不合理时,过量的SO2进入尾气系统加氢反应器,其负荷超过设计值时,多余的SO2进入急冷塔,与水形成亚硫酸,亚硫酸具有很强的腐蚀性,对设备产生严重的腐蚀。
其在水中溶解的电离平衡如下:H2O + SO2= H2SO3=H+ + HSO3一= H++ SO32-亚硫酸与金属反应:2H+ +Fe=Fe2+ +H2↑2、电化学腐蚀在急冷塔系统中,冷却水与过程气直接接触,使冷却水变成酸性水,在系统中形成电解质溶液,换热器材质为碳钢,在换热器管束表面和管束固定板焊口处发生电化学腐蚀。
钢材上的铁失去电子,碳作为电极,氢在其上面接受电子形成氢气,与电解质溶液形成一个回路。
其电化学反应:Fe-2e Fe2+2H++2e Fe这种电化学腐蚀发生在急冷塔系统中的换热器上较为严重。
浅谈加工高含硫原料对加氢裂化装置的影响
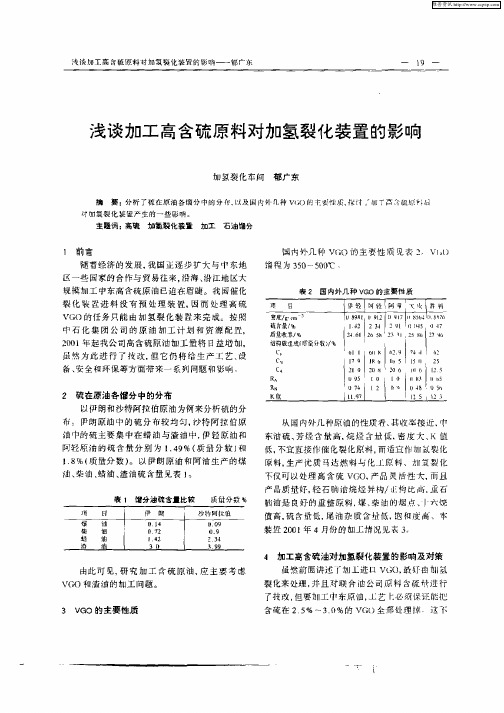
国内外几 种 VG 的主 要 性 质 见表 2 O 。VG O
馏程 为 30 0 " 5 ~5 0 C。
表 2 国内外几种 V O的主要 性质 G
中 石 化 集 团 公 司 的 原 油 加工 计 划 和 资 源 配 置 ,
2 0 年 起我公 司高 含硫 原油 加工 量将 日益 增加 , 01 虽 然 为 此进 行 了 技 改, 它 仍 将 给 生 产工 艺 、 但 设 备 、 全和 环保 等方面带 来一 系列 问题和 影响 。 安
维普资讯
谴 溃 加 工高 含 硫 原料 对 加 氢 裂 化 装 置 的 影 响 —— 郁 广东
1 9
浅 谈/ - 高含 硫 原料对 加氢裂 化装 置 的影响 jv n
加 氢裂化车 间
摘
郁 广东
要 :分 析 了硫 在 原油 各 馏 分 中的 分 布 . 及 国 内 外 几种 VO 以 O帕 T 性 质 . 讨 加 高 疏 料 后 - _ 棒
VG 后, O 对工 艺 。
表 3 原油加工情况 c 管道 +伊朗)
1 5日 ~ 5 ~7日
l
3 0 5 0
l J
【 13
等技术 , 以延长 催化剂 的 使用寿命, 创造 更好 的经
2 硫 在原 油各 馏分 中的分布 伊 朗和 沙特阿 拉伯原 油 为何来分 析硫的分 布 :伊朗原 油 中 的硫 分 布较 均 匀 , 持阿 拉 伯原 沙
油 中的硫主 要 集 中在 蜡 油 与 渣油 中, 轻 原油 和 伊 阿轻原 油 的 硫 含量 分 别 为 1 4 %( 量 分 数 ) .9 质 和 I 8 质 量分 数 ) 以 朗 原 油和 阿 油 生产 的煤 %( 。 油、 柴油 、 油 、 蜡 渣油硫 含量见 表 1 。
加工高含硫油对公用工程装置的影响
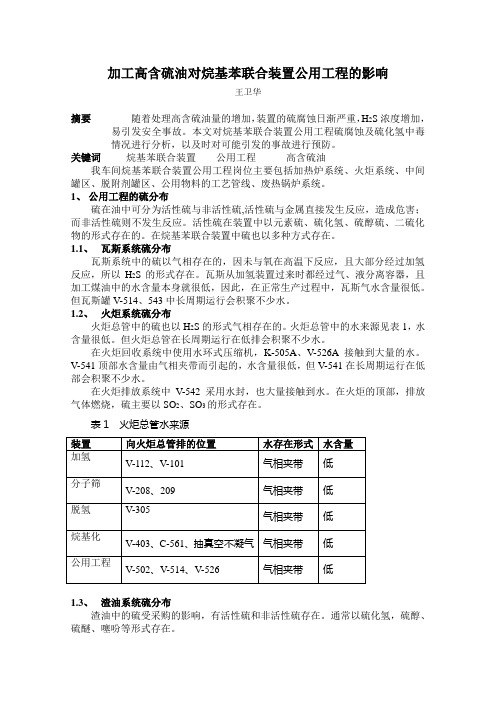
加工高含硫油对烷基苯联合装置公用工程的影响王卫华摘要随着处理高含硫油量的增加,装置的硫腐蚀日渐严重,H2S浓度增加,易引发安全事故。
本文对烷基苯联合装置公用工程硫腐蚀及硫化氢中毒情况进行分析,以及时对可能引发的事故进行预防。
关键词烷基苯联合装置公用工程高含硫油我车间烷基苯联合装置公用工程岗位主要包括加热炉系统、火炬系统、中间罐区、脱附剂罐区、公用物料的工艺管线、废热锅炉系统。
1、公用工程的硫分布硫在油中可分为活性硫与非活性硫,活性硫与金属直接发生反应,造成危害;而非活性硫则不发生反应。
活性硫在装置中以元素硫、硫化氢、硫醇硫、二硫化物的形式存在的。
在烷基苯联合装置中硫也以多种方式存在。
1.1、瓦斯系统硫分布瓦斯系统中的硫以气相存在的,因未与氧在高温下反应,且大部分经过加氢反应,所以H2S的形式存在。
瓦斯从加氢装置过来时都经过气、液分离容器,且加工煤油中的水含量本身就很低,因此,在正常生产过程中,瓦斯气水含量很低。
但瓦斯罐V-514、543中长周期运行会积聚不少水。
1.2、火炬系统硫分布火炬总管中的硫也以H2S的形式气相存在的。
火炬总管中的水来源见表1,水含量很低。
但火炬总管在长周期运行在低排会积聚不少水。
在火炬回收系统中使用水环式压缩机,K-505A、V-526A接触到大量的水。
V-541顶部水含量由气相夹带而引起的,水含量很低,但V-541在长周期运行在低部会积聚不少水。
在火炬排放系统中V-542采用水封,也大量接触到水。
在火炬的顶部,排放气体燃烧,硫主要以SO2、SO3的形式存在。
1.3、渣油系统硫分布渣油中的硫受采购的影响,有活性硫和非活性硫存在。
通常以硫化氢,硫醇、硫醚、噻吩等形式存在。
1.4、加热炉系统硫分布渣油、瓦斯中的硫在加热炉中燃烧生成SO2、SO3,三氧化硫与烟气中的水蒸气化合形成硫酸蒸汽。
因此加热炉及烟囱中的硫主要以SO2、SO3和硫酸的形式存在的。
1.5、积聚硫的分布在装置的有些部位虽然硫含量不高,但经过长周期的运行,局部的硫含量已经很高。
- 1、下载文档前请自行甄别文档内容的完整性,平台不提供额外的编辑、内容补充、找答案等附加服务。
- 2、"仅部分预览"的文档,不可在线预览部分如存在完整性等问题,可反馈申请退款(可完整预览的文档不适用该条件!)。
- 3、如文档侵犯您的权益,请联系客服反馈,我们会尽快为您处理(人工客服工作时间:9:00-18:30)。
加工高含硫原料对装置的影响和对策景录昌中石化金陵分公司(南京210033)摘要金陵分公司作为集团公司进口油加工基地,原料硫含量逐年上升,RFCC作为分公司重油加工的要紧装置之一,硫对装置的阻碍越来越明显,本文将就硫对装置的阻碍,降低产品硫含量和减少硫污染的手段进行调研并简要分析。
关键词高硫原料污染汽油总硫腐蚀1 前言中国石化金陵分公司是一个大型燃料型原油加工基地,依照集团公司的“十五”规划,金陵分公司作为进口油加工基地,“十五”末,高含硫原油加工能力将达到500万吨/年,占加工能力的50%,这其中的绝大部分今后自中东地区。
重油催化装置是按照处理管输蜡油与渣油的混合料而设计的,其设计的原料硫含量只有0.54 %。
而中东原油如典型的沙特轻质原油硫含量为1.7%,中质、重质原油硫含量达2.8%,其催化原料硫含量将达到2%~3%,远远高出装置设计值。
原料中硫杂质的存在不仅阻碍产品质量,对设备腐蚀、环境污染和安全生产也构成一定的威逼。
2 硫在加工过程中分布及危害2.1 硫在加工过程中的分布在催化裂化过程中,原料油中的硫化物以不同形式转化分布到裂化产品中,对产品质量和环境造成一定污染。
清晰地了解和把握了催化裂化过程中硫分布规律,能够估算出再生烟气、酸性气、汽油、柴油中的硫含量,为满足产品质量的要求、防止大气污染、减缓设备腐蚀而采取相应的措施。
表1为国内部分催化裂化装置的硫分布。
从表中能够发觉,硫在气体产品中达到40%以上,催化裂化要紧产品汽油硫含量为原料硫含量的7%~10%(与汽油馏分的切割范畴有关)。
2.2 RFCC装置原料硫含量的变化及装置硫平稳表2是金陵分公司重油催化裂化装置的原料硫分析数据,说明原料硫含量总体呈上升趋势,缘故是进厂原油品种发生了变化,进口原油比例增加,表3为2000年装置硫平稳标定数据。
表2 原料硫含量分析数据时刻1999-06 2000-01 2000-06 2000-10 2001-01 2001-06 2001-09 2002-06硫含0.590.550.580.640.500.650.80.87量,%从表3能够看到,在装置加工过程中,有约50%的硫以硫化氢的形式去硫磺回收制硫,其余的硫则随产品带出,在产品使用中以SO X的方式排入大气,造成污染。
当原料硫含量达到0.66%时,装置精制汽油硫含量已超过国家定于2003年开始实施的新的汽油标准;再生烟气中硫含量也超过了国家大气排放标准。
硫在装置加工过程中造成的阻碍已十分明显,必须引起高度重视并采取相应措施。
2.3 加工高含硫油带来的问题2.3.1 再生烟气携带SO X增加原料通过催化裂化反应后,大约有7%~10%的硫沉积在焦碳上,经再生系统烧焦后,转变成SO2 和 SO3,其中SO2占90%,是形成酸雨的要紧成分。
一套处理量100万吨/年装置满负荷生产、原料硫含量为0.6%时,每天排入大气的硫化物将达到3 000kg,与日益提高的环保要求相距甚远,更不符合清洁生产要求。
2.3.2 汽油总硫不符合新标准国家新的汽油标准要求硫含量小于0.08 %,新标准已于2000年7月在北京、上海、广州三大都市实施,2003年1月在全国范畴内实施。
随着原料硫含量的上升,在原有的工艺条件下,催化裂化装置生产的高标号汽油总硫也会随之升高,国内部分厂家稳固汽油总硫分析见表4。
表4 国内部分FCC汽油总硫项目武石化1号长岭2号九江齐鲁原料硫含量,%0.710.740.84 1.03稳固汽油总硫 /(μg·g-1)983 1 026 1 325 1 572重油催化装置设计时采纳的是管输油,硫含量为0.54%,远低于进口的中东油,因此,装置在处理中东原油时,汽油总硫急剧上升,表5是1999年4月全厂加工15%伊朗油进行大负荷标定时装置汽油硫含量分析。
重油催化装置本次加工的是65%含硫量为0.96%的直馏蜡油(管输油掺炼15%伊朗油时的直馏蜡油)和35%含硫量为0.51%的常压渣油(陆丰油、苏北油),但由于要紧原料—直馏蜡油的含硫量较高,因此精制汽油的总硫大多数超标,有时甚至达0.12%,远高于国家标准,如不采取措施,装置生产的高标号汽油将不能出厂。
表5 重油催化装置汽油总硫μg/g3日4日5日6日8日9日10日12日重催汽油1200 1286 1215 1192 937 354 418 8252.3.3 硫化物危害增大设备腐蚀严峻随着原料硫含量的增大,气体产品中硫化物(硫化氢)也随着增加,含硫化氢浓度高的介质(富气、酸性水、酸性气等)其输送管线、设备腐蚀加剧;脱硫区管线腐蚀严峻,酸性气中硫化氢浓度升高、流量增大,一旦腐蚀泄漏,将产生严峻的后果。
关于FCCU装置来说,气体脱硫单元的设备腐蚀出现普遍性:分公司RFCC再生塔T-3203抽出至重沸器E-3204入口线弯头下方管线在2002年曾显现两次腐蚀穿孔;空冷E-213、E214管束显现4~5根管子腐蚀泄漏;济南分公司脱硫单元2001年先后发生E-602壳程泄漏、E-602管程小帽腐蚀穿孔、E-603腐蚀内漏;洛阳分公司曾显现液态烃管线腐蚀穿孔;广州分公司的液态烃脱硫塔下部人孔加强板信号孔渗漏,经解刨发觉一根裂纹径向深度6.5 mm。
反再系统再生烟气部分的腐蚀也不容忽视:茂名分公司在1998年掺炼马拉西、阿曼等多硫渣油时,1号、2号FCCU的三级旋分器外壳先后显现裂纹,专门是2号FCCU的再生器稀相段以及外集气室经常显现裂纹;1998年底锦西石化FCCU三旋本体一条200 m长的环焊缝上显现裂纹,经认真检查发觉再生器系统共有裂纹120条。
烟气硫含量升高,使烟道露点腐蚀温度升高,对锅炉省煤器管的腐蚀加重,必须采纳提高排烟温度的方法减少腐蚀,但造成能量回收减少。
3 催化裂化应对高硫油的计策3.1 降低催化汽油硫含量的途径催化裂化汽油脱除硫的目的是在保证汽油辛烷值缺失最小的情形下将汽油的总硫降至最低,这几年国内外差不多开发出一整套比较成熟的技术。
3.1.1 催化裂化进料加氢预处理催化裂化进料硫含量为1.2%~2.8%的VGO、硫氮含量高的CGO需要加氢预处理。
象长岭分公司用CH-20钼镍催化剂将硫含量0.89%、氮含量0.45%的焦蜡经加氢后硫含量降到0.04%、氮含量降到0.18%;茂名分公司将中东的减压渣油通过加氢处理,硫含量从3.38%降到0.4%~ 0.5%。
从而保证了催化裂化汽油的硫含量达标。
3.1.2 选择性加氢脱硫该项技术是依照催化裂化汽油中硫的分布特性(见表6),将汽油馏分切割成轻中重馏分,然后进行选择性加氢脱硫。
轻组分可用碱洗、抽提脱硫醇,中重组分进行选择性加氢脱硫。
法国石油研究院开发的Prime-G技术,脱硫率大于95%,可使重组分汽油中硫含量降低到100~150 μg/g,轻中组分汽油硫降至30 μg/g。
表6 催化裂化汽油中硫分布项目占汽油总量比例,% 占汽油总硫比例,%馏分 /℃C5~120 60 15120~175 25 25175~220 15 603.1.3 脱硫催化剂和添加剂目前,国内助剂厂家差不多开发出多种汽油硫转移催化剂,取得了良好成效。
依照调研结果,今年7月在分公司RFCC装置进行试用南京化工厂生产的 NS-FCC汽油硫转移助剂,NS-FCC汽油硫转移助剂的有效组分属L酸,这些L酸能将汽油中的硫化物裂解成碱硫化物,通过吸附和化学反应相互作用而脱硫。
而硫分子通过吸附在催化裂化催化剂上的NS-FCC催化脱硫剂而转化为H2S。
FCC汽油中的含硫化合物要紧以噻吩类化合物的形式存在,在NS-FC C脱硫剂的作用下,L酸能够选择吸附汽油馏分中具有孤对电子的噻吩类化合物,经氢转移反应将噻吩环饱和,提高四氢噻吩裂化为硫化氢的速率,从而减少了四氢噻吩脱氢转变为噻吩的可能性。
使用前后产品硫分布见表7、表8。
日期原料总硫,%稳固汽油柴油含硫,% 硫醇×10-6收率,%硫占原料硫,%硫醇占原料硫,%含硫,% 收率,%硫占原料硫,% 试用前0.87 0.14 102.7 48.34 7.91 0.57 1.16 22.68 30.05试用后0.78 0.08 100.09 45.14 4.76 0.61 0.77 29.09 31.36从表7中数据能够看出,加剂前稳固汽油总硫占原料总硫的百分比平均为7.91%,加剂后平均为5.03%,较加剂前相对降低36.4%。
说明该剂对汽油的脱硫成效较突出。
加剂前后汽油硫醇含量变化不大,说明该剂对硫醇的脱除不敏锐,从另一方面也反映了该剂的脱硫机理。
从表8能够看出,助剂试用期间,干气及液化气中H2S占原料硫的百分比明显上升,说明该助剂有将液体产品中的硫转化为H2S气体的功能。
日期原料总硫,%干气液化气含H2S,%含H2S ,%收率,%占原料硫,%含H2S,% 含H2S,% 收率,%占原料硫,% 试用前0.87 4.07 7.35 1.19 9.95 0.83 0.61 19.25 13.37试用后0.78 3.16 5.99 1.27 9.78 0.79 0.55 18.77 11.15比较0.09 0.90 1.36 -0.08 0.17 0.04 0.06 0.48 2.22图1 助剂占系统藏量百分比与汽油硫占原料硫关系图为了更明显地看出该助剂对汽油的脱硫成效,把该助剂占系统藏量的百分比与汽油总硫占原料总硫的百分比绘制曲线图1,从图1中能够看出,当助剂占系统藏量4%~5%时,汽油脱硫成效趋于平稳,可见该剂用量达4%~5%应为最佳用量。
3.2 降低烟气SO X排放量的方法炼油企业排放的SO X与燃煤企业相比排放量相对较少,但其中的80%以上来自催化裂化装置,从FCC再生器排放的氧化硫一样由90%的SO2和10%SO3组成,由于我国大多数炼厂都靠近大都市,这必将对都市的大气造成环境污染,甚至形成酸雨和迷雾。
在国家颁布的《环保法》里,对FCC的再生烟气中硫化物的排放实行总量操纵,严禁超标排放,其中1997年往常的装置排放量不大于700 mg/m3,以后的装置不大于500 mg/m3,国外的标准更高。
国内外炼厂在降低FCC烟气中硫化物的排放量方面做了大量工作,比较成熟的做法有:a)烟气洗涤,该方法投资较高,操作费用也大,而且在洗涤过程中产生的废弃石灰、苛性碱等废物处理存在一定问题,b)原料加氢脱硫,需要的投资最大,但通过对原料的加氢预处理,可提高目的产品的收率。
c)SO X助剂,需要的投资最少,而且对减少SO X排放专门有效,国内的SO X助剂开发已达到一定水平。
SO X助剂减少烟气中SO X排放分两步:在再生器中,焦碳中的硫氧化成SO2和SO3,这两种氧化硫都能够被吸附在SO X助剂上,但SO3更容易被吸附,SO3与助剂中的一种金属氧化物反应并转化成金属硫酸盐,在氧和助剂中氧化催化剂存在的情形下,SO2第一被氧化成SO3,然后SO3再与金属氧化物反应生成金属硫酸盐。